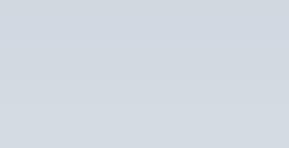
22 minute read
Composite solutions: planning for tomorrow
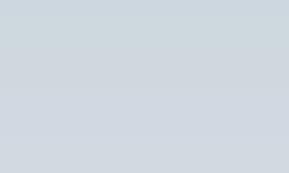
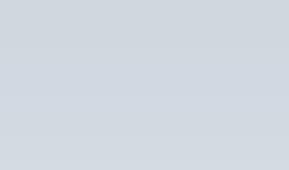
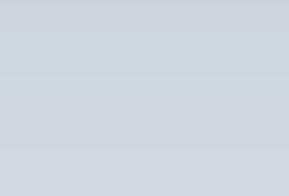
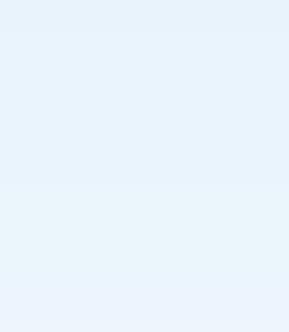


Implementation of SURAP Pipeline and facilities were divided into distinct commissionable sections. Each commissionable section was assigned assurance items, some universal, some unique to the particular section, e.g. subsea section of the pipeline. Changing the order of commissioning would have been possible in terms of executing SURAP.
Recurrent meetings were set to facilitate progress reporting to the SURAP process owners and TAP senior management. The SURAP database was the tool used to track progress towards VoR completion.
Focal points were tasked to provide the assurers with the information needed to satisfy the SURAP requirements and storage of evidence to ensure traceability.
The assurers verified that the evidence met the database requirements and advised the SURAP team if an item could be closed in the database.
The multidiscipline nature of the regular SURAP meetings during the execution phase minimised common errors which often undermine readiness assurance efforts, such as: ) Skipping or forgetting parts of the reviews needed to ensure completeness of the process.
) Omitting safety, commercial, permitting, etc. critical aspects from the review.
Readiness reviews and go/no-go events TAP implemented Readiness reviews as part of the process involving engineering, procurement and construction (EPC) execution teams, project and operations representatives. The reviews were delivered in workshop format a month ahead of the introduction of hydrocarbons into each commissionable section, and included the generation of an action log to allow tracking of outstanding items to completion.
Readiness reviews preceded and supported the go/no-go events. The SURAP VoRs supported the evaluation by the leadership team in their decision making.
Readiness reviews and go/no-go events were effective at ensuring appropriate approval steps were taken before proceeding with IoH.
“All members of the Leadership Team were invested in the process and encouraged their teams to engage with the SURAP during both the Introduction of Hydrocarbons and the Commercial Operations phases,” said Ricardo Ruiz, Operations Director.
Pre-start-up safety review (PSSR) The SURAP included the development of PSSR checklists to support TAP personnel completing full physical asset verification on site. This was typically conducted 48 hours ahead of the introduction of hydrocarbons in each commissionable section.
The PSSR contained the requirements to be checked during the physical inspection. They were divided into themes and included sections to confirm which items were checked with positive and/or negative results.
The steps followed during the SURAP documentation completion phase are summarised in the following:
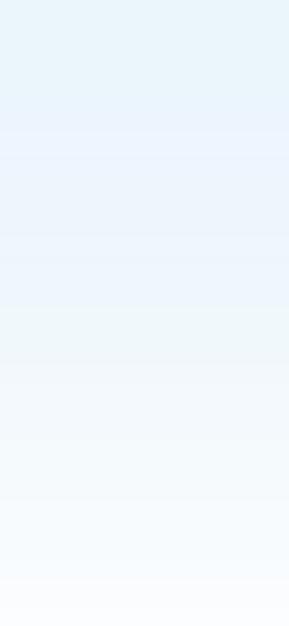
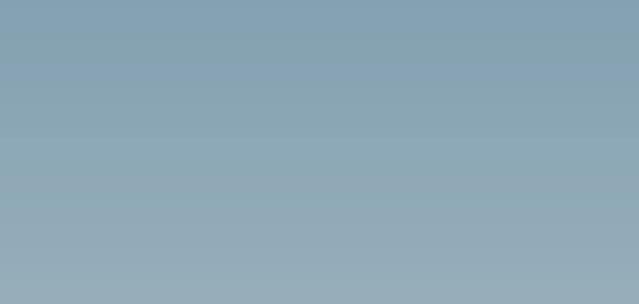
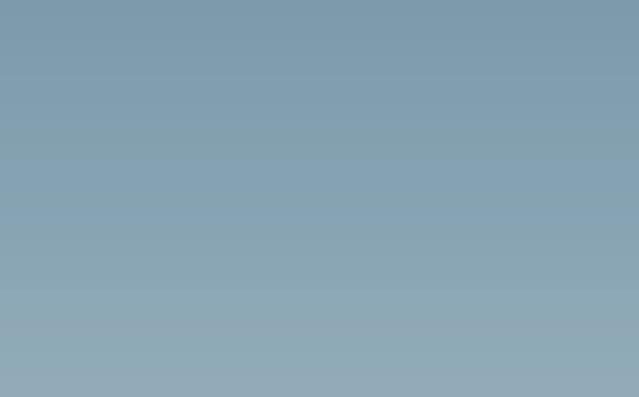
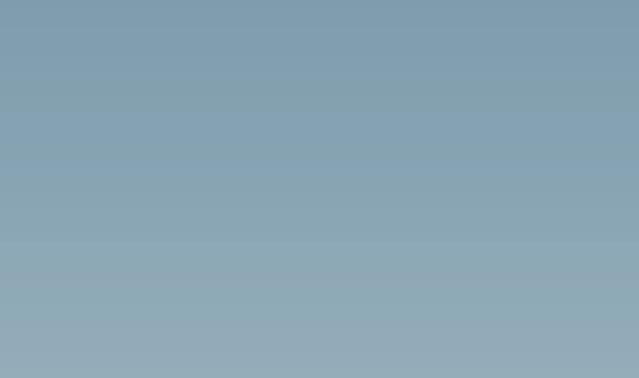
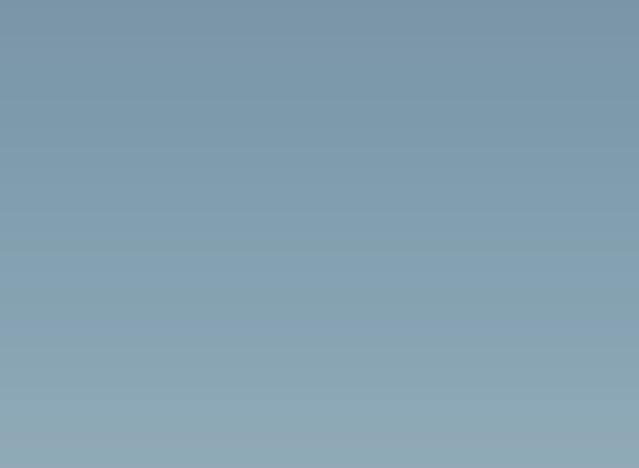
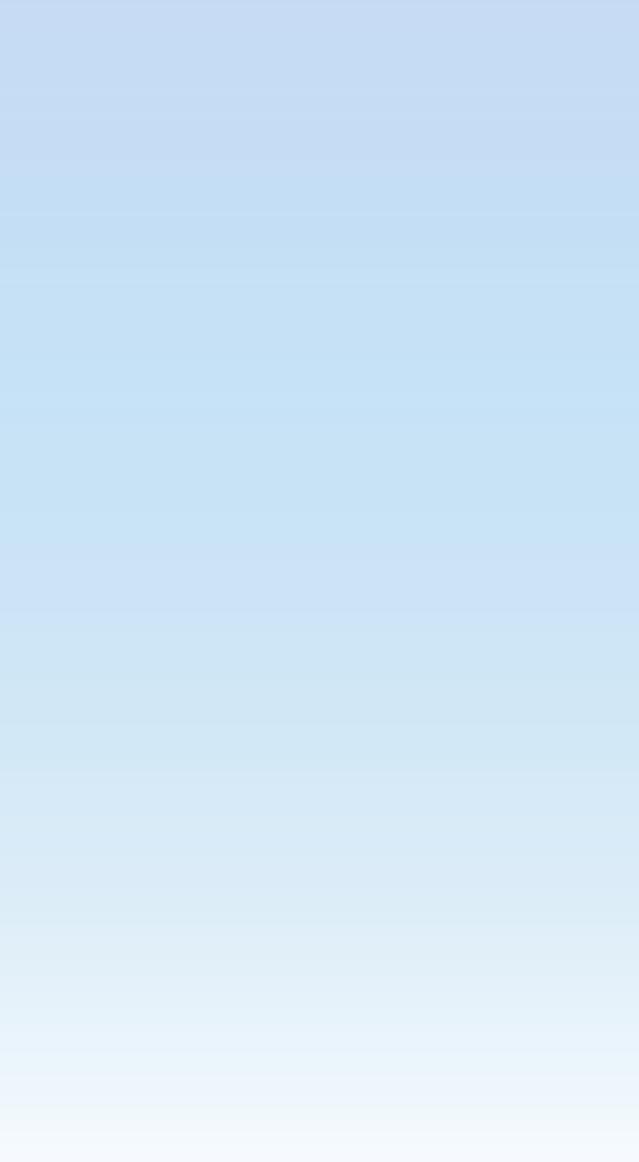
Corrosion & Cathodic Protection Remote Monitoring
Remote Monitoring is the Best and Cheapest AC Mitigation Available
How?
