
10 minute read
The Smart Way To Dewater

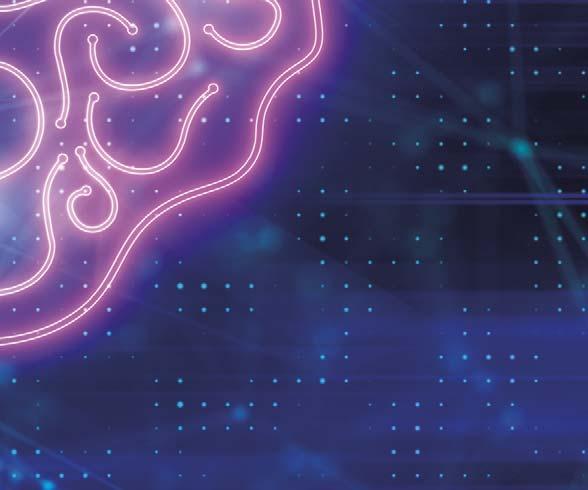
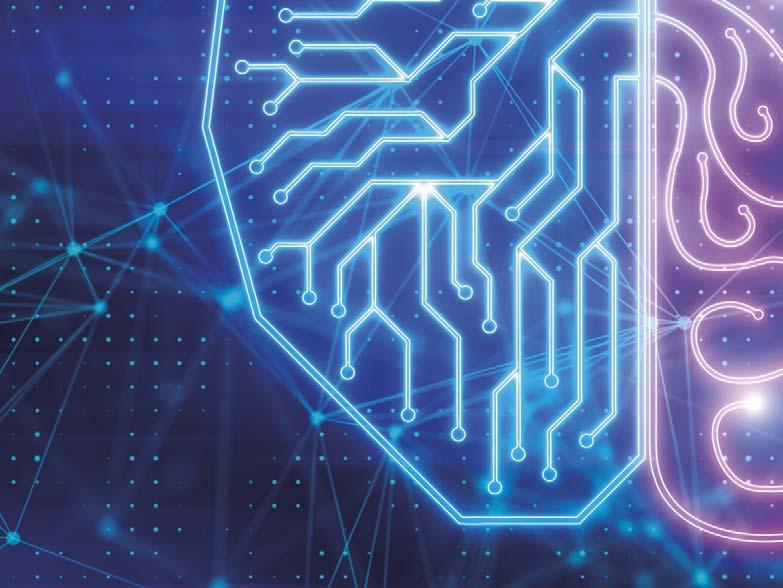
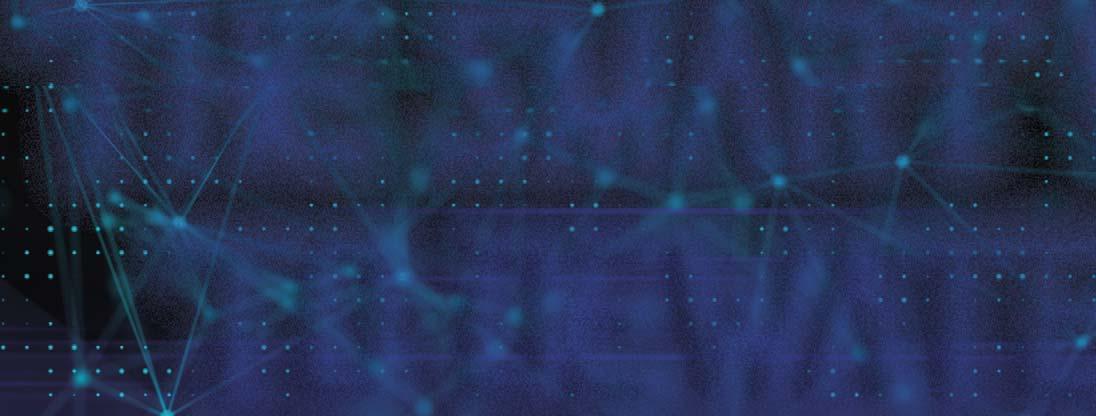
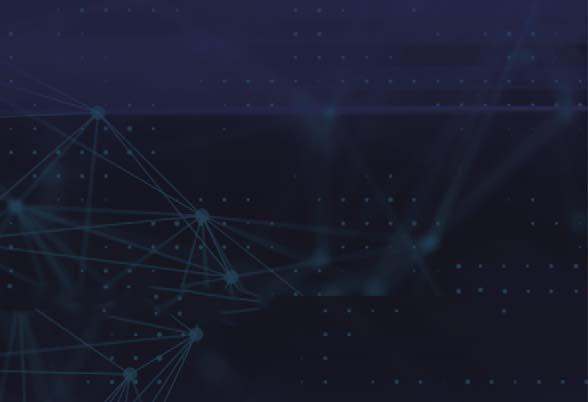
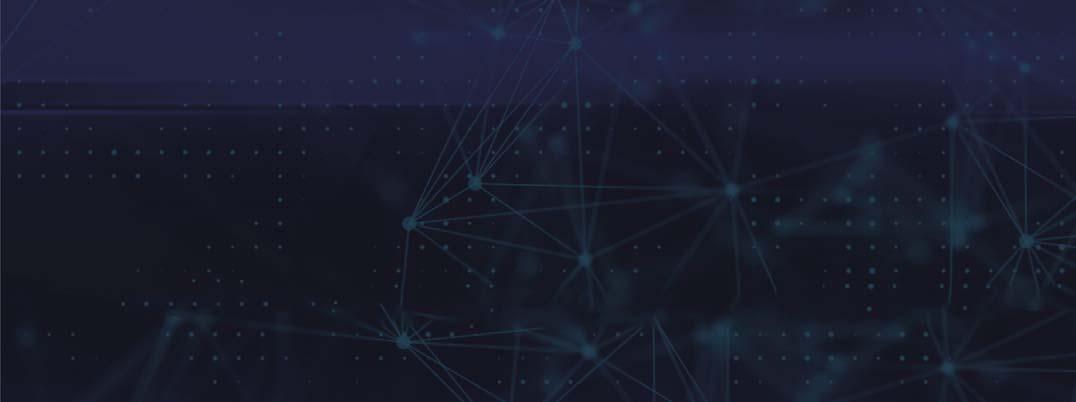
Jessy Parmar, Xylem Industrial Solutions,
Americas, explores how smart technologies can support effi cient and automated mine dewatering.

Many years of experience working with customers across all aspects of mine water management has shown that achieving optimal water processes begins with a holistic view of how the mining operation uses water – from sourcing to dewatering, to treatment and reuse. Every step involving water on site – from intake to reuse – is part of a process that can support increased productivity and lower costs. Time and resources spent ensuring that mine water is
managed as efficiently and sustainably as possible is well worth the investment, and the return can be clearly measured and tracked.
The golden rule of pumping systems
Dewatering is a particularly critical aspect of mine water management, as it is one of the vital processes that ensures resources can be mined efficiently and effectively. If a mine floods, production is halted, and revenue is negatively affected. Dewatering demands tough and reliable pumping equipment and a system tailored to the characteristics of the individual application. It is crucial that the right dewatering pump is selected for the job at hand. Time should be taken to consider all the different factors at play, such as where the pump will be located, the head and flow requirements, and the pressure and quantity of water to be pumped. The availability of electric power and the type of solids to be pumped should also be taken into account, as well as determining if the pump needs a backup for increased demand. A golden rule of all pumping systems, including dewatering systems, is ensuring that each pump in the system is operating as close as possible to its best efficiency point (BEP). This is the crucial first step to establishing a reliable and efficient dewatering system with minimal downtime. Straying too far from a pump’s BEP leads to premature wear, higher energy consumption, increased maintenance requirements, a reduction in overall efficiency, and, as a result, more downtime. Unplanned downtime can cost up to 10 times more than routine maintenance.
