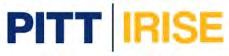
14 minute read
Appendix B: Technology Transfer Workshops
Appendix B: Technology Transfer Workshops
The first workshop with focus on the Autonomous Impact Protection Vehicle (AIPV) was conducted virtually on April 6th, 2022, with a presentation from the major vendor and developer of this technology. Over forty participants attended the workshop.
For the other technologies, a combined workshop was held in-person (with virtual participation as well) on May 24th, 2022, with presentations from experts in both technologies. Again, over forty participants attend the workshop. A field demonstration of the density profiling system (DPS) was conducted at the end of the IRISE Annual Meeting on May 25th, 2022, in a parking lot. Another field demonstration of the DPS was conducted for Allegheny County and invitees on June 9th, 2022, in an active paving project.
Recordings of these presentations are available at the IRISE website.
B.2. Autonomous Impact Protection Vehicle Workshop
The workshop was presented by Maynard Factor from Kratos Defense and Security Solutions. Mr. Factor is the Vice President of Business Development for the Kratos Defense & Security Solutions Unmanned Systems Division. He is responsible for the generation of new business opportunities, world-wide sales, and marketing, and provides technical direction for long range strategic planning including the development of new products, capabilities, and internal research and development endeavors. Kratos Defense and Security Solutions works in collaboration with Royal Truck and Equipment Inc. to develop the autonomous truck mounted attenuators (ATMA) also known as Autonomous Impact Protection Vehicle (AIPV).
B.2.1. ATMA workshop presentation minutes
Standard truck mounted attenuators (TMA) are regularly used in moving work zones in all 50 states and worldwide. Moving work zones are common practice for operations like line painting or patching. These work zones typically move at speeds of 7 – 15 mph along regular
82
moving traffic. TMA are designed to be mobile crash barriers that prevent distracted drivers from entering work zones potentially injuring or killing workers.
Currently, TMA must be driven manually which is a very dangerous assignment. If the TMA is struck, it prevents injuries to workers inside the construction zone but can cause serious injury or death to the TMA driver. Automation would move the worker away from the danger zone and allow them to continue to operate the TMA. The goal is not to eliminate this job but to convert them from a driver in a dangerous position to an operator from afar.
To permit driverless vehicles, Pennsylvania passed ACT 117 which allows driverless construction vehicles for maintenance. This was spurred by TMA driver testimonials which encouraged the development of safer construction practices. The automatic truck mounted truck attenuators (ATMA) designed by Kratos Defense and Security Solutions and the Royal Truck and Equipment Inc. were created for this purpose.
ATMA use a multi-vehicle configuration which Kratos call “leader/follower”. The vehicle performing the work zone operation is the leader and the ATMA follows driverless. A retrofit kit can convert any existing fleet vehicle into an autonomous vehicle to use in an ATMA system. The kit attached to the leader vehicle will collect navigation data to send to the ATMA. The kit attached to the ATMA will install the driverless technology. The operator, now located in the leader vehicle, can adjust the ATMA vehicle alignment and follow distance in real time. The ATMA can follow within an accuracy of 1 inch in a straight path and 3 inches around turns.
ATMA has obstacle detection on all sides and will automatically stop if sensors are tripped. There are redundancies built in for communication and navigational links to prevent connection failure. There are also security protocols that prevent outside interference and hacking. Separate stop buttons are located in the leader vehicle and outside the following ATMA vehicle for emergencies. Retrofit kits are adaptable but they ask for an automatic transmission for ease of use and a newer model vehicle which will not be replaced soon.
ATMA systems have been deployed in 8 states and England through either purchase or lease. At this time, not all states allow for driverless construction vehicles and therefore require a driver in the ATMA. This allows workers and communities to familiarize themselves with the
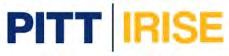
83
technology until legislation is passed. ATMA can easily transition from automated to manual if the need arises.