The purpose of AC mitigation is to prevent AC corrosion of buried pipelines. From a corrosion perspective, it is the AC current density that is the driving parameter. Several studies have shown that this can readily be reduced by careful control of the applied CP. grounding installations. The trick is to keep a balance between AC and CP, and to of this strategy. This has never been easier, than with the ICL (interference corrosion logger), Masterlink (RMU), and high sensitivity ER probes from MetriCorr. the most intuitive parameter; the corrosion rate! And a lot more.

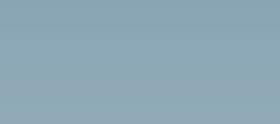
Measured parameters: •Corrosion rate (μm/y) •Pipeline potential (V)
On
IR-free (calculated)
Native (option) •DC current density (A/m2) •AC voltage (VRMS) •AC current density (A/m2) •
Independent verification body The Assurance Strategy included the provision of an internal verification body (IVB) to confirm that TAP carried out their commissioning responsibilities in line with industry best practice. The scope of the IVB included: ) Review and confirmation that the database VoRs and
PSSRs met best industry practice.
) On-site independent verification activities of the following project stages to validate the documentary evidence:
• Commissioning. • Ready for operation.
GL Industrial Services UK Ltd., part of the DNV group, provided “objective, independent evidence, in line with good industry practice that the parts of the TAP Transportation System necessary to provide transportation services are tested and are ready to be put into commercial service”. The IVB issued a certificate of conformity.
For the verification of commissioning and readiness, the IVB prepared a methodology for the verification of readiness to operate (VOCRO) based upon the principles of current verification specifications, including: ) DNVGL-SE-0474, “Risk-based verification”.
) DNVGL-SE-0471, “Verification of onshore pipelines”.
) DNVGL-SE-0475, “Verification and certification of submarine pipelines”.
) DNVGL-SE-0479, “Verification of process facilities”.
The IVB explained that “The methodology identified the people, process and plant aspects which were relevant to TAP’s organisational and asset readiness. Physical asset aspects covered integrity and functionality for which specific verification elements were identified on a schedule for each commissioning section. Then, for each element, an IVB review of documented evidence was conducted, followed by on-site surveillance where necessary. Close liaison was maintained between TAP and IVB throughout project execution to enable a rapid resolution of any elements of concern before they could cause delay to commissioning dates. Some 1292 elements were addressed by IVB over the course of VOCRO.”
Lessons learnt The implementation of the SURAP lasted just under 18 months. The process started when concrete plans and sufficient detail was available to the team. It concluded at the time commercial operations begun.
During this period the SURAP team organised two ‘lessons learnt’ workshops. The first took place in December 2019, six months into the process, and the second in October 2020 after completion of the process. An additional optimisation workshop was completed in December 2019. The following statements were recorded during the final session, reflecting on the execution costs and value added by the SURAP deliverables.
Pro content ) The SURAP database was well structured, robust, very comprehensive and cross-departmental. Very efficient at maintaining focus on essential start-up and readiness deliverables throughout the process.
Pro process ) Weekly workshops for each VoR improved the efficiency of the process and communication between teams.
) Accountable & Assurer belonging to different teams worked well, resulting in improved quality.
) SURAP enabled focus and ensured all disciplines were given the same weighting.
) The reporting tool helped to maintain focus on readiness per discipline.
) The process is fit for purpose and can be adapted for greenfield and brownfield projects.
Future improvement Under aspects for future improvement, the teams listed the interface with other TAP system, as well as the resources required for maintaining the process, including time and manpower.
TAP Operations Assurance Manager added that “The SURAP process sat at the apex of TAP’s assurance pyramid and brought together the different strands of assurance from all areas of the organisation, enabling TAP to demonstrate readiness for start-up and reliable long-term operations.”
DNV created and customised the SURAP process with TAP to provide a robust framework and detailed checklists to undertake readiness reviews of commissioning activities and commercial operations. Asle Venas, DNV Senior Principal Pipeline Specialist and Chairman of one of the SURAP Readiness Reviews, commented “I have never seen a readiness process that covers all issues in such a structured way before”.
Conclusion Meaningful assurance processes, such as SURAP, can have a significant impact on successful start-up events and sustainable long-term operations, whether first time start-up, or post facility turnarounds. Strategic, early decision making on operational assurance objectives by organisational leadership, based on organisational maturity, culture, experience and expertise, can ensure that operational start-up assurance programmes provide value to the organisation in the critical areas of safety, cost and schedule.
Reference
1. “BP America Refinery Explosion”, in CBS Library. https://www.csb.gov/ bp-america-refinery-explosion/. Last accessed 12 Feb 2021.
