AUTOMATYKA
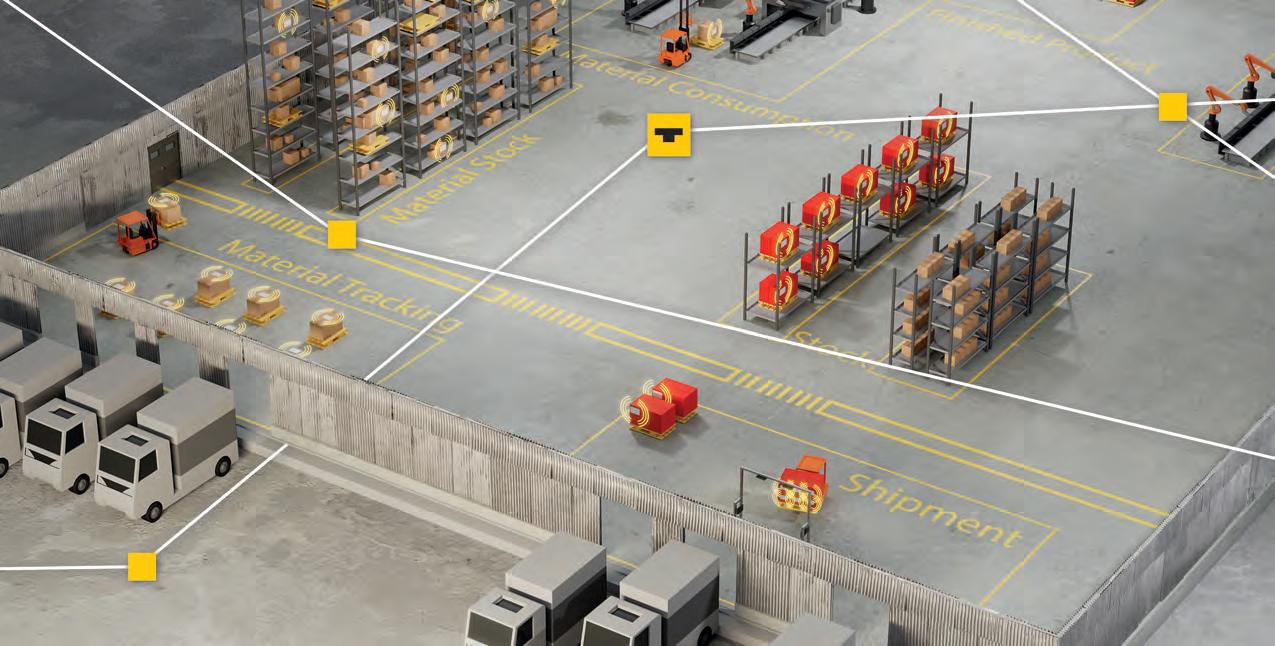
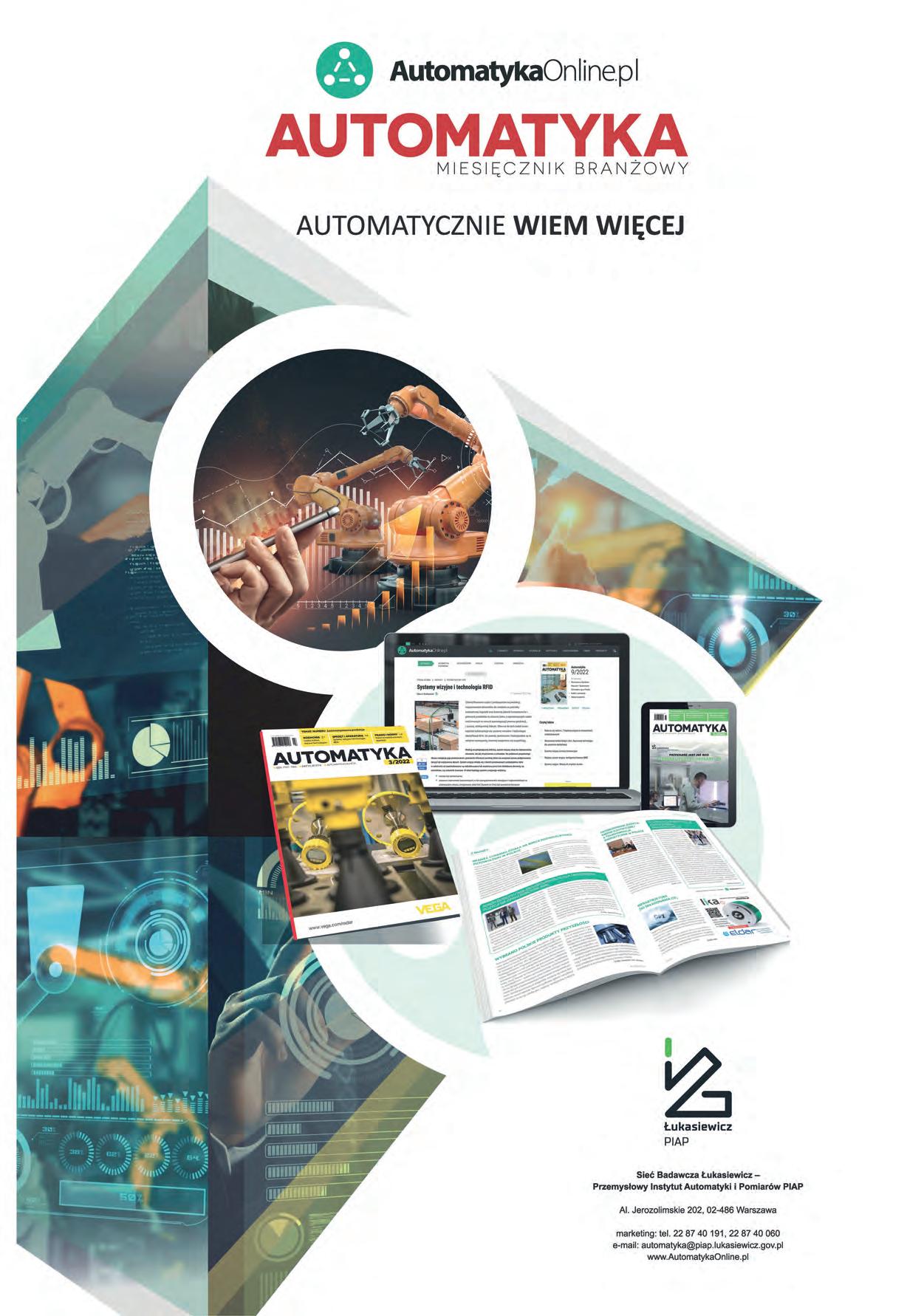
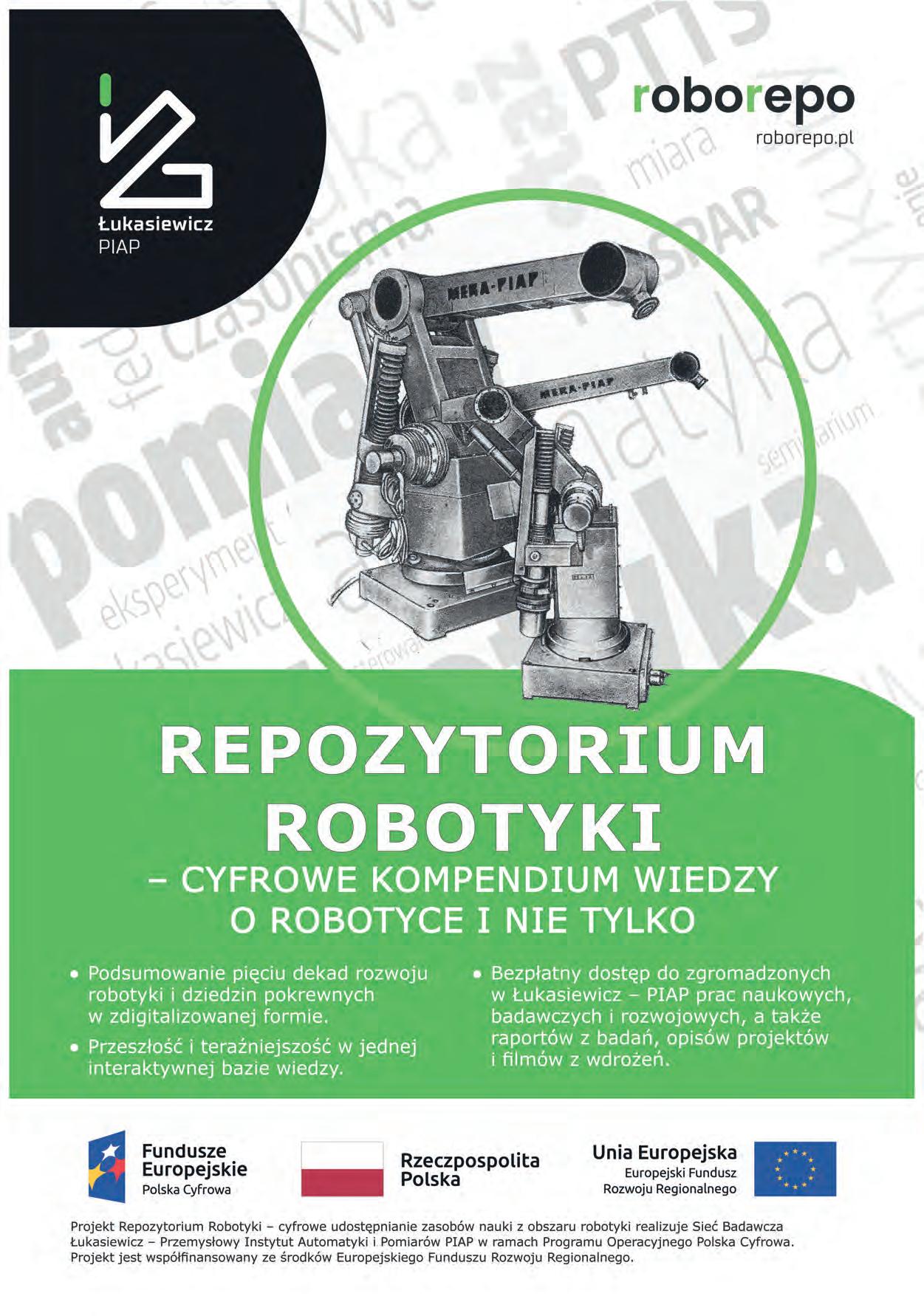
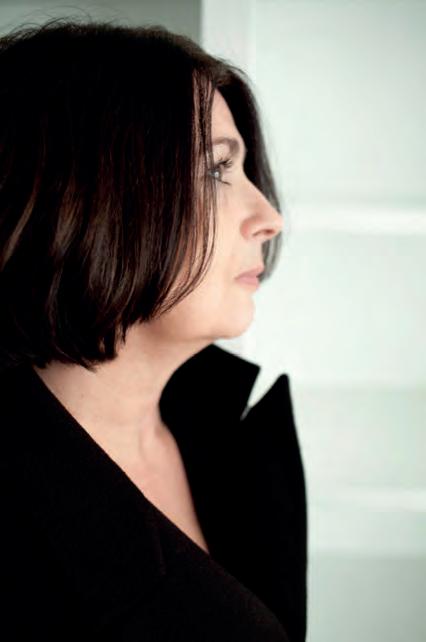
Małgorzata Kaliczyńska redaktor naczelna
Małgorzata Kaliczyńska redaktor naczelna
wrzesień 2024 r. to czas przedłużonej kanikuły – upalny, ale zapamiętamy go też z powodu powodzi, która dotknęła południowo-zachodnie regiony Polski. W tym trudnym okresie odbyły się pierwsze powakacyjne spotkania w klasycznej bezpośredniej formule. Również nasza Redakcja wzięła udział w pierwszych imprezach. Kolejne odbywają się w październiku i listopadzie. Już dziś możemy zapowiedzieć relację z ostatnich Międzynarodowych Energetycznych Targów Bielskich Energetab, ale to dopiero w kolejnym numerze pisma.
Bieżący numer został zdominowany przez systemy automatyki stosowane na halach produkcyjnych oraz mocno związaną tematykę stosowanych tam napędów. Tę część pozostawiamy naszym czytelnikom.
Tym razem skupmy się na czteroczęściowym cyklu poświęconym programowaniu robotów przemysłowych. W numerach miesięcznika
AUTOMATYKA 6/2024, 7-8/2024, 9/2024 i 10/2024 zaproszony autor, prof. dr hab. inż. Cezary Zieliński, zaprezentował metody programowania robotów przemysłowych, wychodząc od podstawowych informacji na temat programowania on-line i off-line oraz roli układów sterowania. W przywołanym cyklu artykułów przedstawiono sposoby programowania robotów czterech globalnych firm produkujących roboty przemysłowe. Takich firm jest więcej, ale konieczne było ograniczenie liczby metod programowania, które można opisać w tekście o ograniczonym wolumenie, i jednocześnie na tyle dużej, by z cyklu artykułów wynikały zarówno różnice, jak i elementy wspólne dla sposobów programowania robotów przemysłowych. Autor skoncentrował się na językach programowania oraz sposobach tworzenia programów, pomijając kwestie drugorzędne z punktu widzenia ogólnego zaznajomienia się z opisywaną materią.
Automatyka przemysłowa sięga po coraz nowsze rozwiązania. Rodzą się pytania. Jakie technologie zdominują automatykę przemysłową w najbliższych latach?
Na czym opiera się sukces wdrażania nowoczesnych technologii? Pytania zadajemy firmie Nexus, która koordynuje projekty realizowane w Polsce przez firmy z Japonii. O swoich doświadczeniach szczegółowo mówi Juliusz Hirotomi, prezes Nexus Engineering Europe.
Stałym Czytelnikom działu Prawo i normy polecamy najnowszy artykuł poświęcony ważnym ustaleniom zawartym w dokumencie Akt o sztucznej inteligencji. Nie wszystkie rozwiązania bazujące na sztucznej inteligencji są bezpieczne i pożądane z perspektywy społeczeństwa, a w szczególności zdrowia, bezpieczeństwa oraz praw podstawowych. Regulacja dotycząca zakazanych praktyk w zakresie AI będzie obowiązywać już od 2 lutego 2025 r. Gorąco zapraszam do lektury!
Przed wdrożeniem konkretnych rozwiązań do produkcji ważne jest, aby móc je przetestować. Z takim przesłaniem zbudowana została sala szkoleniowo-pokazowa Factory of the Future Lab, w której każdy ma szansę poznać, dotknąć, a przede wszystkim zweryfikować na żywo koncepcję Przemysłu 4.0. Odwiedzając nas odkryjesz nowe technologie, pogłębisz swoją wiedzę i znajdziesz najlepsze rozwiązania z wymiernymi korzyściami, dostosowane do specyficznych wymagań swojej fabryki.
Chcemy wraz z Państwem urzeczywistniać interesujące, a czasem nawet zwariowane wizje, na które nie moglibyśmy sobie pozwolić w “normalnej” fabryce, czy w “rzeczywistej” maszynie.
Zapraszamy klientów, partnerów, szkoły i uczelnie oraz wszystkich zainteresowanych najnowszymi technologiami.
REDAKTOR NACZELNA
Małgorzata Kaliczyńska tel. 22 874 01 46 malgorzata.kaliczynska@piap.lukasiewicz.gov.pl
ZASTĘPCA REDAKTOR NACZELNEJ
Urszula Chojnacka tel. 22 874 01 85 urszula.chojnacka@piap.lukasiewicz.gov.pl
REDAKCJA MERYTORYCZNA
Małgorzata Kaliczyńska
REDAKCJA TEMATYCZNA
Sylwia Batorska tel. 22 874 00 60 sylwia.batorska@piap.lukasiewicz.gov.pl
WSPÓŁPRACA REDAKCYJNA
Marcin Bieńkowski, Jolanta Górska-Szkaradek, Agnieszka Staniszewska, Damian Żabicki
MARKETING I REKLAMA
Jolanta Górska-Szkaradek – menedżer tel. 22 874 01 91 jolanta.gorska-szkaradek@piap.lukasiewicz.gov.pl
PRENUMERATA I KOLPORTAŻ
Ewa Markowska tel. 22 874 03 71 ewa.markowska@piap.lukasiewicz.gov.pl
SKŁAD I REDAKCJA TECHNICZNA
Ewa Markowska
KOREKTA
Ewa Markowska
DRUK
Drukarnia „PAPER & TINTA”
Barbara Tokłowska Sp. K. Nakład: 4000 egzemplarzy
REDAKCJA
Al. Jerozolimskie 202, 02-486 Warszawa tel. 22 874 01 46, fax 22 874 02 20 automatyka@piap.lukasiewicz.gov.pl www.AutomatykaOnline.pl
WYDAWCA
Sieć Badawcza Łukasiewicz – Przemysłowy Instytut Automatyki i Pomiarów PIAP
Al. Jerozolimskie 202, 02-486 Warszawa
Szczegółowe warunki prenumeraty wraz z cennikiem dostępne są na stronie automatykaonline.pl/prenumerata.
Redakcja zastrzega sobie prawo do skracania i modyfikacji nadesłanych materiałów oraz nie ponosi odpowiedzialności za treść reklam i materiałów promocyjnych.
Japońska precyzja w parze z europejskim know-how 24 Rozmowa z Juliuszem Hirotomi, prezesem Nexus Engineering Europe.
Jakie technologie zdominują automatykę przemysłową w najbliższych latach? Na czym opiera się sukces wdrożenia nowoczesnych technologii? W jaki sposób firma Nexus koordynuje projekty realizowane w Polsce przez firmy z Japonii? O tym mówi Juliusz Hirotomi, prezes Nexus Engineering Europe.
Roboty kolaboracyjne
Kluczowy element łatwej automatyzacji przemysłowej
Nowoczesne technologie pomiarowe to oszczędności w zakładach przemysłowych
Technika napędowa
Pierwszy uchwyt z tworzywa zgodny z wytycznymi SEMI-S8
Maksymalizacja konkurencyjności w dobie automatyzacji
Metody programowania robotów przemysłowych, cz. 4
Produkcja przemysłowa w dużej mierze polega na ciągłym wykonywaniu powtarzalnych, mniej lub bardziej skomplikowanych czynności. Zastąpienie przy ich wykonywaniu pracy ludzkiej lub zastąpienie obsługiwanych ręcznie maszyn zautomatyzowanymi lub zrobotyzowanymi systemami nie tylko wpływa na zwiększenie wydajności i obniżenie kosztów, ale przede wszystkim podnosi jakość produkcji, a co za tym idzie, zadowolenie klienta.
Jednym z podstawowych zadań układów automatyki jest wprawianie różnych urządzeń i maszyn w ruch. Tutaj niezbędne są układy napędowe oparte na urządzeniach sterujących i kontrolujących pracę silników.
15–17.10 Katowice
Międzynarodowe Targi Obrabiarek, Narzędzi i Technologii Obróbki Toolex www.toolex.pl
15–17.10 Katowice
ExpoWELDING – Międzynarodowe Targi Spawalnicze www.expowelding.pl
16–17.10 Kraków
Międzynarodowe Targi Obróbki, Magazynowania i Transportu Materiałów Sypkich i Masowych Symas
Międzynarodowe Targi Utrzymania Ruchu, Planowania i Optymalizacji Produkcji Maintenance www.symas.krakow.pl
22–24.10 Katowice IX Europejski Kongres Lean Management www.kongreslean.pl
11/2024
5–7.11 Nadarzyn
Międzynarodowe Targi Innowacyjnych Rozwiązań Przemysłowych Warsaw Industry Week www.industryweek.pl
13–15.11 Poznań
Międzynarodowe Targi Techniki Pakowania i Etykietowania Taropak www.taropak.pl
13–15.11 Nadarzyn
Targi Technologii Dla Elektromobilności Emobility Expo www.emobilityexpo.pl
18–19.11 Kraków Środkowoeuropejskie Forum Technologiczne CETEF www.cetef.eu
19–21.11 Lublin
Targi Energetyczne Energetics www.energetics.targi.lublin.pl
Amerykańska firma AFL, spółka zależna japońskiego koncernu Fujikura Ltd. i globalny dostawca infrastruktury sieci światłowodowych, otworzyła zakład produkcyjny w MDC² Park Gliwice. Zakład położony jest na terenie specjalnego kompleksu magazynowego o powierzchni 13,4 ha i oferuje 13 000 m² powierzchni użytkowej. Jego konstrukcja obejmuje panele słoneczne, punkty ładowania pojazdów elektrycznych, zieloną ścianę, ule pszczele i system retencji wody deszczowej.
Zintegrowane praktyki ekologiczne zakładu produkcyjnego w Polsce stanowią istotny krok w kierunku realizacji naszej wspólnej misji, by ograniczyć wpływ działalności AFL i Fujikura na środowisko przy jednoczesnym wyznaczaniu nowych standardów w dziedzinie odpowiedzialności przedsiębiorstw. Przedsięwzięcie następuje po oficjalnej
inauguracji komitetu AFL ds. ESG i nawiązaniu partnerstwa z programem EPA ENERGY STAR. Celem jest dalsze umacnianie firmy na drodze do osiągnięcia celów w zakresie emisji gazów cieplarnianych zgodnie z założeniami Science Based Targets initiative. Jestem pewien, że obiekt przyczyni się do zapewnienia cenionym klientom i partnerom z regionu EMEA wyjątkowych, ekologicznych produktów i usług – mówi Naoki Okada, dyrektor, prezes i dyrektor generalny Fujikura.
Źródło: AFL
Creotech Instruments, wiodący polski producent systemów i podzespołów satelitarnych, został wybrany przez Europejską Agencję Kosmiczną (ESA) do realizacji zamówienia na sześć sond kosmicznych odpornych na radiację. Sondy będą częścią misji naukowej Plasma Observatory. Polska firma po raz pierwszy będzie pełnić rolę dostawcy całych urządzeń. Koszt misji jest szacowany na pół miliarda euro. – Wierzymy, że nasze innowacyjne podejście przyczyni się do sukcesu tej misji. Dla Creotech to duża szansa na dalszy rozwój i umocnienie naszej pozycji na międzynarodowym rynku kosmicznym w roli dostawcy kompleksowych rozwiązań satelitarnych o najwyższym poziomie jakości – mówi
dr hab. Grzegorz Brona, prezes spółki Creotech Instruments.
ESA ma zamiar dokonać zaawansowanych pomiarów za pomocą nietypowego instrumentu badawczego. Ma on mieć kształt zbliżony do olbrzymiego czworościanu, którego jeden bok będzie miał ponad 100 tys. km długości.
Sześć sond kosmicznych, zaprojektowanych właśnie przez Creotech Instruments, w połączeniu ze statkiem matką, uformuje ten zaawansowany technologicznie instrument. Miejsce pomiaru to przestrzeń między Ziemią a Księżycem. Start misji, która przez kilka lat będzie badać plazmę, planowana jest na 2037 r.
Źródło: Evertiq.pl
Grupa Technologiczna HARTING uzupełniła swój zarząd przez utworz enie nowego, kluczowego stanowiska. 1 września 2024 r. Onintza Otamendi Iza została członkiem zarządu ds. sprzedaży, przejmując odpowiedzialność za strategiczne zarządzanie działaniami sprzedażowymi Grupy. – Tworząc nowy dział w zarządzie i mianując panią Otamendi Izę, dajemy jasny sygnał znaczenia sprzedaży w naszej strategii korporacyjnej. Zapewniliśmy usługi menedżera z wieloletnim doświadczeniem branżowym w największych międzynarodowych przedsiębiorstwach. Możemy jeszcze intensywniej skupić się na naszych klientach dzięki profesjonalnemu, kierunkowanemu podejściu – mówi Philip Harting, prezes zarządu HARTING Technology Group.
Źródło: HARTING
Łukasiewicz – PIAP zrealizował zamówienie na roboty mobilne PIAP GRYF z wyposażeniem dodatkowym do neutralizacji i rozpoznania pirotechnicznego do Republiki Togijskiej. To 27. kraj na mapie odbiorców polskiej robotyki EOD i czwarty kraj na kontynencie afrykańskim. Dostarczone roboty to najbardziej znana i sprawdzona konstrukcja średniego robota EOD warszawskiego instytutu. Urządzenia pracują już w kilkunastu armiach i służbach odpowiedzialnych za bezpieczeństwo publiczne na świecie, od Korei Południowej po Indonezję, Francję, Finlandię, Nigerię, Liban, Senegal oraz Rumunię i Włochy. W Polsce roboty PIAP GRYF są wykorzystywane w Policji, Straży Granicznej, Państwowej Straży Pożarnej oraz Oddziale Specjalnym Żandarmerii Wojskowej.
Źródło: Łukasiewicz – PIAP
Raport „Global Life Sciences Outlook. Driving Resiliency”, przygotowany przez firmę doradczą Deloitte, wskazuje, że branża life sciences – do której należy zaliczyć branżę biotechnologiczną, farmaceutyczną oraz ochrony zdrowia – będzie kontynuować działania zwiększające odporność na czynniki zewnętrzne oraz nawiązywać strategiczne partnerstwa technologiczne, aby przyspieszyć badania i rozwój. Większość przedsiębiorstw z tego sektora skupi się na wykorzystaniu potencjału generatywnej sztucznej inteligencji, wdrożeniu usprawnień w obsłudze i leczeniu pacjentów oraz dostosowaniu się do zmian regulacyjnych.
Specjaliści przewidują, że generatywna AI może być jedną z najbardziej przełomowych transformacji technologicznych ostatnich dekad. Już teraz ponad 90 % respondentów z branży biotechnologicznej i medycznej ankietowanych przez
Naukowcy z wydziałów Elektroniki Mikrosystemów Politechniki Wrocławskiej i Zespołu Fotoniki Instytutu Fizyki Politechniki Łódzkiej dokonali znaczącego odkrycia w dziedzinie fizyki laserowej. Zespół, w skład którego wchodzą m.in. dr hab. inż. Maciej Pieczarka, prof. Tomasz Czyszanowski, dr Marcin Gębski, dr hab. Michał Wasiak, oraz doktorantka Aleksandra Piasecka, skupił się w projekcie na laserze o innym niż zazwyczaj zestrojeniu spektralnym między długością fali obszaru aktywnego a długością fali rezonatora laserowego. – Badania przeprowadziliśmy na urządzeniu praktycznie nieróżniącym się od tych stosowanych obecnie w przemyśle, np. w smartfonach, w telekomunikacji itd. Obserwacja kondensacji
Deloitte spodziewa się, że generatywna sztuczna inteligencja będzie miała wpływ na ich organizacje, szczególnie w przypadku działań R&D. W połączeniu z innymi narzędziami transformacji cyfrowej, zwiększy ona ogólną efektywność i innowacyjność procesów. Usprawnienie działań będzie miało odzwierciedlenie w zyskach, a eksperci Deloitte oceniają, że przy wykorzystaniu narzędzi AI firmy biotechnologiczne o średnich przychodach w wysokości 65–75 mld dolarów mogą zwiększyć swoją wartość o 5–7 mld dolarów w ciągu najbliższych pięciu lat.
Źródło: Deloitte, foto: pixabay
Bosego-Einsteina światła w takim urządzeniu jest nowym spojrzeniem na zasady działania laserów półprzewodnikowych – podkreśla dr Maciej Pieczarka.
To odkr ycie otwiera nowe możliwości w nauce, umożliwiając badania nad procesami zachodzącymi w niezwykle krótkich skalach czasowych, co wcześniej było trudne do osiągnięcia. Odkrycie naukowców z Politechniki Wrocławskiej nie tylko umacnia pozycję uczelni na arenie międzynarodowej, ale również ma potencjał, aby zrewolucjonizować wiele dziedzin technologii opartej na zaawansowanych technologiach laserowych.
Źródło: Evertiq.pl
Firma Universal Robots przeprowadziła ankietę wśród 1200 producentów w Amer yce Północnej i Europie, pytając o to, w jaki sposób wykorzystują technologię i jakie inwestycje planują w przyszłości. 50 % ankietowanych zadeklarowało, że wykorzystuje sztuczną inteligencję i uczenie maszynowe w swojej produkcji. – Chociaż stały się one powszechnym tematem rozmów dopiero w ciągu ostatnich dwóch lat, obecnie są kluczowymi czynnikami napędzającymi innowacje i wydajność produkcji – mówi Anders Billesø Beck, wiceprezes ds. strategii i innowacji w Universal Robots. Technologie te będą nadal odgrywać kluczową rolę w przyszłości produkcji, na co wskazuje 48 % producentów planu-
jących dalsze inwestycje w sztuczną inteligencję i uczenie maszynowe do 2025 r. – Obserwujemy duże zainteresowanie fizyczną sztuczną inteligencją. Nasz ekosystem UR+ stale się rozwija, a kluczowym czynnikiem napędzającym ten proces jest szybki wzrost liczby aplikacji i rozwiązań AI pochodzących od naszych partnerów, w tym rosnącej liczby partnerów OEM – dodaje Anders Billesø Beck.
Badanie pokazuje rosnące znaczenie cyfryzacji, ponieważ 47 % producentów korzysta obecnie z takich technologii, jak Internet Rzeczy, przetwarzanie w chmurze i cyfrowe bliźniaki. Ponad 50 % respondentów wskazuje poprawę jakości produktów, zwiększenie produktywności i dokładność jako główne powody przyjęcia nowych technologii. Źródło: Universal Robots
Logistyka paliw płynnych to wymagający segment branży paliwowej. W tak kluczowym dla gospodarki sektorze niezwykle istotna jest stała analiza trendów i wymiana doświadczeń eksperckich. Miejscem ku temu będzie Konferencja Logistyka Paliw Płynnych. Wydarzenie, organizowane przez firmy Endress+Hauser oraz Merrid Controls pod patronatem naukowym Wydziału Mechaniczno-Energetycznego Politechniki Wrocławskiej, odbędzie się w dniach 23–24 października 2024 r. w Uniejowie. Tematyka konferencji obejmie kluczowe aspekty technologiczne, operacyjne i społeczne logistyki paliw płynnych, takie jak obecna geopolityka surowców energetycznych, zaawansowane metody monitorowania i zarządzania stanami magazynowymi, nowoczesne systemy automatyki czy cyfryzacja procesów logistycznych.
Źródło: Endress+Hauser Polska
Dr Sebastian Durst objął stanowisko prezesa Weidmüller. Firma wprowadziła także inne zmiany w zarządzie.
Dr Christian von Toll, wcześniej odpowiedzialny za sprzedaż w regionie Niemcy/Szwajcaria/Austria, objął stanowisko członka zarządu ds. sprzedaży. Dr T imo Berger, dotychczas odpowiadający za kwestie sprzedażowe, a wcześniej pełniący także różne funkcje związane z kwestiami technologicznymi, przejął rolę członka zarządu ds. technologii. Będzie odpowiedzialny za rozwój produktów i rozwiązań. Na stanowisku członka zarządu ds. finansowych pozostanie André Sombecki. Reorganizacja zarządu ma pomóc Grupie Weidmüller skoncentrować się na przyszłych wyzwaniach i konsekwentnej realizacji strategii wzrostu.
Źródło: Weidmüller
Poznaj europejskie partnerstwa i dowiedz się jak uzyskać unijne środki na realizację projektów B+R w Przemyśle 4.0 w ramach programu Horyzont Europa.
Poznaj europejskie partnerstwa i dowiedz się jak uzyskać unijne środki na realizację projektów B+R w Przemyśle 4.0 w ramach programu Horyzont Europa.
Do naszych głównych aktywności należą:
✔ pomoc w pozyskaniu europejskich partnerów i źródeł finansowania dla wspólnych projektów, ✔ reprezentowanie polskich podmiotów na forum międzynarodowym, ✔organizowanie szkoleń, warsztatów i sesji networkingowych, ✔ prowadzenie indywidualnych konsultacji
Do naszych głównych aktywności należą: ✔ pomoc w pozyskaniu europejskich partnerów i źródeł finansowania dla wspólnych projektów, ✔ reprezentowanie polskich podmiotów na forum międzynarodowym, ✔organizowanie szkoleń, warsztatów i sesji networkingowych, ✔ prowadzenie indywidualnych konsultacji
Naszą ofertę kierujemy do firm działających w obszarach:
✔ technologie produkcji
✔ sztuczna inteligencja
✔ przetwarzanie w chmurze
✔ fotonika
✔ inteligentne sieci i usługi
Naszą ofertę kierujemy do firm działających w obszarach: ✔ technologie produkcji ✔ sztuczna inteligencja ✔ przetwarzanie w chmurze ✔ fotonika inteligentne sieci i usługi
Kto może skorzystać z naszego wsparcia? przedsiębiorstwa, startupy, uczelnie wyższe, jednostki naukowe, fundacje, stowarzyszenia, klastry oraz organizacje międzynarodowe.
Kto może skorzystać z naszego wsparcia? przedsiębiorstwa, startupy, uczelnie wyższe, jednostki naukowe, fundacje, stowarzyszenia, klastry oraz organizacje międzynarodowe.
Kontakt: mail: bpkprzemysl@piap.lukasiewicz.gov.pl telefon: 22 874 01 35
Kontakt: bpkprzemysl@piap.lukasiewicz.gov.pl elefon: 22 874 01 35
Firma Bosch Rexroth połączyła konwerter protokołów Anybus Communicator ze Smart Flex Effector, udostępniając globalnej branży produkcyjnej najbardziej wszechstronny moduł kompensacyjny automatyki przemysłowej. – Roboty są zwykle wyposażone w jakieś narzędzie, np. chwytak. Moduł kompensacyjny to część umiejscawiana między ramieniem robota a chwytakiem. Smart Flex Effector wyróżnia się możliwością zapewnienia czułości – elastyczności w odpowiedzi na działające siły – w sześciu stopniach swobody podczas ruchu w przestrzeni trójwymiarowej – mówi David Lehmann, architekt systemów w firmie Bosch Rexroth.
Celem w przypadku tego produktu jest umożliwienie robotom wykonywania nowych zadań, w których do tej pory nie sprawdzały się najlepiej.
