
12 minute read
Turning the corner
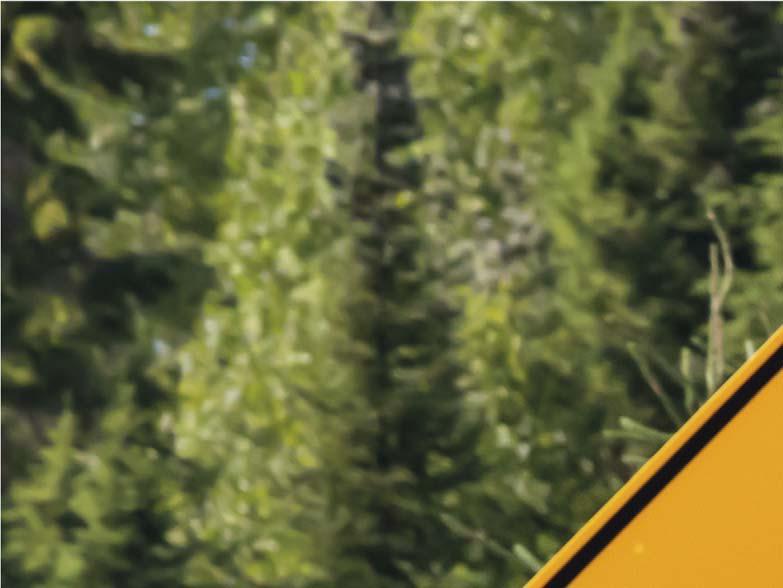
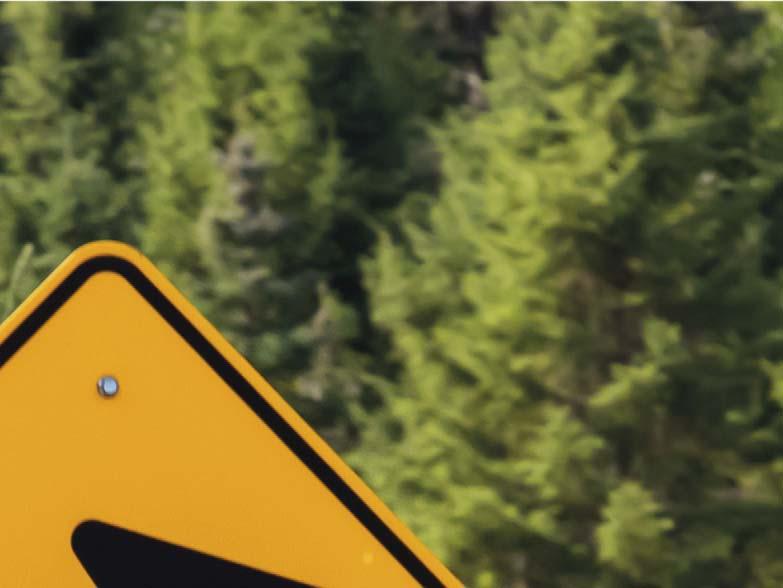
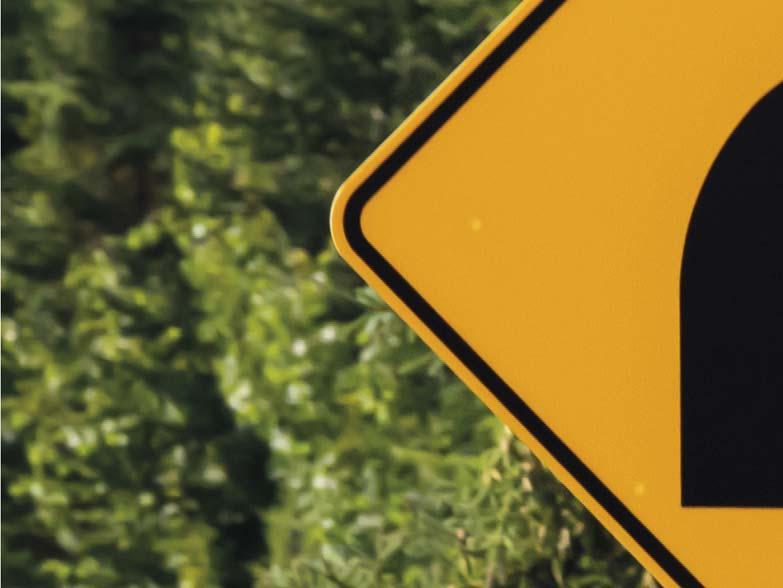
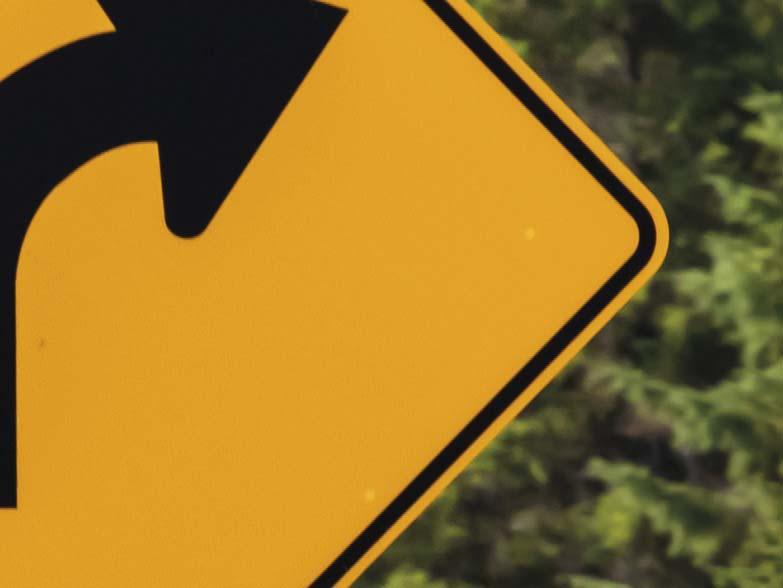