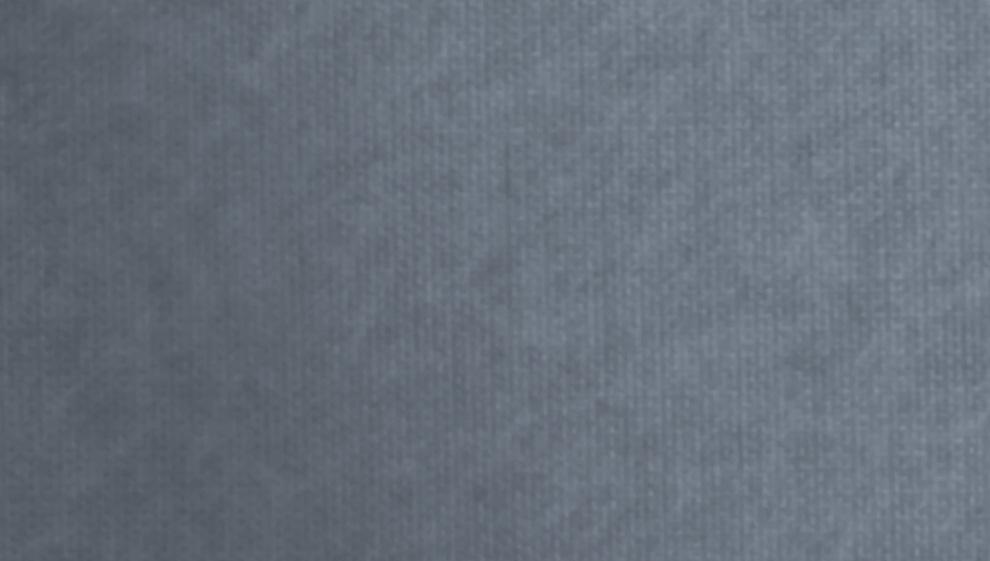
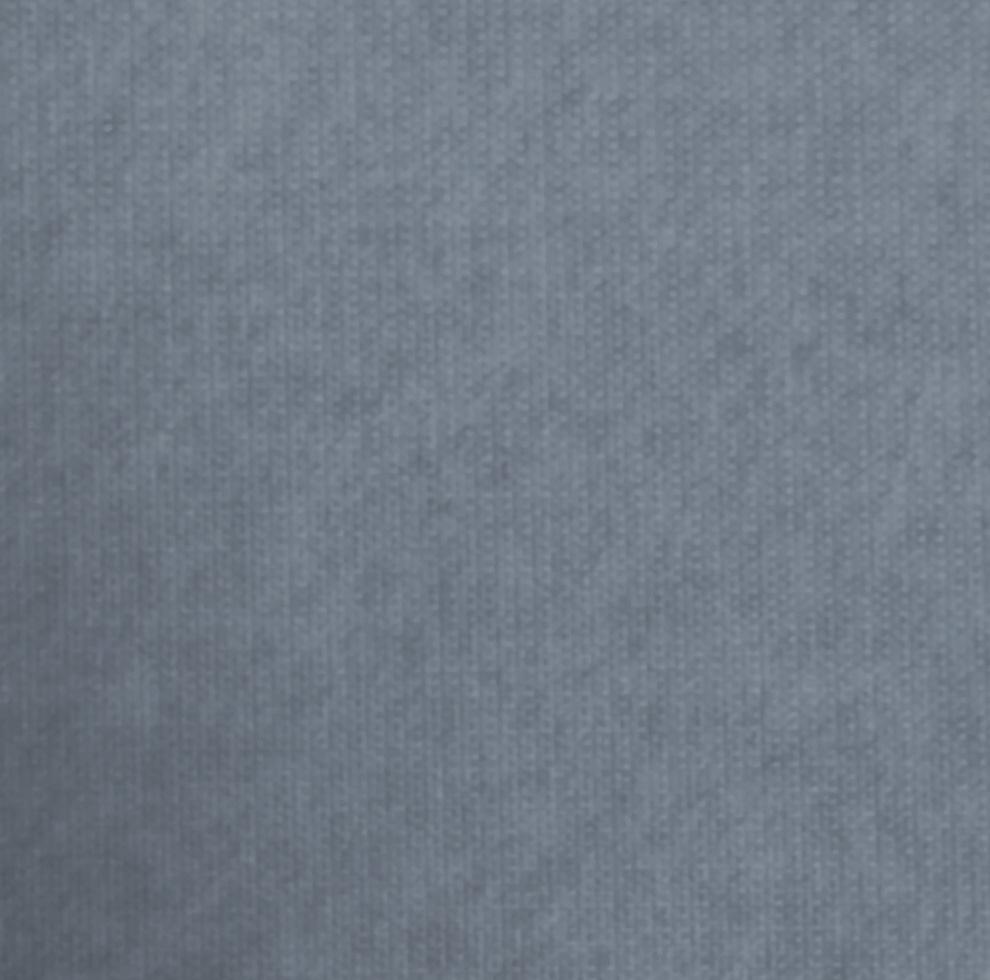
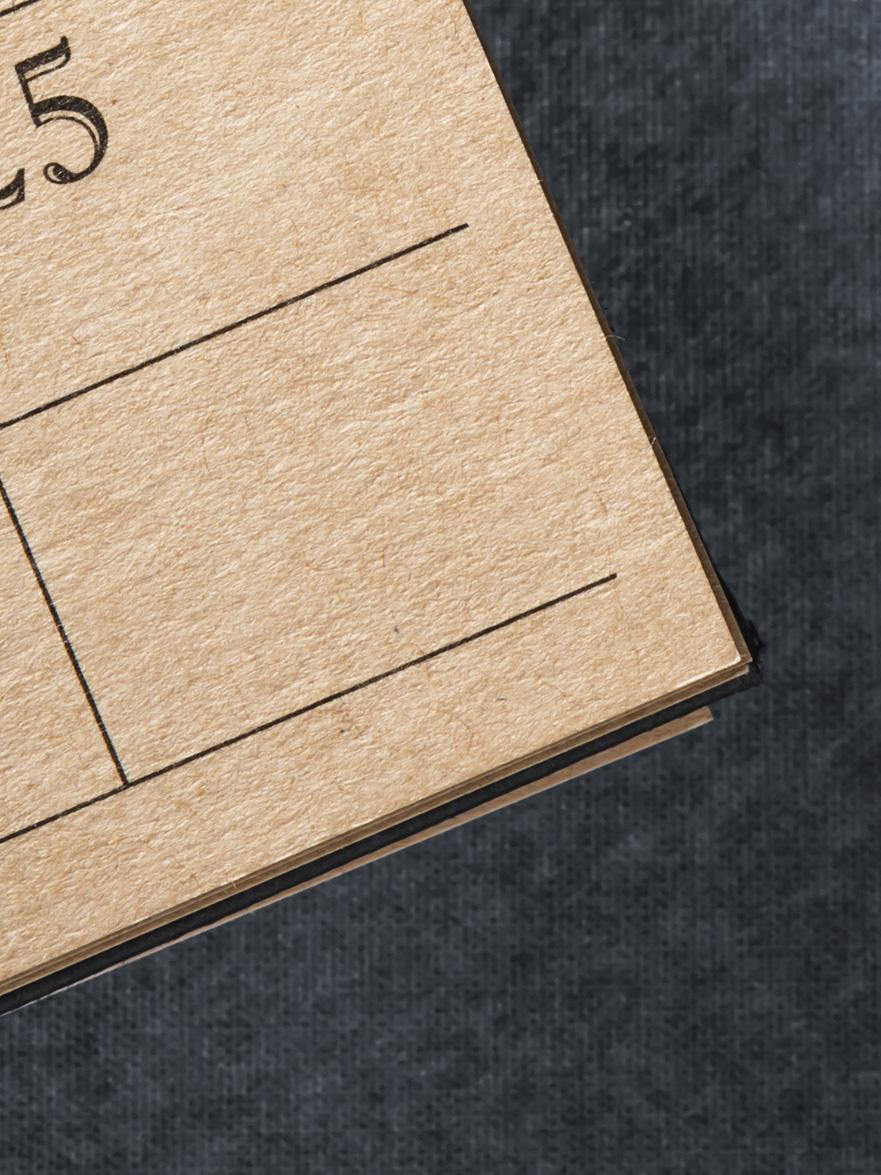
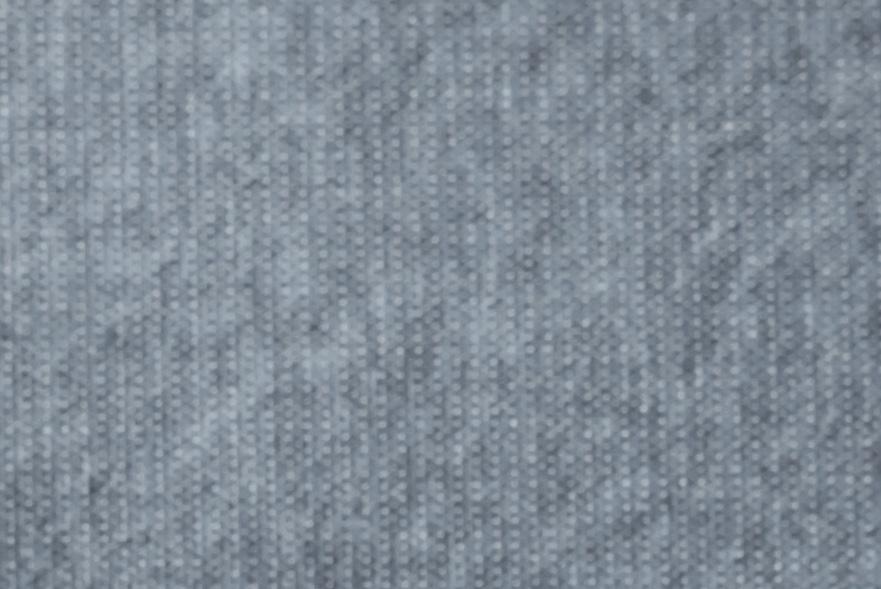

Chip Edwards and Tommy Precht, Allan Edwards, USA, discuss the launch of a new composite repair system and where the technology could be headed in the future.
