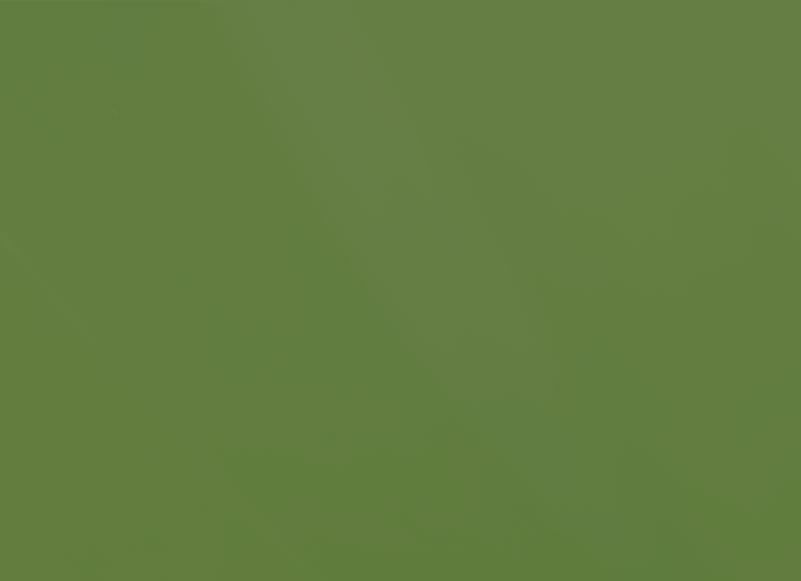
12 minute read
Green SRU in biofuels
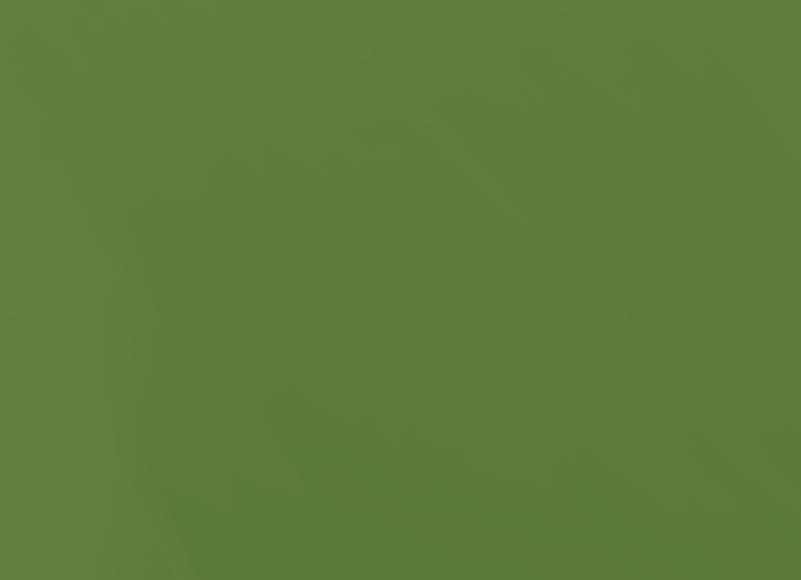
Jan Klok, Desirée de Haan, Joost Timmerman and Rieks de Rink, Paqell B.V., the Netherlands, outline a number of differentiators that make biological desulfurisation suitable for the rising biofuels market.
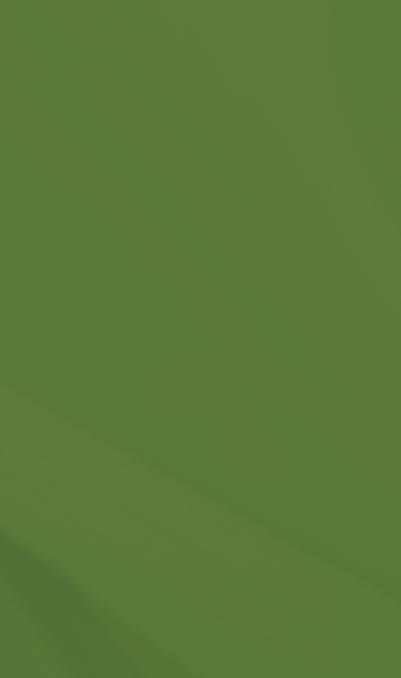
In 2015, 196 countries signed the Paris Agreement, an international treaty with the goal of limiting global warming to well below 2°C. To achieve this, countries have set net-zero greenhouse gas emissions targets that involve both emissions abatement and reduction.
