
14 minute read
Capitalising on waste
A CG model of Centrex Metals’ Ardmore phosphate plant in Queensland.
Why waste shouldn’t go to waste
INDUSTRIAL RECYCLING, WHICH PRESENTS BOTH ENTICING BUSINESS OPPORTUNITIES AND ENVIRONMENTALLY SOUND PRACTICES, IS BECOMING INCREASINGLY DIFFICULT TO IGNORE, WRITES CDE’S REGIONAL MANAGER IN AUSTRALASIA, DAN WEBBER.
Creating value from waste is vital in responding to increasing demand for quality metals, sand, coal and other materials alongside the growing power and energy sectors.
The mining waste management market is estimated to reach 233.56 billion tons at a compound annual growth rate (CAGR) of 6.1 per cent from 2017 to 2022, according to Markets and Markets’ Mining Waste Management Market by Mining Method - Global Forecast to 2022, and forecasts from the United Nations predict resource consumption will double by 2060.
CDE Meta is the mining-focused sector of CDE — the world’s largest wet processing company with some 2000 projects around the world co-created with customers over the past 25 years — and operates in Australia under registered company CDE Australia.
The sector focuses on delivering sustainable mine operations through ore upgrade, tailings diversion and waste dump reprocessing in line with CDE’s commitment to creating a new world of resource.
This expertise has already been recognised by the Australian Mining Prospect Awards 2018, where the company was a finalist in the Excellence in Environmental Management category alongside household names Rio Tinto and Roy Hill Holdings.
CDE Meta made the shortlist for its “pioneering approach to mining waste” transforming more than 17 million tonnes of overburden waste in South Australia into high grade iron ore for steel production.
PIONEERING APPROACH TO MINING WASTE That pioneering approach to mining waste was paramount in 2017 when CDE Meta delivered two turnkey wet processing plants to upgrade 100-plus years of legacy overburden waste from the mining of the Iron Monarch and Iron Princess deposits situated in South Australia’s Middleback Ranges.
The plants, located at the previously Arrium-owned Iron Knob and Iron Baron sites, were acquired by the GFG Alliance and renamed SIMEC Mining.
The two wash plants were designed to convert 17 million tonnes of lowgrade iron ore stockpiled as tailings
CDE regional manager, Australasia, Dan Webber.
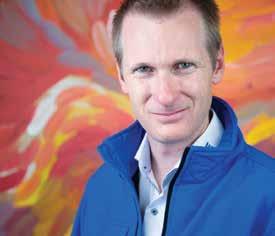
in waste dumps to a saleable product.
The low-grade iron ore to be processed has been accumulated over the life of mining of the Iron Monarch and Iron Princess deposits which first began in 1899 and the Iron Baron deposit in 1930.
These beneficiation plants take lowgrade iron ore stockpiled as tailings and convert it to a 63 per cent grade.
BOOST FOR SIMEC MINING AND LOCAL ECONOMY Operating around the clock, this project, funded by a $49.2 million loan from the South Australian government, provides a vital revenue source to SIMEC, Whyalla and the wider SA region. Some 1000 jobs have been created and $25 million injected into the local economy.
Not only does this provide extensive return on investment through iron ore upgrades, the by-product aggregate produced from ore recovery is stockpiled and sold to the construction industry, further minimising waste while 90 per cent of water used for washing is recycled for immediate reuse in the system. be extracted with CDE equipment, junior mining companies are now turning their sights to the company for solutions.
An integral element to CDE design is a fully modular solution with a small plant footprint. This ‘plug-andplay’ approach delivers faster, safer installation requiring minimal civils and creating significant capital expenditure (capex) cost reductions. It also requires considerably less energy to operate versus traditional stick-build operations. That, combined with innovative highefficiency equipment, reduces electric usage providing maximum operational expenditure (opex) control.
The result is a bespoke modular wet processing solution designed to customer requirements and built exactly to meet production needs.
PHOSPHATE PLANT REDUCES IMPORTS FROM MOROCCO Take, for example, Centrex Metals, which has invested in a state-ofthe-art CDE wet processing solution to create concentrate from the company’s phosphate rock deposit at its Ardmore phosphate rock project on the Mount Isa-Boulia highway in North West Queensland.