For the better part of the past 30 years, composite repair technologies have been used to repair highpressure pipeline systems around the world. In the early days of their use, these repair systems were primarily used to reinforce corrosion features. However, through extensive research and testing efforts over the last 15 years involving pipeline companies, composite repair technology companies, regulatory agencies, research organisations and subject matter experts, their use has extended to the reinforcement of dents, mechanical damage, vintage girth welds, pipe bends, seam welds and, more recently, leaking defects. Studies involving environmental and operational conditions have also been conducted to address elevated temperature conditions and subsea installations.1 Joint Industry Programmes (JIPs) have been instrumental in achieving widespread adoption of composite repair systems. Organisations such as the Pipeline Research Council International, Inc. (PRCI) have played a central role in evaluating composite repair technologies, including E-glass, carbon and even Kevlar fibre systems.2, 3, 4 With standards such as ASME PCC-2 and ISO 24817, minimum design requirements for the composite repair industry have been established, bringing expected uniformity among at least ten internationally recognised composite repair companies. This article will provide a brief examination of the benefits associated with using composite repair systems. A discussion will follow on the development of a new
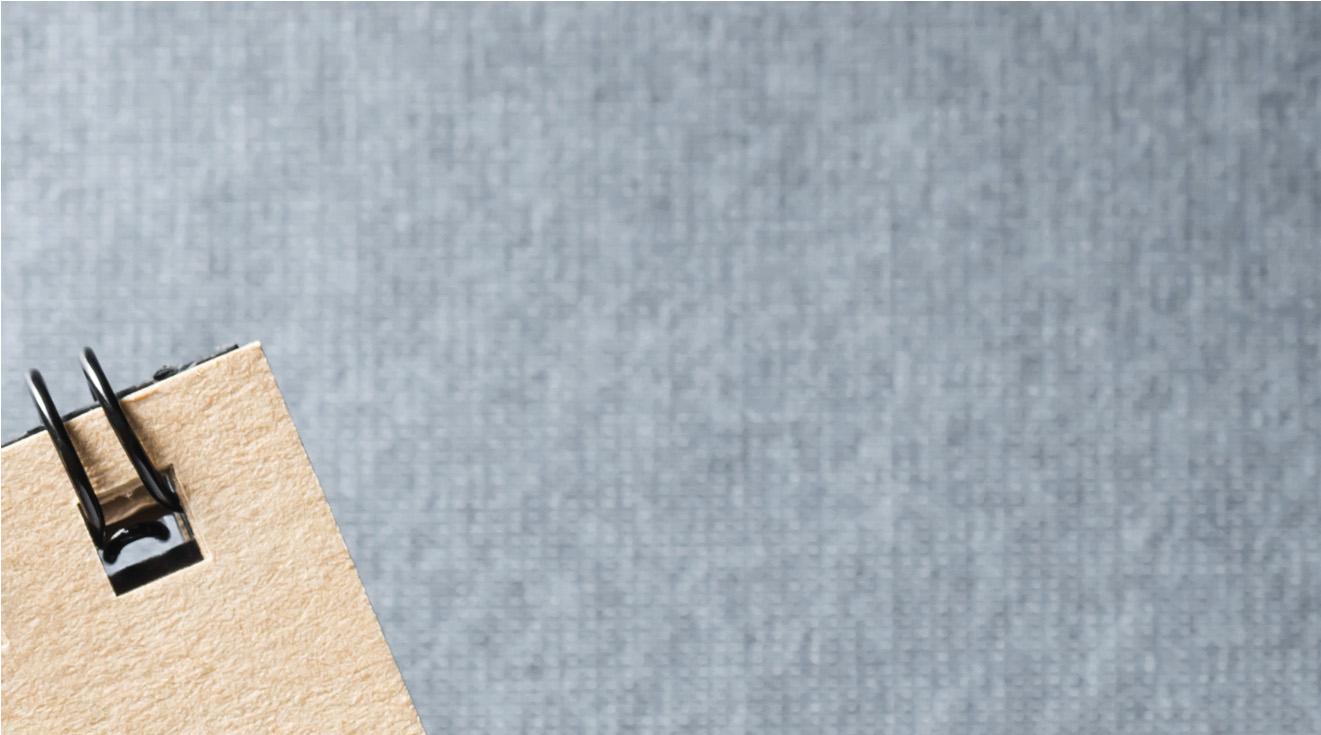
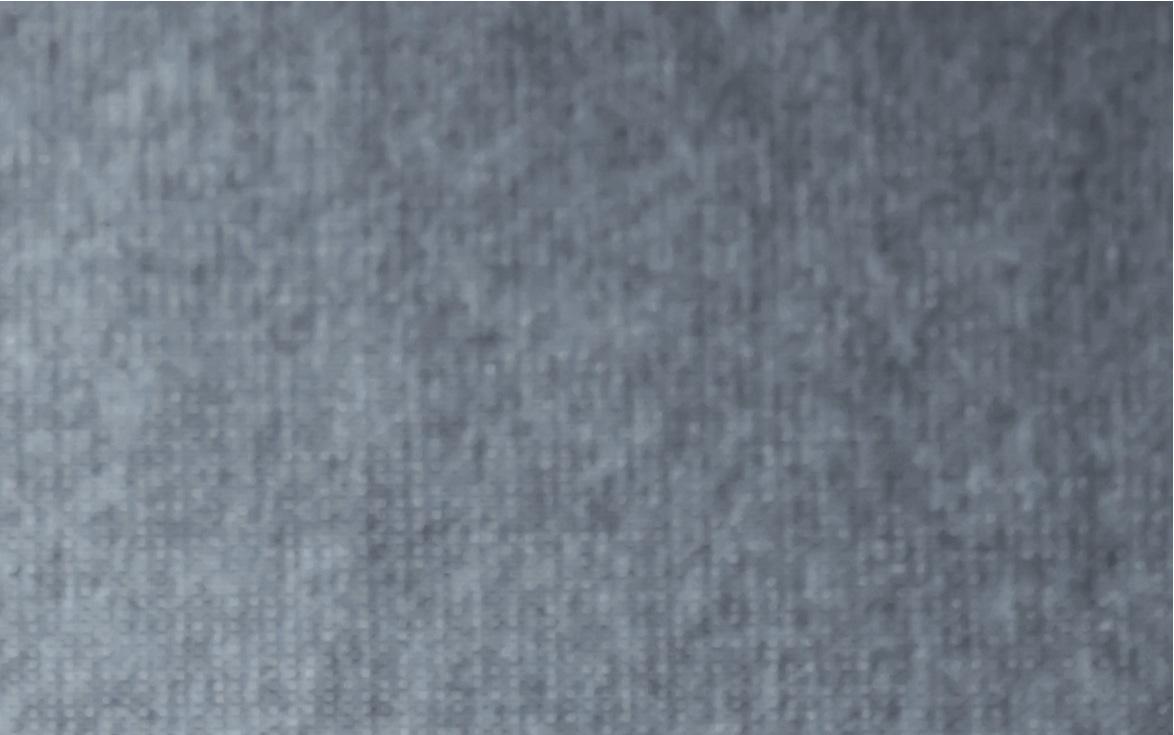
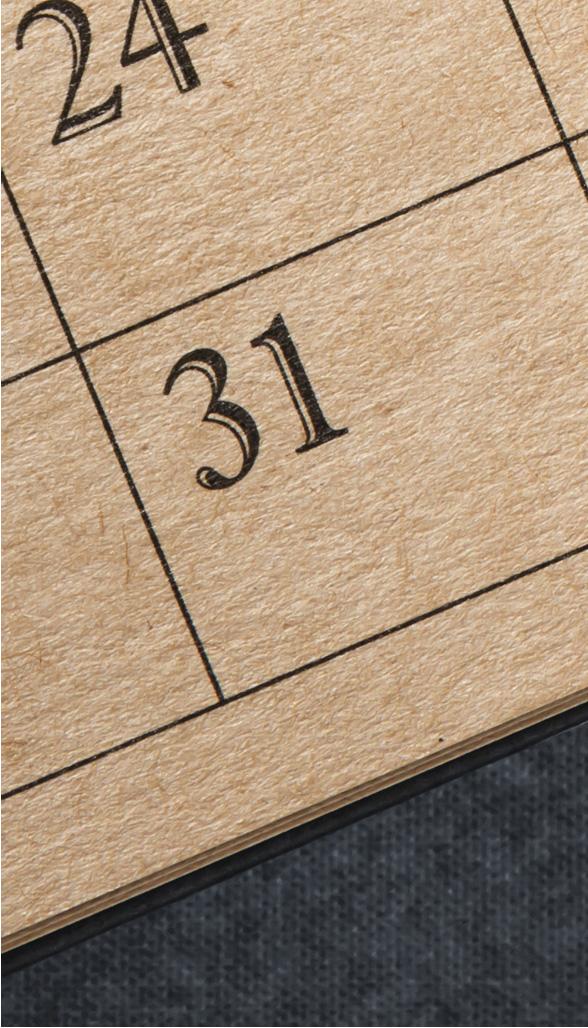
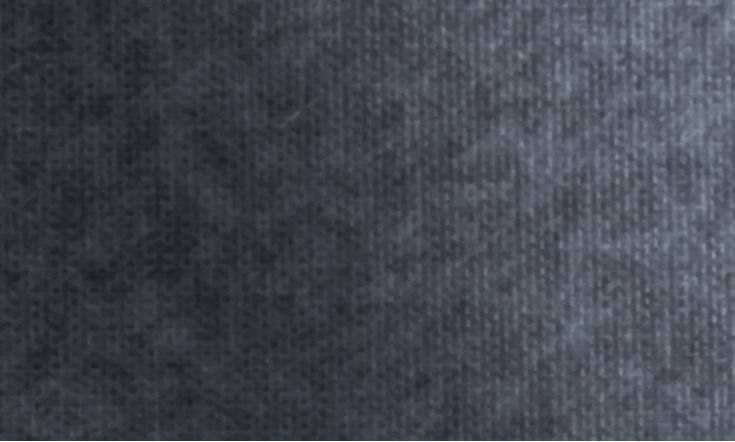

composite solution brought to market by Allan Edwards – the OmegaWrapTM repair system, which is available in both E-glass and carbon variants. Finally, a brief dialogue is provided to address current knowledge gaps and areas for future exploration regarding the use of composite reinforcing technologies.
Motivation Having worked within the pipeline repair industry his entire adult life, Chip Edwards, fourth-generation president of Allan Edwards, recognised an opportunity to enter the composite repair technology space. He enlisted the help of Tommy Precht, an industry veteran with 25 years of experience in pipeline repair applications. This led to the birth of the OmegaWrap composite repair system. Chip and Tommy’s long and unique history with pipeline companies provided them with a strong understanding of the critical role that customer service plays in offering a complete repair package.
