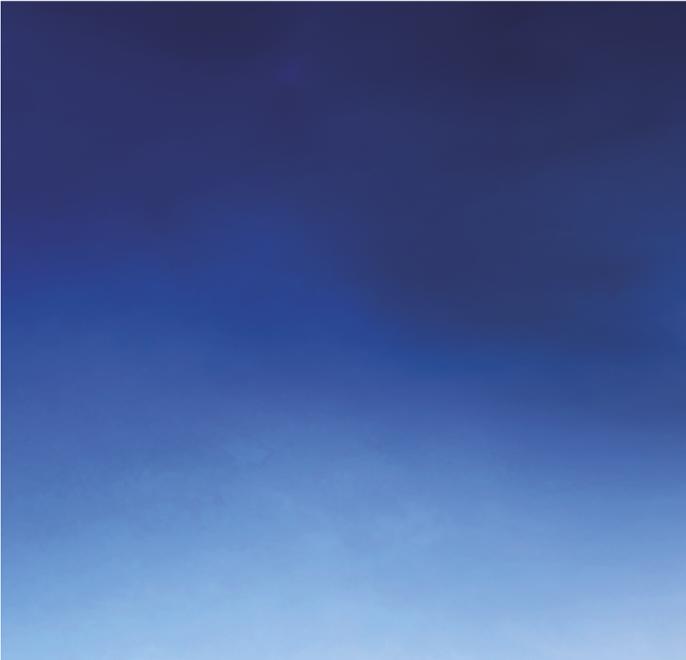
9 minute read
The last mile
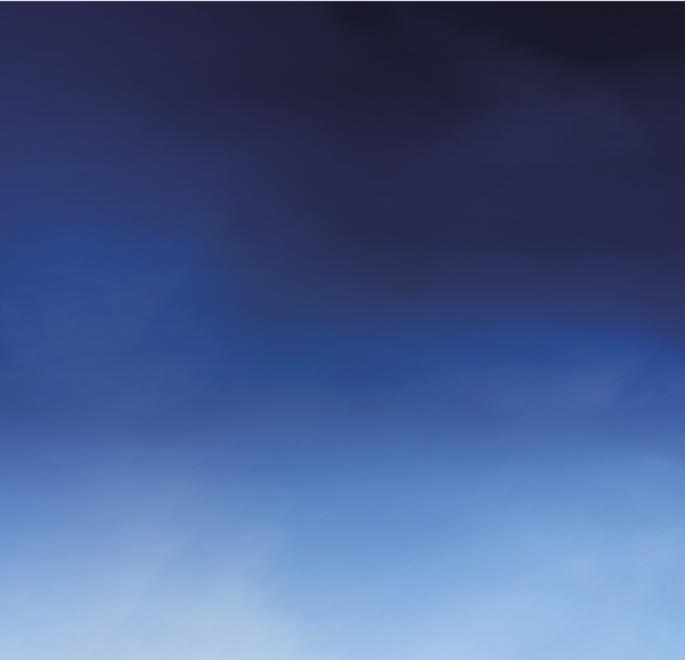
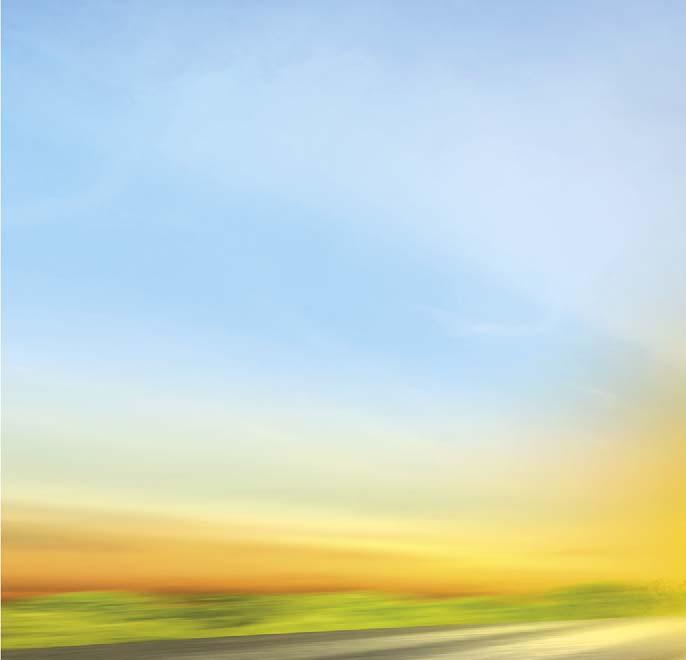
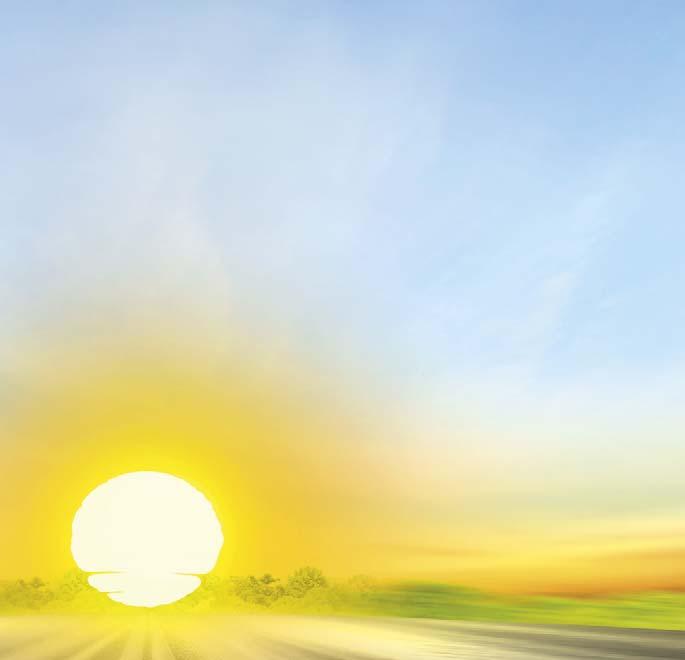


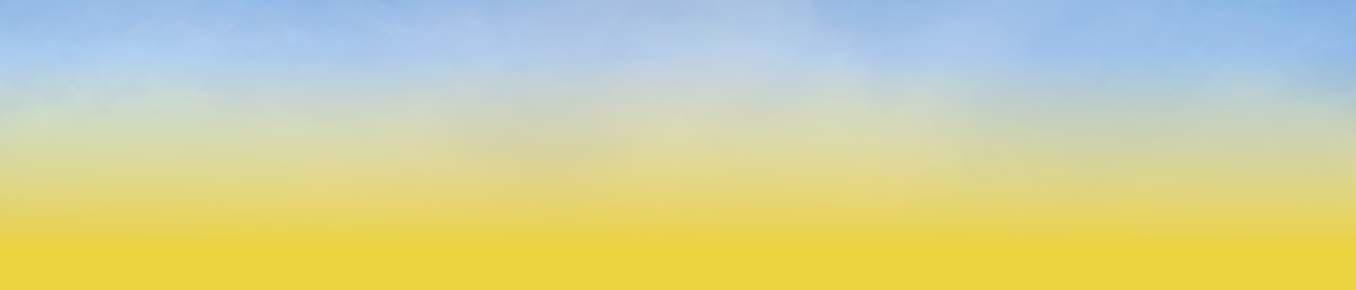
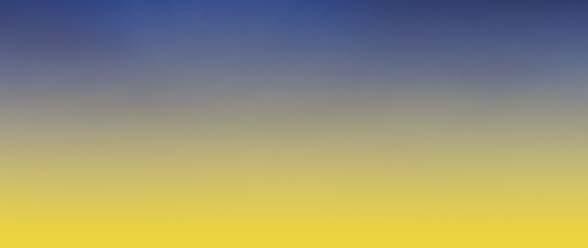
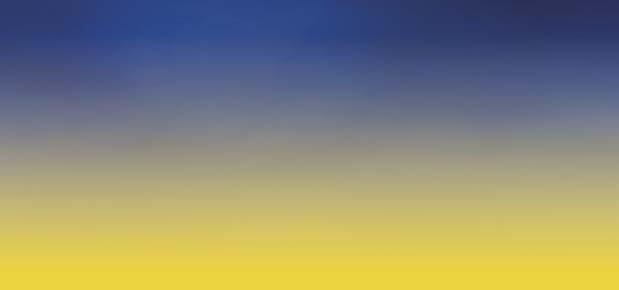
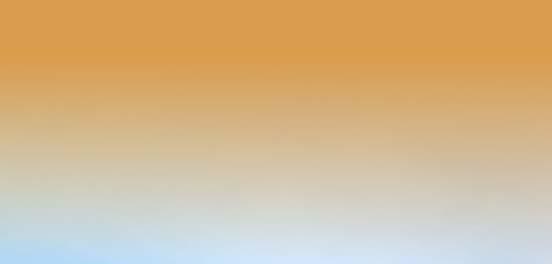
