
8 minute read
Decisions, Decisions
Fabio Mielli, Rockwell Automation, USA, discusses how autonomous decision-making for material handling can help mining operations meet productivity, quality, schedule compliance, and cost-savings goals.
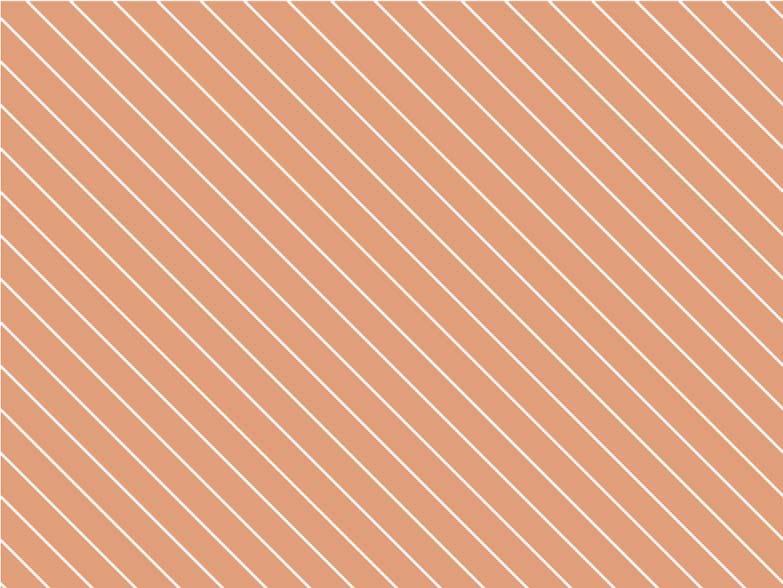

Material handling equipment is a critical part of any supply chain – and it is especially critical in the mining industry. Material handling equipment coordinates the movement, storage, blending, and delivery of materials across the mine site – serving as the link between a mine site and the market.
While all industries must coordinate logistical planning, equipment maintenance, operator performance, and production scheduling for successful material handling in some shape or form, material handling challenges in mining are more complex.
Mining companies face unique challenges when seeking to ship the right product at the right time. Unscheduled equipment relocation, a lack of process standardisation, and operator variability can all lead to consequential costs through the supply chain.
Miners are working with large equipment that transports massive amounts of materials over long distances – sometimes several kilometres – which means a problem upstream will reverberate across the site and down the supply chain. This can lead to backlogs, downtime, spillage, and major delays. So, the right execution plan for material movement is incredibly important. No mining company is immune to these challenges, but for many, reducing complexity as much as possible can provide a more consistent ability to get the right product out the door at the right time.
In addition, material handling on mine sites poses safety risks to workers. The Centers for Disease Control and Prevention (CDC) reports that material handling is the leading cause of non-fatal days lost injuries in mining – with the bulk of these injuries stemming from above-ground movement of coal, stone, and metal.1 Automating material handling wherever possible, shift ing workers to a safe distance to operate equipment, and becoming more proactive with equipment maintenance can make a big diff erence.
The risk for production issues and injuries increases at sites that perform complex material transfer without a fully automated system in place. At these sites, operators are oft en overwhelmed with responding to inputs from multiple interfaces, while simultaneously coordinating the flow of work. Even with the best trained operators, companies are susceptible to unscheduled delays, spillage, and a lack of standardisation due to operator variability and miscommunication.