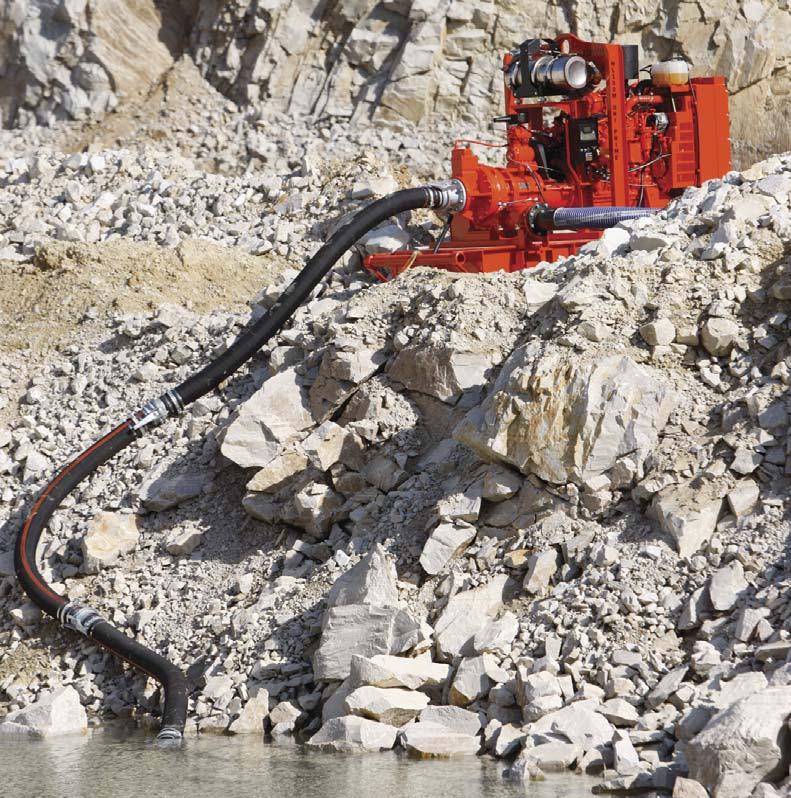
Figure 1. Sample pump performance curve. Straying too far from a pump’s best eff iciency point (BEP) reduces overall eff iciency, leads to premature wear, higher energy consumption, increased maintenance requirements, and, as a result, more downtime.
Figure 2. The Xylem team installed Godwin surface-mounted diesel-driven pumps operated by a remote M&C system at a large opencast copper mine in Peru. This remote dewatering solution helps control the pumps’ flow and operation in a matter of seconds and was particularly beneficial during the rainy season.
Once confident that the right pumps are in place, operating as close to the BEP as possible, it is time to consider smart technology that can enhance the efficiency of mine water management.
Smart technologies that can support efficient and reliable dewatering include the following:
Variable speed drives and controls
These help to optimise pump operations by enabling pumps to respond smoothly and efficiently to fluctuations in demand, and to reduce energy costs by as much as 70%. This minimises equipment wear and tear and unnecessary operating costs.
Adaptive mixers
Adaptive mixers can support efficient dewatering by helping to prevent pump clogging. Hard iron mixers are designed to easily handle chemically aggressive and mechanically abrasive mine slime. They deliver maximum thrust using minimal energy. Distinctive backswept propeller blades allow fibrous material to pass through, while their wide-hub design also deflects fibrous material. By keeping the liquid agitated, they prevent the media from getting too viscous and particles from collecting on the sump floor, which in turn would clog the dewatering pump.
