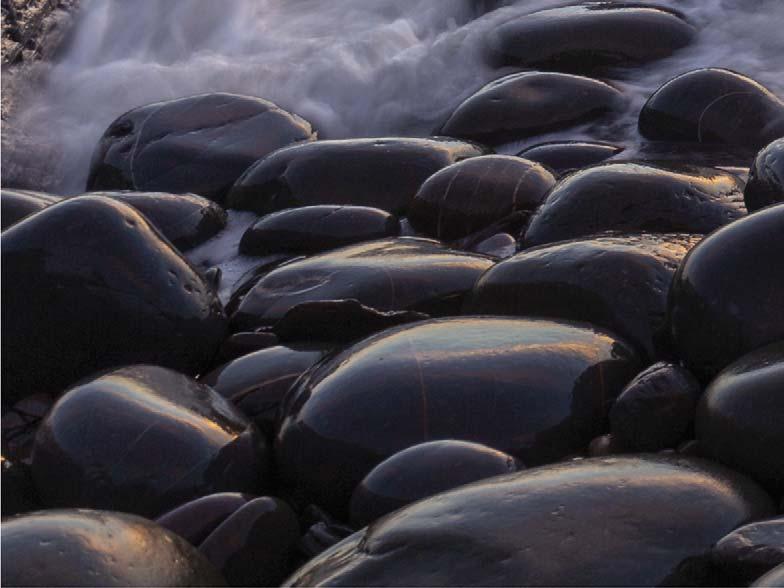
8 minute read
Revitalising mature, shut-in North Sea wells

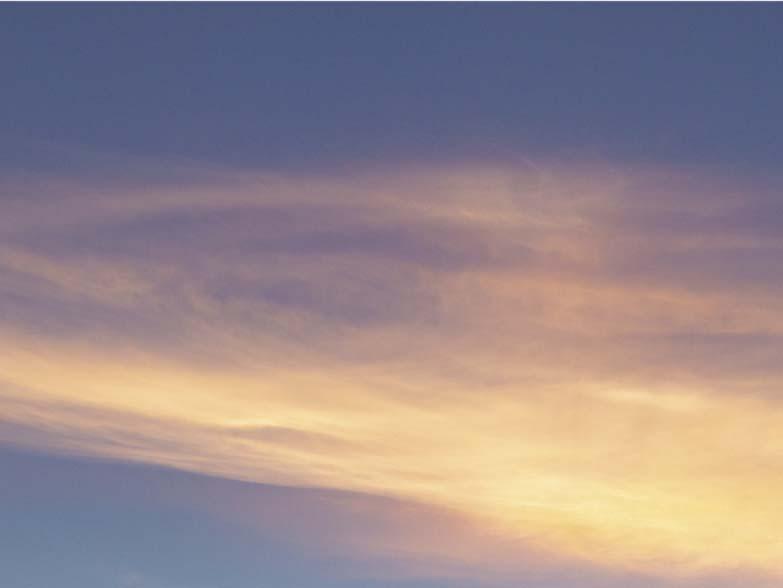
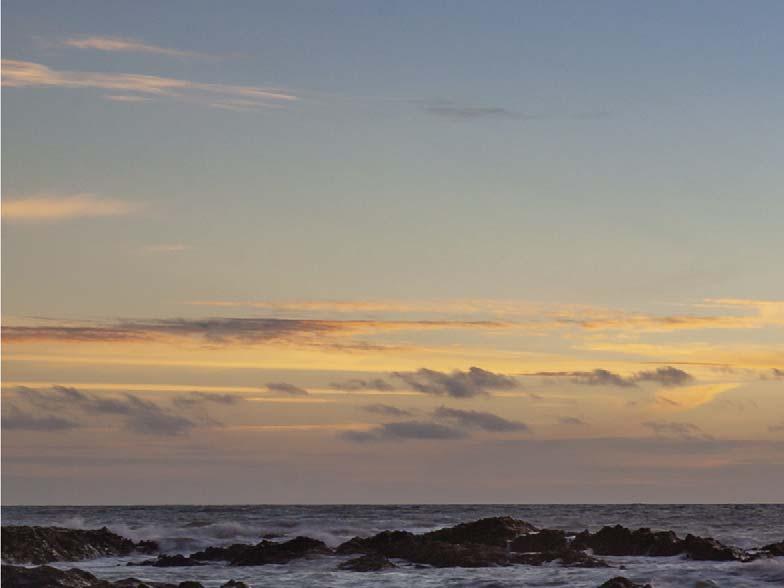

