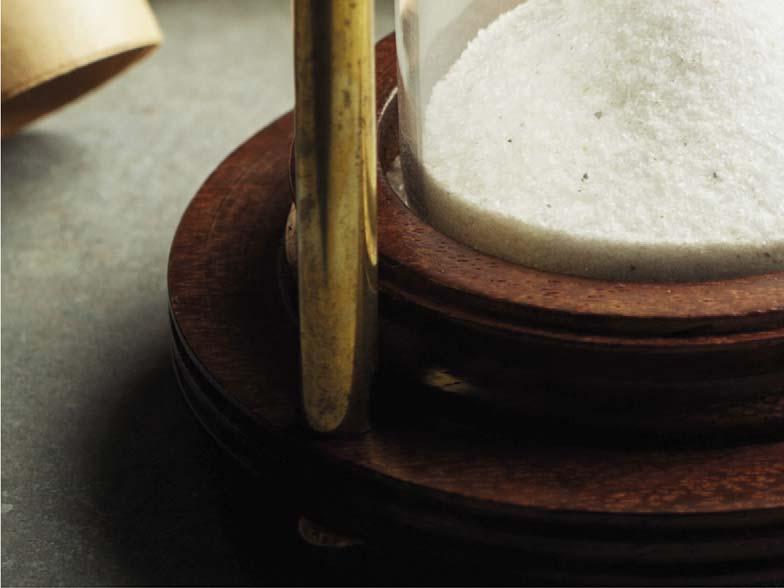
8 minute read
Leveraging History To Transform The Future
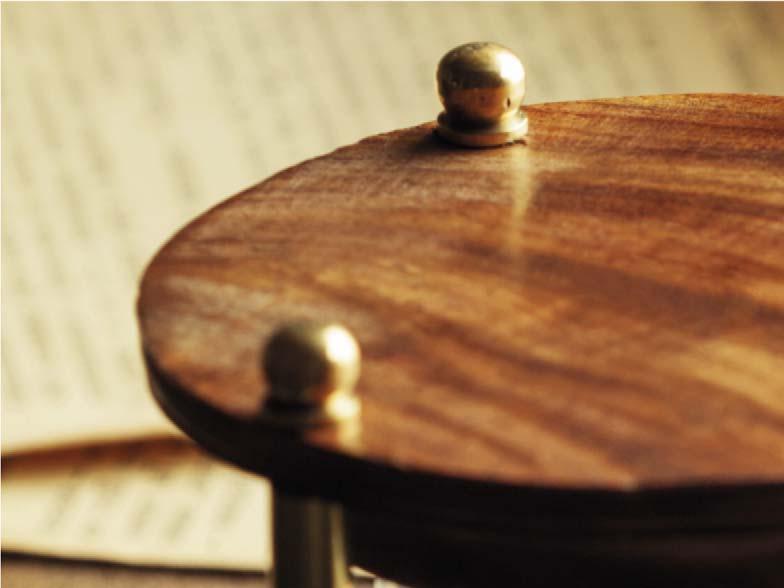
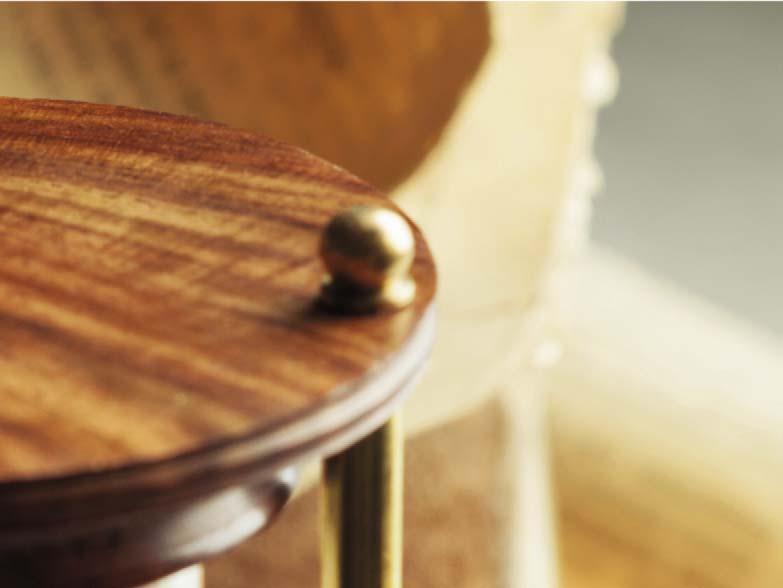
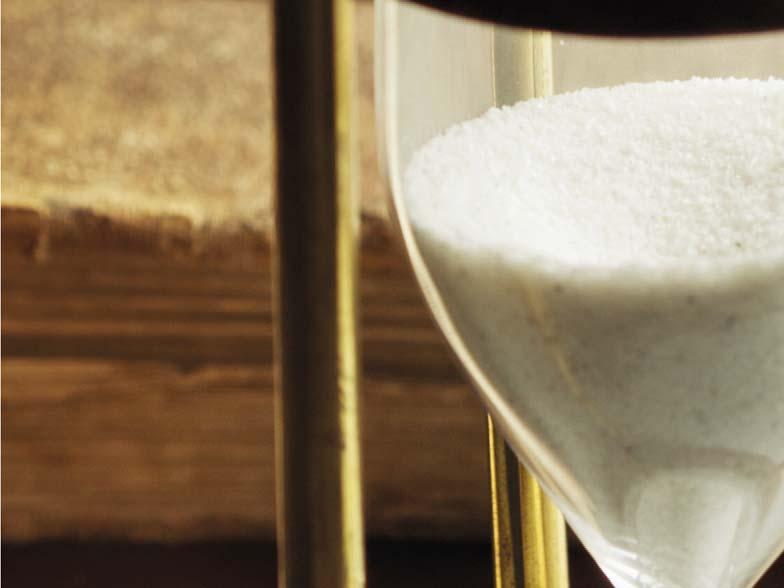

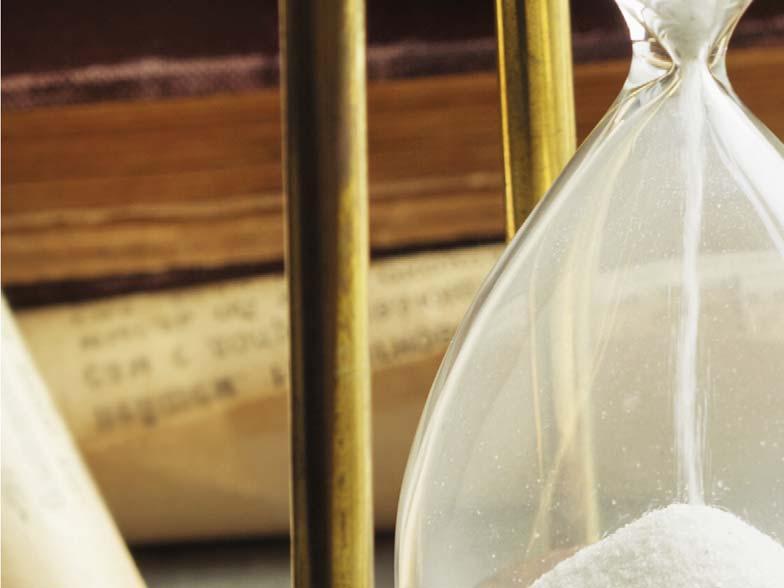
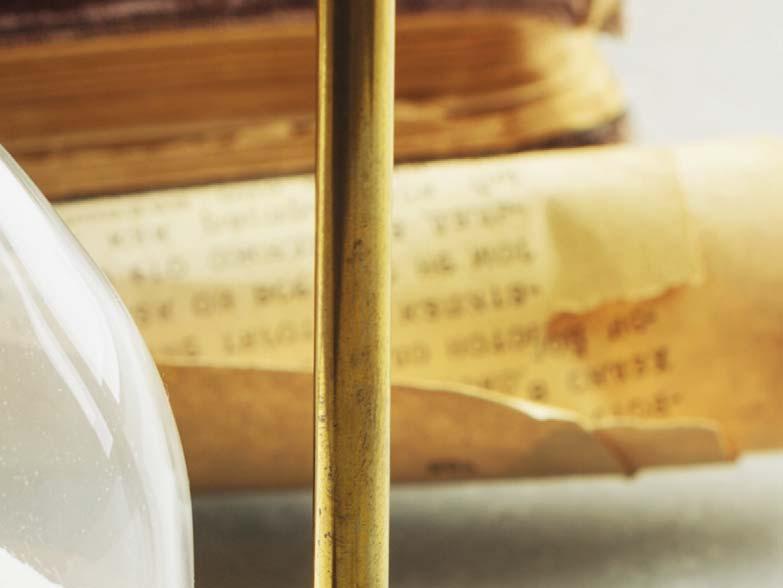
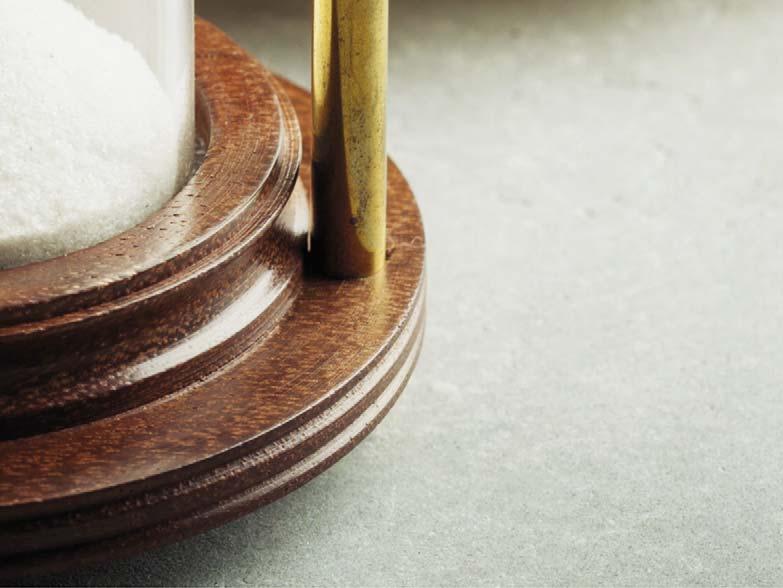
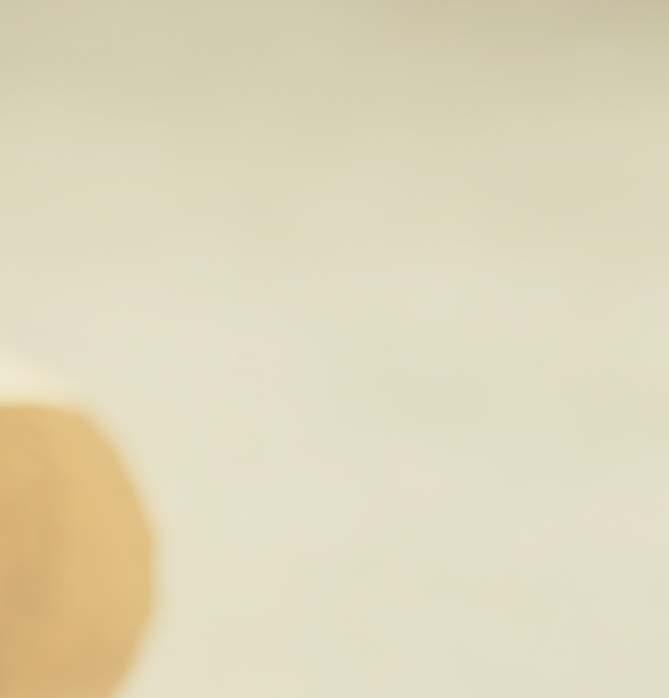
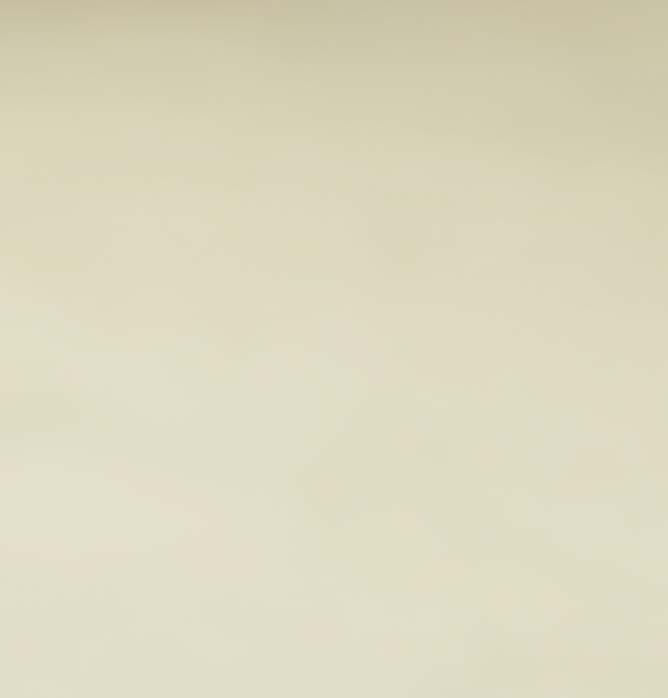
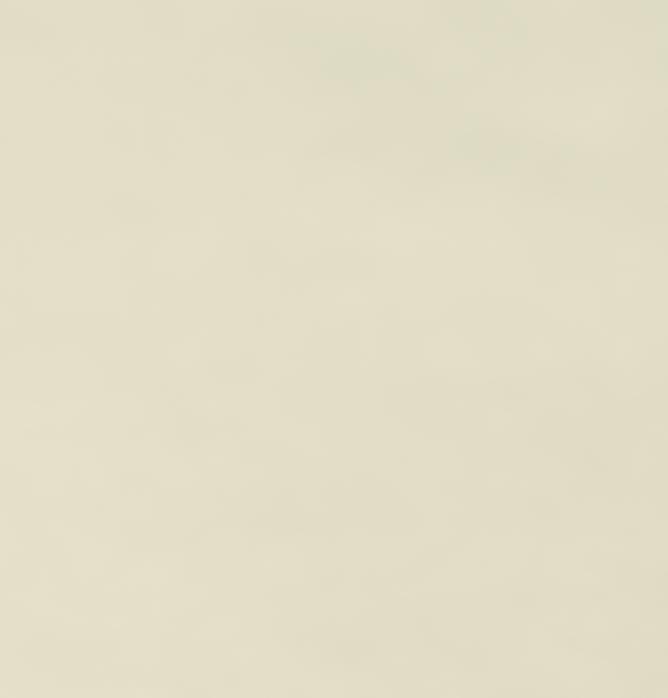
Demetre Harris, Sandvik, USA, outlines how product and solution providers have adapted, and are continuing to adapt, to the challenges of the ever-evolving mining industry.

