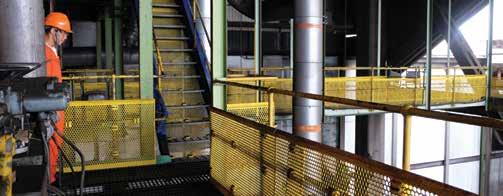
8 minute read
Stopping dropped objects
Putting a stop to dropped objects
Dropped objects pose a significant safety risk at mine sites. Safe Work Australia found in 2017 that eight per cent of work-related injuries in Australia were caused by falling objects.
Incidents involving dropped objects are such a common occurrence that some firms are exclusively focused on tackling this risk.
Dropsafe has been mitigating dropped object risks in the workplace with its product range for more than 20 years.
The company identifies four major threats associated with dropped objects, including the risk of injury or fatality to personnel, the risk of damage to equipment, as well as financial and reputational consequences. The last two categories, while perhaps less obvious, are becoming an increasingly important consideration for miners.
The legal ramifications that arise from workplace fatalities and injuries result in considerable cost to a mine’s perception and bottom line.
Dropsafe commercial director Mike Rice believes firms that cannot show they are prioritising the safety of their personnel by investing in dropped object prevention systems face significant commercial risks.
“Dropped objects do not simply threaten personnel, the equipment they are using and the finances of the site owner; they also pose a significant threat to the reputation of businesses, both large and small,” Rice says.
“Safety performance is highly scrutinised and is increasingly becoming a crucial consideration in commercial decision-making – particularly in challenging market environments where cost-cutting is commonplace.
“To date, an overall lack of standardisation in what constitutes ‘best practice’, coupled with shortfalls and inconsistency in reporting, has posed an obstacle to the adoption of high-quality prevention systems. The tide is turning however, particularly as businesses realise the commercial benefits that go hand-in-hand with a robust safety strategy.”
A key dropped object risk is posed by fixtures and fittings that come loose and fall from height in dynamic environments where vibration and corrosion is common.
The Dropsafe Net — made from SUS316 stainless steel and tested to five times product safe working load — is a widely adopted netting solution that surrounds lighting and other fixtures, mitigating the risk of drops. Objects falling from walkways and stairwells, such as handheld tools and equipment, also pose a risk.
“Dropsafe has continued to see strong demand worldwide for its products from firms throughout the oil and gas, mining, marine, renewables and industrial supply chains,” Rice continues.
“This has resulted in a number of fleet-wide rollouts of the Dropsafe Net as activity has ramped up again in oil and gas, and milestone orders in mining and conventional power for the Dropsafe Barrier, which was recently added to our product range.”
The Dropsafe Barrier, in particular, is designed to prevent objects falling from elevated work platforms (EWP), while the Dropsafe Net keeps overhead fixtures in place.
The Dropsafe Pouch, which boasts a similar stainless-steel design to the company’s nets (albeit miniaturised by design), holsters handheld equipment such as radios and multimeters by cords that prevent them from falling out of reach.
Dropsafe also produces items such as lanyards, securing cables, carabiners and safety shackles, in addition to its main three products.
The company formed a distribution partnership with Pacific Automation in May to meet increased DROPS PREVENTION EXPERT DROPSAFE HAS EXPANDED ITS SAFETY MISSION IN AUSTRALIA THROUGH A NEW PARTNERSHIP. SAFE TO WORK REPORTS. Dropsafe’s barriers can be horizontally or vertically aligned.
demand for its products from Australian mining operators.
Pacific Automation, born as Light and Power Systems in 1969, is wellknown for its distribution of electrical products, a trait dating back to the company’s status as the Western Australian distributor for electric switch manufacturer Kraus and Naimer.
The company will supply Dropsafe products in its range of equipment as part of the deal.
Rice says the partnership will bolster the company’s product and support services in Australia.
“Dropped object prevention is an issue that is currently high on the agenda for Australian firms as they seek to maintain the highest possible safety standards,” he says.
“This has led to steady growth in orders for our prevention systems, which include the Dropsafe Net, Dropsafe Barrier and Dropsafe Pouch.
“As these systems become an essential part of the toolkit for Australian safety professionals, Pacific Automation will help to ensure that they are deployed effectively to project sites and infrastructure throughout the country.”
Pacific Automation has offices in Perth, Brisbane and Melbourne, making the company a good fit for Dropsafe’s expansion ambitions.
Rice says both companies share similar values, which was a factor that attracted the two companies to the partnership.
“At Dropsafe, our products are engineered to stringent manufacturing standards, but we believe that high quality should not necessarily mean high cost, and we focus on delivering systems that remain cost-effective throughout their lifetime,” he says.
“The new partnership in Australia allows us to expand our distribution

Dropsafe’s pouches are designed using a similar technology to its nets.
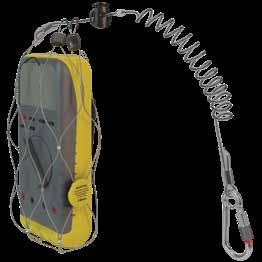
and support network, enhancing the service we offer to our current and future customers in the region.
