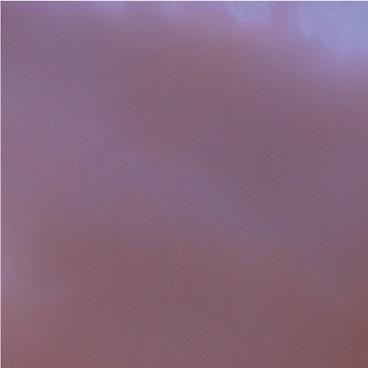
9 minute read
Positioned to weather the storms



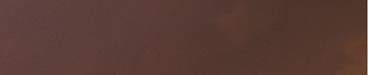
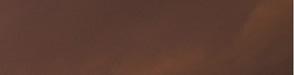

Lyle Hanna, Commonwealth LNG, USA, mmonwealth LNG, US provides an overview of the 8.4 million tpy export LNG terminal project million tpy export LN under development in Louisiana, US. evelopment in Louisia
Resilience. Residents of Cameron Parish, Louisiana, US, have come to know the full measure of the term as they continue to rebound from taking the brunt of two 2020 hurricanes that coincided with a global pandemic and sharp downturn in the energy industry so vital to their economic wellbeing.
Commonwealth LNG’s 8.4 million tpy export terminal project under development at the mouth of the Calcasieu Ship Channel near Cameron was also impacted by these
, Louisiana, US, events. However, Commonwealth now looks to not only aid in f the term as the region’s ongoing recovery, but also expand Southwest the brunt of Louisiana’s prominence as a US leader in exporting clean obal pandemic and affordable LNG to all corners of the world. vital to their ort terminal e Calcasieu d by these events. However, the region’s ongo Louisiana’s promi and affordable LN
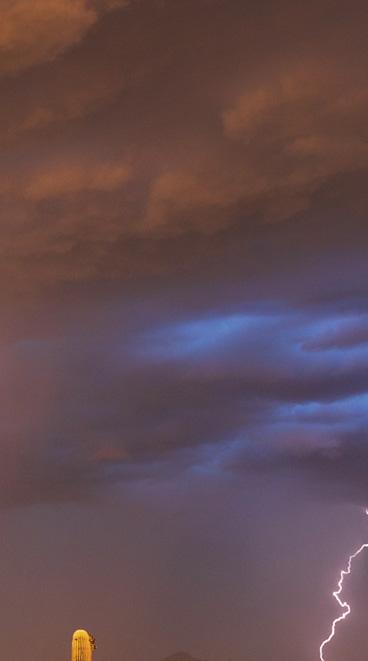
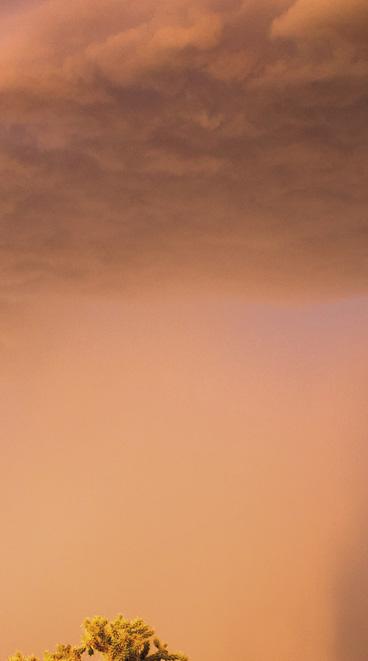
Leading the development Leading th
The project’s leadership team is committed to building a The project’s lead world-class LNG facility by staying relentlessly focused on world-class LNG f managing risk and lowering capital cost. The effort is being managing risk an
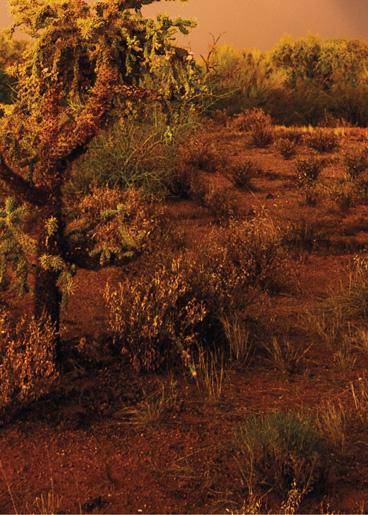
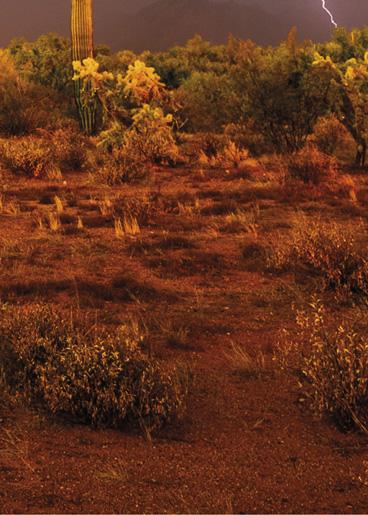
led by Commonwealth CEO Paul Varello, who founded the company in 2014.
