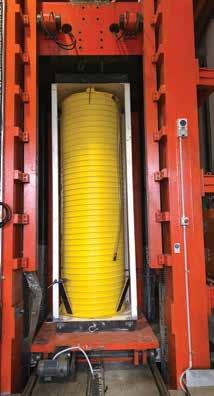
9 minute read
Underground safety from the surface
Approaching underground safety from the surface
CONTACT WITH CHEMICALS, DANGEROUS EQUIPMENT AND UNPREDICTABLE SURFACES ALL EXIST IN UNDERGROUND MINES, BUT MINOVA HAS FOUND A WAY TO REDUCE HUMAN EXPOSURE. ALEX GLUYAS WRITES.
Strata consolidation is a crucial aspect to the safety of any underground mining operation, as it provides stability around mine openings.
Underground mining in general is fraught with safety risks but the upside is enormous given some of the most prominent coal mines in the country lie beneath the earth’s surface.
Generally, the underground mining process involves creating tunnels from the surfa ce into the mineral seam, which can exist hundreds of
A pumpable crib can be filled from the surface in around 15 minutes. metres beneath the surface.
These tunnels are then used to transport machinery and equipment that assist in extracting the materials.
For Minova Australia, the introduction of the ‘surface to seam’ method for strata consolidation offers mining companies a new approach to ensuring the safety of its miners, which diverts from the conventional way.
According to the company’s commercial and operations manager, Dave Hewitt, the new technique is far more effective than the traditional system.
“Traditionally in underground coal and hard rock, when you do strata consolidation, the practise has always been to approach it from underground, which involves a lot of material handling in the underground environment,” he explains.
“That in itself has a lot of safety issues such as dealing with chemicals, different raw materials; there are a lot of exclusion zones and a lot of people in confined spaces.”
A mining industry push to try and undertake this process from the surface means Minova is now capable of offering its ‘surface to seam’ method, creating a huge opportunity for mining companies.
“Undertaking this from the surface eliminates people and reduces the potential exposure to chemicals in a confined space,” Hewitt says.
“It also removes a lot of machinery which always has the pote ntial to hurt people and less people involved in the process means personnel can work on other areas of mine sites.”
The new approach focuses on what the company describes as ‘strata control’ which incorporates roof reinforcement, preventing rib failure and stabilising floor movement within site specifications.
Water ingress is a common way in which ground support systems can be compromised and the injection of chemicals from the surface is one solution Minova offers.
This can also be applied to fill cavities in mines, as increasing pressure on rocks from mining activity and geotechnical conditions can cause fractured ground.
If not reinforced, incidents of rock fall or roof collapse can occur which presents danger to people, assets and infrastructure.
Minova anticipates that the process will cut the human footprint in half and Hewitt notes that the demand for the ‘surface to seam’ approach is already in the market.
Having already been approached by a company struggling with strata, Hewitt was questioned about what could be improved by pumping from the surface.
“Personnel-wise, there’s 37 shifts, 12-hour day and night shifts, just to move the product in and out of the mine – that takes a lot of people and equipment to look after just one part of the mine,” he says.
“There was also 37,000 drums of
Minova CTPM pump unit for pumping injection chemicals from the surface.
materials being lifted across rough ground and steel pallets that weigh 21 kilograms, so the potential for someone to hurt themselves is high.”
To improve the efficiency of the process, the surface to seam approach also utilises bulk handling,
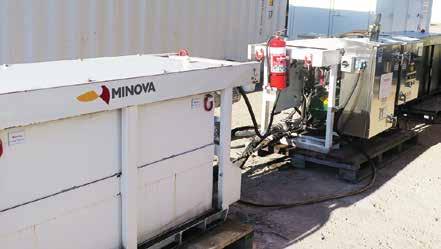
which minimises the number of trips being made.
As Minova looks to launch the surface to seam approach in underground coal mines, Hewitt believes the new method could extend beyond the coal mining sector and into other underground mining areas.
“Block cave mines are now using these chemicals, which they haven’t used in the past as they are starting to get very deep in these caves,” he says.
“To reduce the amount going underground would have significant benefits for an industry that doesn’t have as much experience.”
The new approach is symbolic of a wider industry focus on what Hewitt describes as “remote-type mining”, which involves controlling operations from more distant locations.
The aim is to reduce the exposure staff have to hazardous environments, machinery and chemicals.
