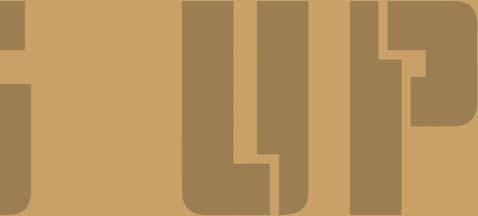
10 minute read
Amping up fracking activity
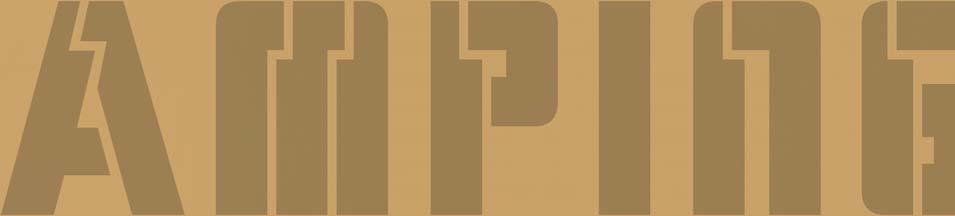
AMPING UP FRACKING FRACKING Travis Bolt, NOV,USA, explains how electric fracturing will help operators usher in the next generation of performance while delivering responsible, cost-effective frac operations. ACTIVITY ACTIVITY
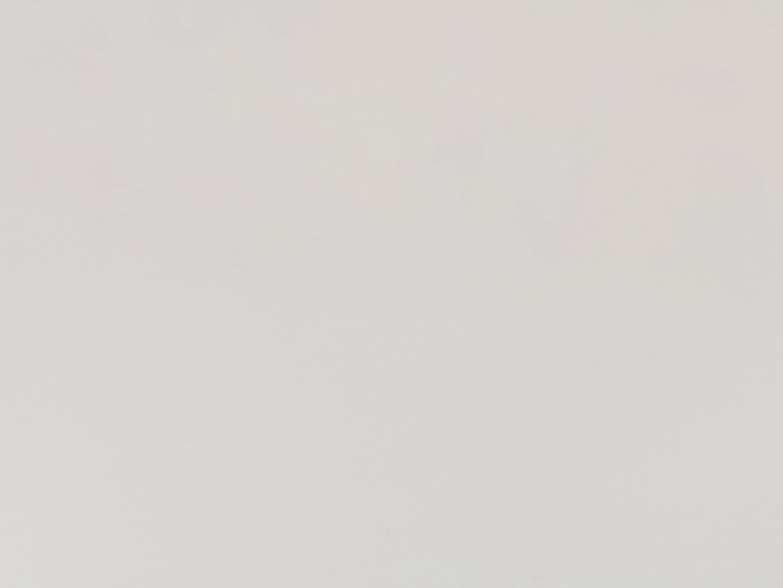
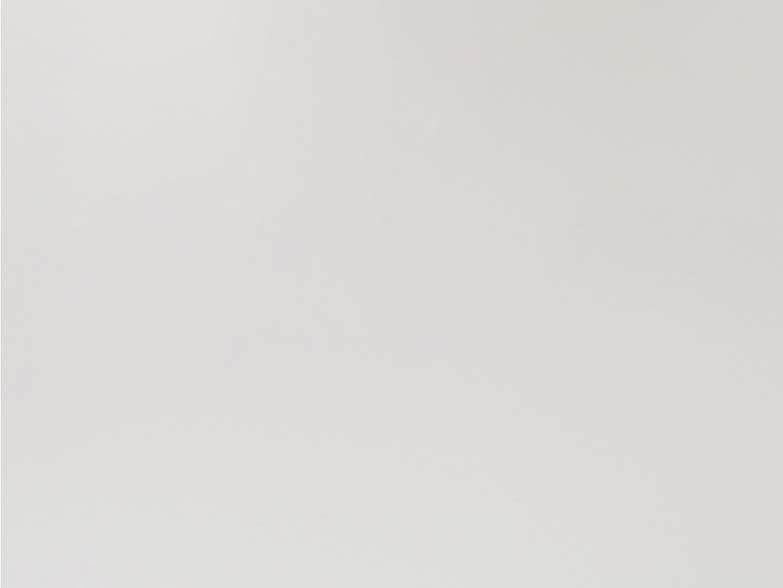
The oil and gas industry has undergone a significant transition over the past few years, as institutional investors which once viewed financial growth as the key to oil and gas investing are now focused on financial return and the way it is achieved. In order to attract today’s investors, operators have prioritised developing best practices that deliver on eff iciency and lowering operational cost to increase profitability. In addition, these same investors are analysing oil and gas companies by their ability to implement environmental, social and corporate governance (ESG) business practices into their daily routine. This combination of market and social drivers has resulted in the evaluation of all operational aspects of energy extraction, and fracturing has not been exempt from that assessment, as it plays a significant part in the total cost of a well’s completion. As a result, service companies are seeing more pressure being exerted to evaluate new frac technologies.