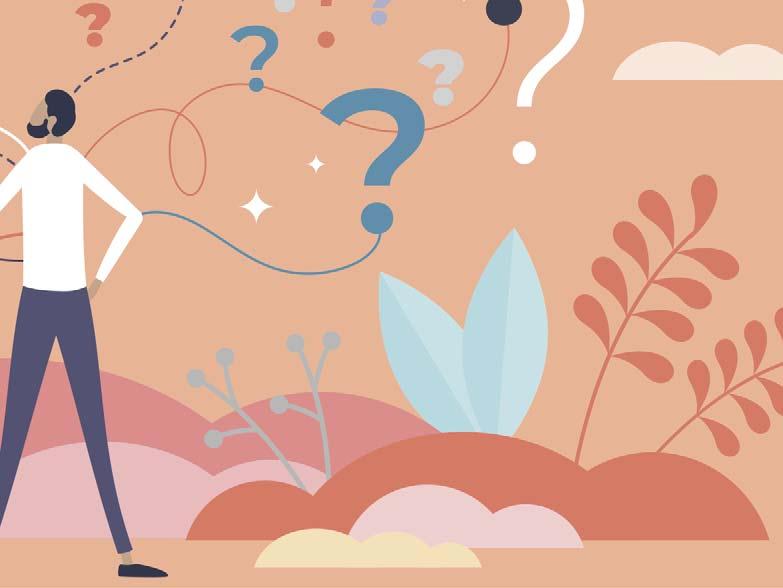

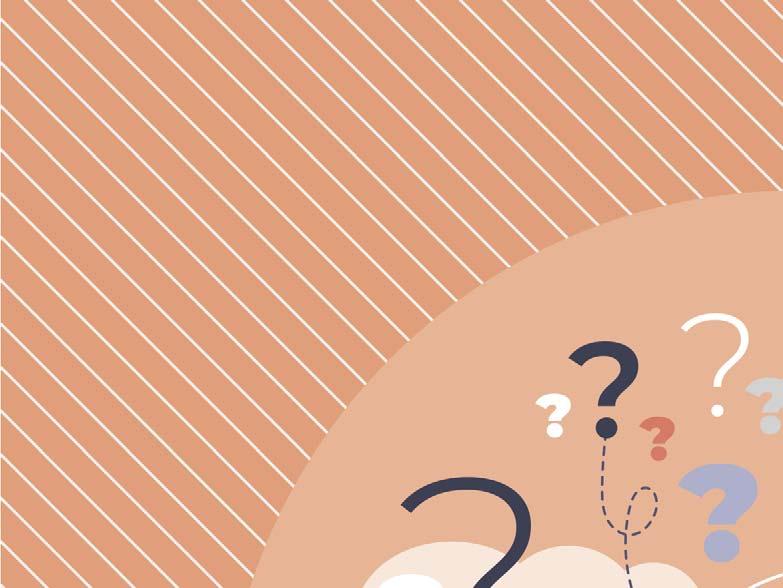
A day at the train load system
Issues oft en come to a head at the load controller. The load controller is the central hub for plant operations, which means that during the busiest parts of the day, train load system (TLO) operators may find themselves working in multiple systems simultaneously, as they seek to remedy several issues at the same time. Each of these systems requires a manual response to every single issue and event, which leads to a lot of variability in operator decision-making and ineff icient use of operator time. Eff ectiveness becomes heavily dependent on an operator’s personal capability, experience, and training.
Compound this by the fact that during busy moments, TLO operators oft en face an overload of alarm information without clear prioritisation of which alerts are most pressing. It is up to the operator to make a call – and even the best operator can easily become overwhelmed and make a mistake. The most common result is equipment not being in the right place at the right time to load a train or ship. Every minute of delay costs the company money and causes further issues down the supply chain.
This reactive means of operation prevents operators from ever getting a proper handle on what is actually happening, and the opportunity for analysing ‘what if’ scenarios thoroughly becomes nearly impossible.
Moving in the right direction How it works
A major mining customer wanted to lower their operating costs by ensuring the material was shipped according to the set schedule, setting out to overcome the challenges that exist for the train loading operation. The solution was decision automation (execution management) for material handling based on FactoryTalk® ProductionCentre® and Logix Controllers. Other industries have benefited from automated execution management systems for years. It was time to take some of those learnings and apply them to the TLO.
The solution coordinates the resources in the customer’s mine. It automates the orchestration of the equipment decision-making process by integrating with the site’s job management system (in this case from the ERP system) to automatically convert a job into a list of all the tasks and equipment needed to correctly execute the job.
The solution then integrates with existing control systems to align the pieces of equipment needed to complete the job. Once the existing control system permissives for the route and equipment are enabled, the stacking/reclaiming job automatically begins. There is no need for an operator to plan or kick off the job. The solution will also continuously update the stockpile inventory management system, as well as the job management system, on the job progress.
Once the job has been completed, the solution will automatically relocate the equipment to the correct position for the next job. This means no surprises. All elements of a job are planned and accounted for before the job initiates. Timing is locked in, and equipment is in position for the next job on time. All of this is done automatically, so that operators can focus on issues that require critical thinking. It also means workers are less distracted and overwhelmed, which leads to fewer accidents.
