
9 minute read
Safety blanket
Jim DeLee and Richard Koeken, Fluid Components International, USA, discuss the importance of thermal flow meters for safety-critical nitrogen tank blanketing.
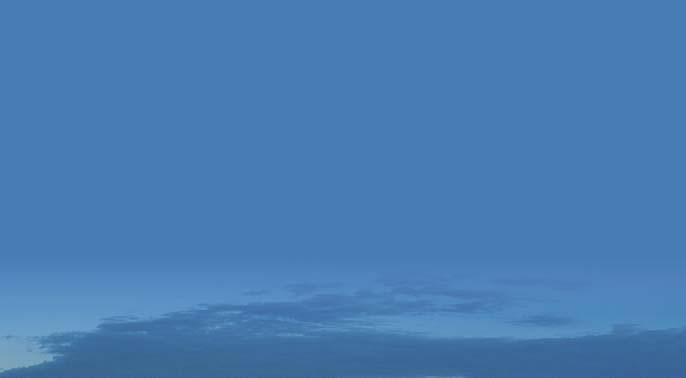
Marine tanker terminals and their frequently adjoining refi neries rely on nitrogen gas tank blanketing to maintain a safe operating environment as oil/gas products are transported, processed, stored and distributed for use. Nitrogen blanketing is a practice commonly used in the chemical and petroleum refi ning industries to reduce the hazards associated with fl ammable liquids, which improves the safety in the plant and can help increase productivity.
The ‘blanketing’ or ‘padding’ is a process of applying inert nitrogen gas to the vapour space of a tank or vessel. This precautionary step minimises the possibility of an explosion or fi re by reducing the oxygen content or the concentration of fl ammable and/or explosive vapours in a tank or vessel with inert nitrogen. In concentrated marine terminal, refi nery and storage areas, safety is critical to prevent large scale fi res and explosions.
Furthermore, blanketing also helps decrease product evaporation and protects the tank from structural corrosion damage caused by air and moisture. Nitrogen usage varies based on the size of the tanks and vessels used in the production, transfer, transportation and packaging of the product.
