


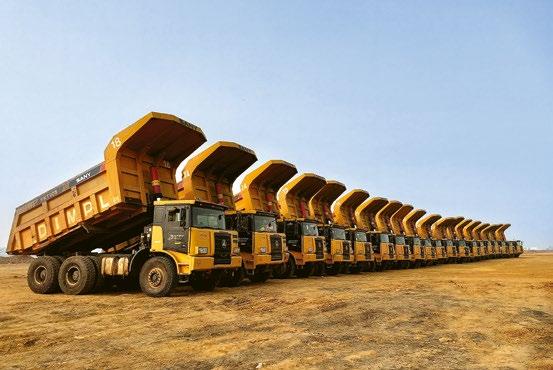
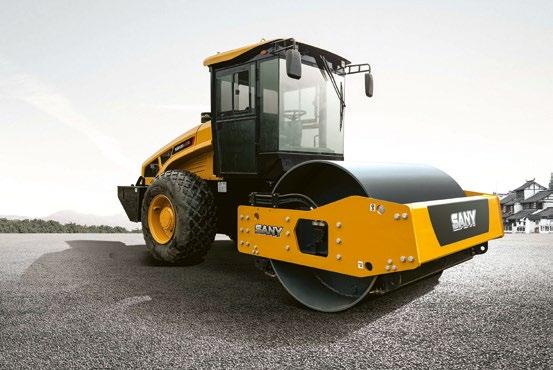
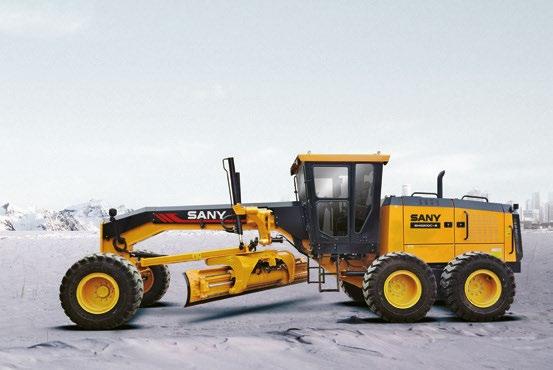


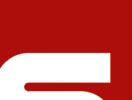

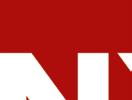
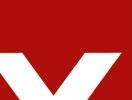
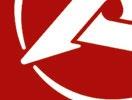
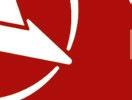
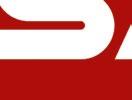
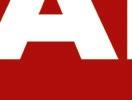
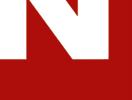

The recent 53 rd Institute of Quarrying Southern Africa (IQSA) conference and exhibition marked my 10 th attendance at this annual industry event which has become a staple on my calendar every year.
Judging from some of the presentations and discussions with exhibitors at this year’s event, it was apparent that the quarrying industry is at an inflection point, where environmental, social and governance (ESG), as well as digital technologies, are starting to take preference.
Amid growing pressure on mining companies to improve their ESG performance, it is encouraging to see a pipeline of new ESG policies among some construction material suppliers. A case in point is Raumix Aggregates, which used IQSA 2024 to outline its ESG initiatives and reinforce its unwavering commitment to improving its ESG performance.
There was a time when the industry’s stance on ESG issues was a public relations tactic. However, in today’s rapidly changing business climate, attention to ESG issues is becoming critical to long-term competitive success.
new concept, initially there was a degree of resistance. However, we are starting to see some senior and experienced engineers getting to understand that technology can deliver what they could previously only dream about.
The industry is increasingly making use of innovative and cutting-edge technologies to run more efficient operations, to manage risk, to improve health and safety, reduce the cost of maintenance and extraction, as well as bringing about a skills uplift.
With several other industries already embracing the digital revolution, the quarrying sector has recognised the potential of digital and technological innovations that could transform and invigorate the industry and is starting to move quickly to catch up. The economic environment presently forces businesses to ‘adapt or die’. The rate at which changes need to happen in a business is faster than it has ever been. Thankfully, technology is not only available but also affordable for enabling digital transformation.
MUNESU SHOKO
Publishing Editor Email: munesu@quarryingafrica.com
LinkedIn:
Munesu Shoko
Quarrying Africa
There is a common understanding that ESG represents one of the mining industry’s most significant opportunities for long-term value creation, building trust and sustainable growth. Miners are making significant strides to engage with their stakeholders and start to ‘bake’ ESG into the core of their strategies. To meet their ESG commitments, mining companies are getting serious about decarbonisation, while they are also working hard to overcome the trust deficit.
Another key talking point from this year’s event was the growing appetite for new technologies, particularly the digitalisation of work processes in quarrying. As with any
As the industry adapts to the changing operational environment, quarry owners are increasingly looking to digital technologies not only to enhance productivity and efficiency, but also to take people out of harm’s way. The importance of good health and safety management at operations cannot be restated enough as the industry presses ahead with its goal for zero harm.