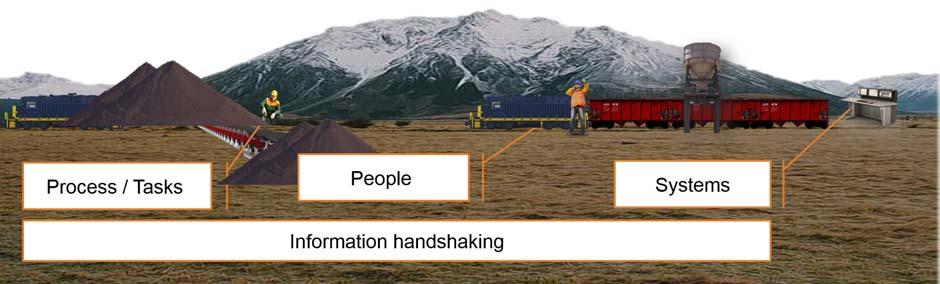
The solution consists of two main components. First, the production management system (based on FactoryTalk ProductionCentre) defines the job number, job quantity, and type of material. Second, the real-time execution management (REM) – based on Logix Controllers – behaves like the interface between the field and the production layers by ‘feeding’ the production management system with information about the start or completion of a job, measurements of materials needed, and measurements of material produced. In addition, the REM commands and orchestrates the automation system from each area, ensuring that all the operations will successfully complete the job.
Figure 1. Autonomous decision making simplified architecture: train loadout. Production management system:
Integrates schedule and control systems (from any vendor). Models material flow paths, work centres, equipment, and process segments. Integrates rail and port systems. Pending train/ship arrivals, orchestrates a plan to be ‘read’ to load/dispatch.
Figure 2. Stockyard management is usually a complex coordination of people, processes, and systems. Real-time execution management:
Contains sets of tools for managing a job, such as: handshaking, process parameters (e.g. material
FIFO), workflows, and tracking the progress of a job. Each work centre (e.g. stacker reclaimer, TLO) has a workflow,

which is a sequence responsible for issuing commands and receive responses between the existing plant.
Case study
Here is an example of what a job looks like from start to finish:
Step 1: Create job (e.g. reclaim 10 000 t)
REM receives job from production management system.
Break down steps and contextualise job (resources, materials, and parameters). Job context downloaded to control system (job available and ready for execution).
Step 3: Control system requests start of job
REM responds with details about how the job should be executed (ingredients, process, and engineering parameters). REM locks resources and hands over control of execution to control system.
Step 4: Control system executes job
Control systems notifies REM of job progress.
