
8 minute read
Maximising annulus integrity
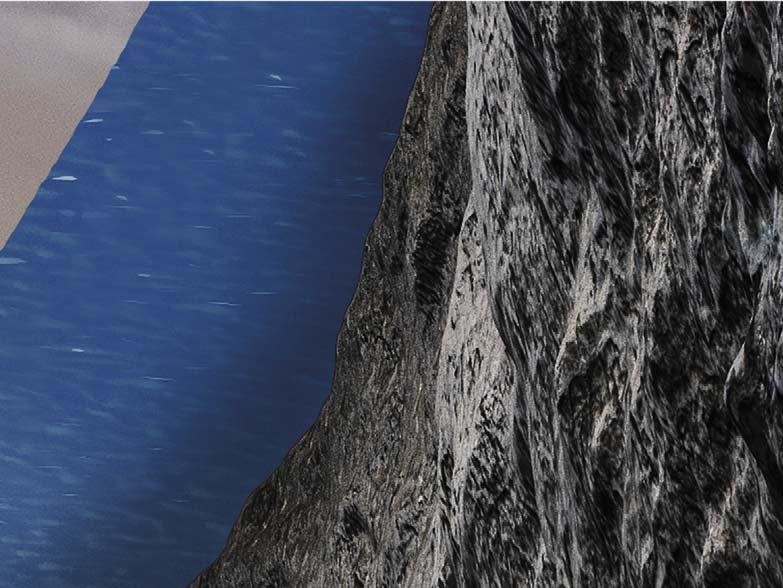

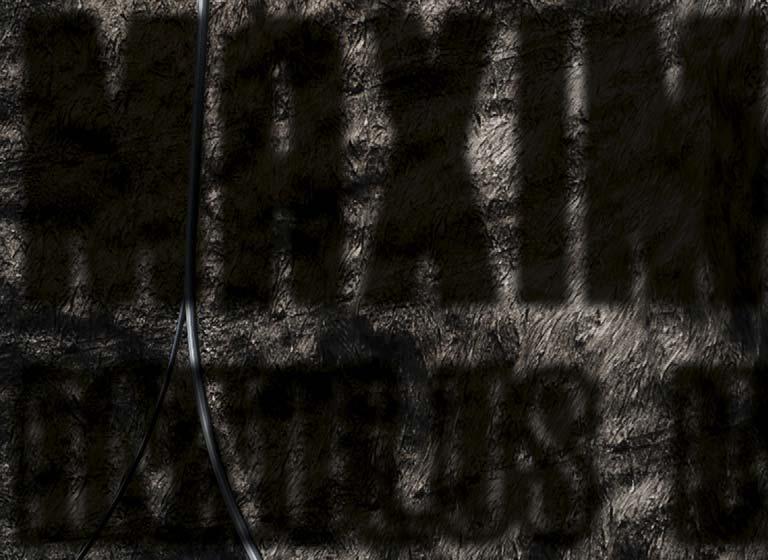
MAXIMISING


ANNULUS INTEGRITY


Brett Hrabovsky, Elisabeth Norheim and Andreas Fliss, Archer, Norway, examine the benefits realised from the successful application of cementing technology.


Well integrity is defined by NORSOK D-10 as ‘application of technical, operational and organisational solutions to reduce the risk of uncontrolled release of formation fluids throughout the life cycle of a well.’1 Well integrity is concerned with the safe and reliable containment of all well fluids throughout the life of a well, including while drilling, running completion, during production and well interventions. A failure of well integrity is oft en related to safety and environmental aspects but also includes loss of production, reputation and asset value.
Annulus integrity is a key component in the assurance of overall well integrity, and challenges may appear in many shapes and sizes. Whether it be annular pressure build-up (APB) in subsea wells, causing potential casing failures; inadequate zonal isolation, leading to less than optimised production rates; compromised barriers due to degradation or geologic events, causing costly intervention operations; or a plethora of other challenges, they all have the potential to cause significant losses for the asset owner.