IQSA 2024 once again demonstrated how companies are strongly showing their commitment to continually evaluating their operating practices in order to work towards a workplace with no illnesses, injuries or deaths. Like most industrial work, mining involves a degree of risk – and getting as close as possible to eliminating that risk and protecting workers always has to be a key initiative.
TIPPING BEYOND BORDERS
SENSORS
MEETING EVOLVING DRILLING NEEDS ‘LEAVING MONEY ON THE TABLE’
Publishing Editor: Munesu Shoko
Sub Editor: Glynnis Koch
Business Development Manager: Elmarie Stonell
Admin: Linda T. Chisi
Design: Kudzo Mzire Maputire
Web Manager: Thina Bhebhe
Quarrying Africa is the information hub for the sub-Saharan African quarrying sector. It is a valued reference tool positioned as a must-read for the broader spectrum of the aggregates value chain, from quarry operators and aggregate retailers, to concrete and cement producers, mining contractors, aggregate haulage companies and the supply chain at large.
Quarrying Africa, published by DueNorth Media Africa, makes constant effort to ensure that content is accurate before publication. The views expressed in the articles reflect the source(s) opinions and are not necessarily the views of the publisher and editor.
The opinions, beliefs and viewpoints expressed by the various thought leaders and contributors do not necessarily reflect the opinions, beliefs and viewpoints of the Quarrying Africa team.
Quarrying Africa prides itself on the educational content published via www.quarryingafrica.com and in Quarrying Africa magazine in print. We believe knowledge is power, which is why we strive to cover topics that affect the quarrying value chain at large.
Printed by:
Email: munesu@quarryingafrica.com
Cell: +27 (0)73 052 4335
Having made its local debut some two years ago, the Liebherr TA 230 has proven itself in some of the toughest operating environments in southern Africa.
Following the official local launch of the Liebherr TA 230 Litronic articulated dump truck (ADT) in June 2022, which marked Liebherr-Africa’s debut in the highly contested ADT market in southern Africa, several units are now hard at work in South Africa and Zimbabwe, where the ADT has proven its mettle in some of the toughest mining applications. By Munesu Shoko.
Having made its local debut some two years ago, the Liebherr TA 230 has proven itself in some of the toughest operating environments in southern Africa. With several units already operating in the field, clocking about 35 000 – 45 000 market hours in the process, Tendayi Kudumba, GM: Earthmoving Technology at Liebherr-Africa, expects the sales of the Liebherr TA 230 to pick up steam on the back of increased enquiries in the region.
“The ADT market in southern Africa is very competitive, but we are very happy with the sales performance and enquiries of the TA 230 to date. Several customers have shown immense interest in the machine, and we expect to put more units into the market soon,” says Kudumba.
With five units in its fleet, Orca Group, a prominent mining contractor operating in Zimbabwe, runs the biggest fleet of Liebherr TA 230 machines in southern Africa to date. In fact, the company was the recipient of the first ever TA 230 in the region, which was handed over during the official launch at the Liebherr-Africa headquarters in Springs, Gauteng, South Africa, in June 2022. The company initially took delivery of three units, before expanding the fleet with two more machines. The five machines have been deployed in a taxing application at Bindura-based Freda Rebecca Gold Mine, hauling ore from the underground tunnels to the overland crushers. Lavell Ruthman, head of sales, Earthmoving Technology at Liebherr-Africa, tells Quarrying Africa that the machines have
45 000
The several units already operating in the field have already clocked about 35 000 – 45 000 market hours
5
With five units, Orca Group runs the biggest fleet of Liebherr TA 230 machines in southern Africa to date
Having made its local debut some two years ago, the Liebherr TA 230 has proven itself in some of the toughest operating environments in southern Africa
With five units in its fleet, a prominent mining contractor operating in Zimbabwe, Orca Group, runs the biggest fleet of Liebherr TA 230 machines in southern Africa to date
Two of the first batch of five units to be delivered in southern Africa are hard at work in the Palaborwa area in South Africa
Another TA 230 operating in South Africa has been deployed in a chrome application in Limpopo
already clocked between 6 000 and 7 000 hours in this challenging application, travelling 15 km out of the pit fully loaded in extremely hot conditions.
Two of the first batch of five units to be delivered in southern Africa are hard at work in the Palaborwa area in South Africa. Running at this particular site for over a year now, the two Liebherr TA 230 units have already passed the 6 000-hour mark.
“Despite the heavy and abrasive nature of magnetite, the two machines have proven their mettle in this tough
Several customers have shown immense interest in the machine, and Liebherr-Africa expects to put more units into the market soon.
application, meeting the requirements of the customer in terms of uptime, efficiency and productivity,” says Ruthman. “The machine’s 28 000 kg payload with a dump body capacity of 18,1 m³ also fits the bill for the customer’s production requirements. The 6-cylinder Liebherr engine with a 12-litre displacement, producing 265 kW of power, has been praised on site for delivering enough power when needed.”