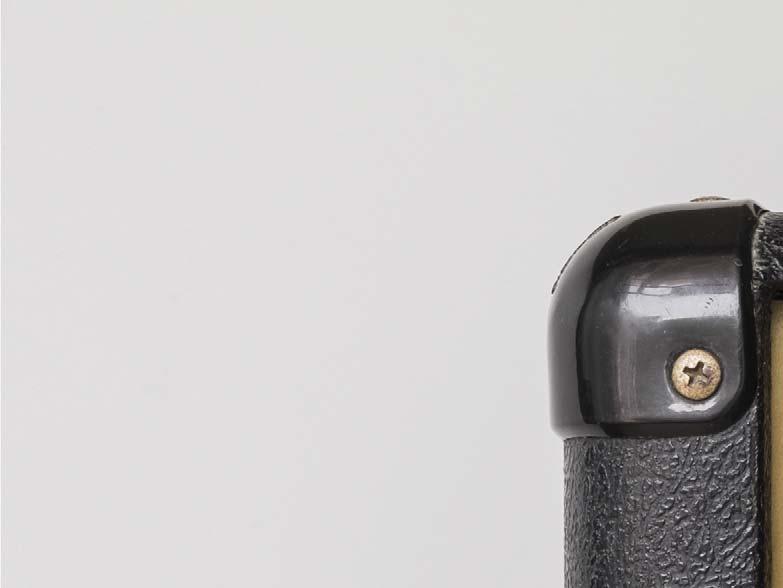



One such technology is electric fracturing (eFrac). eFrac systems remove the traditional diesel engine and transmission drivetrain that powers a frac pump and replaces them with an electric motor, similar to the transition that took place with drilling rigs years ago. As with any new technology, there are challenges that sometimes come with it. eFrac system operators are now identifying a preferred method of converting a fuel into an electric energy to drive their fleet, since electric motors do not consume fuel directly. While the eFrac systems may not be the best fit for all situations, under the right conditions they deliver both cost savings and ESG performance.
With a nod towards the future of frac operations, NOV has launched its new Ideal™ eFrac fleet, designed to reduce greenhouse gases and lower the total cost of ownership for operators. The fleet provides an environmentally and socially responsible frac option that minimises sound and carbon emissions, off ers a clean and simple rig up and significantly increases power density while maintaining the redundancy that eff icient frac operations require.
As an original equipment manufacturer (OEM), NOV focused on the equipment as an empowering technology that delivers on improvements for operations, health, safety and environment (HSE) and control. As part of the development process, the company applied expertise from its electric AC Ideal rig technology, as well as industry best practices to address issues such as electromagnetic interference and air conditioning, among others. This approach allowed the team to simplify the electrification process, reduce HSE risks through engineered solutions and deliver the full value of electrification.
Using intelligent electrical architecture and simplified drivetrains, developers built the Ideal eFrac technology on the foundation of several key components:
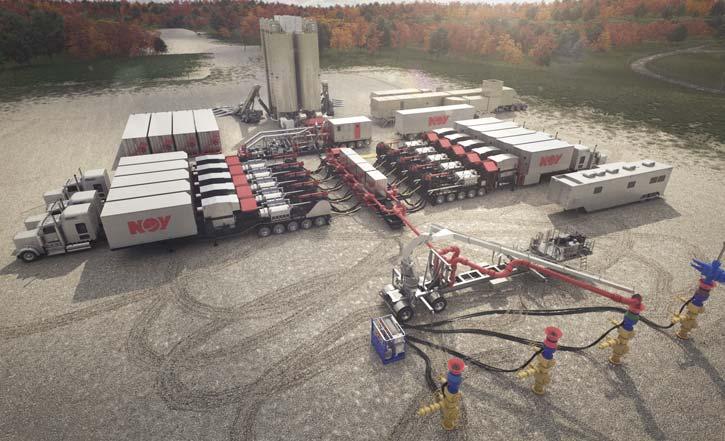
Figure 1. Ideal eFrac fleet is a fully electric fracturing system that off ers a new level of control, reduces total cost of ownership and lowers greenhouse emissions without sacrificing safety or performance.
