
6 minute read
Smooth operator

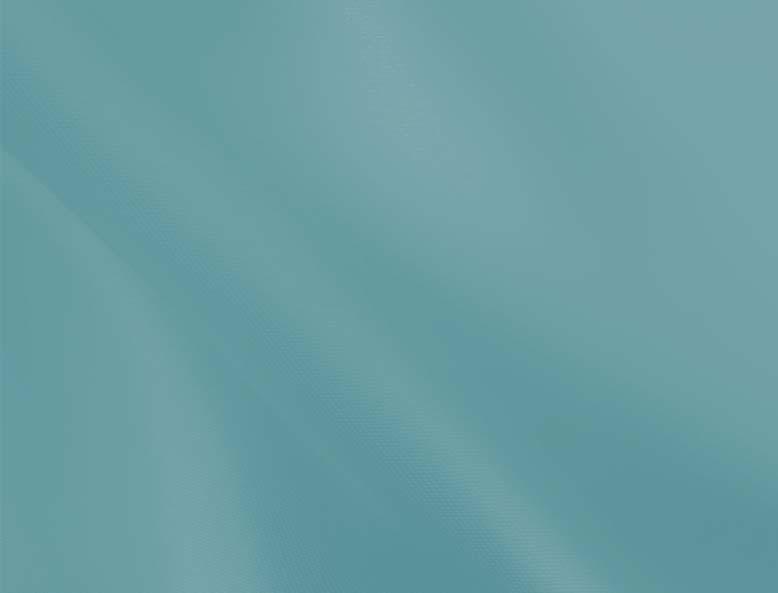
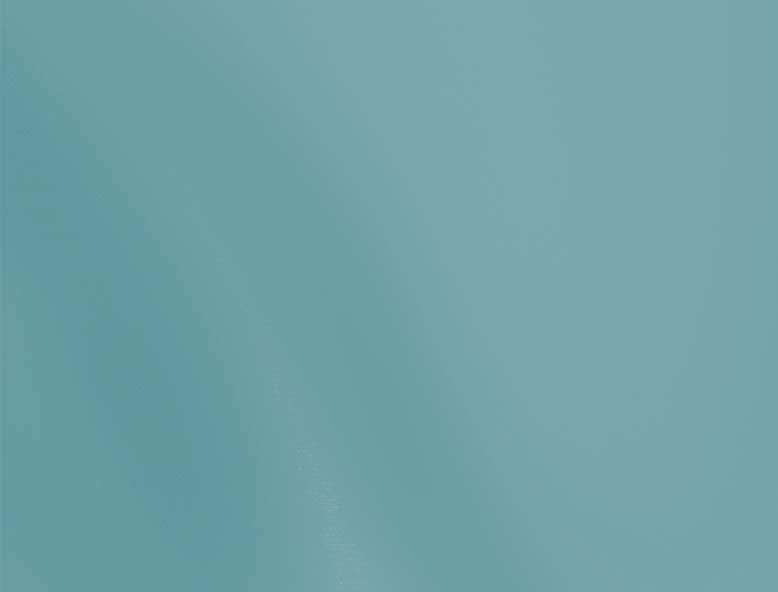
Joshua James, Liquip, Australia, provides maintenance tips and advice to ensure smooth operation during loading operations.
To reduce downtime and ensure continual smooth operations at each terminal, it is vital to implement and follow a regimented equipment maintenance programme. For instance, API couplers and loading arms provide a critical connection between the tanker and terminal, and it is not unusual for API couplers to experience in excess of 50 connections in a single day. By looking out for and addressing the following areas within their existing maintenance schedules, terminals can ensure their equipment is cared for and will continue to provide the utmost safety, reliability and performance:
Seal selection
As the temperature fl uctuates in warm or cold climates, and depending on which products and additives fl ow through the loading arms, it is crucial to use the right product seals for the job. Using incorrect seals may cause the coupler and loading arm seals to become compromised, leading to product leaks. There are a wide variety of product seals available on the market ranging from seals designed to handle typical loading of fuels to those designed to handle ultra-low temperatures and even some harsh chemicals. To determine which seals are best suited to an application, an API coupler manufacturer should be contacted.