Another TA 230 operating in South Africa has been deployed in a chrome application in Limpopo. Delivered in late 2023, the machine has so far performed beyond expectations in what is known to be an abrasive application. The feedback from the customer, confirms Ruthman, has been very positive, with prospects of delivering more units in the near future.
Several customers who have purchased the TA 230 to date have expressed satisfaction with Liebherr’s new machine concept, which has been developed especially for challenging off-road applications. Modern designs in the front-end area create maximum ground clearance for greater off-road performance.
The newly designed articulated swivel joint creates sound off-road capability; it allows independent movement of the front and rear ends, thus ensuring maximum manoeuvrability. The positive-locking swivel joint with tapered roller bearing is perfect for the shear stresses associated with tough underfoot conditions, while it also withstands maximum loads and provides optimal force distribution.
The front and rear axles of the machine are secured using sturdy A-rods at the articulated swivel joint and at the rear end. On front, the truck uses hydro-pneumatic suspension for maximum comfort, which is key to the smooth driving. The shock absorbers at the articulated swivel joint and the position of the separate and oscillating A-rods of the rear axles at the rear end, provide maximum ground clearance.
Powered by a 265-kW 6-cylinder Liebherr engine with a 12-litre displacement, the TA 230 Litronic is driven by an automatic 8-speed powershift transmission which ensures optimal force distribution. The machine impresses with great driving performance and massive pulling force, even in the most difficult ground conditions and on challenging gradients.
“A combination of balanced weight distribution, permanent 6 x 6 all-wheel drive, solid, flexible mounting and large bank angle as well as the machine’s high ground clearance, enable the TA 230 Litronic to deliver unparalleled performance on uneven terrain,” says Kudumba.
The actively controlled inter-axle differential locks mean that the Liebherr TA 230 has automatic traction control. As soon as one axle experiences wheelspin, it is decelerated, and the traction is intelligently redistributed to the other axles. In addition to maximum forward drive, this reduces the power requirement and therefore translates into lower fuel consumption.
Efficiency is further enhanced by the smart gear selection, which enables the machine to adjust
automatically to its current speed and load to ensure optimum torque and fuel consumption at all times. The machine therefore automatically reduces its fuel consumption per tonne of transported material. With productivity in mind, the optimised trough ensures that more material can be moved in a short time. The front of the trough – designed for the effective transport of a 28-t payload – is straight and the sills are low so that loading with a wheel loader, for example, is easily possible across the entire length of the truck.
A standard Liebherr weighing system shows the current payload during loading on the display in the operator’s cab, helping eliminate guesswork in loadout processes. An optional loading light on both sides at the back of the operator’s cab shows the loading level outdoors.
In order to accelerate the release of the material during unloading, the inner edges of the new trough are tapered. The two tipping cylinders at the side give the TA 230 Litronic high tipping pressure. The load can be tipped against the slope easily and quickly.
“During transportation, the long chute at the end of the trough ensures minimal material loss. The trough volume can be increased with the optional tailgate. Thanks to the large opening width, tipping of large and bulky transported material is easily possible. Even with the tailgate the overall width of the TA 230 Litronic is still below three metres, which allows the machine to be easily and quickly transported on a lowbed truck,” concludes Ruthman. a
The appointment of Maretha Gerber as President and CEO marks a new beginning at Daimler Truck Southern Africa (DTSA). In a one-on-one with Quarrying Africa, Gerber – who makes history by becoming the first female to hold this position at DTSA – says she will build on the strong foundations of the market-leading brand to further drive growth and customer satisfaction. By Munesu Shoko
At a press conference attended by Quarrying Africa recently, DTSA announced that Gerber, who has been with the company for over 20 years, will take the reins as President and CEO, effective April 01, 2024. She takes over from Michael Dietz, who is up for a new challenge as President and CEO of Regional Centre Middle East and Africa at Daimler Truck.
Gerber brings a wealth of experience, which puts her in good stead to drive the marketleading brand to even greater heights. Equipped with a degree in marketing, she has held several positions within the Daimler organisation, including previously Daimler Chrysler and Mercedes-Benz South Africa.
She has fulfilled various functions across sales,
marketing and the dealer network before taking up a dealer principal role in the Mercedes-Benz Own Retail dealer network. In 2018, she moved back to the DTSA headquarters as head of Mercedes-Benz Trucks and subsequently Vice President Sales and Marketing for MercedesBenz and FUSO Trucks, a position she held before taking up the new role in April.
