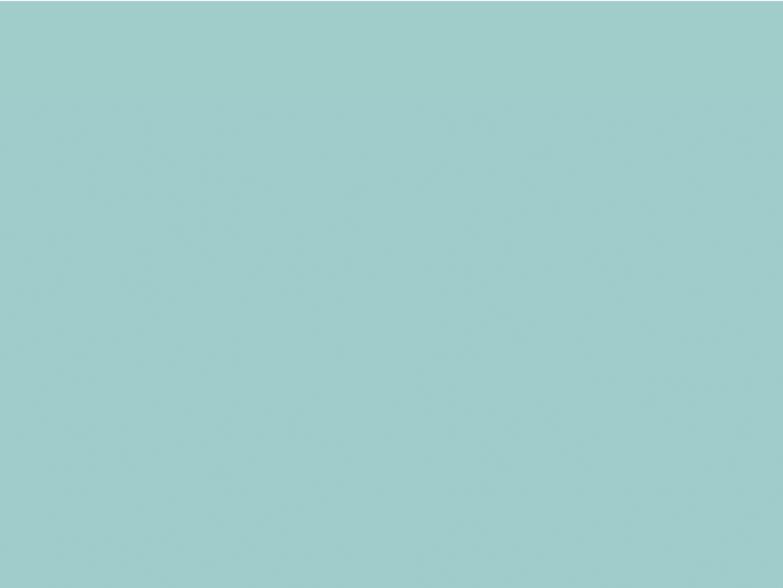
10 minute read
Refi ning the method
REFINING REFINING

THE METHOD
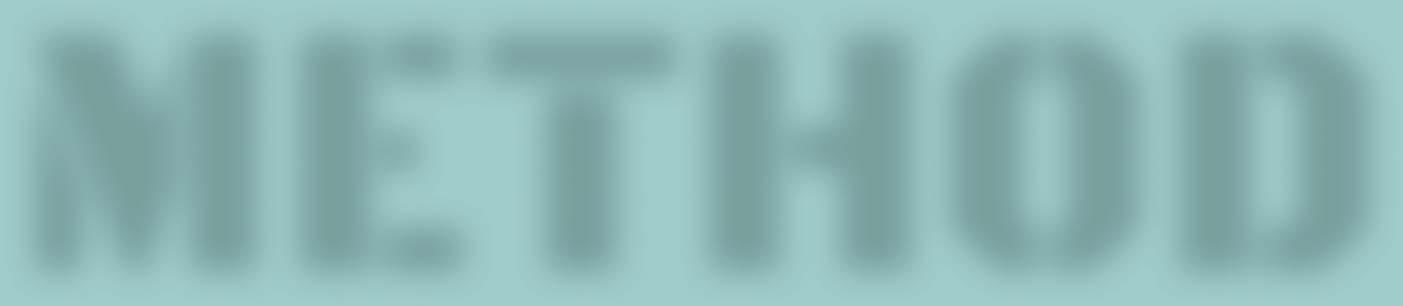


There is always an element of risk when selecting chemistries to facilitate oil, water and gas separation, particularly if the test work is conducted using synthetic emulsions and foams created from dead oils and/or assumed brines, rather than freshly sampled, live, produced fluids. In some cases, such as a new field start-up, this is the only option for product selection testing. It is therefore imperative to ensure the test methodology is correct in order to maximise the likelihood of selecting separation products – such as demulsifiers and antifoams – that will provide effective separation performance for the produced fluids not just in the laboratory but in the live process itself.
This article summarises the demulsifier and antifoam selection test work for a unique heavy oil start-up in the North Sea. The major focus is on the early selection work and field testing (using pre-production drilling samples), then the subsequent changes to approach and methodology used for further product selection work in order to improve upon the original recommended chemistries, with a particular focus on demulsifier and antifoam applications.