Amining company must always anticipate that its products will be used in any possible scenario. Whether terrain is flat or rocky, or temperatures are tropical or arctic, a drill rig must be able to withstand all kinds of conditions, in order for it to be transferable across diff erent climates, terrains, and mineral deposits. Sandvik, an engineering company that provides solutions for the mining and construction markets, has a legacy that spans well over a century, and is therefore very familiar with this need to be adaptable.
Founded in Sweden in 1862, Sandvik has always believed in pushing itself to provide cost-eff ective, sustainable products that are designed with productivity, technology and maintainability in mind, regardless of the circumstances. To continue to innovate requires a strategic mindset and dedication to one’s craft . Sandvik invests SEK 3.4 billion (approximately US$398 million) every year into research and development, while also devoting countless hours to designing equipment that bolsters innovation. In order to understand Sandvik’s longevity and its global outlook, it is helpful to look back at its founder to conceptualise how mining, drilling, and innovation has always been an integral part of Sandvik’s DNA.
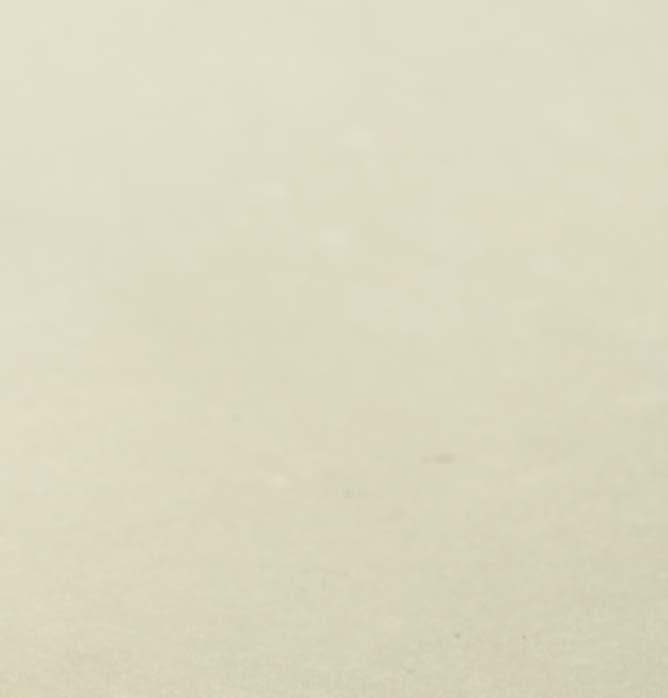
Göran Fredrik Göransson: ‘The Maverick’
In a coincidental twist, Sandvik’s founder, Göran Fredrik Göransson, possessed a life trajectory that mirrors the company’s values generations aft er his passing in 1900. As a young adult, Göransson worked at a shipping company and later travelled abroad – not an easy feat at that time. His travel experiences provided Göransson with the international perspective Sandvik still upholds to this day.