“I took the time to assemble the best team I could find for this very important project, and I continue to be very pleased with the results,” said Varello. “My teammates share my vision for controlling costs while improving schedule, quality, operability, and safety. At our core we are creative engineers and project developers with strong experience in LNG.”
Varello has been in the engineering and construction industry for more than 50 years. He was formerly CEO of Sterling Construction Company, a publicly held construction company with over 6000 employees building major infrastructure projects. Prior to Sterling, he was Founder of Commonwealth Engineering and Construction Company, specialising in the design and construction management of refining, chemical, LNG, and gas processing projects.
Varello began his career at Fluor Corporation and for 18 years was involved in the design and construction of hundreds of major projects around the globe, including modular processing plants built in remote and inhospitable locations in the Middle East and Alaska, US.
Based on this extensive background, Varello recognised early that success in the next generation of LNG facilities would require a more engineering-focused approach to drive down costs and meet escalating environmental standards.
“We are an engineering-driven team with finance and commercial support,” says Varello. “Most other projects are the opposite. Because of this, we have spent the time necessary on the front end designing a facility that will allow us to achieve the lowest cost offering in the Gulf Coast.”
Integral to this success is a highly modularised approach to substantially reduce both costs and schedule. Commonwealth has teamed with Technip Energies for the preliminary stages of engineering. Technip Energies has unparalleled modular LNG experience, delivering 22 million tpy of modularised LNG capacity between 2016 and 2019. Among recent examples of Technip Energies’ work is the Yamal LNG project in Russia, where large and complex modules were successfully implemented in harsh climate conditions.
Commonwealth LNG represents a next generation LNG export facility designed to provide a platform for meeting the unique requirements of the next wave of LNG demand. While the pandemic depressed energy markets worldwide, LNG has been surprisingly resilient, and is currently experiencing a resurgence in pricing and demand.
“We expect the LNG market to continue its growth and increase significantly by the time our facility comes online in 2025,” said Varello. “Projections show the global LNG market will need additional contributions from new supply projects starting right about the middle of the decade, and the requirements grow aggressively thereafter. In the meantime, we are seeing trends toward shorter duration contracts and renewed emphasis on the ability to offer low-cost solutions.”
Varello also sees increasing interest for offtake agreements based on Henry Hub-based pricing.
“The robust production of shale gas results in stable current and forward prices for US natural gas, particularly when compared to other international indexes,” Varello notes. “Our analysis indicates that international LNG buyers will choose to allocate around 30% of their long-term supply portfolio to US-sourced, Henry Hub-priced LNG in order to take full advantage of this lower volatility.”
Looking to ensure its share of this market segment, Commonwealth is offering tenors as short as 10 years and the lowest costs for tolling services in the US.
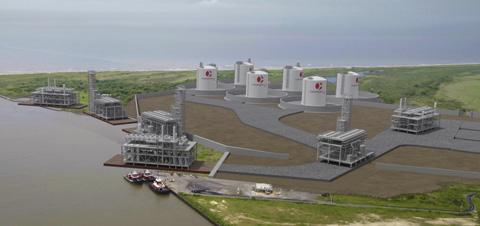
Figure 1. A fully modular design and construction approach for Commonwealth LNG’s liquefaction trains, auxiliary equipment, and LNG storage tanks will dramatically reduce on-site craft labour requirements, lower the overall capital expenditure, and trim a full year off the field construction schedule.
Figure 2. Six 50 000 m3 tanks are being yard-fabricated with a 9% nickel steel inner containment wall and a carbon steel outer wall before transportation to site. Marine facilities will accommodate LNG carriers up to 216 000 m3 .
Figure 3. Commonwealth LNG’s location provides convenient access to a variety of gas supplies and access to the Gulf of Mexico. The facility design calls for high efficiency, state-of-the-art gas turbines, and best-in-class dry low emissions technology.

Marine offloading up to Q-Flex
Admin area Thermal oxiders & hot oil
Utilities 300 000 m3 of modular LNG storage
8.4 million tpy modular liquefaction with six 1.4 million tpy trains
393 acres secured
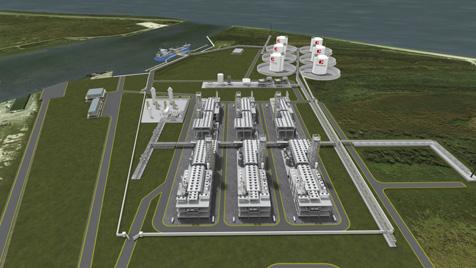
Low CAPEX = low cost The Commonwealth LNG facility site is 393 acres, including a storm surge wall built to withstand severe weather events, including Category 5 hurricanes. The perimeter wall will be 26 ft high on the Gulf and ship channel sides and 21 ft high on the inland sides.
