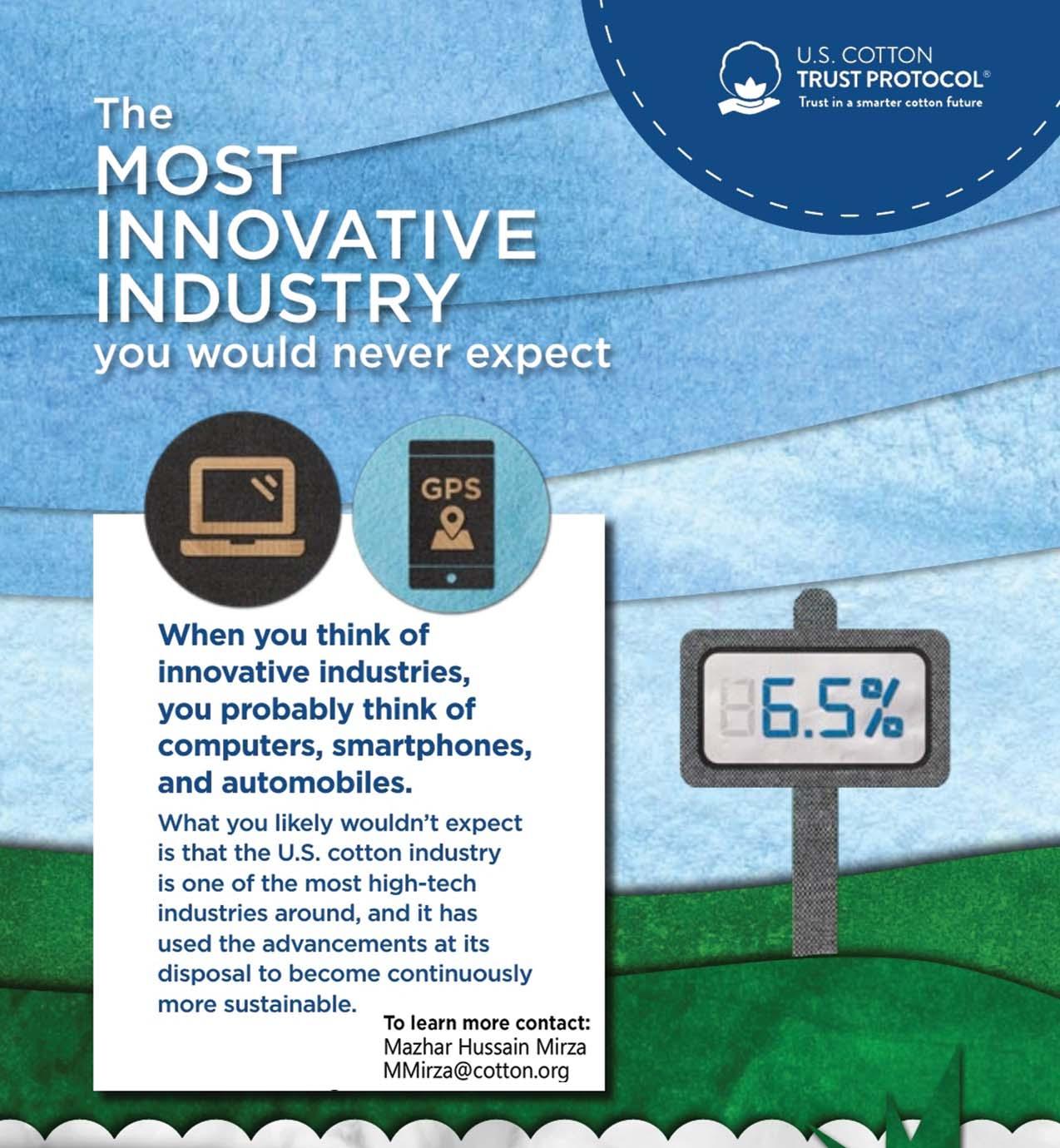



Dates: August 15th to 17th 2022. Venue: Shanghai, China.
Intertex Tunisia
Dates: October 6th to 8th 2022. Venue: Tunisia.
Istanbul Yarn Fair
Dates: February 16th to 18th 2023. Venue: Istanbul, Turkey.
DOMOTEX asia CHINAFLOOR 2022
Dates: August 31th to Sep. 2nd 2022. Venue: NECC, Shanghai, China.
JIAM 2022 OSAKA
Dates: Nov. 30th to Dec. 3nd 2022. Venue: Osaka, Japan.
FESPA 2023
Dates: May 23rd to 26th 2023. Venue: Munich, Germany.
Index 2023
Dates: April 18th to 21th, 2023. Venue: Palexpo, Geneva, Switzerland.
Dates: September 14th to 16th 2022. Venue: Dornbirn Austria.
INTEX SOUTH ASIA 2022
Dates: December 8th to 10rd 2022. Venue: New Delhi, India.
ITMA 2023
Dates: June 8th to 14th, 2023. Venue: Milan, Italy.
IGM 2022
Dates: September 8th to 6th 2022. Venue: Istanbul, Turkey.
IGATEX Pakistan 2022, Lahore
Dates: December 1st to 4th 2022. Venue: Expo Centre, Lahore.
ITMA ASIA + CITME 2023
iCADEX Pakistan 2022, Lahore
Dates: December 1st to 4th 2022. Venue: Expo Centre, Lahore.
Textile Asia 2022, Faisalabad
Dates: October 29th to 31th 2022. Venue: Quilim Marquee, Canal Road Faisalabad, Pakistan
Textile Asia 2023, Karachi
Dates: March 11th to 13th 2023. Venue: Expo Centre, Karachi.
DOMOTEX Hannover 2023
Dates: January 12th to 15th 2023. Venue: Hannover, Germany.
Dates: November 2023. Venue: NECC, Shanghai, China.
ITM 2024
Dates: June 6th to 8th, 2024. Venue: Istanbul, Turkey.
Founded in 1951 by Mazhar Yusuf (1924-2009)
Publisher Nadeem Mazhar
Editor in Chief Amina Baqai
Associate Editor Dr. Noor Ahmed Memon
Associate Editor Nimrah Nadeem
Associate Editor Shahnawaz Khan
Production Manager Mazhar Ali
Dr. Hafizur Rehman Sheikh Ph.D (UK) F.T.I. (UK)
Syed Mahfooz Qutab C.TEX, F.T.I (U.K), B.Sc. Fellow I.C.T.T Atlanta, GA; (USA)
Mian Iftkhar Afzal B.S.N.C State, M.Sc. (Leeds) C.TEXT.F.T.I (UK)
Dr. Zubair Bandukda PhD (Textiles), CText ATI
Editorial & Advertising Office B-4, 2nd Floor, 64/21, M.A.C.H, Miran M. Shah Road, Karachi - Pakistan
Tel: +92-21-34311674-5
Fax: +92-21-34533616
Email: info@ptj.com.pk
URL: http://www.ptj.com.pk
PTJ Europe Ltd.
Correspondence & Mailing address: PTJ Europe Ltd.
93 Fleming Place, Bracknell, RG12 2GN, United Kingdom
Tel: +44 792 2228 721
Registered Office: Dairy House, Money Row Green, Holyport, Maidenhead, Berkshire, SL6 2ND, UK
Registered no. 09141989
Available on Gale and Factiva affiliated international databases through Asianet Pakistan
Printed at: Color Plus Korangi, Karachi.
Published by Nadeem Mazhar from D-16, K.D.A. Scheme No.1. Karachi.
Vol. LXXI No. 07-08 July-August 2022 Rs. 565.00
EDITOR’S PAGE . . . . . . . . . . . . . . . . . . . . . . . . . . .7
Textile industry facing daunting challenges despite remarkable performance in 2022
TEXTILE BRIEFS . . . . . . . . . . . . . . . . . . . . . . . . . . .8
NEWS & VIEWS . . . . . . . . . . . . . . . . . . . . . . . . . .10
AROUND THE WORLD . . . . . . . . . . . . . . . . . . . . . .14
Forward-thinking and transparent communication keeps Loepfe ahead in delivery fidelity . . . . . . . . . . . . . . . . . . . . . . . . . . . . . . . . . . . . . . . . . . . . .18
Rieter continues to be successful in the market in the first half of 2022 . . . . .20
RGE spearheads initiative to develop first-of-its-kind urban-fit closedloop textile-totextile recycling solutions . . . . . . . . . . . . . . . . . . . . . . . . . . . . . . . . . . . . . .22
VDMA
Bräcker: ORBIT Ring-Traveler System . . . . . . . . . . . . . . . . . . . . . . . . . . . . . . . . .34
MS Printing & JK Group at FEBRATEX 2022 . . .
. . . . . . . . . . . . . . . . . . . .36
Novibra offers right spindle to make the difference . . . . . . . . . . . . . . . . . . . . . .38
U.S. Cotton: The U.S cotton industry most innovative industry . . . . . . . . . . . . . .40
Trützschler: The TCO 21: Boost your high-speed combing . . . . . . . . . . . . . . . . . .42
Record Sales at ITM 2022 Exhibition Bringing Textile Technology Leaders Together .44
Mimaki Eurasia: Advanced digital textile printing solutions . . . . . . . . . . . . . . .46
Jeanologia presents the fastest laser technology on the market at ITM 2022 . . .48 Baldwin’s sustainable TexCoat G4 finishing system . . . . . . . . . . . . . . . . . . . . .50
Glimpses of ITM 2022: International Textile Machinery Exhibition in Istanbul . . .52
The exports of textile commodities surged by 25.53pc during the fiscal year 2021-22 as compared to the corresponding period of last year.
The textile exports were recorded at $ 19,329.985m in July-June (202122) against the exports of $15,399.083m July-June (2020-21), showing growth of 25.53pc, according to the latest data released by Pakistan Bureau of Statistics (PBS). The textile commodities that contributed in trade growth included cotton cloth the exports of which increased by 26.91pc to $2,437.875m during the FY2022 as compared to the exports of $ 1,921m last year. The other commodities that witnessed growth in trade included cotton yarn, the exports of which grew by 18.67pc, from $ 1,016.970m to $ 1,206.838m and raw cotton by 714.94pc from 0.807m to $ 6.577m.
Exports of bed wear increased by 18.80pc, from $ 2,771.786m to $3,292.880m, towels by 18.54pc, from $ 937.533m to $ 1,111.334m, readymade garments by 28.75pc, from $ 3,032.812m to $ 3,904.658m, art, silk & synthetic textile by 24.20pc, from $ 370.417m to $460.061m, made up articles (excluding towels and bead wear) by 12.25pc, from $756.444m to $849.120m whereas the exports of all other export materials increased by 20.39pc, from $ 632.492m to $ 761.438m.
Despite this record breaking performance which has surpassed all expectations, the industry is facing challenges that are certain to hinder the growth and impact the future of the textile industry. Unprecedented flooding since July has destroyed almost half of of the cotton crop which will result in severe shortage of the raw material in the near future. Pakistan is the 5th largest cotton producer in the world and the destruction of the cotton crop will definitely impact the global cotton prices as the demand will surge with the increasing shortage of cotton.
Dwindling foreign exchange reserves and severe restrictions on the opening of the letters of credit have impeded the imports of machinery and raw material needed to run the industry.
According to Asif Inam, Chairman All Pakistan Textile Mills Association South Zone, the textile sector is facing a severe liquidity crunch, as well as issues of the opening letters of credit, as banks are reluctant to issue the necessary guarantee documents for the import of spare parts, machinery and raw materials. He pointed out that the issues were worse for the spinning sector, with units being closed down.
Increase in the energy cost and the gas crisis have contributed to almost unmanageable high cost of production. When coupled with the shortage of the record breaking flooding, destruction of the cotton crop, depleting foreign exchange reserves, and the global slowdown, the situation looks bleak and needs political and economic stability and the will to address these daunting challenges.
Ambassador of Denmark to Pakistan, said that Denmark is ready to provide new technology to Pakistan’s textile sector specially to knitwear sector to reduce export product production cost and improve the quality in Pakistan.
2Pakistan Hosiery Manufacturers Association, said that the industry would face losses due to an additional 10 pc super tax and they would close down. He said that the government had already increased the price of electricity and gas by 30-40pc.
1Lis Rosenholm3Patron in Chief All Pakistan Textile Mills Association (APTMA)
Dr. Gohar Ejaz in his statement has indicated that the Pakistan Textile Industry is expecting a notable increase in exports during FY23 with a growth rate above 20 percent given that the Government continues with the Policy of ‘Regionally Competitive Energy Tariffs’ for exports.
4Pakistan’s trade deficit ballooned to an all-time high of $48.66 billion in the outgoing fiscal year from $30.96bn a year ago, indicating an increase of 57 per cent on the back of
higher-than-expected imports, as per provisional official data released recently.
5The monsoon rains have improved the outlook for major summer (Kharif) crops as water has become available for plantations.
1The Australian Cotton Conference will begin on August 16. The conference will be hosted by Cotton Australia and the Australian Cotton Shippers Association. With the theme #HEREFORGOOD, delegates can expect to be informed and challenged by a range of technical and non-technical topics that puts Australian cotton at the cutting edge of agriculture.
2Azerbaijan increased its non-oil exports by $280.6 million, or 30.9 percent, in January-May of 2022.
