
7 minute read
Doing more with data
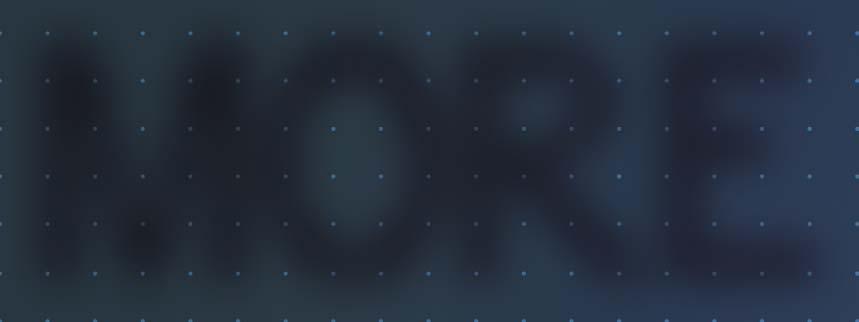
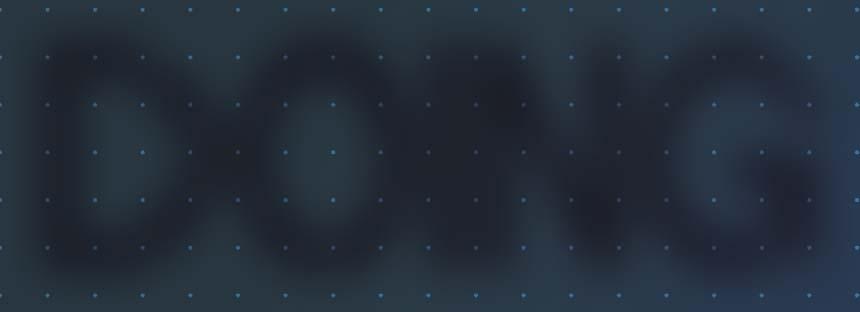
xploration and production (E&P) operators oft en say that it is not a lack of data related to well performance that is the problem, but rather the lack of suff icient, actionable insights. In order to continue to drive margin improvement at the wellhead, finding ways to interpret data meaningfully and implement impactful changes based on those interpretations is key. Operations teams are running lean and struggle to find the time during their already busy days of data analysis and fighting fires to focus on production optimisation. So, the question for operators remains: how can they get more with their existing workforce?
This is where digital oilfield technologies utilising artificial intelligence (AI) can make a diff erence. Leveraging over 250 million hours of labelled operations data, Ambyint delivers improvements to E&P outcomes and margins by combining physics and subject matter expertise with AI to automate and optimise production operations and engineering workflows across all well types. These solutions help operations teams scale their processes across large well populations by automating repetitive, manual tasks. AI can increase an operator’s workforce eff iciency by at least 25% through actionable real-time information, early detection of well anomalies and autonomous setpoint changes, resulting in more wells being managed and optimised daily.
Ultimately, E&P companies see production levels increase as high as 7% and operating costs drop as much as 30%, improving bottom line performance and answering the question of how to get more with their existing workforces. Additionally, when production optimisation solutions are implemented and operations become more eff icient, other benefits come online, such as reductions in failure rates on rod lift wells and reduced greenhouse gas emissions on plunger lift wells. Ambyint has demonstrated these outcomes across major North American basins, providing proof points to other E&P companies wanting to achieve similar results. This article takes a closer look at these proof points.

Increased production
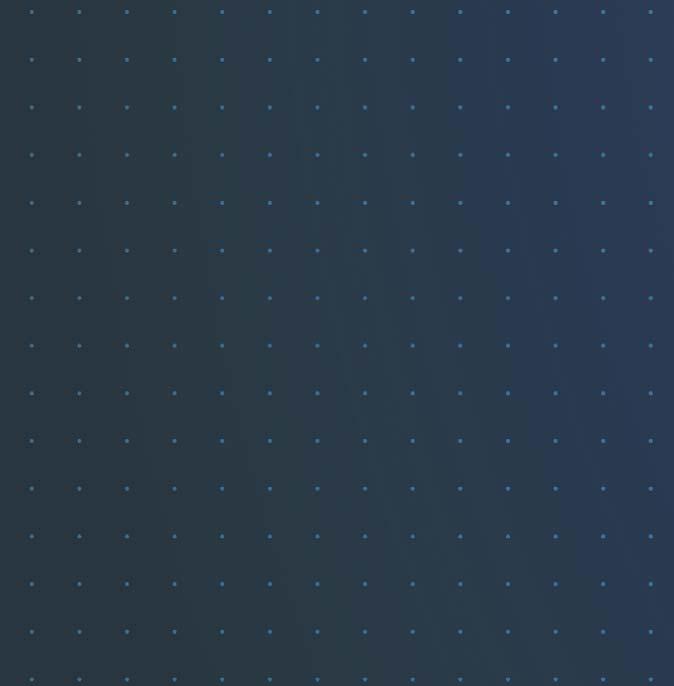
An E&P operator in the Marcellus Shale, US, utilising legacy production optimisation tools to manage a field of horizontal, plunger lift gas wells had plateaued in driving further operational improvements. Many of the wells experienced production-impacting anomalies, well instability and unoptimised controller setpoints. The operator searched for technological solutions to optimise these wells further and increase production volumes.