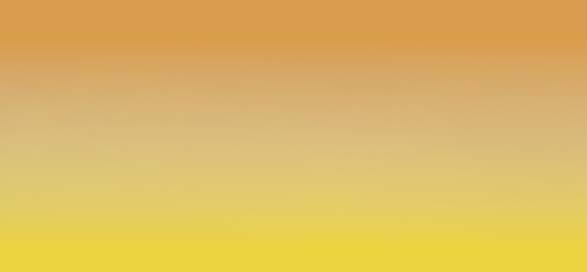
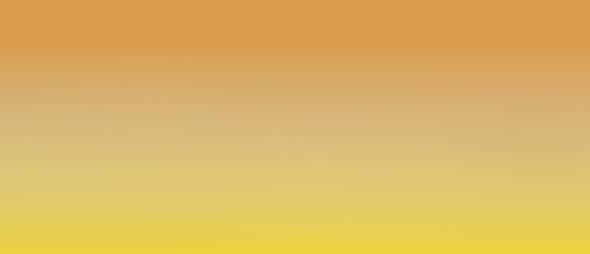
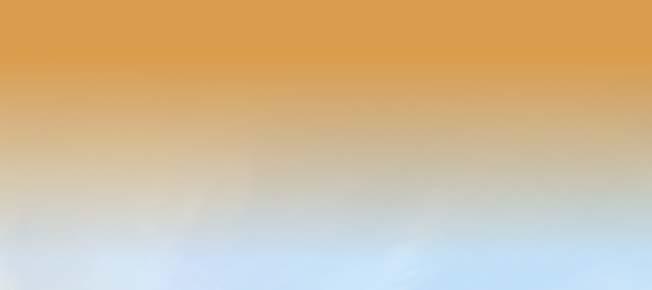

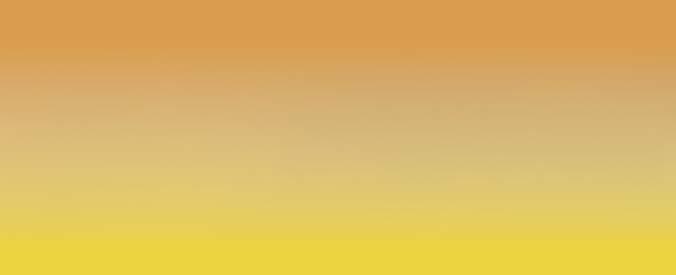
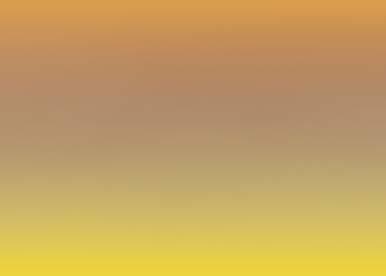
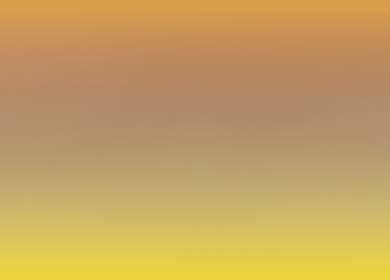
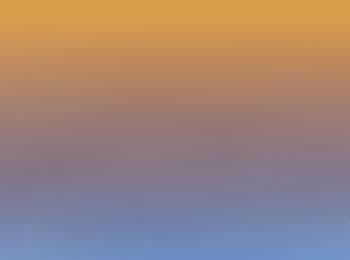
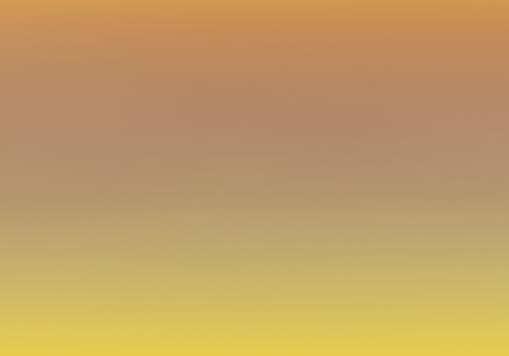
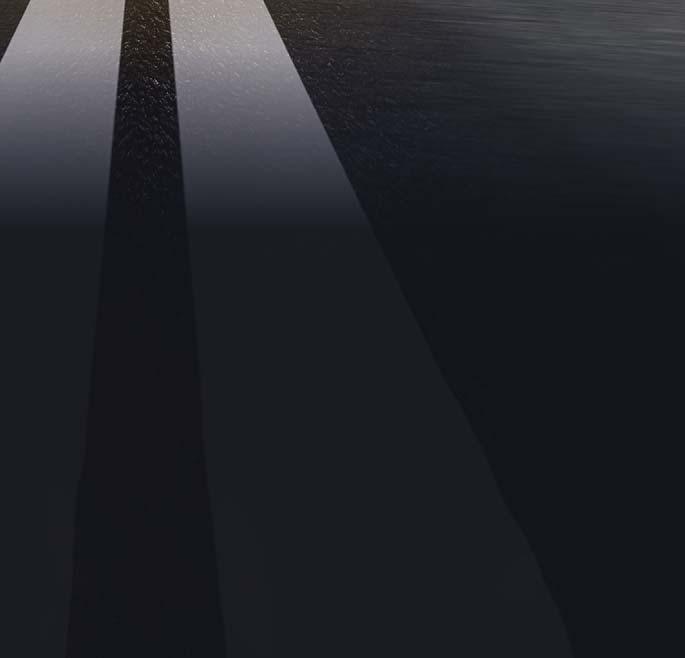