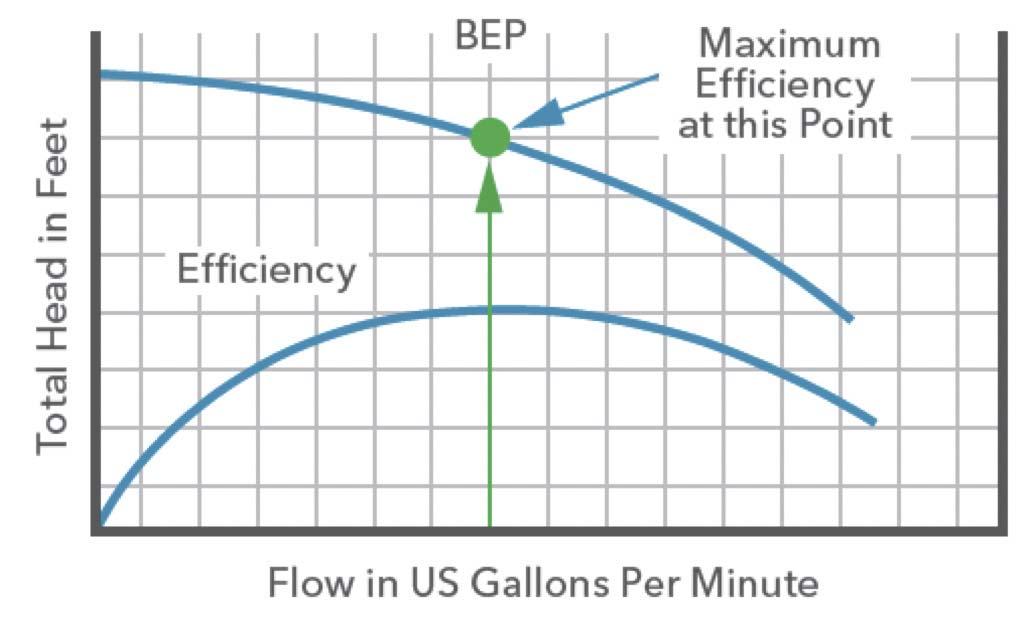
Remote monitoring and control
Monitoring and control (M&C) with real-time continuous monitoring systems give mine operators a better understanding of water use and ensures water can be extracted from multiple sources, transported, and treated at the desired pressure and quantity. They also support operational continuity and efficiency, minimising costly, unplanned maintenance and unwanted downtime, while reducing safety risks. Visibility and understanding the health of dewatering pumps, for example, enables efficient scheduled maintenance, smart inventory management, and reduced energy consumption.
Smart dewatering in action
An example of the benefits of remote M&C can be demonstrated using an application the company worked on in Peru. With the discovery of more copper and the forthcoming rainy season, a large opencast mining operation in Peru sought a smart dewatering solution. The depth of the mine – 1200 ft (365 m) below the surface – made routing power for electric-driven dewatering pumps challenging, as well as heightening safety risks; staff were required to travel down into the pit to physically handle the dewatering pumps’ controls. Explosives used to excavate deeper into the mine added to safety concerns.
Xylem’s team installed Godwin surface-mounted diesel-driven pumps operated by a remote M&C system. Connected to the mine’s supervisory control and data acquisition (SCADA) system, the M&C solution can remotely start and stop the pumps, monitor capacity and fuel levels, and communicate operating parameter data to mine staff. Mine operators can now monitor and control the pumps’ flow and operation in just a matter of seconds when the pump is approaching maximum capacity, for example, or in advance of anticipated heavy rain events.
Previously, reconfiguring pumps required retrieving the power cable and disconnecting hoses. As well as increased safety and efficiency, labour costs associated with switching pumps or running electrical power down into the mine were eliminated.
New technologies coming on stream
In addition to the wealth of smart technologies already on the market, exciting developments are unfolding. For example, Xylem has been working closely with New Boliden's RenstrÖm mine in Sweden on a pilot project as part of a process to introduce automation into its mines. New Boliden first began experimenting with digital solutions in 2012 and was the first to employ a combination of wireless networks, IP telephony and positioning at its Kristineberg mine. The New Boliden vision is of a mine where production continues non-stop, safety is maximised through remote control and monitoring, and the overall cost of operation is minimised.
