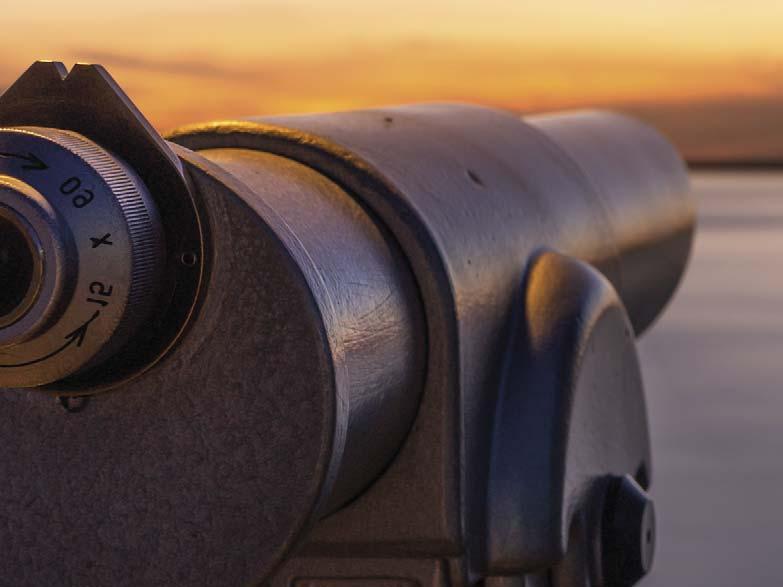
8 minute read
Seeking Sustainable Comminution Solutions
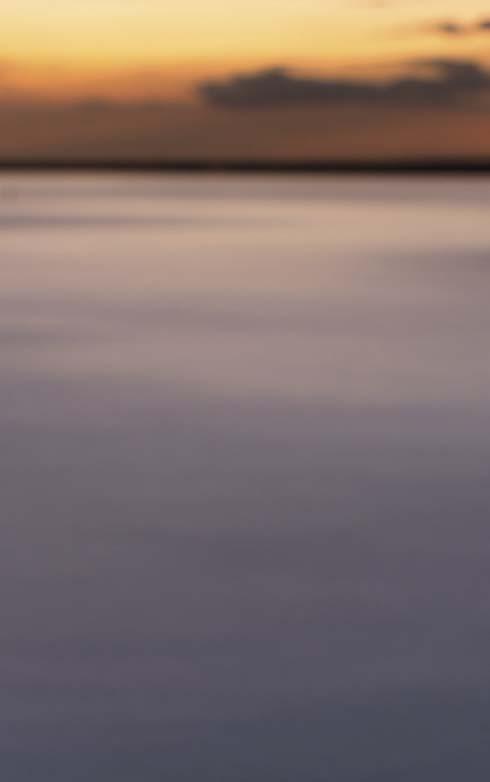

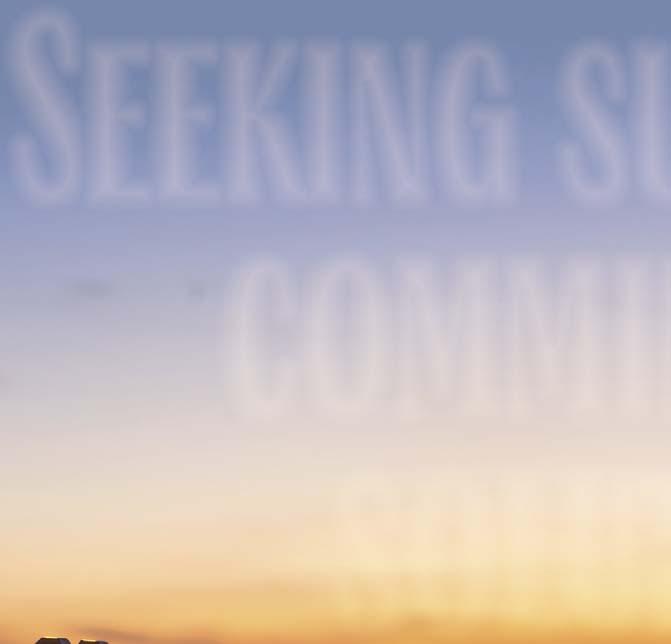
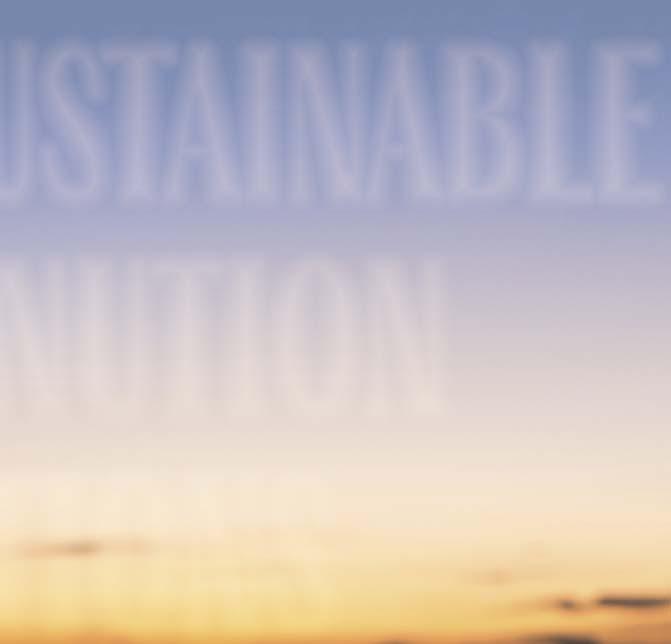



Bjorn Dierx, Weir Minerals, the Netherlands, explains why greenfi eld projects are increasingly turning to high pressure grinding rolls technology to reduce their energy consumption, lower their greenhouse gas emissions, and improve their throughput capacity.
The global mining industry must move away from legacy systems and processes if it is to meet the challenge of decarbonisation, according to a new report which calculates mining’s share of global energy consumption and identifies ways the industry can aid the transition to net zero emissions, in order to limit temperatures in line with the Paris Agreement.
The report, commissioned by the Weir Group, quantifies energy use in five commodities: copper, gold, iron ore, nickel, and lithium. Bringing together mine energy use data from more than 40 published studies from 2007 to 2020 into a single narrative (each of which references dozens more studies), the report aims to build a more comprehensive understanding of energy use in the mining industry.
It shows that the total amount of power used by the mining industry – which plays an essential role providing the metals used at the heart of the modern economy – is equal to approximately 3.5% of global energy use.
The metals produced by mining are critical for enabling the global transition to low-carbon infrastructure. However, without action, energy use in mining itself is set to trend higher in the coming years, as demand increases for the minerals required