Stuart Morstead, Honeywell Connected Industrial, presents an overview of the main trends shaping the future of the industry, and outlines the need to connect processes, people and assets to meet new challenges.
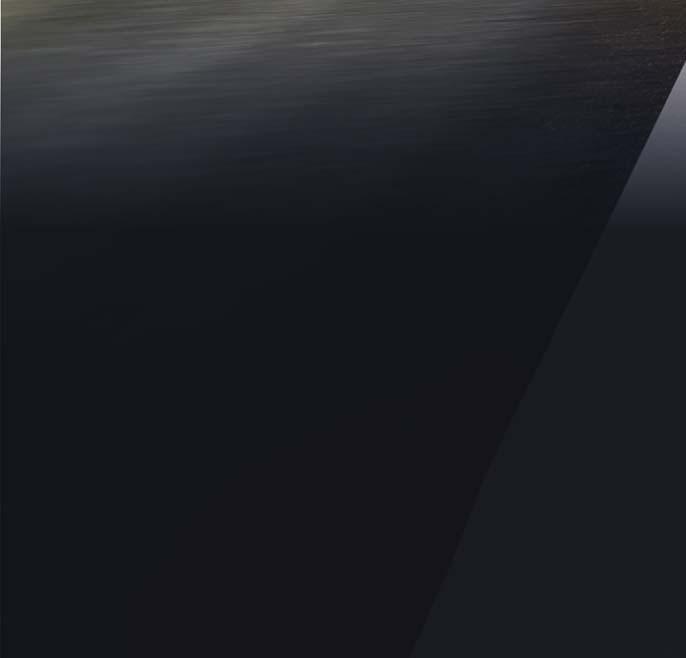
A2020 Honeywell survey of 3000+ managers in multiple industries found that a majority of respondents said they were “worried they may be too late with their digital transformation efforts and will fall behind their competitors.”1 New challenges, including macro volatility, continue to drive the need to transform, and nowhere more so than industrials that have been historically sheltered with fewer transactions and lower user experience expectations than consumer oriented sectors.