With the help of ADV Integrity, Inc. (ADV) and its president, Dr. Chris Alexander, PE, development was planned and executed for both an E-glass-epoxy and carbon-epoxy version of the OmegaWrap composite repair system. The following six months involved a rigorous schedule of selecting, testing and evaluating different combinations of fabrics and resins before settling on the optimised configuration that is now available. Full-scale testing at the ADV test lab was conducted to validate the OmegaWrap composite repair technology.
Though steel repair sleeves are the ‘tried and true’ method for repairing pipelines, composite repair technologies offer several unique advantages. First, composite materials that are installed ‘wet’ can be used to reinforce a variety of pipe geometries and configurations, including wrinkle bends, elbows and branch connections.6, 7 The capability of conforming to pipe ovalities also cannot be discounted. Secondly, the flexibility to select different fibre types, fibre orientations and resins produces a wide range of technologies that can be used to reinforce everything from corrosion, which primarily requires ‘hoop’ (circumferential) reinforcement, to wrinkle bends and girth welds that require axial reinforcement. Lastly, with continued advances in fibre types and resins, there are numerous opportunities for expanded growth in the composite repair space. These advantages, coupled with the ability to expand repair options beyond conventional steel sleeves, made the development of the OmegaWrap composite repair system both an attractive and necessary investment.
Development of a composite repair system As mentioned previously, the ASME PCC-2 and ISO 24817 standards have contributed significantly to the introduction of new and innovative composite repair technologies. Prior to the introduction of these standards, there were only a few companies offering composite repair technologies. Since the acceptance and utilisation of these new repair standards, however, the ‘barrier to entry’ has been lowered, allowing new companies and technologies to be introduced to the marketplace.
The OmegaWrap composite repair system was developed using a very strategic approach. This involved not only identifying and testing different material combinations, but also designing and conducting a testing programme to better understand the performance capabilities of the OmegaWrap system. The most fundamental test in designing and qualifying a composite repair system involves fabricating panels and conducting tensile testing to determine the tensile strength, strain-to-failure and elastic modulus. Shown in Figure 1 is a photograph of a panel where the tensile coupons were extracted via water jetting, as well as a photograph showing one of the tensile samples being loaded in a tensile testing machine.
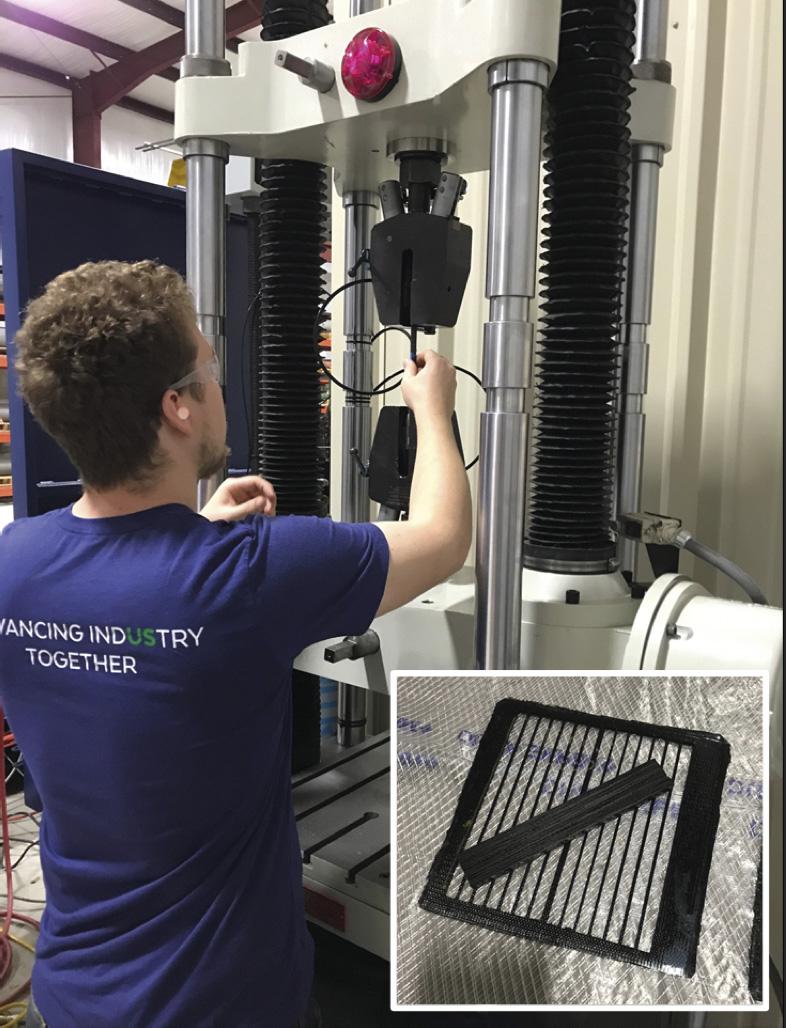
Figure 1. Tensile testing of a coupon extracted from a composite panel.
