Nottingham Custody Suite
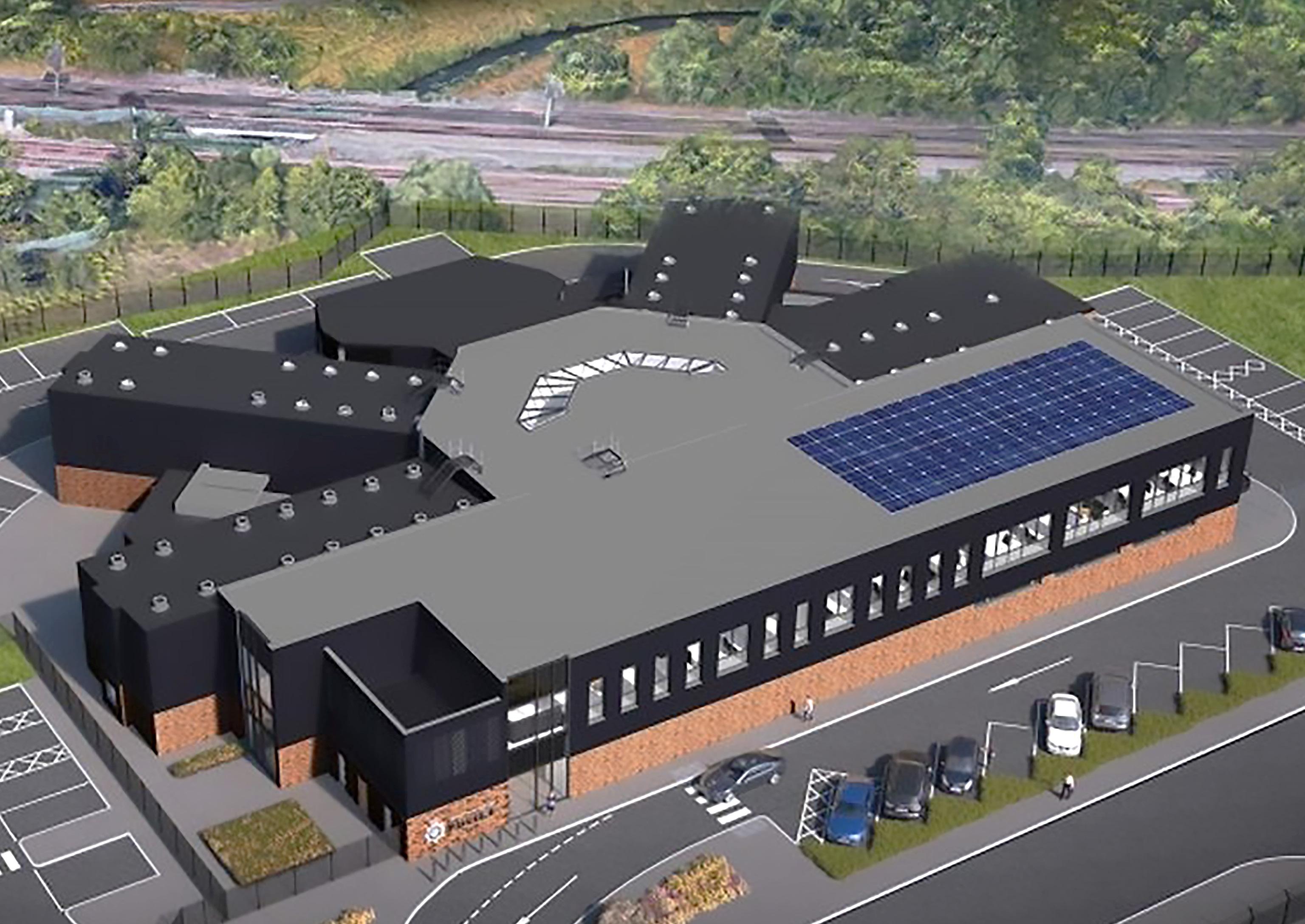
HybriDfMA Secure Custody System
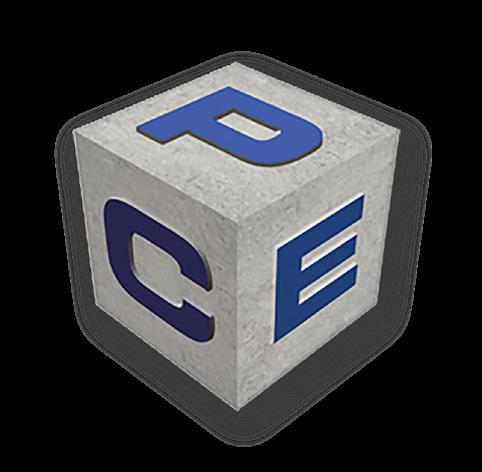
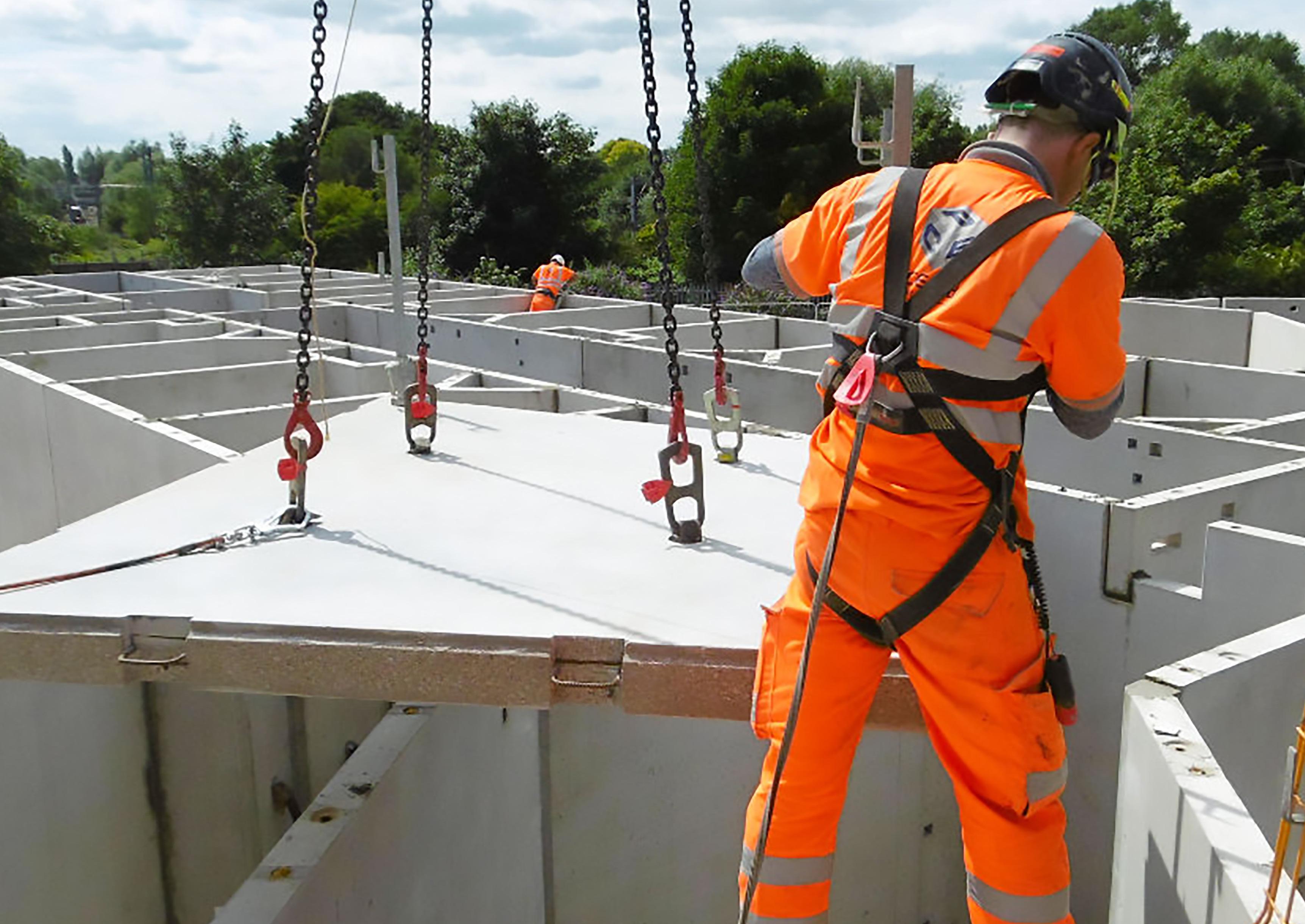
The Nottingham Police Secure Custody suite built just off Radford Road, Nottingham continued the close working partnering relationship of PCE Ltd with Main Contractor Willmot Dixon who delivered the £17.8 million project for Nottinghamshire Police, with Gleeds as Project Managers, Architects Corstorphine + Wright, and HSP Consulting Engineers Ltd The project, built to replace the old city centre Victorian Bridewell was the 15th Secure Custody suite in recent times that PCE had been undertaken with the company being responsible for the design, offsite manufacture and onsite assembly of 5 cell block wings. containing 50 holding cells for male, female and young offenders in addition to ancillary rooms and a charge desk area.
