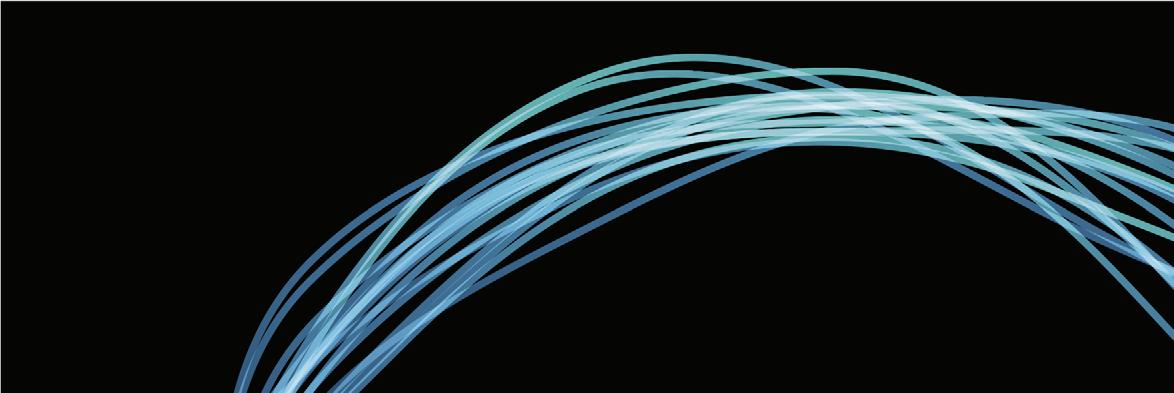
8 minute read
Isolating instrumentation
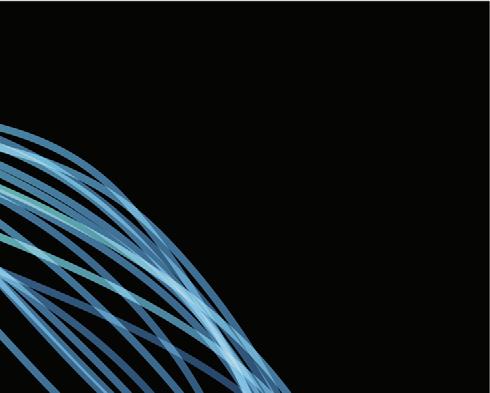
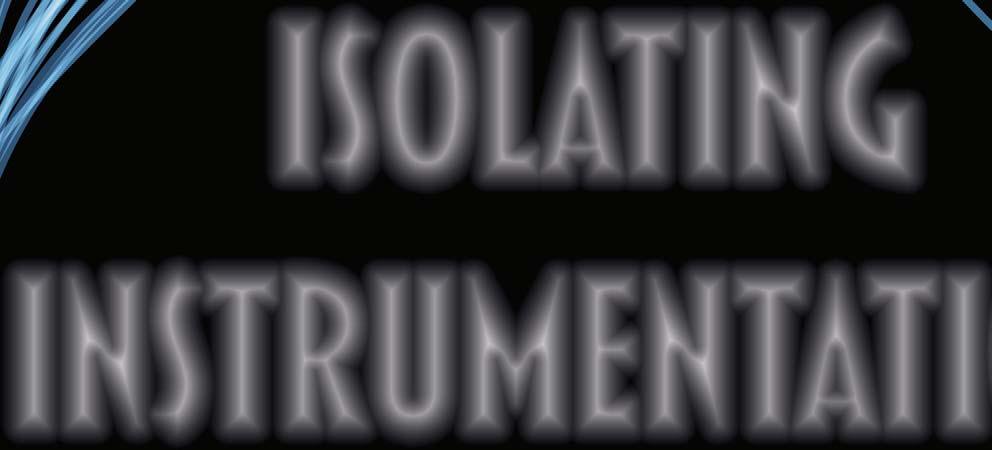
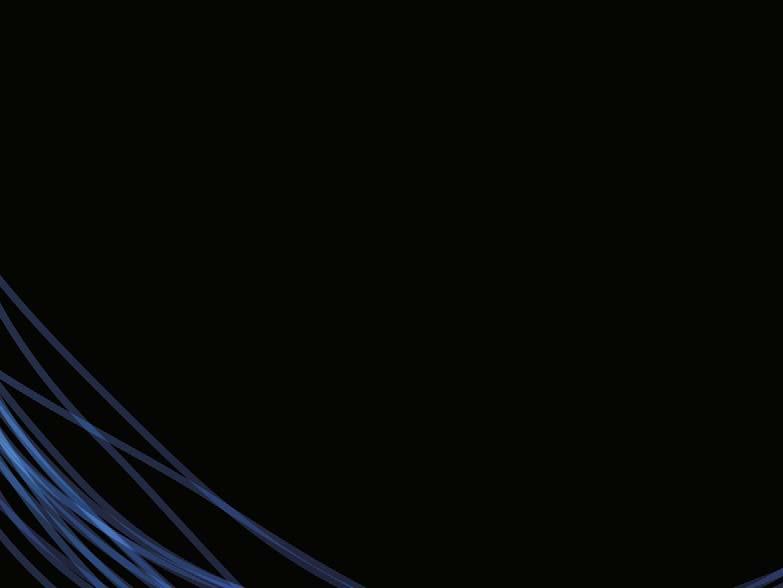
Tai Piazza and Greg Tischler, VEGA Americas, USA, present two case studies to emphasise the importance of being able to isolate instrumentation on a valve and still receive reliable level measurements.
High-value processes are found everywhere in the chemical industry. Massive storage vessels hold volatile yet precious chemicals, and base ingredients move through complex continuous processes to create all-important chemical components. In both scenarios – and everywhere in between – the ability to isolate instrumentation on a valve and still receive accurate and reliable level measurements is key to safe, continued operation. Two chemical plants with very different processes on opposite sides of the US were dealing with similar level measurement dilemmas: unreliable, high-maintenance instrumentation in processes that are costly to take offl ine.