There are several common types of blanketing: continuous purge, pressure control and concentration control. The continuous purge method employs a constant fl ow of nitrogen. This approach is simple, but nitrogen consumption is high. The pressure control and concentration control methods are more costly to implement and rely on the pressure in the tank or the concentration of the oxygen to initiate the fl ow of nitrogen, but these methods improve overall safety and the effi ciency of the process. Fluid Components International’s (FCI) mass fl ow meters are used in all three of these types of purging methods.

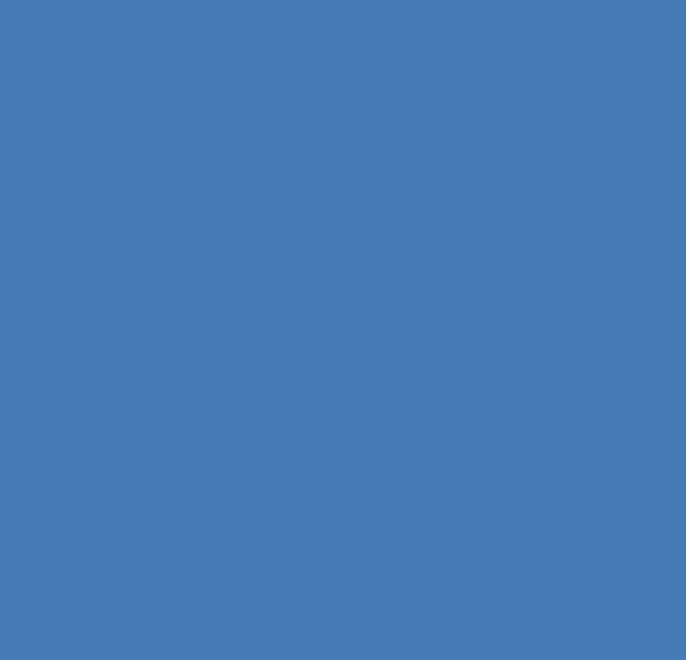
Challenges
Terminal and refi nery engineering teams are generally concerned with measuring the fl ow rate of nitrogen accurately and dependably in their tank blanketing operations. The blanketing process is important in tank storage applications

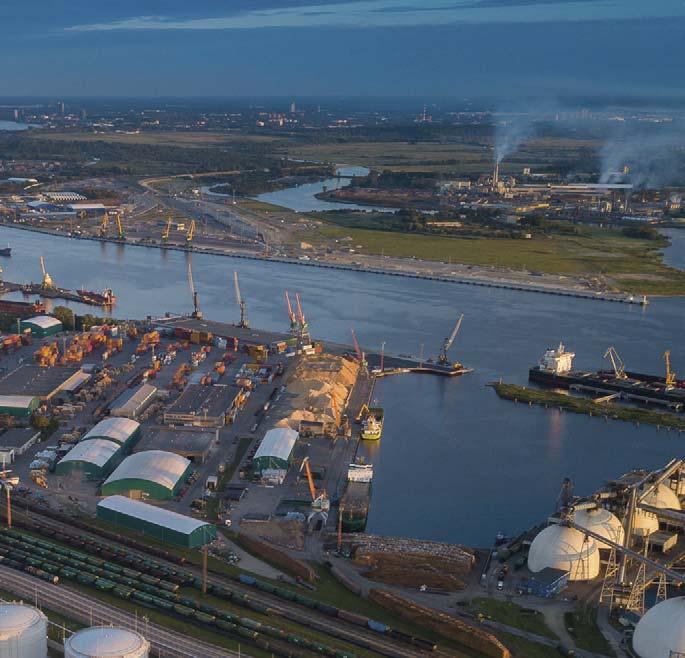
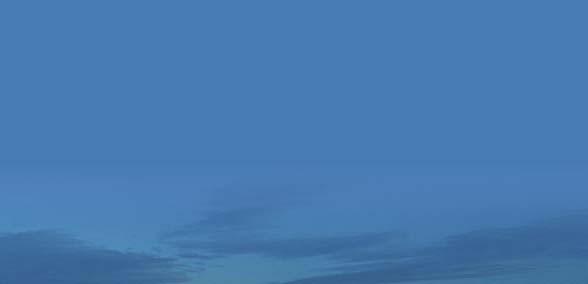
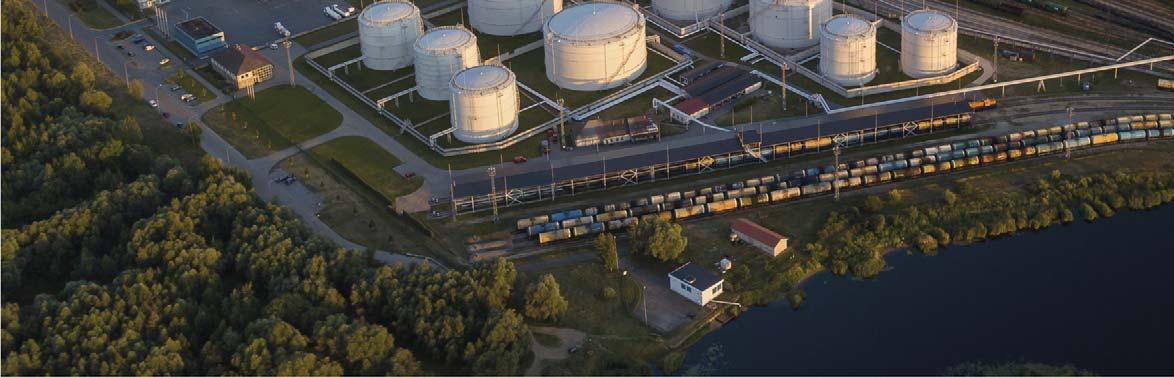
due to the possibility of static electricity build up, and the nitrogen displaces one leg of the fi re triangle. Implementing the pressure control system satisfi ed the plant team’s major concern, which is always safety fi rst.
