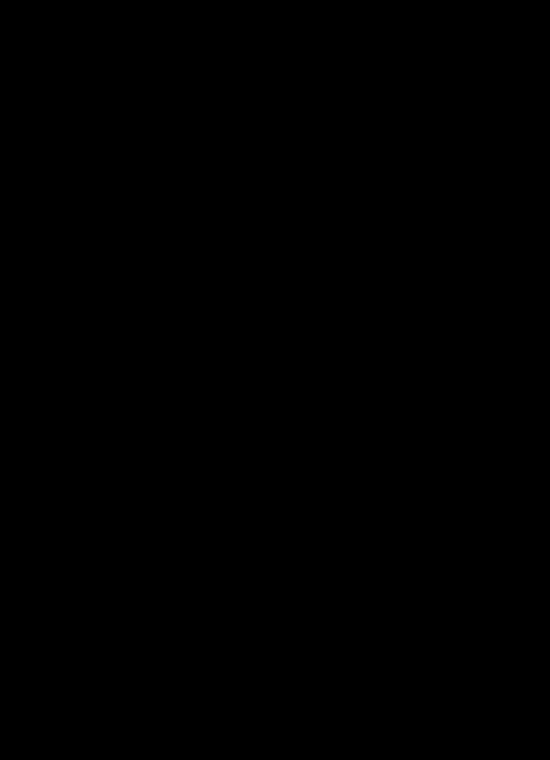
13 minute read
Closing the gap
many great people who share my vision of a future with low carbon emissions, championing communities, and including more people at the decision-making table.
I’m truly proud to be working in oil and gas, and working at Enbridge. It’s been an excellent career so far and I’m excited to see what the future brings.
EC: Do you have any mentors or role models in the pipeline industry? KE: I have many notable mentors in my life, including Michelle George, VP of Engineering, Storage and Transmission Operations at Enbridge Gas. She teaches me so much about leadership, building my technical abilities and how to improve my people skills. I’m so grateful to spend time with her, and I really respect and look up to her. I aspire to a similar career path.
I am regularly mentored by my people leaders at Enbridge Gas, most notably Paul Hammell (Direct Supervisor) and Dan Wallace (Manager of Engineering Construction). I think the most important thing I’ve learned from the both of them is what kind leadership looks like, and how to really be there for the team. I hear a lot of leaders talk about being there for their teams, but a leader who will get scrappy for you, who will hangout in a muddy trench with you, or who will bring coffee at 9 pm to a job site during unexpected circumstances are the real deal, and thats what Paul and Dan teach me about. Being an engineer in training, both of them are also particularly talented at guiding me through the problem-solving process from the perspective of an engineering professional. Paul and Dan demonstrate an unwavering dedication to not only being there for me, but also contributing to my growth. This is authentic leadership.
I also want to mention an important field mentor to me, his name is Derek Johnson. He is a construction superintendent. I really appreciate his mentorship because he has many years of field and construction experience, and everytime we talk I learn a lot from him. People in-field respect and trust him, and his mentorship allows me this opportunity to develop my skills around that. I aspire to be someone who folks on the frontline can trust and rely on. Growing up with a dad that was a union-rep (and still is), electrician and then electrical engineer – those values have been instilled in me from the beginning.
Culturally, Anishinaabeg people understand leadership as a circle as opposed to a hierarchy. To me, this means everyone has something critically important to offer. Its something I always want to carry with me as a future leader in oil and gas. You really have no business being any kind of leader if you’re only accessible to the C-suite, standing on a soap box in a suit and tie. To all the leaders out there: get your coveralls dirty and earn the respect of the frontline.
EC: What is your message to other young pipeline professionals? What makes this industry rewarding and attractive for young professionals? KE: Right now, we are on the cusp of energy transition. This requires diversity of thought because so much innovation is on the horizon, and the oil and gas pipeline industry knows this. It
Designed with you in mind, the UltraBox features a patented modular approach to quickly and conveniently provide custom
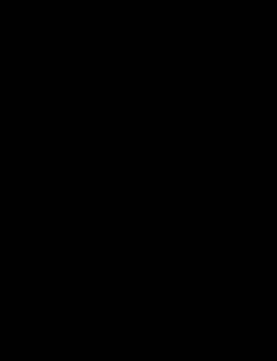
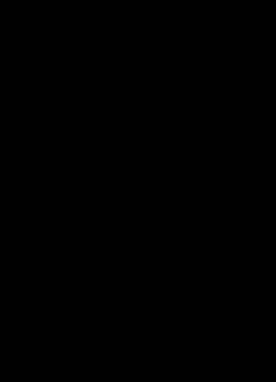
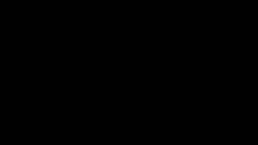
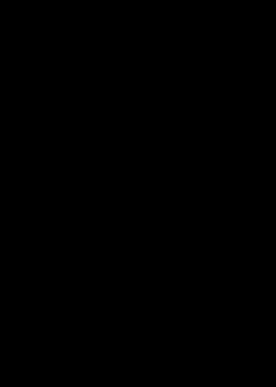

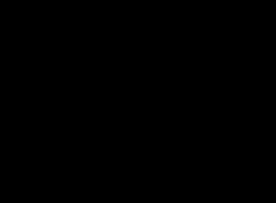
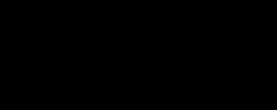

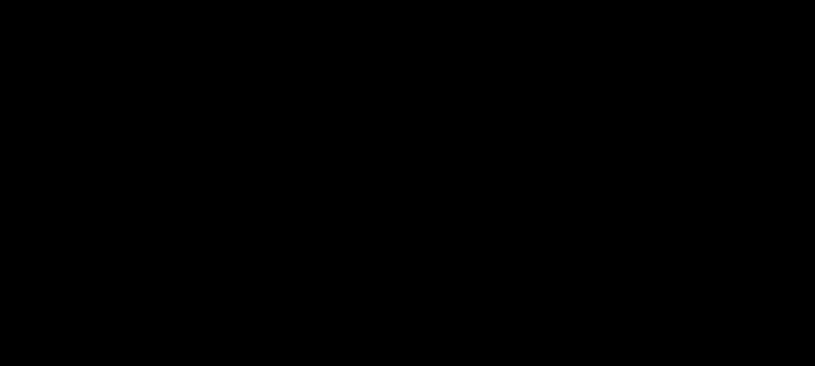
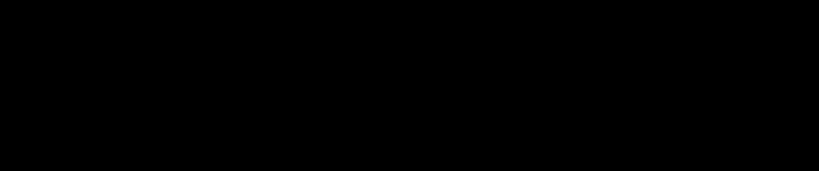



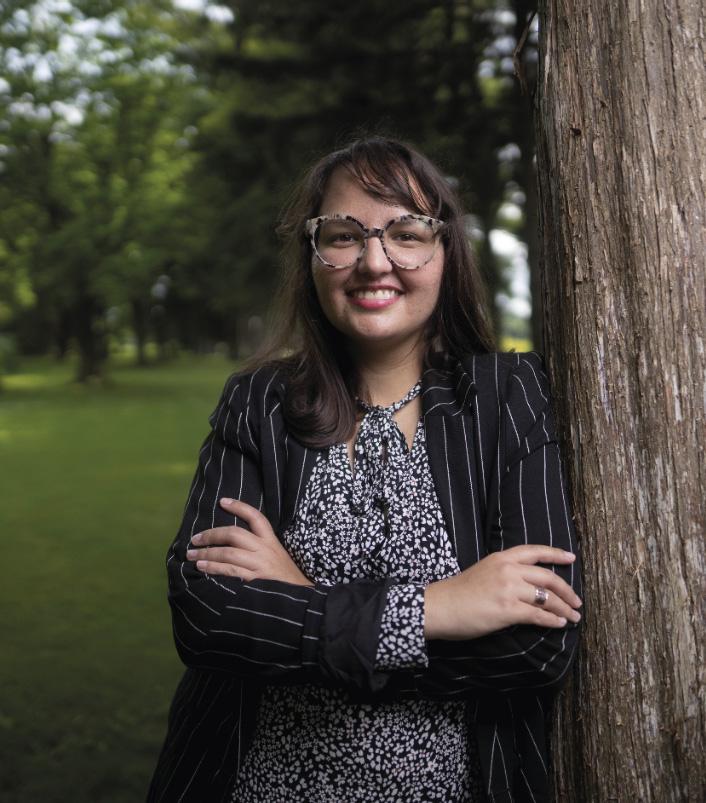
Kaella-Marie Earle.
makes working in energy an incredibly dynamic and fast-moving place to be right now. I work with a big group of absolutely amazing young people.
There’s so much room to do some good, whether its technological advances, retooling energy infrastructure, carbon emissions reduction, or outreach work involving local communities. Energy policies are changing too, as we learn more about what we need to do to address climate change. Theres so much to do. Trust me when I say you will be surprised at how progressive the industry is. We are moving forward, full speed ahead, into a brighter future – providing safe and reliable energy to people. Its such rewarding work. And its different everyday.