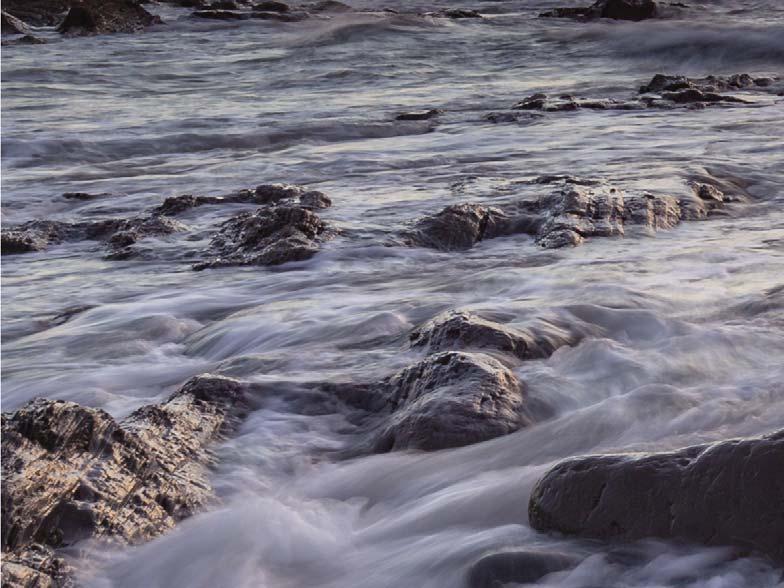

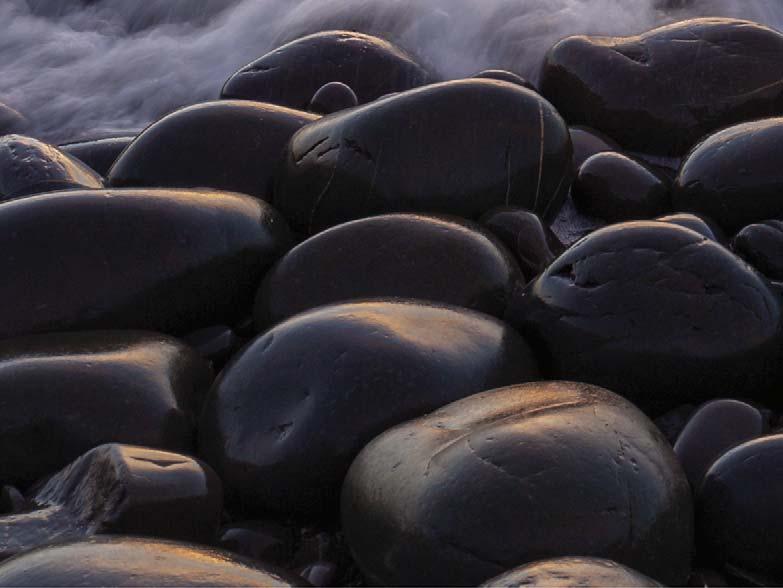
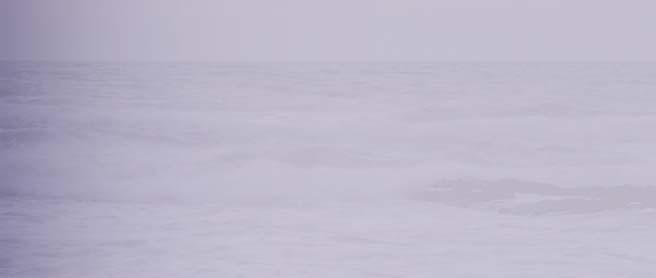

