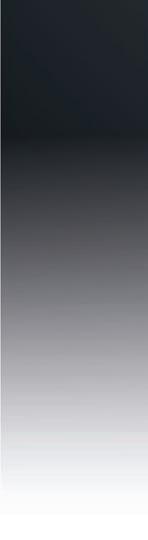

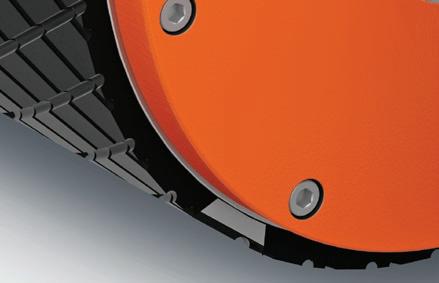
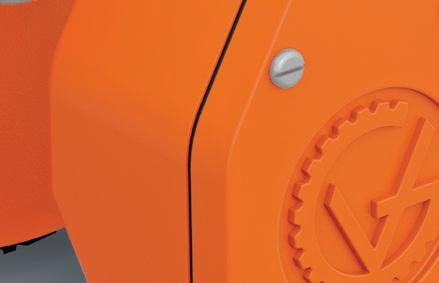
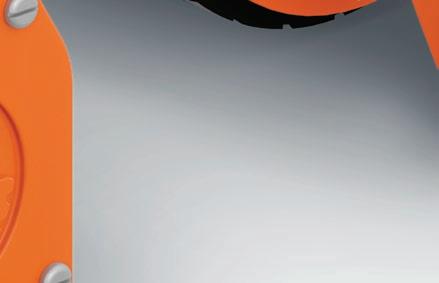
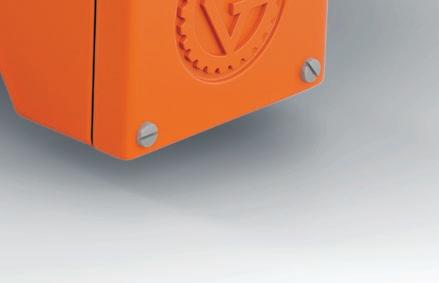
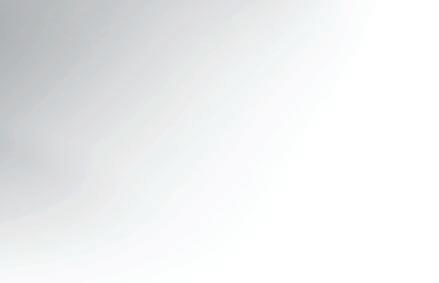
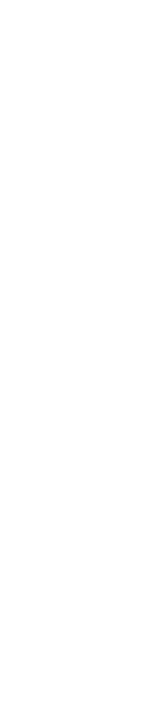
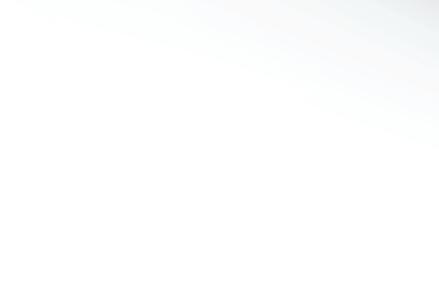
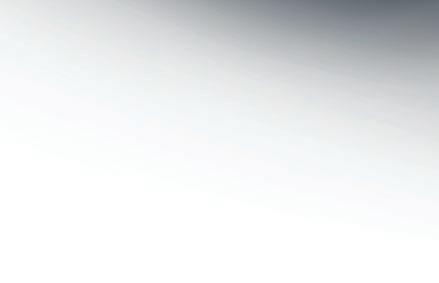
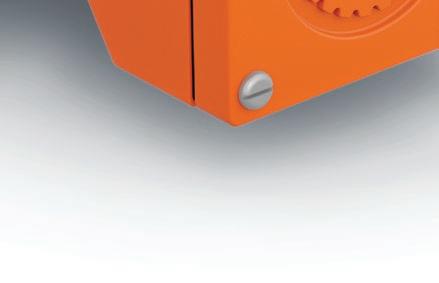

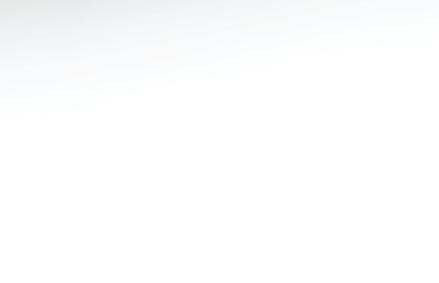
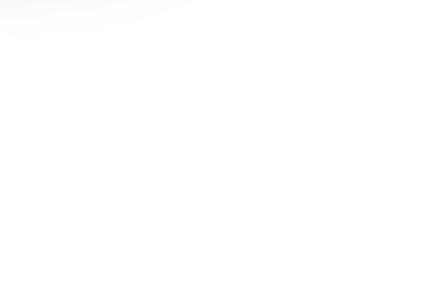



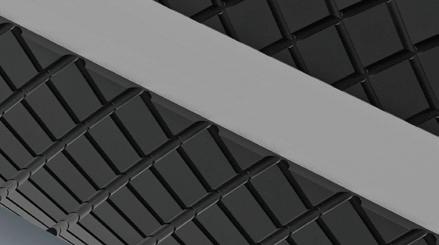
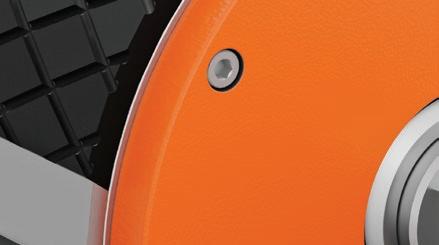
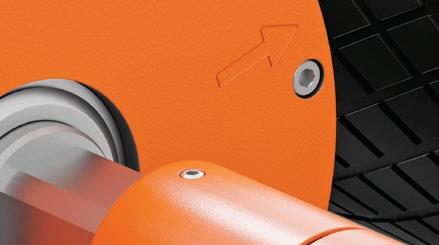
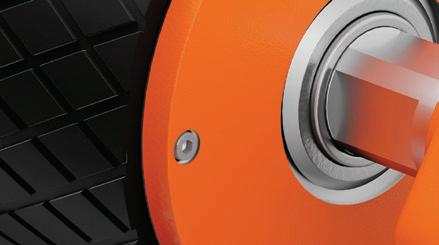
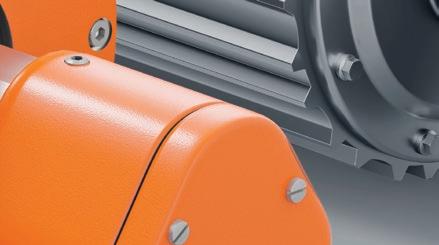
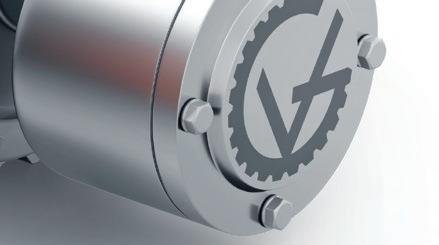
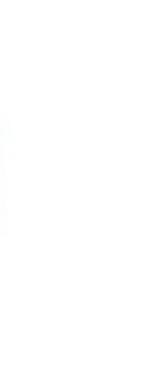
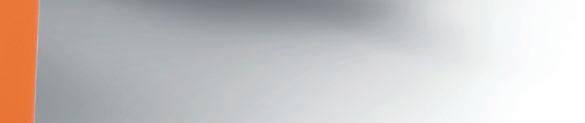


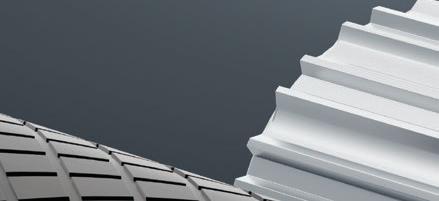
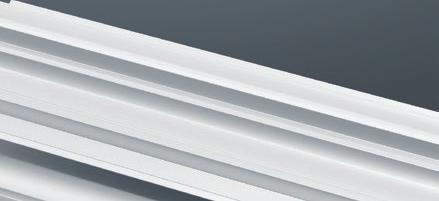
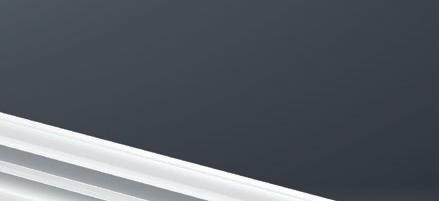
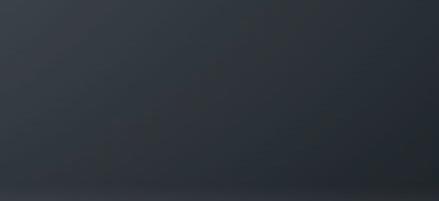
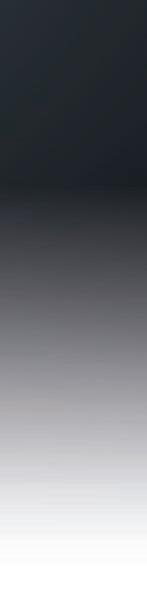
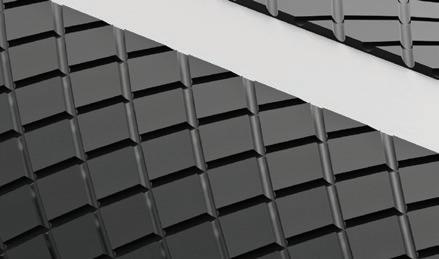

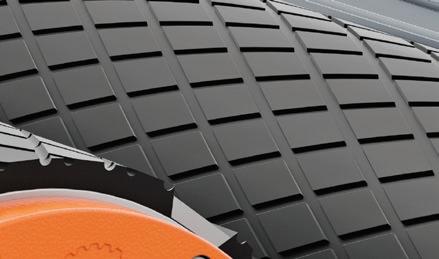

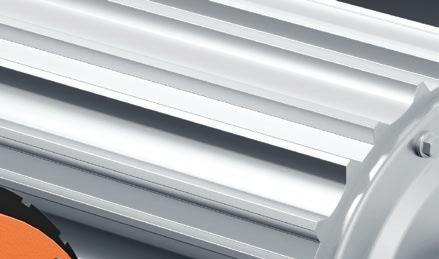
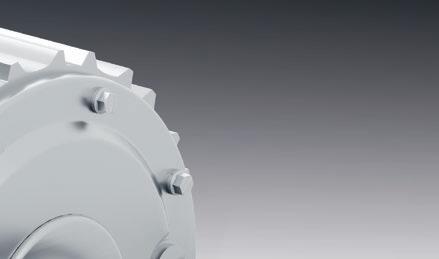





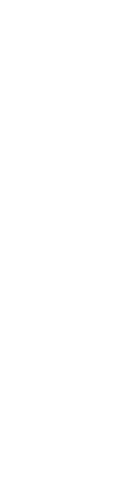


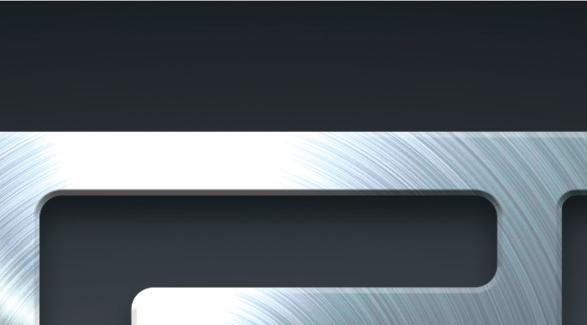
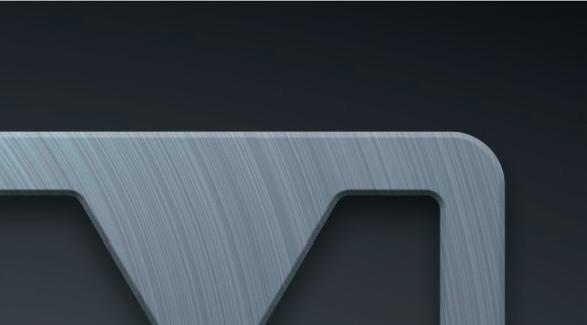
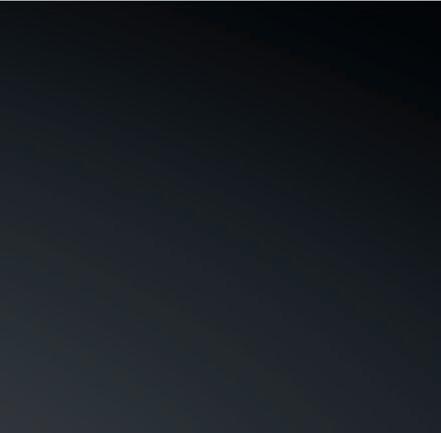
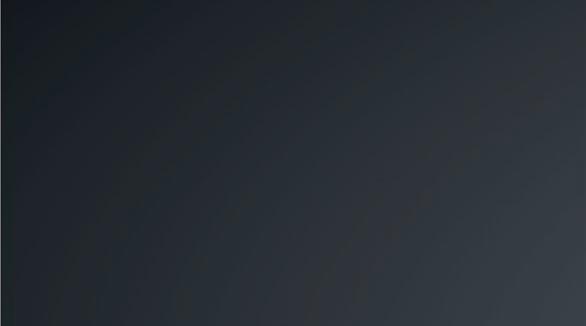


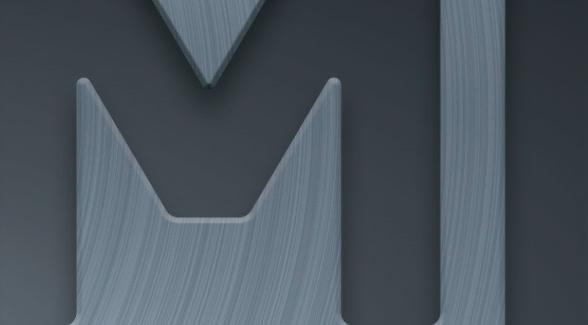
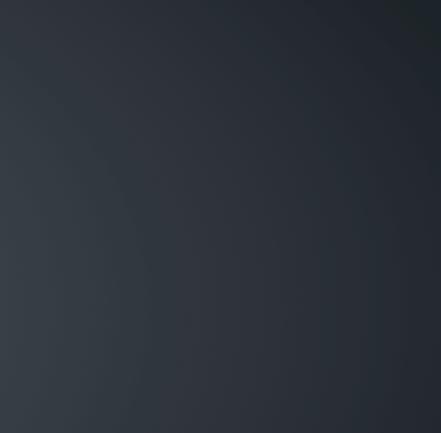

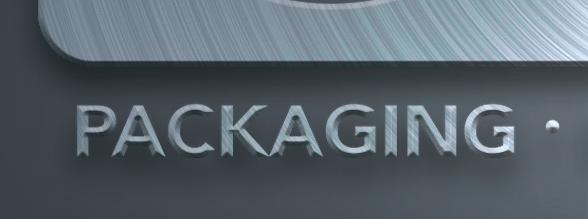

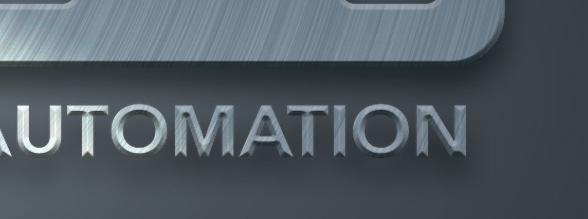






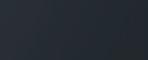
Engineered for reliability and longevity, VDG Drum Motors are designed for 80,000 hours of continuous operation before maintenance, reducing operational and maintenance costs and increasing throughput.