for a clean energy transition. Assuming that present trends continue, there will be 250 million electric vehicles on the road by 2030. To meet this demand, production of cobalt, lithium, graphite, and nickel will need to be scaled up significantly.
The report suggests there are technologies available today that could make a significant diff erence in reducing energy consumption. For example, it highlights that comminution – i.e. crushing and grinding processes – is the single biggest user of energy at mine sites, typically accounting for 25% of mining’s final energy consumption. This is equivalent to the power used by 221 million typical UK homes, or approximately 1% of total consumption globally. Comminution is therefore a natural target for the most impactful energy savings opportunities.

Figure 1. A 2.4 m Enduron® HPGR being built in Weir Minerals’ dedicated, state-of-the-art HPGR assembly centre in the Netherlands.
Figure 2. The Enduron HPGR’s larger rollers reduce the number of lines per concentrator.
Figure 3. An Enduron HPGR with unique L:D ratio for hard-rock grinding.
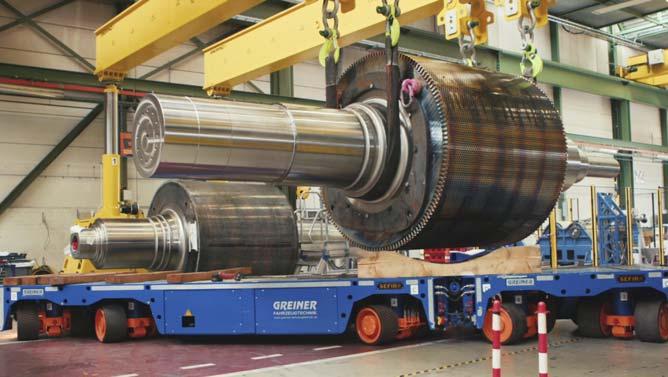

Improving comminution effi ciency
Small improvements in comminution technologies can lead to relatively large savings in both energy consumption and greenhouse gas emissions. For example, a 5% incremental improvement in energy eff iciency across comminution could result in greenhouse gas emissions reductions of more than 30 million t of carbon dioxide equivalent (CO2-e). The replacement of traditional comminution equipment with new grinding technology also reduces indirect emissions in the mining value chain, for example by removing the need or reducing the manufacture of emission-intensive steel grinding balls, which absorb 6 kWh/kg within the supply chain.
