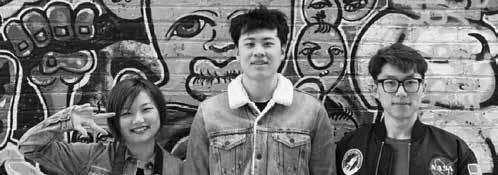
17 minute read
Feasibility study of kinetic, thermoelectric, and RF enery harvesting powered sensor system
Feasibility study of kinetic, thermoelectric and RF energy harvesting powered sensor system
Keting Zhao a , Jiangyin Huang a , Hongye Xu a and mentor Dr. Jingtong Hu a a Department of Electrical and Computer Engineering, University of Pittsburgh, Pittsburgh, PA
Team: Keting Zhao, Hongye Xu, Jiangyin Huang (left to right)
Keting Zhao is an electrical engineering student concentrating in communication and signal processing with a minor in computer science. She is interested in pursuing further training in signal processing and robotics controls. Hongye Xu is a computer engineering student concentrating in digital system and computational modeling. He is interested in studying further about neural network and machine learning. Jiangyin Huang is an electrical engineering student concentrating in communication and signal processing. He wants to learn deeper into computer vision and signal analyzing during his graduate level education.
Dr. Jingtong Hu
Dr. Jingtong Hu is currently an Assistant Professor in the Department of Electrical and Computer Engineering. His main research interests include embedded systems, FPGA, and cyber-physical systems. He is a recipient of Employer Diversity Recognition Award from Pitt Career Center.
Significance Statement
Using the combination of kinetic, thermoelectric and RF energy harvesting to power a communication system has not yet been tested. This feasibility study of this system will further indicate the feasibility of implementing the energy harvesting communication system into devices or equipment which involve in human daily activities for long-term usage.
Category: Device Design Keywords: Energy Harvesting, Software Duty Cycle, Power ORing Achitecture Abbreviation: microcontroller unit (MCU), radio frequency energy harvester (RFEH), kinetic energy harvester (KEH), thermoelectric energy harvester (THE), piezoelectric energy harvester (PEEH), electromagnetic energy harvester(EMEH), low power mode (LPM)
Abstract
Batteryless and wireless energy harvesting systems are critical to internet of things (IoT) vision as well as the sustainability of long-lived, untethered systems. The systems can be implemented into wearable devices, which are used for monitoring vital body signals. They can also help the process of making insectwearable devices that monitor changes in the environment. In general, this kind of system can be divided into three levels: energy harvesting subsystems (EH), an embedded microcontroller unit (MCU), and peripherals (sensors, radios, etc.) [1]. This research will provide a feasibility study of integrating all the levels mentioned above. This paper will focus on the radio frequency energy harvester (RFEH), kinetic energy harvester (KEH) and thermoelectric energy harvester (THE) as well as an instruction on designing the rest of the system to be compatible with all three EHs and able to handle frequent power shortages during the process. The reason for choosing KEH, TEH and RFEH as power sources is because these energy are closely related to the human activities. Thus, this feasibility study could contribute towards further studies on energy harvesting communication system within wearable devices. The main result of this study indicates a positive and promising future of integrating multiple energy harvesters into a wearable communication system.
1. Introduction
The IoT serves to relate mechanical and digital machines through a large interconnected system, which, in some cases, must collect data on even the minutest details. This is costly in both the number of devices required and the power to run them. It stands to reason that in order to progress the field something must be introduced to combat this limiting factor. To that end, the feasibility of designing these devices to harvest ambient energy instead of being supplied from a separate device comes to mind. There are a number of methods to perform this such as TEH, KEH and RFEH, but the uncertainty comes from whether it is feasible to rely on such methods. It would only be unfeasible if these combined systems cannot generate enough power. Radio frequency energy harvesting is a technique that harvests energy from the electromagnetic field in the air and converts it into the electrical domain, voltage and current. TEH generates voltage when differing temperatures are placed side by side. For the energy harvester, this study will follow the insight that is provided by Leonov’s research on TEH of human body heat [2] and Gorlatova’s research on KEH of human activities [3] as well as Lu’s survey research paper on RFEH [4]. For integrating the sensor, we will take reference from the research Mementos: System Support for LongRunning Computation on RFID-Scale Devices [5]. This study will show whether energy harvesting methods can sustain the needs of IoT devices.
