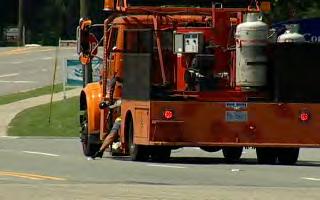
2 minute read
Figure 5: Marker placement with (a) manual method and (b) automated system [19
captured by UAS can be used to calculate earthwork and stockpile volumes. Several studies have been conducted in this area in the US and abroad. Most studies report minimal error in comparison with more traditional methods like GPS and Light Detecting and Ranging (LiDAR) without UAS. The success of the measurements depends on the post processing of the images to build the 3D models [17, 18].
2.2.2 Pavement Marking 2.2.2.1 Automated Marker Placement
Traditional marker placement methods require a worker to manually install the marker on the pavement (Figure 5). This exposes the worker to traffic and high-temperature adhesives. Automated marker placement systems install the marker without exposing the worker who remains inside the vehicle controlling the device (Figure 5b). In initial tests, comparative results showed that the automated system matched productivity and quality of high-end marker teams [19].
(a)
(b) Figure 5: Marker placement with (a) manual method and (b) automated system [19]

2.2.3 Inspection 2.2.3.1 Remote-Controlled Ground Penetrating Radar (GPR) for Asphalt Density
Uniform and adequate asphalt compaction is critical for pavement performance. Minimal reductions in asphalt density can cause huge impacts on pavement service life. Conventional quality control for asphalt density involves in-situ random determination of density from cores or 11
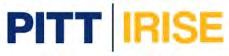
nuclear density gauges. Both methods are costly, labour intensive, and not necessary representative of the overall compaction quality. To overcome these issues, research has been focused on non-destructive methods that can evaluate asphalt density in a larger portion of the pavement like the Density Profiling System (DPS) with successful results.
Currently, the Minnesota Department of Transportation (MnDOT) is leading a pooled program to advance the use of DPS for Quality Assurance activities for asphalt pavements. The team has also developed a prototype of a DPS that can be remote-controlled from a safer distance. In this way the inspector would no longer need to be on the pavement in close contact with traffic and other equipment.
2.2.3.2 Integrated GPR and Infrared (IR) Imaging in Non-destructive Testing (NDT) Vehicle
NDT vehicles that can collect data at highway speeds have been used for some time now in the paving industry. Besides the benefit of limiting traffic interruption and continuous data collection, these vehicles also protect inspectors since they are not required to exit the vehicle to collect data on-foot. As an upgrade to these systems, The Advanced Highway Maintenance and Construction Technology (AHMCT) Research Center from the University of California, Davis proposed an integrated NDT vehicle with a typical 3D GPR system along with infrared cameras for thermal imaging [20].
2.2.3.3 E-Construction Inspection
Many activities performed during work inspection for the paving industry still uses a paper-based process. The advances in mobile technology can facilitate and expedite inspection records prompting fast sharing of information between inspectors and workers. Recently, the Louisiana Department of Transportation and Development sponsored a project using a econstruction inspection system called HeadLight [21]. Results indicate a 28% increase in productivity for inspectors when developing daily work reports among other benefits. While adopting e-construction inspection does not directly improve inspector safety, the fact that inspectors can effectively resume work in less hours, avoiding losing data and therefore having
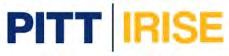
12