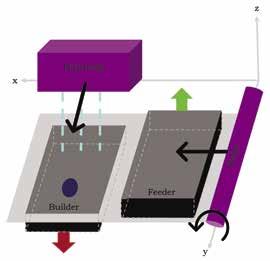
12 minute read
WC-Co
Effects of printing parameters on density and mechanical properties of binder jet printed WC-Co
Pierangeli Rodríguez De Vecchis a , Danielle Brunetta a , Katerina Kimes a , Drew Elhassid a and Markus Chmielus a a Department of Mechanical Engineering and Materials Science, University of Pittsburgh
Pierangeli Rodríguez De Vecchis
Dr. Markus Chmielus
Pierangeli Rodríguez De Vecchis is a Materials Science and Engineering senior. She works in Dr. Chmielus lab on Binder Jet 3D Printing (BJ3DP). She has been awarded the sophomore and junior PCEASASM and WAAIME scholarships. She is the vice-president of materials advantage 2019-2020.
Dr. Markus Chmielus is an Associate professor at the University of Pittsburgh (MEMS). His research is focused on binder jet printing of metal alloys and the study of magneto-caloric materials. He teaches Junior and Senior Materials Science classes and is the Advisor for the Material Advantage Chapter.
Significance Statement
Traditional manufacturing of WC-Co parts is slow and expensive, while Additive Manufacturing offers a commercially viable and fast solution. This project shows how choosing optimal printing parameters for binder jet printing (BJP) can produce parts with equally excellent mechanical properties, allowing to pair WC-Co (complex material) with BJP (innovative technology).
Category: Methods Keywords: Binder jet printing, tungsten carbide, printing parameter, design of experiments.
Abstract
Tungsten carbide-cobalt (WC-Co) is a cermet material widely known for its excellent combination of mechanical properties including high hardness provided by small WC grains, and high toughness provided by the Co-matrix binder metal. Its applications range from mining and drilling tools to cutting gears. Traditionally, WC-Co parts are formed through powder metallurgy processes. The WC and Co mixed powders are typically pressed with added wax that results in a low-density part, which is later put through a de-waxing and hot isostatic pressing (HIP) process. However, this process demands mass production resulting in a slow and expensive process. Additive Manufacturing, particularly binder jet-printing (BJP) appeared as an option to supplement traditional WC-Co manufacturing, allowing the production of fast, specific, and highly detailed parts. A design of experiments was set-up to find the optimal printing parameters to form parts with high green densities, translating to high hardness and fracture toughness. The highest green densities were obtained with a 220% binder saturation, 45 s drying time, 100 µm layer thickness, 5 mm/sec roller speed, and a build-to-feed ratio of 2. Sintered-HIPed parts resulted in 99% relative density, 1310 HV hardness and 14.74 MPam 0.5 fracture toughness.
1. Introduction
Tungsten carbide-cobalt (WC-Co), also known as cemented carbide is a cermet (ceramic-metal) material widely known for its excellent mechanical properties (including high density, hardness, toughness and flexural stress). It is used in wear resistant applications, including machining, cutting, and rolling, as well as mining and oil drilling tools [1]. Morphologically, the WC-Co microstructure is composed of hard/brittle, small, polygonal WC grains within a tough Co matrix. Co is known as the binder metal as it is chosen to melt at a lower temperature than WC to wet the grains and allow strong metallic bonds to form between WC particles during sintering, reducing brittleness without greatly decreasing hardness [2].
Traditionally, WC-Co parts are manufactured by powder metallurgy through which WC and Co particles are blended and ball-milled, after having previously carbonized W, typically with carbon monoxide (CO). Parts are formed through mechanical pressing or molding to obtain a green state. A small amount of paraffin is added to increase its density which is removed through a de-waxing process, followed by sintering and hot isostatic pressing (HIP), resulting in the final, fully dense cermet part [3]. This technology is slow and expensive, requiring the mass production of molds and limited in resolution. As a result, additive manufacturing (AM) appeared as an option to create WC-Co shapes fast and with specific design requirements.