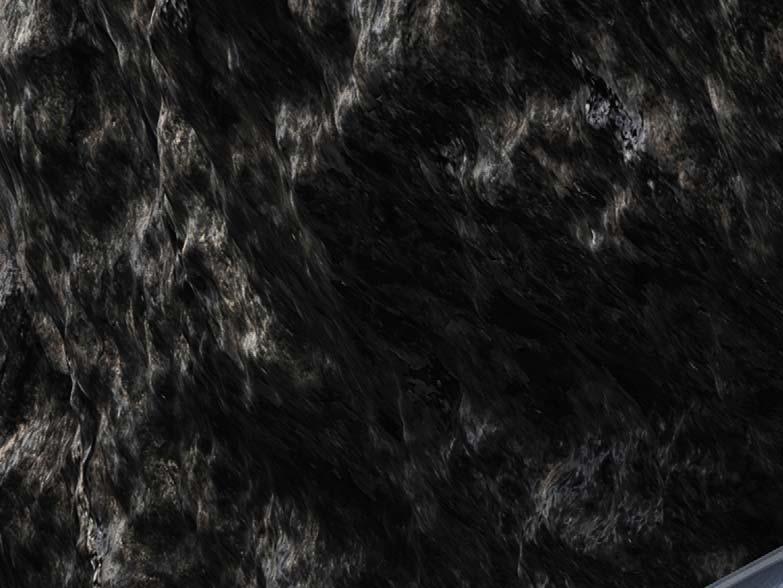
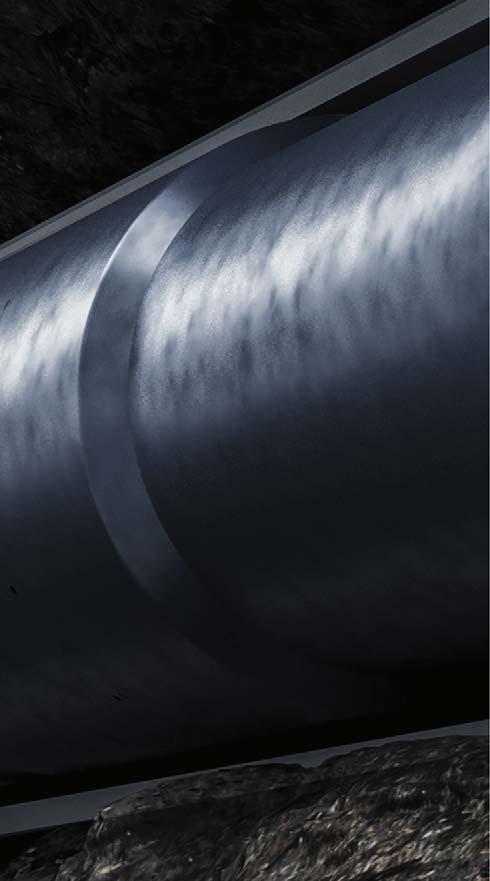

COVER STORY

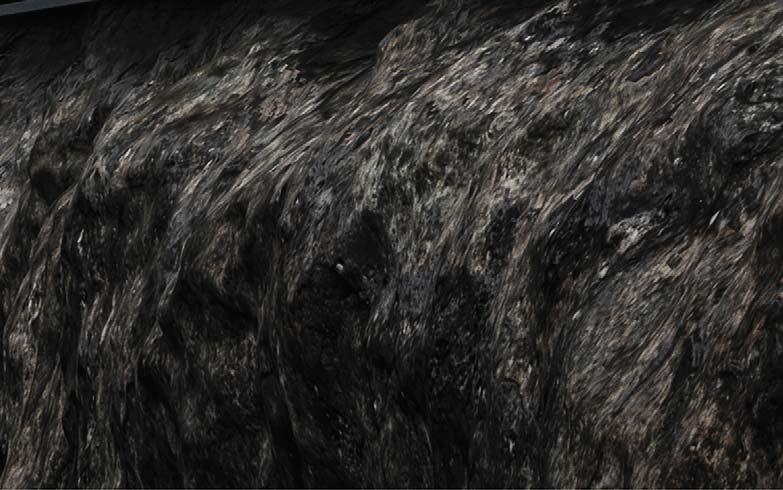
As the industry recovers from the downturn, the challenges associated with improving and maintaining annulus integrity through operational eff iciency, prompt results and – of the utmost importance – cost-savings will continue to remain.
Archer Oiltools provides smart and robust solutions where well integrity, reliability and time-savings are of the highest importance. The company’s Cementing Solutions Product Line – GuardianTM – includes technologies that deliver better wells by extending well life, maximising well performance and minimising environmental impact (Figure 1).
Flexibility in barrier placement and verification
The Cflex® is a mechanically activated downhole sleeve that provides controlled, secure and selective access to the annulus space typically used for stage or remedial cementing applications (Figure 2). The flexibility, reliability and confidence in annular access allows for use in other applications that also require this functionality. This includes, but is not limited to, barrier verification (i.e. creeping shale) and APB mitigation as a pressure relief port.
The Cflex is V0 qualified through rigorous testing, equivalent to the ISO 14998 standard, which means it provides an absolute ‘gas tight’ seal. Locking the sleeve so that it is permanently closed following a successful operation adds further security.
In terms of eff iciency and performance operating the Cflex is straightforward, fast and precise. The multi-function operating tool is designed to both operate the Cflex valve and inject fluids. If multiple sleeves are present, each can be accessed and controlled selectively according to the multi-stage programme. Archer has successfully installed up to five Cflex’s in a single string and up to nine in a single well.
The Cflex-F takes the technology a step further and incorporates an annulus cement base that activates during the opening of the cement ports. This ‘fundament’ creates a solid base and prevents cement contamination below the tool.