Figure 2. The Ideal fleet features SPM® QEM 5000, which is a 5000 hp pump that provides higher power density and contributes to the frac fleet’s smaller footprint. Pumps

From electricity through high-pressure frac fluid, the Ideal pressure pumping unit is a fully integrated pump platform that withstands the rigours of frac operations. The system’s 5000 hp pumps deliver a higher power density that can reduce the frac fleet footprint by as much as 47% versus conventional frac equipment. Additionally, the simplified electrical architecture allows the system to be serviced much like traditional frac equipment, providing easier connect and disconnect features for service and maintenance without disrupting adjacent equipment.
Manifold
The manifold system was designed to optimise the electric pressure pumping operation and reduce the complexity of rigging up and operating an eFrac system. The Ideal manifold provides 10 positions for 5000 hp eFrac trailers and two positions for conventional diesel frac trailers, off ering operational flexibility and reducing potential non-productive time (NPT). The manifold uses intelligent connections such as interlocks, digital feedback and monitoring systems to ensure that electrical and mechanical rig-up is safe and eff icient. The system requires the fewest electrical connections of any eFrac fleet in the industry while still supporting up to 50 000 hp for the toughest frac jobs.
Process plant
A benefit of eFrac systems is that they are not strictly limited to high-horsepower pumps. Designed as a new perspective on the processing of frac fluids, the Ideal processing plant brings the value of electrification to frac operations through greater reliability, feedback and control. The process plant is a fully redundant system, both mechanically and electrically. The system replaces two conventional blenders on a single platform, feeding the most challenging frac jobs up to 150 bbl/min. As a fully integrated processing system, the fleet complies with the most stringent of silica regulations and is capable of conventional, slip-steam and simultaneous-frac operations.
Substation
The substation acts as the primary connection point between the electrical fleet and the power source. The company recognised that operators and service companies vary in their approach to power, ranging from electric power transmission (grid power), infield power, large turbines or multiple reciprocating generators. Focused on providing value in whichever power format the customer chooses, the system was designed to be power-source agnostic and IEEE519-compliant, allowing the fleet to be flexible in an emerging market with varying business models.
Building an advanced system