The focus of this project is the AM technology of binder-jet printing (BJP). BJP has the potential to produce WC-Co objects by selectively stacking layers of powder and binder alternatively, according to a computer design, as shown in Figure 1. It is a fast, cost-effective process that allows the formation of complex internal and external geometries [4]. In contrast with other AM
methods, like Selective Laser Melting (SLM), this process does not introduce internal thermal stresses and does not need support pieces for complex hanging shapes. Nevertheless, BJP requires post-processing of curing and sintering to obtain a fully dense part without binder content. Only a few publications have BJPed WC-Co, like [5], who mainly addressed the wear resistance of the parts, but did not show a systematic approach to printing or tested other mechanical properties.
Figure 1: Binder jet printing process. (a) Roller spreads powder in x-direction, (b) Printhead deposits binder on design silhouette along y-direction, the binder is partially cured, (c) Feeder moves one layer down and builder one layer up to provide powder in z-direction. Repeat.
The objective of this project was to find the optimal set of printing parameters and characterize the microstructure of WC-Co parts resulting in similar properties to those obtained conventionally. This was achieved through two series of design of experiments (DoE). Firstly, the powder packing density was studied by comparing the effects of rolling speed, feed-to-build ratio and layer thickness, and secondly, the green density of the parts was studied when changing the binder saturation and drying time. Best parameters were chosen by judging the green density and quality of the part (integrity, edge and shape retention), and confirmed through post-sintering properties. Furthermore, the printed parts were prepared through metallography and their density (through Archimedes method), hardness and fracture toughness were compared. From previous experience, it was expected that low roller speed and intermediate feed-to-build ratio, paired with layer thickness of at least twice the size of the agglomerates would yield higher powder packing density, and that high levels of saturation and drying time will be needed to bind the porous powder.
2. Methods
Spray-dried, half-sintered WC-Co powder (12.5% Co) from General Carbide was characterized through scanning electron microscopy (SEM) and stereological analysis (line intercept method [6]). Cubes of 1x1x1 cm3 were BJP with an ExOne Lab varying settings in two DoE studies. The first DoE study involved comparing roller speed (5 or 15 mm/s), layer thickness (50 or 100 µm), and build-to-feed ratio (1.5 or 2) to obtain the highest powder-bed packing density without binder. Packing densities of the resulting eight “prints” were calculated as mass (OHAUS AX324) per volume. The combination yielding highest packing density was chosen: 100 µm layer thickness, 5 mm/s roller speed and a 2:1 build-to-feed ratio. The second DoE stage used the previous results as constants and consisted in varying binder saturation (100%, 160% or 220%) and drying time (30 s, 45 s or 60 s). These iterations resulted in nine prints of 12 cubes each that were cured at 200°C for 8 h. Green density was measured as before, as mass over volume.
Green parts were sintered by General Carbide at 1440°C. One sample per print was sectioned, mounted, ground, polished (Struers LaboPol 5), etched with Murakami reagent, and imaged (Zeiss Smartzoom5 optical microscope). Relative density was calculated with ImageJ ® software [7]. To measure hardness and fracture toughness, three indents were imprinted (Rockwell 724 Wilson) on each sintered sample, with a Vickers diamond tip and major load (P) of 60 kgf. Vickers hardness (H) was calculated by measuring the indent’s diagonals (Keyence VH-Z500 digital microscope). Toughness was calculated by plugging the measured edge cracks (L) in Shetty’s formula (Equation 1) for brittle materials exhibiting Palmqvist cracking [8].
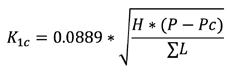
(1)
3. Results 3.1 Powder characterization
SEM images of the powder were taken to characterize its morphology. As shown in Figure 2, powders are collections of fine polygonal particles forming nearly spherical agglomerates, typical of WC-Co powders. Stereological analysis showed individual particles with an average diameter of 0.52 µm, forming agglomerates of about 21.3 µm.
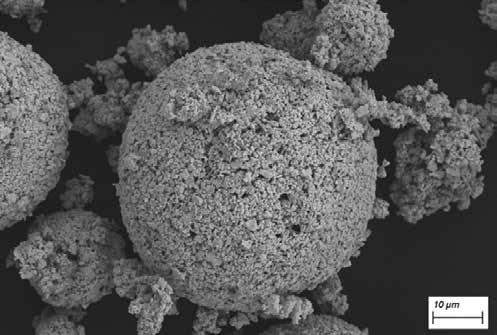
Figure 2: SEM of WC-Co powder. The submicron-sized particles form nearly spherical agglomerates.