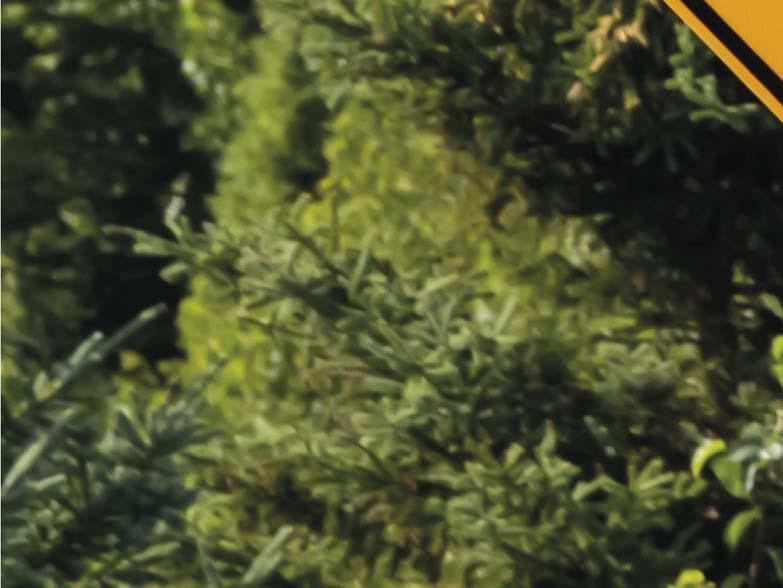
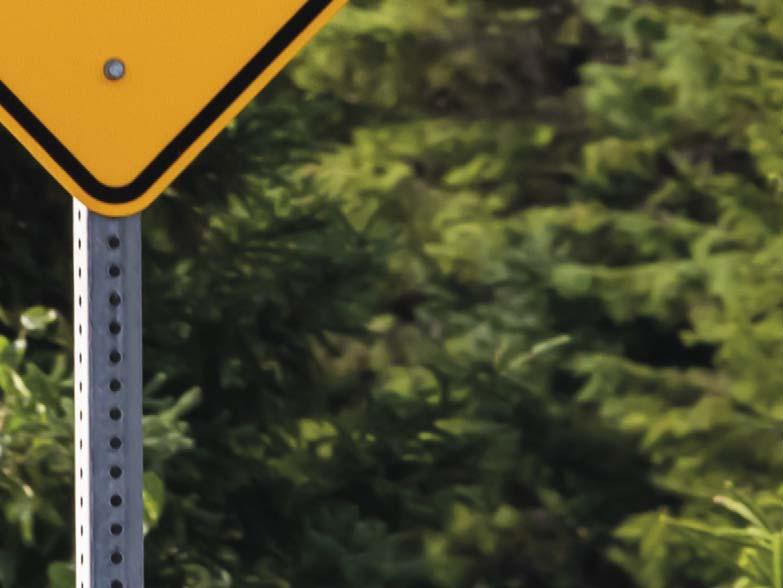
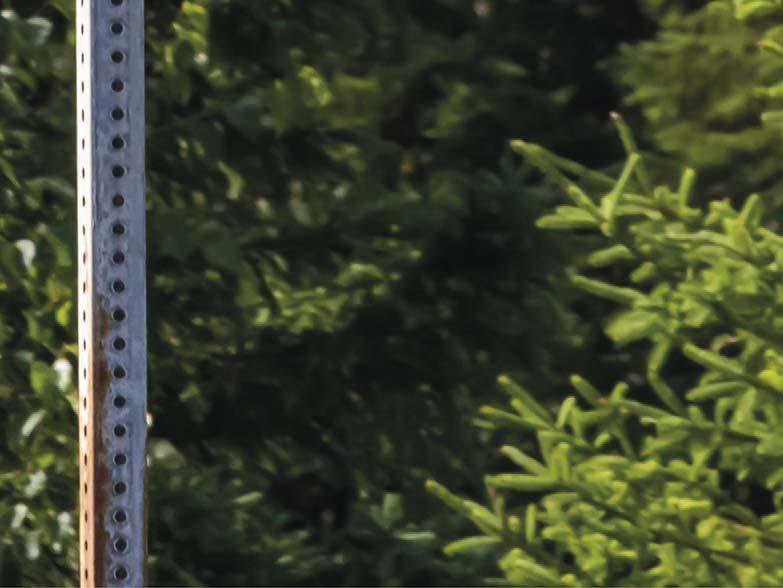
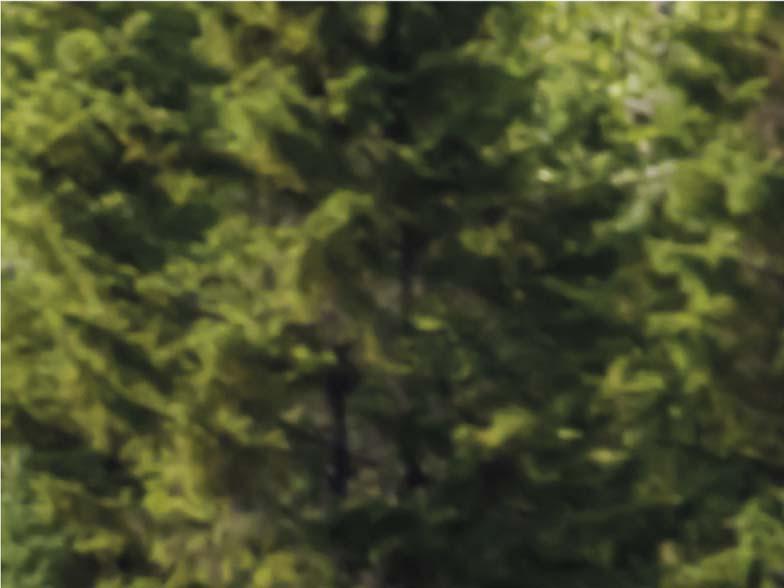
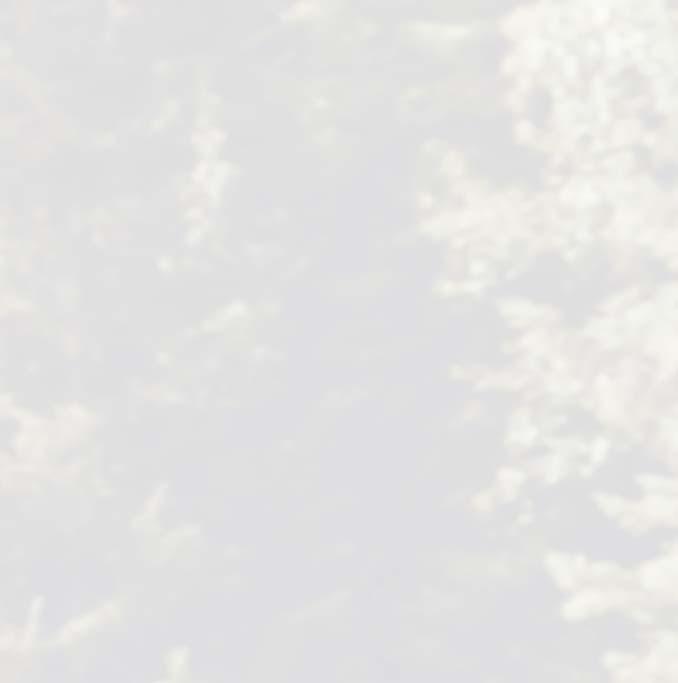
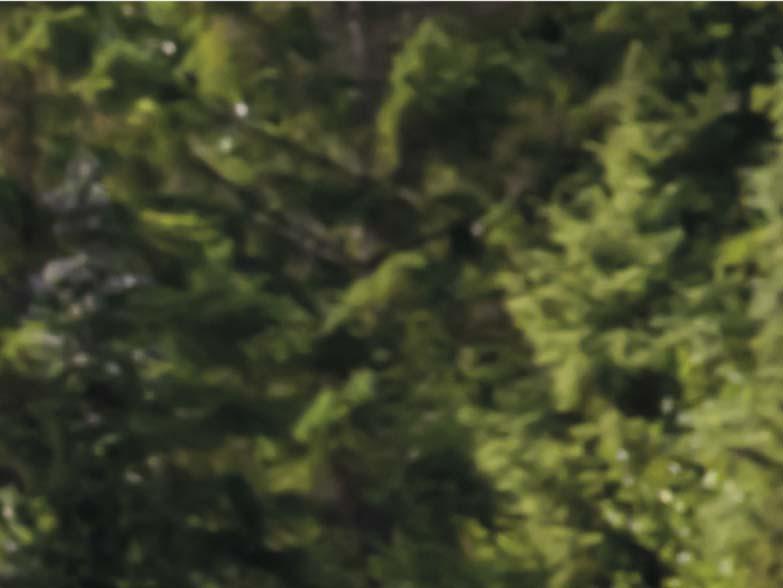