When considering disruptive technologies, the solution’s technical implications need to be evaluated and weighed against competing technologies. When examining conventional frac operations, companies are oft en confronted with the challenges of the high rate and high pressure of sand-ladened fluids, which drive a majority of the operational costs. These costs primarily fall within two areas – drivetrain and pump.
From a drivetrain perspective, the Ideal eFrac system removes the need for reciprocating engines and transmissions by replacing them with a direct-drive electric motor. With minimal parts and
PRESENTED BY
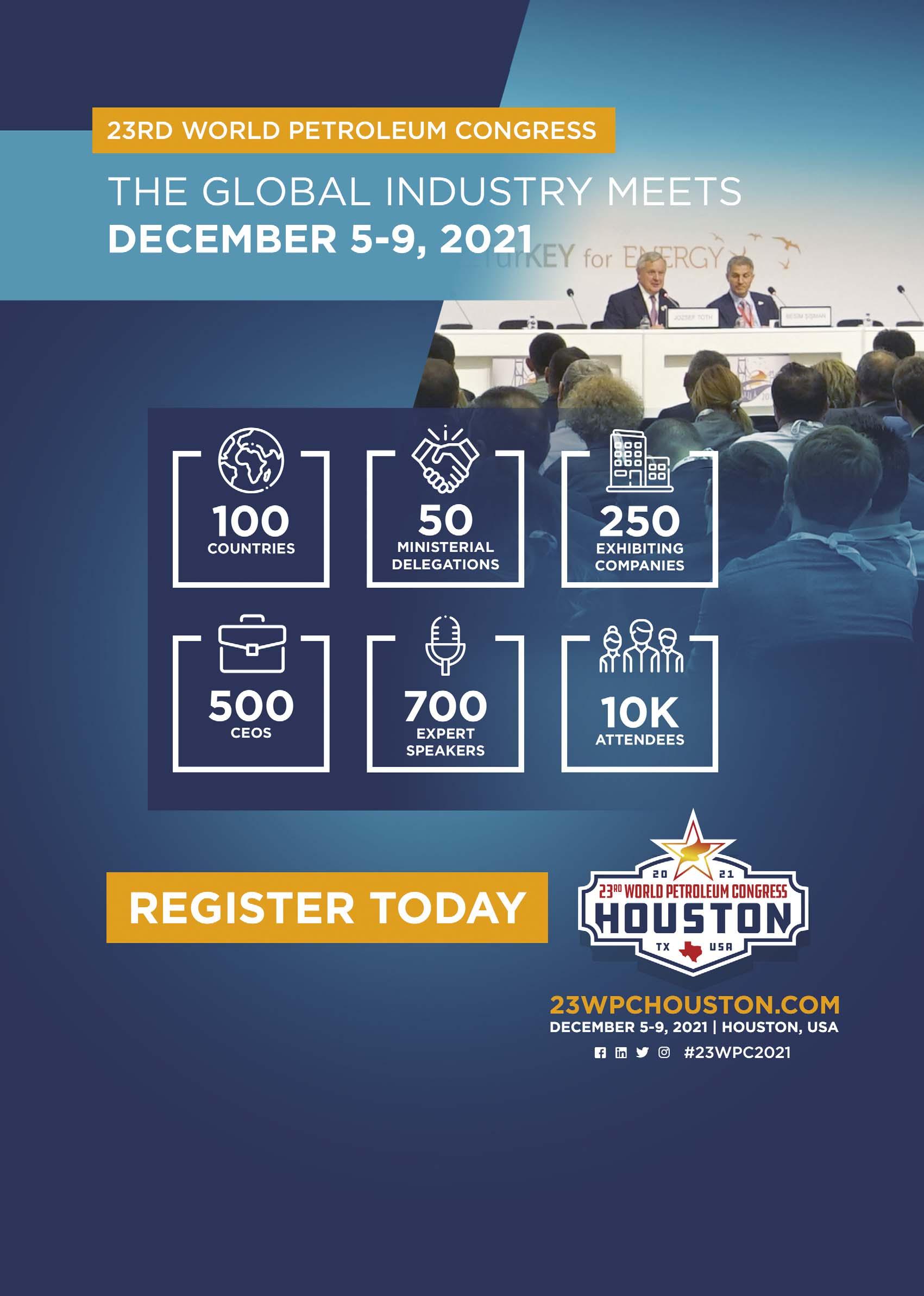
maintenance, the electric motor allows operators to move away from a 500 to 1500 hr maintenance cycle to a 20 000 hr cycle that significantly reduces maintenance costs and NPT.
Additionally, a conventional fleet’s drivetrain, coupled with the mobility requirement of frac equipment, has historically limited the systems to 2500 to 3000 hp per trailer. Leveraging the high power density of electric motors, NOV developed the Ideal system with a 5000 hp road-legal frac trailer that reduces the number of bores on location by 50% and reduces high-pressure joints by as much as 89% when used with flexible connections.
When looking at the unit’s overall weight-to-power ratio, the system supports a pump technology that meets the performance of the single electric motor’s higher power density. The system’s design depends on the motor and pump working together, and as a result it has evolved into an optimised solution that off ers high levels of performance, mobility and reliability. Since a conventional gear ratio would require a much larger motor, the eFrac pump system’s gear ratio and lower torque translates to a lower overall weight, minimising the impact on the roads and community.
As a net result of harnessing both pump and drivetrain technology, the Ideal eFrac system can positively impact the total cost of ownership. When implementing the fleet technology versus conventional frac fleets, an estimated 38% reduction in total cost of ownership can be achieved aft er six years of operation, and the savings continue to increase aft er 10 years and beyond.
When looking at other facets of costs related to a frac operation, they are not strictly limited to the drivetrain’s parts and maintenance. The system’s consumption of wellhead gas is a good example of measurable performance savings. When compared to conventional operations, the Ideal system’s use of wellhead gas versus diesel can reduce fuel costs from ~US$14.12 per 100 hp/hr to US$1.38 per 100 hp/hr, resulting in fuel savings of up to US$1 million per month for a 50 000 hp fleet at 79% uptime.