Plus its just fun. At my first pigging job I remember an operator yelling “Let ‘er rip, potato chip!” just before the cleaning pig launched. I was grinning as I listened on the receiving end of the gas storage pipeline for the pig to get there. An amazing amount of work goes into taking care of the lines and making sure they are safe and properly maintained, including maintenance of the surrounding environment. Who knew sending a foam bullet through a pipeline to clean it was such a good time? I sure didn’t.
You won’t regret a career in pipelines. Take it from me, the former anti-pipeline and climate change/environmental activist. You can work in pipelines and still care about the land, and have a meaningful career where you can enact as much change as you want.
It’s been an absolutely astounding couple of years for me at Enbridge. I’m grateful everyday that I work there.
EC: Can you talk about your hopes for the future? KE: I read a story once in a book by the Harvard Business Review on Leadership. The story was about the World Bank in the middle of an existential crisis. Circumstances of the world at the time were pushing the organisation into irrelevance, a movement driven by people and what they cared about. The strategy of the World Bank no longer made sense.
The bank knew it had to change, and it was just a few people within the organisation who understood inside of themselves that they needed to do something about it. So they did. They initiated this massive cultural renaissance at the organisation, aligning themselves with what society was looking for, recreating a compelling new direction forward. A new direction to re-energise the people working at the bank, and empower them to focus on social issues. These actions launched the World Bank into success once again.
My hope, or rather, my plan for the future is to help do exactly this. I’d like to help the oil and gas pipeline industry move into the future through a cultural renaissance. Business continuity is dependent on it. When people are empowered to make the change they want to see, they do. So we must ask ourselves, what tools must leaders provide to inspire people in a new direction for the industry?
It can be scary to enter into an era of so much change, because there is risk in doing things a different way – you always need to make space for failure. But this is what it will take to reduce carbon emissions inside of oil and gas. Its not going to be easy, but I fiercely believe in it. I have to.
I envision a future where oil and gas workers are re-employed, working in renewables or carbon-emission reduction. The work isn’t disappearing, it’s changing. We need to keep up. I imagine a future where Indigenous inclusion is normalized, and socioeconomic gaps are closed because the industry builds up the communities around them. I imagine a future where people view stewardship-to and their relationship-with the land in a new way. I imagine an industry where the CEO of Enbridge (or TC, or Suncor, or Cenovus, etc) is an Indigenous woman. Is a black woman. Is trans. I dream of an industry that has led energy globally into the next few decades on a new frontier. And I’m prepared to do what it takes to help get us there.
About Young Pipeliners International Young Pipeliners International (YPI) is a forum where young pipeliner groups from all over the world collaborate to share experiences and best practices.
Representatives from groups in USA, Canada, Mexico, Brazil, Europe, Australia, India, Nigeria, Malaysia, and China share the common goal of building the next generation of pipeliners.
YPI helps newcomers to the industry to gain knowledge, experience, and understanding of different facets of pipelines.
YPI is a vehicle to help the next generation prepare themselves for the transfer of duty of care in the pipeline industry.
