
18 minute read
Innovation for underground mining
Machinery innovation aims to enhance underground environment
International equipment manufacturers and Australian companies alike are showing their commitment to changing the underground mining environment.
Epiroc and Safescape both used the Austmine 2019 Conference in Brisbane during May to unveil details of their plans to innovate the underground with battery electric technology.
Battery electric machinery is set to provide numerous benefits to underground mining in the coming years, such as improved safety, as well as reduced greenhouse gas emissions, diesel fuel consumption and power use.
For Epiroc, the technology continues to become further entrenched in the original equipment manufacturer’s (OEMs) future with the development of its Batteries-as-a-service business model.
The new division of the company will be another step towards its ambition to lead mining towards a sustainable future with zero emission machines.
Epiroc has rapidly moved in this direction in recent years, making a key move in 2016 by releasing its first generation battery electric machinery, which focused on smaller models of the company’s underground trucks, loaders and drills.
In 2017, the Swedish company started development of a battery platform involving scalable, modular architecture that could be used across its product range, from the smallest to largest machines.
The OEM then unveiled its second generation battery electric equipment late last year, including a number of larger machines that will appeal to a broader market, particularly in Australia.
To support this expansion, Epiroc realised it needed to change the way it does business to accelerate the transformation.
As Epiroc introduced its new battery system, the company also started to plot the Batteries-as-a-service business model to take its development breakthroughs further.
Epiroc is shaping the business model to remove the obstacles that come with a transition to the technology, providing an ‘instant technology leap’ to battery electric machinery.
Batteries-as-a-service will move the upfront costs of batteries from capital expenditure to operational expenditure, with the responsibility of this function assumed by the OEM.
Epiroc senior executive vice president, mining and infrastructure, Helena Hedblom believes Batteriesas-a-service will be a natural choice for many customers.
“The bigger mining houses often have the capacity to buy it all, but for the smaller and mid-sized customers the capital expenditure (of battery electric THE 2019 AUSTMINE: MINING INNOVATION CONFERENCE DEMONSTRATED WHAT IS BEING ACHIEVED TO MAKE UNDERGROUND MINING SAFER AND MORE ENVIRONMENTALLY FRIENDLY. SAFE TO WORK WRITES.
Epiroc’s second generation of battery electric machinery.
machinery) could still be resistance,” Hedblom says.
“We believed if we could find a way to turn the batteries into OPEX we would have customers wanting to try this, especially as we expect the technology to improve every year.
“With this model we can put the new technology in as it is developed, which is not the case if we just sell the batteries. By that we can have a seamless improvement of technology into the fleet that is out there.”
Safescape, meanwhile, is trialling a light EV in an Australian gold mine in a collaborative partnership with 3ME Technology and METS Ignited.
The Bortana EV, based on the Agrale Marruá heavy-duty utility vehicle from Brazil, has been designed to offer a significant increase in sustainability and durability compared with existing options for underground mining.
It has been developed to provide several key benefits over dieselpowered vehicles. The Bortana EV provides minimal heat, minimal noise and no exposure to diesel particulate matter (DPM) for workers within confined spaces.
A prototype of the EV will go into the gold mine on a three-month trial before further exposure to other mining companies and contractors.
Safescape managing director Steve Durkin says the vehicle has a simple design, but it is also incredibly strong and robust.
“The vehicle we are using has been designed from the ground up for a military platform in Brazil. The whole body is galvanised,” Durkin says.
“So we have a vehicle that is strong enough for the environment, strong enough for the loads that we are carrying, and resists corrosion for an extended period of time.”
Safescape displayed the vehicle at the Austmine Conference, before launching it at the Mt Cotton Training Centre in Brisbane following the event. 3ME Technology chief executive Justin Bain says a vehicle of this nature is sorely needed in the Australian mining landscape.
“Vehicles used in underground Australian mining operations have faced issues of corrosion, durability and emissions for a long time – there is a sore need for a better solution,” Bain says.
“The Bortana EV was developed for the harsh environments of Australian mine sites and we’re really excited to see this vehicle in action. We have focused on achieving the highest levels of safety and compliance whilst delivering superior performance and efficiency. ”
Bortana EVs are future proofed, according to the developers. They are also equipped for integration with current and future artificial intelligence development.
The project is partly funded by METS Ignited, which provided $500,000 for the initiative under its collaborative project funds in 2018.