This system has had many positive reviews and constructive comments which have been actively used to farther improve the technology. Several awards have been given for this system as well. ATMA have clear benefits including worker safety and a simple introduction to autonomous vehicles for departments of transportation.
B.2.2. ATMA workshop Q&A
Some questions and concerns were raised by the attendees. The main questions concerned pricing and deployment requirements.
To purchase an ATMA system, the initial cost would be about $350,000. This would include training, installation, and deployment assistance as well as the two full kits: one for the lead vehicle and one for the follow vehicle. After comfort is established with the system, additional systems would cost about $150,000 - $200,000. However, if the vehicle to retrofit is different than those currently used, additional cost is required to design the retrofit kit to the new vehicle. Leasing is also an option either through pre-configured vehicles or through temporary retrofit installation. The first week is at least $20,000 depending on transportation or installation of equipment and training. Additional time would cost about $10,000 per week. To deploy, it typically takes 6 months to a year depending on many factors including location and previous experience in automation.
There was a question regarding the top speed of the driverless vehicle. An ATMA has a standardized speed limit of 20 mph, but it is adjustable up to 70 mph. There was a concern on the effect of hills and slopes on navigation to which this issue was previously discovered and addressed so that the latest ATMA technology does not have this problem. Another concern was if a passenger vehicle accidently got between the leader and follower vehicle. An interrupting vehicle does not disrupt the connection unless the vehicle is within the obstacle detection range. The ATMA would then stop automatically. If the leader instructs the ATMA to continue operation, the ATMA would continue following the navigation path set by the leader at a slightly elevated speed until the set follow distance is recovered.
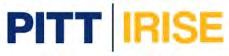
84
A final note was the existence of a pooled fund of information on deploying ATMA shared between 13 states. This includes experiences, user manuals, and training procedures. Currently, Pennsylvania is not part of this fund.
B.3. Automated Real-Time Thermal Profiling & Density Profiling System Workshop
This workshop had four presenters. First, Joe Reiter from Applied Research Associates (ARA) talked about the Paver Mounted Thermal Profiler. Mr. Reiter works as a senior engineer at ARA specializing in non-destructive testing of pavement systems, materials, and construction. He participated in the SHRP2 R06C study [52] using infrared scanning of new construction asphalt and presented demonstrations of the paver mounted thermal profiler (PMTP) from 2015 to 2019.
In the Density Profiling System (DPS) part of the workshop, Dr. Lev Khazanovich, Anthony Gill Professor at the University of Pittsburgh, introduced Ground Penetrating Radar (GPR) concepts and the DPS technology. Dr. Khazanovich has many years of experience with GPR and DPS for asphalt inspection. He participated in the SHRP2 study [63] which focused heavily on field testing and procedures for DPS. He was followed by Dr. Kyle Hoegh from the Minnesota Department of Transportation talking about DPS benefits and implementation. Dr. Hoegh currently leads a pool-funded study with several institutions to implement DPS. Finally, Ken Corcoran from GSSI presented the robotic platform for the DPS technology. Mr. Corcoran is a GPR product specialist with 25 years of experience with GPR.
B.3.1. Automated Real-Time Thermal Profiling & Density Profiling System workshop presentation minutes
The first presentation was on Paver Mounted Thermal Profilers given by Joe Reiter from ARA. He began by discussing the importance of temperature monitoring as it is an indicator of density non-uniformity. If temperature differentials are not known during construction, the roller pattern cannot be altered to the new temperature to correct the density. Traditional temperature measurements rely on point-based methods like standard temperature guns or infrared cameras.
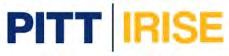
85
These methods can identify temperature differences but only at certain chosen points and relocating problem areas can be challenging. The methods also require the inspector to stand behind the paver which can be dangerous, especially at night. To remove inspectors from hazard areas, a continuous temperature infrared scan was developed that is attached to the back of the paver. This provided an improved temperature profile but was a safety concern for workers on the back of a paver.