For more information on YPI or to learn how to join or form a regional group, email youngpipelineprofessionals@gmail.com
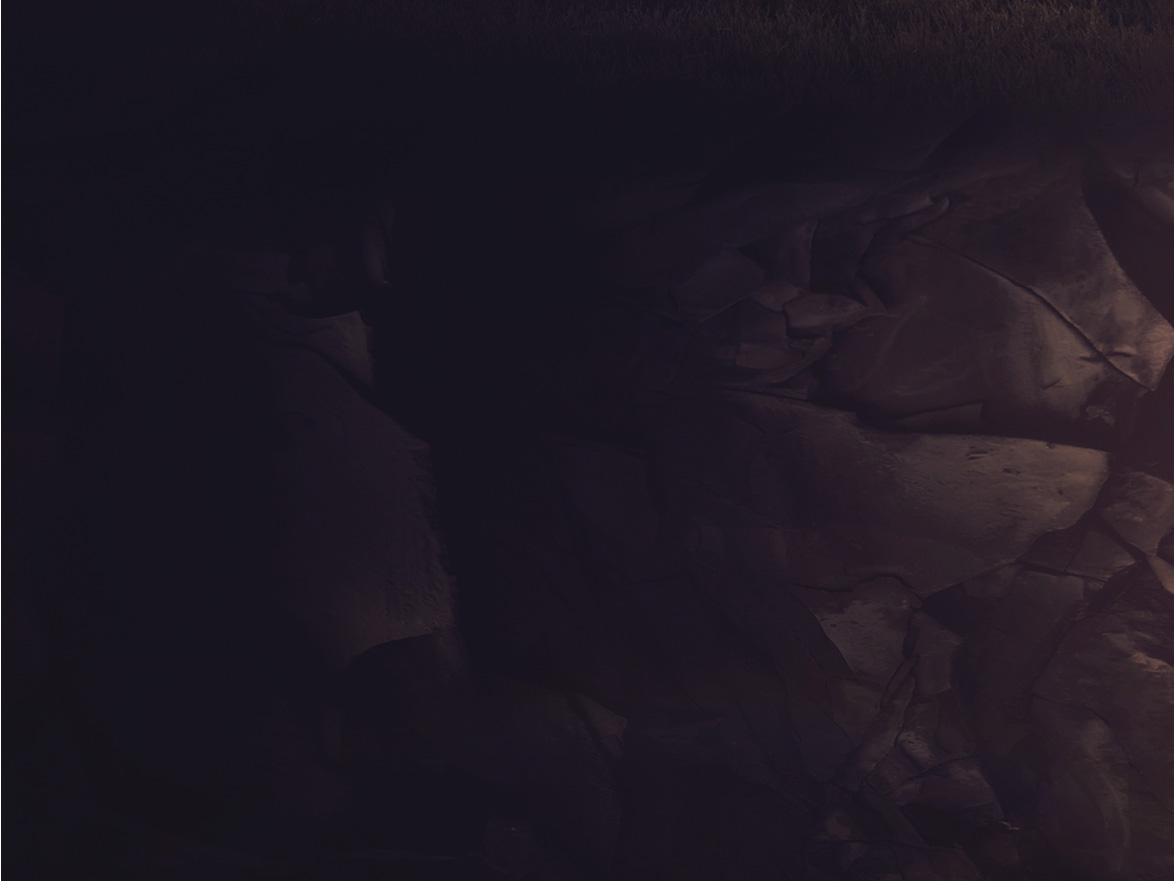
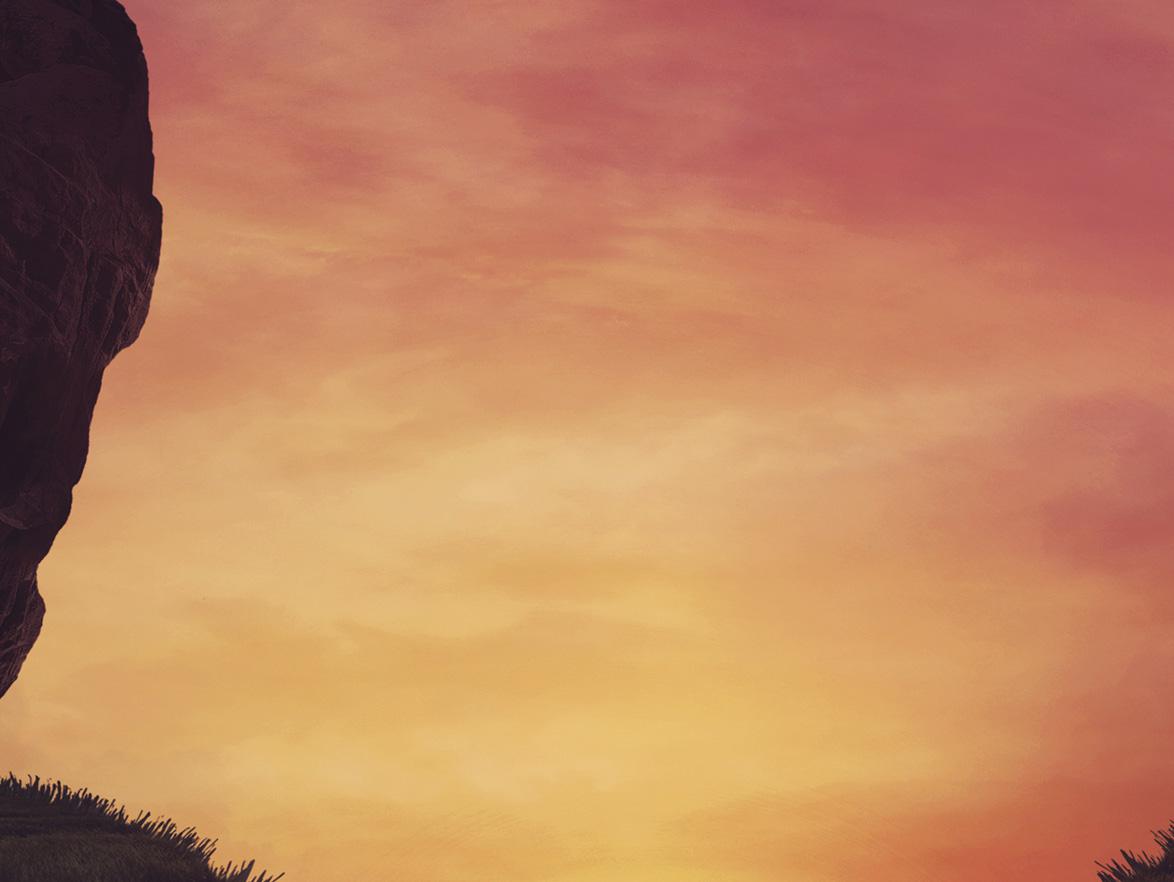
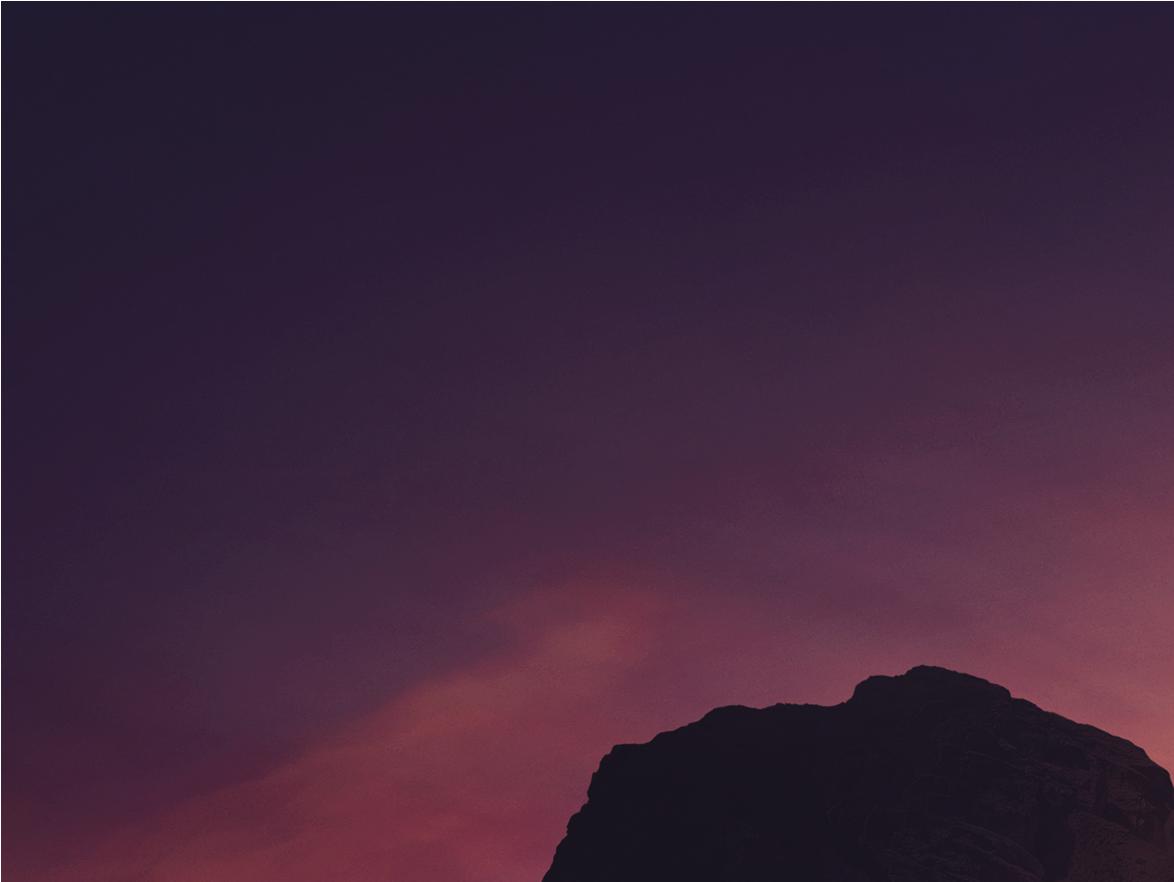
The Trans Adriatic Pipeline (TAP) is one of Europe’s most strategic energy projects. A part of the Southern Gas Corridor, TAP transports natural gas from the Caspian region to Europe by connecting to the Trans Anatolian Pipeline (TANAP). The 878 km TAP pipeline crosses Greece and Albania, under the Adriatic Sea, and comes ashore in southern Italy. TAP began commercial operations midNovember 2020 and first gas started flowing at the end of December 2020.
Senior managers have long considered handover to operations to be a critical process, not only because of capital cost implications, but also due to the number of stakeholders involved in complex projects. The benefits of an effective handover to operations are twofold: reducing the risk of costly remedial actions and improvement of operational safety. The Barry Monk, TAP Operations and Maintenance Country Manager, and Rocio Miguez, Principal Engineer, Energy Systems, DNV, explain how TAP’s robust Assurance Process ensured a seamless transition between project, commissioning and operations.