Epiroc’s development of its battery electric range, along with the Bortana EV trial, demonstrates there is a growing appetite for these innovations in Australia.
Shaiful Ali, Epiroc business line manager, says Australian mining companies are already showing interest in the prospect of a Batteries-as-aservice model.
The interest comes around six months after Epiroc released its second generation battery electric equipment, which the company is confident will be attractive to Australian mine sites.
Epiroc anticipates that Australian underground miners will increasingly pursue battery electric opportunities as the technology improves from an economic perspective.
“That’s mainly because in Australia there are not a lot of greenfield mine sites – a lot of the mines in Australia are going deeper,” Ali says.
“Obviously as you go deeper it gets hotter and it’s a driver for certain mining companies to sustain the mine life. The drivers for batteries are also obviously the cost savings involved with ventilation and the safety aspects they provide.”
The OEM expects an Australian mine to receive a machine from its second generation battery electric fleet by the end of the year.
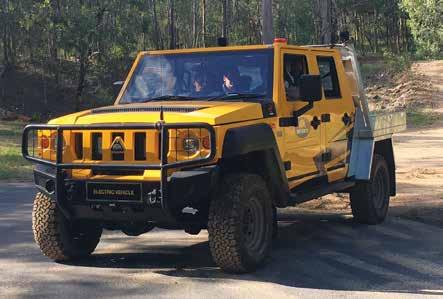
Technology: Is it now a way of mining?
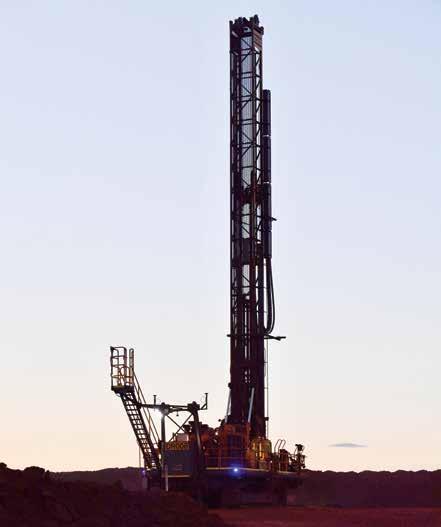
Digital technology is leading to significant changes in the way mining operations are conducted, and the impact can be felt site-wide.
Technology has changed the way things are done, from exploration through to project conception and execution, to mining operations and maintenance, to the logistics of road, rail, port and shipping operations.
Just as key processes and job roles in the wider society have been and are being changed through digital technology, the same can be said for the mining sector, according to Neometals director Jennifer Purdie.
Although the overall change can be transformational, a lot of it is incremental rather than transformative in the same way as in daily lives.
“People working in the sector are changing the way they work and their expectations of the workplace just as they are changing what they are doing at home and in their leisure time,” Purdie tells Safe to Work.
“Different people will handle change differently depending on the individual impacts on what they do day to day in their role and their own circumstances and preferences.”
Roy Hill employee Annette Baker, for example, was working in the company’s remote operations centre (ROC) as a controller dispatch for the truck fleet. She later expressed an interest in taking on a new role within the company, leading to her current position as drill controller.
Baker’s transition was made possible despite her minimal drilling experience, using Roy Hill’s newly developed training plan.
Roy Hill began its transition to autonomous drills in April 2017, with control fully centralised within the company’s ROC in May this year (involving a fleet of nine Epiroc Pit Viper 271 drills). The project has been met with a positive response from Roy Hill’s employees.
“Previously, drillers were operating in TECHNOLOGY IS EMBRACED AS A NEW WAY OF MINING AS MUCH AS IT IS A NEW WAY OF LIFE. VANESSA ZHOU SPEAKS WITH MINING EXPERTS IN AUSTRALIA AND SWEDEN TO GET A CLOSER LOOK ON HOW IT’S BEEN INTEGRATED. Roy Hill’s Atlas Copco Pit-Viper 271 drill fleet has been automated and is now operated remotely from Perth.
an exposed, hot environment at our mine site. The conversion to an autonomous drill fleet meant these employees were able to transition their roles to Perth and operate up to four drills per person using a control console and a screen working from an air-conditioned office at the ROC,” a Roy Hill spokesperson says.
RECEPTIVITY V RESISTANCE Some resistance is understandable when considering digitalisation in traditional mining organisations.
A new workplace environment has its own issues of skills, personal integrity and work environmental problems, leading to workers’ resistance during a transition period, according to Luleå University of Technology chair professor of human work science and dean Lena Abrahamsson.
