
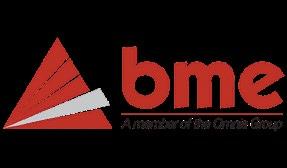


As we embark on another new year, one thing for certain is that the global macroeconomic backdrop and outlook have become tremendously complex. Economies are moving at different speeds, some contracting or slowing, while others are expanding and growing. It is, however, encouraging to see that Africa dominates the list of the world’s 20 fastest-growing economies in 2024.
In its latest Macroeconomic Performance and Outlook (MEO) report, the African Development Bank Group says Africa will account for 11 of the world’s 20 fastestgrowing economies this year. Overall, real gross domestic product (GDP) growth for the continent is expected to average 3,8% and 4,2% in 2024 and 2025, respectively. This is higher than projected global averages of 2,9% and 3,2%. In fact, the continent is set to remain the second-fastest-growing region after Asia.
As you will see in this edition of Quarrying Africa , we cast the spotlight on southern Africa, as part of our regional focus series. What is the state of affairs in the region?
Economic growth is expected to remain sluggish at 2,2 and 2,6% in 2024 and 2025, respectively. This is a reflection of continued economic weakness in South Africa, the region’s largest economy, which expects a meagre 1% GDP growth this year.
elections this year. Elections by their nature tend to introduce a certain degree of uncertainty in various economic sectors, including commercial construction. Historically, these years often see businesses and investors adopting a more cautious stance, potentially leading to a temporary slowdown in investment decisions.
However, elections might also be a good thing for public infrastructure spending. Building infrastructure in Africa is often an inherently political act. It has been proven that elections greatly influence investment choices for incumbent governments. The flow of infrastructure funds creates winners and losers, and investment decisions often favour those in power.
To provide context, tender activity generally accelerates in the run-up to an election year in South Africa, as evidence has shown historically. The South African construction sector has seen a robust increase in civil tender activity, with the estimated nominal rand value of civil tenders up 29% year-on-year in 2023, with most of the provinces showing an increase compared to 2022. The estimated value of road tenders rose 60%, with SANRAL a major contributing client.
MUNESU SHOKO Publishing Editor Email: munesu@quarryingafrica.comSpeaking of South Africa, most of us are no doubt anticipating the upcoming election with mixed feelings. With the governing African National Congress (ANC) staring the prospect of declining below the 50% + 1 threshold for the very first time since 1994, one of the possible scenarios is the inauguration of coalition governments.
Some believe a government of national unity is what South Africa needs at this point in time, following 30 years of the ANC’s dominance, with influence in policy-making a major upside. However, some are sceptical that the new order of political fragmentation, as witnessed in municipalities, may be too chaotic and uncertain for a national government.
Apart from South Africa, several other southern African countries, including Botswana, Mozambique and Namibia, will be holding
While South Africa still exhibits pockets of opportunity in the face of economic obstacles, it is countries bordering South Africa that have also chipped in with significant growth during the past two years, particularly Zimbabwe, Botswana and Namibia. This was the overarching message from my recent interview with a leading capital equipment supplier.
While Botswana has in recent years turned its infrastructure development attention to water and pipelines, its focus is seemingly turning back to roads and bridges. Despite it being a small market, Namibia has also shown signs of growth on the construction front.
In Zimbabwe, construction activity has been a major growth driver. The Zimbabwean government has embarked on massive reconstruction and rehabilitation projects on major road networks to enhance both domestic and regional connectivity.
As a long-standing believer in the potential of southern Africa, I believe, as always, there are concerning factors and cause for hope – and as so often happens, these two seem balanced on a knife-edge.
Publishing Editor: Munesu Shoko
Sub Editor: Glynnis Koch
Business Development Manager: Elmarie Stonell
Admin: Linda T. Chisi
Design: Kudzo Mzire Maputire
Web Manager: Thina Bhebhe
Quarrying Africa is the information hub for the sub-Saharan African quarrying sector. It is a valued reference tool positioned as a must-read for the broader spectrum of the aggregates value chain, from quarry operators and aggregate retailers, to concrete and cement producers, mining contractors, aggregate haulage companies and the supply chain at large.
Quarrying Africa, published by DueNorth Media Africa, makes constant effort to ensure that content is accurate before publication. The views expressed in the articles reflect the source(s) opinions and are not necessarily the views of the publisher and editor.
The opinions, beliefs and viewpoints expressed by the various thought leaders and contributors do not necessarily reflect the opinions, beliefs and viewpoints of the Quarrying Africa team.
Quarrying Africa prides itself on the educational content published via www.quarryingafrica.com and in Quarrying Africa magazine in print. We believe knowledge is power, which is why we strive to cover topics that affect the quarrying value chain at large.
Printed by:
Contact Information
Email: munesu@quarryingafrica.com
Cell: +27 (0)73 052 4335
In an industry where environmental performance is considered the new currency, quarries and mines continue to shift their strategies and operating models to meet this new business imperative. To help the industry achieve its sustainability goals, leading bulk mining explosive and blasting technology supplier, BME, places value on sustainable solutions, innovation and security of supply. By Munesu
The critical role of quarries and mines in advancing economic development cannot be reiterated enough. At the same time, sustainability has become an underlying principle, with environmental, social and governance (ESG) performance considered the new currency in the industry.
In order to help support global sustainability goals, quarries and mines have in recent years accelerated their sustainability efforts. In a one-on-one with Quarrying Africa, Nishen Hariparsad, GM Technology & Marketing at BME, says beyond usual compliance imperatives such as health and safety, pro-sustainability actions have taken root in the industry’s quest to validate its social licence to operate, with blasting service providers being expected to contribute to customers’ efforts to lower their carbon footprint.
ShokoAs the first unit operation with a significant impact on downstream mining processes, blasting plays a big role in reducing a quarry’s overall carbon footprint. Through a full basket of complementary blasting technologies, coupled with advanced low-carbon emission emulsion explosives, BME continues to pave the way on the industry’s sustainability journey.
BME constantly innovates its explosive solutions and technology to provide customers with more efficient and productive operations – thus helping to reduce their energy consumption as well as the carbon emissions generated.
“As blasting and blasting technologies continue to evolve, we have encapsulated a suite of products, systems and services into a sustainable ecosystem of solutions that meets our customers’ needs,” says Hariparsad.
20 000
1 600
In order to help support global sustainability goals, quarries and mines have in recent years accelerated their sustainability efforts
Through a full basket of complementary blasting technologies, coupled with advanced low-carbon emission emulsion explosives, BME continues to pave the way on the industry’s sustainability journey
One of the key pillars of BME’s innovation roadmap has been digitalisation which has played a transformative role in improving blast outcomes
The Omnia Group’s focus over the past two years has been to strategically strengthen security of supply, all the way from sourcing of raw materials to the storage of finished products
Building on the flexibility and accuracy of electronic detonation, BME’s digital tools can make quarrying more efficient and less carbon-intensive through controlled blast energy, minimal waste, improved safety, lower energy consumption and optimal fragmentation. For example, with the use of flagship products such as BME’s premium electronic detonation system, AXXIS, together with the company’s BlastMap blast design software, whether independently or as a package, unlocking sustainable benefits for quarries and mines is made easier.
To provide context, while the AXXIS Titanium allows for
large blasts of up to 20 000 detonators, the AXXIS Silver is designed for up to 1 600 detonators – 800 per blast box, which is more than enough for the quarrying industry’s blasting requirements. The accuracy of detonation delays has been enhanced, reaching 0,0067% firing accuracy for consistent quality blasting that results in optimal rock fragmentation and consistency. The programmability of 15 seconds with 1-millisecond intervals allows for blast designs to be precision-designed, resulting in better fragmentation.
The benefits of good fragmentation are well documented, says Hariparsad. Firstly, it eliminates the need for costly secondary blasting or mechanical breaking of oversize material. Secondly, there is a positive impact on downstream processes such as load and haul. Crusher throughput also increases due to improved overall particle size distribution. The overarching benefit from all this is reduced energy consumption in the mining value chain, which in itself constitutes a sustainability effort achieved.
Over the years, BME has pioneered the inclusion of used oil in its emulsion explosives and is said to be the largest consumer of used oil in the explosives sector. This initiative contributes to a circular economy by safely disposing of used oil in a responsible manner, while preventing any of this oil from contaminating water or land.
It is estimated that it takes only a litre of oil to contaminate a million litres of water, making the safe disposal of oil a strategic global imperative – especially for water-scarce countries. BME’s used oil initiative is aligned
Blasting plays a big role in reducing a quarry’s overall carbon footprint.
with the United Nation’s Sustainable Development Goals (SDGs) – which focus on goals such as access to clean water, food security and eradication of pollution.
In South Africa alone, the company consumes almost 25-million litres of used oil annually and plans to increase its collection and processing capacity steadily over the next few years. The company’s oil collection network has evolved over time – aligning each phase with its ISO 9000 quality certification. It is also registered as an approved collector and processor with the Recycling Oil Saves the Environment (ROSE) Foundation.
BME’s sustainable manufacturing processes ensure security of supply – a 100 MW solar plant contributes to sustainable sourcing and decarbonisation.
In addition, BME is pioneering the use of dual salt emulsions in blasting operations. Dual salt emulsions are less harmful in terms of nitrate contamination and greenhouse gas emissions than single salt emulsions. These emulsions can be transported long distances, pumped multiple times, and still provide improved performance, such as high energy in a blast.
The recent acquisition of a minority stake in Swedish-based Hypex Bio Explosives Technology by BME’s parent company, Omnia Holdings, further positions BME ahead of its competition in terms of sustainable emulsions. Hypex has developed the first nitrate-free explosive emulsions in the market and reduced the carbon content by 90% over traditional sources. This technology has the potential to completely change the explosives supply industry.
The mining industry of today, says Hariparsad, is dependent on technology and innovation to improve efficiency, safety and environmental sustainability. Consequently, BME believes in incessant innovation to continue delivering on the evolving technological needs of the industry.
“As mining companies shift their strategies and operating models to leverage digital transformation and cloud-based technologies, we see blasting technologies playing a critical role in delivering bottom line improvements for the mining value chain, more so for quarries that are cost-sensitive by their very nature,” he says.
For BME, adds Hariparsad, innovation in various technologies across all streams of the company’s product stack is not about feature benefits, but rather a strategic imperative to remain relevant through industry-leading technologies that provide data, analytics, digital connectivity and integrated automation across all functional streams.
One of the key pillars of BME’s innovation roadmap has been digitalisation which,
according to Hariparsad, has played a transformative role in improving blast outcomes, enhancing safety and efficiency as well as achieving environmental sustainability.
By integrating advanced digital technologies, quarries and mines can optimise blast designs, reduce waste and minimise their environmental impact. BME’s digitalisation seeks to decrease inputs and increase outputs and raise safety levels in mining processes.
One of the design focus areas for BME has always been the integration of its own systems, also incorporating third-party solutions that customers might have at their operations. For example, BlastMap, the company’s blast design software now integrates with Xplolog, a system for capturing and analysing data on blast holes and decks, which further integrates with BME’s mobile manufacturing units (MMUs), allowing the operator to charge and top up holes accurately from the source application. This, says Hariparsad, represents an ecosystem of blasting software and digital technologies
providing real-time data at various levels of the blasting value chain.
With digitalisation comes a lot of data which, according to Hariparsad, has become ‘king’. However, he highlights the importance of understanding the data to address customer pain points. “We are therefore building a repository of information that targets key elements of not just the blasting process, but the mining value chain at large, because we acknowledge that these are all interconnected,” he explains.
“Our blast design data can ‘talk to’ drilling data, which in turn ‘talks to’ geological data. Utilising this data across all streams of the mining value chain, including crushing and screening, allows us to better paint a complete picture. Operations can only realise value downstream if they understand what their pain points are. Having access to data and making sense of it makes it possible,” he states.
Apart from technological advances, Hariparsad believes that one of the key trends to emerge in the aftermath of the Covid-19 pandemic is a re-focus on the security of supply for key mining inputs such as explosives.
The industry’s supply chains, he says, had been honed for many years to become as cost-efficient as possible, often driven by the ‘justin-time’ philosophy. The economic lockdowns, closure of borders and logistical disruptions worldwide have led to a re-evaluation of this approach.
Customers now tend to be more concerned about security of supply, and often adopt more of a ‘just-incase’ attitude. It was interesting to note that, throughout the Covid-19 disruption, BME was able to continue supplying its customers within and across borders without a single stock-out.
“The Omnia Group’s focus over the past two years has been to strategically strengthen security of supply, all the way from sourcing of raw materials to the storage of finished products. We have multiple suppliers of raw materials, various
transporters and plants, to ensure that all possible risk is sufficiently mitigated,” says Hariparsad.
Omnia Group is the only producer in South Africa that has a dual supply of ammonia, a key feedstock for all emulsion blasting providers, which ensures security of supply. “We have redundancy of supply, not just at our operations, but also at customer sites to ensure that we keep minimum stock levels all the time.”
In addition, BME’s sustainable manufacturing processes ensure security of supply. Its initiatives in green hydrogen, green ammonia, water recycling, grey harvesting and a 100 MW solar plant all contribute to sustainable sourcing, which in turn delivers security of supply for customers. These projects are particularly significant in South Africa, where the company has to grapple with power shortages, constraints in water infrastructure and challenges in logistics infrastructure.
Leveraging lessons from its home market of South Africa, this approach has been replicated in international markets where BME has a presence as part of its globalisation strategy. Over the years, BME has developed a wellcrafted globalisation strategy which has strategically positioned it in growing markets outside of its home base of South Africa and Africa. Its growth strategy in markets such as Australia, Asia and the Americas hinges on the expansion of its manufacturing footprint to ensure security of supply.