Both facilities consequently employed the VEGAPULS 64.
They mounted the radar sensor on complex process connections, and it did not interfere with their measurement, due to the sensor’s 80 GHz technology.
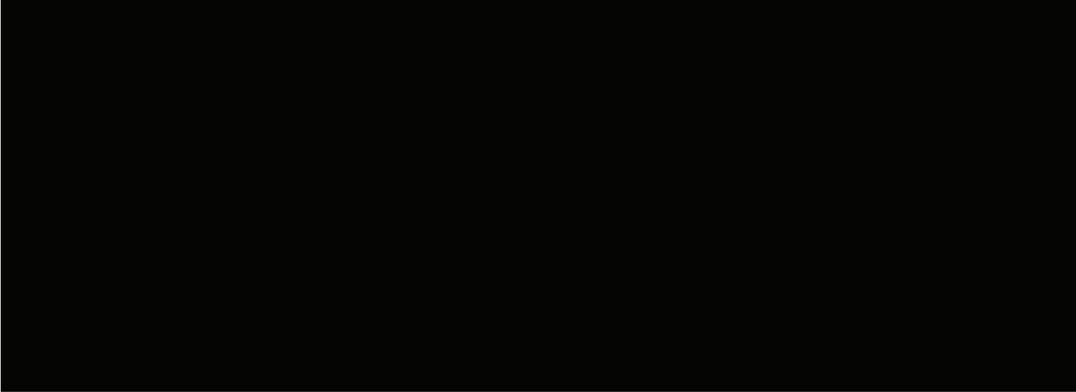
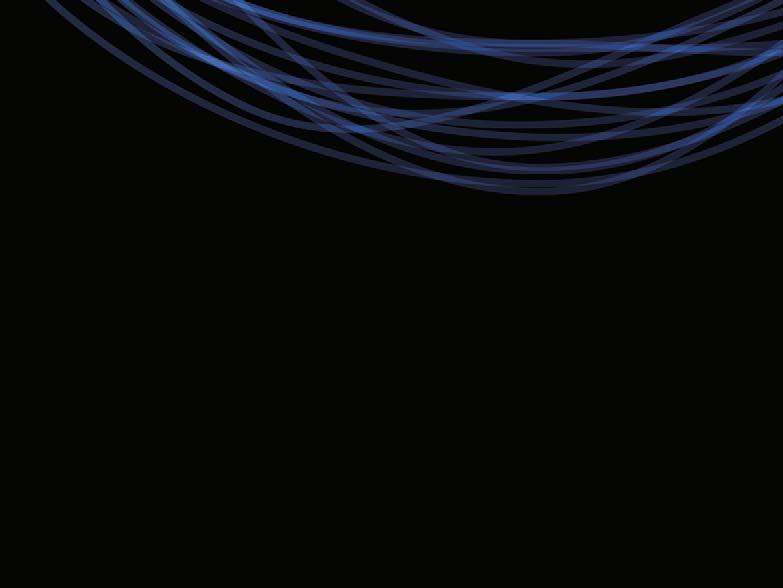
Measuring in tight spaces
High frequency radars for level measurements have several benefi ts, but when it comes to mounting on more complex process connections such as ball valves and knife gate valves, a highly-focused signal and narrow beam angle are important. A radar’s beam angle is determined by two factors: antenna size and transmission frequency. Both factors are inversely proportional to the radar beam. A larger antenna or a higher frequency will emit a tighter signal.
An 80 GHz radar sensor with a 3 in. antenna has a beam angle of less than 4°, enabling the sensor to emit an uninterrupted signal past the many refl ective surfaces and tight spaces found within a ball valve. Additionally, when more of the radar