To suit various belt conveyor applications, a variety of diameter sizes, belt speeds, horsepower, face widths, and industry specific options are available.
The SSV Series Drum Motor is the most hygienic and efficient conveyor drive for sanitary belt conveyor applications. It has the belt profile machined directly onto the drum and drives modular conveyor belts without using sprockets, reducing time and water used for washdown.
Learn more at: vandergraaf.com/OEM
Opportunities Available: Sales Personnel • Sales Representatives • Resellers Apply at: vandergraaf.com/jobs • (888) 326-1476
The new UC18GS series combines the advantages of ultrasonic technology with powerful features to create a sensor solution that meets virtually any application challenge.
The official publication of PMMI OEMMAGAZINE.ORG
EDITORIAL
Stephanie Neil Editor-in-Chief sneil@OEMmagazine.org / 781 378 1652
Victoria Sanchez Managing Editor vsanchez@pmmimediagroup.com / 571 612 3200, ext. 9298
Sean Riley Senior News Director sriley@pmmi.org / 571 266 4419
Jonathan Fleming Art Director
David Bacho Creative Director
George Shurtleff Advertising Production Manager
Mike Prokopeak Senior Director, Content & Brand Growth
Kim Overstreet Director, Emerging Brands Alliance
Sharon Taylor Director of Marketing
Amber Miller Senior Marketing Manager
Janet Fabiano Financial Services Manager
PMMI Media Group
401 N. Michigan Ave., Suite 1700, Chicago, IL 60611
Phone: 312 222 1010 | Fax: 312 222 1310 www.pmmimediagroup.com
David Newcorn President
Kelly Greeby Sr. Director, Client Success & Media Operations
Elizabeth Kachoris Vice President, Digital
Jen Krepelka Director, Digital Media
PMMI, The Association for Packaging and Processing Technologies
12930 Worldgate Dr., Suite 200, Herndon VA, 20170 Phone: 571 612 3200 | Fax: 703 243 8556 www.pmmi.org
Jim Pi as President and CEO
Joe Angel Executive VP, Industry Outreach Glen Long Senior VP
Tracy Stout VP, Marketing and Communications
Laura Thompson VP, Trade Shows
Andrew Dougherty Senior Director, Membership
SUBSCRIPTIONS
To subscribe
Colin
The most notable feature of the EZGUIDE™ system is it does not have any protruding brackets or shafts which could be a major safety hazard. The EZGUIDE™ system does not have any mechanical components which protrude from the sides of the conveyor during adjustment. All the mechanics are done without the need to protrude past the conveyor, keeping everything safe for those walking close by.
Another feature of EZGUIDE™ is it is designed to remain adjustable through curves. That is, the radius of the guides can change as the guide width is increased/decreased in the curve. While there are many traditional guide rail systems which can be made to adjust their width in straight sections, there are very few that can truly be adjustable through a curved portion of conveyor. The reason is because changing the radius of a section is di cult – the guides must bend, and the length of the guide has to increase/ decrease as the radius is changed. The EZGUIDE™ system handles both of those problems with its unique design.
In this issue of OEM magazine, we highlight the awardwinning projects and people that made 2022 so memorable for the packaging and processing community. The first recognition goes to PMMI for the production of PACK EXPO International in October. The exhibit aisles were packed with attendees and there were some major milestones, like the debut of the Emerging Brands Summit, and a record-breaking audience at the Packaging & Processing Women’s Leadership Network (PPWLN) breakfast. About 1,000 people came to hear PPWLN keynote speaker Dawn Hudson, former CEO of Pepsi N.A. and former CMO for the NFL. An interview with Hudson can be found on pg. 44, including a link to the full UnPACKed podcast.
Also in this issue we spotlight the 2022 Emerging Leaders On the Rise winners. The awards recognize 10 young professionals who have demonstrated leadership potential in packaging and processing. Turn to pg. 10 for a quick introduction to each winner with a link in their short bio to the full interviews on the OEM website. Another PPWLN achievement is the introduction of the “Voices of Women in Packaging and Processing” digital resource done in col-
laboration with the OpX Leadership Network. This tool outlines five core characteristics that will help women navigate a career in manufacturing. Learn more on pg. 16.
As part of this “Best of 2022” issue, we also introduce you to the PMMI 2022 Technology Excellence Awards winners (pg. 32) and the winners of the ProFood World Sustainable Excellence in Manufacturing awards (pg. 34).
In addition to these accolades, I thought it would be nice to recognize an OEM that represents the greatest achievement of all: The American dream. PDC was founded in 1968 by Anatole Konstantin, who immigrated to the U.S. after World War II. The maker of shrink sleeve labeling and tamper evident banding has a fascinating history and now, under the leadership of Konstantin’s son, Neal, an exciting new future (pg. 18).
Lastly, a big thank you to every machine builder out there. You’re all winners in my book!!
Stephanie Neil is the Editor-in-Chief of OEM Magazine. She may be reached at sneil@oemmagazine.org or at www.linkedin.com/in/ stephaniesneil.
Industrial robots have come a long way since their initial introduction in the automotive industry. In the last few years, robots have become smaller, more affordable, and more widely available. Their capabilities have steadily expanded through improvements to machine vision, EoAT technology, AI/machine learning, durability, and safety, according to PMMI Business Intelligence’s 2022 report “Robots and Cobots—An Automated Future.”
Robots have also become simpler to program and operate, reducing the level of technical skill needed for successful deployment. As these robot capabilities progress, robots are steadily expanding into new applications and even entirely new industries. To that end, robots have become more readily accessible in recent years, with availability increasing and cost decreasing. In addition, robots are steadily moving toward simple, intuitive programming that does not require a highly specialized skill set to configure and operate. These advancements have enabled small and medium sized enterprises across industries to more readily add robotics to their operations.
Additional features of the robot evolution include:
Robots that adhere to IP69k washdown standards are now common, enabling their use in the pharmaceutical, food, and beverage industries.
These robots are able to withstand the harsh chemicals required for washdown and are designed to eliminate any dead spots where liquid could collect. The most advanced of these robots can even wash down their own work cell themselves, all without the need for human intervention.
AI and machine learning have been key developments in robotics that are continually expanding the realm of possibility for robot applications. Closely intertwined, AI and
Robot technology is more advanced and applicable than ever with the help of machine learning, washdown capability, and safety improvements, but there is still plenty of room for innovation.
machine learning allow robots to adapt to new scenarios by building on a constantly increasing volume of relevant data. These technologies have opened up a world of complicated tasks for robots, from dynamically picking items the robot has never encountered before to rapidly and accurately inspecting incoming and outgoing products on a line.
Improvements to safety design and proximity sensing have steadily broken down the barrier between robot and human tasks. While the early days of robotics required large cordoned off safety cells for robots to operate in, the newest modern class of cobots can safely and efficiently work alongside human employees. These cobots are increasingly compact, modular, and mobile, enabling their deployment to virtually any part of a manufacturing operation.
Advancements in EoAT technology have dramatically expanded the picking capabilities of robots, enabling their use in a much wider variety of markets than ever before. Tactile sensing allows robots to pick delicate and oddshaped items like baked goods and fragile electronic wafers without sacrificing speed and accuracy. Modern robots can even pack multiple cases at once, holding up to three dozen items at the same time and accurately placing them into separate cases.
Despite this amazing growth, advancing technology still stands to carry robotics to entirely new frontiers of possibility. While the following examples are by no means certainties that will come to pass, the robotics industry is
awash in visionary speculation of what robots of the future will be able to accomplish.
While seven-axis robots already exist through solutions such as attaching a six-axis robot to a tracked, linear gantry, the future of seven-axis robots could be even more dynamic. There are already some rudimentary deployments of robotic arms attached to mobile, wheeled platforms. As AMR technology improves in the next decade to the point where AMRs can reactively navigate their environment and then spontaneously plot and resume a new course in real time, they could be mounted with six-axis arms to enable fully autonomous redeployment of robotic units to all areas of an operation.
The horizon for AI and machine learning applications of the future is wide open. Tools such as elaborate, deeplearning neural networks may soon be available for standard manufacturing robotics, with the potential to drastically expand the intelligence of robots. It is not impossible that robots of the future will be able to evaluate a new task, assess the environment the task will be conducted in, and then formulate a process to accomplish that task—all without any human intervention.
Robots can already see and touch at levels fast-approaching human capability, but that may soon expand to other human senses. Robots capable of hearing—and most importantly—understanding unscripted, spontaneous verbal commands are a possibility. Robots of the future could even be equipped with olfactory capabilities, enabling them to detect dangerous emissions or contamination long before they would ever register in a human nose.
New materials are currently under development that have the ability to self-repair tears and breaks. With the support of future AI networks, these materials could be applied to robots, enabling a robot to detect damage in its “skin” and initiate a repair sequence. Advancements in sensor technology could even enable robots to repair and replace their own hardware proactively, such as detecting a loosening screw and independently tightening it before damage occurs.
➲ Download the PMMI Business Intelligence report, 2022 Robots and Cobots: An Automated Future here: oemgo. to/2022futureofrobots
Easily share this article with your peers: oemgo.to/robotfrontier2022
These up-and-coming professionals are leading efforts within their respective organizations that are making a difference in business as well as addressing industry issues.
Sean Riley, Senior News DirectorPMMI’s On the Rise Awards began in 2018 as a way to recognize young talent making their mark on the packaging and processing industries. Developed by PMMI’s Emerging Leaders Committee, the awards recognize 10 young professionals who have demonstrated leadership potential in packaging and processing while also showcasing the accomplishments that made them worthy of recognition. OEM interviewed each of the winners and their individual stories are available online (see oemgo.to/ links). Here is a summary of why each of the winners deserved the distinction, but you would be remiss not to give these young upstarts their due by reading the longer digital articles!
Alison Zitzke’s most recent achievement spearheaded the development and launch of ORBIS’ flagship 40x48 pallet, the Odyssey, bringing ORBIS’ pallet portfolio into new manufacturing applications and markets within the reusable packaging space. Alison is no stranger to breaking barriers as she continues to challenge the status quo in the industry to support the conversion from wood pallets prevalent in the marketplace to a sustainable, reusable plastic pallet solution. Alison is passionate about promoting the circular economy and experimenting with incorporating post-consumer and post-industrial recycled materials back into manufacturing new products. (oemgo.to/ alisonzitzke)
In just six months, Allison Wagner grew the Morrison communications manager role into a full-fledged marketing department. Aligning with sales, Allison helped Morrison achieve over 20% year-over-year growth for three consecutive years. She cultivated the brand story, “Innovative Container Handling, Expert Design, and Support Built-In,” bringing the customer’s needs front and center. During COVID, Allison took it upon herself to transform the company digitally by overhauling the SEO and social media. This led to an average website traffic improvement of over 120% per product page, and lead generation form fills went up 200% annually. (oemgo.to/allisonwagner)
Caitlin Eargood helped transform the project management role into a more efficient, structured process to better support the field service team and improve the customer experience while maintaining the required KPI data. Caitlin thoroughly tested the installation performance & acceptance sign-off criteria and new tools for enhanced visibility, accountability, and overall customer experience. She was instrumental in developing new software tools to professionalize and harmonize the XR process. On top of being a new mother, Caitlin is currently enrolled in college to obtain her master’s degree, having just completed PMP certification in March 2022. (oemgo.to/caitlineargood)
Delkor Systems, Inc.
Eric Andersen is a pace-setting, performance-driven team player. He is a fearless change agent who is unafraid of disrupting the status quo and continuously exceeds expectations. Eric is a leader of Delkor’s brand strategy and has focused on implementing a branding campaign that ensures each interaction with Delkor provides a consistent experience. Eric’s marketing leadership has delivered some of the most successful sales years in recent company history. He partnered with executive leadership, sales, and engineering teams to create and execute significant sales strategies to help grow and diversify the customer base. Eric has continued his education by taking an assortment of advanced classes in videography, which has ushered in a new era for Delkor and significantly advanced the company’s marketing capabilities. (oemgo.to/ericandersen)
Formers International
Nancy Garza–Castaneda performs the accounting and procurement functions for Formers International. She is unbelievably resourceful and has streamlined the process for securing consumable gases used in Formers International’s manufacturing process. Nancy established providers of telemetry services that have dropped changeover times by 30% and have reduced costs by 72%, which resulted in over $100k in savings annually. Additionally, she played a massive role in implementing ISO 9001:2015 in 2021. She obtained an internal auditor certification and was a primary member of the team that increased on-time delivery by 63% over 12 months. Nancy is currently pursuing a business degree and enjoyed networking at the PMMI Young Professionals Conference in 2022. (oemgo.to/garzacastaneda)
Controls
ID Technology / ProMach, Inc.