Figure 2. Photographs showing installation of the OmegaWrap EG system.

Depicted in Figure 2 is a series of photographs detailing the installation of the OmegaWrap EG (E-glass) system. Noted in these photographs is a pipe surface contour tool, printed with ADV’s 3D printer, that was used to ensure that an optimised contour of the load transfer material was achieved (as observed in the middle photo).
In addition to meeting the minimum requirements specified in ASME PCC-2, the OmegaWrap EG and C (carbon) system variants were subjected to testing to evaluate their performance in reinforcing dents, severe corrosion and cracks subjected to extreme cyclic pressure conditions. Burst testing was also conducted on test samples reinforced with the OmegaWrap carbon-epoxy technology, containing 15% and 50% EDM notch features that were pre-cycled to ensure cracking was present. The following bullets provide details of testing conducted on the 50% deep crack sample that was estimated to fail at 1039 psig using the PRCI MAT-8 fracture mechanics software. The sample failed at 1942 psig (157% SMYS) and failed outside the repair, as shown in Figure 3. ) 12.75 in. x 0.188 in., Grade X42 pipe.
) Crack dimensions: 3 in. long by 50% deep (0.094 in.).
) Fracture toughness of pipe: Kmat = 231 ksi √in.
) Carbon epoxy system with a thickness of 0.33 in. (7 layers). The OmegaWrap EG System: where are we now? The new OmegaWrap E-glass system has officially launched as of April 2021. Thanks to the relentless dedication of Allan Edwards and ADV Integrity, the OmegaWrap EG composite repair system is one of the strongest e-glass offerings available on the
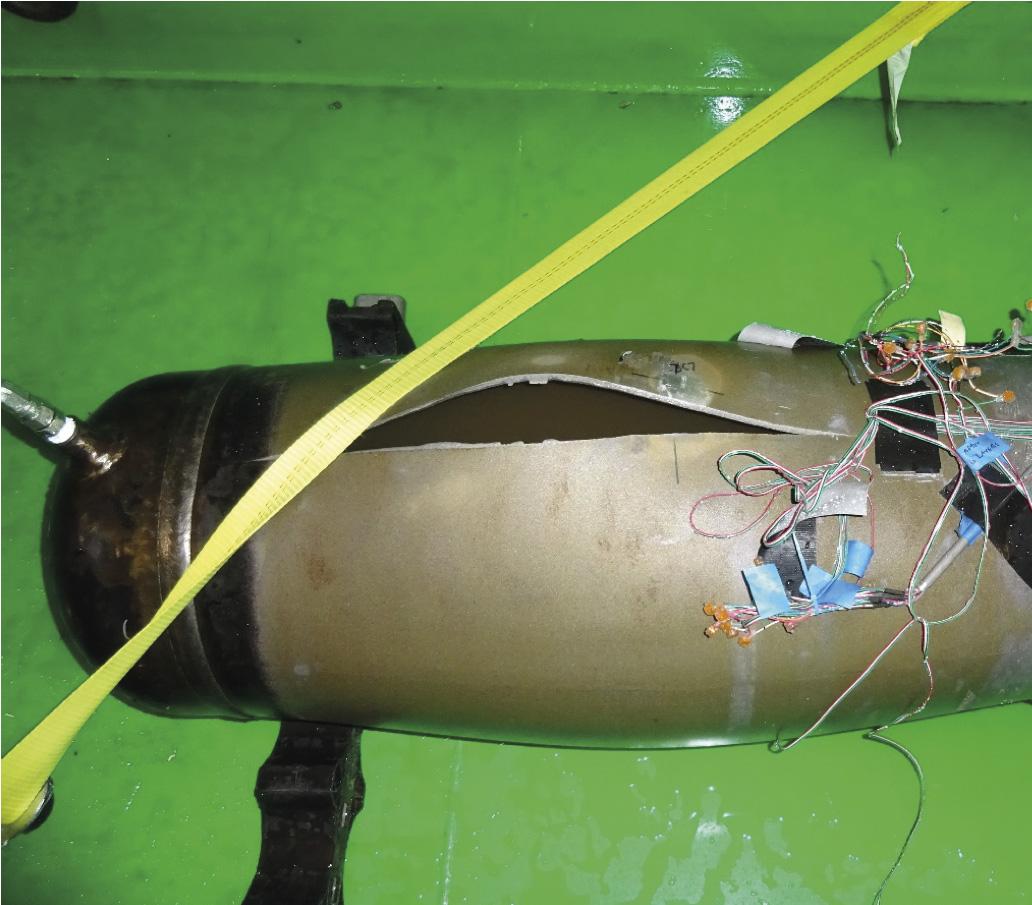

Figure 3. Post-test photo showing reinforcement of 50% crack feature.

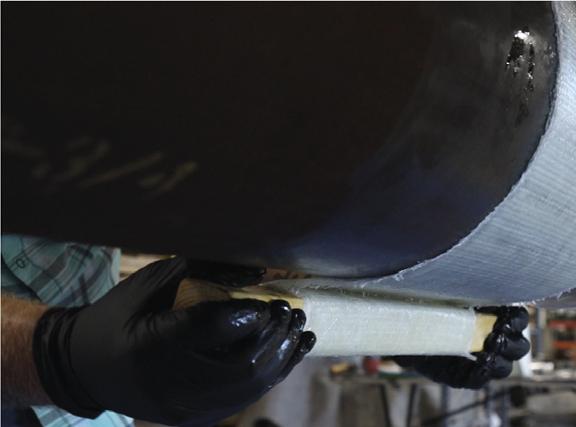

Figure 4. Wrapping the pipe with the OmegaWrap EG (E-glass) composite repair system.

Figure 5. Saturating the E-glass fabric with the epoxy resin component prior to wrapping the repair zone.
market. With a tensile strength of 91 000 psi and a strain-tofailure exceeding 2%, it is ideally suited for applications including the reinforcement of corrosion, dents, wrinkle bends and girth welds subject to geohazard bending loads. The OmegaWrap C (carbon) system is currently in its final stages of testing. As a stiffer fabric, the OmegaWrap C system will be an optimal choice for enhanced performance under dynamic loads. Comprehensive local and on-site trainings will be offered by Allan Edwards for both the OmegaWrap EG & C systems.
The future of composite reinforcing technologies Because of the extensive assessment and world-wide use of composite materials, there is no doubt their use will continue to expand in the coming years. With the innovative approach employed by oil and gas service companies, the composite repair industry will continue to advance existing repair systems and develop new technologies that meet challenging repair scenarios posed by pipeline operators. To ensure that tomorrow’s technologies are designed to meet these challenges, it is important to identify today’s knowledge gaps.
One area that will require continued development concerns the inspection of composite repair technologies. The role of inspection not only involves the technologies but requires that an assessment criterion be constructed against which feature measurements may be consistently measured. The ability to identify features such as interlaminar delamination and pipe-to-composite disbondment are only meaningful when they are compared to values identified as either ‘acceptable’ or ‘unacceptable’. Another area that requires continued development involves validation associated with pipeline operation, namely elevated temperature conditions and aggressive pressure cycling. Fortunately, previous testing programmes have demonstrated that certain composite repair technologies exist that can meet these demands. However, additional work is required to achieve widespread acceptance and adoption.