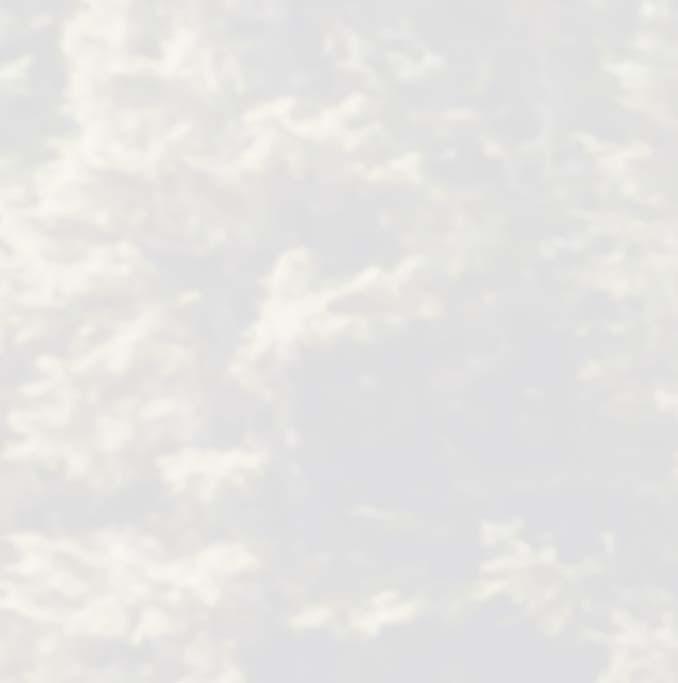
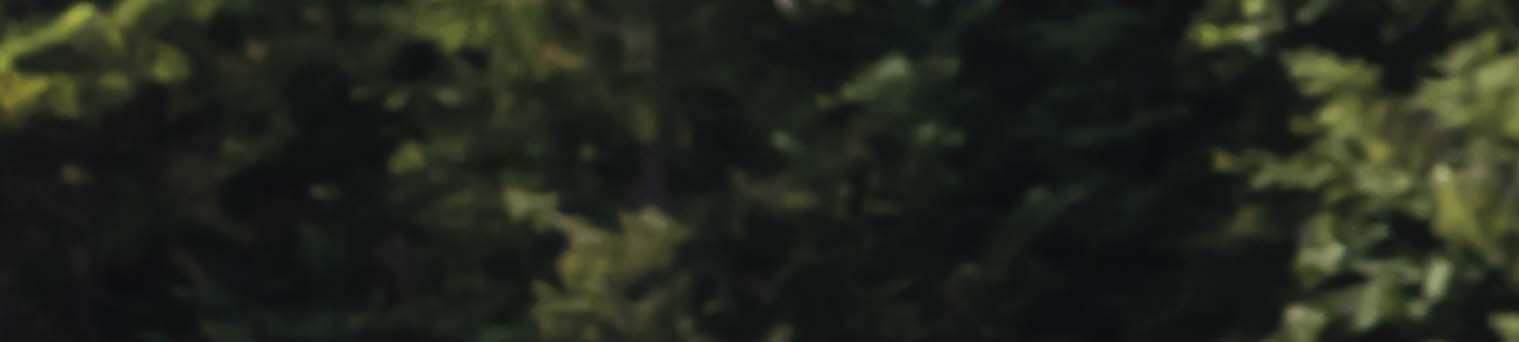
Gordon Cope, Contributing Editor, predicts a hopeful future for the tanks and terminals sector in North America.