3In an exclusive interview with Dhaka Tribune’s Saddam Hossain, Júlio Cézar Busato, chairman of the Brazilian Association of Cotton Growers (ABRAPA), speaks
about Brazil's intention to increase their cotton export to Bangladesh
4Egyptian exports to Brazil increased over three times from $155 million in 2017 to $541 million in 2021, as the FTA agreement provided access to many strategic goods at competitive prices.
With Bangladesh likely to approve commercial cultivation of genetically modified (GM) Bt cotton varieties sourced from an Indian company soon, seed manufacturers in the country have urged regulatory approval of the new generation of herbicide tolerant Bt (HTBt) cotton varieties whose application is pending with Genetic Engineering Appraisal Committee (GEAC).
exports to Afghanistan saw a deeper drop since the Taliban took control of Kabul in August 2021, the government took a major decision to allow trade of all products to Kabul in the rupee via land routes owing to the nonavailability of tradable currency through banking channels.
7Despite being in the sweet spot on the notable depreciation of the Pakistani rupee (PKR) against the US dollar, the textile exports will likely witness a loss of $1 billion in July 2022 due to the gas closure and Eid holidays.
least 300 textile mills have been closed, said All Pakistan Textile Mills Association (APTMA)
Chairman Abdul Rahim Nasir, amid severe energy crunch and subsequent suspension of gas supply in the country.
earnings from home textile exports maintained robust growth in the past two financial years .Exporters said that Bangladeshi manufacturers gained the confidence of global buyers by keeping production uninterrupted during the Covid outbreak in 2020
7According to the estimate of the China Chamber of Commerce for Import and Export of Textiles, the scale of China’s textile and apparel order transfer was about 6 billion US dollars in the first half of 2020, of which the cotton textile order transfer scale was about 1 billion US dollars.
8Union minister Piyush Goyal emphasized the need to introduce
“advanced technologies and innovative agronomy” to enhance the productivity of cotton. Addressing an interactive meeting with the Textile Advisory Group in Mumbai, the textile minister said the supply of good quality seeds is a vital necessity for improving the productivity of cotton.
Export Finance has signed a GBP 66 million (US$80m) deal to support the construction of four new garment factories in Aqaba, Jordan.UK Export Finance (UKEF) announced the deal yesterday, aimed at facilitating the construction of four factories for Classic Fashion Apparel Industry Group.
Pakistan to see over 20% growth in exports: APTMA
Patron in Chief All Pakistan Textile Mills Association (APTMA) Dr. Gohar Ejaz in his statement has indicated that the Pakistan Textile Industry is expecting a notable increase in exports during FY23 with a growth rate above 20 percent given that the Government continues with the Policy of ‘Regionally Competitive Energy Tariffs’ for exports.
this year from the USA and Brazil. Pakistan’s cotton imports are on the rise again. After importing just 3.1 million bales of 170 kg during the first nine months, over 1.1 million bales made their way through ports of entry during April and May 2022.
Textile Industry has posted record exports of $4 billion in FY22 with its expansion and investment plans of about $5 billion under LTFF and TERF schemes –YOY growth of 25 percent up till June 30, 2022. Earlier, APTMA stated that the growth was only possible due to the supply of energy at regionally competitive tariffs.
Currently, textile is the only sector that continues to grow and bring foreign exchange to the country, gearing up to close at $20 billion in June 2022 compared to $15.4 billion in June 2021. In addition, Pakistan Textile Industry plans to import 6 million bales of cotton
In April, APTMA reported that the overall cotton area in this decade has declined by 33 percent from 2.9 million hectares to 1.9 million hectares. Almost 1.5 million farmers grow cotton out of which 75 percent is grown in Punjab while the rest is grown in Sindh, while the cotton area in Punjab has decreased by 50 percent from 2.53 million hectares (2012) to 1.28 million hectares (2022).
In Pakistan, Cotton yields have fallen by 26 percent from 880 kgs/hectare to 652 kgs/ hectare over the last 10 years, while in Punjab the decline has been more pronounced and productivity has fallen by 36 percent from 814 kgs per hectare (2012) to 520 kgs per hectares (2022). Therefore, APTMA had advised the government to announce at least Rs 7,000 per mound MSP of putti, which will not only enhance yields but also the acreage sown. A delay in the announcement of the minimum support price (MSP) of cotton for 2022-23 will result in a significant loss in cotton production which will again lead to importing cotton of billions of dollars.
Lis Rosenholm, Ambassador of Denmark to Pakistan, said that Denmark is ready to provide new technology to Pakistan’s textile sector, especially the knitwear sector, to reduce the export product production cost and improve the quality in Pakistan.
In this regard, joint ventures with major Denmark companies will also be encouraged. She said this while addressing a meeting at the office of the Pakistan Hosiery Manufacturers and Exporters Association.
He said that the main purpose of her visit was to further enhance trade relations between the two countries and for this she would encourage Denmark businessmen to visit Pakistan.
She said she would tell Denmark businessmen that Pakistan is a very peaceful country to do business and safe to invest in. She said that she would also ask her Commercial Consul to pave the way for enhancing contacts between Pakistani and Denmark businessmen.
Industrial organizations have expressed concern over the imposition of a 10pc super tax on industries. Chaudhry Salamat Ali, patron-in-chief of the Pakistan Hosiery Manufacturers Association, said that the industry would face losses due to an additional 10pc super tax.
He said that the government had already increased the price of electricity and gas by 30-40pc while the mark-up rate was increased to more than 13pc, which made it impossible for the local and export industry to continue the business.
Pakistan Hosiery Manufacturers Association (North Zone) Chairman Mian Kashif Zia said the corporate sector was already paying 29pc tax and the imposition of the additional super tax would hurt it badly. “The tax hike would make it difficult for the industry to maintain global competitiveness,” he maintained.
Rana Zahid Tauseef, former chairman of the Pakistan Textile Exporters Association, said industries that were running a bit would shut down after the super tax.
“The government is forcing those who are paying taxes not to pay taxes at all. It should first bring those who are not paying taxes into the tax net,” he suggested. Atif Munir Sheikh, president of the Faisalabad Chamber of Commerce and Industry, said the government had disappointed the industry by presenting a new mini-budget in the name of super tax before the annual budget. “The move will not only slow down the performance of the industrial sector but also lead to a dramatic increase in inflation,” he added.
Pakistan’s trade deficit ballooned to an all-time high of $48.66 billion in the outgoing fiscal year from $30.96bn a year ago, indicating an increase of 57 percent on the back of higher-than-expected imports, provisional official data showed on Saturday. The trade deficit reached such an alarming level despite a ban imposed on more than 800 items in May. The coalition government’s battle against a bloated trade gap has failed to produce the desired result as it widened by 32.3pc to $4.84bn in June from $3.66bn a year ago. It was largely driven by an almost double increase in imports compared to exports.
The outgoing fiscal year’s trade deficit has crossed the $37bn figure of 2017-18, which was mostly led by imports related to the China-Pakistan Economic Corridor. In the subsequent years, the trade gap dropped to $31.8bn in 2018-19 and then further to $23.2bn in 2019-20 before bouncing back to $30.8bn in 2020-21 and then a whopping $48.664bn in 2021-22. The outgoing year’s trade deficit is propelled by the highestever increase in oil prices and commodities in the international market.
The trade deficit has been on the rise owing to an unprecedented increase in imports due to a rise in global commodity prices, while exports stagnated at around $2.5bn to $2.8bn a month, mostly those of semi-finished products and raw materials. The trade deficit came in at $4.04bn in May and $3.78bn in April, which indicates that no let-up was seen in monthly deficits when former prime minister Imran Khan was ousted in April through a vote of no confidence in parliament.
The widespread monsoon rains have improved the outlook for major summer (Kharif) crops as water has become available for plantations. The recent rainfall has provided the required water to kick-start the sowing of major Kharif crops including cotton, paddy (raw rice), sugarcane, and maize, which were delayed earlier by almost a month because of water scarcity.
“There was 40% less water available for the Kharif season (during May-June 2022),” an official of the Ministry of National Food Security and Research said while talking to the media. The highpowered Federal Committee on Agriculture (FCA) said on March 31, 2022 “for the Kharif year 2022, the water availability in canals head will be 65.84 million acre-feet (MAF) against last year’s 65.08 MAF”.
“Cotton production is expected to improve to 9.5-10 million bales (one bale
weighs 170 kg) in the wake of ongoing rainfall in cotton belts in Punjab and Sindh,” said Pakistan Central Cotton Committee Vice President Dr. Muhammad Ali Talpur.
“Cotton production will remain high, as farmers have improved crop management in the backdrop of higher prices in the domestic (and international) market.” However, the output will remain lower by 5-10% compared to the initial production target of 10.5 million bales of cotton due to sowing over less-thantargeted areas across the country. Farmers have started the first round of picking seed cotton – raw cotton containing seed and lint – in southern Sindh. They are yet to harvest the crop in northern Sindh and Punjab. “Low water availability, however, has delayed the second round of cotton production,” said Sindh Abadgar Board Vice President Syed Mahmood Nawaz Shah last week. Cotton is a water-sensitive crop, which may be damaged in heavy showers. “The crop cannot survive if the rainwater stands in the fields for over 24 to 48 hours,” Talpur concluded.
Despite being in the sweet spot on the notable depreciation of the Pakistani rupee (PKR) against the US dollar, the textile exports will likely witness a loss of $1 billion in July 2022 due to the gas closure and Eid holidays. According to the news report, the sector will not be provided gas from July 1, 2022, to July 8, 2022.
Meanwhile, textile units will observe another shut down on the back of the upcoming Eid holidays.
As a result, the sector which contributes more than 60% to the total exports of Pakistan will face daunting challenges to
complete the export orders on time. The consequences of the decline in exports are not limited to only the company’s profitability and competitiveness but it will force the cash-strapped government to borrow more dollars to fund the current account deficit.
After touching a record high level in April 2022, Pakistan’s textile exports witnessed a fall of 5.6% in May 2022 to $1.64 bn owing to insufficient availability of LNG/Gas to the sector.
In addition to it, the government has not yet settled the rate of the Regionally Competitive Energy Tariffs (RCETs) for the fiscal year 2023 which also requires to be settled at the earliest to maintain the regional competitiveness of the sector in the international market.
Industry players are of the view that the unprecedented situation demands the government’s immediate attention otherwise the sector will have to suffer unbearable losses.
Muhammad Jawed Bilwani, Chairman of Pakistan Apparel Forum brought this matter to the attention of Prime Minister Shehbaz Sharif and said, “In contradiction to the government's Textile & Apparel Policy 2020-2025, the economic team has not considered for continuation RCETs despite repeated requests and appeals by the Value-Added Textile Export Industry of Pakistan during submission of their pre-budget and postbudget proposals for FY2023.”
He added that it is highly important to ensure a level playing field for Pakistani textile exporters to enable them to compete regionally and globally by reducing and bringing at par the cost of manufacturing with the regional competing countries.
In this connection, the continuation of competitive energy tariffs is highly inevitable and crucial for the sustainability and enhancement of exports.
Further, the utility tariff (power and water), as well as the exchange rates of US Dollar and Euros, should also be fixed for exporters with regards to import of export industries to manufacture goods meant for export.
At present, exporters are unable to negotiate new export orders due to extreme uncertainty about the cost of manufacturing to produce export goods.
Pakistan’s textile exports increased by 25.5 percent during the fiscal year 202122 (FY22) and stood at $19.35 billion compared to $15.42 billion in the fiscal year 2020-21 (FY1). The textile exports increased by 4.2 percent on a year-onyear (YoY) basis to $1.73 billion in June 2022, compared to $1.66 billion during the same period last year.
Similarly, textile exports increased by 5.5 percent to $1.73 billion in June 2022, compared to $1.64 billion in May 2022. According to data released by the Pakistan Bureau of Statistics (PBS), the country’s total exports increased by 25.51 percent and stood at $31.760 billion in FY22, compared to $25.304 billion during the same period of FY21.
Further, exports registered 5.83 percent growth on a year-on-year basis and increased from $2.758 billion in June 2021 to $2.887 billion in June 2022.
According to a research report by the All Pakistan Textile Mills Association (APTMA), textile exports in FY22 have increased by 57 percent compared to
$12.3 billion in FY12 and 43 percent compared to FY18.
At least 300 textile mills have been closed, said All Pakistan Textile Mills Association (APTMA) Chairman Abdul Rahim Nasir in a press conference, amid a severe energy crunch and subsequent suspension of gas supply in the country. Earlier this week, Pakistan sought more gas imports on deferred payments from Qatar to restore gas supply to the textile industry on an urgent basis. Nasir said a 26 percent upsurge in the export of textiles during the fiscal year 2021-22 was made possible only due to the supply of energy at a regionally competitive tariff, stressing a loss of almost USD 1 billion in exports has already been incurred, according to sources.
The exponential growth in the textile sector has promoted investment of over USD 5bn and the establishment of 100 new textile units, which, after becoming operational, would result in fetching additional exports of USD 6.0bn per
annum, Media reported, quoting the Vice-Chairman. Elaborating the detail on what could have majorly caused the loss, the APTMA chairman explained that gas supply to the industry was suspended for a week, which led to the large-scale closure of mills that ultimately resulted in massive layoffs and unemployment.