“We are delighted to welcome Maretha Gerber as the new President and Group CEO for DTSA and the second female on the Daimler Truck Overseas ExCom team. With her vast experience and excellent client rapport, we cannot think of anyone better for this position,” says Andreas von Wallfeld, head of Daimler Truck Overseas. “Likewise, with his extensive knowledge and broad experience, we are pleased to have won Michael for the Regional
Maretha Gerber makes history by becoming the first female to be appointed President & CEO at DTSA 20
Maretha Gerber has been with the company for over 20 years, which puts her in good stead to drive the marketleading brand to even greater heights
She takes over from Michael Dietz, who is up for a new challenge as President and CEO of Regional Centre Middle East and Africa at Daimler Truck
Gerber brings a wealth of experience, which puts her in good stead to drive the market-leading brand to even greater heights
She seeks to build on the strong foundations of the market-leading brand to further drive growth and customer satisfaction
Centre Middle East and Africa. We wish both Maretha and Michael all the best in their new roles.”
Following a record-breaking year in 2023, DTSA maintained its market-leading position in the extra heavy commercial vehicle market. Gerber says she will build on the strong foundations laid by her predecessor and the DTSA team at large. Her leadership will seek to create a “strong force” amongst DTSA employees, building on the strengths of the team. She also aims to build additional strong collaboration between DTSA, its dealers and, more importantly, its customers.
“I am truly honoured to be afforded the opportunity to lead DTSA. I am excited to work with the experienced leadership team and talented employees at DTSA and to lead the group of companies to new heights,” she says. “Together with our dealers and general distributors, we look forward to contributing to further growth and success and to build a brighter future for all stakeholders.”
Commenting on the record-breaking year in 2023, Gerber tells Quarrying Africa that several drivers were key to the growth of the commercial vehicle market. Firstly, the rail infrastructure challenges had a major impact on the growth of the trucking market, with the majority of South Africa’s freight now moved by road.
“Another major driver behind last year’s growth was the fact that most of our loyal customers had delayed their replacement cycles and it was time for them to replace as they could not ‘sweat their assets’ any longer. About 70% of our sales last year were from loyal customers who were either replacing or expanding their fleets to meet their business requirements,” says Gerber.
In recent years, the neighbouring African markets – including Zimbabwe, Zambia, Mozambique and Malawi – have seen steady growth. As part of her growth plans, Gerber wants to further grow DTSA’s sales volumes into these markets and higher up into Africa.
“Our focus this year is to increase our volumes into Africa. These markets have in recent years seen yearon-year growth. We believe there is opportunity for sustainable growth in Africa in years to come,” she says.
While the growth in construction activity is not at the levels experienced during the so-called ‘boom days’ in the run up to the 2010 Soccer World Cup, Gerber says the industry has definitely come out of a prolonged downturn.
“We see a lot more enquiries for our Arocs vehicles in particular,” she says. “We are not at the levels experienced during the boom days, but the sentiment in the market is much more positive, particularly in some of our export markets. That said, we need more investment in construction in South Africa.”
Apart from the Mercedes-Benz Arocs range, Gerber says the FUSO FJ range is doing phenomenally well in the construction market. The truck, she adds, has built a strong reputation for reliability and fuel-efficiency, and has taken the company to the next level within the construction market.
Commenting on the outlook of the market in 2024, Gerber says she believes that truck sales will normalise this year following the record growth last year. “I am of the view that the market will come to its normal levels this year, especially given that most of the big replacement cycles happened last year. However, I believe it will still stay strong, given the continued rail infrastructure challenges in the country,” concludes Gerber. a
BELL 4X4 ADTS ARE THE IDEAL HAUL TRUCK, OFFERING THE TIGHTEST TURNING CIRCLE AND LONGEST TYRE LIFE.
FINLAY MOBILE CRUSHERS, SCREENERS AND CONVEYORS ARE DESIGNED TO PRODUCE THE BEST SIZE AND SHAPE OF PRODUCT REQUIRED.
KOBELCO EXCAVATORS PROVIDE THE BENCHMARK IN HYDRAULIC AND FUEL EFFICIENCY WITH PROVEN DURABILITY AND RESALE VALUE.
JCB WHEEL LOADERS ARE GAINING TRACTION INTHE QUARRY INDUSTRY WITH THEIR SIMPLE YET EFFICIENT DESIGN AND PERFORMANCE.
With the existing old primary plant at its Cape Lime Langvlei operation proving uneconomical to run, Afrimat invested in a two-phased plant upgrade entailing the installation of a completely new primary plant. The project has contributed greatly to the sustainability of Langvlei through the addition of scale and reduction of operational costs as a result of better efficiencies and higher output.
By Munesu ShokoThe history of Cape Lime, now a subsidiary of Afrimat since the 2016 acquisition, dates back as far as 1943 when the first vertical shaft kiln was commissioned by Cape Lime Company Ltd on the farm Langvlei near Robertson in Cape Town.
