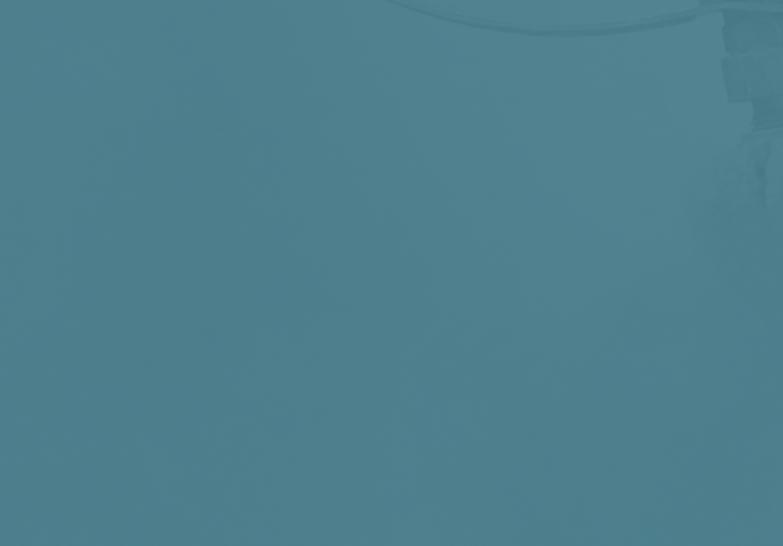
8 minute read
To spray or not to spray?
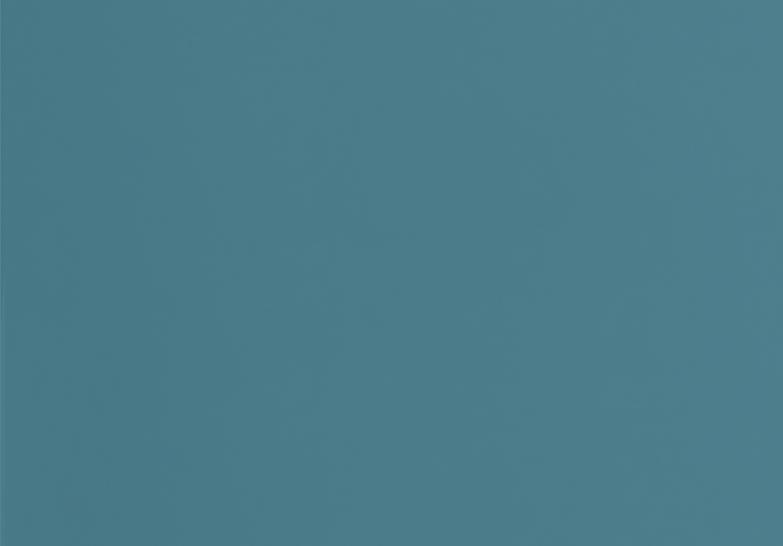

Ian Wade, Belzona Polymerics, UK, outlines the benefits of protecting storage tanks with sprayable, polymeric coatings.
Aslow-down in bulk liquid usage is putting increasing pressure on tank farm assets to either maintain, replace, or expand their current storage tank capacity.
In these unprecedented times, maintenance and inspection of tank integrity may be overlooked or ignored. This is especially true for newer tanks, as these should be constructed with the addition of a corrosion protection lining. However, this is not always the case due to costs or the expectance that any corrosion allowance will be minimal.
There is an added pressure on the turnaround times of any planned scheduled maintenance or inspection intervals. These also may be delayed, resulting in reactive measures (such as weld repairs or the introduction of a lining) which can cause irreversible deterioration of the substate with through-wall defects and loss of containment, ultimately landing the asset owners with hefty costs and fi nes.
If planned maintenance does go ahead, it is important to identify the following key areas to sustain the fi t-for-purpose use of storage tanks.