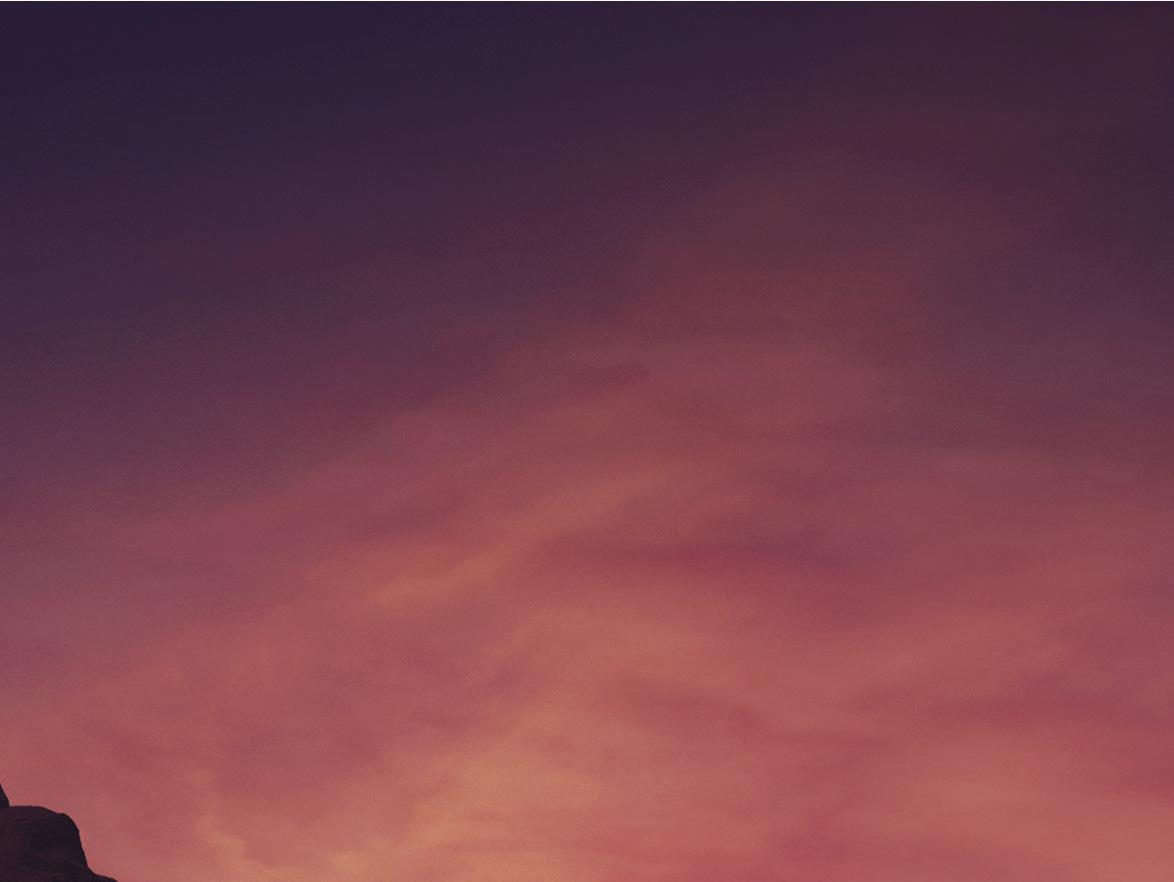

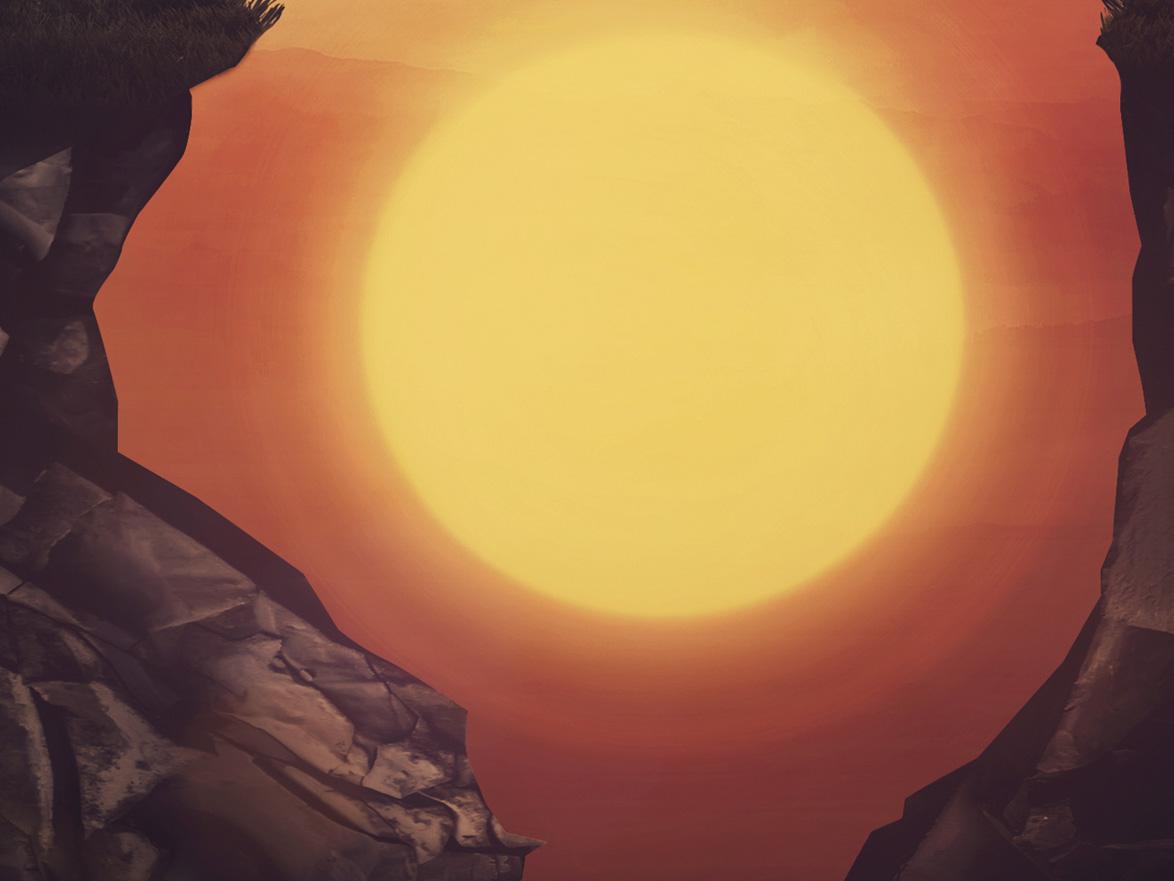

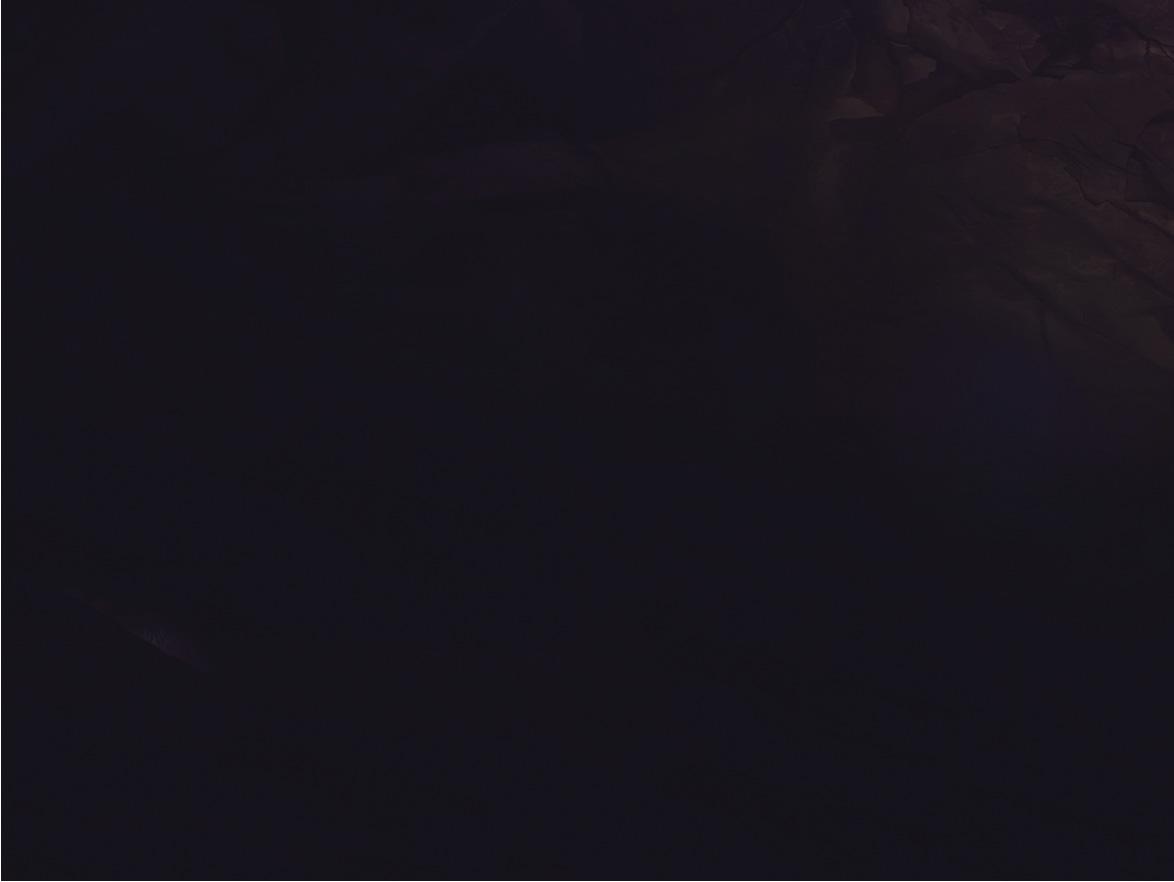
latter was one of the key driving factors behind TAP’s successful Assurance Process, which complemented the handover.
Effective start-up and readiness assurance processes can prevent incidents. One notable example of an accident linked to an ineffective implementation of such processes is the BP Texas City refinery incident which killed 15 and injured more than 170 others.1
TAP Operations Assurance Manager, explains: “We recognised that TAP was a new organisation and as such did not have well-established legacy systems nor an embedded culture of operational assurance. There was an opportunity to develop a robust assurance system, reflecting industry best practice techniques, adapted to suit TAP’s specific needs. Ultimately, this became TAP’s Start Up Readiness Assurance Process – SURAP.”
Once the strategic decision had been made to implement SURAP, TAP engaged DNV to produce a procedure that combined technology with TAP’s organisational structure and methods to support the transition from project to operations, and enable operations to demonstrate readiness for start-up and early transmission operations. A dedicated