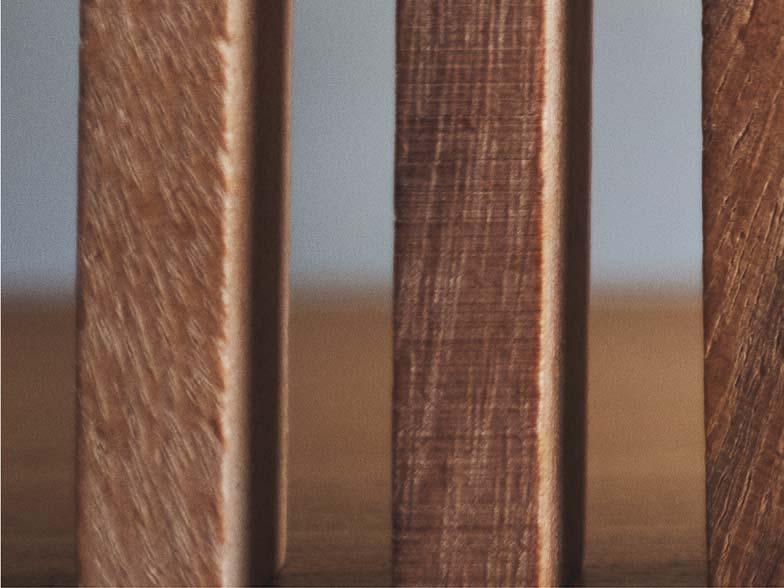
9 minute read
Trading risk for reliability, fl exibility and effi ciency
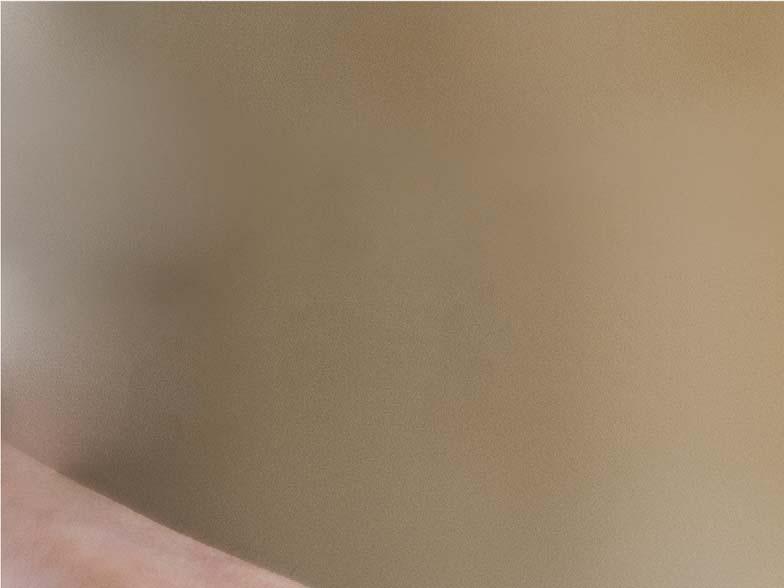
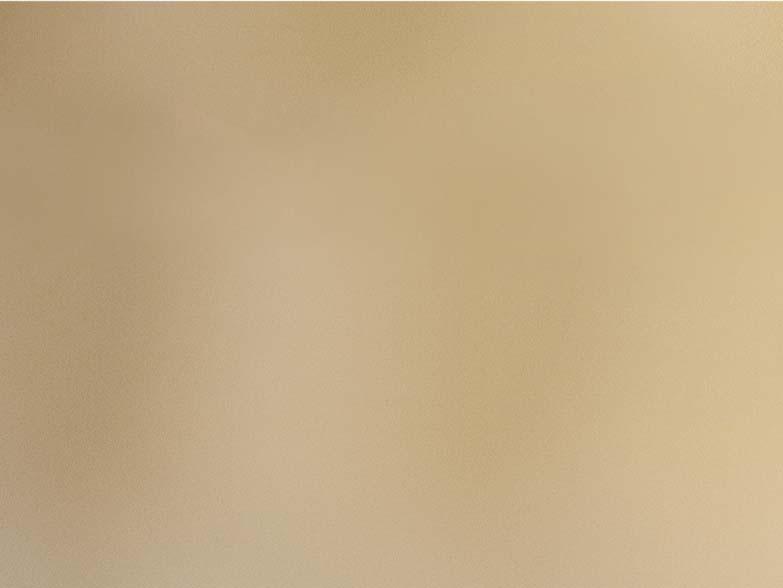