Production of biofuels, e.g. fuel produced from biomass through contemporary processes, is undergoing a tremendous expansion with new biofuel projects being executed.1 When hydrogen sulfi de (H2S) is formed during the production of biofuels, desulfurisation is required to control the emission of sulfur compounds. For projects with a high sulfur load, i.e. >100 tpd of sulfur, the combination of the amine and Claus process is the most cost-effective desulfurisation line-up.
However, for gas streams with intermediate and low sulfur loads (e.g. up to 20 tpd of sulfur), several commercial technologies are available.
The sulfur load of a typical biofuel project is in this range. In addition, the off-gases associated with biofuel production typically have a very unfavourable CO2/H2S ratio. Therefore, the traditional Claus technology is not a suitable desulfurisation process for biofuel projects. Besides the economics (i.e. OPEX and CAPEX), other project specifi c requirements determine which technology is most suitable to apply. For example, fl exibility, project timeline and CO2 footprint are often important considerations in the selection of the most adequate desulfurisation technology.2 The concept defi nition is known to be crucial for successful project development. Recently, several biofuel projects located in the US, Europe, and Asia, selected the Thiopaq O&G (TOG) biological desulfurisation process. This article discusses essential differentiators of this technology to highlight its suitability for sulfur recovery units (SRUs) in biofuel projects.
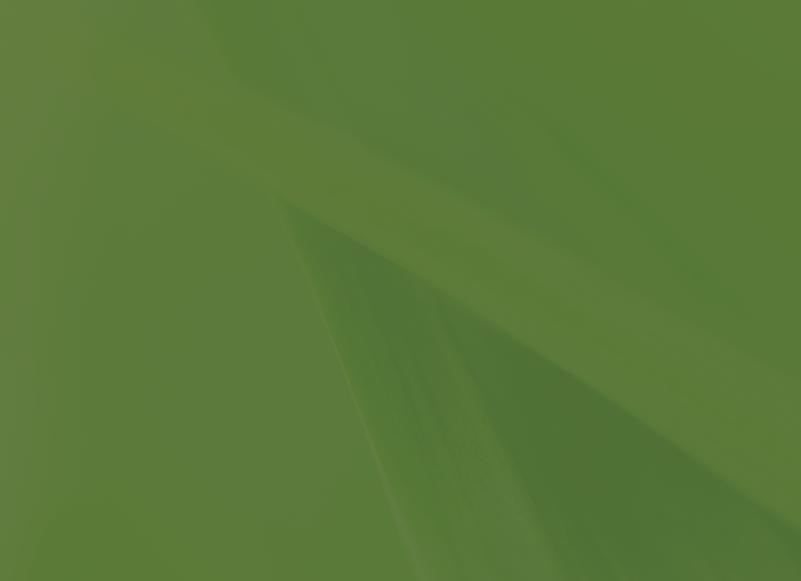
The technology
Thiopaq is a biological desulfurisation process that uses naturally occurring bacteria to oxidise H2S to biological elemental sulfur. The process has its origins in biogas treatment and more than
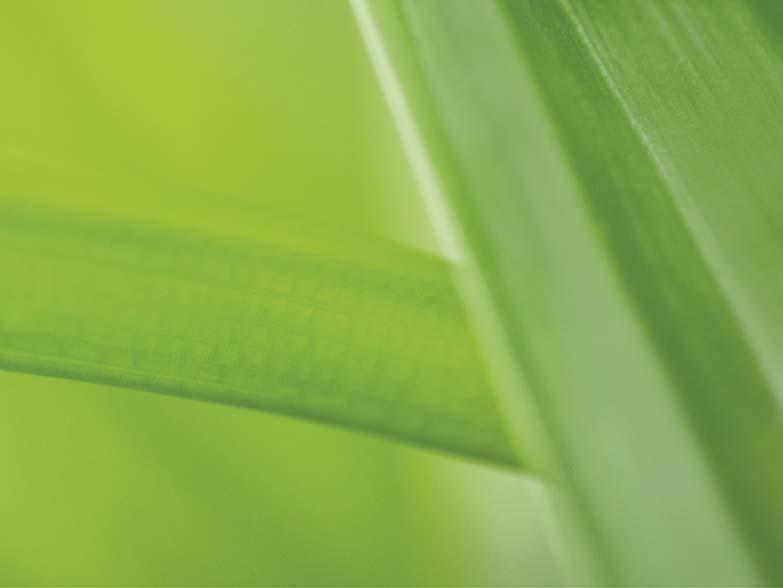
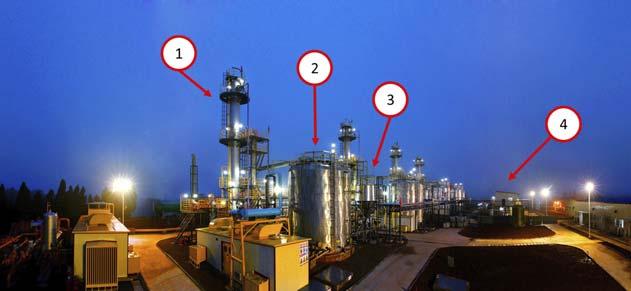
Figure 1. A Thiopaq O&G facility treating high pressure (60 barg) natural gas in four lines. Each line is designed to treat 5.4 tpd of sulfur. The TOG consists of three steps. 1: H2S removal in an absorber, 2: solution regeneration in a bioreactor, and 3: sulfur dewatering section using a settler for sulfur settling (3) and decanter-centrifuges, which are typically placed in a separate building (4).