The operation’s main business is producing bagged hydrated lime through a calcining, hydrating and milling process. Aggregates
and agricultural lime add further value to the business as the run-of-mine fragmentation results in a finer yield of product, enabling the Afrimat commercial team to have a diversified product split and customer base.
To provide context, lime is used across industries for various purposes such as to neutralise and cleanse drinking water and in sugar production. It also serves as a calcium supplement in vitamins and some foods. In road
When Afrimat took over in 2016, the management team realised that the structural integrity of the primary processing plant was problematic, and an audit by external engineers highlighted and confirmed these concerns
The old AgLime plant produced at approximately 10 tph, while the upgraded Phase 1 AgLime plant can now produce at approximately 30 tph, representing a 200% increase in production capacity
Phase 2 of the project entailed the construction of an entirely new primary plant which feeds both the kilns on site with run-of-kiln feed, and the aglime plant with feedstock.
Afrimat has invested in a two-phased plant upgrade entailing the installation of a completely new primary plant at its Cape Lime Langvlei operation
Phase 1 entailed the installation of four conveyors of different sizes (designed by Afrimat engineering), a Techroq VSI crusher and a Union High Frequency screen with Afrimat-engineered bins and transfer points
Phase 2 scope comprised newly built conveyors, bins, screen structures, transfer points, as well as refurbishing a 6 x 16 double-deck screen for primary screening and refurbishing a 5 x 12 triple-deck screen for secondary screening
Following the two-phase plant upgrade, kiln feed availability has increased, and the operation does not need to run a double shift anymore to ensure stock availability for the kilns
construction, lime is used in asphalt, below the asphalt and during construction. Buildings are also constructed using at least one type of lime product, while it is also deployed to produce paper. In addition, it is used for food security (agricultural lime).
The operation also supplies crusher run to civil contracts within its vicinity, which are few and far between. The last project the Langvlei team supplied was in 2021 when a contractor built the Ashton bridge and rehabilitated the R60 between Ashton and Montagu. The operation also supplies local readymix companies, brick and block manufacturers, as well as local hardware stores with aggregates.
The Langvlei operation has produced high-quality pressure-hydrated dolomitic lime since 1943, and much of the original infrastructure has remained intact. A few upgrades took place in the early days when Cape Lime managed the business (after a management buyout
Following the two-phase plant upgrade, kiln feed availability has increased, and the operation does not need to run a double shift anymore to ensure stock availability for the kilns.
from Trans Hex), including improvements to the hydrator and the milling section.
When Afrimat took over in 2016, the management team realised that the structural integrity of the primary processing plant was problematic, and an audit by external engineers highlighted and confirmed these concerns. The first round of safety improvements was rolled out, including upgrades and improvements to catwalks, walkways, platforms and some structures and chutes. This was always going to be an interim solution that would require the team to still investigate a long-term, sustainable solution.
Due to its old age, the primary plant could not be economically upgraded to meet the growing demand and the broadening range of materials. The management team at Afrimat therefore decided that the best remedy to the situation was to build an entirely new primary plant. Stephan Becker, Manager at Cape Lime Langvlei, championed the project, with support from Afrimat’s Engineering Department and project lead, Robert Hurn.
“There were effectively two phases to the primary plant upgrade at Langvlei,” explains Andrew Wray, MD Afrimat Industrial Minerals. “Phase 1 entailed the construction of a dedicated Aglime plant to meet the growing need for agricultural lime in the Western Cape; and Phase 2 was for the construction of an entirely new primary plant which feeds both the kilns on site with run-of-kiln feed, and the aglime plant with feedstock. We also geared the primary plant to produce a range of aggregate sizes, including G-materials.”
Phase 1 of the project, explains Becker, was planned, designed, manufactured and erected in two months and commissioned for production by the end of April 2022, just in time for the AgLime season. This phase comprised the installation of four conveyors of different sizes (designed by Afrimat engineering), a Techroq vertical shaft impact (VSI) crusher and a Union High Frequency screen with Afrimat-engineered bins and transfer points. The old AgLime plant produced at approximately 10 tonnes per hour (tph), while the upgraded Phase 1 AgLime plant can now produce at approximately 30 tph, representing a 200% increase in production capacity, confirms Becker.
“We took a different approach on the building process and actually built the plant from the backend to the front. This allowed us to still produce with the old plant to ensure that we met aggregate demand,” says Becker.
Upon completion of Phase 1, the engineering team began the construction of Phase 2, the primary crushing and screening plant. This part of the plant was designed to tie into the old layout that made use of the existing jaw crusher (Osborn 25x36), a cone crusher (Osborn 36-7s) and the original T7 Oremaster VSI.
The scope also entailed newly built conveyors, bins, screen structures, transfer points, as well as refurbishing a 6 x 16 double-deck screen for primary screening and refurbishing a 5 x 12 triple-deck screen for secondary
screening. The team also built a new motor control centre (MCC) substation and central control room (CCR) and located them approximately in the centre of the layout so that the operator has prereferral views of the process.