Moduł Smart Flex Effector i Anybus Communicator współpracowały ze sobą tak dobrze, że firma Bosch Rexroth dołączyła do oferty konwerter Anybus jako część kompletnego rozwiązania. – Postanowiliśmy stworzyć numer zamówienia dla konwertera Anybus, aby klienci mogli go kupić bezpośrednio u nas i sprzedajemy oba urządzenia razem jako kompletne rozwiązanie – podsumowuje David Lehmann. Źródło: Bosch Rexroth
Największe centra danych konsumują w ciągu roku tyle energii elektrycznej, co 80 000 gospodarstw domowych. Jak wynika z raportu McKinsey, do 2030 r. jej zużycie przez dostawców tego typu usług osiągnie 35 GW, w porównaniu z 17 GW w 2022 r. Tak ogromne zapotrzebowanie wynika m.in. z tego, że wdrażanych jest coraz więcej rozwiązań bazujących na sztucznej inteligencji. Umożliwiają one klientom centrów danych świadczenie nowatorskich usług, ale pomagają też w utrzymywaniu tego typu placówek –zapewniają optymalizację i automatyzację zarządzania danymi oraz zasilaniem, a także pozwalają na stworzenie inteligentnego
systemu sterowania klimatyzacją infrastruktury. Jednak w kontekście zrównoważonego rozwoju energetycznego i ochrony środowiska należy korzystać z AI w odpowiedni sposób. Co prawda największe usługi generatywnej sztucznej inteligencji, jak ChatGPT, Dall-E, Midjourney czy Gemini, obsługiwane są przez gigantyczne centra danych, ale coraz więcej firm korzysta z mniejszych mechanizmów sztucznej inteligencji na własne potrzeby i wdraża je w lokalnych centrach danych.
Algorytmy sztucznej inteligencji potrzebują ogromnej mocy obliczeniowej, co przekłada się również na większy popyt na energię. Eksperci prognozują, że w ciągu najbliższych kilkunastu lat obciążenie energetyczne związane z użyciem AI w centrach danych wzrośnie dwukrotnie.
Źródło: Vertiv
POLSKI ASTRONAUTA PROJEKTOWY POLECI
Firma Axiom Space poinformowała o nawiązaniu współpracy z Indiami, Węgrami oraz z Polską za pośrednictwem Europejskiej Agencji Kosmicznej w celu wysłania astronautów z tych krajów na Międzynarodową Stację Kosmiczną w ramach misji Axiom 4 (Ax-4). Sławosz Uznański, astronauta projektowy ESA, został mianowany specjalistą misji pod dowództwem Peggy Whitson, doświadczonej astronautki Axiom Space. Pozostali dwaj członkowie załogi Ax-4 to pilot Shubhanshu Shukla z Indii oraz specjalista misji Tibor Kapu z Węgier. Załoga oczekuje na zatwierdzenie Wielostronnego Panelu Operacji Załogowych (Multilateral Crew Operations Panel, MCOP). MCOP podejmuje decyzje na zasadzie konsensusu przedstawicieli wszystkich pięciu partnerów Międzynarodowej Stacji Kosmicznej. Są to: NASA, ESA, Roskosmos, JAXA i Kanadyjska Agencja Kosmiczna.
Ax-4 będzie drugą komercyjną załogową misją kosmiczną z udziałem astronauty projektowego ESA. Misja obejmuje ambitny program technologiczny i naukowy. Jest sponsorowana przez polski rząd, i wspierana przez ESA, Ministerstwo Rozwoju i Technologii (MRiT) oraz Polską Agencję Kosmiczną (POLSA). W ramach programu przeprowadzone zostaną eksperymenty zaproponowane przez polski przemysł kosmiczny i opracowane pod przewodnictwem ESA.
Źródło: Europejska Agencja Kosmiczna
Firma Schneider Electric otrzymała od HMS Networks nagrodę 10-milionowego modułu Anybus. Schneider Electric, integrując interfejsy łączności sieciowej Anybus ze swoją linią napędów o zmiennej prędkości (przemienników częstotliwości), zapewnia klientom różnorodną gamę napędów, które można precyzyjnie dostroić zarówno w zakresie wydajności, jak i efektywności energetycznej. To optymalizuje procesy klientów i ogranicza negatywny wpływ na środowisko naturalne. Ceremonia wręczenia nagród odbyła się w siedzibie Schneider Electric w Paryżu. Na uroczystości byli obecni Magnus Jansson, dyrektor ds. marketingu produktów w HMS Networks, Jean-Louis Guillou, wiceprezes ds. napędów w Schneider Electric i Peter Greenfort, menedżer ds. klientów strategicznych w HMS Networks.
Źródło: Schneider Electric
SUNEX i Nar odowe
Centrum Badań i Rozwoju podpisały umowę na dofinansowanie projektu autorskiej technologii wytwarzania i wdrożenia kompozytowych zbiorników CWU w instalacjach grzewczych opartych na OZE. – Zmierzamy do wprowadzenia na r ynek nowej generacji zasobników – lżejszych, trwalszych i bardziej efektywnych ekonomicznie niż masowo stosowane na rynku zasobniki stalowe. Opracowywana technologia jest odpowiedzią na rosnące społeczne i rynkowe zapotrzebowanie na rozwiązania materiałooszczędne. Cieszy nas, że NCBiR powtórnie wspiera zrównoważone projekty SUNEX – mówi Romuald Kalyciok, prezes SUNEX. Produkt znajdzie zastosowanie w instalacjach grzewczych opartych na odnawialnych źródłach energii – w ciepłownictwie, energetyce, budownictwie mieszkaniowym i gospodarczym.
Projekt SUNEX, prowadzony przez zespół B+R, będzie realizowany do 2025 r. Później nowe rozwiązanie trafi na rynek.
Źródło: Sunex
W dniach 22–24 października 2024 r. Katowice staną się centrum wymiany wiedzy na temat zarządzania Lean. IX Europejski Kongres Lean Management zgromadzi ekspertów, praktyków i liderów branży, którzy przedstawią najnowsze trendy, case study oraz doświadczenia w zakresie transformacji Lean.
Kongres rozpocznie się mocnym akcentem. Eksperci m.in. z Leroy Merlin, Cedrob Foods i Mercedes-Benz Manufacturing Poland podzielą się swoimi doświadczeniami z transformacji Lean. Kluczowe tematy będą obejmować automatyzację procesów, zarządzanie zmianą oraz shop floor management. Dzień dopełnią panele dyskusyjne na temat roli IT w Lean oraz wpływu robotyzacji i AI na przemysł. Nie zabraknie również paneli
dyskusyjnych, które umożliwią wymianę doświadczeń między uczestnikami. Elementem wydarzenia są wizyty studyjne, które mają na celu pokazanie praktycznych aspektów transformacji Lean, jak również umożliwienie bezpośredniego wglądu w realne procesy produkcyjne i logistyczne. Uczestnicy będą mogli zobaczyć, jak firmy Mercedes-Benz Manufacturing Poland, Ficomirrors Polska, Cedrob Foods oraz Filters International stosują zasady Lean do optymalizacji swoich operacji, co pozwala im na osiąganie wyższej efektywności oraz redukcję kosztów. Więcej informacji oraz pełny program Kongresu dostępne są na stronie www.kongreslean.pl.
Źródło: Brainstorm Group
Przeprowadzone przez pracownię Kantar badania pokazały, że klienci
Endress+Hauser Polska bardzo wysoko oceniają współpracę z firmą.
Aż 93 % z nich uważa ją za godnego zaufania partnera biznesowego w perspektywie długoletniej kooperacji. Wyniki przeprowadzonego badania są dla Endress+Hauser potwierdzeniem skuteczności podejścia Customer Centric w relacjach z odbiorcami.
Do udziału w wiosennym badaniu ankietowym zaproszonych zostało kilkadziesiąt tysięcy polskich klientów lokalnego oddziału Endress+Hauser. Ich odpowiedzi posłużyły do przygotowania podsumowania, w którym znalazły się wyniki
przedstawione m.in. za pomocą stosowanego przez Kantar indeksu TRI*M. Jest to wyrażona liczbą miara zadowolenia i przywiązania klienta, która w przypadku Endress+Hauser Polska wyniosła 86 pkt w skali od –50 do 150. Z kolei wskaźnik NPS, za pomocą którego bada się poziom lojalności klientów, osiągnął poziom 60 pkt w skali od –100 pkt do 100 pkt, a 67 % respondentów to tzw. „promotorzy marki”, polecający jej produkty i usługi innym.
Wśród aspektów, które mają największy wpływ na tak dobrą ocenę Endress+Hauser u klientów znalazły się jakość produktów, doświadczenie w branżach przemysłu, partnerska postawa wobec klientów oraz szerokie portfolio produktów. 82 % klientów pozytywnie oceniło usługi serwisowe i wsparcie posprzedażowe.
Źródło: Endress+Hauser Polska
Położona w prowincji Banten, godzinę jazdy od Dżakarty, tama Karian jest przykładem zaangażowania Indonezji w zarządzanie zasobami wodnymi. Obszar tamy obejmuje ponad 2200 ha, co pozwala na zebranie do 314,7 mln m3 wody. Pozwala to przykładowo nawadniać 22 000 ha pól ryżowych, dostarczając 13,9 m³ wody na sekundę, również do potrzeb publicznych i przemysłowych. Tama Karian jest kluczową infrastrukturą dla tego obszaru.
Jednym z głównych wyzwań, z jakimi przyszło się zmierzyć podczas realizacji projektu zapory, była potrzeba gromadzenia dużej ilości danych. Firma inżynieryjna wybrała platformę PcVue ze względu na jej przyjazność dla użytkownika i elastyczność. – PcVue była łatwiejsza w obsłudze od innych produktów – mówi Pan Satrio, dyrektor w PT Sartika Mitrasejati, podkreślając intuicyjność interfejsu oprogra-
mowania i nowoczesne funkcje. Oprogramowanie PcVue pozwala zespołowi nadzorować przepływ wody w tamie i integrować wiele podsystemów w ramach jednej platformy. Prawdziwym wyzwaniem było zebranie danych. Elastyczność i skalowalność PcVue były kluczowe w r ozwiązaniu tego problemu. Platforma PcVue została połączona z innymi systemami, co poprawiło wydajność operacyjną zapory, ponieważ dostarcza ona operatorowi skonsolidowaną platformę informacyjną.
Źródło: PcVue
DLA STWORZENIA NOWEJ GENERACJI AKUMULATORÓW
W ramach wspólnego projektu badawczego COOLBat naukowcy z Instytutu Obrabiarek i Technologii Formowania im. Fraunhofera IWU połączyli siły z partnerami, aby opracować obudowy akumulatorów nowej generacji do pojazdów elektrycznych. Celem jest zmniejszenie masy obudów, głównego elementu każdego pojazdu elektrycznego oraz zmniejszenie o 15 % emisji dwutlenku węgla podczas ich produkcji. Partnerzy projektu chcą to osiągnąć przez łączenie poszczególnych systemów, „upakowanie” większej liczby funkcji na mniejszej przestrzeni instalacyjnej oraz zastosowanie nowych materiałów przewodzących ciepło i powłok zmniejszających palność na bazie biologicznej.
Zidentyfikowanym przez badaczy sposobem potencjalnego zmniejszenia masy jest połączenie w obudowie poszczególnych systemów, które wcześniej oddzielnie pełniły funkcje termiczne i mechaniczne.
Źródło: Instytut Fraunhofera
AMAZON URUCHOMIŁ
KOLEJNE CENTRUM
LOGISTYCZNE W POLSCE
Firma Amazon, świętująca 10-lecie działalności w Polsce, otworzyła w Gorzyczkach 11. centrum logistyczne w naszym kraju i trzecie w woje wództwie śląskim. W ciągu pierwszego roku od uruchomienia obiekt ma zapewnić ponad 1000 stałych miejsc pracy.
Gorzyczki to znacząca lokalizacja w regionie. Miejscowość leży przy granicy z Czechami i dzięki autostradzie A1 tworzy ważny węzeł komunikacyjny z północno-zachodnią częścią kraju. Lokalizacja nowego centrum logistycznego pozwala na efektywne zarządzanie naszą siecią transportową – odległości pomiędzy poszczególnymi obiektami nie przekraczają trzech godzin jazdy, co umożliwia szybką i sprawną obsługę zamówień. Co więcej – do centrum przynależy zintegrowany plac manewrowy oraz parking dla 82 ciężarówek, co czyni go pier wszym budynkiem Amazon w Europie o tak dużym potencjale logistycznym.
Obiekt w Gorzyczkach zajmuje się głównie zamówieniami typu „non sortable”, czyli produktami wielkogabarytowymi i niestandardowymi.
Źródło: Amazon
Comarch od lat należy do liderów sprzedaży systemów ERP (Enterprise Resource Planning) w Polsce. Firma nie tylko jest w czołówce, ale też regularnie zwiększa udział w rynku. Według najnowszego raportu IDC „Poland Enterprise Application Software Market Analysis and 2023 Vendor Shares” udział Comarch to już 24,3 % (przed rokiem 23,6 %). Przekłada się to na przychody rzędu 95,03 mln dolarów (75,84 mln dolarów rok wcześniej). Autorzy raportu szacują wartość całego rynku na 391,84 mln dolarów. Jako najważniejsze czynniki napędzające zmiany na r ynku ERP w Polsce wskazano zmianę podejścia firm do aplikacji (przedsiębiorstwa coraz chętniej zmieniają przestarzałe aplikacje on-premise na rozwiązania chmurowe), dynamiczne zmiany w prawodawstwie, generatywna sztuczna inteligencja oraz wzrost gospodarczy i ożywienie na r ynku. To ważne wskaźniki dla firm, które będą inwestować coraz mocniej w nowoczesne rozwiązania informatyczne do zarządzania procesami, by zwiększyć efektywność i automatyzację.
Rynek ERP zmaga się jednak również z wyzwaniami, takimi jak rosnące koszty prowadzenia działalności (m.in. koszty pracy, energii). To z kolei wpływa na zdolności rozwojowe organizacji. Część z nich ze względu na koszty może chcieć pozostać przy użytkowaniu dotychczasowych aplikacji, zamiast inwestować w ich modernizację lub nowe produkty. Źródło: Comarch
Tablet RTC-1010RK firmy AAEON stanowi odpowiedź na potrzeby nowoczesnych przedsiębiorstw. Łącząc platformę Rockchip RK3399 z systemem operacyjnym Android 11, nowy tablet RTC-1010RK umożliwia dynamiczne przetwarzanie i lepsze dostosowanie interfejsu użytkownika do sprzętu o wytrzymałości wojskowej.
RTC-1010RK to tablet stworzony z myślą o trudnych warunkach przemysłowych. Wyposażony w procesor Rockchip RK3399 gwarantuje szybką i niezakłóconą pracę. Co więcej RTC-1010RK korzysta z połączenia czterordzeniowego procesora Arm Cortex-A53 z dwurdzeniowym procesorem Arm Cortex-A72 do przetwarzania równoległego i zoptymalizowanej wielowątkowości oraz 2/4 GB wbudowanej pamięci LPDDR4, a także do 64 GB eMMC.
RTC-1010RK to pierwszy wytrzymały tablet firmy AAEON o przekątnej 10,1”, obsługujący system operacyjny Android.
Kolektor danych Sunmi L2Ks to narzędzie skanujące, które znajduje zastosowanie w wielu branżach. Funkcjonalne urządzenie sprawdzi się przede wszystkim w magazynowaniu, logistyce i tych sektorach, gdzie skuteczne i szybkie przechwytywanie danych jest podstawą optymalnego działania. Wbudowana bateria o pojemności 5000 mAh daje duży komfort użytkowania bez obawy o konieczność doładowywania kolektora w trakcie pracy. Lekka i ergonomiczna konstrukcja zapewnia wygodę a stopień szczelności IP68 zabezpiecza przed działaniem wody oraz kurzu. Duża wytrzymałość pozwala na stosowanie w wymagających środowiskach magazynowych i logistycznych. Kolektor jest odporny na upadki z wysokości 1,8 m.
Udostępnia narzędzia typu open source, za pomocą których można dostosować interfejs i wbudowane aplikacje do konkretnych wymagań użytkownika. Dzięki obsłudze systemu Android 11, tablet wprowadza kolejne zabezpieczenia, jak jednorazowe uprawnienia, ograniczony zakres przechowywania i ulepszone uwierzytelnianie biometryczne. Dzięki temu nadaje się do utrzymywania integralności środowisk zarządzania zapasami, ochrony danych czy kontroli. Dotykowy wyświetlacz TFT WXGA o rozdzielczości 1280 px × 800 px i jasności 800 lub 300 nitów zapewnia doskonałą czytelność w każdych warunkach oświetleniowych. Jest to istotny element, zwłaszcza w środowiskach, w których liczy się każdy detal.
Źródło: CSI
L2Ks działa w oparciu o system operacyjny Android 11, ma ośmiordzeniowy procesor oraz pamięć do 4 GB RAM i 32 GB ROM. Dodatkowe funkcje odczytu zapewniają dwa aparaty: z tyłu urządzenia (13 Mpx) oraz na froncie obudowy (5 Mpx).
Kolektor został wyposażony w baterię ATL o dużej pojemności, która daje swobodę działania na wiele godzin. System zarządzania baterią SUNMI chroni ogniwo przed przeładowaniem, dzięki czemu L2Ks są bezpieczne i niezawodne w użyciu. Ekran LCD o wysokiej jasności (do 650 nitów) umożliwia dobr y podgląd danych i komfort obsługi urządzenia, nawet w bezpośrednim świetle słonecznym.
Źródło: Koncept-L S.A.
Firma FAULHABER oferuje silniki bezszczotkowe z serii 22xx...BX4 z miniaturowym kontrolerem ruchu 22xx…
BX4 IMC. Całość obejmuje kontroler ser womotoru ze wszystkimi niezbędnymi funkcjami oraz 12-bitowy enkoder. Komponent zwiększa całkowitą długość silnika o około 18 mm i występuje w wersji z interfejsem RS-232 lub CANopen. Kontroler zapewnia pełną zgodność ze standardem serwonapędów CiA 402, co umożliwia bezpośrednią obsługę z typowych sterowników PLC. Niemniej jednak, nawet przy użyciu wersji z interfejsem RS-232, można sterować kilkoma
napędami za pomocą jednego portu urządzenia. Typowe zadania, takie jak pozycjonowanie, mogą być wykonywane bezpośrednio przez zintegrowany kontroler za pomocą lokalnych wejść/wyjść cyfrowych i analogowych.
Obie wersje kontrolera mogą być obsługiwane bez urządzenia nadrzędnego (pracować w trybie autonomicznym). Cyfrowe i analogowe linie I/O służą w tym wypadku do lokalnych zadań sterowania. Dodatkowo kontroler 22xx…BX4 IMC może być łączony z wieloma produktami firmy, jak przekładnie GPT i siłowniki liniowe FAULHABER 22L. Zawiera zabezpieczenie przeciążeniowe i wbudowane funkcje diagnostyczne. Może pracować w trybie sterowania momentem obrotowym, prędkością lub położeniem.
Źródło: FAULHABER
Wpisując się w trend ograniczania emisji CO2 i integrowania surowców odnawialnych, firma igus zaprezentowała na Targach Hanowerskich nowe łożysko wieńcowe iglidur PRT, wykonane z kompozytu WPC (Wood Plastic Composites), łączącego w 50 % drewno i w 50 % polimery. Jego zaletą jest duża wytrzymałość mechaniczna i trwałość oraz przyjazny dla środowiska proces produkcyjny. Łożysko jest produkowane w technice formowania wtr yskowego. Zawiera smar y stałe, zapewniające płynną pracę, bez konieczności smarowania i konserwacji. Zawartość
drewna nadaje całości naturalny wygląd. Zarówno oprawa, jak i sam komponent, zostały wykonane z kompozytu WPC, a do połączenia obu sekcji potrzebne są tylko cztery śruby. Łożysko iglidur PRT charakteryzuje się solidną konstrukcją, spełniającą wymogi wielu aplikacji. Jego ważną cechą jest wyjątkowo niski ślad CO2, wynoszący zaledwie 0,0577 kg. Dla porównania, model PRT-02-30-ECO, wykonany w 97 % z regranulatu, charakteryzuje się ekwiwalentem CO2, wynoszącym 0,819868 kg. Testy wytrzymałościowe, przeprowadzone w wewnętrznym laboratorium firmy igus, potwierdziły wysoką jakość i dużą niezawodność produktu w różnych warunkach pracy.
Źródło: igus
Inteligentny czujnik fotoelektryczny serii BOS R254K dedykowany jest wymagającym aplikacjom, np. w przemyśle spożywczym i sektorze opakowań. Nowa seria czujników wpisuje się w kompleksową filozofię automatyzacji firmy Balluff oznaczoną skrótem SAMS (Smart Automation and Monitoring System). Ten inteligentny system automatyzacji i monitorowania obejmuje jednolitą i ustandaryzowaną koncepcję obsługi, konfiguracji i diagnostyki, oferując szeroki zakres dodatkowych funkcji i dodatkowych informacji o poszczególnych komponentach.
Czujnik optoelektroniczny BOS R254K to urządzenie, które można wykorzystać do wymagających zastosowań, szczególnie tam gdzie regularnie przeprowadza się czyszczenie za pomocą agresywnych środków i wysokiego ciśnienia. Spełniając standardy Ecolab w zakresie odporności na agresywne środki czyszczące, wilgoć, silne wibracje oraz cykle czyszczenia, Balluff BOS R254K umożliwia zastosowanie w krytycznych aplikacjach o trudnych warunkach otoczenia, również dzięki zapewnieniu stopni ochrony IP67 i IP69K.
Wieloletni Partner Grupy CP Trade firma Weidmüller wprowadza na rynek nową linię niezarządzalnych switchy z technologią Single Pair Ethernet (SPE), znacząco podnoszących wydajność aplikacji przemysłowych. Technologia ta oferuje niezrównaną długość zasięgu i jednoczesną transmisję danych oraz energii.
Technologia SPE umożliwia transmisję na odległość nawet 1000 m, zachowując przy tym wysoką wydajność. Switch Weidmüller 10Base-T1L SPE osiąga przepustowość 10 Mbit/s, co jest znacznym wzrostem w porównaniu ze standardem RS-485 na podobnych dystansach. To sprawia, że SPE to niezawodne i wydajne rozwiązanie do zastosowań przemysłowych, jak np do połączeń z czujnikami.
Nowa seria BOS R254K wyposażona w interfejs IO-Link nie tylko precyzyjnie rejestruje butelki, pojemniki i palety, ale charakteryzuje się licznymi dodatkowymi funkcjami, które gwarantują zaawansowane wykr ywanie obiektów szczególnie szybkich procesów, dużych zasięgów i przezroczystych obiektów. BOS R254K oferuje funkcje czasu i zliczania, dynamiczną zmianę progu przełączania, monitorowania stanu, pomiar temperatury własnej oraz otoczenia, wilgotności, wibracji, nachylenia, zanieczyszczenia lub rezerwę funkcji, dostarczając pomocnych danych diagnostycznych o potencjalnych ekstremach. Resumując, czujnik umożliwia dostarczanie pomocnych danych diagnostycznych dzięki funkcji samokontroli, uzyskując cenne informacje o aplikacji i miejscu użytkowania, co można wykorzystać do zwiększenia dostępności aplikacji, a finalnie zapewni to dłuższe działanie samego sprzętu.
Źródło: Balluff
Jedną z najważniejszych cech switcha 10Base-T1L SPE jest wsparcie dla technologii Power over Data Line (PoDL) do klasy 15, która pozwala na zasilanie urządzenia końcowego do 50 W. Dzięki temu, zarówno dane, jak i zasilanie mogą być przesyłane za pomocą jednego przewodu.
Switch 10Base-T1L SPE firmy Weidmüller spełnia wymagania klasy zgodności z Profinet A. Funkcja Quality of Service (QoS) umożliwia efektywne zarządzanie zasobami sieciowymi i priorytetyzowanie ruchu danych. Pozwala to użytkownikom optymalnie wykorzystywać dostępne pasmo i zapewniać płynne działanie kluczowych aplikacji.
Źródło: Weidmüller
Firma Schmersal zaprezentowała najmniejszą blokadę elektromagnetyczną AZM40, która oferuje teraz jeszcze bardziej wszechstronne możliwości zastosowania. Blokada AZM40 jest znana ze swoich niezwykle kompaktowych wymiarów (119,5 mm × 40 mm × 20 mm), jak również dużej osiąganej siły blokowania 2000 N, która predysponuje to urządzenie nie tylko do lekkich i ograniczonych przestrzeni montażowych.
Nowe wersje blokady elektromagnetycznej AZM40 mogą być również rozszerzone o funkcje odblokowania awaryjnego lub wyjścia awaryjnego, ponadto nowe typy dostępne są w wersji z dźwignią lub przyciskiem. Zarówno wersje z dźwignią, jak i z przyciskiem są dostępne jako odblokowanie ewakuacyjne lub odblokowanie awaryjne, przy czym wersja z przyciskiem jest tak zaprojektowana, że sam przycisk charakteryzuje się dużym podobieństwem do znanego wszystkim
przycisku zatrzymania awaryjnego, przez co jego awaryjne użycie nasuwa się samoistnie.
Praca w zakresie temperatury od -20 °C do +55 °C oraz stopień ochrony IP69 poszerzają możliwości zastosowania blokad. Nie sposób nie wspomnieć o wydłużonej żywotności, która zapewnia 500 000 cykli przełączania w cyklu siłownika oraz 1 000 000 cykli przełączania w cyklu blokady, a zasada bistabilnej blokady pozwala na znaczne obniżenie zużycia energii, nawet o 50 % w stosunku do monostabilnych blokad elektromagnetycznych.
AZM40 ma elastyczność kątową 180°, która sprawia, że siłownik może zbliżać się do blokady w sposób ciągły Takie rozwiązanie umożliwia stosowanie AZM40 w klapach, które nie zamykają się pod kątem 90° lub otwierają się do góry pod kątem 45°.
Źródło: Schmersal
W odpowiedzi na systematycznie rosnące zapotrzebowanie na wytrzymałe czujniki działające niezawodnie w trudnych warunkach pracy, firma Baumer wprowadziła na rynek czujnik ultradźwiękowy UF401V Zaprojektowany specjalnie z myślą o maszynach mobilnych wyróżnia się niezrównaną trwałością i precyzją. Stopień ochrony IP68/IP69K zapewnia maksymalną niezawodność nawet w najtrudniejszych warunkach.
Dzięki zgodności z normami ISO 14982, EN 13309, ISO 13766, ISO 15003, EN 60947-5-2/-5-7, UF401V oszczędza producentom OEM konieczność przeprowadzania skompli kowanych testów żywotności, skracając czas wprowadzania swoich produktów na rynek. UF401V ma specjalistyczną funk cję kompensacji zakłóceń, która tłumi zakłócenia w pomiarze
Firma Leuze przedstawiła nowe czujniki indukcyjne serii IS 200MM.2 o większym zasięgu działania.
Czujniki dos tępne w cylindrycznych obudo wach o wymiarach M12, i M30, wykonanych z trwałego niklowanego mosiądzu. ducent oferuje dwa różne warianty montażu: do instalacji quasi-zabudowanej i niezabudowanej, które odpowiadają na zróżnicowane potrzeby użytkowników. Dzięki tej styczności czujniki można z łatwością dostosować do nych aplikacji przemysłowych – od wykrywania ruchomych części maszyn, po monitorowanie narzędzi oraz różnych materiałów, takich jak stal, aluminium czy stal nierdzewna.
odległości, zapewniając spójne dane pomiarowe, nawet w przypadku krótkich przerw spowodowanych przez rośliny wchodzące
GENETEC ROZSZERZA
OFERTĘ KONTROLI DOSTĘPU
O BEZPIECZNY MODUŁ
I/O STID
Genetec Inc. ogłosił wpr owadzenie do swojego portfolio systemów k ontroli dostępu modułu
I/O o wysokim poziomie bezpieczeństwa. Nowy moduł I/O umożliwia europejskim klientom spełnienie najbardziej r ygorystycznych przepisów z zakresu cyberbezpieczeństwa.
System kontroli dostępu Genetec w połączeniu z modułem STid I/O jest idealny dla instytucji rządowych, branż wymagających wysokiego poziomu bezpieczeństwa, usług kluczowych, takich jak sektor wydobywczy i paliwowy, bankowość, usługi komunalne, produkcja oraz opieka zdrowotna. Oferuje bezpieczne zarządzanie punktami dostępu, zapewniając jednocześnie, że poufne informacje pozostaną w zabezpieczonym obszarze.
Moduł został tak zaprojektowany, aby jego wdrożenie było szybkie i łatwe.
Źródło: Genetec
Przekaźniki serii G9KC firmy Omron Components są polecane do zastosowań w stacjach ładowania Mode 3, falownikach i zasilaczach impulsowych. Na tle odpowiedników, wyróżniają się małą rezystancją kontaktu i małą emisją ciepła, co wydłuża ich czas bezawaryjnej pracy. Mogą pracować w przemysłowym zakresie temperatury otoczenia od -40 °C do 85 °C. Są odporne na udary mechaniczne do 25 g.
Przekaźniki serii G9KC występują w dwóch wersjach: 4PST-NO (4a) o napięciu znamionowym cewki 12 V DC oraz 4PST-NO (4a) + SPST-NC (1b) o napięciu znamionowym cewki 24 V DC. Są zamykane w obudowach o wymiarach 35 mm × 58 mm × 47 mm (W × L × H) i odstępie między kontaktami min. 3,6 mm. Zapewniają dużą odporność na zwarcie (zgodną z wymogami IEC 62955), izolację na poziomie 1000 MΩ oraz małą rezystancję kontaktu.
Źródło: Omron
Firma Balluff wprowadziła wieloczęstotliwościowy procesor RFID BIS V, pozwalający zintegrować rozwiązanie RFID z przemysłowym Internetem Rzeczy (IIoT). Wprowadzenie maszyn i systemów do IIoT to zadanie inteligentnych procesorów wykorzystujących powszechnie stosowany i znormalizowany interfejs komunikacyjny MQTT oraz protokół REST API. Interfejsy upraszczają wdrażanie i standaryzację, a zebrane dane są przesyłane do systemów wyższego poziomu. Do takich właśnie celów służy procesor RFID BIS V Do jego czterech portów można podłączyć głowice odczytu/zapisu (LF, HF, UHF), zapewniając maksymalną elastyczność aplikacji.
Dodatkowe urządzenia IO-Link można również podłączyć do zintegrowanego portu głównego IO-Link, z kolei dodatko-
we narzędzia UHF, takie jak filtry pętli do wstępnego przetwarzania i filtrowania danych lub PowerScan, pomagają w uruchomieniu i obsłudze aplikacji UHF. Szybka i intuicyjna konfiguracja odbywa się za pomocą graficznego interfejsu użytkownika w przeglądarce i interfejsu API REST. Możliwa jest funkcja tzw. „Sformatowany odczyt”, która umożliwia konwersję danych binarnych z nośnika danych do żądanego formatu, pozwalając na bezproblemową integrację z systemem MES lub ERP.
Źródło: Balluff
Czujnik wizyjny Inspector83x firmy SICK wykorzystuje sztuczną inteligencję do zadań kontroli w wymagających liniach pracujących z duża prędkością. AI odpowiada za funkcję uczenia kamery SICK Inspector83x, co przekłada się na proste, wydajne i precyzyjne do konfigurowania inspekcje, dostępne nawet dla niewykwalifikowanych operatorów.
SICK Inspector83x jako urządzenie all-in-one ma wydajne parametry, takie jak np rozdzielczość do 5 MP, wbudowane oświetlenie oraz czterordzeniowy procesor umożliwiający przetwarzanie inspekcji AI bezpośrednio na urządzeniu. Takie połączenie gwarantuje znacznie większą prędkość inspekcji względem poprzedników i nie straszne są mu złożone inspekcje średnich i dużych scen oraz nieprzewidywalne cechy i ich
złożone zespoły. Czujnik z łatwością radzi sobie także z odczytem i weryfikacją OCR/OCV.
W przypadku złożonych scen obejmujących duże zbior y danych i wiele przykładów, firma SICK umożliwia dostęp do usługi chmurowej o nazwie dStudio, udostępniając jej moc obliczeniową w celu trenowania własnej sieci neuronowej.
SICK Inspector83x jest zoptymalizowany do szybkiego przesyłania danych w sieciach przemysłowych z podwójnymi portami do integracji EtherNet/IP lub Profinet a dedykowany port Gigabit Ethernet umożliwia przesyłanie obrazów o wysokiej rozdzielczości oraz rejestrowania danych i integracji TCP/IP. Sumar ycznie czujnik ma siedem wejść i pięć wyjść, a dzięki wbudowanym funkcjom opóźnienia i kolejkowania precyzyjnie kalibruje wyjścia obrazu kamery w oparciu o czas lub wejścia enkodera.
Źródło: SICK
Firma Burkert ma w swoim porfolio dwudrogowy zawór proporcjonalny przeznaczony do integracji z urządzeniami medycznymi lub laboratoryjnymi.
Typ 2852, bo tak brzmi oficjalne oznaczenie tej serii zaworów, to urządzenia łączące w sobie takie cechy jak kompaktowe wymiar y, które mimo swojej wielkości umożliwiają przełączanie wysokiego ciśnienia roboczego przy jednoczesnym zapewnieniu względnie wysokiego natężenia przepływu, zachowując przy tym niewielkie straty. Zawór typu 2852 jest niezwykle oszczędny również dzięki niskiemu zużyciu energii. Kompaktowa konstrukcja o szerokości zaledwie 16 mm pozwala na instalację zaworu w urządzeniach, gdzie każdy centymetr jest niezwykle ważny, tak samo jak niewielkie nagrzewanie się samego zaworu. Szczególnie jest to istotne w aparaturze medycznej, takiej jak respiratory czy insuflatory. Taka apara-
tura musi być maksymalnie wydajna przy niewielkich wymiarach, a przy tym mobilna. Oczywiście zawór typu 2852 może być również używany w innych aplikacjach o podobnym zastosowaniu.
Zawór proporcjonalny typu 2852 z kompensacją ciśnienia może pracować przy ciśnieniu roboczym do 7 bar na wlocie zaworu i ma wysoki zakres nastaw (>1:500), zapewniając wartości kvs na poziomie 0,2 m³/h. W przypadku awarii zasilania zawór zamyka się automatycznie, eliminując w ten sposób potrzebę instalowania dodatkowego zaworu bezpieczeństwa.
Zawór typu 2852 udostępnia dwa rodzaje integracji mechanicznej i trzy różne typy połączeń elektrycznych (przewody, wtyczka i styki lutowane), które obsługują wszystkie dobre opcje integracji w systemach mechatronicznych.
Źródło: Burkert
Firma Hengstler zaprezentowała nowa wersję dobrze znanego, absolutnego enkodera obrotowego ACURO AD37. To zaawansowane urządzenie pomiarowe dedykowane precyzyjnie sterowanym standardowym silnikom serwo, zapewnia nie zrównaną precyzję i niezawodność odczytów pozycji, nawet przy wysokich prędkościach obrotowych. Od teraz dostępna jest wersja z wałem stożkowym 1:3 upraszczając integrację z jednostkami standardowymi. Enkoder ten został zaprojektowany z myślą o wymagających aplikacjach, w których dokładność i bezpieczeństwo są kluczowe, szczególnie w dynamicznych aplikacjach o krytycznym znaczeniu dla bezpieczeństwa.