signal’s energy reaches the product surface below, the radar antenna will receive a stronger return signal to provide a more reliable measurement – even when it is measuring a product with poor refl ective qualities.
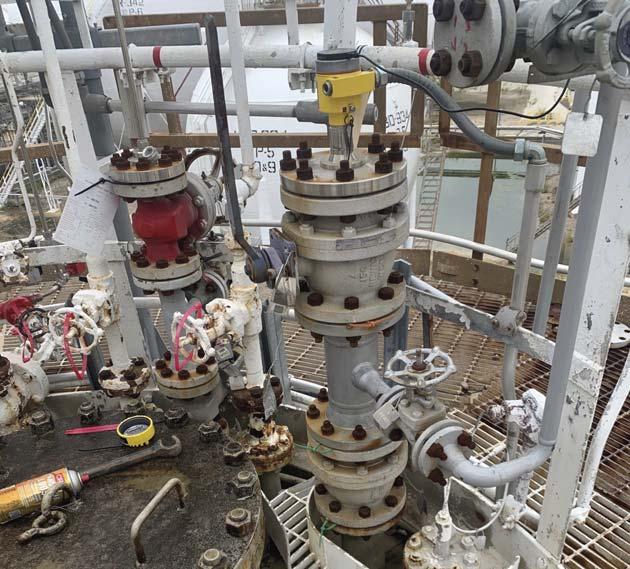
Figure 1. High frequency 80 GHz radar technology has allowed users to mount radar level sensors on increasingly complex process connections without sacrificing reliable, accurate measurements.
Figure 2. Radar level sensors using a lower 26 GHz frequency (left) lose their signal on the multiple surfaces within a ball valve. High frequency 80 GHz radar sensors (right) use a more focused beam angle, which enables the sensor to make a measurement through complex valves.
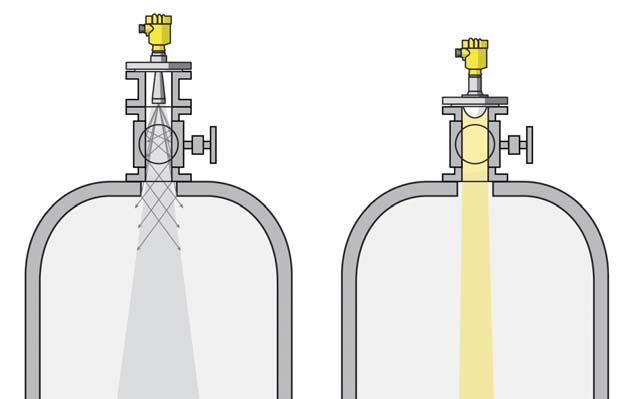
The VEGAPULS 64 has a high dynamic range, or sensitivity. The added sensitivity allows the radar sensor to output an accurate level measurement. This article will discuss the use of this technology in three different scenarios at two different chemical facilities.
