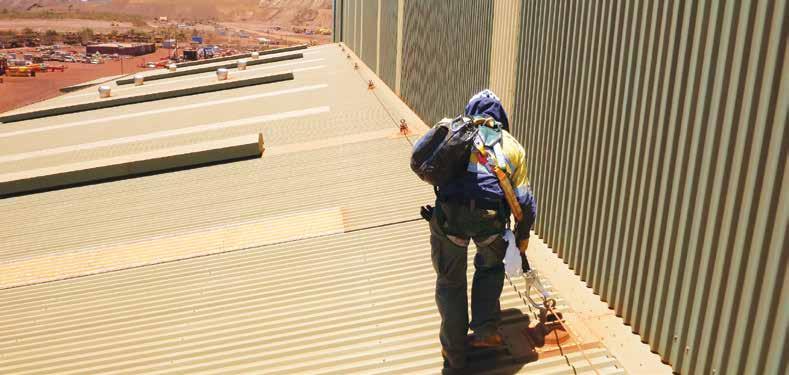
11 minute read
Training and working at heights
Ben Shadgett at work at a site in Western Australia.
The importance of training when working at heights
WORKING AT HEIGHTS IS AN EVERYDAY RISK FOR THE MINING INDUSTRY AND IT IS IMPORTANT STAFF ARE UP TO SPEED. SAFE TO WORK SPEAKS WITH SAFETY TRAINER BEN SHADGETT TO FIND OUT WHY THIS TRAINING IS SO IMPORTANT.
When it comes to modern mining, working at heights can be a crucial part of the job. Human factors are the leading cause of incidents related to working at heights — tiredness, carelessness or rushing are all contributors to possible slips, trips and falls.
It is therefore important that workers in high-risk industries such as mining and oil and gas receive sufficient training in order to recognise and deal with these issues.
Ben Shadgett is a safety trainer at Tasmania-based company Impact Safety Group, which focuses on safety training, inspections and installations of fall arrest safety systems.
The company’s training courses encompass a wide spread of the safety net, including confined space training, first aid and rescue training, gas detection (including gas test atmospheres and breathing apparatus operation) and working safely at heights.
The company’s Working Safely at Heights course is one of its most popular, involving groups of six to 12 participants over a seven-hour day with assessment via written and practical components. Upon successful completion of the course, participants are then handed a nationally recognised statement of attainment.
Shadgett’s heights training and certifications at Impact Safety Group draw on a decade of experience working in Western Australia and Tasmania as a trainer assessor and onsite supervisor at RTOs in diverse industries including mining, oil and gas, civil and construction.
In mining specifically, Shadgett has worked on projects such as shutdown supervisions, plant and fall arrest installations (including elevated work platforms), heights training and confined space standby rescue.
He says the company’s heights training course, which is delivered under the auspices of the RIIWHS204D competency, is among the company’s most popular.
“That unit of competency lists all the core elements anyone working at heights has to do under the nationally accredited training, so there’s a specific training we have to get them through to deem them competent,” he explains.
“It includes things like the correct fit of fall arrest equipment e.g. harnesses, as well as permits, risk assessment and practical components — all those types of things they have to do is ticked off under the RIIWHS204D.”
The Australian Standards designation it falls under talks about selection, use and maintenance of fall arrest systems such as anchor points, static line systems, harnesses and auxiliary equipment.
Servicing and recertification of systems are also included under the Australian Standards (AS) 1891 series standard (specifically 1891.4), which dictates that webbing and rope-based products must be inspected every six months.
For mine sites, especially those in Western Australia that often operate under specific safety regulations in addition to AS standards, this can be as
frequent as every three months.
“Damage, cuts, wear and tear, burns — out-of-date equipment is another one — if you’re talking about mining specifically, a lot of that equipment is used for maintenance work fixing things on site, so they can also get a lot of grease, dirt, cuts, burns and abrasions,” Shadgett says.
“Those are the kind of things that a certified and competent inspector will be trained to look for.”
While the training includes modules for how to properly identify fall risks, dropped objects are another key component. This includes dropping objects such as tools from height, a risk mitigated through installation of drop nets and personal tool lanyards.