Göransson’s vision helped the shipping company to invest in iron and steel. When the company came to purchase an annual production of pig iron, it was this acquisition which ultimately kick-started Sandviken Jernverk – now known as Sandvik since 1972. As a pioneer Göransson became the first person to utilise the Bessmer process on a massive scale. This process assists steel production by removing impurities from iron via oxidation. Currently 80% of the metal in Sandvik’s steel is recycled, which conveys how Sandvik continues to take sustainability seriously.
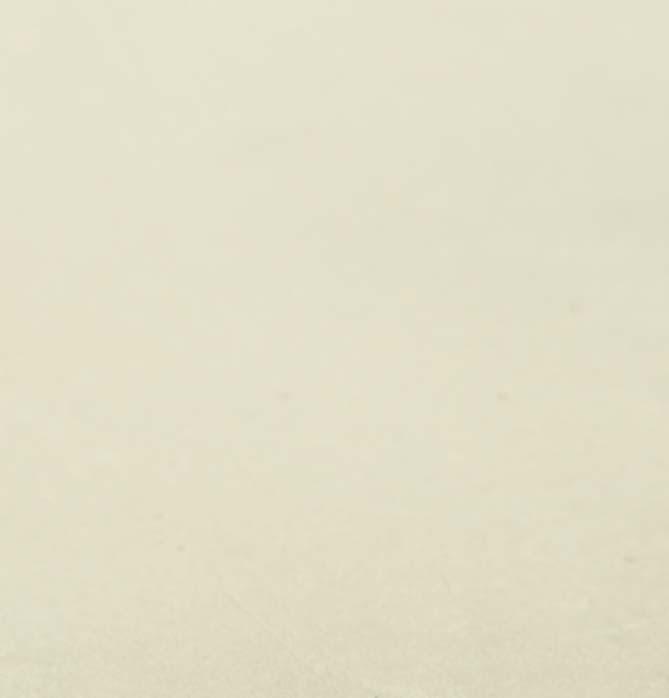

The following sections outline how Sandvik continues to strive to uphold the values and vision of its founder through its products and services.
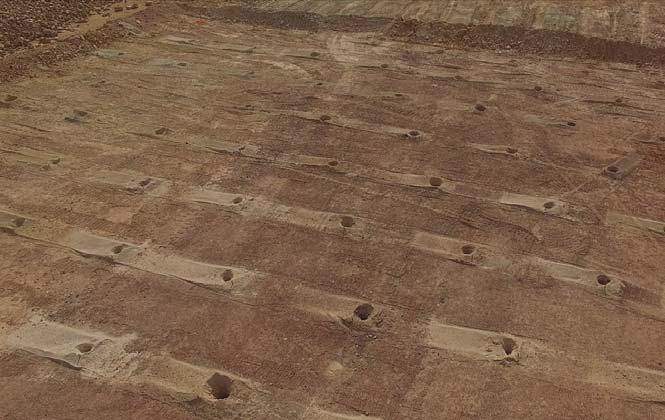
Figure 1. iSeries drill rigs utilise high precision GPS to help the onboard operator produce clean holes in the correct locations, improving fragmentation.
Figure 2. The Sandvik TIM3D Navigation Solution, which operates on the Sandvik Intelligent Control System Architecture (SICA), uses advanced visual tools for planning, reporting and analysis, in order to enable operations to spend less time on administrative tasks and more time drilling accurate and consistent holes.
Figure 3. Ergonomic cabin design features enhance the operators interface with the machine leading to improved production.