operational readiness team was established to work with the project, commissioning and long-term operations teams. According to Ruurd Hoekstra, Operations Readiness Transition Manager, “Early input from the Operations team was recognised as a critical component of the design and construction process. A key aspect of that was to maximise operational experience and insight during the design and execution phase, working with the projects team to ensure pipeline and facilities’ long-term reliability.” DNV was further tasked to support the execution of the process as part of the integrated operational readiness team, and to provide independent consistency of assurance across disciplines and countries during the construction and commissioning phases of the TAP project. The SURAP had to provide an opportunity for a cross functional team to: ) Verify that all technical requirements for each specific asset or facility and interdependent assets and facilities were in place, and supported by the associated technical documentation and certification dossiers.
) Verify that all information regarding operational readiness, including HSSE and operations
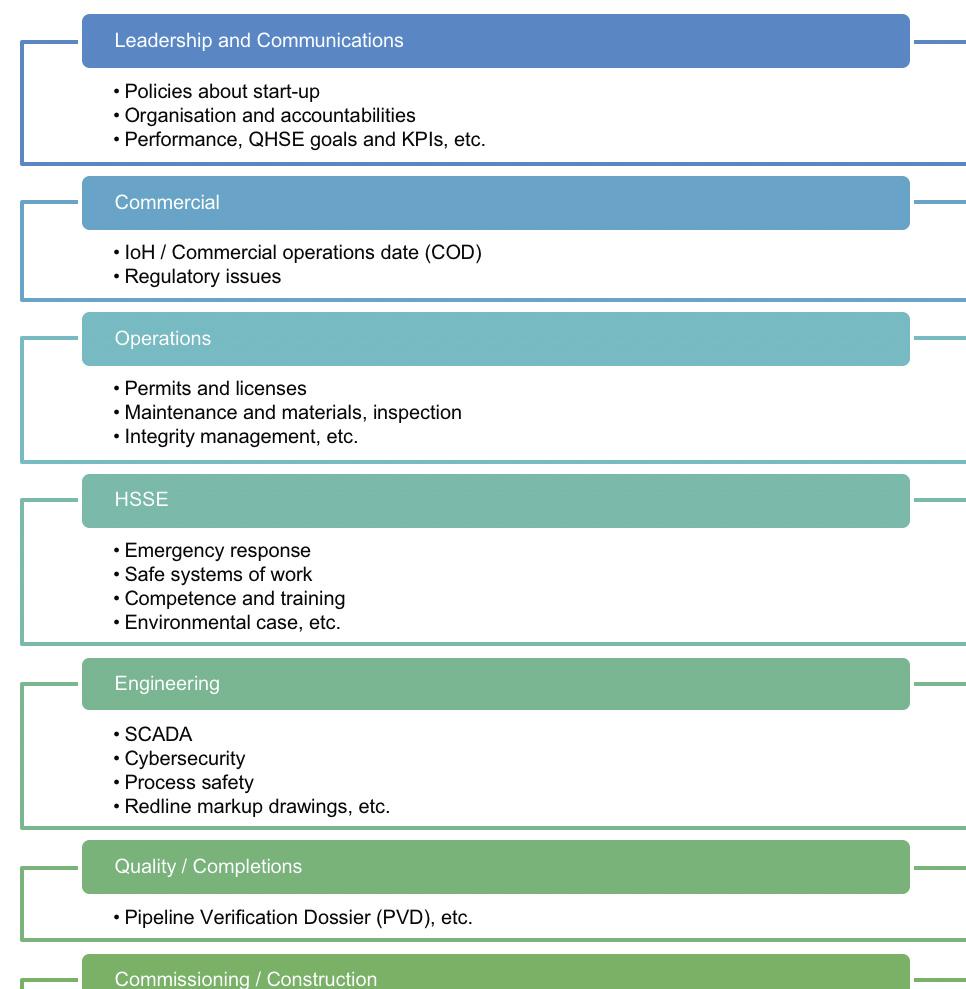

Figure 1. The seven sections depicting Verification of Readiness (VoR).