Figure 2. Scanning electron microscopy picture of produced biosulfur from a TOG. Biologically formed sulfur particles have a bipyramidal shape. Due to the relatively small particle size and hydrophilicity of the biologically produced elemental sulfur, the process solution does not require the addition of chemicals to stabilise the sulfur.
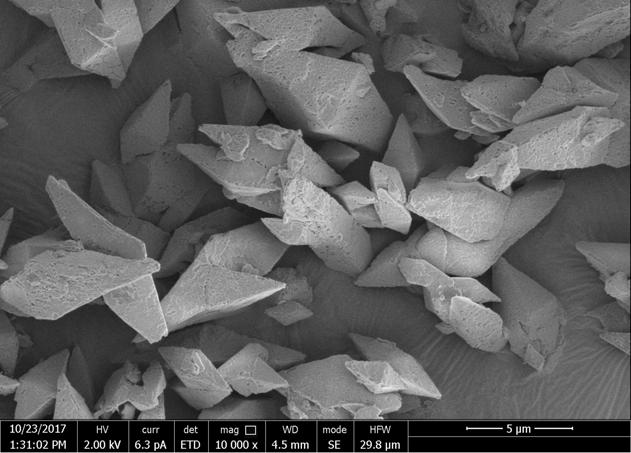
270 units have been installed worldwide.3 The process was introduced to the oil and gas industry in 2002 and is currently marketed under the name Thiopaq O&G (TOG).
The traditional biotechnological desulfurisation process consists of three simple, integrated steps: absorption, solution regeneration, and sulfur recovery (see Figure 1). The process starts by absorbing H2S into the process solution, thereby forming dissolved sulfi de which consumes the alkalinity of the process solution. The treated gas leaving the absorber column (containing <25 ppmv H2S) can be further processed. If needed, TOG can guarantee <4 ppmv H2S. The sulfi de-rich process solution is mixed with air in the bioreactor where bacteria oxidise the dissolved sulfi de to elemental sulfur (see Figure 2). This regenerates the process solution as alkalinity is restored. A slipstream of the process solution is directed to the sulfur recovery section. The sulfur is dewatered, yielding a sulfur cake of approximately 65 wt% solids. The fi ltrate is recycled back to the system. Caustic, make-up water and nutrients are supplied to control the alkalinity, salinity and biomass concentration of the process solution.
Based on lessons learned from operating plants, a new process line-up has been developed: the TOG Ultra. This process has a considerably higher conversion effi ciency of sulfi de to sulfur. It uses a more active biocatalyst, leading to a doubled bioreactor effi ciency, and allowing for a smaller bioreactor. Furthermore, due to improvements in process conditions, the absorbed hydrogen sulfi de is oxidised more effectively, leading to lower caustic consumption and make-up water. The optimised process conditions are the result of the implementation of an extra bioreactor between the absorber and the aerated bioreactor. The new line-up brings a further benefi t of improved operational stability and improved settling of the produced bio-sulfur, resulting in easier separation in the sulfur recovery section.4 While the fi rst TOG Ultra has been sold in Iraq in 2018, several others are currently under construction in Europe and Asia.