The training also covers postfall recovery options in the case that someone does end up falling from a height. This covers rescue planning for workers who have to deal with colleagues who might suffer an injury in this way. The training also accounts for a condition known as suspension intolerance (formerly known as suspension trauma), an orthostatic effect that occurs among some people who are suspended in harnesses for extended periods of time.
“It’s something we focus on quite heavily in our course, because there are proprietary build kits these days that allow you to hook on to someone who has fallen over and lower them to the ground or bring them back up to the level you were at as a post-fall rescue scenario,” Shadgett says.
“Effectively what they’re trying to do is say to work groups, ‘Don’t just have a mechanism of calling 000 as your plan because it can take some time to get someone down’.
“What we’re trying to do is teach people that post-fall recovery plan to get people on the ground as soon as possible to prevent this suspension intolerance from occurring.”
This ‘000’ strategy is a salient point. FIFO workers, who often work at a considerable distance from the nearest hospital, make up a significant proportion of the company’s mining trainees. While it is important that safety measures be taken at all mine sites regarding heights risks, workers at the most remote sites are particularly vulnerable given that their workplaces can be located so far from help.
“In Tassie, we’re a unique company because a lot of the FIFO workers are specifically based in Western Australia and Queensland. If they’re Tassie-based, however, we offer public courses for our accredited training,” Shadgett says.
“They can come in on their weeks off, do the training, fly back to site and hit the ground running, rather than have to fly to Perth and do the training there.”
At a time when entire companies dedicate themselves to new technologies that push site safety forward, such courses serve a vital purpose to account for the basic training that helps to mitigate the risks of human factors.

The danger of acid mine drainage
ACID AND METALLIFEROUS DAMAGE IS ONE OF THE MOST IMPORTANT ENVIRONMENTAL ISSUES FACED BY MINE SITES. SO HOW DO MINERS DEAL WITH IT? EWEN HOSIE WRITES.
Acid and metalliferous drainage (AMD) can be a big problem for mine sites. Also known as acid mine drainage or acid rock drainage (ARD), it is an environmental issue that requires considerable preparation to prevent.
In May, the Northern Territory Supreme Court found that the NT Primary Industry and Resources Department had failed to effectively monitor the former Frances Creek iron ore mine site owned by Territory Resources (formerly Territory Iron). This situation resulted in groundwater contamination and the seepage of acid water into Jasmine Creek, with clean up costs pegged at $20 to $30 million.
The NT Government had attempted to increase the site’s rehabilitation bond from $5.4 million to $18 million retroactively, which was challenged successfully by Territory Resources due to the government’s failure to sufficiently monitor the operations.
But what is AMD, and how does it cause damage? In essence, it is initiated by the oxidation of sulfide minerals through exposure to the air. There are numerous sulfide minerals but one of the most common at many Australian mines and elsewhere is pyrite, a shiny yellow mineral that, under some conditions, breaks down to form sulphuric acid. The acid that migrates from the pyrite grain lowers the pH of water, making it capable of dissolving other minerals, which can lead to
Water turned red by AMD.
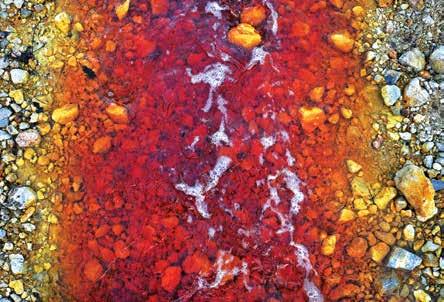
pollution. A telling sign of AMD in water streams is a yellow or reddish tint to water streams
“When exposed to elements such as oxygen and water, pyrite can oxidise and produce hydrogen ions, sulphuric acid, sulphate and ferrous iron,” explains Dr Jeff Taylor, an environmental geochemist and founding director of environmental consulting firm Earth Systems.
“In most places in Australia and certainly in eastern Australia the water table would certainly be located within the upper two to 10 metres of the Earth’s surface.
“As you drill down they find groundwater there and because all the sulfide minerals are submerged in water no air can get to them so that reaction doesn’t occur. But when you have a mine and dig a big hole in the ground, whether it’s an underground or an open cut mine, you’re digging out those minerals from underneath the groundwater table and exposing all of that sulphidic material to air.”