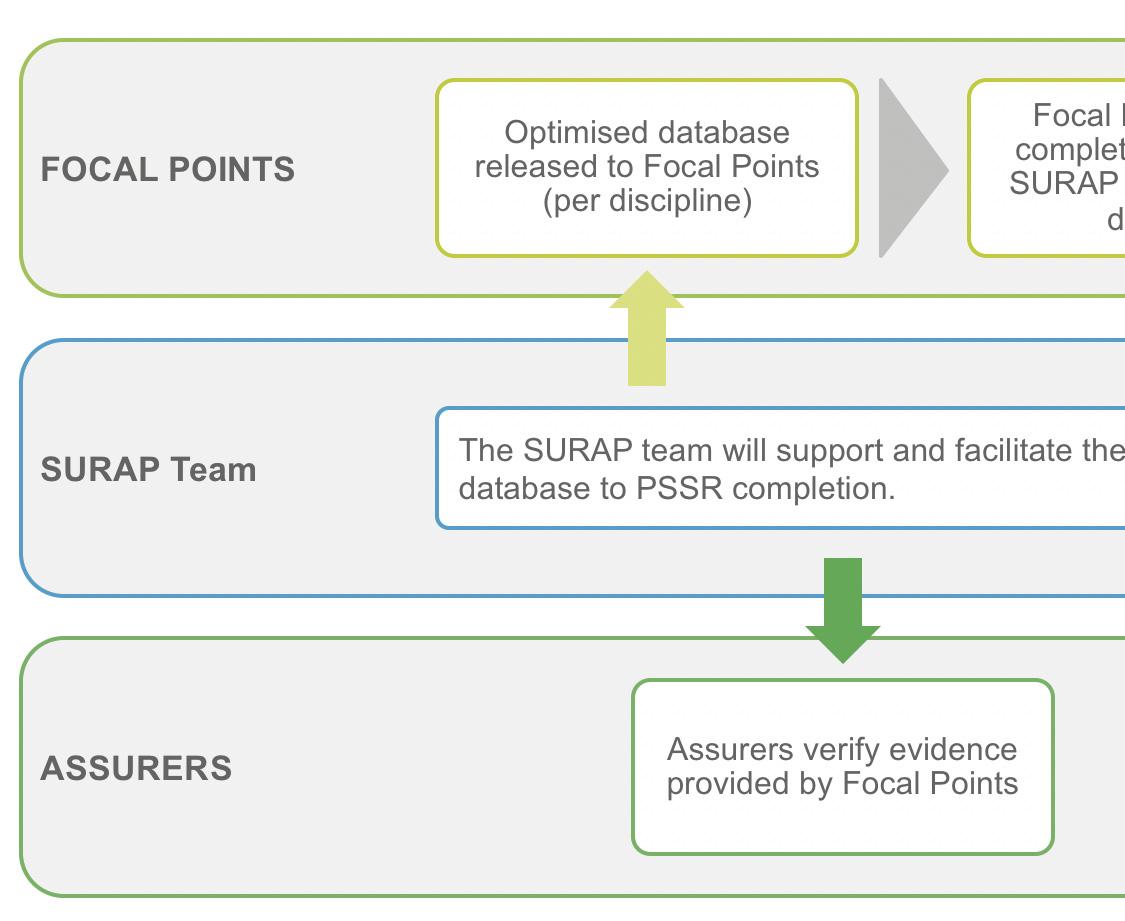

Figure 2. SURAP responsibility relationships.
management system, permits, consents and management system, permits, consents and licences, as existing operations and maintenance industry codes. TAP’s licences, as well as organisational structures, well as organisational structures, including trained and code of choice EN 1594 (Pipelines for maximum operating including trained and competent resources competent resources were in place and in a state of pressure over 16 bar. Functional requirements) referenced EN readiness. were in place and in a state of readiness. 12327 (Pressure testing, commissioning and decommissioning procedures. Functional requirements) for commissioning, but ) Verify that the required business processes, e.g. the standard did not contain specific assurance requirements, documentation & data management, logistics, supply enabling TAP to determine the level of verification required. chain, materials & spares, contracts & procurement, The checklists were drafted drawing from both TAP and commercial arrangements, hydrocarbon accounting, DNV expertise, as detailed in: were in place prior to the progressive start-up of ) DNV International Safety Rating System ISRS. the integrated gas transmission system (commercial operations). ) Centre for Chemical Process Safety (CCPS) Guide to PreStart up Safety Reviews.
In addition, the SURAP had to: ) Ensure seamless communication and transfer of Ruurd Hoekstra explains that the database goes beyond asset-related information between the stakeholders: the level of assurance he has experienced working for other contractors, suppliers, and operators. operators, as the TAP organisation and assets are start-ups with no operational history. ) Ensure senior managers were provided readily accessible Cross-checks and reviews of the Verification of Readiness progress information to support any go/no-go decision- (VoRs) sheets and Pre-Start Safety Reviews (PSSR) contents making process. were subsequently conducted by the SURAP Process Owners and by TAP key personnel and subject matter experts. The
The delivery of the SURAP objectives was based SURAP database was divided into seven VoRs, each of on the use a of a bespoke TAP-specific checklist to them referring to a specific discipline to be checked before verify all required parts of the process were completed introduction of hydrocarbons (IoH) into the system: simultaneously. Each sub-VoR was driven by a nominated focal point, one or more accountable persons responsible for the completion Creating the SURAP database of the SURAP requirements, and assurers with a level of The first phase of the SURAP process was devoted to independence, who verified that the evidence provided met generating the database. The Assurance team looked at the the requirements in a timely manner.