In summary, Hariparsad says the company’s growth strategy and its business imperatives are interconnected. “We do this to remain inoculated against the challenges of the system, while promoting the greatness of the values that we offer, namely sustainable solutions, integrated ecosystems of products and services, resource efficiency, contribution to the circular economy, responsible business partnerships, as well as safety and reliability for our people and the communities in which we operate,” concludes Hariparsad. a
Despite the economic headwinds in South Africa, Heinrich Schulenburg, MD of Wirtgen Group South Africa, sees some positives to write home about in the construction sector. It is, however, in countries bordering South Africa where the company has experienced significant growth in the past two years. Looking ahead, Schulenburg believes that Wirtgen Group SA’s next wave of growth will be driven by the Kleemann range of crushers and screens. By Munesu
Shoko.That the South African economy has faced headwinds in the past decade is no overstatement. Chief among them has been the rolling scheduled power cuts (load-shedding), which started in 2007 and have intensified exponentially, reaching close to nine hours daily in 2022. This has had a devastating impact on several economic sectors.
The construction sector, reasons Schulenburg, has had its own fair share of obstacles. Principal among them has been the lack of spend by state-owned enterprises (SOEs), not necessarily because of the shortage of capital, but due to the lack of capacity to implement projects.
Positives
“Despite the apparent negative trajectory in the growth of the economy, I believe there are some positives to dwell on,” says Schulenburg. “As a
major equipment and technology supplier to the construction industry, we have seen some doubledigit growth of the market in the past two years in South Africa, although from a very low base.”
To provide context, the South African road construction equipment market – including product groups such as recyclers, milling machines, pavers and rollers, amongst others – has contracted from about 630 units in 2013 to 330 in 2023. However, Schulenburg says despite the drastic decline during that period, the market has seen some progress over the last two years, recording a 17,8% growth between 2021 and 2022 and a 21,6% increase between 2022 and 2023. Despite the consecutive double-digit growth, the market is only half of its 2013 sales volumes.
Another positive to highlight, says Schulenburg, is the recent Infrastructure Fund, which he believes is likely to boost the much-needed infrastructure
The South African road construction equipment market – including product groups such as recyclers, milling machines, pavers and rollers, amongst others – has contracted from about 630 units in 2013 to 330 in 2023
Despite the apparent negative trajectory in the growth of the South African economy, there are some positives to write home about in the construction industry
The construction equipment market has seen some double-digit growth in the past two years in South Africa, although from a very low base
Countries bordering South Africa have chipped in with significant growth for Wirtgen Group SA in the past two years, especially Zimbabwe, as well as Botswana and Namibia
Significant future growth for Wirtgen Group SA will come from the Kleemann brand, with big opportunity from both the aggregates and mining markets
investment in South Africa. Announced by South African President Cyril Ramaphosa in 2018, the aim of the Infrastructure Fund is to transform public infrastructure through bespoke blended financing solutions, using means such as sourcing and blending capital from the private sector, institutional investors, development finance institutions and multilateral development banks.
In addition, Schulenburg says the pension fund, which by law is now allowed to invest in infrastructure, is sitting on the cusp of an infrastructure boom that provides an excellent opportunity for diversifying portfolios and
R750-million
Wirtgen Group SA sees a positive outlook for the business in 2024, with a substantial R750-million worth of deals in the pipeline
supporting the development of critical infrastructure for the country.
The growth in popularity of public private partnerships (PPPs) – not so much in road construction but in other areas such as renewable energy – is encouraging and holds the key to more investment into public sector projects and more effective public resources management.
On the project rollout front, Schulenburg commends the South African National Roads Agency Limited (SANRAL) for its usually well designed and executed projects. The roads authority has announced a R28billion injection into the construction industry for the first half of the 2024. The announcement comes after SANRAL closed 77 tenders worth R6,43-billion in December 2023. This, he says, is encouraging and will keep the construction industry ticking in 2024.
While South Africa still exhibits pockets of opportunity in the face of economic obstacles, Schulenburg says it is countries bordering South Africa that have chipped in with significant growth during the past two years, particularly Zimbabwe, as well as Botswana and Namibia.
While Botswana has in recent years turned its infrastructure development attention to water and pipelines, Schulenburg says its focus is seemingly turning back to roads and bridges. Despite it being a small market, Namibia has also shown signs of growth on the construction front.
In Zimbabwe, construction activity has been a major growth driver for Wirtgen Group SA. The Zimbabwean government has embarked on massive reconstruction and rehabilitation projects on major road networks to enhance both domestic and regional connectivity.
Of note is the nearly 600-km Harare-Masvingo-Beit Bridge highway, which is now almost complete with many parts of the road open to traffic. Part of the North South Corridor, which begins in Durban, South Africa, passing through Zimbabwe and ending in Lubumbashi, the DRC, the project is divided into three sections: the 580-km Harare-Masvingo-Beit Bridge highway with its eight toll plazas, the 342-km Harare-Chirundu highway, and the 59-km Harare Ring Road with three toll plazas.
Meanwhile, the Mbudzi Interchange Project is said to be halfway complete. For years, the old Mbudzi roundabout has been a major traffic hold-up in Harare, which is why government committed US$88-million to turn it into an interchange. Elsewhere, work on the Beitbridge-Bulawayo-Victoria Falls Highway, another strategic trade route in the regional North South Corridor, has commenced, marking another significant
construction project in the country.
“Leveraging the exceptional support of our capable dealer, Machinery Exchange, Zimbabwe has been an outstanding market for us,” says Schulenburg. “On the back of government’s massive investment in road infrastructure projects in recent years, we have had major successes in marketing our products.”
Commenting on some major milestones, Schulenburg tells Quarrying Africa that the company has sold about seven Wirtgen recyclers, nine Vögele pavers and about 30 HAMM rollers in Zimbabwe alone in the past two years. Wirtgen Group SA has also recently delivered its first ever Ciber mobile asphalt plant in Zimbabwe. Known as the iNOVA 2000 model, it has been successfully commissioned and already has produced numerous tonnes of asphalt for major road projects.
“We have also been successful with our Kleemann range of crushers and screens, which have been deployed on borrow pits that supply main road works in the country. In fact, we have delivered two trains – each comprising an MC 110 EVO2 jaw crusher, an MCO 9 EVO2 cone crusher and an MSC 703 EVO screen. We also have two more Kleemann trains on order, which are scheduled for delivery in 2024,” he says.
Commenting on some emerging trends in these markets, Schulenburg notes a growing appetite for new technologies in Zimbabwe and Botswana. This is in direct contrast with South Africa, where there is a general belief that technology takes away jobs from workers. Consequently, he says, the market continues to “fight its way into older technology”, which is less productive.
“Zimbabwean and Botswanan contractors are much more open to new technology, mainly because they fully understand that using machinery does not inhibit job creation. A machine does things efficiently and at a perfect quality level. These contractors are now reaping the benefits of increased productivity and ultimately lower costs of projects,” he says.
Apart from technology adoption, Wirtgen Group SA has adopted a new approach in the past two years, which has seen the company investing heavily in stock. This is aimed at shortening lead times
for contractors, especially given the challenges associated with global supply chains and the delays at South African ports. In addition, the company has strengthened its used equipment offering to ensure it has a comprehensive offering for all customer profiles, especially cash-strapped start-up construction contractors.
Looking ahead, Schulenburg sees a positive outlook for the business in 2024, with a substantial R750-million worth of deals in the pipeline. He is encouraged by the Kleemann range of mobile crushers and screens, which is gaining traction after a slow start in the market.
“We have initially struggled to gain traction with the Kleemann brand. It is always difficult to introduce a new product, especially in a market where there are already some established brands. We are doing quite well with Kleemann in Zimbabwe and Botswana. In addition to the orders of two trains in Zimbabwe, we have another train on order in Botswana,” he says.
In fact, he adds, significant future growth for Wirtgen Group SA will come from the Kleemann brand, with big opportunities from both the aggregates and mining markets. The Kleemann range distinguishes itself with a range of capabilities. Firstly, says Schulenburg, it is a sturdy machine – the stability of the chassis results in better crushing performance, and this has been proven on many reference sites where the machines have been deployed.
“Another key competitive edge of the Kleemann offering is its lower fuel consumption, largely driven by new technology engines combined with on-board generators that drive most components. This is particularly important for customers in our region where fuel prices are prohibitive. A Kleemann train on average achieves anything between 20% and 30% better fuel consumption than most of our competition. It is even much more efficient with the dieselelectric option,” says Schulenburg.
To close a crucial gap in its Kleemann offering, Wirtgen Group SA will introduce a smaller impact crusher during the first half of this year – the MR 100 NEO. The new machine will be suited for smaller crushing operations such as brickyards and recycling applications. a
This flagship Lintec CSD2500B containerised asphalt mixing plant in Zambia features a modular construction that is fully enclosed in ISO certified sea containers. The benefits of our industry-leading range of Lintec CSD containerised asphalt plants include easy transportation and rapid installation, making it ideal for both small and big projects.
See you at Gallagher Convention Centre, Johannesburg, South Africa
4 Jun - 6 Jun Booth No. 603
www.lintec-linnhoff.com
info@lintec-linnhoff.com
Elsie Snyman, CEO of Industry Insight.Although the South African construction industry experienced another difficult and challenging year in 2023, turnover in the sector recorded a moderate 4% growth for the first three quarters
Residential construction growth slowed to 5% YoY in the first three quarters, following a double digit increase during 2022
There has been a robust increase in civil tender activity, with the estimated nominal rand value of civil tenders up 29% YoY in 2023, with most of the provinces showing an increase compared to 2022
The total number of road contracts out to tender increased by 11% YoY in 2023, with an increase of 66% from SANRAL
Despite a generally challenging environment for the South African construction sector in 2023, the industry recorded some moderate growth of 4% in the first three quarters. If infrastructure spending, particularly in economic infrastructure or civil construction, is anything to go by, Elsie Snyman, CEO of Industry Insight, believes that the outlook of the sector has certainly improved. By Munesu Shoko.
Speaking exclusively to Quarrying Africa, Snyman says although the South African construction industry experienced another difficult and challenging year in 2023, turnover in the sector recorded a moderate 4% growth for the first three quarters, recovering from a 10% decline in nominal terms in 2022. This is according to Stats SA’s quarterly financial statistics, which somehow differs from the gross capital formation estimates that have shown an average increase of between 8% and 9% in 2022 and 2023 (first three quarters).
Snyman notes that gross fixed capital formation estimates entail a broader definition for construction, and that includes machinery and equipment used in the sector. To provide context, actual turnover in construction was around R95-billion lower compared to gross fixed capital for the sector (including construction works, residential and non-residential investment). With the rapid growth in renewable energy projects, Snyman notes that the impact of imported machinery and equipment is more profound on official investment estimates and can be misleading.
Commenting on sector performance in 2023, Snyman says residential construction growth slowed to 5% year-on-year (YoY) in the first three quarters, following a double digit increase during 2022, whereas nonresidential investment growth accelerated from 2% to 11% YoY, during the same period.
“It must be noted, however, that investment growth in the non-residential market is coming off a dismally low
9%
There was around R8-billion more invested in buildings up to September 2023, with R11-billion added to construction works, representing a nominal increase of 9%
60%
The estimated value of road tenders rose 60%, with SANRAL a major contributing client
in the 2023 Budget.
base, as private sector demand in this sector has declined substantially over the last few years,” she says. “There was around R8-billion more invested in buildings up to September 2023, with R11-billion added to construction works, representing a nominal increase of 9%.”
The construction labour force reacted positively to the moderate increase in investment, and expanded by an average of 116 000 work opportunities, or 10%, recovering to 2018 levels in the process and even surpassing preCovid levels.
“Some provinces significantly outperformed others, with the construction labour force in the Western Cape reaching record high levels and Northern Cape, albeit a smaller province in economic and construction terms, coming close to breaching its own record. Several other provinces have exceeded their long-term average, including KwaZulu-Natal, North West, Mpumalanga and Limpopo,” says Snyman.
Margins were also better, with contractor profitability improving to an average of 5% by the end of September 2023, compared to an average of 2,4% in 2022, although larger contractors are still underperforming against the industry average, with an average margin of around 3%.
Although confidence amongst building and civil contractors reached its highest level since 2017, Snyman says the majority of contractors are still feeling rather pessimistic.
It was a difficult year for the listed construction sector companies, as average market capitalisation values declined by an average of 22% YoY for retailers and contractors, and around 2% for construction material suppliers such as Afrimat, PPC and Sephaku.
Interestingly, the cumulative market capitalisation of
retailers in construction (including Cashbuild and Italtile) represented only 7% of the total market capitalisation values of contractors in 2008, but was 14% higher by comparison in 2023, as contractors lost 80% since 2008 (excluding Group Five and Basil Read). On the other hand, Wilson Bayle Holmes and Stefanutti Stocks outperformed the average, with average market cap values up by between 42% and 66% compared to 2022. Afrimat bucked the trend in terms of suppliers, while Cashbuild and Italtile both recorded weaker values on average in 2023.
If infrastructure expenditure is anything to go by, then, says Snyman, the outlook of the construction sector has certainly improved. However, she says, this largely relates to economic infrastructure, or civil construction. Investment in the civil sector is largely public sectordriven, and with anticipated higher levels of investment coming from the private sector, that will add more impetus for improved growth rates in the sector.
“On average, President Ramaphosa has mentioned infrastructure in his State of the Nation Address (SONA), 66% more times during this four-year tenure than Jacob Zuma did during his entire tenure. The 2023 SONA alone referred to infrastructure a record number of 22 times since the 1994 SONA. This shows that the need for infrastructure expenditure has clearly become a national priority,” says Snyman.