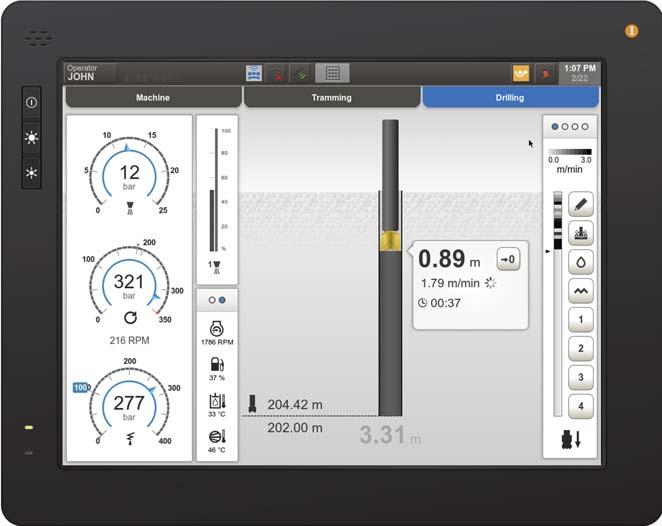
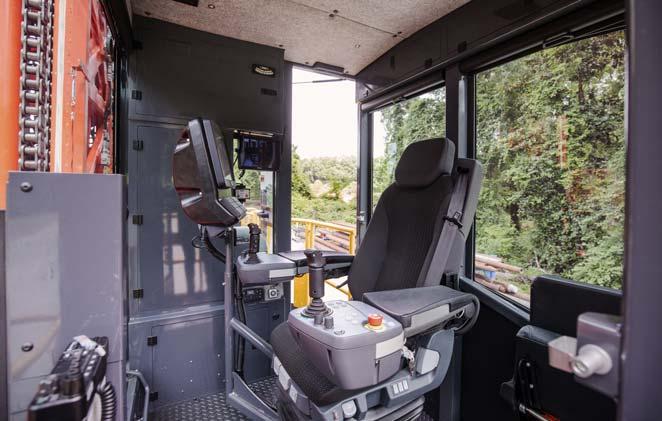
The iSeries family
The iSeries drill rig family is the cornerstone of Sandvik’s rotary drilling portfolio. The series features the DR410i, DR412i, and the DR416i. Although each drill has its respective features, there is consistency across all models in terms of operator experience. Sandvik’s iSeries is the embodiment of Sandvik’s commitment to implementing modern design. Overall, the iSeries increases eff iciency because of the onboard functionality of the drill. iSeries drill rigs have sensors on the drill and within the rig itself. These multiple sensors allow the operator to make calculated decisions regarding drill depth when taking into consideration the terrain and altitude of a drill site. The feedback provided by the sensors monitors crucial information, such as fuel and water levels and information about pull-down, just to name a few.
Sandvik’s iSeries represents the future because it provides a window into automation and data reporting, while concurrently having a focus on who operates the machinery. The iSeries informs the present, but will always be a symbol of the future, and of how Sandvik will continue to strive to push the envelope and lead the mining industry forward.
Smooth operator
The link between human and machine is inextricable and undeniable. An advancement in drill rigs means a completely diff erent experience for the operator. If a rig is eff icient and easy to use, that means it democratises the experience of the operator by levelling the playing field. Operators with diff erent skill levels will be able to utilise the rig, which means that not only an ‘expert’ would have to be in charge. Designing from an ergonomic perspective involves maintaining the operator’s day-to-day tasks as a top priority. Sandvik’s drill rigs have an adjustable operator’s seat, large touch screens, seat mounted buttons, and joysticks within an arm’s length. All of these attributes keep the operator’s body and mind from working too strenuously. The operator will therefore be more productive, and the site as a whole reaps these benefits.
For over 150 years, Sandvik has prioritised customer feedback, as it is a catalyst for innovation. Mining is an industry that deals with many variables, some known and some that may arise at a moment’s notice. Therefore, a paramount sentiment among the mining industry has to include safety as one of its core tenets. For Sandvik in particular, it believes in ‘zero harm’ and this motto is inclusive of its own employees and customers’ employees as well.
Supporting the customer
Data is the driving force behind how customers make informed decisions about purchases and how companies are able to assist customers. Although mining has to focus on the present and the task at hand to maximise productivity, concurrently mining companies must always grapple with the future. Mining companies must be nimble and plan ahead. They want to see tangible improvements and the data that backs up a particular innovation. Mining customers are especially active in the buying process because they are deeply invested in learning about products before they purchase them. Even aft er a purchase, customers require a personal connection, particularly when it comes to a tech issue.