This plant, which is currently in factory pre-assembly, will prove the value of the concentrated ore as a 70 tonnes an hour pilot plant before moving to full-scale production at 140 tonnes per hour in 2020.
The company is committed to providing an alternative to the high level of imports of fertilisers — around a million tonnes per year — mainly from Morocco.
The Ardmore site is one of the few remaining under-developed phosphate rock deposits in the world focused on producing high quality phosphate rock concentrate to deliver this vital commodity to fertiliser plants in Australia.
To ensure perfect results, the pilot plant will wash, scrub and de-slime a free-digging ore material to produce premium 35 per cent phosphorus pentoxide (P2O5) and ultra-low cadmium phosphate rock concentrate ready for the manufacturing of phosphoric acid.
CDE has also provided a water recycling system comprising its innovative AquaCycle technology to ensure maximum water recovery in this challenging remote location.
CDE Meta is transforming the world’s approach to mining operations, challenging companies to rethink what they consider a low value or waste product and paving the way towards a zero-tailings mining economy.
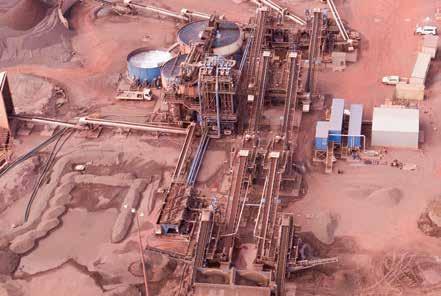
MINING JUNIORS SEEK CAPEX REDUCTIONS AND OPEX CONTROL While CDE Meta provides solutions for top mining companies with legacy waste for processing or tailings dams containing valuable fractions, which can SIMEC Mining’s Iron Baron iron ore beneficiation plant in South Australia.
Why titanium is the medical metal of choice
TITANIUM ISN’T JUST USEFUL FOR PLANES — IT’S ALSO PRIZED AMONG MEDICAL PRACTITIONERS FOR ITS USE IN IMPLANT SURGERIES. EWEN HOSIE FINDS OUT WHAT MAKES IT SO WELL-SUITED FOR THIS PURPOSE.
An X-ray showing a post-operational titanium hip replacement.
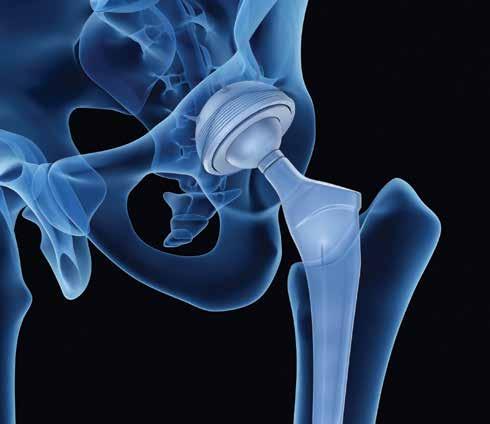
Titanium is a word that can conjure stirring images in the mind. Being one of the foremost metals of the Space Age, it is a material etched in the public consciousness for its association with space rockets, corporate sculpture and shiny robots.
The reality, however, is a bit more grounded. Over 90 per cent of titanium recovered by the mining sector is actually used to support the pigment industry by creating titanium dioxide for inks, paints, plastics and paper. The remaining 10 per cent is used to produce titanium metal, which is used in a wide variety of fields, most commonly the aerospace industry.
Neometals, a producer of vanadium and titanium, owns the Barrambie project in Western Australia.
The company updated its definitive feasibility study (DFS) for vanadium in May while commencing its titanium pilot project.
Neometals general manager, commercial and investor relations Jeremy McManus says the majority of consumption by application is split between pigments (i.e. materials for paints and coatings), as well as a certain percentage for high-strength alloys and a balance for vanadium redox batteries.
“Of the contained resource metal in the project, circa 95 per cent relates to titanium,” he says.
“The vanadium market was red hot when we started the revised vanadium DFS — it’s backed off but we’re satisfied the vanadium production numbers still look robust.