The system burns wellhead gas to power the electric equipment, while conventional systems require diesel fuel to be trucked to the frac location to power equipment, during which operators flare gas. When consuming clean-burning wellhead gas, the gas can be piped directly to the location and consumed in its current form with minimal processing or filtering to power the equipment, making eff icient use of gas that may have otherwise been flared. When conventional systems run on diesel, the oil must be produced, piped to a refinery, processed and then transported back to the location, with each step increasing the carbon footprint. In conjunction with diesel processing, transportation and burning, the action of flaring excess natural gas creates additional emissions. Considering these examples, the Ideal system can reduce carbon dioxide (CO2) by up to 71% based on a 24 hour operating period at 70% uptime while running at 10 000 psi and 90 bbl/min. In addition to decreased CO2 emissions, the system reduces the presence of nitrogen oxides (NOX), methane (CH4) and other major pollutants that are contributors to smog and the carbon footprint.
Safety is always a high priority, and the Ideal eFrac system was designed to decrease risks and complexity in all areas. The company focused on minimising the number of fluid and electrical connections as well as eliminating complex cable routing to reduce the risks associated with electrical systems. A multilevel approach to electrical connections, including physical layout, hardware protections, control interlocks and HMI feedback, ensures that electricity is only provided when both hardware and operators are ready to receive power. These protections are essential during the rig-up process and operation. The electrical system uses monitored cable shielding and technology such as last-to make/first-to-break to ensure that it defaults to a safe state if something unplanned occurs during a frac job. The Ideal system’s safety features not only focus on the electrical platform, but personnel risks are also reduced through a fleet design that addresses fall hazards, silica exposure and lift ing strains, to name a few.
As a full-remote-operated fleet, the control system is not limited to pump-rate control. The system can also change flow paths, isolate units and provide all the functionality of boots on the ground from a safe, remote location. The remote operation capabilities are enhanced by intelligent machine monitoring and analytics that provide accurate information on the health of the equipment and allow for live feedback, as well as post-job analysis, providing advanced tools to reduce NPT and increase asset utilisation.
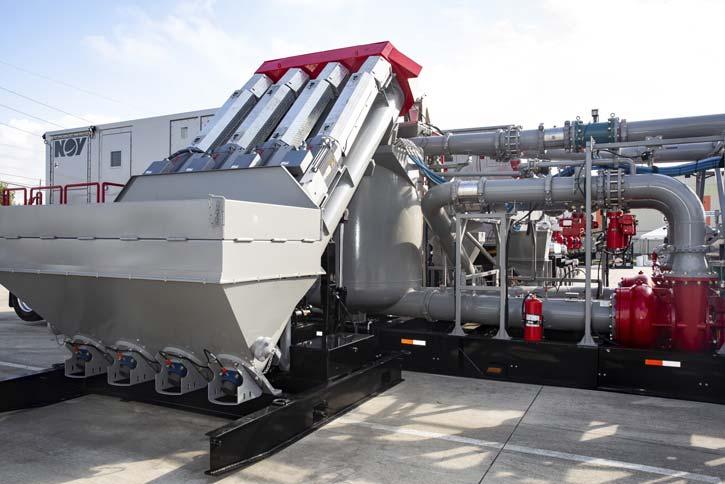
Figure 3. Featuring a modular auger skid and onboard chemical system, the Ideal eFrac processing plant replaces two conventional blenders on a single platform and delivers greater feedback and control.

Figure 4. The Ideal mobile 5000-hp frac trailer delivers the power needed for challenging frac operations while reducing road traff ic and carbon emissions.
Conclusion
Fracturing is a costly and mechanically intensive operation, and the introduction of a technology platform that is both innovative and environmentally conscious is a significant step towards reducing total cost of ownership and simplifying the fracturing process. A comprehensive, streamlined solution gives operators an upper hand in a fast-changing pressure pumping industry. By reducing carbon emissions, decreasing disruption to the community and minimising trucking requirements related to equipment needs, systems such as the Ideal eFrac system will help those same operators usher in the next generation of performance while delivering responsible, cost-eff ective frac operations.