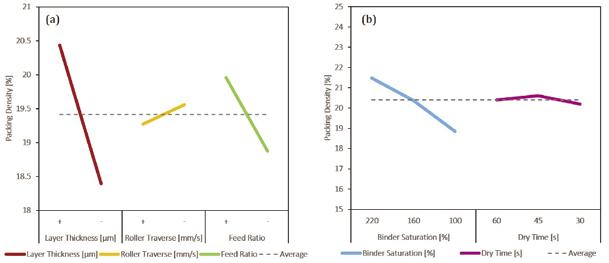
Figure 3: Design of experiments main variables’ effect on green density. (a) Powder packing DoE, (b) Printing parameters DoE.
3.2 Design of Experiments
The first DoE (Figure 3a) showed the effect of layer thickness, rolling speed and feed ratio on packing density. Green density increased with layer thickness and feed ratio but decreased with roller speed. Judging by the slopes of the lines, the most influential parameter was layer thickness. The parameters 100 µm layer thickness, 5 mm/s roller speed and feed ratio of 2 were chosen. For the second DoE (Figure 3b), it is observed that green density of the parts increased with binder saturation and with respect to drying time, it was a maximum at the midpoint. Again, judging by the slope of the lines, it seems that binder saturation has a greater effect than drying time on the density of the parts. From this experiment, nine resulting sets of prints, were obtained and evaluated to understand their properties beyond green density, although it is expected that the higher the green density the better the final density and properties. 3.3 Microstructure and Mechanical Properties
Prints #4, #5 and #8 did not survive handling and transportation due to their fragility (very low binder saturation). From the remaining samples, all microstructures, after sintering at 1400° C and HIPing, were similar to that shown in Figure 4 (lighter WC grains in dark Co matrix) with an average WC grain size of ~1.72 µm. Prints #2 and #7 showed some porosity, especially near the corners, and samples #1, #3 and #6 showed some free C.
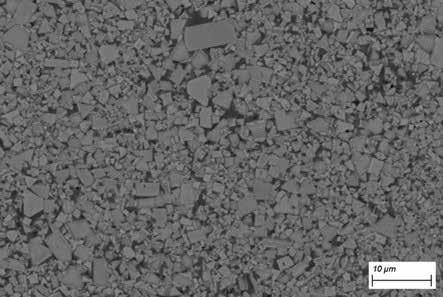
Figure 4: Sintered WC-Co microstructure showing WC grains in Co matrix (etched).
Both relative green and sintered densities are shown in Table 1. Sintered densities were approximately the same. Hardness and fracture toughness (Table 1) were calculated in order to compare their mechanical properties. Although some are very close, the samples with the best mechanical properties are those of print #1 (1310 HV and 14.74 MPam 0.5 ).
Print # Binder saturation [%] Drying time [s] Green Density [%] Sintered Density [%] Hardness [HV] Fracture Toughness [MPam0.5] 1 220 45 21.9 98.5 1310 14.74 2 160 45 21.6 99.7 1298 11.90 3 220 60 21.0 98.7 1294 10.36 4 100 60 NA NA NA NA 5 100 30 19.4 NA NA NA 6 220 30 21.6 98.8 1284 10.76 7 160 60 19.8 99.5 1266 8.26 8 100 45 18.4 NA NA NA 9 160 30 19.7 99.9 1277 11.27 Table 1: Settings, densities and mechanical properties of printed parts (color coded from best/green to worst/red).