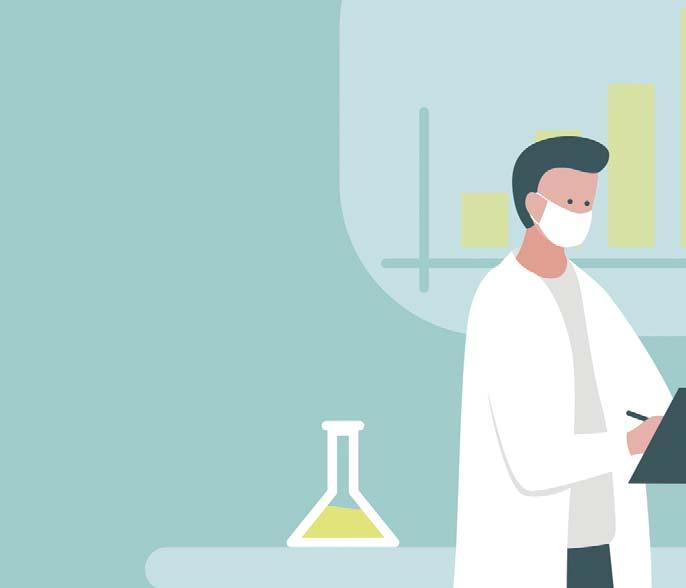

Alan White and Robert Miller,
Clariant, consider the evolution of selection methodology for heavy oil separation treatments.
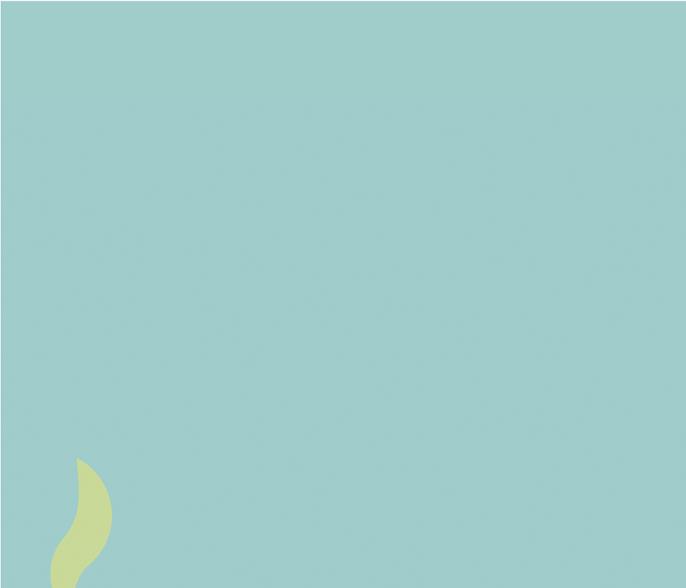
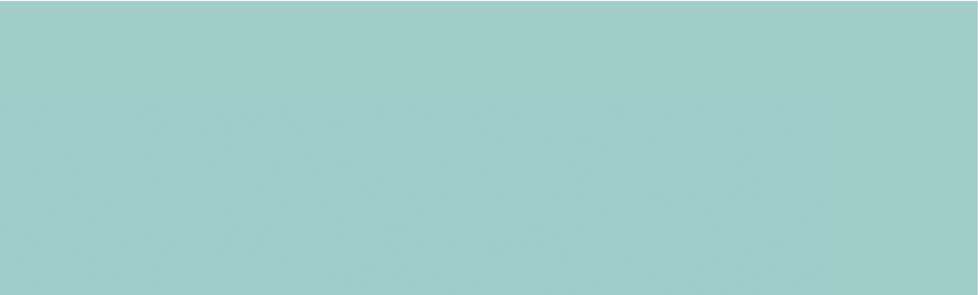
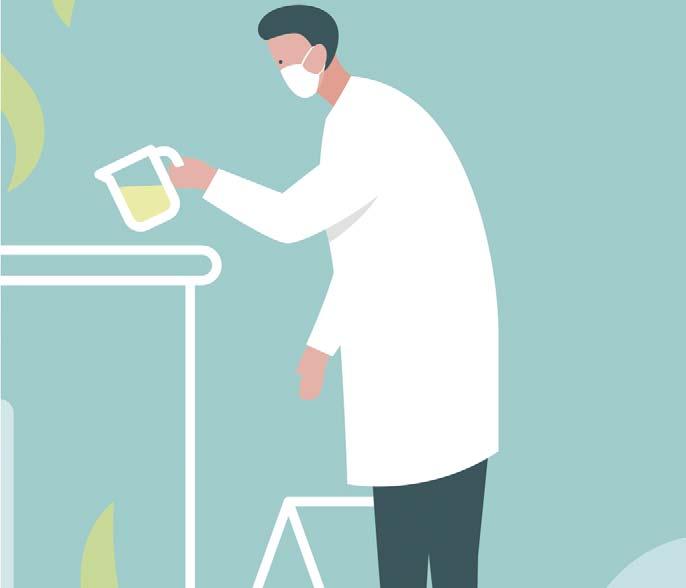


Case study: North Sea
Demulsifiers and antifoam chemicals are essential for separation of the oil, water and gas phases of emulsions and foams formed during the extraction of fluids from an oil reservoir. All oils, and subsequent emulsions, are uniquely different. The components and natural surfactants vary greatly, as do the conditions of extraction and processing, such as temperatures, pressures and production facilities. It is therefore standard practice, certainly in the case of demulsifiers, to conduct formulation and selection work on-site using freshly sampled fluids, in order to get as representative an emulsion as possible and therefore representative separation trends. In some cases this is just not possible, either due to lack of access to the field or, more often, because the field is new and has not started producing yet. In these situations there is often no choice but to conduct tests using a man-made emulsion from dead oil and synthetic field brine. This is far from perfect, as the emulsion is unlikely to be analogous to the true field emulsion and any chemical recommended as a result of this sort of testing is hardly likely to be the best possible demulsifier for the process.