Meanwhile, APTMA North Zone Chief Hamid Zaman stressed that the textile sector has repeatedly delivered on its commitment to enhancing exports, proving they are a viable and long-term solution provider for the economic stability of the country, according to media. “If this momentum is lost due to energy supply and cost constraints, Pakistan will be forced to seek an additional USD 6bn in loans from abroad, which under the circumstances may not even be possible,” he said, underlining the immediate restoration of gas supply to the export-oriented industry, as media quoted. Quetta, Peshawar, Gujranwala, Multan, Faisalabad, Mirpurkhas, and other cities in Pakistan are reportedly suffering from a gas shortage, according to sources. Not only residents but owners of hotels and restaurants are also complaining of a gas shortage, as it is hurting their business.
The Australian Cotton Conference unveils program with the theme #HEREFORGOOD, delegates can expect to be informed and challenged by a range of technical and non-technical topics that puts Australian cotton at the cutting edge of agriculture, at the Australian Cotton Conference that will begin on August 16. The conference will be hosted by Cotton Australia and the Australian Cotton Shippers Association.
A holistic and considered program of expert (and entertaining) speakers drawn from inside and outside cotton, cuttingedge research and innovation, practical advice, and good old-fashioned conversation, will engage and inspire delegates from the farm, right along the cotton supply chain.
The conference will host sessions on topics such as opportunities for carbon and nitrogen farming, developments and opportunities for smart sensing in cotton, doing business differently, tax issues for carbon farming, measuring the social wellbeing of the cotton industry in Australia, smart sensing and automation, taking cotton’s pulse in the market, driving WUE by replacing flood systems with simple low-cost drip and such others, the case for changing our understanding of temperature responses of cotton, Bayer Crop Science cotton pipeline, and research priorities, moving the farm to carbon energy neutrality, Fish entrainment: A mitigation prioritization process, the organizers said.
Azerbaijan increased its non-oil exports by $280.6 million, or 30.9 percent, in January-May of 2022, Media reports per the June export review of the Center for Economic Reforms Analysis and Communication of Azerbaijan.
In the first five months of the year, Azerbaijan’s exports totaled $15.4 billion, including $1.2 billion in the non-oil
sector. Fruit and vegetable production increased by 6.4 percent to $219.2 million compared to January-May 2021.
The cotton yarn came in first with $123.7 million in non-oil exports, followed by tomatoes with $91 million and carbamide with $84.1 million.
Turkey ranked first with $390.2 million in non-oil product exports in January-May, followed by Russia with $263.4 million and Georgia with $74.7 million.
(CBRA), the Brazilian cotton fiber is highly traceable, contamination-free, and of high quality.
Egypt is actively engaged with Brazil to boost bilateral trade in various sectors including textiles. The free trade agreement (FTA) between Egypt and the Mercosur countries (Argentina, Brazil, Paraguay, and Uruguay), which entered into force in 2017, plays a pivotal role in promoting trade between Egypt and Brazil. Exports have jumped three times since the FTA.
In an exclusive interview with Dhaka Tribune’s Saddam Hossain, Júlio Cézar Busato, chairman of the Brazilian Association of Cotton Growers (ABRAPA), speaks about Brazil's intention to increase their cotton export to Bangladesh
As of now, Brazil is the second-largest exporter in the market and the fourthlargest cotton producer globally. Undergoing the industry-standard laboratory HVI testing by partnering laboratories such as the Brazilian Reference Center for Cotton Testing
There are distinguished investment opportunities for the Brazilian business community in the Egyptian market in the areas of the manufacture of textile, spare parts, pharmaceuticals, engineering, along with new and renewable energy, Egyptian minister of trade and industry Nevine Gamea said at an event of ArabBrazilian Economic Forum, which she attended virtually.
The FTA between Egypt and Mercosur countries contributed to increasing the competitiveness of Egyptian exports and enhancing its access
Brazilian cotton is produced under best sustainability practices
not only to Brazil but to all Mercosur countries, given that the Brazilian market remains a focal point in the penetration and marketing of goods to neighboring countries, the minister added.
After the FTA entered into force, Egyptian exports to Brazil increased over three times from $155 million in 2017 to $541 million in 2021, as the agreement provided access to many strategic goods at competitive prices.
The FTA also encouraged the export of Egyptian apparel and home textile products to Brazil. Egypt’s apparel exports to Brazil were just $0.944 million in 2017, which increased to $2.281 million in 2020 and $2.249 million in 2021, according to media sources. Inhome textiles, Egypt’s exports to Brazil were valued at $1.158 million in 2017, which increased to $3.507 million in 2020 and $9.223 million in 2021, as per sources.
With Bangladesh likely to approve commercial cultivation of genetically modified (GM) Bt cotton varieties sourced from an Indian company. The seed providers in the country have urged regulatory approval of the new generation of herbicide-tolerant Bt (HTBt) cotton varieties whose application is pending with Genetic Engineering Appraisal Committee (GEAC).
According to Ram Kaundinya, director general, Federation of Seed Industry for India, the government has to go ahead with the deployment of modern GM technology urgently to cut down on the rising cost of pesticides and labor in cotton cultivation.
Home textiles shine as buyers shift orders to Bangladesh
Though Bangladesh’s earnings from home textile exports maintained robust growth in the past two financial years and the earnings posted the second highest amount in the just concluded financial year of 2021-22 as global buyers shifted their orders to Bangladesh from other manufacturing countries, including Pakistan.
Exporters said that Bangladeshi manufacturers gained the confidence of global buyers by keeping production uninterrupted during the Covid outbreak in 2020.
Though Pakistan is the leader of home textiles on the global market, the country lost some of its buyers
during the global outbreak pandemic due to the factory closure. Exporters said that buyers also shifted orders for home textiles from China and Turkey as factories remained closed in the countries due to the pandemic.
In the just concluded fiscal, the home textile sector remained the second highest export earning sector after the readymade garment sector.
Chinese textile industry suffers profit erosion, orders flow to Vietnam and India
Chinese textile industries suffered profit erosion throughout the pandemic period and will continue to bear the loss due to rising raw material prices.
The report revealed that since the onset of 2020, the textile industry has been experiencing massive losses as the industry is unable to raise product prices due to the pandemic. Moreover, orders are 40 percent lower than last year.
According to the estimate of the China Chamber of Commerce for Import and Export of Textiles, the scale of China’s textile and apparel order transfer was about 6 billion US dollars in the first half of 2020, of which the cotton textile order transfer scale was about 1 billion US dollars.
stakeholders including the government, research institutes, and the industry.
For delivery-based contracts and open position limits on commodity exchange MCX, Goyal directed his ministry, textile commissioner, CCI, and TAG to engage with MCX/SEBI and find structured solutions on the contract front.
Any possibilities of manipulations on the price front to the disadvantage of the cotton textile value chain have to be contained, the minister concluded.
The trade deficit widened last month as the country’s purchases of goods from abroad significantly outpaced the rise in sales of locally-made products, putting more pressure on the local currency to further depreciate against the US dollar.
The Philippine Statistics Authority (PSA) reported recently that the country’s trade gap, or the difference between the value of export and import, reached $5.68 billion, up 78 percent from $3.18 billion in May last year.
Month-on-month, the trade deficit also rose by six percent from $5.35 billion in April. In the first five months of the year, the trade deficit reached P24.92 billion, higher by 70 percent compared with P14.62 billion in the same period in 2021.
UK Export Finance has signed a GBP 66 million (US$80m) deal to support the construction of four new garment factories in Aqaba, Jordan.
UK Export Finance (UKEF) deal is aimed at facilitating the construction of four factories for Classic Fashion Apparel Industry Group, which include three satellite manufacturing units, enhancing Jordan’s textile industry.
Classic Fashion supplies a wide range of products including activewear, outerwear, denim, twill, formal pants and work-wear. Previous customers include Under Armour, Walmart, HanesBrands, Lands’ End, One Jeanswear Group, American Eagle Outfitters and Gap.
It produces around 550,000 garments per day and contributes to over 42% of all garment exports from Jordan, says UKEF. The company produced 130 million garments in 2021 and expects production to grow to 165 million garments this year.
The UKEF is providing support through a combination of direct lending and a buyer credit guarantee, allowing Classic Fashion to move quickly with its project and benefit from its flexible repayment terms.
Union Minister Piyush Goyal emphasized the need to introduce “advanced technologies and innovative agronomy” to enhance the productivity of cotton. Addressing an interactive meeting with the Textile Advisory Group in Mumbai, the textile minister said the supply of good quality seeds is a vital necessity for improving the productivity of cotton.
He also called for a focus on ways to enhance the productivity of cotton with specific outcome-oriented actions from all
South Africa’s major fashion retailers want to source fabrics locally after relying on cheaper imports from China which crippled the country’s once-thriving farmers and producers.
Cotton fabric has a rich history in South Africa. Farmers, producers, designers, and retailers all benefited from the thriving local textile industry, but that all changed in the late 1990s when South Africa opened to trade with China.
The new planned site, located in Aqaba Special Economic Zone, is expected to create around 4,000 jobs for Jordanians by 2024. Jobs for the local community are offered at varying levels, with the potential to grow and the opportunity to enter the business of garment manufacturing. The location is near Aqaba port, giving Classic Fashion an exporting advantage.
The project will contribute to boosting manufacturing exports and jobs, in line with the targets for the sector contained in Jordan’s recently launched Economic Modernisation Vision 2033.
Classic Fashion Apparel Industry chairman and managing director Sanal Kumar said: “Classic Fashion is
India needs innovative agronomy to enhance cotton production
Fashion retailers prefer domestic fabrics – reviving sectors crippled by Chinese imports
committed to giving its best to the deserving people in the rural areas of Jordan,” adding that it would focus on vertical expansion, bringing SME units into open-source manufacturing excellence program, and efficiency enhancement.” British Ambassador to Jordan Ms Bridget Brind OBE said of the deal: “It will help create new jobs and increase exports, contributing to Jordan’s economic growth and future prosperity. I hope it can act as a success story which can inspire more similar agreements in the future for the benefit of Jordan and the United Kingdom.” UK Minister of State for Asia and the Middle East, Ms Amanda Milling MP, who is visiting Jordan as part of a regional visit welcomed the initiative and the opening of a new apparel and textiles factory in Aqaba. The UK’s support will extend beyond the funding scheme, as more than 30% of the services and supplies for the project, such as machinery and other building materials, will come from directly from UK providers.
The U.S. 2022/23 cotton projections show lower production, exports, and ending stocks compared with last month. While the June 30 Acreage report shows nearly 250,000 additional acres planted than in the previous NASS survey, the harvested area is forecast nearly 600,000 acres lower this month.
Continued below-average precipitation - primarily in Texas - means abandonment is projected higher this month, nearly 4 times the previous year’s level. U.S. production is projected one million bales lower than in June, at 15.5 million.
U.S. exports are also projected lower, down 500,000 bales to 14.0 million reflecting both lower U.S. production and a reduction in world trade. At 2.4 million bales, 2022/23 U.S. ending stocks are now expected to be 1 million bales lower than in 2021/22.
Despite daily reports of global supply chain issues, Loepfe Brothers Ltd. rise above market uncertainty to continue exceeding customer expectations. Loepfe, positioning itself for future growth, has made several key strategic moves to allow them to continue its mission to champion customer-centricity.
Loepfe report that committed customer orders are being delivered on time, making them a reliable partner within the very uncertain business environment. Loepfe consider transparent communication and their collaborative approach with all the involved parties as main success factors.
Delays in international sourcing has been the downfall for many market players, however, Loepfe are committed to sourcing with a future vision to ensure that customer expectations can still be met. Clearing sourcing bottlenecks, holding increased stocks, and building closer working relationships with both new and existing suppliers, as well as customers, has allowed them to gain additional business against a challenging
procurement backdrop. Also, strengthening relationships with transport partners and increasing the use of air freight has helped Loepfe fulfil their commitments.
Further, Loepfe’s broad product range has played a crucial part. With more complete product families, they have the flexibility to use multiple products to fit the needs of the customer. The respective product components are sourced independently from long-standing suppliers, and product production runs in parallel thanks to successful recruitment and new employment models. Swissmade hardware quality along with the offering of software updates give products greater longevity and the ability to adapt to changing demands.
However, all these initiatives have come with higher cost pressure and increased capacities and have required a great level of dedication and flexibility from every individual in the Loepfe team and its partners. In an ever-changing landscape they recognize there is no room for complacency and remain committed to evolving their processes to
ensure customer satisfaction.
Dr. Ralph Mennicke, CEO of Loepfe Brothers Ltd. said: “We are delighted we have been able to fulfil our commitments to customers, old and new. We are constantly looking for innovative ways to retain our strong position. There are many pressures in the market right now, and our strong position has required a great deal of foresight, dedication, and troubleshooting. While full availability of all components in our complex sensor products cannot be taken for granted nowadays, we are making the utmost efforts to ensure transparency to our partners and to find solutions along the way that meet our customers’ needs. I’m grateful to every individual in our team who has helped to make this happen. We remain committed to our long-standing clients and look forward to welcoming even more new customers into the Loepfe world.”
Dr. Ralph Mennicke, CEO of Loepfe Brothers Ltd.
Rieter continued to be successful in the market in the first half of 2022. Based on the company’s technology leadership, innovative product portfolio and the completion of the ring- and compactspinning system, a high order intake and a significant increase in sales were generated. The increase in sales was achieved even though preproduced deliveries in the three-digit million range had to be postponed until the second half of 2022.
The order backlog is at a record level. Despite higher sales, the significant increase in material and logistics costs, additional costs for compensation of the material shortages and the expenditure incurred for the acquisition in the years 2021/2022 resulted in a loss.
