
9 minute read
The critical measurements
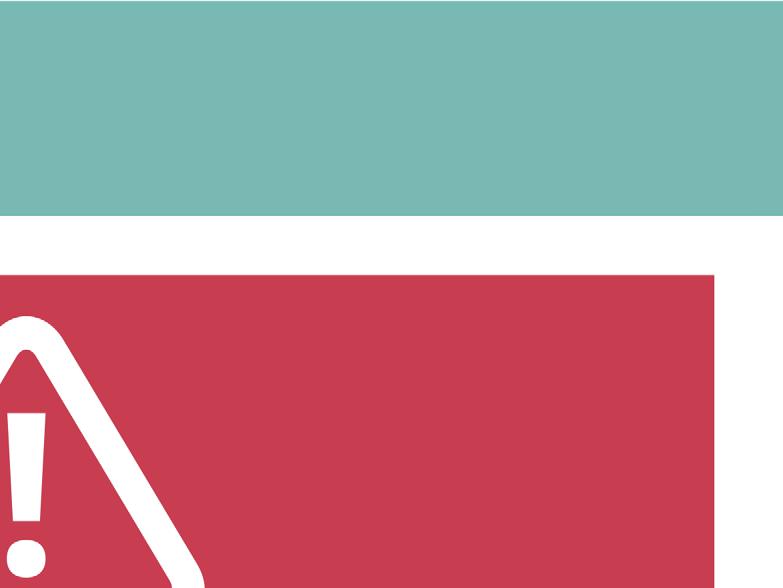
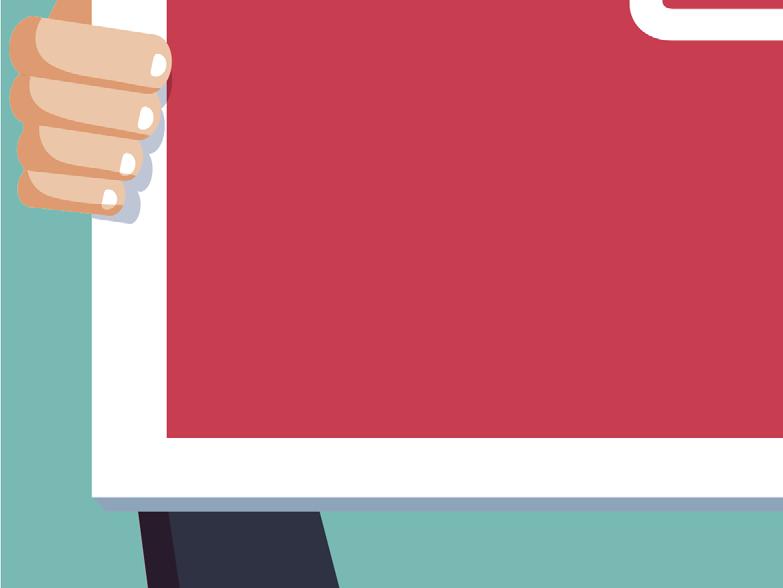

Dr Stephen Firth, Servomex, UK, examines the critical measurements for safety and control in PTA production processes.
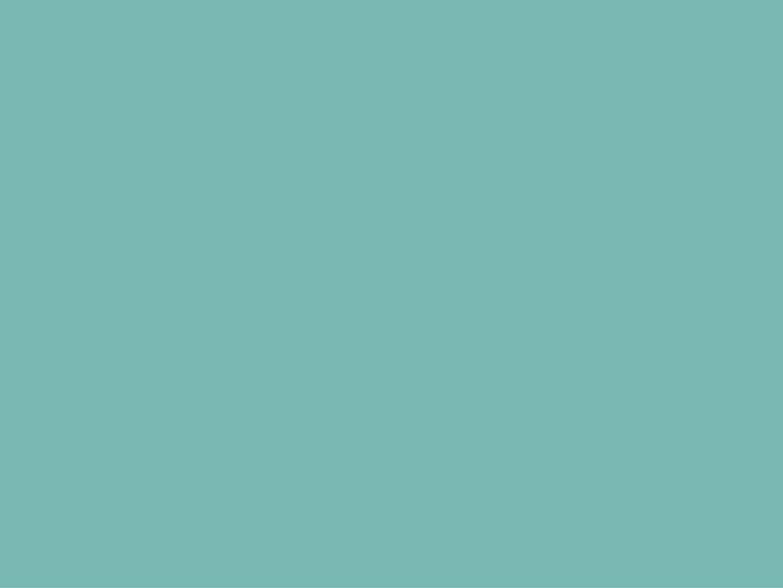
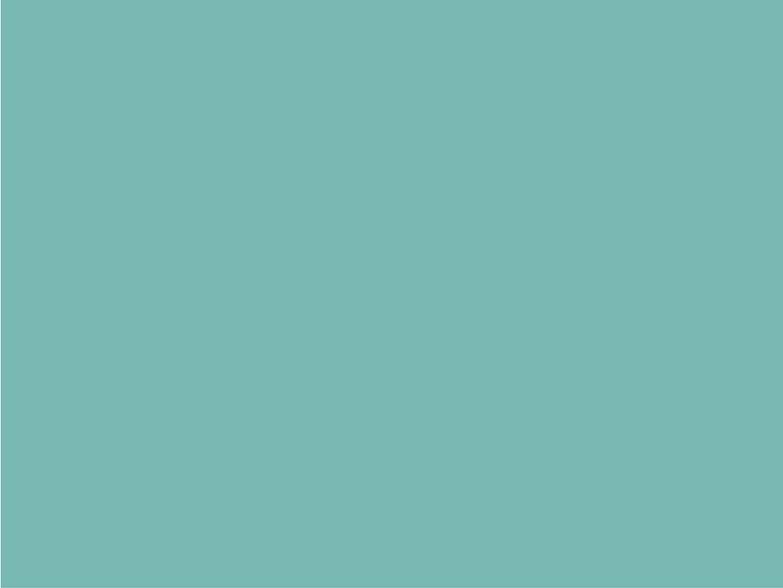
Purifi ed terephthalic acid (PTA) – sometimes referred to as polymer-grade terephthalic acid – is a white crystalline substance that plays an important role as a precursor for plastic production. Its high melting point of 427˚C (801˚F) makes it particularly valuable in ensuring the thermal stability of the plastics created from it. It is most commonly used as the key component in the manufacture of polyethylene terephthalate (PET), a recyclable thermoplastic resin with US Food and Drug Administration (FDA) approval for use as food and drink containers and bottles.