Urządzenie wyróżnia się niezwykle precyzyjną i dynamiczną pracą oraz zdolnością do działania przy prędkościach do
12 000 obr./min. Dokładność wynosząca ±36 sekund kątowych i powtarzalność poniżej ±10 sekund kątowych umożliwiają osiągnięcie maksymalnej wydajności sterowania. ACURO AD37 firmy Hengstler oferuje rozdzielczość 20 bitów w trybie jednoobrotowym i 12 bitów w trybie wieloobrotowym. Takie parametry uzupełnione o dwukanałową redundantną konfigurację sprawiają, że enkoder jest certyfikowany zgodnie z SIL3 (kategoria PLe), co świadczy jednocześnie o jego niezawodności i bezpieczeństwie w aplikacjach krytycznych. Dodatkowo enkoder charakteryzuje się dobrą jakością sygnału, która zapewnia płynne sterowanie jednostkami napędowymi i bezstratną transmisję danych o pozycji i temperaturze z szybkością 10 Mbaud na odległość do 100 m. Źródło: Hengstler
Firma Pilz wprowadziła na rynek bezpieczny, modułowy system sterownia ruchem kolejowym PSSrail. Składa się ze sterownika spełniającego wymagania bezpieczeństwa do SIL4 oraz różnych modułów sprzętowych, takich jak moduł CAN do integracji istniejących systemów. Programowanie lub konfiguracja odbywa się za pomocą dołączonego pakietu oprogramowania, a certyfikowane przez kolej bloki funkcyjne są przechowywane w bibliotece programów zapewniając szybką implementację. Dzięki zasadzie bloków konstrukcyjnych użytkownicy mogą projektować swoje rozwiązania według własnych potrzeb, co wiąże się z faktem, że firma Pilz opracowała ten sterownik jako produkt gotowy do użycia prosto „z półki” czyli tzw. COTS (commercial off-the-shelf).
Now dyski SSD E1.S firmy ATP są zgodne ze standardem Ent erprise and Datacenter Standard Form Factor (EDSFF). Zostały zaprojektowane do serwerów 1U Edge. Charakteryzują się efektywnym wykorzystaniem przestrzeni oraz zaawansowanymi funkcjami i technologiami. Cechuje je duża pojemność (8TB), wydajność sekwencyjna odczytu/zapisu, 1 DWPD przez 5 lat zgodnie ze standardem JESD219A.
Dyski E1.S powstały z myślą o pracy w trudnych warunkach eksploatacyjnych, w tym w wysokiej temperaturze (od -40 °C do 85 °C), gwarantując ochronę przed utratą za-
System sterowania PSSrail jest kompatybilny z architekturą EULYNX, która koncentruje się na standaryzacji interfejsów i elementów systemów sygnalizacji w europejskiej branży kolejowej. PSSrail zapewnia rozwiązanie sterowania, które umożliwiają cyfryzację w trakcie pracy, dzięki temu operatorzy mogą np stopniowo modernizować przestarzałe blokady sterowane przekaźnikami. Konstrukcja PSSrail czyni go rozwiązaniem bardzo elastycznym, niezawodnym i ekonomicznym, umożliwiającym wdrażanie niezbędnych elementów modernizacji kolei europejskiej. Źródło: PILZ
silania sprzętowego (HW PLP), przez bezpieczne zapisanie danych na pamięci NAND flash.
Dyski SSD E1.S mają zwiększoną odporność na korozję. Specjalna konstrukcja umożliwia przepływ powietrza przez tylną płytę ser wera, zapewniając w ten sposób większą wydajność chłodzenia. Obsługują funkcję hot-plugging, umożliwiająca wymianę i konserwację bez przestojów.
Dyski są zgodne z TCG Opal 2.0, wyposażone w szyfrowanie AES 256-bit dla solidnej ochrony przed kradzieżą danych i manipulacjami. Opcjonalne funkcje samoszyfrujących dysków (SED) z protokołem uwierzytelniania dostępu IEEE 1667 zapewniają dodatkową warstwę zabezpieczeń, dzięki pełnemu szyfrowaniu dysku i ochronie dostępu. Źródło: CSI
Firma Genetec ogłosiła uruchomienie Operations Center, opartego na chmurze rozwiązania do zarządzania pracą. Operations Center został stworzony specjalnie z myślą o wspieraniu procesów operacyjnych w zakresie bezpieczeństwa technicznego. Nowe rozwiązanie, dostępne jako część Security Center SaaS lub jako samodzielny produkt. Powstało w celu usprawnienie współpracy, komunikacji i zarządzania zadaniami w zespołach odpowiedzialnych za bezpieczeństwo. Operations Center integruje funkcje centrum dowodzenia, zarządzania zgłoszeniami oraz monitorowania aktywności na jednej, spójnej platformie. Dzięki temu zunifikowanemu podejściu użytkownicy mogą skuteczniej zarządzać zadaniami, mieć pełną widoczność operacji w cza-
sie rzeczywistym i bezproblemowo współpracować w ramach zespołów.
Rozwiązanie dostarcza szczegółową listę kontrolną dla każdego zadania, co pomaga pracownikom ochrony w terenie w wykonywaniu różnorodnych zadań – od wysyłania patroli po reagowanie w miejscu zdarzenia.
System automatycznie informuje przełożonych o postępach, statusie i lokalizacji jednostek. Ponadto mogą oni przeprowadzać kontrolę oraz generować raporty dotyczące poszczególnych zdarzeń, całych zmian lub wydajności zespołu. Wszystkie działania są rejestrowane w czasie rzeczywistym, nawet poza siedzibą firmy.
Źródło: Genetec
Wraz z wprowadzeniem kamery AXIS Q1809-LE Bullet Camera firma Axis zaczyna realizować swój cel dostarczania produktów zgodnych ze standardem FIPS 140-3 Level 3 federalnych standardów przetwarzania informacji.
Standard FIPS 140-3 określa wymagania bezpieczeństwa dla modułów kr yptograficznych, które przetwarzają i zapewniają poufność oraz integralność danych. Poprawia to stan cyberbezpieczeństwa klientów, zwłaszcza w amerykańskich i kanadyjskich agencjach federalnych czy w sektorze infrastruktury kr ytycznej,
którzy muszą spełniać wymagania zgodności ze standardem FIPS 140-3.
Firma Axis jako pier wsza wprowadziła na rynek urządzenie zabezpieczające sieć z wbudowanym dyskretnym elementem zabezpieczającym, które zostało zwer yfikowane zgodnie z najnowocześniejszym standardem FIPS 140-3 Level 3.
Sprzęt został wyposażony w dyskretny element zabezpieczający – EdgeLock SE052F, firmy Półprzewodniki NXP, lidera w dziedzinie bezpiecznych rozwiązań łączności dla aplikacji wbudowanych.
W przyszłości firma Axis będzie nadal rozszerzać ofertę urządzeń zgodnych ze standardem FIPS 140-3 dla różnych zastosowań – od dozoru, przez optymalizację biznesową (dzięki analityce), po kontrolę dostępu i dźwięk.
Źródło: Axis
Nowy czujnik A2G-500 służy do pomiaru różnicy ciśnień, ciśnienia manometrycznego i podciśnienia w powietrzu, a także w nieagresywnych i niepalnych gazach w systemach wentylacyjnych i klimatyzacyjnych.
Piezorezystancyjny element pomiarowy jest kompensowany temperaturowo i szczególnie stabilny w długim okresie czasu. Rejestruje nawet najmniejsze różnice ciśnień, zapewniając tym samym wysoką niezawodność i najwyższą dokładność pomiaru. Zmierzone wartości są dostępne jako analogowe sygnały napięciowe i prądowe, cyfrowo przez interfejs RS-485 z wykorzystaniem Modbus RTU lub przez LoRaWAN.
Czujnik A2G-500 ma dowolnie regulowane zakresy pomiarowe. Przyrząd można ustawić za pomocą aplikacji WIKA i NFC oraz, w zależności od wersji, za pomocą przycisków i diod LED
lub przycisków i wyświetlacza. Wydajna dokumentacja projektu jest możliwa dzięki odczytowi pliku parametrów przyrządu za pośrednictwem NFC i smartfona. Wskazania maksymalnie czterech wartości pomiarowych i dwóch stanów pr zekaźnika można odczytać pod każdym kątem dzięki 2” kolorowemu wyświetlaczowi TFT z funkcją sygnalizacji świetlnej i zindywidualizowanymi napisami parametrów pomiarowych. Konstrukcja A2G-500 jest solidna i odporna na warunki atmosferyczne (stopień ochrony IP65).
Źródło: WIKA
Firma Zebra Technologies wprowadziła do swojej oferty uniwersalną serię terminali mobilnych MC33xx, która umożliwia wybór modelu o właściwym, ergonomicznym kształcie do każdego zastosowania. W serii MC33xx dostępne są terminale pistoletowe, wieżyczkowe z obrotową głowicą, z oknem skanera skierowanym na wprost i kątem skanowania 0º oraz model z oknem skanera skierowanym na wprost i kątem skanowania 45º (wariant wieżyczkowy i z kątem skanowania 45º dostępne są tylko w modelu MC3300x).
Seria MC33xx została stworzona z myślą o różnych środowiskach pracy. Stąd urządzenia mają różne poziomy odporności na upadki, wielokrotne wstrząsy i ochronę przed wnikaniem zanieczyszczeń. Wybór najlepszego urządzenia do danego środowiska prac można zoptymalizować pod kątem potrzeb związanych z konkretnym zastosowaniem.
Zebra MC33xx wyposażona jest w dwa tryby komunikacji – Wi-Fi lub krótkofalówkę.
Źródło: Zebra Technologies
Firma Farnell poinformowała o wprowadzeniu na rynek Raspberr y Pi Pico 2 – nowego modułu z autorskim mikrokontrolerem RP2350. To ulepszona wersja poprzedniego modelu z RP2040 – jest taktowany zegarem 150 MHz, ma podwójne rdzenie Arm Cortex-M33 oraz Hazard3 RISC-V. Wyposażony jest w 520 kB pamięci SRAM oraz wbudowaną pamięć OTP 8 kB, a także większą pojemność Flash (do 4 MB). Zestaw interfejsów per yferyjnych zawiera: 2-kanałowy UART, dwa kontrolery SPI, dwa kontrolery I2 C, 24 kanały PWM, kontroler USB 1.1 i PHY ze wsparciem hosta. Model zabezpieczeń oparto na Arm TrustZone for Cortex-M. Raspberry Pi Pico 2 jest jeszcze bardziej wydajny energetycznie.
Źródło: Farnell
Wydarzeniu towarzyszyć będą: 15-17 października 2024 r.
Międzynarodowe Centrum Kongresowe w Katowicach
Jakie technologie zdominują automatykę przemysłową w najbliższych latach? Na czym opiera się sukces wdrożenia nowoczesnych technologii? W jaki sposób firma Nexus koordynuje projekty realizowane w Polsce przez firmy z Japonii? O tym mówi Juliusz Hirotomi, prezes Nexus Engineering Europe.
Grupa Nexus ma japoński rodowód, ale także w innych krajach powstały spółki wchodzące w jej skład. Od kiedy funkcjonuje polska firma Nexus Engineering Europe i co zdecydowało o uruchomieniu działalności w naszym kraju?
Decyzja o uruchomieniu działalności w Polsce była strategicznym krokiem, mającym na celu rozszerzenie wpływów Grupy Nexus na r ynek europejski. Wybór Polski nie był przypadkowy –kraj ten oferuje doskonałe połączenie wykwalifikowanej siły roboczej, dynamicznie rozwijającego się sektora przemysłowego, sprzyjających
warunków inwestycyjnych, a ponadto jest jedną z moich dwóch Ojczyzn. Po sukcesie oddziału w Indonezji postanowiłem osiągnąć jeszcze więcej w Polsce. Dzięki powstaniu siedziby w Niepołomicach, Nexus mógł połączyć japońską precyzję z europejskim know-how, dostarczając zaawansowane technologicznie rozwiązania automatyzacyjne i robotyzacyjne, które szybko znalazły uznanie na r ynku. Polska lokalizacja ułatwia również dostęp do kluczowych rynków europejskich, co dodatkowo przyczyniło się do podjęcia decyzji o uruchomieniu działalności w naszym kraju. Zakres
działalności Nexus Europe obejmuje całe terytorium Europy.
Rozwiązania Grupy Nexus do automatyzacji produkcji w przemyśle obejmują stacje zrobotyzowane, maszyny kontrolno-pomiarowe, wózki autonomiczne czy urządzenia transportujące. Które z nich stanowią największą grupę i cieszą się największym zainteresowaniem? Automatyzacja linii przemysłowych jest kluczowym aspektem projektowym grupy Nexus. Jej atutem jest zwiększenie efektywności, precyzji i konkurencyjności współczesnych przedsiębiorstw.
Dzięki zaawansowanym technologiom, takim jak stacje zrobotyzowane, maszyny kontrolno-pomiarowe, wózki autonomiczne i urządzenia transportujące, firmy mogą nie tylko przyspieszyć swoje procesy produkcyjne, ale także zredukować liczbę błędów, poprawić jakość produktów i optymalizować koszty operacyjne. Automatyzacja pozwala również na lepsze wykorzystanie zasobów, minimalizację przestojów oraz elastyczne dostosowanie produkcji do zmieniających się potrzeb rynku. W efekcie przedsiębiorstwa, które inwestują w automatyzację zyskują przewagę konkurencyjną, mogąc oferować swoje produkty szybciej i taniej, przy zachowaniu najwyższych standardów jakości.
Nasi konstruktorzy i klienci nie zamykają się na jedną dziedzinę proponowanych przez nas rozwiązań, dzięki szerokiemu spektrum produktów i usług jesteśmy w stanie sprostać różnorodnym potrzebom przemysłu.
Nasze kompleksowe podejście pozwala na dostosowanie automatyzacji do specyficznych wymagań każdej branży, oferując rozwiązania, które integrują nowoczesne technologie z unikalnymi potrzebami klientów. To zróżnicowanie sprawia, że nasi partnerzy mogą liczyć na wsparcie w różnych aspektach swojej działalności, co przekłada się na jeszcze większą efektywność i innowacyjność w ich procesach produkcyjnych.
Poza gotowymi rozwiązaniami Nexus oferuje także usługi. Jakie i do kogo adresowane?
Zakres naszych usług obejmuje przede wszystkim programowanie sterowników PLC oraz instalację maszyn u klienta. Skierowane są one do firm, które już posiadają maszyny, a w szczególności te importowane z Japonii. Dzięki naszym usługom klienci mogą liczyć
na pełne wsparcie w dostosowaniu i optymalizacji swoich urządzeń, co pozwala na ich efektywną integrację z istniejącymi procesami produkcyjnymi. Nasza wiedza i doświadczenie w pracy z japońskimi maszynami gwarantują, że każda instalacja przebiegnie sprawnie, a maszyny będą działać zgodnie z najwyższymi standardami.
Jak szerokie wsparcie oferuje Nexus firmom produkcyjnym?
Oferujemy kompleksowe pakiety produkcyjne, obejmujące wszystko, od dostawy i montażu u klienta, aż po przeprowadzanie regularnej konserwacji maszyn w ustalonym okresie.
Czy może Pan przytoczyć przykład wdrożenia, które było najtrudniejsze albo najciekawsze?
Jednym z największych wyzwań, z jakimi się zmierzyliśmy, było dostarczenie systemu wizyjnego wyposażonego w sztuczną inteligencję. Opracowanie tego zaawansowanego rozwiązania zajęło miesiące, głównie z powodu trudności związanych z wibracjami, które znacząco wpływały na jakość obrazów z kamer wykorzystywanych do analiz. Gdy czas cyklu był wyjątkowo krótki, a maszyna poruszała się z dużą prędkością, konieczne było zastosowanie innowacyjnych metod, aby zapewnić precyzyjne działanie systemu w takich wymagających warunkach.
W których sektorach przemysłu i w jakich obszarach zastosowań widzi Pan największy potencjał wdrożeniowy w zakresie automatyzacji i robotyzacji produkcji?
Automatyzacja jest kluczowym elementem w każdej branży przemysłowej, dlatego nie ograniczamy się do jednego segmentu rynku. Nasze rozwiązania znajdują zastosowanie w różnych sektorach, ponieważ wiemy, że jedynym
JEDNYM Z NAJWIĘKSZYCH WYZWAŃ, Z JAKIMI SIĘ ZMIERZYLIŚMY, BYŁO
DOSTARCZENIE SYSTEMU WIZYJNEGO WYPOSAŻONEGO W SZTUCZNĄ
skutecznym sposobem na obniżenie kosztów produkcji, bez konieczności importowania w przyszłości produktów z krajów oferujących tańsze rozwiązania, jest automatyzacja linii produkcyjnych. Inwestowanie w automatyzację pozwala firmom utrzymać konkurencyjność, zwiększając jednocześnie efektywność i jakość produkcji, co jest niezbędne na dynamicznie zmieniającym się globalnym rynku.
Co stanowi barierę w pełnej automatyzacji fabryk i procesów technologicznych?
Rozwój automatyzacji w Polsce to ogromny krok naprzód, szczególnie biorąc pod uwagę liczne genialne pomysły, które powstają w naszym kraju. Jednak jednym z głównych wyzwań jest efektywna praca zespołowa. Sukces wdrożenia nowoczesnych technologii nie opiera się tylko na innowacyjnych pomysłach, ale przede wszystkim na umiejętności współpracy w zespole. Technologia musi pozostać wewnątrz firmy i być rozwijana w ramach spójnego zespołu, a nie przez odizolowanych indywidualistów. Tylko dzięki zgranej pracy zespołowej możemy osiągnąć optymalne rezultaty i skutecznie wprowadzać innowacje na rynek.
Czy usługi serwisowe, które świadczy Nexus Engineering Europe dotyczą tylko japońskich urządzeń i linii technologicznych, czy również innych?
Nie ograniczamy się tylko do klientów z Japonii – współpracujemy także z firmami z USA, Włoch, Szwecji i Niemiec, które mają swoje fabryki w Polsce. Dzięki naszej międzynarodowej współpracy jesteśmy w stanie wspierać każdą firmę, która potrzebuje naszych usług, niezależnie od jej lokalizacji. Nasze doświadczenie z różnorodnymi rynkami i technologiami pozwala nam dostarczać rozwiązania dostosowane do specyficznych potrzeb klientów z całego świata.
Jakie sektory przemysłu są obecnie głównymi klientami firmy?
W naszej działalności z zakresu automatyzacji, ponad 50 % projektów stanowi motoryzacja. Pozostałe segmenty rynku obejmują druk, łożyska, szkło i akumu-
Prezes, dyrektor generalny i członek zarządu spółki Nexus Engineering Europe. Inicjator założenia firmy. Absolwent Politechniki Wrocławskiej. Doświadczenie w dziedzinie inżynierii zdobywał na całym świecie (Japonia, Polska, USA, Wielka Brytania, Niemcy, Chiny, Indonezja). Jego misją jest stworzenie europejskiego oddziału i najbardziej niezawodnych maszyn opartych na japońskich technologiach.
latory. Dzięki temu możemy dostarczać specjalistyczne rozwiązania dostosowane do zróżnicowanych potrzeb różnych branż, zapewniając wszechstronność i elastyczność w naszych usługach.
Jakie działania prowadzi firma w zakresie badawczo-rozwojowym?
Kluczowe obszary badań i rozwoju w naszej firmie to systemy Bin-Picking oraz systemy Vision ze sztuczną inteligencją. Skupiamy się na udoskonalaniu tych technologii, aby dostarczać innowacyjne rozwiązania, które rewolucjonizują automatyzację procesów przemysłowych.
System Bin-Picking umożliwia precyzyjne pobieranie luźno rozrzuconych komponentów z pojemników, co jest kluczowe dla zwiększenia efektywności i dokładności w procesach produkcyjnych.
Systemy Vision ze sztuczną inteligencją pozwalają na zaawansowaną analizę obrazów, identyfikację wad oraz optymalizację procesów produkcyjnych, dzięki czemu możemy dostarczać rozwiązania o wysokiej precyzji i niezawodności.
Koncentrując się na tych obszarach, dążymy do nieustannego rozwoju technologii, które odpowiadają na rosnące wymagania przemysłu i przyczyniają się do dalszej automatyzacji oraz innowacji w różnych branżach.
Na czym polega koordynacja projektów na linii Japonia – Polska?
Firma Nexus specjalizuje się w koordynacji projektów między Japonią a Polską, zapewniając wsparcie dla japońskich firm oraz ich pracowników w Polsce. Ze względu na znaczną różnicę mentalną i kulturową, od początku projektu kluczowa jest skuteczna koordynacja, szczególnie w fazie tworzenia specyfikacji.
Nasze doświadczenie w zarządzaniu międzynarodowymi projektami pozwa-
la nam efektywnie mostkować różnice kulturowe i operacyjne, co zapewnia płynny przebieg prac i precyzyjne dopasowanie rozwiązań do wymagań obu stron. Dzięki temu japońskie firmy mogą liczyć na profesjonalne wsparcie na każdym etapie projektu, od koncepcji po wdrożenie, co umożliwia osiągnięcie optymalnych rezultatów i skuteczną realizację celów.
Jakie trendy w automatyce przemysłowej będą dominować w bliskiej przyszłości?
Przewidujemy, że w nadchodzących latach automatyka przemysłowa będzie rozwijać się w kierunku zaawansowanych systemów sztucznej inteligencji oraz robotyzacji transportu.
Systemy AI będą coraz bardziej integrowane z rozwiązaniami automatyzacyjnymi, umożliwiając inteligentną analizę danych, przewidywanie awarii oraz optymalizację procesów produkcyjnych. Dzięki sztucznej inteligencji systemy będą mogły uczyć się i dostosowywać do zmieniających się warunków, co przyczyni się do jeszcze większej precyzji i efektywności.
Transport robotyczny będzie natomiast rozwijał się w kierunku coraz bardziej autonomicznych i zintegrowanych rozwiązań. Roboty transportowe będą mogły efektywnie zarządzać przepływem materiałów w zakładach produkcyjnych, redukując koszty operacyjne oraz zwiększając elastyczność i szybkość procesów logistycznych.
Te trendy wskazują na rosnące znaczenie innowacji w automatyce, które pozwolą tworzyć bardziej zaawansowane, elastyczne i efektywne systemy produkcyjne i logistyczne.
Jakie są strategiczne plany firmy na najbliższe lata?
Strategią firmy na nadchodzące lata w kwestii technicznej jest skoncentro-
wanie się na rozwoju i wdrażaniu dwóch kluczowych technologii: systemu zbierania pojemników Bin-Picking oraz systemu kamer ze sztuczną inteligencją. Naszą strategią rozwojową jest natomiast szerokie zaprezentowanie naszej oferty oraz pokazanie wyjątkowej jakości i precyzji naszych rozwiązań. Skupiamy się na dotarciu do szerszego grona klientów, aby przybliżyć im nasze innowacyjne pomysły i wysoką jakość pracy. Dążymy do prezentacji marki Nexus jako wyjątkowych rozwiązań i zespołów ludzi o szerokich horyzontach w zakresie inżynierii i konstruowania.
Czy w strategii rozwoju Grupy Nexus większy nacisk kładziony jest na rozwój lokalny czy centralny?
Szczególny nacisk kładziemy na rozwój lokalny. Nasze działania koncentrują się na kilku obszarach działań w tym zakresie. Pierwszy z nich to wzmacnianie lokalnych rynków. Dążymy do pogłębiania naszej obecności na r ynkach lokalnych, co pozwala nam lepiej rozumieć i odpowiadać na specyficzne potrzeby klientów w różnych regionach.
Kolejny to wspieranie lokalnych inicjatyw. Angażujemy się w lokalne projekty i współpracujemy z regionalnymi partnerami, co przyczynia się do wzrostu gospodarczego i innowacyjności w danym obszarze.
Następny obszar działania to rozwój lokalnych talentów. Inwestujemy w rozwój lokalnych zespołów, oferując szkolenia i możliwość kariery, co pozwala nam budować silne, kompetentne zespoły w każdym regionie, w którym działamy.
Ostatnim elementem jest optymalizacja procesów lokalnych. Skupiamy się na dostosowywaniu naszych rozwiązań do specyficznych warunków i potrzeb lokalnych rynków, co zapewnia większą efektywność i lepsze wyniki dla naszych klientów. Nasza strategia rozwoju lokalnego ma na celu nie tylko zwiększenie naszej konkurencyjności na rynku globalnym, ale także przyczynienie się do rozwoju lokalnych społeczności i gospodarek.
Rozmawiała
Urszula Chojnacka AUTOMATYKA
Profesjonalne szkolenia dla przemysłu oraz kadry inżynierskiej
Centrum Szkoleniowe Sieć badawCza łukaSiewiCz
Przemy Słowy inStytut automatyki i Pomiarów PiaP
Centrum Szkoleniowe PiaP
Programowanie robotów abb – kurs podstawowy - szkolenie u klienta
Programowanie robotów Comau – kurs podstawowy - szkolenie u klienta
Sieć Badawcza Łukasiewicz - Przemysłowy Instytut Automatyki i Pomiarów PIAP
al. jerozolimskie 202, 02-486 warszawa www.piap.pl tel. 22 874 0 194, 198 cspiap@piap.pl
Programowanie robotów kuka – kurs podstawowy - szkolenie w Instytucie - szkolenie u klienta
Szkolenie zaawansowane z programowania robotów kuka - szkolenie w Instytucie - szkolenie u klienta
Produkcja przemysłowa w dużej mierze polega na ciągłym wykonywaniu powtarzalnych, mniej lub bardziej skomplikowanych czynności. Zastąpienie przy ich wykonywaniu pracy ludzkiej lub zastąpienie obsługiwanych ręcznie maszyn zautomatyzowanymi lub zrobotyzowanymi systemami nie tylko wpływa na zwiększenie wydajności i obniżenie kosztów, ale przede wszystkim podnosi jakość produkcji, a co za tym idzie, zadowolenie klienta.
dr inż. Marcin Bieńkowski
Wiele podręczników definiuje automatyzację procesów produkcyjnych jako wykorzystanie technologii automatyki przemysłowej i zrobotyzowanych systemów i systemów komputerowych do wykonywania zadań produkcyjnych, które wcześniej były realizowane ręcznie lub w sposób półautomatyczny. Celem automatyzacji jest zwiększenie efektywności, redukcja kosztów, poprawa jakości oraz zwiększenie bezpieczeństwa pracy. Automatyzacja może obejmować:
• Roboty przemysłowe – wykorzystywane są do wykonywania powtarzalnych zadań, np. montażu, spawania, pakowania czy malowania.
• Maszyny CNC (Computer Numerical Control) – pozwalają na precyzyjne
sterowanie obróbką materiałów, takich jak metal, drewno czy tworzywa sztuczne.
• Systemy transportu i magazynowania – zautomatyzowane systemy przenoszenia i składowania towarów, np. taśmociągi, magazyny automatyczne.
• Czujniki i systemy kontroli – monitorują i kontrolują parametry produkcji, takie jak temperatura, ciśnienie czy wilgotność, aby zapewnić wysoką jakość produktów.
• Oprogramowanie i systemy ERP/ MES – zarządzają procesami produkcji i synchronizują je, monitorują zużycie materiałów i kontrolują planowanie produkcji.
• Systemy SCADA (Supervisory Control And Data Acquisition) – nadzo-
rują przebieg procesu technologicznego lub produkcyjnego. Główną ich funkcją jest zbieranie i archiwizowanie aktualnych danych z pomiarów, ich wizualizacja, a także sterowanie procesem za pośrednictwem komend i instrukcji wydawanych elementom układu automatyki. Zastąpienie ludzi i prostych maszyn systemami automatyki przemysłowej niesie za sobą wiele korzyści. Automatyzacja produkcji pozwala przede wszystkim na wyeliminowanie błędów i przyspieszenie realizacji procesów. Co więcej, można uzyskać rezultaty, jakich nie dałoby się osiągnąć w inny sposób. Do korzyści zaliczyć należy również [1]:
• możliwość zredukowania ilości wykorzystywanych zasobów oraz odpadów produkcyjnych;
• ochrona zdrowia pracowników –brak ryzyka wynikającego np. z kontaktu z niebezpiecznymi substancjami;
• wzrost komfortu pracy – dzięki przeniesieniu personelu produkcyjnego na stanowiska związane np. z obsługą i nadzorem maszyn;
• uzyskanie idealnej powtarzalności wyrobów – każdy produkt ma dokładnie taką samą jakość;
• możliwość prowadzenia produkcji niezależnie od pory dnia;
• możliwość produkcji dostosowanej do bieżących potrzeb, eliminowanie przestojów.
Wykorzystanie odpowiednio dopasowanych rozwiązań pomoże spełnić określone potrzeby przedsiębiorstwa i zredukować występujące problemy. Dzięki temu wszelkie działania mogą być realizowane znacznie skuteczniej, co przekłada się na większe zyski. Skutkiem automatyzacji produkcji zwykle jest też wzrost jakości wyrobów oraz związany z tym wzrost zadowolenia ich odbiorców. Dzięki temu firma może poprawiać swoją pozycję na r ynku i zdobywać nowych klientów, a dzięki temu dalej rozwijać swoją działalność.
Kluczowe technologie automatyzacji produkcji
W firmach produkcyjnych spotkać się można z dwoma rodzajami automatyzacji – automatyzacją lekką i przemy-
słową. Pierwsza polega na stosowaniu rozwiązań IT do zarządzania produkcją i do kontroli jej przebiegu (czujniki i sensor y, analiza danych, predykcyjne utrzymanie ruchu, systemy ERM, SCADA itp.), w tym sztucznej inteligencji. Druga to tradycyjna automatyzacja procesów przemysłowych, w automatyzacja wykorzystująca sterowniki PLC, falowniki, napędy liniowe, enkodery itp. urządzenia, w tym obrabiarki CNC, które wspierają ludzi podczas pracy na hali produkcyjnej. Dotyczy ona zarówno procesów wytwarzania, magazynowania, jak i pakowania gotowych wyrobów, które wysyłane są do klienta.
Sterowniki PLC (Programmable Logic Controllers) odgrywają kluczową rolę we współczesnych systemach automatyki. Są to programowalne urządzenia cyfrowe, które mogą bez problemu zarządzać sekwencją działań maszyn i urządzeń w procesach produkcyjnych. PLC nie tylko monitorują i kontrolują różne operacje, ale są także fundamentem integracji rozproszonych systemów produkcyjnych, pozwalając na precyzyjną synchronizację z różnymi elementami infrastruktury przemysłowej. W sprzedaże dostępne są też sterowniki PLC, które skonstruowane z myślą o pracy w trudnych warunkach pracy, takich jak zmienna temperatura, wibracje czy wysoka wilgotność.
Nowoczesne sterowniki PLC są zdolne do zbierania i analizowania ogrom-
nych ilości danych produkcyjnych w czasie rzeczywistym. Dzięki temu możliwe jest wykrywanie anomalii w pracy maszyn, przewidywanie awarii oraz optymalizacja zużycia energii i surowców. Współpraca z narzędziami analitycznymi w chmurze umożliwia jeszcze bardziej zaawansowane analizy, co prowadzi do poprawy efektywności produkcji.
Do zbierania danych oraz do sterowania urządzeniami wykonawczymi wykorzystywane są moduły wejścia/ wyjścia (Moduły I/O). Są to elementy, które pozwalają sterownikom PLC na interakcję z fizycznymi komponentami systemu, takimi jak czujniki (wejścia) oraz urządzenia wykonawcze, np. siłowniki czy przekaźniki (wyjścia). Moduły I/O mogą być zarówno cyfrowe, jak i analogowe. Te ostatnie wykorzystywane są do obsługi sygnałów ciągłych, np. zmian temperatury czy ciśnienia.
Sterowniki PLC są często wyposażone w porty do komunikacji z innymi urządzeniami, takimi jak komputery przemysłowe, systemy SCADA czy inne urządzenia sterujące. Standardowe protokoły komunikacyjne obejmują tu Ethernet, Modbus, Profibus i Profinet, umożliwiając tym samym zdalne sterowanie oraz integrację z większymi sieciami produkcyjnymi [2].
Pilz, jedna z czołowych firm dostarczających rozwiązania automatyzacyj-
ne, oferuje zaawansowane sterowniki PLC w ramach swojego systemu PSS 4000. To modułowe rozwiązanie, które umożliwia elastyczne zarządzanie bezpieczeństwem i automatyzacją procesów produkcyjnych. Dzięki zastosowaniu technologii PLC możliwe jest precyzyjne kontrolowanie ruchu maszyn, zapewniając nie tylko wydajność, ale także bezpieczeństwo pracy.
Turck z kolei oferuje linię wytrzymałych sterowników TBEN-PLC, które mogą być stosowane w najbardziej wymagających warunkach przemysłowych. Dzięki wbudowanym interfejsom sieciowym i protokołom komunikacyjnym, takim jak Profinet czy Modbus, sterowniki te umożliwiają integrację z szeroką gamą urządzeń peryferyjnych oraz systemów wyższego poziomu. Firma BOSCH REXROTH dostarcza natomiast swoim klientom systemy sterowania, takie jak CtrlX CORE, które łączą tradycyjne funkcje sterownika PLC z technologiami IIoT (Industrial Internet of Things), co pozwala na jeszcze większą elastyczność i wydajność w zarządzaniu produkcją.
Przemysłowy Internet
Rzeczy IIoT
Internet Rzeczy odgrywa coraz większą, jeśli nie kluczową rolę w automatyzacji produkcji. Dzięki wykorzystaniu czujników, systemów sieciowych i technologii komunikacyjnych, IIoT pozwala na zbieranie, przetwarzanie i analizę danych z różnych punktów w procesie produkcyjnym. Informacje te wykorzystywane są do optymalizacji produkcji, przewidywania awarii oraz zarządzania zasobami w czasie rzeczywistym.