Process economics
Next to technical feasibility, a main driver for process selection is the process economics. As SRU selection is case specifi c, e.g. gas composition, fl ow, sulfur load and site requirements, extensive techno-economic studies have been performed.4, 5, 6, 7 As a fi rst rule of thumb, TOG is economically attractive for gas streams with a sulfur load between 50 kg/d of sulfur up to 150 tpd of sulfur. At the lower end of the sulfur load spectrum (<50 kg/d of sulfur), non-regenerable scavengers are typically more cost-effective. At the higher end of the sulfur load, the cost-effectiveness depends on the nature of the feed gas. For example, the cost-effectiveness of TOG (Ultra) increases at higher and thus more challenging CO2/H2S ratios. Typically, the production of biofuels is associated with effl uent gas streams containing these higher CO2/H2S ratios.
TOG is also applied for direct treatment of natural gas streams.5, 8 For these gas streams, the general scheme of AGRU-SRU-TGT line-up can be replaced with TOG, resulting in: Less equipment. No requirement for burners and reboilers. Regeneration and sulfur recovery sections are operated at atmospheric pressure and ambient temperature.
Examples of direct treatment of natural gas streams with TOG are shown in Figures 1 and 3. When the natural gas requires CO2 removal, a sweetening unit (AGRU) is required upstream of the TOG. In these cases, the technology is particularly cost-effective for lean acid gases (i.e. H2S concentrations <20%) up to 70 – 150 tpd of sulfur. To treat lean acid gas streams with the Claus process, one or more enrichment steps are required, which severely impacts the economics and operability.6 However, the technology might still be cost-effective for rich acid gas (i.e. without the need of an enrichment step).4
Other typical gas streams with challenging CO2/H2S concentrations are Claus tail gas streams. H2S removal with conventional tail gas treatment technologies is very energy consuming. While the Claus process produces valuable steam that can be reused in other parts of the plant, it has been shown that the energy used by a TGTU to achieve World Bank
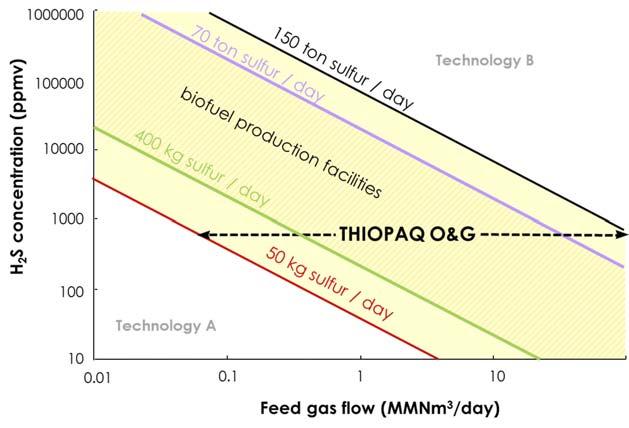
Figure 3. The economical envelope based on sulfur load: the project sulfur loads where TOG economics are favourable compared to other technologies. At the lower end of the sulfur load spectrum (<50 kg/d of sulfur, indicated by the red line), technology A is typically more cost-effective, whilst for very high sulfur loads (>150 tpd of sulfur, indicated by the black line) technology B is most feasible. The area between the green and purple line marks the sulfur load that is representative for biofuel production facilities. At the higher end of the sulfur load, cost-effectiveness depends on the feed gas composition. The more challenging CO2/H2S feed gas ratio, the more favourable a TOG as SRU is.