Ravi Patel was promoted to controls engineering manager in 2021 based on his strong technical and leadership skills. His extraordinary efforts and ingenuity have enabled ID Technology / ProMach, Inc. to keep up with customer demands, including complex overseas installations. Ravi’s leadership and communication abilities also help attract, retain, and develop new engineers and technicians. He has introduced improved documentation processes and procedures, which have reduced six hours of work for each project. Ravi is currently working toward his Certified Automation Professional (CAP) certification through the International Society of Automation and is also a Six Sigma White Belt. (oemgo.to/ravipatel)
Samantha Hoover’s initiatives within the applications team have led to advancements in Spee-Dee Packaging Machinery’s processes and designs for even the most complex product properties. This work has included in-depth interviews with known product specialists and documentation of findings, expansion of product testing, and data utilization and evaluation. The trait that has impressed the team the most about Samantha has been her ability to get things done quickly, efficiently, and with a high level of quality assurance. Samantha is passionate about education and has led Spee-Dee Packaging Machinery’s “Pack Challenge” initiative. She maintains multiple positions with the American Society of Mechanical Engineers to further expand her knowledge and share that information with others. (oemgo.to/ samanthahoover)
Taz Lombardo developed the “Packed with Expertise” blog, which elevates Barry-Wehmiller Packaging Systems team members’ voices worldwide on topics ranging from packaging sustainability to calculating the total cost of ownership. By taking a collaborative, listen-first approach, Taz utilizes his time to fully understand these topics before helping the subject matter experts write about them. Due to the engaging and informative nature of the blog, many of these stories have also been featured in trade publications. Taz led a project to develop the new BW Packaging Systems website, which helps customers connect with the five divisions faster by allowing them to browse a portfolio of solutions by market, equipment, or packaging type. (oemgo.to/tazlombardo)
Tom Lex is a process improvement wizard and has completely revamped the engineering department at TechniBlend into a finely tuned, processoriented, and streamlined team. He opened communications among all engineers and implemented accountability and procedural standards, which has the team delivering on time with error-free results. Tom managed a value-stream-mapping project called “quote to cash,” which led to TechniBlend’s productivity and manufacturing efficiency reaching new levels. He is currently on a career track to become the COO and is a steadfast company representative. Tom has been invited to attend classes and speak at local tech colleges to further his corporate development. (oemgo.to/tomlex)
William Reese’s attention to detail and excellent communication skills launched him into a sales position managing Garvey’s central territory. After several successful years in sales, the management team recognized that his experience would make him the perfect person to manage the proposals department, where he maximized communication and teamwork between management, engineering, sales, and production. In his management role, William reduced the time to prepare detailed proposals by 75% and increased overall pricing accuracy. He also worked with the marketing group to promote innovations, design advertisements, and trade show displays. William’s hard work and dedication have earned him a seat on Garvey’s steering committee, where he plays a crucial role in major decisions and long-term strategic planning. (oemgo.to/williamreese)
Easily share this article: oemgo.to/ontherise2022
Machine builders can use the Nupano cloud-based platform to create new machine related digital services and revenue streams through the ability to remotely and securely update and maintain equipment in the field.
Melissa Griffen, Editor-in-Chief, Contract Manufacturing and PackagingAt Lenze’s 75th anniversary celebration in Hameln, Germany, the company launched Nupano, its open automation platform designed to help OEMs combine information technology (IT) and operations technology (OT) in their equipment.
Nupano is a cloud-based machine and app-management platform that supports the sharing of functions for equipment testing and validation, and provides access to publicly available apps as well to the OEM’s machine-specific apps through open IT standards, such as Linux with native Docker as container technology. This allows the handling of environment variables and volumes, and provides IP-based communication such as OPC UA, MQTT, TCP/IP, UDP, HTTP(S), etc. Any existing software that can be integrated into a Docker container run as a Nupano app without modification. This also applies if users want to access over 100,000 container images on Docker Hub or integrate open-source software from GitHub. Open-source software does not need to be customized to run on Nupano because the Nupano platform has no proprietary interfaces.
According to Lenze, Nupano apps are based on standardized programming languages (such as Java, Python, Go, TypeScript, C++, Rust or any other language which can be wrapped
in the Container Technology), which eases the process of embedding them into equipment interfaces without the need for specific IT skills. For OEMs, Lenze says Nupano provides a single tool to keep machines operating efficiently in the field by enabling OEMs to continuously update them across
thousands of versions. With this technology, OEMs can securely equip each machine individually with new app versions throughout its lifecycle, while also ensuring that the OEM retains ownership of associated digital revenue streams.
Nupano security measures are designed according to IEC 62443, which includes:
• Two-factor-authentication
• Encrypted communication and signed data exchange between the machine’s digital twin and the Nupano Runtime on an industrial PC
• Secure pairing of the digital twin and the Nupano Runtime using a Public-Key-Infrastructure
• Access control and user management are managed via the Nupano Cloud with no direct user access and user management on the Nupano Runtime on premise
• Apps are executed in containers on the Nupano Runtime
To bridge the IT and OT worlds, Nupano focuses on three main areas: simplifying access to IT technology, integrating IT services into the machine through transparent release management of software, and maintenance throughout the integrated lifecycle management of the installed base.
Because it is cloud-based, Nupano can be accessed from any device, including mobile devices like tablets, to manage both apps and machines. Each machine connected to Nupano has a digital twin in the cloud to protect the OEM’s projects. In other words, the equipment’s operating functions do not reside solely on the machines’ controllers. Nupano applications are transferred to an industrial PC on the machine via the digital twin. From there, the applications operate using Nupano Runtime.
Nupano Runtime is hardware-independent and runs on almost any industrial PC or on IT servers. According to Lenze, customer feedback shows that machine builders want IT to be separated from OT. There are two main reasons for this: First, separating the IT services from the OT (i.e. the PLC applications) allows the machine builder to scale from small to large PLCs while keeping the IT application independent. On the other hand, IT services can be added to existing machines on site in the so-called “brownfield.” Examples here would be data extraction and analytics.
“The key to [OEM] success lies in leveraging the innovation potential of information technology at the machine and plant level because, in the future, differentiation from competition will mainly be achieved through digital services linked to the machines,” said Annekatrin Konermann, Lenze’s product manager of Nupano.
By using IT standards, OEMs can work with any preferred IT service. “Nupano allows you to maintain ownership of these services,” said Werner Paulin, head of new automation technology at Lenze. “Currently, the competitive advantage of your machine is determined by its ability to control the process, to be precise, and to be fast. But in the future, IT services will contribute to that competitive advantage.”
After developing custom IT services that fit a company’s needs, those services must be integrated into the machine, which requires working in parallel with various teams, including IT service to develop app versions, electrical engineering and mechanical engineering to download and install them, and process engineering to feed back to IT service the performance of the apps.
Nupano can then update the hardware with new functionality through the installation of new or updated apps.
“On a machine, it is important to know which version is installed in order to update it,” said Paulin. “Every version of your IT services is handled with [Nupano’s] lifecycle management, which means you can control which version is released or which one is discontinued. When you want to update a machine, the transparent update service of Nupano allows you to specifically pick a machine, find out what it has installed, and update specific versions.”
Exisiting apps can be uploaded to the Nupano platform using the open IT standards. Applications can be tested together on the platform, and a release workflow and lifecycle maintenance strategy can be created for the customer’s entire machine inventory. Once an OEM’s applications are programmed using common standards, they can be tested and transferred to Nupano, which also provides access to more than 100,000 programs on Docker Hub.
Easily share this article with your peers: oemgo.to/nupano
Building off the success of PACK EXPO East as a Northeast regional trade show powerhouse, PMMI turns its eyes to the manufacturing-rich Southeast U.S., debuting PACK EXPO Southeast, March 10-12, 2025, at the Georgia World Congress Center in Atlanta. Located within driving distance of key manufacturing cities and a mere two-hour fl ight from 80% of the U.S. population, the new regional opportunity for the packaging and processing industry will harness all the power of the PACK EXPO portfolio of trade shows.
“This show represents a big opportunity to bring the industry together in a region of the country that is not currently served by a trade show focused on packaging and processing,” said Jim Pittas, president and CEO of PMMI. “PACK EXPO Southeast in Atlanta is the perfect location to focus on targeted opportunities in this robust market, which is home to some of the top manufacturing industries in the region.”
The sixth show in PACK EXPO’s growing catalog will offer a depth and breadth seen by no other Southeast regional events, offering solutions for over 40 vertical markets to address the packaging and processing needs of area manufacturers.
Exhibitors seeking exposure to new customers and key decision-makers can request to be notified when space sales open at packexposoutheast.com or by contacting Wendy Moore, PMMI trade show sales manager, at 571-612-3185 or sales@pmmi.org.
To help women identify opportunities, recognize obstacles, and navigate a career in manufacturing, the Packaging & Processing Women’s Leadership Network (PPWLN), and OpX Leadership Network, teamed up to deliver the new digital work product: Connect, Share, Inspire: Voices of Women in Packaging and Processing.
The annual Institute of Packaging Professionals (IoPP) 2022 Salary Survey results, a portion of which is included in the new work product, reveal a continued gender wage gap, pointing out the need to help women succeed in manufacturing careers. The new resource highlights five core skills needed for success: business acumen, negotiation, communication, emotional intelligence, and networking. Insights from subject-matter experts and perspectives from influential
women leaders in the industry are included.
“As a manufacturing professional with 20-plus years of experience, I’ve sometimes felt that I didn’t have control over my career path,” says Lisa Rathburn, vice president of engineering for T. Marzetti, who is also an executive council member of both the OpX Leadership Network and PPWLN. “I wanted to contribute to this project because I understand how difficult the road can be. Having information and an accessible network of like-minded people can make a big difference in an individual’s overall experience.”
The collaborative work of PPWLN, which serves to recruit, retain, and advance women’s careers in packaging and processing, and the OpX Leadership Network, combines cross-functional knowledge and information with a single goal in mind—to show how instrumental people are to the manufacturing and packaging process, and how meaningful this journey is for the women who are here today—and who have yet to come aboard.
The Connect, Share, Inspire: Voices of Women in Packaging and Processing work product, as well as other industry solutions, are available for free download at: https://www.opxleadershipnetwork.org.
Anatole Konstantin’s fascination with machines 50 years ago has evolved into a successful shrink sleeve labeling and tamper evident banding OEM business that uses total vertical integration to control the quality, performance, and time-to-delivery of every system.
If you want to hear an inspiring story about an immigrant living out the American dream, look no further than Anatole Konstantin, the founder of PDC International Corp. Originally from what is now Ukraine, he arrived in the United States after World War II with only the clothes on his back and a degree from the Technical University of Munich in his pocket. He worked his way through various jobs and eventually earned a graduate degree from Columbia University.
Konstantin’s fascination with machines resulted in the start of his company in 1968, called Product Design Corporation (PDC), which offered services ranging from consumer product development to machine design. Within one year, Konstantin moved the growing company out of his home and into a 400 square foot space in an industrial building in Norwalk, CT.
Soon, machine design and automation became the company’s primary focus and has since evolved into the company it is today. PDC is now located in a 27,000 square foot facility in Norwalk with over 60 employees and specializes in shrink sleeve labeling machinery, tamper evident banding machinery, and shrink tunnels for the food, beverage, pharma, dairy, and personal care industries.
Anatole, now 94 years old, has since retired, and the company is currently led by his son, Neal Konstantin, who is the CEO, as well as Gary Tantimonico, President of PDC.
Neal Konstantin joined PDC in the early 1980s with a college degree in archeology and history—so he’s not exactly an automation engineer, but he does bring
a unique point of view to the business. “Archeology gives perspective on time horizons and keeping things in context, and the sense of history gives good perspective on business as well,” he explains. “It gives you longer term views and separates the immediate fires that need to be put out from more significant long term topics.”
His ability to evaluate a situation for short and long term impact was an important viewpoint when the next generation Konstantin started working at PDC, because it was right at the time that the Tylenol incident in Chicago occurred—when someone poisoned the bottles of pain medicine. Suddenly, there was high demand for tamper evident banding and sleeving machinery. And PDC answered the call.
“We are total vertically integrated as a company, from engineering to machining, sheet metal, welding, and fabrication,” says Tantimonico. PDC does not rely upon subcontractors, so the company controls every aspect of the manufacturing process and can respond quickly in every circumstance. “Companies come to us for our deep knowledge of the science of this technology. This includes longstanding relationships with major material raw stock and resin suppliers and label converters, an understanding of film chemistry and performance, as well as the printing process. We collaborate with customers to ensure that container designs are shrink-friendly and compatible with required line speeds to produce a product that meets our customers’ expectations.”
Konstantin echoes Tantimonico’s statement, pointing to the history of the organization and its strong automation and engineering background which allows PDC to deliver systems that other OEMs often can’t. “Our automation background enables us to do challenging applications that many of our competitors can’t consider. We are able to design peripheral systems and integrate them.” he says. “And, we do business the old-fashioned way,
ing up the lathe.
straight-forward and customer-focused. It means we’ve invested in technical staff, machine tools, and our personnel. It requires an investment over the years that most companies just don’t make anymore.”
All PDC machines are ruggedly designed for durability, reliability, safety, and ease of maintenance with quick, tool-less changeover of parts. Over the years, PDC machines have been built for higher speeds, zero downtime during film changeovers, and more challenging applications. Recent developments include steam shrink tunnels with integrated boilers, and zero-downtime unwind stands for use with PDC or other brands of sleevers.
R&D is often tied to custom projects. For example, the PDC StackAlign Multipacker, introduced in 2021, allows a number of individual units to be grouped, or multipacked, by stacking and shrink sleeving them. It takes the individual products from an infeed conveyor, counts, and stacks them, placing them onto fixed pedestals on a servocontrolled indexing conveyor. The product stacks are then centered and aligned prior to
the sleeve application, while a dual zone hot air tunnel provides a smooth tightly-fitting finish. “This required heavy development a couple of years ago, and we’ve sold many machines since that time,” Konstantin says, noting that the PDC team listens carefully to clients’ requests to develop machines that meet their specific needs.
The most recent customer requests revolve around sustainability and the need for new films. PDC collaborates with resin and film suppliers, co-developing substrates by testing and vetting new films in the PDC Shrink Lab.
“All films have different performance fingerprints. They shrink at different temperatures and rates. Some are quite different than traditional films, so shrink systems have to be more precise and deliver heat in just the right places on a given package to produce a perfectly sleeved product for the consumer,” Konstantin explains.
For customers rolling out new product and label designs, PDC Shrink Lab conducts free shrink sleeve prototyping tests, and provides videos of the product running through the shrink tunnels. This test helps determine the required label specifications, including shrink percentage and material selection, all of which are critical for successful projects.
Konstantin notes that some PDC machines can handle very small diameters at high speeds, which is a perfect fit for the pharmaceutical industry, in particular. But perhaps the biggest value-add PDC brings to the table is in its cutting systems, which have been designed in-house and will last for months between replacement. Most other blades are spinning knives, which dull quickly and require them to be changed every few weeks or even days. “Our main
benefits are vertical integration, technical know-how, and these cutting systems, which are amazing and will last for months,” he says. This results in less downtime and greater productivity.
Efficiency flows through to the factory, as well. When PDC doubled the size of its facility 10 years ago, they brought in lean experts to create an environment that minimized the movement of materials, parts, and people. So, even with more space, they consolidated operations to less square footage that resulted in more efficient operations. This has allowed the company to deliver a Just-In-Time manufacturing approach in the machine shop whereby raw materials are purchased and turned into finished products “just in time” to meet customer demands.
Of course, PDC is not immune to the ongoing industry issues that impact all OEMs, such as the skills shortage. But, an optimistic attitude, a family-oriented company culture, and an investment in employees helps with retention while drawing more people into the organization. Tantimonico, who was appointed president in January of 2020, has been with the company for over 30 years. And the average employee tenure is in the 15-to-20-year range.