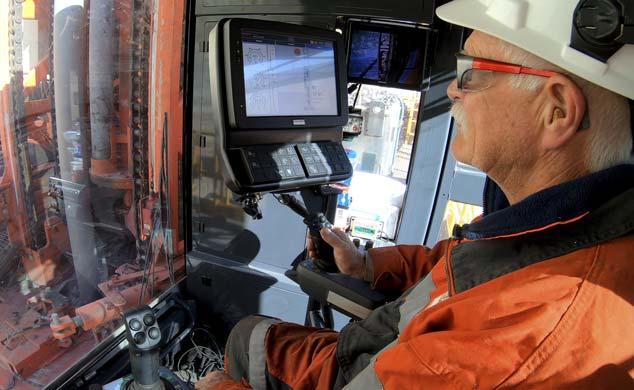
Figure 4. Instant access to information, drill plans, and machine health improve operator engagement and productivity.
If a problem arises, Sandvik’s technical service team can assist an engineer using diff erent methods of remote support, no matter where an operator is located. With the permission of the client, a Sandvik support team member can assist an operator or engineer using technology that allows the support team member to see what the operator sees. This technology makes the Sandvik support team feel as though they are inside of the drill rig, allowing the support team member to accurately pinpoint the issue causing a malfunction and provide specific directions to rectify the problem. Currently a malfunction is rectified aft er it has occurred, but with continued technological advances there will be a point where it is possible to anticipate a malfunction before it happens. Remote support is not just about maintenance, it is about equipment uptime and eff iciency as well. Advanced diagnostics can provide suggestions on how to optimise drill performance. As the world continues to move more and more into a world that relies on virtual interactions, remote support will continue to evolve.
The future is now
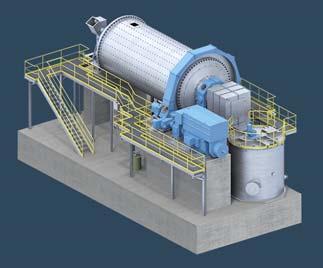
As opposed to an industry like automobiles that has always been rapidly changing and innovating, the mining industry has taken a diff erent approach in that it did not initially latch on to the use of advanced technology. The shift in adopting a more technological mindset has meant major upgrades throughout the mining industry, including high precision (HP) GPS navigation. Embracing this technology means being committed to the management of change, implementing improved processes which use less energy and in turn increase productivity, thereby producing a ripple eff ect of eff iciency. The mining industry has always been connected to technology in varying ways, but now we are living in an era that ensures that data is always of the utmost importance. Although automation cannot solve every problem, it is an important part of how technology has advanced. It is clear from the last couple of decades that the mining industry has been making tangible progress with innovation. As the mining industry continues to grow, sustainability, productivity, and maintainability will be the trifecta that guides progress.
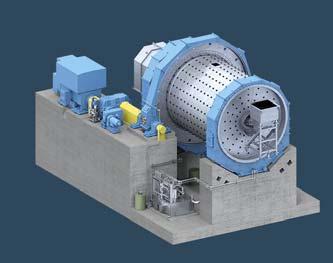
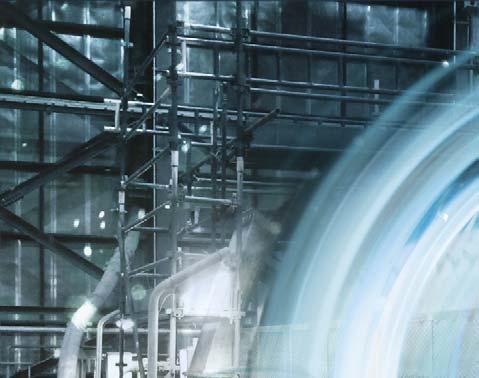

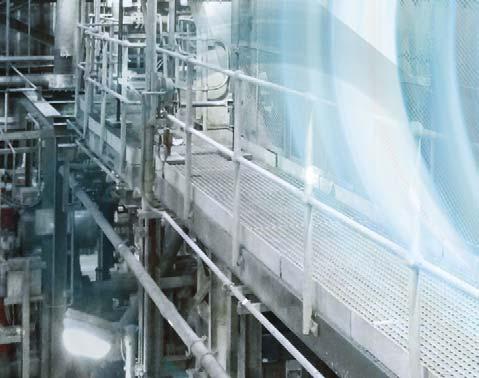


Toughest conditions, coarsest materials – time for EFFICIENT
PROCESSES
Autogenous/ Semi-autogenous mills
Slide shoe bearing mills
Trunion bearing mills
Visit us at christianpfeiffer.com