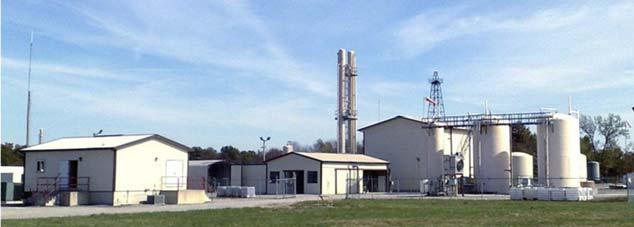
Figure 4. A Thiopaq O&G facility in the US, designed for 1.5 tpd of sulfur. The facility treats associated gas, required to produce LNG. The overall facility pay-back time was in the order of 2.5 – 3 years.8
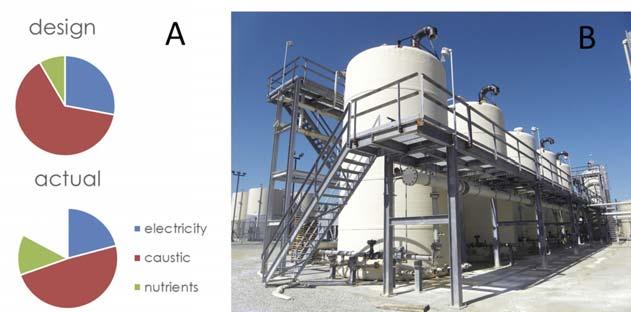
Figure 5. A: comparison of consumable costs between design criteria of consumptions per t of sulfur and actual data under turndown conditions collected over a year of operation.11 B: flexible design of the TOG facility with two absorbers (not visible in the picture), five road-transportable bioreactors, and pumps mounted on skids. standard sulfur emission limits results in a net energy consumption.9 Alternatively, the THIOPAQ process always achieves <25 ppmv H2S, making it suitable to reach even the strictest sulfur emission specifi cations. As such, it is suitable in revamp cases where tight SO2 emissions standards are being introduced. In addition, it is also a suitable technology for greenfi eld applications.10
Process flexibility and fast track construction
A unique aspect of the technology is its catalyst – a mixture of different species of sulfi de-oxidising bacteria. These organisms are naturally occurring and use the released energy from the oxidation of sulfi de to elemental sulfur to multiply themselves. The use of a biocatalyst has several advantages over traditional catalysts, since traditional catalyst is subjected to degradation, and hence continuous replenishment is required, and the catalyst in the biological process is not affected by turndown, i.e. less sulfi de entering the system will typically result in lower growth rates but still guarantees the complete oxidation of all captured hydrogen sulfi de. Recently, turndown operation of a TOG unit, operated at 16% of the design capacity, has been studied and reported.11 H2S levels in the treated gas always remained within permit. In addition, based on its fl exible, skid-built design, the facility is able to deal with turndown operation while securing design criteria for consumables per t of sulfur (see Figure 4).
Another differentiator of this technology is the speed of construction. In 2017, an early production facility (EPF) was taken in operation, treating a gas from a gas fi eld located in the Mediterranean Sea.12 TOG was selected to be used as a SRU in the EPF, as the technology can be designed and constructed in less than a year, has favourable CAPEX and OPEX, and is fl exible in the amount and concentration of H2S it can handle. More TOG facilities have been constructed following fast track. For example, in the facility depicted in Figure 1, fi rst gas was taken in 9 months after defi nition of the basis of design.
HAZID study
Recently, a health, safety and the environment (HSE) comparison between TOG and other technologies has been performed, using the HAZard IDentifi cation (HAZID) methodology.6 HAZID is used for early identifi cation of potential hazards and issues. The benefi t of this methodology is that it includes assessment of operational aspects of a process and is used to select the most suitable technology for a given project. In this HAZID study, three different SRU technologies including TOG were compared. The study indicated that the THIOPAQ O&G process has fewer hazards in comparison with the two other SRU technologies, because there is no free H2S once the feed gas enters the unit. Furthermore, it has a better operability because it requires less operator attention and maintenance, and it has an infi nite turndown with respect to gas rate and H2S content.
Desulfurisation in the market of biofuels
An important requirement for the SRU in biofuel projects is a strong fl exibility towards fl uctuations in sulfur load and gas composition because of frequent changes in feedstock.
