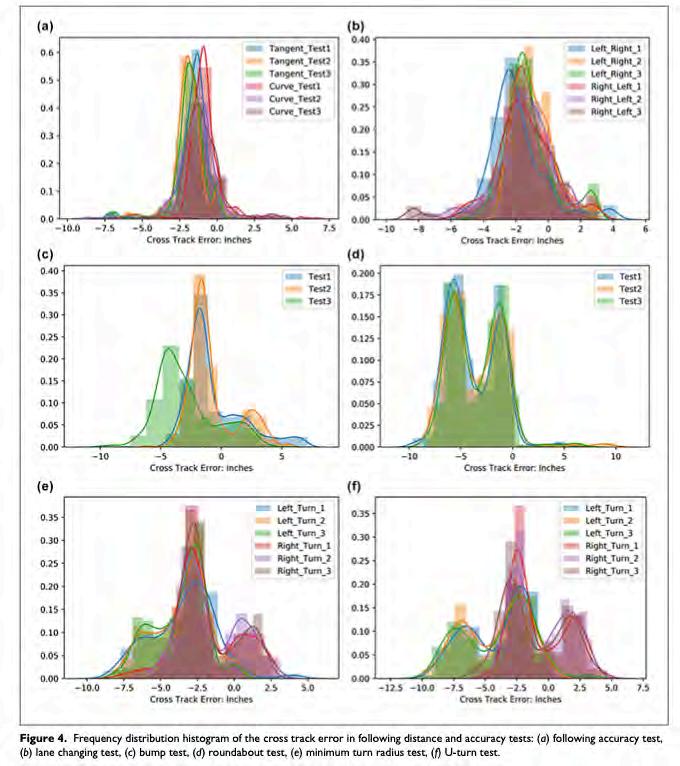
12 minute read
accuracy tests: (a) following accuracy, (b)lane changing, (c) roundabout operation, (e) minimum turn radius, (f) U-turn [86
Figure 39: Frequency distributions histograms of the cross-track error in following distance and accuracy tests: (a) following accuracy, (b)lane changing, (c) roundabout operation, (e) minimum turn radius, (f) U-turn [86]
A 2020 study evaluated the performance of the LT and FT in different scenarios regarding car-following distance, critical lane-changing gap distance, and intersection clearance time. For car-following distance results indicated a minimum of 75 ft for a LT and 30 ft for a FT. In terms of a lane-changing gap distance, the system needs a minimum time headway of 20 seconds for a 100 ft distance between LT and Ft to perform a safe lane change. If the distance is
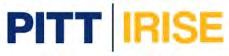
62
doubled (200 ft) the headway time increases to 26 seconds. Concerning the intersection clearance time, for a gap distance of 100 ft or 200ft, the system requires 15 or 25 seconds, respectively, to cross an intersection (or to make a right turn). These numbers are significantly higher than for common passenger vehicles, according to the authors, indicating the need for extensive training of the AIPV operators and FT drivers [100].
3.3.1.2 Past and Present Experience
In this section experience from other DOTs and research institutions are presented. The majority of this information was previously compiled for the pool study [95].
California
The University of California, Davies have tested the AIPV in 2020 with 40 hours of operation time mostly on flat roadways. Although the testing was promising, the AIPV failed when tested under an overpass [96]. The AIPV was considered optimal for operations like sweeping, lane striping, and other moving mainline highway maintenance activities. The Advanced Highway Maintenance & Construction Technology Research Center (AHMCT) at UC Davies was contracted by Caltrans to evaluate AIPV. The report of this project should be available soon. Caltrans is also developing a training program for potential AIPV operators [95].
Colorado
Colorado’s Department of Transportation (CDOT) reported approximately 110 highway test miles of striping operations with AIPV, through June 2019. CDOT is now testing the second generation Kratos system with a new paint truck. The second-generation system includes upgrades in cybersecurity, side view sensors, improved cameras, improved user interface, vehicle to vehicle communication, data storage, external human-machine interface (E- HMI), Astop, backup navigation, and operation in GPS denied mode.