Seal wear
A coupler performs a high number of connections each day which can cause seals to wear over time. Worn seals may cause minor leaks during loading or after the coupler has been disconnected from the truck API adaptor. This is usually an indication that the product (nose) seal, or one of the other seals such as the poppet adaptor O-ring or bush and O-ring, are due for replacement. Terminal operators should inspect couplers on a regular basis and
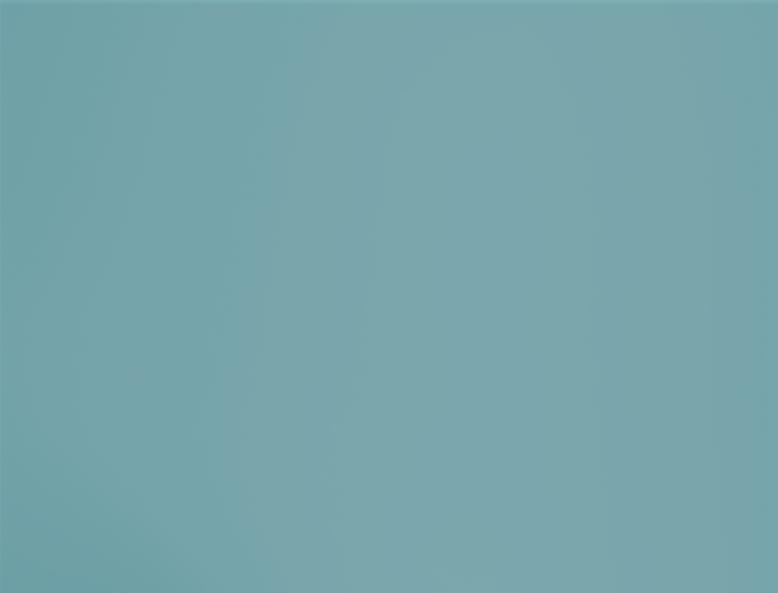



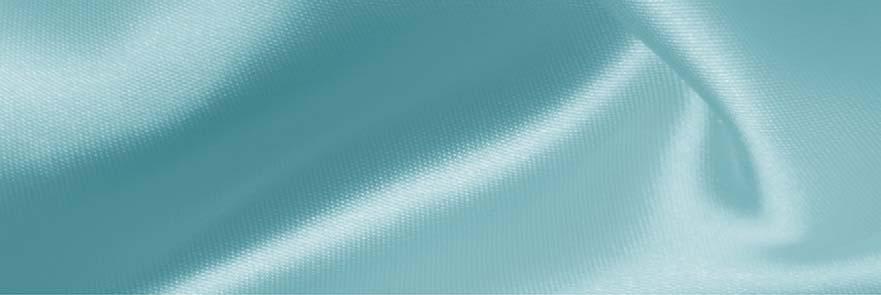
changeout any seals at the fi rst sign of wear. To assist with seal changeouts, Liquip, OPW and other manufacturers can provide detailed changeout procedures.
Safety interlocks
API couplers are fi tted with safety interlocks whereby the coupler cannot be opened until it is fully latched on to an API truck adaptor and it cannot be disconnected until the API coupler has been closed. During maintenance, the latching function of a coupler should always be checked to continue trouble-free operation.
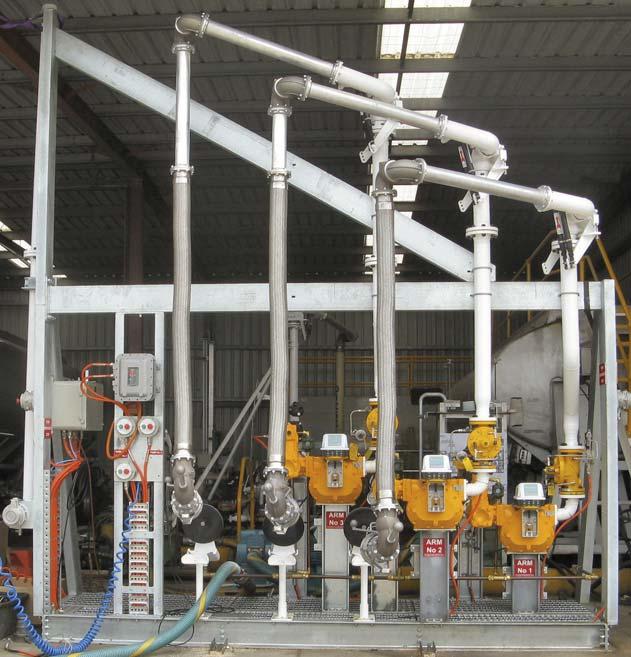
Figure 1. Three-arm bottom loading skid configuration using gas strut loading arms.
Figure 2. The LYNX API bottom loading coupler shown in a typical loading configuration.