Waste rock piles are a prime source of acid at mine sites, with tailings material and pit walls serving as subordinate sources. Some natural minerals such as calcite and dolomite can help to neutralise this acid; when the pH levels are near-neutral but with elevated levels of salinity from dissolved metal sand sulphates, this is referred to as neutral metalliferous drainage (NMD).
“You either have AMD or NMD or sometimes you just have saline drainage, where only the sulphate from
the sulfide is present in the water — there’s just salinity there and no metals. It’s probably less harmful than acid metalliferous or neutral metalliferous damage but that salinity is a problem,” Taylor explains.
The worst areas for occurrences of AMD are regions with high rainfall. While Australia’s precipitation levels are generally quite low, there are still mines that have historical issues with AMD, such as the defunct Mt Lyell coppergold mine in Tasmania.
The mine, which was placed on care and maintenance in 2014 and is poised for an eventual restart under Indian-owned Vedanta Resources, has received criticism from the Tasmanian branch of the Environment Protection Authority (EPA) due to the damaging effects of its legacy tailings deposits on King River, Queen River and Macquarie Harbour.
Another notable abandoned mine in Australia known for its AMD issues is the Mount Morgan copper-gold-silver mine in Central Queensland, which turned the downstream Dee River blue following an overflow of the old gold mine caused by ex-tropical cyclone Oswald in 2013.
“Probably the worst areas in the world are the highest rainfall areas and I think in Australia that Tasmania is perhaps one of the worst with the Mt Lyell copper mine, which is no longer operating. Most of the acid is historical or legacy acid,” Taylor says.
“Coal mines in the Bowen Basin have salinity issues which are also related to AMD. If you could stop the AMD or oxidation of pyrite you could stop the salinity issues.”
Mine sites have various preventative measures in place to mitigate concerns surrounding AMD, with many government regulators requiring that there is an assessment made for the potential of acid metalliferous drainage as part of their permitting process.
It is important to reduce the access of oxygen to the sulfide minerals as soon as possible because sulfide mineral oxidation will start when the sulphides are exposed to oxygen. Therefore, effective sulfide mineral management strategies should be developed at the early stages of mine planning and implemented as the sulfide bearing wastes are produced.
The most effective method of controlling or preventing the occurrence of AMD is to prevent the sulfide mineral from making contact with oxygen, which requires considerable engineering.
One way this can be done is to place sulfide minerals underwater. Another is to cover the sulfide materials with an appropriate cover, with one example being a layer of highly saturated clay, where the water is provided by rainfall.
Synthetic variants such as geomembranes and geotextile fabrics can also be used, but these are expensive and since the areas that need to be dealt with can be very large they are less common than using clay and earthen materials, explains Dr Andrew Garvie, a principal consultant at SRK Consulting.
“An issue in Australia is that mines may not have adequate quantities of clay combined with an adequate rainfall that’s uniformly distributed throughout the year so coming up with an effective cover can take a reasonable amount of engineering in terms of design and construction,” he explains.
“Disposing of sulphidic material in subaqueous fashion is reasonably rare in Australia at early stages of mining, partially because there’s a lack of water in Australia compared to, say, Canada, where it is more common,” he explains.
“At the later stages of mining the sulphidic materials might be placed back inside the pit and the water levels in the pit may rise and inundate the sulfide bearing wastes, but a common approach in Australia is to cover the wastes with a solid material, often more waste that doesn’t contain sulphides.”
Garvie explains that this reintroduction of waste back into the pit after mining is completed has become more popular with mines in parts of Australia that don’t have enough clay or rainfall.
Miners who dewater earth in preparation for mining of a pit can reintroduce the problematic material to the pit once mining has ceased. After switching off their dewatering pumps, water levels would rise causing the material to become inundated.
“It’s not a new way of covering but it’s a way that people are now looking at addressing in some parts of Australia to address a lack of clay and rainfall,” Garvie explains.

The yellow-orange tint of the King River in Tasmania is the result of AMD caused by tailings from the abandoned Mt Lyell mine.