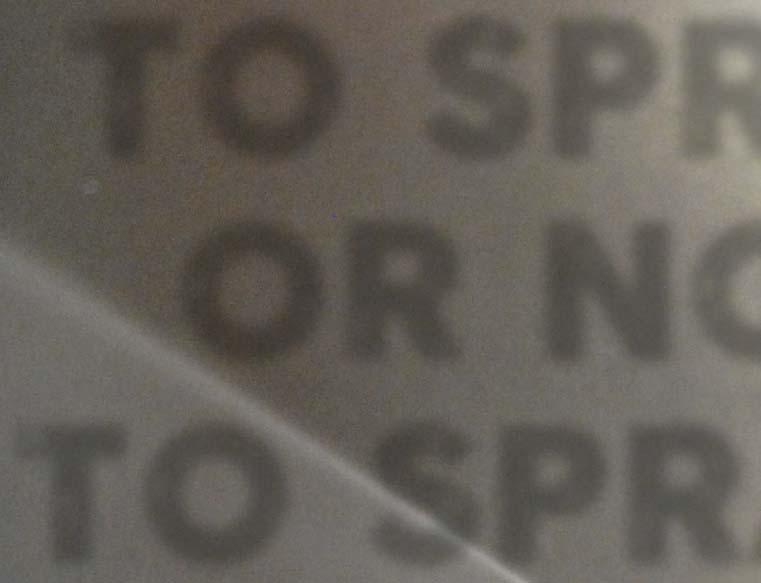
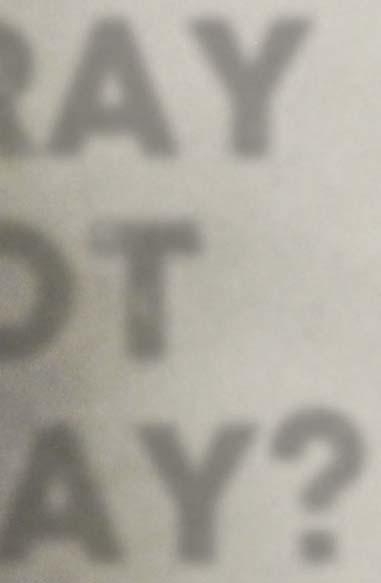

Pitted areas
If the internals of the tank steel are exposed, or a less suffi cient coating is used, then pitting corrosion can occur.
Exposed steel is more susceptible to corrosion and chemical damage. The pits can become either wide and shallow or narrow and deep, which can quickly affect the wall thickness of the steel, becoming penetrated and requiring immediate action. Pitted areas can be repaired by weld overlay or welding a plate over the top, but these may have inherent issues such as heat affected zones (HAZ). The intense process of heating and subsequent cooling of the substrate can generate weaknesses in the metal and limit the structural integrity at the weld point.
Cold applied epoxy repair composites can be utilised to repair deep pits quickly, restoring large areas to their original profi le and avoiding the need for hot work.
Weld and seams
The causes of failure of welded structures are often associated with low quality joints. The defects arise from deviations from the principles of welding technology, the use of inadequate primary techniques, additional welding material, or poorly qualifi ed welders.
There are several common weld deposit/base metal combinations that are known to form galvanic couples. Even when special care is taken to select the materials, certain environments can worsen the issue.
To eliminate the need for any welding repairs, epoxy-based paste grades in conjunction with reinforcement sheets can isolate the weld seams and protect them from any further corrosion.
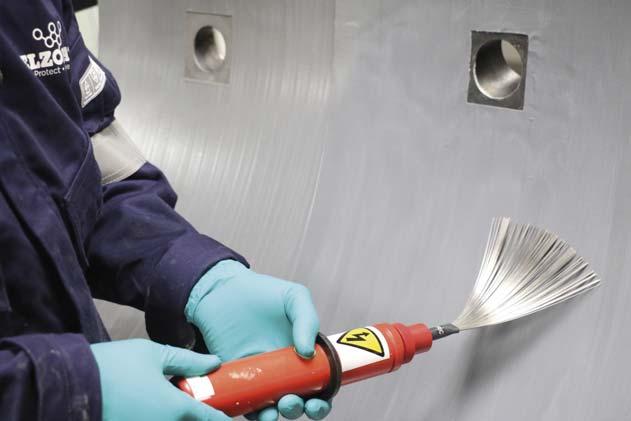
Figure 1. A high voltage spark tester.