Czujniki i sensor y są podstawowymi elementami systemów IIoT dostarczającymi informacji o warunkach pracy maszyn, stanach procesów produkcyjnych oraz parametrów środowiskowych. Przemysłowe czujniki IIoT mogą monitorować temperaturę, wilgotność, ciśnienie, poziom wibracji, przepływ, jakość powietrza, a także inne kluczowe parametry, od których zależy prawidłowy przebieg procesu produkcyjnego. Czujniki te mogą przesyłać dane w czasie rzeczywistym
do s ystemów nadzoru, takich jak SCADA, lub bezpośrednio do chmur y, umożliwiając szybką reakcję na potencjalne awarie i zakłócenia. Z kolei bramki IIoT pełnią funkcję pośrednika między czujnikami a systemami informatycznymi, zbierając dane z urządzeń i przesyłając je do chmur y lub lokalnych systemów obliczeniowych. Mogą one również przetwarzać dane bezpośrednio na miejscu, zmniejszając potrzebę przesyłania dużych ilości informacji do zewnętrznych serwerów. W przemysłowych aplikacjach bramki IIoT umożliwiają integrację starszych systemów z nowoczesnymi sieciami IT i ułatwiają wdrażanie rozwiązań IIoT w istniejących infrastrukturach produkcyjnych. Z punktu widzenia systemu automatyki kluczowym elementem IIoT są urządzenia wykonawcze zwane też aktuatorami IIoT. Sprzęt ten nie tylko odbiera polecenia z systemów sterowania, ale również reaguje na nie w czasie rzeczywistym, wykonując określone operacje. Do tej kategorii urządzeń zalicza się zawory sterujące, siłowniki, napędy oraz inne mechanizmy odpowiedzialne za regulację procesów produkcyjnych. Dzięki integracji z systemami IIoT, urządzenia wykonawcze mogą działać w znacznie większym stopniu autonomicznie, re-
agując na dane w czasie rzeczywistym bez konieczności interwencji człowieka.
Firma Turck oferuje zaawansowane systemy IIoT, które integrują czujniki, systemy sterowania i rozwiązania sieciowe w jeden spójny ekosystem. Przykładem są rozwiązania Turck Cloud Solutions, które umożliwiają zdalne monitorowanie i zarządzanie danymi produkcyjnymi w czasie rzeczywistym. Dzięki temu menedżerowie produkcji mogą na bieżąco reagować na zmiany w procesie, optymalizując jego efektywność.
Bosch Rexroth oferuje rozwiązania z zakresu IoT, takie jak IoT Gateway. To bramka IoT, która umożliwia integrację starszych maszyn i urządzeń z nowoczesnymi systemami IoT, umożliwiając monitorowanie i analizę danych w czasie rzeczywistym. Dzięki swojej elastyczności, IoT Gateway może łączyć się z różnorodnymi czujnikami, systemami sterowania oraz oprogramowaniem analitycznym.
IIoT w produkcji to nie tylko zbieranie danych, ale także ich analiza i przekształcanie w wartościowe informacje. Dane te mogą być następnie wykorzystywane do automatycznego dostosowywania procesów produkcyjnych, np. przez zintegrowanie z systemami PLC i SCADA. Tego rodzaju roz-
W AUTOMATYCE PRZEMYSŁOWEJ OBEJMUJĄ:
• Monitorowanie i wizualizacja procesów – SCADA umożliwia operatorom monitorowanie stanu maszyn i urządzeń w czasie rzeczywistym poprzez interaktywne interfejsy graficzne. Na ekranach wyświetlane są szczegółowe informacje na temat bieżących parametrów pracy, co pozwala na szybkie diagnozowanie ewentualnych problemów.
• Sterowanie procesami – SCADA pozwala operatorom na zdalne sterowanie elementami procesu, takimi jak zawory, pompy, silniki i inne urządzenia. Dzięki temu możliwe jest reagowanie na zmiany w procesie bez konieczności fizycznej obecności przy maszynach.
• Alarmowanie – Systemy SCADA mogą generować alarmy w przypadku, gdy określone parametry przekroczą ustalone wartości, np. zbyt wysoka temperatura lub zbyt niskie ciśnienie. Pozwala to na szybkie podjęcie działań zapobiegawczych, co minimalizuje ryzyko awarii i przestojów.
• Akwizycja danych – SCADA zbiera dane z w ielu źródeł w zakładzie, takich jak czujniki, sterowniki PLC, DCS (Distributed Control Systems), a także z systemów ERP (Enterprise Resource Planning) i MES (Manufacturing Execution Systems). Dane te są gromadzone w centralnej bazie danych, gdzie mogą być analizowane i wykorzystywane do optymalizacji procesów.
wiązania pozwalają na tworzenie tzw. inteligentnych fabryk, gdzie systemy produkcyjne są samodzielne i zdolne do podejmowania decyzji na podstawie zebranych danych.
Komputery przemysłowe Komputery przemysłowe IPC (Industrial PC), to kolejny filar nowoczesnej automatyzacji, który pozwala na przetwarzanie ogromnych ilości danych w czasie rzeczywistym oraz na komunikację między różnymi systemami sterowania. Wykorzystywane są one głównie do zadań wymagających dużej mocy obliczeniowej, np. w złożonych procesach monitorowania i kontroli jakości. W praktyce przemysłowej spotkamy się z całą gamą tego typu urządzeń –począwszy od wersji Box PC, poprzez komputery typu embedded, komputery panelowe, terminale POS, urządzenia jednopłytkowe, systemy HMI, a na dużych systemach serwerów kasetowych sterujących produkcją i działaniem całej fabryki skończywszy. W zależności od zastosowania, komputery przemysłowe można podzielić na kilka podstawowych kategorii:
• Komputery panelowe – urządzenia te integrują jednostkę obliczeniową z wyświetlaczem dotykowym, co czyni je idealnym rozwiązaniem do bezpośredniego sterowania maszynami lub liniami produkcyjnymi.
Są powszechnie stosowane w interfejsach HMI (Human Machine Interface), dzięki temu operatorzy mogą monitorować i sterować procesami produkcyjnymi bezpośrednio z linii produkcyjnej. Komputery panelowe często mają wytrzymałe, przemysłowe obudowy odporne na uszkodzenia mechaniczne, a ich ekrany są przystosowane do pracy w środowiskach o wysokim poziomie pyłu, wilgoci lub chemikaliów.
• Komputery jednopłytkowe (SBC –Single Board Computers) – to komputery przemysłowe o małych rozmiarach, które integrują wszystkie niezbędne komponenty na jednej płytce drukowanej. Używane są w aplikacjach wymagających niskiego zużycia energii i kompaktowej budowy, np. w systemach osadzonych, które pełnią specyficzne funkcje w automatyce, takie jak monitorowanie czujników, kontrola napędów czy zarządzanie systemami logistycznymi.
• Komputery kompaktowe – są to jednostki centralne o niewielkich roz-
miarach, które mogą być montowane w ciasnych przestrzeniach lub bezpośrednio w szafach sterowniczych. Tego typu komputery przemysłowe są wykorzystywane do obsługi aplikacji SCADA, systemów monitorowania w czasie rzeczywistym oraz w zarządzaniu danymi produkcyjnymi.
• Komputery serwerowe – stosowane w dużych zakładach przemysłowych, gdzie istnieje potrzeba obsługi dużych ilości danych oraz zapewnienia wysokiej dostępności i bezpieczeństwa. Serwery przemysłowe mogą obsługiwać scentralizowane systemy SCADA, magazyny danych, a także złożone aplikacje analityczne, np. związane z analizą predykcyjną w oparciu o dane IoT. W praktyce przemysłowej komputery IPC działają najczęściej jako pomost między różnymi elementami systemu automatyki i infrastruktury IT, umożliwiając integrację sterowników PLC, systemów SCADA, urządzeń IIoT oraz baz danych obsługiwanych np. przez systemy ERP/CRM. Mogą one zbierać
i przetwarzać dane z wielu źródeł, a następnie udostępniać je w postaci scentralizowanych raportów lub analiz w czasie rzeczywistym. Integracja ta pozwala na lepszą kontrolę nad całością procesu produkcyjnego.
Jednym z najnowszych trendów w automatyce przemysłowej jest rozwój komputerów Edge AI (Edge Artificial Intelligence). Są to urządzenia, które łączą funkcje klasycznych komputerów przemysłowych z zaawansowaną analizą danych i sztuczną inteligencją (AI) na krawędzi sieci, czyli blisko źródeł danych. Zamiast przesyłać dane do scentralizowanych serwerów lub chmury do analizy, komputery Edge AI przetwarzają i analizują dane bezpośrednio na poziomie produkcji, co znacząco przyspiesza reakcję systemu na zmiany.
Firma Bosch Rexroth oferuje zaawansowaną platformę CtrlX CORE, która jest wszechstronnym komputerem przemysłowym o modularnej architekturze. Platforma ta integruje
funkcje sterowania z przetwarzaniem danych, umożliwiając jednoczesną obsługę systemów automatyki, IIoT oraz aplikacji analitycznych. Dzięki wysokiej elastyczności i możliwościom rozbudowy, CtrlX CORE może obsługiwać zarówno tradycyjne procesy sterowania, jak i nowoczesne systemy Edge AI.
WObit oferuje komputery przemysłowe z serii EPC, które wyróżniają się wysoką wydajnością, kompaktowymi rozmiarami oraz szerokimi możliwościami integracji. Komputery te są doskonałym rozwiązaniem do złożonych aplikacji sterowania, a także systemów monitorowania, które wymagają dużej niezawodności i odporności na trudne warunki pracy.
Czas na SCADA
Pod względem funkcjonalnym współczesne systemy automatyki oraz systemy sterowania urządzeń są dość mocno do siebie zbliżone. Jak już wspomniano, komputer przemysłowy, bądź sterownik PLC podejmuje
decyzje związane z pracą podłączonych do niego urządzeń na podstawie zbieranych w czasie rzeczywistym informacji o stanie maszyny czy linii produkcyjnej. Informacje te pochodzą z podłączonych do jego wejść czujników, np. temperatury lub położenia oraz różnego rodzaju przetworników, które są zazwyczaj sprzężone z elementami wykonawczych maszyny lub instalacji automatyki przemysłowej. Urządzenie sterujące na podstawie zebranych danych realizuje automatycznie zaprogramowane wcześniej algorytmy związane z procesami sterowania i regulacji, reagując tym samym w czasie rzeczywistym na wszelkiego typu zdarzenia związane z wykonywaniem ustalonych uprzednio czynności dotyczących pracy maszyny bądź linii. W praktyce, to sterownik PLC na podstawie wejść, a więc danych otrzymanych z urządzeń pomiarowych i wykonawczych wykonuje operacje sterowania zgodnie z wgranym do niego programem. Następnie wy-
AVEVA InTouch (dawniej Wonderware) – Platforma Systemowa
AVEVA InTouch to pakiet programów, które pozwalają stworzyć spójny, skalowalny system klasy HMI/SCADA/MES. W wypadku funkcjonalności SCADA, podstawowym elementem systemu jest moduł AVEVA InTouch. Pakiet nastawiony jest na wizualną prezentację procesu produkcyjnego i ułatwienie interakcji z systemami automatyki przemysłowej. Wyróżnikiem InTouch’a jest technologia Industrial Graphics (dawniej ArchestrA Graphics), która daje nieograniczone możliwości w procesie tworzenia obiektów graficznych. Każdy użytkownik w zestawie otrzymuje potężną bibliotekę gotowych obiektów, także tych zgodnych z metodyką Situational Awareness, którą określić można mianem bibliotek świadomości sytuacyjnej. Dzięki temu zapewnić można operatorom w czasie rzeczywistym dostęp do wszystkich informacji kontekstowych, których potrzebują danej chwili, aby szybko i dokładnie reagować na sytuacje krytyczne związane z procesem produkcyjnym, zanim wpłyną one na bieżące operacje wykonywane w ciągu technologicznym.
Siemens SIMATIC WinCC – SIMATIC WinCC to system nadrzędnego sterowania i akwizycji danych SCADA i jednocześnie interfejs operatorski HMI. Obecnie zintegrowany jest z platformą inżynierską TIA Portal. System pozwala na tworzenie aplikacji służących do monitorowania i sterowania fizycznymi procesami przemysłowymi oraz infrastrukturą technologiczną. Platforma projektowa TIA Portal pozwala na integrację nowoczesnych komponentów automatyki przemysłowej, co ułatwia realizację koncepcji Przemysłu 4.0 w fabrykach i zakładach produkcyjnych. SIMATIC WinCC (TIA Portal)
składa się z oprogramowania inżynierskiego w wariantach WinCC Basic do konfiguracji prostych paneli HMI, WinCC Comfort do tworzenia bardziej zaawansowanych aplikacji oraz WinCC Advanced do projektowania systemów HMI opartych na komputerach PC. WinCC Advanced jest również dostępny jako Pakiety Oprogramowania Runtime.
Schneider Electric EcoStruxure – To otwarta i skalowalna platforma SCADA skoncentrowana na integracji z systemami IIoT i skupiająca się na optymalizacji zużycia energii w zakładach przemysłowych. EcoStruxure łączy technologie IoT, chmurę obliczeniową, analitykę danych oraz sztuczną inteligencję (AI), oferując rozwiązania na poziomie monitorowania, automatyzacji i zarządzania zarówno dla małych zakładów, jak i dla rozległych infrastruktur przemysłowych. EcoStruxure jest platformą otwartą i interoperacyjną, co oznacza, że może być integrowana z urządzeniami i systemami innych producentów. Jego struktura opiera się na trzech kluczowych poziomach: poziom Connected Products (poziom urządzeń), gdzie znajdują się urządzenia przemysłowe takie jak czujniki, sterowniki PLC, przetworniki, liczniki energii, napędy oraz inne urządzenia automatyki; poziom Edge Control (poziom sterowania lokalnego), na którym EcoStruxure wykorzystuje lokalne jednostki sterowania i przetwarzania danych, takie jak komputery przemysłowe i sterowniki PLC do analizy danych w czasie rzeczywistym i do sterowania procesami produkcyjnymi; oraz poziom Apps, Analytics & Services (poziom analityki i usług ), który obsługuje aplikacje, sztuczną inteligencję i usługi analityczne.
Gwałtowny wzrost cen energii, który obserwujemy w ostatnich latach, sprawił, że optymalizacja kosztów zużycia mediów stała się jednym z priorytetów dla przedsiębiorstw. W obliczu tego wyzwania coraz większą rolę odgrywają nowoczesne technologie, pozwalające na monitorowanie i zarządzanie zużyciem energii w czasie rzeczywistym. Takie rozwiązania, jak inteligentne liczniki, systemy automatyki budynkowej czy instalacje odnawialnych źródeł energii (OZE) umożliwiają nie tylko ograniczenie kosztów, ale także zwiększenie efektywności energetycznej. Optymalizacja zużycia mediów jest kluczowa i tutaj z pomocą przychodzą systemy klasy EMS (Energy Management System). Ważnym ich aspektem jest możliwość objęcia jednym systemem wszystkich mediów obecnych na terenie zakładu, przez integrację urządzeń pomiarowych różnych producentów.
Świetnym przykładem takiego rozwiązania jest Asix Energy firmy ASKOM, który oferuje głównym energetykom narzędzia umożli-
syła dane do systemu SCADA, gdzie następuje ich przetwarzanie i archiwizacja. Na podstawie tych danych system SCADA generuje wizualizację parametrów pracy procesu a operator może nie tylko obserwować stan procesu produkcyjnego, wartości określonych wyjść oraz alarmy, ale może również zadawać parametry procesu, wyłączyć lub włączyć proces bądź też przejść na prowadzenie sterowania w trybie ręcznym.
Jak widać z przedstawionych wyżej informacji, systemy SCADA odgrywają kluczową rolę w nadzorowaniu procesów technologicznych i zarządzaniu infrastrukturą przemysłową. Innymi słowy, system SCADA to zbiór zaawansowanych narzędzi do nadzoru, sterowania i akwizycji danych w systemach automatyki przemysłowej, które to narzędzia pozwalają na uzyskanie szybkiego wglądu w faktyczny stan funkcjonowania oraz pracy urządzeń produkcyjnych i wykonawczych. Dzięki nim nie tylko możliwa jest zamiana języka procesowego maszyn i urządzeń na informację w postaci zrozumiałej dla ludzi, ale także umożliwiają szybką lokalizację alarmów, podstawowe logowanie danych czy też automatyczną reakcję na określone sygnały pochodzące z urządzeń. System SCADA w warstwie graficznej odpowiada zaś
wiające dokładną analizę zużycia mediów (energii). Ranking zużycia jest jednym z nich –pozwala na szybki wgląd w listę największych odbiorców energii, wskazując miejsca, gdzie można osiągnąć największe oszczędności. Możliwość porównania pomiarów z różnych okresów czasu ułatwia ocenę efektów termomodernizacji budynków. Obsługa taryf, celów energetycznych, strażnik mocy to tylko niektóre z funkcji ułatwiających energetykom codzienną pracę. Na poziomie dyrekcji i zarządu jest to możliwość wysyłania informacji do chmury i prezentowania ich w przejrzysty i esencjonalny sposób w narzędziach Power BI. Aplikacje EMS są również bardzo pomocne podczas audytów energetycznych oraz w procesie ubiegania się o białe certyfikaty. Dla firm, które są operatorami systemu dystrybucyjnego OSD, ważna jest możliwość komunikacji z powstającym systemem CSIRE.
za jednoznaczne prezentowanie dynamicznie zmieniających się informacji. Zdefiniowane wcześnie algorytmy przyspieszają i wspomagają operatora w jego pracy [3, 4].
Rozproszone systemy sterowania DCS
Rozproszone systemy sterowania DCS to zaawansowane platformy zarządzania i kontroli procesów przemysłowych, które umożliwiają bardziej precyzyjne sterowanie, monitorowanie i optymalizację skomplikowanych operacji w zakładach produkcyjnych. W przeciwieństwie do omówionych przed chwilą systemów SCADA, które koncentrują się na centralnym monitorowaniu i nadzorze, DCS kładą nacisk na rozproszoną architekturę, dzięki której sterowanie jest bardziej niezawodne, szybkie i elastyczne.
DCS to systemy, w których sterowanie i przetwarzanie danych odbywa się lokalnie w wielu węzłach rozproszonych w różnych punktach zakładu przemysłowego. Te węzły są często odpowiedzialne za konkretne sekcje lub procesy, co pozwala na autonomiczne funkcjonowanie poszczególnych jednostek, ale jednocześnie umożliwia centralne monitorowanie i koordynację. Dzięki rozproszonej architekturze DCS, możliwe jest efektywne zarządza-
nie złożonymi procesami, takimi jak rafinacja ropy, produkcja chemiczna, przemysł energetyczny czy przetwórstwo spożywcze.
DCS odgrywają kluczową rolę w automatyzacji procesów przemysłowych, szczególnie w przypadku skomplikowanych i rozległych systemów produkcyjnych. Dzięki swojej rozproszonej architekturze zapewniają większą niezawodność, skalowalność oraz elastyczność w porównaniu do innych systemów sterowania, takich jak SCADA czy tradycyjne sterowniki PLC.
Integracja systemów automatyki produkcyjnej z infrastrukturą IT
Zdolność do wymiany informacji między systemami operacyjnymi OT (Operational Technology) a infrastrukturą IT (Information Technology) otwiera nowe możliwości w zakresie monitorowania, optymalizacji procesów, analizy danych i podejmowania decyzji w czasie rzeczywistym.
Integracja systemów automatyki przemysłowej (OT) z infrastrukturą technologii informatycznych (IT) polega na połączeniu dwóch kluczowych środowisk funkcjonujących w przedsiębiorstwie produkcyjnym. Jak już wspomniano systemy OT obejmują takie urządzenia, jak sterowniki PLC,
komputery przemysłowe, systemy SCADA, DCS oraz inne, wymienione wyżej technologie kontrolujące procesy przemysłowe, natomiast systemy IT odpowiadają za zarządzanie danymi, za systemy ERP (Enterprise Resource Planning), chmurę obliczeniową oraz inne używane w firmie narzędzia analityczne, sprzedażowe i systemy zarządzania kontaktów z k lientami klasy CRM (Customer Relationship Management). Jak można się domyślić, celem takiej integracji jest synchronizacja operacji produkcyjnych z zasobami informacyjnymi przedsiębiorstwa, co pozwala na pełne wykorzystanie zalet cyfryzacji i automatyzacji procesów produkcyjnych.
Integracja systemów OT z IT wymaga zastosowania szeregu technologii, które pozwalają na wy mianę informacji między systemami operacyjnymi a aplikacjami IT. Po pier wsze, są to różnego rodzaju aplikacyjne interfejsy programistyczne API (Aplication Programming Interface). Umożliwiają one integrację różnych systemów, takich jak systemy auto -
matyki, ERP, SCADA czy chmury obliczeniowej pozwalają na swobodną wymianę danych pomiędzy różnymi platformami. Ułatwiają one też wdrażanie nowych rozwiązań technologicznych w istniejącej infrastrukturze przedsiębiorstwa.
DCS składają się z kilku kluczowych komponentów:
Sterowniki procesowe – Lokalne jednostki kontrolne, które zarządzają określonymi procesami w zakładzie. Każdy sterownik monitoruje dane z czujników i odpowiada za sterowanie urządzeniami, jak np. zawory, pompy czy mieszadła. W przypadku awarii jednego z nich, reszta systemu może nadal funkcjonować bez zakłóceń.
Czujniki i urządzenia wykonawcze – To urządzenia, które zbierają dane o stanie procesu (temperatura, ciśnienie, przepływ itp.) i przekazują je do lokalnych sterowników. Z kolei urządzenia wykonawcze, takie jak zawory czy napędy, realizują polecenia sterowników w celu regulacji parametrów procesowych. Sieć komunikacyjna – Kluczowy element DCS, umożliwiający wymianę danych między sterownikami, czujnikami oraz systemem nadrzędnym. Sieci te muszą być wysoce niezawodne i charakteryzować
się niskim opóźnieniem, aby zagwarantować szybkie i skuteczne reakcje na zmiany w procesach. Współczesne systemy DCS często korzystają z sieci Ethernet przemysłowego, co umożliwia bardziej elastyczną i szybką komunikację.
Interfejs operatora (HMI) – Umożliwia operatorom monitorowanie i sterowanie procesami z poziomu centralnego. Systemy HMI dostarczają operatorom wizualne informacje o stanie procesu oraz pozwalają na interwencję w razie potrzeby. Interfejsy te są często oparte na systemach SCADA, oferując zaawansowane narzędzia do wizualizacji, raportowania i analizy danych.
System zarządzania bazami danych –DCS gromadzi ogromne ilości danych, które są przechowywane i analizowane, co umożliwia długoterminową optymalizację procesów. Zebrane dane można wykorzystać do predykcyjnego utrzymania ruchu, optymalizacji wydajności czy redukcji zużycia energii.
Warto tu też wspomnieć o systemach MES (Manufacturing Execution Systems). Systemy MES działają na styku OT i IT, zapewniając pełną widoczność procesów produkcyjnych oraz integrację z systemami ERP. MES monitorują wykonanie zleceń produkcyjnych, śledzą jakość oraz zbierają dane o stanie maszyn, które mogą być następnie analizowane w systemach ERP lub innych narzędziach IT.
Z kolei obliczenia brzegowe (Edge Computing) są technologią, która pozwala na przetwarzanie danych blisko źródła ich powstawania, czyli w urządzeniach i maszynach znajdujących się na hali produkcyjnej. Wykorzystanie Edge Computingu umożliwia lokalne analizowanie danych, co zmniejsza opóźnienia i redukuje obciążenie sieci, zanim informacje zostaną przesłane do centralnej infrastruktury IT.
Bezpieczeństwo w automatyzacji i produkcji
Automatyzacja procesów produkcyjnych niesie za sobą ryzyko związane z pracą w pobliżu maszyn i robotów przemysłowych. Dlatego niezwykle istotne jest stosowanie rozwiązań
zapewniających bezpieczeństwo pracowników, takich jak kurtyny świetlne, czujniki obecności czy systemy blokujące dostęp do niebe zpiecznych stref.
Kurtyny świetlne to zaawansowane urządzenia bezpieczeństwa stosowane w zautomatyzowanych liniach produkcyjnych. Tworzą one niewidzialną barierę z promieni świetlnych między nadajnikiem a odbiornikiem. W przypadku naruszenia tej bariery – np. przez rękę pracownika – maszyna natychmiast zostaje zatrzymana, co eliminuje ryzyko wypadków. Kurtyny świetlne znajdują zastosowanie przy obsłudze maszyn, gdzie pracownicy muszą mieć bezpieczny dostęp, np. w procesach pakowania lub montażu.
Czujniki obecności są używ ane w strefach zagrożenia, aby wykrywać obecność człowieka w pobliżu maszyny. W momencie, gdy pracownik znajdzie się w zasięgu działania maszyny, czujniki zatrzymują jej pracę, co zapobiega wypadkom. Zastosowanie tech-
nologii takich jak czujniki optyczne, ultradźwiękowe czy termiczne zwiększa poziom bezpieczeństwa przy jednoczesnym minimalizowaniu ryzyka w trakcie obsługi maszyn. Blokady bezpieczeństwa są mechanizmami, które uniemożliwiają pracownikom dostęp do ruchomych części maszyn, gdy te są w stanie pracy. Przykładem są drzwi ochronne wyposażone w czujniki, które automatycznie wyłączają maszynę, gdy drzwi są otwarte. Takie rozwiązania są niezbędne przy obsłudze linii produkcyjnych, gdzie istnieje ryzyko kontaktu z niebezpiecznymi elementami. Zapewnienie bezpieczeństwa produkcji obejmuje nie tylko ochronę ludzi, ale także maszyn, urządzeń i całych procesów technologicznych. W celu zagwarantowania zgodności z międzynarodowymi standardami, zakłady produkcyjne muszą spełniać określone normy oraz uzyskiwać certyfikaty, które potwierdzają ich zgodność z przepisami. Wymienić tu moż-
na normy ISO, takie jak ISO 13849 (Bezpieczeństwo maszyn – Części układów sterowania związane z bezpieczeństwem) czy ISO 45001 (Systemy zarządzania bezpieczeństwem i higieną pracy), które określają wymogi dotyczące projektowania i wdrażania systemów automatyki w sposób zapewniający bezpieczeństwo operatorów i procesów produkcyjnych. Przestrzeganie tych norm jest kluczowe dla zakładów produkcyjnych, które chcą działać zgodnie z międzynarodowymi standardami i zapewnić najwyższy poziom bezpieczeństwa.
dr inż. Marcin Bieńkowski AUTOMATYKA
Materiały źródłowe:
[1] Materiały firmy Inrel Engineering Services, www.inrel.pl
[2] Janusz Kwaśniewski, Sterowniki PLC w praktyce inżynierskiej, Wydawnictwo BTC, Legionowa 2008
[3] Materiały firmy ASTOR
[4] Materiały firmy Schneider Electric
Przedsiębiorstwa produkcyjne stoją obecnie przed tak dużą liczbą wyzwań, jak chyba nigdy dotąd w historii. Cyfryzacja, zmieniające się modele biznesowe, indywidualne preferencje odbiorców, komplikacje w łańcuchach dostaw, rotacja i brak kadr, inflacja i rosnące koszty surowców i energii czy wreszcie zrównoważony rozwój, czyli zmniejszanie negatywnego wpływu na środowisko, to tylko najważniejsze z nich.
Zmiany są konieczne, bez nich przedsiębiorstwa tracą na tle konkurencji, wstrzymują swój rozwój albo wręcz się cofają. Z pomocą przychodzą nowe technologie i rozwiązania. O ile duże jednostki chętniej i śmielej zmieniają sposób funkcjonowania, o tyle małe i średnie przedsiębiorstwa są bardziej ostrożne w dokonywaniu zmian. Przyczyn jest wiele, ale kluczowa jest chyba konieczność inwestowania w nowe technologie i narzędzia, a to niestety kosztuje. Jak zatem sobie z tym radzić? Jedną z opcji jest realizacja działań małymi krokami, na początek w jednym wybranym obszarze. Czasem niewielkie zmiany i inwestycje przynoszą bardzo zauważalne korzyści w funkcjonowaniu firm i zbliżają je widocznie do wyznaczanych standardów, pozwalających na pozostanie w grze. Poniżej podajemy kilka przykładów rozwiązań, które przy relatywnie niewielkich inwestycjach optymalizują procesy i obniżają koszty funkcjonowania.
Systemy Pick-by-Light to idealne rozwiązanie wspomagające pracowni-
ków m.in. przy kompletacji zamówień czy skomplikowanych montażach. Nużące, powtarzalne operacje pobrania komponentów montażowych czy pozycji zamówień realizowanych na podstawie papierowej dokumentacji prędzej czy później nieuchronnie wygenerują błędy ludzkie, które spowodują braki jakościowe czy dodatkowe koszty związane z wysyłką niewłaściwie spakowanych elementów. Pick-by-Light to nic innego, jak system sygnalizacji świetlnej, który na podstawie zamówień czy dokumentacji technicznej prowadzi pracownika krok po kroku, wskazując właściwą kuwetę do pobrania części oraz pilnując sekwencji pobierania i ilości. Doskonale przyspiesza procesy, eliminuje błędy w wysyłkach, poprawia jakość finalnych produktów. Bardzo duże znaczenie ma użyteczność systemów Pick-by-Light w procesach wdr ożenia nowych pracowników. Braki i rotacja kadr to zjawisko powszechne, z którym mierzą się wszyscy przedsiębiorcy. Dzięki systemowi Pick-by-Light wdrożenie nowego pracownika na stanowisku montażu czy kompletacji czasem skraca się z wielu
dni do kilku godzin. Odpowiednio zaprojektowany interfejs użytkownika pomaga też w przypadku barier językowych. Nie jest przecież problemem, aby panel operatorski – gdzie programuje się sekwencje procesu –zawierał kilka opcji językowych, które można szybko i łatwo zmieniać, jak w przypadku wyboru języka w laptopie czy na komórce.
Automatyzacja zbierania i analizy danych
Temperatura i wilgotność to parametry, które w wielu obszarach produkcji oraz składowania gotowych wyrobów muszą być stale kontrolowane, aby zapewnić deklarowaną przez producenta i oczekiwaną przez klienta jakość. Sprawdzanie parametrów i ich raportowanie manualnie jest zwykle żmudne i zabiera sporo czasu, szczególnie w dużych obszarach magazynowych i z dużą liczbą wymaganych punktów pomiarowych. Zbieranie tych danych, ich dokumentowanie oraz sposób prezentacji można łatwo i niedrogo zautomatyzować. Dzięki temu nie angażujemy personelu, zapobiegamy stratom oraz ograniczamy do minimum możliwość manipulacji danymi. Automatyzacja zbierania danych i raportowania pozwala na efektywniejsze wykorzystanie zasobów ludzkich. System powiadamiania zdalnie przez SMS/e-mail, lokalnie na panelu operatorskim czy za pomocą sygnalizacji świetlnej umożliwia szybkie reagowanie na nie właściwe parametry środowiskowe, co pozw ala na ograniczenie strat wynikających z nie właściwego składowania gotowych wyrobów. System jest niezależny od istniejących systemów sterowania czy monitoringu, a ponadto zwykle nie ingeruje w istniejącą infrastrukturę teleinformatyczną. Dostęp do danych w każdym czasie i miejscu jest możliwy dzięki serwisom w chmurze. Kontrola i dokumentowanie warunków środowiskowych są wykorzystywane w wielu aplikacjach, m.in. przy składowaniu wyrobów spożywczych, kontroli przechowywania leków, magazynowaniu wyrobów stalowych czy zapewnieniu właściwej temperatury w halach produkcyjnych.
Predykcyjne utrzymanie ruchu
Zmiana podejścia i sposobu funkcjonowania może dotyczyć nie tylko obszaru produkcji oraz logistyki, ale także utrzymania ruchu. Najbardziej popularny model funkcjonujący nadal w większości zakładów produkcyjnych to strategia prewencyjna opierająca się na planowanych i regularnych przeglądach i konserwacjach, mających minimalizować wystąpienie awarii i utrzymywać majątek produkcyjny w możliwie najlepszej kondycji. Alternatywą jest predykcja, czyli przewidywanie i zapobieganie awariom na podstawie obserwacji trendów zmian istotnych parametrów diagnostycznych maszyn i urządzeń. Planowanie czynności konserwacyj-
nych odbywa się wtedy, kiedy jest konieczne, a nie zgodnie z założonym harmonogramem. Inaczej mówiąc: „nie naprawiaj, jeśli nie jest zepsute”. W praktyce predykcyjne utrzymanie ruchu opiera się głównie na danych o stanie wibracji kluczowych maszyn. Odpowiednio umiejscowione czujniki (zwykle jeden lub dwa na maszynę) dostarczają danych systemowi, który umożliwia obserwację trendów zmian, alarmuje o przekroczeniach oraz pozwala na symulacje i określenie czasu do wystąpienia potencjalnej awarii. Tak zorganizowane utrzymanie ruchu daje świetne rezultaty, pozwala na lepsze planowanie i podejmowanie trafnych decyzji biznesowych, a to przekłada się na mniejsze koszty UR. Do osiągnięcia satysfakcjonujących rezultatów w pre-
dykcji nie trzeba stosować drogich zaawansowanych systemów do analizy wibracji, wystarczą standardowe czujniki, których koszt jest naprawdę nieduży (zwykle 1000–2000 zł). Do prezentacji danych można użyć dedykowanego software’u, ale równie dobrze można włączyć czujniki np. do istnie-
jącego systemu SCADA i z jego pomocą analizować trendy czy alarmować o przekroczeniach. Z dostępnych w różnych źródłach analiz wynika, że dzięki strategii predykcyjnej można uzyskać oszczędności rzędu przynajmniej 8–10 %. Z perspektywy przedsiębiorstwa jest więc o co walczyć.
To trzy przykłady, które bez wielomilionowych inwestycji widocznie usprawnią procesy i przyniosą policzalne oszczędności. Takie i wiele innych aplikacji, optymalizujących produkcję, logistykę i utrzymanie ruchu, pomaga zrealizować kompleksowo Dział Solution w Turck Polska. Opracowuje koncepcje, dobiera aparaturę, szacuje koszty i nadzoruje wykonanie i rozruch aplikacji. Wszystkie projekty firmuje marką Turck, a realizuje je, bazując na sieci rzetelnych i doświadczonych firm integratorskich programu Turck Solution Partner. Więcej szczegółów można znaleźć na stronie www.turcksolution.pl.
TURCK Sp. z o.o.
ul. Budowlanych 131/4, 45-123 Opole tel. +48 77 4434 800 e-mail: poland@turck.com www.turck.pl
Opatentowana przez firmę
Bosch Rexroth funkcja regulacji temperatury prowadnic liniowych i napędów śrubowych zwiększa precyzję, wydajność i modułowość obrabiarek. Gwarantuje większą stabilność procesów, krótsze czasy cykli, więcej prawidłowych części dzięki rozpoczęciu produkcji bez rozruchu oraz zwiększenie dokładności wytwarzania nawet o 75 %.