For Hewitt, the equation is simple; “the more you can reduce your underground footprint in relation to human and loader interaction, the better off mine sites are.”


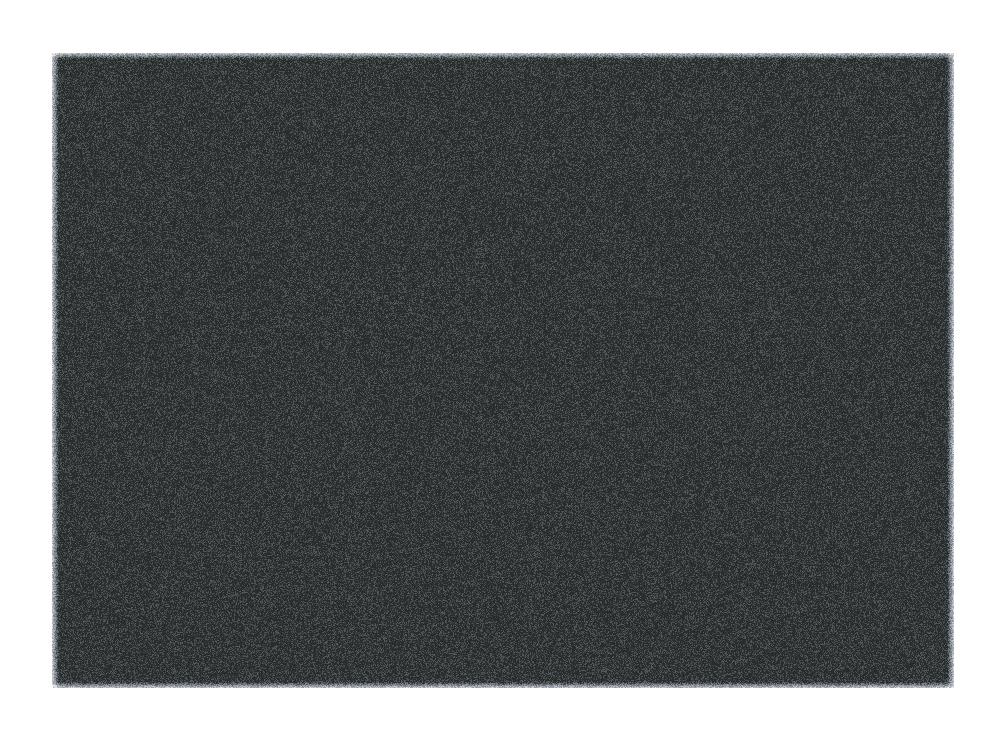
The dangers of gas in underground coal mining
EXPLOSIVE UNDERGROUND GASES ARE ONE OF THE BIGGEST SAFETY CONCERNS UNDERGROUND COAL MINERS FACE. HOW DOES AUSTRALIA STACK UP? SAFE TO WORK REPORTS.
Underground coal mining is safer than it has ever been in the history of the Australian resources industry, but it can still be dirty and dangerous work.
Not only do underground mine workers have to deal with confined spaces, darkly lit environments and heavy machinery as part of their day-today activities, they also have to consider the dangers of gas and ventilation.
Coal mines are naturally gaseous environments and can contain flammable coal dust, so there is a danger of fires or explosions caused by gas, dust or a mixture of both if careful steps are not taken to contain the work environment.
Minerals Council of Australia (MCA) analysis of underground coal mine safety performance in Queensland and New South Wales from 1970-2015 showed the years with the highest combined incidents of fatalities were generally the ones in which fire and explosion-based disasters had occurred.
Notably, the Central Queensland town of Moura has suffered three significant coal mining disasters in that time frame, all of which were related to explosions.
The first was the Kianga No. 1 mining disaster in 1975; the second the Moura No. 4 disaster in 1986; and the third the Moura No. 2 disaster in 1994. Combined, these three incidents resulted in the deaths of 36 people, leaving a significant impact on the town’s psyche.
While a single fatality can rightly be considered one too many, Australia’s coal mining industry in general remains one of the safest in the world when compared with certain international operations in less-regulated regions such as China, which is one of the worst offenders in terms of death tolls.
A November 2009 Xinxing mine
Quality ventilation is critical in reducing the risk of gas-based explosions.