Table 1. Suggested voltages for high voltage spark testing
Total dry film thickness Suggested inspection μm mils Voltage
200 – 280 8 – 11 1500
300 – 380 12 – 15 2000
400 – 500 16 – 20 2500
530 – 1000 21 – 40 3000
1010 – 1390 41 – 55 4000
1420 – 2000 56 – 80 6000
2060 – 3180 81 – 125 10 000
3200 – 4700 126 – 185 15 000
Conventional linings
Conventional linings can provide limited chemical resistance at high temperatures. However, they also contain solvents which can complicate applications from a health and safety point of view, with specialist environmental controls required – especially in the confi ned spaces of a tank.
If a lining system, such as glass fl ake, is damaged or fails in service, it is very diffi cult to perform isolated repairs. Generally, the full system would require removing before applying a new system.
The root causes of coating defects such as delamination, blisters, cissing and cracking need to be identifi ed in order to avoid triggering further problems in the connecting pipelines or fi ltration systems.
Cleaning regimes
Cleaning regimes are an often-overlooked factor when renewing or rejuvenating current assets. Ultra-high pressure washing at elevated temperatures and the potential use of strong chlorinated chemicals can cause penetration into the coating, resulting in swelling, softening and even dissolving of the coating. In this case, before any inspections of the coating take place, it would be visually evident that the tank will require full replacement.
To spray or not to spray?
Full lining of the tank may be ideal, but it is not always an option. In some instances, heated oil storage tanks can contain traces of water which corrode the bottom of the tank. At elevated temperatures, this can increase the rate of corrosion expected. As a minimum, internal linings can be applied 1.5 m from the bottom of the tank up, as there tends to be higher levels of corrosion in this area. This is also useful for when maintenance budgets are tight, and may also save costs for the asset owner without the need for scaffolding or platforms to be erected and dismantled while applying any coating system.
If a tank is storing liquids or gases, or creates a vapour phase due to heating, then a full lining of the tank, including the roof, is the only option.
When selecting a corrosion protection lining for storage tanks, a few keys requirements should be considered: Quick and easy application. Corrosion protection. Chemical resistance. High temperature resistance. Inspectable and easy maintenance.
Conventional sprayable ceramic-fi lled coatings not only cause extensive damage to spray equipment, but
also provide a limited level of erosion corrosion protection. However, improvements in sprayable epoxy technology mean that they can be sprayed more quickly, offer more fl exibility, and create a higher fi lm build-up and higher temperature resistance if required.
Sprayable epoxy systems have been proven to reduce downtime and enhance return to service, whilst also offering 24-hour overcoating windows, reducing the pressure infl icted on applicators to apply a two-coat system. Solvent-free materials also allow it to be safely applied in confi ned areas, with chemical resistance against a wide range of chemicals including hydrocarbons and amines.
With the use of standard airless spray equipment, epoxy linings can be applied effortlessly, but only if the correct set-up has been achieved. For instance, the water temperature for the heat trace lines that introduce heat into the coating as it travels from the pump to the spray gun, thus lowering its viscosity, need to attain a spray tip temperature between 40 – 45°C. The correct inlet pressure for pumps with ratios from 56:1 up to 80:1 and the correct spray tip are all crucial for any spray application to run successfully.
The expected wastage factor involved with spray applied coatings using single leg airless spray equipment can be in the region of 30 – 40% due to the lining being pre-mixed before entering the pump. This is lower for plural systems, as unmixed material is pumped to a mix manifold before making its way through a minimum 15 m whip line. This includes two inline fl uid mixers to further mix the components before reaching the spray gun, meaning that any wastage is within the 15 m of lines with the added benefi t of being able to recirculate the unmixed material back into the relevant tins.