Sadly, adds Snyman, infrastructure was not as prominent in the 2024 address compared to 2023. This, she says, does not mean however, that the Budget for 2024 will be reprioritised lower, as the momentum set in 2022 and 2023 should filter
through to higher infrastructure expenditure. The question is whether the momentum will be sustained for at least the next three to five years, or even post-election.
The focus is largely to mitigate the current crises in energy, transport and logistics, as this has had the direst economic impact, which means, concerningly, there is less focus on social infrastructure expenditure (housing, education and health). So, she says, there is not much expected in terms of government support in investment in buildings. This will see continued pressure on investment in buildings following last year’s contraction.
To provide context, private sector demand for buildings deteriorated in 2023, with approvals for new construction work down 16% YoY in the 12-months up to November 2023 (measured in square metres). The residential sector was particularly hard-hit, with approvals declining by 21%. However, Snyman notes that there is some momentum in terms of commercial office space approvals, coming off a dismally low base, with approvals up 26% by November 2023, support also coming from retail space (up 4%) and renovations recording a second year of double-digit growth.
The industrial sector, previously the star performer in the non-residential space, is much weaker, with approvals declining by 16% in 2023. While there may be pockets of growth, the overall impact at a national level is weaker expected investment into the non-residential sector, aggravated by declining demand in the residential market.
Investment in buildings has shown no recovery since Covid hit in 2020, and with heightened political uncertainty, the impact of higher interest rates along with dismal economic performance, it seems unlikely that the building industry will recover any time soon.
“On the upside, we may have reached the turning point in terms of interest rates, with a broad consensus that interest rates will start to ease at a moderate pace in the second half of 2024, hoping to reach normality (around 10%) by the end of 2025,” she says.
Economic growth forecasts remain weak, however, with most projections not expecting economic growth to breach 2% in the next three years; previous forecasts of
SANRAL is the most prominent player in the road sector, and any delays to tender adjudication has a significant impact on the industry.
around 1,5% for 2024 have already been revised lower, to around 1%, given the state of key institutions such as Eskom and Transnet.
“What we have seen, however, is a rather robust increase in civil tender activity, with the estimated nominal rand value of civil tenders up 29% YoY in 2023, with most of the provinces showing an increase compared to 2022,” says Snyman. “The estimated value of road tenders rose 60%, with SANRAL a major contributing client.”
Tender activity, she says, generally accelerates in the run-up to an election year, as evidence has shown historically, so one cannot help but be concerned that the current momentum in tender activity is going to slow down post-election (as it almost always does). The awarding of contracts has also been a problem, but there seems to have been some progress in 2023, as the pace of awards in civil tenders has improved. The big question, says Snyman, is around sustainability of this momentum and the infrastructure expenditure estimates projected for the next three years.
“SANRAL is the most prominent current player in the road sector, and any delays to tender adjudication has a significant impact on the industry. It is therefore imperative that any unnecessary delays, as experienced in 2023, are prevented in the future. Uncertainties created by the Public Procurement Bill, passed in December 2023, have severely impacted the construction sector, with multibillion-rand projects being delayed by a wave of court interdicts that could have been prevented,” she says.
SANRAL has a significant footprint across all provinces, where it remains the dominant player in road construction, except in the Western Cape. The total number of road contracts out to tender increased by 11% YoY in 2023, with an increase of 66% from SANRAL. All in all, despite the delays, conditions for the road segment have improved.
Commenting on some trends in the market, Snyman says a few things are at play that could ultimately transform the construction landscape. Of note is the increasing role of the private sector in economic infrastructure development. The result is a rather robust expansion of public-private partnerships (PPPs), which is currently taking place at an unprecedented level.
The upside of a broad-based infrastructure collapse that is having a debilitating impact on the economy, is the acceleration of privatisation as government scampers to find appropriate and ‘fast’ solutions to the economic crisis. For now, she says, this is still very much focused on energy distribution, but the platform for greater participation in transport and even water services is being laid.
is not by any means perceived to be under control, with the construction mafia still overpowering many projects across the country.
“We have already seen an increase in the announcement of large scale, or high economic impact, PPP projects in 2023, expected to filter through even to local government level. Developmental plans associated with green hydrogen are also moving at a faster than expected pace and can transform the provincial landscape for provinces such as the Northern and Eastern Cape,” says Snyman.
Part of this privatisation process is to streamline the regulatory framework and to bring greater consistency within the various policy frameworks, in order to reduce uncertainties. Business confidence remains depressed, however, given the fact that corruption in South Africa
“I must say, however, that I feel there is a fundamental shift presently taking place, where government and the private sector can finally take hands and share the developmental responsibility so desperately needed for the country.
2024 is likely to remain another challenging year, with the IMF’s latest economic forecast for South Africa having been revised lower to just 1% and the impact of higher lending rates on consumers still rippling through the economy, and expected to continue to do so for at least the next two years,” she says.
In conclusion, Snyman says the biggest wildcard is the 2024 National Election (one of many across the world) that may result in weaker tender activity, directly impacting the construction sector, where political appointments are affected, or even potentially, a complete revision of the country’s economic policy. The local construction sector almost always pays the price for these political changes, especially at local government level. a
The curved line to profit
If you want to significantly increase productivity, reduce energy consumption, and extend tool life you need the most advanced top hammer tool system ever made. Meet the curved thread CT55 and CT67 for hole sizes from 89 to 140 mm.
A year into her rein as director of ASPASA, Letisha van den Berg has covered extensive ground in the quest to give small-scale miners the much-needed voice. In a one-on-one with Quarrying Africa, she unpacks some of the milestones achieved thus far, pressing matters of concern to the industry and key focus areas for the association this year. By Munesu Shoko.
Ayear ago, Van den Berg assumed her role as the director of ASPASA, the association for small-scale surface miners in South Africa. On her immediate to-do list was a range of pressing issues for the industry, including amplifying the voice of small-scale miners, re-engaging several key stakeholders and addressing compliance issues, amongst others.
“The first year has been a rollercoaster of learning and engagement with various stakeholders,” she says. “It has been an amazing learning curve for me personally, which has also presented the association with the right platforms of engagement to afford a voice to small-scale miners.”
The first year, she says, was largely about engagement and there were several successes achieved in that regard. Firstly, consultation with
A year ago, Letisha van den Berg assumed her role as the director of ASPASA, the association for smallscale surface miners in South Africa
The first year was largely about engagement and there were several successes achieved in that regard
ASPASA used last year to maximise engagement with its parent association, the Minerals Council South Africa
Change management, both from a strategic and operational perspective, will take centre stage this year
This year, ASPASA will inaugurate its own annual one-day conference, which is scheduled to take place on October 31 at a venue yet to be confirmed
the legislator was of paramount significance. Van den Berg secured a one-on-one with the chief inspector of mines, a principal figure at the Department of Mineral Resources and Energy (DMRE), who has opened the door for the association to interact with the regulator on a regular basis.
In addition, ASPASA used last year to maximise engagement with its parent association, the Minerals Council South Africa. As part of that process, Van den Berg successfully held a meeting with the new CEO, Mzila Mthenjane. As a member of the Minerals Council, ASPASA seeks to leverage the organisation’s influence and resources to find lasting solutions for quarries and smallscale miners in general. The Minerals Council represents about 95% of mines in South Africa and is a leading voice when it comes to lobbying on behalf of the industry.
As part of the engagement process, ASPASA also met with Reginald Demana, the new CEO of the South African National Roads Agency Limited (SANRAL), a key stakeholder in the quarrying fraternity. Some of the key issues of discussions included quality of aggregates and areas of cooperation in the best interests of both organisations.
During Van den Berg’s first year, ASPASA managed to set up new networks, for example, with the Agricultural Business Chamber of South Africa (Agribiz), a voluntary, dynamic and influential association of agribusinesses operating in South and southern Africa. Given Agribiz’s track record in creating an environment in which agribusinesses of all sizes and in all sectors can thrive, expand and be competitive, ASPASA seeks to collaborate with like-minded organisations in the quest
Under the theme, “The World of Quarrying in 2050”, this year’s conference will focus on the future of the industry in an everchanging world
to advance the success of its own members.
“We also had a very good discussion on insurability of operations. On this platform, we demonstrated how our audit protocols can help mining operations be insurable at lower premiums. That discussion opened new doors at Santam, a leading insurer in South Africa, to engage our members and provide insurance that speaks directly to the needs of small-scale miners,” explains Van den Berg.
In 2023, ASPASA also secured two partners – Implats and AMSA – to help with training of Government Certificate of Competency (GCC)engineers. As part of the qualification process, GCC engineers need exposure to an underground mining environment, and the two mining companies have agreed to provide access to ASPASA members.
Joining forces with the Institute of Quarrying Southern Africa (IQSA) has paid dividends for the two associations and the industry at large, says Van den berg. For example, the two organisations have made significant headway in training. For instance, they have managed to map career paths for all key positions in the quarrying sector. Through a combined effort between IQSA and ASPASA, the next step is to link all career paths with the Mining Qualifications Authority (MQA) training to help members align their MQA training with a career path of their choice in the quarrying sector.
Another key milestone for Van den Berg was visiting all top performing mines across the country, taking a gift to every member of the operation. “It is important for us as the ASPASA to recognise those on the ground, the foot soldiers, who make it happen on a daily basis,” she says.
A major talking point during her first year was also the advances made in the Royalty Tax case. Over the years, payment of royalties has been a hotly contested issue among quarry owners and operators as to where the value of a mined product needs to be determined in order to calculate exact payments. The industry’s dispute with the South African Revenue Services (SARS) exists over the first point of sale at which the value of royalties needs to be calculated. The ‘taxman’ argues that royalties should be calculated from the stockpile, while the industry insists that it should be from the muckpile.
“The issue of Royalty Tax has been dragging on for years, making it costly for members. Official engagements started as far back as 2009. I am glad to announce that we have made significant headway – we have now applied for a court date and we are seeking a declaratory relief,” she says.
Van den Berg has also been successful in the quest to grow membership. Through collaborative efforts between herself, auditors and the Management Committee, ASPASA added four new producer members last year and a few associate members.
Van Den Berg’s tenure at ASPASA coincided with the gazetting of the Collision Avoidance Systems (CAS) regulations by the DMRE in December 2022. She tells Quarrying Africa that some operations have already been issued with Section 54 orders for not implementing Level 9 technology, which she believes is too soon.
One of the concerns regarding the enforcement of the CAS regulations is the inconsistence between regions. Certain regions, explains Van den Berg, call for Level 9 implementation at all costs, while others follow the riskbased approach as per the legislation. These were some of the issues that ASPASA managed to raise with the chief inspector of mines.
“Let me put it on record that both the Minerals Council and ASPASA are for saving lives. One fatality or injury is too many. However, we ask the inspectorate to consider what risk assessments and hard controls have been put in place to protect lives at a mine. The regulation clearly states that if a mine has significant risk, it needs to reduce it. It can do that through traffic management, which can eliminate significant risk,” she says.
That said, Van den Berg says the quarrying sector must realise that the move towards new technology is gaining momentum. She calls on members of ASPASA to start engaging suppliers of CAS technology, which not only protects lives, but also helps reduce costs of operation and productivity.
“We must continuously look at our risk and investigate fitting technologies. Risk can be reduced through traffic management, but it is also advisable to look at costeffective technologies that speak directly to the needs of an operation. We must also understand that apart from safety, technology helps us improve efficiencies and productivity on site,” she says.
To help ease the burden of economic challenges for ASPASA members, Van den Berg implemented a levy structural change. Traditionally, ASPASA had a flat membership fee for associate members which did not differentiate between the size of operations. For example, a company with five people had to pay the same
membership fee as an entity with 100 people. Members have been split into small, medium and large operations, and now pay a fee in line with their size category.
“Our producer members have always paid based on a rand per tonne structure, which in my view is still fair. When you are a small operation, obviously your tonnages are small and you pay accordingly, which I believe is a fair structure that we have maintained,” she says.
Apart from levies, ASPASA offers free information-sharing platforms for members. Leveraging its wide network, the association brings experts on board to impart knowledge on several subjects that affect the industry.
In her second year in charge, Van den Berg has set her sights on several focus areas. Chief among them is to improve internal engagement through the recent reorganisation of regions. Previously, she says, there were too many regional meetings. Regions have therefore been restructured in order to remedy the situation. The Western Cape has been combined with Northern Cape and Eastern Cape, while Gauteng and North West have been merged. Limpopo and Mpumalanga are now a single region, and so are KwaZulu Natal and the Free State.
“Previously, we had two health and safety as well as two environmental meetings. As part of a newly adopted structure, we are going to have four meetings a year, but we will combine both environmental and health and safety to make it more impactful,” she says.
This year, ASPASA will inaugurate its own annual one-day conference, which is scheduled to take place on October 31 at a venue yet to be confirmed. Under the theme, “The World of Quarrying in 2050”, this year’s conference will focus on the future of the industry in an everchanging world.
In terms of training, the association has identified areas of immediate attention across subjects, including health and safety, environmental and social compliance. In addition, change management, both from a strategic and operational perspective, will take centre stage this year.
ASPASA will also cast the spotlight on the Mine Health and Safety Council (MHSC) milestone reporting this year, which is related to a mine’s exposure to noise and dust as well as cultural transformation. If done correctly, mines can get up to a 10% discount on their MHSA levies. ASPASA is also on the MHSC board.
“In conclusion, we intend to automate our statistics this year. This initiative was on our radar last year, but we started the project very late in the year. We will also focus our efforts on helping members comply with blasting regulations, particularly the issue of blasting within 500 m of buildings, infrastructure and communities,” concludes Van den Berg. a
Different quarries need different cone crushers. Weir Minerals is the only global manufacturer that offers both. TRIO® live and xed shaft cone crushers are made for modern quarries with advanced hydraulics, wear resistant materials and the latest technology. You get what’s right for your circuit. No unnecessary redesigns needed. Plus, with a lifelong commitment from the Weir Minerals global network, we’ve got you covered. Visit info.global.weir/trio
For the third year running, Free State-based Afrimat Qwa Qwa scooped the overall Top Performer position.