Rieter is implementing an action plan to increase sales and profitability. The sales process for the remaining land owned by Rieter was initiated.
Rieter posted an order intake of CHF 869.4 million, which included CHF 176.6 million from the businesses acquired in the years 2021/2022. As expected, demand has thus returned to normal compared with the exceptionally high figure for the prior-year period, but remains well above the average figure for the last five years of around CHF 570 million (first half 2021: CHF 975.3 million, first half 2022 excluding acquisition effect CHF 692.8 million).
The regional shift in demand with investments in additional spinning capacity outside China along with investments in the competitiveness of Chinese spinning mills continues. Rieter benefits from its technology leadership, the innovative product portfolio and the completion of the ring- and compactspinning system through the acquisition of the automatic winding machine business. The largest order intakes came
from India, Turkey, China, Uzbekistan, and Pakistan.
On June 30, 2022, the company had an order backlog of more than CHF 2 100 million (June 30, 2021: CHF 1135 million). Cancellations in the reporting period amounted to around 5% of the order backlog.
The Rieter Group posted sales of CHF 620.6 million, which included CHF 68.9 million from the businesses acquired in the years 2021/2022 (first half 2021: CHF 400.5 million).
As a result, sales were significantly higher than in the prior-year period, although preproduced deliveries, which mainly affected the Business Group Machines & Systems, in the three-digit million range had to be postponed until the second half of 2022. The reasons for the postponements were the COVID lockdown in China and supply chain bottlenecks.
Rieter posted a loss of CHF -10.2 million at the EBIT level in the first half of 2022. Earnings were impacted by significantly higher material and logistics costs. The price increases already implemented are having a delayed effect, mainly in the Business Group Machines & Systems, and were therefore unable to compensate for the high increase in costs. In addition, costs in connection with material shortages negatively impacted profitability. The result also includes acquisition-related expenses of CHF -11.2 million.
The loss at the net result level was CHF -25.2 million, of which CHF -17.6 million was due to the acquisition.
Free cash flow was CHF -57.1 million, attributable to the build-up of inventories in connection with the high order backlog and postponed deliveries.
Rieter is implementing a comprehensive package of measures with the aim of increasing sales and profitability in the second half of 2022.
The package focuses on two main priorities: Firstly, Rieter is continuing to systematically implement price increases while working to improve the quality of margins of the order backlog, so as to compensate for cost increases in materials and logistics.
Secondly, Rieter is working closely with key suppliers and is developing alternative solutions to eliminate material bottlenecks, as far as possible, in order to safeguard deliveries.
The Board of Directors has decided to begin the process for the sale of the remaining land at the Rieter site in Winterthur (Switzerland). In total, around 75,000 m2 of land will be sold. The Rieter CAMPUS is not part of this transaction; the construction project is progressing according to plan.
As already reported, Rieter expects demand for new systems to normalize further in the coming months. Due to the
JanuaryJune 2021 Difference Difference adjusted1
Rieter 869.4 692.8 975.3 -11% -28%
Machines & Systems 579.3 455.4 714.8 -19% -36%
Components 180.9 143.9 154.9 17% -6%
After Sales 109.2 93.5 105.6 3% -10%
Order Intake CHF Million JanuaryJune 2022
JanuaryJune 2022 w/o acquisition
JanuaryJune 2021 Difference Difference adjusted1
Rieter 620.6 551.7 400.5 55% 39%
Machines & Systems 383.8 357.7 28.9 75% 63%
Corporate News Components 159.9 123.4 112.9 42% 12%
After Sales 76.9 70.6 69.2 11% 4%
capacity utilization at spinning mills, the company anticipates that demand for consumables, wear & tear and spare parts will remain at a good level.
For the full year 2022, due to the high order backlog and the consolidation of the businesses acquired from Saurer, Rieter expects sales of around CHF 1400 million (2021: CHF 969.2 million).
The reduced sales forecast compared to early 2022 (March 2022: CHF 1500 million) reflects the impact of global supply bottlenecks. The realization of sales revenue from the order backlog continues to be associated with risks in relation to the well-known challenges.
Despite significantly higher sales, Rieter expects EBIT and net result for 2022 to be below the previous year’s level. This is due to the considerable increases in the cost of materials and logistics, additional costs for compensation of material shortages as well expenses in connection with the acquisition in the years 2021/2022. Despite the price increases already implemented, global cost increases continue to pose a risk to the growth of profitability.
As market and technology leader, Rieter will benefit from the exceptionally high order backlog and the continuation of the regional shift of demand.
Royal Golden Eagle (RGE), a global group of resource-based manufacturing companies, which includes leading viscose fibre producers Sateri and Asia Pacific Rayon (APR), is developing urban-fit, closed-loop textile-to-textile recycling solutions, through the newlyformed RGE-NTU Sustainable Textile Research Centre (RGE-NTU SusTex).
This is a five-year research collaboration between RGE and Nanyang Technological University, Singapore (NTU), to accelerate innovation in textile recycling that can be deployed in urban settings. The research centre will develop new technologies to recycle textile waste into fibre and create new, nextgeneration eco-friendly and sustainable textiles.
This move comes on the back of the tightening of waste import bans in countries such as China, India and Indonesia, which are among the world’s largest waste processors. The stricter import bans have left cities in need of viable local textile recycling solutions to tackle the immense textile waste generated.
RGE Executive Director, Mr Perry Lim, said, “Current textile recycling technologies, which rely primarily on a bleaching and separation process using heavy chemicals, cannot be implemented due to environmental laws. At the same time, there is an urgent need to keep textiles out of the brimming landfills.” He added, “As the world’s largest viscose producer, we aim to catalyse closed-loop, textile to-textile recycling by developing optimal urban-fit solutions that can bring the world closer to a circular textile economy.”
Globally, an estimated 90 million tonnes of textile waste is generated and disposed of every year, with less than 1%
being upcycled into new clothing or other textile materials. By 2030, the amount of global textile waste, which currently accounts for almost 10% of municipal solid waste, is expected to reach more than 134 million tonnes. The textile industry is also responsible for 10% of global greenhouse gas emissions – more than international flights and maritime shipping combined.
At present, most of the available textile recycling technologies are openloop, where textile waste is typically downcycled to lower-quality products (insulating materials, cleaning cloths, etc.) or be used in waste-to-heat recycling.
“Closed-loop textile-to-textile recycling processes, particularly chemical recycling, are still under development. Scaling up the technologies to industrial scale remains a challenge. A key bottleneck is that refabricating textile waste into fibre needs purity standards for feedstock. However, most of the clothes that we wear are made of a mixture of different synthetic and natural
fibres, which makes separating the complex blends of materials challenging for effective recycling.
“Our aim is to address this industry pain point by developing viable solutions that use less energy, fewer chemicals and produces harmless and less effluents, and then potentially scale up across our global operations,” Mr Lim said.
To tackle the key challenges in closed-loop textile recycling, RGE-NTU SusTex is looking into four key research areas, namely cleaner and more energy efficient methods of recycling into new raw materials, automated sorting of textile waste, eco-friendly dye removal, and development of a new class of sustainable textiles that is durable for wear and, at the same time, lends itself to easier recycling.
Technologies developed by RGE-NTU SusTex will be test bedded at RGE’s pilot urban-fit textile recycling plant in Singapore, which is projected for completion as early as 2024. If successful, RGE has plans to replicate the plant in other urban cities within its footprint.
Archroma, a global leader in specialty chemicals towards sustainable solutions, launches Smartrepel® Hydro SR liq, a new PFC-free* technology for the repellence of water-based stains.
The innovation has been developed in line with the principles of “The Archroma Way to a Sustainable World: Safe, efficient, enhanced, it’s our nature”.
Smartrepel® Hydro SR liq is the latest addition to a range of microencapsulated, highly biodegradable, non-PFC based technology offering exceptional, durable water repellency to all cotton and synthetic fibers, and their blends.
The new Smartrepel® Hydro SR liq has been specifically developed for soil
repellent finishes aiming to offer industryleading protection against water-based stains such as coffee, red wine and ketchup, in applications such as home textiles, table clothes upholstery, car seats and interior textiles.
The new grade offers the signature Smartrepel® high performance standard: a perfect symbiosis of water protection, soil repellence, breathability and durability – with the soft hand-feel that is sought after by consumers.
The Smartrepel® product range supports the increasing adoption of ecoadvanced materials and production processes by textile producers and brand owners adhering to standards such as ZDHC, bluesign and Oeko-tex.
Smartrepel® Hydro SR liq at the core of the new SAFE SEATS NextGen system, was also launched at Techtextil.
Roland Borufka, Head of Competence Center Repellents at Archroma, comments: “Archroma creates innovations that help make end-articles that are safe, efficient and enhanced. We are therefore very proud of the new addition to our Smartrepel® series. With this, we bring a durable repellence solution for water-based stains, one that is not only PFC free* but is also showing industry-leading performance. Because it’s our nature.”
* Below limits of detection according to industry standard test methods.
Archroma to introduce new PFCfree* Smartrepel® technology for durable water-based soil repellence.Bluesign has teamed up with Sustainable Chemistry for the Textile Industry (SCTI™) to develop a sustainable chemistry index that will provide a standard communication guide for chemical suppliers, manufacturers, brands, and NGOs
The first-of-its-kind index is intended to inspire change in the industry by making it easier for stakeholders to assess the sustainability of textile chemical products against the highest standards while safeguarding the intellectual property (IP) of participating chemical companies. IP protection is critical to ensuring ongoing investment in sustainable solutions.
SCTI™ is an alliance of leading chemical companies that strives to empower the textile and leather industries to apply sustainable, state-of-
the-art chemistry solutions that protect factory workers, local communities, consumers and the environment.
Bluesign will implement and manage the sustainable chemistry index as an independent authority with a holistic approach to help companies throughout the textile supply chain improve their sustainability performance.
Chemical products, such as dyes and textile auxiliaries, are often characterized with the attribute of “free of a certain substance.” Rather than prioritizing ingredients only, the bluesign® SYSTEM already goes beyond this. The chemicals and the production site where they were created must meet certain criteria regarding environmental performance,
occupational health and safety, and product stewardship performance to be bluesign® APPROVED.
The sustainable chemistry index will be reserved for substances that offer transparency on a number of additional indicators including the chemical’s circularity viability, greenhouse gas emissions during production, and the source of the raw materials. The sustainable chemistry index will also require that the downstream use of the chemical is optimized, meaning, for example, that it promotes resource saving in textile finishing. Additionally, excellent corporate governance paired with welldefined environmental and social (ESG) goals will be a pre-condition.
Dr. Wolfgang Anton Schumann, SCTI™ Chairman, said: “Through its independent position, Bluesign has earned the industry’s trust to provide sustainable chemical solutions and impact reductions across the supply chain for the past two decades.This partnership exemplifies our organizations’ joint expertise and how collaboration creates solutions that can drive meaningful change across an industry to reduce impact on people and our planet.”
Daniel Rüfenacht, Bluesign CEODaniel Rüfenacht, Bluesign CEO, added: “SCTI™ offers deep sustainability knowledge in the chemical industry. The new sustainable chemistry index will help the industry progress beyond current regulations and realize the EU Chemicals Strategy for Sustainability by providing textile chemical users a clear rating on a substance’s environmental and social impact to advance decision-making”.
The mission for the joint partnership between Bluesign and SCTI™, and the sustainable chemistry index in particular, is to drive transformational change through sustainable chemical solutions. Providing textile and apparel industry players with a verified inventory of sustainable chemical products is a first step on this shared journey.
Online visitor registration for ITMA ASIA + CITME 2022, Asia’s leading business platform for textile machinery, is now open. Visitors who pre-register online on the combined show websites (itmaasia.com and citme.com) before 19 November will enjoy special badge rates at a 40% discount.
The early-bird rates are RMB 60 (US$9) for a five-day badge and RMB 30 (US$5) for a one-day badge. Standard onsite rates are RMB 100 for a five-day badge and RMB 50 for a one-day badge.
The 8th combined exhibition will be held from 20 to 24 November 2022 at the National Exhibition and Convention Centre, Shanghai. According to its show owners - CEMATEX and Chinese partners comprising the Sub-Council of Textile Industry, CCPIT (CCPIT-Tex), China Textile Machinery Association (CTMA) and China Exhibition Centre Group Corporation (CIEC) – the combined show has received a favourable response from the industry.
Since space application was launched 10 months ago, many exhibitors have responded positively, displaying strong
confidence in the combined show, and enthusiasm for a face-to-face exhibition.
To date, it has attracted some 950 textile and garment machinery manufacturers from 21 countries and regions to apply for space. Among the international names who will be represented at the combined show are: CHTC, Dornier, Eltex, Epson, Fil Control, Fong’s, Groz-Beckert, Itema, Jeanologia, Karl Mayer, Murata, Oerlikon, Picanol, Rieter, Shima Seiki, Stäubli, Toyota, Trützschler, Tsudakoma, Uster, Vandewiele, Vanwyk and Wira Instrumentation.
Grossing over 120,000 square metres, ITMA ASIA + CITME 2022 will be an exciting showcase of the latest technologies. Exhibits will occupy the following halls at the venue:
Hall 3 - knitting and weaving machinery.
Hall 4 - dyeing and finishing machinery.
Hall 5 - printing, garment and spinning machinery.
Hall 6 - spinning and nonwoven machinery, as well as chemicals other textile making machinery.