Innowacyjna technika liniowa optymalizuje działanie nowoczesnych obrabiarek. Oferowana przez Bosch Rexroth nowa opcja regulacji temperatury sprawia, że prowadnice szynowe profilowe i mechanizmy śrubowe działają z jeszcze większą precyzją i wydajnością w tej samej przestrzeni montażowej. To ekonomiczne rozwiązanie stabilizuje procesy obróbki w obrabiarkach oraz pozwala zminimalizować liczbę wybrakowanych produktów i zaoszczędzić materiał. Przyspiesza też rozpoczęcie produkcji i skraca czasy cykli. Użytkownicy mają do dyspozycji różne pakiety wydajnościowe, które można ekonomicznie stosować w dotychczasowych i nowych obrabiarkach.
Producenci maszyn, którzy chcą utrzymać swoją pozycję rynkową w sektorze wysoce precyzyjnych urządzeń, potrzebują innowacji pozwalających na jeszcze stabilniejsze odwzorowywanie procesów bez nadmiernych kosztów. Zintegrowana regulacja temperatury w technice liniowej to ekonomiczne rozwiązanie, które poprawia parametry termiczne prowadnic liniowych i komponentów napędowych uczestniczących w procesie. Przynosi
to korzyści m.in. w postaci frezowania z dużą prędkością i precyzją.
Prowadnice szynowe profilowe i napędy śrubowe z opcjonalną funkcją regulacji temperatury wykorzystują systemy rur, które są zintegrowane bezpośrednio z prowadnicą lub wrzecionem mechanizmu śrubowego i umożliwiają łatwe podłączenie do centralnego układu chłodzenia w maszynie. W ten sposób z prowadnicy liniowej można odprowadzać energię powstającą w wyniku tarcia. Dzięki podgrzewaniu wstępnemu można szybko osiągnąć idealną temperaturę roboczą, maszyna jest więc gotowa do pracy bez konieczności rozruchu i pracuje bezbłędnie już przy obróbce pierwszej części. Zwiększa to produktywność przy jednoczesnej minimalizacji liczby wadliwych produktów i zużycia materiałów.
Dostępność
Bosch Rexroth oferuje funkcję regulacji temperatury jako opcję dla wszystkich standardowych wymiarów prowadnic szynowych kulkowych i rolkowych, a także dla napędów śrubowo-tocznych i planetarnych napędów śrubowych. Opatentowane rozwiązanie Thermo Compensating Rail System (TCRS) dla prowadnic szynowych profilowych jest dostępne jako opcja dla zintegrowanego systemu pomiarowego IMS. W ten sposób firmie Bosch Rexroth po raz pierwszy udało się połączyć trzy funkcje – prowadzenie, pomiar i regulację temperatury – w bardzo kompaktowym rozwiązaniu umożliwiającym modernizację. W wyniku zintegrowania funkcji enkodera liniowego i opcjonalnego systemu TCRS z prowadnicą szynową profilową można realizować lub modernizować aplikacje o najwyższej dokładności przy minimalnych kosztach konstrukcyjnych i eksploatacyjnych, bez dodatkowej przestrzeni montażowej.
Modułowe pakiety
W przeciwieństwie do rozwiązań niezintegrowanych, oferowana przez Bosch Rexroth opcja regulacji temperatury, nie wymaga zewnętrznych systemów chłodzenia ani dodatkowej przestrzeni montażowej. Dzięki temu bez dużych nakładów można realizować bardzo wydajne aplikacje o tych samych właściwościach mechanicznych. Pozwala to również minimalnym kosztem przekształcać istniejące instalacje w precyzyjne maszyny lub oferować różne pakiety wydajnościowe dla istniejących koncepcji maszyn, aż po modernizację. Takie modułowe podejście sprawia, że oferowana przez firmę Bosch Rexroth zintegrowana regulacja temperatury zwiększa konkurencyjność w branży produkcji obrabiarek.
Zintegrowana regulacja temperatury w technice liniowej to ekonomiczne rozwiązanie, które poprawia aspekty termiczne prowadnic liniowych i komponentów napędowych uczestniczących w procesie.
BOSCH REXROTH Sp. z o.o. ul. Jutrzenki 102/104, 02-230 Warszawa tel. 22 738 18 00 e-mail: info@boschrexroth.pl www.boschrexroth.pl
Roboty kolaboracyjne – koboty – istotnie wspierają producentów w zwiększaniu produktywności. Są silne, szybkie i proste w użyciu, dzięki czemu mogą sprawić, że procesy produkcyjne staną się bardziej wydajne, a sama działalność – bardziej konkurencyjna. Dziś przyjrzymy się temu, co robią koboty, jak wspierają produkcję i jak rozwija się firma Kassow Robots od czasu przejęcia większości jej udziałów przez Bosch Rexroth.
Wiele wydarzyło się, odkąd duński producent kobotów stał się częścią Bosch Rexroth. Dzięki przeprowadzce do nowej lokalizacji możliwe stało się zwiększenie mocy produkcyjnych w bardzo profesjonalny sposób i znaczna poprawa wydajności produkcji. Zespół powiększył się zarówno w Kopenhadze, gdzie firma została założona, a także w oddziale w Pradze oraz w zespole sprzedaży z siedzibą w Ulm. Firma Kassow Robots znacznie rozszerzyła swoją globalną działalność sprzedażową, uczestnicząc w targach branżowych w wielu krajach oraz w wydarzeniach organizowanych przez firmę Bosch Rexroth.
Nieprzerwany rozwój rynku robotów kolaboracyjnych
Siedmioosiowy kobot firmy Kassow Robots
Roboty kolaboracyjne to ważny element inteligentnej produkcji oraz skuteczny sposób redukcji kosztów przy jednoczesnym zabezpieczeniu produkcji w obliczu obecnych braków siły roboczej. Są one coraz częściej wykorzystywane w przemyśle do automatyzacji procesów realizowanych w tej samej przestrzeni roboczej, w której pracują ludzie. Umożliwiają małym i średnim przedsiębiorstwom realizację automatyzacji z udziałem własnego personelu, ponieważ koboty mogą być łatwo programowane i obsługiwane przez niemal każdego. Już teraz zapotrzebowanie na nie jest duże, a r ynek ten nadal będzie się rozwijał.
Koboty mogą z łatwością wykonywać szereg różnych zadań oraz udostępniają wiele elastycznych opcji automatyzacji, które niosą ze sobą znaczne korzyści:
• można je łatwo zintegrować z procesem produkcyjnym przy minimalnych zmianach w pozostałej części linii – zapewniając w ten sposób
opłacalny punkt wejścia do automatyzacji z użyciem robotów, którą z czasem można rozszerzać,
• są szybkie i dokładne, co poprawia wydajność produkcji i pomaga obniżyć ogólne koszty operacyjne,
• pracują bezpiecznie ramię w ramię z ludźmi,
• przejmują pracochłonne lub powtarzalne czynności, pozwalając pracownikom skupić się na zadaniach o większej wartości dodanej, co pomaga rozwiązać problem niedoboru umiejętności.
Siedem osi i duża elastyczność
W firmie Bosch Rexroth postrzegamy koboty jako ważną i wszechstronną gałąź przyszłościowych rozwiązań automatyzacji przemysłu. To właśnie dlatego rozszerzyliśmy naszą ofertę produktów o roboty współpracujące firmy Kassow Robots. Firma ta opracowuje, produkuje i sprzedaje unikatowe i wydajne siedmioosiowe lekkie roboty współpracujące do zastosowań przemysłowych. Są one niezwykle przyjazne dla użytkownika, dzięki czemu zapewniają firmom dużą elastyczność oraz umożliwiają, małym i średnim przedsiębiorstwom bez własnych specjalistów ds. robotyki, realizację złożonej automatyzacji oraz programowanie w opłacalny i niezależny sposób.
Firma Kassow Robots zaprojektowała swoje roboty z myślą o pracy w najciaśniejszych przestrzeniach produkcyjnych. Zostały one wyposażone w siedem osi, potrafią sięgać za narożniki, tak jak ręce człowieka, i podnosić ładunki o masie do 18 kg. Obecnie rodzina produktów obejmuje pięć modeli robotów współpracujących o zasięgu 850–1800 mm i prędkości przegubów do 225 stopni na sekundę.
Nieustannie opracowywane są nowe produkty. Na tegorocznych targach Automatica w Monachium firma Kassow Robots zaprezentowała rozwiązanie Edge Series: prototyp kontrolera zintegrowanego z podstawą kobota. Brak konieczności umieszczania dodatkowej szafy sterowniczej w pobliżu robota sprawia, że siedmioosiowe roboty współpracujące mogą być wykorzystywane w jeszcze bardziej elastyczny sposób i z użyciem mniejszej ilości miejsca, co jest bardzo ważne w przypadku zastosowań mobilnych, takich jak roboty autonomiczne AMR (Autonomous Mobile Robot).
Przygotowania do dalszego rozwoju Dzięki większościowemu udziałowi Bosch Rexroth firma Kassow Robots rozszerza obecnie swoją działalność produkcyjną i sprzedażową na całym świecie. Z Kristianem Kassowem, dyrektorem generalnym i współwłaścicielem stojącym na czele firmy, zespół jest gotowy do wprowadzenia swoich produktów na światową scenę przez udział w targach i wydarzeniach wewnętrznych, a także rozwój sieci partnerów handlowych. Obecnie grono obejmuje ponad 60 partnerów na całym świecie, a liczba ta stale rośnie.
Aby wspierać dalszy rozwój, rok temu firma Kassow Robots przeniosła się do nowej siedziby. Nowoczesny budynek w Kastrup, blisko Kopenhagi, zapewnia wystarczającą przestrzeń nie tylko do zwiększania mocy produkcyjnych, ale także na potrzeby działań rozwojowych i zaplecza biurowego. Większa zdolność produkcyjna oznacza również większą przestrzeń do testowania – po montażu roboty kolaboracyjne przechodzą zautomatyzowany program testowy, zanim zostaną zapakowane i przygotowane do dostawy.
– Ostatnie półtora roku przebiegło pod szyldem ekscytującego i pełnego wyzwań procesu skalowania, który z powodzeniem opanowaliśmy dzięki naszemu wysoce zmotywowanemu zespołowi. Oczywiście naszym głównym celem jest dostarczanie najnowocześniejszych technologii w wysokiej jakości, zgodnie z wymogami rynku – mówi Kristian Kassow, dyrektor generalny Kassow Robots.
Jak koboty współpracują z produktami Bosch Rexroth?
Wszystkie pięć typów lekkich kobotów Kassow Robots komunikuje się płynnie z platformą sterowania ctrlX CORE. Dodatkowo stale rozbudowywany jest ekosystem sterowników, które ułatwiają konfigurację urządzeń peryferyjnych komunikujących się z robotami, takich jak chwytaki i kamery. W efekcie liczba kompatybilnych narzędzi i urządzeń na końcu ramienia robota stale rośnie, co sprawia, że praktycznie każdego dnia rośnie również zakres ich zastosowań.
Duże zamówienie od Project Service & Production
Firma Project S&P, integrator systemów i klient Kassow Robots specjalizujący się w optymalizacji procesów produkcyjnych, opracowała rozwiązanie automatyzacji dla przemysłu tekstylnego, którego zadaniem jest wspieranie procesu podawania szpul do maszyn.
Aby zapewnić płynną zmianę szpul przędzy, firma Project S&P opracowała i zbudowała mobilne rozwiązanie manipulacyjne z wykorzystaniem robota współpracującego. Zautomatyzowane pojazdy zostały wyposażone w specjalny magazyn, system obsługi i kobota KR1018 firmy Kassow Robots. Częścią rozwiązania jest oś liniowa, dzięki której kobot może podawać szpule do maszyn na różnych wysokościach.
Oprócz przejęcia ręcznych zadań związanych z obsługą bardzo dużych ciężarów, możliwości automatyzacji siedmioosiowego robota KR1018 przyczyniają się do płynniejszej zmiany pakietów przędzy. W efekcie oszczędności są osiągane na trzech poziomach: przez redukcję kosztów personelu, lepszą jakość otrzymywaną w tym samym czasie (dzięki delikatniejszej obsłudze opakowań) oraz możliwość śledzenia materiałów – a wszystko to dzięki zastosowaniu tego rozwiązania do automatyzacji. Nie byłoby to możliwe w przypadku konwencjonalnego robota sześcioosiowego. Sukces tego rozwiązania spowodował, że większa liczba robotów kolaboracyjnych jest obecnie dostarczana do klienta.
Jeśli chcesz dowiedzieć się więcej o Kassow Robots, zeskanuj kod QR.
z o.o.
Jutrzenki 102/104 02-230 Warszawa tel. 22 738 18 00 e-mail: info@boschrexroth.pl www.boschrexroth.pl
Współczesny przemysł staje przed coraz większymi wyzwaniami związanymi z koniecznością optymalizacji procesów produkcyjnych, ograniczania zużycia energii oraz minimalizacji kosztów operacyjnych. W dobie rosnącej konkurencji i zaostrzających się regulacji środowiskowych, zakłady przemysłowe są zmuszone do inwestycji w technologie, które pozwalają na lepsze monitorowanie i zarządzanie zasobami. Kluczowym narzędziem w tym zakresie są nowoczesne technologie pomiarowe, które nie tylko dostarczają precyzyjnych danych o zużyciu energii, wody czy innych surowców, ale także pomagają zwiększać efektywność procesów produkcyjnych i zmniejszać straty, a co za tym idzie – generować znaczące oszczędności.
Energia jest jednym z największych kosztów operacyjnych w przemyśle, a zarządzanie nią w sposób efektywny to klucz do sukcesu każdego zakładu produkcyjnego. Nowoczesne technologie pomiarowe, takie jak ultradźwiękowe przepływomierze i liczniki ciepła, stanowią podstawę monitorowania rzeczywistego zużycia energii w różnych częściach zakładu. Zrozumienie, ile ciepła i energii jest faktycznie potrzebne do zasilania maszyn, ogrzewania przestrzeni roboczych czy procesów produkcyjnych, pozwala na lepsze zarządzanie tymi zasobami.
Przykładem zaawansowanego narzędzia do pomiaru energii jest ultradźwiękowy i przenośny ciepłomierz KATflow 230 firmy Katronic, który umożliwia monitorowanie przepływu ciepła
w systemach grzewczych i chłodniczych bez konieczności ingerencji w rur y czy instalacje. Urządzenie dokonuje pomiaru w pełni bezinwazyjnie, dzięki zastosowaniu wysokiej jakości sond oraz czujników montowanych bezpośrednio na rurociągu. Dzięki zasilaniu akumulatorem, użytkownik KATflow 230 może dokonywać pomiarów wszędzie tam, gdzie to potrzebne, bez konieczności zapewnienia dostępu do sieci elektrycznej bądź ograniczoną przestrzeń.
Monitorowanie przepływu ciepła
W jednym z przypadków, brytyjski dostawca systemów grzewczych wykorzystuje KATflow 230 do monitorowania przepływu ciepła w obiektach przemysłowych, takich jak szpitale czy duże fabryki żywności. W celu doboru właści-
wego systemu grzewczego dla klienta, dostawca montował sondy wykonane ze stali nierdzewnej na rurociągach z gorącą wodą, tak blisko głównego wymiennika ciepła, jak to możliwe. Czujniki temperatury Pt 100, zainstalowane na rurach dopływu i powrotu, rejestrują temperaturę, która zintegrowana z pomiarem przepływu, pozwala uzyskać bezpośredni pomiar ciepła rzeczywistego i całkowitego zużycia ciepła w systemie, jak i – co najważniejsze – szczytowego zapotrzebowania na energię w całej sieci.
Firma stosuje przenośny ciepłomierz ultradźwiękowy KATflow 230 w każdym projekcie. Cytując jednego z inżynierów tej firmy: „Przepływomierz KATflow 230 jest dla nas naprawdę ważnym narzędziem. Mieliśmy wiele projektów, w których było naprawdę trudno ocenić obciążenie kotłowni, ale miernik KATflow pozwolił nam rejestrować przepływy, zobaczyć liczby i szczytowe zapotrzebowanie, a dzięki temu składać rzetelne oferty naszym klientom”.
Dzięki pomiarom ciepła, wykonawca systemów grzewczych może udowodnić klientom, że oferty przez niego składane są tworzone w oparciu o rzeczywiste zapotrzebowanie na energię. W wielu przypadkach doprowadziło to do bardzo znaczących oszczędności w zużyciu energii, a w co najmniej jednym przypadku przełożyło się na roczne oszczędności przekraczające aż 500 000 funtów.
Pomiary KATflow 230 zostały już wykorzystane przez tę firmę w ponad 20 dużych badaniach wymienników
ciepła, w tak różnych zastosowaniach, jak opieka zdrowotna i szpitale ogólne, fabryki żywności i napojów, cukiernia i mleczarnia. Zapewniają klientom generowanie znaczących oszczędności kosztów oraz zmniejszają emisję dwutlenku węgla, co potwierdza przydatność tego typu technologii w nowoczesnych zakładach
Optymalizacja zużycia wody i ścieków
Woda jest kolejnym kluczowym zasobem stosowanym w zakładach przemysłowych. W wielu branżach, takich jak przemysł spożywczy, chemiczny czy farmaceutyczny, zużycie wody jest ogromne, a niewłaściwe zarządzanie może prowadzić do marnotrawstwa oraz nadmiernej produkcji ścieków. W obecnych czasach, gdy dbałość o minimalizację zużycia zasobów, a tym samym dbanie o środowisko, jest stawiane wśród najwyższych priorytetów i wyzwań przemysłu, zarówno właściciele zakładów, jak i producenci
technologii pomiarowych, stają przed koniecznością rozwijania i wprowadzania narzędzi, pozwalających osiągnąć te cele. Tego rodzaju inwestycje często kojarzą się z wielkim wydatkiem i projektami wartymi miliony dolarów. Nie zawsze jednak jest to konieczne. Często istniejąca struktura procesów produkcyjnych oferuje duży potencjał do działania przy minimalnych inwestycjach.
Tego rodzaju rozwiązanie wprowadziła firma Seli GmbH Automatisierungstechnik w zakładach jednego z potentatów branży piwowarskiej. To doskonały przykład zastosowania nowoczesnych technologii pomiarowych do optymalizacji procesów produkcji.
Firma Seli GmbH to producent nowoczesnych technologii pomiarów i analizy właściwości cieczy, w tym pomiarów mętności i przewodności. Wychodząc naprzeciw potrzebom rynku, Seli od wielu lat koncentruje się na rozwoju urządzeń, które mo -
głyby niezawodnie i szybko wykrywać zmiany właściwości produktów w aplikacjach higienicznych. Jak wiadomo, monitorowanie procesów filtracji, separacji faz czy procesów CIP/SIP, jest niezbędnym elementem we wszelkich zakładach przetwórczych, zapewniającym prawidłowe funkcjonowanie systemu oraz uzyskanie najwyższej jakości produktu. Dotychczasowe rozwiązania dostępne na r ynku napotykały problem wydajności, wynikający z konstrukcji urządzeń.
Firma Seli GmbH skupiła się na tym zagadnieniu i dzięki temu stworzyła czujniki pomiaru przewodności i mętności, w których czas odpowiedzi zredukowano do minimum. Pozwa-
la to na bardzo szybkie wykrywanie zmian, a co za tym idzie, szybkie podejmowanie decyzji w zakładach przetwórczych. Dodatkowo konstrukcja urządzeń zapobiega gromadzeniu się zanieczyszczeń na czujnikach, a tym samym ogranicza potrzebę przeprowadzania konserwacji, czyszczenia urządzenia czy niepożądanych błędów pomiarowych, gwarantując długą i niezawodną pracę.
Dzięki zastosowaniu rozwiązań Seli GmbH, zakład browarniczy mógł nie tylko zmniejszyć zużycie wody, ale także ograniczyć ilość ścieków produkowanych w procesach czyszczenia. Precyzyjne pomiary umożliwiły także poprawę jakości produktów i zopty-
malizowanie całego procesu produkcji. Wiąże się to z redukcją kosztów i poprawą jakości we wszystkich procesach produkcyjnych.
Menedżer ds. automatyki tak opisał swoje doświadczenie z urządzeniami Seli GmbH: Od kilku lat z powodzeniem stosujemy najnowszą technologię pomiarową firmy Seli GmbH do kontroli procesów. Urządzenia do pomiaru mętności kontrolują i monitorują nasze produkty w procesach filtracyjnych oraz kontrolują nasze separatory. Dzięki tym nowym urządzeniom pomiarowym, mogliśmy całkowicie wyeliminować użycie powietrza procesowego w porównaniu z urządzeniami używanymi wcześniej. Wcześniej stosowane urządzenia miały problem z zaparowywaniem optyki, co przekładało się na błędy w wynikach pomiarów i wynikające z nich fluktuacje produktu. Dzięki wymianie na technologię Seli GmbH problem został rozwiązany i nie powtórzył się. Od czasu wdrożenia urządzeń znacznie zmniejszono odstępy między przeglądami i związane z nimi koszty. Rezultatem jest dodatkowe bezpieczeństwo produktu, oszczędności wody i ścieków oraz redukcja kosztów czyszczenia. W innych naszych procesach konieczne jest rozdzielanie faz. Szybkie i nie zawodne wykrywanie zmian i kontrolowanie naszych produktów, wody procesowej oraz cykli czyszczenia ma kluczowe znaczenie. Dzięki zastosowaniu urządzeń do pomiaru mętności i przewodności firmy Seli GmbH, dysponujemy najszybszymi obecnie dostępnymi urządzeniami. Wykrycie prawidłowej wartości pomiaru może trwać od 70 ms do 9 s, w zależności od zastosowania. W porównaniu z poprzednio stosowanymi metodami, osiągamy znaczne oszczędności we wszystkich obszarach. Mniej ścieków, mniej świeżej wody, więcej produktu w butelce. Ponadto nowa technologia pomiarowa gwarantuje bardzo wysoką stabilność. Mniej awarii urządzeń, mniej konserwacji, mniej czyszczenia... Łatwe do sprawdzenia, kalibracji i uruchomienia! […] Jeśli chodzi o możliwości zwiększenia wydajności naszych procesów, zwrot z inwestycji w tę technologię pomiarową jest doskonały.
Urządzenia do analizy i monitorowania właściwości cieczy produkcji Seli GmbH pozwalają optymalizować procesy nowoczesnych zakładów. Rezultatem szybkiego wykrywania problemów jest mniej strat zasobów, takich jak woda/ścieki, mniej strat w produkcie, oszczędność energii i czasu, a przede wszystkim najszybsze wykrywanie zanieczyszczeń i wtrąceń produktu w obiegach ciepła lub zimna. Dzięki wieloletniemu doświadczeniu w tych obszarach Seli GmbH może czerpać z setek już wdrożonych aplikacji i pomagać klientom osiągnąć doskonałe rezultaty przy możliwie niskich nakładach finansowych.
Ekonomiczne rozwiązania do pomiarów przepływu masowego
Firma systec Controls, zajmująca się rozwojem i produkcją innowacyjnych urządzeń dla pomiaru przepływu, podeszła do tematu z innej strony. Jej celem było opracowanie technologii umożliwiającej osiągnięcie precyzyjnych wyników pomiarów przepływu metodą pomiaru różnicy ciśnień, przy jednoczesnym zachowaniu szerokiej funkcjonalności i przyjazności użytkowania przepływomierza.
Dzięki współpracy z Uniwersytetem Fryderyka Aleksandra w Erlangen i Nor ymberdze, firma systec Controls opracowała zupełnie nową konstrukcję rurki Pitota. Inspiracją dla nowego kształtu rurki było profilowanie skrzydeł samolotowych, opracowane przez
Porównanie strat ciśnienia na (od góry) kryzie, zwężce Venturiego i rurce Pitota deltaflow produkcji systec Controls
NACA (National Advisory Committee for Aeronautics).
Udoskonalony profil sondy powoduje, że opływające ją medium przyspiesza, a nowy kształt krawędzi dodatkowo redukuje problem dryftu i tzw. punktu odcięcia. Dzięki tym właściwościom uzyskiwana jest wyższa różnica ciśnień, a tym samym wyższa dokładność pomiaru. Dodatkowo stało się także możliwe osiągnięcie precyzyjnych pomiarów przy niskich
prędkościach przepływu – rozwiązano problem, z którym zazwyczaj borykają się standardowe przepływomierze różnicy ciśnień.
Opatentowana konstrukcja sondy wykorzystana w przepływomierzach deltaflow systec Controls czyni ją wyjątkową w szerokiej gamie dostępnych na r ynku przepływomierzy różnicy ciśnień i stanowi rewolucję wśród rurek Pitota. Dzięki tak dokładnym pomiarom, przy jednoczesnej niskiej stracie
ciśnienia, użytkownik może osiągnąć znaczną redukcję zużycia energii na instalacji.
Producent aparatury zdawał sobie jednak sprawę z tego, że w przypadku pomiaru przepływu z wykorzystaniem różnicy ciśnień, sporym wyzwaniem dla użytkownika może być konieczność wprowadzenia w prz etworniku ciśnienia wielu parametrów l ub przeprowadzenia samodzielnie skomplikowanych obliczeń, co jest konieczne do u zyskania przepływu objętościowego i masowe go mierzonego medium. Często wymaga to wiedzy eksperckiej oraz żmudnego programowania przetworników czy sterowników, by można było rozpocząć prawidłowy pomiar przepływu. Inżynierowie z firmy systec Controls skupili się również na tym problemie. Wynikiem ich działań jest wieloparametrowy przetwornik przepływu masowego SYSMMF. Urządzenie jest wyjątkowo przyjazne w obsłudze, a do rozpoczęcia pomiarów wymaga wprowadzenia zaledwie kilku parametrów: typu medium, współczynnika przepływu (FlowCoef) i współczynnika kompensacji ekspansji (KEPS), które są dostarczane wraz z przetwornikiem. Dzięki temu, przetwornik można łatwo skonfigurować i szybko rozpocząć pomiary. Aby dodatkowo wspomóc użytkowników, systec Controls udostępnia również darmowe oprogramowanie do obliczeń Deltacalc, które w sposób prosty i czytelny umożliwia dobór przepływomierzy czy weryfikację parametrów. Przetworniki SYS MMF działają w oparciu o pomiar różnicy ciśnień (dp), ciśnienia absolutnego (pabs) oraz temperatury (mierzonej za pomocą zewnętrznego czujnika Pt 100, trójprzewodowego). Na podstawie tych trzech pomiarów urządzenia obliczają natężenie przepływu masowego, objętościowego oraz zliczają przepływ całkowity. Funkcje te umożliwiają kompleksowe monitorowanie mediów, dzięki czemu zwiększane jest bezpieczeństwo i efektywność procesów produkcyjnych. Przetworniki uzyskują dokładność 0,5 % spełniającą wymagania większości aplikacji.
Przetwornik SYSMMF w połączeniu z przepływomierzem deltaflow systec Controls stanowi kompaktowe, wysokoprecyzyjne i ekonomiczne rozwiązanie dla pomiaru przepływu masowego. Ta kombinacja jest optymalna nie tylko pod względem kosztu zakupu. Pozwala na generowanie dodatkowych oszczędności. Pomiary wieloparametrowe SYSMMF wykluczają konieczność wprowadzenia do instalacji dodatkowych urządzeń, a niski spadek ciśnienia osiągnięty przez deltaflow redukuje koszty energii.
warunków procesowych umożliwiają dodatkowo zachowanie ciągłości i bezpieczeństwa procesów.
Wprowadzenie zaawansowanych systemów monitorowania i automatyzacji procesów przynosi również korzyści w postaci ograniczenia interwencji człowieka. W praktyce oznacza to nie tylko oszczędności związane z kosztami pracy, ale także większą przewidywalność operacji oraz mniejsze ryzyko wystąpienia błędów, wynikających z działania operatorów.
Wieloparametrowy przetwornik różnicy ciśnień SYS-MMF
Podsumowanie
Nowoczesne technologie pomiarowe odgrywają kluczową rolę w optymalizacji procesów przemysłowych, redukcji kosztów operacyjnych oraz zmniejszaniu zużycia zasobów. Dzięki precyzyjnym systemom pomiarowym, zakłady przemysłowe mogą generować znaczące oszczędności energii, wody i surowców, jednocześnie poprawiając jakość swoich produktów i zwiększając efektywność operacyjną. Brak konieczności przeprowadzania dodatkowych prac konserwacyjnych oraz możliwość szybkiej reakcji na zmiany produktu czy
Opisane przykłady udowadniają, że mimo iż wdrożenie nowoczesnych technologii pomiarowych wiąże się z pewnymi kosztami początkowymi, to oszczędności, jakie generują te technologie, szybko przynoszą zwrot z inwestycji. Zmniejszenie kosztów operacyjnych oraz poprawa efektywności produkcji czynią zakłady bardziej konkurencyjnymi oraz odpowiedzialnymi ekologicznie.
Dystrybucja w Polsce W Polsce dystrybucją technologii i urządzeń firm Katronic, Seli GmbH Auto ma tisierungstechnik i systec Controls zajmuje się firma AEA Technique, mająca 20letnie doświadczenie w doradztwie technicznym, imporcie i dystrybucji przyrządów do pomiaru, sygnalizacji i regulacji przepływu, poziomu, temperatury i ciśnienia mediów przemysłowych.
Jakość świadczonych przez firmę AEA Technique usług potwierdza certyfikat ISO 9001:2015 oraz setki udanych aplikacji i kilkanaście tysięcy działających punktów pomiarowych.
Zainteresowani opisaną w artykule technologią pomiarową będą mieli okazję zobaczyć ją z bliska podczas Warsaw Industry Week 5–7 listopada 2024 r., na stanowisku AEA Technique B3.33a.
AEA TECHNIQUE Sp. z o. o. ul. Toszecka 99 44-100 Gliwice tel. 32 775 65 24
e-mail: info@aea-technique.pl www.aea-technique.pl
Redakcja AUTOMATYKA
Sieć Badawcza Łukasiewicz – Przemysłowy Instytut Automatyki i Pomiarów PIAP
Al. Jerozolimskie 202, 02-486 Warszawa
Marketing tel. 22 87 40 191
e-mail: automatyka@piap.lukasiewicz.gov.pl www.AutomatykaOnline.pl/Automatyka
Jednym z podstawowych zadań układów automatyki jest wprawianie różnych urządzeń i maszyn w ruch. Tutaj niezbędne są układy napędowe oparte na urządzeniach sterujących i kontrolujących pracę silników.
Agnieszka Staniszewska
Do precyzyjnego określania pozycji oraz przemieszczenia w przypadku najprostszych aplikacji wystarczające jest użycie softstarterów oraz przemienników częstotliwości. Bardziej zaawansowane aplikacje wymagają stosowania ser wonapędów oraz urządzeń pomiarowych.
Softstarter to urządzenie, które zapewnia łagodny start i zatrzymanie silnika. Jest alternatywą dla rozrusznika gwiazda–trójkąt oferującą zdecydowanie więcej możliwości. Sterowanie napięciem zasilającym silnik pozwala na obniżanie prądu rozruchowego oraz unikanie udarów. Tym samym elementy mechaniczne ulegają wolniejszemu i mniejszemu zużywaniu. Ponadto softstartery ograniczają r yzyko naliczania potencjalnych kar za przekroczenia na rzecz dostawców energii. Softstarter sprawdzi się w aplikacjach, w których nie ma konieczności zmiany
częstotliwości, a więc prędkości obrotowej silnika, np w wentylatorach, sprężarkach, kruszarkach, podajnikach i przenośnikach. Otwierają możliwość monitorowania pracy silników oraz ich diagnozowania. Warto zauważyć, że softstartery po uruchomieniu silnika można zbocznikować, używając bypassu. Silnik jest zasilany wtedy bezpośrednio z sieci.
Firma Danfoss oferuje softstartery VLT serii MCD100, MCD201, MCD202 i MCD 600. Urządzenia z pierwszej serii są kompaktowe i ekonomiczne i mają podstawowe funkcjonalności, modele serii MCD 200 cechują się łatwym montażem na szynie DIN oraz współpracą z urządzeniami do 30 kW. Softstartery serii MCD 600 gwarantują elastyczność, w tym przypadku można korzystać z różnych komunikacyjnych kart rozszerzeń, wewnętrznego bypassa oraz wbudowanych funkcji, np czyszczenia pompy, kalendarza, planowania opartego na czasie pracy.
Eaton Electric ma w swoim portfolio rodzinę softstarterów DS7 dostępną w zakresie prądów do 200 A. Umożliwiają korzystanie z innowacyjnego sposobu podłączenia o nazwie SmartWire-DT, bez konieczności wykonywania okablowania sterującego ani adresowego z wykorzystaniem przełączników DIP.
Schneider Electric oferuje softstartery serii Altistart. I tak Altistart 01 jest przeznaczony do prostych zastosowań w urządzaniach o mocy od 0,37 kW do 15 kW, Altistart 22 do pomp i wentylatorów o mocy od 4 kW do 400 kW, a Altistart 48 do urządzeń o mocy do 900 kW, używanych w przemyśle ciężkim.
Przemienniki częstotliwości
Gdy istnieje potrzeba zmiany prędkości obrotowej silnika, niezbędne okazuje się użycie przemienników częstotliwości. Przemienniki częstotliwości umożliwiają wykorzystywanie ramp prędkości i hamowania, co ogranicza zużycie elementów mechanicznych wynikające z naprzemiennie po sobie następujących cyklów pracy i postoju napędzanych elementów. Przemiennik umożliwia precyzyjną kontrolę prędkości obrotowej silnika podłączonego do przemiennika niezależnie od zmian momentu. Ponadto ma możliwość wpływania na przyspieszanie i hamowanie oraz potrafi dynamicznie dobierać prędkości do aktualnego zapotrzebowania. Tym samym zwiększa energooszczędność danego napędu.
Można wyróżnić dwie główne metody sterowania prędkością obrotową silnika elektrycznego – skalarną, która polega na zachowaniu stałej proporcji napięcia do częstotliwości U/f oraz wektorową – bazującą na wyliczonym modelu silnika. Metoda skalarna sprawdza się w aplikacjach z lekkimi obciążeniami silnika, wektorowa wszędzie, gdzie występujące obciążenia i momenty są duże.
Rynek przemienników częstotliwości jest dosyć bogaty i można na nim znaleźć urządzenia wielu producentów i dystrybutorów automatyki takich jak : Danfoss, Eaton Electric, EURA Drives, Nord, Mitsubishi Electric, Multiproject, Parker, Schneider Electric czy Yaskawa.
Przemienniki regeneracyjne
Efektywność energetyczna przemiennika częstotliwości może być znacząco wyższa, gdy możliwe jest odzyskiwanie energii hamowania. Urządzenia z taką funkcjonalnością, zwane regeneracyjnymi, podczas zatrzymywania napędzanych elementów efektywnie zagospodarowują energię hamowania. Nie jest ona tracona w postaci zbędnego wydzielania ciepła w rezystorach hamujących. W związku z dużym udziałem przemienników częstotliwości w zapotrzebowaniu procesu produkcyjnego na energię elektryczną, w przedsiębiorstwach przywiązuje się coraz większą uwagę do aspektu efektywności energetycznej i kosztów z tym związanych.