PCE had agreed their programme of onsite works to be undertaken in 6 weeks. Despite the overall project start on site being at the commencement of the first Covid pandemic lockdown due to enhanced development of the design process and details, a more efficient manufacturing strategy as well as improvement of onsite assembly methods the multi-skilled PCE site team completed the assembly in only 4 weeks.
As usual Health and Safety of all was the top priority and the site programme reduction of a third was achieved without any accidents or associated issues, including the extra safe working requirements that had to be developed and implemented due to the pandemic. The reduction in site assembly duration and other time gained due to the manufacturing strategy meant that the overall programme saving achieved was 6 weeks.
The project comprised of a single level of cell block wings laid out in a radial footprint containing 50 holding cells for male, female and young offenders in addition to ancillary rooms and a charge desk area.
In total 311 reinforced precast concrete components were used to provide the facilities using PCE’s Secure Custody ‘kit of parts’ approach for police holding cell construction principally based on repetitive use of four common component types. The external wall, duct wall, corridor wall and cell roof components creating an exceptionally durable ‘concrete box’ with the walls between and to the front and rear of the cells, along with the roof of the cell forming, once constructed, a monolithic concrete structure including a central access corridor between the lines of cells.
This project was another example of PCE’s HybriDfMA approach to providing Secure Custody solutions, based on Design for Manufacture and Assembly principals, using a common ‘kit of parts’ of reinforced precast concrete components configurable to meet the specific needs of this client’s particular scheme.
PCEs internal design team embraced the fully Level 2 BIM requirement for the project, with 3-dimensional modelling using Revit, including the clients design team requirements for mechanical and electrical services cast in conduits and builders-work openings. All were fully coordinated in the digital environment to ensure accuracy of requirement and positioning avoiding anti-clash.
Security features such as cell doors, windows and roof lights were easily integrated during the design process within the precast concrete components via an approved set of common interface details. The Architectural intent and finish requirements were managed to understand which surfaces were critical. This enabled a casting strategy to be developed ensuring that where required high quality finish requirements for direct decoration were easily obtained.
The project was delivered in accordance with PCE’s Digital Delivery Strategy providing real time data at every stage of the design, manufacture and assembly process. This strategy ensures the integrity of the design data along with providing the project teams with the means to make informed decisions throughout the lifecycle of the project and collate lessons learned to help improve future projects.
CLIENT
MAIN CONTACTOR
ARCHITECT
PROJECT MANAGER
CONSULTING ENGINEERS
PCE LTD PROJECT MANAGER
£807,000
Nottinghamshire Police
Wilmott Dixon
Corstorphine & Wright Architects
Gleeds HSP Daniel Gallagher
The Custody Suite is located off Radford Road, behind Selco builders warehouse with a boundary being against the Midlands trainline. Nottingham Custody Suite Radford Road, Basford, Nottingham, NG7 7EF
Designed to comply with the latest edition of the Home Office Police Buildings Custody Design Guide, and the resultant ‘Lambeth Cell’ configuration. The PCE Secure Custody System has been developed and refined over many years to maximize the many benefits of offsite manufacturing and onsite assembly efficiency.
An Overview of the concept can be found at:
https://pceltd.co.uk/hybridfma-secure-custody-system-overview/
Co-ordination with the Main Contractor and other specialized contractors formed a critical part of this project delivery. The structural steel frame structure for example fixed above, and supported by, the precast concrete structure required careful design co-ordination to ensure structural loads were transferred effectively. By maximizing the many benefits achieved by use of the standard ‘kit of parts’ component set and their predetermined geometric features and limits, design integration between structure, building services, architecture and security features was simplified and streamlined, with significant reduction in time and cost from the design development phases.