2. Methods 2.1 Equipment Setup
2.1.1 PowerCast RFEH A RFEH is made of three parts, an antenna, a rectifying circuit and a matching circuit to give a DC output [4]. The RF energy harvester module used in this research is the model TX91501 PowerCast transmitter, which can broadcast unlicensed 915MHz ISM band radio wave and can produce 3 watts of EIRP and data up to 40-50 feet by using a matched receiver. The module P1110B receiver can rectify a 915MHz center frequency at a maximum of 23 dBm input power giving 4.3V/100mA as its maximum output. The beam pattern of TX91501 transmitter is 60 by 60 feet. Therefore, a patch directional antenna with 122 horizontal and 68 vertical energy pattern and 6.1 dBi gain is used to capture power from the transmitter. In order to boost the power, the DC-DC booster module BQ25570 is connected to the RFEH. 2.1.2 EMEH and PEEH For PEEH, device PPA-1011 is used in this research. However, there is no developed EMEH for commercial use. Therefore, the EMEH used in this project is built based on Kwon’s research [6]. This EMEH is mainly structured as repulsively stacked multilayer magnets with washer in between each one and placed in the middle of an independent coils which stands on compression springs for the purpose of oscillation as shown in Figure 1. With this setup, the magnetic flux density alternates multiple times depends on the number of stacked magnets during oscillation. This design can give a relative higher oscillating frequency of magnetic flux which can help produce AC power more efficiently [6]. To use these in conjunction, AC/DC converters are needed in the system since they output different forms of electricity. After the initial testing, a zener diode regulator is therefore implemented. Two zener diodes are connected back to back and with voltage output limited by Vz. 2.1.3 TEH with Different Scales There are multiple available TEHs in the market with similar designs, only different in sizes. The efficiency of all products are highly correlated to their sizes. Based on the data sheet, the power generated by TEH is stable but relatively small compared to the other two kind of EHs. Thus, power management module LTC-3108, which is designed for boosting ultra-low voltage input to 3.3V is used with TEHs. The output of the TEH is connected to LTC-3108, and four 1 F capacitors are connected in parallel to the output of LTC-3108 as storage. 2.2 Multi-inputs EHs Design
Figure 2 shows a Power ORing architecture, which is a modular design that allows multiple EH sources to be connected in parallel through diodes [7]. A supercapacitor is used to smooth the raw output voltage from EHs. The modified final system schematics are based on this architecture with the testing result as seen in Figure 3. Each EH module is connected to the switch so that the user can choose which sources or sources to use. The diode connected to the RFEH has a cut off voltage at 0.7V. The MCU used for this research is a model MSP430G2553. A magnetometer sensor, a radio communication module, and a UART to USB converter, are connected to the MCU. The idea is to put MCU in stasis when the EHs are charging the supercapacitor. Once the supercapacitor is charged up to the operation voltage, 3.3V, the MCU will switch to its active mode, reading and transmitting data repeatedly until the supply power is below threshold. It will then revert to sleep mode until the next time the supercapacitor is fully charged. A software duty cycle is implemented to realize this idea.
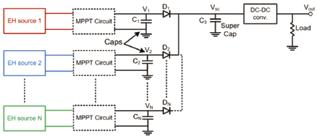
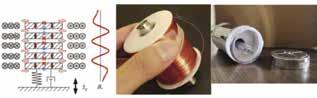
Figure 1: EMEH cut section indication and self-made EMEH final product Figure 2: Power ORing architecture
Figure 3: Schematic of the System Design

2.3 Software Duty Cycle Control
An interruptible computation is integrated to complete the duty cycle control. The source code of the interrupt is from course CSE466 at University of Washington [8]. In the MSP430 architecture, there are several types of interrupts: timer, port and ADC interrupts. In this case, the timer and port interrupts are configured and used. MSP430G2553 has four different low power modes (LPM), and LPM0 is used. During LPM0, the CPU and the MCLK are disabled, while the ACLK and SMCLK remain active. Additionally, MSP430 uses a watchdog timer to reset itself after a certain amount of time in order to avoid a counting overflow. In order to avoid an unexpected reset during an interrupt, once the CPU receives a digital 0 from pin P1.4, the watchdog timer will be put on hold from counting and an interrupt will set on pending. Then pin P1.4 selects the high-to-low edge and clears the interrupt pending flag as the interrupt begins. ISR saves the state and redirects the stack pointer to interrupt functionality.
After an interrupt happens, the interrupt service routine continues sensing the input from pin P1.4 and compares it against digital 1. When the input voltage is under its minimum operation voltage requirement, the input from P1.4 will indicate as digital 0, and vice versa. Now if input indicates the digital 0, the system remains in stasis; however, if input indicates a digital 1, the MCU exits LPM0 and resumes the main program’s next state. The clock will begin running from where it had been halted, and the MCU will execute the instructions from main program code again, reading data from sensors repeatedly, until the next interrupt is triggered. Additionally, a voltage divider is implanted so that when the input source voltage reaches 3.3V, the voltage across pin P1.4 will be 2.4V. In order to minimize the loss on input current, resistors with large resistance value are used to build the voltage divider. The resistors with value of 0.9kΩ and 2.4 kΩ are connected into the circuit as shown in Figure 4.