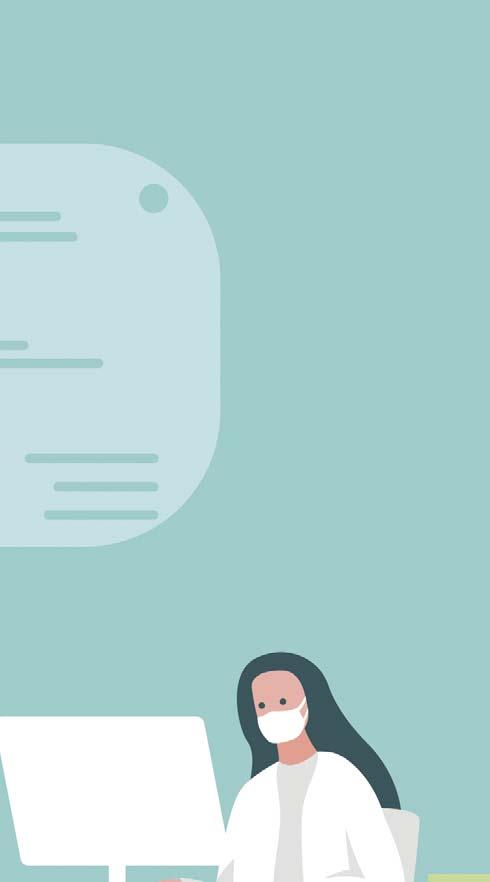

A good illustration of this issue is test work conducted for a new heavy oil development in the North Sea. As previously alluded to, new, yet to be produced developments require chemical recommendations, but it is impossible to test live fluids on-site. In this case, the initial recommendation had to be made without any test work at all as no fluids were available, but the operator needed to run a well test project. An initial set of ‘off-the-shelf’ products for a number of applications was recommended for the project, including demulsifier and antifoam chemicals. The result was a fairly successful well test programme. The demulsifier was found to separate fluids satisfactorily, although the performance of the original antifoam was below that expected while foam was found to be a major challenge.
Samples of chemical-free crude oil were taken during the well test for further laboratory work and product development onshore. Demulsifier tests began with simple bottle testing, where the oil and water were shaken together to create an emulsion which was then treated with various demulsifier chemistries. The results from this were fairly unsatisfactory, with many chemistries giving the same performance and untreated ‘blank’ samples also separating fairly easily. The emulsion created was not particularly stable and therefore unrepresentative.