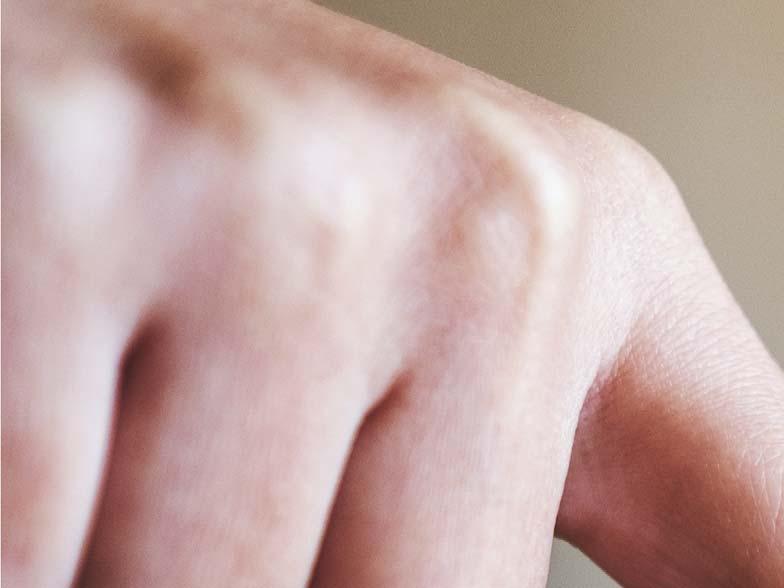
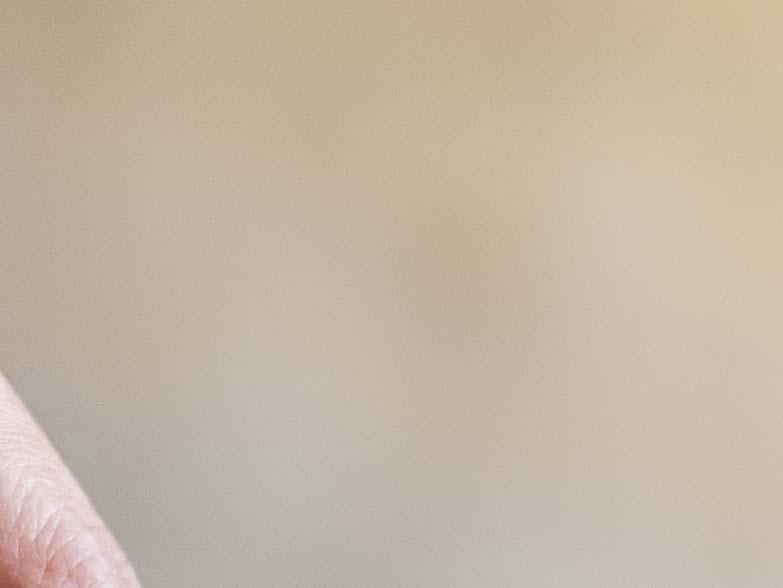

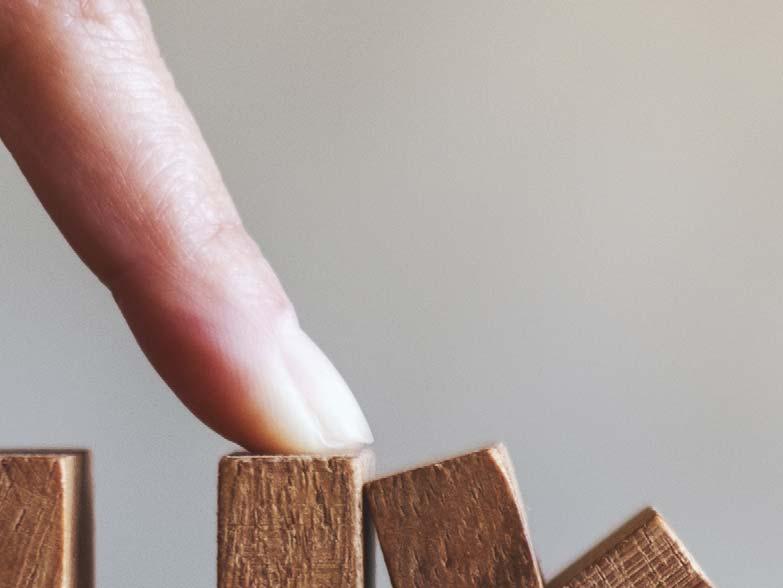
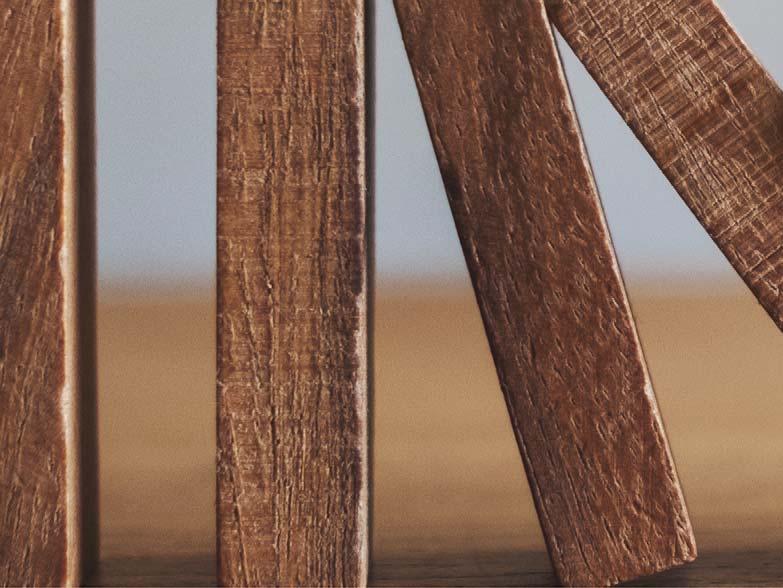


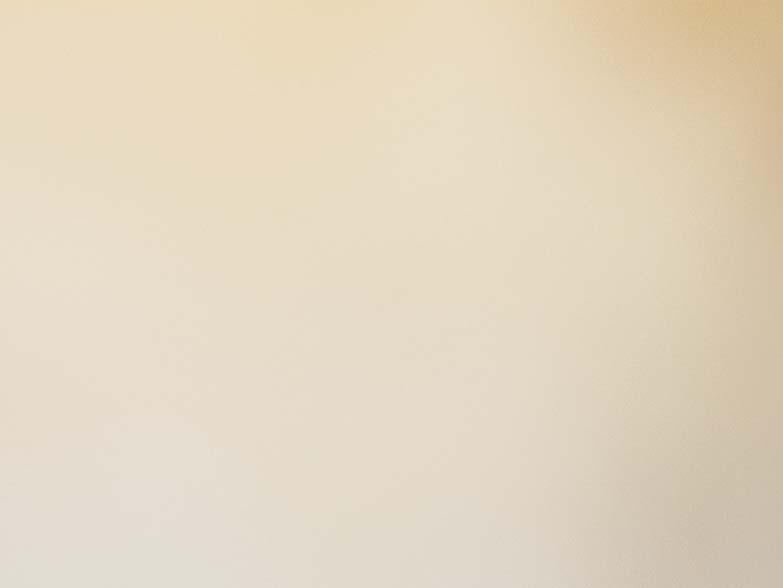
Sami Tabaza, Atlas Copco Gas and Process, USA, explains why integrally geared centrifugal compression technology is increasingly being used in NGL plants alongside oil-flooded gas screw compressors.