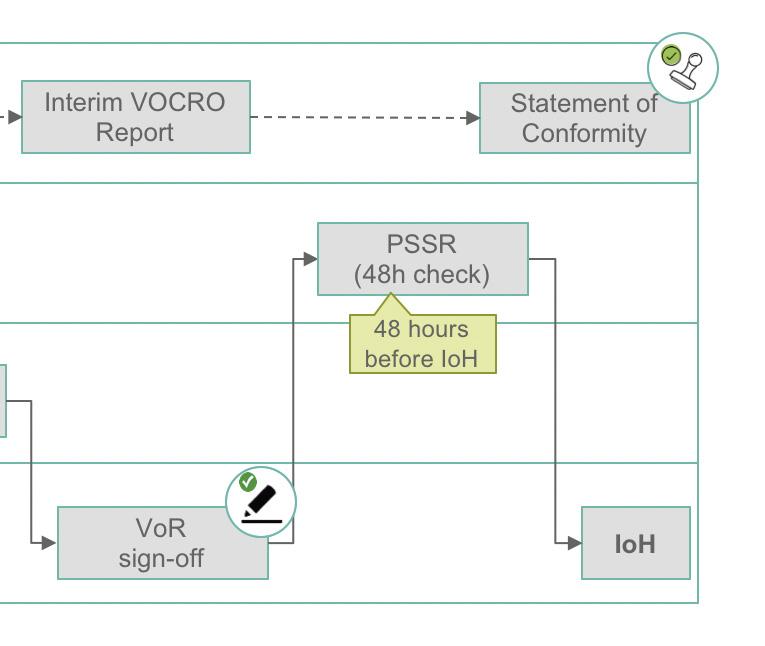
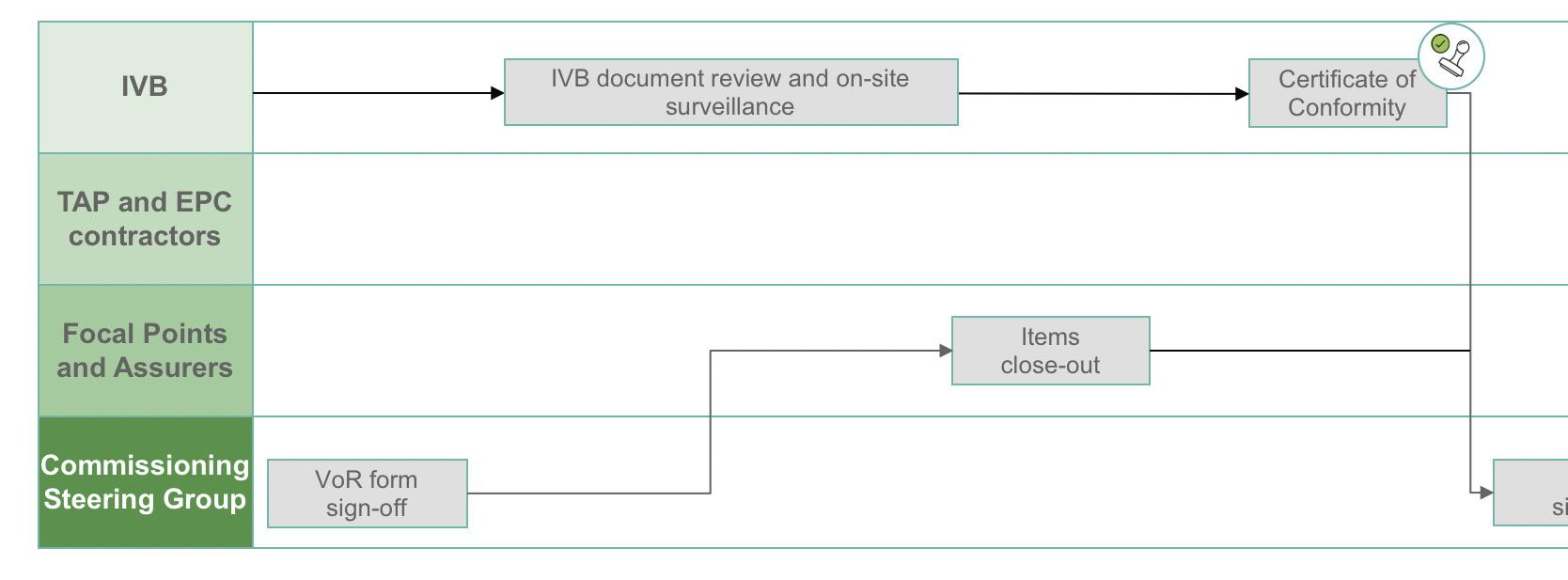
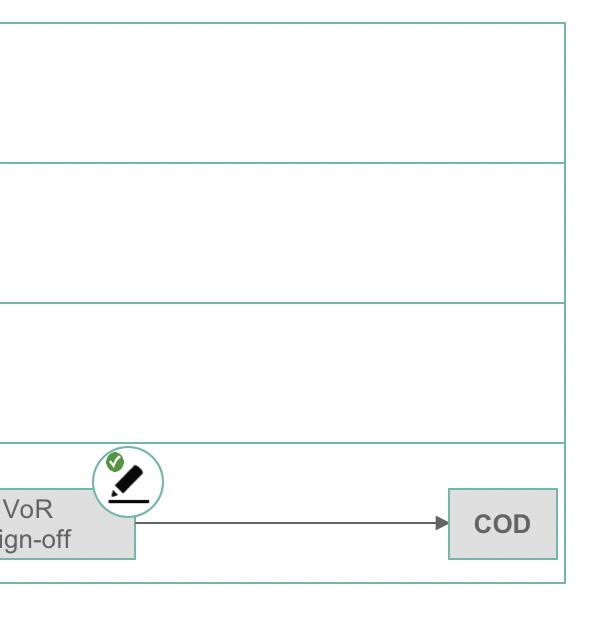
Figure 3. SURAP VoR Completion through Introduction of Hydrocarbons (IoH) to Commercial Operations (COD).