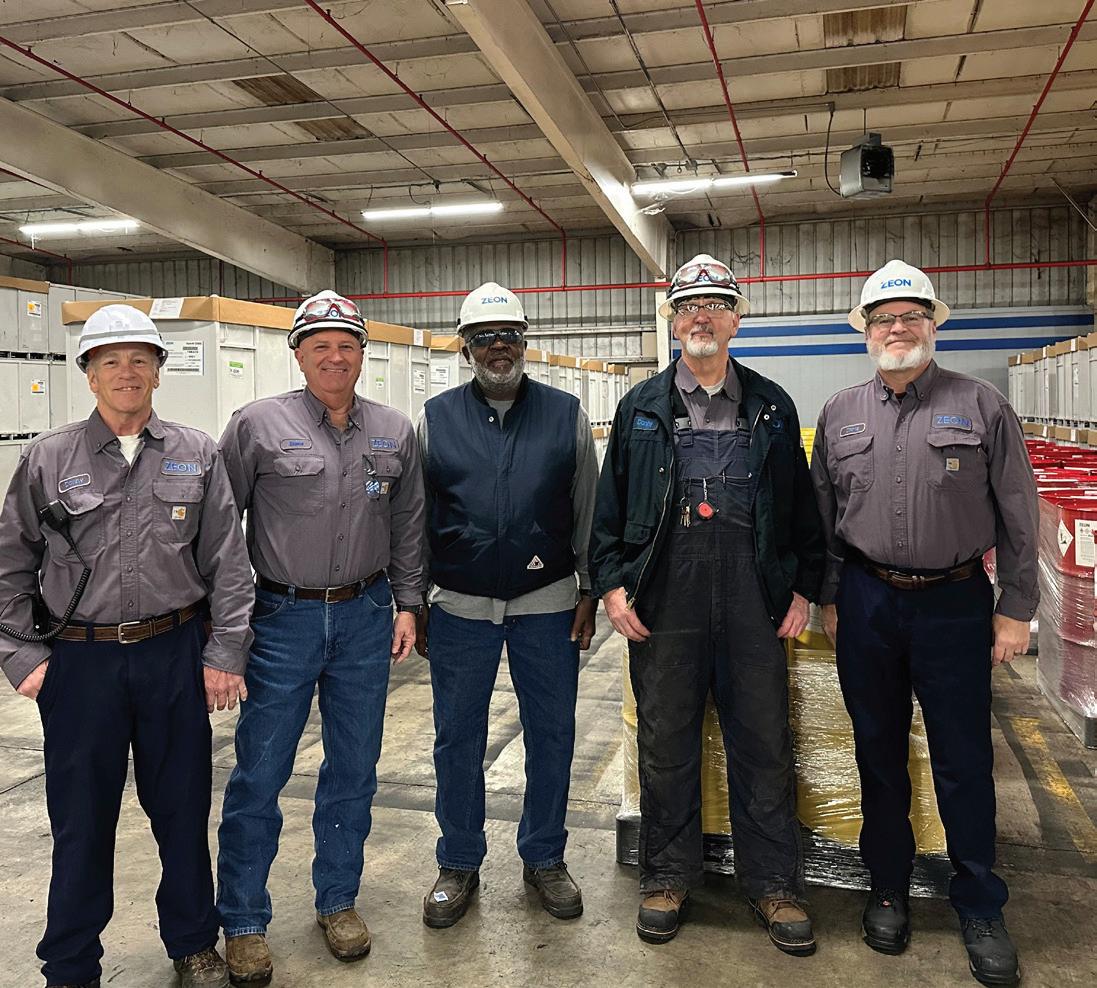

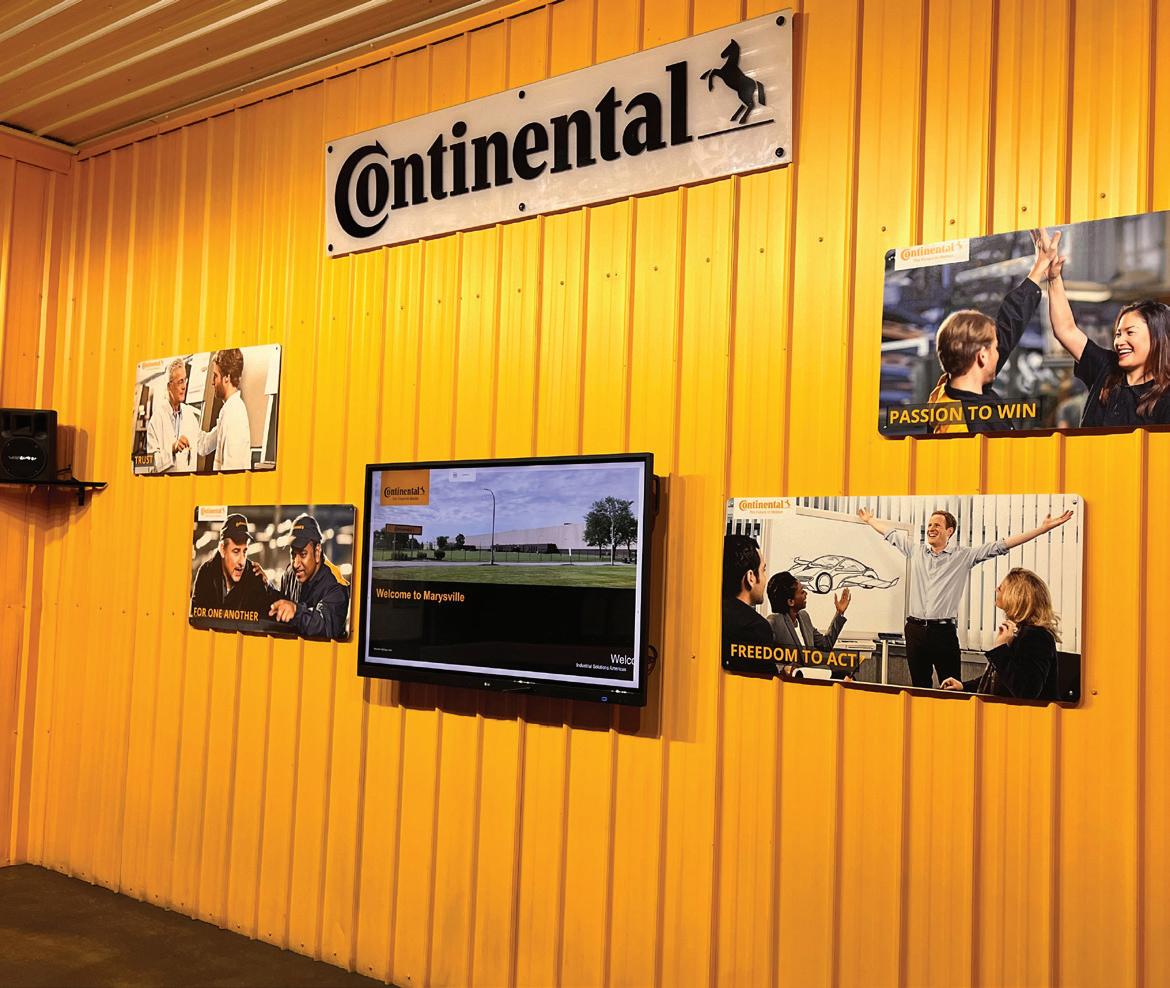
Benchmarking & Best Practices Conference Preview
Mitigate Risks with a Crisis Plan
Legislative Changes in Manufacturing
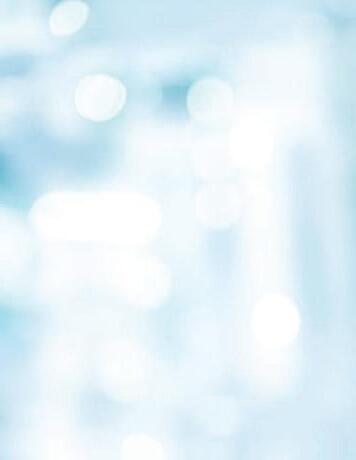
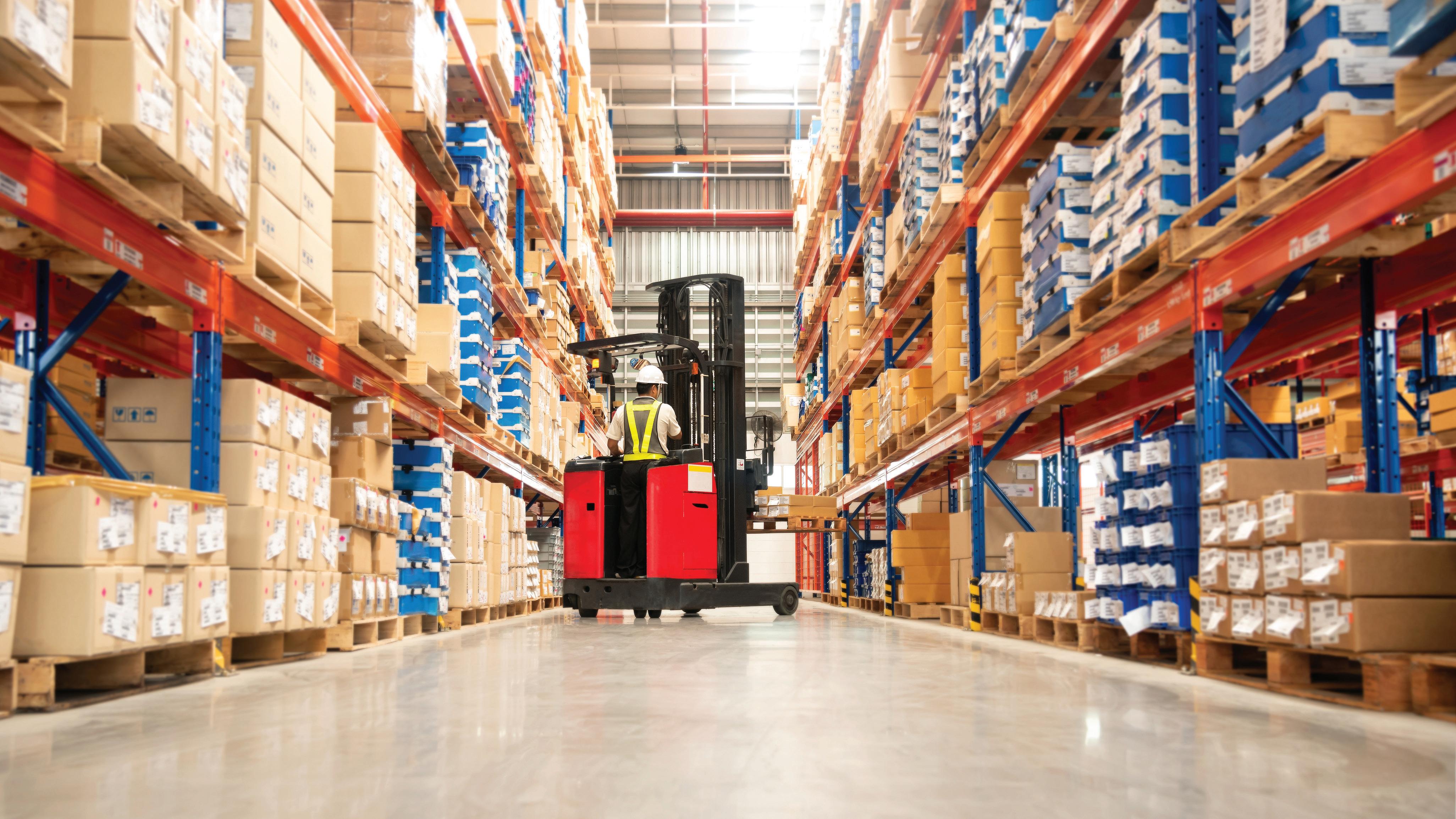

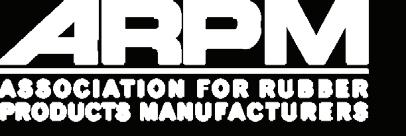
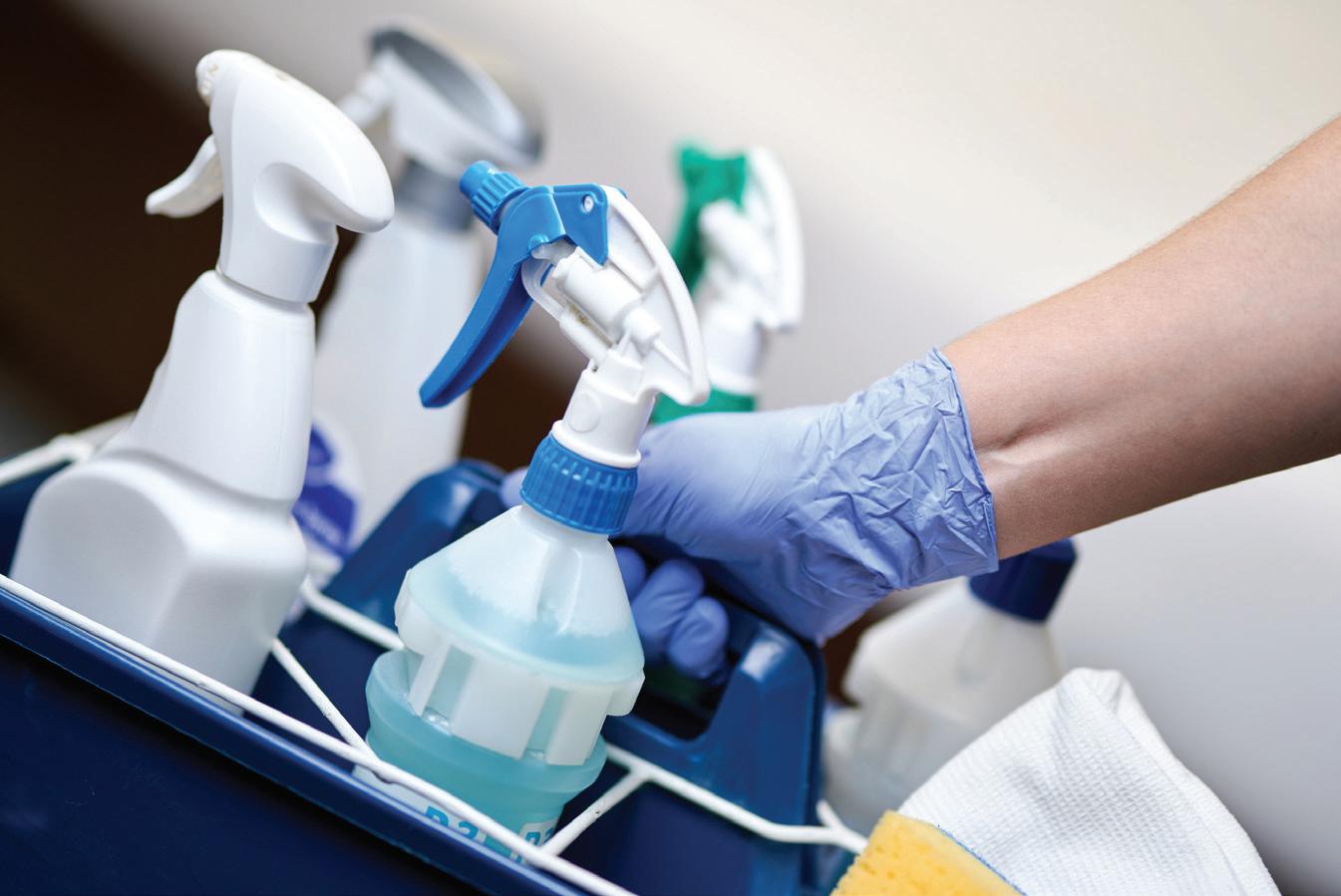
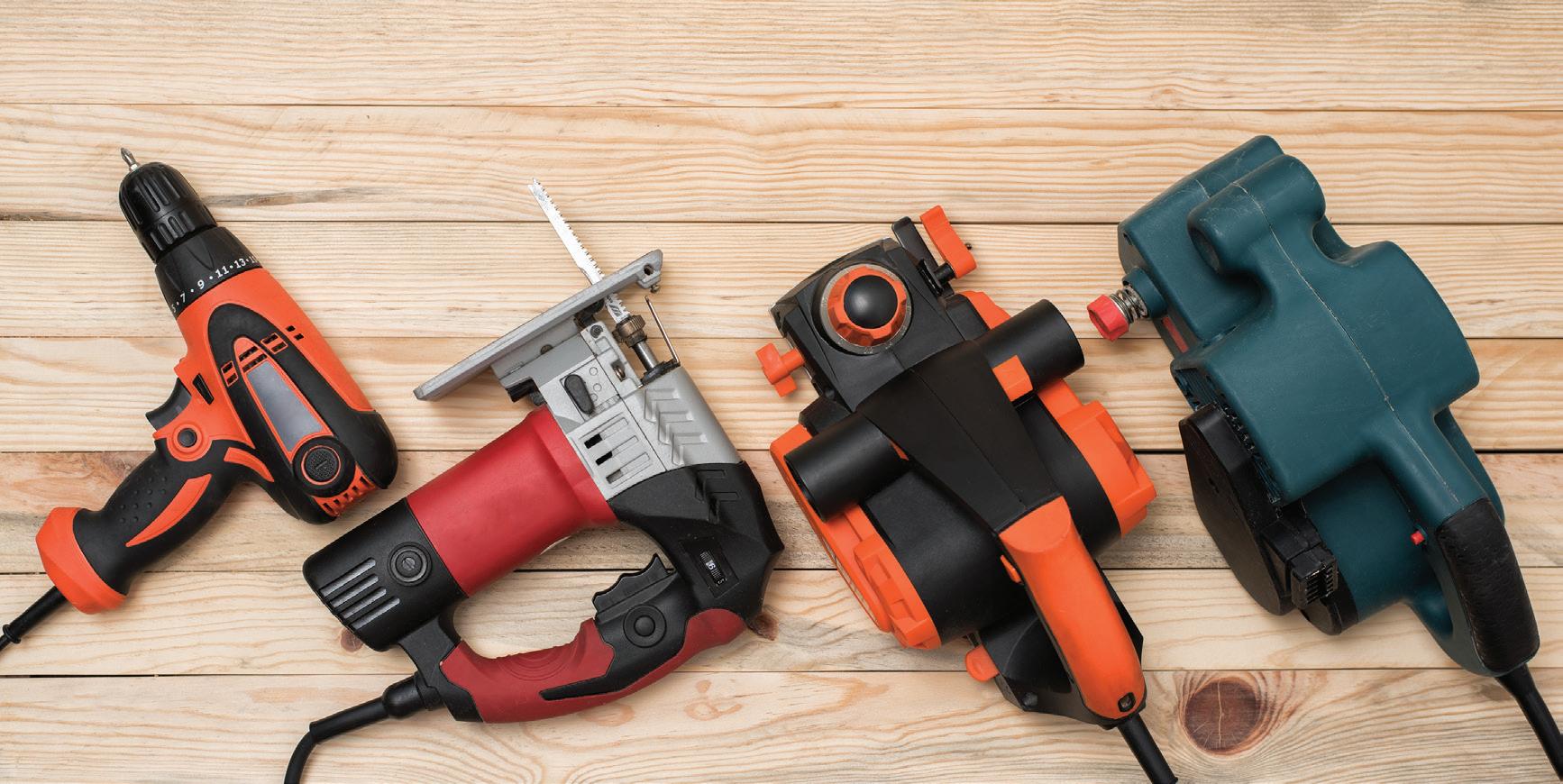
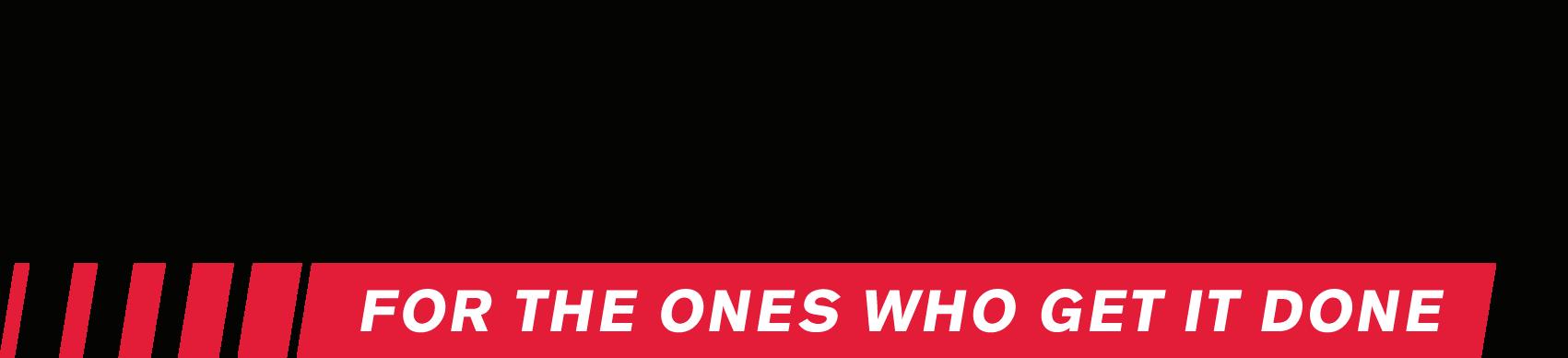
Benchmarking & Best Practices Conference Preview
Mitigate Risks with a Crisis Plan
Legislative Changes in Manufacturing
As we gear up for another exciting year, it’s time to mark your calendar and prepare for our upcoming Benchmarking and Best Practices Conference! This year’s theme, “Ingenuity at Work,” promises to be a dynamic exploration of creativity, innovation and forward-thinking solutions in the industry. Whether you’re a seasoned veteran or just starting out in your career, here’s why you simply can’t afford to miss this event.
Inspiring Keynote Speakers: Our lineup of speakers is second to none. Experts and visionaries will share their insights and experiences, offering you a fresh perspective on the latest trends and challenges in manufacturing. These sessions are designed to spark ideas and ignite your passion for innovation.
Networking Opportunities: The conference isn’t just about learning – it’s about connecting. Connect with fellow professionals, industry leaders and potential collaborators during receptions, networking breaks or our famous Lunch and Learn. The connections you make here could open doors to new partnerships, ideas and opportunities for growth.
Skill Development: Stay ahead of the curve with our BC Labs. Whether you’re looking to sharpen your technical skills or enhance your leadership capabilities, we will offer 30-plus practical learning experiences tailored to your job title.