Step 5: Control system completes job
Control system notifies REM of job completion. REM releases resources.
Maximising asset return on investment
For this mining company, implementation was easy – the execution management solution integrated with the existing control system, so all the existing control and safety systems remained in place. Once installed, the benefits of the implementation exceeded the company’s expectations. Improvements to conformance scheduling were seen immediately based on a standardisation of the most eff icient operational processes for the site. The customer also saw a reduction in the workload and dependency on the operators, as well as reduced unscheduled process delays. This solution resulted in an annual saving of US$200million for the company. The customer is currently investigating the possibility of rolling this solution out at additional sites.
Conclusion
Production management and real-time execution management have obvious applications in the TLO, but they can also bring business value to other parts of the operation as well. Solutions can be deployed at a single site or at multiple sites – helping miners meet a range of productivity, quality, compliance, and cost-saving goals.
References
1. ‘Mining Topic: Manual Materials Handling’, CDC, https://www.cdc.gov/ niosh/mining/topics/manualmaterialshandling.html
REGISTRATIONS NOW OPEN
Perth, Australia and online | 8 – 10 November
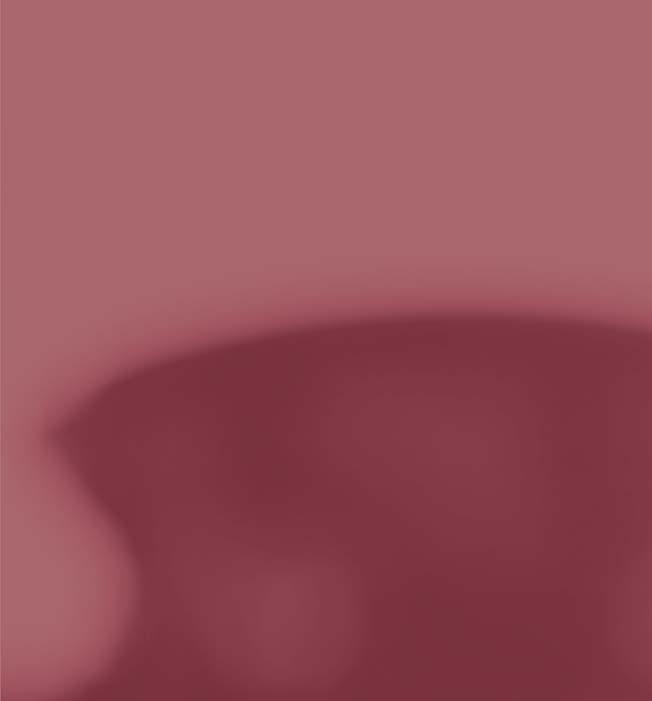
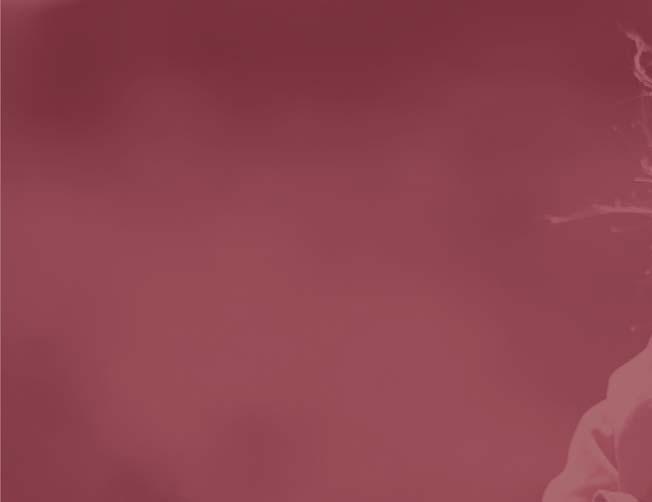
Hosted by AusIMM and CSIRO, the Iron Ore Conference 2021 will explore current and future challenges facing the iron ore industry and offer sustainable solutions to address the carbon footprint of iron and steel mining. Hear from industry experts from some of the world’s top mining companies and steel producers, including Dr Koji Saito, Nippon Steel Corporation; Gerard Danckert, Rio Tinto and Alison Terry, Fortescue Metals Group. Delegates can join robust discussions, see the latest innovations at the full trade exhibition and virtual booths and connect with over 600 industry professionals.
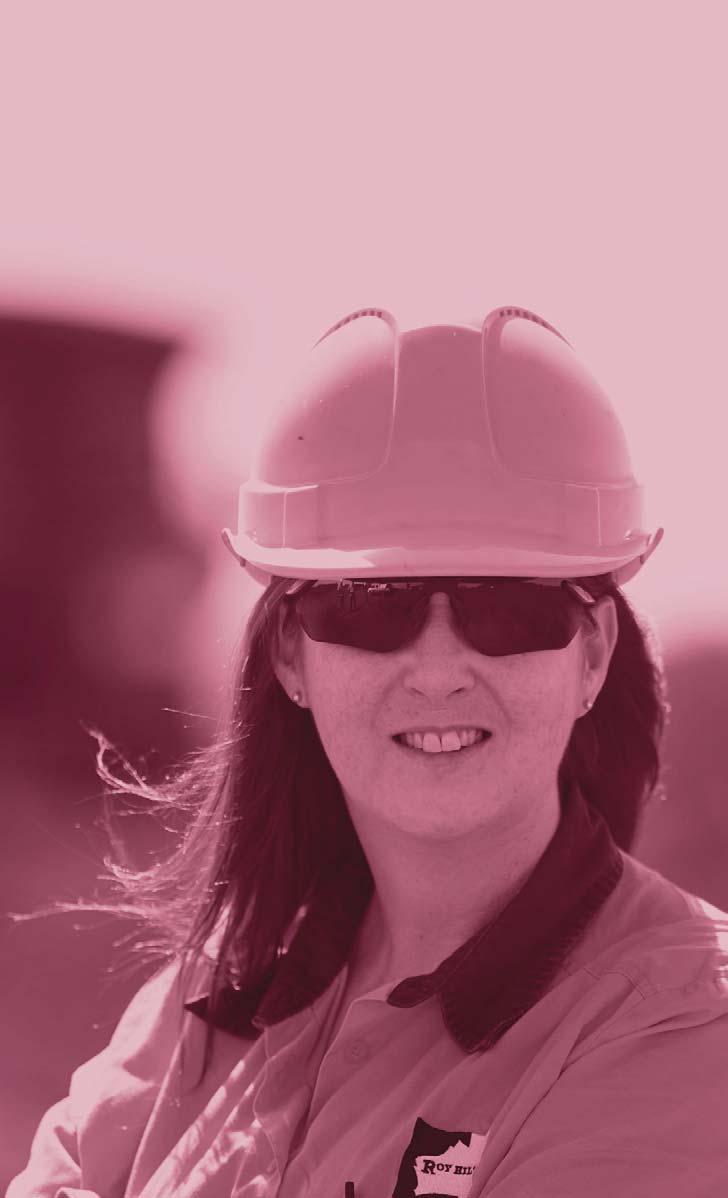