The consequences of a major accident at a marine terminal and adjoining refi nery have the potential to result in a major loss of life, destruction of expensive equipment and damage to nearby populations and communities. In addition, the shutdown of such a facility can have a crippling effect on any region where energy supplies are tight or where there are limited additional supplies. Beyond these consequences, a prolonged smoky fi re has the potential to cause further harm to the environment through global warming and the run-off consequences of stored petroleum fl uids can cause major harm to marine life in the area.
Any time combustible, fl ammable or explosive materials are stored, processed or generated, the use of nitrogen tank blanketing helps to prevent these materials from coming into contact with oxygen in the air. The inert blanket of nitrogen gas creates a non-fl ammable environment, which prevents the possibility of fi re or explosion, and therefore provides protection to nearby people, equipment and entire facilities.
The other reasons that port teams want more accurate gas fl ow measurement are to improve effi ciency, to lower the plant’s nitrogen consumption and costs, and to eliminate any unexpected supply shortages. After facility safety to protect people and equipment, controlling facility consumables costs is always a top priority in any business.
The quantity of nitrogen pumped into or released out of the tank’s vapour space is controlled by a predetermined pressure set point. When product is pumped from the tank, the vapours inside expand and the pressure falls below the set point, and additional nitrogen is then introduced. As the tank is fi lled, the vapours begin to compress and the nitrogen vapours are released and usually sent to a vapour recovery system. In practice, it is demonstrated that there can also be minor leakages in the nitrogen blanketing system, reducing the pressure in the vessel over time. When the pressure falls below the set-point, a small top-off nitrogen fl ow is introduced in the vessel to increase the pressure above the set-point.
When tank product falls and rises, it can create static electricity. Therefore, the amount of nitrogen in this vapour space is an extremely important safety factor. Typically, oil/gas marine ports and refi neries require a fl ow meter that can provide a mass fl ow output, measure a low fl ow rate of 1 – 17 normal m3/hr (36 – 600 standard ft3/hr) at 70°C (158°F) with a pressure maintained at 5 bar(g) (60 psig) in a 25.4 mm (1 in.) schedule 80 pipe with limited straight-run. With these process requirements, the gas fl ow meter choices available narrow to some degree.
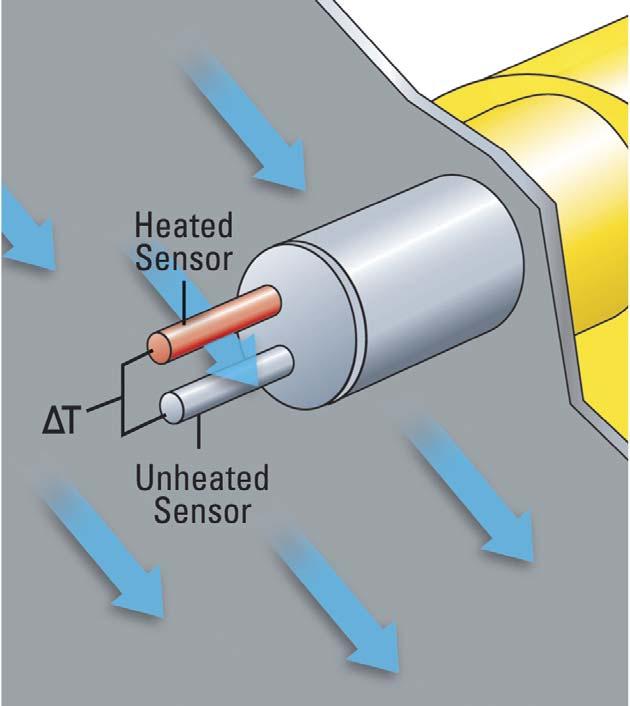
Figure 1. Thermal dispersion principal of operation.
Solutions
Figure 2. Nitrogen tank blanketing process on refinery tanks. Typically, the engineering team at an oil/gas marine terminal or adjoining refi nery will need to work with a fl ow meter manufacturer’s application engineering team to consult on their specifi c tank blanketing needs. Discussions will include any specifi c problem issues or goals and then review a facility’s overall operating environment.