Following high levels of compliance and implementation of practices and principles exhibited in the 2023 ISHE Audit, ASPASA members have once again demonstrated their commitment to the health and safety of employees and interested parties affected by their operations. By Munesu Shoko.
A total of 81 audits was conducted during 2023, with an average score of 89,84%
97,59%
For the third year running, Free State-based Afrimat Qwa Qwa scooped the overall Top Performer position with a 97,59% score
97,27%
BluRock Quarry was named the overall runner-up and Top Independent Performer with a 97,27% score
n the quest for ‘Zero Harm’, members of surface mining industry association, ASPASA, have over the years placed safety at the centre of their operational activities, and 2023 was no different. In a one-on-one with Quarrying Africa, Marius van Deventer, Health and Safety auditor at ASPASA, says ‘Zero Harm’ has become a catchphrase in the mining sector and ASPASA members have once again shown that it is achievable.
“Members who participate in the ISHE Audit process understand and accept their responsibilities when it comes to health and safety compliance,” says Van Deventer. “All participants should be commended for their efforts and enthusiasm to achieve high levels of compliance.”
The ISHE Audit covers all functions on the mine or quarry that fall under the legal requirements of the Mine Health and Safety Act and applicable regulations. Audits were also conducted at member operations governed by the Occupational Health and Safety Act. Both audit
protocols are revised annually in line with new legal requirements and industry standards.
The audit process entails in-depth inspections of facilities at the quarry or mine, as well as the inspection of the documentation of the Health and Safety System. Own legal registers, inspections, pre-start checklists, licences to operate machines and isolation records are among some of the critical documents assessed during the auditor’s site inspection.
The auditor has in-depth knowledge of the legal requirements for technical, plant, machinery and mining area requirements and these are also evaluated for compliance. The main aim of the entire audit process is to provide guidance and add value to the industry’s quest for Zero Harm. Knowledge is shared right across the industry to uplift the understanding, behaviour and attitude towards health and safety, says Van Deventer.
Every year, the auditor highlights areas of the audit scope that members should improve on. Van Deventer commends
members audited in 2023 for the general improvement at the majority of sites. One of the key initiatives implemented at industry level during 2023 was the sharing of information – a crucial aspect of the auditing process.
“It is encouraging to see that quarry managers are always eager to learn from one another to improve the health and safety performance of their own operations,” says Van Deventer. “One of the positive takeaways from the 2023 audit was the health and safety conditions sustained and maintained throughout the industry, even
“One of the positive takeaways from the 2023 audit was the health and safety conditions sustained and maintained throughout the industry, even under difficult conditions.
In the quest for ‘Zero Harm’, ASPASA members have over the years placed safety at the centre of their operational activities, and 2023 was no different
Following high levels of compliance exhibited in the 2023 ISHE Audit, ASPASA members have once again demonstrated their commitment to health and safety of employees
No mining fatalities were recorded at ASPASA member operations during the audit period
Full implementation of effective Traffic Management Plans will take centre stage in 2024
under difficult conditions.”
Van Deventer also commends the industry for the general improvement in compliance to machine guarding requirements. Another key observation was that mine developments were done in accordance with mine planning guidelines and there were no serious incidents recorded because of mine failures.
In fact, no mining fatalities were recorded at ASPASA member operations during the audit period. Van Deventer says this is a true reflection of employees’ knowledge and understanding of the industry’s drive for Zero Harm.
1
However, Van Deventer has also noted a few areas of concern highlighted in the 2023 ISHE Audit. While members continue to demonstrate high levels of compliance, some serious injuries were unfortunately recorded at some member operations during the audit period. “This is very unfortunate, and steps have been taken to prevent recurrence,” he says.
In some cases, the investigation of accidents and incidents is still questionable. Members, he says, should conduct thorough investigations to identify the root cause of every accident on site and subsequently establish control measures to prevent these from happening again.
“Too many lost time injuries, disabling injuries and reportable injuries were recorded during the auditing period,” he says. “In 2024, more effort should be directed towards the identification of risks and/or noncompliances. Member operations should also strive to improve their own inspections and pre-start inspections for plant and trackless mobile machinery.”
In addition, full implementation of effective Traffic Management Plans will take centre stage in 2024. Operations, adds Van Deventer, should also
strive to improve housekeeping on plants to reduce dust exposure and the dangers of running machinery.
Other key focus areas for 2024 include full compliance to isolation and lockout requirements; attention to accident/ incident investigations to establish root causes; Planned Task Observations to eliminate accidents and incidents, nearmiss reporting and recording of Section 23 refusals and improved contractor management, as well as emergency training and mock drills, should be of prime importance.
A total of 81 audits was conducted during 2023, with an average score of 89,84%, up from 88,91% in 2022. Of the 70% of members audited, 90% achieved scores of 90% and above, demonstrating high levels of compliance. The highest score of the audit was 97,59%, with the lowest being 68,97%.
For the third year running, Free Statebased Afrimat Qwa Qwa scooped the overall Top Performer position with a 97,59% score, while KwaZulu Natal-based BluRock Quarry was named the overall runner-up and Top Independent Performer with a 97,27% score. Midmar Quarry achieved a Showplace Status for the fifth consecutive year, with a 96,52% score.
“The results of the 2023 ISHE Audit are still of an extremely high standard and all participating members should be commended for their exceptional effort and commitment to health and safety. Overall feedback from members was incredibly positive and the consistent feeling is that the process does add value to every operation and contributes significantly to members’ Zero Harm efforts,” concludes Van Deventer. a
BME’s AXXIS Silver electronic detonation system raises the bar on safety, efficiency and sustainability, for quarries and smaller mines.
Vibration control for ease of use
Precision for reduced operational costs
Accuracy to prevent environmental issues
To help its customers navigate tough market dynamics in an unpredictable operating environment, UD Trucks Southern Africa has reiterated its renewed focus on total cost of ownership (TCO), highlighting a myriad of initiatives to assist fleet owners in reducing both their fixed and variable costs. By Munesu Shoko.
Despite the tough regional and international economic conditions, the South African commercial vehicle market once again experienced solid growth in 2024. This was the overarching message from UD Trucks Southern Africa’s annual press conference held on January 31, 2024.
Overall, the new vehicle market recorded a total of 32 169 sales, up from 29 455 in 2022, representing a 9,2% growth. UD Trucks Southern Africa equally concluded the year with a solid sales growth. While 2023 was certainly not ‘a walk in the park’, Filip Van den Heede, MD of UD Trucks Southern Africa, says the company is pleased to have successfully lived up to its holistic proposition –“delivering transport and service solutions that the world needs today”.
“In pursuit of this goal, we have accomplished various objectives, including retail excellence, introducing innovative transport solutions, enhancing our aftersales offering to reduce total cost of ownership and improving parts availability at dealer premises. All these have led to even further improved uptime and resale value for our customers, among other achievements. With improved cost of ownership and uptime, we are ultimately driving customer satisfaction,” says Van den Heede.
Rory Schulz, Sales Director at UD Trucks Southern Africa, says, as fleet operators continue to grapple with the
As fleet operators continue to grapple with the effects of high fuel prices and generally tough operating conditions, the importance of considering TCO in all their decisions cannot be emphasised enough
In its approach to tackling TCO, UD Trucks Southern Africa has divided total operating costs of a vehicle into two segments – fixed and variable costs
Fixed vehicle expenses, explains Schulz, are the costs that come with owning a truck, whether it is on the road or not
Variable costs in trucking fluctuate with the operation of trucks. In other words, the more kilometres one drives, the more variable costs are incurred
effects of high fuel prices and generally tough operating conditions, the importance of considering TCO in all their decisions cannot be emphasised enough. With that in mind, UD Trucks Southern Africa has in the past few years paid particular attention to TCO to help maximise customer profitability. This, he says, forms part of the company’s drive
44%
UD Trucks Southern Africa has seen massive growth of its service and maintenance contract portfolio in recent years, with the penetration rate for new vehicles increasing from 23% in 2020 to 44% in 2023
“In pursuit of our goal to ‘deliver transport and service solutions that the world needs today’, we have accomplished various objectives, including retail excellence, introducing innovative transport solutions, enhancing our aftersales offering to reduce TCO and improving parts availability at dealer premises.
to provide total transport solutions to its customers.
“Traditionally, we have always had a huge focus on lifecycle costs. However, in recent years we have expanded the scope to total lifecycle costs, factoring not only the purchase price of a vehicle but also the cost of operating it and the resale value, amongst other considerations,” says Schulz. “In our view, the TCO of a vehicle plays a critical part in the life of any logistics operation, especially in the South African context, where the cost to perform logistics largely influences the profit and loss dynamics of a business.”
In its approach to tackling TCO, UD Trucks Southern Africa has divided total operating costs of a vehicle into two segments – fixed and variable costs.
Fixed vehicle expenses, explains Schulz, are the costs that come with owning a truck, whether it is on the road
67%
Fuel is the main cost driver for truck owners. In a recent TCO analysis, UD Trucks Southern Africa found that fuel now constitutes 67% of the total operating costs of a vehicle
“Traditionally, we have always had a huge focus on lifecycle costs. However, in recent years we have expanded the scope to total lifecycle costs, factoring not only the purchase price of a vehicle but also the cost of operating it and the resale value, amongst other considerations.
or not. Fixed costs largely remain the same from month to month, no matter how much the vehicle is used. Fixed costs include the purchase price of the vehicle, the cost of capital, repayment costs, balloon or residual costs, vehicle depreciation, insurance, vehicle licence and registration, fleet management fees, driver and crew costs, as well as carbon tax, amongst others.
To help its customers lower their fixed costs, UD Trucks offers various solutions and mitigations. Firstly, through UD Trucks Finance solutions, the company offers customised and flexible financing solutions that speak directly to each customer’s needs, based on UD Trucks’ better understanding of the trucking business than that of traditional financiers. Whether the customer is looking at tax-efficient financing, tax liability reduction or cash flow improvement, UD Trucks Finance has the right on-balance or off-balance sheet finance solutions available. Instalment
options can be customised to suit unique business needs.
“To help customers reduce their fixed costs, a dependable and costeffective product is a must. UD Trucks is known for its ‘value for money trucks’ designed to get the job done, without any unnecessary extra ‘bells and whistles’. Several generations of UD trucks have provided trusted durability and reliability to several generations of regional and global customers,” says Schulz.
In addition, UD Trucks Southern Africa places high value on driver training, all the way from the headquarters through to its dealers. Why driver training? A trained driver, says Schulz, generally drives more efficiently. In an environment where fuel costs continue to soar, effective driver training can help improve fuel consumption, allowing fleet owners to get more fuel for their hard-earned money. With better driving, there is also less strain on vehicles and therefore, less maintenance required.
A wide dealer network is also key to ensuring maximum vehicle uptime for customers. This is complemented by service and maintenance contracts (UD Trust Service Agreements) to ensure customer vehicles have Original Equipment Manufacturer (OEM) support throughout their service life. Routine maintenance resolves potential hazards before they unfold further and become costly breakdowns. Regular OEM servicing ensures consistent performance across the truck fleet so that production stays on track and meets the fleet owner’s objectives.
Through UD Connected Services, drivers and fleet managers can look forward to greater fuel efficiency, more time savings and better drivability. As the successor to UD Trucks’ acclaimed UD Telematics Services, UD Connected Services places the power of smart logistics in the fleet manager’s hands – giving them powerful tools to monitor fuel efficiency, route planning and improve delivery turnaround times with an eagle-eye view on driving performance, trip details and individual vehicle health.
UD Trucks Southern Africa also offers Euro 5 technology as standard ahead of regulations, which enhances efficiency and optimises TCO, all while lowering the vehicle’s environmental impact. Euro 5 reduces NOx emissions by about 43% compared to Euro 4, thus reducing the carbon footprint of the vehicle through cleaner emissions. This helps fleet owners lower their carbon tax liability.
Variable costs in trucking fluctuate with the operation of trucks. In other words, the more kilometres one drives, the more variable costs are incurred. Variable factors in trucking are wide-ranging and include
fuel, tyres, Ad Blue, lubricants, service and maintenance, repairs, daily checks, toll fees, fines, downtime costs and resale value, amongst others.
According to Schulz, fuel is the main cost driver for truck owners. In a recent TCO analysis, the company found that fuel now constitutes 67% of the total operating costs of a vehicle. “Some ten years ago, fuel was about 35% of the total cost of running a truck. Due to soaring diesel prices, it has increased to 67% of the costs to operate a vehicle,” he says.
With Euro 5 technology, which provides high power and torque through optimised combustion without increasing the size of the engine, customers will reduce their fuel bill significantly. In addition, Euro 5’s lower maintenance requirements reduce operational costs. Given that Ad Blue may not be readily available at fuel stations, UD Trucks Southern Africa’s dealer network now stocks Ad Blue to ensure adequate supply for customers operating Euro 5 trucks across the region.
“With Fuel Coaching, we have the answer to fuel costs. Our trucks are equipped with a built-in fuel coach, an onboard solution clearly displayed to give instructions to the driver in real time,” explains Schulz. “Fuel coaching encourages an optimal driving style at all times. It gives feedback and simple suggestions on how to improve safety and fuel efficiency, immediately and over the long term.”
This is complemented by UD Connected Services, which is designed to encourage better driving behaviour and protection of fuel assets. Fuel utilisation reports demonstrate how the truck and driver are performing, while fuel advisory services help to improve driving behaviour.