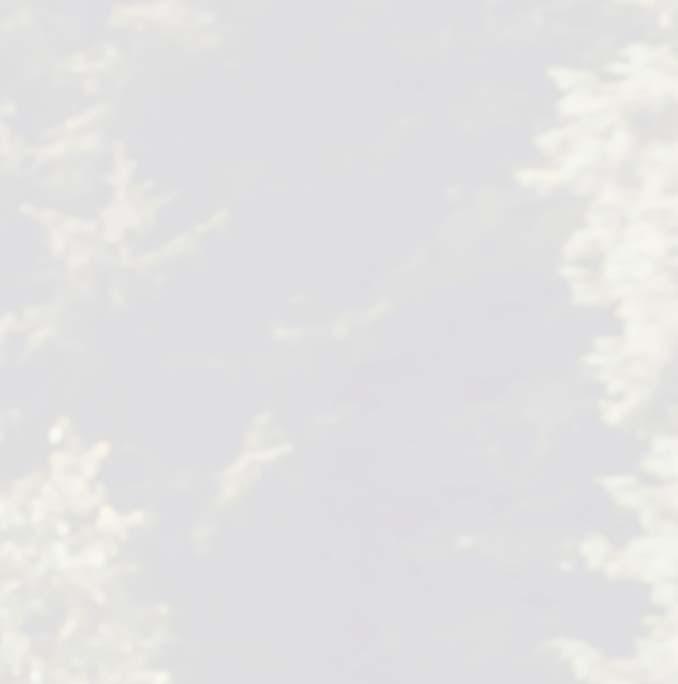
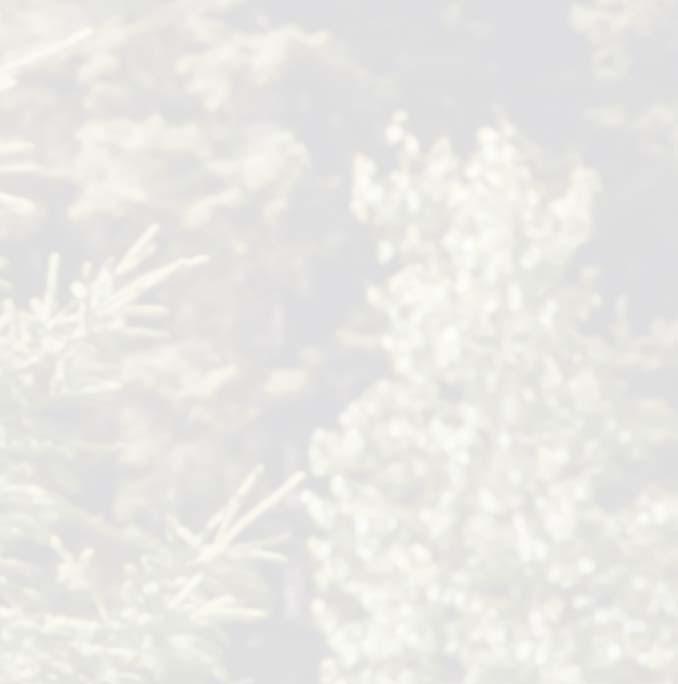
Tanks and terminals in North America have had a challenging year, as everything from pandemics to extreme weather has had an impact on both assets and future planned growth. But the sector remains strong, with tantalising opportunities for new fuel infrastructure just over the horizon.
Crude storage hubs
The Cushing, Oklahoma, storage hub experienced several large oscillations in storage throughout 2020. Normally, the hub, which acts as the delivery point for NYMEX crude oil futures contracts, averages roughly 45 million bbl of storage. When demand crashed in April 2020, stocks climbed to 65 million bbl (about 83% of the site’s working storage capacity), causing panic-trading that saw prices enter into negative territory for the fi rst time. While stocks diminished to around 40 million bbl in mid-2020, they had begun to climb again in late 2020 above 80% capacity.
In late 2020, Enbridge purchased the Cushing assets of Blueknight Energy Partners for US$132 million. The deal saw the transfer of 34 storage tanks with a total capacity of 6.6 million bbl. This lifts Enbridge’s hub storage capacity to approximately 26 million bbl. The company commented: “This acquisition will provide connectivity to new production basins, Oklahoma and the Rockies, and support Enbridge's strategy for directing barrels to the US Gulf Coast.”