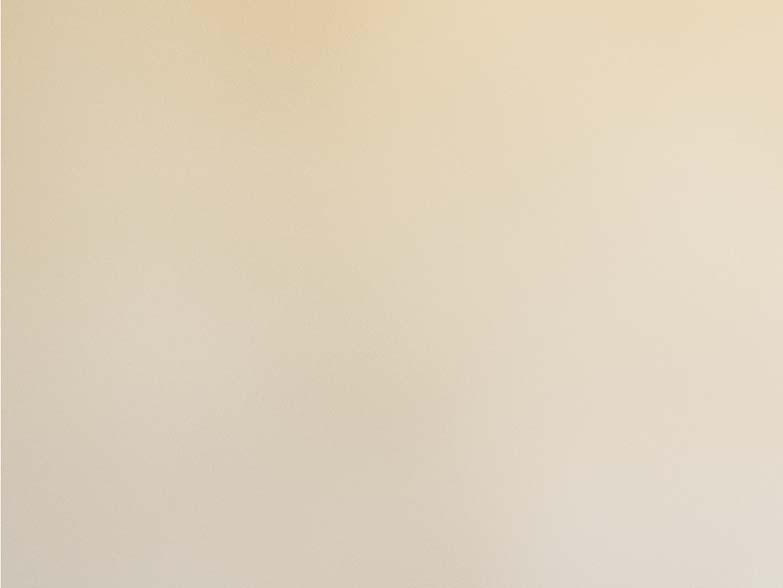
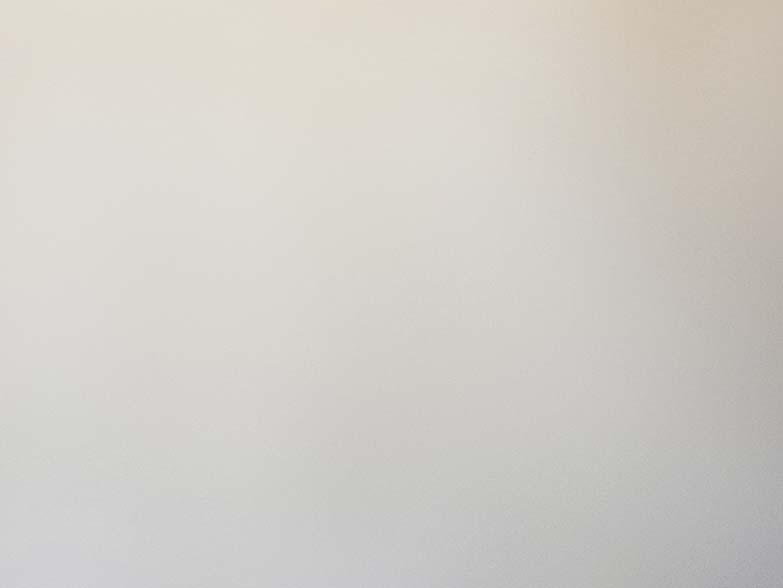
Gas processing plants need to cope with varying and often uncertain conditions. Operators typically face challenges with the mode of operation (ethane rejection or ethane recovery) and feed gas uncertainty (rich gas or lean gas). In terms of equipment reliability, fl exibility and effi ciency, these circumstances also place signifi cant requirements on the compressor technology used. The case study within this article will discuss the deployment of a mechanical refrigeration cycle using commercial-grade propane (95 – 98.5% propane, with the rest being heavy hydrocarbons, or HD5, or higher-grade propane). It will also examine the performance characteristics of compressor technology applied in gas processing plants, including oil-fl ooded screw, and integrally geared centrifugal.