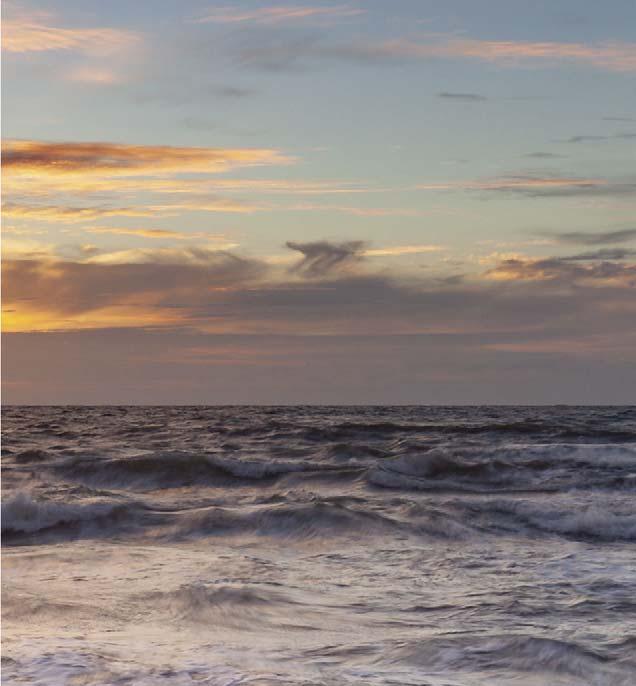


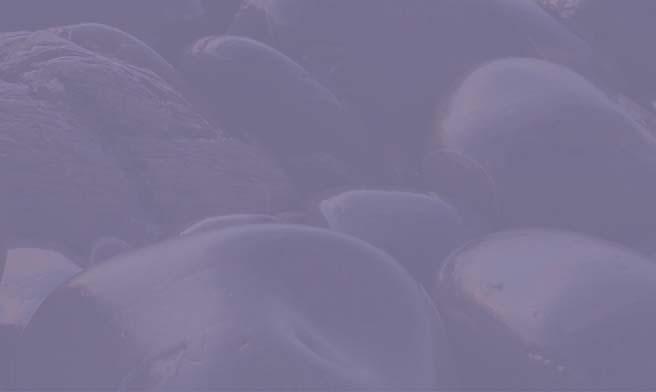



Bjornar Sneeggen and Sondre Klakegg, Weatherford, Norway, outline a novel solution designed to re-establish well integrity, resume production and reduce non-productive time.
REVITALISING REVITALISING MATURE, MATURE, SHUT-IN SHUT-IN NORTH SEA NORTH SEA WELLS WELLS
major North Sea operator recently approached Weatherford with a challenge: devise a solution to revitalise non-producing wells that have been taken off -line due to casing integrity issues, a not-uncommon fate befalling many North Sea wells.
In search of the best alternative for bringing these wells back to life and, at the same time, providing means to enhance productivity and regain full wellbore functionalities, Weatherford worked with the operator to develop and advance the alternative gas lift system (AGLS) completion concept. AGLS enables operators to restore the primary and secondary well barriers while regaining gas lift capabilities. Together, Weatherford and the operator identified viable technologies and solutions to re-establish well integrity and resume production in compliance with the well barrier envelope policies and philosophies. Also critical was the challenge of successfully expanding reservoir possibilities. The project was coordinated from concept through to execution, eff ectively deploying two wells while recording no incidents and zero non-productive time.
Across the North Sea, many mature fields face challenges in which the casing can no longer be utilised as a secondary barrier for gas lift injection. As these wells enter the late stage of their lifecycle, there is simply not enough pressure to continue production, even though plentiful reserves remain in place. In addition, gas lift is widely used across the North Sea portfolio of liquid-producing wells. Oft en, this is done by utilising the A-annulus to transport natural gas down to the required depth in the well. The gas is injected deep into the production tubing through side pocket mandrels, eff ectively using artificial lift to extract liquids from the reservoir. Under normal circumstances, i.e. no well integrity concerns, the production casing is the primary barrier against gas injection system leaks into the surrounding and secondary barriers towards the reservoir.