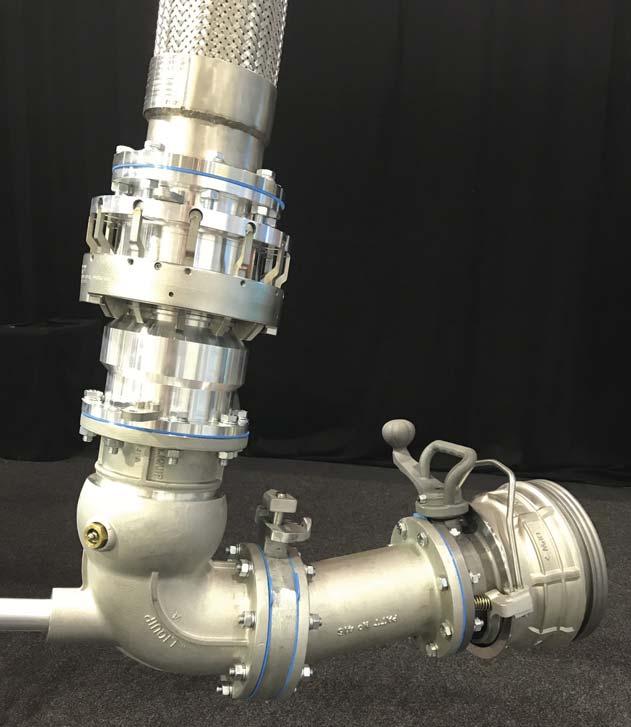
Dirt build up on latches
API couplers come into contact with a number of different vehicles each day and during this process dirt and other debris can build up on the API coupler latches. If too much dirt builds up on the latches, it may create a fl awed seal and might prevent the coupler from latching correctly to the truck adaptor. Operators should regularly inspect and remove dirt and debris from coupler latches.
Latch wear
As a result of the large number of connections API couplers experience with truck adaptors, latches may wear over time. It is important for operators to check that all latches operate correctly when conducting routine maintenance. To assist operators in determining latch wear, API-LI gauges have been developed that allow operators to quickly and effectively measure the latching capability of API couplers.
Loading arms adjustment
Over time the balance mechanism of all loading arms, whether compression, torsion spring or gas strut style, will droop and could lead to the loading coupler sitting just outside of the API envelope (based on API RP 1004). This could result in a coupler position that is too low to ergonomically operate or connect to the tanker.
If the loading coupler is no longer in its most optimum loading position, operators will need to increase or decrease upward force to adjust the loading arm. It is important to remember that the horizontal spool must always be suitably supported before commencing any adjustments to the arm. When it comes to gas strut operated arms, adjustments are easily completed by turning the nut on the adjustor bracket. A successful adjustment will allow the coupler to be easily manoeuvred within the API envelope.
Loading arms clashing with obstructions
The up/down stops can be used to allow the loading arm to move freely without clashing into any nearby obstructions. During maintenance, it is good practice to check that the horizontal arm is parallel to ground and to adjust it as needed, as this will ensure the maximum vertical movement of the arm.
To simplify terminal operations, many bottom loading equipment manufacturers have developed advanced technologies to address the above areas and improve bottom loading operations. Liquip’s LYNX API coupler and 'Velvet Touch' LBM gas strut loading arms are just one example of this. When used together, these technologies create an effective bottom loading process.
The LYNX seal design of the coupler allows for increased site safety and minimal product leakage during disconnect.
Four ‘true interlocking’ stainless steel latches ensure good automatic latching and maximum product
containment during delivery. The coupler can be quickly disassembled through a U-Pin design, while the main seals can quickly be replaced, on or off the arm.
The coupler, which has a typical coupler pressure of 80 psi (5.5 bar/550 kPa) and a maximum surge pressure of 493 psi (34 bar/3400 kPa), also has a 150 – 200 mm handle with a positive lock.
Liquip’s LBM 800 gas strut balance mechanism has 360° rotation in the horizontal plane, allowing it to easily move from a parked to loading position and, in some applications, to service vehicles on either side of the loading bay.
It can be easily configured to suit different styles of loading arms including low profile loading and unloading, A-frame bottom loading, and Pantograph and long reach top loading arms.
The LBM mechanism has a slim line drop leg bracket, which provides easy and out of the way installation, and can be easily adjusted through a heavy-duty adjustment mechanism.
The LYNX API coupler and the LBM800 balance mechanism coupler can be equipped with seals to handle various products and temperatures ranging from -40°C to +90°C.
Figure 3. Components of the LYNX API bottom loading coupler.
Conclusion
The millions of litres of fuel that pass through a storage terminal every year would have nowhere to go without API couplers. Therefore, their design and reliability must be second to none if a terminal is to feature a truly efficient loading-rack operation. By incorporating the above tips into terminal maintenance regimes, loading equipment will continue to provide safe and reliable performance.