The paver mounted thermal profiler is a single scanner mounted on the paver, above the workers, which pivots to scan the pavement width. This method creates a thermal profile across the entire pavement as it is being paved providing more data with greater accuracy.
The thermal profiler has a display inside the paver which shows the operator the average temperature across the width, the full thermal profile, paver speed, an analysis on uniformity, and more. The data allows contractors to adjust construction practices in real time. It also removes temperature data from any obstructions, only considering the pavement. Data gathered by this device can be stored on a USB or the cloud. The cloud will update automatically and constantly, allowing inspectors and others to observe the paving from anywhere.
This device is primarily used as a quality assurance tool. Contractors can use it to monitor production and placement, minimize penalties, and as a forensic tool. Agencies can also benefit by identifying areas to sample, determine why a pavement fails in the future, and reduce or prepare for future distresses and maintenance. Overall, it helps to determine what and when changes are needed during paving by using temperature variation to predict density variation and reconsider roller patterns to correct the issue.
Lessons learned in this research were thermal profilers reinforces good construction practices, provides information to use to adjust roller patterns to get uniform density, and provides information on when to add delivery trucks or tarps.
The second presentation on Density Profiling Systems (DPS) was given by Dr. Lev Khazanovich from the University of Pittsburgh. He began by stressing the importance of good density to improve rutting and fatigue cracking resistance and to reduce moisture penetration. Density is traditionally measured by coring or nuclear density gauges, but both these methods have well-known issues. A nondestructive test called ground penetrating radar (GPR), which
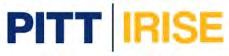
86
measures the amplitude of a reflected signal which depends on the dielectric constant of the pavement, presents many benefits. The dielectric constant is the material property to store electric energy. A low dielectric constant means there is a high air void content resulting in lower density.
The DPS is a high frequency, air coupled device that measures the dielectric constant providing real time density estimations. This allows users to continuously monitor compaction uniformity. Small changes in the dielectric constant causes a large change in air content therefore high accuracy is necessary. The device must also only consider the newly paved layer, not the underlying structure.
DPS is a simple device that requires minimal training. The user can immediately follow the paver to quickly acquire and analyze the dielectric data. This device is also geotagged so areas of interest can easily be revisited. DPS is not able to directly measure air voids, measure thickness, or consider underlying layers or subsurface objects. Many of these can be done using other GPR types but not DPS. DPS requires calibration to determine the air void content from the dielectric constant and the calibration depends on each individual mixture. Other devices such as intelligent compaction or infrared sensors can be used in tandem to analyze different aspects.
The next presentation was on moving Toward Improved Asphalt Pavement Density Acceptance given by Dr. Kyle Hoegh with the Minnesota Department of Transportation. This effort was part of a collaboration of 14 agencies and the Federal Highway Administration. Density profiling systems (DPS) provide real time continuous density assessment of the placed asphalt after the finish roller and the goal of this project is the use DPS to improve pavement density and construction practices. DPS would allow improved coverage and comprehensiveness of density measurements and ultimately reduce coring. Pavement density is highly dependent on construction practices and coring does not provide enough information to locate low density areas.
Density mapping can be used as a process control tool to adjust field work and certain aspects are needed for accurate mapping. Dr. Kyle showed several two examples of this adjustments done in real-time during paving projects. The correct equipment must be used that
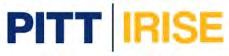
87
provides good precision and standardized sensors. Sensor standardization includes regular sensor testing using a line test or a steel of fiberglass material scan to test for sensor consistency. Improved calibration can be performed on gyratory compacted asphalt samples to remove coring from calibration. This method falls well within the repeatability requirements and provides stable results. They still recommend coring in the field for data validation. A routine collection habit is needed that requires the same number of passes and user movement method (walk verses driving). Proper training must also be a requirement.
The final presentation was on the Pavescan Robotic Platform given by Ken Corcorank with GSSI. He was able to receive user feedback on density mapping devices that was both technical feedback and user experience. It was noted that there was still a safety concern with nearby traffic and with technicians walking many miles on the hot mat. There were three new methods to the traditional pushed device: segways for technicians, vehicle mounted device, or remote-controlled robots.