“With the revised vanadium DFS in place, it allows us to look at the next step for a hydrometallurgical pathway to recover titanium and vanadium. This work will allow us to determine the optimal flowsheet to process the ‘whole of deposit’ — the last piece of the puzzle if you like.”
But titanium – more specifically, titanium alloys – doesn’t just sit there looking shiny. It turns out they are one of the most sought-after metals in the medical field.
Titanium metal is notable for its use in the medical industry for surgical implants, particularly joint replacements. Titanium is capable of osseointegration, whereby living bone fuses to the metal without the need for soft tissue, a property that was discovered in the 1940s. (Incidentally, Neometals’ secondary product, vanadium, is also used in small amounts for the creation of titanium alloys that are suitable for medical use.)
Due to the metal’s light density and high degree of biocompatibility
with the human body, it is a desirable metal among surgeons and dentists to replace or insert ailing hip joints, tooth caps, shoulder joints, knees, elbows, jawbones, heels and ribs, and for fusing spinal columns.
This also extends to other surgical implants such as pacemakers, certain hearing aids and cranioplasty plates and, among dentists at least, cap and crown screws for oral implants.
Titanium alloy is noted for its high level of osseointegration – the innate ability to heal with bone. This makes it ideal for artificial implants such as joint replacements.
Devinder Garewai, an orthopaedic surgeon who works as a shoulder specialist at the Melbourne Arm Clinic in Victoria, explains that titanium alloy’s strength, rigidity and lightness are all qualities that make it ideal for implants.
“It’s very uncommon to see a titanium stem snap in two. It’s very rigid and has very good ‘fracture toughness’, which is the medical research,” he explains.
At the same time, itanium alloy also has a very low modulus of elasticity, meaning it is not so stiff that it prevents the bone from healing. Young’s modulus (named after 19th-century British scientist Thomas Young) relates to the measurement of stiffness in a material. It is important that the implant has a degree of elasticity to avoid leading to later complications.
Failure to fuse the bone with the implant can lead to problems such as cysts, looseness and pain, Garewai says.
“If you are putting an implant into the humerus, for example, you need the implant and the bone to be working together because if you stress the bone at the same time, the bone will be constantly remodelled so that it can actually survive for a long time,” he says.
“If you’ve got an implant that’s too stiff, all the force goes through the implant instead and the bone around it stops being stressed and remodelled, Workers drilling at Neometals’ Barrambie titanium-vanadium project in Western Australia.

which leads to failure of that bone.”
Titanium alloy’s ability to fuse with bone is referred to as osseointegration – the process by which the implant fuses to the bone to allow for mechanical stability, thus making it an ideal material for artificial implants.
In addition, titanium is handy for surgeries on the outside too – highquality surgical instruments such as forceps and tweezers also tend to be made from the metal.
Garewai adds that another important consideration when dealing with titanium for joint implant surgeries is when dealing with total replacements, where both the ball and socket of a joint are replaced. The artificial socket – called a glenoid – generally uses plastic components to avoid corrosion issues arising from metal-on-metal contact.
“The Joint Registry of Australia highlighted that when you use implants on the socket side, they have a higher rate of failure,” he explains. “I actually put a plastic component on the socket side that needs to be cemented into the glenoid and the humeral side I definitely use an implant that is made of titanium.
“Osseointegration means the bone is healed to the implant. It’s not a problem that the component was healing to the bone, it’s that you can’t have a metal socket and a metal ball as it causes too much corrosion – you need to have that plastic in between.”
The future looks exciting for titanium in the medical field. The advent of 3D printing technology, for example, is adding to the versatility of titanium alloy, lowering costs and making it easier than ever before to produce implants of all shapes and sizes.
Whether it’s titanium alloys or titanium chemicals, medical or mining – things are looking bright for titanium.
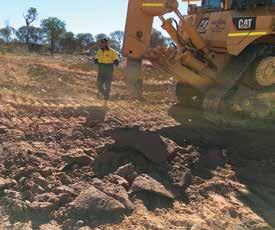
Final excavations take place at Neometals’ Barrambie project in 2018.