The underground workplaces in the Swedish mining industry are a context where digitalisation processes in a traditional organisation are extra visible, Abrahamsson says in her think piece, Gender perspectives on the impact of technological change in mining.
Sweden’s mining industry is “not really unique” compared to the global mining industry, where many challenges and opportunities are shared.
This includes the adoption of a high level of new technology, including remote control, automation and digitalisation, with the ambition for even more.
“But at the same time the Swedish mining sector has, in some ways been a reluctant context when it comes to changes at the workplaces … (including) changes related to new technology,” Abrahamsson says.
“The symbolism of mining work, the mineworker identity and culture have for a long time stayed in an old-fashioned mode in many aspects, at least in relation to what the new technology, such as digitalisation and automation, imply.”
Resistance to digitalisation typically arises from a fear of change around roles and the new skillset required to be successful in the role, according to Roy Hill.
A key contributor to any resistance can be uncertainty or lack of exposure to technology.
Roy Hill’s focus on providing career development pathways ensures there is a clear training plan in place, including any training required on using more advanced digital technologies.
In fact, there have been no redundancies as a result of Roy Hill’s move to autonomous drills.
“Automation projects are always still predominantly about people. This (ROC) project has highlighted that by being open, transparent and committed to people’s development, advanced technology projects can be implemented in conjunction with enriching our people’s career paths,” Roy Hill head of mining Ian Wallace says.
Purdie continues: “People I have worked with in mining are all keen for improved safety in the workplace, and often where there is reduction in manual intensity, this also makes work safer and easier for all.
“A particular benefit may be that some older workers may find it easier to continue in the workforce for longer.”
It is, however, important for mining companies to be able to address questions relating to employees’ role evolution to appease resistance.
These questions are ‘Do they have the skills for new roles or will they be trained?’, ‘Will their jobs disappear, and if so what else will they be able to do?’ and ‘What is the impact in terms of salary and conditions?’
Purdie believes that occasional physical presence and a level of experience on site is still required for those working in ROC to be the most effective, though technologies may overcome this need in the future.
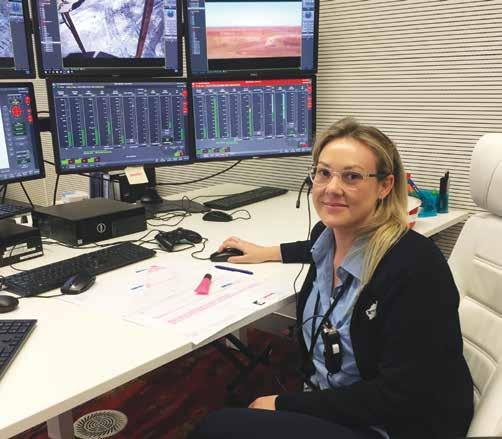
Taking water back to the environment
VIRTUAL CURTAIN PROVES THAT CLEANING UP CONTAMINATED MINING WASTEWATER CAN BE COST-EFFECTIVE, IN CONTRADICTION TO POPULAR BELIEFS ABOUT RESPONSIBLE MINING. VANESSA ZHOU WRITES.
CSIRO senior principal research scientist Grant Douglas has brought a double-edged sword to wastewater treatment – a critical part of every mining operation.
He invented a technology called Virtual Curtain, which demonstrated its worth by successfully treating 56 million litres of acidic, contaminant-laden mine pit water in a Queensland copper mine within just two weeks.
The technology not only extracted water safely, but also returned a better water quality to the environment.
The miner then recovered around $1 million worth of ore back from the bottom of the mine pit, with over 90 per cent of the treated solute being discharged to the environment. The material produced by the Virtual
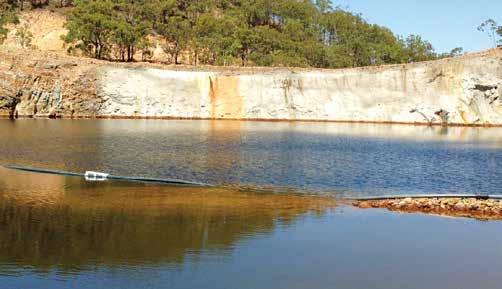
Queensland copper pit prior to treatment.
Curtain process contained an ore grade that is substantially higher than what was mined – eight per cent copper and four per cent zinc – with potential for reprocessing.