Figure 1. Cflex and MCAP global footprint.
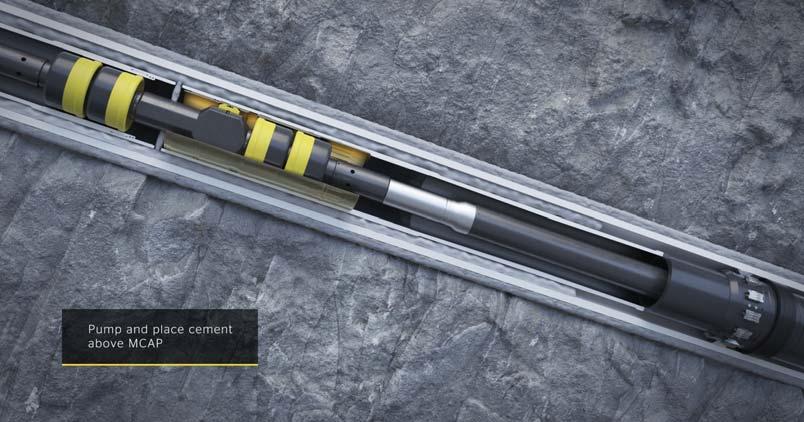
Figure 2. Pumping cement through a Cflex.

Figure 3. Activation of MCAP.
Providing protection on its own or in support
The MCAP® is a mechanically set packer designed to seal off the annulus between two casings. It is activated by a drill pipe deployed activation tool, having over pull when latched into the MCAP (Figure 3).
As with the Cflex, if multiple packer devices are present each can be accessed and controlled selectively on the same trip.
The packer device has been subjected to similarly rigorous validation testing protocols, and both the element section and internal seals have been qualified as a gas barrier according to ISO 14998/14310, with a pressure rating up to 10 000 psi.
The MCAP can be used as a stand-alone tool for isolation of the annulus between two casings for many applications, including prevention of sustained casing pressure (SCP) and a tieback anchor/packer. It can also be installed in combination with a Cflex where the MCAP will create a fundament for placing cement above and isolate below the Cflex, preventing any influx from lower zones from contaminating the column of cement above prior to cure.
Integrated operations
Since 2015, Archer has made it possible to run operations off shore without company personnel themselves being on board the rig. Integrated operations (IOs) ensure a high standard of operational quality and safety and, through the use of advanced real-time technology, deliver a significant reduction in personnel-on-board (POB) to operators, as well as a substantial decrease in carbon footprint globally.
In 2020, Archer performed more than 300 IOs worldwide, from Canada and the Gulf of Mexico to the North Sea and the Caspian Sea. The company has increased the scope of products and solutions delivered with IOs over recent years, with a 100% success rate. In 2020, the company’s IOs saved approximately 20 000 t of CO2 emissions.
Case study 1
Challenge
During drilling of the 17.5 in. section the operator experienced heavy losses, followed by significant gains from a suspected drilling-induced fracture. Although the well was somewhat stabilised for casing installation, it was
Solution
The operator decided to install one Cflex approximately 5500 ft above the shoe at approximately 6500 ft as a contingency cementing option if the primary was unsatisfactory. A second Cflex was installed approximately 140 ft above the 18 5/8 in. casing shoe at approximately 2300 ft , directly above the MCAP, to isolate the problematic zones deeper in the well. This upper Cflex and MCAP contingency would help the customer ensure isolation in the uppermost section of the 13 5/8 in. casing.
Results Results
The execution of the job from start to finish was successful, with all equipment performing as expected (Figure 5). Subsequent logging of the casing showed significant improvements in cement coverage across the target zones.
The solution allowed the NOC the option to change well design and save 7 – 10 days in rig time per well, equating to approximately US$700 000 in cost.
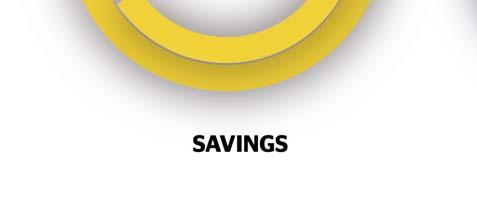
The primary cement job was performed conventionally through the shoe and, as expected, did not achieve the required cement coverage due to losses encountered when pumping cement.