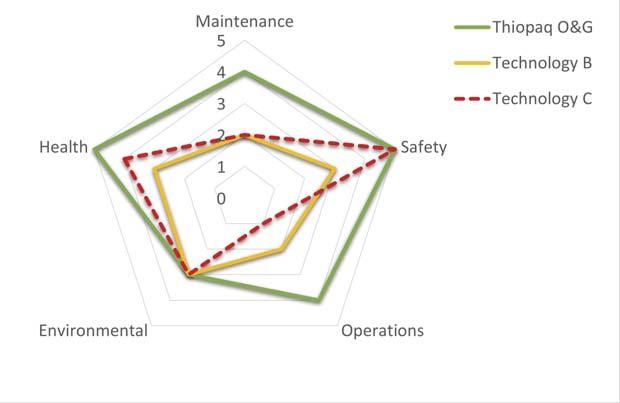
Figure 6. HAZID comparison for Thiopaq O&G and two other technologies based on HSE, operations and maintenance.6
Furthermore, the SRU should be cost-effective in the sulfur load range from 400 kg/d of sulfur up to 20 tpd of sulfurand should be able to treat gas streams with challenging CO2/H2S ratios.
While biofuel projects are long-term projects, return on investment (ROI) in biofuel projects using TOG is currently estimated to be less than three years. In addition to economics, TOG can also cope with fl uctuations in feed gas. The recent studies on TOG discussed in this article show excellent performance under the required fl exible turndown conditions. Another advantage of this technology as an SRU is that the treated gas is well suited for carbon capture and storage (CCS). Since biofuel production aims to reduce CO2 emissions, CCS will be of great support. Lastly, one of the end-products of TOG is the formation of a cake of biological sulfur. Due to the unique properties of the biosulfur, it can be used in the fertilizer and fungicide industry. The latter will not only reduce the carbon footprint but will also move the circular sulfur economy forward.
References
1. RODIONOV, M. V., et al. ‘Biofuel production: challenges and opportunities’, International Journal of Hydrogen Energy, 42.12 (2017): 8450-8461. 2. JACQUES, M. and KÖNING-ADOLPH, A., ‘Sulphur management for an unconventional gas-condensate field’, Sulphur, pp. 37 - 41, (2017). 3. O’CALLAGHAN, P., et al., ‘Assessing and anticipating the real world impact of innovative water technologies’, Journal of Cleaner Production, (2021): 128056. 4. KLOK, J.B.M., et al., ‘Techno-economic impact of THIOPAQ-SQ, the next generation of the THIOPAQ O&G process for sulfur removal’, SOGAT,
Abu Dhabi, UAE, (2017). 5. VAN HEERINGEN, G, and KLOK, J., ‘A new generation’,
Hydrocarbon Engineering, (February 2018), pp. 77 - 81. 6. LEE, K. et al., ‘Thiopaq O&G bio-desulphurisation; an alternative recovery Technology’, GPA, Edinburgh, UK, (2013). 7. CURTESCU, A. et al., ‘Why choose a one-size fits-all TGTU and risk leaving money on the table?’, CRU Middle East Sulphur, Abu Dhabi, UAE, (2017). 8. LANNING, A., et al., ‘Stranded No More – Turning Sour Casinghead Gas
Into Profits Using Shell-Paques® Bio-Desulfurization’, Laurance Reid
Gas Conditioning Conference, Norman, Oklahoma, USA, (2008). 9. SLAVENS, A., et al., ‘Sulphur Plants Produce Valuable Energy Use it
Wisely!’, CRU Middle East Sulphur, Abu Dhabi, UAE, (2017). 10. CURTESCU, A. and VAN HEERINGEN, G., ‘Strike a balance’,
Hydrocarbon Engineering, (October 2017), pp. 77 - 80. 11. KLOK, J. B. M., et al, ‘Desulfurization of amine acid gas under turn down:
Performance of the biological desulfurization process’ Laurance Reid
Gas Conditioning Conference, Norman, Oklahoma, USA, (2018). 12. KLOK, J. B. M., et al, ‘Sulfur recovery in Early Production Facility’, GPA,
Kuwait, (2019).