Rezystory hamujące wykorzystywane w przemiennikach napędzających silniki, które często i szybko się zatrzymują muszą radzić sobie z dużą ilością ciepła, co powoduje, że wymagają solidnego chłodzenia. To z kolei wiąże się z nie-
Warsaw, 05.–07.11.2024
Halla B, Stoiska B3.42a
Zastosowania FAULHABER
Dzięki wytrzymałości układów napędowych FAULHABER możesz zmniejszyć liczbę postojów operacyjnych automatycznie sterowanych pojazdów. www.faulhaber.com/logistics-robot/en FAULHABER Polska sp. z o.o. info@faulhaber.pl
komunikacja
pożądanymi kosztami. Oprócz korzyści ekonomicznych stosowanie przemienników regeneracyjnych w aplikacjach z częstym i nagłym zatrzymywaniem napędzanych elementów, tj. dźwigi, suwnice czy przenośniki, należy pamiętać, że jest to rozwiązanie przyczyniające się do ochrony środowiska.
Oszczędzoną energię można wykorzystać na dwa sposoby – albo oddać ją z powrotem do sieci zasilającej, albo wykorzystać do zasilenia układów napędzanych za pomocą innych przemienników częstotliwości. Stopień wyjściowy przemienników regeneracyjnych jest podobny do stopnia wejściowego dla umożliwienia dwukierunkowego przepływu energii.
Modbus EtherNet/IP Profinet
Modbus EtherCAT EtherNet/IP Profibus Profinet DeviceNET Modbus EtherCAT CANopen
Przykładowe serie modułów, które umożliwiają odzysk energii podczas hamowania w przemiennikach częstotliwości to propozycje firm Yaskawa – R1000 oraz Induprogress – REG2000.
Serwonapędy
W branży automatyki i robotyki często spotykanymi urządzeniami w technice napędowej są serwonapędy. Są one wykorzystywane do precyzyjnej kontroli ruchu w aplikacjach, w których precyzyjne pozycjonowanie odgr ywa znacząco rolę dla zachowania dobrej jakości. Serwonapędy pracują w zamkniętych pętlach ze sprzężeniem zwrotnym i składają się z serwowzmacniacza, sterownika i serwosilnika z enkoderem.
Modbus
EtherCAT EtherNet/IP CC-Link Profibus Profinet DeviceNET
Wzmacniacz porównuje wartości zadawane przez sterownik z wartościami zmierzonymi na obiekcie, otrzymana w ten sposób odchyłka jest podstawą do podejmowania odpowiednich działań prowadzących do jej zmniejszania. Ser wonapędy mogą w zależności od aplikacji regulować położenie, prędkość, moment obrotowy lub różne ich kombinacje. Układ sterowania ser wonapędem ma wielopętlową strukturę z zagnieżdżeniami.
Tryb sterowania momentowy jest stosowany do realizowania takich zadań jak nawijanie – wymagane jest utrzymanie stałego naprężenia nawijanego materiału oraz wtr yskiwanie – konieczna jest nie zmienna
Modbus
Modbus EtherCAT CANopen Powerlink EtherNet/IP
siła docisku do formy. Z kolei tr yb prędkościowy stosowany jest w przenośnikach, dozownikach i maszynach sterowanych numer ycznie do obróbki i cięcia termicznego materiałów. Ze względu na charaktery tych procesów k onieczne jest utrzymyw anie stałej prędkości dla zachowania wysokiej jakości obróbki. Tryb pozycyjny sterowania jest stosowany w aplikacjach, w których element jest przesuwany w z góry zaplanowany i znany sposób po określonym wcześniej torze.
Bezpieczeństwo
Ważnym aspektem związanym z serwonapędami jest be zpieczeństwo.
Modbus
EtherCAT CANopen
EtherNet/IP Profibus Profinet
Najczęściej spotykaną w sterownikach napędów wbudowaną funkcją bezpieczeństwa jest STO, czyli be zpieczne w yłączenie m omentu. J est a bsolutną p odstawą d o tego, a by układ napędowy mógł być zastosowany w linii produkcyjnej. Zatrzymanie silnika następuje przez wybieg. Aktywacja funkcji powoduje natychmiastowe zaprzestanie generowania momentu przez sterownik.
Kolejną popularną funkcją be zpieczeństwa dostępną w napędach jest SS1 – bezpieczne zatrzymanie silnika. Hamowanie jest wykonywane po rampie, po czym wywoływana jest funkcja STO. Funkcja jest nie zbędna w przypadku, gdy ruch napędzane -
Modbus EtherCAT CANopen Powerlink EtherNet/IP Profibus Profinet DeviceNET
Modbus
EtherCAT CANopen Powerlink
EtherNet/IP Profibus Profinet DeviceNET
go elementu musi być zatrzymany w kontrolowany sposób.
Inne popularne wbudowane funkcje bezpieczeństwa to: SLS, SSR, SBC, SDI. SLS zapobiega prz ekroczeniu przez silnik zdefiniowanego limitu prędkości, jest użyteczna w trakcie prac konserwacyjnych i konfiguracyjnych na pracującym urządzeniu. SSR ogranicza be zpieczny zakres osiąganych p rędkości. Funkcja S BC s łuży do kontrolowania mechaniczne go hamulca i jest przydatna w przypadku obecności aktywnego obciążenia np. wiszącego ładunku. SDI jest funkcją kontrolującą k ierunek o brotu wału silnika. Staje się użyteczna, gdy jest wymagany ruch tylko w jedną stronę.
PRODUCENT / DYSTRYBUTOR
opcjonalnie dostępne wbudowane funkcje bezpieczeństwa
narzędziowe
Napędy specjalne
Na rynku automatyki są dostępne napędy z zabezpieczeniami przed przegrzaniem. Taką ochronę można osiągnąć poprzez monitorowanie pobieranego przez silnik prądu, zastosowanie czujników zaników fazy, wbudowanie zabezpieczeń zwarciowych i przeciążeniowych, zadbanie o bezpośrednią kontrolę temperatury na obudowie silnika i jego uzwojeniach. Wszystkie z wymienionych sposobów to przykłady realizacji wspomnianej funkcji zabezpieczenia przed przegrzewaniem.
Wśród napędów dostępnych na rynku automatyki można wyróżnić grupę napędów zintegrowanych, które charakteryzują się występowaniem wszystkich składowych elementów napędu w jednej obudowie. Takie podejście znacząco obniża koszty montażu oraz uruchamiania napędu ze względu na znaczącą redukcję okablowania. Wymaga jednak odpowiedniej przestrzeni do montażu,
czego nie można zapewnić w przypadku każdego projektu konstrukcji.
Kolejną grupą są napędy wieloosiowe, które pozwalają napędzać kilka osi za pomocą jednego wzmacniacza. Taka koncepcja ułatwia synchronizację poszczególnych osi, redukuje ilość okablowania i ułatwia utrzymanie przejrzystości w szafie sterującej.
Koncepcja decentralizacji
Na rynku automatyki można również wyróżnić grupę napędów zdecentralizowanych. Te znajdują zastosowanie przede wszystkim w rozbudowanych systemach automatyki, szczególnie takich, które zajmują duże powierzchnie. Wtedy niepraktycznym i nieergonomicznym staje się umieszczanie wszystkich komponentów napędów w jednej szafie, w jednej lokalizacji. Z koncepcją decentralizacji wiąże się modułowość rozwiązania. Łatwiej jest rozbudować dany system automatyki bez konieczno-
ści znacznej ingerencji we wnętrze szafy sterowniczej oraz okablowanie. Używanie napędów zdecentralizowanych najczęściej wiąże się z wykorzystaniem sieci przemysłowych, które zapewniają szybką, sprawną i niezawodną wymianę danych pomiędzy poszczególnymi elementami układu napędowego rozmieszczonymi w różnych punktach systemu automatyki. Koncepcja decentralizacji sprawdza się m.in. w oczyszczalniach ścieków, przepompowniach oraz centralach klimatyzacyjnych.
Za przykład napędu zdecentralizowanego może posłużyć przemiennik częstotliwości EURA EP-66 o mocy maksymalnej z zakresu 0,75–90 kW, znajdujący się w ofercie firmy HF Inverter. Komponent charakteryzuje się wysokim stopniem ochrony IP66 oraz obecnością dodatkowej przestrzeni w obudowie, umożliwiającej umieszczenie dodatkowych elementów automatyki w jej wnętrzu. Wspomniane rozwiązanie nosi
INDUPROGRESS
EtherCAT CANopen EtherCAT CC-Link EtherCAT CanOpen Profibus Profinet DeviceNet EtherNet/IP
STO, SS1, SS2, SOS, SBC, SLS, SSM, SDI, SLI, SLT
nazwę Opti-Box Concept. Przemiennik jest wyposażony w filtr przeciwzakłóceniowy oraz dławik.
Firma Nord oferuje przemienniki zdecentralizowane SK 250E NORDAC LINK o mocy z zakresu 0,37–7,5 kW ze zintegrowanym tr ybem pozycjonowania, pracą synchroniczną oraz możliwością komunikacji z użyciem wielu różnych protokołów komunikacyjnych.
Bosch Rexroth oferuje serię napędów zdecentralizowanych IndaDrive Mi. Protokół bezpieczeństwa CIP Safety umożliwia przesyłanie sygnałów bezpieczeństwa jednym połączeniem sieciowym wraz z pozostałymi sygnałami i danymi. W skład omawianych napędów wchodzą ser wosilniki synchroniczne z nadbudowanymi sterownikami oraz zasilaczami ze zwrotem energii do sieci.
Napędy liniowe
Gdy dynamika serwonapędu obrotowego okazuje się niewystarczająca, zasto-
STO, SS1, SS2, SOS, SLS, SLP, SLI, SDI, SSM
STO, SS1, SS2, SOS, SBC, SLS, SSM, SDI, SLA, SBT
sowanie znajdują silniki liniowe. Duże przyspieszenia oraz dopuszczalne prędkości maksymalne sprawiają, że są one coraz częściej stosowane w systemach pozycjonujących, manipulatorach i obrabiarkach. Silniki liniowe nie generują ruchu obrotowego w napędzanych obiektach, zaś płynnie, dynamicznie, poruszają nimi wzdłuż określonych krzywych. Składają się z dwóch części –ruchomej z uzwojeniami silnika i ścieżki magnetycznej z magnesami tr wałymi. Kilka ruchomych elementów na jednej ścieżce umożliwia zwiększenie siły ciągu, gdy są one połączone równolegle. Elementy mogą pracować również niezależnie. Istnieje możliwość łączenia ścieżek w dłuższe odcinki umożliwiające realizację przejazdów o dowolnej długości. Silniki liniowe wprawiają w ruch bez udziału elementów przełożenia takich jak: przekładnie, pasy napędowe, koła zębate, zębatki, mechanizmy korbowe czy łańcuchy. Energia
prądu jest bezpośrednio zamieniana na energię kinetyczną ruchu postępowego. Przykładami serii silników liniowych dostępnych na rynku automatyki są: LMSA, LMFA, LMC, LMFB (wszystkie HIWIN), Sl2 (SEW-EURODRIVE) i DM01 (Multiproject).
Kontrola pozycji i przemieszczenia Niezbędnym elementem precyzyjnego układu napędowego jest komponent odpowiedzialny za kontrolę pozycji i przemieszczenia. Najczęściej tym elementem jest enkoder. Wśród enkoderów można wyróżnić modele inkrementalne oraz absolutne. Inne kr yterium podziałowe wyróżnia wśród enkoderów modele optyczne i magnetyczne. Na enkoder optyczny składają się układ nadajnika i odbiornika oraz tarcza obrotowa ze szczelinami, przez które przechodzi wiązka nadawana do odbiornika. Liczba szczelin wpływa na rozdzielczość
urządzenia. Enkodery magnetyczne mogą być zlokalizowane w większej odległości od tarczy, tym samym umożliwiając oddzielenie sekcji mechanicznej od elektronicznej, co wpływa na zwiększenie żywotność całego układu. Pole magnetyczne umożliwia wykonywanie pomiarów metodą bezdotykową, nie ma konieczności stosowania przekładni mechanicznej i zasilania bateryjnego. Przykładem enkoderów mogą być absolutne enkodery AVM78E z oferty firmy Pepperl+Fuchs. Są to komponenty w wersji wieloobrotowej wykonane zgodnie z dyrektywami ATEX, a więc mogą pracować w strefach zagrożonych wybuchem. Ich ognioszczelna obudowa została wykonana z aluminium lub stali nierdzewnej, a dostępna rozdzielczość maksymalna wynosi 16 bitów, a 14 bitów jest użytych dodatkowo do określania liczby zrealizowanych obrotów.
Inny przykład enkoderów to seria OCE-EC00B dostępna w ofercie firmy Positial Fraba. W jej skład wchodzą wieloobrotowe, absolutne urządzenia z interfejsem EtherCAT o szesnastobitowej rozdzielczości i liczbie obrotów zakodowanych na 14 bitach. Część modeli jest dostępna w wersji przeciwwybuchowej.
Kolejne przykładowe enkodery to: jednoobrotowy absolutny enkoder HS58 EP z interfejsem EtherNet/IP, który oferuje Eldar i absolutny, wieloobrotowy, osiemnastobitowy enkoder 842E wykonany w stopniu ochrony IP67 oferowany przez Rockwell Automation.
Do pomiaru przemieszczeń liniowych służą enkodery liniowe. Składają się one z głowicy i taśmy magnetycznej. Głowica zawiera sensor magnetyczny, który podczas przemieszczania się względem taśmy, na której znajdują się naprzemiennie umieszczone bieguny N i S, generuje sinusoidalny sygnał elektryczny, który jest następnie przez obwody elektroniczne przetwarzany na przebiegi prostokątne. Liczba impulsów w otrzymanym przebiegu jest proporcjonalna do przesunięcia, zaś ich częstotliwość do prędkości posuwu.
Przemysł 4.0
Rewolucja przemysłowa w zakresie procesów produkcyjnych wiąże się z rozwojem techniki napędowej. Nowatorskie rozwiązania proponowane przez pro-
ducentów i dystrybutorów systemów napędowych mają na celu sprostanie wyzwaniom stawianym branży automatyki w związku z postępującym rozwojem Przemysłu 4.0. Główny nurt zmian dotyczy analizy danych. Nieuniknione jest również wykorzystanie sztucznej inteligencji, której rozwój jest coraz bardziej dynamiczny Na podstawie analizy danych archiwalnych zbieranych z napędów i odpowiednich algorytmów oraz dokonań sztucznej inteligencji można projektować aplikacje służące optymalizacji procesów produkcyjnych. Niezbędna jest ścisła współpraca inżynierów oraz programistów. Wszystkie dotychczasowe metody optymalizacji są wzbogacane zautomatyzowanymi działaniami. Działania te są dyktowane wnioskami wyciągniętymi z obserwacji i analizy zachowań urządzeń napędowych w przeszłości. Cały czas sposób działania napędów jest doskonalony. Dodatkowo łatwiej jest prowadzić działania prewencyjne. Na podstawie archiwalnych danych można ustalić jakie parametry i okoliczności poprzedzały awarie i uszkodzenia urządzeń. Pojawienie się takich symptomów może generować odpowiednie ostrzeżenia, które zapobiegną awarii, skrócą lub wyeliminują czas postoju, zredukują
koszty związane z ewentualną usterką. Niezbędnym działaniem związanym z zainicjowaniem wprowadzania do przedsiębiorstwa Przemysłu 4.0 jest zintegrowanie maszyn i urządzeń w jedną sieć. Dzięki temu zbierane dane są kompletne i prezentują pełen obraz realizacji procesu produkcyjnego. Obrazowo ujmując, nowoczesne urządzenia, podzespoły i komponenty są w stanie same się konfigurować oraz dopasowywać do otoczenia i panujących warunków, w tym integrować z działającymi już systemami. Ich cechą jest samodoskonalenie. Ludzie, systemy IT i napędy automatycznie wymieniają się informacjami w trakcie trwania procesów produkcyjnych. Ważną cechą charakteryzującą napędy działające zgodnie z założeniami Przemysłu 4.0 jest dostęp do wszystkich informacji z dowolnego miejsca, w dowolnym czasie. Dzięki integracji systemów produkcyjnych łatwiej jest zarządzać produkcją, zwiększa się potencjał przedsiębiorstwa, można dostosowywać się do potrzeb klientów i realizować produkcję małoseryjną.
Napędy inteligentne potrzebują wyłącznie sygnału z systemu sterującego o potrzebie wykonania określonego ruchu lub sekwencji ruchów Same mogą kontrolować sytuację i adaptować się do zastanych warunków. Modyfikacje linii technologicznej związane ze zmianą produkowanego komponentu są dokonywane w sposób zautomatyzowany, nie wymagają ingerencji mechaników. Do identyfikacji produktów oraz aktualnych potrzeb służą czujniki.
Rynek techniki napędowej ulega ciągłej ewolucji. Wprawianie w ruchu elementów wykonawczych wymaga weryfikowanie aktualnych potrzeb i dostosowywania oferty do bieżącego zapotrzebowania. Każda aplikacja jest inna i wymaga stosowania innych rozwiązań. Niniejszy przegląd miał na celu nakreślenie aktualnej sytuacji na rynku napędów, wskazanie przykładowych produktów i wyszczególnienie wybranych zagadnień związanych z tematyką.
Agnieszka Staniszewska AUTOMATYKA
M.453-SEMI-S8
SEMI to skrót od Semiconductor
Equipment and Materials International. Jest to stowarzyszenie ponad 3000 firm z całego świata z branży technologii półprzewodników. Natomiast SEMI-S8 to zbiór wytycznych dotyczących bezpiecznej i ergonomicznej konstrukcji urządzeń oraz oprzyrządowania do produkcji półprzewodników. Norma ta uwzględnia wzajemne oddziaływanie między użytkownikiem a sprzętem w środowisku produkcyjnym.
Korzystając z wytycznych SEMI-S8, producenci i użytkownicy urządzeń produkcyjnych mogą współpracować i projektować sprzęt, który zminimalizuje zmęczenie i zmaksymalizuje bezpieczeństwo pracowników przez dopasowanie urządzeń do oczekiwanej wielkości ciała, siły i zakresu ruchu. SEMI-S8 zapewnia efektywność urządzeń/narzędzi, a także wygodę, komfort i bezpieczeństwo pracowników podczas ich obsługi.
Ergonomiczna konstrukcja Wychodząc naprzeciw oczekiwaniom klientów i r ynku, firma Elesa+Ganter wprowadziła do oferty nowy uchwyt M.453-SEMI-S8, który został zaprojektowany zgodnie z wytycznymi zawartymi w SEMI-S8 (wydanie 1116).
Według wymagań normy SEMI-S8 wszystkie elementy obsługowe, z których korzysta pracownik – takie jak uchwyty – muszą mieć ergonomiczną konstrukcję, zaokrąglone krawędzie i szeroką przestrzeń na dłonie. Wszystko po to, aby zminimalizować wysiłek operatora w przypadku częstych operacji, a także zwiększyć bezpieczeństwo podczas pracy. W normie SEMI-S8 jest rozdział poświęcony konstrukcji uchwytów, w którym szczegółowo opisano geometrię w zależności od typu uchwytu.
Cechą wymaganą dla uchwytów mostkowych (jak M.453-SEMI-S8) jest wysokim stopień ergonomii, ponieważ uchwyty muszą gwarantować wygodny i mocny chwyt, szczególnie wtedy, gdy operator ma na dłoniach rękawiczki. Istnieją dokładne wskazania dotyczące wymiarów części
chwytnej, na przykład prześwit na rękę operatora musi mieć szerokość co najmniej 122 mm i wysokość minimum 41 mm, a krawędź części chwytnej musi mieć promień krzywizny wynoszący 6,5 mm.
W uchwycie M.453-SEMI-S8 prześwit na rękę operatora ma szerokość 126 mm i wysokość 41,5 mm, natomiast grubość części chwytnej wynosi 13 mm, więc wszystkie warunki są spełnione.
Wysoka wytrzymałość mechaniczna
W normie SEMI-S8 nie zawarto szczególnych ograniczeń dotyczących materiałów, dlatego firma Elesa+Ganter zdecydowała się wybrać poliamid wzmocniony włóknem szklanym, zapewniający najwyższą wytrzymałość mechaniczną (w zależności od płaszczyzny działania, maksymalne obciążenia robocze wynoszą 3500 N i 4900 N).
Reasumując, jeżeli się buduje, projektuje lub modernizuje urządzenia czy oprzyrządowanie okołoprodukcyjne dla branży półprzewodników, to uchwyt M.453-SEMI-S8 będzie bardzo dobrym wyborem. Sprawdzi się też wszędzie tam, gdzie zależy nam na wygodzie i ergonomii obsługi, również przy pracy w rękawicach.
ul. Słoneczna 42A, Stara Iwiczna 05-500 Piaseczno
tel. 22 737 70 47
pomoc techniczna: tel. 609 914 500 fax 22 737 70 48
e-mail: egp@elesa-ganter.com.pl www.elesa-ganter.pl
W dobie powszechnej automatyzacji procesów przemysłowych przychodzi taki czas, gdy firmy zadają sobie pytanie dotyczące wyboru sposobu maksymalizacji zysków. Oczywiście odpowiedzi jest mnóstwo, gdyż chodzi o zwiększenie konkurencyjności firmy na rynku tak, by było to dla niej jak najbardziej korzystne. Jak można tego dokonać? Istnieje wiele możliwości i sposobów, a jednym z nich jest automatyzacja zarządzania energią w zakładach przemysłowych, która przyczynia się do optymalizacji kosztów produkcji. Obecnie wiele firm inwestuje w odnawialną energię OZE, ale spójrzmy na inne podejście do redukcji kosztów energii.
Coraz częściej obserwujemy jak nowe technologie umożliwiają przenikanie się świata OT z IT. Dzięki nowoczesnym systemom zarządzania energią możliwe jest monitorowanie zużycia prądu, gazu czy innych nośników energii w czasie rzeczywistym. Zastosowanie sztucznej inteligencji (AI) i uczenia maszynowego (ML) pozwala na jeszcze większą optymalizację, ponieważ systemy te analizują ogromne ilości danych i uczą się wzorców zużycia energii.
Dzięki temu możliwe jest dokładniejsze prognozowanie zapotrzebowania oraz szybsze reagowanie na nieprawidłowości. Firmy korzystające z algorytmów sztucznej inteligencji mogą automatycznie dostosowywać pracę maszyn i urządzeń do rzeczywistego zużycia
energii, unikając jej strat oraz jednocześnie obniżając koszty. Rozwiązania tego typu dodatkowo pozwalają na szybkie wykrywanie obszarów o nadmiernym zużyciu i podejmowanie działań naprawczych, co prowadzi do znacznych oszczędności. Wdrożenie odpowiednich narzędzi do automatyzacji nie tylko obniża koszty operacyjne, ale także zwiększa efektywność procesów produkcyjnych, co przekłada się na większą konkurencyjność firmy na rynku.
Znaczenie efektywności energetycznej i cele optymalizacji
Efektywność energetyczna w przemyśle to proces, który polega na maksymalnym wykorzystaniu energii przy minimalnych stratach. W kontekście zakładów
produkcyjnych oznacza to, że wszystkie urządzenia, maszyny i instalacje powinny działać tak, aby zużywać jak najmniej energii przy zachowaniu tej samej, pełnej wydajności. Dzięki automatyzacji procesów zarządzania energią, przedsiębiorstwa mogą monitorować, gdzie i kiedy zużywana jest energia, co pozwala szybciej reagować w niestandardowych sytuacjach oraz wpływać na poprawę sprawności energetycznej fabryki.
Czy przed wdrożeniem do zakładu systemu zarządzania energią opartego na uczeniu maszynowym, konieczne jest najpierw unowocześnienie infrastruktury z wykorzystaniem IIoT? Modernizacja infrastruktury zakładu produkcyjnego z użyciem Przemysłowego Internetu Rzeczy jest bardzo korzystna, a czasami wręcz konieczna dla efektywnego wdrożenia aplikacji zarządzania energią opartej na uczeniu maszynowym. IIoT umożliwia zbieranie danych w czasie rzeczywistym z różnych czujników i urządzeń, co jest kluczowe dla aplikacji ML. Potrzebują one dużych, dokładnych i aktualnych zestawów danych do prognozowania zużycia energii, optymalizacji oraz wykrywania anomalii. Modele ML do analizy potrzebują danych historycznych i bieżących, a dokładność prognoz poprawia się, gdy informacje są zbierane z wielu źródeł w czasie rzeczywistym, co często jest możliwe dzięki zastosowaniu IIoT.
Rola AI oraz ML w zarządzaniu energią IoT dostarcza ogromne ilości danych, co sprawia, że powstaje potrzeba ich maksymalnego wykorzystania. W jaki sposób można tego dokonać? Z pomocą przychodzi sztuczna inteligencja oraz uczenie maszynowe, które umożliwiają efektywne przetwarzanie tych informacji i zamianę ich na konkretne działania. Dzięki AI i ML firmy mogą nie tylko usprawniać procesy, ale także znacząco obniżać koszty operacyjne. Analizując dane w czasie rzeczywistym, te technologie pomagają przewidywać zapotrzebowanie na energię, przekroczenie zadeklarowanych przez firmę mocy, identyfikować nieefektywności w systemach, a także zapobiegać awariom, co przekłada się na zwiększenie stabilności sieci.
Wdrożenie rozwiązań opartych na AI może przynieść znaczące oszczędności zarówno dostawcom energii, jak i użytkownikom końcowym. Automatyzacja procesów i precyzyjna analiza danych pomagają minimalizować straty energii oraz zwiększać zyski dzięki bardziej efektywnemu zarządzaniu zasobami.
Algorytmy i modele optymalizacji zużycia energii
W procesie optymalizacji zużycia energii przy użyciu AI i ML można stosować różne algorytmy i modele, które pomagają analizować dane oraz podejmować decyzje w czasie rzeczywistym. Poniżej przedstawiamy przykładowe typy modeli uczenia maszynowego.
Sieci neuronowe
Sieci neuronowe (ANN) są używane do analizy dużych zbiorów danych, które zawierają informacje o zużyciu energii, jak i do prognozowania przyszłego zapotrzebowania na energię. Modele te mogą optymalizować procesy produkcyjne, uwzględniając wzorce zużycia energii. Ich wadą jest jednak wydłużający się czas przeznaczony na trening wraz ze wzrostem liczby neuronów w sieci.
Algorytmy uczenia głębokiego Modele algorytmów uczenia głębokiego (Deep Learning), szczególnie sieci neuronowe z rekurencją (RNN)
i Long Short-Term Memory (LSTM), są efektywne w analizie danych czasowych (np. monitorowanie zużycia energii w czasie rzeczywistym). Mogą przewidywać przyszłe maksima (piki) zużycia energii i automatycznie dostosowywać zużycie do potrzeb.
Drzewa decyzyjne i lasy losowe
Drzewa decyzyjne i lasy losowe (Random Forests) to algorytmy elastyczne i łatwe w użyciu. Często bez dostrajania ich parametrów potrafią wygenerować świetne wyniki. Dużą ich zaletą jest wszechstronność. Mogą być używane do zadań klasyfikacji, jak i regresji. Algorytmy te mogą również pomóc w podjęciu decyzji dotyczących wyłączania lub zmniejszania mocy urządzeń.
Maszyny wektorów nośnych
Maszyny wektorów nośnych (SVM) są stosowane do klasyfikacji danych i identyfikacji anomalii w zużyciu energii. Mogą być używane do optymalizacji pracy urządzeń, minimalizując zbędne zużycie.
Algorytmy grupowania
Algorytmy grupowania (Clustering) –takie algorytmy, jak k-means, mogą grupować urządzenia lub procesy o podobnym wzorcu zużycia energii, aby lepiej dostosowywać ich pracę. To często wykorzystywany algorytm w diagnostyce żywotności silników.
Przykładowy model predykcji zużycia energii zakładu przy użyciu korelacji przestrzenno-czasowej procesu technologicznego
System zarządzania energią przez AI w praktyce Dobrym przykładem tego, jak sprawdza się system zarządzania energią przez AI jest projekt Canal de Isabel II w Madr ycie – firma Siemens osiągnęła redukcję zużycia energii rzędu 15–20 %, co przyniosło znaczne oszczędności finansowe. Siemens wdrożył system predykcyjnej konserwacji i optymalizacji procesów, co pozwoliło na wczesne wykrywanie usterek oraz lepsze zarządzanie pracą urządzeń. Dzięki temu oczyszczalnie zaczęły działać bardziej efektywnie, a jednocześnie zmniejszono koszty operacyjne związane z energią o ponad 15 %. Długofalowe oszczędności dla Canal de Isabel II to nie tylko redukcja kosztów, ale także znaczne zmniejszenie emisji gazów cieplarnianych, co ma duży wpływ na środowisko.
Google jest pionierem w stosowaniu AI i ML do optymalizacji zużycia energii w swoich centrach danych. W jednym z takich centrów, zlokalizowanym w USA, Google zastosował AI waną przez DeepMind do systemami chłodzenia, które stanowią jedną z głównych składowych zużycia energii w tego typu obiektach. AI lizowała ogromne ilości danych z temów monitorujących temperaturę, wilgotność i zużycie energii, ucząc się, jak zoptymalizować działanie systemów chłodzenia. Wdrożenie AI się do zmniejszenia zużycia energii po trzebnej do chłodzenia o całego centrum danych takie działania przyniosły roczne oszczędności sięga jące milionów dolarów. Google dono si, że efektywność energetyczna całego centrum danych poprawiła się o co jest znaczącym wynikiem, biorąc pod uwagę skalę operacji i wysokie utrzymania chłodzenia serwerów. Johnson Controls to glob specjalizująca się w rozwiązaniach do tyczących efektywności energetycznej i automatyzacji budynków. Jednym z flagowych produktów jest OpenBlue – zaawansowany system do nia budynkami, który łączy technologię IoT, sztucznej inteligencji oraz anality ki, aby optymalizować zużycie energii i poprawiać zrównoważony rozwój budynków. W raporcie zrównoważo
nego rozwoju 2024 „Smart, healthy, sustainable tomorrows” firma Johnson Controls przedstawiła ciekawy projekt realizowany w parku NRG w hrabstwie Harris w Teksasie.
Modernizacja obejmuje m.in. wymianę systemów HVAC, oświetlenia oraz systemów oszczędzania wody, zaś kluczowym elementem jest właśnie integracja systemu OpenBlue, który pozwoli na monitorowanie oraz optymalizację zużycia energii w czasie rzeczywistym. Efektem tego projektu będą oszczędności energetyczne na poziomie 54 mln dolarów oraz redukcja emisji gazów cieplarnianych o 33 %.
Podsumowanie
Optymalne zarządzanie energią przynosi wiele korzyści, takich jak redukcja kosztów operacyjnych, lepsze wykorzystanie zasobów oraz mniejsze zużycie energii, co pozytywnie wpływa na konkurencyjność firm na r ynku. Zastosowanie technologii IoT i AI umożliwia
urządzeń do rzeczywistych potrzeb, co minimalizuje straty energii, poprawiając ich sprawność energetyczną. Zaletą takich systemów jest ich precyzja i szybka reakcja na zmiany, jednak wadą mogą być wysokie koszty wdrożenia oraz konieczność modernizacji infrastruktury, aby w pełni wykorzystać potencjał nowoczesnych rozwiązań.
Niejednokrotnie firmy w celu zredukowania wysokich kosztów wdrożenia i modernizacji decydują się na etapowe wprowadzanie systemu, co pozwala na rozłożenie inwestycji w czasie. Ponadto wykorzystują one istniejące chmury obliczeniowe, takie jak Siemens Mindsphere, Google Cloud IoT, Microsoft Azure IoT, Cisco IoT i wiele innych, co eliminuje potrzebę zakupu drogiego sprzętu. W dłuższej perspektywie działania te przyczynią się nie tylko do znacznych oszczędności, ale są też istotnym krokiem do zrównoważonego rozwoju.
Arkadiusz Rosa
Źródła:
• Kopyt M., „Prognozowanie obszarowe zapotrzebowania i produkcji energii elektrycznej”, Warszawa 2023
• Haq I.U., Ullah A., Khan S.U., Khan N., Lee M.Y., Rho S., Baik S.W., „Sequential Learning-Based Energy Consumption Prediction Model for Residential and Commercial Sectors”, Mathematics, 2021, DOI: 10.3390/math9060605
• Guo J., Han M., Zhan G., Liu S., „A Spatio-Temporal Deep Learning Network for the Short-Term Energy Consumption Prediction of Multiple Nodes in Manufacturing Systems”, Processes, 2022, DOI: 10.3390/pr10030476
• Bu S.-J., Cho S.-B., „Time Series Forecasting with Multi-Headed Attention-Based Deep Learning for Residential Energy Consumption”, Energies, 2020, DOI: 10.3390/en13184722
• Güldner F., Surepelly N., „End-to-End Energy Efficiency Solutions for Industrial Drive Systems”, ARC view, 2021
• „BuildingIQ Develops Proactive Algorithms for HVAC Energy Optimization in Large-Scale Buildings”, MathWorks –
Ostatnią część cyklu artykułów poświęcono programowaniu robotów firmy FANUC oraz podsumowaniu, co z tego przeglądu wynika.
prof. dr hab. inż. Cezary Zieliński
Wpoprzednich numerach miesięcznika AUTOMATYKA przedstawiono ogólną problematykę związaną z metodami programowania robotów przemysłowych oraz trzy konkretne przykłady sposobów programowania robotów firm: Universal Robots, ABB Ltd i Stäubli International AG. Ostatnią część cyklu artykułów poświęcono programowaniu robotów firmy FANUC oraz podsumowaniu, co z tego przeglądu wynika.
Roboty firmy FANUC
Sterownik robota FANUC odpowiedzialny jest za sterowanie ramieniem robota oraz innymi urządzeniami do
niego dołączonymi. Podstawowym urządzeniem służącym do komunikowania się operatora ze sterownikiem jest panel programowania TP (teach pendant), który jest dołączony do sterownika za pomocą kabla. Panel ten służy do:
• ręcznego sterowania ruchami robota,
• tworzenia programów użytkowych,
• testowego bądź automatycznego ich odtwarzania,
• konfigurowania systemu,
• określania aktualnego stanu systemu. Panel programowania, prócz klawiszy numerycznych oraz aktywujących szereg funkcji, wyposażony jest w ekran
dotykowy (touch panel), na którym wyświetlane są okienka umożliwiające komunikację między operatorem a sterownikiem. W zależności od aktualnych działań operatora wygląd wyświetlanych okienek i ich zawartość się zmieniają, by dostosować zawartość do aktualnie realizowanej funkcji.