Figure 1. The Weatherford alternative gas lift system (AGLS) enables operators to restore primary and secondary well barriers while regaining gas lift capabilities.
Figure 2. The customised solution incorporated the API 14A V1-validated Optimax safety valve to enhance life-of-well safe operations in the unlikely event of uncontrolled pressure into the wellbore.

To re-establish the well barrier philosophy for gas lift production and to equip the wellbore so that flow assurance and wellbore access concerns are addressed, an enhanced AGLS concept was further reassessed and engineered, culminating in a robust and cost-eff ective solution to this challenge. First, it was necessary to re-establish the barriers for injection of lift gas, which was accomplished by moving the secondary barrier against gas lift inwards, creating an extra annulus between the existing 9 5/8 in. casing and a new 7 5/8 in. casing.
The existing 13 3/8 in. casing could not be used as a barrier for gas lift as its integrity would have been compromised. By retrieving the existing upper completion and installing a new 7 5/8 in. casing with gas tight rated production packer inside the existing 9 5/8 in. casing, full casing integrity could be restored. The next step was to find a solution for installing new upper completion inside 7 5/8 in. casing, while maintaining the capability of injecting lift gas at required rates as well as satisfying all other requirements for the completion design. This was a key challenge presented to Weatherford engineering as standard completion technologies were not currently available in the market, and the quick turnaround was crucial to the ultimate success of the project. In response to the challenge, the company implemented a combination of existing and new technologies, drawing on previous success within gas lift completions across the globe.
Meeting safety standards in the North Sea
Earlier in 2020, the company successfully concluded the expansion of the large bore annular safety system portfolio with a subsequent installation of the 10 ¾ in. annular safety valve (ASV) system in the North Sea and had anticipated the 7 5/8 in. slim design system booked for an enhanced recovery project in the region. The challenge of this project further accelerated the timeline while complying with one of the industry’s most stringent technical standards on a tailor-made design.
The project took on increased complexity from a portfolio suitability and value-added solution. The ASV system itself, considered the backbone of the design, incorporated the API14A V1-validated Optimax™ safety valve.
In addition to the launch of 7 5/8 in. ASV, the AGLS demanded a series of high-end components in order to make it robust enough to withstand the challenges anticipated over the life of the well. To that end, systematic technical due diligence was conducted with key subject matter experts. From the combined load analysis that was carried out, the Weatherford OptiPkrTM production packer was recommended as the means to deliver the robust performance of a permanent packer with the flexibility of a retrievable packer all in one tool. In addition, with the nodal analysis having been completed, an Optimax tubing retrievable safety valve was incorporated to ensure the well would be safely maintained in the unlikely event of uncontrolled pressures into the wellbore.
Optimising chemical injection
Another critical challenge posed by the anticipated well lifecycle was the need for precise wellbore chemical management with the aim to optimise flow assurance and production performance while reducing the potential for expensive intervention. Weatherford assessed the reservoir and wellbore conditions and deployed its RCI-2QS chemical injection system, enabling pressure fluctuations to be absorbed and controlled while still delivering gas tight metal-to-metal (MTM) sealing, even aft er high circulation rates. The chemical injection system deployed to meet this challenge was