Showcase Your Ingenuity: Are you working on a groundbreaking project or initiative? The Innovation Award provides a platform to showcase your innovations and gain recognition for your hard work. Share your successes, receive valuable feedback and inspire others with your ingenuity. Don’t miss this opportunity to highlight your achievements and make a lasting impact!
Kaitlyn Triplett, ARPM
Stay Informed: In today’s fast-paced world, staying informed is crucial. The conference offers insights into the latest industry trends, regulatory updates and technological advancements. Arm yourself with the knowledge you need to make informed decisions and drive your organization forward.
Recharge and Rejuvenate: Take a break from your daily routine and invest in yourself. Our conference venue provides an environment away from the hustle and bustle, allowing you to relax, reflect and return to work with renewed energy and motivation.
Join us at the Benchmarking and Best Practices Conference on October 2-4, 2024, in Indianapolis, Indiana, and be part of a transformative experience that will leave you inspired, informed and ready to take on new challenges. Together, let’s harness the power of ingenuity to shape the future of the rubber industry. The agenda and registration information can be found at www.arpminc.com/conference
We look forward to welcoming you to Indianapolis! n
“TOGETHER, LET’S HARNESS THE POWER OF INGENUITY TO SHAPE THE FUTURE OF THE RUBBER INDUSTRY.”
By Andrew Carlsgaard, analytics director, ARPM
By Josh Guilliams, vice president of consultancy, Smithers
Chris Kuehl, managing director,
By Paige Heck, project
manager, ARPM
ARPM Team
Executive Director Letha Keslar – lkeslar@arpminc.org
Managing Director Kaitlyn Triplett – ktriplett@arpminc.org
Project Manager Paige Heck – pheck@arpminc.org
Marketing Director Marcella Kates – mkates@arpminc.org
Analytics Director Tony Robinson – trobinson@arpminc.org
Director of Publications Susan Denzio – sdenzio@arpminc.org
Analytics Lead Andrew Carlsgaard – acarlsgaard@arpminc.org
ARPM Officers and Board of Directors
President
James Wideman, MBL (USA) Corporation
Vice President
Ryan Fleming, Freudenberg-Nok Sealing Technologies
Treasurer
Donovan Lonsway, BRP
Secretary
Joe Keglewitsch, Ice Miller LLP
Past President
Travis Turek, Bruckman Rubber Corporation
ARPM Board of Directors
Rich Balka, Home Rubber Company
Bill Bernardo, Ebco, Inc.
Kirk Bowman, The Timken Company
Russ Burgert, Maplan Rubber Machinery
Aaron Clark, Danfoss Power Solutions
Joe Colletti, Marsh Bellofram
Randy Dobbs, Sperry & Rice LLC
Carl Flieler, Zochem LLC
Doug Gilg, Continental ContiTech
Cedric Glasper, Mechancial Rubber Products Corp.
Diya Garware Ibanez, Fulflex, Inc.
Jeff Leach, Passaic Rubber Co.
Jon Meigan, Lake Erie Rubber & Manufacturing
Mike Rainey, HBD Industries Inc.
Mike Recchio, Zeon Chemicals L.P.
Brandon Robards, Ace Extrusion
Caitlin Steele, Gates
John Stone, The Rubber Group
Graphic
By Liz Stevens, writer, Inside Rubber
Company culture – it’s the talk of the industry. Corporations know that culture is a crucial aspect of a company’s success, preserving its good name and ensuring its longevity. But what is culture and how is it demonstrated in a manufacturing production company? In the Forbes article, “The Hidden Value Driver: Why Your Corporate Culture Isn’t All Puppies And Rainbows,” author Sherzod Odilov said, “Culture is essentially the organization’s ‘personality’ or behavior at scale.” 1
Odilov, however, recognized that this can be a confounding concept. “Even the most seasoned leaders often grapple with truly understanding what culture represents and its profound influence on organizational success. Culture is not just about office aesthetics or corporate social activities. It’s an intricate tapestry woven from shared values, beliefs and behaviors that guide how an organization operates and communicates both internally and externally.”
For this article, Inside Rubber reached out to three prominent rubber industry players to pose questions on their definition and implementation of company culture. ContiTech, Industrial Solutions AMERICAS, Fairlawn, Ohio, provides material-driven solutions for aerospace, agriculture, automotive, construction, energy, household and mining. The Fairlawn, Ohio ContiTech group sector focuses on smart, sustainable solutions beyond rubber and develops digital and intelligent solutions in future-oriented sectors.
The Rubber Group, Rochester, New Hampshire, is a rubber molding company specializing in custom molded rubber products. The company manufactures precision molded seals and components using highly engineered materials for a variety of high-reliability applications, including medical devices, aerospace, fluid control and electrical power transmission.
Photos top to bottom: ContiTech’s Four Values on display. Photo courtesy of ContiTech. It’s “Safety First” at The Rubber Group. Photo courtesy of The Rubber Group.
Zeon’s most senior employees at the Mississippi plant during the company’s 36th anniversary in 2024. Photo courtesy of Zeon.
Zeon Chemicals L.P., with North American regional headquarters in Louisville, Kentucky, produces innovative specialty elastomers, polymers and specialty chemicals. The company is known for its specialty heat- and oil-resistant elastomers and specialty nitrile elastomers.
Acknowledging that “company culture” is a wide topic, are there any overarching concepts that pertain to several aspects of the company’s culture?
Tyler Rhinehart, head of Continental Business System –Marysville, ContiTech: “Here at ContiTech, we incorporate four main values that drive our company culture in every aspect: Trust, For One Another, Freedom to Act and Passion to Win.” By integrating these values into daily business, ContiTech constantly reinforces a positive and successful company culture. “These values are prominently displayed in the plant through banners and other media, and are tied to a quarterly employee highlight program,” said Rhinehart. “In addition, we encourage employees to model and practice these values in their day-to-day operational activities.”
Rob Pruyn, president and CEO, The Rubber Group: At The Rubber Group, the overall cultural umbrella is succinct and very clear. “Our guiding principle is the Golden Rule,” said Pruyn. “We apply this principle to all our interactions with the goal of developing lifelong, mutually beneficial relationships. It is fundamental to who we are, and it informs how we act.”
Lindsey Heimbrock, human resources manager, Zeon Chemicals: Heimbrock cited the company’s principle of Making Rubber that Makes a Difference. “Zeon Chemicals’ commitment to this principle,” said Heimbrock, “reflects a deep-seated dedication to not only the products we produce but also to the broader impact they aim to have on society.” The company’s purpose-driven approach is supported by a set of values encapsulated in the acronym RESPECT – Relationships, Empowerment, Safety, People, Environment, Community and Trust. “These values,” Heimbrock explained, “are not just words, but are the guiding principles that inform every decision and action within the company. We foster a culture where employees feel valued and empowered, where safety is paramount, and where the environment and community are considered in every aspect of the business.” Trust, as the final value, said Heimbrock, “seals the commitment to these principles, ensuring that stakeholders can rely on Zeon Chemicals to act with integrity and responsibility.” This purpose architecture is a robust framework that not only shapes the internal workings of the company but also projects a clear, positive image to its employees, customers and other stakeholders, demonstrating what Zeon Chemicals stands for as an employer and as a corporate entity.
How does the combination of a company’s mission, vision and culture make for a successful business with a great team of employees?
Pruyn, The Rubber Group: “Our thesis is that through the application of the Golden Rule, we will drive an exceptional customer, supplier and team member experience. This experience leads to more long-term opportunities and the creation of promoters within all three groups.” The company executes that thesis through some relatively simple strategies. “The first,” said Pruyn, “is soliciting feedback and actively listening to develop a clear understanding of what’s important to everyone. It’s clear that certain things are more important to certain organizations and individuals. It is key to understand what these things are and then to cater the experience to deliver them.” The second, said Pruyn, is to communicate organizational objectives and filter these down to each function. “We try to make sure that everyone understands how their behavior affects the experience, and we create specific ‘smart’ objectives that drive the right behaviors,” he explained. “It is equally important to develop a support and feedback structure to ensure that team members have the skills and experience to meet expectations.” The Rubber Group creates an environment that is highly supportive and develops leaders who hold the team accountable while providing feedback, coaching and support to allow team members to achieve their objectives. “Finally, and most importantly,” said Pruyn, “be introspective. We use data and subjective feedback to make sure we are tracking in the right direction.” Pruyn believes that organizational honesty is paramount to the journey to excellent experiences. “Some things that we try simply don’t work,” he said. “We have the tools in place to recognize these shortcomings. And we have the emotional intelligence to admit the failures, which allows us to quickly pivot and implement a fix.”
Rhinehart, ContiTech: Rhinehart, explained how mission, vision and culture combine at ContiTech. “From my position at the plant level,” he said, “we relate all our continuous improvement initiatives directly back to the company’s mission, vision and culture through a monthly strategy deployment process we call ‘mission control.’ During these sessions, we review specified metrics, set goals, report status, remove roadblocks and celebrate successes as a cross-functional team that includes all departments.”
Heimbrock, Zeon: The synergy between a company’s mission, vision and culture is pivotal for attaining business success and cultivating a great team. “Our purpose – ‘Making Rubber that Makes a Difference’,” she said, “guides our employees towards a common mission. We believe in delivering innovative solutions by stretching the power of chemistry. We believe this all starts with people.” Zeon’s employees, customers and community are at the heart of its success. Culture is the fabric
at Zeon that holds everything together – the shared values, behaviors and practices that shape the day-to-day experiences of the company’s employees. “When these elements align,” said Heimbrock, “they create an environment where our employees are engaged, productivity flourishes and innovation thrives. This alignment also helps in attracting and retaining talent who are committed to the company’s goals, fostering a sense of belonging and teamwork that is essential for longterm success.”
Among
the elements
of culture, which are the top three must-have practices to form a strong cultural foundation?
Rhinehart, ContiTech: “From my personal experience at the plant, the top three practices that form a great cultural foundation are diversity, a feedback-and-ideas culture and a corporate values statement. These elements create a sense of safety at work, and they unify our goals and facilitate open communication, which allows us to function as a cohesive, well-rounded team. Further, workforce career advancement is essential for motivating employees and for fostering a culture of growth and development, which leads to a more engaged and skilled team.”
Pruyn, The Rubber Group: “The foundation is the Golden Rule. We create a structure that enables us to deliver on that promise. Our employment practices – like being committed to investing in people and technology – and our promises to customers – like helping them make the best choice of highperformance materials for their safety-critical applications – these are simply tools to ensure that we create the best possible experience.” The culture at The Rubber Group also includes beliefs such as “everyone deserves a pleasant and safe environment,” “we succeed and fail as a team,” “we are accountable for our behavior” and “we persevere.”
Heimbrock, Zeon: “Building a positive culture that creates a sense of belonging and teamwork is vital to the success of a company. At Zeon Chemicals, we believe that the must-have practices to form that cultural foundation include 1) creating a team environment with both social and community activities where we are not only giving back to our employees but also making a positive impact on the communities we work in; 2) offering a wide variety of benefits such as cost-effective health insurance, retirement benefits, work-life balance and more to support our employees and their families; and 3) offering the industry’s best customer service, which gives our employees the opportunity to build relationships and make an impact each day.”