The company’s work with Vistage, an executive training
•Energy
•High
and development program, has also made a big difference in the leadership, Konstantin says. Vistage includes a peer group that meets once a month to share key information and goals within a circle of business confidants and advisors. “We’ve invested in memberships for six of our employees and I’ve been in a Vistage group for over 20 years. It is a fabulous organization for the ongoing education of executives and key personnel.”
Bringing new folks into the fold is also important. Many new employees were found through referrals, and recently, PDC started an internship program working with local trade schools and colleges. “We have a great new group of energetic and excited employees who are new to the industry but are going to be great contributors and leaders as we go forward,” says Konstantin. “The next generation of employees and leaders will provide that infusion of technology and innovation we’ll need to continue to stay at the forefront of our industry.”
Four years ago, PDC celebrated its 50th anniversary. In a video commemorating the company’s five decades, founder Anatole Konstantin—who was also celebrating his 90th birthday at the time—explained his motivation for starting the company: “Fifty years ago, when I started this company, I was hoping I would be able to feed my family, that was my vision at that time. I couldn’t see this far.”
But, oh, how far this company has come. Now, on to the next 50 years.
To learn more about Anatole Konstantin’s life, read his memoirs: A Red Boyhood – Growing Up Under Stalin, and Through the Eyes of an Immigrant.
Easily share this article with your peers: oemgo.to/pdcinternational
Headquarters/manufacturing
Executive team: Bill Chesterson (CEO), Mike DeRosier (Business Development/ Safety Manager)
Number
Range
Advent Design was ahead of the automation curve, serving as a partner for companies seeking to automate operations as far back as the early 1980s. With automation exploding to suit the needs of consumers clamoring for product and an alternative solution to the workforce crisis, Advent has seen its business expand to include customer automation, stop-time analysis, and machine safety solutions. OEM magazine spoke with Mike DeRosier, Business Development/Safety Manager, to offer Advent Design a chance to share what makes them unique among PMMI Members. Can you provide a brief history of your company?
Advent Design was established in 1984 with a handful of people in a rented house in Malden, Massachusetts. From these humble beginnings, we quickly grew to a few thousand square feet in a historic mill in Bristol, Pennsylvania, in 1986. Today, in the same location in Bristol, we have grown and increased our space to utilize more of the Grundy Building, allowing us to service various diverse companies in a global marketplace. With a team of extremely talented engineers, project managers, technicians, machinists, and production specialists, Advent Design provides manufacturing and engineering support to companies in virtually every manufacturing sector imaginable.
What went into the decision to join PMMI?
In reviewing PMMI, Advent Design was confident we could be a total solution provider to the PMMI community. Our focus is on helping customers excel and optimizing
their ROI with automation. It is not an all-or-nothing solution. In doing this, many equipment manufacturers fit a niche perfectly. Advent Design can help customers match the custom solution we provide with other equipment manufacturers specializing in a specific process.
What’s your approach to new product development? How do you come up with ideas for new machines and market-test them?
As Advent Design works with custom solutions, the challenge is brought to us by a customer. We work closely with a customer and their request to automate. Part of being a partner is helping them determine if automation is the best solution for their production or process, what the ROI would be and whether it makes sense for full automation or semiautomatic. This is also where we are different. We are not designing and building to a standard platform or targeting a specific industry. Most of the solutions we develop, design, build and install are customer-focused to their operation and needs.
How have your services broadened over the years?
Advent Design has broadened our services to fit customers’ needs with custom automation, engineering, machine safety, and robotic integration. With our experience and group of engineers and technicians, we also
diversified our services. Becoming an authorized system integrator for some robot manufacturers provides a complete solution for a customer with full support. There are times when customers have limited resources and need an engineering consultant. Advent Design can be their external resource to help manage an integration project and provide options and recommendations for machine suppliers to fit their integrated production line goals. Advent Design has expanded into machine safety by focusing on where customers need help with solutions, as many companies now focus on machine safety and being OSHA and ANSI-compliant. You see more risk assessments performed than in the past.
One of the largest challenges is finding resources that can evaluate an existing machine, review the risk assessment and be able to design, fabricate, and install a customized guarding solution for those existing machines. Along with machine safety, Advent Design recognized another area with which most companies have issues: stop-time analysis. Advent Design partnered up with a company from Germany called HHB Electronic. They design and manufacture a highquality stop-time analyzer.
What is your standard automation platform?
While we work hard to meet cus-
tomer requirements, we do have a few standard options that we like to utilize
• Machine control (PLC / PAC): Beckhoff, Allen-Bradley, Yaskawa
• Servos & motion control: Yaskawa, Allen-Bradley
• Machine safety platform: Beckhoff, Allen-Bradley, Schmersal, Euchner, Banner, KNew Member Profilence
Having diversification in projects, we always have something new to do. There is a new or different challenge, leading to our employees always learning something, including staying up to date with the latest technologies. Also, having stability and longevity with employees, you always have a team to bounce ideas off of. There is a great team atmosphere with Advent Design.
How do you balance standardized machine configurations with those requiring customization?
As most of what we do is custom solutions, there are still ways we try to standardize. One of those ways is having all of our control engineers program in the same format with the same structure. These provide flexibility in the support after the sales. Customers may want to change something about the operation of a machine. We are not locked into the controls engineer that did the initial program. Any of our controls engineers can review the code and jump in to make the requested changes.
Are you incorporating lean manufacturing? If so, please give some examples.
We incorporate lean manufacturing, primarily in finding the best solution in the machine design for loading raw materials and removing the finished product. This also becomes important in an integrated multiplemachine line solution. Sometimes, lean becomes a better solution for a
customer versus full automation. We may identify with a customer that the ROI on automation may not entirely be there yet based on their production volumes, but a solution that we can offer is how to make their process more lean.
What’s your process for handling a customer’s initial inquiry and needs assessment?
Even though quoting sounds quick and straightforward, there is a reasonable amount of time put into it with custom solutions.
1. Discussion—Review with the customer the needs, scope documents, pictures, videos, what they are looking for, type of automation, etc.
2. Pricing Needs—Determine if it is a budgetary number the customer needs to get funding approval or if they need a firm fixed price to place an order against.
3. Timeline—It is crucial to establish a timeline, not just for how long it takes for equipment to be designed and built but from the start of the quoting process. Establish when a quote is needed, the goal for placing an order, when the customer is looking for the machine to be in production, etc.
4. Quote—There may be discussions in between with the customer with concept review and developing some additional questions on the scope. In our firm quote, we provide a description of what we envision the automation to be and a detailed budget of where our pricing was developed.
What influences a new machine’s turnaround/delivery time, and what happens during this process?
As with all companies, the two main factors are backlog and availability of parts. With a reduction in workforce and an even greater desire to automate, it creates a backlog of projects that customers need, which is addressed in the quote phases by providing realistic delivery expectations. Also, logistics and getting standard off-the-shelf components have made it more difficult for custom machine builders to get some standard parts. Sometimes it is an adjustment in the quote stage, such as setting up an invoicing milestone based on receipt of long lead items so they can be ordered sooner than typically would have been done in the past. Also, we have more flexibility in looking at alternative solutions as we may not be locked into a previously approved design.
What’s the process for factory acceptance tests?
The project manager develops a factory acceptance test document as to what is seen as the required testing, rate, faults, performance, etc., based on the scope of the work document. This is sent to our customer before arrival for review and agreement. When the customer visits our facility, the project manager and engineering team work through any runoff and testing as designated by the agreed testing document.
How do you handle field service and training? Do you have dedicated training personnel, or do service technicians typically conduct training?
It depends on both the complexity of the machine as well as the needs and capabilities of the customer. We have different situations where it could be an engineer or a technician. Primarily, the lead controls engineer on the project does the training, as most of the training tends to deal with the controls and programming, with assistance from a mechanical engineer as needed.
What challenges do you foresee affecting your firm and all companies in this industry?
The biggest challenge, as it has been for many years, is finding the right people for an organization. Companies are looking for people who are not only qualified but also reliable, looking to work with a team and can provide valuable contributions to the team and themselves.
Automation and technology in automation are going to continue to grow. We have all heard of growing pains. It may be more challenging to get the parts that are needed as a result. However, it is essential for companies looking for automation to ensure they partner with a machine builder they can trust and will continue to be a resource for them. Custom solutions may be viewed as once it is built, it is done. Advent Design approaches every project and every customer as a partner and forms a relationship. A machine may be “one and done,” but a good relationship lasts a long time.
Easily share this article with your peers: oemgo.to/adventdesign
At PMMI, we know staying ahead of your customers’ needs and on top of emerging technologies is critical to your business. An easy way to do that is to utilize PMMI member resources like our industry-leading market research and trend reports, personalized customer research, and media brands—like Packaging World, ProFood World, and OEM—that connect members to the latest solutions, trends, and innovations year-round.
Is your company a PMMI member? Take advantage of the resources available to every employee in your company.
pmmi.org
PMMI is your answer, connecting you to customers 365 days of the year.
The Anheuser-Busch facility in St. Louis serves as the hub of innovation for over 30 brands— the most popular being Budweiser and Michelob Ultra. Multiple lines are running at high speed on the packaging floor. As an example, one can line can package 1,950 12 ounce cans per minute and 1,650 16 ounce cans per minute.
With so much activity, operators have to be familiar with equipment and procedures. Unfortunately, the beverage manufacturer is not only dealing with the skills shortage that is impacting the entire industry, but it is also ready to lose about 40% of its workforce that is ready to retire. That means novice operators will be running machines and trying to interpret some of the antiquated HMIs that serve as the interface to equipment that has been in place for decades.
Fearful for what the future holds for the packaging floor, Ken VonderHaar, global director of the AnheuserBusch Can Division, has been going back to the drawing board in some cases, and asking OEMs to design machines that are much easier to learn and to use.
“Essentially, we’re asking for simplicity,” he says. “We would like for all of the complexity to be under the hood [of the machine], and we would like an operator interface that’s very simple, that’s easy to understand, and that enables our younger employees to interface with some type of video
screen. We also look for set-up procedures that are built into the operator screen. And we’d love it if [OEMs] could help train our operators.”
Lisa Rathburn, vice president of engineering at food manufacturer T. Marzetti, agrees that training and easy interfaces can help close the skills gap. “We walk through the interfaces during design reviews to ensure that terminology matches what is used by our teams on the plant floor,” she says. “We are focused on standardizing where possible to simplify the diversity of knowledge needed. And we are also favoring changeover parts, rail adjustment, etc., that have clear indicators or push button operations to reduce human error and manual adjustments.”
OEMs are listening to customers’ requests and delivering intuitive HMIs, visual learning components, as well as offering augmented reality (AR), and remote management and diagnostic technologies in order to offload most of the maintenance issues.
The goal is to avoid a big problem when there’s an easy fix.
“We can solve 90% of the issues remotely and within an hour,” says Robert Mize, a technical support representative at Pearson Packaging Systems, a provider of end-of-line automated packaging systems.
Pearson’s remote service offering is free and available 24/7. They use several technologies to connect
with customers and help them get back up and running quickly. The simplest form is Vuforia augmented reality technology from PTC, which allows the technician to make annotations on a shared screen. It’s a simple process that starts by sending a code to a phone with the Vuforia app and pulling up the software that allows operators and technicians to share the same screen. It does not require a remote connection to the machine and is especially useful when opera-
tors have language barriers or don’t know maintenance terminology. “It’s one of the first things we mobilize. We can see the machine and we can annotate in real time,” says Mize.
The next level of support is given via an Ewon router that connects to the PLC via a secure VPN tunnel. This router provides the technical support team the ability to see the state of the machine, including PLC and sensor data, as well as make corrections to the code if necessary. “Back in 2019, we made the decision that we were going to equip any plant or industrial network [our machines] are in with the ability to remote connect,” says Brian Patrick, Pearson’s vice president of engineering. “It’s allowed us to make further investments, not only just putting remote connection on machines, but also being able to send things out quickly from a support standpoint.”
In certain cases, Pearson also provides cameras that can be set up around the machine so that when a remote session takes place, technical support can see what the customer is seeing. This is especially helpful when a situation has to be assessed over a period of time.
These types of services are proving to be vital given the current state of the workforce. For example, during a routine customer service call to Pearson tech support, Mize was answering questions about a machine while trying to gauge the operator’s familiarity with the technology. That’s when he learned that the caller had actually been a cashier at the warehouse retail site just an hour before being reassigned to the machine operator role.
“Even the tone of the callers is totally different than it was a few years ago,” Mize says. “There’s a sense of urgency. It’s like they’ve been dropped off in the middle of the ocean and they have to learn to swim for themselves.”
The urgency is heightened because every second counts. “Our customers make money when they get boxes out the door,” says Paul Wolf, director of customer service at R.A. Jones, a provider of primary and secondary packaging machinery. “So how do you get a new hire to operate a line in a day?” One solution, Wolf says, is a two
minute training video.
The company has identified several of the most common faults on its machines and are now scripting out in a short, documentary-like form, videos on how to fix them. “A lot of documentation gets lost, but with a video of how to fix it, we can get an operator up to speed in record time,” Wolf says, noting they are also embedding videos in HMIs and online manuals, which can be customized to customer needs.
Other OEMs are aiding the untrained operator by developing somewhat self-sufficient machines.
At PACK EXPO International in October, BellatRx introduced a new labeling machine that includes a piece of equipment that takes the measurements of a bottle, which when entered into the HMI, automatically creates a recipe
in which all of the conveyors, label dispensing, wrap, and metering wheel speeds are automatically set and synchronized without further operator intervention. This gets the operator to 90% of where the set up needs to be just by measuring the bottle. “They don’t need to understand dispense speed or any of that because we understand it, and we write in the code and algorithms to calculate the speeds,” explains BellatRx president and CEO Alan Shuhaibar. “All you need to do is measure the bottle and enter the dimensions.”
The second part of this is the physical setup. A short animation or video serves as a step-by-step guide in the HMI on how to get the BellatRx labeler up and running. The video is coupled with an LED light strip installed along the length of the machine. When setup is required to be done on a certain assembly, the section of the LED strip in front of that assembly will light up to draw the operator’s attention to that point. The mechanical adjustments include electronic feedback, which turns the LED light green when it is in the correct setpoint or red when it is not. On the HMI, the operator cannot progress to the next screen unless all setpoints for that assembly are green.
In the past, the OEM’s expectation was that the operator knew how to set up the machines. But that doesn’t exist anymore. In addition, people expect the same user-friendly interface as an iPhone. “We are trying to take that mindset and put it into the machines. You shouldn’t need a PhD to run a labeler,” Shuhaibar says.
In its own factories, industrial control supplier Bosch Rexroth does something similar, which it calls the ActiveAssist assistance system that guides the operator through the assembly process. It provides instructions projected on a workstation with a vision system that confirms when something is done correctly.