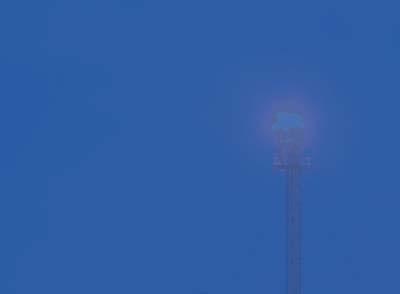

Global coverage of the downstream oil and gas sector


Figure 3. The final step in enhancing production is determining reservoir behaviour and recovery potential. This solution incorporated quartz reservoir monitoring sensors that provide real-time pressure and temperature data.
proven eff ective in rigorous qualification testing that addressed multiple well scenarios.
For the gas lift system itself, decisions regarding the optimum number and setting depths of valves in gas lift ed wells are traditionally made considering only a small number of operating scenarios. As a result, wells oft en do not perform as expected. Weatherford’s turnkey gas lift solutions include gas lift design, monitoring and analysis to maximise the performance and profitability of operators’ wells. With this in mind, a project was initiated to enhance the completion design and enable future accessibility for remedial services that could deliver optimal production performance over the life of the well.
Determining reservoir behaviour
Finally, the company sought to ensure that each originally planned outcome assessed during the initial phase was being achieved. Knowing reservoir behaviour determines recovery potential, production eff iciency and the cost of asset ownership, the company deployed a reservoir monitoring solution to deliver continuous and actionable intelligence on the well, eff ectively delivering real-time data to diagnose production problems and enhance recovery. ForeSite Sense™ quartz technology was also incorporated into the solution.
With the service delivery plan reviewed and agreed upon by the stakeholders and key technologies integrated into a coherent interfaced system, the technologies were deployed using a multidisciplinary crew that reduced personnel onboard by 45%. This streamlined communications and operational eff iciency leverages workflows established in the Weatherford CompleteTM post-TD solution, which integrates all post-drilling services, including liner hangers, wellbore clean-up, tubular running, completions, fishing, slickline and well services.
During 2Q20, the first two AGLS completions were successfully installed, returning the mature wells to life with production numbers meeting and exceeding operator expectations. In comparison to a conventional 13 3/8 in. sidetrack, the approach provided total savings in excess of 40% while expanding its application to slot recovery wells, given its plugging and abandonment (P&A) friendly design and the associated operational savings.
MICRO AND NANO CONNECTORS FOR EXTREME ENVIRONMENTS
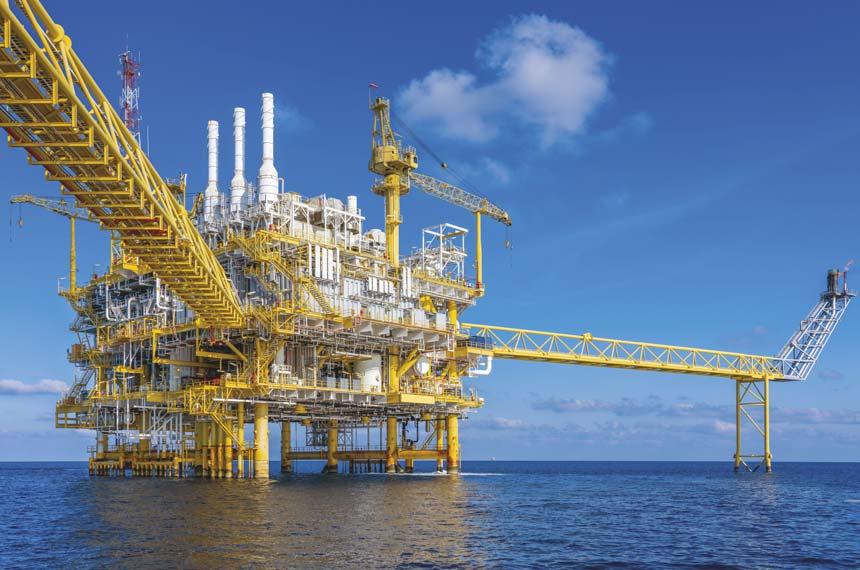

THE PETROLEUM-INDUSTRY MICRO AND NANO SIZED CONNECTORS ARE SPECIFICALLY DEVELOPED FOR THEIR SMALL SIZE AND RUGGEDNESS, TO PROVIDE HIGH TEMPERATURE, HIGH DENSITY AND HIGH SHOCK RESISTANCE COMMONLY NEEDED IN DOWN-HOLE, RESEARCH AND RESERVE EXPANSION.
Conclusion
As the industry continues to lock down capital spending, stakeholders must make the most of their current resources to remain viable. Rather than placing profitability on hold, the chief challenge, of course, is doing more with less capital and fewer people. Using proven, integrated technology systems – such as an end-to-end alternative gas lift solution – to economically revive non-producing wells is critical to keeping oilfield ventures in the black.