Contaminated wastewater in a copper project being treated with the Virtual Curtain technology.
“Virtual Curtain has absolute technological advantage over current technologies in that you do have that opportunity now to produce an even greater ore grade that was originally mined. You can get that out of the wastewater by concentrating up the contaminants into a solid,” Douglas tells Safe to Work.
“That’s really why Virtual Curtain is at the forefront with advantages over a lot of existing techniques.”
What’s more, Virtual Curtain allowed copper mining to commence about six weeks after the treatment. This is only one of Douglas’ success stories in completing the full cycle of processing contaminated, acid pit water back to re-mining.
Douglas, who developed the invention in 2008, has 25 years of experience in surface, groundwater
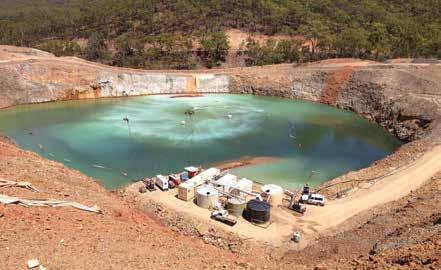
An emptied mining pit in Queensland following wastewater treatment.
and sediment geochemistry.
In the Beverley uranium mine in South Australia, Virtual Curtain removed a suite of radionuclides while evaluating the treatment of its effluent in a benchtop study.
“We were able to take out any remaining uranium following processing, and take out a lot of the radioactivity. So you have the opportunity, if required, to release a higher quality water,” Douglas says.
Virtual Curtain demonstrates that wastewater processing can go to another level, often far beyond current industry capability.
The technology can be applied to copper and zinc, as well as other hard rock mining in Australia and internationally.
Not only can Virtual Curtain be implemented from the initial mining stage, acid wastewater treatment, metallurgical processes through to improving the performance of other technologies, it can also be used to clean up the water after commodity extraction.
In China, the Virtual Curtain technology was used to treat seven billion litres of coal to chemicals wastewater a year – ‘a big drink’ according to Douglas – producing reductions of 60 per cent in total
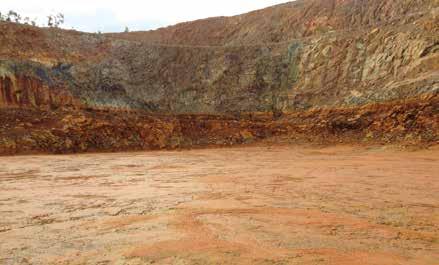
hardness, 66 per cent in silica and 85 per cent in turbidity.
The result was a 50 per cent increase in reverse osmosis output at a fraction of the comparable infrastructure costs.
Wastewater treatment with Virtual Curtain requires only a couple of tanks, while recovering much less solid and more water (up to 90 per cent) compared to the traditional lime method (often around 60 per cent).
“A lot of the time, the use of lime is the default in mine wastewater treatment. It is the traditional method that has been used since the Roman times. But lime is imperfect and involves quite an intensive process and considerable infrastructure costs,” Douglas says.
While Virtual Curtain is mostly retrofitted, its subsidiary Virtual Curtain China is building the first ever sites dedicated to the technology at China’s biggest copper operation and in a chemical plant north of Beijing.
Both plants are designed to treat a couple of gigalitres of water a year to a standard in line with China’s ‘water 10 plan’ – a rigorous action plan to control the country’s pollution discharge.
That policy is the reason behind Douglas’ 11 trips to China in the past three years. Given the sheer scale of mining operations in China entail a significant volume of water, what the companies need is an efficient solution and now.
“It’s the 21st century and there is universal acknowledgment among mining companies and legislators that there’s a need to operate more efficiently,” Douglas says.
“Everyone is reasonably openminded in that aspect. And there is certainly a drive to improve operational and environmental efficiency among mining companies. There’s no doubt about that.”
On the push side, environmental legislations challenge mining companies to operate to a higher standard. On the pull side, mining companies are taking up the mantle in being more efficient with water use and reuse. The push and pull drives the search for more efficient technologies, according to Douglas.
Not many technologies are currently available to remove contaminants rapidly, leaving only a small volume of material and producing water of sufficient quality at the end. But Virtual Curtain allows mining operation to treat its wastewater often to a much higher standard .