Table 1. Water droplet size estimated distribution results
Droplet size range (μm) Estimated distribution (%)
< 2 3
2 – 4 15
4 – 6 35
6 – 8 25
8 – 10 15
10 – 20 5
> 20 2
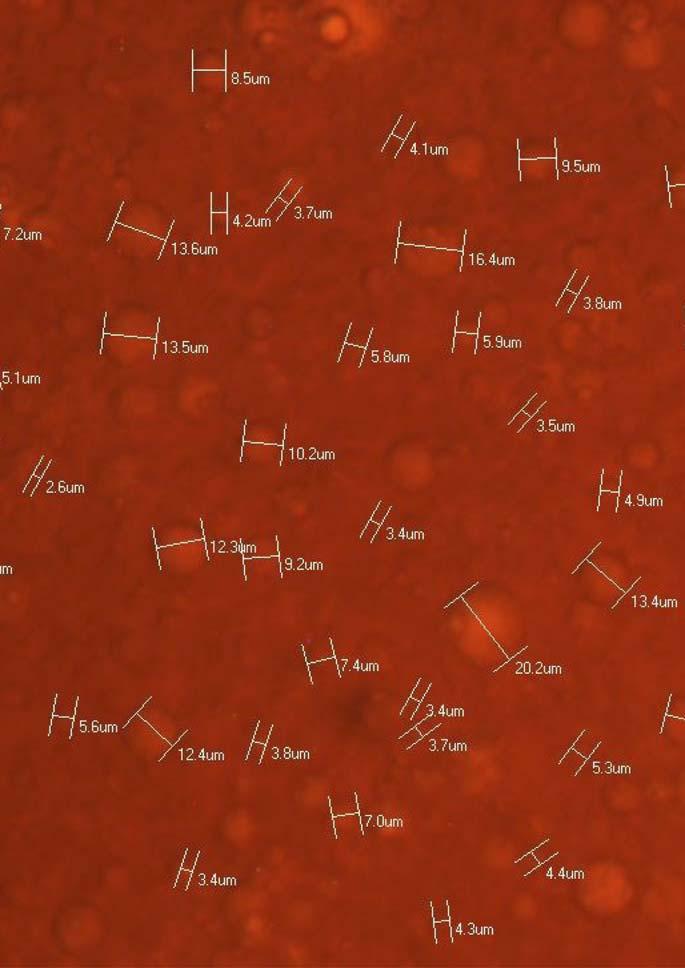
Figure 1. Droplet size distribution (x 200 magnification). Experimental
In order to try to better simulate the true-life situation, the condition of the produced fluids during the well test was reviewed again. The dead oil being used for the onshore emulsion was different to the live oil, as all the co-produced gases had been lost as well as some of the lighter hydrocarbon components. The testing facilities available for the bottle testing did not allow for any artificial re-conditioning of the oil to try to more truly mimic the field composition; this was therefore not a viable route for improving the demulsifier test. Instead, focus shifted to the size and distribution of the water droplets within the oil phase. These parameters had been measured during the well test phase and therefore a reasonable composition of the emulsion in terms of water distribution was available.
Using a submersible high shear mixer it was possible, after some trial and error, to create an emulsion with a similar water droplet size distribution as had been observed during the well test. This distribution is summarised in Table 1 and illustrated by the microscopy image in Figure 1.
This emulsion was found to be very stable, showing only trace separation over a 48-hour period at the process temperature.
Bottle testing was repeated using this new, more stable, emulsion. Separation trends, illustrated in Figures 2 and 3, were markedly different for the same products under the same test conditions. Demulsifier A, used for the well test project and therefore considered to be the benchmark product, was now found to be significantly slower at separating water than some of the other demulsifiers that had previously been found to perform as well as Demulsifier A at best. The tests using the emulsion created using droplet size matching identified a new product, Demulsifier G, as the most effective for resolving this particular emulsion. Demulsifier G was seen to separate the water from the crude oil more quickly and more completely than the original Demulsifier A, which was only able to remove approximately 75% of the water present.
The antifoam application was more problematic than the demulsifier during the well test project. The original chemical recommended was a ‘best-in-class’ fluorosilicone product. This chemistry is typically the highest performing oil antifoam; however, throughout the well test this particular product was found to be ineffective across a wide range of doses. Standard foam collapse tests were conducted using sampled fluids at atmospheric pressure in a glass measuring cylinder sparged with CO2. The maximum foam height and time taken for the foam to collapse were measured for both untreated and treated samples. The results were fairly ambiguous, with little difference found between doses or different chemicals.