“Pacific Automation has a longstanding reputation for sourcing and supplying best-in-class, high-quality products and therefore was a natural fit for Dropsafe.”
Responsible automation emerges into a worldwide agenda
THE INDUSTRY SEES A NEED FOR CONSISTENCY IN AUTOMATION PROJECTS AND HAS MOVED TO DEVELOP A UNIFIED FRAMEWORK FOR THEIR SAFE MANAGEMENT. VANESSA ZHOU WRITES.
Like-minded organisations are driving change in the mining industry. They’re not only consumers of automation technology, but also advocates of safety during this period of change.
The Global Mining Guidelines Group (GMG) enables one such network. Together, multi-stakeholders from
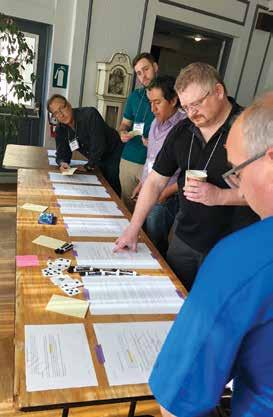
Courtesy: Global Mining Guidelines Group
GMG Guidelines autonomous mining workshop in Canada last year. mining companies, original equipment manufacturers (OEMs), original technology manufacturers (OTMs), research organisations and consultants around the world monitor the pulse of the industries and develop guidelines to manage risks associated with change.
Leading organisations involved in preparing the guideline include Anglo American, Barrick Gold, Caterpillar, Codelco, CSIRO, Deloitte, Komatsu, Liebherr, National Research Council Canada, Rio Tinto, Roy Hill, Schneider Electric, University of British Columbia, and Western Australia Department of Mines Industry Regulation and Safety.
Their finished product is a true example of what can be achieved when industry comes together, Roy Hill senior legal counsel and head of external affairs Julian Hill tells Safe to Work.
The industry interest reflects the growing importance of autonomous systems in mining and the need for a unified framework while maximising the value of autonomy, according to Symbiotic Innovations principal innovator and GMG vice-chair working groups Andrew Scott, who facilitated many of the workshops.
Roy Hill was an active participant in the various collaboration workshops conducted over 11 months. In April, the guideline for implementation of autonomous systems was published, offering a broad overview of autonomous systems and promoting consistency across projects of various scales.
“The guideline has taken an umbrella approach, covering single autonomous and hybrid vehicle projects to multi autonomous fleets, outlining consistent practices in order to deliver a successful autonomous project,” Roy Hill general manager improvement and smart business Christine Erikson says.
The guidelines provide insights for business case development, health and safety risk management, change management, regulatory and community engagement, as well as operational readiness and deployment.
In fact, the strong engagement of the participants in these workshops is reflected in the quality of the guidelines.
Scott says there has been an “incredible level of engagement” in the project since its launch.
“Roy Hill was asked to participate in the development of the guideline as part of a group of mining companies seeking to drive improved safety outcomes, better manage risk and enhance performance,” Erikson says.
“The guideline was developed over a series of workshops conducted around the globe with industry representatives.”


GMG accounted for its leading participants’ experience during the development of the guideline, from an individual to an industry level.
The development was built on individual contributions that are based on expertise and collation of previously developed standards; shared knowledge collected during workshops; and experience gained by the industry, including review of previous and current deployments.
Mitigating risk and managing change while maximising the value of an autonomous project are key principles underpinning the guideline.
The most important objective was to create a guideline that enables organisations to confidently embark on the automation journey, according to Erikson.
“With so many industry participants contributing to the project, the guideline captures industry learnings that can be applied in future projects – enhancing their safety and sustainability,” she says.
“Consistency in application of these guidelines across autonomous projects, particularly the handling of changes to safety through automation and remote operation, has the potential to improve the safety and efficiency of mining operations, while lowering maintenance costs.”
The guideline points out that while improved safety is a frequently cited benefit of automation technology, it can also “present new safety risks”.
Furthermore, improved safety resulting from the switch to automation can be “difficult to measure” when compared with other value drivers, such as reduced downtime and cost reduction.
“Companies should invest sufficient time and resources to ensure autonomous operations can start up safely and meet production expectations,” the report says.
Its relevance to industry makes it a compelling resource for any mining operation considering the adoption of automation, according to Hill.
The biggest success of this guideline development to Hill, however, was in engaging and collaborating with like-minded industry participants, who are all focused on delivering a relevant industry framework.
“GMG sets the benchmark for the positive evolution of mining industry autonomy, where international whole-ofindustry engagement improves the safety and sustainability of the mining sector,” Hill says.
After all, Roy Hill has a firm belief that sharing learnings across mining, and outside mining, accelerates safety and productivity benefits of autonomous projects.
With GMG’s international network of industry stakeholders, it has the ability and reach to support the adoption of its guidelines.