There are wide-ranging emerging industrial trends and diverse stakeholder needs that have to be met, including sustainability, product mix and fi nancial performance. These trends and stakeholder needs represent a signifi cant challenge to both conservative and aggressive operators alike.
The good news is that one digital lever in particular can play a role in meeting a broad set of transformation drivers: design, build, operate and optimise.
The big three dividers
Increased volatility
High volatility in supply and demand severely tests operators’ abilities to hit their volume and mix targets – all while maintaining profi tability. Both sides of the supply/demand equation are seeing increased complexity, which can be an impediment to productivity gains.
The global regulatory environment, the cyclicality of commodity prices, and the impact of generational events or black swans have all convened to increase volatility, especially in supply chains. While not necessarily fragile, supply chains in many industries are not as resilient as they need to be, and the interdependencies can result in major problems when a crisis hits.
On the fl ip side of the supply chain, the demand patterns in end markets are rapidly creating new product mixes for operators with which to contend.
Many industries are dealing with new demands for new types of products in their portfolio. For instance, automotive is facing a demand for lighter materials and electric vehicles (EVs), as well as autonomous vehicles. In construction, the demand for pre-fab and 3D printed modules has increased. Manufacturing and refi ning are facing their own new product trends and demands.
As demand shifts in consumer end markets, operators are struggling with a fl exible manufacturing response, and it is challenging to deliver a more diverse product set.
Sustainability as a core imperative
The second urgent need relates to the global call for decarbonisation, methane reduction, and green/blue/grey hydrogen issues. In short, the need for real movement on operational sustainability. Many organisations are asking themselves how they can properly respond to these societal demands. How do we all balance profi t and effi ciency against being a responsible steward of the environment?
And the challenges are different for each industrial factor. For instance: Refining: irrespective of recovery pattern, the large volume of emissions contributed by refined products must be offset through efficiency or capture. Chemicals: plastics recycling promises the creation of a circular economy, but investments, partnerships and infrastructure are all still required. Mining: CO2 and water challenges are this sector’s biggest environmental, social, and governance (ESG) issues to solve in order to earn ‘the right to play’.
Regardless of the specifi c sector – improved monitoring of CO2 emissions, better management of energy usage, new implementations of carbon capture technology, and process information-sharing between partners – all of these challenges require digital solutions to properly execute. The demographic cliff
The third set of challenges involve the impending ‘demographic cliff.’ There are two factors at play in the creation of this ‘cliff.’ First is an ageing workforce which has started to retire – taking decades of expertise with them. Going through this ‘great crew change’ has impacted manufacturers who must increase their training programmes while enduring a decrease in productivity at the same time.
The second factor is the ‘deskless employee.’ A lack of remote access to key data can greatly impair productivity across the entire organisation. This gap is especially evident in departments that operate across a far-fl ung plant – such as maintenance, where personnel may need to be in one location but not have access to accurate data about that equipment and processes. Solving these workforce challenges truly depends on having the right information and right expertise for frontline workers – all at the right time.
A successful industrial digital transformation solves all these issues and brings with it the following benefi ts: Enhanced situational awareness. Minimised human exposure to safety risks. The ability to make better, faster decisions. Enhanced process safety and execution. Improved knowledge capture and management. Valuable, actionable insights and proactive guidance via the use of machine learning (ML)/artificial intelligence (AI). A paradigm shift in training and skills-upgrade, enabled by augmented reality (AR)/virtual reality (VR).
