
6 minute read
Dust control in action
This dozer is fit for purpose with dual HEPA filtration and pressurisation .
No doom and gloom: dust control in action
BREATHESAFE OWNER AND DIRECTOR NICHOLAS JOHNSTONE REVEALS THAT KEEPING AN EVERYDAY WORK ENVIRONMENT AS DUST-FREE AS POSSIBLE IS TRULY ACHIEVABLE. VANESSA ZHOU WRITES.
Machine operators have direct contact with the air they breathe inside the cabins. Though the work environment is inescapable, it is certainly not one without hope.
Breathesafe owner and director Nicholas Johnstone proposes four ways to keep dust exposure levels to a minimum inside the cabin.
What do you think about Safe Work Australia’s plan in slashing the regulated occupational exposure limits for respirable silica dust? At this moment it’s just a draft proposal. I think it’s going to bounce backward and forward between the industry and Safe Work. I’m hoping that the minimum that comes through is 0.05 – at the moment it’s 0.1 milligrams per cubic metre over an eight-hour period, and they’re talking about 0.02. I think that’s what they should do, based on the fact there are systems available for providing air quality better than 0.02. Based on the trials we’ve done, we can easily achieve it, and it’s not going to cost an arm and leg to do it.
How does the industry achieve that? We’re talking to the mines and quarries inspectorate, which up here in Queensland has been extremely proactive in really talking to sites and saying, ‘Look, what are you doing about respirable dust? Are you using HEPA filters?’ They’re very simple statements to say, but really, most sites will be still using the original equipment manufacturers’ filters.
All the OEMs of mobile equipment, whoever it is, have different grades for filters – what we find is that end users are still under the impression that what comes supplied in the vehicles is providing a safe work environment for the operator. The fact of the matter is that is not the case. There are statements from all OEMs saying, you might buy a machine and have the options of up to five different grades of filters to go into it. However, there is a disclaimer that states that any of these
filter options which come with the machine are not designed to work in a hazardous environment.
The act of digging a hole in the ground is going to generate mine dust, whether it’s really bad like silica or asbestos, or whether it’s coal dust, all of them are bad for you. It’s just the degrees of how bad it is for the operators over time.
If you were to provide four key things in respiratory protection, what would they be? To provide what we believe to be the best practice and air quality for a mine or a quarry environment, there are essentially four key things.
One, you need to train your operators to understand what you’ve done and how they need to use the equipment. It doesn’t matter how good the filtration system inside the cabin is if they keep the door and window open – that operator would get zero protection.
The second thing is to have a positive pressure inside the cabin. This is generated by a cabin pressuriser. That pressuriser must have HEPA H13 filters in it, so the air comes from outside contaminated and goes through the filters with the dust removed right down to sub-micron levels, and that clean air gets blown into the cab. So, you have more pressure inside the cabin than outside, and that stops dust from coming into the cabin – that’s what positive pressure does. But positive pressure does not mean ‘safe’ – positive pressure using clean air is safe, positive pressure using dirty air is not.
This brings us to the third point: positive pressure inside the cab will stop any more dirt getting into the cab, but it means nothing if you don’t clean the air inside the cabin through a HEPA filter. The operators getting into the cab would have walked across an unsealed yard or go line to get into the machine, and they are now covered in contaminant, whether that be in their boots, their trousers or their shirts. So, we need filtration inside the machine to filter the air as well.
The last one is an in-cabin display that is fitted inside the cab to let the operator know that everything is working as it should be, and that positive pressure has been maintained. This warning device will remind the operator to close the door or window properly, because the whole idea of providing a safe work environment is for it to stay that way for the entire time somebody is in the machine.
Why is it important to monitor dust in real-time? All the research and trials that we have done demand for any engineered solution to be tested and audited periodically. You need to ensure that workers are in a safe working environment and you must have a plan. We’ve had instances in the past where the system has been installed, but some spare parts weren’t available, so people use other parts – the wrong filters. They put a non-HEPA filter into a system that should be taking a HEPA filter. When it comes to real-time dust monitoring, you will know within half an hour whether the system is working effectively or not.
What’s the one thing that could help mine sites the most? Have some clear direction as to what removes respirable dust. I would love if the mines or the inspectorates do some real-life trials over a three- to six-month period, proving what can be achieved. There’s some advice, but no trials have been done recently. There are several systems on the market making claims of what can be achieved, but it would be good to know what actually works over an extended period of time. The long and Breathesafe owner and director Nicholas Johnstone.
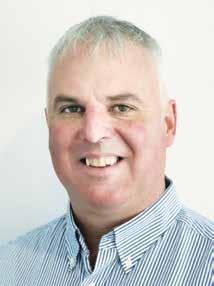
short of it is when we look at reducing dust exposure, there’s a lot of different ways of doing it.
Where do you think the mining industry stands now? There are a lot of people right now who are educating themselves to make sure they are doing their utmost to work out what exactly they need to do to provide that safe work environment for their colleagues. Most hygienists and superintendents are taking it seriously.
The sites that invite us to do a live demonstration are always impressed when they see that we can provide protection factors considerably better than using respirators. It used to be costly in the past, but not anymore. The return of investment is usually within 12 months.
Breathesafe have several trials in progress in large and small mine sites. We always say, let us do the trial on the machine that your operators are complaining about the most – give us the worst machine you’ve got! We will install an engineered solution – the improvement will be noticeable within a week of auditing and testing the system, but your operators will be able to tell whether it’s working or not within days.