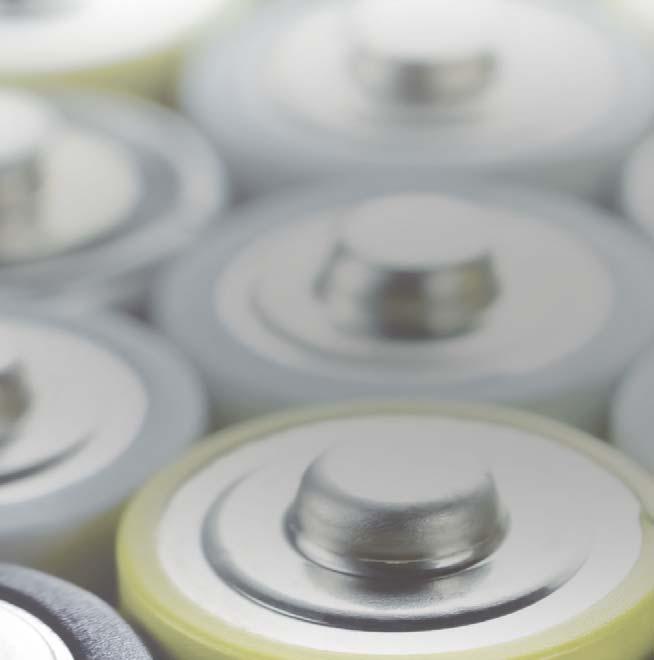
WANT TO SECURE A GREENER FUTURE WITH EFFICIENT BATTERY RECYCLING?


ASK YOUR SEPARATION SPECIALIST
Electric vehicles, smartphones, computers and many more everyday items rely on lithium batteries. And as our society continues to move towards green technologies, it is essential to ensure that these batteries are not disposed of by landfill when they reach the end of their usable life. Luckily, both the recycling process for old batteries and the process for valorization of production rejects are not exactly rocket science. For example, ANDRITZ can assist you with process know-how and proven technologies for separating the battery coating from the black mass and recovering the valuable base metals, such as lithium, cobalt, or graphite. Be it breaking down with shredders, dewatering with filter presses, peeler or pusher centrifuges, or drying with paddle, helix or plate dryers – with our broad portfolio and comprehensive experience, we can offer you a turnkeysolution that will make your old batteries a valuable commodity again and protect the environment at the same time. Contact us today – we are happy to help.
Xylem provided a next generation dewatering pump that utilises digital intelligence beyond standard pumping solutions: the Flygt Biboα. The fully automated dewatering pump shares the same platform of integrated power electronics as Xylem’s Flygt Concertor, an intelligent wastewater pump. Compact and stable, the solution breaks the mould of traditional dewatering pumps with its robust design, built with 30% fewer components for a more stable operation, and reduced need for inventory.
With built in intelligence, the pump will cover a range of traditional drainage pumps since it adapts speed and performance covering a field instead of a static curve. The pump’s fully embedded variable frequency drive (VFD) automatically controls the motor’s speed and rotation, without any hands-on intervention or configuration by the operator.
Snoring is also a common problem in typical dewatering practices, causing significant system wear over time as the pump continues to operate at full-speed without enough water inflow. Flygt Biboα's advanced technology optimises pumping and overall performance, and, by only pumping when needed, it eliminates snoring to significantly extend the lifetime of the pump and reduce service time and maintenance costs.
The company’s submersible dewatering pump can adjust itself to the water inflow – its optimum performance is determined in direct response to its operating environment. When water starts to enter the sump, the pump will speed up, and it will continue to increase its speed until the water level is low again. By letting the pump run continuously, there is no need for any additional sensor – the incoming water triggers the pump to start, so it will always be ready to respond to changeable conditions in the field. As the pump constantly adapts to its environment, each 10 hp (7.4 kW) pump can cover an equivalent range up to 15 hp (10 kW), enabling greater flexibility and allowing standardisation to fewer pump models. This flexibility is paramount to a mine like Renström, which is constantly adapting and evolving its operations to meet operational requirements. Previously, operators at Renström would have to change to a different pump model every other shift, due to the variable duty points created across the different pumping stages as the mine expanded. The prototypes have developed the way dewatering processes are carried out at the mine. Due to the adaptive capabilities of the pump, operational wear at the mine has been reduced by 80%, leading to less pump downtime and disruptions to production. In addition, maintenance costs as a result of service call-outs have been reduced, with the mine experiencing periods of trouble-free pumping up to four times longer when compared to traditional pumps, representing a cost saving of 20%/y. Fleet management at the mine has also been simplified, as the pump can handle a wide range of applications, limiting the need for pumps of different sizes and parts on site. After 3 years of field testing at Renström, the solution has delivered product and repair savings of up to 40%, while also reducing the cost of its dewatering processes at the mine by almost 30%.