Mr. Ernesto Maurer, President of CEMATEX said: “Despite the setbacks caused by the coronavirus pandemic,
companies are finding ways to overcome the challenges. They are very eager to tap new opportunities provided by innovative technologies, especially those offering sustainable benefits and productivity gains.”
Mr. Gu Ping, President of China Textile Machinery Association added: “As part of China’s 14th Five-Year Plan, we endeavour to accelerate industrial upgrading and develop a more hightech-driven textile and apparel industry. The combined show will provide manufacturers with innovative solutions that will help them to be more competitive as the textile and garment industry embarks on its recovery path.”
ITMA ASIA + CITME is organised by Beijing Textile Machinery International Exhibition Co., Ltd and co-organised by ITMA Services. Japan Textile Machinery Association is a special partner of the combined show.
Mr. Gu Ping, President of China Textile Machinery AssociationAward winners with foundation chairman and professors.
The Chairman of VDMA’s Walter Reiners-Stiftung Foundation, Peter D. Dornier awarded prizes to seven successful young engineers during Techtextil fair in Frankfurt.
For the first time, the Foundation awarded two Sustainability Awards. They are awarded to academic works in which, for example, solutions for resource-saving products and technologies are developed.
A Sustainability Prize in the category Project Work, endowed with 3000 euros was awarded to Simon Hoebel, TU Dresden, for his thesis on recycled thermoplastic fibres for composite components.
Marina Michel, TU Dresden, received a Sustainability Award in the category Master, worth 3500 euros. The topic of her master thesis was the functionalisation of yarns for the filtration of micro- and nanoplastics from water.
Marina Andrea Michel.
A Promotion Prize in the category Project Work, endowed with 4000 euros, was awarded to a student group from RWTH Aachen. The teamwork of Luis Gleissner, Leopold Habersbrunner, Frederic Olbrich and Frederik Schicks was the construction of a test rig for tests on oil-adsorbing textiles.
Felix Zerbes, RWTH Aachen, was awarded a Promotion Prize of 3500 euros in the category Master. He developed a technical solution for air jet weaving to improve the quality of woven fabric.
The key to success of a ring spinning mill lies in its ability to produce flawless quality with the highest possible production speed. Selecting the best ringtraveler system is crucial here. ORBIT allows exceptional speeds above 23000 rpm without compromising quality.
When the spindle speed is increased, the frictional power between the ring and the traveler, and thus the heat generation, increases exponentially.
When speeds are too high, C-shaped travelers are therefore thermally damaged and fail.
The ORBIT features a large contact surface between the ring and the traveler (Fig. 1), which is four to five times bigger than that of a T-flange ring. This drastically reduces the pressure and thus the heat generation. It also provides more stable running conditions and allows the traveler weight to be reduced, so speeds above 23,000 rpm can be reached.
The size of the yarn passage also plays an important role (Fig 1), especially when processing man-made fibers which are prone to heat damages. The ORBIT ring traveler system benefits from a large
yarn passage which minimizes thermal damages for better yarn quality.
The large contact area of ORBIT between the ring and traveler contributes to the gentle handling of fibers. The stable running conditions coupled with the reduced surface pressure and the optimal heat conduction result in low yarn breakage rates. Recent tests (Fig. 2) conducted at spinning mills across the world confirm that even at higher speeds, the ORBIT shows better results in yarn quality than traditional systems.
Often imitated but never duplicated, the ORBIT ring-traveler system (Fig. 3) is the reference for spinning at the highest speed. With a wide scope of applications for all kinds of fibers, with yarn counts between Ne 20 and Ne 80, the ORBIT ring-traveler system is the solution to reach higher production and, in some cases, even better quality.
Rieter is the world’s leading supplier of systems for short-staple fiber spinning. Based in Winterthur (Switzerland), the company develops and manufactures machinery, systems and components used
Fig. 1: With its large yarn passage (1) and contact area (2), the design of the ORBIT ring-traveler system allows exceptional speeds above 23,000 rpm without compromising quality.
to convert natural and man-made fibers and their blends into yarns. Rieter is the only supplier worldwide to cover both spinning preparation processes and all four end-spinning processes currently established on the market. Furthermore, Rieter is a leader in the field of precision winding machines. With 17 manufacturing locations in ten countries, the company employs a global workforce of some 4 900, about 18% of whom are based in Switzerland. Rieter is listed on the SIX Swiss Exchange under ticker symbol RIEN.
Fig. 3: ORBIT allow speeds above 23,000 rpm without ever compromising on quality.Bräcker, the world’s leading supplier of rings and travelers for ring spinning systems, is a subsidiary of the Rieter
Group. Bräcker, based in Pfäffikon ZH (Switzerland), creates customer value through system expertise, innovative solutions, after sales excellence and global presence. The company
manufactures its main products – rings and travelers for ring spinning machines –in Pfäffikon and Wintzenheim (France). In addition, Bräcker offers grinding machines used for maintenance of cots.
What we do to meet your sustainability printing goals by focusing on concrete actions
Come and visit us at FEBRATEX! The largest fair for the textile industry of the Americas (23-26 August – Blumenau –Hall 3 - Stand 102). Here is what you will see at our booth:
JP7. The versatile scanning industrial digital printing machine can print both fabric & paper and scale up the number of printheads (from 8 up to 16). JP7 is the key to modulate your investment and improving process efficiency by reducing operating costs and ensuring a rapid return of the investment. JP7 reaches industrial printing speed (https://www.msitaly.com/00/p00000013/jp7.html ), satisfying today's time-to-market. Same Printing Results is a concrete advantage. Visitors will also get the chance to speak to our team about our full portfolio to support their growth: the advanced industrial machine models, equipped with 32 printheads, JPK EVO, and the 64-
printhead Minilario, and the most known single-pass Lario. The entire portfolio is equipped with the same Kyocera printhead technology, creating a platform to maximize flexibility, reliability, and reproducibility of results.
Digistar Bellagio BIB – reactive ink by JK Group - at work into JP7. You will see first hand the results of your next investment in printing quality, color intensity, depth of black colors, and runnability. The high-performance level is possible thanks to the perfect balance between printability and drying. Then, look at the bag-in-box packing, which permits:
A significant reduction, around 80%, in plastic use compared to the traditional HDPE bottles.
A significant reduction in volume, around 90%, in space requirements for shipping and warehouse waste, thus contributing to and reducing the environmental impact.
The BIB plastic and cardboard components are separable, allowing easy cardboard recycling. We will be talking about Pigment printing, therefore less water and energy consumption. Printing with pigment inks is an easy and waterless process, suitable for a wide range of fibers. The printing process by pigment allows a sustainable production chain, ensuring cost-effective printing outputs. This is possible, thanks to the flexibility and versatility of JP7 which can be easily “shifted" to other printing processes, making the investment extremely cost-effective. We help your sustainable development goals with concrete actions by offering disperse, dye-sub, pigment, and reactive inks that comply with the major textile international environmental standards, among which there are ZDHC and Eco Passport certifications. Let's talk about this, come and visit us.
Spindles are at the core of spinning machines and play a crucial role in their performance. With an impact on productivity, quality, energy saving or work environment, selecting the right spindle for an application is key. Thanks to Novibra’s wide range of spindles, finding the perfect spindle is child’s play.
As the leader in spindle technology, Novibra offers a great selection of innovative and high-performance spindles (Fig. 1).
First-ever spindle to run at 30 000 rpm – NASA HPS 68
Famous for extending service periods, reducing noise level and ensuring maximum durability, Novibra’s flagship and best-seller NASA HPS 68 (Fig. 2), already convinced premium machine manufacturers such as Rieter, Toyota or top-class Chinese producers.
Installations in the optimum range for NASA HPS 68 – at medium to fine
yarn counts and 20,000 to 30,000 rpm speed – represent a completely different type of load on the spindle than coarse yarn count applications. Smaller repeated loads at high frequency occur causing micro vibrations. Therefore, a chamber filled with lifetime grease was introduced as a second damping system. Noise is thus significantly reduced, making the spinning mill a better place to work.
Reliable solution for medium and fine yarn counts – HPS 68
Novibra’s second best-selling spindle, HPS 68, has been a technical revolution in the switch from conical types to spindles with a flat tip. Its unrivalled spindle insert constitutes a base for all Novibra spindles of younger generations. HPS 68 is the right spindle to spin standard short-staple fibers to medium and fine yarn counts.
Although higher speeds are possible, the spindle outperforms at speeds up to 20,000 rpm with favorable noise levels and long lifetime.
It also makes operators’ lives easier with substantially longer oil exchange periods.
When spinning coarse yarn counts, L HPS 68 is the right spindle. Its unique wharve diameter of 18.5 mm ensures optimized energy consumption and load on the machine driving elements. In most applications, a full cop and high tension of the yarn put a heavy load on the spindle neck bearing – which is increased by further imbalances occurring in the spinning process of coarse yarns. The special design elements of the L HPS 68 spindle absorb heavy loads and ensure the desired harder damping.
The spindle mostly runs with tube lengths from 220 to 250 mm, but it can also be operated with tube lengths of 280 mm, e.g. by wool spinners. While speed increases up to 20,000 rpm are an option, the speed is limited by the desired yarn count and twist.
Figure1: The wide range of Novibra spindles covers any requirement.The latest addition to the Novibra spindle family was especially designed to achieve high speeds with lowest energy consumption and reduced noise.
LENA is the right spindle to spin yarn counts of Ne 30 and finer, with tube lengths up to 210 mm at speeds up to 30,000 rpm. Thanks to the uniquely small wharve diameter of 17.5 mm, 4 to 6% energy savings can be achieved. As creating a more sustainable future for the textile industry is getting more and more urgent, LENA is an attractive choice.
To leverage on its spindle range, Novibra also provides an extensive range of clamping crowns for underwindingfree doffing. The development of each crown has been thoroughly studied, with only one goal in mind: boosting customer’s competitiveness. Based on the machine type, doffing system and raw material or yarn count, Novibra offers countless designs from replaceable EASYdoff to sturdy steel crowns and from SERVOgrip (Fig. 3) to selfcleaning CROCOdoff.
On request, Novibra also provides customized spindles without catching crowns for machines without automatic doffers.
There is an ongoing debate about the introduction of a universal spindle type. However, only optimally selected spindles give the best results. Yarn count, speed, lifetime, maintenance, or energy consumption requirements must be considered in the selection process. Novibra sales teams assist customers in choosing the right spindle to achieve the optimum performance.
When you think of innovative industries, you probably think of computers, smartphones, and automobiles.
What you likely wouldn’t expect is that the U.S. cotton industry is one of the most high-tech industries around, and it has used the advancements at its disposal to become continuously more sustainable.
Growers made much progress through innovations like windbreaks, contour farming and conservation tillage, which have been widely adopted across the U.S. to prevent soil loss.
During the past 35 years, U.S. cotton growers have made huge strides to improve the sustainability of their farms. They have improved soil health, reducing loss and erosion by 37% per acre all while increasing soil carbon levels, according to the 2016 national indicators report from Field to Market: The Alliance for Sustainable Agriculture.
Additionally, they have used 79% less water and 54% less energy, reduced greenhouse gas emissions by 40% and land use by 49%, all while increasing yield by approximately 42%.
As technology has improved, growers have utilized emerging innovations to grow cotton more efficiently. According to a study from Duke University and Cotton Incorporated, in 2015, almost 51 percent of U.S. growers used GPSenabled swath control to ensure they were not overlapping crop practices such as planting, fertilize applications, and crop protection applications. In fact, nearly 7 in 10 growers used GPS auto-steering functions on their tractors, tillers, pickers, and more. Now, 63% of U.S. cotton growers use precision agriculture technologies including GPS receivers, multi-spectral images and ground-based sensors to further improve their sustainability.
Precision agriculture technology gathers farm-specific parameters
including soil conditions, nutrients and water availability.
It can assess the farm to deploy site specific crop management practices to maximize yields and minimize crop input requirements. U.S. growers use precision technology throughout the cotton season.
Consulting real-time weather radar improves the efficiency of farm activities by allowing growers to avoid activities that would be affected by weather such as nutrient and herbicide applications getting washed off by thunderstorms. Yield maps show the site-specific yield within a field and are extremely useful to understand which areas of a field need different management. Precision farming technologies also have the potential to reduce GHG emissions from optimized nutrient management and water use efficiency.
U.S. cotton growers utilize precision agriculture to reduce land use through expanding irrigation and fertilization
techniques based on in-field measurements. They use analytics and automation to better increase efficiency and improve soil health.
Varying soil conditions affect nutrient requirements, so soil testing is used to determine optimum nutrient requirements allowing the precision application to change rates within the field.
According to the Duke-Cotton Incorporated study, 86% of U.S. cotton growers apply fertilizers based on soil testing and analysis. Most growers reported higher yields and improved resource efficiencies based off better testing.
In terms of water use, growers use computer-driven moisture sensors, soil moisture probes, real-time weather forecast and evaporation weather stations to understand how much water is in their soil and in the skies. With this information, they can better understand how much water they need to replace.
Drip irrigation technologies can help growers improve crop productivity and water efficiency, while reducing nitrous oxide emissions from soils and GHG emissions. Based on the NC State study,
59% of growers in the U.S. used these flow measuring devices to track the water consumption per acre, regulate water flow and ensure the functioning of irrigation systems, thereby improving water management.
