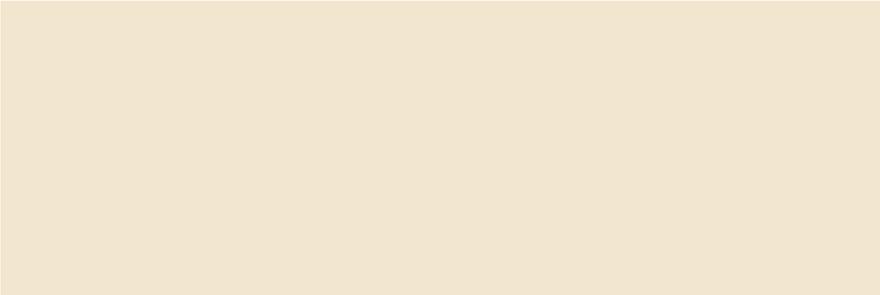
6 minute read
Pump it greener
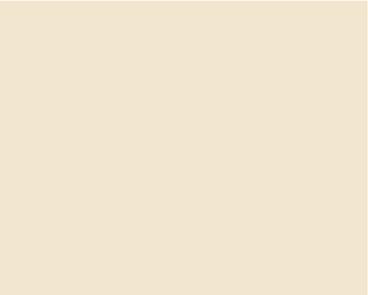

Stefano Calandri, Vanzetti Engineering, Italy, provides an overview of the journey of LNG and the role of cryogenic pumps throughout the stages.

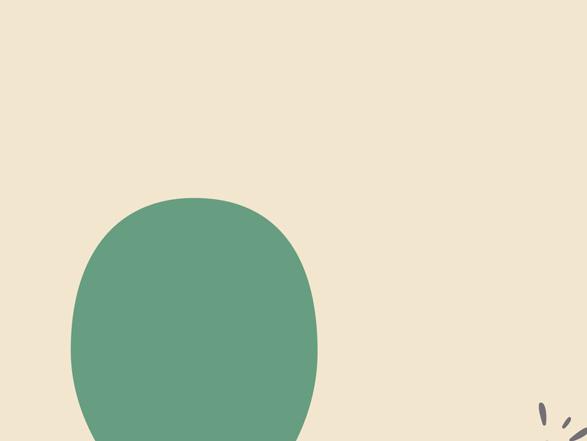
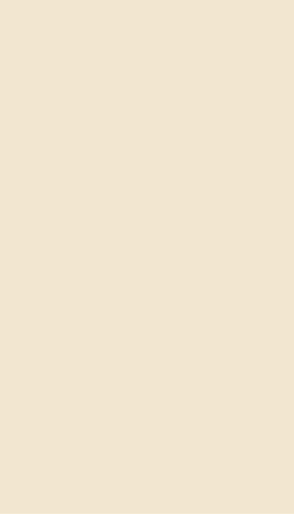
nergy trends are increasingly focused on alternative, renewable, and green energy. In terms of transport, in addition to the electric and hybrid option, there has been a shift towards fuels with an extremely low environmental impact. In a global situation that is adapting to worldwide low emission standards correlated with values defined by the 2030 zero emissions protocol, now more than ever it seems indispensable to continue the change towards all those sources of energy with a low environmental impact. However, it should be noted that unfortunately renewable energy alone is not able to cover the entire need of countries.
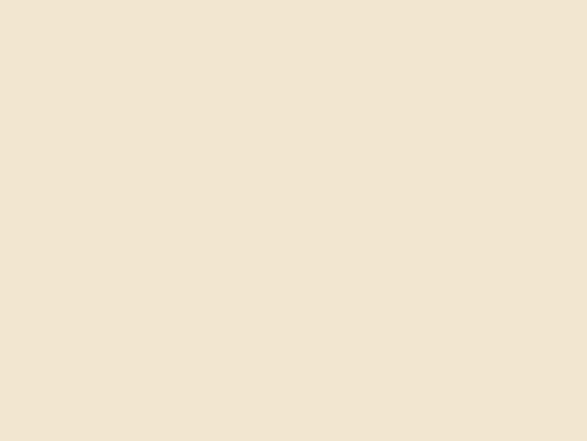
A solution exists
LNG is one of the alternatives that is proving successful. It has properties that can contribute to achieving the goals set by the 2030 protocol. The future that awaits, in terms of clean energy, could provide new and numerous opportunities. The increase in the use of LNG is not limited to just the transport sector but a reality that encompasses industrial areas and the equally important energy production sector. This transition fuel has significant advantages if compared to the parameters of fossil fuels. Vanzetti Engineering, an Italian enterprise with over 30 years of experience in the LNG sector, understood the potential of this type of fuel right from the start, manufacturing cryogenic pumps that are able to support any downstream or upstream application of the LNG value chain.
A sector continuously expanding
LNG is a valid energy source as long as some basic rules are followed. As a matter of fact, when LNG is handled safely, it represents the best alternative to fossil fuels, since its carbon emissions are 85% lower, and thus it is characterised
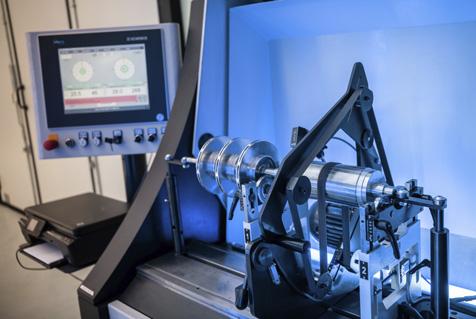
Figure 1. Computerised test and control phase on the rotor of a centrifugal pump.
Figure 2. Rotor and helicoid detail of a centrifugal pump.