The Secure Custody System generated significant benefits throughout manufacture and onsite phases enabling the overall 6-week reduction by PCE compared to the original programme.
The 311 precast concrete components were manufactured by Bison Precast, Part of the Forterra Group using a combination of their standard mouldage and PCE owned bespoke moulds.
Specifically designed for the Secure Custody System to ensure high quality delivery with regards to assembly accuracy and surface finishes required PCE have invested in precision made steel moulds and mould formers for door openings and for casting M&E requirements.
Such investment ensured the project would benefit from reduced tolerances with improved surface finishes and casting details, thus providing a superior product and reducing the necessity of on-site finishing works for this project helping to enable the programme reductions achieved.
A new Duct wall mould was also purchased by PCE, as project specific requirements of the Nottingham Police Custody Suite departed from the traditional ‘Lambeth Cell’ layout and required some ‘Y’ shaped ducts as well as rectangular.
As PCEs extensive experience in delivering Secure Custody Systems has grown so too has their expectations for precision and quality from the manufacturing supply chain and the Nottingham Police Custody Suite is a great example of this constantly evolving drive for improvement.
Each of the Secure Custody `kit of parts` reinforced precast concrete components had its unique manufacturing methodology that created the correct degree of quality required from the most efficient designs. Types of finish, intricacy, design constraints and delivery/assembly orientation were all considered within the manufacturing methodology, and all manufactured in accordance with PCE Ltd ISO9001 Quality System.
The clients team visited manufacturing facilities to sign off one of each respective component type, to be used for acceptable standard acceptance purposes. They were very complimentary on the coordination with other trades in order to deliver the desired M&E strategy and the high quality being achieved.
For the 5 separate cell wings and ancillary areas that PCE were responsible for the crane use strategy and its positioning were key to ensure the assembly works were carried out as efficiently as possible.
potential hazard was the close proximity the very busy Midland trainline which required and dictated a very clear and concise sequence for the assembly construction, with all the necessary checks, restrictions and necessary Network Rail approvals to be in place.
The fork shaped Duct walls were cast vertically using PCE owned bespoke steel moulds so that all the visible faces were formed against the mould faces to provide a high-quality finish. Set into the moulds at standard positions were steel formers for the sinks, toilets and vents. Radii and skirting recesses were also set into the moulds to ensure the accuracy of key important detailing.
Cell roof components covering the area of two cells and associated ducts were cast flat on steel tables in their final orientation, ensuring a high-quality finish to the cell ceiling and providing a floated finish to the upper face which formed the plant room floor. Magnetized steel formers were fixed onto the moulds to create the main roof light opening.
The intricate Corridor walls were cast from steel vertical moulds so that all the visible faces were formed against the mould faces to provide the required high-quality finish. The PCE owned bespoke profiled steel formers for the cell and riser door were set into the vertical mouldage at standard positions with specific key positions set within the moulds for containment of them, ensuring they could be positioned accurately and held firmly during concrete placement.
External walls were cast flat on variable steel tilt tables, ensuring a high-quality finish to the internal cell face and a floated finish provided for the cavity face. Tilt tables were used to minimize unnecessary handling reinforcement that would otherwise have been required to turn the unit vertically into its delivery orientation.
• Finite Element Analysis Modelling
• Preconstructed Families with Intelligent Data
Architectural Model
Mechanical & Electrical services design
Structural Design
Componentised Model
SCIA Model PCE Revit Families Systems Library Systems Library
• Kit of Parts Designs
• Typical Connections
• Temporary Works Designs
• Typical Connections
• Custody Specification
• Typical Interface Details
• Confirmed Setting Out & Component Specifications
• M&E Components
• Secure Doors
• Secure Windows & Roof Lights
Families M&E & Secure Component Designs
Procurement Schedules
Free Issue M&E Components
Smart Integration Model
Fully Coordinated Model
Fabricated Drawings
Construction Assembly Drawings
Systems Library Procurement Schedules
• Typical Details
• Moulds
• Fixtures & Fittings
• Casting Schedules
• Assembly & Logistics Schedules
PCC Component Manufacture
Method Statement
Critical to the success of delivering the project was for PCE to manage the alignment of all the supply chain partners to enable the efficient and timely manufacture of the ‘kit of parts’ components required for assembly on site.