Ambyint deployed its plunger lift optimisation solution, InfinityPLTM, across the operator’s approximately 300-well asset, enabling enhanced analytics, physics-based insights and improved management of plunger open/close triggers and setpoints. By implementing the recommendations made by the soft ware, the operator realised a 7% increase in production volumes as well as improved operational scalability (Figure 1).
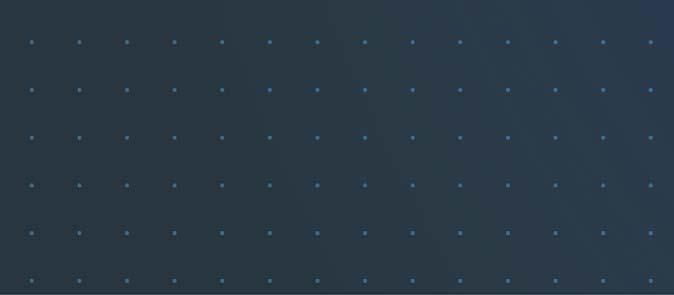
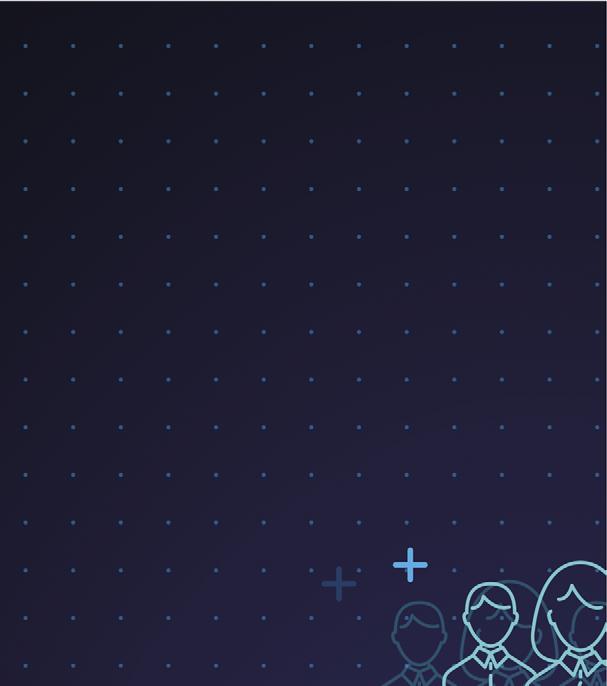

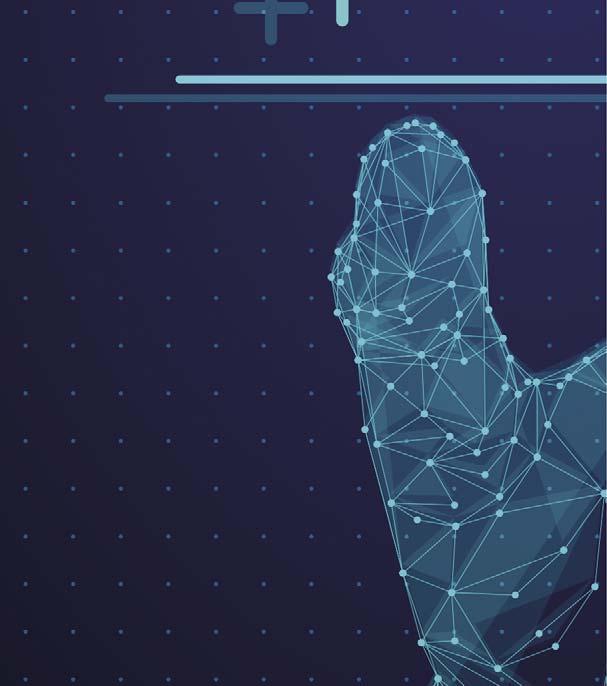
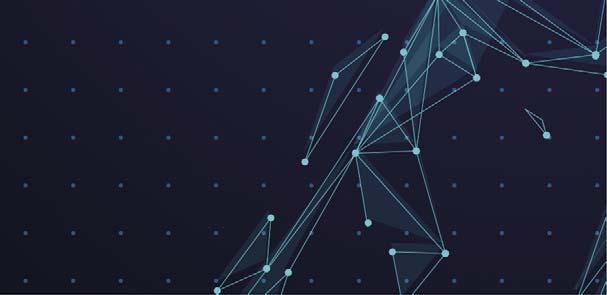
Ginger Shelfer, Ambyint, USA, outlines how advanced production optimisation technologies can deliver improved production volumes, lower operating costs and reduced greenhouse gas emissions.