Now, growers are adding an innovative program to better measure their sustainability progress. The U.S. Cotton Trust Protocol underpins and verifies U.S. cotton’s sustainability progress through sophisticated data collection and independent third-party verification. Brands and retailers will gain access to U.S. cotton with sustainability credentials proven via Field to Market: The Alliance for Sustainable Agriculture, measured via the Field Calculator and verified with Control Union Certifications.
“ The Trust Protocol helps growers easily measure their progress towards targets aligned with the UN Sustainable Development Goals .”
Thanks to significant adoption of precision agriculture, the Trust Protocol helps growers easily measure their progress towards targets aligned with the UN Sustainable Development Goals for six key sustainability metrics including soil
loss, soil carbon, water use, soil carbon, energy use, and greenhouse gas emissions.
All this innovation has been useful in helping the U.S. cotton industry provide brands and retailers the confidence that U.S. cotton is more sustainably grown. Choosing Trust Protocol cotton will give brands and retailers the critical assurances they need that the cotton fiber element of their supply chain is more sustainably grown with lower environmental risk.
The Trust Protocol will also enable full supply chain transparency through its Protocol Credit Management System (PCMS) using a powerful combination of the Trust Protocol Platform and the TextileGenesis™ platform. It uses blockchain technology to record and verify the movement of U.S. cotton fiber along the entire supply chain. Starting from the initial fiber sale, every transaction recorded in the PCMS is double verified.
The PCMS will provide critical information about Trust Protocol cotton throughout the member’s supply chain. Once brands and retailers have received their finished products, they can claim data-backed, verified Trust Protocol credits based on their individual consumption.
The total number of Protocol Credits a brand has consumed during the Protocol Year will determine its environmental performance data, which the brand or retail member can communicate through its own sustainability claims.
U.S. cotton growers have evolved their sustainability practices by incorporating cutting-edge technology. The U.S. Cotton Trust Protocol joins a long line of advancements that will allow them to continuously improve the sustainability of their operations.
Life is not easy for yarn producers. They need to improve raw material utilization. They need to boost productivity while balancing between quality and economy. They need to increase yarn quality to fulfill customer requirements. And they need to do it in combed applications where high-quality standards are essential. Those are some big challenges. The TCO 21 combing machine from Trützschler offers an innovative solution.
Since it was first launched in 2021, the TCO 21 has been delighting customers around the globe with its innovative features and enormous optimization potential. The first largescale installations are now up and running in the world’s most important combing markets. And the results are extremely positive!
The TCO 21 offers automatic optimization functions and is the first ever comber to feature 100% Trützschler technology. That powerful combination is now improving efficiency, productivity and quality in yarn-producing markets worldwide.
The TCO 21 is unique because it features the PIECING OPTIMIZER technology, which reduces fiber stress, especially during high-speed combing. And it works at the push of a single button. This is valuable for yarn producers because the pilger step movement – and the overall acceleration behavior of the detaching rollers – often acts as a bottleneck when operating at high speeds of up to 600 nips/min. A simple comparison: A detaching roller (48 g) in a high-speed comber accelerates
roughly 8 times faster than a formular one car (6 g).
Testing data: High-speed combing
Tests clearly show the potential value offered by the PIECING OPTIMIZER technology for high-speed combing. Technologists examined the level of performance that customers can achieve with a yarn count of Ne 30 made from US cotton.
The number of yarn imperfections remained constant even when increasing the combing speed from 500 to 600 nips/min – which is a 20% higher production rate. Most important, the amount of noil also remained in the same range for all three trials. In fact, the total number of imperfections in the yarn (measured as IPI) was slightly lower because of fewer thick spots and neps.
Overall, the TCO 21 has demonstrated its capacity to deliver
optimal yarn results even when increasing the production rate by up to 20%.
Testing data: Production increase with a yarn count of Ne 20
Trials have shown that the TCO 21 can achieve a 20% increase in production output compared to the current combing machine from a competitor for yarn counts of Ne 20 – while also generating less noil. Operating at a rate of 600 nips/min instead of 500 increases yarn production per comber set by around two metric tons per day (depending on the specific settings). Importantly, the TCO 21 is able to provide this production increase while delivering similar yarn quality in terms of IPI and uniformity –and also reducing noil. The tests show that the TCO 21 can reduce the comber noil by 0.43% compared to the competitor’s machine.
Testing data: Production increase with a yarn count of Ne 40
The TCO 21 also demonstrated a 20% production increase and similar yarn quality compared to a competitor’s machine for yarn counts of Ne 40. With a production increase of 10% – e.g. producing 550 nips/min instead of 500 nips/min – the yarn results improved with the TCO 21. Furthermore, the number of faults per kilometer only very slightly worsened with a 20% increase in production. In addition, yarn uniformity remained at the same level in all trials, even when the production rate increased. The comber noils were at the same level too.
Testing data: Production increase with a yarn count of Ne 60
In the final trial, which involved a yarn count of Ne 60, the TCO 21 proved its capacity to achieve a 5% or 10% higher production rate with up to 26% better results for yarn quality. Of course, it is more difficult to improve production rates and maintain quality when working with finer yarns. But also in this comparison the TCO 21 demonstrated its excellent performance and advantage compared to the competitor product. Remarkably, yarn results improved in this test when the production rate for the TCO 21 was increased by 5% and 10%. The overall IPI was 21% and 26% lower compared to the competition. Despite higher production rates, yarn evenness also remained slightly better than the competitor machine’s level. And the noil
was constant across all three production rates that were tested.
The results from these tests are extremely positive and we are confident that the unique machine concept has additional potential. Trützschler’s experts are now working side-by-side with our customers to open up new ways of further optimizing the performance of this machine in various application areas. However, the TCO 21, our first comber with 100% Trützschler technology, will help our customers improve their competitive position in the global yarn market.
The Trützschler Group SE is a German textile machinery manufacturer headquartered in Mönchengladbach, Germany. The company is divided into four business units: Spinning, Nonwovens, ManMade Fibers, and Card Clothing. Trützschler machines, installations and accessories are produced and developed in ten locations worldwide. This includes four factories in Germany (Dülmen, Egelsbach, Mönchengladbach, Neubulach), as well as sites in China (Jiaxing and Shanghai), India (Ahmedabad), the USA (Charlotte), Brazil (Curitiba) and Switzerland (Winterthur). Service companies in Turkey, Mexico, Uzbekistan and Vietnam and service centers in Pakistan, Bangladesh and Indonesia provide customer proximity in key regions for the textile processing industry.
The state-of-the-art combing machine TCO 21.Over Euro 1.5 billion in business volume during five days.
ITM 2022, the first major international textile machinery exhibition held in the world after a three-year hiatus, hosted textile technology leaders in Istanbul for five days.
Record sales were achieved at the ITM 2022 Exhibition, where the latest innovations in every field of textile from weaving, knitting, yarn, digital printing, finishing to denim were exhibited and with several world launches. The ITM 2022 Exhibition, where a business volume of over 1.5 billion Euros was created in five days, accelerated the Turkish and world economy.
Organized by the partnership of Teknik Fairs Inc. and Tüyap Tüm Fuarcılık Yapım Inc., ITM 2022- International Textile Machinery Exhibition was held at Tüyap Fair and Congress Center between 14-18 June. The ITM 2022 Exhibition, which was organized in 12 halls on an area of 120,000 square meters, broke records with both exhibitors, visitors and machinery sales. ITM 2022 Exhibition, attended by 1280 companies and company representatives from 65 countries, was visited by 64,500 people from 102 countries, consisting of 44%
international and 56% domestic visitors. At the exhibition, where companies sold machinery worth million Euros, a business volume of over 1.5 billion Euros was created.
The successful sales graph achieved at the ITM 2022 proved that the difficulties experienced due to the pandemic for the last three years have been left behind. Turkey has become a supply center for European, Middle Eastern and African countries, especially with the disruption of the supply chain in Far East countries, including China. The profile of the professional visitors visiting the ITM 2022 Exhibition revealed that in the new world order that has shifted after the pandemic, the trade network has also changed hands and new players have appeared on the scene. The fact that manufacturers from all over the world such as Andorra, Angola, Honduras, Peru, Seychelles, Sierra Leone, Brazil, Sri Lanka, Tanzania, Egypt, Iran, and Oman purchased machinery and signed strong collaborations at the ITM 2022.
The ITM Exhibition pleased the participating companies with the number of visitors and performed machinery sales amounting to millions of Euros. Many company officials, who stated that they have achieved a sales graphic far above their expectations starting from the very first day of the ITM 2022 and that they have hosted visitors from all over the world, decided to enlarge their stands at the ITM 2024 Exhibition.
ITM 2022: Go to address for world launches
ITM 2022 has turned into a textile feast with the participation of hundreds of manufacturers who developed technologies in their field, and the visits of global investors and commercial delegations. Many companies, which focus on product development and new productions under pandemic conditions, had the opportunity to introduce their products to their customers for the first time in three years at the ITM 2022 exhibition. Company owners, managers, employees and sector representatives
Satisfied exhibitors of ITM 2022 resolve to enlarge their Stands for ITM 2024visiting the exhibition had the opportunity to see the latest technological innovations for the first time and witnessed their world launches.
Due to Istanbul's ease of transportation and the absence of visa requirements, ITM 2022 Exhibition hosted thousands of visitors from all over the world. Almost 64,500 people from 102 countries, including Turkey, visited the ITM 2022 Exhibition to see the latest innovations in textile technologies.
The countries where the visitors come to the ITM 2022 Exhibition are as follows: Afghanistan, Albania, Algeria, Andorra, Angola, Argentina, Armenia, Austria, Azerbaijan, Bahrain, Bangladesh, Belarus,
Belgium, Benin, Bosnia and Herzegovina, Brazil, Bulgaria, Canada, China, Colombia, Democratic Republic of Congo, Croatia, Czech Republic, Denmark, Dominican Republic, Egypt, Estonia, Ethiopia, Finland, France, Georgia, Germany, Greece, Honduras, Hungary, India, Indonesia, Iran, Iraq, Israel, Italy, Japan, Jordan, Kazakhstan, Kenya, Korea, Kosovo, Kuwait, Kyrgyzstan, Lebanon, Libya, Lithuania, Macedonia, Malaysia, Mauritius, Mexico, Moldova, Mongolia, Morocco, Nepal, Netherlands, Nigeria, Oman, Pakistan, Palestine, Peru, Poland, Portugal, Qatar, Romania, Russia, Saudi Arabia, Serbia, Seychelles, Sierra Leone, Singapore, Slovakia, Slovenia, Somalia, South Africa, South Korea, Spain,
Sri Lanka, Sudan, Sweden, Switzerland, Syria, Tajikistan, Tanzania, Thailand , Tunisia, Turkmenistan, Northern Cyprus s Turkish Republic, Turkey, Uganda, Ukraine, United Arab Emirates, United Kingdom, America, Uzbekistan, Vietnam and Yemen.
The next meeting of the ITM and HIGHTEX Exhibitions, which bring together the world's textile technology leaders, will be held in Istanbul between 4-8 June 2024.
Mimaki presented four textile printers at the Mimaki booth at ITM in Istanbul. The TS100-1600 sublimation transfer printer, TS55-1800 sublimation transfer printer, Tx300P1800B direct-to-textile printer and TS330-1600 sublimation transfer printer during the exhibition.
Comprehensive solutions for sublimation and direct-to-textile printing
Mimaki's TS55-1800 sublimation transfer printer reduces operating costs thanks to the new two litre costeffective inks and increases productivity with a single pass printing speed of 140 m2 per hour.
TS100-1600, another sublimation transfer printing solution, is another option for the entry segment. TS1001600, reaching print speeds of up to 70 m2 per hour, is equipped with all the necessary functions for low-volume print production on demand. TS100-1600 uses a media take-up system that supports rolls up to 45 kg and has the power to enable mass production at the same time.
The TS330-1600 sublimation transfer printer presented to the Turkish market for the first time at ITM 2022. This printer in the 330 Series can reach speeds 135m2 per hour. Error-free colour reproduction and
superior colour and print quality achieved thanks to the innovative Mimaki Weaving Dot Technology (MWDT).
Proving its expertise in direct-to-fabric printing, Mimaki highlights Tx300P-1800B direct-to-textile printer at its booth. This blanket printer makes it possible to print high-quality large volumes on flexible fabrics with a printing speed of up to 53 m2 per hour.
Tx300P-1800B is able to work with sublimation, disperse, reactive, acid and pigment dyes and is preferred for dozens of different applications from fashion and clothing products to upholstery fabrics, from bedspreads to curtains.
Mimaki Eurasia Area Sales Manager Hüseyin Şarerler has disclosed that digital printing provides new opportunities to the textile industry and expressed that there is a rapid digitalization in the market for this reason.
traditional methods have become accessible with digital printing. Thanks to the advanced printing process, the time between order and product delivery dates has decreased from months/weeks to days. Increasing personalization demands can be met and there is no longer a necessity such as high volume. Digital textile printing is completed easily and error-free in a few steps, increasing the competitiveness of the industry.”
Şarerler disclosed; “Our textile printers, equipped with special Mimaki Core Technologies, can be used safely and comfortably for numerous different applications such as clothing, decoration, home textiles, industrial advertising and so
Şarerler said the following; manufacturers' concerns about quality and efficiency are ending Mimaki Eurasia, Area Sales, Manager Hüseyin Sarerler.Jeanologia promotes a more sustainable and competitive textile industry through the integration of its technology in order to meet MissionZero: zero discharge production.