The future use of composite repair technologies is promising, and their numerous uses will undoubtedly continue to expand dramatically. The key to ensuring long-term progress involves the forward-thinking mindset of companies and their willingness to invest time, capital and resources into developing new and improved technologies, coupled with validation through numerical modeling and full-scale testing. The ultimate goal is to ensure that the performance capabilities of a composite repair technology meet and exceed the rigorous demands of pipeline integrity programmes around the world – continually refining today’s technology to meet tomorrow’s needs.
References
1. ALEXANDER, C., SHEETS, C., HARRELL, P., RETTEW, R., BARANOV, D., “Experimental Study of Elevated Temperature Composite Repair Materials to Guide Integrity Decisions”, Proceedings of IPC 2016 (Paper No. IPC201664211), 11th International Pipeline Conference, 26 - 30 September, 2016, Calgary, Alberta, Canada. 2. ALEXANDER, C., and KANIA, R., “State-of-the-Art Assessment of Today’s Composite Repair Technologies”, Proceedings of IPC 2018 (Paper No. IPC201878016), 12th International Pipeline Conference, 24 - 28 September, 2018, Calgary, Alberta, Canada. 3. ALEXANDER, C., RIZK, T., WANG, H., CLAYTON, R., SCRIVNER, R., “Reinforcement of Planar Defects in Low-Frequency ERW Long Seams Using Composite Reinforcing Materials”, Proceedings of IPC 2016 (Paper No. IPC201664082), 11th International Pipeline Conference, 26 - 30 September, 2016 Calgary, Alberta, Canada. 4. ALEXANDER, C., “Advanced Techniques for Establishing Long-Term Performance of Composite Repair Systems”, Proceedings of IPC 2014 (Paper No. IPC2014-33405), 10th International Pipeline Conference, 29 September - 3 October, 2014, Calgary, Alberta, Canada. 5. ALEXANDER, C., PRECHT, T., and EDWARDS, C., “Steel Sleeves: A New Look at a Widely-Used Repair Method”, Pipeline Pigging & Integrity Management Conference, Houston, Texas, 18 - 22 February, 2019. 6. ALEXANDER, C., and KULKARNI, S., “Evaluating the Effects of Wrinkle Bends on Pipeline Integrity,” Proceedings of IPC2008 (Paper No. IPC2008-64039), 7th International Pipeline Conference, 29 September - 3 October, 2008, Calgary, Alberta, Canada. 7. ALEXANDER, C., VYVIAL, B., IYER, A., KANIA, R., ZHOU, J., “Reinforcing Large Diameter Elbows Using Composite Materials Subjected to Extreme Bending and Internal Pressure Loading”, Proceedings of IPC 2016 (Paper No. IPC201664311), 11th International Pipeline Conference, 26 - 30 September, 2016, Calgary, Alberta, Canada.
PIPELINE MACHINERY
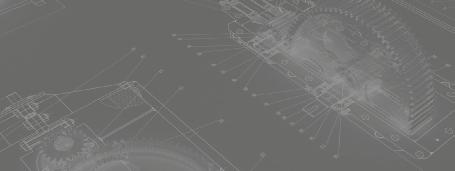
World Pipelines’ quarterly pipeline machinery focus. review
Allu, Finland
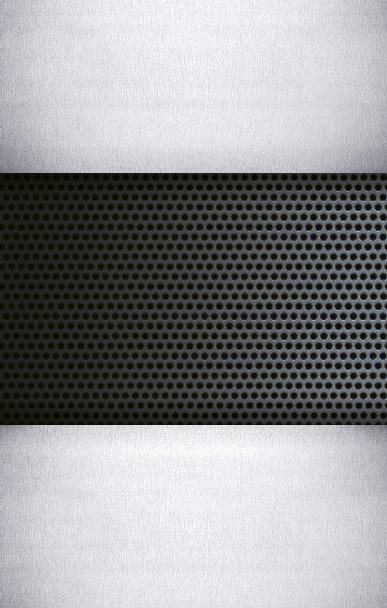
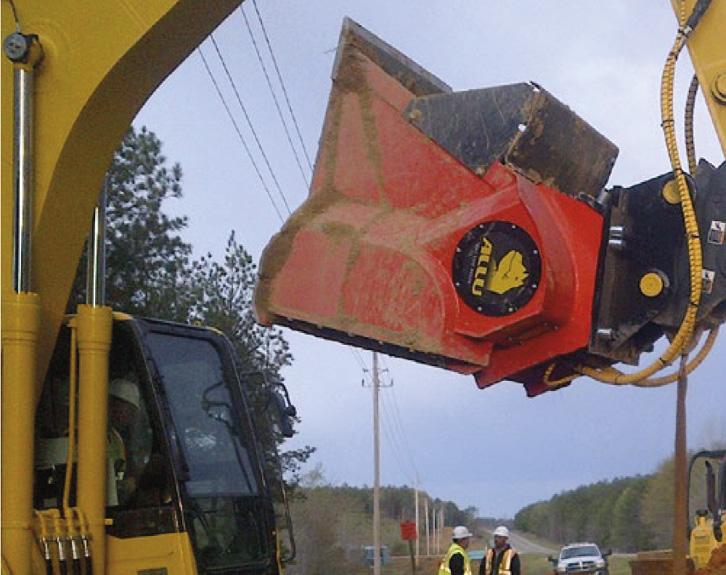

The ALLU Transformer TS Drum Assembly is an effective tool for pipeline padding and backfilling applications. By allowing material to be screened onsite and then backfilled directly into a trench, it eliminates the need for dedicated stationary screening or purchase of fine soil, saving time and money.
ALLU D-Series attachments work with wheel loaders, excavators, skid steers or back hoes to screen, crush, pulverise, aerate, blend, mix, separate, feed and load materials all in one stage – increasing the ALLU Transformer working on pipelaying. profitability and efficiency of pipeline construction operations.
The core of the ALLU TS Drum Assembly technology A case study with one pipeline contractor recently is the configuration of the screening blades that spin realised 80% savings per cubic yard using an ALLU between the screening combs. The end product size is D-Series attachment with TS drum assembly – the ALLU defined by the space between the combs, and different DH 3-12 TS16 – on a standard excavator. In looking at fragment sizes can be achieved simply by repositioning several options, this contractor realised that traditional the combs. Because the screening combs carry most of screening had a low productivity rate and large particle the material weight, the drums and bearings experience soil and stones could easily fall into the trench, whilst less impact and load. The design of the assembly purchasing fine soil is also a high cost. ensures the machine works well in wet and dry materials The pipeline contractor opted for crushing and without any clogging. screening with ALLU DH3-12 TS16, which demonstrated
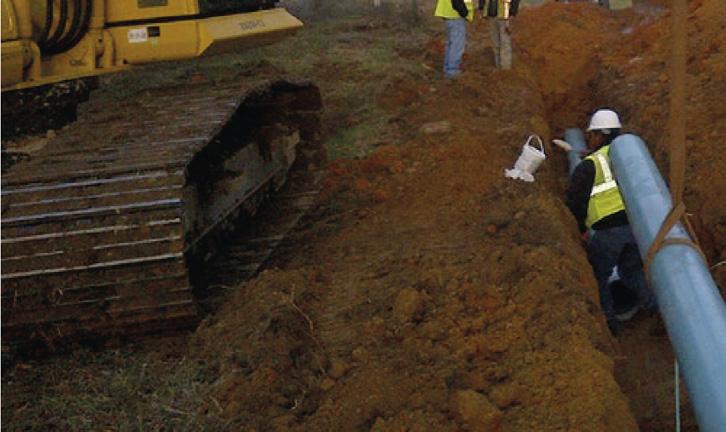
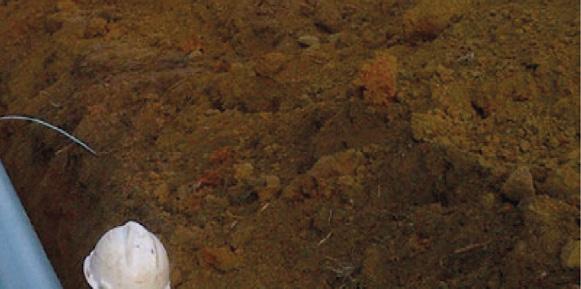
a lower cost than the other options and an 80% saving per cubic yard. Also giving them total flexibility as its available with two different blade types: standard blades for screening applications and axe blades when a crushing or shredding effect is required. The TS assembly is available in seven different models for 17.6 - 49.6 t (16 - 45 metric t) excavators and 7.7 - 33 t (7 - 30 metric t) wheel loaders.