PET is also the most widely used of the polyester type of man-made fi bres. Approximately 80 – 100 million tpy of PTA is produced, with the vast majority manufactured in Asia – eight of the ten largest PTA plants in the world are currently located in the region. There is a continuing and growing demand for PTA throughout the world, particularly in the fast-expanding Asian economies, which also make up the largest demand for PTA;
China alone uses 60% of the PTA produced globally.
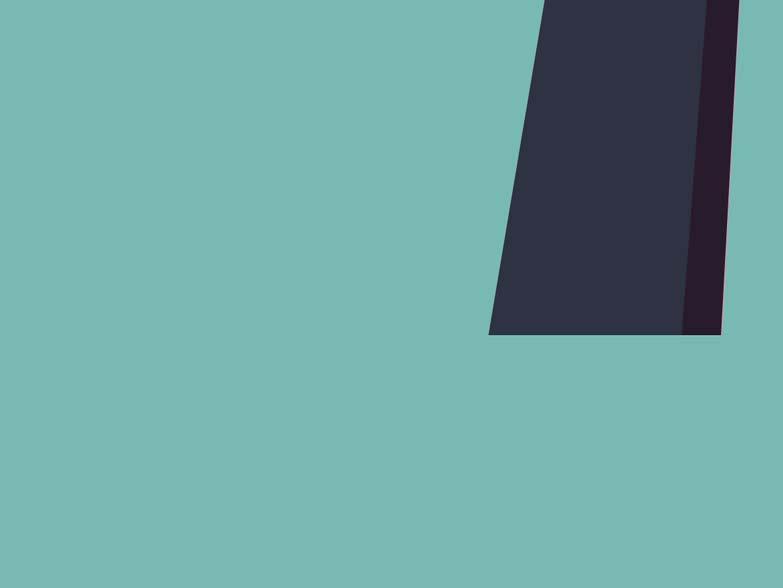
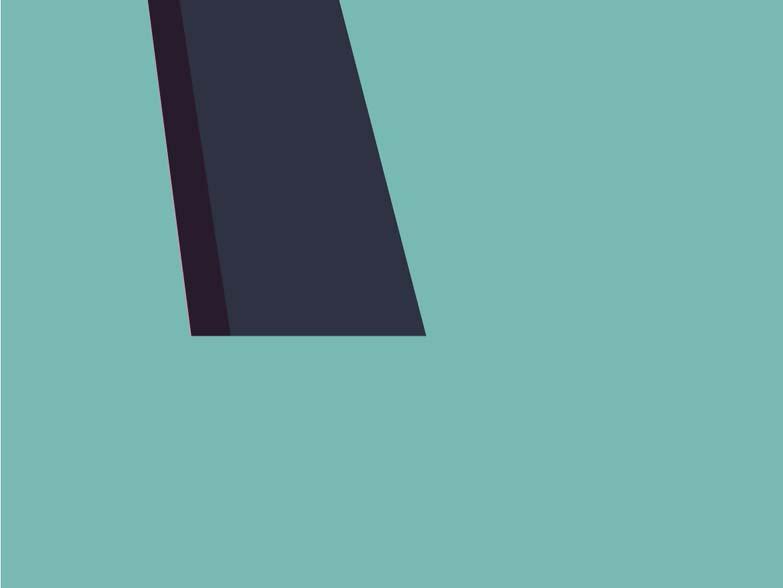
PTA production processes
There are a number of licensed methods for the production of PTA. These all follow roughly the same basic process.