The Spanish company is offering the most efficient energy management systems as well as simplifying processes, providing hyper realistic designs and avoiding second quality garments. They exhibited the fastest laser on the market during ITM2022.
As pioneers in the development and application of advanced lasers for garment finishing, the company provides greater productivity to the textile industry with a better cost per garment, thanks to the perfect integration of its hardware and software.
Jeanologia showcased system and solution which are 40% faster than other laser technologies. Specifically, its
Compact Super range of laser solutions achieves productivity of 2,000 garments per day, reducing operational costs and speeding up time-to-market guaranteeing a more competitive and sustainable industry.
The Compact Super integrates the revolutionary software e-Mark X2 which increases the laser speed as well as allowing a more efficient energy management. The integration of hardware and software makes it possible to increase the marking speed while maintaining the same power, simplifying processes as well was allowing infinite design possibilities with great quality and authenticity. At the same time as avoiding second quality garments, achieving perfect reproducibility from the first to the last garment.
Adrián Baldó, Division Director EMEA at Jeanologia, highlighted how Jeanologia
has led the way with its laser technology, creating a more sustainable, ethic and eco-efficient industry, “We have achieved the trust of the market because we have added value to our customers with the investment in R+D to develop the most advanced laser that ensure the best return on investment.
“Our mission is to digitally transform the industry and to do so we added our efforts to that of our customers, accompanying them in the implementation of our technologies to optimize their production.”
At ITM Jeanologia will show its laser Compact Super, designed to obtain maximum production flexibility, precision and power with a compact design and high profitability.
Intended to take maximum advantage of space in production centers, creating a safe and comfortable working environment for its operators, this advanced laser range satisfies the needs of large productions with garment versatility, detailed and precise designs, while being easy to use.
During ITM, Jeanologia showed its commitment to the textile industry by promoting sustainability and competitively, turning it into a key piece in meeting MissionZero: Jeanologia’s challenge to eliminate the use of water and discharge completely from global jean production.
The integration of laser, G2 ozone, e-Flow, Smart Boxes and H2Zero (the company’s first water recycling system creating productions that are 100% ecological), developed by Jeanologia make it possible to produce with zero discharge, stimulating productivity and efficiency in the textile industry for garment finishing.
For 20 years Jeanologia has been active in Türkiye as a supplier of key solutions to make the Turkish textile industry more efficient and
sustainable, promoting production techniques that increase productivity and reduce water, chemical and energy consumption.
World leaders in ozone technology, it has more than 15 years’ experience. To support the Turkish market, it opened a production center in Izmir for ozone technology in 2015, along with a center for demonstrating its technologies. Currently, there is a team of more than 20 specialist technicians and creative professionals that directly attend customers’ needs within the country.
More than 35% of the 5 billion jeans produced every year in the world are made using Jeanologia technologies and it is trusted by the biggest market brands.
Non-contact precision-spray system supports textile finishers managing high energy and chemical costs
Baldwin Technology Company Inc. presented sustainable TexCoat™ G4 finishing system at ITM in Istanbul. This technology was also on display at the Techtextil and Texprocess trade fairs.
The TexCoat G4 non-contact precision-spray technology helps textile finishers up their game by enabling consistent, high-quality finishing, with zero chemistry waste and drastically minimized water and energy consumption.
With a cost-sensitive global economy and an increased focus by brands and consumers on the environment, customers are placing a premium on sustainability in textile production.
TexCoat G4’s non-contact spray technology offers numerous advantages compared to conventional methods of applying finishing chemistry. With Baldwin’s innovative system, the chemistry is precisely distributed across the textile surface and is applied only where it is required, on one or both sides of the fabric. The non-contact technology eliminates chemistry dilution in wet-onwet processes, allowing full control of maintaining consistent chemistry coverage rates. Plus, pad bath contamination is eliminated, and changeovers are only required when there is a change of finish chemistry
More specifically, with Baldwin’s TexCoat G4, textile finishers can expect unprecedented tracking and control of the finishing process for consistent quality. Changeovers are easily and quickly performed thanks to recipe management, including automated chemistry and coverage selection. Furthermore, the system offers automated speed tracking, fabric-width compensation, and real-time monitoring to track system uptime, performance and chemistry usage, as well as active care alerts.
In addition, the TexCoat G4 system can process a wide range of low-viscosity water-based chemicals, such as durable
Baldwin’s Sustainable Texcoat G4 system provides textile finishers with high-quality, costeffective finishing.
water-repellants, softeners, antimicrobials, flame retardants and more. Baldwin’s innovative technology utilizes the same chemicals used in the traditional pad bath, and no special auxiliaries are required. The recipe is adjusted by increasing the concentration and reducing the pickup by a corresponding amount, so that the same level of solids is applied.
Some applications, such as durable water repellents, are only applied on the face of the fabric, instead of the traditional method of saturation through dipping and squeezing.
Drier fabric entering the stenter means lower drying temperatures and faster process speeds. Single-side applications also open up the opportunity to process back-coated or laminated fabrics in a single pass of the stenter, instead of two passes.
“Today, sustainability challenge is such a high priority for fabric producers and brands. Energy and chemical costs are skyrocketing, and our TexCoat G4 is the ultimate tool to assist manufacturers in managing these costs in the finishing department.”
In Italy there are approximately 300 companies who produce textile machines and related accessories, for a total of about 12,900 employees. In 2021 the value of Italian production was Euro 2.4 billion, with exports worth Euro 2 billion.
Approximately 85% of Italian total sales are realized in about 130 destination countries. The process of internationalization and the vocation for innovation in the sector, allowed Italian companies to consolidate and further improve the leading position of Italy in the world textile machinery industry.
In 2021 period the main destination of Italian exports of textile machines was
Italian Textile machinery exports by segments (2021) ACIMITAsia (42%), followed by Europe extra EU (20%) and European Union (19%). The biggest contribution to the Italian exports of textile machinery came from China. In 2021 period Italian sales toward Chinese market amounted to a value of Euro 304 million. Others main markets are Turkey, Pakistan and United States of America.
The supply of Italian manufacturers covers all the classic sectors into which we can divide textile machines. Each type of machines are well represented in the Italian exports.
Italian companies involved in this sector, are small-size companies, deeply committed to R&D activities, looking for close cooperation with end users to create new opportunities, new machines, new systems and technologies.
The ability to understand the needs of potential customers enables Italian companies to turn them quickly into dedicated machines and devices which give rise to new high value-added market niches (such as the technical textiles) in the world textile market, both as regards economical and technological aspects.
Italian textile machinery companies are placed in areas of ancient textile tradition, where an exchange of experience with end users offers a strong impetus to the constant technological upgrading of machinery. Textile clusters are located in Northern and Central Italy: Bergamo, Biella, Brescia, Como, Milan, Prato, Vicenza.
Main characteristics that distinguish Italian textile machinery sector are given as under:
Skilled workforce that ensures a high quality of products;
The dimensions of Italian companies that allow a quick response to the need of each customer;
The flexibility and versatility ensure a customized production for satisfying the needs of each customer;
The high technological level of the supply, due to the constant attention paid by Italian companies to the R&D activities and to innovative solutions.
2018 2019 2020 2021 2021/20 Change
Production 2,537 2,266 1,775 2,388 +35%
Export 2,108 1,865 1,481 2,031 +37%
Domestic Sales 429 401 294 357 +21%
Import 513 478 412 514 +25%
Domestic Consumption 942 879 706 871 +23%
Source: ACIMIT
Italian textile machinery exports to main countries (2021) (Million Euro)
Source: ACIMIT.
Italian textile machinery exports by area (2021) (Million Euro)
Source: ACIMIT
The objective critical issues faced by Italy as a whole throughout the course of 2021, primarily dictated by a pandemic that upset any and all pre-existing equilibriums, have not slowed or halted the Italian textile machinery sector.
Indeed, data presented during the annual assembly of ACIMIT, the Association of Italian Textile Machinery Manufacturers, held on 1 July proved decidedly positive, showing that in 2021 the sector recovered significantly compared to 2020, to the point of returning to pre-Covid levels.
Specifically, Italian textile machinery production amounted to 2.388 billion euros (+35% over 2020 and + 5% over 2019), with total exports amounting to 2.031 billion euros (+37% over 2020 and +9% over 2019).
However, these results do not cancel the obstacles that companies are still facing. Looking to the near future, expectations are for a rather uncertain outlook, as underscored by ACIMIT President Alessandro Zucchi: "2022 remains a year replete with unknown factors, starting with the RussianUkrainian conflict, along with the persistence of the pandemic, which seriously risk delaying expected growth consolidation for businesses in the sector.
Difficulties in finding raw materials and components negatively affect the completion and fulfilment of orders processed as far back as 2021. To boot, rising energy costs and inflationary trends affecting numerous commodities are depressing overall business confidence. So the outlook for the sector is not so good."As such, the two cornerstones through which ACIMIT aims to support the Italian textile machinery sector are digitilization and sustainability.
The road to digital transformation has already led numerous manufacturers to completely rethink their production processes, rendering them more efficient and less expensive.
The digital world is moving ahead at a decisive rate in the textile machinery sector, where the buzzwords are increasingly, for instance, the Internet of Things (IoT) connecting to a company's ecosystem, machine learning algorithms applied to production, predictive maintenance, and the integrated cloud management of various production departments.
It is no coincidence that ACIMIT has focused decisively on its Digital Ready project, through which Italian textile machinery that adopt a common set of data are certified, with the aim of facilitating integration with the operating systems of client companies (ERP, MES, CRM, etc.).
Combining production efficiency and respect for the environment: a challenge ACIMIT has made its own and which it promotes among its members through the Sustainable Technologies project.
Launched by the association as early as 2011, the project highlights the commitment of Italian textile machinery manufacturers in the area of sustainability.
At the heart of the project is the Green Label, a form of certification specifically for Italian textile machinery which highlights its energy and environmental performance. An all-Italian seal of approval developed in collaboration with RINA, an international certification body.
Annual emissions generated by companies who implemented technological modifications on their equipment (comparison between old and new versions of the machines).The assembly held on 1 July provided an opportunity to take stock of the Sustainable Technologies project, more specifically, with the presentation of the Rina Consulting survey on the Green Label's evolution and impact in recent years.
The results have confirmed the initiative's extreme validity. The technological advances implemented by the association's machinery producers participating in the project have effectively translated into benefits in terms of environmental impact (reduction of CO2 equivalent emissions for machinery), as well as economic advantages for machinery users.
With reference to the year 2021, a total of 204,598 tons of CO2 emissions avoided on an annual basis have been quantified, thanks to the implementation of improvements on machinery.
This is a truly significant reduction which, for the sake of comparison, corresponds to the carbon dioxide emissions generated by 36,864 automobiles travelling an average of 35,000 km a year. In terms of energy savings, the use of green labeled textile machinery has provided excellent performances in allowing for a reduction of up to 84% in consumption.
The environmental and economic impact generated in production processes for Italian textile machinery through the use of Green Label technologies was the
focus of the round table which concluded the ACIMIT assembly.
Moderated by Aurora Magni (professor of the Industrial Systems Sustainability course at the LIUC School of Engineering), the debate involved Gianluca Brenna (Lipomo Printing House administrator and Vice President of the Italian Fashion System for Welfare), Pietro Pin (Benetton Group consultant and President of UNI for the textile-clothing area), Giorgio Ravasio (Italy Country Manager for Vivienne Westwood), as well as ACIMIT President Alessandro Zucchi.
Called on to compare common factors in their experiences relating to environmental transition processes for their respective companies, the participants were unanimous: the future of Italian textile machinery can no longer ignore advanced technology developments capable of offering sustainable solutions with a low environmental impact while also reducing production costs.
This philosophy has by now been consolidated, and has proven to lead directly to a circular economy outlook.
Lastly, a word on ITMA 2023, the most important international exhibition for textile machinery, to be held in Italy from 8 to 14 June 2023 at Fiera-Milano Rho. Marking the 19th edition of ITMA, this trade fair is an essential event for the entire industry worldwide, providing a global showcase for numerous innovative operational solutions on display. A marketplace that offers participants extraordinary business opportunities. The participation of Italian companies is managed by ACIMIT.
ACIMIT (Association of Italian Textile Machinery Manufacturers) was founded in 1945 with the primary objective of promoting the Italian textile machinery industry, by supporting its activities in Italy and abroad. A non-profit organization, it currently brings together some 180 producers of textile machinery, divided into different categories: spinning, weaving, knitting, finishing and other machinery.
CFP reduction as divided per sector (reference year: 2021).
ACIMIT represents an industrial sector that includes roughly 300 companies (employing some 13,000 people) and which produces machinery for a total value of around 2.4 billion euros, of which about 85% is exported. Creativity, sustainable technology, reliability and quality are the characteristics that have made Italian textile machines industry leaders worldwide.
The orders index for textile machinery for the first quarter of 2022, processed by ACIMIT, the Association of Italian Textile Machinery Manufacturers, shows a slight decrease (4%) compared to the same period from January to March 2021. In absolute value, the index stood at 117 points (basis: 2015 = 100).
On the domestic front orders shrank by fully 22%, whereas abroad the decline was more contained (-2%). The absolute value of the index in Italy was set at 136 points. On foreign markets, the index scored a value of 114.9 points.