CONFERENCES, SEMINARS & WORKSHOPS
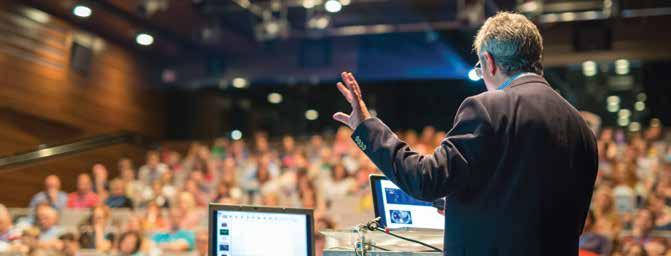
EVENT SUBMISSIONS CAN BE EMAILED TO EDITOR@SAFETOWORK.COM.AU
NSW MINING HSEC CONFERENCE AND AWARDS DINNER, HUNTER VALLEY, AUGUST 5–7
With over 600 delegates in attendance in 2018, industry leaders, senior government representatives, as well as health, safety, environment and community (HSEC) professionals will be back again this year. Discussion will be held to address operational and regulatory challenges, issues and opportunities in the NSW resources industry. Topics range from risk, communications and safety to rehabilitation, mine closure planning and community engagement. The NSW Mining HSEC Awards recognises leading practice and celebrate innovation. • nswmining.com.au
QUEENSLAND MINING INDUSTRY HEALTH & SAFETY CONFERENCE, GOLD COAST, AUGUST 18–21
The annual Queensland Mining Industry Health and Safety Conference is hosted jointly by the Queensland Government, Queensland Resources Council, and mining unions (CFMEU and AWU). The threeday conference continues to be one of the largest health and safety conferences in the southern hemisphere. It is designed to provide Queensland resources companies with valuable information on critical issues that may impact on the sector. The gathering also celebrates and promotes the ingenuity of practice home-grown safety through statewide innovation and health awards. The event will start with a luncheon on Sunday August 18 and conclude with the conference dinner on Wednesday August 21. • qldminingsafety.org.au
MINE VENTILATION CONFERENCE 2019, PERTH, AUGUST 26–28
Ventilation controls are one of the core risk activities at mines. Significant developments in practice and research in recent years have helped ensure we maintain and improve levels of safety within the underground mining sector. The Australian Mine Ventilation Conference 2019 calls on expertise to present these developments, explore achievements and build a better industry. The conference will give presenters the chance to exchange information on topics such as: ventilation planning, main and boster fans, heat and refrigeration, coal mine ventilation, hard rock mine ventilation, sulphide dust explosions, and more. • minevent.ausimm.com
AIMEX, SYDNEY, AUGUST 27–29
The largest free-to-attend mining conference in Australia returns to Sydney in 2019. The conference is designed as a platform to facilitate discussions around mining techniques and deliver operational improvements. Key themes of the conference include developments in drilling and blasting, processing and bulk materials handling; automation and digital advancements to improve operational efficiency and maintenance; and fleet performance and tyre management. The program offers visitors the opportunity to create a personalised program that addresses specific areas related to their job function or site. • aimex.com.au
THE SAFETY IN ACTION CONFERENCE, MELBOURNE, SEPTEMBER 10-11
Bringing together leaders in the health and safety professions, the Safety in Action Conference is a two-day conference aimed at encouraging global involvement and networking. Held at the Melbourne Convention and Exhibition Centre, the conference has welcomed over 700 delegates in the last two years. It allows delegates to hear from regulators, thought-leaders and international keynotes that are making an impact on safety culture. This year’s program will explore key health and safety topics by linking safety strategy, leadership and culture. • informa.com.au/event/conference/safetyconference/
GASTECH VICTORIAN MINES RESCUE COMPETITION (VMRC), LATROBE VALLEY, OCTOBER 20-22
From humble beginnings 20 years ago, the VMRC has emerged as a highly competitive national event that combines mines rescue and emergency response capacity building exercises. The event tests theory, firefighting skills, search and rescue, first aid, rope rescue, breathing apparatus, as well as featuring the Spence Herd Challenge. The challenge is designed to test, encourage and develop team cohesion and values by completing a number of tasks in a short time frame while the team carries its captain on a stretcher. The VRMC sees mines rescue and emergency response teams from sites across the country competing against each other in a variety of simulated emergency situations. • minerals.org.au/victoria/victorian-minerescue-competitions-vmrc
THE FIRST PRIORITY FOR AUSTRALIA’S MINING INDUSTRY
ISSUE 4 - JULY-SEPTEMBER 2019
Personal protection The considerations for coal
Technology Environment Materials handling Working at heights
Throughout the cycles of the mining industry there is one constant for everyone involved in the industry – safety. A safe workplace is critical to the continued success of your business.