In Canada, production and exports are on an upward trajectory. Oil output in Western Canada is expected to rise from 3.9 million bpd in 2020 to 4.45 million bpd by the end of 2021. Canada now exports approximately 3.8 million bpd to the US, which is expected to rise to
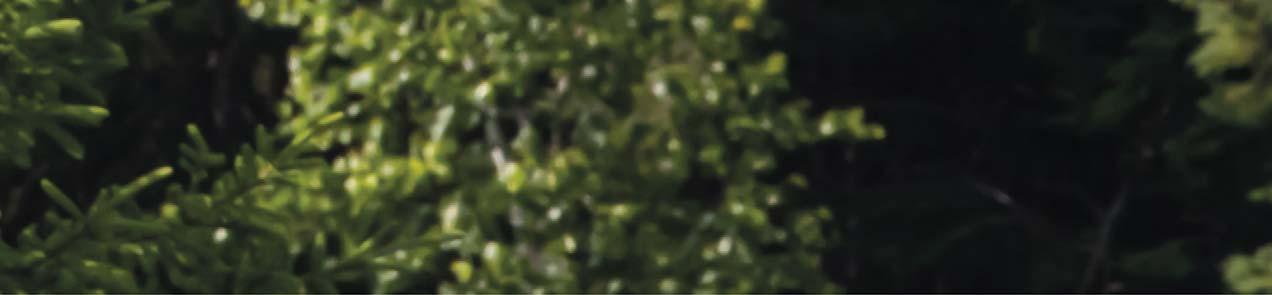
4.2 – 4.4 million bpd by 2026. Pipeline expansions in progress will add almost 1 million bpd capacity by 2025, and crude-by-rail capacity is continually growing.
To handle growth in Canada, Gibson Energy has earmarked up to CA$200 million for tank expansion projects, primarily at its Hardisty and Edmonton terminals. The company had approximately 12 million bbl of storage at the end of 2020, and is expected to add between two and four 500 000 bbl tanks in 2021 at Hardisty. Gibson also recently entered a 25-year contract to supply Suncor Energy with biofuel services at its Edmonton terminal. Under the agreement, Gibson will add substantial blending, storage and transportation infrastructure to its terminal (which sits adjacent to Suncor’s refi nery) in order to handle the company’s renewable diesel production.
Export terminals
For the last two years, Alta Gas has been operating the Ridley Island propane export terminal (RIPET) in Prince Rupert, British Columbia. The CA$500 million terminal (which can ship tanker loads to East Asia in 10 days) has an advantage over Gulf of Mexico suppliers (which can take up to 4 weeks). In 2020, it averaged 39 000 bpd of exports. The availability of propane is expected to grow as production of shale gas from the Montney formation in northeastern British Columbia continues to expand, and Alta Gas has federal approval to enlarge RIPET by 40 000 bpd. Pembina Pipelines has been building a Greenfi eld CA$250 million terminal on nearby Watson Island with a capacity of 25 000 bpd, and expects the facility to be commissioned in mid-2021; the company already has a further 15 000 bpd expansion in the engineering phase.
In the US Gulf Coast (USGC), COVID-19 had a signifi cant negative impact on planned deep water export terminals. In early 2020, there were a dozen proposals to build facilities that could accommodate very large crude carriers (VLCCs) capable of carrying up to 2 million bbl to market. A signifi cant drop in Permian production as well as decreased consumption in consumer markets took the urgency out of export plans, and there are now only three active proposals before federal maritime regulators. Phillips 66 and Trafi gura are slow-walking their application for the Bluewater Texas terminal (BWTX) project in Corpus Christi. Enterprise Product Partners and Enbridge’s Sea Port Oil Terminal (SPOT) in the Houston Ship Channel are pushing the approval process into latter 2021, and Sentinel Midstream has suspended permit reviews for the Texas GulfLink deepwater port in Freeport.
Not all tanks and terminals activity in the USGC is stalled; in mid-2020, Moda Midstream commissioned the fi nal 500 000 bbl tank in a 10 million bbl expansion at its Moda Ingleside Energy Center (MIEC) in Ingleside, Texas. The expansion now gives the company approximately 12 million bbl of storage to help producers facilitate the export of crude through Moda’s terminal in Taft, Texas. In addition, Moda has announced a new phase of construction that will add a further 3.5 million bbl of storage.
LNG
In December 2020, Corpus Christi LNG facility in Texas commissioned its third and fi nal liquefaction unit. The US currently has 10.8 billion ft3/d of LNG capacity at six facilities in the USGC, and was running in excess of 90% capacity during the busy winter heating season. The US Energy Information Administration (EIA) forecasts that LNG exports will average 8.5 billion ft3/d in 2021 and 9.2 billion ft3/d in 2022.
In Western Canada, the Montney and Duvernay shales of northwest Alberta and northeast British Columbia contain trillions of cubic feet of gas and immense reserves of NGLs. Output now stands at 5.6 billion ft3/d of liquids-rich gas. While most of the gas is currently processed and distributed through Alberta to markets in Eastern Canada and the US, plans are underway to tap an entirely new market. The west coast of Canada is signifi cantly closer to Asia than Australia or the USGC, making LNG transport much more economical. LNG Canada, led by Royal Dutch Shell, is building a plant in Kitimat, British Columbia, with a capacity of up to 26 million tpy.
Challenges
Recent inclement weather has had an impact on storage assets in North America. The strategic petroleum reserve (SPR) facility in West Hackberry, Louisiana, was hit by Hurricane Laura in August 2020. The SPR has a total of 648 million bbl of crude stored in four underground caverns; West Hackberry holds slightly under 200 million bbl. The hurricane temporarily disabled surface installations and power, but did not damage any assets below ground.
The natural gas system in Texas was not so fortunate. A Polar vortex hit the state in February 2021, causing gas wells to freeze and production to drop from around 24 billion ft3/d to as low as 11 billion ft3/d. The outage should not have been an issue; Texas has a large amount of gas storage, approximately 500 billion ft3 (about 10% of the nation’s total), and it was topped up with 300 billion ft3 when the storm hit. The system is rated to deliver up to 17.5 billion ft3/d. Therefore, it can be concluded there should not have been a gas storage.