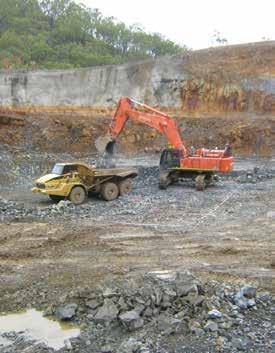
Rio Tinto deploys ‘world’s biggest robot’ in Pilbara
AUTONOMOUS TRAINS ARE HELPING RIO TINTO DELIVER IRON ORE IN A SAFE AND PRODUCTIVE MANNER AT ITS PILBARA OPERATIONS. ALEX GLUYAS WRITES.
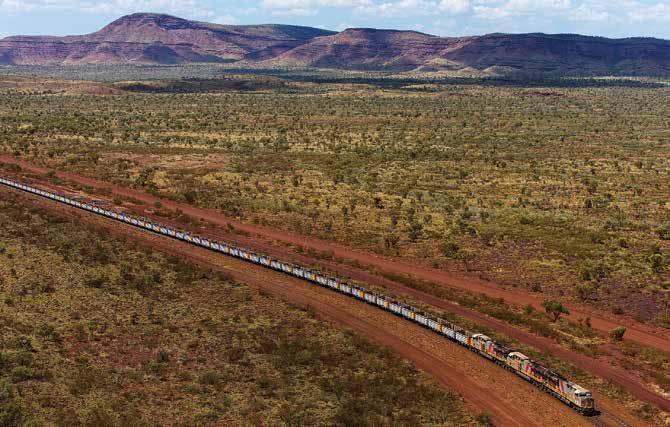
Rio Tinto’s launch of the AutoHaul rail system is a decade in the making.
Rio Tinto has launched its landmark AutoHaul project in the Pilbara, marking the world’s first automated heavy-haul long distance rail network.
The launch of the project is the culmination of $US940 million ($1.37 billion) worth of investment over the space of more than 10 years.
AutoHaul was deployed by Rio Tinto in June alongside the Western Australia Government and its technology partner Hitachi Rail STS, who celebrated the project’s completion with its development partners Calibra, New York Air Brake and Wabtec.
The 2.4-kilometre-long trains, which are monitored remotely from an operations centre in Perth, travel across a network of 1700 kilometres of railway tracks.
Iron ore from 16 mines is delivered to ports in Dampier and Cape Lambert, with the trains already having travelled over 4.5 kilometres autonomously since they were first deployed last year.
The autonomous trains improve safety through reduced risk at level crossings and automated responses to speed restrictions and alarms.
All Rio Tinto locomotives are fitted with AutoHaul safety systems that include collision detection systems and on-board video cameras to record the front view from the train.
They are also equipped with automatic train protection technology, which controls the trains speed to ensure adherence to speed limits.
AutoHaul removes the need for almost 1.5 million kilometres of road travel per year that was previously required to transport drivers to and from trains mid-journey.
The average return distance of the trains is about 800 kilometres with the average journey cycle, including loading and dumping, taking about 40 hours.
Rio Tinto Iron Ore managing director rail, port and core services Ivan Vella says the deployment of AutoHaul positions the company and Western Australia as a world leader in autonomous technology.
“This project has cemented Western Australia as a leader in the heavy-haul rail industry and has attracted interest from around the world,” he says.
“The successful deployment of the world’s first heavy-haul long distance rail network demonstrates the potential for significant further improvement in such operations with others around the world looking to replicate.”
WA Minister for Mines and Petroleum Bill Johnston reinforced this message by congratulating Rio Tinto and its partners, noting that the project highlights the innovation in the state’s resources industry.
“AutoHaul has brought the rail freight industry in this country into the 21st century and is rightfully the subject of global interest,” he says.
“I’d also like to mention that the development of the world’s biggest robot is such a success because of the contribution from Western Australia’s skilled engineers and innovative workers.”
Hitachi Rail STS president Americas and APAC business unit, Michele Fracchiolla, says the company is proud of the lead technical and delivery role it has played in the project’s deployment.
“This is a new technical benchmark for the freight rail industry worldwide and the result of a long-established and collaborative partnership between Rio Tinto and Hitachi Rail STS,” he says.
“Now that the trains are running autonomously, the levels of continuous improvement that can be achieved in safety, operational efficiency and sustainability are endless, and we look
Copyright © 2018 Rio Tinto.
Rio Tinto’s port facilities will be linked to its mines by the autonomous locomotives. forward to continuing to collaborate with Rio Tinto to enhance the AutoHaul system.”