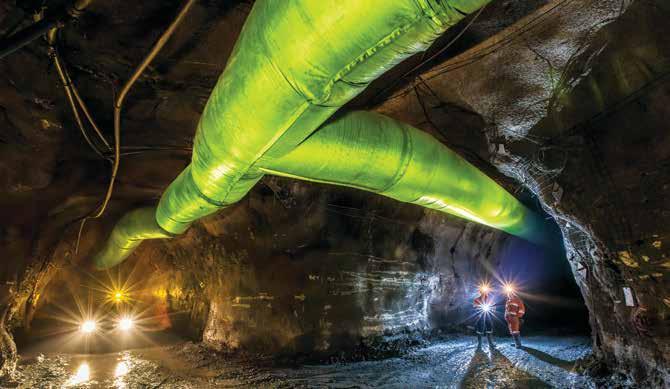
explosion in Heilongjiang province killed 108 workers, for example, though the country’s safety record has improved over the last decade. China also holds the record for the worst recorded disaster in coal mining history, an explosion at Benxihu Colliery in April 1942 that killed 1549 miners.
There is also no one gas to be on the lookout for, according to a spokesperson from the Queensland Government’s Department of Natural Resources, Mines and Energy (DNRME), meaning miners must remain particularly vigilant.
“A number of different types of gas can be present in underground coal mines and they may differ from mine to mine,” the DNRME spokesperson tells Safe to Work.
“A common gas that can be present is methane. Methane forms and is entrapped in the coal seam, but once the coal is mined, the methane is released into the atmosphere. The main danger is the potential for an explosion but only if an ignition source is present in the immediate vicinity.”
Such safety incidents in Australian underground coal mines have dropped considerably since the 1990s as more stringent practices and better detection technologies have come to pass.
Gas monitors have come a long way from the days of the caged canary. Generally categorised by an ability to detect either combustible and toxic gases, modern gas detecting technology can be subdivided into catalytic and infrared detection for the former and metal oxide semiconductor (MOS) or electrochemical monitoring for the latter, although this separation is by no means exclusive.
“Technology plays a pivotal role in gas detection in underground coal mines,” the spokesperson continues.
“An example of these are real-time monitors with sensor heads. These give readings and analyse samples of the atmosphere in various parts of the mine, to detect gas and the levels of gas.”
Catalytic combustible gas detection technology generally uses platinumtreated coils of wire to enable the detection of the catalytic oxidation of hydrocarbons, which become oxidised when they come into contact with a catalytic surface.
This catalytic contact results in temperature changes that alter the resistance of the wires and allow for the reaction to be detected. While catalytic sensors are still widely available, it is an older technology compared with infrared (IR) gas detectors, which requires less calibration.
IR detectors are designed to detect hydrocarbon vapours using an optical IR light source (the transmitter) with a filter set to a certain wavelength, and an IR light detector (the receiver).
Hydrocarbon vapour that comes into contact with the light path between the transmitter and receiver will cause the light to change colour. This is because the hydrocarbon molecules absorb infrared energy in the light.
IR technology is similarly used to check for the presence of other gases, such as carbon dioxide.
Each state has different regulations in place concerning flammable and toxic gases. In Queensland, the Coal Mining Safety and Health Regulation 2017 cites gas management, methane drainage, mine ventilation and spontaneous combustion as four of six major components of an effective principal hazard management plan for underground mining.
It also states that a mine’s safety and health management system must minimise the risk of dust explosions (including the collection and removal of airborne coal dust) and that if an explosion does occur, it should be suppressed to limit its propagation to other parts of the mine.
The NSW Work Health and Safety (Mines) Act 2013 has similar rules in Detectors help to bring attention to potentially hazardous gas atmospheres.

place, stating that mine managers must limit coal dust generation, including generation by coal crushers, belt conveyors and belt conveyor transfer points.
“Controls for gas in underground coal mines are common across all mines,” the spokesperson says. “There exist multiple regulations that relate directly to gas management and especially methane. Limits are set on the amount of gas that can be present in a mine atmosphere but again this can depend on which gas it is.
“They include ensuring any gas in an underground coal mine atmosphere does not reach dangerous levels, ensuring underground equipment in coal mines is intrinsically safe or fire proof and employees are educated in the risks that these gases present.”
Education is really the key word. One day, technology may serve to put an end to underground deaths as the industry’s push towards automation and real-time monitoring continues to evolve.
But until the theoretical day comes when coal mining becomes fully automated, education, training and proper planning will still be the most important factors that ensure combustible gas remains under control.