It was suspected that the primary reason for the fluorosilicone chemistry being ineffective as an antifoam on this particular crude was due to the chemical not being suitably dispersed in the oil, and therefore not being able to reach the surface of the bubbles to destabilise the foam. This lack of dispersion may have been due to the large viscosity differential between the antifoam (5 cP) and the oil (approximately 1000 cP). Theories suggest that with viscosity differentials of greater than a factor of 10, the lower viscosity fluid will be encapsulated by the higher viscosity fluid and very little dispersion can occur, even in turbulent systems. One way
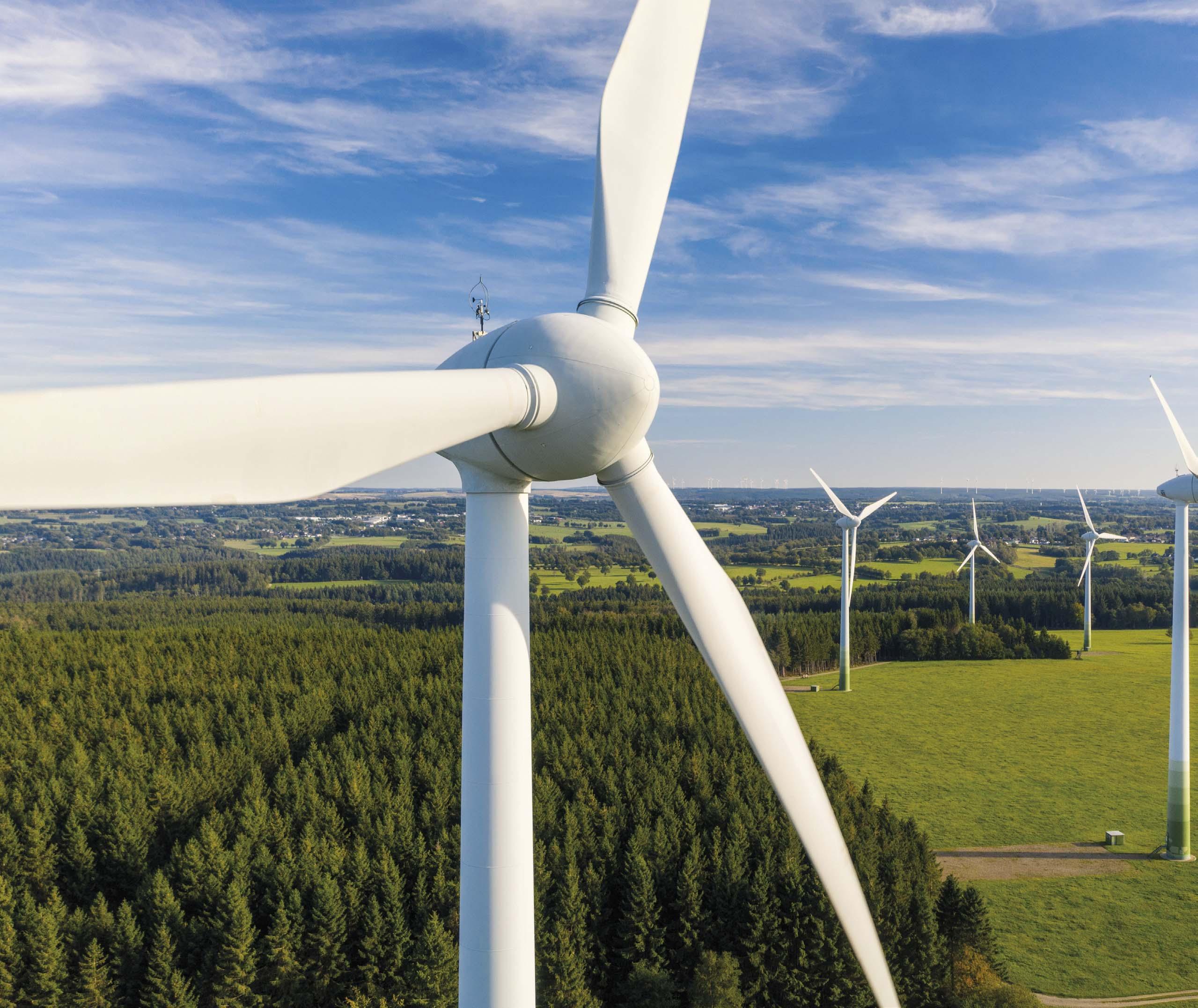
The premier source of the latest information for the renewable energy industry, covering solar, wind, bioenergy and storage.
to overcome this phenomenon would be to use a higher viscosity antifoam to address the problem as a physical issue, rather than a chemical one.