With UD Trust Service Agreements, customers can ensure that their vehicles always operate at optimal performance, thus ensuring fuel savings, product quality assurance and peace of mind. With local fleet owners realising the value, UD Trucks Southern Africa has seen massive growth of its service and maintenance contract portfolio in recent years, with the penetration rate for new vehicles increasing from 23% in 2020 to 44% in 2023.
In conclusion, Schulz says other solutions to variable costs include a wide dealer footprint, driver training, a 24/7 Uptime Support, call centre to ensure vehicle uptime and a used truck centre to support customer trade-ins. a
With sourcing of sand from natural sources such as rivers and coastlines outlawed in many African countries, manufactured sand is proving to be the most economical and ecological alternative. Renowned for its efficient rock-on-rock crushing principle, the vertical shaft impactor (VSI) crusher can play a critical role in the production of high-quality manufactured sand with a consistent shape and gradation. By
Sand has traditionally been obtained from natural sources such as rivers and coastlines. However, new regulations have been enacted to protect these sources in many countries across Africa and the world at large. Given these realities, the construction industry has been forced to adopt a suitable and sustainable alternative fine aggregate, better known as manufactured sand.
Considering the depletion of natural sand reserves and the stringent regulations on sand mining, demand for manufactured sand is projected to witness significant growth in the next few years. Factors such as urbanisation and the ultimate growth of construction activities will further drive demand.
Despite the scourge of illegal mining in many parts of the continent, the migration to manufactured sand has taken root in many countries. To provide context,
Munesu Shoko.
several quarries in South Africa already report that a large share of their sales is attributed to sand. Given this rising demand, it is important that quarries and sand producers deploy the right equipment to produce highquality manufactured sand.
Wayne Warren, Africa sales manager at Pilot Crushtec International, says manufactured sand has become a hot topic in several African countries with quarries striving to fill the gap created by the loss of natural sand reserves. In many instances, he says, the VSI has become the go-to crusher due to its ability to produce highquality, cubical and well-graded sand, an application where traditional solutions such as cone crushers have proven uneconomical to use.
Before VSIs became as common as they are now, says Warren, cone crushers were preferred, but they are an
45-315 kW
Pilot Crushtec’s VSI models cover a broad range of kW units in three shells, from 45 kW to 315 kW
Despite the scourge of illegal mining in many parts of the continent, the migration to manufactured sand has taken root in many countries
Given this rising demand, it is important that quarries and sand producers deploy the right equipment to produce high-quality manufactured sand
The VSI has become the go-to crusher due to its ability to produce high-quality, cubical and well-graded sand
In March this year, Pilot Crushtec will be introducing the Metso HRC8 high pressure grinding roll for manufactured sand and aggregate production
uneconomical way of producing sand. The downside is that for cone crushers to produce sand, one needs to crush with a very tight closed side setting (CSS), which by its nature is not economical because of the extremely high wear it causes.
“When using a cone crusher to manufacture sand, the crusher needs to be closed down to a very tight CSS, resulting in liner-on-material crushing. This is not ideal because the wear rate increases dramatically, and the shape is generally poor. The crusher works effectively in liner-onmaterial, on-material, on-liner crushing,” explains Warren.
The VSI’s rock-on-rock crushing principle is more efficient in producing high-quality manufactured sand as it directly crushes the rocks without any intermediate crushing stages.
“The VSI makes use of material-on-material crushing
50%
With the TwisterTrac VS350E, customers can expect to reduce their cost per tonne by up to 50%
“The VSI makes use of material-onmaterial crushing – the stone is accelerated at high speed into a rock box of the same hardness material, resulting in maximum breakage of the feed material. Depending on the speed, this can accomplish two things: stone shaping with some sand generation or, on a higher speed, a higher percentage of sand.
Wayne Warren, Africa sales manager at Pilot Crushtec International– the stone is accelerated at high speed into a rock box of the same hardness material, resulting in maximum breakage of the feed material,” explains Warren.
“Depending on the speed, this can accomplish two things: stone shaping with some sand generation or, on a higher speed, a higher percentage of sand.”
Charl Marais, sales manager at Pilot Crushtec, says another major advantage of using a VSI over a cone crusher is the ability to achieve constant product grading.
“If you feed a VSI constantly, it yields a constant grading. On the contrary, with a cone crusher there is inconsistency in quality because of the way the liners wear. As soon as you have an uneven wear pattern on your mantle and bowl liners caused by intermittent feed conditions, your grading fails as well. It is also difficult to rectify intermittent feed conditions and to supply a cone crusher
with a constant feed to keep the cavity full; surge bins are installed which drives up capital expenditure,” says Marais.
Warren agrees, saying that with a cone or a horizontal shaft impact (HIS) crusher, there is constant variability, completely the opposite of the VSI, which does not have any variability because of the fact that there is no CSS to wear out and change the grading. Even though a VSI makes use of a rotor, which is a wearing component, the gradation of the sand does not change.
This, adds Marais, makes the VSI the crusher of choice for processing the material used in building bridges and dam walls, where constant grading is a principal parameter.
With a rich heritage in the design and manufacture of VSIs, which dates back to over 30 years ago, Pilot Crushtec has established itself as a major player in the international VSI market, with key successes recorded in markets such as New Zealand, Australia and selected European countries. More recently, the company has also introduced its VSI offering in the United States. “As the success story grows, so does the demand in outlying areas. The majority of our mobile trackmounted VSI crushers are therefore being exported,” says Warren.
Pilot Crushtec’s VSI models cover a broad range of kilowatt (kW) units in three shells, from 45 kW to 315 kW. The three base models comprise the VS100, VS200 and VS350 (up to 350 tph), covering five different rotor diameters and 14 different configurations to suit varying customer needs.
The rotor sizes are 600 mm, 700 mm, 800 mm, 900 mm and 1 000 mm, as well as the open top rotor option. On the small kW units, the 600 mm rotor is ideal, and as the feed size increases, the bigger rotor sizes are the standard. The open top rotor is generally used with anvil rings, where the feed size is slightly larger.
In addition to the three base models, Pilot Crushtec offers the mobile TwisterTrac VS350E, a diesel-electric version of the hydraulic mobile TwisterTrac VS350. Being a bi-powered machine, the VS350E provides increased operational efficiency, while reducing the
carbon footprint. With this model, customers can expect to reduce their cost per tonne by up to 50%, while increasing throughput by 15-20% compared to the hydraulic version.
While the VSI has proved itself as the ultimate sand maker, it is not without its limitations. According to Warren, one of the downsides is that a VSI by its nature is a power-hungry machine. “The VSI gives you highquality manufactured sand with a consistent shape and gradation, but it uses a fair amount of energy and has high wear, especially when the feed has a high silica content, which is often the preferred material in sand making,” says Warren.
In addition, with the machine highly dependent on constant feed material, there is a high possibility of excess fines. This, says Warren, can be difficult to overcome when generating sand. In a standard crushing plant, fines generation is often higher than recommended, calling for blending of material to meet requirements for concrete production, for example. To mitigate excess fines in sand, washing has become a go-to solution for ultra fines removal. Given the water shortages in southern Africa and several other regions on the continent, washing is often out of the question.
Considering these challenges, Pilot Crushtec believes it has a perfect solution to complement the VSI crusher where fines generation cannot be controlled. In March this year, the company will be introducing the Metso HRC8 high pressure grinding roll (HPGR) for manufactured sand and aggregate production. Metso has traditionally used this technology in mining applications, but has recently adapted it to suit the aggregate market.
“The HPGR’s adjustable pressure allows you to vary the curve grading for finer or more coarse grading. Based on available data from other regions, the machine consumes about 50% less power in sand production compared to other technologies for the same volume of net product. We have been watching the results from many installations across the globe and based on that, we have decided to add this technology to our regional offering,” concludes Warren. a
As South African quarries and surface mines at large prioritise the implementation of proximity detection systems (PDS) in line with the regulator’s directive, Anton Lourens, CEO of Booyco Electronics, stresses the importance of managing the human side of change to ensure successful adoption of the technology. By Munesu Shoko.
Following the gazetting of the Collision Avoidance Systems (CAS) regulations by the Department of Mineral Resources and Energy (DMRE), PDS and CAS technology implementation have both become a key focus for organisations seeking to comply with the regulations.
However, Lourens cautions that embarking on a PDS/CAS journey involves much more than just deploying the technology; it calls for careful attention to the management of what
he refers to as ‘the people aspect’ of change to ensure successful adoption and utilisation of the technology.
“In our opinion, the people aspect is the most important part of the PDS implementation journey, or any new technology in general,” says Lourens. “Employees’ willingness to adopt the new tools in day-to-day operations is central to the success of the technology. It is important for people who use the technology to understand its purpose, benefits, capabilities and expected outcomes, which increases
Booyco Electronics offers refresher training after every three or six months depending on the identified needs of the specific mine
The people aspect in PDS implementation should take a holistic approach that places value on both the technology and people
“In our opinion, the people aspect is the most important part of the PDS implementation journey, or any new technology in general. Employees’ willingness to adopt the new tools in day-to-day operations is central to the success of the technology.
their cooperation in adopting the new technology.”
The people aspect in PDS implementation, explains Lourens, should take a holistic approach that places value on both the technology and people. It is, however, important to involve more than just the daily users of the technology. The approach is to include all stakeholders, from those at the ‘coal face’, all the way up to top management and executives, in order to ensure that the whole organisation understands why the mine or quarry is adopting the technology, the reason why they chose the specific technology and its impact on operations.
Anton Lourens, CEO of Booyco ElectronicsPDS and CAS technology implementation have both become a key focus for organisations seeking to comply with the regulations
Embarking on a PDS/CAS journey involves much more than just deploying the technology; it calls for careful attention to the management of the people aspect of change
It is important for people who use the technology to understand its purpose, benefits, capabilities and expected outcomes, which increases their cooperation in adopting the new technology
While the primary objective is to ensure safety of people, PDS installations also have a direct bearing on other critical parameters such as equipment availability and ultimately productivity on site
Implementing PDS technology has a direct impact on people’s behaviour, and that is its purpose in the first place, stresses Lourens. While the primary objective is to ensure safety of people, PDS installations also have a direct bearing on other critical parameters such as equipment availability and ultimately productivity on site. It is therefore important to place value on people’s adoption of the technology to ensure that the intended benefits and objectives of implementing the technology are realised.
“Ultimately, the main objective is to make the workplace safer and ensure the safety of people. This should be communicated effectively for employees to understand why their adoption is critical to the success of the technology. Effective communication of the intent of the PDS deployment minimises potential resistance and ensures a smoother transition,” he says.
Based on years of experience, Booyco Electronics has noted that where there is no proper change management around the people element, there is limited buy-in from employees, which effectively results in safety and productivity setbacks despite the rollout of the PDS technology. Involving employees in the change management process empowers them to become active participants, which increases their understanding, motivation and sense of ownership, leading to increased equipment availability and better safety outcomes, which has an upside in production.
Commenting on Booyco Electronics’ change management process, Lourens says the first process is to conduct a technical readiness assessment to understand how the technology will impact a specific quarry or mine, especially given that each and every mine has its own unique operating conditions.
“We engage with the engineering and mining
stakeholders first to explain the capabilities of the technology – what it can and what it cannot do, and how it addresses the mine’s risk assessment” explains Lourens. “Managing expectations is an important part of change management which ensures that everyone is on the same page, from an engineering, safety and management perspective. Once the parameters have been defined, we start with training, explaining to employees why the mine has invested in the technology and how it works.”
An important part of the change management process, he says, is the understanding of the consequences of not working within the confines of the system. “It is more of an education process than training. Once they understand the what, how and why, a solid foundation for success has been laid. We also offer refresher training after every three or six months depending on the identified needs of the specific mine,” he says.
Another important part of the change management process is optimisation of the PDS technology, which is based on the feedback from the users.
Optimisation and continuous improvement help support the ongoing success of the technology, thus maximising safety, reducing costs and boosting productivity.
In conclusion, Lourens advises that it is also important to manage the unintended consequences of PDS implementation. “Over the years, we have observed that in time people become oblivious to the technology. In the case of collision avoidance systems, for example, people get used to the fact that if they do not stop the machine, the machine will stop on its own. In some cases, some operators adopt this behaviour while driving on public roads, which can result in serious accidents. This can undermine the safety benefit that the technology offers. It is therefore important to try to foresee these unintended consequences and manage them better. Continuous training is a contributor to this complex situation.” a
Following the December 2022 gazetting of the Collision Avoidance Systems (CAS) regulations by South Africa’s Department of Mineral Resources and Energy (DMRE), Schauenburg Systems reports a spike in demand for CAS technology. In line with its ‘innovation that saves’ mantra, the company has over the years evolved its offering to meet the industry’s quest for safety without compromising productivity. By Munesu Shoko.
In December 2014, the DMRE promulgated the mandatory use of collision prevention systems (CPS), collision avoidance systems (CAS) and motion inhibitors. After years of uncertainty, the regulator brought into law the Chapter 8 clauses of the Mine Health and Safety Act regulations relating to Level 9 vehicle intervention for collision avoidance in trackless mobile machinery (TMM), both on surface and in underground operations.
Consequently, says Martin Marais, Sales and Business Development director at Schauenburg Systems, there has been a massive increase in
the demand for CPS, mainly driven by the mining sector’s need to comply with the legislation. In fact, some of the bigger mining groups started investing in these systems as far back as 2017, well ahead of the gazetting of the legislation.
However, says Marais, there has been a phenomenal spike in demand for CPS in the past two years, with more mines investing in the technology ahead of the anticipated gazetting of the law, which was initially anticipated for December 2025, before the Minister of Mineral Resources and Energy signed an order for subregulations 8.10.1.2 (b) and 8.10.2.1 (b) in Chapter 8
2017
Some of the bigger mining groups started investing in CPS as far back as 2017, well ahead of the gazetting of the legislation
2008
Schauenburg Systems started working on its first generation of collision detection systems as early as 2002 and successfully completed its first commercial installation in 2008
“Over time, market needs have evolved from collision detection to collision prevention, data logging and mapping out of safe zones to avoid impact on production. It is about ensuring the safety of people on site, but without compromising on productivity.