4. Discussion
Spray-dried WC-Co powder was originally chosen due to its uniform size distribution and flowability required in BJP. However, WC-Co is an intrinsically complex powder as agglomerates are porous, requiring binder saturation levels above 100%, which in turn is the driving force for the DoE. The first DoE step showed that the higher layer thickness was required as it cannot be smaller than the agglomerate size, and it is optimized when it is about three times bigger as layers can be composed of more than one agglomerate. The slower roller speed and higher feed ratio prevent the powder being pushed instead of spreading uniformly. The second DoE step showed that binder saturation is the variable with greater effect on the print’s density. The highest value (220%) was selected. This does not imply that the more binder the better density. ExOne solvent binder is C-based, and it is well known that excess C worsens WC-Co properties, by promoting WC grain growth and free carbon (graphite) precipitation. Drying time is also a relevant variable. Short times result in part bulging and long times in delamination as each layer is over-dried and does not bind to the next. Intermediate drying (45 s) was found to be optimal. High densities were achieved for almost all samples. The pores present in some samples, were small and aligned, suggesting delamination (layers of the green part may separate during handling and transportation due to low green density). Microstructurally, the samples are characterized as having a medium sized (1.4-3.4 µm) WC grain structure [9]. The presence of free C, might be due to retained binder or most likely because there is stoichiometrically more C than W in the prepared powder [9]. In terms of mechanical properties, both Vickers hardness and Palmqvist fracture toughness were comparable to those reported by General Carbide through traditional manufacturing (1245 1633 HV, 13-14 MPam 0.5 [3]). It is important to note that calculated fracture toughness is a macroscopic approximation requiring deeper study. The load at which cracks start to appear (Pc) was approximated to 80 kgf, since there were at 100 kgf, but not at 60 kgf. Nano-indentation would give better values ([10]).
5. Conclusion
It was found that BJPed WC-Co parts can be produced with nearly full density and mechanical properties similar to traditional parts. The two-step DoE allowed to formulate an optimal set of printing parameters (Print #1): 220% binder saturation, 45 s drying time, 100 um layer thickness, 5 mm/sec roller speed, and a build-to-feed ratio of 2. Through these settings a sintered density of 98.5%, hardness of 1310 HV and fracture toughness of 14.74 MPam 0.5 were obtained. Microstructurally, a medium-grained structure was generated with some free C (not too harmful). These results prove BJP can be used to a wider variety of metallic powders and even expand into cermets that were differently treated. For both WC-Co manufacturing and BJP expansion, the combination of a traditional powder with a new technology shows the possibilities of combining them to reduce cost and time, while emphasizing detail and shape particularity. In the future, differently shaped WC-Co powders, as well as green part preservation will be studied.
6. Acknowledgements
Thanks to the Swanson School of Engineering and the Office of the Provost, as well as PMFI, General Carbide and all Chmielus Lab group, especially Katerina Kimes.
7. References
[1] N. Alves Nery Balbino, E. Otoni Correa, L. Carvalho Valeriano, Development of the 90WC-8Ni-2Cr3C2 cemented carbide for engineering applications, Int. J. Adv. Manuf. Tech. (2018).
[2] L. Fu, Two-step synthesis of nanostructured WC-Co powders, Scr. Mater. 44 (2001).
[3] General Carbide, The Designer’s Guide to Tungsten Carbide, (2008).
[4] A. Mostafaei, E.L. Stevens, J.J. Ference, D.E. Schmidt, M. Chmielus, Binder jetting of a complex-shaped metal partial denture framework, Addit. Manuf. 21 (2018).
[5] R.K. Enneti, K.C. Prough, Wear properties of sintered WC-12%Co processed via Binder Jet 3D Printing (BJ3DP), Int. J. Refract. Met. Hard Mater. 78 (2019) 228–232.
[6] C. Russ, John, T. Dehoff, Robert, Practical Stereology, 2nd ed., Plenum Press, 2000. doi:10.1088/1751-8113/44/8/085201. [7] C.T. Rueden, J. Schindelin, M.C. Hiner, B.E. DeZonia, A.E. Walter, E.T. Arena, K.W. Eliceiri, ImageJ2: ImageJ for the next generation of scientific image data, (2017) 1–26.
[8] R. Spiegler, S. Schmauder, L.S. Sigl, Fracture Toughness Evaluation of WC-Co Alloys by Indentation Testing, J. Hard Mater. 1 (1990).
[9] J. García, V.C. Ciprés, A. Blomqvist, B. Kaplan, International Journal of Refractory Metals Cemented carbide microstructures : a review, Int. J. Refract. Met. Hard Mater. 80 (2019)
[10] T.A. Fabijanic, et al, Vickers Indentation Fracture Toughness of Near-Nano and Nanostructured WC-Co Cemented Carbides, Metals (Basel). 7 (2017).