Separately, the maker of industrial control and motion technology has reinvented its automation approach over the last two years with its software-driven ctrlX Automation platform. Going back to the drawing board, the company erased the traditional boundaries between machine control systems, IT, and Internet of Things (IoT), creating a flexible and scalable platform based on the Linux real-time operating system, open standards, comprehensive IoT connectivity, with web-based engineering.
Using the Blockly visual programming language, the platform provides a drag-and-drop function block that builds sequentially. “So now, instead of memorizing dozens of lines of code, you just have to understand that this block means a kinematic move sequence. This makes it easy to use, and to train someone to use,” explains Brad Klippstein, product manager for smart mechatronics at Bosch Rexroth. “In under five minutes we can teach you how to use this interface and program your process.”
In addition, Bosch is helping out OEMs and customers
The Ewon router provides a secure remote connection to Pearson machines, allowing tech support to see the state of the PLC and more.
alike by providing them with its LinSelect online tool for use in the designing and commissioning of machines. “It allows you to input the parameters of whatever you are trying to do.” If you are trying to move boxes from point a to point b, for example, just input the distance needs, weight of the box, and a few other details pertinent to the process. “Our system sizes and selects the mechanical, electrical, and software components that fit together based on your application.”
Of course, the easiest thing for OEMs to do to help their customers is to fully manage the machines onsite. However, the thought of allowing a third party to remotely control a machine is completely off-limits. Or is it?
Desperate times call for desperate measures. Given the current circumstances, it’s becoming acceptable to relinquish control to the experts. “We always have a plan b with the remote connection of a machine,” says Pearson’s Patrick. “We have the ability to take over the machine, so if an operator is not comfortable doing something, they can grant us access to use the HMI remotely.”
To be clear, this scenario requires specific conditions with the machine in a certain state in order for it to work, Patrick notes, emphasizing, “there is no opportunity to put someone in danger.”
But, even this one small step for remote control of machines is a big deal, and something the manufacturers could ultimately be asking for.
“It’s always a challenge with our IT team to remote into anything in the brewery,” says Anheuser-Busch’s VonderHaar. “And that’s just because of the risk. But I think the trend is there, and we have to figure out how to do that. And at the end of the day, yes, we want to do that. We need to figure out how to do that safely and try to do it in a manner that doesn’t put our operations at risk.”
Easily share this article with your peers: oemgo.to/skillsgap2022
The winners of the 2022 Technology Excellence Awards were announced in October at PACK EXPO International in Chicago in the categories of Food/ Beverage, General Packaging & Processing, Personal Care/ Pharma, and Sustainability. What started as months of reviewing 60 qualified entries by a panel of PMMI Media Group editors and industry professionals, culminated in three days of onsite voting by show attendees who ultimately decided which companies showcased the most innovative materials and technologies at the show.
“Congratulations to this year’s winners for their outstanding materials and technologies,” said Laura Thompson, vice president of trade shows at PMMI, The Association for Packaging and Processing Technologies, which owns and produces PACK EXPO. “The abundance of quality entries received this year made the selection process quite challenging. We are proud to celebrate and showcase the best of the industry, and encouraged to see that the Technology Excellence Awards are attracting the top innovations.”
Here’s a look at this year’s four winners:
The Proxima tethered closure provides a solution to enhance the recyclability of the closure while still offering consumers a convenient and comfortable drinking experience for cold fill and aseptic applications, including still water and functional drink.
The design of the closure features a special feature on
the tamper-evident band that means once the band has been broken, the closure remains attached. When the bottle is opened for drinking or pouring, the closure is placed adjacent to the neck at a wide angle, thus ensuring that consumer convenience in not compromised in any way but enabling easy reclosing of the bottle.
This solution meets two important sustainability benefits. Because the closure remains with the bottle and is not thrown away at any time, recycling rates for the closures can be greatly increased. Equally important, keeping the closure on the bottle avoids the danger of littering and unnecessary plastic waste when closures are carelessly or thoughtlessly discarded.
IMA North America Inc.—IMA Ilapak Vegatronic 6400 Hygiene, accessibility, and efficiency are the trademarks of the IMA Ilapak Vegatronic 6400 continuous motion vertical bagging machine developed to meet the specific needs of highly demanding industries in terms of sanitary design, accessibility, fast changeover, and OEE. Full open-frame design and IP66 through IP69K rated electrical components are some of the features of this cutting-edge machine.
Fully AISI 304 film reel carriage, rollers and bearings, sloped cabinet tops and splicing table, inclined forming tube support, EHEDG compliant electric panel are the main features that limit the areas where product can accumulate and harbor bacteria, making this bagger ideal for harsh environments where hygiene and sanitation are primary requirements.
Accessibility is granted by fully openable front and side doors to make sure every single component of the machine can be reached by operators or maintenance people as fast as possible with the lowest downtime.
Efficiency on the Vegatronic 6400 has been enhanced in several ways. Improved usability of the HMI by introducing auto-adaptive and multiclient features to make the setup easy and fast. The splicing table is vacuum assisted, making it very quick to operate. The forming tube is mounted on a swivel arm for easy changeover. And, the film reel shaft is pneumatically activated in a variety of executions to meet the customer requirements, i.e single cantilevered or drop-in, dual reel holder, or automatic splicing system to further enhance efficiency.
Eurotrol—CueSee Mix/Dual Chambered Device for storage of liquids/ powdered/lyophilized components
CueSee Mix is a unique, patented packaging form that is revolutionizing the In Vitro Diagnostics (IVD), pharmaceutical, and cosmetic markets. The innovative, dual chambered device keeps various fractions separated, preventing reactions between components of the desired matrix. A simple twisting motion allows the previous separated components to combine. After mixing via a “static stirrer” the product is ready to use by either the integrated dropper bottle or aspirating into a syringe. CueSee Mix eliminations the need for manual combination or dilution of product components while providing added ease of use and increased safety.
Graphic Packaging International—ClipCombo
The ClipCombo machinery solution is the latest machinery innovation from Graphic Packaging. Delivering the
ability to run two different paper-based multipack styles on the same machine, the ClipCombo solution uniquely allows rapid changeovers and delivers high speeds no matter what is running.
The ClipCombo range offers machinery solutions for multiple combinations, including:
• KeelClip and EnviroClip paper-based clips for can multipacks
• GripClip and EnviroClip paper-based clips for can multipacks
• Cap-It and EnviroClip paper-based clips for PET bottle multipacks
To learn more about the 2022 winners and finalists go to: oemgo.to/technologyawards2022
Sustainability is the new watchword for a huge and growing band of consumers, according to a June 2022 report from PMMI titled “Achieving Packaging Sustainability.” The ongoing green movement presents an opportunity for businesses facing increasing competitive and economic pressures to gain value in competitive advantage as they respond to environmental concerns and the pressures of resource scarcity, population growth, and higher and more varied consumer expectations.
Perhaps unfairly, the packaging industry is seen as one of the worst environmental offenders, the PMMI report states. At a recent Top to Top event held in Florida, PMMI hosted roundtables with participants from across the packaging value chain. Participants indicated that it’s not just CPGs that should be implementing sustainability strategies. OEMs also have a crucial part to play in energy savings. In fact, a current hot topic in Europe is a carbon footprint rating for each new machine.
Download the 2022 report, “Achieving Packaging Sustainability,” from PMMI. h ps://www.pmmi.org/report/2022-achievingpackaging-sustainability
Overall, the message from participants at the Top to Top meeting is that it’s all about the collaboration between CPGs, material suppliers, and OEMs as they plan ahead for the next generation of packaging materials.
However, while consumers continue to seek sustainable products, they may not be willing to pay the price, according to a recent report from market research firm AMC Global and OpinionRoute, a company that provides insights into process management. These survey results say that many consumers want sustainably produced and sourced products, but price remains the top consideration when making purchasing decisions. According to AMC Global, consumers believe these products are more expensive than their mainstream counterparts, and recent inflation and price increases are making affordability a key concern. In addition, a high percentage of respondents say it is hard to tell which brands are sustainable and which are not.
While 43% of people believe it is worth it to pay more for sustainable products, 66% say they can’t afford to do so due to recent price increases across the board.
While consumers often look to retailers and product packaging to guide them on sustainability, the winners
of ProFood World’s annual Sustainability Excellence in Manufacturing Awards are focused on reducing greenhouse gas emissions, electricity, and water, as well as food waste and materials management. Following are the six 2021 Program and Project Category winners.
first place | program category
The Oakdale, Calif., Conagra Brands facility makes Hunt’s and Ro-Tel brands, and other food products. Over the past year, the facility’s cross-functional team made excellent progress in reducing food waste. The team implemented a comprehensive plan and problem-solving program throughout 2021 to eliminate ingredient loss points for both jalapeños and tomatoes. The program addressed three causes of jalapeño waste (spoiled ingredients, batch planning, and fill controls) and two processes for tomato waste (peelers and fillers). As a result, the plant utilized 650,000 lb of jalapeño and 13.8 million lb of tomato raw ingredients compared to 2020, which reduced the site’s solid waste footprint by about 10%.
“By manufacturing food ingredients more efficiently, we are using utilities more efficiently,” says Kate Pitschka, director of supply chain sustainability, pointing to Scope 1 and 2 greenhouse gas (GHG) emissions. “We are also moving a significant portion of the site’s food waste up in the recovery hierarchy from animal feed and compost.”
The plant is located in a high water-risk region, and eliminating some of the organic load being sent to wastewater operations is reducing some stress on the region’s water cycle. By eliminating food waste, the facility is reducing the amount of Scope 3 GHG emissions (EPA WARM and Biogenic) that the food waste would create downstream.
Teams were established during March to May 2021, project scopes were defined within one to two months, and specific projects were implemented between July and October 2021, resulting in a 4% jalapeño yield improvement and a 1.8% tomato yield improvement.
“Savings were strictly through better use of available equipment resources and process improvements, with limited costs,” explains Pitschka.
The winners of ProFood World’s annual Sustainability Excellence in Manufacturing Awards are focused on reducing greenhouse gas emissions, electricity, and water, as well as food waste and materials management.Joyce
The Oakdale cross-functional team delivered a $471,000 jalapeño yield loss reduction (spoiled ingredients, under net weight rejections, and overfill) and a $730,000 tomato yield loss reduction. These calculations do not include the energy cost savings associated with treating the food waste going to wastewater, nor the hauling costs of the solid waste.
Committed to creating a sustainable future while inspiring joy with wholesome foods, Bob’s Red Mill Natural Products fosters nourishing a healthy planet. One of the company’s main goals is reducing food loss from farm to fork through wasted food rescue. “By rescuing unavoidable scrap, we are avoiding climate emissions that would occur downstream,” says Julia Person, sustainability manager for Bob’s Red Mill. “We donate food to local non-profits, as well as send inedible product to animal feed. Another way we are furthering this work is by joining the Pacific Coast Food Waste Commitment to collectively work with other food businesses to cut food waste in half by 2030.”
The Milwaukie, Ore.-based company’s materials management focus extends beyond food waste to refuse, reduce, reuse, and recycle the maximum possible material flow at the plant, with a goal to reach zero waste. At Bob’s Red Mill, wasted food rescue and materials management programs have helped reduce operations costs for the employee-owned company and have a positive impact, both environmentally and socially, in the local community.
“In 2021, we kept over 385,000 lb of edible food from going to waste, upcycled 2,293 tons as animal feed instead of landfill or compost waste, and recycled more than 1,600 tons of materials such as cardboard, plastic, metal, and wood,” states Person. “Our food donations help provide healthy, wholesome food to those in need in our surrounding community.” Through donations to the Oregon Food Bank network, Bob’s Red Mill provided 161,521 meals to those experiencing hunger in 2021. It donated rescued food to four main organizations in the Portland, Ore., metro area—Oregon Food Bank, The Canby Center, Sunshine Division, and Gleaners of Clackamas County.
Conagra Brands’ Troy, Ohio, team implemented a comprehensive continuous improvement program on the site’s bakery line when running pizza, and have set up new
process and operating standards, organization, and line planning. Ongoing efforts are expected to deliver more than $325,000 in cost savings by reducing yield loss by 13.4% and eliminating 267,000 lb of meat, cheese, and breading waste.
“Every opportunity to manufacture food more efficiently will allow us to use water and energy resources [Scope 1 and 2 GHG] more efficiently,” says Kate Pitschka, director of supply chain sustainability. “However, they are not directly quantified in this submission. Also, by eliminating food waste, we reduce the amount of Scope 3 GHG emissions [EPA WARM] that the food waste would create downstream.”
Meat toppings process and planning analysis took six months and concluded in August 2021; cheese process and planning improvements took five months and concluded in November 2021; extra toppings and cheese reuse took one month to implement in September 2021; and over a two-month period, employees’ continuous improvement skills were developed, beginning in November 2021.
The reduction of the weight average per case is forecasted to deliver annualized savings of more than $325,000.
The main objective of the project at Conagra Brands’ Irapuato, Mexico, plant was the reduction of water consumption. In this project, two specific situations were considered:
• Identification of water leaks and improvements in the sweet corn process and canning process equipment.
• Completing sanitation more efficiently on various lines to reduce the consumption of cleaning chemicals, resulting in greater production line availability. Also, some of the sweet corn equipment required a redesign to eliminate or make more efficient use of water.
Reducing water consumption is a benefit for the entire community since the plant is located in an area with limited water availability. By improving the operating conditions of its wastewater treatment facility and discharge parameters, the water can be reused for farmland irrigation.
“The corn/cannery production improvements were completed over seven months, finishing in September 2022, and the sanitation improvements were completed from April 2021 to May 2021,” says Fernando Alcántar Gómez, EHS manager. “Both projects resulted in an 8% reduction in water use per production year over
Conagra facility saves nearly 9 million gallons of waterConagra Brands - Irapuato, Mexico Smithfield Food’s - Milan, Mo. Conagra Brands - Marshall, Mo.
year, with ROI in less than a month.”
The project returned more than 10 times its cost, saved nearly 9 million gallons of water, and reduced chemical usage by 2,680 gal.
second place | project category
Early in 2021, Smithfield Foods’ Milan, Mo., plant started sending out hams for further processing, transporting them in cardboard combos. The facility quickly realized it could save money and reduce cardboard usage by using reusable plastic combos.
Less than 30 days into the project, the plant ordered 720 plastic reusable combos. On average, the Milan facility ships 100 combos of hams per day. “Although 720 plastic combos are not enough to replace every cardboard combo we ship, it will reward us with a 50% reduction in cardboard usage,” says Wes Maulsby, wastewater operator at the Milan facility.
The combo project’s goal included:
• Reducing GHG emissions—Cardboard savings can be directly related to the release of methane, a GHG, as it breaks down in a landfill. Per ton released, methane will contribute to global warming at a pace more than that of carbon dioxide.
• Reducing water usage—Using less cardboard creates less demand and reduces manufacturing water usage.
• Reducing energy—Fuel sources to manufacture cardboard are no longer needed.