The weather crisis illustrated weaknesses in the state’s gas delivery system. Most natural gas pipes are fi lled with associated gas derived from shale oil wells because it is easier to access under normal conditions. However, unlike gas in storage caverns, which are pressurised and can fl ow under their own power, associated gas needs to be pumped by compressors into the pipeline system. When power lines supplying Permian basin fi elds failed, compressors went down, leaving the gas stranded.
Several issues compounded the problem. First, theoretical and actual extraction rates from underground storage can differ due to pressure fl uctuations. Unlike storage systems under federal jurisdiction, Texas’s state-run system does not necessarily have to prioritise energy utilities over other users, such as fertilizer or petrochemical plants. Spot prices quickly soared from US$4.50/million Btu to US$400.
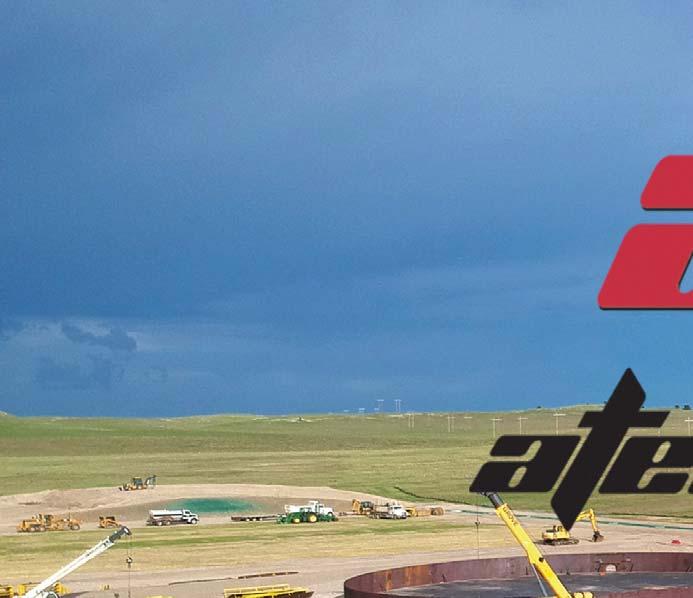
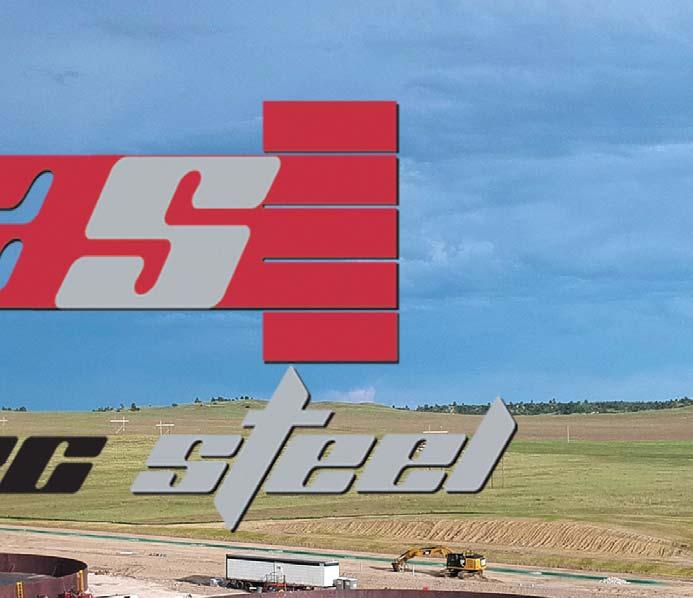
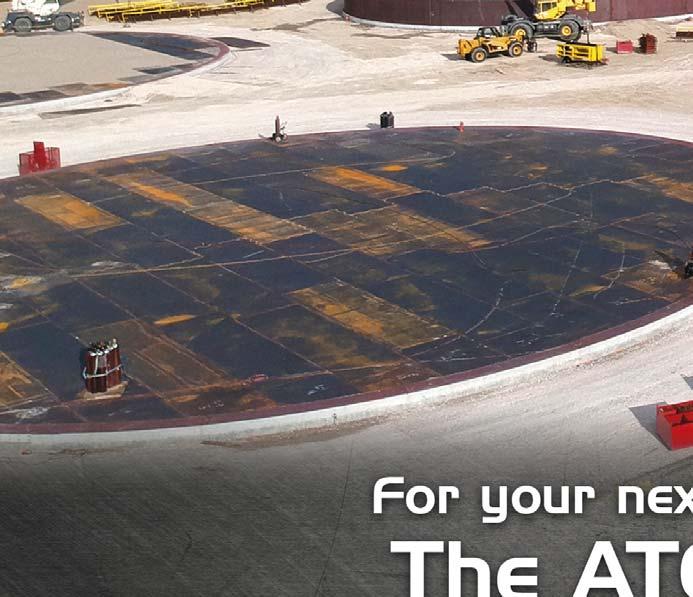
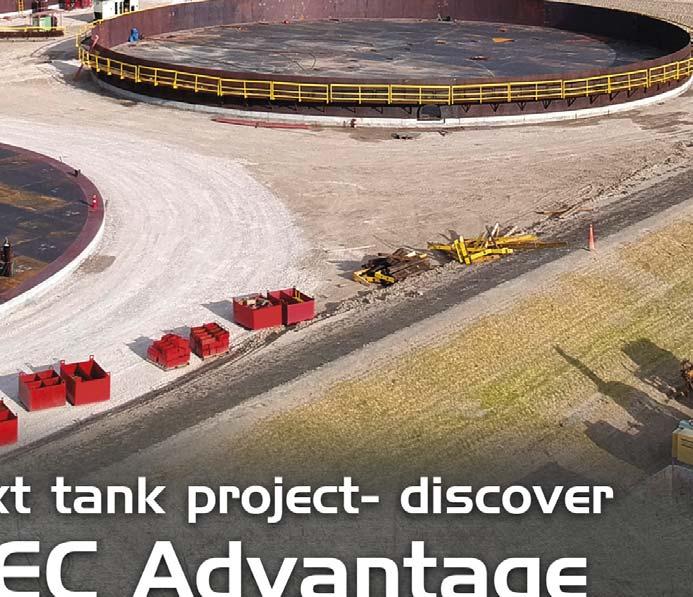
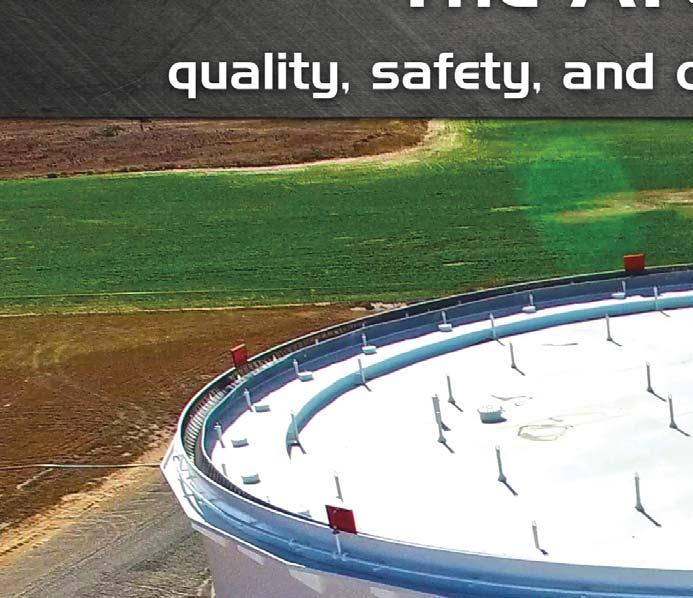
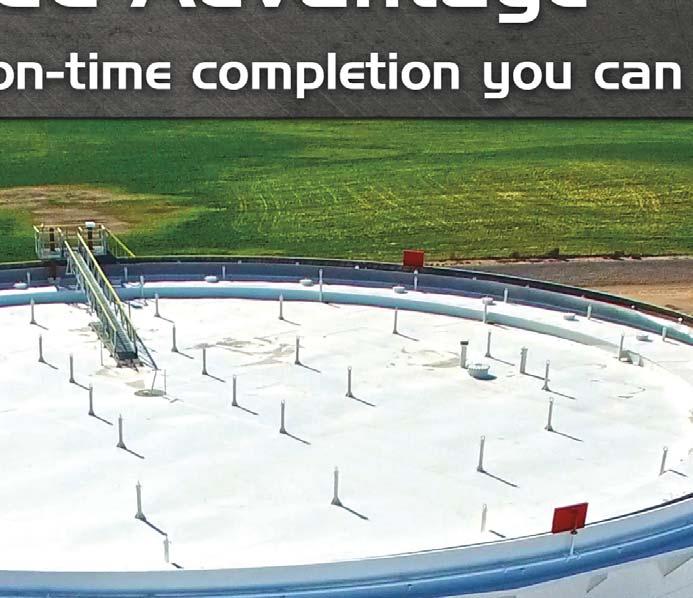
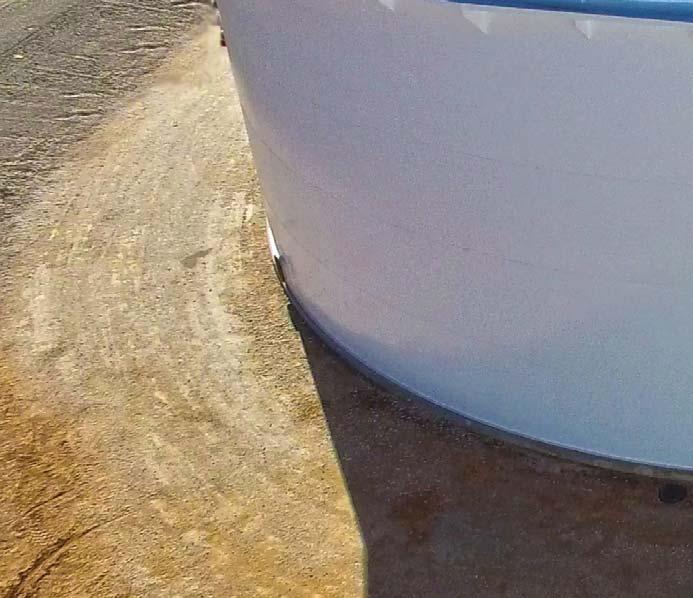
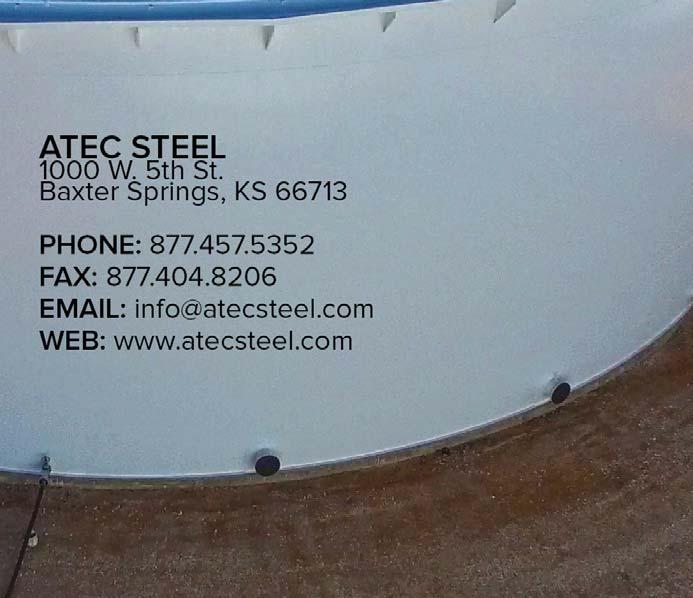
In the end, the disruption caused widespread physical hardship and billions of dollars in commercial losses. The working storage capacity in Texas is deemed suffi cient to meet needs; delivery capacities can be improved through engineering. However, analysts note that a comprehensive overhaul of regulations and procedures governing gas storage and delivery during emergency situations is needed in order to avoid similar catastrophes in the future.