Factory 7
Window and Door Security
Design Tracker
• Engineering
• Modeling
• Detailing
• Issue for fabrication
Manufacture
• Scheduled for manufacture
• Manufactured
• Inspected and ready for dispatch
• Dispatched
• Received on site
• Assembled
• Secure connection completed
•
• Temporary works
• Inspected and signed off
As with all PCE projects, safety remains the number one priority, Nottingham Police Secure Custody Suite, an assembly/build methodology plan complete with all necessary risk assessments and method statements ensured that all safety issues were identified ahead of time and managed accordingly.
Daily on-site briefings were conducted to enable site operatives safely and efficiently, with all necessary information provided on information boards. The information boards were updated day by clearly demonstrate progress to date, identifying access routes any being carried out by other trades that may have an impact. PCE on This information was imparted by drawings showing 3 dimensionally erection sequence and all interface and temporary works considerations required.
Leading edge barriers were generally fixed to components prior to protect the work force, however in instances where this was not due to the direction of work, the viper line fall restraint system was
Project Specific Health & Safety
priority, and for the methodology statements managed to work on the site by day to any work on that day. dimensionally the considerations to erection not possible was used.
50 Cells Installed
480 Cumulative Man Hours
0 Accidents
0
Near Miss
To ensure all components arrived on site ready to be installed, requirements were progressed offsite wherever possible thus reducing the requirement for on-site manual handling, Temporary hole covers for cell roof openings and other necessary bracketry and leading-edge protection barrier Site Operatives were provided with detailed drawings, the build so they always understood how and where to and the required build sequence.
Willmott Dixon helped to facilitate the forward thinking wider design team and other trades activities accordingly information ahead of traditional build timelines and encouraging construction strategy possible.
installed, temporary works possible during the manufacture stage handling, drilling, and cutting works. other penetrations complete with barrier feet, were all installed offsite. clearly illustrating the sequence of to install the necessary components
thinking PCE processes, managing their accordingly to provide all necessary encouraging the best offsite
The diagrams illustrate how the ‘kit of parts’ components formed part of a cell wing block.
Base connections of the wall and duct components consist of cast in sockets with threaded projecting dowels that were grouted into pockets formed into the foundations.
Cell roof components connected to the walls and each other with projecting reinforcement loops from the roof components going over projecting dowels from the wall component to form a fully grouted shear key joint.
Duct walls connected to corridor walls with reinforcement ties and projecting wire loops in a fully grouted flush finished keyed joint.
Cell roof components connected to walls with projecting dowels from the walls into grouted pockets, finished flush with the top of the roof component.
The police cell wings were assembled with all necessary grouting works completed before the cell roof components were installed.
Grouting works needed careful planning to ensure sufficient time for grout strength development resulting in the most efficient sequence for the release all temporary propping and ensuring the safety of the grouting team whilst the crane and erection team continued in other areas.
With onsite assembly works being completed well ahead of the initial contract programme, the final unit was installed on the last wing. The Client and Wilmott Dixon were delighted with the achievements of the whole PCE team involved with the project.
With another Secure Custody System project completed PCE are even better placed for future similar contracts, absorbing and reacting to ‘lessons learnt’ and continually progressing advancement in design, manufacture and assembly techniques.
The Nottingham Police Custody Suite project team included:
Daniel Gallagher – PCE Ltd Project Manger
Andy Matheson – Responsible for Design, Manufacture and Assembly technical coordination
Steve McEvoy – QS
Gary McBride – Construction Manager
Scott Lambert - General Foreman
Gareth Loveridge – Erector
Jamie Ashley – Erector
Dave Carroll – Slinger
The site assembly team completed all erection works in 18 working days, a great achievement. Andy Matheson graduated in Civil Engineering from Nottingham Trent University before joining PCE Ltd and this Nottingham project was the first for which he took full control of all Design, Manufacture and Construction technical co-ordination responsibilities and demonstrates the career path and learning that PCE can offer to its staff.
Construction team
The projects Carbon footprint was significantly reduced by PCE’s approach including sourcing the precast concrete components from Midlands based manufacturing facilities and the site team also from the same region thus reducing travel distances.
By manufacturing in factory-controlled environments skilled workers reduce the amount of construction waste that would have occurred for a full on-site build.