After completing this process with FCI, the team at a large terminal chose the model ST100AL thermal dispersion air/gas in-line mass fl ow meter and the Vortab® fl ow conditioner with an accuracy of +/-0.75% of reading, +/-0.5% of full scale with a maximum of 5% of reading. This fl ow meter is an inline, spool piece gas fl ow meter for industrial process and plant applications, which combines good transmitter/electronics and calibration with a built-in fl ow conditioner and a standard turndown ratio of 100:1 (optionally 1000:1). The integral Vortab fl ow conditioner provided a low-pressure loss solution for fl ow profi le irregularities produced by elbows, valves, and other disturbances that are commonly present at terminals and refi neries. When suffi cient pipe straight run is not available to generate the necessary fl ow profi le, the fl ow conditioners combine proven swirl removal technology with a unique mixing process to achieve effi cient fl ow conditioning.
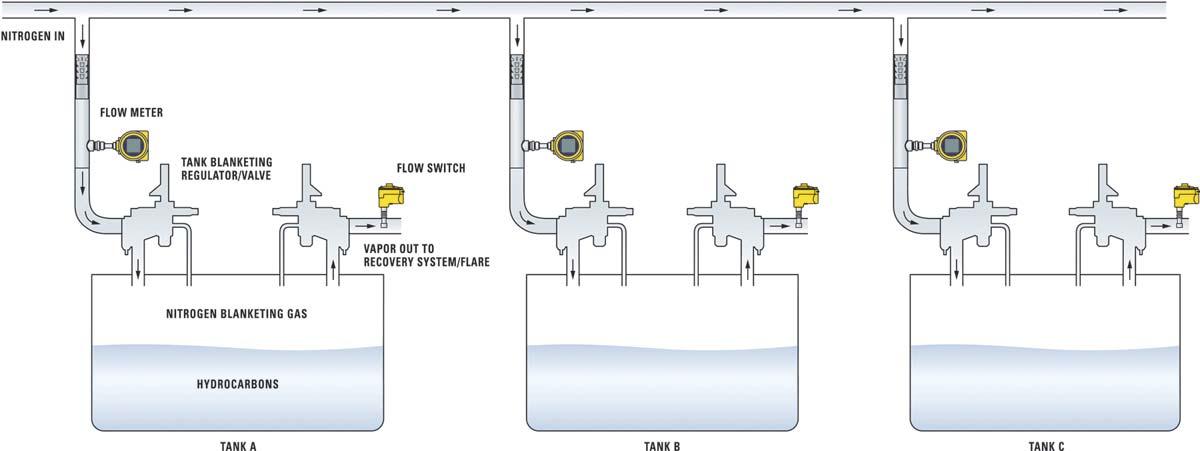
Tabs are located strategically within the conditioner. They promote rapid mixing that creates a uniform fl ow profi le for proper meter fl ow measurement by eliminating swirl and distortion or any other profi le irregularities that could be present through the transitional fl ow range (Reynolds’ Number 1000 – 4000).
The ST100AL fl ow meter is factory calibrated in FCI’s NIST and ISO17025 traceable calibration laboratory for nitrogen service. The laboratory includes multiple calibration stands and is capable of calibrating in virtually any other process gas as well as mixed gases or fl uid-entrained gases.
Once installed, the use of a thermal fl ow meter provides the accurate, repeatable and reliable output under all fl ow conditions (low fl ow during top-off fl ow and high fl ow during re-fi lling of the vessel) necessary for the tank blanketing system to operate as designed and to provide the safety and cost savings expected in this application.
The ST100A insertion style air/gas meter has the same accuracy specifi cations as the ST100AL, but allows the end user the capability to insert the probe directly into the line. This provides a solution for applications with larger lines.
Up to fi ve calibration groups can be stored to support a broad fl ow range, differing same gas mixtures, multiple gases, with a fl ow range of 100:1 (optionally 1000:1). An on-board data logger is included with a removable 2 GB micro-SD memory card to store process fl ow data.
Users may select from three 4 – 20 mA analogue outputs, frequency/pulse, or certifi ed digital bus communications such as HART, FOUNDATIONTM Fieldbus, PROFIBUS PA or Modbus RS-485 ASCII/RTU. Should a plant’s communication need to change in the future, the ST100AL meter can be fi tted with a replacement card that can be installed by technicians in the fi eld.