Flexibility and performance
Standardised gas processing plants up to 200 million standard ft3/d (~223 000 Nm3/hr) are typically built with a two-stage refrigeration cycle, using a fl ashing inter-stage economiser. Vaporising the commercial-grade propane refrigerant used in these plants in a two-stage process helps to improve effi ciency. The process is driven either by two compressors or, ideally, by a single compressor using two sections (i.e. two process stages).
While the oil-fl ooded screw compressors are a widely used option in the gas processing industry, the oil-free integrally geared compressor (IGC) has been growing in popularity in recent years. Because of their effi ciency, availability, reliability and a comparatively low CAPEX, integrally geared centrifugal compressors are increasingly being used in upstream, midstream and downstream markets. The technology’s compact size and ability to accommodate side streams also helps to enable fl exible plant operations.
Natural gas processing plants need the fl exibility to handle both rich and lean feed gas without reducing performance. Plants must also be agile enough to operate in ethane recovery or rejection mode, and are often required to operate in extreme ambient (summer and winter) temperature conditions. Furthermore, on plants processing shale gas, such as several plants operating in North Dakota, US, with integrally geared technology, the compressor design must account for the variability of feed gas conditions. In other words, fl exibility
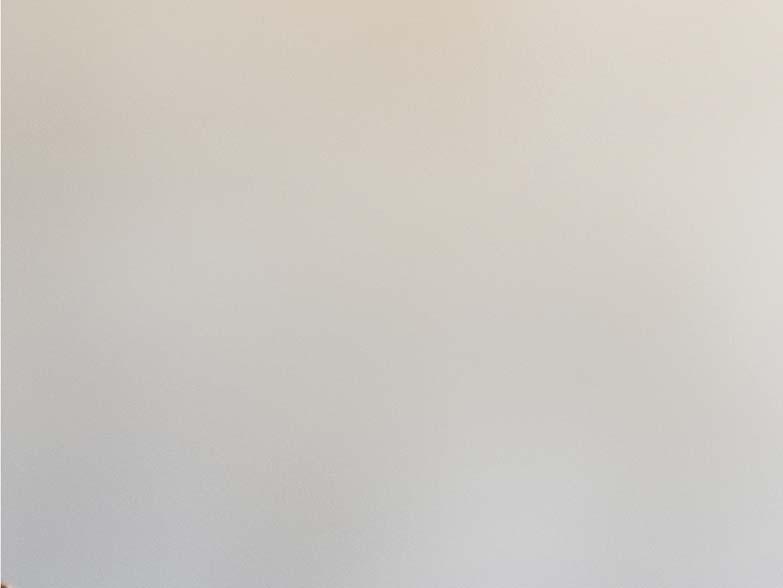


is an essential requirement for enabling a refrigeration compressor to meet these different modes of operation. The ultimate target of a natural gas liquids (NGL) train is its ability to extract 95 – 99% of the heavy hydrocarbon (C2/3+) components of the feed, known as the Y grade.
The North Dakota plants highlighted in this case study were designed for a nominal capacity of 20 million standard ft3/d (~223 000 Nm3/hr). For one of the plants, the objective was that it would start operations at 50 million standard ft3/d (55 800 Nm3/hr) and then increase the fl ow rate to 100 million standard ft3/d (111 600 Nm3/hr) and later even to 200 million standard ft3/d (223 000 Nm3/ hr) over the plant’s fi rst year of operation. This rapid ramp-up in plant capacity had to be considered in the compressor design, as did the variation in suction pressure due to different modes of operation. The ability of integrally geared technology to fl exibly adapt to such process conditions in the optimal manner made it a viable compressor solution for these specifi c plants.