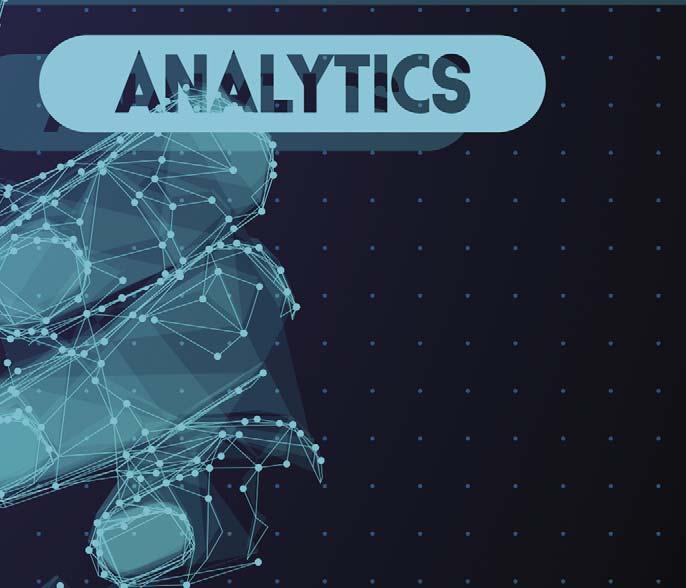
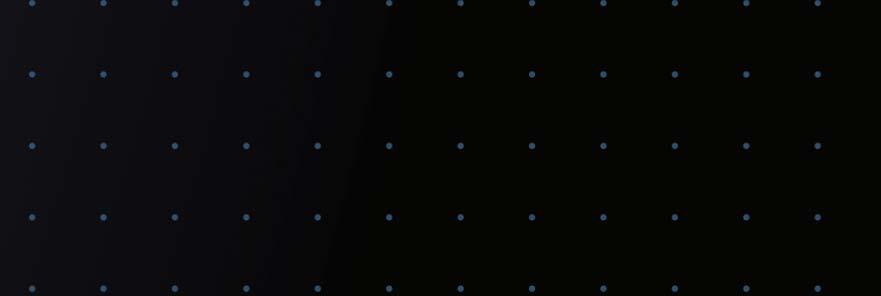

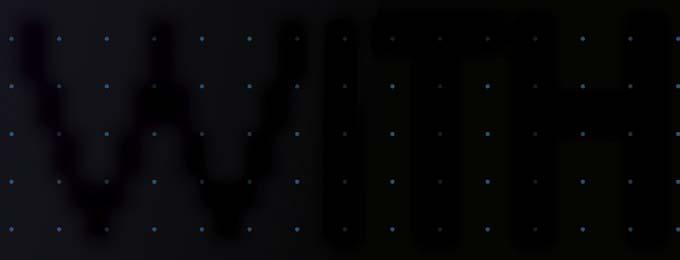
In another case study, an E&P operator in the Marcellus had over 30% of flowing and plunger lift wells producing below plan. With a field of more than 200 horizontal wells, the company saw lower production primarily due to wellsite anomalies. The company looked for capabilities to improve the scalability of their engineering and operations team, including alerts for when wells go off -plan, predictive maintenance and more centralised operational event tracking.
Ambyint deployed its production assurance solution, SmartStreamTM , across the company’s wells, generating a decline curve based on historical production data, monitoring for off -plan conditions and utilising AI to detect anomalies impacting well performance. Engineers gained greater operational scalability with an early warning system for anomalies and better visibility into the production impacts of well interventions. The solution detected anomalies with an accuracy greater than 90%, resulting in quicker well interventions and higher production outcomes.
Reduced operating expenses
Two-thirds of an E&P operator’s rod lift wells in the Eagle Ford, US, were overpumping, causing higher failure rates and excessive power consumption. Limitations on engineers’ time meant daily optimisation opportunities went unrecognised, leading the company to search for a technology solution to bridge the gap.
Ambyint deployed InfinityRL across the company’s asset, establishing connectivity at remote well locations, providing high-resolution dynamometer cards, delivering AI-based setpoint recommendations and automating controller updates.
Engineers gained time back in their day by avoiding time-consuming data gathering and analysis. With automated well optimisation and greater span of control, engineers shift ed their focus to other high value activities. Optimised production translated into a 6% increase in production volumes for underpumping wells, a 17% reduction in strokes per minute (SPM) and an 11% decrease in power consumption.