There has been a phenomenal spike in demand for CPS in the past two years, with more mines investing in the technology ahead of the anticipated gazetting of the law
One of the critical foundations to the successful implementation of the technology is to ensure that risk evaluation and the ultimate traffic management plans are done properly
Schauenburg Systems offers two SCAS Surface solutions, the portable Light Vehicle Basic (LVB+) system and the Heavy Vehicle Basic (HVB+) system
Schauenburg has developed SmartMine IoT to provide customers with powerful business intelligence and data modelling tools for insights into valuable operational data
Martin Marais, sales and business development director at Schauenburg Systems
of the Mine Health and Safety Act, 1996, to come into force on December 21, 2022.
Gawie Croeser, head of the Strategic Business Unit at Schauenburg Systems, says one of the critical foundations to the successful implementation of the technology is to ensure that risk evaluation and the ultimate traffic management plans are done properly. This informs the level of risk on site and the unique needs of a mine from a technology-adoption point of view.
To close the knowledge gap, it is therefore important for mines to consider dealing with reputable and experienced CPS providers who not only have the right technology, but also understand all the critical
parameters that are key to the successful rollout of the technology. Having started working on its first generation of collision detection systems as early as 2002 and successfully completed its first commercial installation in 2008, well ahead of the legislation, Schauenburg Systems has ‘paid its school fees’ when it comes to the development of this technology, stresses Marais.
On the back of growing demand for CPS, Schauenburg has expanded its workforce to more than 1 000, and 70% of that number are service-related personnel
Based on the everchanging market requirements, the company has consistently evolved its offering. “Some 16 years later after the launch of our first system, a lot has changed,” says Marais. “Over time, market needs have evolved from collision detection to CPS, data logging and mapping out of safe zones to avoid impact on production. It is about ensuring the safety of people on site, but without compromising on productivity.”
With the move from collision detection to collision prevention systems, one of the realities is that there are now more stakeholders involved in the process. Apart from the CPS technology supplier, other custodians of the installation are the vehicle OEM and third-party ISO 21815 CAN-BUS interface suppliers.
Leveraging lessons learnt over time, Schauenburg Systems developed its second-generation underground collision prevention systems (SCAS II), which uses advanced detection technologies and algorithms designed to save lives and reduce costs.
The company also offers two SCAS Surface solutions, the portable Light Vehicle Basic (LVB+) system and the Heavy Vehicle Basic (HVB+) system. The LVB+ system is intended for daily visitors to ensure compliance prior to entering an operational site, whereas the HVB+ system caters for bigger vehicles and fixed installations. The HVB+ complies with the ISO21815 standard and is classified as a full Level 9 system.
Both surface systems offer dynamic zone configurations and three programmable detection zone sizes –warning, danger and critical zone. These zones can be adjusted to best fit individual customer needs and traffic management plans. Furthermore, Schauenburg’s dynamic detection zone algorithm complements the production targets of clients as Potential Unwanted Event (PUE) detection which is a function of vehicle speed and eliminates the occurrence of false warnings and Level 9 TMM intervention.
These systems have been proven in open pit mines and quarries for their ability to display the detected remote objects in eight quadrants around the vehicle, thus greatly increasing operator situational awareness.
Even though the company offers a base line solution, Croeser says Schauenburg appreciates the unique requirements of every operation, and therefore adapts its solution – within its capability – to accommodate each mine’s or quarry’s requirements.
The needs of a big open pit mine are completely different from those of a small quarry. In large opencast
mines, assets ought to be confined within the operation, whereas in the quarries, assets are decentralised. In addition, because of the low-margin nature of the business and the price-sensitive approach to buying decisions, quarries generally require low-cost, low maintenance products that speak directly to their unique needs.
“Based on the tripartite meetings between government, the mining sector and labour organisations which we have been attending, the regulator notes that there are about 5 000 quarries in South Africa. In terms of numbers, this is much more than the 400 underground mines in the country. Quarrying is therefore an extremely big market in South Africa, but it is much decentralised, with low quantities of machines per site compared to mainstream mines,” says Marais.
Given these special needs of the market, Schauenburg works closely with stakeholders to provide fitting solutions for the quarrying sector. For example, the company attends tripartite meetings as previously mentioned, between government, the mining sector and labour organisations. In addition,
Schauenburg is a proud associate member of ASPASA and attends the surface mining association’s information-sharing events. For the past three years, Schauenburg has been attending the Institute of Quarrying Southern Africa’s annual events.
One of the key trends that stands out for Marais is that quarries want integrated solutions which not only offer collision avoidance capabilities, but also include, for example, monitoring of traffic movement and production on site. Therefore, systems need to be integrated with a GPS type of technology to make data available in real time.
“In line with these needs, we have something exciting coming at the end of 2024. This will allow us to offer integrated solutions to the industry and will reinforce our position as frontrunners in the development of CPS technology, not only in South Africa, but globally,” says Marais.
Whether in an underground or opencast mining environment, the importance of aftersales support in this industry cannot be stated
enough, stresses Marais. Once a mine has gone the Level 9 route, the supplier must have enough support available. On the back of growing demand for CPS, Schauenburg has expanded its workforce to more than 1 000, and 70% of that number are servicerelated personnel.
This is complemented by a network of branches located in all the major mining regions, including Rustenburg, Thabazimbi, Welkom, Fochville, Steelpoort, Secunda and Emalahleni. The company also has advanced plans to open a new branch in the Northern Cape province.
“We are very proud of our extensive support footprint. Over the years we have also continued to invest in people through a fully integrated digital training platform called e-Learning, which is available for both our employees and customers,” says Marais.
In addition, Schauenburg has introduced a digital maintenance tool, Digisol, aimed at capturing all the parts and maintenance performed. In future, the company will invest in analytics to predict issues such as failure rate and risk rate.
In conclusion, Marais says the purpose of this technology is to save lives and improve productivity. In future, communication and optimisation of data from CPS devices will be critical. With that in mind, Schauenburg has developed SmartMine IoT to provide customers with powerful business intelligence and data modelling tools for insights into valuable operational data.
“SmartMine IoT allows us to process data at the source through an edge-computing platform and provides information in real-time. This will allow customers to make split-second decisions to save lives and increase productivity. SmartMine IoT’s design allows us to integrate with any equipment manufacturer’s hardware and accumulate data into a centralised data lake for processing,” concludes Marais. a
Schauenburg’s dynamic detection zone algorithm complements the production targets of clients as Potential Unwanted Event detection, which is a function of vehicle speed, eliminates the occurrence of false warnings and Level 9 TMM intervention.Hauling run of mine material represents a significant component of the total operating costs of a quarry or surface mine. Consequently, the incentive to increase efficiency and reduce costs in this area is very high. How can quarry operators increase hauling efficiency with articulated haulers? By Munesu Shoko.
That off-highway and articulated trucks are the most popular hauling systems in quarry operations is no overstatement.
Gary Martin, senior market professional, Heavy Construction & Quarrying Industries, Caterpillar, says the application and the ground conditions determine which system should be used. Articulated trucks, says Martin, are ideally suited for overburden tasks and are popular in sand and gravel operations.
“Overburden is often wet, loamy material with poor underfoot conditions. With permanent 6x6, Cat articulated dump trucks (ADTs) excel in these
conditions. With a nimble turning circle and superior climbing ability, the Cat articulated trucks are a great choice in such an application,” says Martin.
According to Jeremiah Mokhomo, ADT product manager at Bell Equipment, ADTs excel on rough, uneven terrain found in quarries because of their high ground clearance, excellent manoeuvrability thanks to the articulated frame, and their powerful engines. They can handle steep inclines, tight turns and loose surfaces better than many other trucks.
“ADTs are built to withstand harsh quarrying environments with features such as robust frames, heavy-duty axles and strong suspension systems.
25%
Hauling accounts for approximately 25% of total operating costs of a quarry
“When deciding on the best fleet mix, consider payload capacity, ground clearance, manoeuvrability and engine power. Match the number of ADTs to production goals, ensuring there are enough trucks to keep loaders and crushers running at full capacity without bottlenecks.
It is important to determine the appropriate ADT size and type by considering the typical haul routes, terrain characteristics and materials to be handled
The maintenance of haul roads is a key factor in reducing hauling costs and increasing efficiency
Match the number of ADTs to production goals, ensuring there are enough trucks to keep loaders and crushers running at full capacity without bottlenecks
If the hauling fleet is too large, there is a big risk of excessive idling as trucks line up to dump their load at the crusher if the hauling frequency is too high and does not match the crusher’s capacity
3
Ideally, haul roads should be at least three times the width of the largest hauling unit on site
“Depending on application, the height and width of the hauling unit may be a key consideration. For example, if there is side spillage at the crusher, the area needs to be cleaned frequently, adding extra equipment and manpower and increasing the time spent at the crusher.
During the rainy season, when the roads become sticky, rigid trucks may struggle, while ADTs continue to work,” says Mokhomo.
This, he adds, translates into a dependable operation with minimal downtime. In addition, ADTs can handle a wide range of materials, from crushed rock and gravel to sand and clay, due to their strong dump beds and ability to adjust bed angles for proper unloading.
Commenting on the importance of maximising hauling efficiency on quarry sites, Mokhomo says hauling accounts for approximately 25% of total operating costs. It is therefore important to find ways to optimise hauling efficiency in order for quarries to maximise profitability.
Mokhomo says efficient trucks consume less fuel, while optimised routes and improved loading/unloading practices reduce wear and tear, leading to overall cost savings and reduced environmental impact. Lower fuel consumption
due to efficient hauling translates into lower emissions and ultimately a reduced ecological footprint, which is becoming increasingly important in the industry.
There are several factors to consider in the quest to increase hauling efficiency. “Firstly, it is important to determine the appropriate ADT size and type by considering the typical haul routes, terrain characteristics and materials to be handled,” stresses Mokhomo. “When deciding on the best fleet mix, consider payload capacity, ground clearance, manoeuvrability and engine power. Match the number of ADTs to production goals, ensuring there are enough trucks to keep loaders and crushers running at full capacity without bottlenecks.”
efficient hauling in quarry operations, stresses Martin. The maintenance of haul roads is a key factor in reducing hauling costs and increasing efficiency. Ideally, haul roads should be at least three times the width of the largest hauling unit on site.
“Haul roads should be built with adequate drainage to allow for water to flow freely across the surface to avoid flooding and ensure super elevated corners to allow the truck to maintain its speed along its haul,” says Martin. “Continuous or gradual changes in grades allow trucks to upshift smoothly without operator input. Haul road maintenance is critical to manage and reduce rolling resistance. Less rolling resistance translates into higher speeds, increased productivity, less effort, less fuel and longer tyre life.”
The same view is shared by Martin, who says that not sizing the right truck to the required production level can be costly. If the hauling fleet is too large, there is a big risk of excessive idling as trucks line up to dump at the crusher if the hauling frequency is too high and does not match the crusher’s capacity.
“Depending on application, the height and width of the hauling unit may be a key consideration. For example, if there is side spillage at the crusher, the area needs to be cleaned frequently, adding extra equipment and manpower and increasing the time spent at the crusher,” says Martin.
Haul road design and maintenance are critical to enable
To help quarrying customers maximise hauling efficiency, the Bell ADT range is powered by Mercedes-Benz engines that have been optimised to deliver high power and low fuel consumption, while operating at optimal runs per minute (RPM) for maximum efficiency.
FuelSense 2.0’s intelligent shifting technology reduces fuel consumption by 6% compared to previous versions, while maximising performance. The weight-saving design of Bell ADTs means no fuel is wasted on unnecessary metals. The machines are designed to operate efficiently while maximising payload capacity.
“Automated performance features such as i-Tip and speed control shorten cycle times, allowing operators
to focus on productivity rather than manual tasks, while on-board weighing ensures consistent precision on target loads,” says Mokhomo.
Bell offers Comfort Ride Suspension, an adaptive suspension system that provides better stability and comfort when driving over rough terrain. Improved comfort leads to higher ground speed and improved productivity.
Bell ADTs are now equipped with a range of safety features, including cameras, and the ability to integrate with proximity detection systems (PDS) and collision avoidance systems (CAS), which help to improve visibility and prevent accidents. Bell ADTs also come with onboard weighing and angle sensors which help in refining the downhill descent system, Hill Assist as well as Safe Tipping.
Fleetm@tic® technology allows fleet owners to track truck location, speed, fuel consumption and maintenance schedules in real time to improve utilisation, identify inefficiencies and schedule preventive maintenance.
“Real-time tracking and monitoring, as well as fleet management software, help our customers optimise truck movements and reduce waste. Bell trucks come standard with Fleetm@tic® for the first two years, allowing customers to measure machine productivity, utilisation and even plan preventative maintenance,” says Mokhomo.
Bell also offers an option of 4x4 ADTs for quarrying; these trucks have less tyre scuffing, which can translate into huge savings for the operation and less environmental impact. The 4x4 has a smaller turning circle, making it manoeuvrable when working in tight spaces.
Bell recognises a shift towards environmentally friendly machines and is investigating various options for driving low- to zero-carbon operations across our product line. “We recognise the gravity of the situation and are committed to exploring all options to pave the way for a more sustainable future. Our unwavering goal is to exceed our customers’ expectations by creating environmentally responsible ADT solutions with long-term environmental benefits,” says Mokhomo.