Deployment of oil-flooded screw compressors in NGL plants
When deployed in NGL plants, oil-fl ooded screw compressors feature a design that enables them to function in a variety of conditions, as outlined above. For example, these machines can divide the total refrigeration duty in two (50% duty), three (33% duty) or four (25% duty) compressors. Depending on a plant’s operating requirements and approach, this allows for anywhere from 10 to 100% turndown. Because oil-fl ooded screw compressors are based on the principle of positive displacement, they are not unduly affected by fl uctuations in mole weight, suction pressure or temperature. Accordingly, these machines operate in the gas plant with a traditional effi ciency of 65 – 70%.
While oil-fl ooded screw compressors are generally considered easy to operate, they are subject to oil contamination of the propane, which reduces the reliability of this solution, as reported by the designers and operators of the sites in study. If proper maintenance of the oil removal system is not performed, or if unexpected performance issues arise, preventing the contamination of process gas (in this case, commercial grade propane refrigerant) downstream from the compressor becomes a challenge. If oil in the compression chamber is carried over with the process gas and fl ows downstream, contacting the refrigerant fl uid, it can cause failures in the brazed aluminium heat exchanger or condensers. Additionally, if there is a bypass for the condenser, the leaked oil will also affect the accumulator. Because of these factors, screw compressors require more frequent maintenance than IGCs, both in terms of regularly changing the coalescing fi lter and oil fi lters, and for verifying that oil has not been carried into the process.
Suction pressure and flow control methods for extended compressor turndown
One of the key factors in any refrigeration application is the handling of process changes, which affects refrigeration duty. Variable diffuser guide vanes (vDGVs) provide greater operational fl exibility and help maintain stable compressor operation over a wide range of conditions and at a constant discharge pressure. In cases where air-cooled condensers are utilised, when a rise in ambient temperature occurs, refrigerant condensing temperature also increases due to increasing pressure in the cycle. To retain a consistent level of cooling, the system requires higher fl ow at higher pressures. IGCs may incorporate two control types: vDGVs and inlet guide vanes (IGVs). vDGVs extend compressor turndown by up to 50% in both single and multi-stage refrigeration applications. The combination of aerodynamically engineered components such as impellers, vDGVs and volutes serves to boost effi ciency in centrifugal compressors. These aerodynamic components can be matched by selecting the right gearbox and incorporating the proper pinion speeds in the compressor design process.1,2 This can then be complemented with stable rotor dynamics to achieve maximum effi ciency. When a change in a machine’s operational mode to rejection mode is made, it will normally be with the lower head and smaller fl ow (assuming lower duty). This can be achieved as the refrigeration machine will adapt to that change by turning down the compressor’s vDGVs and adjusting the machine to the required discharge pressure. vDGVs help to optimise IGCs by enabling the machines to handle high settle-out conditions Figure 1. Integration of the integrally geared refrigeration compressor inside the gas at start up. processing plant. By comparison, screw compressors


Figure 2. Typical refrigeration compressor package using integrally geared technology.
Figure 3. vDGV typical performance map showing range of operation.
Efficiency characteristics
As has been shown in numerous hydrocarbon installations, integrally geared technology can generate savings due to its overall effi ciency characteristics, though this always depends on the specifi c application and case at hand.2,3 For propane refrigeration applications, for example, IGCs can attain polytropic effi ciency in the range of 80 – 84% through aerodynamic enhancements and stage optimisations. Depending on which process design is used on the NGL plant, this can generate total energy savings of between 10% and 12% compared to oil-fl ooded screw compressors. In one of the North Dakota plants, where the assumed polytropic effi ciency was 80%, a three-stage IGC operating at full availability for 17 million Btu/hr (4 982 kW) chiller duty realised power savings of approximately 10% compared to a base oil-fl ooded screw compressor design. Because IGCs typically offer higher maintainability than oil-fl ooded screw compressors, they also generate maintenance cost savings.