Zastosowanie panelu programowania nie jest jedynym sposobem programowania robota. Roboty FANUC mogą być programowane na kilka sposobów:
• za pomocą panelu programowania iPendant, z użyciem języka ikonicznego (graficznego),
• wykorzystując oprogramowanie symulacyjne Roboguide,
• korzystając z edytora tekstowego na dowolnym komputerze klasy PC lub
• na komputerze zewnętrznym z użyciem języka KAREL.
W zasadzie zarówno panel programowania, jak i oprogramowanie Roboguide korzystają z tego samego języka programowania, ponieważ w Roboguide odtworzono graficznie wygląd panelu. Niemniej jednak Roboguide ma rozbudowany interfejs graficzny symulujący wygląd gniazda obróbczego zawierającego robota.
Oprogramowanie symulacyjne Roboguide Roboguide umożliwia przede wszystkim tworzenie graficznej trójwymiarowej symulacji wykonania programu w gnieździe roboczym. Przygotowanie symulacji wymaga:
• wyboru typu robota spośród wszystkich typów oferowanych przez firmę FANUC,
• selekcji jednego z wielu typów sterowników,
• zdefiniowania urządzeń i innych obiektów, które znajdują się w gnieździe,
• określenia programu czynności, które mają być wykonane. Rozróżniono dwa rodzaje obiektów, które mogą współegzystować w gnieździe. Są to: część (part) oraz urządzenie mocujące (fixture) dostarczające lub odbierające obiekty. Oba typy obiektów można stworzyć z brył podstawowych lub korzystając z rysunków CAD. Roboguide zawiera dużą bibliotekę gotowych rysunków CAD
różnych typów obiektów, a co więcej rysunki te są sparametryzowane, więc można dostosowywać ich wygląd do potrzeb tworzonego gniazda. W trakcie aranżowania widoku gniazda oraz symulacji wykonania programu można zmieniać punkt widzenia, co wydatnie ułatwia ustawianie obiektów.
Obiekty przesuwa się i obraca poruszając nimi za pomocą kursora albo wprowadzając numeryczne współrzędne początku układu współrzędnych oraz jego orientację względem globalnego układu odniesienia. Zarówno z częściami, jak i urządzeniami związany jest szereg parametrów. Ponieważ części przemieszczają się w trakcie obróbki, trzeba ustalić, w którym miejscu gniazda się pojawią, a w którym znikną. Co więcej, należy określić, po jakim czasie znajdzie się w miejscu wejściowym replika tego obiektu. W ten sposób można zobrazować powtarzalne działanie gniazda na częściach wprowadzanych i wyprowadzanych z niego, np. przez taśmociągi. Symulator określa też czas wykonania cyklu.
Symulator nanosi na rysunek obraz przestrzeni roboczej samej końcówki manipulatora lub narzędzia, co ułatwia ustalenie, czy obiekt jest w zasięgu robota. Ponadto symulator wykrywa kolizje ramienia z otoczeniem w trakcie wykonania programu. Pod kątem działania programu robota nie ma różnicy między tym, który wykonywany jest przez sterownik robota, a tym realizowanym przez symulator. Symulacja jest bardzo wierna. Uwzględnia masę prze-
mieszczanych przedmiotów, a nawet określa energię cieplną generowaną przez silniki manipulatora.
Narzędzie, którym ma się posługiwać robot, można wybrać z biblioteki lub stworzyć własny jego rysunek CAD. Skala rysunku może być zmieniana, więc wielkość narzędzia można dostosować do jego rzeczywistych wymiarów. Tak przygotowane narzędzie trzeba przytwierdzić do końca manipulatora. Co więcej, należy określić masę narzędzia oraz lokalizację jego TCP (punkt środkowy narzędzia określający położenie początku układu odniesienia z nim związanego oraz jego orientację).
Jeżeli tworzymy np. chwytak, to korzystamy z dwóch rysunków – jednego, gdy szczęki są rozwarte i drugiego, gdy są zaciśnięte. Dzięki temu w symulacji szczęki będą się poruszały. Obraz robota może być poruszany na wiele sposobów, np. można poruszać poszczególnymi osiami manipulatora odpowiednio przemieszczając kursor na ekranie za pomocą myszki lub w podobny sposób przemieszczać końcówkę manipulatora lub narzędzie w przestrzeni operacyjnej.
Program robota może być tworzony za pomocą panelu programowania. W związku z tym w Roboguide istnieje symulowany panel programowania, który może być stosowany tak samo, jak ten rzeczywisty dołączony do sterownika. Można więc nauczyć robota pozycji, do których ma dochodzić stosując obraz gniazda. Te pozycje stanowią argumenty instrukcji ruchu. Po
stworzeniu programu można zasymulować jego wykonanie lub przesłać go do rzeczywistego robota, by ten odtworzył ten program. Taka symulacja może być nagrana w postaci filmu w formacie AVI do odtworzenia w sposób niezależny od Roboguide.
Przed wykonaniem programu w trybie automatycznym należy go uruchomić w trybie testowym. Trzeba rozpocząć od wykonania programu w sposób krokowy – linia po linii kodu, następnym etapem będzie wykonananie programu ze zredukowaną prędkością ruchów, na koniec powinien być testowany z właściwą prędkością ruchów manipulatora. Istnieje też możliwość wykonania niektórych fragmentów programu wstecz. W odpowiednim trybie pracy panelu programowania na jego ekranie pojawia się graficzny model robota, wyświetlane są niektóre dane, np. o aktualnym położeniu TCP. W zależności od trybu można poruszać tylko modelem albo modelem i rzeczywistym robotem równocześnie. Model robota może być obserwowany z różnych punktów i z różnej odległości.
Stosowane rejestry i ich rola Język stosowany w panelu programowania operuje różnymi rejestrami zamiast zmiennych. Nie można więc dowolnie nazwać zmiennych według swego upodobania. W sterowniku istnieje 200 rejestrów (P) mogących przechowywać wartości całkowite bądź rzeczywiste. Źródłem tych danych mogą być inne rejestry, stałe, grupy sygnałów
wejściowych bądź wyjściowych zarówno cyfrowych, jak i analogowych, bądź zegary (timer). Rejestry używane są do prowadzenia obliczeń arytmetycznych w ograniczonym zakresie. Dopuszczalnymi operatorami są: +, –, *, /, MOD, DIV. Ponadto istnieje 100 rejestrów pozycyjnych (PR), w których przechowywane są dane dotyczące pozycji. Dane te mogą dotyczyć albo przestrzeni konfiguracyjnej (złącz manipulatora) albo operacyjnej, a więc określać trzy współrzędne kartezjańskie oraz trzy kąty obrotu definiujące orientację. W tym przypadku można stosować operatory: + i –. Na elementach składowych rejestru pozycyjnego można wykonywać wymienione operacje arytmetyczne. Ponieważ rejestry mogą być stosowane przez wykonywane równolegle zadania, należy zadbać o to, by zadanie modyfikujące ich zawartość miało wyłączny dostęp do nich. Do tego służą instrukcje LOCK PREG oraz UNLOCK PREG. Jest to szczególnie istotne przy wykonywaniu wielu segmentów ruchu bez zatrzymywania się w pozycjach pośrednich. Taki ruch wymaga uwzględnienia wielu segmentów ruchu, których parametry zapisane są w rejestrach. By uniknąć zmiany zawartości tych rejestrów zanim dany segment ruchu zostanie zrealizowany, należy zablokować dostęp do tego rejestru za pomocą instrukcji LOCK. Do nadawania wartości rejestrom lub wyjściom służy instrukcja podstawienia (=). Można tworzyć wyrażenia arytmetyczne bądź logiczne korzystając z rejestrów, wejść i wyjść
oraz wymienionych operatorów. Priorytet operatorów może być zmieniony przez zastosowanie nawiasów okrągłych w tworzonym wyrażeniu.
Dostępne są też rejestry przechowujące łańcuchy znaków (STRING – SR). Liczby mogą być konwertowane na łańcuchy znakowe i na odwrót, jeżeli tyko zawierają cyfry. Łańcuchy znakowe mogą być konkatenowane za pomocą operatora +. Do dyspozycji są funkcje działające na łańcuchach określające liczbę znaków w łańcuchu (STRLEN) oraz wyszukujące podłańcuch w łańcuchu (FINDSTR, SUBSTR).
Pozycję można wyrażać na dwa sposoby. Pierwszy dotyczy przestrzeni konfiguracyjnej, w której określa się poszczególne zmienne złączowe (joint variables), stanowiące kąty między kolejnymi członami manipulatora. Podczas procesu uczenia, wartości zmiennych złączowych, sterownik odczytuje z enkoderów umieszczonych na silnikach. Określenie pozycji w przestrzeni operacyjnej wymaga podania więcej informacji. Po pierwsze, należy określić układ współrzędnych, względem którego podana zostanie pozycja. Po drugie, należy podać współrzędne kartezjańskie (X, Y, Z) początku układu związanego z narzędziem (TCP) oraz orientację tego układu względem wcześniej wybranego układu odniesienia. Wreszcie należy określić pożądaną konfigurację ramienia – to jest związane z wielością rozwiązań odwrotnego zagadnienia ki-
nematyki i służy wyborowi tego właściwego. Orientacja definiowana jest przez podanie trzech kątów obrotu względem osi głównych (X, Y, Z) nieruchomego układu odniesienia (roll, pitch, yaw). Przy programowaniu robota korzysta się z wielu układów odniesienia. Podstawowym jest tzw. układ złączowy (joint coordinate system), czyli wektor wyrażony w przestrzeni konfiguracyjnej. Ponadto wykorzystywane są układy kartezjańskie. Interfejsem mechanicznym nazywany jest układ związany z kołnierzem stanowiącym zakończenie manipulatora. Względem tego układu definiuje się układ narzędzia. Początkiem tego układu jest punkt centralny narzędzia (TCP). Układ świata (world coordinate system) związany jest z bazą manipulatora. Względem tego układu wyznacza się układy użytkownika (user coordinate system) oraz układ, względem którego chcemy przemieszczać końcówkę manipulatora (jog coordinate system). W istocie jedynie orientacja tego ostatniego układu jest istotna. Jeżeli w gnieździe znajduje się więcej robotów niż jeden, to definiowany jest układ gniazda (cell coordinate system). Jest to układ odniesienia wspólny dla wszystkich robotów. Układy odniesienia mogą być definiowane za pomocą ramienia robota. Metodą trójpunktową można ustalić TCP, natomiast sześciopunktową zarówno TCP, jak i orientację definiowanego układu.
Stosując te metody definiowania układów odniesienia należy zadbać, by wskazywane punkty w znaczący sposób różniły się od siebie zarówno co do położenia, jak i orientacji narzędzia doprowadzanego do danego punktu. Istnieje wiele wariantów wspomnianych metod. W okienku na panelu programowania wyświetlane są wskazówki, co należy zrobić, by uzyskać zamierzony cel. Ponadto należy wskazać układ związany z podłożem gniazda (cell floor). Warto też zdefiniować bezpieczną pozycję odniesienia (reference position), do której może przemieścić się robot, np. by wystartować realizację nowego programu. Można zdefiniować do dziesięciu takich pozycji. Ze względów bezpieczeństwa można ograniczyć ruch w poszczególnych złączach manipulatora. Można także z pewnymi
obszarami przestrzeni roboczej skojarzyć sygnały wejścia/wyjścia. Sygnały te służą porozumiewaniu się robota z urządzeniem dodatkowym. Dzięki temu, gdy urządzenie to zajmuje wskazaną przestrzeń roboczą, robot do niej nie wniknie i na odwrót. Aby uniknąć zakleszczenia (deadlock) urządzeniom można nadać priorytety. Obszary wykluczenia definiowane są jako prostopadłościany, przy czym można wybrać, czy obszarem wykluczonym jest wnętrze czy zewnętrze prostopadłościanu. Jak głęboko manipulator wniknie do obszaru wykluczonego, gdy jest on zajęty przez urządzenie dodatkowe, zależy od aktualnej prędkości ruchu ramienia. Manipulator zatrzymuje się z określonym przyspieszeniem ujemnym, a nie natychmiast. Należy to wziąć pod uwagę przy określaniu wymiarów prostopadłościanu.
Wskazanym jest, by sterownik był poinformowany, jak będzie obciążone ramię robota (PAYLOAD). W tym celu należy podać masę narzędzia i przemieszczanego obiektu oraz gdzie się znajduje ich środek ciężkości. Sterownik dysponuje funkcją automatycznej identyfikacji parametrów obciążenia manipulatora. Właściwe określenie tych parametrów jest konieczne dla uzyskania ruchów pozbawionych wibracji oraz dla optymalizacji prędkości ruchu.
Struktura programu
Program składa się z instrukcji przeznaczonych do wykonania przez sterownik oraz atrybutów. W skład atrybutów wchodzą: nazwa programu, jego podtyp (subtype), daty utworzenia oraz ostatniej modyfikacji, nazwy pliku źródłowego, rozmiar programu, wskazówki, czy zawiera dane pozycyjne, rozmiar stosu, maska grupy, zabezpieczenie przed modyfikacją, włączenie/wyłączenie przerwań etc. Instrukcje programu są ponumerowane.
Program może składać się z następujących elementów: zadanie (job), proces (process), makro (macro), program warunkowy (condition) oraz kolekcji (collection). Zadanie stanowi program główny. Proces jest podprogramem wywoływanym przez program główny. Makro stanowi program stworzony, by wykonać makroinstrukcję – należy go
traktować jako rodzaj podprogramu obsługi zdarzenia (nie ma nic wspólnego z makrem znanym z informatyki). Makro wywoływane jest przez: przycisk na panelu programowania, uaktywnienie odpowiedniego pola na jego ekranie, bądź sygnał wejściowy (te źródła zdarzeń nazywane są w dokumentacji urządzeniami – device). Makro może być też wywołane w innym programie przez użycie jego nazwy. Program warunkowy związany jest z funkcją monitorującą stan systemu. Kolekcje stanowią programy nieprzeznaczone do wykonania przez roboty. Ponieważ sterownik może oddziaływać nie tylko na silniki manipulatora, ale także na silniki związane z innymi urządzeniami, można je pogrupować. Do tego służy maska grupy. W ten sposób wskazuje się, którymi silnikami steruje dany program.
Podstawową grupą instrukcji są rozkazy ruchu, które określają, jak i dokąd należy przemieścić narzędzie. Ich parametrami są:
• rodzaj ścieżki ruchu,
• pozycja, do której ma dotrzeć narzędzie,
• prędkość ruchu (feed rate),
• czy narzędzie ma dotrzeć do wskazanej pozycji precyzyjnie oraz
• dodatkowa instrukcja, która ma być wykonana w trakcie realizacji ruchu. Wyróżniono cztery rodzaje ścieżek ruchu:
• wyrażone w przestrzeni konfiguracyjnej J (joint),
• liniowe w przestrzeni operacyjnej L (linear),
• po okręgu w przestrzeni operacyjnej C (circular),
• po łuku A (arc circle).
W przestrzeni konfiguracyjnej wszystkie silniki rozpoczynają ruch jednocześnie i kończą go w tym samym momencie. Czasy rozpędzania i czasy hamowania wszystkich złącz są jednakowe. Ruch liniowy w przestrzeni operacyjnej powoduje przemieszczenie TCP narzędzia wzdłuż linii prostej od pozycji aktualnej do docelowej. Orientacja narzędzia zmienia się liniowo wokół jego TCP. Ruch po okręgu odbywa się od pozycji aktualnej przez pośrednią do docelowej. Orientacja narzędzia zmieniana jest liniowo. Ruch po łuku jest podobny do tego po okręgu. Różnica polega na tym, że w ruchu po okręgu określa się pozycję pośrednią i docelową, natomiast w ruchu po łuku określa się jedynie pozycję docelową. Sekwencja pozycji wymienionych w kolejnych instrukcjach ruchu po łuku tworzy pożądaną krzywą.
Niezależnie od rodzaju ścieżki z pozycjami pośrednimi może być związany
jeden z atrybutów – dokładnie (FINE) lub kontynuuj (CNT). W pierwszym przypadku narzędzie zostanie ustawione dokładnie w zadanej pozycji i ruch zostanie wstrzymany, natomiast w drugim przypadku narzędzie nie zostanie doprowadzone dokładnie do wskazanej pozycji, a ruch będzie kontynuowany bez zatrzymania. Można wskazać procentowo, w jakim stopniu narzędzie może się oddalić od wskazanej pozycji. Można też ograniczyć maksymalną prędkość ruchuza pomocą instrukcji JOINT_MAX_SPEED[i], która nakłada ograniczenie na maksymalną prędkość ruchu złącza [i] manipulatora bądź urządzenia dodatkowego, oraz LINEAR_MAX_SPEED, która ogranicza prędkość ruchu narzędzia w przestrzeni operacyjnej. Instrukcja PAUSE powoduje przerwanie aktualnie wykonywanego ruchu (robot wyhamowuje). Wykonanie programu po restarcie rozpocznie się od kolejnej instrukcji w programie po tej, której wykonanie zostało przerwane. Instrukcja ABORT działa podobnie, z tą różnicą, że program nie może być zrestartowany.
Istnieją dodatkowe instrukcje wpływające na sposób wykonania ruchu określonego przez kolejne rozkazy ruchu. Przykładowo, dodanie instrukcji Wjnt powoduje, że w trakcie ruchu po prostej lub okręgu TCP nadal podąża zadaną ścieżką, ale nadgarstek nie
zmienia orientacji w zadany sposób. Umożliwia to przejście przez pozycję osobliwą. Można też spowalniać ruch wykorzystując instrukcję ACC, która redukuje maksymalne przyspieszenia. Instrukcja SKIP powoduje badanie wskazanego warunku w trakcie realizacji ruchu. W zależności od jego spełnienia aktualny ruch jest przerywany i wybierany jest inny wariant wykonania ruchu – opisany innymi instrukcjami ruchu. Instrukcja OFFSET bądź TOOL_OFFSET modyfikuje pozycję docelową w zależności od spełnienia zdefiniowanego warunku. Wartość modyfikacji może być wyrażona w przestrzeni konfiguracyjnej albo operacyjnej. Zazwyczaj wspomniane warunki konstruowane są tak, by zawierały wartości sygnałów wejściowych, co umożliwia wpływanie na wykonanie programu zależne od sytuacji zewnętrznej.
Instrukcja Simultaneous EV powoduje, że ruch manipulatora zostanie zsynchronizowany z ruchem dodatkowego urządzenia, np. taśmociągu. W efekcie ruchy obu urządzeń rozpoczną się i zakończą równocześnie. Istnieje również wariant tej instrukcji (Independent EV), w którym manipulator i urządzenie dodatkowe rozpoczną ruch jednocześnie, ale skończą go niezależnie od siebie. Zastosowanie instrukcji WAIT w sekwencji instrukcji ruchu spowoduje oczekiwanie na spełnienie warunku, który może być wyrażony jako czas oczekiwania albo pojawienie się odpowiedniego sygnału wejściowego. Jeżeli poprzedzająca instrukcja ruchu zawierała CNT, ruch będzie powstrzymany, a narzędzie będzie się starać dojść do wyspecyfikowanej pozycji. Jeżeli czas oczekiwania jest dostatecznie długi, a dodatkowo użyto instrukcji BREAK, to osiągnięta zostanie wyspecyfikowana pozycja dokładnie. Wszakże, jeżeli nie użyto instrukcji BREAK, to oczekiwanie odbędzie się na łuku łączącym aktualny i kolejny segment ruchu w pewnej odległości od wyspecyfikowanej pozycji. Wykorzystując instrukcje TB (time before) lub TA (time after) można spowodować równoległe do ruchu wykonanie dodatkowego programu lub ustawienie wyjścia przed lub po zakończeniu ruchu. Umożliwia to uruchomienie lub wyłączenie dodatko-
wych urządzeń w odpowiedniej fazie ruchu. Można również zmodyfikować wykonanie instrukcji ruchu tak, aby wywołany został program lub ustawione wyjście, gdy narzędzie pojawi się w pewnej odległości od punktu docelowego lub pośredniego ścieżki DB (distance before). Instrukcje ruchu modyfikowane za pomocą TA, TB lub DB mogą wykonać zestawy instrukcji z nimi związane bez odwoływania się do programu (podprogramu). Zestaw takich instrukcji wyróżniany jest za pomocą słowa kluczowego POINT_ LOGIC. Instrukcje zestawu nie mogą zawierać instrukcji ruchu. Zestaw kończony jest pojawieniem się instrukcji ruchu. Bezpośrednio w instrukcji ruchu można wymienić wyjścia, które mają być ustawione podczas ruchu. Istnieje też możliwość zdefiniowania warunków, które monitoruje sterownik niezależnie od jego innych aktywności. Monitorowanie dotyczy instrukcji umieszczonych w sekcji MONITOR <nazwa> <instrukcje> MONITOR END <nazwa>. Monitorowany warunek określony jest przez <nazwa> WHEN <warunek> CALL <nazwa programu warunkowego> . Wykrycie spełnienia warunku aktywuje związany z nim program warunkowy.
Translacja ruchu
Program zapisany jako sekwencja ruchów do określonych pozycji może być odtworzony w innym miejscu niż został pierwotnie stworzony. Do tego służy instrukcja SHIFT. Wszystkie pierwotne po-
zycje programu mogą być przesunięte o pewien wektor. By tak się stało albo należy wskazać, który punkt pierwotnego programu ma być przesunięty, do którego nowego punktu albo trzeba wyspecyfikować wektor translacji. Można też przesunąć i jednocześnie obrócić zaprogramowane ścieżki ruchu. W tym celu należy podać trzy punkty ścieżek wymienionych w pierwotnym programie oraz gdzie te trzy punkty mają się znaleźć w nowym położeniu. Można też zażądać lustrzanego odbicia pierwotnego programu względem płaszczyzny równoległej do płaszczyzny XZ układu związanego z narzędziem.
Wprowadzono ułatwienie specyfikacji zestawu tych samych czynności wykonywanych w różnych miejscach obróconych względem siebie o ten sam kąt względem wskazanej osi obrotu (angle entry shift function). Specyfikacja wymaga podania trzech punktów na obwodzie okręgu oraz kąta obrotu. Możliwe jest też dodanie punktu leżącego na osi obrotu będącej prostopadłą do płaszczyzny wyznaczonej przez te trzy punkty. Funkcja ta może być przydatna np. przy wykonywaniu tych samych operacji na otworach przeznaczonych do mocowania koła samochodowego do piasty. Można też zmieniać układy odniesienia, względem których realizowane będą ruchy. Wtedy czynności będą wykonane względem nowego układu odniesienia, zamiast w stosunku do układu odniesienia, względem którego pierwotnie nauczono program (coordinate system
change shift function). Takiej zmianie może podlegać również układ związany z narzędziem.
Paletyzacja
Ponieważ zadanie paletyzacji jest często wykonane przez roboty, wprowadzono specjalną instrukcję złożoną PALLETIZING. Podstawową kwestią jest wybór sposobu paletyzacji. Są cztery sposoby wynikające z dwóch wzorców: wzorca stosu paletyzacji oraz wzorca ścieżki. Wzorzec stosu paletyzacji może być prosty bądź złożony, natomiast wzorzec ścieżki może być pojedynczy albo wielokrotny.
Definicja wzorca paletyzacji wymaga określenia kolejności i sposobu układania obiektów na palecie oraz jej miejsc charakterystycznych. Określa się je za pomocą instrukcji ruchu. Ponadto potrzebna jest instrukcja sterująca chwytakiem. Paleta może być jedno-, dwu- lub trójwymiarowa. Ułożenie elementów na palecie nie musi być prostopadłościenne, a obiekty mogą mieć różne orientacje. Koniec definicji wzorca zaznacza się instrukcją PALLETIZING-END. Wzorce ścieżek określają sposób dochodzenia do i odchodzenia od paletyzowanych obiektów. Instrukcja paletyzacji korzysta
z rejestrów pozycyjnych do swej realizacji. Ponadto korzysta z rejestrów paletyzacji (PALLETIZING REGISTER - PL), w których przechowuje informacje na temat kolumny, wiersza oraz warstwy obiektu na palecie, czyli pełni rolę złożonego licznika. W programie można skorzystać z co najwyżej 32 takich rejestrów. Na elementach rejestru paletyzacyjnego można wykonywać operacje dodawania i odejmowania.
Instrukcje wejścia/wyjścia
Wprowadzono dużą gamę instrukcji wejścia/wyjścia umożliwiających wczytanie wartości sygnałów wejściowych bądź wysłanie wartości do wyjścia. Instrukcje te zostały pogrupowane w zależności od przynależności wejść/wyjść do odpowiednich części systemu oraz ich rodzaju. Istnieją wejścia/wyjścia związane z pakietami montowanymi w sterowniku (I/O unit): binarne systemowe (DI/DO), analogowe (AI/AO), przekształcane na formę cyfrową i binarne grupowe (GI/GO), operujące na liczbach szesnastkowych. Wejścia binarne czytane są za pomocą instrukcji podstawienia (np.\ =DI), natomiast wyjścia (np.\ DO) są zerowane lub ustawiane (ON/OFF). Na wyjścia cyfrowe można też wysłać impuls o określonym czasie trwania (PULSE). Z wejścia analogowego (AI) można odczytać wartość i umieścić ją w rejestrze, natomiast do wyjścia analogowego można przesłać albo wartość stałą albo zawartość rejestru (R). Wejścia i wyjścia cyfrowe mogą być zgrupowane i wtedy można wczytywać lub wysyłać liczby binarne. Dostępne są też wejścia/wyjścia specjalizowane: cyfrowe robota (RI/RO), związane z kołnierzem manipulatora, peryferyjne (UI/UO), związane z panelem progra-
mowania oraz panelem operatora (SI/SO); związane z panelem sterownika.
Instrukcje warunkowe skoku, pętle
Instrukcje sterujące wykonaniem programu umożliwiają zmianę sekwencji wykonywanych rozkazów programu. Można zdefiniować etykietę skoku (LBL) oraz wykonać do niej skok bezwarunkowy (JMP LBL). Ponadto można wykonać skok warunkowy za pomocą instrukcji IF. Warunek budowany jest jako porównanie wartości wejścia lub wyjścia odpowiedniego typu z zawartością rejestru albo stałą. Można też konstruować złożone wyrażenia logiczne stosując spójniki AND oraz OR, ale w ramach pojedynczego wyrażenia tylko jednego z tych dwóch rodzajów. Dopuszczalne jest również użycie negacji, jako prefiksowy operator oznaczany wykrzyknikiem. Skok może być wykonany do wskazanej etykiety albo można wywołać inny program (CALL) – w istocie jest to wtedy podprogram. Program może być również wywołany bezpośrednio za pomocą instrukcji CALL. Do programu wywoływanego można przekazać argumenty. Każdy program kończony jest instrukcją END. Dojście do tej instrukcji zwraca sterowanie programowi, który wywołał program zawierający instrukcję END. Istnieje też instrukcja wielokrotnego wyboru SELECT rejestr = wartość skok, = wartość skok, … ELSE skok, gdzie skok to skok bezwarunkowy (JMP LBL) albo wywołanie programu
(CALL). Ponadto istnieje standardowa instrukcja warunkowa IF THEN ELSE ENDIF. Instrukcje te mogą być zagnieżdżane. Można też konstruować pętle za pomocą FOR ENDFOR. W zależności od tego, czy licznik pętli ma liczyć w dół czy w górę stosuje się słowo kluczowe TO bądź DOWNTO przed wartością określającą liczbę powtórzeń. Dopuszczalne jest dziesięciokrotne zagnieżdżenie pętli FOR, ale trzeba dopilnować, by każda z pętli używała innego rejestru licznika.
Praca współbieżna
Sterowniki robotów FANUC umożliwiają współbieżną realizację programów (multitasking). Wszakże należy zadbać, by instrukcje ruchu nie dotyczyły tych samych napędów. Można np. utworzyć dwa programy działające współbieżnie, jeden sterujący manipulatorem, a drugi taśmociągiem. Sposób tworzenia współbieżnych programów jest identyczny z tworzeniem indywidualnych programów. Jeden z programów musi być nadrzędny i ten powinien uruchomić pozostałe za pomocą instrukcji RUN.
Synchronizacja pracy dwóch programów odbywa się za pomocą wskazanego rejestru. Jeden program go ustawia, a drugi oczekuje (stosując instrukcję WAIT) na pojawienie się w nim odpowiedniej wartości, np. 0 lub 1. Ponieważ pod pewnymi warunkami programy mogą być wykonywane zarówno w przód, jak i wstecz, to wykonanie programu głównego wstecz pociąga za sobą realizację instrukcji programu
współbieżnego, również w odwrotnej kolejności ustawienia jego instrukcji.
Instrukcje oczekiwania
Instrukcja WAIT powoduje wstrzymanie wykonania programu na określony czas lub do momentu zajścia zdarzenia opisanego warunkiem. Warunki są konstruowane tak samo, jak dla instrukcji warunkowych. Dodatkowym parametrem oczekiwania na zajście zdarzenia może być czas, po którym należy przerwać oczekiwanie mimo braku zajścia zdarzenia (TIMEOUT). Istnieje też możliwość wystartowania, wyzerowania, ustawienia bądź zatrzymania czasomierza za pomocą instrukcji TIMER. Jeżeli wybrany zostanie czasomierz globalny, to różne zadania mogą się względem niego synchronizować. Czasomierze mogą być stosowane do pomiaru czasu wykonania pewnych fragmentów programu. Umożliwiono też sygnalizację operatorowi systemu zachodzących zdarzeń. Służy do tego instrukcja sygnalizacji alarmu użytkownika UALM wstrzymująca działanie programu i wyświetlająca odpowiedni komunikat na panelu programowania. Można zwiększyć czytelność programu używając komentarzy, poprzedzając je wykrzyknikiem.
Język KAREL
Programy dla robotów FANUC mogą też być tworzone bez udziału panelu programowania. Można je pisać na dowolnym komputerze, wykorzystując język KAREL. Program w języku KAREL musi być poddany translacji, w wyniku której powstaje program w kodzie pośrednim (p-code) akceptowany przez panel programowania, a następnie wynik kompilacji ładowany jest do sterownika R-30iA/R-30iB w celu jego interpretacji. Nie ma możliwości bezpośredniego tworzenia programu w języku KAREL na panelu programowania, ani wykonania kodu źródłowego takiego programu bezpośrednio na sterowniku robota. KAREL jest językiem programowania wyższego poziomu niż język panelu programowania (TP). Program w języku KAREL (PROGRAM) składa się z następujących sekcji:
• dyrektyw dla translatora,
• deklaracji stałych (CONST),
• typów danych (TYPE),
• zmiennych (VAR) oraz
• podprogramów (ROUTINE).
Struktura programu w języku KAREL
Program główny zapisywany jest między słowami kluczowymi BEGIN i END, po których znów mogą pojawić się deklaracje podprogramów. Zmiennym można nadać ich wartości w tradycyjny sposób lub za pomocą panelu programowania za pomocą uczenia. Do sterownika można załadować wiele programów powstałych w wyniku kompilacji źródeł zapisanych w języku KAREL. Zmienne mogą być wspólne dla wielu programów. W trakcie wykonania programów tworzony jest plik LOG, w którym zapamiętywany jest ślad wykonanych instrukcji. Można go obejrzeć wydając polecenie SHOW HISTORY. Ułatwia to wskazanie przyczyny błędu, jeżeli taki powstanie.
Język KAREL wykorzystuje identyfikatory zarówno podprogramów, stałych, jak i zmiennych, tworzonych standardowo, jak we wszystkich innych językach. Korzysta też z etykiet (zakończonych podwójnym dwukropkiem), które wskazują miejsca skoku dla instrukcji GOTO. Czytelność programów zwiększana jest przez zastosowanie komentarzy, poprzedzanych podwójnym myślnikiem (--). Zmienne i stałe mogą być typów prostych, strukturalnych bądź zdefiniowanych przez użytkownika. Typami prostymi są: BOOLEAN, INTEGER, REAL, STRING oraz FILE. Typami strukturalnymi są:
• tablice (ARRAY), mające co najwyżej trzy wymiary,
• konfiguracja (CONFIG) określająca wariant ułożenia członów ramienia,
• wektor wartości zmiennych złączowych (JOINTPOSi, i = 1 ,…, 9),
• model (MODEL),
• ścieżka wyrażona jako lista węzłów (PATH), gdzie węzły zawierają m.in. informację o pozycjach (POSITION) definiujących ścieżkę,
• pozycja w przestrzeni operacyjnej zdefiniowana przez podanie współrzędnych początku układu oraz kąty orientacji (w konwencji: yaw, pitch, roll) i uzupełniona o pożądaną konfigurację złącz (POSITION),
• pozycja w przestrzeni operacyjnej zdefiniowana przez podanie współrzędnych początku układu oraz kąty orientacji (w konwencji: yaw, pitch, roll) i uzupełniona o konfigurację (XYZWPR),
• pozycja XYZWPR uzupełniona o pozycje złącz sprzętu dodatkowego (XYZWPREXT) oraz
• trójwymiarowy wektor (VECTOR). Typy danych użytkownika tworzone są z typów prostych i strukturalnych i mają postać rekordu definiowanego między słowami kluczowymi
STRUCTURE i ENDSTRUCTURE. Każde pole takiej struktury ma nazwę własną oraz typ. Nazwa własna pola służy do odwoływania się do zawartej w tym polu wartości. Stosuje się odwołanie do zmiennej danego typu oraz notację z kropką wskazującą, o które konkretnie pole chodzi. Na zmiennych typów prostych, w zależności od ich typu, można przeprowadzać standardowe operacje: logiczne, arytmetyczne i relacyjne (porównania), uzupełnione o specjalne operacje na pozycjach oraz operacje na stringach.
Instrukcje języka KAREL Język KAREL zawiera standardowe instrukcje sterujące wykonaniem programu. Są to instrukcje warunkowe (IF THEN ELSE ENDIF) oraz wielokrotnego wyboru (SELECT CASE ENDSELECT), pętle (FOR ENDFOR, REPEAT ENDREPEAT oraz WHILE ENDWHILE), skoku do etykiety (GOTO), przerwania wykonania programu (ABORT), wstrzymania wykonania programu na określony czas (DELAY), zawieszenia wykonania programu (PAUSE) oraz wstrzymania wykonania programu do chwili zajścia odpowiedniego zdarzenia lub spełnienia odpowiedniego warunku (WAIT). Istnieją również zestawy akcji, które wykonywane są, gdy wykryte zostanie spełnienie warunku (CONDITION WHEN). Warunki te są monitorowane równolegle do wykonywania standardowych programów. Obsługa warunku może być uaktywniana (ENABLED) oraz dezaktywowana (DISABLED). Akcje, które mają być wykonane w przypadku spełnienia warunku są ograniczone. KAREL dysponuje również procedurami i funkcjami, czyli podprogramami (ROUTINE). Te pierwsze nie zwracają wartości, natomiast te drugie robią to. Procedury są wywoływane bezpośrednio wewnątrz programów bądź procedur, natomiast funkcje są wywoływane wewnątrz wyrażeń. Dopuszcza się wywołania rekursywne tej samej funkcji bądź procedury. Powrót z podprogramu następuje po napotkaniu albo instrukcji RETURN albo końca jego definicji (END). Parametry podprogra-
mu mogą być przekazywane albo przez wartość albo przez referencję. Oprócz procedur i funkcji definiowanych przez programistę KAREL dysponuje potężną biblioteką wbudowanych podprogramów.