The emergence of COVID-19 and the ensuing crash in demand hit refi neries hard. While the US has a refi ning capacity exceeding 18.6 million bpd, output shrank as low as 13.3 million bpd in April 2020. Demand destruction during lockdowns was the main culprit, but refi neries also ran out of room onsite to store diesel and gasoline. Producers turned to vessels, rail tankers and fuel trucks to store product, but were eventually obliged to mothball facilities. In April 2020, Marathon idled its 165 000 bpd refi nery in Martinez, California, as did operators of the 130 000 bpd Come-by-Chance refi nery in Newfoundland. By the end of 2020, the US had permanently lost around 600 000 bpd of refi ning capacity, including the 335 000 bpd Philadelphia Energy Solutions plant in Philadelphia.
Biodiesel is offering some refi neries an opportunity to persevere. CVR Energy is revamping its 74 500 bpd refi nery in Wynnewood, Oklahoma, to produce 100 million tpy of renewable fuel. The US$100 million project will see an existing hydrocracker reconfi gured using Haldor Topsoe’s HydroFlex technology to convert soybean oil to ASTM D975 biodiesel that is compliant with the California low carbon fuel standard. The re-fi t is expected to be completed in mid-2021
The future
The potential for hydrogen as an environmentally-friendly transportation fuel has grown dramatically over the last several years.
The world currently produces around 75 million tpy, primarily using the steam-methane reforming process, where high-temperature steam is used to strip hydrogen from natural gas. This has consequences for the atmosphere; the International Energy Agency (IEA), estimates that greenhouse gas (GHG) emissions associated with the production amounted to roughly 830 million tpy of CO2e.
At the end of the tailpipe, however, hydrogen is a boon; when it is consumed in a fuel cell to produce electricity, the only emission is water. If the hydrogen produced in North America (about 12 million tpy) were used as a fuel, it would power up to 40 million fuel cell vehicles annually.
The key to environmental neutrality is to purify the hydrogen without emitting GHGs. So-called blue hydrogen is made using the steam-methane process, but the carbon dioxide is captured and sequestered underground (CCS). Hydrogen can also be made with electrolysis (running an electric current through water to separate hydrogen from oxygen). If the electricity is sourced from solar or wind power, the output is called green hydrogen.
Many nations in Europe are already developing hydrogen hubs (also called hydrogen valleys and hydrogen clusters). The EU has developed plans to build up to 40 GW of renewable hydrogen electrolysers and produce as much as 10 million t of renewable hydrogen by the year 2030.
Government and energy companies are now looking at potential sites in Canada, especially to develop blue hydrogen. Fluor Canada built Royal Dutch Shell’s Quest Carbon Capture & Sequestration facility at the Scotford refi nery outside of Edmonton, Alberta. The engineering fi rm also designed the nearby North West Redwater Sturgeon refi nery, which captures carbon for transport via the Alberta carbon trunk line to enhanced oil recovery projects in central Alberta. The existing infrastructure can readily be adapted to hydrogen.
In other parts of the country, green hydrogen has great potential. Canada derives almost 60% of its electricity from hydro power, primarily in Quebec and British Columbia. Hydro-Quebec has commissioned Thyssenkrupp to build an 88 MW water electrolysis plant in Varennes, Quebec. When the plant enters service in 2023, it will generate 11 000 tpy of green hydrogen, which will then be used to generate biofuels. A consortium is also looking at building a similar plant in British Columbia.
In the US, SGH2 announced plans to build the world’s largest green hydrogen production facility in Lancaster, California, north of Los Angeles. The plant will combust mixed waste paper in a plasma gasifi cation technology partially developed by NASA to produce up to 3.8 million kg/yr of hydrogen fuel for use in the state. The plant is expected to be commissioned by 2023.
To deal with infrastructure issues, two major hydrogen equipment suppliers, Chart Industries and Matrix Service Co., have entered into a joint venture to provide standardised hydrogen fuel solutions to the North American market. With long histories in the cryogenic sector, the duo expect to provide a wide range of liquefaction, transportation and regional storage facilities for the retail distribution of the fuel.
Hydrogen still has several major hurdles to overcome; the biggest barrier is price. In 2019, S&P Global estimated that conventional hydrogen cost €1.24/kg to produce, blue hydrogen stood at €1.31/kg, and green hydrogen at €3.43/kg. Scaling up to major production is bound to lower costs; European advocates estimate that green hydrogen could be as low as €1.70/kg by mid-decade. If that is the case, hydrogen fuel could skyrocket. Analysts project that the global hydrogen market could reach US$12 trillion by 2050, when up to 30% of fuel needs will be met by hydrogen.
Conclusion
While disruptions due to COVID-19 and weather have caused major upsets to the energy sector, tanks, terminals and other infrastructure have shown remarkable fl exibility and the ability to adapt. In the near term, domestic consumption will recover and export opportunities for all forms of energy will continue to grow. Over the longer term, the emergence of hydrogen as a major fuel source could create signifi cant opportunities for tanks and terminals in North America, as well as around the world.