3. Results 3.1 RFEH Modify with DC-DC Booster
The testing result of output voltage and current with different distances between the RF transmitter and RF receiver is shown in Figure 4. The result shows that the maximum output power of RF energy harvester is 1.037mW and rapidly decreases as the distance from the source increases. When the distance between the transmitter and the receiver is greater than 150 cm, the output power is stable at average of 0.04mW. The minimum requirement for MCU to execute the program is 3.3V and 190µA, which the testing result clearly does not meet.
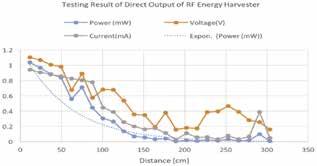
Figure 4: Raw outputs of RFEH vs Distance
After interageting the DC-DC booster with the RFEH, the retesting result shows that the output voltage from the receiving end is stable at 4.1V upon 487cm from the source. The relationship between output current and distance is shown in Figure 6. As distance increases to 7 feet from the source, the current drops down to 0.159 mA, which is lower than the threshold of powering up the rest of the system. Therefore, the RFEH now powers up the system around 200cm away. As shown in Figure 5, the modified
RFEH is connected to the diode of cutoff voltage 0.7V. Thus, the maximum voltage across the supercapacitor when using RFEH alone will be 3.5V, which is in its safe range.
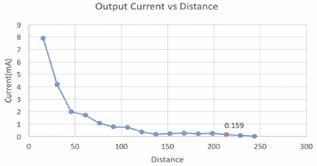
Figure 5: RFEH Output Current vs Distance with Booster
3.2 PEEH Modify with Zener Diode Regulator and EMEH Modify with Diodes
The average raw output power from PPA-1011 is RMS voltage at 14V and AC current at 100A. However, PPA-1011 does overshoot unexpectedly and has peak voltage as high as 40V. Based on datasheet of LTC3588, the maximum input of this device is 18V. Thus, the raw voltage of PPA-1011 can damage the power management device. Zener diodes with Vz at 17V are then used to build the regulator and connected to PEEH, so that the input voltage of LTC3588 will not overshoot. As a result, the output average RMS voltage of PEEH is 8.25V which is in a safe range. AC current is negligible and maintains at 100µA.
When the vibration frequency is in the range of 1.5Hz to 3.1Hz, the EMEH can produce output RMS voltage from 3 to 7 V and AC current from 5 to 7mA. After the raw EMEH power goes through the bridge rectifier with the capacitor, the average DC output voltage is 5.5V and the average DC current is 2.05mA. The operating voltage range of the MCU is from 1.8V to 3.6V. Thus, the output voltage of EMEH needs to be regulate before connects to the MCU.
In order to reduce the output voltage of EMEH, three diodes which have cut off voltages at 0.7V are connected in series between EMEH and the super capacitor. EMEH produce the DC voltage at average of 3.4V and no significant changes on output current after connecting diodes into the design. 3.3 Three TEHs Testing Result Comparison
Three different TEHs are all placed on arms, metals under sun, in room and in wind in order to test and compare the efficiency of harvesting. According to the result in Table 1, it can conclude that the efficiency of a TEH is higher when either the fluid speed around it is faster or the temperature difference between two sides is larger. Module EHA-PA1A is integrated into the system since it generates considerable power with only the coin size. Module EHA-PA1A can stably generate 25mV with 3.5mA when placed on arms according to the experiment. To simulate the charging process, 25mV with 3mA is connected to the input of the LTC3108. After 2 hours charging, the voltage at the input of the MCU stabilizes at 2.4V and the input of the GPIOs stabilizes at 3.3V. DS18B20, 4.5mW thermal sensor, is connected to MCU, used as a test peripheral. With stable 25mV input, the sensor works for half an hour. 3.4 Voltage Divider Implement
The datasheet indicates that the operation voltage range of MSP430 is from 1.8V to 3.6V. However, after a few tests, it shows that if the input voltage is lower than 2.3V, the input from pin P1.4 will indicate as digital 0, vice versa. This is higher than the expected minimum voltage, 1.8V. After the voltage divider has been introduced, the system can functional properly when RFEH keeps generating power. Other two kind of EHs could support the system after RFEH initializes the system properly. Once EHs stops supplying power, the supercapacitor starts discharging and the MCU could still be active as long as 45 seconds before switching to LPM. The MCU could stay in LPM for another 90 seconds before completely shutting down. If RFEH or other EHs start generating power again in this time period, MCU will be able switch back to active mode without being reset. The final design demonstration is shown in Figure 6.