Operacje na szeregowych strumieniach danych (np. RS-232) wykonywane są, jak na plikach (FILE). W związku z tym zarówno dla strumieni danych, jak i plików zdefiniowano standardowe operacje: OPEN, CLOSE, READ oraz WRITE. W ten sposób sterownik może się kontaktować zarówno z panelem programowania, jak i zewnętrznym komputerem (CRT/KB). Przed otwarciem szeregowego łącza trzeba zdefiniować jego atrybuty za pomocą instrukcji SET_FILE_ATR. Pliki mogą być binarne bądź w formacie XML. W tym drugim przypadku można skorzystać z wbudowanego interpretera języka XML. KAREL ponadto umożliwia korzystanie z gniazd (socket). Dzięki temu sterownik może kontaktować się z innymi komputerami używając protokołu TCP/IP. Istnieje biblioteka funkcji służących do przesyłania wiadomości poprzez gniazda. Dostępna jest także możliwość przesyłania zawartości rejestrów pomiędzy sterownikami robotów połączonych siecią Ethernet. Do tego służą funkcje języka KAREL, które działają w trybie klient-serwer (RGETNREG, RSETNREG, RGETPREG, RSETPREG). W tym przypadku także stosuje się protokół TCP/IP.
Za pomocą instrukcji języka KAREL można zdefiniować pozycje w prze -
strzeni operacyjnej. Wprawdzie ruch do tych pozycji można wykonać, ale nie bezpośrednio za pomocą instrukcji tego języka, ale za pomocą instrukcji języka programowania panelu programowania (TP). Procedury języka KAREL (move_to_pr – move to pose register, movl_to_pr – move linear to pose register) wywołują instrukcje języka panelu programowania. Dane pozycyjne, jak już wspominano, definiuje się za pomocą: POSITION, XYZWPR, XYZWPREXT i JOINTPOS oraz listy złożonej z tych elementów, czyli PATH. Pozycje te wyrażane są względem układów odniesienia. Wprowadzono trzy typy tych układów:
• WORLD – globalny układ odniesienia związany z konkretnym typem robota,
• UFRAME – układ określony przez użytkownika, wyrażony względem układu globalnego i o tej samej orientacji, co on, oraz
• UTOOL – układ TCP związany z narzędziem, także określany przez użytkownika, ale względem kołnierza manipulatora.
Ruch robota może być definiowany:
• w przestrzeni konfiguracyjnej (JOINT),
• w przestrzeni operacyjnej względem układu globalnego (WORLD), wtedy orientacja określana jest względem jego osi głównych,
• w przestrzeni operacyjnej względem układu narzędzia (TOOLFRAME),
• w przestrzeni operacyjnej względem układu uczenia (JOGFRAME),
• w przestrzeni operacyjnej względem wybranego układu użytkownika (USER FRAME).
We wszystkich tych przypadkach ruch interpolowany jest liniowo w odpowiadającej jego definicji przestrzeni.
KAREL, podobnie jak język panelu programowania (TP), umożliwia operowanie na wejściach i wyjściach sterownika. Tu także wyróżniono wejścia i wyjścia cyfrowe (DIN, DOUT), analogowe (AIN, AOUT) i zgrupowane porty DIN/DOUT (GIN, GOUT). Ponadto można bezpośrednio odwoływać się do wejść i wyjść sterownika połączonych z manipulatorem (RDI, RDO) bądź z panelem operatora (OPIN, OPOUT), a także panelem programowania (TPIN, TPOUT).
Można także sterować chwytakiem (OPEN/CLOSE HAND).
KAREL umożliwia tworzenie słowników i formularzy, które wykorzystywane są do komunikacji z operatorem przez panel programowania (TP) oraz zewnętrzny komputer (CRT/KB). Słowniki zawierają teksty przeznaczone do wyświetlania użytkownikowi, ale nie zawierają informacji, jak dany tekst ma być przedstawiony. Opis, jak ma być sformatowany tekst, określany jest za pomocą formularza. Dzięki temu okna tworzone przez użytkownika przypominają te standardowe wyświetlane na panelu programowania. Formularze służą też wprowadzaniu danych. Ponadto sprawdzają, czy wczytywane dane są odpowiedniego typu.
Wielozadaniowość
Sterownik robota umożliwia wielozadaniowość, więc ta możliwość została odtworzona w języku KAREL. Oczywiście jest to wielozadaniowość realizowana w podziale czasu, bo sterownik ma jeden procesor. Ponieważ programy są interpretowane na sterowniku, każdy uruchomiony program (zadanie) ma własny interpreter obsługujący go. Na instrukcje zawarte w zadaniach narzucono ograniczenie mówiące, że dwa zadania nie mogą zawierać instrukcji ruchu sterujących tymi samymi osiami – powinny to być rozdzielne grupy napędów (manipulatora i urządzenia dodatkowego traktowanymi zbiorczo). Zadania mają przyporządkowane priorytety, na podstawie których program harmonogramujący decyduje, które z nich ma być wykonywane w danej chwili.
Do działań na zadaniach język KAREL stosuje się instrukcje: RUN_TASK, CONT_TASK, PAUSE_TASK, ABORT_TASK, GET_TSK_INFO, CONTINUE, ABORT, PAUSE. Ostatnie trzy instrukcje dotyczą programów warunkowych, natomiast te wcześniej wymienione odnoszą się do zadań. Synchronizacja pracy zadań odbywa się za pomocą semaforów wielowartościowych. Instrukcja CLEAR_ SEM zeruje wartość semafora, natomiast POST_SEMA dodaje 1 do jego aktualnej wartości. Instrukcja SEMA_ COUNT umożliwia odczytanie aktualnej wartości semafora. Oczekiwanie na semaforze realizowane jest za pomocą instrukcji PEND_SEMA. Jej wykonanie powoduje odjęcie 1 od jego wartości i zatrzymanie wykonania zadania, jeżeli jego wartość jest niedodatnia. Informacje między zadaniami mogą być przekazywane poprzez kolejki. Po zainicjalizowaniu kolejki instrukcjię NIT_QUEUE, można do niej wprowadzać informacje (APPEND_QUEUE) oraz pobierać je (GET_QUEUE).
Praca na zdalnych urządzeniach
Na zdalnym komputerze można pracować z wykorzystaniem środowiska programowego KAREL Command Language (KCL). Komendy skierowane do tego środowiska składają się ze słowa kluczowego oraz odpowiednich parametrów. Służą one do działania na plikach (LOAD, COPY, DELETE, DIRECTORY), edytowania programów (EDIT), uruchamiania programów (RUN, CONTINUE). Jeżeli program zawiera instrukcje ruchu, to zostaną one wykonane na dołączonym sterowniku. Można też tworzyć pliki wsadowe (.CF) zawierające sekwencje komend KCL, które następnie można wykonać jednym poleceniem (RUNCF). Ponadto KCL umożliwia korzystanie z wielozadaniowości.
Programowanie
za pomocą tabletu
Niektóre sterowniki robotów FANUC (R-30iB Plus, R-30iB Mate Plus, R-30iB Mini Plus) można programować za pomocą tabletu. Tablet musi być przytwierdzony do specjalnej bazy i musi mieć zainstalowane odpowiednie
oprogramowanie. Baza jest wyposażona w przycisk stopu awaryjnego oraz urządzenie uaktywniające. Ekran tabletu podzielony jest na: menu, ikony zależne od wybranej opcji, obszar wyświetlający stan robota, graficzną reprezentację robota. W zależności od wybranej opcji można edytować programy, wykonywać je lub sterować ręcznie ruchami robota zarówno w przestrzeni konfiguracyjnej jak i operacyjnej.
Programowanie odbywa się za pomocą języka ikonicznego, którego funkcje odzwierciedlają te, które realizuje język panelu programowania (TP), wszakże lista instrukcji jest nieco rozszerzona. Argumenty numeryczne wprowadzane są do odpowiednich pól w aktualnie wyświetlanym okienku lub wykorzystując udostępnione suwaki. Jednym z rozszerzeń jest ruch wzdłuż ścieżki wyrażanej jako funkcja sklejana (spline). Dla robotów serii CRX wprowadzono instrukcję ruchu do wskazanego celu lub do wykrycia kontaktu (Touch Skip). Innym udogodnieniem jest instrukcja umożliwiająca zapamiętanie punktów wzdłuż ścieżki powstającej wskutek ruchów ręcznych. Punkty zapamiętywane są w regularnych odstępach czasu. Dla robotów spawających wprowadzono wiele instrukcji ułatwiających ich programowanie, w tym możliwość nanoszenia ruchu oscylacyjnego w poprzek zadanej ścieżki (weave), co ułatwia rozprowadzanie spoiwa w szczelinie między spawanymi elementami.
Za pomocą tabletu można wywoływać poszczególne operacje w środowisku programistycznym nie tylko klikając w ikony, ale również wywołując je za pomocą komend wydawanych głosem. Wówczas tablet musi być podłączony do Internetu i odłączony od sterownika. Rozpoznawanie głosu obsługuje oprogramowanie Google. Stosowanie tabletu umożliwia ładowanie do sterownika oprogramowania (PLUGIN) dostarczanego przez producentów sprzętu dodatkowego, np. sterujące czujnikami bądź chwytakami. Wtedy sterownik będzie nadzorować pracę takiego sprzętu. Jedną z możliwości jest użycie kamery do lokalizacji przedmiotów, które mają być uchwycone. Wcześniej należy kamerę skalibrować. Zestaw instrukcji ruchu wykorzystujących informację z kamery nieco się różni od zestawu podstawowego, bo dodatkowym parametrem jest informacja pozyskana dzięki kamerze. Koboty CRX, które wyposażone są w czujniki siły, mogą stosować instrukcje siłowe udostępniane przez tablet. Instrukcje te mogą powodować wywieranie stałej siły, wprowadzanie wałka w okrągły otwór, wprowadzanie belki o kwadratowym przekroju w otwór o tym samym przekroju, dopasowanie powierzchni, wykrywanie nadmiarowego obciążenia, śledzenie konturu lub dokręcanie śruby.
Podsumowanie
W zaprezentowanym cyklu artykułów przedstawiono sposoby programowania robotów czterech globalnych firm produkujących roboty przemysłowe. Takich firm jest więcej, ale koniecz-
ne było ograniczenie liczby metod programowania, które można opisać w tekście o ograniczonym wolumenie, i jednocześnie na tyle dużej, by z cyklu artykułów wynikały zarówno różnice, jak i elementy wspólne dla sposobów programowania robotów przemysłowych. Wprawdzie starano się dość dokładnie opisać możliwości sterowników tych robotów, ale w przeglądowym cyklu artykułów trudno jest odzwierciedlić wszelkie szczegóły. Skoncentrowano się na językach programowania oraz sposobach tworzenia programów, pomijając kwestie drugorzędne z punktu widzenia ogólnego zaznajomienia się z opisywaną materią. Wszakże, gdyby ktoś chciał na tej podstawie napisać złożony program, zapewne natrafiłby przy jego uruchomieniu na problemy. W opisie pominięto wiele niuansów, które mają wpływ zarówno na przetwarzanie, jak i wykonanie kodu programu. Celem cyklu było wprowadzenie w dziedzinę. Ci czytelnicy, którzy zetknęli się z dokumentacją do robotów przemysłowych, zapewne docenią takie streszczenie. Dokumentacja, na podstawie której przygotowano ten zestaw artykułów, liczyła kilka tysięcy stron.
Z przedstawionego opisu wynika, że obecny stan języków programowania odzwierciedla historyczne zaszłości. Panuje skłonność rozszerzania możliwości sterowników przez dodawanie instrukcji oraz ich parametrów. Nie sądzę, by ułatwiało to użycie tych języków. Podejrzewam, że bez solidnego szkolenia trudno uzyskać dobrego pro-
gramistę. Ciekawym jest, że instrukcje ruchu, pomijając szczegóły, ograniczają się w zasadzie do trzech rodzajów: ruchu w przestrzeni konfiguracyjnej oraz dwóch typów ruchów w przestrzeni operacyjnej: po prostej i po okręgu. Oczywiście dzięki łączeniu segmentów bez konieczności dokładnego dojścia do poszczególnych pozycji ścieżki powstają krzywe bardziej złożone, ale o bliżej nieznanym opisie matematycznym. Zastosowanie matematycznych generatorów trajektorii niewątpliwie zwiększyłoby różnorodność opisu ścieżek i zachowania się narzędzia wzdłuż nich, a jednocześnie zredukowało liczbę parametrów niezbędnych do wymuszenia pożądanego ruchu. Niemniej jednak nie widać u producentów robotów chęci skorzystania z takiego podejścia. Zasadniczy trend rozwojowy dotyczy przede wszystkim graficznych symulatorów gniazd roboczych oraz programowania ikoniczno-okienkowego. W tym cyklu artykułów nie przedstawiono dodatkowych bibliotek, które firmy udostępniają, ułatwiających tworzenie programów do konkretnych zastosowań.
Pierwszy robot przemysłowy pojawił się w 1960 r. Od tego czasu minęło ponad 60 lat, więc metody programowania tych robotów okrzepły, co z jednej strony powoduje, że zachowywane są dawne instrukcje, a z drugiej zachodzi powolna ewolucja polegająca na dodawaniu kolejnych drobnych modyfikacji. Należy się spodziewać, że zmiana paradygmatu związana z wprowadzeniem kobotów może zasadniczo wpłynąć na programowanie tych urządzeń. Robot przemysłowy zawsze był odgradzany od ludzi, by nie dochodziło do wypadków. W przypadku kobotów roboty te muszą bezpośrednio współpracować z ludźmi, więc nie można ich od nich odgrodzić. Bezpieczeństwo zapewnia się za pomocą ustanawiania stref bezpieczeństwa oraz bogatego oczujnikowania. Chwilowo jednak sposoby programowania kobotów tylko nieznacznie się różnią od metod wykorzystywanych przez roboty przemysłowe.
prof. dr hab. inż. Cezary Zieliński Politechnika Warszawska Fot.
Myślisz o robotyzacji?
Odkryj nowy wymiar robotyzacji Twojej produkcji z PIAP
Kompleksowa realizacja projektów przemysłowych
Renomowani dostawcy podzespołów
Ponad 150 inżynierów
Zaawansowane zaplecze projektowo-wytwórcze
Nowoczesne Centrum Szkoleniowe
Serwis gwarancyjny i pogwarancyjny
Przeszło
250 wdrożeń w obszarach automatyki i robotyki
Ponad
200 robotów zainstalowanych w zakładach produkcyjnych
Sieć Badawcza Łukasiewicz - Przemysłowy Instytut Automatyki i Pomiarów PIAP
Al. Jerozolimskie 202, 02-486 Warszawa
tel. 22 8740 194, 22 8740 442
e-mail: marketing@piap.lukasiewicz.gov.pl
www.przemysl.piap.pl
MARLENA KUDŁA Associate SKP Ślusarek Kubiak Pieczyk
Sztuczna inteligencja to dziedzina, która nieustannie się rozwija i oferuje coraz więcej możliwości oraz korzyści dla ludzkości. Nie wszystkie rozwiązania są jednak bezpieczne i pożądane z perspektywy społeczeństwa, a w szczególności zdrowia, bezpieczeństwa czy praw podstawowych. Akt o sztucznej inteligencji adresuje ten problem przez wskazanie tzw. zakazanych praktyk w zakresie AI.
Odpowiedzi na pytanie, jakie systemy AI będą już wkrótce zakazane w Unii Europejskiej, należy szukać w treści art. 5 Aktu o sztucznej inteligencji 1 (dalej AI ACT). Artykuł ten wyszczególnia bowiem kolejno w swojej treści praktyki uznane za szkodliwe i stanowiące nadużycie, przez co powinny być zakazane.
Aby filmy sci-fi nie stały się rzeczywistością Artykuł 5 rozpoczyna się od omówienia systemów AI stosujących techniki podprogowe (wykorzystujące bodźce wykraczające poza ludzką percepcję), manipulacyjne czy wprowadzające w błąd. Jak wskazano w motywie 29 do AI ACT, ma to na celu uniknięcie nakłaniania przez systemy AI osób do niepożądanych zachowań czy skłaniania do podjęcia decyzji wbrew ich swobodzie wyboru. Co istotne, prze -
pis mówi jednak, że systemy wykorzystujące takie techniki muszą prowadzić do istotnego zniekształcenia zachowania danej osoby lub grupy, np. sprawiając, że osoba podejmuje decyzję, której w innym wypadku by nie podjęła, co w konsekwencji powoduje lub może spowodować dla niej „poważną szkodę”. Co ciekawe, w motywie 29 wyjaśniono, że zakaz praktyk polegających na manipulacji nie powinien mieć wpływu na zgodne z prawem praktyki w kontekście leczenia – jak np. terapia psychologiczna czy rehabilitacja fizyczna – jeżeli są prowadzone zgodnie z prawem i za zgodą danej osoby. Podobnie z legalnymi i zasadnymi praktykami w dziedzinie reklamy.
Innym przykładem zakazanych praktyk w ramach systemów AI są systemy wykorzystujące tzw. social scoring, który może być nam znany z popkultury (np. film „Raport
mniejszości”). Klasyfikowanie osób na podstawie ich zachowania lub ich wnioskowanych cech osobowości będzie wkrótce prawnie zakazane, jeżeli miałoby prowadzić do dyskryminowania niektórych osób w jakimś innym kontekście lub w sposób nieuzasadniony do zachowania tej osoby.
AI ACT zakazuje ponadto systemów AI, które wykorzystują słabości danej osoby lub grupy, ze względu na ich wiek, niepełnosprawność, czy szczególną sytuację społeczną lub ekonomiczną, co także miałoby skutkować zniekształceniem zachowania takiej osoby/grupy i prowadzić lub móc prowadzić do spowodowania „poważnej szkody”. Jak wskazano w motywie 29, osoby żyjące w skrajnym ubóstwie, osoby z mniejszości etnicznych lub religijnych, mogą być potencjalnie bardziej narażone na ich wykorzystanie.
AI to nie wróżka
Artykuł 5 AI ACT pochyla się ponadto nad systemami AI wykorzystywanymi do predykcji kryminalnej, czyli do przewidywania ryzyka ponownego popełnienia przestępstwa na podstawie profilowania danej osoby, jej cech osobowości czy cech charakterystycznych, takich jak narodowość, miejsce urodzenia, miejsce zamieszkania, liczba dzieci, poziom zadłużenia lub rodzaj samochodu 2 Takie systemy AI również są uznawane za niedozwolone. Wyjątek dotyczy wspierania przez takie systemy dokonywanej przez człowieka oceny zaangażowania danej osoby w działalność przestępczą, o ile mamy uzasadnione podejrzenie co do tego, dodatkowo oparte na obiektywnie możliwych do zweryfikowania faktach. Zakaz ten nie dotyczy jednak analizy ryzyka, która nie opiera się na profilowaniu czy cechach osobistych lub charakterystycznych danej osoby. Przykładowo dopuszczalne są sytuacje, gdy analizowane są podejrzane transakcje w celu oceny prawdopodobieństwa nadużyć finansowych przez daną osobę 2
Za niedozwolone uznano systemy AI służące do rozpoznawania lub wyciągania wniosków na temat emocji osób w ich miejscu pracy, szkołach lub uczelniach, chyba że ma to związek ze względami medycznymi (np. do użytku terapeutycznego) czy bezpieczeństwa. Unijny ustawodaw-
dów politycznych, przynależności do związków zawodowych, przekonań religijnych lub filozoficznych, życia seksualnego lub orientacji seksualnej”. Zakaz ten nie dotyczy ścigania przestępstw czy etykietowania l egalnie zdobytych danych biometrycznych, np. w postaci sortowania
ca dostrzega ryzyka związane z takimi systemami AI, mają one bowiem ograniczoną wiarygodność i są nieprecyzyjne, choćby z uwagi na to, że wyrażanie emocji różni się w zależności od danej kultury czy sytuacji. Taki system AI wiąże się zatem z ryzykiem uzyskania dyskryminacyjnych wyników, a w efekcie prowadzi do niekorzystnego traktowania niektórych osób lub grup.
AI ACT zakazuje systemów AI, które pozyskują wizerunki twarzy z Internetu lub nagrań z telewizji przemysłowej w celu tworzenia lub rozbudowywania baz danych służących rozpoznawaniu twarzy. Praktyka ta bowiem wprowadza poczucie masowego nadzoru i może prowadzić do naruszeń prawa do prywatności.
Skomplikowane meandry biometrii Dosyć szczegółowa wydaje się kwestia związana z systemami AI wykorzystującymi biometrię. Zakazane są systemy kategoryzacji biometrycznej, które wykorzystują dane biometryczne osób fizycznych do wnioskowania informacji na temat ich „rasy, poglą-
obrazów według koloru włosów czy oczu, co można potem wykorzystać w ściganiu przestępstw (motyw 30). Temat biometrii przewija się także w kontekście zakazu systemów zdalnej identyfikacji biometrycznej w czasie rzeczywistym w przestrzeni publicznej do celów ścigania przestępstw. Ustawodawca unijny zauważa, że takie systemy mogły wywoływać „poczucie stałego nadzoru i pośrednio zniechęcać do korzystania z wolności zgromadzeń i innych praw podstawowych” (motyw 32). Aby nie było tak łatwo, unijny ustawodawca wskazuje wyjątki, umożliwiające wykorzystywanie takich systemów. Są nimi sytuacje, gdy wykorzystanie jest „absolutnie niezbędne” do któregoś z poniższych celów: 1) poszukiwania konkretnych ofiar uprowadzeń, handlu ludźmi, wykorzystywania seksualnego, poszukiwania zaginionych, 2) zapobiegania „konkretnemu, poważnemu i bezpośredniemu” zagrożeniu życia lub bezpieczeństwa fizycznego osób fizycznych albo rzeczywistemu zagrożeniu atakiem terrorystycznym,
3) lokalizowania lub identyfikowania osoby podejrzanej o popełnienie przestępstwa w celu prowadzenia postępowania przygotowawczego, ścigania lub wykonania kar w odniesieniu do takich przestępstw, jak np. terroryzm, handel ludźmi, wykorzystywanie seksualne dzieci, nielegalny obrót środkami odurzającymi lub bronią, zabójstwo, nielegalny obrót organami ludzkimi, zgwałcenie, sabotaż, rozbój przy użyciu broni.
rzeczywistym w przestrzeni publicznej, wymaga uprzedniego zezwolenia udzielonego przez sąd lub odpowiedni organ administracyjny. Tak jak w przypadku rejestracji w unijnej bazie, tak samo w przypadku wspomnianego zezwolenia w nadzwyczajnych przypadkach system może zostać wykorzystany bez zezwolenia, przy czym taki wniosek musi zostać następnie złożony w ciągu 24 godzin. Gdy odpowiedni sąd lub organ nie wyda takiego zezwolenia, wykorzy-
AI ACT wskazuje również, że jakiekolwiek wykorzystanie takich systemów AI do wyżej wymienionych celów musi przebiegać z zachowaniem niezbędnych i proporcjonalnych zabezpieczeń, a także zgodnie z prawem krajowym. Co istotne, aby taki system mógł być zastosowany, musi najpierw zostać zarejestrowany w unijnej bazie danych, chyba że mamy do czynienia z nadzwyczajną sytuacją – wówczas można zarejestrować taki system później, jednak bez zbędnej zwłoki. Warto również odnotować, że każde wykorzystanie systemu zdalnej identyfikacji biometrycznej w czasie
stywanie systemu musi zostać wstrzymane natychmiast, a wszystkie dane i wyniki muszą zostać usunięte.
O użyciu takiego systemu AI informuje się dodatkowo właściwy organ nadzoru rynku i krajowy organ ochrony danych, oczywiście bez podawania wrażliwych danych operacyjnych. Te organy natomiast mają corocznie raportować takie wykorzystania do Komisji Europejskiej, która następnie publikuje roczne sprawozdania na ten temat.
Ochrona osób fizycznych w przypadku wykorzystania systemu zdalnej identyfikacji biometrycznej w czasie rzeczywistym w przestrzeni publicz
Specjalizuje się w ochronie dóbr osobistych osób fizycznych i prawnych. Bliskie są jej zagadnienia ochrony wizerunku, renomy i dobrego imienia. Zaangażowana w postępowania z zakresu zwalczania nieuczciwej konkurencji. Zajmuje się także prawem własności intelektualnej, ze szczególnym uwzględnieniem prawa autorskiego, prawa reklamy i mediów. W zakresie jej zainteresowań znajduje się również prawo nowych technologii. Kontakt: m.kudla@skplaw.pl. Strony internetowe: www.skplaw.pl, www.skpipblog.pl.
nej ma jeszcze jeden aspekt. W przepisie wprost wskazano bowiem, że nie można podjąć decyzji wywołującej niepożądane skutki prawne dla danej osoby wyłącznie na podstawie wyników uzyskanych z takiego systemu.
Istotnie jednak państwa członkowskie mogą podjąć decyzję o wprowadzeniu możliwości pełnego lub częściowego zezwolenia na wykorzystywanie takich systemów w granicach i na warunkach określonych w AI ACT. W związku z tym, jak wyjaśnia motyw 37, państwa członkowskie mogą w ogóle nie przewidywać takiej możliwości lub przewidzieć ją jedynie w odniesieniu do niektórych celów mogących uzasadniać dozwolone wykorzystanie.
Na koniec rozważań dotyczących danych biometrycznych, warto wskazać, że zgodnie z AI ACT nie jest tak, że automatycznie wszystkie systemy zdalnej identyfikacji biometrycznej są zakazane. Zakazane są bowiem te dokonujące tego w czasie rzeczywistym w przestrzeni publicznej. Inne zostały bowiem skategoryzowane jako systemy AI wysokiego ryzyka, na które to został nałożony szereg obowiązków. Nie są one jednak niedozwolone. Podobnie systemem AI wysokiego ryzyka będą systemy AI przeznaczone do stosowania przy kategoryzacji biometrycznej, według wrażliwych lub chronionych cech lub na podstawie wnioskowania o nich, a także systemy AI przeznaczone do stosowania przy rozpoznawaniu emocji.
Kiedy wejdzie w życie zakaz?
Zgodnie z treścią AI ACT, przepisy rozporządzenia co do zasady będą stosowane od 2 sierpnia 2026 r. W przypadku zakazanych praktyk w zakresie AI, określonych w art. 5, jest jednak inaczej. Regulacja ta będzie obowiązywać już od 2 lutego 2025 r.
Marlena Kudła
1 https://eur-lex.europa.eu/legal-content/ PL/TXT/?uri=OJ%3AL_202401689.
2 Motyw 42 AI ACT.
Różne technologie:
malowanie, pokrywanie, dozowanie
montaż/demontaż
obsługa maszyn (załadunek/rozładunek)
technologie spawalnicze
spawanie
zgrzewanie
cięcie/ukosowanie
zadania transportowe
Różne branże
konstrukcje stalowe
materiały i urządzenia medyczne
podzespoły i części dla motoryzacji
produkcja urządzeń elektrycznych, w tym AGD
przemysł meblowy
przemysł spożywczy
rolnictwo/leśnictwo
tworzywa sztuczne i wyroby gumowe
Oferujemy kompleksową realizację instalacji zrobotyzowanych: Projekt Wdrożenie Szkolenie Serwis
Sieć Badawcza Łukasiewicz - Przemysłowy Instytut Automatyki i Pomiarów PIAP Centrum Automatyzacji i Robotyzacji
Al. Jerozolimskie 202, 22 874 02 04; 22 874 01 54 02-486 Warszawa mechatronika@piap.lukasiewicz.gov.pl www.piap.lukasiewicz.gov.pl
Adam Zalewski, Mariusz Deja, Krzysztof Jarosz, Adam Ruszaj, Wit Grzesik (red. nauk.) Wydawca: Wydawnictwo Naukowe PWN rok wydania: 2024, objętość: 410 stron, oprawa: miękka
Historia sterowania numerycznego zaczęła się w 1952 r. Prekursorem był znany w świecie Massachusetts Institute of Technology w Cambridge, USA. Okres intensywnego rozwoju nastąpił z chwilą pojawienia się ok. 1972 r, i w następnej dekadzie, możliwości zastosowania technologii sterowania komputerowego. W ciągu 70 lat sterowanie i programowanie przeszło od układów analogowych, po komputerowe, do obecnie rozwijanych układów inteligentnych. Książka zawiera informacje na temat wyposażenia narzędziowego i technicznego obrabiarek CNC, układów sterowania, integracji obróbki i pomiarów współrzędnościowych, wspomagania programowania technikami symulacji numerycznej procesu i sztucznej inteligencji, a także omówiono programowanie obrabiarek wieloosiowych i platform wytwórczych oraz zamieszczono opisy najnowszej wersji pakietu programowania MasterCAM 2024 i SOLID EDGE 2023.
Joseph Romm (tłum. Agnieszka Adamczyk-Karwowska) Wydawca: Wydawnictwo Naukowe PWN rok wydania: 2024, objętość: 336 stron, oprawa: miękka
W książce znajdziemy odpowiedzi na liczne pytania: czym jest efekt cieplarniany i jak wpływa na ogrzanie Ziemi; na ile klimatolodzy są pewni, że działalność człowieka jest przyczyną globalnego ocieplenia; czy w ostatnich latach globalne ocieplenie spowolniło; dlaczego w ocieplającym się świecie niektóre zimy nadal są surowe; jaki będzie wpływ wzrostu poziomu mórz; jakie są prognozowane skutki zmian klimatycznych dla zdrowia; dlaczego naukowcy i rządy uznali, że 2 °C to granica, po przekroczeniu której zmiany klimatyczne staną się „niebezpieczne” dla ludzkości; kim są negacjoniści klimatyczni; czy energia jądrowa odegra znaczącą rolę na rzecz zminimalizowania zmian klimatycznych; jak można zmniejszyć emisję CO2 w sektorze transportowym; jaką rolę mogą odegrać pojazdy elektryczne; jak zmiany klimatyczne wpłyną na nas w nadchodzących dziesięcioleciach? I wiele innych – warto przeczytać!
Szymon Ciach
Wydawca: Helion rok wydania: 2024, objętość: 408 stron, oprawa: miękka
Większość pracowników IT wie, że znajomość prawa dla obszaru, w którym działają, jest przydatna. Nieznajomość prawa szkodzi, a jego zrozumienie i umiejętność praktycznego stosowania są kluczowe dla funkcjonowania w branży. Książka stanowi kompendium wiedzy nie tylko dla prawników, ale także konsultantów IT, menedżerów do spraw bezpieczeństwa informacji, wreszcie wszystkich tych, którym zależy na zrozumieniu i stosowaniu prawa w obszarze technologii informatycznych. Lektura niezbędna dla osób chcących się efektywnie poruszać w cyfrowej rzeczywistości i skutecznie chronić swoje interesy w świecie Internetu i nowych mediów. Autor koncentruje się na wymiarze praktycznym zagadnień, co pozwala lepiej zrozumieć, jak działa prawo w odniesieniu do stanów faktycznych związanych z IT – pokazuje zestaw istotnych przepisów oraz wskazuje sposób myślenia, jaki można „zaimplementować”, by radzić sobie ze stosowaniem prawa w tym obszarze.
Opracowanie – dr inż. Małgorzata Kaliczyńska
Kompleksowe wsparcie dla firm w zakresie wykorzystania technologii addytywnych, prototypowania oraz nowoczesnego utrzymania ruchu
Badania
Twoje potrzeby to nasze wyzwania
PIAP design
Laboratorium Szybkiego Prototypowania i Obliczeń Numerycznych
Sieć Badawcza Łukasiewicz - Przemysłowy Instytut Automatyki i Pomiarów PIAP Al. Jerozolimskie 202, 02-486 Warszawa
Tel.: +48 603 713 997 I e-mail: design@piap.lukasiewicz.gov.pl I www.design.piap.pl
Doradzamy / Projektujemy / Wdrażamy / Szkolimy
Automatyzacja i robotyzacja w MŚP w programie Fundusze Europejskie dla Polski Wschodniej 2021-2027
W lipcu 2024 roku ogłoszono kolejny nabór wniosków w konkursie działania 1.2
Automatyzacja i robotyzacja w MŚP ( https://www.parp.gov.pl/component/grants/ grants/automatyzacja-i-robotyzacja-w-msp).
Konkurs obejmuje kompleksowe wsparcie MŚP z makroregionu Polski Wschodniej w zakresie automatyzacji i robotyzacji mające na celu zwiększenie innowacyjności procesów produkcji lub usług oraz produktywności.
Instytut Łukasiewicz – PIAP, mając wieloletnie doświadczenia w automatyzacji i robotyzacji procesów produkcyjnych, oferuje wsparcie w przygotowaniu firmy do udziału w tym konkursie. Wsparcie obejmuje przeprowadzenie diagnozy dojrzałości cyfrowej oraz opracowanie mapy drogowej transformacji w kierunku Przemysłu 4.0, na podstawie której zostanie wdrożona innowacja procesowa lub produktowa. Zakres naszych prac może obejmować wybrane zadania:
– Analiza procesu produkcyjnego firmy i wytypowanie obszarów podatnych na automatyzację i robotyzację.
– Opracowanie planu modernizacji firmy w kierunku cyfryzacji procesu w duchu koncepcji Przemysł 4.0 poprzez wprowadzanie automatyzacji i robotyzacji wybranych obszarów.
– Pomoc w przygotowaniu wniosku do złożenia w ramach naboru.
– Realizacja planowanych prac wdrożeniowych – w przypadku otrzymania dofinansowania.
Zainteresowanych zapraszamy do kontaktu
Sieć Badawcza Łukasiewicz - Przemysłowy Instytut Automatyki i Pomiarów PIAP Centrum Automatyzacji i Robotyzacji
Al. Jerozolimskie 202, 22 874 02 04; 22 874 01 54 02-486 Warszawa mechatronika@piap.lukasiewicz.gov.pl www.piap.lukasiewicz.gov.pl