PTA is manufactured from p-xylene by careful and specifi c air oxidation in a reactor at high pressure and elevated temperature. Liquid acetic acid, which is highly fl ammable, is used as a solvent for this reaction.
The crystalline PTA product is separated from the reaction liquor in separate crystalliser vessels and then recovered and purifi ed.
Gas analysis plays a vital role in the PTA production process, delivering the measurements that support product quality, process effi ciency, and safety.
The two critical measurements within the process are made at the oxidation reactors and the crystallisers.
Measurements at the oxidiser
Gas analysis at the oxidiser stage is focused on oxygen (O2), carbon monoxide (CO), and carbon dioxide (CO2). These measurements are primarily for safety, but they also focus on process control.
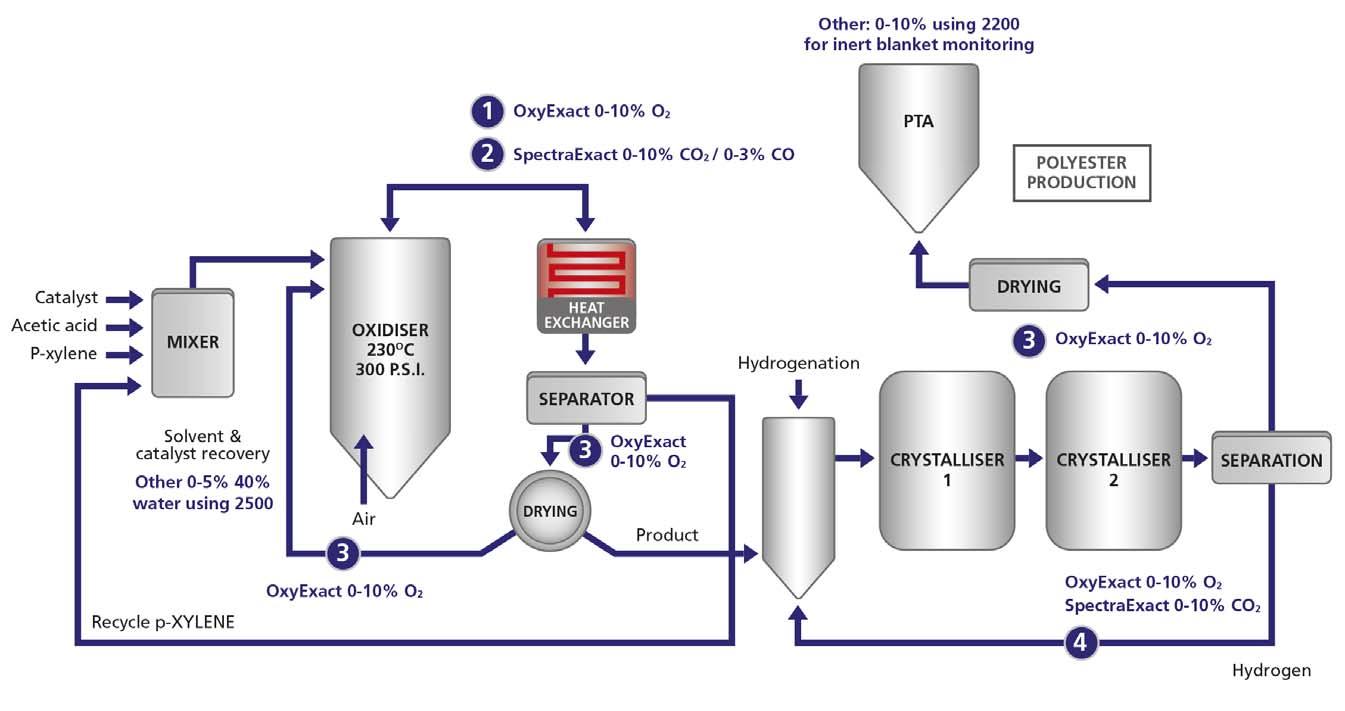
Figure 1. Purified terephthalic acid (PTA) application.