This presentation focused on the robotic platform. The first model had the sensors attached externally to the robot. The robot itself was light with a long battery life that was able to last the workday. The remote-controlled aspect removed the technician from hazardous areas or a line mode setting automatically drives the robot in a grid formation. The second model improved the device by internalizing the sensor and connecting the sensor to the robot battery. A grid mode setting was designed in an app to determine scan distances and path types the robot can automatically drive. The remote-controlled option is also still available. The robot creates a dielectric constant contour map within the app. The next steps for the robotic device are to scan faster, mark areas of low dielectric constant with chalk on the pavement surface, add collision sensors, develop smarter route planning, and to simplify the GPS.
On May 25th a DPS device was demonstrated in a parking lot at the University of Pittsburgh campus. Attendees of the demonstration were able to calibrate and operate the device (Figure B.1a) measuring dielectric constant and levels of compaction of the existing asphalt layer. A week later the device was demonstrated for Allegheny County and invitees in an active paving project (Figure B.1b).
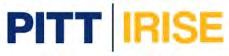
88
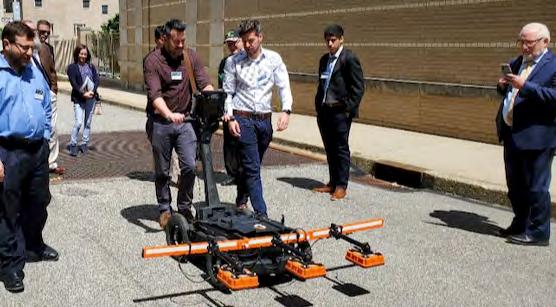
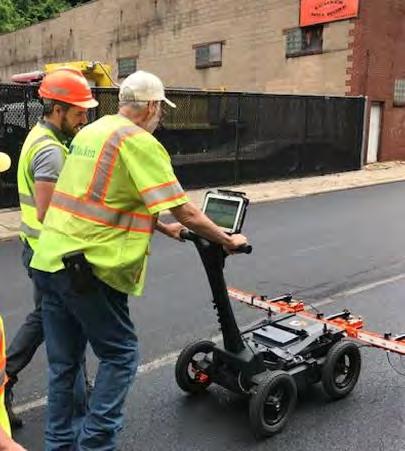
(a) (b) Figure B.1 – DPS field demonstration at (a) the IRISE annual meeting, and at (b) an active paving project.
B.3.2. Automated Real-Time Thermal Profiling & Density Profiling System Workshop Q&A
For the automated real-time thermal profiling presentation, the audience had several questions for the presenter. One was concerning how the workers know where the scan is occurring and how to stay out of the way. They simply inform the workers of its locations and advise to avoid when possible. Another question was how much the device costs to buy or rent. It was advised to contact the manufacturer for renting costs but buying costs range between $35,000 and $45,000 depending on installation. There is also an annual fee to access the cloud.
There was a concern about the security of the cloud. It is password protected but for additional information, contact the manufacturer. An audience member asked what the biggest issue is in implementation. The presenter said that they are having difficulties explaining that it is supposed to be used to improve the paving process. It is not a device to highlight errors in a negative way, but to show where improvements can be made. Finally, there was a question on using the device with incentives and disincentives. The Minnesota Department of Transportation requires this device on all their pavers and has incentives and disincentives based on temperature
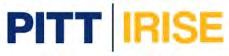
89
differentials which has been used with success. Federal funds cannot use incentives because they do not have independent measurements.
On the DPS presentations, there was a question on the effect on surface water on DPS measurements. It is a minimal concern since the device is used immediately after paving when there will not be surface water. There was another question on the use on concrete, but DPS is not for concrete use. Finally, there was a question on a roller mounted DPS which are currently being researched.
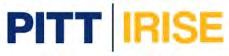
90