Heimbrock, Zeon: “Leadership during challenging times is a true test of character and commitment. Mike Recchio, as president and CEO of Zeon Chemicals, exemplifies this through his actions and dedication.” Heimbrock explained that Recchio took the helm just as the world faced the unprecedented crisis of the COVID-19 pandemic, and navigated the company with a clear focus on the well-being of employees and the overall success of the organization. “By revitalizing the company’s purpose and values,” said Heimbrock, “Recchio has not only aligned them with the current identity of the company but also ensured that these principles are lived out daily by the executive team.” Recchio’s leadership approach resonated throughout the organization; the company was named one of the most recent Best Places to Work by a rubber industry publication, based on the high percentage of Zeon employees who believe in the commitment of their leaders to the company’s core values. “Such a belief system fosters a strong, unified corporate culture,” said Heimbrock, “which is essential for any company striving to be recognized as a great place to work.”
Rhinehart, ContiTech: “Yes, our culture definitely emanates from the top. The great culture of this company is established by our executive team, which actively reinforces the culture we strive for. In our facility, we feel immense support from the executives, who prioritize making physical visits to the
A Partnership with Thayer Leadership at West Point
"NO MATTER IF YOU ARE LEADING A TEAM OR ONE INDIVIDUAL, IT STARTS WITH LEADING ONESELF. THE TRAINING HAS HELPED ME RECOGNIZE WHO I AM AND WHO I WANT TO BECOME AS A LEADER.”
-PLANT MANAGER
Registration is open now for the September session.
u
plant floor and engaging with employees at every level of the organization.” Rhinehart noted an additional key cultural aspect practiced by senior executives at ContiTech. “Our executives demonstrate our commitment to trust and transparency,” said Rhinehart. “Executives regularly touch base with employees at all levels, holding town hall meetings and open forums to discuss company performance and upcoming initiatives, and to address any concerns.” This open communication fosters a sense of trust and inclusivity throughout the organization, ensuring that every employee feels valued and informed about ContiTech’s collective goals and progress. “Also,” said Rhinehart, “executives lead by example in promoting our corporate values, actively participating in community service projects and supporting initiatives that encourage diversity and sustainability.”
Pruyn, The Rubber Group: “I am very fortunate to have been a part of the organization since our inception in 1986. It has taken us some time to develop who we are and why we exist, and I’ve been a part of that development.” After joining the company, Pruyn was given the opportunity to grow within the organization. He started in an inside sales role and was allowed to take on more responsibility over time. “As a result,” he said, “we think it is important to allow all team members the opportunity to grow and develop. Many of our current leaders started in different and more tactical roles. We review and evaluate team members’ skills and drive and give them the opportunity and tools to advance.” Many people in Pruyn’s group have direct experience in the roles they support, giving them a deep understanding and empathy for the demands of those roles. And this also creates a group of culture promoters. “Customer engagement is baked into our DNA,” Pruyn said. “Sometimes we need to do something extraordinary and potentially costly to satisfy our customers. We always commit the resources to get the job done. The team recognizes that commitment by the company and it reinforces our core values.”
What cultural elements were difficult to apply throughout the company? Were barriers faced while trying to promote a new cultural attitude or behavior; how were they overcome within the company?
Rhinehart, ContiTech: “Implementing cultural changes within an organization like ContiTech can indeed present significant challenges, especially when these changes clash with operational productivity or misalign with the company’s strategic goals.” Rhinehart acknowledges that with any change comes resistance, and that this is just human nature. “To overcome our roadblocks, we use the leading-by-example approach to gain trust. We’ve found that the most important foundation one can set is a trustworthy communication flow. This includes providing opportunities for employees to voice their opinions and share improvement ideas.”
Pruyn, The Rubber Group: “We understand that many of our team members value flexibility.” The Rubber Group has a goal of trying to allow the maximum amount of flexibility without disrupting productivity and machine utilization. “This presents significant challenges, and it requires the whole team to come together,” Pruyn explained. “We’ve been able to work with the team to create bespoke schedules while continuing to meet customer requirements. This adds some complexity to our planning process, but our team loves it. We settled on a four-day, 10-hour shift schedule for the majority of our production and support team, but other team members work a more traditional eight-hour day.”
Heimbrock, Zeon: “The rapid transition to remote work during the COVID-19 pandemic was indeed a monumental shift for many businesses. Companies had to swiftly adapt to maintain productivity, with some employees transitioning to work from home, while others, particularly in manufacturing, continued to work on-site.” This required a delicate balance and innovative management strategies at Zeon to ensure both safety and efficiency. “The implementation of flexible work options,” Heimbrock said, “has been a key factor in this transition, allowing us to offer a variety of working arrangements to accommodate as many employees as possible. These changes have not only helped businesses to survive during challenging times but also have paved the way for a more adaptable, resilient workforce for the future.”
As a member of the Association of Rubber Products Manufacturers, describe how the company’s involvement is demonstrated within its culture?
Heimbrock, Zeon: “Zeon Chemicals’ engagement with ARPM reflects a broader commitment to excellence and community involvement within the industry. This partnership is a testament to Zeon’s dedication to not only advancing its own team’s expertise but also contributing to the collective knowledge base of the sector.” By participating in industry training and networking events, Zeon demonstrates its resolve to impact the industry positively. “Such collaborations are crucial,” said Heimbrock, “as they foster an environment of shared learning and growth, enabling technical teams like Zeon’s to disseminate their knowledge and expertise, ultimately benefiting the industry and its customers.”
Rhinehart, ContiTech: “Our facility has a strong research and development presence, encompassing fabric, compound and application engineering fields. These groups have close ties and many longstanding relationships that help drive innovation and ensure a customer-centric approach. Some of the impact of our involvement with ARPM can be seen throughout the plant, where it influences how we design and manufacture our products.”
Pruyn, The Rubber Group: “A part of treating others the way you want to be treated includes openness and transparency. The Rubber Group has always worked hard to collaborate with our peers and is willing to share our experiences. We’ve been blessed with some great partners and friendly competitors that have helped us along the way, and we like to do the same.”
Pruyn, The Rubber Group: “We haven’t seen new trends, but we are working hard to understand how we impact the environment and how we can create a sustainable future. Also, we continue to enhance the work environment by reducing the physical demands for the team.”
Heimbrock, Zeon: “Zeon Chemicals leadership and HR teams constantly watch and research trends as they come up and incorporate when they fit our culture and workforce. Some things we currently are focused on are employee recognition and engagement, and employee health and well-being. These are areas that we feel contribute to employee morale and to
the overarching culture principle that we aim to be the best workplace for our employees.”
Rhinehart, ContiTech: “I wouldn’t say there are any new cultural trends at this time. We continue to maintain a fresh, positive approach and to stay true to our company values.”
The cultural foundations at the three companies – “Trust, For One Another, Freedom to Act, Passion to Win,” “The Golden Rule” and “Making Rubber that Makes a Difference” – are easy to grasp yet very potent. These companies exemplify author Sherzod Odilov’s assertion that corporate culture isn’t all puppies and rainbows. To reiterate: “Culture is not just about office aesthetics or corporate social activities. It’s an intricate tapestry woven from shared values, beliefs, and behaviors that guide how an organization operates and communicates both internally and externally.” 1 n
References
1. Sherzod Odilov. “The Hidden Value Driver: Why Your Corporate Culture Isn’t All Puppies And Rainbows.” Forbes. com. November 19, 2023. https://www.forbes.com/sites/ sherzododilov/2023/11/19/the-hidden-value-driver-why-yourcorporate-culture-isnt-all-puppies-and-rainbows/
ARPM is excited to announce newly updated sealing product standards.
y OS-1-1: Dynamic Seal Technical Bulletin – Shaft Finish Requirements for Rotary Lip Seals
y OS-7: Storage and Handling Guide for Radial Lip Type Shaft Seals
y OS-16: Recommended Methods for Assuring Quality of Radial Lip Seal Characteristics
y OS-17: Dynamic Seal Technical Bulletin – Sealing System Leakage Analysis Guide
ARPM members can access these and other publications for free with their membership.
Non-members can find these publications and other industry standards at www.arpminc.com/publications.
Garware Fulflex, Brattleboro, Vermont, will host ARPM’s third quarter plant tour on August 15! Plant tours offer an opportunity for APRM members to visit other member facilities, see how others are approaching challenges and help the host company see new areas of opportunity.
Being able to attend member-hosted plant tours is one of the top benefits of being an ARPM member.
During this plant tour, attendees will have the opportunity to listen to the Fulflex team discuss how it has empowered its workforce to operate independently to foster a culture of trust and productivity, maintain a positive atmosphere during challenging hiring circumstances and how lean management has driven efficiency and resilience.
In the spirit of continuous improvement, attendees will have the opportunity to walk away from this plant tour with several implementable best practices and solutions to challenges the rubber industry is facing.
There are a limited number of spots reserved for non-members on this tour. Interested in seeing what a plant tour is all about? Email Kaitlyn Triplett at ktriplett@arpminc.org
Join other finance and accounting colleagues and leaders at this unique virtual event designed to help address current benchmarks, best practices and challenges facing the manufacturing industry today.
This event will include presentations by experienced industry professionals, facilitated panels and peer-to-peer networking opportunities with other manufacturing finance professionals to help deliver answers and solutions to some of the biggest questions and challenges in the industry.
Interested in sharing a best practice or topic request? Send it to Letha Keslar at lkeslar@arpminc.org.
For more information and to register, visit www.arpminc.com/ events.
Unleash the Power of Automation! Join ARPM every other Wednesday for its exclusive Automation Webinar Series. The series will dive deep into the latest trends, strategies and technologies transforming the manufacturing landscape. Whether a seasoned industry professional or new to automation, ARPM’s expert-led sessions will cover everything in the webinar series.
As a manufacturing operation, don't miss this opportunity to stay ahead of the curve and drive innovation.
For more information on each session and to reserve a spot for the Automation Wednesday Webinar Series, visit www.arpminc.com/events.
PartnerShip, ARPM’s endorsed shipping provider, provides cost savings to members on FedEx Express, Priority Overnight, Standard Overnight, International Priority, International Economy, FedEx Ground and more.
In addition to these discounts, PartnerShip supports ARPM members within the world of freight and logistics. With access to a network of reliable carriers, members can rest assured that their freight will be safely delivered and on time.
To learn more and take advantage of these cost savings, contact Camille Bagnola, ARPM PartnerShip program coordinator, at cbagnola@arpminc.org
“Leveraging data and analytics from ITR Economics can be highly beneficial for MBL (USA) Corporation in navigating the complexities of business environments.
These insights provide valuable market data points that are crucial for making informed, strategic decisions.
With ITR Economics' insights, MBL (USA) Corporation can assess factors, such as industry trends, consumer behavior shifts and economic indicators relevant to its
operations. This knowledge enables us to adjust our strategies proactively, optimize resource allocation and mitigate risks.”
– Jim Wideman, president, MBL (USA) Corporation
For more information on the ITR Economics program, visit www.arpminc.com/resources/itr-economic-program/
Please join ARPM in welcoming the following new members!
Alttran
Prince Rubber & Plastics
Hulpac
Specification Rubber
Copper State Rubber n
The Benchmarking and Best Practices Conference will bring together over 600 rubber and plastics professionals to Indianapolis, Indiana, on October 2-4, 2024, to educate and empower them with practical strategies, real-world case studies and actionable insights.