High pressure grinding rolls
Weir Minerals’ Enduron® high pressure grinding rolls (HPGRs) technology can help save up to 40% in power consumption when compared to traditional grinding circuits, allowing mine operators to produce more for less. Each installation of an Enduron HPGR unit is estimated to save 12 000 tpy of CO2, or the same as removing 3500 cars from the road. In the current market, this makes economic, social, and environmental sense.
The Enduron HPGR reduces particles by compressing and grinding the feed between two counter rotating, parallel rollers. This forces the rocks against each other and compresses the feed’s density to 85% of its solid volume. This compression is achieved by applying high pressure of up to nearly 300 Mpa, exceeding the compressive strength of the feed material. In applications where HPGR is followed by tumbling mills, the induced micro cracks generally result in a reduction of the Bond Work Index. For most ores this reduction is in the range of 10 – 25%.
Traditionally, HPGR manufacturers have shied away from skewing designs for fear of roller misalignment, which can create unfavourable load distributions and prevent the use of flanged guards to reduce the edge eff ect. However, the Enduron HPGR’s roller bearings design allows for skewing alongside eff ective self-adjusting cheek plates, reducing wear and promoting better grinding.
Skewing ensures that pressure is distributed across the full width of the tyre, minimising recirculation. This is particularly applicable in segregated feed conditions, which are typical in mineral processing applications. The Enduron HPGR can dynamically accommodate these changing feed conditions through skewing, allowing for the passage of oversized crushing material and tramp metal, resulting in less downtime.
In order to accommodate this uneven pressure, Enduron HPGRs utilise a spring-loaded cheekplate that has been specifically designed to facilitate roll skew and reduce the edge eff ect (maintaining a gap of as little as 1 mm). Put simply, it maintains an even pressure distribution across the entire feed, saving energy and reducing wear.
Enduron HPGRs also include a protective bearing arrangement that has been designed to protect against premature failure and reduce the number of peak loads that can be transferred to the bearings.
They are supplied with a multi-row cylindrical roller bearing system and a Weir Minerals bespoke tailored rubber thrust pad that is arranged directly in front of the
bearing housings. This unique design ensures the bearings are always parallel with the shaft , mitigating the peak pressures and bearing contamination. It also allows for oil lubrication to the main bearings, which delivers market leading bearing life with proven performance guarantees in excess of 100 000 hours.
The Enduron HPGR’s roll length:diameter (L:D) ratio delivers the highest product quality, minimising recirculation, and reducing operational costs. It enables smaller tyre diameters for a given tonnage relative to all competitors. This optimises the operating gap, ensuring full pressure across the full tyre length, exceeding the ore’s compressive strength. This L:D ratio and compact cylindrical bearing arrangement means that Enduron HPGR operators enjoy significantly reduced infrastructure costs, as the required civil structural height is kept to a minimum.
Greenfi eld opportunities
HPGRs, like Enduron, are increasingly replacing conventional mills in comminution circuits for greenfield projects because of their substantially lower energy consumption and potential for significant total cost of ownership reductions.
Engineering a sustainable future
In the coming decades, the mining industry will face the twin challenges of scaling up production of minerals required for the conversion to renewable energy sources, accelerated adoption of electric vehicles and the general move toward increased electrification, while simultaneously reducing its carbon footprint. This transition will require nothing less than a re-examination of every aspect of a mine’s operation, but because comminution is so energy intensive it is a logical starting point. The Enduron HPGR is one example of how energy savings can be achieved.
Through innovative engineering and partnerships across the industry, mining can be more sustainable for generations to come.