• Reducing global warming—Deforestation is a huge contributor to global warming. The facility can save 17 trees per ton of corrugated cardboard savings, and every eight pallets saved will yield one saved tree.
• Reducing landfill—For every ton of cardboard savings, landfill area can be cut by 9 yd3.
The project was completed in the first quarter of 2021, when the Milan plant shipped the first hams for further processing. In February 2021, the facility received its first load of plastic reusable combos and, in March 2021, shipped the first load of hams in reusable combos. third place | project category
Degradation of freezer blast cells was resulting in improper airflow and inefficiency of the blast cell function at Conagra Brands’ Marshall, Mo., facility. Repairs were made to air segregation, and baffle design was changed to reduce
potential damage from the forklift loading process.
“Baffles were added at the back of each rack column in the blast cells to force the airflow through the product pallets to improve the heat transfer of the freezer,” explains Scottie McKenzie, plant engineering manager. “This reduces the freeze time, lowers electricity consumption, and increases plant capacity.”
The project will reduce the plant’s electricity consumption by 5.7% and reduce the plant’s Scope 2 GHG footprint by almost 1,300 metric tons. “Efficiency projects like this will be an important piece of the entire company’s sciencebased target,” he adds.
In September 2021, a freezer evaluation uncovered inefficiencies in the blast cells. Contractors installed baffles inside the blast cells in November 2021, and performance monitoring occurred in December 2021. The project paid for itself in less than one year.
At the Marshall facility, product requiring freezing is estimated at 500,000 lb/day. Now the plant has seen a 10% reduction in freeze time, a 5.7% total site electricity reduction, and an overall reduction in kWh/lb usage. The result is a yearly savings of more than $200,000.
Easily share the full story with your peers: oemgo.to/sustainabilityawards2022
→ PMMI, The Association for Packaging and Processing Technologies, continued its membership growth at its Annual Meeting (Sept. 12-14; Oak Brook, Illinois), adding 29 new member companies this fall, bringing membership to 981 total member companies.
“PMMI’s membership growth reflects our continued hard work and commitment to supporting the packaging and processing industry and our membership,” says Andrew Dougherty, vice president, member services, PMMI. “We are focused on the heart of our mission, to provide members the resources they need to succeed in a global marketplace. We do that by helping them to stay ahead of industry challenges and emerging technologies, and, most importantly, connecting them to customers – and each other.”
PMMI’s new members are: GENERAL Advent Design Corp., Bristol, Pennsylvania AES Packaging Solutions, Inc., Port Coquitlam, British Colombia AGR International, Inc., Butler, Pennsylvania American Mechanical and Manufacturing, Inc., Rancho Cucamonga, California
BESSEN Corp., Brooklyn, New York Pacteon Corporation, Brewerton, New York Quickdraft, Inc., Canton, Ohio TechniBlend, Waukesha, Wisconsin Vinco Automation, Alexandria, Minnesota
ASSOCIATE
HEUFT USA, Inc., Downers Grove, Illinois
KORSCH America Inc., South Easton, Michigan Matcon Americas, Delran, New Jersey PACRAFT, Shoreham, Michigan
AFFILIATED SUPPLIER
COPA-DATA, East Windsor, New Jersey Kiewit Industrial Group Inc., Lenexa, Kansas SLIPNOT, Detroit, Michigan Tekscape, New York, New York The Austin Company, Cleveland, Ohio
COMPONENT SUPPLIER
Burkert Fluid Control Systems, Huntersville, North Carolina Fenner Precision Polymers, Manheim, Pennsylvania GIMATIC srl, Roncadelle, Italy Smart Vision Lights, North Shores, Michigan
MATERIALS SUPPLIER
Cheer Pack N.A., W Bridgewater, Massachusetts Craemer US Corporation, Palm Harbor, Florida Georgia-Pacific Corrugated, Norcross, Georgia Iljin Gratec USA, Inc., Santa Fe Springs, California Mold-Rite Packaging, Lake Forest, Illinois
Teinnovations LLC, Warrenville, Illinois TekniPlex Healthcare, Wayne, Pennsylvania
PMMI, The Association for Packaging and Processing Technologies, raised over $67,000 during its second annual Silent Auction to benefit the PMMI Foundation and support the future of the packaging and processing industry. Donations are used to fund student scholarships and education programs.
“PMMI received an overwhelmingly positive response of donations from all across our industry to support the PMMI Foundation’s mission of advancing the packaging and processing workforce,” says Jim Pittas, president and CEO, PMMI. “Our sincerest gratitude to all who took the time to participate in this event by donating items, money, and bidding on items. These gifts will help ensure the future of our industry.”
The Silent Auction was held in conjunction with the 2022 PMMI Annual Meeting (Sept. 12-14; Chicago) and raised money through bids and donations both online and in person, with a live component held during the event. Items available for bid included vacation getaways to Montana, New Orleans, Hilton Head, St. Petersburg, and Colorado; autographed guitars from the American rock band Styx that were signed during PACK EXPO International’s PACK Gives BACK event (October 23-26; Chicago); sports tickets; bourbon gift sets; and more.
Several companies made significant cash donations during the event: Gold Donor
Pacteon Group Pro Mach Silver Donor Garvey PAC Machinery
The Foundation is always thankful for cash donations, and this year, the Silent Auction drew substantial generosity from members through donations and purchased items during the event.
PMMI and the Foundation would like to thank the following member companies and individuals for generous gift donations:
• Barry Wehmiller
• Bob and Lisa Williams
• Festo Corporation
• Harpack–ULMA
• Jordan Hamrick
• Matt Jones
• Mark Ruberg
• Pearson Packaging
• Polypack
• RA Jones
• Spee Dee Packaging
• Starview Packaging
• Wipotec
Because of these members, The PMMI Foundation exceeded its fundraising financial goal this year. “We would like to thank those who participated in the silent auction,” says Kate Fiorianti, director of workforce development, PMMI. “We had bidding wars right up to the end of the auction on several items. There were so many members who participated that we cannot list them all, but we want to give a special thank you to several members who successfully and generously, bid on multiple big-ticket items.”
Those members include:
• Andrew Barrieau, Felins USA
• Emmanuel and Montserrat Cerf, Polypack
• Kevin Mauger, NCC Automated Systems
• Greg Schombert, Hoosier Feeder Company
• Nancy and Nick Wilson, Morrison Container Handling Solutions
Donations to the PMMI Foundation can be made anytime at pmmi.org/ foundation.
PMMI’s Packaging & Processing Women’s Leadership Network (PPWLN) and the OpX Leadership Network teamed up to deliver an easy-to-access digital resource that outlines five core skills to help women succeed in a manufacturing career: business acumen, negotiation, communication, emotional intelligence, and networking. It includes insight from subject-matter experts, as well as perspectives from women leaders reflecting on their personal experiences. Also featured is an excerpt from the Institute of Packaging Professionals (IoPP) 2022 Salary Survey results, highlighting salary trends for women. The document serves as an important resource for organizations and individuals alike. To download the work product, visit: oemgo.to/ voicesofwomeninpackaging
Take full advantage of your free listings in PMMI ProSource, our online directory, by using Features!
Just like your favorite online consumer sites, PMMI ProSource uses check box Features–such as levels of automation, material type, machine type, and package type—to get specific about your packaging and processing products, making your company more visible in search results and driving more web traffic to your PMMI ProSource profile.
It’s easy to update your Features on PMMI ProSource. Have your company’s PMMI ProSource contact log into ProSource Portal, where they can find Feature boxes under each approved category. A four-minute how-to video for PMMI members also includes a section on how to fill out Features. Find the how-to video here: oemgo.to/ prosourcehowtovideo
Questions? Just email us at prosource@pmmi.org.
The PMMI Foundation continues to promote awareness of the packaging and processing industry to the future workforce. There is no better way to showcase the industry to potential leaders than by attending PACK EXPO trade shows. The PMMI Foundation has developed the PACK EXPO Internship Reimbursement Program to assist members in bringing interns to PACK EXPO.
Through this new program, members can apply for reimbursement for travel costs, up to $750, associated with interns attending a PACK EXPO trade show.
For any questions, contact Kate Fiorianti, director workforce development, at 571.266.4406 or kate@ pmmi.org.
Labor shortages are driving consumer packaged goods (CPG) companies to adopt automated solutions,
according to The Future of Automation in Packaging and Processing report released at PACK EXPO International. The report highlights how CPGs are looking to enhance and optimize their production, storage, and distribution processes using automated solutions, including automated guided vehicles, industrial robots, collaborative robots, and mobile robots, with some of these technologies being supported by artificial intelligence (AI) and advanced vision tools.
Spending on automation in the consumer packaged goods industry has increased across the board, and many CPGs expect this trend to continue. With 90% of U.S. CPGs reporting that labor shortages are impacting them, some companies have had to choose between automating a line or stopping production. As a result, over two-thirds of American CPGs have reported an increase in their spending on automated solutions over the past three years.
PMMI’s 2022 Guide to Global Markets provides insight into key packaging and processing machinery markets over the last year. Highlights
include forecasts on crucial packaging and processing machinery markets and an in-depth analysis of significant market trends. If you need actionable guidance on expanding your business internationally, this report is for you. Find the report here: pmmi.org/report/guide-globalmarkets-2022
The cybersecurity gap between Information Technology (IT) and Operational Technology (OT) has become increasingly challenging as computer and network systems become ubiquitous in manufacturing processes. Through the work PMMI has done with its MaX Member Forum, a document has been developed to help solve the issue of effectively bridging the IT-OT gap. For more information: pmmimaxmemberforum.org/workproducts
Showcase your latest innovations to high quality end users looking for solutions to their packaging and processing challenges. Here are four key reasons to secure your space at PACK EXPO Las Vegas 2023:
1. Develop Solid Leads: 49% of attendees are CEOs, GMs, or senior management, and over 20% are in engineering, allowing direct access to the machinery users.
2. Quality face-to-face interactions: Exhibitors benefit from ample time to discuss and see problem-solving applications with prospects. 88% of end users agree seeing machinery in person is important.
3. Reach New Buyers: Nearly half of attendees are completely new to PACK EXPO, never having at-
tended a previous PACK EXPO Event.
4. Expand Network: Attendees come from a broad range of industries: 47% of attendees are from food and beverage and 37% are from top pharma companies, with the remaining industries in life sciences, cosmetics, personal care, industrial, chemical, and more.
Have questions or ready to reserve a booth? Contact Wendy Moore, trade show sales manager, PMMI, at wmoore@pmmi.org. For more information visit packexpolasvegas.com.
The new rules of work require more deliberate interactions with colleagues.
PMMI’s 2022 Annual Meeting in Chicago, Sept. 12-14, embodied the theme “Change is Now,” with over 240 PMMI member executives from 140 member companies attending the event. Annual Meeting speaker Jason Young, president of LeadSmart, Inc. and author of The Culturetopia Effect, sat down with OEM’s Sean Riley for a podcast scheduled for January. Below is an edited for space preview of some of the workforce challenges Young addressed.
Riley: You were one of our culture gurus for the annual meeting this year and coined the word “culturetopia.” It’s a topic that’s discussed constantly, particularly with the Great Resignation and many changes that came out of the shutdown from COVID-19. So, what defines a good culture?
Young: Well, culturetopia’s just a word I made up. And culture stems from a value system, as values will help shape culture. Culture is what’s going to shape behavior and, ideally, foster teamwork. I use a term called “relational coordination,” and it’s just a way of functioning together that’s a little more deliberate than saying, “I’m on a team.” Be more deliberate about how I interact with my boss, coworkers, vendors, and suppliers, in this coordinated way. And that’s what’s going to help to form this freedom. Ultimately, in culture, the idea is to keep people’s tension as low as possible so you can raise performance.
Riley: How do you get people who are already on board, they’re on the team, and get them on board to your culture or to more of a collaborative environment?
Young: We’ve just had like you described, the Great Resignation, and now people do not want to return to the workforce. And that separation can be a culture killer unless you’re deliberate about [maintaining] connection. I’ve seen some very successful remote employees. My performance, or relational coordination, improves if I can keep tension low. And that’s what helps facilitate a healthy culture.
Riley: How do you change that if you’re not one of the people running the company? And if there is resistance from the top, how do you convince leadership, or how do leaders adapt if they’re unwilling to change?
Young: I was working with a technology company, and they had about 400 engineers. Their culture was that if you’re at your desk working, your job’s safe. So, they would spend 12 hours of unproductive time, but they’re logging in. But we worked with it and said, “Okay, we want to look at productivity, not just time spent.” And then they became more of a productive culture, instead of just trading hours for dollars.
Riley: Packaging and processing...most manufacturing is typically a traditional industry. So that might be a stricter culture to change just because it is an
established thing that has worked for decade after decade. So how do you break out of it?
Young: Getting an agreement, whether it be a department, ideally it would be at the top, there’s going to be this agreement on how we want to operate. But I’ve seen companies that write these beautiful mission statements about how they want to treat their employees and how great it’s going to be, and then they don’t do any of it. And all that does is create mistrust and disappointment.
Riley: Do you have tips, tools, or ways to integrate [generational differences] into a culture that doesn’t breed resentment between the different generations? It’s
such a hot-button topic versus the opportunity that it should be, that we’re bringing in new people, new ideas.
Young: I suggest being more creative. I was working with a restaurant company, and the average age of their employees was 17 or 18. And they were having trouble getting people to cover their shifts. I didn’t think of this idea, but they started assigning a scope of work to a group of servers. They took the scheduling and put it in the hands of [the servers, giving them ownership.] Which is what they want.
Riley: I’d like to look into retention. How do we retain?
Young: Often, it’s a retention bonus, “At 18 months, you’re going to get $500,” or you’re going to get whatever it might be. And I think those things work. But, ultimately, first, I don’t think people quit companies; I think they quit supervisors.
Riley: That’s an interesting way of putting it.
Young: And if you’re not happy or unsatisfied with the person that you’re reporting to, or you don’t feel like you’re getting adequate communication, I just don’t think you’re going to have a lot of help in retaining those employees. Unless we start understanding the employee and what they need, and what they would like to see in terms of how we communicate. At Southwest Airlines, they just got completely flexible with everybody. Do you want to work four 10-hour days? Great. Do you want to work 6:00 to whatever? Great.
Riley: But if you’re a pilot, you have a schedule.
Young: Yeah, if you’re a mechanic, you need to be there overnight so you can do the checks. The same thing with working remotely. I know some people just say, “No, you’re coming back into the office, period.” But if you think about it, [the employee] doesn’t have to have childcare or [doesn’t] have to commute an hour each way. But I do think it’s good to have a connection. Just have an office day where you connect with your coworkers or [supervisor.] I think it’s going to be an interesting, continual shift. As more new people come into the workforce, it will continue to shift. But I just think if we can celebrate that and not make it problematic, then we can make that work.