Cat ADTs are equipped with automatic features, such as auto traction control, hoist and retarder, amongst others. These features assist novice operators to be more efficient. Auto wait brake reduces operator input while waiting for the truck to be loaded. Stability Assist alerts the operator when approaching unsafe working conditions. As an example, unless road conditions dictate a lower gear, the Cat 745 starts in fourth gear to eliminate unnecessary shifting.
“In the case of a haul road that is not well maintained, a Cat ADT with its automatic features and two-piece hitch ensures permanent six-wheel ground contact to navigate challenging terrain. When handling abrasive and hard rock, brunel 450 steel liners can be added to extend the life of the ADT body. A tailgate can also be added to the articulated truck’s body to aid material retention when working on steep inclines or when carrying soft, loose or wet material,” concludes Martin. a
Bell ADTs can be fitted with the latest and most advanced PDS/CAS* technology on the market to comply with mining regulations and ensure the safety of operators, pedestrians, and other mobile equipment on the job site.
At the same time, owners have the flexibility to choose a PDS/CAS* solution that best suits their needs and budget, and the option of fitting this solution to a new PDS/CAS*ready Bell ADT, or an older Bell ADT retrofitted with a PDS kit
Contact your nearest Bell dealer today to enquire about upgrading your Bell ADT.
With the support of Volvo Construction Equipment (Volo CE) and its dealer partners, women across Africa are pursuing careers in the traditionally male-dominated field of mechanics, enhancing their opportunities in life, and delivering outstanding aftermarket service for customers.
olvo CE is on a mission to “build the world we want to live in”. This vision encompasses not only a commitment to sustainability and connectivity but also an unwavering dedication to achieving gender equality within the company.
A few years ago, Volvo CE set an ambitious target to have at least 35% female leaders and employees by 2024. To this end, the company has implemented significant initiatives to encourage
women, especially young women, to consider careers in the construction equipment industry. Since then, Volvo CE has witnessed remarkable progress, not only within its own ranks but also among its network of dealer partners.
The Ghabbour Foundation for Development, established by GB Auto, the parent company of Volvo CE’s Egyptian dealer Ghabbour, for example, is working tirelessly to bridge the gender gap in vocational education. Out of 1 000 students currently enrolled across three vocational schools set up by the foundation in Egypt, 150 are now female.
35%
A few years ago, Volvo CE set an ambitious target to have at least 35% female leaders and employees by 2024
150
Out of 1 000 students currently enrolled across three vocational schools set up by the Ghabbour Foundation for Development in Egypt, 150 are now female
“The foundation acts as a gateway for companies to recruit highly qualified technicians who match their needs and for students to find well-paid jobs that align with their qualifications. We are particularly dedicated to promoting women’s roles in a traditionally maledominated sector and encouraging women to join the commercial vehicle specialisation programme,” says Aleya Serageldin, executive director for the Ghabbour Foundation for Development.
Dina, a third-year student at one of the Ghabbour vocational schools, specialising in commercial vehicle maintenance, says: “As I entered this specialisation, I developed a genuine passion for it and am determined to excel. My trainers have been incredibly supportive from the beginning, urging me to strive for excellence. After completing my education, I dream of working and honing my skills, and I envision enrolling in a university in the same field for higher education. Ultimately, I aspire to establish the service centre I have always dreamed of owning.”
Volvo CE has implemented significant initiatives to encourage women, especially young women, to consider careers in the construction equipment industry
Volvo CE has witnessed remarkable progress, not only within its own ranks but also among its network of dealer partners
The Ghabbour Foundation for Development, established by GB Auto, the parent company of Volvo CE’s Egyptian dealer Ghabbour, is working tirelessly to bridge the gender gap in vocational education
Babcock, Volvo CE’s dealer partner in southern Africa, meanwhile, has developed a strong team of female mechanics at its workshops
Babcock, Volvo CE’s dealer partner in southern Africa, meanwhile, has developed a strong team of female mechanics at its workshops. Thando, a 26-year-old woman working at Babcock, began her journey with an apprenticeship programme in 2019.
“My fascination with mechanics started at a young age when I helped fix my father’s taxis,” she says. “On my journey, I met an amazing neighbour who taught me that mechanics is about more than just cars. His help sparked a strong interest in me. I have had incredible mentors guiding me throughout my journey. On Saturdays, we have special training sessions where we simulate faults and solve problems. It is a great learning experience. Day-to-day, I handle various tasks such as stripping engines and overhauling transmissions and brakes. I am also the designated driver on site. I manage the loading and off-loading of machines from transport. I am licensed to operate everything from forklifts to rigid trucks. Right now, I am focused on advancing my career. I am studying instrumentation at the University of South Africa (Unisa). It helps me stay up-to-date with improvements in engine management, emissions, control, telematics, and other related topics. Believing in yourself opens endless possibilities. I tell everyone – go out and follow your dreams!”
Lonah has another inspiring story. She started working at a Babcock workshop in 2018. “After high school, a friend suggested I should try diesel mechanics. The more I researched, the more fascinated I became with machines. I decided to give it a shot and guess what? I found it to be perfect! I absolutely love being a diesel mechanic! Today, I am proud to say that there are six women working alongside me in this workshop. We support and encourage each other every day. It is amazing to see this progress. To all the girls out there
who dream of pursuing a career in mechanics, do not let anyone tell you that you cannot do it. Gender should never limit your potential. Embrace your passion, work hard and believe in yourself. You can achieve anything,” she says.
After working at Leal in Mauritius for 14 years, Wendy exemplifies the career growth and success that women can achieve. She started as a mechanic aged 17 and is now a customer support representative, responsible for travelling across the island to meet customers, assess their needs, and advise them outside of the workshop.
“My passion for mechanics came from growing up with two older brothers. I was always in the garage with my brothers, working with them on cars and trucks,” she says. “Mechanics is an interesting subject and becoming a technician seemed logical for me. I am a problem solver and working on a difficult case motivates me. To allow an excavator or truck to go back into the field or on the road and see the satisfaction of our clients is very rewarding for me. For my clients, I am always there to give them the best advice and share my knowledge in order for them to exploit the full potential of the machines.”
The significance of achieving a better gender balance in the construction equipment industry goes far beyond a social obligation; it is also a smart business move. The industry, faced with challenges such as a shortage of skilled labour, especially among service technicians, recognises that nurturing talent, regardless of gender, is essential.
As Christophe Lagandre, Head of Market Area Africa at Volvo CE aptly puts it: “Having a better gender balance is not just the right thing to do for society. It is also good for business and helps us deliver the best possible support for our customers.” a
eft unchecked, spillage and airborne dust can be extremely dangerous and expensive. Fugitive material in any form is a dirty and costly concern, whether to workers’ health or to conveyor components.
Martin’s transfer point products (such as belt support, sealing and tracking) control the load on the belt and diminish dust-related problems. When bulk material transfer systems are properly designed and maintained, operations run cleaner, safer and more efficiently.
Martin Engineering. Very good.
BEST PRACTICE: Bulk handling specialists who conduct a site-specific analysis before any training sessions.
As with all industrial equipment, one of the most important elements of safe, efficient conveyor operation is proper training. By
JeradHeitzler, training manager at Martin Engineering and Todd Swinderman, president emeritus at Martin Engineering.
Mining conveyors are typically massive, powerful systems that can move tonnes of material per hour, often configured in complex networks and over long distances, thereby minimising costs while performing work that would otherwise create both labour and logistical nightmares. But their size, speed and power also present the risk of a catastrophic injury that can occur in the blink of an eye.
Even the reaction time of a highly-trained professional athlete is no match for a bulk material
conveyor. Conveyors apply large amounts of mechanical energy to what is essentially a giant elastic band, stretched tight and threaded through a maze of components.
This stretched band is often loaded with tonnes of material, sometimes using drive motors as large as 600 hp (450 kW). A typical conveyor belt moves at a relatively constant speed, commonly running between 0,5 to 10 m per second. Given the weight, speed, inertia and kinetic energy, enormous forces are involved. The human body, able to generate less than 1 hp (0,75 kW), simply cannot compete.
300 000
A 2003 study by a major corporation found a correlation between fatalities and unsafe practices, indicating that for every fatality there are an estimated 300 000 unsafe behaviours
One of the challenges facing conveyor operations is the expertise and knowledge leaving many industries through retirements. A deep understanding of how conveyors function may not be handed down through basic onthe-job training passed from worker to worker. Although valuable, this type of training cannot be vetted to be sure that the underlying concerns are understood by a learner, nor does it allow for adjustments that may need to be considered with changes in production or auxiliary equipment.
In addition, information that is transferred to new employees may not reflect industry best practices. When mines take a “here is how we do it” approach, they are vulnerable to past workers’ teaching techniques that may not be the best long-term resolutions. This introduces risks to the mine in terms of safety hazards, inefficiency and premature equipment failure.
In many mines, there is a lack of qualified conveyor trainers. Most conveyor training comes from vendors of systems and components. Suppliers can train very well on how their products should be maintained and installed and what problems they can solve. But much of this type of training is done from the vendor’s or manufacturer’s own point of view. Rarely is training available that
Conveyors apply large amounts of mechanical energy to what is essentially a giant elastic band, stretched tight and threaded through a maze of components, sometimes using drive motors as large as 600 hp
As with all industrial equipment, one of the most important elements of safe, efficient conveyor operation is proper training
Training based on a combination of deep industry experience and modern engineering will greatly improve operating decisions, resulting in higher productivity, fewer safety incidents and reduced unplanned outages
Equipment vendors and third-party trainers can be a highly effective source of training, but there are hundreds of companies providing such services, and expertise and approaches vary widely
Insufficient safety training can be incredibly costly to a mine, with direct and indirect costs of every accident
addresses the mine personnel’s perspective. This can tarnish training effectiveness, reducing the learner’s interest if it does not speak directly to the worker’s recognised needs.
There are also generalisations that are accepted as truisms and seemingly require no proof due to their long-standing use in conveyor operations. But it is easy to perpetuate bad habits unless operations personnel have solid, real-world knowledge in bulk material handling and can make educated decisions when addressing problems. With the ‘old salts’ who developed and handed down these practices fast retiring, there is a need to provide knowledge to the younger operators and maintenance
workers to avoid the trial and error associated with applying many of the handed-down approaches.
While the loss of ‘tribal’ knowledge is an issue, it also creates an opportunity to significantly improve operations through third-party expert training. Factory-trained specialists who focus on overall conveyor performance and safety rather than just component function can deliver thorough, objective instruction that is untainted by a “we have always done it this way” approach.
Training based on a combination of deep industry experience and modern engineering will greatly improve operating decisions, resulting in higher productivity, fewer safety incidents and reduced unplanned outages.
Dealing with complex and changing regulations can present additional challenges. Some regulations may not fully protect a worker, depending on an individual mine’s circumstance, so local governments and corporations often add their own requirements in an effort to improve productivity and minimise injuries.
In addition, new conveyor systems are increasing in size, speed, complexity and sophistication, with automation playing an ever-increasing role. The move toward automation was originally targeted at reducing labour costs but is now focused more on productivity improvements. As systems start to “run themselves”, the reasons for unplanned shutdowns can be misunderstood and not addressed, and systems may be bypassed, resulting in going back to the same old procedures. Maintenance is becoming more driven by data knowledge and less by ‘wrench smarts’.
Updated design and control philosophies are becoming more critical for making informed operating and repair decisions, and conveyor operators and maintenance personnel are increasingly in need of a deeper understanding of the entire system. All these factors indicate a need for training that is specifically tailored to individual sites and operations. The one-size-fits-all
approach is becoming less attractive – and less effective –with each passing year.
Understanding how and why accidents happen is also critical in preventing them from occurring. Some might argue that workers’ unsafe acts are the primary cause of accidents. Yet many safety professionals have realised for some time that the root causes of accidents are not that straightforward.
Often, the employee’s action is not the only – or even the most significant – root cause. The real underlying causes are usually more involved and require a more complete accident analysis, followed by thoughtful corrective action. Addressing the symptoms with workable long-term root cause solutions will reduce unsafe practices, improving availability and safety, while enhancing profitability.
A 2003 study by a major corporation found a correlation between fatalities and unsafe practices, indicating that for every fatality there are an estimated 300 000 unsafe behaviours.
Most operations personnel are only expected to know the basics of how conveyors operate, but they may not be fully aware of their limits, safety protocols and best maintenance practices. However, optimising a conveyor system requires an advanced understanding of how fugitive material relates to safety and the newest technologies to control dust and spillage, as well as accommodating changing production demands and how to use existing designs to meet those demands. Some mines lack a deeper understanding of equipment limitations, which encourages workers to treat symptoms such as fugitive material by adjusting skirt seals, for example, when the real culprit may be insufficient belt support or wear liners.
Equipment vendors and third-party trainers can be a highly effective source of training, but there are hundreds of companies providing such services, and expertise and approaches vary widely. Most are not bulk
It is estimated that direct costs of an accident are 50 times greater than direct costs.
handling specialists, and even among those that focus on conveyors, their offerings are rarely mine-specific. That means the nuances of an individual facility and its equipment are addressed by a generic programme presented to all bulk handlers. Training is often piecemeal, with little follow-up to evaluate progress toward minespecific goals and spotty access to industry experts.
Some firms take training seriously yet fail to repeat and update training often enough. Any approach that allows maintenance personnel to drift back toward trial-anderror learning is certain to increase costs and reduce effectiveness. The results can include a lack of deep understanding of the mine’s conveying systems and how the various components should work together, as well as increased regulatory oversight, disengaged workers, reduced productivity, poor safety records and increased labour turnover.
In contrast, dedicated educators with a specific focus on (and a reputation for) expert conveyor training will guide personnel along a path of best practices and continuous learning. The most successful trainers develop a sitespecific curriculum that pertains directly to the individual facility, delivering information that not only educates, but also motivates learners to change behaviours.