Air is passed into the oxidation reactors, oxidising the p-xylene to terephthalic acid and generating CO2 and carbon monoxide CO.
Some O2 remains unreacted, so the most critical gas analysis measurement is to monitor this residual O2 level in the off-gas (Figure 1, point 1), which should be around 4 – 5% O2. If the level rises too high, it means a dangerous situation could be developing in the reactor; sudden, runaway oxidation of the fl ammable materials could occur, resulting in an explosion.
However, if the O2 level is too low, then insuffi cient oxidation occurs, leading to poor effi ciency and a low product yield. To achieve the optimum results, the O2 level must be monitored with the best possible accuracy and the fastest response time – below 60 seconds, at least.
Additionally, many plants require a measurement of the CO2 level – and sometimes the CO level – in the off-gas (Figure 1, point 2), as this reveals more information about the progress of the oxidation reaction.
An infrared gas analyser can be used for this measurement, ideally confi gured to deliver simultaneous measurements for both CO2 and CO.
Because of the importance of the O2 measurement, the system must operate with minimal errors. Therefore, to ensure reactor safety, a voting system is used to monitor the O2 concentration (Figure 1, point 3 [multiple measurements]).
Voting systems use multiple analysers, and the process relies on the measurement agreed upon by the majority of analysers. Nearly all PTA plants use a three-analyser voting system, where if one analyser detects a signifi cant change, it is outvoted by the other two and no action is taken.
However, if two of the three analysers (or all of them) detect a change, this reading is held as correct, and action may be taken, ranging from informing the operator to automatically halting the process.
Voting systems provide an extra layer of reliability in safety applications, and also allow any problem with an analyser to be detected at an early stage without endangering the process. If two analysers agree on a measurement and the third differs, it indicates a potential problem that can be investigated and corrected before the process is affected.
Measurements at the crystalliser
Off-gas applications in the crystalliser are broadly similar, and use identical analytical solutions for the measurement of O2 and CO2.
The crystalliser measurements are all about safety. At this stage, acetic acid vapour is driven off as the PTA product crystallises out of the solvent liquor. Acetic acid is not just corrosive but highly fl ammable, so a measurement of the residual O2 in the crystalliser vapour is vital to provide a warning of any explosion risk.
Monitoring the presence of CO2 in this vapour (Figure 1, point 4) provides an indication of any post-oxidation that may be occurring, and so is a useful measurement. Dewpoint control is also very important to stop any sample condensing.
Gas analyser technologies
The off-gas from the process is generally at a pressure of >10 barg and a temperatures of 50˚C, so the area classifi cation required by gas analysis equipment may be ATEX Category 2 or 3 (Zone 1 or 2), depending on the plant conditions.
Gas analysis measurements are normally specifi ed on a dry basis with required ranges between 0 – 10% for O2, 0 – 5% CO2, and 0 – 1% CO.
Speed of response is critical for gas analysis in this application, particularly for the O2 measurement. Typically, 30 – 45 sec. for overall T90 of the complete system is required.
A paramagnetic analyser is recommended for the O2 measurements, as this sensing technology is highly specifi c to oxygen, and so delivers high levels of accuracy in the reaction conditions. It also offers a fast response to changing O2 concentrations in the reactor.
Paramagnetic cells each consist of two nitrogen-fi lled glass spheres, mounted on a rotating suspension within a magnetic fi eld. Light shines on a centrally-located mirror, and is refl ected onto a pair of photocells.
Because O2 is naturally paramagnetic, it is drawn into the magnetic fi eld, and so displaces the glass spheres, causing the suspension to rotate. This motion is detected by the photocells, which generate a signal to a feedback system. This, in turn, sends a current through a wire mounted on the suspension, creating a motor effect.
The current produced is directly proportional to the concentration of O2 within the gas mixture, allowing an accurate and linear percentage reading to be made.