North Dakota
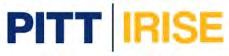
63
The North Dakota Department of Transportation (NDDOT) tested AIPV in the second semester of 2020. Testing was conducted on relatively flat low volumes road. Researchers reported successful operation regarding gap control, but some GPS connection issues that led to the loss of connectivity between the leader and the follower vehicle. However, these issues were solved during the testing [96].
Minnesota
Kratos is also the system supplier for the Minnesota’s Department of Transportation (MnDOT) which is retrofitting an existing MnDOT truck with the system. MnDOT is interested in identifying procurement needs and delivery considerations, such as transport, insurance, schedule, and determining inspection requirements on AIPV components upon delivery and integration.
Missouri
The Missouri Department of Transportation (MoDOT) has worked through several stages of AIPV development initiating in 2017. Their system was also provided by Kratos for the AIPV technology in outfitted dump trucks. In 2019, MoDOT performed extensive testing for 32 hours. The main difficulties that the testing revealed were 1) reaching highway speeds by platooning the trucks, 2) following through both traffic signals and intersections, and 3) driving laterally offset from the lead vehicle. The department has reported that several issues identified during the initial testing were solved to finish the 32-hour testing. However, it is unclear which issues were identified and solved. Full initial deployment is expected in 2020 – 2021.
Tennessee
TDOT conducted an AIPV a pilot demonstration with twenty-four case scenarios to analyze the different operational components of the system [96]. In agreement with Caltrans, Tennessee DOT testing also concluded that the AIPV system is better suited for work zone operations that require continuous movement for longer periods of time like retracing or installation of pavement markings and roadway sweeping. For stop-and-go operations, like
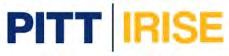
64
pothole patching, weed spraying, and trash pick-up, researchers found that the tested AIPV system needs further developing and testing.
In addition, the system denied locations when operating with Global Positioning System (GPS) for a short period of time. This issue was also mentioned by Caltrans, confirming that the tested AIPV system requires improvement for operations at locations with overpasses, heavy foliage, tunnels, and other locations that will induce long periods of sustained GPS signal loss.
Additionally, due to the “e-crumb” following technology, the testing pointed to issues with the ability of the AIPV system to consistently shadow/protect the service vehicle at all times. In some situations, the autonomous follower vehicle will not immediately shift to the lane behind the service vehicle. Since the pilot testing in Tennessee, an offset functionality has been developed for the system. Researchers point out that extensive training and practice is crucial to ensure a safe operation of the AIPV system.
Virginia
The Virginia Tech Transportation Institute formed a consortium in 2018 for the development of AIPV. The program is divided in several phases covering design, demonstration, and testing in real operations. The program has concluded phase 1 which dealt with the design of the leader-follower system.
International Experience: England
England with Kratos system is also developing a program to test AIPV. The program comprehends three main stages: operation at Goodword, deployment on M4 highway, and finally unmanned operation. Initial operation on M3 highways was of 1,000+ miles. Researchers indicated several needed improvements like a more robust user interface, V2V Hardening for radio frequency (RF) interference, and robust obstacle detection to support cone lanes. Resolving these and other issues during testing resulted in GPS card upgrade, antenna upgrade, and configuration setting adjustment. The program moved into Stage 2 in November 2019. All issues identified during the British testing have been retrofitted into an existing system by CDOT, MoDOT, Caltrans, and MnDOT.
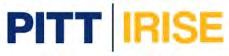
65
3.2.1.3 What is needed for PA implementation?
In this Tech-Scan the AIPV technology is considered as a technology requiring additional development, but able to be implemented in the near future. The additional development is more related to definition of proper deployment for the AIPV along with the development of rigorous testing and training protocols. Below are some considerations for AIPV implementation in Pennsylvania:
Acceptance of the technology
In October 2018, Governor Tom Wolf signed Act 117 of 2018 into law. Act 117 allows for PennDOT and the Pennsylvania Turnpike Commission to implement Highly Automated Work Zone Vehicles in work zones. The 2019 RIF also shows increase interest for automated solutions for IPV in work zones [94].