Early results from the deployment of AutoHaul indicate the technology’s potential to improve productivity and flexibility through reducing bottlenecks in Rio Tinto’s iron ore system.
Rio Tinto operates around 200 locomotives across the largest privatelyowned rail network in Australia, having deployed software on the vehicles in December last year.
The AutoHaul program is the latest element in Rio Tinto’s autonomy-focused Mine of the Future program, which launched in 2008 with an initial focus on autonomous haul trucks.
Over the decade since its announcement, the program has expanded to incorporate drills, trains and even smaller vehicles such as light trucks.
The program’s effect on Rio’s iron ore production has been positive, with the company reporting strong shipment results from the Pilbara throughout 2018.
Shipments increased two per cent on 2017 to 338 million tonnes, putting the company at the upper end of guidance as it continues to ramp up mine expansions.
Rio’s focus on its autonomous operations has contributed to its forecast of Pilbara shipments to range between 320-330 million tonnes this year.
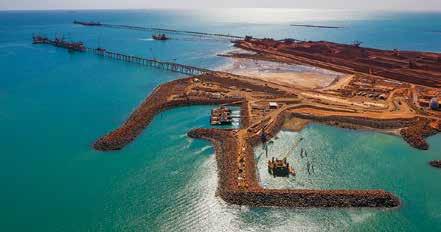
SUPPORTING SPONSORS
ASSOCIATION PARTNERS
EXHIBITION SPACE NOW
ON SALE
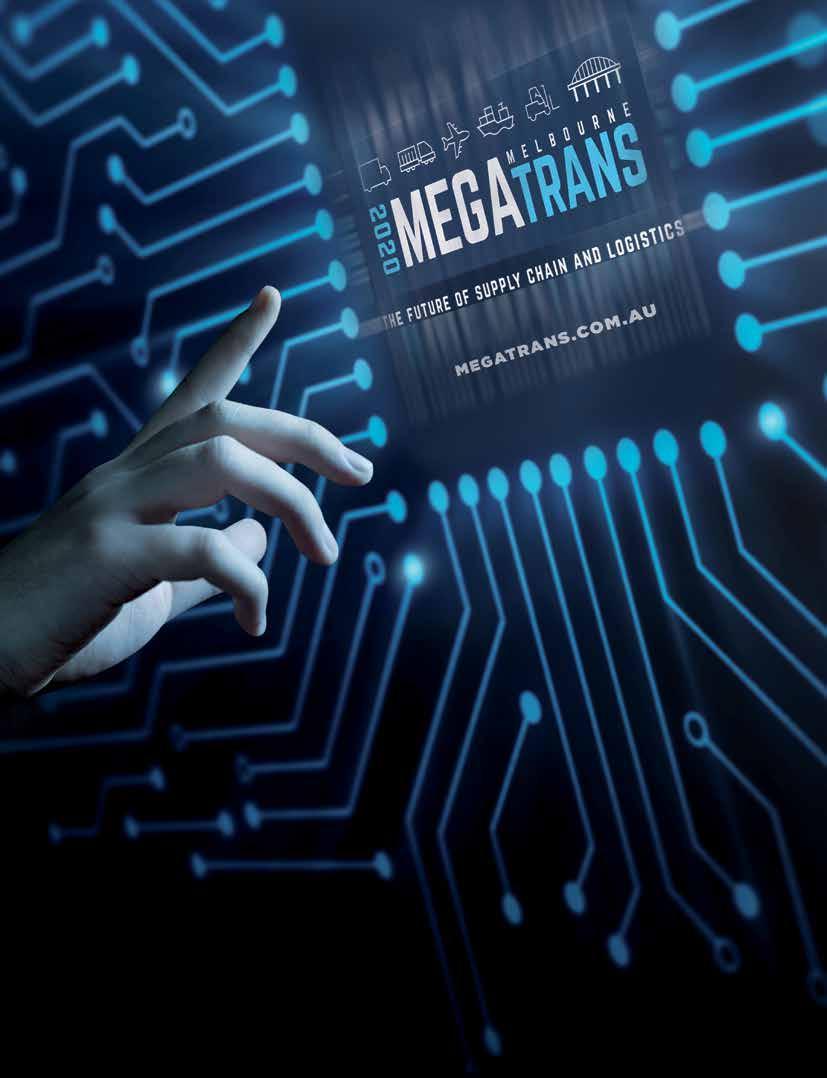