Figure 6: Multi-inputs EHs powered sensor system demonstration

Metal under sun (stable) Human body room temp (first touch) Human body room temp (stable) 85ºC metal with room temp Voltage under wind comparing to no wind Size (mm) EHA-PA1AN1 120mV/11mA CP2,127,06 180mV/45mA OT20-66-F0-1211-11-W2.25 35mV/2mA
85mV/8.8mA 125mV/38mA 25mV/100uA
25mV/3.2mA 25mV/5.1mA 3mV/70uA
330mV
130% ↑ 400mV
120%↑ 80mV
Not significant
4. Discussion
The result shows a success to power the MCU with sensor module by RFEH indecently. TEH and KEH, however, needs the support from RFEH to power the rest of system initially. There are still few issues still remain with this design.
RFEH is easily affected by kinetic motions along the energy collection path. When people pass by, the voltage will rise for a short amount of time. It is also easily affected by cellphones and other devices that generate radio waves. Adding the dc-dc booster, these issues can be eliminated when the distance from receiver to transmitter is at most 200cm, but exist otherwise.
TEH takes approximately 2 hours to charge up four 1 F capacitors to 3.3V when the system is placed on human body. Even with smaller and fewer capacitors, due to the low input voltage, it still takes a long time to charge. The solution taken in this experiment is to charge the capacitors to 3.3V first and use the TEH to stabilize the voltage. Since the voltage generated would change the temperature difference, the hot side of the TEH (the side on skin) gets colder as time goes on. Thus the TEH is very inefficient, considering the amount energy it absorbs.
The current design of EMEH is relatively big for wearable device. Due to the limitation of available material and handcraft technique, only two third of the wire around the coil is used while the rest of the wire is disconnected, but adds extra weight to the EMEH. The frequency of vibrating and number of turns of wire do have effect on the amount of power KEHs can generate. A shaker and coils with different number of turns are used to perform further analyzing in later testing which will help optimizing the volume of EMEH.
The software duty cycle control only functions when the MCU is not completely shut down, which means the power shortage cannot be longer than 8.3 minutes. In this research, four EHs are in use, so power shortage is controlled under this threshold. In some case, this can be challenge and the possible way to solve this issue is to implement a duty cycle with logic ICs in the hardware design. In addition, the digital read for MCU I/O pin shows an inconsistent when super-capacitor is charging and when it is discharging. This makes the determination of when MCU is supposed to enter Low Power Mode vague and unstable. The power loss of the voltage divider is also not necessary. In order to eliminate this problem, a software ADC interrupt or a hardware duty cycle are going to be added into the system.
5. Conclusion
The result shows it is feasible to integrate all three levels of the system together with commercial products on a relatively large scale. TEHs and KEHs needs further research and adjusting on method of support sufficient power independently. RFEH will need customized the antenna and matching circuit in order to capture the energy from Wi-Fi rather than the special radio frequency generator. A hardware duty cycle should be tested as well as making PCB based on this design to scale down the system. The radio module is still in design and has not yet been calibrated. Once it is connected into the system, the power consumption will increase. A super-capacitor with a larger capacitance might be needed in the modified the design.
6. Acknowledgement
Funding for this project was provided by the Swanson School of Engineering and the Office of the Provost. Special thanks to Dr. Hu and his PhD student, Yawen Wu, for providing the source of devices and the help we needed on this project.
7. Reference
[1] J. Hester and J. Sorber, “Flicker,” Proceedings of the 15th ACM Conference on Embedded Network Sensor Systems - SenSys 17, 2017.
[2] 1. V. Leonov, “Thermoelectric Energy Harvesting of Human Body Heat for Wearable Sensors,” in IEEE Sensors Journal, vol. 13, no. 6, pp. 2284-2291, June 2013. doi: 10.1109/ JSEN.2013.2252526
[3] 2. M. Gorlatova, J. Sarik, G. Grebla, M. Cong, I. Kymissis and G. Zussman, “Movers and Shakers: Kinetic Energy Harvesting for the Internet of Things,” in IEEE Journal on Selected Areas in Communications, vol. 33, no. 8, pp. 1624-1639, Aug. 2015. doi: 10.1109/JSAC.2015.2391690 [4] Lu X., Wireless Networks with RF Energy Harvesting: A Contemporary Survey, vol. 17,2015 [5] B. Ransford, J. Sorber, and K. Fu, “Mementos,” Proceedings of the sixteenth international conference on Architectural support for programming languages and operating systems - ASPLOS 11, 2011. [6] Soon-Duck K., “Electromagnetic energy harvester with repulsively stacked multilayer magnets for low frequency vibrations”, March 2013.
[7] Estrada-López JJ, Multiple Input Energy Harvesting Systems for Autonomous IoT End-Nodes. 2018 [8] Hemingway B. (2015, Fall), Lecture 4: MSP430 Interrupt.