Case study
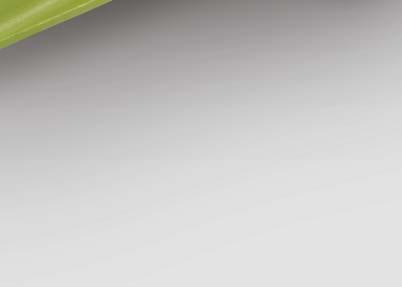
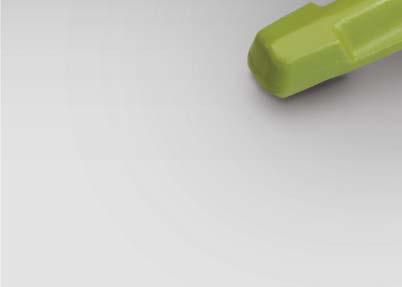
Weir Minerals was recently awarded a £36 million order to provide industry-leading energy saving solutions to Ferrexpo, one of the world’s largest exporters of iron ore pellets to the global steel industry. Ferrexpo is developing production of direct reduction (DR) pellets, which are higher grade (67% iron) and lower impurity than alternative forms of iron ore pellets. DR pellets are expected to represent the future of global steel production, as steelmakers transition to the production of carbon-free green steel, with DR pellets the primary source of virgin iron utilised in this process.
As part of their Green Steel Initiative, Ferrexpo challenged Weir Minerals to help create the most energy and cost-eff icient flow sheet. Weir Minerals’ process engineers provided a solution that uses its large-format high volume equipment to increase capacity while also delivering significant carbon savings.
The initial order, which includes a range of Weir Minerals comminution products, including Enduron HPGRs and screens, will reduce energy consumption by more than 40% compared with traditional mining technologies, bringing substantial reductions in carbon emissions.
Ferrexpo plans to increase output from its operations in Ukraine from 32 million tpy to more than 80 million tpy. Detailed test work with Weir Minerals’ Enduron HPGR technology showed it delivered significant capacity and environmental benefits.
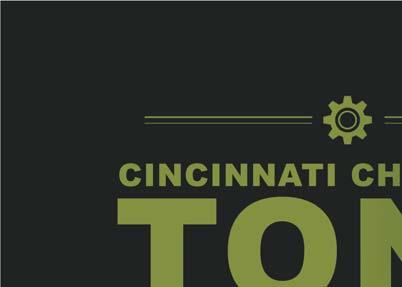

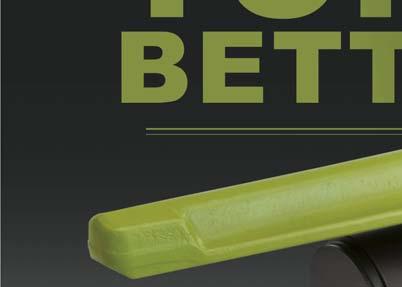


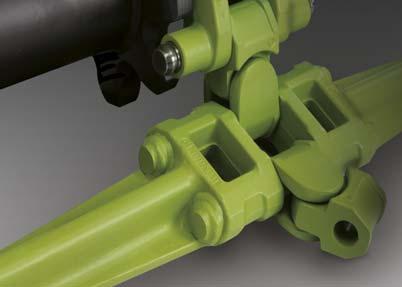
C incin nat i D ual ua Sp roc ket Conveyor Cha hains are proven to to be be tt e r than ot her mining chains. Tons better, in fact. Tests confirm m our c h a i ns d e li v er 20 perce nt m or e stre ngt h . The h re sul t i t i s g s g re rea ter durabi lit y, m a x im u m availability and a t roub l e -f ree se rvi ce lif e . Th a t’s how we deliver the lowest cost per ton. Fo r 90 y ears , C incinnat i h a s proven to b e T HE S TR O N G E S T LI N NK .
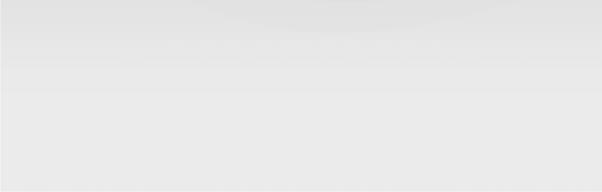