ALLU designs, manufactures and sells products for adding value to customers in numerous ALLU Transformer recycling onsite work material to backfill pipeline. applications for processing, separating, sorting, mixing and crushing materials. Typical applications include e.g. soil and waste material recycling, operations of the customers. The history of ALLU goes back for processing contaminated soil, transforming waste to usable over 30 years and today over 95% of the business is done with material. international customers globally.
Driven by customer needs, the company has innovated the The serving network of ALLU consists today of own methods and equipment for transforming the processes and subsidiaries and a dealer network in more than 30 countries.

Trencor, USA
With difficult ground conditions, changing climates, and varying crew experience, no two jobsites are the same. This is especially true for pipeline projects that are built to transport crucial daily resources like water, gas and oil. It is important that every stage of the project is done safely and efficiently. This means even before the pipe is in the ground crews must dig a clean trench to set the stage for the rest of the project. To accomplish this, every pipeline installation jobsite needs a trencher

Trencor T16 Trencher.
ADVERTISERS’ DIRECTORY
Advertiser Page
ABC
25
Allan Edwards
AMPP
OFC, OBC
31
BAUMA
CDI
CRC-Evans
CSNRI
Dairyland Electrical Industries
DeFelsko
Electrochemical Devices, Inc.
Energy Global
Girard Industries
IPLOCA
Laurini
LNG Industry
MetriCorr
Pigs Unlimited International LLC
Pipecare
Pipeline Inspection Company
Qapqa B.V.
Ritchie Bros.
ROSEN Group
SCAIP S.p.A.
Winn & Coales International Ltd
2
51
4
23
41
29
35
31
29
55
17
19
47
23
IBC
36
13
9
IFC
Bound insert
7 that is reliable regardless of the many other changing factors. That is why Trencor’s large-scale trenchers have been used on jobsites around the world since 1945. Their rock-solid structure is built to withstand the ever-changing conditions in the field to get the job done.
The Trencor T16 was built to rock the trencher world. The rugged and proven machine can combat the challenges of today’s large diameter pipeline installation projects and tough ground conditions. Designed with ideal weight, power and size, the T16 maximises productivity for a wide range of trenching applications, including water, sewer, oil and gas. With no two jobsites created the same, the T16 can help tackle hard rock and changing ground conditions with ease.
“At Trencor we are proud that the T16 is utilised around the world to install pipelines that transport the resources we depend on daily,” said Steve Seabolt, Trencor product manager. “To help pipeline construction contractors complete these important projects efficiently, we build our equipment with the operators in mind. The features and technology on the T16 enable heavy equipment professionals to prioritise safety and optimise operations on any water, gas or oil jobsite.”
The T16 is equipped with telematics for remote monitoring and support, allowing operators to more easily manage their fleet and provide timely maintenance. The mechanical drive feature reduces tooth wear to prolong the chain life and minimise downtime needed to replace the chain. It is also equipped with a crumb shoe to ensure a clean trench for easy installation of water, gas, and oil products. Each of these features allows for optimal operator efficiency by increasing productivity and minimising downtime.
The specifications of these large track trenchers provide unmatched performance. The T16 is powered by a CAT C27 950 hp engine and 3206 lb-ft of torque, giving operators the power to withstand the toughest soil and hard rock conditions. It is equipped with a mechanical digging chain drive and digging chain choices with widths up to 60 in. (1.52 m), which provides a variety of options for every jobsite.
Whether a T16 trencher is being used for a water installation project in Indonesia or a natural gas project in Ohio, it is inevitable that the equipment operators will need access to quick and reliable service. This is why Trencor, sold and serviced through one of the more than 175 Ditch Witch dealerships worldwide, can provide world-class parts, service and support to all underground construction professionals at each and every stage of the machine’s lifecycle.
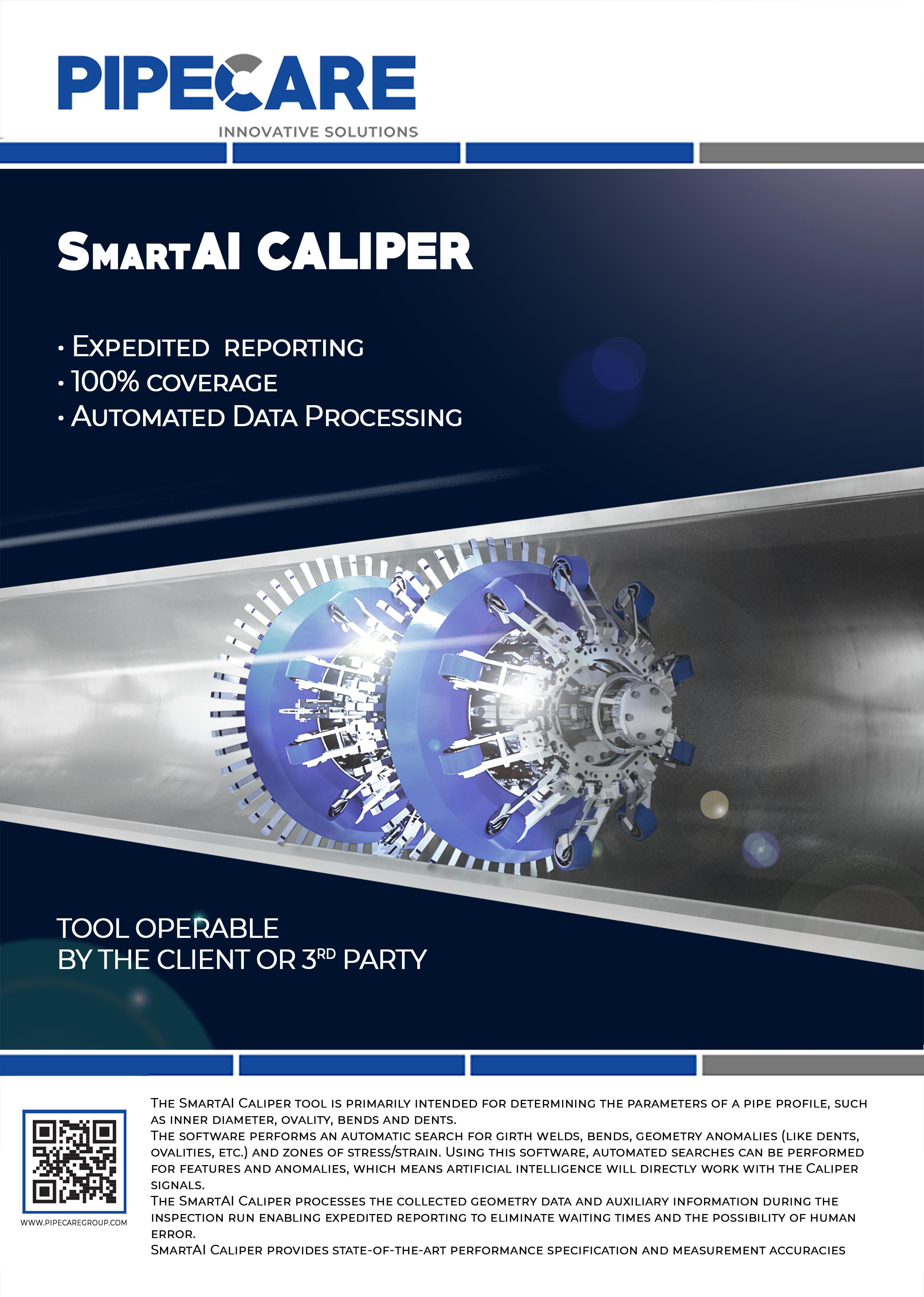