As this technology is non-depleting, paramagnetic cells never need changing, and the performance does not deteriorate over time, with signifi cant benefi ts to ongoing maintenance costs and sensor lifespan.
For the other measurement needs, a single infrared analyser is usually suffi cient. Infrared sensing technology depends upon the property of some gases to absorb unique light wavelengths.
By focusing an infrared light source through a sample cell holding a continuously fl owing sample and onto a detector, after wavelength selection, it is possible to determine the concentration of a selected gas in a mixture.
Infrared sensing delivers a real-time measurement response and, like paramagnetic technology, is non-depleting, so has very low maintenance requirements.
Gas fi lter correlation (Gfx) sensing is an enhanced version of infrared sensing that offers a higher degree of accuracy where low-level measurements are needed or background gases may interfere with the measurement. It is often used to measure ppm CO in the reactor off-gas.
A well-designed sample conditioning system is also required to ensure the analyser is able to cope with the high-pressure, high-temperature off-gas, which will contain trace p-xylene and signifi cant levels of corrosive acetic acid vapour.
For both reactor and crystalliser measurements, the sample conditioning system must be well designed to ensure a fast overall response time, and to handle the signifi cant levels of condensibles in the sample, removing them prior to the measurement.
Sampling in the reactor off-gas stream also needs to correctly handle the high pressures involved. A water-washing ‘lute’ system may be used, and highly corrosion-resistant materials (e.g. titanium, Hastelloy) may be specifi ed for construction, because of the presence of acetic acid and possible catalyst traces.
Solutions for PTA
Servomex has provided gas analysis solutions for PTA production since the infancy of the process in 1987. Dozens of PTA plants around the world use the company’s technology for process control, safety, effi ciency, and emissions monitoring.
For O2 measurements, Servomex supplies the SERVOTOUGH OxyExact 2200, a high-performance paramagnetic analyser with an optional solvent-resistant cell, delivering an accurate, reliable measurement that is unaffected by fl ammable and corrosive solvent traces.
The analyser complies with Safety Integrity Level (SIL) 2 and is fully certifi ed for ATEX Category 2 or 3 (Zone 1 or 2) hazardous areas, including use with fl ammable samples. It operates across a wide ambient temperature range, with a good speed of response, typically delivering a T90 response time of 4 sec. Up to six O2 transmitters can be linked to a single control unit, making the technology a good choice for voting systems.
For single-component CO2 analysis, the SERVOTOUGH SpectraExact 2500 analyser series is an option, while a variant, the SpectraExact 2550, is used for dual-component CO2 and CO measurements.
Using infrared sensing technology, the SpectraExact offers a stable, sensitive performance with minimal cross-interference. The robust measurement cell is separated from the electronics, so the sample passes through it without damaging delicate instrumentation.
It has full certifi cation for ATEX Category 2 or 3 (Zone 1 or 2) hazardous areas regardless of the sample type, so the certifi cation is not affected by the fl ammable gases used in PTA manufacture. It operates over a wide temperature range, and has a rugged construction.
The SpectraExact 2500 can be used to measure water in liquid acetic acid as a quality control measurement, to assist with controlling the recovery and purifi cation of the acetic acid solvent before recycling.
Other measurements
While the reactor and crystalliser stages are the key measurement points in the PTA process for control, effi ciency, and safety, there are other points throughout the process where gas analysis is highly advantageous.
Ancillary plant operations, such as auxiliary boilers, may require measurements of O2 and combustibles in the fl ue gas, typically provided by a specialist combustion analyser, such as Servomex’s SERVOTOUGH FluegasExact 2700.
Emissions monitoring may also be needed to demonstrate that the plant complies with environmental regulations. A variety of sensing technologies exist to support this application. Servomex’s SERVOPRO 4900 multigas provides continuous multi-component measurements of criterion pollutants, greenhouse gases, and reference O2, using confi gurable digital sensors to meet plant requirements.
In addition to providing analytical instrumentation, Servomex Systems can deliver an entire, comprehensive gas analysis solution for PTA plants, with project management from design to installation and commissioning.
Conclusion
The volatile nature of key reactions in the PTA process emphasises the need for a ‘safety-fi rst’ mindset in the design and operation of the gas analysis system. By carefully understanding the risks in the process, and selecting both the appropriate measurements and best-suited sensor technology to apply to each point of analysis, a well-integrated gas analysis system will not only protect process and plant, but yield measurable effi ciency and emissions monitoring benefi ts.