In comparison, a hand applied wastage factor can be 10 – 20%; however, the possible coverage achievable is less. This can be up to 10 times quicker with spray applications than hand.
The skill of the sprayer will also determine the uniformity of the applied coatings. If applied too thin, the coating may not perform for as long as expected. If applied too thick, it can eat away into potential savings and could cause issues in service.
On the completion of any linings, it is important to visually inspect the coatings for any misses or debris when the lining has achieved its minimum cure or hardness. Further inspection can then proceed.
Most coating inspections used to confi rm continuity are carried out with a high voltage spark tester/holiday detector (Figure 1) in accordance with international standards (such as NACE SP 0188) which, following the manufactures guidance, can be set at the expected minimum thickness of the coating (Table 1). Once the probe passes over a fl aw or pinhole, completing the circuit to the earth return, an alarm will be set off. The coating inspector or maintenance team will mark these areas for remedial work which, if the lining’s overcoat window allows, can be easily applied over the marked-up area without any surface preparation. All these steps can ensure full longevity of the lining.
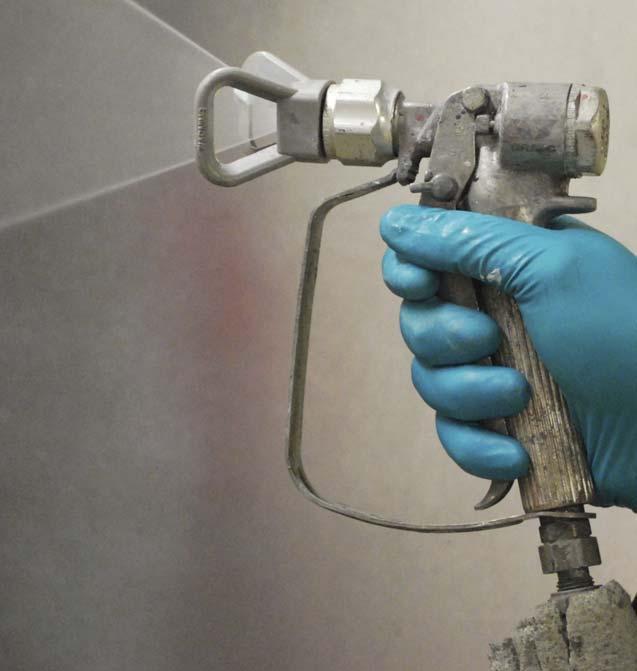
Figure 2. A Belzona polymetric coating being spray applied.
Return to service
The importance of return to service is crucial for asset owners. Once the lining has achieved a certain level of cure, the asset can be placed back into service. In some cases, assets can be back to service within less than 24 hours of the final application due to the chemical nature of epoxy systems.
When mixed, epoxy systems cure through chemical exothermic reactions. This is generally done at ambient temperatures, but there may be circumstances where a quick return to service is desired. The client can post/force cure the epoxy linings in service if the required level of temperature can be reached. This allows any free polymers to find other free polymers, achieving better cross linking and ultimately improving the chemical or temperature resistance of the applied lining.
When a lining is subjected to service conditions, this can affect a coating’s lifespan. Sprayable epoxy systems are easy to inspect at any time during their expected life expectancy using dry film thickness (DFT) gauges, high voltage spark testers, ultra-sonic (UT) gauges or Xray machines, making any scheduled maintenance checks seamless.
If the thickness of the lining has been reduced by erosion, general defects from mechanical damage, or is simply coming to the end of its service life expectancy, straightforward remedial work can be performed on the coating, potentially without the need for a full replacement of the lining.
In conclusion, sprayable 100% solid epoxy systems can be utilised to speed up application time with the use of standard spray equipment while simultaneously reducing overall costs. The maintenance and easy inspection of the lining is paramount to ensuring a long useable life of the lining.