All in all, the plant consists of 10 newly built conveyors of various sizes (Afrimat engineering design), a 6 x 16 double-deck primary screen and a 5 x 12 triple-deck secondary screen. The screens were salvaged from two different Afrimat yards. The double-deck screen came from the Langvlei operation’s salvage yard, while the triple-deck screen was salvaged from the Glen Douglas yard in Gauteng. Both the screens were refurbished by a service provider in Blackheath, Cape Town. “Part of the project’s cost-saving initiatives was to repurpose available machines within Afrimat,” explains Becker.
All chutes, transfer points, screen structures and product bins were also designed by Afrimat engineering. One of the major talking points is the innovative chute designs that enable the production team to manually dictate what products can be produced, how much gets produced, and how much of the product stream can be sent to the agricultural lime plant for further processing to achieve the stringent specification: 100% passing 1,7 mm and 50% passing 250 microns.
“We can say, with confidence, that we achieved 90% of what we set out to achieve and it was done within 125 days from start to completion,” says Becker.
Following the two-phase plant upgrade, kiln feed availability has increased, and the operation does not need to run a double shift anymore to ensure stock availability for the kilns. Kiln feed sizing has also been improved significantly, ensuring an optimised calcining
process, thus improving oxide quality and ensuring less wear and tear on refractory linings, as well as reducing consumption of burning fuel.
“Some of the key benefits of the upgrade include improved aggregate product quality (shape and size); production flexibility (which improves production to sales yields); improved production capacity of agricultural lime; enhanced safety; as well as improved key performance indicators such as overall plant performance, plant availability, plant utilisation and planned maintenance percentages,” explains Becker. In addition, the upgrades have ensured better employee morale and reduced production costs.
Executing both phases was not without challenges. Time constraints and the Western Cape winter weather presented a fair share of contests. This was exacerbated by logistical challenges to transport the components. To provide context, all structures, bins, transfer chutes were manufactured in Gauteng, and had to be transported to Robertson, Western Cape.
The project team also encountered some challenges with regards to electrical reticulation as they did not know where old cables were running underground. As a result, there were some damages incurred during the trenching stage to fit new plant cables.
“The Afrimat project team and project manager are very competent, making a project like this, where second hand equipment is repurposed and erected with new structures, a pleasure to be part of. Proper planning, project scope drafting, communications between the project team, client and suppliers were well managed, ensuring a successful result,” concludes Becker. a
Loutjie
Loadtech has appointed Loutjie Van der Merwe as Loadrite divisional manager. In a oneon-one with Quarrying Africa, he discusses his blueprint to further position Loadrite as a top choice in the market, some emerging trends in load weighing and how the new L5000 SmartWeigh system changes the game in weighing operations. By Munesu Shoko.
To entrench the Loadrite offering as a market leader in the payload management systems market, Loadtech, the authorised Loadrite distributor in sub-Saharan Africa, has assigned Loutjie van der Merwe to lead the brand, effective March 1, 2024.
His role entails overseeing and managing all aspects of the Loadrite brand, including developing and implementing branding strategies, managing brand messaging and positioning, ensuring brand
consistency across all marketing channels, as well as monitoring and analysing brand performance.
“I will work closely with other departments such as marketing, sales and product development to ensure that the brand accurately reflects the company’s values, goals and target audience,” says Van der Merwe. “Additionally, I will be responsible for monitoring market trends, competitor activities, and consumer feedback, to continuously refine and improve the brand’s image and reputation.”
Ultimately, his goal as a divisional manager is to
With its WiFi readiness and touchscreen interface, the new L5000 SmartWeigh system from Loadrite will revolutionise the industry by providing more convenience, accuracy and efficiency in weighing operations
With its WiFi readiness and touchscreen interface, the new L5000 SmartWeigh system from Loadrite revolutionises provides more convenience, accuracy and efficiency in weighing operations.
Loutjie van der Merwe has been appointed the Loadrite divisional manager at Loadtech, effective March 1, 2024
Van der Merwe notes increasing demand for advanced technology integration such as cloud connectivity to enable real-time data monitoring and analysis
In addition, there is a growing emphasis on accuracy and precision in load weighing systems to ensure compliance with industry standards and regulations
Additionally, there is a trend towards the development of more user-friendly interfaces and mobile applications for easier operation and data management
build a strong and recognisable brand that resonates with consumers and drives business growth.
Van der Merwe brings a wealth of experience. As a student at the University of Pretoria, he joined the campus radio station, Tuks FM 107.2, as marketing executive in 2003. He went on to fulfil various functions, including marketing manager, sales executive, business manager and eventually station manager from 20062013.
3, 2024
Loutjie van der Merwe’s appointment as Loadrite divisional manager at Loadtech is effective March 1, 2024
The L5000 SmartWeigh system is poised to streamline weighing processes, improve productivity and provide valuable insights for better decisionmaking in various industries.