A collective shift in operating context
Collectively, the three main drivers create a dramatic shift in the operating context for industrials. Figure 1 demonstrates how the operating context has shifted in recent history, driving the need for digital transformation.
The bottom row illustrates how, in the last few decades, industry has already undertaken several shifts driven by the operating context. This encompasses the internal environment of the physical plant and process, the external environment, and the responsibilities that lie with the social contract (worker safety to water/energy consumption, etc.).
In the next row, it is shown how these challenges can be managed, with tools that can be easily implemented, such as: preventive maintenance/computerised maintenance management system (CMMS) protocols, automation systems, isolated data analysis, and digital point solutions. But comprehensively, these have not resulted in an integrated view of the industrial enterprise, and so the promise of the ‘smart plant’ or of ‘industry 4.0’ remains elusive.
While the ultimate destination in the future may be autonomous, self-optimising plants, the journey to cover the ‘last mile’ for operating technology, especially in chemical processing plants, is a diffi cult one and still lacks critical connectivity.
Connecting assets and connecting processes, highlighted in the third row of Figure 1, results in
connected plants and enterprises – in other words, plants that can be optimised across the production process using technologies such as process digital twins, asset performance management, and data orchestration.
But there is a missing piece of this connectedness: ‘connected workers’, the people who ensure the work gets done the right way, safely and effi ciently.
By combining the top two rows, along with a robust, interoperable connected data solution, Enterprise Performance Management for Industrial can be created.
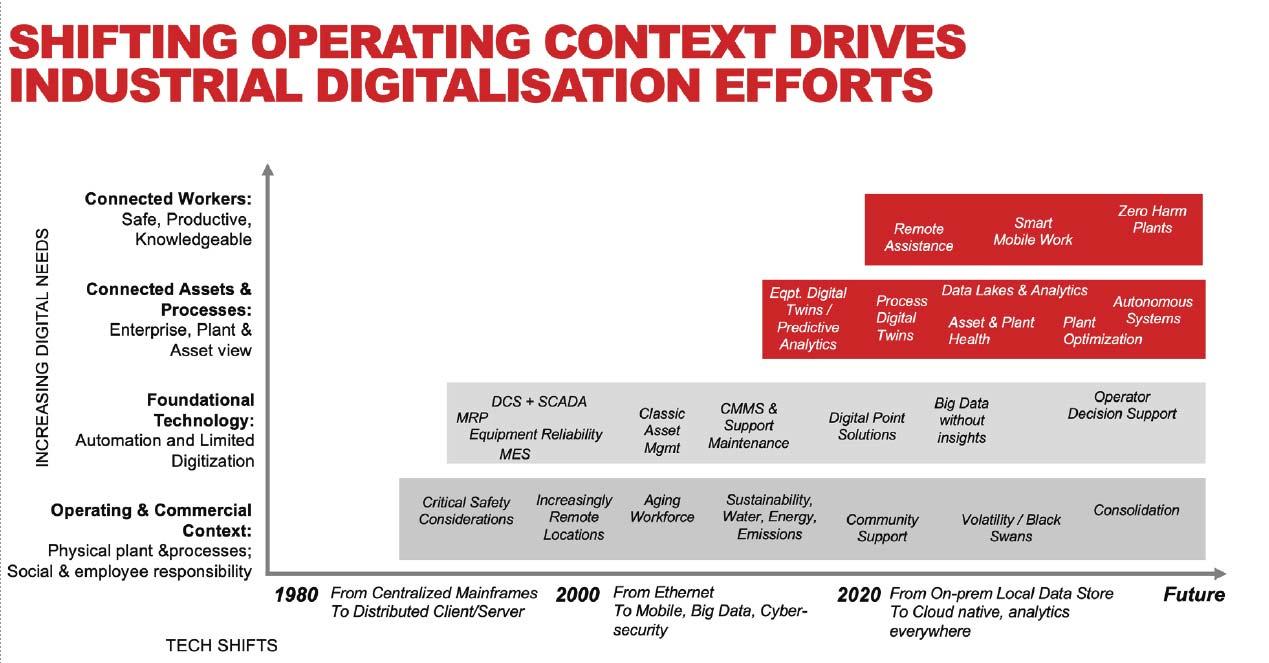
Figure 1. This table demonstrates how the operating context has shifted in recent history, driving the need for digital transformation.