The conference team is pleased to welcome the following keynote speakers:
An expert on innovation, creativity and breakthrough thinking, Stainton is a 29-time Emmy Award winner, a Hall of Fame keynote speaker and author of The Innovation Blueprint. For 15 years, he produced the longest-running, highest-rated and most award-winning regional comedy TV show in the US. Stainton also has written for HBO, Comedy Central and The Tonight Show, and is the creator of the Elite Innovation Roundtable, a think tank for innovative leaders.
Recognized as the world’s leading futurist, trends and innovation expert, Carroll’s global client list gives him a front-row seat to the high-velocity change that is occurring as disruption comes to take hold of every industry and every organization. With that insight and the customized research that he undertakes for every engagement, Carroll helps to transform growth-oriented organizations into high-velocity innovation heroes.
As a founding partner with The Franklin Partnership and having worked in the nation’s capital for over 25 years, Nashashibi lobbies the White House and Congress on behalf of manufacturing. He works with policymakers on trade, taxes, environmental and workplace regulations, job training and identifying grants and funding to support projects.
A key member of ITR Economics’ team of expert economists and consultants, Feuz contributes to the production of client reports, forecast reviews, economic research and regular clientfacing communications. Feuz has helped manufacturers, construction companies, oil and gas firms, financial institutions and small businesses enhance their operational efficiencies.
An attitude expert, Booth has shared his message of positive attitude change throughout the US and internationally. He believes that if we want to make a real difference in the world, we first need to change our attitudes. His keynote speeches are powerful, insightful and engaging – inspiring audiences to take massive action and achieve their goals.
Harbour is a partner with more than 35 years of manufacturing and consulting experience. Prior to joining Wipfli, she was the co-owner of Harbour Results, Inc., and has spent her career helping clients develop strategies, improve operations, reduce risk and optimize business performance.
Please note, this agenda is still a work in progress. The Conference committee wanted to share the general timeline of the event to assist attendees with travel arrangements. All times are EDT.
WEDNESDAY, OCTOBER 2
1:00 PM Young Professionals Pre-Con
1-7:00 PM Registration
1:00 PM MBS Advisors Pre-Con
1:00 PM DelmiaWorks User Group Pre-Con
4:30 PM Sponsor Meeting
5:00 PM Building Leaders of Character Alumni Reception
5:30 PM Industry Welcome Reception
5:30 PM Automation Hall Opens
THURSDAY, OCTOBER 3
7:00 AM Registration Opens
8:00 AM Conference Welcome and Keynote Troy Nix
8:20 AM Keynote Bill Stainton
9:55 AM Keynote Jim Carroll
11:00 AM BC LABS Session One
12:10 PM Lunch and Learn with Keynote Bill Stainton (ticket-only) Or Networking Lunch
1:15 PM BC Labs Session Two
2:15 PM Networking Break Amongst the Sponsors
2:45 PM Keynote Michael Feuz
3:40 PM BC MASTER CLASS
4:00 PM Keynote Matt Booth
5:00 PM Members’ Choice Reception
FRIDAY, OCTOBER 4
8:00 AM Peer to Peer Networking
8:50 AM BC Labs Session Three
9:50 AM Networking Break Amongst the Sponsors
10:20 AM Innovation Awards Ceremony
10:50 AM Laurie Harbour, Wipfli
11:35 AM Omar Nashashibi, The Franklin Partnership
12:20 PM What’s Next?
12:30 PM Conference Adjourned
This year’s event will take place at the Indianapolis Downtown Marriott, 350 W. Maryland, Indianapolis, IN 46225.
A room block has been secured for the event. Book at www.arpminc.com/conference.
AEC/Cumberland/Sterling American Mold Builders Association
Aurora Material Solutions Bamberger Amco Polymers
Beaumont Technologies, Inc.
Benesch, Friedlander, Coplan & Aronoff, LLP
Chase Plastic Services, Inc. Conair
DELMIAWorks
DME
Federated Insurance Frigel Globeius Ice Miller, LLP iD Additives, Inc.
INCOE Corporation
LS Mtron M. Holland Company
Management Recruiters of Tallahassee Maplan
MBS Advisors
Noble Plastics – Automated PCS Company Plante Moran Plastics Business PolySource, LLC Progressive Components Prophix Software QSI Automation, Inc. RapidPurge Rehmann Resin Technology, Inc. RJG, Inc.
Routsis Training
SIGMASOFT® Virtual Molding Stout US Compliance Vive, LLC
MEMBERS | In-Person pricing:
Members Through Aug. 16, 2024 After Aug. 16, 2024
(Processors only): Non-Members Through Oct. 3, 2024
By Shelly Otenbaker, president, WayPoint Marketing Communications
“An ounce of prevention is worth a pound of cure.” Many are aware of this phrase, but few follow it. In manufacturing, taking small, proactive steps to prevent a problem is far more effective and less costly than dealing with the consequences once the problem occurs –especially when managing a crisis.
A business crisis is a situation that negatively impacts customers, employees and/or a company’s reputation. They come in all shapes and sizes, including organizational (e.g., acquisitions, cybersecurity, reorganizations), natural disasters, accidents and work stoppages.
The best way to mitigate the risk and minimize the negative impact of a crisis is to be prepared. Many manufacturers have people in environmental, health and safety roles who have developed a plan for the facility to manage a crisis, but few have established a communication plan.
A crisis communication plan helps ensure clear and consistent messages are conveyed during times of uncertainty or emergency. A well-structured plan helps to manage information flow, minimizing misinformation and reducing panic. It outlines the roles and responsibilities of key personnel, ensuring everyone knows their tasks and can swiftly act. This preparation helps maintain trust and credibility with stakeholders, including employees, customers, investors and the public.
Developing a crisis communication plan does not have to be overly complicated. But it does need to be a living plan that adjusts as the business changes, and it must define processes and action steps. Here are a few steps companies can take when developing an effective crisis communication plan.
It is important to identify the employees that will support the plan because this will be the team responsible for managing and communicating during a crisis. When developing a team, think about the entire organization and the people who could be impacted by a crisis. It should include facility people – EHS, HR, plant leadership – as well as communications, legal and, potentially, the business owner.
If a company has multiple facilities, the team may need to expand to a head of the region or the corporate team. Having a pre-identified and trained team ensures all members know their roles and will help improve response time and effectiveness.
The response protocol is a step-by-step guide to guide the organization through a crisis and should contain several key tools.
First, the crisis team should brainstorm the type of crises the organization could face. This should be realistic but include scenarios that are not highly likely – before 2020, it is doubtful an organization had a pandemic in its crisis plan.
Additionally, the team should create crisis levels and the criteria that define each level. For example:
y Level 1 – controlled, minimal impact on employees or business, no injuries
y Level 2 – temporary, confined to facility, minor injury
y Level 3 – significant business impact, multiple or severe injury, community impact
y Level 4 – significant business impact (e.g., multiple facilities), death, regional impact
The levels should include general categories, align specifically to the business, cover all facets of the organization and increase in severity.
The next important tool is an incident report or some sort of mechanism to collect important data related to the crisis, such as what happened or is happening, who is involved and impacted, whether it’s an isolated/one-time incident or ongoing and any details related to the situation. Having access to correct information will be critical to an organization’s crisis response team’s ability to make informed decisions.
Next, an organization must define how to respond to different types of crises. An organization should ask: How will communication happen? Who initiates it and when does it start? What are the appropriate action steps based on the crisis levels and timing – immediate, first 12 hours, 24 hours and beyond? What communication tools will be used and what are the expected milestones?
During a crisis, every second counts so it is helpful to have materials or templates created and easily accessible to be utilized by the crisis team as needed.
y Key messages: Predefined messages about what the company does, what makes it unique and its values and priorities.
y Facility statistics: Information about all facilities – size, number of employees, products produced, etc.
y Scenario-specific messaging: Established messaging targeted at high-priority stakeholders (e.g., employees, customers) for specific scenarios that could occur within the facility.
y Contact lists: Create a list of names, emails and phone numbers for key stakeholders – employees (and emergency contacts), customers, emergency services and local media outlets.
y Spokespeople: Identify and train a small group of people who are tasked to communicate with employees, customers and media during a crisis.
y Communication tools: Identify and prepare tools that will be utilized to communicate during a crisis. Remember crisis teams may not always be able to utilize their facilities or traditional communication tools for all crises (e.g., loss of power, cell service).
Although there is no perfect outcome when it comes to a crisis, companies regularly should conduct drills and simulation exercises to test the effectiveness of their crisis communication plan. Creating different scenarios and running through them allows a team to practice roles and refine the plan based on lessons learned.
Finally, a crisis communication plan should be dynamic and responsive to changes in the organization and its environment. Regularly review and update the plan to reflect new employees, risks, stakeholders and communication technologies.
A crisis communication plan can significantly impact the overall outcome of a crisis. Anyone who has endured a crisis without a plan will share that it often can be chaotic and extremely stressful.
By having predetermined strategies and communication channels, organizations can address concerns, provide necessary updates and demonstrate control over the situation. This proactive approach not only protects the organization’s reputation but also reassures stakeholders the organization is competent and prepared to handle adverse situations. n
Shelly Otenbaker is the president of WayPoint Marketing Communications, a leading business-to-business marketing communications agency focused on helping manufacturers attract and retain talent and acquire new business. The company specializes in building customized, strategic programs tailored to meet the unique needs of each client.
More information: www.waypointmc.com
“REGULARLY REVIEW AND UPDATE THE PLAN TO REFLECT NEW EMPLOYEES, RISKS, STAKEHOLDERS AND COMMUNICATION TECHNOLOGIES.”
By Letha Keslar, executive director, ARPM
As discussed in previous Technical Standards columns, the influence of ARPM technical teams reaches far beyond the confines of its immediate community and borders. Through active participation and leadership roles in International Standards Organization (ISO) committees, ARPM members are not just shaping standards; they are shaping the future of industries globally.
The Association for Rubber Products Manufacturers (ARPM) continues to lead the specialty rubber industry with cuttingedge research and standard development. When ARPM teams see a need for new specifications/guidelines, they create them! Highlighted below are several key projects currently underway through ARPM.
The Effect of Out-Of-Roundness and Lobing on Seal Performance
ARPM is revisiting a 1968 GM study that established limits for seal lips following non-concentric shaft movement. Although the industry has long adhered to these GM recommendations, the original data is unavailable. Initial tests suggest a correlation to the GM study, with variations prompting a second test to investigate machining differences in how the shaft lobing was prepared.
Traditionally, evaluating cold temperature limits of shaft seals involves costly and time-consuming test rigs. ARPM aims to introduce a quicker, cost-effective screening method using Dynamic Mechanical Analysis. Successful tests with ACM, NBR and HNBR materials have been completed, though FKM results varied. Revised testing is in progress with new material batches from two suppliers.
The current ARPM standard, OS-1-1, uses a thread method to measure shaft lead but may miss non-continuous lead in surface roughness. ARPM is evaluating optical lead measurement equipment from four suppliers to detect macro and micro noncontinuous machine lead. Two suppliers have completed blind test measurements, with a third in progress.
ARPM TC 41 SC 4 is gearing up to work with the China delegation on a newly proposed industry standard for the correct installation of synchronous belt drives, emphasizing proper pulley flanging, drive alignment and belt installation tension. This proposal, titled ISO 24920, aims to provide comprehensive installation guidance to improve belt drive performance. Expected to take three years to develop, this standard will serve as a valuable reference for maintenance associates.