PennDOT and the Turnpike Commission are involved along with other state transportation agencies and research institutions in several connected and automated vehicle initiatives like the PennSTART Test Track, the 2040 Vision, and the Statewide Connected and Automated Vehicle Strategic Plan [101]. Although these initiatives are more focused on traffic and transportation, they also mention the support for testing and interest maintenance and operations. This shows that there could be high interest and acceptance of AIPV within the IRISE community.
Specifications and guidelines for deployment of AIPVs
PennDOT Temporary Traffic Control Guidelines (Pub. 213) informs that any non-work vehicle can be used as a shadow vehicle (popular term for IPV) provided that the vehicle is equipped with flashing, oscillating, or revolving yellow lights which are visible from any direction. The publication also mentions that when the work zone is placed on or along freeways and expressways, the shadow vehicle must be equipped with a truck mounted attenuator (TMA). In this case, the shadow vehicle weight must be greater than the minimum weight as specified by the TMA manufacturer. TMAs are optional in other types of highways. The use or not of an
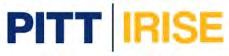
66
AIPV has implications on the necessity of some Temporary Traffic Control (TCC) devices and the distances from the TCC signs and the work zone [102].
On a more National level, concerning guidelines for deployment of AIPV, Parts 5 and 6 of the Manual on Uniform Traffic Control Devices (MUTCD) from the FHWA can be valuable indicators of the process [95]. Part 5 refers to signs regarding Autonomous Vehicles for work zones while Part 6 accounts for many different situations. According to the authors, Part 5 and Part 6 can be used for low and high-volume road, respectively.
Despite MUTCD having useful general principles, the manual refrains from giving direct guidelines for AIPV. Researchers and practitioners have expressed doubts on when and where to deploy an AIPV. Another project of the beforementioned pool study involves coming up with reasonable guidelines for deployment of AIPV. The study will focus on what is an adequate level of AADT to use AIPV due to the low speed (5 to 15 mph) of usual AIPV operation. Since there is no clear guidance on this matter, State DOTs adopt their own criteria. Colorado DOT is using an AIPV on low-volume roads (AADT less than 6000). That may apply for different states like New York where most roads are much busier than that.
Therefore, there is the need to develop clear specifications and guidelines regarding AIPV use in Pennsylvania.
Testing
Pennsylvania allows the testing of highly automated vehicles (HAV) under current state law provided that a licensed driver is behind the wheel, with the ability to intervene in the HAV operation if necessary [103]. AIPV allows for testing to be conducted with a driver in the follower truck but it is unclear how much controlling power the driver is allowed.
There is the need to define for which operation would benefit most from using AIPVs. From initial testing in other states, recommendations are being made for slow moving maintenance and cleaning operations. Testing can be conducted initially in test tracks and then moved to low volume road operations.
The pool study suggested potential areas of future research for AIPV broader implementation [95]:
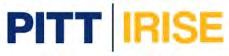
67
1) Calibration frequency 2) Standard verification procedures 3) Standard Concept of Operations 4) Cybersecurity 5) Crash protocols
Training
Extensive training of operators is needed as the AIPV system required the driver to make decisions, not only from the LT’s perspective, but also considering the potential implications on the FT operation [95]. Training protocols need to be established regarding the deployment decisions as discussed before.
Costs and developers
The leading developer of the leader-follower AIPV system is Kratos Defense & Security Solutions, Inc. a US National Security developer.
The Pitt Gazatte (2018) estimated that the cost to truck plus system is $350,000 according to conversations with the Royal Truck & Equipment marketing department [59]. There is also the possibility to retrofit existing trucks with the system. Royal Truck & Equipment also offers leasing options. All of these come with technical support and onsite training.