For ease of local on-site data view, the meter also features a graphical, multivariable, backlit LCD display/readout. It provides local information with a continuous display of all process measurements and alarm status, as well as service diagnostics.
Designed for rugged industrial applications, it operates at up to 125°C (257°F) and is available with both integral and remote (up to 300 m [1000 ft]) electronics versions. The entire instrument is SIL 1 compliant (IEC 61508) and has been agency approved for hazardous environments. The enclosure is NEMA 4X/IP66/IP67 rated. Ex approvals include FM, FMc, ATEX Zone 1/21, IECEx Zone 1/21, INMETRO (Brazil) and EAC/TRCU 12/20/32.
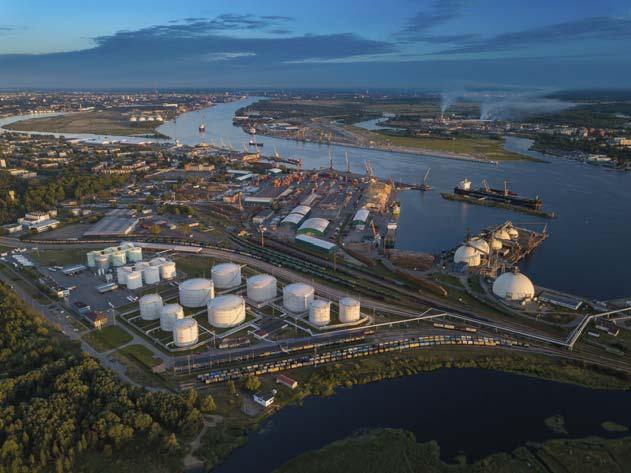
Figure 3. Marine terminal with petrochemical, refining and storage tanks.
Figure 4. Model ST100AL thermal mass flow meter with Vortab flow conditioner.
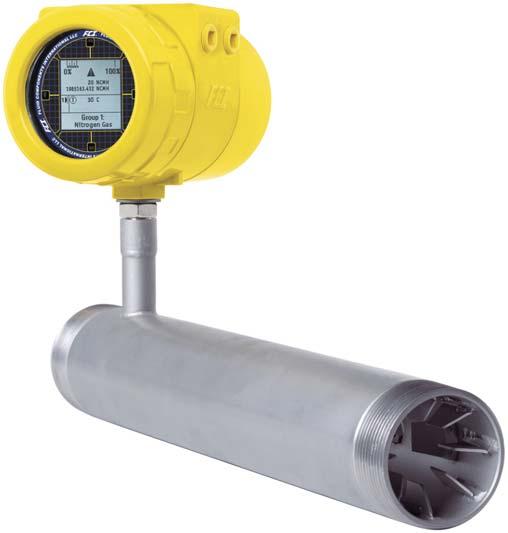
Thermal dispersion sensing
Mass fl ow meters such as the ST100AL are designed with rugged and reliable thermal dispersion sensing technology, which provides direct mass fl ow measurement. This technology places two thermowell protected platinum RTD temperature sensors in the process stream.
One RTD is heated while the other measures the actual process temperature. The temperature difference between these sensors is varying or maintained based on the media cooling effect. FCI thermal dispersion fl ow meters can provide mass fl ow rate measurement without the need for additional pressure or temperature transmitters (Figure 1).
With direct mass fl ow sensor technology, the thermal fl ow meters also include built-in real-time temperature compensation, which ensures repeatable measurement even in applications where wide process seasonal temperature variations are present, such as in some marine terminals in continuous operation throughout the year (summer and winter).
With no moving parts or orifi ces to plug, foul or wear, thermal mass fl ow meters are virtually immune to dust and dirt. The instruments are almost maintenance-free.
Conclusion
ST100AL fl ow meters have been installed in marine terminals around the globe in multiple nitrogen tank blanketing applications. The fl ow meters provide accurate mass fl ow measurement with limited straight run, which provides a safe environment in the processing, storing and generating of their fl ammable and combustible products.
Multiple terminal and refi nery operators have also reduced their nitrogen consumption considerably, which in turn reduced their overall operating costs of consumption.