Good teachers should provide a variety of delivery methods, based on different learning styles, that is, good graphics for visual learners, clear documentation for those who learn best by reading, and demonstration models or actual equipment for hands-on learners, all designed to increase the probability that there will be measurable positive results.
Some trainers are even able to integrate their programmes with customer Learning Management Systems, so companies can ensure thorough and convenient training for all employees – at all levels – across
multiple sites. Customers can make effective use of their learning management system (LMS) by centralising conveyor training, delivering consistent high-quality content inexpensively that is available 24/7 and by ensuring that all workers have the same level of education on vital bulk handling systems. This also gives trainers an opportunity to review data that helps identify trends or indicates a need for additional content or refresher courses.
While most maintenance workers are skilled technicians, they are often not expected to understand the conveyor holistically. Conveyors are complex, integrated systems; a change to one component will often have unintended consequences for others, affecting the rest of the system.
Without a complete understanding of how conveyors are designed, and components selected, maintenance becomes an exercise in finding the longest-lasting ‘band aids’ to treat the symptoms rather than solving the root causes. Before long, an accumulation of bad choices in treating symptoms results in a system that cannot operate at maximum efficiency.
Some companies continuously focus on an effective training culture (and thereby improve safety) from the top down. Organisations that embrace this approach show significant performance advantages over the competition. The proof is reflected in safety, productivity and environmental records, along with above industry-average financial returns and share prices.
While the goal of many training efforts is to maximise productivity, a key element in achieving this objective is improving safety, minimising injuries and the associated repercussions. Literature and research offer many pieces of the puzzle on how safety pays, showing a correlation between reduced expenses and a clean, efficient conveyor. Numerous case studies revealing the positive relationships between safety and productivity are backed up by organisations that gather global statistics on accidents and incidents.
Insufficient safety training can be incredibly costly to a mine, with direct and indirect costs of every accident. When mines ensure workers have sufficient training on particular risks, the risks and costs are minimised. Indirect costs are harder to understand, and often the return on investment is unclear to personnel. Expert training helps bridge that gap, and instead of simply teaching workers how to maintain a conveyor system, educators must also help students understand the consequences of not performing adequate maintenance.
The most effective approach to training examines a mine’s specific conveyor challenges and helps companies run cleaner, safer and more productive operations by treating the root causes of its problems.
When workers and management understand why certain actions are important, as well as the cascading effects that result from poorly trained staff, they are more likely to adjust behaviours and ultimately reap the benefits. a
Having taken delivery of the Anaconda SR520 finishing screen late last year, a South African mining contractor has deployed the machine in three challenging applications where it has already proven its mettle. Munesu Shoko visited the site in Brits, North West Province, to see the machine in action.
Following the official local launch in the third quarter of 2023, several Anaconda SR520 finishing screens are already hard at work at different sites, and Quarrying Africa recently had the opportunity to put one of the machines through its paces at a site in North West Province.
At the time of the visit, the machine had already completed its first job on site – screening recycled bricks for reuse at a brickmaking factory. The site manager at this particular project expressed satisfaction with the machine’s ease of set up, operation and maintenance, as well as its high production capabilities.
“We are happy to take delivery of one of the Anaconda SR520 units in southern Africa,” he says. “Despite operating it for a short period, we are already pleased with the high-production capabilities of the machine and its ease of operation. It is standing up to the challenging applications we have deployed it in.” At the time of writing, the machine had been on site for less than two weeks, but it had already processed more than 5 000 tonnes of material.
In its first job, the machine was deployed to produce a -9 mm material from recycled bricks. To meet its 500 tonnes per hour (tph) output capacity, the machine had
to be fed by two crushers – a jaw crusher and an impact crusher – at the same time. The two crushers broke down the scrap bricks to a smaller size, which in turn were fed onto the SR520, which stockpiled the required -9 mm material. Any material greater than -9 mm would go to the oversize conveyor of the SR520, which then fed it back to the impact crusher for recrushing.
Apart from this application, the machine is also deployed to process granite at the same site. Working in conjunction with a jaw crusher, the SR520 is deployed to produce two material sizes – 19 mm and a -9 mm. Feed material with a top size of up to 300 mm is fed into the available jaw crusher, which crushes it down to a -90 mm, before it is fed into the SR520, which then screens out the desired 19 mm and -9 mm sizes. The feed from the jaw to the SR520 is kept at a constant 600 tph, allowing the machine to produce 500 tph of product.
In addition, the machine has been deployed to process chrome, which is known for its unforgiving, abrasive nature. In this application, the SR520 is deployed to produce a -40 mm product. Similar to the granite setup, feed with a top size of up to 300 mm is fed into the jaw, which then crushes it down to a finer material, which in turn is fed into the SR520 for screening. A constant feed of about 500 tph is maintained to allow the machine to produce 400 tph of product.
At the time of writing, the machine had been on site for less than two weeks, but it had already processed more than 5 000 tonnes of material
The Anaconda SR520 is a high-production screen that can stockpile up to four different products at an output of up to 500 tph depending on screen size and product moisture content.
A leading mining contractor has deployed its new Anaconda SR520 finishing screen at a site in North West Province, South Africa
At the time of the visit, the machine had already completed its first job on site – screening recycled bricks for reuse at a brickmaking factory
Apart from this application, the machine is also deployed to process granite at the same site
In addition, the machine has been deployed to process chrome, which is known for its unforgiving, abrasive nature
The Anaconda SR520 is a high-production screen that can stockpile up to four different products at an output of up to 500 tph depending on screen size and product moisture content.
Complete with a 6 m x 1,52 m screen box, the machine has an option of either two or three decks. However, Shaun O’Toole, sales manager – Mining, Crushing & Screening at Vermeer Equipment Suppliers, confirms that the company has brought the first unit in a two-deck configuration, weighing in at 33 000 kg.
With a maximum hopper capacity of 6 m³, the machine comes with a main conveyor and either three or four hydraulically folding stockpiling conveyors. The screen is said to be extremely easy to commission and can
be up and running within 20 minutes of arrival on site. Commissioning is aided by the hydraulic controls to position and guide all the conveyors, screen box and landing legs into place.
Since its global launch, the SR520 is said to have established itself as a leading player in the global market. This recognition particularly stems from the machine’s ability to suit fine screening operations such as sand and other fine material. This screener can also be fitted with a rinsing screen to allow users to introduce primary washing to their operation.
While the Anaconda product is fairly new in the local market, the site manager says the existing relationship with Vermeer Equipment Suppliers, was key to the buying decision. In addition, he says the machine comes at a very competitive price point, yet it is a premium solution that ticks all the right boxes for the contract miner’s projects.
“We have known Shaun for a long time, and he is always willing to help whenever we need any form of technical assistance. It was therefore easy for us to make this decision. Apart from machine performance, we have been impressed by the support from the supplier,” he says.
The Anaconda product benefits from Vermeer Equipment Suppliers’ proven aftermarket support regime in southern Africa. The company stocks a full range of spare parts, demonstrating its commitment to providing a dedicated and responsive service to its customers in the region. This, says O’Toole, is particularly important for the contracting fraternity where machine downtime is out of the question. a
Always
Downtime is inevitable. And when you are up against the clock and the pressure is on – that is when accidents happen. From risks of falls or back injuries and cuts, rushed jobs where production is waiting on the change-out can lead to distracted workers and greater risk of accidents. By
specialist.
Aregular preventative maintenance schedule can help alleviate these risks, but sometimes unplanned maintenance is necessary. Breakdowns happen. In these cases, there are steps workers can take to reduce risk in screen media change-outs. Here is how.
Serge Raymond, MAJOR productThis may seem like an obvious statement, but personal protection equipment (PPE) is not something to take lightly. A good example of this is hand safety. It can be tempting to forego wearing work gloves for convenience or increased dexterity when handling nuts and bolts, but the risk is never worth it. Sharp
MAJOR recommends bringing a toolbox along with all the necessary tools, including extra bolts, washers and nuts. A good rule of thumb is if you need to replace five, bring 15
Workers should never change screens alone, but should ensure that someone else is always there to help, should an individual get into a dangerous situation.
OEM
Be sure that every employee is well trained on proper safety procedures when it comes to screen media installation, and work closely with your OEM or OEM-certified technician
edges on the tail end of screens and at the hooks can cause cuts to workers’ hands, not only posing a danger to the individual, but further delaying the operation resuming production.
To reduce risk of injuries, look for a screen media manufacturer that puts safety first. For example, some manufacturers include metal shrouds on their media.
That means no sharp edges on the wire for workers to worry about during handling and installation. However, this should never be thought of as a replacement for PPE.
This is probably the most effective way to prevent injuries, but often the hardest to accomplish – especially in a situation where production is waiting on the changeout. In these scenarios, it is important to remember that safety and attention to detail go hand in hand. Workers must take the time they need to complete their work safely, constantly being aware of their surroundings and taking the extra steps necessary to minimise risks.
For example, if a nut becomes jammed in an impact socket, workers should always disconnect the power source before trying to remove it. Though this can take a few extra seconds, it can prevent harmful accidents to employees.
Workers should never change screens alone, but should ensure that someone else is always there to help, should an individual get into a dangerous situation. Additionally, it is important that workers are diligent about using proper lockdown procedure, as well as wearing safety harnesses if the vibrating screen is high off the ground. While these steps may seem timeconsuming in the moment, they can prevent serious and even life-threatening injuries.
From risks of falls or back injuries and cuts, rushed jobs where production is waiting on the change-out can lead to distracted workers and greater risk of accidents
A regular preventative maintenance schedule can help alleviate these risks, but sometimes unplanned maintenance is necessary
To reduce risk of injuries, look for a screen media manufacturer that puts safety first
Planning the job properly is extremely important to not only the job’s efficiency, but the crew’s safety
Planning the job properly is extremely important to not only the job’s efficiency, but to the crew’s safety. Every trip up and down extends the process and exposes workers to more risk. MAJOR recommends bringing a toolbox along with all the necessary tools, including extra bolts, washers and nuts. A good rule of thumb is if you need to replace five, bring 15. This ensures you will have what you need to finish the job, even if a few things are accidentally dropped.
These tips should help operations minimise safety risks when changing out screen media, but they are just a starting place. Be sure that every employee is well trained on proper safety procedures when it comes to screen media installation, and work closely with your OEM or OEM-certified technician. a
AfriSam
AfriSam is a leading construction materials group in southern Africa. Since establishing its first cement plant in 1934, the company has grown into a formidable construction materials group with operations in South Africa, Lesotho and Eswatini.
www.afrisam.co.za
Babcock
Through several business units, Babcock offers a range of products and services, including construction and mining equipment, engineering solutions for steam generation and power plants, crane hire and gear rental, industrial generators, welding equipment and DAF truck sales and service.
www.babcock.co.za
Booyco Electronics
With more than 16 years of experience in Proximity Detection Systems solutions, Booyco Electronics has supplied over 6 500 sets of mining vehicle equipment installations across southern Africa, as well as more than 55 000 pedestrian RFID installations.
www.booyco-electronics.co.za
Bunting
Bunting’s range of magnetic separators and metal detectors for quarries and mines ensures the protection of crushers, screens and conveyors. Overband magnets, suspension magnets and pulley magnets automatically remove tramp ferrous metal from conveyed quarried rock.
www.bunting-redditch.com
IPR
IPR is recognised across the SADC region as the pump, heavy duty slurry handling and dredging specialist operating in underground and surface mining, quarrying, construction, wastewater, petrochemical and oil and gas sectors. www.pumprental.co.za
Pilot Crushtec International
Pilot Crushtec International (Pty) Ltd is South Africa’s leading supplier of mobile and semi-mobile crushing, screening, recycling, sand washing, stockpiling, compacting and material handling solutions.
www.pilotcrushtec.com
Sandvik
As a world-leading mining equipment manufacturer, Sandvik Mining and Rock Solutions is committed to improving your productivity and profitability. Our products and services provide you maximum value in terms of performance, quality, safety, flexibility and total economy.
www.rocktechnology.sandvik/en/
Astec
Astec Industries has been a global leader in providing innovative Rock to Road™ solutions since 1972, specialising in equipment for asphalt road building and aggregate processing.
www.astecindustries.com
John Deere
John Deere offers a comprehensive range of construction equipment, including ADT’s, excavators, loaders, dozers, graders, skid steers and TLB’s, designed to enhance productivity, efficiency, and performance on job sites of all sizes.
www.deere.africa/en/construction
Loadtech
LOADTECH Load cells Onboard Weighing are specialists in onboard weighing providing complete solutions onboard your heavy goods vehicle, primarily in the application of load cell and transducer systems for payload protection and accuracy in the commercial vehicle sector. www.loadtech.co.za
Schauenburg Systems
Schauenburg Systems is a South African company that specialises in providing technology solutions for safety and productivity in mining and industrial markets. It positions itself as an active partner for
Lintec & Linhoff
Lintec & Linnhoff is a global manufacturer and distributor of leading-edge solutions for the asphalt and concrete industries under the Lintec and Linnhoff brand names. Its products include asphalt mixing plants, concrete batching plants, pavement related technologies, and specialist concrete cooling solutions.
www.lintec-linnhoff.com
Weir Minerals
Weir Minerals Africa offers a wide range of equipment solutions including pumps, hydrocyclones, valves, dewatering equipment, wear-resistant linings, rubber products, screens and crushers – backed throughout the product lifecycle by high levels of aftermarket support.
www.global.weir
digital transformation to meet the needs of the “Connected Worker.” The company has a strong focus on innovation and has a brand promise of “Innovation that Saves”.
www.schauenburg.co.za
Sixteen brands, thousands of Innovative products, proven by a century of work. With unmatched strength from Rock to Road. We design and manufacture products used to build the infrastructure that physically connects the world. We were founded on innovation and a passion to help our customers succeed, and we are committed to growing as a partner to the industries we serve.