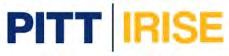
68
4. Summary and Recommendations
A remote-controlled tech scan brief analyzed over 20 technologies with promising safety benefits for pavement construction, inspection, and maintenance. Three of these technologies were selected for an in-depth review, namely, the Automated Real-Time Thermal Profiling for Asphalt Paving, the remote-controlled Density Profiling System (DPS), and the Autonomous Impact Protection Vehicle. A comprehensive performance and construction safety features of each technology were summarized in a detailed literature review. Finally, the technologies were classified based on their feasibility of implementation in Pennsylvania using the following criteria: • Technologies ready for immediate implementation. • Technologies requiring addition development, but able to be implemented in the
near future.
• Technologies promising significant benefits but requiring substantial enhancement
prior to implementation.
4.1. Automated Real-Time Thermal Profiling for Asphalt Paving
The Automated Real-Time Thermal Profiling for Asphalt Paving system showed many benefits. Besides removing the need for inspectors to actively collect data directly from the paving work and thus reducing their exposure to hot materials and heavy equipment, the technology also has the potential to improve quality of asphalt paving by providing continuous, full coverage, and high accuracy temperature data for both operators and inspectors. In addition, the technology provides real-time paver speed which can also be used for quality assurance. The Paver Mounted Thermal Profiler (PMTP) system has been tested and approved by many state DOTs over the last 15 years with a great cost-benefit ratio. Therefore, this technology is classified as ready for immediate implementation.
We recommend the following steps for the initial implementation of this technology: 1) Perform demonstrations of the device in real paving projects to show the benefits of the technology. 2) Conduct training of operators and inspectors to access and interpret the collected data. 3) Develop a strategic plan in case of real-time data showing cold asphalt mat areas.
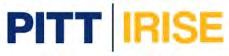
69
4) Establish acceptable and unacceptable temperature and temperature variation criteria as measured by the PMTP. 5) Modify PA specifications to include the use of the PMTP.
4.2. Remote Controlled Density Profiling System
The remote-controlled DSP (Figure 40a) technology is in the final stages of development. The robotic prototype has been successfully tested in different scenarios. However, the device has not yet been deployed in any major asphalt pavement project. Additional features are in development with focus on faster scanning, marking of areas of interest, inclusion of collision sensors, and GPS simplifications. This way, the DPS robot was classified as a technology
promising significant benefits but requiring substantial enhancement prior to
implementation.
However, IRISE members can benefit from the use of the conventional man operated DPS (Figure 40b) before the robotic platform is commercially available. The conventional DPS provides abundant high-quality asphalt density information without the need to extract material (coring) from the constructed pavement. The conventional DPS is classified as ready for immediate implementation and its implementation will provide guidelines for the use of the robotic platform in the near future.
(a) (b)
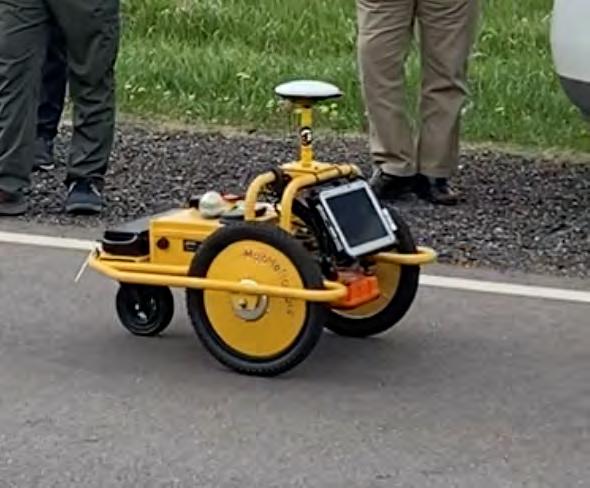
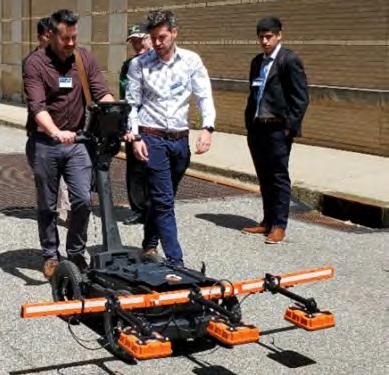
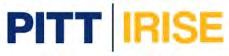
70