by a very low environmental impact. Moreover, this type of fuel is increasingly used in the field of transport, in light of the European regulations on emissions. One of the most significant advantages of LNG is that it rarely needs special treatments after extraction and can be used directly, unlike fossil fuels that require energy to be refined. Its composition is almost all methane (between 90 - 98%) combined with other gases such as butane and ethane for the remaining percentage. For example, LNG has been witnessing increasingly growing uses in the marine transport sector where, among other things, numerous ships are undergoing conversion processes for engine fuel supply, from traditional fossil fuels to LNG. Various plants have already been designed in Italy for LNG distribution for road transport, and this details a lot regarding the future developments of this type of fuel and its multiple uses.
LNG’s journey
LNG is obtained by lowering the temperature to a value equal to -160˚C. The main advantage is that for the same quantity of gas, the volume occupied by LNG is 600 times less than the volume of the same quantity in a gaseous state. LNG undergoes various steps during its journey, these range from transport via methane tanker towards storage facilities or regasification, to then be sent to various uses through a range of distribution types. The latter can be performed through pipelines or transport of the molecule by tankers. It is necessary to constantly comply with the temperature and pressure values to keep LNG in a liquid form. Therefore, specific requirements are necessary that make it possible to operate without problems in this condition. Vanzetti Engineering uses the ARTIKA pump which represents the type of pump specifically studied to work submerged, inserted in the cryostat or storage tanks. The alternative cryogenic pumps, like the VT series, centrifugal and submerged centrifugal are suitable for working in the marine, automotive, and industrial sectors. In terms of the marine sector, the applications refer to fuelling systems for vessel engines and ship refuelling. For the automotive sector, cryogenic pumps are used in LNG and L-CNG refuelling stations as well as in transferring systems from tank trucks to storage tanks. In the industrial field, which includes numerous handling systems, there are satellite stations for fuelling and supporting the pipeline network, as well as the distribution to power plants for the generation of electricity and cogeneration via gas turbines. There is also the area of smaller container filling for industrial and refuelling use: medium and high-pressure nitrogen, argon, and oxygen cylinders that are loaded through lines that use cryogenic pumps.
Cryogenic pumps with a high technical level
To work safely and problem free, both pump types must be designed to have a maximum level of reliability, an absolutely vital condition when making LNG transfers with pressures around several hundreds of m3/h. In terms of the type of submerged pump, the simple construction, quality of materials, and flexibility are the results of thorough research and development. An example of the ARTIKA construction approach is represented by the absence of gaskets and bearing lubrication that exploits the liquid condition of the same LNG. This aspect is very important since any type of fault that occurs on a submerged pump entails more intrusive solutions which are not necessary for an external pump. Thus, having a safe and reliable device makes it possible to significantly reduce any machine downtime and all the consequent problems.
Not just quality but also expertise
The LNG journey from extraction until its use is a complex flow that requires an in-depth understanding. The success in designing or setting up any LNG value chain is the result of joint work of two teams: supplier and customer. The higher the customer’s level of expertise the easier it will be to design an LNG system with excellent characteristics. As discussed earlier, reliability and long duration of the devices are absolutely necessary factors for providing a continuous energy flow. In this case, training that a manufacturer can offer its customers represents a plus that can really make a difference. As for the customer, having an in-depth knowledge of the product means being able to use all its characteristics in favour of the bottom line. The objective of training is also to offer the user all of the information necessary for optimal use of the devices, thus avoiding any useless faults or damage and managing to extend the useful life of the pump, with considerable savings of money and time due to maintenance. Vanzetti Engineering, along with supplying pumps for LNG, proposes training courses (including customised courses) for all customers to expand their expertise and learn the details of all cryogenic device aspects, allowing the final user to be able to act personally if faults occur or for routine maintenance.