Locating the facility right on the coast offers transit cost savings, better access during periods of fog, and advantages when channels to more inland facilities become blocked (grounded ships, barges, sunken vessels, or debris) to deep draft ships such as LNG tankers.
The project’s 3-mile long, 42 in. dia. feed gas pipeline will connect the LNG facility with existing intrastate and interstate pipelines, creating a header system for the receipt of feed gas. The feed gas will be pretreated to remove mercury, carbon dioxide, water, and heavy hydrocarbons. It will then be routed to the liquefaction unit for multiple stages of cooling at high pressure. In each stage, the gas stream will be cooled and partially liquefied at the lower temperatures provided by the refrigeration cycle.
Six liquefaction trains, each with 1.4 million tpy of nominal liquefaction capacity, will use Air Products and Chemicals Inc.’s proprietary single mixed refrigerant (AP-SMRTM) technology. Air Products is one of the world’s leading providers of natural gas liquefaction technology, coil-wound heat exchangers, and related equipment and services. The company has designed, manufactured, and successfully started-up nearly 120 mid scale and large LNG plants.
Commonwealth’s modular approach emphasises offsite fabrication for the liquefaction trains, other utilities, and larger piping racks. In addition to the reduction in cost and construction schedule, the plan minimises on-site laydown space and construction workforce requirements.
“We are designing and building a project that will start-up easily and run efficiently,” noted Varello. “We believe that our modular design could be efficiently replicated on other LNG projects.”
The company is even extending modularisation to its storage tanks. The tanks are being yard-fabricated with a 9% nickel steel inner containment wall and a carbon steel outer
wall before transportation to site. Upon installation, a concrete secondary containment wall will be added against the outer carbon steel wall. The prefabricated storage tanks will be hydrostatically tested on site. Each tank will provide 50 000 m3 of storage capacity for an aggregate capacity of 300 000 m3, or approximately 5.4 days of LNG production. The marine facilities are designed to accommodate LNG carriers ranging from 10 000 m3 (small scale carriers) to 216 000 m3 (Q-flex carriers). Four 16 in. dia. loading arms will be installed; two liquid arms, one hybrid arm that can handle liquid or vapour, and one vapour-only loading arm. Commonwealth LNG’s six process trains are Figure 4. Superimposing a scale rendering of one of Commonwealth each being designed as two connected modules LNG’s liquefaction modules on the image of Houston’s NRG football stadium in the US illustrates the size of the units to be incorporated in the six-train facility. for the pre-treatment and liquefaction processes. The modular components will be fabricated in subcontracted yards, likely in Asia, before being preassembled and transported by heavy lift vessels or large barges to the site for installation. Equipment carriers will be offloaded and transported to the prepared foundations by crane or self-propelled modular transporters. Most of the facility piping will also be fabricated and loaded into modules. Installation of LNG process components, major utility equipment, and interconnecting piping will be co-ordinated and sequenced for efficient, simultaneous workflow. Equipment and modules will be delivered after foundation pads have been completed to eliminate the need for additional on-site storage. System testing will be conducted shortly after installation. Over the duration of its construction period, the project is expected to create an average of 800 on-site engineering and construction jobs, with the workforce peaking at approximately 2000. Once operational, staffing will include slightly more than 200 personnel. At only 36 months from Final Investment Decision (FID) to substantial completion, Commonwealth’s facility will have one of the shortest implementation schedules to date for a baseload LNG project. Much of this expected schedule advantage stems from the proposed mid scale, multi-train modular strategy, which makes train fabrication more compact, simpler, and more repetitive, and reduces both the quantity and duration of needed on-site resources. Meeting current and future environmental goals As the newest entrant on the growing southwest Louisiana LNG landscape, Commonwealth will be evaluating technically feasible options in its design for reducing the amount of CO2 and methane generated. Varello said his company is also exploring various partnering relationships with suppliers of technologies capable of capturing CO2 emissions for commercial use or sequestration. Although liquefaction represents only a small portion of the lifecycle impact of the natural gas carbon footprint, Commonwealth is committed to minimising or eliminating carbon emissions toward a goal of providing carbon-neutral LNG to support long-term national and international goals in climate management.
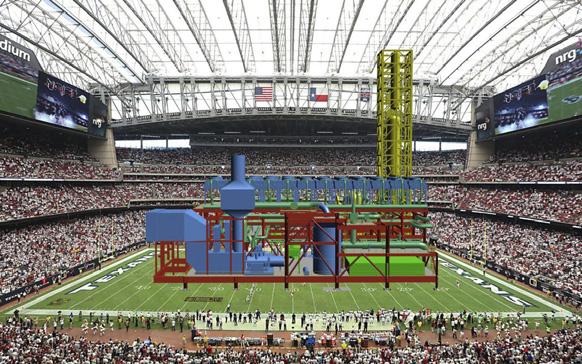