A block and bleed valve for liquid gas storage
Along the Gulf Coast is one of the US’ largest oil and gas producers and petrochemical manufacturers. Storage tanks scatter the landscape, containing a variety of hydrocarbons, petrochemicals, and raw material chemicals. These vessels come in all shapes and sizes, but a group of massive 40 ft spheres stands out.
These spheres hold liquid butadiene, an important monomer used in the production of synthetic rubber, primarily for tyres. Butadiene’s physical properties make it a signifi cant fi re and explosion hazard, and in poorly ventilated areas, butadiene vapours can accumulate, displace oxygen, and lead to asphyxiation. To complicate matters even more, each sphere is continuously receiving off gases from other units, meaning that they are constantly being fi lled, requiring fi ne process control.
The Gulf Coast facility could not achieve the level of process control that it needed with its current level measurement instrumentation – a 26 GHz radar sensor. The radar sensor would only receive a weak return signal at best because of butadiene’s poor refl ective properties. With an unreliable measurement, operators needed a better solution.
This type of measurement conundrum is typically resolved by adding a stilling well to the vessel. The stilling well helps to focus the radar signal straight down to the surface of the product and direct more of the return energy to the radar antenna. A stronger return signal provides a more reliable measurement. However, the lengthy shutdown and excessive construction costs required for this solution make it unreasonably expensive.
Fortunately, a radar sensor with a higher frequency and resultant smaller beam angle could provide a more accurate and reliable measurement with a simpler, more cost-effective installation. Installers mounted and calibrated an 80 GHz VEGAPULS 64 on a double ball valve block and bleed assembly without having to drain the massive vessel or take it out of service. A measurement through this complex process connection is only possible because of the radar’s high frequency, small beam angle, and improved sensitivity.
A sticky, messy process
A chemical facility closer to the East Coast specialises in caprolactam, the primary feedstock in the production of nylon polymer used in carpet fi bres, plastics, and fi lms. A single step in making this all-important product involves adding a dry powder and water to a mixing vessel, which creates a substance with a sticky, cake batter consistency. The product inside tends to stick to any level measurement instrumentation, and regular cleaning is a necessity.
This process alone is a multi-million dollar continuous process, meaning that each maintenance shutdown is a costly endeavour. Until recently, expensive cleaning had become routine. An 80 GHz VEGAPULS radar sensor and a creative process connection saved this facility millions of dollars in lost revenue.
Operators installed a fl ushing ring and knife gate valve with the radar sensor mounted on top. The fl ushing ring shoots a burst of water on the face of the sensor to keep it clean. In instances of extreme buildup, maintenance crews can close the knife gate valve while the process continues to run, quickly clean the sensor, and return the sensor to operation. All of this is done without the huge expense of shutting down the process and draining the tank.
With other level measurement technology, pressure sensors would likely begin outputting erroneous measurements because of excessive buildup. A guided wave radar probe would have similar issues with buildup, requiring regular cleaning, but the sensor could not be isolated from the process. A non-contact radar with 26 GHz technology would lose its signal in the complex process connection, making a reliable measurement nearly impossible.
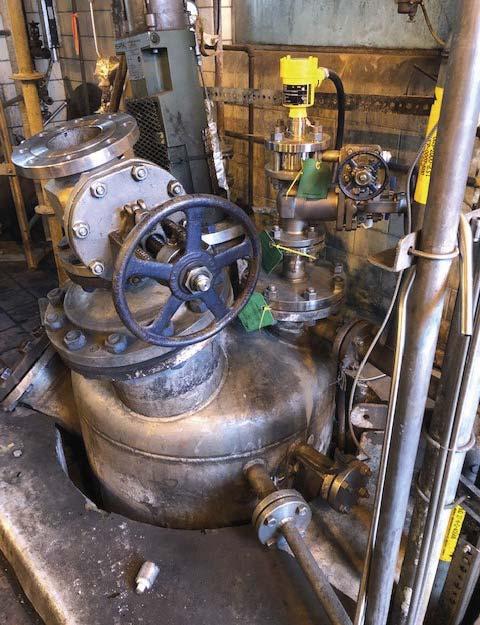
Figure 3. The knife gate valve isolates the 80 GHz radar level sensor from the process, so maintenance can clean the sensor as needed without stopping the process.