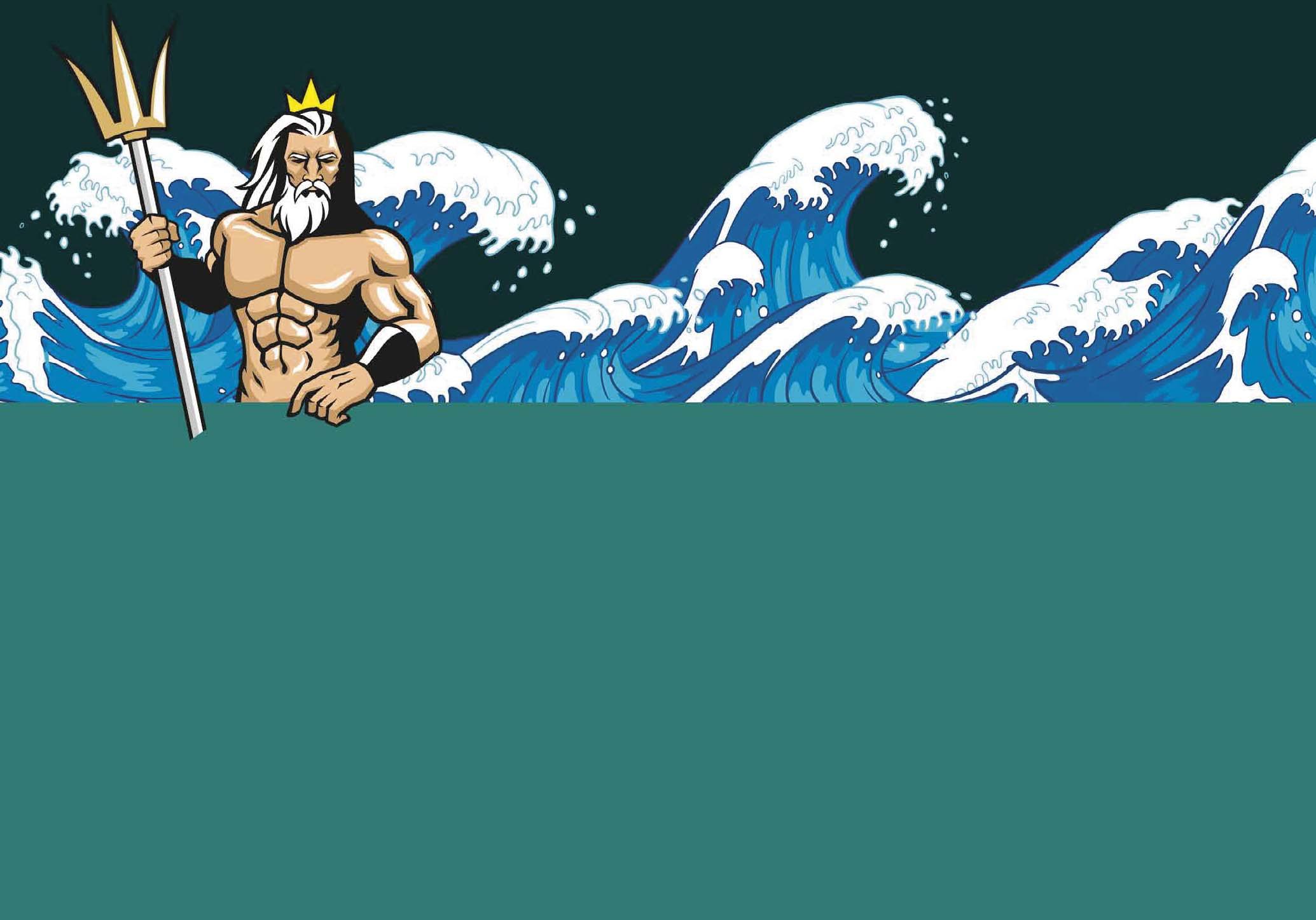
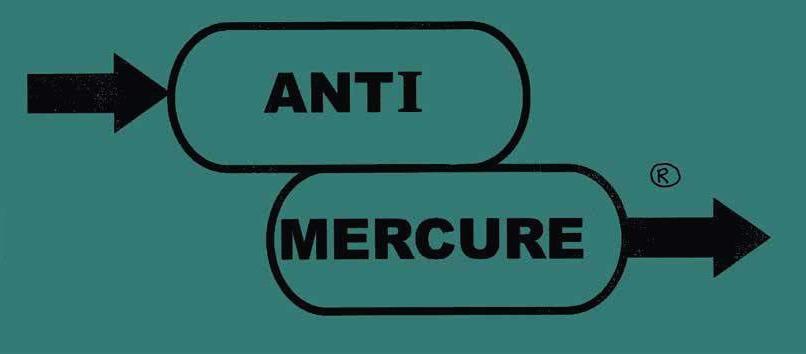
AntiMercure® Systems
• Proven 99% mercury removal from water • Continuous operation • Easy installation and start-up • Pre-engineered, skid mounted – 3 standard sizes