This theory was not proven in the standard foam collapse test; however, when the opportunity to try another antifoam product at the new field arose it was decided to go with a much higher viscosity polydimethylsiloxane product (350 cP) despite conventional wisdom suggesting that this type of antifoam is less effective than the fluorosilicones. The result of the trial was very different; the polydimethylsiloxane was found to be much more effective at knocking down the foam produced in the process and, therefore, was selected for use at the field.
A successful recommendation is of course always welcome, but if the successful result could not be replicated using the standard antifoam test procedures then there was clearly something not optimal with the procedure commonly used. It was this question that then led to a test method development project being undertaken in order to find a method to assess foaming characteristics and antifoam performance more in line with real-life conditions. The most obvious difference between the standard test method and the real-life situation is that the tests are usually conducted using ‘dead’ crude at atmospheric pressure. In the process, the crude is ‘live’ and under pressure – it is indeed the depressurisation of the crude that causes the gases to break out of the crude and create the foam. In the laboratory test, gas is merely sparged through the crude to try to create a foam which, with heavier crudes, can be very difficult.
The solution to these differences was therefore to try to bring the crude oil ‘back to life’ and to try to create the foam in the same way as in the process, through depressurisation. Recreating ‘live’ crude can be achieved fairly simply by sparging gas through the oil under pressure in order to saturate the crude. The pressurised ‘live’ crude was then depressurised rapidly and it was found that significant quantities of foam were created. Using this method, it was possible to then test the efficacy of different types of antifoam chemistries at reducing the foam created when the live crude samples were depressurised. With these tests it was possible to better differentiate performance between chemicals on the heavy crude and, more significantly, it was demonstrated that the higher viscosity polydimethylsiloxane was more effective than the low viscosity fluorosilicone product. This gave some validation to the test method, as it reproduced the result observed in the field trials.

Figure 2. Comparison of water separation trends at 60˚C with 20% water cut.
Figure 3. Separation trends for droplet size matched emulsion treated with diff erent demulsifiers aft er 2 hours at 60˚C.
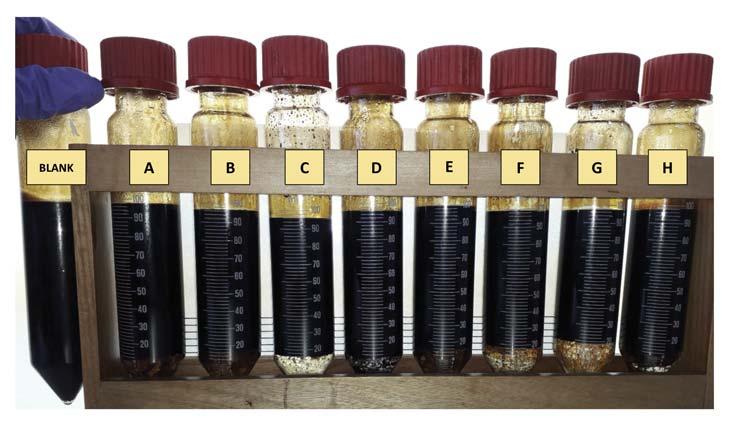
Summary
Clear variances in performance of demulsifiers were found between test methodologies. Simple, basic bottle tests using dead oil were not able to demonstrate significant performance differences between several demulsifier types, with all candidates showing similar performance to an ‘off-the-shelf’ product previously used during a well test exercise. Matching the emulsion more closely with that produced during the well test did, however, yield different trends to the original tests, highlighting significant performance differences between demulsifiers and identifying a better performing product for the next stage of the field development.
Likewise, with the antifoam application, the initial recommendation of the ‘best-in-class’ chemistry was found to be ineffective in the field and the standard laboratory test was again unable to differentiate performance between other chemistry types, even though an alternative product had been subsequently seen to be effective in the field. Retrospective test development was able to demonstrate that saturating the dead crude with gas then rapidly depressurising was a far more realistic way of creating foam and therefore of testing the efficacy of antifoam chemistries; the new test was able to replicate the performance differential seen in the field between the original recommended product and the product tested more successfully later on.
This all leads to the fairly unsurprising, yet all too often ignored, conclusion that test methodology and conditions are crucial when selecting production chemicals such as demulsifiers and antifoams. It is not enough to merely have the ‘best’ chemistries; it is also essential to know how to test them in a representative manner. Performance trends observed in tests using dead oil can be wholly unreliable if no efforts have been made to re-condition the fluids to be more truly representative of the fluids actually produced in the oilfield.