Figure 4. The bright yellow non-contact radar sensor replaced an old guided wave radar. Because of its focused beam angle, it was able to reliably make a level measurement in this bridle.
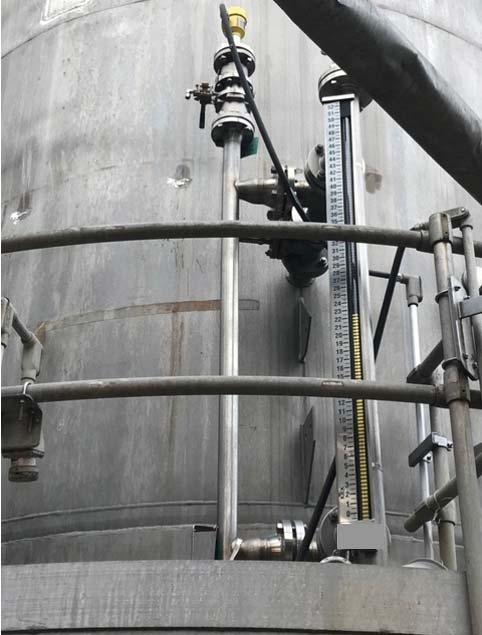
Measuring hazardous liquids in a bridle
The same East Coast chemical company stores nitric acid in large vessels to use within its many processes. To monitor the acid’s usage and maintain an adequate supply, the company monitors the level in two bridles on the side of the vessel. Different technologies are used in each of these bridles to provide redundant level measurements for additional safety.
In one bridle, a magnetic level indicator (MLI) is used for an easy, non-electronic visual representation of the level measurement. In the other, the company had been using a guided wave radar. The guided wave radar worked, but maintenance employees had no way of safely servicing or cleaning the sensor without stopping the process.
Operators wanted a level measurement sensor that could be isolated from the corrosive materials it was measuring. To do this, however, the new technology would have to be non-contact and have the ability to make accurate, reliable measurements in the tightly enclosed space of the bridle. Already familiar with the 80 GHz VEGAPULS 64, the company enquired about testing the sensor and pushing its limits in such an enclosed space.
During the installation, technicians installed a double block and bleed valve to isolate the process from the sensor when necessary. The VEGAPULS 64 began receiving a strong return signal immediately. The new non-contact radar sensor provided an accurate measurement despite the uphill battle.
When an isolated, non-contact measurement is paramount
At both chemical facilities, isolating level measurement instrumentation was critical to their process.
On large storage vessels, a double block and bleed process connection with the 80 GHz VEGAPULS 64 mounted on top is an excellent solution. With the radar sensor mounted this way, operators can remove the instrumentation, perform maintenance, or swap it out entirely without ever emptying the vessel. Operators only receive a small interruption in level measurements while the sensor is offl ine, and there is no need for a process shutdown.
At the same time, high-value processes can mount the 80 GHz VEGAPULS 64 to a fl ushing ring and knife gate valve to minimise downtime for cleaning and maintenance. Creatively mounting the sensor like this keeps the process running longer with fewer shutdowns, and operators continue to receive a consistent level measurement.
When it comes to corrosive substances, the high focus of 80 GHz radar allowed the East Coast facility to use radar technology on an existing bridle. The facility was also able to add a block and bleed system to improve employee safety without sacrifi cing measurement reliability or accuracy.
For many applications, isolating instrumentation is a necessity for safety or monetary reasons. Regardless of the purpose, an 80 GHz radar mounted on a ball valve, knife gate valve, or a more complex block and bleed valve provides a safe and cost-effective solution that operators can depend on.