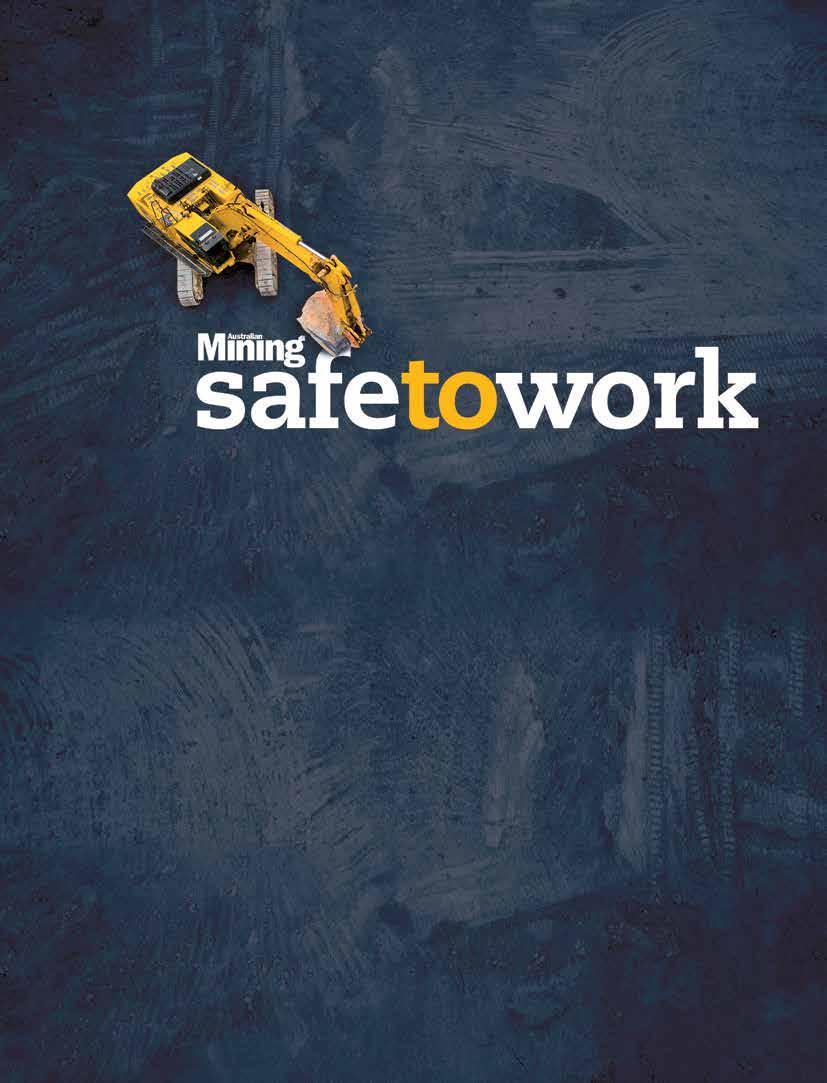
Launched in 2018, Safe To Work provides a high-quality, multi-platform publication for the Australian mining sector, with safety as its key focus.
Safe To Work’s promotional features deliver a forum for organisations to showcase the role each aspect of safety plays in helping the industry achieve the industry’s No. 1 priority.
SECURING MINING. TOGETHER.
Minova is an international producer of high-performance ground support products for the coal mining industry.
Our innovative high volume pumpable grouts and injection chemicals, applied from the surface to the seam, provide: • Maximum levels of safety • Increased efficiency • Minimal labour footprint
Comprehensive training and assessment is available to all customers, with on site quality control programs that can be specifically developed and managed to suit your individual requirements.