As a result, the Cflex cementing tool and MCAP activation tool were run in hole past the upper Cflex and MCAP and down to the lower Cflex. The Cflex was then opened successfully and a second stage job was performed through it in an attempt to achieve better cement coverage. Due to extremely challenging loss conditions it was not possible to achieve the column of cement required via the lower Cflex. The MCAP was then successfully set and tested to 500 psi and the Cflex opened using the activation tools in the drill string. This isolated the problematic formations and allowed a controlled third stage to be performed, ensuring competent cement throughout the 13 5/8 in. x 18 5/8 in. casing annulus.
The execution of the job from start to finish was successful, with all Archer equipment performing as expected. Subsequent logging of the casing showed very good cement coverage inside the 13 5/8 in. x 18 5/8 in. casing annulus (Figure 4).
Case study 2 Summary
In the cost-conscious market of today’s oil and gas industry, remedial and intervention work to repair or put in place annular barriers can be costly and delay or postpone production. Archer’s Guardian product family of annular integrity solutions provide operators with greater confidence that they can secure wells the first time, as well as providing flexibility in contingency measures and barrier verification. Further benefits include minimising cost and potential environmental impact, extending well life and maximising well performance throughout the life of the well.
Reference
1. NORSOK D-010 Well integrity in drilling and well operations, Rev.4 (June 2013), https://www.standard.no/en/sectors/energi-og-klima/ petroleum/norsok-standard-categories/d-drilling/d-0104/
Challenge
A national oil company (NOC) in the Gulf Cooperation Council (GCC) region has historically been unable to consistently achieve competent cement above a loss zone approximately 2000 – 2500 ft above the 9 5/8 in. casing shoe at approximately 7500 ft . This challenge oft en leaves 5000 ft or more of inadequately cemented casing, leading to corrosion issues and resulting in compromised well integrity over time. The current solution utilises top down cement squeeze jobs from surface that are mildly eff ective and oft en leave areas un-cemented, leading to multiple issues in the future, including sustained annulus pressure and casing corrosion. Figure 4. Case study 1: well schematic illustrating placement of the Archer equipment.
Figure 5. Case study 2: cost, time and equipment savings for Cflex and OH packer technology.
Solution
The solution proposed was a two-stage cement job utilising an inner string that would allow eff icient, accurate and eff ective placement of cement around all target zones.
The primary job was performed through a tag in float system supplied by Archer that allowed the packer to be set and Cflex opened before the first stage cement set-up. The openhole packer, situated just above the loss zone, was then inflated to isolate the losses and provide a fundament for the column of second stage cement. Aft er packer inflation the Cflex directly above it was opened with an inner string cementing tool and excess cement was circulated out from the first job.
A second stage cement job was then performed through the Cflex above the openhole packer.
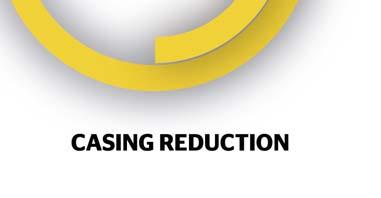