ACIMIT President Alessandro Zucchi commented that: "The global pandemic and Russian Ukrainian conflict have accentuated the climate of uncertainty for the whole of the textile industry. Critical issues already present in the past year (such as a sharp rise in prices of raw materials and their scarce availability, as well as increased transport costs) are now accentuated more than ever. While orders appear to have settled on foreign markets, domestically, following a strong recovery in 2021, we now have to deal
with a general negativity permeating the Italian economy. "
The ongoing conflict in Ukraine, together with successive lookdowns in the main market for textile machinery manufacturers, namely China, have undermined the confidence of Italian companies in the sector. "I believe 2022 will be a transition year for the industry, as we await a calming international economic scenario. In the meantime, adds Zucchi, "Our association continues to work to strengthen the positioning of Italy's textile machinery industry worldwide through promotional initiatives in collaboration with Ministry of Foreign Affairs and International Cooperation and Italian Trade Agency.
The latest of these initiatives was carried out at the end of April, with the opening of an Italian technology training center for textile machinery in Mongolia, a country that ranks among the world's leading producers of raw cashmere. ACIMIT's president concludes that, "With the training center starting its operations,
our sector is laying the foundations for further business opportunities in an emerging market. I'm certain the initiative will bear a return in terms of image not only for individual Italian companies who are participating by supplying machinery, but on the entire Italian textile machinery sector as a whole.
The Index of Orders Intake at Constant Value (Bases 2015=100)
Alessandro Zucchi; ACIMIT PresidentSharabati Denim is among the renowned denim mills in the world, featuring a customer portfolio that includes globally famous fashion brands and mass retailers, and exporting its fabrics to 27 countries worldwide. With production sites in Egypt and Turkey, Sharabati Denim weaves more than 80 million meters of denim, corduroy, and grey fabrics every year.
Sharabati Denim introduced process optimizations to decrease water and energy waste and promote responsible employment of chemicals. The fundamental driver of the mission of the Company is, in fact, the eco-centric approach that consists of solutions for sustainable production to reduce the environmental impact to provide final consumers with sustainable fabrics.
The R9500-2denim rapier weaving machine launched in 2018 is exclusively dedicated to weaving denim.
Sharabati Denim was among the pioneers to install the first group of this machine model, equipped with iSAVER®, the device that eliminates weft and warp waste on the left side of the fabric leading to significant cotton and water savings.
The R9500-2denim and iSAVER® performance parameters are the best in their category – and therefore led to a repeat order in 2021 for both Egyptian and Turkish plants for a total of more than 180 machines.
Just consider that – as reported by the company – the iSAVER equipped on the weaving machines in production ensures Sharabati Denim a yarn saving that ranges from 650 Kg to 900 Kg per machine per year.
In 2022, Sharabati Denim implemented an expansion project aimed at significantly increasing its production capacity.
The weaving partner selected to provide 200 weaving machines for the Egyptian mill is Itema and, once again, its rapier R9500-2denim with iSAVER®.With this last order, Sharabati Denim owns a fleet of more than 400 Itema rapier R9500-2denim, thus achieving outstanding levels of performance, sustainability and technological prowess.
Sustainability and textile mastery are the added values that led Sharabati Denim to confirm the trust in the Itema weaving technology, also considering the significant enhancements introduced on iSAVER® due to the fruitful cooperation between the two companies.
Electronics For Imaging, Inc. (“EFI™”), a Siris portfolio company, acquired Inèdit Software S.L., a developer of raster image processors (RIPs) and related software for digital industrial textile printing.
The acquisition extends EFI’s strategy to accelerate digital transformation in industrial print through investments that advance the company’s presence and capabilities in Packaging & Corrugated, Display Graphics, Textile, and Building Materials/Décor applications. Inèdit will be integrated into the Reggiani textile business.
“Digital represents the biggest transformational opportunity we have ever seen in industrial printing,” said EFI CEO and Executive Chairman Jeff Jacobson. “We are committed to driving innovation and expanding our offerings through all economic cycles as we address our customers’ critical need to digitize and automate their workflows.”
Delivering powerful digital print workflows for textiles
Based in Barcelona, Inèdit will help build on the market leadership of the EFI Reggiani portfolio of digital inkjet printing products for the industrial textile space.
“We are enthusiastic about the expanded business opportunities this acquisition creates by reinforcing EFI Reggiani’s strategic role as a trusted advisor for our customers,” said EFI
Reggiani Senior Vice President and General Manager Adele Genoni. “Inèdit’s products and its world-class professional services organization open the door to creating complete digital printing workflows that leverage best-in-class digital technologies. Our customers can continue to win new opportunities and grow by establishing higher-volume, higher-quality digital production services in ways that reduce the textile industry’s high carbon footprint.
“Inèdit’s extensive market coverage will be a key point of emphasis to fully leverage the strategic synergies arising from the combination of the EFI Reggiani and Inèdit businesses,” Genoni continued. “It is an acquisition that
significantly strengthens our presence in key textile markets.”
Similar to EFI’s Fiery® digital front end and RIP technologies for the digital commercial and industrial printing markets, Inèdit’s neoStampa product is a recognized benchmark solution for RIPs in digital textile printing. The Inèdit product portfolio features proven, highly advanced workflow solutions for textile profiling, calibration, design integration and much more. Inèdit’s RIP technology is employed across the worldwide textile industry and is a leading RIP used to drive EFI Reggiani digital printers and other digital industrial textile printer brands. As part of EFI Reggiani, Inèdit will continue to support products for a broad range of digital printers.
“Becoming part of the EFI Reggiani business empowers us to develop and deliver an even greater level of end-toend textile integrated workflow solutions and Industry 4.0-driven automation enhancements that will further drive customers’ productivity, printing performance, profitability and sustainability in textile printing,” said Jose Antonio Caballero, Co-founder and Sales Manager of Inèdit. “Our team is excited to join a company that is a leading innovator in digital textile printing.”
Inèdit’s employees are joining EFI Reggiani but will continue to work from their current offices.
EFI Reggiani Senior Vice President and General Manager Adele GenoniMarzoli – a Camozzi Group company excels in the supply of complete spinning lines, components and digitalised solutions that optimise performance in the spinning process.
Marzoli is now concentrating its efforts on research and innovation in order to develop an exclusive textile engineering concept that now consists of four distinct, interconnected, and complementary technological areas:
Spinning technology.
Digital textile. Nonwoven solutions. Circular technologies.
The phrase “Textile Engineering” –incorporated in the Marzoli’s logo –perfectly expresses this ability to innovate and work in close contact with customers, supporting them to create value, providing the know-how able to support
the customer throughout all phases of the process: from feasibility and preliminary studies to plant construction, line startup, optimization, management and subsequent commissioning. Added to this: staff training and organization of maintenance activities; turnkey solutions and support in financing activities; business plan development; automation level analysis and project management.
This approach makes Marzoli the global partner for the textile industry of the future.
Marzoli offers complete lines for opening, preparing and spinning natural, synthetic and technical fibers. At ITM, Marzoli presented the new combing technology: CMX, the unique 10-head
combing system which, with a capacity of up to 115kg/hour, guarantees a level of productivity 25% higher than the previous model, along with energy savings equal to 20% kW/kg.
Another company strength is the expertise in developing the most advanced digital technologies. Marzoli presented five solutions for a fully digitalized spinning mill during the recently concluded ITM exhibition in Istanbul.
1. Marzoli Remote Maintenance: The world’s first AI based platform able to analyse Big Data generated by machinery processes and also to continuously monitor mission critical operations. This ensures a reduction of machine
downtime, a longer useful life of parts, and more timely and effective maintenance.
Alongside this, integrated management can be enabled by YarNet, highly innovative software, through which users can manage the entire Marzoli spinning process directly from their PC. With it, every machine in a plant can be monitored with ease – a real value-added technology for customers aiming to maximise productivity and profitability.
2. Brain Box: The patented software with an integrated APP, based on AI technologies, which significantly improves plant performance. Tests confirm that Brain Box can generate a 5.5% increase in productivity, an 8% increase in efficiency, and 1.5% in energy savings. Installation is a fast and simple four-step process: mount sensors to each machine, connect the sensors to Brain Box, download the APP, and activate the monitoring function for the detection of any issues.
3. TAOMAPP: The innovative approach to cotton analysis in which the trash level inside the cotton is accurately determined through photographs taken by smart phone. It is based on ultra-high resolution image recognition techniques and quantifies the results on the Marzoli
Trash Index. The user is just need to download the app, start the analysis and get the benefits.
4. Trash Analyzer: The automatic tool that, together with Marzoli software platforms, analyses cotton’s trash content to optimise machinery set up. It can be applied wherever there is a flow of material in a pipeline.
These five solutions, constantly monitoring machines and process performance, allows to make intelligent and informed decision, based on constantly updated information. Each of these decisions is a further step to increase the flexibility and customization and to reach the highest level of efficiency and productivity.
Marzoli also presented innovative solutions for the nonwoven sector at ITM. With its deep experience and technological knowledge in fibre preparation, Marzoli is uniquely qualified in the implementation of plants for nonwoven products. By developing strategic partnerships with each customer, bespoke nonwoven manufacturing lines, can be developed, with each one based on exact production needs. Range of applications: wipes, medical-surgical, disposable and filtration products.
The circular economy, embracing sustainability, recycling and other green disciplines are important considerations for Marzoli. which has focused on continuous innovation in the mechanical regeneration of textile fibres.
Marzoli know-how focuses on the transformation of post industrial and post consumer textile waste, creating highvalue recycled fiber to be process with ring spinning tecnology.
“For Marzoli, developing and adopting green technologies means carefully balancing business needs with environmental sustainability, explains Cristian Locatelli, Marzoli General Manager. “Circularity through fabrics regeneration, is creating a synergetic value chain that benefits all stakeholders. The new paradigm of a circular fibre supply chain will accelerate learning and development of know-how pushing innovation and opening up to new potential.”
Synergies with the digital capabilities of the Camozzi Group have enabled the development of software solutions that enable informed and optimized management of the spinning process.
Turkey is one of the biggest textile markets for Savio, so attention to Turkish customers is fundamental to support their new projects with the most advanced and automated machines. Savio, therefore, exhibited solutions-oriented machinery portfolio: winding, winding for continuous shrinkage, bulking and heat setting and TFO twisting.
To decide which spinning technology is best suited to customer’s needs, Savio offers numerous solutions to support the quality of the final yarn product. To quote a few solutions for Turkish market:
Savio automatic winders can easily process special yarns, such as the dual core spun yarns. The Savio winding unit is equipped with clearing, splicing and tension control devices for ensuring perfect splices and perfect package shape.
Many years of experience and a close collaboration with customers have allowed Savio to offer several solutions for production of acrylic yarns. The effect of the Volufil machine process gives acrylic fibers dimensional stability, higher volume, wrinkle resistance or temperature resistance, which acquires a regular geometrical structure with excellent volume.
“Multicone” technology and Sirius twisting machines are also addressed to our customers producing acrylic packages for dyeing, knitting and home furnishing.
The yarn package weight and density are two important parameters which are to be standardized for uniform and trouble free dyeing. The soft package
winding is the most important pre-dyeing operation, which directly affects not only the dyeing quality but also post dyeing operations. Savio winding machines for all kind of short staple yarns, are suitable for dye package winding, warping preparation and rewinding with or with out waxing devices.
According to the complexity in the production process of TENCEL™ fiber, Savio pays great attention to yarn control during the winding process.
Savio Multicone technology and Sirius twisting machines are especially addressed to customers producing packages for dyeing and very fine counts, from Nm 200 and above.
The revision of the popular TENSOLAB semi-automatic single-column strength tester was announced during the last ITMA with the introduction of the 4th generation, the TENSOLAB 4.
TENSOLAB 4 replaced the former model which several hundreds were sold worldwide in the past 20 years. The new TENSOLAB 4 embodies a combination of the best ingredients: Latest technology, best electronics, new software and accessories, performances (in terms of capacity, versatility, accuracy and testing efficiency).
The new TENSOLAB 4 represents the forefront of testing flexibility, being configurable for testing any kind of textile and leather material, from single and bundle fibers up to garment accessories and technical fabrics.
Based on the new structure of TENSOLAB 4, a new single-position automatic version was developed, the AUTODYN 3, endowed with the automatic yarn-loading device.
Ideal for the automatic multiple testing of a single bobbin/yarn package.
It can be used in the semi-automatic mode as well for testing all other materials, such as fibers, threads, skeins, fabrics, etc.
The latest innovation, the AUTOFIL, a fully automatic 24 positions yarn strength tester offers an integrated automatic cop feeding system, the built-in PC, its versatile applications, compact design and high testing speed are only few features that characterize the new AUTOFIL.
To complete the range, Mesdan offers two models of double column heavy-duty strength testers, TENSOLAB 1000 (10KN
capacity) and TENSOLAB 5000 (50KN capacity), designed for high tenacity technical yarns and fabrics, ropes, straps and similar heavy materials.
Last but not least, the third generation of the well-known portable SPLICE SCANNER. The first model was launched 25 years ago, its success and popularity are unrivaled, from spinning to dye-houses.
The functional diversification, the product diffusion and its price fairness brought forward to rank MesdanLab range of strength testers among the most complete and popular worldwide.
Such a long presence of MesdanLab products across the global textile supply chain testifies, not only its leadership, but also its commitment to serve the textile industry with constant up-to-date technologies and improvements.
For more information please contact Mesdan: https://www.mesdan.com.
AUTOFIL: Fully automatic yarn strength tester.