Easily share this article with your peers: oemgo.to/culturetopia
➲ To hear this episode of UnPACKed and more, go to: pmmi.org/podcasts
When considering an end-of-line strapping system partner, choose the industry leader with 40 years experience.
Our machines easily integrate with other equipment in the packaging process, and our engineers collaborate with you for a hassle-free solution providing optimum performance and value. We’re committed to after-market service and support, continuing the relationship beyond the machine purchase.
Call today for a free in-plant survey or virtual consultation.
How Dawn Hudson, former president and CEO of Pepsi Cola North America and former CMO of the National Football League, introduced a fresh, female-influenced narrative to male-dominated organizations.
During the Packaging & Processing Women’s Leadership Network (PPWLN) breakfast, which took place at PACK EXPO International in Chicago this past October, keynote speaker Dawn Hudson shared stories and advice to an audience of about 1,000 people. In a podcast with OEM editor Stephanie Neil, Hudson reflects on some of the experiences during her career at Pepsi and the NFL, and offers guidance for women adjusting to challenging circumstances. Here is an excerpt of that conversation.
Neil: You said in the beginning of your keynote that you didn’t set out to build a career in a man’s world, but that’s exactly what happened to you. Can you briefly bring us through that journey?
Hudson: Sure. I grew up outside of Boston… I went to Dartmouth College, and there were very few women there when I went…I will tell you, as much as I learned from my coursework, when you’re in an overall environment of 10% women and 90% men and there are no sororities and no college centers for the women to hang out at, you learned to find other ways [to get by]. I became very good friends with many of the women that I was there with. But also, I learned to be friends with men, to compete in the classroom with men, to compete on sports fields with men. And I didn’t realize it was part of my education, but it was.
After Dartmouth I went into advertising, which seemed to be a good fit with me. I’m analytical on one side and creative on the other and that industry supports both. Today, the
advertising industry is more than 50% women. At the time, it was 10% women. And, unfortunately today, it still doesn’t have enough women at the senior ranks and it definitely didn’t have women at the senior ranks then, so my Dartmouth experience was just carried over into advertising. I went on from there to work with a variety of clients including Frito-Lay. Frito then hired me…And from there I went to Pepsi in the marketing department, became chief marketing officer, eventually became president and then CEO of about a $5.5 billion division. But what was really interesting to me about Pepsi is at the time I was there, the bottling system was a franchise organization and it was 100 bottlers, from small familyowned businesses with seven trucks to multi-billion dollar
publicly traded companies. And 99 of the 100 were men. And so the big part of my job was trying to get alignment with this group that really invested their capital into making new products and putting them on their trucks and investing in launching them. I went out and got to know a lot of the men, I got to know their families, and it served me well. From there I ended up going to a consulting firm. But when we sold that firm to Ernst & Young and I was trying to figure out what to do, Roger Goodell at the NFL, whom I had worked with at Pepsi, offered an opportunity for me to go to work for them.
Neil: When you walked into the NFL what kind of reception did you get?
Hudson: I did feel like I was stepping back in time and I think that, while people outwardly supported me, I had to prove myself and I had to come to the table with something different. I wasn’t [initially] embraced and brought into the fold, but I would say six months later I very much had great relationships pretty much across the senior team. When I joined the NFL, it was literally in the middle of the Ray Rice domestic violence incident. And when organizations are under real stress and times of challenge, they change more and they have to act differently. So all of a sudden, I had a set of skills in my past, having fought the cola wars and been in Washington to defend soft drinks against obesity, that was very valuable in that environment. And I had a female perspective. So I really had to partner with everyone from the head of football operations to how we were communicating with the players to obviously PR to working with the media group. And I think that cemented and made me feel very much part of the team more quickly than ordinarily would’ve happened had I got into a business as usual, everything’s going great situation.
Neil: So, you’re walking into a crisis, but do you feel like maybe your perspective as a woman was an advantage here to shift the narrative?
Hudson: Oh, I think absolutely. First of all, it was a few other of the women at the NFL that had already started down a path. I literally joined the NFL and took my mom to Africa and safari to play out something I’d planned for a long time. And I came back and the Ray Rice video had gone viral while I was gone. So there were a set of people already starting to work on some initiatives, and they were women. I’m always someone that used data…One in four people in this country are affected by domestic violence. We must listen, learn, and figure out what can we do to help. And so the first thing we did was make people aware of the issue, [and to] know that there’s help out there. Then as we started to get toward the Super Bowl, we learned that we were really growing awareness and there was a lot more outreach to these services…Anyone in that situation, regardless of sex or race or creed, they need a community to help them get out of that situation. So that’s what we focused on in the playoffs and it led to a Super Bowl commercial. But I do believe that a female perspective, and personal knowledge through others, and a team of women that I was working with certainly helped. And that didn’t mean that there wasn’t male perspective in it too.
Watch the NFL’s Super Bowl 2015 commercial addressing domestic violence.
Neil: I want to switch gears a little bit here and ask you, who are the band of sisters?
Hudson: The band of sisters. We are a group of six women who grew up at PepsiCo and some of us were there for over
Partner with us, get high-performance, ultra-reliable products, tap into exceptional engineering applications support...and take your business to a whole new level.
(866) 238-5127 americas.fujielectric.com/pinnacle
20 years. I was there for 11 years. But we were in a really great time at the company where we were growing share, having fun, and we really made friendships that as we all, at different times, left PepsiCo to go on to our next company or experience, we carried those relationships forward. So we were six women who got together at an event and started talking and laughing about some of the things that happened to us back in those early days of Pepsi working with this very male-dominated bottling system. And we ended up talking about, not #MeToo moments, but these little mini moments that occurred during the day out on a business trip that you laugh at looking back at, but you also cringe because they’re uncomfortable. But you’d take a subject and all of a sudden we’d all start talking about it. We ended up becoming passionate about helping younger women enter their career with our advice about how to handle these little situations, and how men and women in the room might help when they see something like this happening.
Neil: And the book you wrote, tell us about the title.
things you could talk about. [Smiling] is a personal thing and that shouldn’t come into a business review. So we all had a lot of chats on what we should call the book, and we thought that one connected with women.
Neil: Any advice for women entering a male-dominated industry like manufacturing?
All Paxton Air Systems are custom-engineered to maximize performance and minimize energy usage.
All Paxton Blowers carry a full three year warranty.
Hudson: So we wrote a book…31 chapters and we tried to give them catchy handles. One of the chapters was called, “You Should Smile More.” The six of us were talking about things that have happened to us in performance reviews. And it’s never happened to me that somebody has told me that I should smile more, but for my other five sisters, every one of them had that circumstance where somebody had given them that feedback. And we asked men if you’ve been told to smile more, they’re not told to smile more. And smiling more is more personal. Can you work harder with the sales group? Can you develop your public speaking? I mean, have you built the best promotional program integrated with Salesforce? Those are functional
Hudson: So it’s really important that as you enter a different culture that you make sure you bring your whole self to work and you voice, again, in a nice way, how things could be done differently. Or if you have a certain dressing style and they don’t dress that way, still dress that way because that’s you and that’s your personality. And I think that over time, you will connect better with people if you’re being yourself, you’re being authentic. Coming in and trying to be something that you’re not usually doesn’t win in terms of connecting with people. Second, make sure that you find a sponsor, male or female, likely male, but somebody who you can go to. Well first, there’s a mentor that you can go through for advice, how to handle this situation. And generally speaking, mentors are lateral or just a little bit ahead of you and they give you good advice but they’re people you have lunch with that you have fun with. But the sponsor is probably somebody you don’t interact a lot with. Maybe it’s the person that hired you, maybe it’s the person that runs your department, but you want to develop that relationship with a sponsor so you can go to them for help. And they’re in a more powerful position to then advocate for you. So think about developing your own network of mentors and sponsors.
Listen to this podcast: oemgo.to/ppwlnpodcasts
Easily share this article with your peers: oemgo.to/dawnhudson
From short, entertaining snippets for social media to longer, how-to explainers showcasing product details, video is a critical part of the marketing toolbox in 2023.
Sharon Taylor, Director of Marketing, PMMI Media GroupToday, most businesses are utilizing video marketing. A State of the Video Marketing 2022 report from video content creator Wyzowl found 86% of businesses use video as a marketing tool. In our own Packaging Supplier Marketing Trends and Best Practices 2022 survey, PMMI Media Group found 77% of respondents are currently utilizing or plan to invest in video marketing. In 2023, we predict further video adoption as manufacturers catch up with the broader B2B segment.
In considering why video has become such an important part of marketing strategies, there are three reasons that stand out to me. First, video humanizes the brands they represent. Advances in mobile phone cameras and lightweight editing tools mean more people have access to create video and can film outside of a studio at locations such as plant facilities and trade shows. To help ease the minds of camera-shy on-air talent, follow simple tips such as drafting a script and filming short takes that can be edited together.
A second benefit to video is that it breaks through the clutter of marketing content. While most marketers utilize video in some form, the overall amount of video produced is still much less than other more saturated channels such as email.
And third, video helps audiences digest content. Just because someone opens an email or clicks on a webpage, it doesn’t mean they’re paying enough attention to fully consume the message. Sharing content through multiple channels offers more ways for the message to penetrate through and video is certainly an engaging channel.
For more on the Packaging Supplier Marketing Trends and Best Practices 2022 survey, go to: oemgo.to/marketingtrends2022
Video is a great tool to showcase locations viewers might not otherwise see, like plant facilities and corporate offices. A plant video can show your product in action, while filming on location at your corporate office can further humanize your brand. Consider small touches, such as highlighting office staff leading into an executive interview video.
Videos are always a great way to show product detail and 64% of our survey respondents said they currently use video to showcase product demos. Other types of educational video include broad “how to” content relevant across the industry and specific product detail for customers postpurchase.
Content doesn’t need to be long, and in fact, for social media, shorter snippets are best. A 15 to 30 second clip introducing a new product, highlighting an employee, or promoting an upcoming event is a great way to jumpstart your video marketing strategy.
Video can be promoted through just about any channel, but two that are a particularly good fit are social media and a company website. With social media, platforms such as Facebook and LinkedIn advocate for video as an engaging content type and reward companies for using video with
•Include captions as up to 85% of people watch social media videos without sound.
•Aim to keep length to 30 seconds or less. (Note: When creating a longer video, plan to break it into smaller segments for social).
•Don’t forget the copy! Include a compelling headline and limit body copy to 150 characters or less.
•Expand your reach by including mentions (of brands or people) and hashtags.
higher impressions than non-video content.
A company website offers a home for videos of all types from company overviews, to testimonials, to a library of tutorial videos. And incorporating video on your website adds significant value. According to research by ComScore, a media measurement and analytics company, websites with video increase their average visitor time on site by two minutes. Regarding search rankings, Forrester Research found video content is 50 times more likely to organically rank on Google vs. plain text results.
Other channels to promote video include events and email. With events, video can serve as either an anchor during event programming or supplemental content such as a looped video at a trade show booth. Including video in
marketing email can help increase engagement and even just adding the word “video” to an email subject line has been shown to increase open rates.
Sales teams are also incorporating video into email. With tools like Loom, Vidyard, and Wistia, sales team members can easily record, send, and track videos sent to customers and prospects to supplement introductions, proposals, and feedback requests. For example, including a video RFP response along with a written submission can help you stand out from the competition.
Incorporating more video into your marketing strategy will take practice and commitment. The good news is, it’s easy to start small and a short video is the perfect format to share on social media. If you’re looking to set future goals, most marketers are creating video content monthly.
E asily share this article with your peers: oemgo.to/videomarketing2022
Watch this engaging and entertaining short video from the Emerging Brands Alliance, featuring PMG’s Senior News Director Sean Riley. This is the first in a series of introductions to package types and how they are made: oemgo.to/pillowbaggingvideo2022
www.mknorthamerica.com
Eliminate safety concerns and decrease changeover times with EZGUIDE Adjustable Guide Rail. | Span Tech Conveyors
Tackle Tricky Angles & Elevation Change. Topper Lift • Incline/Decline
With a combination of high-friction and conventional chain types the Topper Lift can incline and decline products with ease in a very small footprint.. | Span Tech Conveyors
Outrunner Spiral • Incline/Decline
Capable of handling a wide range of products without any adjustments. The Outrunner Spiral gives you the capacity to move several product types without ta ing up valuable oor space. Span Tech Conveyors
High Speed Switch • Sorting & Merging
Move your products 24 hours a day. The High Speed Switch divides your products effectively, hile maintaining product pitch. Span Tech Conveyors
With all drive components enclosed inside the drum, the VDG Drum Motor eliminates maintenance intervals associated with external conveyor drives, increases efficiency, operator safety, and optimi es space utili ation. esigned for 0,000 hrs. of operation before maintenance, reduces operating costs. an er raa
SSV
ost ienic on e or elt ri e o ri e Sproc ets it S uare S a t he rum otor features an P sealing system, ithstands 3,000 psi ashdo n pressure, and drives modular, ire mesh, and monolithic conveyor belts ithout using sproc ets. t eliminates crevices that trap food by products and harbor bacteria, reducing ashdo n time and ater usage by 50 . an er raa
S nc ronous er anent a net ru otor i cienc ata ee ac he lntelli rive features ne permanent magnet drum motor technology, delivering 0 higher electrical efficiency, greater performance, and an increase in electric motor lifespan compared to standard induction motors. t provides data feedbac and ider belt speed selection ithout loss of tor ue. an er raa
ron rip La in ten s on e or elt Li espan ru otor La in ption he patented lron rip agging offered for the drum motor extends the life of the belt and reduces the cost of maintenance. t improves belt trac ing, increases belt traction by 0 , eliminates uneven belt ear and has 5 times longer service life compared to standard lagging. an er raa
The A1C Series Single Flex CD Coupling has very low weight and inertia, making it an excellent choice for today’s most demanding servo motor applications. The unique design delivers two features that are not often found in a precision coupling: High torsional stiffness and high durability. ZERO-MAX
cient an co pact solution ere n ress rotection an or corrosion protection.