At the end of 2013, he was appointed general manager for the online division of IT giant, Pinnacle Africa, before joining South Africa’s leading commercial trailer manufacturer, AFRIT, as head of marketing, a year later. After eight fruitful years at AFRIT, he had the urge to learn and experience something new, so in 2023 he joined Trail-Link, a South African manufacturer of electrical coils and suzis, as brand and sales representative.
“I feel that all the contacts and relationships I have built over the past 20 years will certainly stand me in good stead to take the Loadrite brand and its exposure to the next level, and I look forward to being the brand custodian connected to this journey,” he says.
Commenting on some of his immediate objectives in the new role, Van der Merwe tells Quarrying Africa that
Commenting on some of the trends observed in the market, Van der Merwe notes increasing demand for advanced technology integration such as cloud connectivity to enable real-time data monitoring and analysis. In addition, there is also a growing emphasis on accuracy and precision in load weighing systems to ensure compliance with industry standards and regulations.
“Additionally, there is a trend towards the development of more user-friendly interfaces and mobile applications for easier operation and data management. Overall, the market is moving towards more efficient, reliable and technologically advanced load weighing systems to meet the changing needs of industries,” he says.
crafting a clear and compelling brand positioning and messaging strategy that differentiates Loadrite from competitors and resonates with the target audience is principal.
In addition, he aims to develop a multi-channel marketing plan to effectively communicate the brand messaging and reach the target audience through various touchpoints. He will also monitor the key performance indicators (KPIs) to track the impact and success of branding initiatives and make data-driven decisions to optimise future strategies.
“I also aim to build strong relationships with internal stakeholders, such as marketing, sales and product development teams, to align brand objectives and collaborate effectively,” he says. “In addition, it will be important to stay up-to-date with industry trends, consumer insights and competitor activities to identify opportunities for brand growth and innovation.”
Another key objective for Van der Merwe is to implement feedback mechanisms to gather insights from customers and stakeholders in order to continuously refine and improve the brand experience. These objectives, he says, will help him establish a solid foundation for the brand and set a clear direction for future growth and success.
To further entrench the Loadrite offering as a market leader in the industry, Loadtech, in partnership with its principal, Loadrite, will ideally focus on enhancing product features and capabilities to meet evolving customer needs.
“Additionally, we will invest in marketing strategies to increase brand visibility and awareness to help position Loadrite as a top choice in the market. It is also important to build strong relationships with customers and provide excellent customer service to solidify Loadrite’s reputation as a leader in the industry,” he says.
In line with these trends, Van der Merwe believes that the new L5000 SmartWeigh system from Loadrite, with its WiFi readiness and touchscreen interface, will revolutionise the industry by providing more convenience, accuracy and efficiency in weighing operations.
The system’s wireless connectivity enables seamless data transfer and real-time monitoring. The touchscreen interface offers intuitive and userfriendly navigation, enhancing ease of use for operators.
Overall, the L5000 SmartWeigh system is poised to streamline weighing processes, improve productivity and provide valuable insights for better decision-making in various industries. Its cutting-edge features, he adds, have the potential to change the way weighing systems are used and perceived, making Loadrite a frontrunner in the market.
“This year, our goals for the L5000 SmartWeigh system launch include increasing market adoption, establishing the product as a leading solution in the industry and showcasing its value through customers’ successes and testimonials. We aim to drive revenue growth, expand our customer base and solidify our position as a trusted provider of innovative weighing technology. Additionally, we hope to receive positive feedback, gather insights for future product enhancements and continue to innovate and improve our offerings based on customer needs and market trends,” concludes Van der Merwe. a
In July this year, AfriSam turns 90, a remarkable milestone in business longevity. Over the nine decades, the leading construction materials supplier has seen good times and has also survived extremely turbulent periods. For a business that operates in such a cyclical environment, organisational resilience, innovation and adaptability have been key to its longevity. By
Munesu ShokoAs an industry leader in building and construction materials, AfriSam’s business model has always been dedicated to customer satisfaction, a philosophy that has been at the core of the company’s success for the past 90 years.
The company’s story began in 1934 with the launch of Anglovaal Portland Cement Company Ltd, a small building materials supplier. After several name changes, mergers, company expansions, technological innovations and the addition of a slagment business to the portfolio, the AfriSam brand was born in 2008.
Over the years, AfriSam has cemented itself as a leading construction materials supplier in southern Africa, with operations in South Africa, Lesotho and Eswatini. With a workforce of about 1 300
people (including permanent, contract and learner employees), the company operates two fully integrated cement plants in South Africa, a milling plant with blending and packing facilities, five blending plants (three in South Africa, one each in Lesotho and Eswatini), a slag grinding plant, 19 readymix plants and 12 aggregate quarries.