ARPM’s TC45/SC1 also has its hands full with new publications and partnership with Japan on a newly introduced New Work Item Proposal, ISO NP 25308, to address gas-leakage in hose and tubing assemblies caused by assembly faults. This standard will provide a method to determine leakage at the interface between hose/tubing and fittings, accounting for permeation and trapped air. The project aligns with ISO goals for industry, innovation and infrastructure, and for responsible consumption and production.
ARPM’s collaboration extends to organizations such as the Compressed Gas Association, maintaining standards like CGA E-1 for rubber welding hoses and assemblies. These efforts underscore ARPM’s dedication to advancing the rubber industry through updated and new standards, ensuring members have access to the most current, reliable information. ARPM’s ongoing efforts to update and create new standards reflect its unwavering commitment to excellence. By staying at the forefront of technological advancements and industry best practices, ARPM ensures that its members have access to the most current and reliable information available. This dedication helps improve product quality, safety and efficiency across the specialty rubber industry – solidifying ARPM’s role as a leader in the field. n
If interested in joining one of these committees, contact the ARPM office.
More information: www.arpminc.com.
By Alan Rothenbuecher, partner, and Brad Wenclewicz, associate lawyer, Benesch, Friedlander, Coplan & Aronoff LLP
The landscape of employment law is undergoing changes that could significantly impact the manufacturing industry. These developments necessitate employers to stay informed and proactively update their policies to ensure compliance with evolving regulations. This update summarizes key legal changes across several areas.
The US Equal Employment Opportunity Commission (EEOC) issued its first update on workplace harassment guidance in 25 years. This long-awaited update, effective April 2024, offers clarifying and expansive protections for employees. Notably, the new guidance expands the definition of sex-based discrimination under Title VII to include sexual orientation and gender identity. Harassment based on sexual orientation or gender identity includes epithets regarding sexual orientation or gender identity; physical assault due to sexual orientation or gender identity; outing (disclosure of an individual’s sexual orientation or gender identity without permission); harassment because an individual does not present in a manner that would stereotypically be associated with that person’s sex; repeated and intentional use of a name or pronoun inconsistent with the individual’s known gender identity (misgendering); or the denial of access to a bathroom or other sex-segregated facility consistent with the individual’s gender identity.
The EEOC’s updated guidance goes beyond physical workplaces, recognizing the growing importance of virtual work environments. This means offensive behavior on virtual platforms (e.g., Zoom, Teams), such as inappropriate comments or images, now can be considered harassment. The guidance also reaches beyond the traditional workday,
acknowledging that even activity on personal social media accounts can contribute to a hostile work environment if it targets a colleague.
Importantly, the EEOC’s new guidance isn’t legally binding, but is meant to serve as a “resource” for employers and the courts. Although the guidance contents “do not have the force and effect of law,” employers should be aware that the new guidelines may lay the foundation for employees to allege workplace harassment in broader contexts, and employers should review their harassment policies in light of the new guidance.
In January 2024, the US Department of Labor (DOL) issued a final rule making it harder for businesses to classify workers as independent contractors under the Fair Labor Standards Act (FLSA). This new, final rule repeals a prior rule (issued by the Trump administration) with a new, less predictable multifactor test. The new rule uses an “economic realities” test, which considers the following factors:
y The contractor’s opportunity for profit or loss;
y The investments made by the contractor and the putative employer;
y The degree of permanence of the relationship between the contractor and the putative employer;
y The nature and degree of control by the putative employer over the contractor;
y The extent to which the work performed by the contractor is an integral part of the putative employer’s business; and
y The contractor’s skill and initiative. u
R U B B E R I N D U S T R Y P U B L I C A T I O N S
ARPM PROVIDES INDUSTRY TECHNICAL STANDARDS FOR THE FOLLOWING CATEGORIES:
CONVEYOR BELT HOSE
POWER TRANSMISSION
PROTECTIVE LINING RAW MATERIALS
SEALING HANDBOOKS AND GUIDES
Some workers may require reclassification from independent contractors to employees, thereby making them eligible for minimum wage and overtime protection (and, in some instances, eligible for employer benefits such as health coverage and/or retirement benefits). As recommended, all employers should review their classification of independent contractors to determine whether any reclassifications are necessary to comply with the new rule.
The DOL also increased the minimum annual salary requirements in order to qualify under some of the FLSA’s most frequently invoked exemptions – the executive, administrative and professional (EAP) exemptions, and the highly-compensated employee (HCE) exemption. The final rule took effect on July 1, 2024.
Under the new EAP threshold, effective July 1, 2024, employees classified as exempt under the EAP exemptions must be paid at least $844 per week (or $43,888 per year), marking a 23% increase from the current $684 per week (or $35,568 per year) threshold. The final rule does not stop there, and imposes a new threshold of $1,128 per week (or $58,656 per year) effective January 1, 2025, a near 65% increase from the current threshold. In addition, beginning July 1, 2027, and every three years thereafter, the final rule calls for additional updates to the EAP salary threshold based on then-current earnings data.
Under the new HCE threshold, effective July 1, 2024, employees classified as exempt under the HCE exemption must be paid at least $132,964 per year, up 23% from the current $107,432 threshold. Of that $132,964, an amount equal to the EAP exemption threshold – at least $844 per week – must be paid on a salary or fee basis. And, like the EAP threshold update, the HCE update also comes with forward-looking increases, with an increase to $151,164 on January 1, 2025, and updates every three years beginning on July 1, 2027.
Although adjustments to these salary thresholds have been successfully challenged in the past, employers should prepare with the expectation that the final rule will take effect. As an initial step, employers should review their exempt staff salary levels and understand how these changes may impact their organization.
The fight for a national heat stress standard to protect workers is nearing a critical juncture. A proposed rule by the Occupational Safety and Health Administration (OSHA) currently is under review at the White House, raising hopes for a long-awaited safeguard against a growing threat.
While the specifics of the proposal (RIN: 1218-AD39) have not been made public, OSHA previously indicated that mandatory protections could kick in any time the heat index reaches 80° F.
Absent a formal standard, OSHA currently relies on the General Duty Clause under Section 5(a)(1) to protect workers from heat stress. For example, in March 2024, OSHA cited a Florida employer under the General Duty Clause due to employees performing their duties in temperatures ranging from 76° F to 87° F. As noted in the citation, such “exposures are likely to lead to the development of serious heat-related illnesses… such as heat cramps, heat stress, heat exhaustion and heat stroke.” The citation outlined a plan to prevent future heat-related illnesses and deaths, including:
y Assign a program manager to oversee the program and enforce its protocols.
y Gradually acclimate new or returning workers to hot environments to minimize risk.
y Encourage frequent water intake and provide electrolyte drinks for extended work periods.
y Schedule more frequent breaks in cool, shaded areas during high temperatures.
y Monitor workers for signs of heat stress and remove them from the work area if necessary.
y Train supervisors and employees on heat illness symptoms, risk factors, response procedures and the effects of certain substances in hot environments.
y Develop an emergency plan for remote work locations to ensure prompt medical attention in case of heat illness.
With a new rule from OSHA on the horizon, employers should monitor the heat index for those vulnerable employees, and make sure proper rest and hydration are provided to prevent against heat-related incidents.
In the 1990s, the OSHA ergonomic rules were in major dispute. Before Bill Clinton left office, his administration issued a final ergonomic standard in November 2000, which was to go into effect January 16, 2001, and employers had until October 14, 2001, to comply. Before October came around, however, newly elected President George W. Bush signed a bill repealing the OSHA ergonomic rule.
Although an OSHA ergonomic rule does not exist today, it may come back into light given the newly appointed US Occupational Safety and Health and Review Commissioner, Mark Eskenazi, who is a former National Labor Relations Board lawyer. Even if an ergonomic standard never comes to pass, OSHA remains vigilant in protecting workers from musculoskeletal disorders (MSDs) through the General Duty Clause. Recent citations against nursing homes, manufacturers and even Amazon fulfillment centers demonstrate OSHA’s
ongoing enforcement. Indeed, OSHA’s 2023 National Emphasis Program on Warehousing and Distribution further emphasizes ergonomic and heat stress hazards in these facilities.
OSHA emphasizes employers’ responsibility to provide a safe and healthful workplace. Implementing an ergonomic process can significantly reduce MSD risks. Key steps in this process include providing management support; including workers in assessments, solution development and implementation; educating workers about ergonomics and workplace risks; encouraging workers to report MSD symptoms; and implementing solutions like workstation adjustments, proper lifting techniques or breaks to reduce MSD risks.
California employers beware! Effective July 1, 2024, Senate Bill 553 strengthens Cal/OSHA’s authority to penalize businesses lacking a Workplace Violence Prevention Plan (WVPP). The law defines four categories of workplace violence and mandates WVPP implementation, employee training and recordkeeping for incidents (minimum five years). Non-compliance can result in hefty fines, ranging from $18,000 for initial violations to over $161,000 for willful or repeated offenses.
Technical Consulting
Outside of California, OSHA has made protection of employees a priority under the General Duty Clause in Section 5(a)(1). In 2017, OSHA published an updated compliance directive providing OSHA officers with guidance in responding to complaints of workplace violence. To combat workplace violence, employers can establish zero-tolerance policies, conduct workplace assessments to identify risk and implement violence prevention programs with clear procedures and employee training. n
For more information about any of the preceding items or to use the membership free legal time benefit through ARPM, contact Alan Rothenbuecher at har@beneschlaw.com/216.363.4436 or Brad Wenclewicz at bwenclewicz@beneschlaw.com/ 216.363.6191.
More information: www.beneschlaw.com
• Physical & Mechanical Testing
• Dynamic Testing
• Custom Test Design
• Engineering Consulting
• Rubber and Plastics Mixing
• Rubber and Plastics Molding
• Chemical & Analytic Testing
• Formula Reconstruction/Reverse Engineering
• Microscopy
• PPE Testing
• Pharmaceutical & Microbiological Services
Smithers, Akron, Ohio, a provider of testing, consulting, information and compliance services, announced the promotion of Chad Atzemis to the role of commercial director. In this role, Atzemis leads the commercial activities for the Smithers Materials Science and Engineering Division in North America. His work focuses on building and nurturing client relationships through streamlined processes and effective communication. Atzemis joined Smithers in 2023 as a senior consultant on the company’s rubber technical consulting team. He has over 20 years of technical service and business development experience in rubber, plastic and color additives.
In addition, Smithers has announced the opening of its new laboratory near Frankfurt, Germany, dedicated to testing medical devices and pharmaceutical products. As part of Smithers Medical Device Testing Division, the facility is 800 m2 of office and laboratory space, providing drug delivery device testing services to clients in Europe and around the globe. For more information, visit www.smithers.com.
Zochem, Dickson, Tennessee, a producer of zinc oxide powder, has awarded Palmer Holland, Cleveland, Ohio, a national specialty chemical and ingredient distributor of raw materials, its Distributor of the Year Award for 2024. Palmer Holland has been a Zochem distribution partner for many years and has earned this award because of its responsiveness and customer service. Palmer Holland’s focus on coatings, adhesives, sealants and elastomers, and the plastics markets are a true fit for Zochem’s customer base. For more information, visit www.zochem.com.