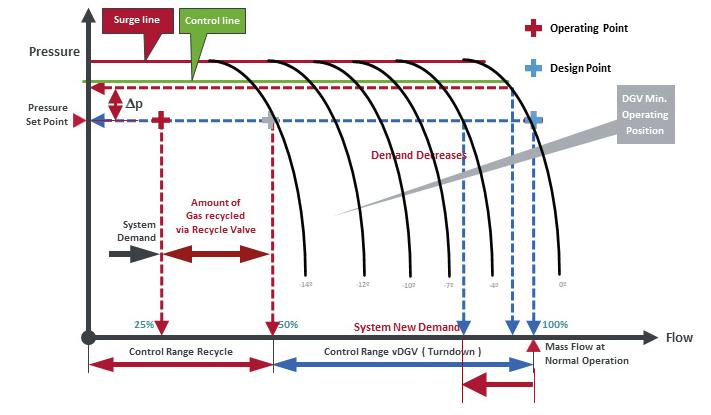
manage suction fl ow with sliding vanes, thereby using a different method to handle the same situations. While both processes are effective, vDGVs offer greater precision in terms of response time and amount of fl ow that can be controlled.
Compressor reliability in NGL plants
The design of the IGC ensures that no oil can enter the compression chamber. As a result, IGCs provide 100% oil-free operation, increasing compressor reliability while also requiring less maintenance. These compressors provide continuous service with greater than 98% availability.
To help safeguard reliability, the IGC units deployed in North Dakota feature a combination of tapered land thrust bearings with tilted pad radial bearings. This enables the machine to offer stable operation even during high settle out conditions and also when the thrust load is much higher than it would be during normal operating conditions.
The thrust tapered land with tilting pad radial bearings employed in the North Dakota units help maintain stable operation even during high settle-out conditions, enabling high availability. Generally, the hydrodynamic bearings used in the North Dakota compressors offer advantages in terms of reliability and longer life compared to competitive technologies.3 Many screw compressors utilise anti-friction bearings, which have less robustness, reliability, and lifespan characteristics. This design is complemented by dynamic dry gas seals backed by fl oating carbon ring seals, which results in oil-free operation in all conditions, even during emergency stops or if seal failure occurs. Atlas Copco Gas and Process is the fi rst manufacturer in the world to employ dynamic dry gas seals in IGCs and expanders.
Conclusion
Given its ability to operate reliably and effi ciently, integrally geared centrifugal compression technology is increasingly being used in NGL plants alongside oil-fl ooded gas screw compressors. From a CAPEX perspective, this technology provides an economically attractive solution, in addition to generating extensive OPEX savings over the course of the plant’s lifecycle. Furthermore, the compressor units installed by Atlas Copco Gas and Process at plants in North Dakota demonstrate how this technology can match the need for fl exibility required by gas plant operations. Existing installations such as this show that IGCs can provide a reliable, effi cient compression solution that offers the agility and fl exibility demanded by the modern gas processing industry globally.
References
1. RINALDO, J., ‘Gearbox Specs – Getting Them Right’, Turbomachinery
International Handbook, (2017). 2. BEATY, P., EISELE, K., and MACEYKA, T. et al., ‘Integrally-geared API 617 process gas compressors,’ 29th Turbomachinery Symposium, Houston,
Texas, US, (2000). 3. PATEL, T. and STRUCK, H., ‘Ensuring integrally-geared compressor reliability with API 617’, 10° Fórum de Turbomáquinas, Rio de Janeiro,
Brazil, (28 - 30 November 2017). 4. PATEL, T. and RENKEN, H., ‘Achieving greater agility in LPG recovery with integral-Gear Compression Technology for Propane Refrigeration’,
Abstract prepared for the World Gas Conference 2018, (2017).