The ‘last mile’
Enterprise Data Management for Industrial (EDM) is key to a safe, successful, effi cient digital transformation. It means collecting and analysing disparate data from the plant fl oor, other systems, and orchestrating it across multiple applications in those connected processes, assets and worker suites. Ultimately, it provides visualisation and insights into enterprise performance. It is the foundation of the system and is not suffi ciently available today for operators.
Honeywell asserts that, on a global scale, the lack of EDM today is holding operators back. There are various digital point solutions for asset monitoring, or isolated process management, or enabling knowledge workers. Data storage and historians are readily available. But to deliver digital transformation – to connect IT to OT – industrials must cross the last mile to that future with true EDM.
EDM for manufacturing is like the enterprise resource planning (ERP) systems that are used by fi nance functions today, or the customer relationship management (CRM) systems that have revolutionised sales teams.
October 12-13, 2021
Moody Gardens Convention Center GALVESTON, TX
True industrial EDM provide an integrated management of operations in real time with cybersecurity, data connectivity, orchestration, contextualisation and visualisation as the foundational elements. EDM can be thought of as a new System of Record for IT and OT – just as ERP is a system of record for fi nance and accounting. And like ERP, it has the potential to unlock enormous enterprise value.
Over the last 30 – 40 years, the industry has invested in foundational technology, including automation to improve profi tability and run safer, reliable operations. Today, as we move out of the COVID-19 pandemic, the industry faces many challenges and disruptions – from an ageing workforce, to sustainability/net zero/decarbonisation needs, to a volatile supply and demand.
Process industries are in the early stages of digitising manufacturing operations, with increased focus on monetising data and the orchestration of information. Achieving both of these goals will maximise performance from assets, processes and people. After a history of point solutions and individual transformation initiatives, the time has come for the process industries to pivot to a new digital future.
By adding a system of record (SOR), coupled with visualisation and advanced analytics in a complete EDM solution, Honeywell aims to drive ‘the last mile’ around connecting processes, people and assets. This will address new industry challenges and maximise profi tability for customers in a safe, reliable and sustainable way.
The path to safe, autonomous, optimised plants is an SOR that covers the following. Connected assets: Maximise asset performance and optimise for reliability. Manage planned and unplanned maintenance activities. Plan, track, optimise energy and emissions. Connected processes: Optimise processes and production performance across enterprise with integrated planning. Dynamically adapt processes to changing plant conditions. Provide workforce competency and productivity improvements. Connected workers: Manage operational risks and ensure safety. Enable new ways of working with people away from work sites, regardless of which of these needs is driving digital transformation.
The time to start transforming is now. Focusing on this last, crucial link is the only way to guarantee that a plant is fully optimised, truly effi cient and completely connected.
Reference
1. Multiple sources including Gartner articles 2020 - 2021,
Honeywell analysis.
Page Number | Advertiser 21| ABC 15| AMETEK Process Instruments
OFC & 47 | Atlas Copco Gas and Process 32| BORSIG GmbH 11| Comprimo 02| CS Combustion Solutions GmbH 41| ERTC 2021 04| Eurotecnica OBC| Filtration Technology Corp. (FTC) 63| Gulf Coast Conference IFC| IPCO 55| Koch Engineered Solutions 17| Merichem Company

AD INDEX
31| NAPCON 35| NEO Monitors 27| Optimized Gas Treating, Inc. IBC, 31, 39 & 45 | Palladian Publications 23| Paqell 52 | Rembe® GmbH Safety + Control 21| S.A.T.E. 51| SBS Steel Belt Systems S.r.l 24| Selective Adsorption Associates, Inc. 07| Shell Catalysts & Technologies 45| Sulphur + Sulphuric Acid 2021 13| Uniper 59| Zeeco Inc.