The L.S. Starrett Company, Athol, Massachusetts, a global manufacturer of precision measuring tools and gages, metrology systems and more, has announced the introduction of its No. W4900 Wireless Digital Electronic Indicator. This innovation is a precision measurement gage featuring
touchscreen technology, multiple resolution and color settings, digital and analog readouts in the same indicator, seven languages, wireless output and many other features. Starrett W4900 AGD Group 4 Indicators are versatile with large, easyto-read and navigate capacitive touchscreen user interface menus, and have wireless output for statistical process control (SPC) via data collection systems such as Starrett DataSure® 4.0. For more information, visit www.starrett.com
Stockwell Elastomerics, Philadelphia, Pennsylvania, a manufacturer of custom gaskets, has announced the launch of its new website, featuring a bold visual design and updated enhanced navigation. Its website also features a new company logo and tagline, “Experts in Silicone Gasket Solutions.” The website continues to provide technical information that engineers and designers need to find the right materials and products for advanced technology projects. It introduces a revamped menu system that makes it easier for visitors to find information about material, capabilities and products such as custom gaskets and pads. Engineers easily can find the technical data sheets they need along with tech tips and the frequently updated Elastomerics blog. For more information, visit www.stockwell.com.
Under the leadership of the Fraunhofer Institute for Applied Polymer Research IAP, four Fraunhofer Institutes now are developing alternative, bio-based raw material sources for synthetic rubber as part of the project, “Sustainable biomonomers for synthetic rubbers with application-related adjustable viscoelastic properties NaMoKau.” Fraunhofer funded the three-year project with 3.25 million euros and started in April 2024. With the depletion of fossil resources and the urgent need to reduce CO2 emissions, there is a need for sustainable alternatives for rubber producers. To meet these challenges, the team of four includes The Fraunhofer Institutes for Applied Polymer Research IAP, Microstructure of Materials and Systems IMWS, Industrial Mathematics ITWM and Environmental, Safety and Energy Technology UMSICHT. For more information, visit www.iap.fraunhofer.de/en.html.
4
[6] Trelleborg Announces Innovation Center, Names Muroski President
Trelleborg, a global supplier of engineered polymer solutions that seal, damp and protect critical applications, has announced the launch of Trelleborg Sealing Solutions Innovation Center in Plymouth, Minnesota. The Innovation Center provides global industrial customers with a single partner for design, rapid prototyping, development and serial production, ensuring cost control and scalability of customers’ solutions. It comprises several core competencies, including design, consultation, toolmaking, prototyping, high-precision machining, silicone molding, thermoset elastomer molding, thermoplastic molding,
automation, assembly and secondary operations. By using Trelleborg’s manufacturing facilities, customers have access to raw material traceability and established validation processes. These facilities are ISO certified and meet requirements of the Food and Drug Administration and global water regulations.
Additionally, Trelleborg has named Linda Muroski as the business area president of Trelleborg Medical Solutions and a member of Group Management. She joined Trelleborg in 2016 and recently served dual roles as Trelleborg’s president, Marketing Americas and as president, Global Healthcare and Medical. For more information, visit www.trelleborg.com. n
By Andrew Carlsgaard, analytics director, ARPM
The ARPM 2024 Wage and Salary Report continues to reflect the impact of heightened inflation on wages and salaries across the US workforce. The survey results of 233 manufacturers, representing over 37,000 employees, show an increasingly prevalent upward trend, as 59 of the 70 industry job categories (88%) tracked year-over-year have reported increases from 2023 to 2024. These increases primarily are due to the extreme inflation experienced in the previous three years and higher than average current-year inflation. Fortunately, the elevated demand for workers in manufacturing seen from 2020 to 2022 has declined somewhat in 2023 and 2024. The US Bureau of Labor Statistics 1 reported that workforce participation and unemployment gradually have rebounded to pre-pandemic levels. While low unemployment, plentiful job openings and lower participation had created a favorable market for workers in the past few years, gradually decreasing inflation and heightened economic uncertainty in 2023 and 2024 have slowed this trend over the past three years compared to levels seen in 2020 and 2021. Those three factors are not as significant contributors to wage increases in 2024, compared to current-year inflation combined with catch-up from the previous three years’ cumulative inflation.
1
The ARPM 2024 Wage and Salary Report reveals significant trends in specific roles across the manufacturing industry (Chart 1). The average increase year-over-year for the 59 positions that experienced increases was approximately 5.1%, down from 6.0% in the 2023 report. The remaining 11 positions decreased or stayed the same in median salary – averaging around 2.2% lower in 2024 (3.5% lower in 2023). Notably, the most substantial salary increases were for marketing directors or managers (19% increase – however, with a relatively low sample size this year), semi-skilled technicians (16% increase) and materials managers (13% increase). Conversely, the most substantial median wage decreases were for marketing specialists (6% decrease), tooling engineers (5% decrease) and IT support technicians/specialists (4% decrease). This data suggests somewhat of a reversal of a 2023 trend where white-
collar positions that were not directly involved in the plant’s day-to-day operations most often saw declines year-over-year compared to those closer to operations or engineering. There is less of a clear pattern for the increases and decreases by position in 2024.
While the average yearly wage increases for all tracked positions in 2024 has increased from 2023, inflation still likely accounts for much of this, particularly with the unprecedented level of inflation from 2022 (8.0%) that industry wages still are catching up to, as the rate of inflation almost doubled the wage increases in that year (Chart 2). The consumer price index 2 (the primary measure tracked by the US Bureau of Labor Statistics to measure year-over-year price inflation) started to surge in early 2021 and peaked in June 2022 at around 9.1%. However, the rate fell to a three-year low of 3.0% as of June 2023 and has remained in the 3%-4% range over the past year. For context, this is twice as high compared to average pre-pandemic rates (an average of 1.8% in 2019). The average yearly inflation for 2024 (through May) is 3.3%, while the median wage growth from the prior year for all positions tracked in the 2024 Wage and Salary Report was 3.9%. While that percentage wage increase is 0.2 percentage points higher than the prior year (3.7% in 2023), inflation catch-up from 2022 likely is the driving factor for the general increase, as workers seek raises or higher salaries elsewhere to offset the massive 8.0% increase in prices of goods and services in 2022. Additionally, this wage increase still is lower than wage increase data tracked by the US Federal Reserve 3, which reports yearly wage increases of
5.1% for US manufacturing jobs and 5.4% overall for US jobs. With these elevated year-over-year wage increases, processors report softer hiring demand overall than the prior two years. In the ARPM 2022 Wage and Salary Report, 92% of processors said they would be hiring new employees over the next 12 months, but this dropped to 87% in 2023 and now sits at 80% as of the publishing of the 2024 report (Chart 3). This decrease in demand for labor is a result of both economic uncertainty and government intervention to curb consumer demand. These factors have influenced manufacturers’ profitability and capacity utilization, forcing them to cut costs and postpone investments.
While the survey results may be unfavorable to the employers’ bottom line, the wage and salary increases observed in the 2024 report are unsurprising, given the current state of the economy and inflationary pressures. For manufacturing organizations, facing external strains on their bottom line in other areas (such as heightened energy and raw material costs), hiring new or backfilled roles slower than in the previous few years or maintaining a consistent level of employment may become necessary to maintain profitability, while preventing any future reductions in force in the near term. If economic conditions remain favorable for workers, there will continue to be some degree of upward movement in wages. However, lower inflation ultimately will be vital to curbing these upward yearly wage trends that have become common since 2020. Likewise, if the labor market shifts more favorably toward employers in a recession, processors need to adjust only to the current market if it fits the current needs of their business.
As a best practice, leaders should carefully examine the results of each position in the 2024 Wage and Salary Report and adjust wages where appropriate to reflect industry averages for organizations of the same size or location to remain competitive in the labor market – by not correctly addressing wages, organizations risk losing valuable internal resources and incurring additional costs to replace departed employees. Additionally, knowing the going rate for those positions is imperative to attracting and retaining the talent to keep operations steady in an uncertain economy. n
The entirety of ARPM’s 2024 Wage and Salary Report is available to purchase from the ARPM website at www.arpminc.com/publications.
References
1., 2. US Bureau of Labor Statistics –https://www.bls.gov/data/apps.htm
3. Federal Reserve Bank of Atlanta –https://www.atlantafed.org/chcs/wage-growth-tracker
300+ lawyers in Columbus and other offices
Ice Miller focuses on meeting the needs of our clients quickly, efficiently and cost-effectively. Ice Miller attorneys with rubber industry experience can assist with your greatest legal challenges. Contact Josef Keglewitsch at 614-462-2279 or josef.keglewitsch@icemiller.com for more information. icemiller.com
By Josh Guilliams, vice president of consultancy, Smithers
Quality control is critical in the rubber manufactured goods industry. Quality control ensures that rubber components are manufactured to specification and perform as expected. Depending on the application, quality can translate to better adherence to design standards, greater efficiency, reduced costs and better performance in the field.
Achieving quality is not necessarily a simple task. Quality is the product of many variables working in concert. This ranges from raw material characteristics to the skill level of the mixing technician to ambient temperature in the processing or manufacturing environment. Variations in any of these factors can affect quality and can occur unintentionally. Manufacturers expect to see changes when they adjust their processing methods or tweak a product design, but changes also can arise unexpectedly, as a result of:
y Changing from one raw material supplier to another.
y Hiring a new technician.
y Climatic conditions at the processing facility.
y Undetected machine malfunctions.
Identifying the root cause of unexpected quality changes or processing issues can be challenging, especially with limited data. Manufacturers can give themselves an advantage by developing a regular quality auditing program.
A regular quality auditing program is a series of tests conducted at prescribed intervals to monitor the quality of a rubber
manufactured product. A first round of testing establishes a baseline against which future testing data can be compared.
For example, samples from the latest production run of a coolant hose may undergo pressure, vibration, temperature and fluid exposure testing once per quarter. The specific tests depend on the component’s intended service environment and will differ from product to product.
Collecting and reviewing test data at regular intervals gives manufacturers long-term insight into trends and changes. There are numerous scenarios in which this can be a tremendous benefit. Examples include:
Some traditional quality assurance processes don’t detect issues or defects until the product has failed in the field, at which point correcting the problem can be costly and timeconsuming. Regular quality audits allow manufacturers to collect more data, spot patterns or inconsistencies more quickly and implement solutions right away – saving time, money and potential damage to the brand in the market.
When product issues or failures occur in the field, it is critical for manufacturers to understand the cause so they can make the necessary changes to solve the problem and prevent recurrences. Quality auditing data is a valuable starting point for these investigations. Inconsistencies or anomalies in the data often serve as a first clue that manufacturers can trace back
to the source of the issue, so they can develop and implement a solution without having to “guess and check.”
Extreme weather events, geopolitical unrest and the COVID-19 pandemic have all caused supply chain disruptions in recent years. Many manufacturers were forced to change raw material suppliers when their usual sources became unavailable. However, switching from one supplier to another is not necessarily a simple process. There can be small variations between seemingly identical materials that come from different sources. Quality auditing allows manufacturers to quickly determine whether materials from the new supplier can seamlessly be introduced into their existing production process or whether they need to make changes to accommodate any variations.
Regulatory requirements can shift for a variety of reasons. If the regulatory requirements for a product or material change, manufacturers can use quality audit data to determine whether their product is still compliant. Some recent material regulations may require a change in raw materials. Having audit data for material or product performance can be critical to evaluating potential material replacements. This can save companies from unintended consequences affecting performance or give manufacturers a head-start on a necessary redesign.