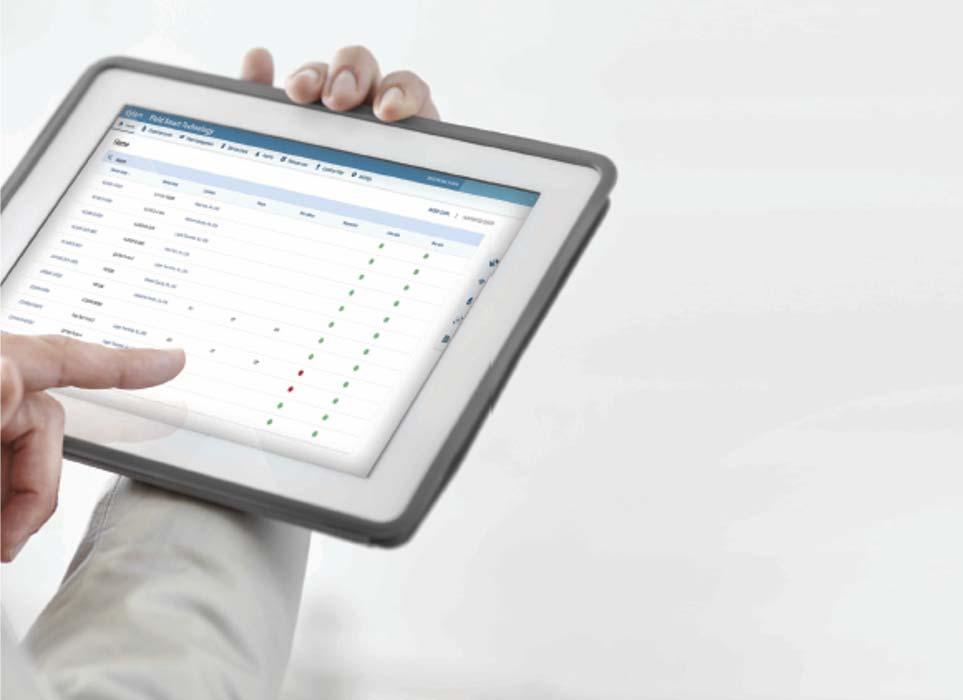
Figure 3. Xylem’s remote M&C solutions support operational continuity and eff iciency, minimising costly, unplanned maintenance and unwanted downtime, while reducing safety risks. Visibility and understanding the health of dewatering pumps, for example, enables eff icient scheduled maintenance, smart inventory management, and reduced energy consumption. Figure 4. Flygt Biboα prototypes have developed the way dewatering processes are carried out at New Boliden’s Renström mine in Sweden. Aft er 3 years of field testing at Renström, Xylem’s Flygt Biboα has delivered product and repair savings of up to 40%, while also reducing the cost of its dewatering processes at the mine by almost 30%.
Conclusion
With exciting technical solutions coming to market, the future looks bright. Now is the time to embrace digital technologies and get smart about mine dewatering. Doing so will enhance not only reliability and sustainability but ultimately, productivity on site.
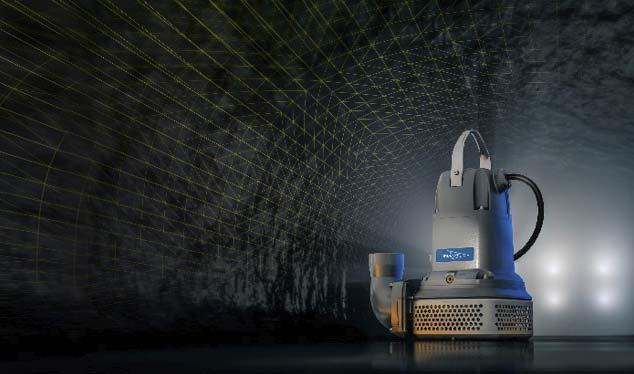