In the Bakken, an E&P operator found that a significant percentage of their rod lift wells were underpumping, leaving revenue in the ground, while a majority of wells were overpumping, causing high failure rates and consequently deferred revenue. To gain optimisation scale across its wells, the company recognised the need for improved real-time operational visibility with anomaly detection, recommended optimisation opportunities and automated setpoint management.
Aft er deployment of rod lift production optimisation, engineers gained immediate access to well performance data spotlighting intervention needs and optimisation opportunities. Aft er gaining confidence in the AI-driven setpoint recommendations over an initial period, the customer allowed the soft ware to update setpoints automatically, ensuring an ongoing, full-field optimisation state. In addition to enhanced operational eff iciencies, the operator realised a 6% increase in production volumes, 14% improvement in pump eff iciency, an 11% reduction in rod strokes and 20% improvement in mean time between failures (MTBF) (Figure 2).

Figure 1. Ambyint InfinityPL increased gas production volumes with improved management of plunger open/close triggers and setpoints.

Reduced greenhouse gas emissions
An operator in Texas, US, had a field of 200 rod lift wells that were operating sub-optimally. Ambyint technology classified 65% of the wells as overpumping. This led to high electricity consumption, increased failure rates and inflated operating costs. The high electricity consumption also meant excess greenhouse gas emissions, which if lowered would align with the company’s corporate sustainability goals.
Deploying a rod lift production optimisation solution into the field enabled the operator to make data-driven decisions with real-time performance data, receive AI-based setpoint recommendations and automate controller setpoint changes.
Over a one-year deployment, approximately 1400 automated setpoint changes were implemented, allowing for closed-loop optimisation of existing control systems. With improved optimisation, the operator realised an 11% reduction in power consumption, a resulting 13% reduction in greenhouse gas emissions and improved engineers’ eff iciencies, leaving more time to focus on additional, high value activities (Figure 3).
Delivering value in challenging times
Figure 2. Optimised production translated into less energy expended, lower costs and increased revenue, with the operations team exerting greater management control over more wells on a daily basis.
As history has shown, the oil and gas industry is highly volatile. This volatility challenges companies to explore advanced technologies to enhance their oilfield operations with the focus on getting the most out of producing wells for less. Operators that have embraced digital oilfield technologies utilising AI gain the additional opportunity to yield reduced greenhouse gas emissions that have broader environmental and even public relations benefits. AI-powered production and artificial lift optimisation solutions deliver sophisticated technology, automation and data science that help drive improved production volumes, generate increased cash flow, achieve greater returns, reduce greenhouse gas Figure 3. Ambyint’s technologies lower greenhouse gas emissions with production optimisation and emissions and boost workforce eff iciency and setpoint management. productivity.
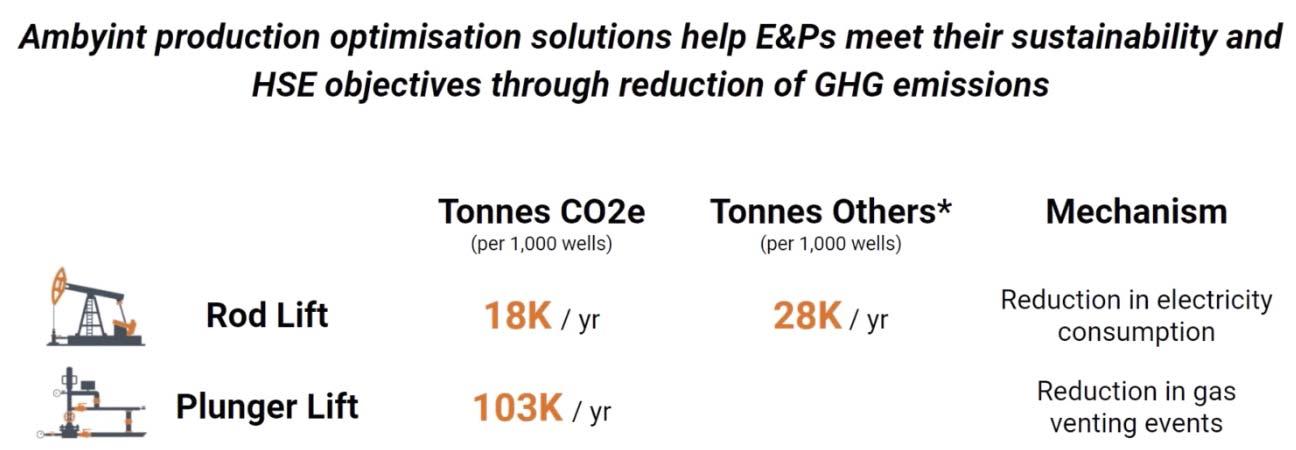