Establishing and maintaining a consistent quality auditing program can be a significant undertaking, especially in the fast-paced manufacturing industry. A quality auditing program requires:
y Space and budget for testing equipment.
y One or more employees with the time and skills required to develop and manage the program and review data regularly.
Some manufacturers have ample resources to undertake such a project internally. For others, an internal quality auditing program may be impractical due to space, time or staffing constraints.
One option for implementing a quality auditing program that doesn’t require internal resources is to partner with an independent, third-party testing laboratory. Independent labs have extensive testing capabilities and in-house expertise. An independent lab can closely work with a manufacturer to design a custom quality auditing program that meets its needs, manage the program and provide regular reports and guidance on potential solutions to issues that arise.
Partnering with an independent lab also allows manufacturers to leverage the collective experience of the lab’s in-house
experts. With their years of practical experience with a wide range of components and testing scenarios, seasoned testing professionals bring a valuable perspective to every project. While there certainly is a cost to establishing a proactive quality control program, it can be looked at as an insurance policy against much more costly warranty or recall issues that could occur.
The following is a hypothetical scenario demonstrating the value of laboratory testing and regular quality auditing.
• Over the course of one quarter, a hose manufacturer receives more warranty claims than usual on a particular automotive hose. Leadership is concerned about the increased cost of quality and time to investigate the root cause through internal resources, as well as damage to brand image.
y The manufacturer engages an independent testing laboratory to identify the source of the issue.
y The testing laboratory develops and executes a quality testing program. After successfully recreating the product failure in a controlled environment, the laboratory pinpoints the exact source of the recurring issue and recommends a design change to address it.
y Upon implementation of the recommended change, warranty claims decrease.
By outsourcing testing to an independent laboratory, the manufacturer avoided spending even more valuable staff time dealing with the issue. However, the issue may have been avoided altogether with a proactive quality auditing program. Strategic testing, conducted at regular intervals, may have detected the issue before the faulty product went to market, and the manufacturer could have implemented a solution right away – foregoing any failures in the field or warranty claims entirely. n
Regular quality auditing is a proactive strategy for rubber manufacturers striving to elevate their quality assurance practices. Partnering with an independent, third-party laboratory makes regular quality auditing accessible and practical for manufacturers with limited time, space or expertise to manage a program. Having the right data to make the best product development decisions is a cost-effective insurance policy against the potential of higher costs of quality issues.
Josh Guilliams is vice president of consultancy at Smithers and leads the company’s technical consulting team. Guilliams manages client relationships and works with other Smithers experts on complex projects. He also conducts in-depth investigations into a wide variety of rubber materials and final products on behalf of clients.
More information: www.smithers.com
By Chris Kuehl, managing director, Armada Corporate Intelligence
Has it been mentioned that the sole function of economic forecasting is to make astrology respectable? This was a rather famous and appropriate quote from John Kenneth Galbraith. It’s not that economists are that bad at forecasting – but they are only as good as the data, and when these numbers keep changing, it makes life interesting.
Lately, there have been several significant and unexpected changes, and suddenly, the economic picture has shifted – in some positive ways and some not so positive ways.
The most important of these changes are interest rates and the potential for decline later this year. Since the start of 2024, there have been assertions that the Fed Funds rate would start to come down from its current level of 5.5%.
The markets seemed to think this would happen by the second quarter, despite the fact the Fed never suggested this decision would be made that soon. The assumption was changed, and predictions of a rate cut by the third or fourth quarter dominated.
Now that expectation has been altered by the latest data on inflation, job growth and overall economic progress. Remember the mantra of the central bank, “We raise rates until we break something, and then we lower rates to fix what we broke.”
The pressing question is – has the Fed broken anything with these rate hikes? Looking at the data, it would be difficult to assert that it has. Unemployment fell back to 3.8% in the latest Labor Department reading, and there were an additional 300,000 jobs added. At the same time, the inflation rate ticked back up to 3.5% (from 2.5%). The estimates for first-quarter growth originally were less than 2% but now are at 2.4%.
In other words, there is no pressing reason for the Fed to consider a rate cut, and now analysts are suggesting that these
reductions will not come until 2025. The bond buyers already have signaled they think the European Central Bank will cut its rates before the Fed does.
This means that companies counting on rate cuts may have to wait longer than expected. The Fed has not officially declared its intention but the hawks on the Open Market Committee are making a case.
The second important change involves the outlook for oil prices. It was just a few weeks ago that analysts were confidently asserting that per-barrel prices would stay in the $70 to $85 range “in perpetuity” based on the new technology deployed in oil production. It now was possible for producers to react almost instantly to changes in the spot price per barrel. There was a little asterix with that assertion – pending geopolitics.
In the last few weeks, geopolitical concern has come front and center, and prices have soared into the $90s again and analysts are suggesting that $100 and above will be in the future. The bottom line – oil is a globally priced commodity, and it doesn’t matter that the US is North American independent as far as oil production goes. The US is hitting record levels of crude production [over 13 million barrels per day (bpd)] and consumes around 20 million bpd (that which the US does not produce and gets mainly from Canada and Mexico).
The fact is that Iran and Israel are on a collision course and neither seems inclined to back off.
Iran now has threatened to shut down the Straits of Hormuz as the Houthi rebels have shut down the Red Sea. If this takes place, there is no route for Saudi oil to reach the markets and no route for the production of the other Gulf oil states. That sends the price of oil into orbit and could trigger attacks that escalate that war in a hurry.
The very latest wrinkle in all this saw the oil markets calm down a bit and conclude that neither Iran nor Israel is ready to make this an all-out war that would drag in many more combatants. The per barrel prices had been spiking and seemed headed for the $90s and maybe higher, but now they have settled back to the mid-$80s for the time being.
And that’s not all – there is yet another change that will prove economically disruptive. China is facing a serious deflation crisis, and this has combined with the collapse of the property market (as well as the overall stock market).
China has not seen levels of foreign direct investment this low since the early 1990s. The upshot is that China is in economic distress and ordinarily that would trigger reductions in production and subsequent layoffs. China is not about to risk large numbers of unemployed so these operations keep producing and that creates massive surplus.
Given that China still is a command economy (where output keeps accumulating and China then dumps it on the global economy), that means a surge of Chinese goods priced lower than they have been in years. This will stall the reshoring effort in the US and Europe. If one buys from China, this is good news, but if one competes with China, this is bad news indeed. China has been trying to reduce dependence on exports, but right now, it needs all the business it can get.
One more issue and change to give some thought to is one that is not yet imminent. The Baby Boom generation has accumulated a great deal of money and has reached the stage where that money may start to end up in the hands of the next generation. There are over 1,000 billionaires over the age of 70, and collectively, they hold over five trillion dollars.
In 2023, there were more billionaires created with inherited wealth than through entrepreneurial activity, and that has not happened in decades. One of two things likely is to happen to that accumulated cash.
First, governments are looking at this cash as a windfall they can access with higher inheritance taxes, and many are quickly moving in that direction despite the fact this is a most unpopular tax. If the governments succeed in grabbing that money, it will trigger some behaviors on the part of the holders of that wealth. They likely will try to spend it before it can be taxed, and that means billions flooding into an economy that already is trying to dampen inflation.
Second, remember that one of the main triggers of the current inflation surge was the cascade of money that flowed in reaction to the pandemic. If the Boomers try to spend rather than get hit with taxes, there would be a surge that dwarfs the pandemic spend and inflation will resume its upward march –triggering another round of interest rate hikes. This is not yet imminent and may not come to pass if there are no attempts to go aggressively after inherited wealth, but given the budget issues facing the government, that tax target is tempting. n
Chris Kuehl is managing director of Armada Corporate Intelligence. Armada executives function as trusted strategic advisers to business executives, merging fundamental roots in corporate intelligence gathering, economic forecasting and strategy development. Armada focuses on the market forces bearing down on organizations.
More information: www.armada-intel.com
By Paige Heck, project manager, ARPM
In a rapidly changing corporate landscape where leadership is not just a role but a defining character trait, Thayer Leadership’s Building Leaders of Character program stands out as a source of transformative learning. Rooted in the storied traditions of West Point and the US Army, the partnership between the Association for Rubber Products Manufacturers (ARPM) and Thayer Leadership was designed to build strong, character-driven leaders.
Participants will engage in a 14-week journey consisting of 18 virtual sessions. The program was meticulously crafted to blend live interactions with seasoned leaders, real-time keynote presentations and immersive video-based training. There will be academic sessions, interactive experiential sessions, mentoring with expert faculty, networking and inspirational speakers.
The Building Leaders of Character program is structured to ensure a comprehensive learning experience, including:
y Accountability: Strengthening the ability to uphold standards and create team accountability.
y Trust: Building and maintaining trust is a key pillar to effective leadership.
y Team Unity: Techniques to unite teams and drive toward common organizational goals.
y Feedback Mastery: Strategies to deliver timely and constructive feedback.
y Communication: Applying proven military communication approaches to enhance clarity and efficiency.
y Performance Improvement: Utilizing After Action Reviews to enhance organizational outcomes.
With limited enrollment on a first-come, first-served basis, the program ensures an impactful learning environment. Participants emerge not only with enhanced leadership intelligence and practical leadership tools but also with a network of peers committed to the same methodologies built throughout the program.
The Building Leaders of Character program is more than just a learning opportunity offered through the ARPM Training Academy – it is a catalyst for driving profound professional and personal growth in the leadership realm. The need for resilient, principled and effective leadership is critical in every organization.
“This leadership program exceeded my expectations. I would highly recommend it for any level of leader desiring to grow and improve their skills.” – vice president, engineering
“This has been a great training experience. I wouldn’t even call it training – elements of leadership we can apply. It has been valuable and impactful for me!” – general/plant manager
“No matter if you’re leading a team or one individual, it starts with leading oneself. The training has helped me recognize who I am and who I want to become as a leader.” – plant manager
ARPM’s Executive Director Letha Keslar was part of the development and construction of the leadership program and is a graduate. She shared, “Upon working with Thayer Leadership Development Group (TLDG), we knew that we found what our members were looking for... a customized leadership program that specifically was designed to positively impact and give usable leadership tools to manufacturing leaders of the ARPM network. The experience included such items as how leaders effectively and efficiently communicate to all levels of the organization; how teams accomplish missions in Volatile, Uncertain, Complex and Ambiguous (VUCA) environments; and how building and maintaining organizational culture is essential to not only winning battles, but wars – and how those lessons apply directly to the complex business world the industry operates in daily.” n
ARPM’s next class of the “Building Leaders of Character” series will begin on September 10, 2024. Space is limited, so to save a seat(s), register by August 31, 2024, on the ARPM website at www.arpminc.com.
H E I N D U S T R Y N E E D S Y O U
J O I N T H E N E T W O R K
T O D A Y !
A S S O C I A T I O N F O R R U B B E R P R O D U C T S M A N U F A C T U R E R S
B e n c h m a r k i n g | I n d u s t r y S t a n d a r d s | T r a i n i n g | N e t w o r k i n g | a n d m o r e . . .
L i s t e d i n R u b b e r a n d P l a s t i c s N e w s " T o p 5 R u b b e r
I n d u s t r y A s s o c i a t i o n s Y o u S h o u l d K n o w . "
V i s i t a r p m i n c . c o m f o r m o r e .