Dependable, economical transfer of speed or power, the Zero-Max Crown Gear right angle gearboxes are compact and feature efficient, uiet operating spiral bevel gears. IP65-Rated drives with Nickel-Plated housings available from stock in 1:1 and 2:1 speed ratios and two and three-way versions. | ZERO-MAX
With almost 50 years of experience, All-Pro Fasteners has established a global sourcing network that ensures its customers a reliable fastener supply chain. | All-Pro Fasteners
Reliable Fastener Quality • Fasteners
All-Pro's manufacturing arm, All-Pro Threaded Products, meets the quality requirements of O 00 : 0 5, il 5 0 , O 0 5, , and specifications, all supported by the company's A2LA-accredited Quality Assurance Lab. | All-Pro Fasteners
eed a specific fastener until a reliable supply can be sourced, or re uire a related piece of hard are ll Pro s manufacturing division, ll Pro hreaded Products, can meet your needs, offering custom manufacturing meeting the uality re uirements of O 00 : 0 5, il 5 0. All-Pro Fasteners
ll Pro Fasteners offers a ide range of and services to meet the re uirements of material handling O s. ith decades of and fastener supply experience, ll Pro can be counted on to maintain a reliable fastener supply chain for your operation. | All-Pro Fasteners
High Precision Beam Steering Components and Solutions
XY Galvanometer Sets, Modular Scan Heads, Enclosed Scan Heads
High precision beam steering components and solutions engineered to deliver consistent reliability, speed, and accuracy to meet the needs of our OEM and system architect partners. | Novanta
Zero Contact Digital Processing Application Specific Laser Solutions
Uni uely configured, application specific solutions that include laser source, beam delivery systems, controllers, and software to improve the customer's process performance. | Novanta
CO2, Solid-State CW, and Ultrafast Lasers
Compact, reliable CO2, solid-state continuous wave, and ultrafast laser sources engineered for faster, easier integration into machines and systems for a wide range of zero-contact processing, precision measurement, and inspection applications. | Novanta
Keyless Shaft Bushings are excellent alternative to keyways and tapers. ETP-EXPRESS keyless shaft bushings have only one actuation screw for pressurizing and allow very fast and accurate repositioning of the hub applications where frequent adjustments are required. Other components can be mounted on the shaft all the way up to the ange. tainless and non stainless models. ZERO-MAX
Overload safety couplings won’t corrode
Overload safety couplings from Zero-Max Torq-Tenders are available in special models designed for washdown applications. They clean up easily, won’t corrode, and operate in a wide temperature range. Providing torque limiting and coupling functions in a single, compact unit. | ZERO-MAX
The PMI F90 positioning system monitors the guide roller during unwinding and winding of foils and fabrics in packaging machines. To prevent material cracks and tears, the system automatically adapts the speed. Reliable functionality of the positioning system is guaranteed even under harsh conditions: Since it is independent of the distance, exact measurements are achieved within the tolerance range—even under strong vibrations. | Pepperl+Fuchs
eliable presence detection is ey, and the U has it covered. nstead of ta ing a point by point measurement, a sound beam hits the surface of the container over a ide area. his ensures detection even ith varying contours and position deviations and ma es the color and texture of the container surfaces irrelevant. he output configuration as ell as the sound beam radius can be set ith push buttons on the device. Pepperl+Fuchs
On automated conveyor systems, every ob ect needs to be positioned correctly, and every defective ob ect has to be sorted out. ased on the po erful ura eam laser technology, the 0x series photoelectric sensors detect even the smallest ob ects and their features. Pepperl+Fuchs
Ultra compact U F ultrasonic sensors are ideal for space restricted applications and retrofitting existing machines. hey deliver reliable measurement of roll diameter and detection of material brea s, regardless of the material si e, color, or surface. utomatic synchroni ation prevents cross tal and ensures reliable measurements. O in simplifies parameteri ation and enhances sensor communication. Pepperl+Fuchs
Compact pressure sensor with ceramic cell • Measurement Instrumentation
is a compact pressure sensor outfitted ith a ceramic measuring cell for the measurement of gases, li uids, and vapors up to 30 . luetooth connectivity ma es it easy to set up and configure the sensor irelessly, and the color light ring provides status info at a glance. VEGA Americas, Inc.
VEGAPULS 6X
One sensor for any level application • Measurement Instrumentation
is the one sensor for any level measurement application, li uids or bul solids. imply provide ith your application details, and they ll build a PU that s right for you. uipped ith s custom radar chip, this sensor offers unparalleled precision and reliability. VEGA Americas, Inc.
VEGABAR 38
Pressure sensor with ceramic measuring cell
• Measurement Instrumentation
3 is a universal pressure sensor capable of measuring gases, li uids, and vapors at temperatures as high as 30 . porting a ceramic measuring cell, this sensor is able to measure abrasive substances ithout ta ing damage. built in display ma es for easy on site operation. VEGA Americas, Inc.
VEGAPOINT 24
Capacitive Point Level Switch for Adhesive Media • Measurement Instrumentation
PO is a capacitive point level sensor for the measurement of adhesive or pasty materials, capable of detecting the coverage state even ith the strongest of buildup. ts customi able 3 0 color status display allo s for easy monitoring of the measured vessel at a glance. VEGA Americas, Inc.
ll Pro Fasteners offers a ide range of fasteners and related services global fastener sourcing, custom manufacturing, and programs. upported by its accredited uality ssurance ab, ll Pro hreaded Products meets the uality re uirements of O 00 : 0 5, il 5 0 , O 0 5, , and specifications. www.apf.com | Arlington, TX | 800-361-6627
Contact: Todd Grzych, Director of Engagement, tgrzych@apf.com
Novanta is a trusted technology partner to industrial and medical OEMs with deep proprietary expertise in photonics, vision and precision motion technologies. We engineer mission-critical digitally controlled core components and sub-systems that deliver extreme precision and performance to improve productivity and achieve breakthrough performance.
www.novantaphotonics.com | Bedford, MA | 781-266-5700
Contact: rick.elento@novanta.com
From reliable detection to safe identification to exact positioning and measuring: Our automation technology enables smooth processes in a wide range of packaging industry applications. Pepperl+Fuchs is a world leader in the design, manufacture, and application of high-quality factory and process automation products and services. Pepperl+Fuchs pioneered the development of proximity sensors 50 years ago, and continues to set the standard for innovation and quality today. Pepperl+Fuchs has established itself as a partner for globally active operators of automation technology and offers the broadest portfolio of proven components for the requirements of factory and process automation
www.pepperl-fuchs.com/ | Twinsburg, OH | 330-425-3555
Contact: sales@us.pepperl-fuchs.com
Span Tech is recognized as a global leader in developing unique, customizable technical solutions for processing applications in core industries that include: Food & Beverage production, Manufacturing, Packaging, Distribution, Cosmetics, Pharmaceuticals, and E-Commerce.
www.spantechconveyors.com | Glasgow, KY | 270-651-9166
Contact: cary_bolinger@spantechllc.com
VDG manufactures drum motors for belt conveyor applications with a strong focus on reliability and longevity, delivering robust and efficient conveyor drive solutions for over 35 years. Using cutting-edge production technology, automation, and in-house R&D, VDG ensures product quality, fast delivery, and customer support to a wide customer base.
www.vandergraaf.com | Shelby Township, MI | 888-326-1476
Contact: Wan Lin, Customer Service Manager, wlin@vandergraaf.com
For more than 60 years, VEGA Americas, Inc. has provided industry-leading products for the measurement of level, pressure, density, and weight. Located in Mason, Ohio, VEGA Americas combines manufacturing, distribution, and service for products that represent the most sophisticated process measurement technologies anywhere in the world. www.vega.com | Mason, OH 45036 | 1-800-FOR-LEVEL
Contact: americas@vega.com
For over 70 years, Zero-Max, Inc. has been a leading provider of motion control and power transmission solutions worldwide. With strategic distribution points located throughout the world, Zero-Max can deliver your motion control component solution. The Zero-Max brand is known throughout the world for its high quality and premium performance.
www.zero-max.com | Plymouth, MN 55441, MI | 763-546-4300
Contact: Brian Mishuk, Vice President of Sales & Marketing, bmishuk@zero-max.com
All Pro Fasteners Inc www.apf.com/material C-4
Eam-Mosca Corporation www.eammosca.com 43
Eriez www.eriez.com 22
Fuji Electric Corp. of America www.americas.fujielectric.com/pinnacle-oem 45
Lubriplate Lubricants www.lubriplate.com C-2 mk North America, Inc www.mknorthamerica.com 49 Novanta www.novantaphotonics.com 6
PACK EXPO Las Vegas 2023 www.packexpolasvegas.com 31
PATLITE (U.S.A.) Corporation www.shop.patlite.com 23
PAXTON Products www.paxtonproducts.com 46
Pepperl + Fuchs www.pepperl-fuchs.com/pr-UC18GS 1
PMMI 365 www.pmmi.org 27
PMMI Emerging Brands Alliance www.emergingbrandsalliance.org/grants 47
PMMI Foundation Silent Auction www.pmmi.org/foundation 13
PMMI Media Group Custom Research www.pmmimediagroup.com/cusom-research 17
POBCO, Inc. www.pobcoplastics.com 37
ProFood World Sustainability Excellence in Manufacturing Awards www.pfwgo.to/sema C-3 Slideways, Inc. www.slideways.com 4
SpanTech, LLC www.spantechconveyors.com 5
TAKEX America Inc www.takex.com 59
VDG (Van der Graaf) www.vandergraaf.com/OEM C-1 (onsert)
VEGA Americas www.vega.com/vegapoint 7
Voices of Women in Packaging and Processing www.pmmi.org/ppwin 41
Wipotec - Weighing Technology www.wipotec.wt.com 21
Zero Max www.zero-max.com 3
OEM Magazine (ISSN# 2377-293X) is a trademark application of PMMI, The Association for Packaging and Processing Technologies. OEM Magazine is published four times annually by PMMI with its publishing office, PMMI Media Group, located at 401 N. Michigan Ave., Suite 1700, Chicago, IL 60611; 312.222.1010; Fax: 312.222.1310. Periodicals postage paid at Chicago, IL, and additional mailing offices. Copyright 2022 by PMMI. All rights reserved. Materials in this publication must not be reproduced in any form without written permission of the publisher. Applications for a free subscription may be made online at www.oemmagazine.org/subscribe. Paid subscription rates per year are $80 in the U.S., $125 Canada and Mexico by surface mail; $200 Europe, $400 Far East and Australia by air mail. Single copy price in U.S. is $20. To subscribe or manage your subscription to OEM Magazine, visit www.oemmagazine.org/subscribe. Free digital edition available to qualified individuals outside the United States. POSTMASTER; Send address changes to OEM Magazine, 401 N. Michigan Ave., Suite 1700, Chicago, IL 60611-3789. PRINTED IN USA by Quad Graphics. The opinions expressed in articles are those of the authors and not necessarily those of PMMI. Comments, questions and letters to the editor are welcome and can be sent to: support@oemmagazine.org. Mailing List: We make a portion of our mailing list available to reputable firms. If you would prefer that we don’t include your name, please write us at the Chicago, IL address. Volume 5 • Number 4
Ihate to start another column with a line I’m sure you have heard throughout 2022. Still, after the triumphant return of PACK EXPO International in October, it bears repeating. Although our industry has been slowing down a bit from unprecedented highs the past couple of years, our members continue to tell us that they have never been busier, yet familiar challenges remain.
The supply chain continues to be an issue, and experts from Bloomberg to economic forecasters at our Executive Leadership Conference indicate that will be the case through at least the end of 2023. PMMI provided two Town Halls addressing the issue, one from the manufacturers’ perspective and one offering a point of view from suppliers.
The workforce issue we have noted for years was reaching crisis levels has, unfortunately, come to fruition. This, coupled with record inflation, continues to challenge the packaging and processing industry and drive change. As we look back at 2022, I see our industry rising to these challenges, old and new.
As I mentioned, after four years, the industry came together in a big way at PACK EXPO International. As the largest packaging and processing event in 2022, the show attracted over 44,000 attendees, surpassing the 2018 event. Like PACK EXPO International, EXPO PACK México 2022 also returned after a four-year hiatus and provided nearly 19,000 attendees a place to meet and experience the best and newest packaging and processing technologies in the dynamic Latin American market.
Before those two one-of-a-kind events returned, PACK EXPO East in Philadelphia was the largest since its inception, serving as the premier packaging and processing event in the Northeast. Since producing world-class tradeshows is one of our most important jobs, in 2025, PMMI will launch PACK EXPO Southeast in Atlanta. (See pg. 16)
One of the most vital features at all of our shows is the engagement of students interested in our industry. At PACK EXPO International 2022, six PMMI Education Partner schools’ students received scholarships at PACK gives Back, totaling $30,000, bringing the total amount of academic scholarships to over $200,000 from the PMMI Foundation in 2022 alone. Our first-ever PACK Challenge brought together some of the brightest high-school-aged students from six schools for a machine-building challenge. Following the competition, the machines were shipped back to the schools to use as a learning tool. With prizes in several categories, the top school won over $10,000 for these future leaders.
PMMI workforce initiatives included our usual array
of training and certifications, with the PMMI U Skills fund helping to bridge skills gaps for both the current and future workforce. Pearson Packaging, JLS Automation, and R.A Jones are just a sampling of members who have taken advantage of this program to aid the next generation in learning about our industry, helping them train, and, in turn, ensure a skilled future workforce for future hires. I can’t urge you enough to take advantage of this program as PMMI matches your company’s contribution to in-house training or supporting regional education programs of your choice.
Throughout the year, we were fortunate to get back together for essential networking and idea exchanges ranging from Top to Top and Vision 2030 to the Executive Leadership Conference with over 150 members from 90 member companies and our Annual Meeting with over 240 PMMI members from 140 member companies.
With our PMMI Roadshow, we brought PMMI members and CPG professionals together in St. Louis for a one-day event on addressing industry hot topics. We have done Roadshows in the past, but with Barry-Wehmiller as host and a tour of Anheuser-Busch, it was our most extensive roadshow ever. We followed that up with another event targeting emerging leaders in the current workforce: our first-ever PMMI Young Professionals Conference. This event convened entry to mid-level professionals with sessions on leadership, strategies for employee retention, and more.
In addition to providing tools and programs to address specific challenges facing our industry, we know the number one thing you want from PMMI is to connect you with customers. This year we launched PMMI 365, a campaign highlighting all of PMMI’s resources like our industryleading market research and trend reports, personalized customer research, and media brands—like Packaging World, ProFood World, and OEM—to connect members to the latest solutions, trends, and innovations year-round.
Finally, I kicked off 2022 talking about it, so ending the year with one more reminder about ProSource seems ideal. I am pleased to say that 90% of our members have completed their member profiles in the directory. Customers taking advantage of ProSource include industry heavyweights Conagra, Hasbro, J.M. Smucker, The Honest Company, Fresh Del Monte, Estee Lauder, Pfizer, Pepsi, AnheuserBusch, GlaxoSmithKline, and Procter & Gamble.
Have a wonderful holiday season and all the best wishes for a healthy and prosperous 2023.
Jim Pittas is the President & CEO of PMMI. He may be reached at jpittas@pmmi.org or at linkedin.com/in/jimpittas.
ProFood World added a new category to its annual Sustainability Excellence in Manufacturing Awards. The Processor/Supplier Partnership Category recognizes the growth and importance of collaboration between processors and industry suppliers in protecting the planet.
Learn how past winners in this new category— Li ey Meats and Graphic Packaging International—worked in tandem to create a new PaperSeal tray for Lidl.
View video at pfwgo.to/meat.
DEADLINE FOR ENTRIES IS MARCH 1, 2023.
Learn how to enter at pfwgo.to/sema.
Produced by Awards to be presented at