YOUR ADVANTAGES WITH FLOTTWEG TECHNOLOGY FOR OIL RECOVERY FROM RESIDUALS DURING TANK CLEANING
· Reusing the recovered oil as a valuable product · Reduction in the quantity of sludge in the closed system · Low personnel costs because of automatic operation · Significant saving in operating and disposal costs · Explosion-proof and safe process
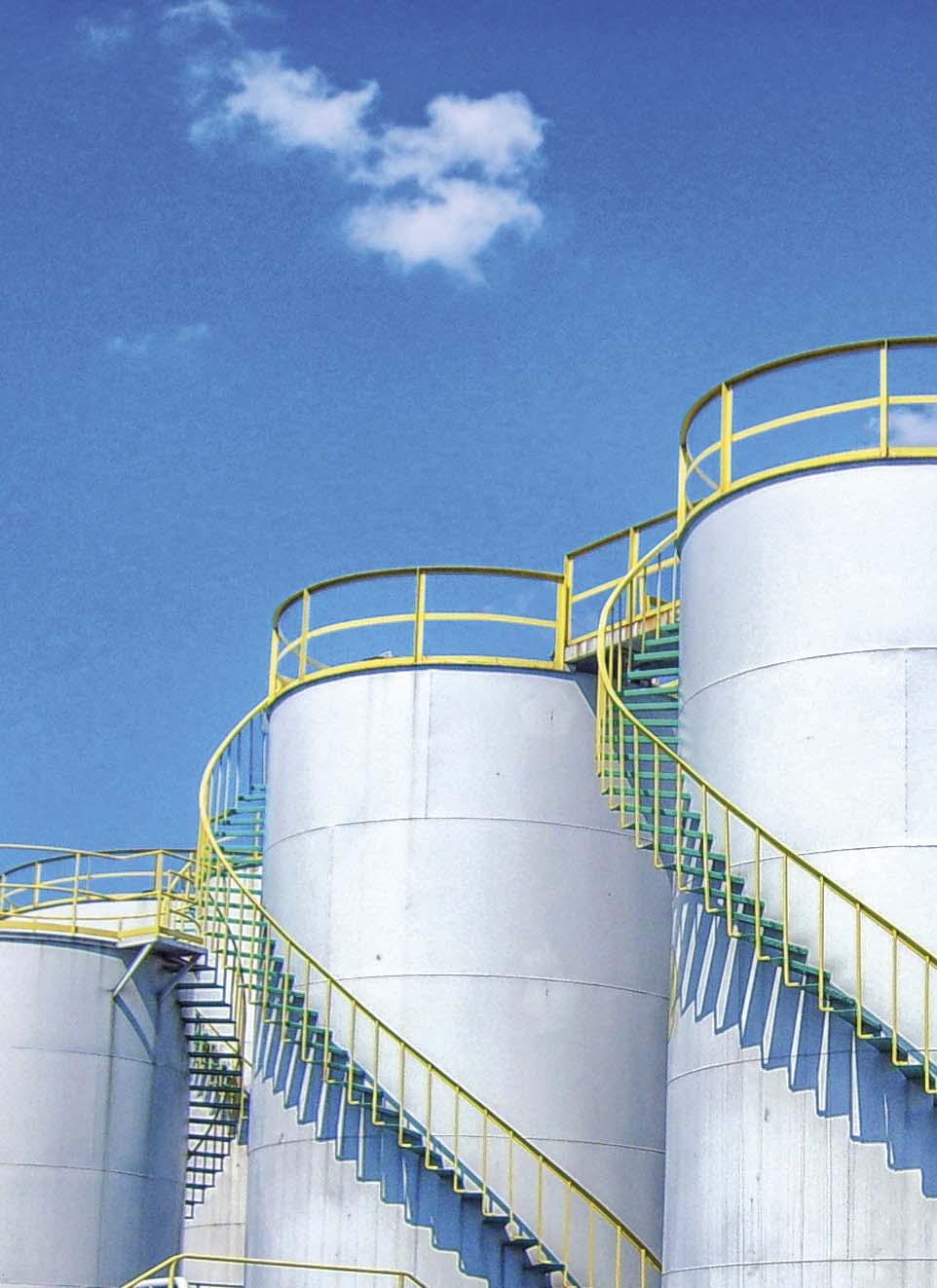
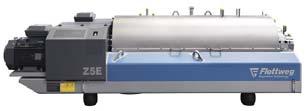