Across these operations, the company has the capacity to produce 4,5-million tonnes (t) of cement, 800 000 t of slagment, over 5-million t of aggregates and 1,5-million m³ of readymix concrete per annum.
Reflecting on the past 90 years, Glenn Johnson, Executive: Construction Materials, Operations, says AfriSam’s journey is a true reflection of the road that South Africa has travelled during the past century. “Our history as a company interrelates
With a workforce of about 1 300 people (including permanent, contract and learner employees), AfriSam operates two fully integrated cement plants in South Africa
The Gautrain was a milestone project for us. To provide context, we supplied 200 000 t of cement to the Gautrain Rapid Rail Link Project South Section and nearly 439 000 t of 73 mm ballast. On average, some 300 t of crushed material was used daily on this project.
with key periods of structural change in the country. Our transition over the years pretty much mirrors what the country has gone through over the past 90 years,” he says.
While AfriSam’s 90-year milestone is a legacy of successful creation of concrete possibilities, the road has not been without speed bumps. Surviving some of the of the worst financial disasters of the 20 th Century – the Great Depression and the Great Recession of 2008 in particular – has provided the blueprint to weather recent economic storms.
Amit Dawneerangen, Executive: Construction Materials, Sales & Product Technical, says the lack of infrastructure spending in the past decade has been one of the key challenges of recent times. In fact, adds Johnson, the construction sector in South Africa has contracted approximately 40% since 2010, yet the construction industry has the ability to be the single
4,5-million tpa
Across its operations, AfriSam has the capacity to produce 4,5-million tonnes of cement per annum
“Our history as a company interrelates with key periods of structural change in the country. Our transition over the years pretty much mirrors what the country has gone through over the past 90 years.
AfriSam’s story began in 1934 with the launch of Anglovaal Portland Cement Company Ltd, a small building materials supplier
Over the years, AfriSam has cemented itself as a leading construction materials supplier in southern Africa, with operations in South Africa, Lesotho and Eswatini
On the project front, the company has supplied its quality construction materials to some of the flagship projects in the country
In the early 2000s, AfriSam was instrumental in the construction of the Nelson Mandela Bridge in Johannesburg, the largest cable-stayed bridge in South Africa
The construction industry has the ability to be the single largest source of employment across all sectors.
largest source of employment across all sectors.
Furthermore, the influx of imported cement in South Africa has been ‘a thorn in the side’ of local cement producers. To provide context, South Africa has an installed capacity of 21-million tonnes per year (tpy). Due to the lack of meaningful infrastructure investment, the industry currently produces in the region of 12-million tpy. Yet, there are about a million tonnes of imports coming into the market annually, mainly in the coastal areas of the country, leaving the industry battling with about 9-million tpy of extra capacity.
In addition, says Dawneerangen, the demise of the socalled “Big Five” construction contractors post the 2010 infrastructure boom was a big shock to the system. This had a significant effect on the order book and the AfriSam business at large. Suddenly, says Dawneerangen, the customer profile shifted from large companies to medium sized and smaller emerging contractors.
“We have had to adjust accordingly to be able to serve this group of customers. For example, we had to create new procedures for credit facilities that speak directly to emerging contractors. In the process, we had to streamline our processes and become more flexible for us to be able to trade with these enterprises,” explains Dawneerangen.
The same view is shared by Johnson, who says the requirements of small companies are different to those of the large contractors, and this has called for a greater degree of adjustment and flexibility on AfriSam’s part.
“We have streamlined the business to be more agile and flexible. In fact, we have eliminated the traditional layers of reporting structures to ensure efficiency and the ability to operate in the new business environment,” explains Johnson.
Skills shortage has been one of the recent key challenges facing AfriSam and the construction fraternity in general. According to Johnson, the brain drain has left a big skills hole that is hard for the industry to fill. As a result, companies such as AfriSam have had to invest significantly in their own skills development programmes.
From around 2017, government’s reduced infrastructure budget contributed to depressed market conditions.
AfriSam, however, managed to tighten its belts and maintained its aggregates and readymix concrete footprint. When it looked like conditions could not get any worse, the Covid-19 pandemic struck, and AfriSam had to go into a rationalisation mode to survive the tough market conditions. Consequently, the company had to reduce its Construction Materials (CM) division’s capacity by almost 50%. Only nine out of the company’s 17 aggregate quarries, and 17 out of the 40 readymix plants were kept operational at the time. Through a Section 189 process, the company had to reduce its CM staff complement by half.
However, a Covid-19 recovery plan demonstrated the company’s adaptability. The experienced management team, with the support of the board, was able to navigate this difficult process independently.
Despite these challenges, AfriSam has recorded some major successes during its 90-year journey. On the project front, the company has supplied its quality construction materials to some of the flagship projects in the country.
In the early 2000s, AfriSam was instrumental in the construction of the Nelson Mandela Bridge in Johannesburg, the largest cable-stayed bridge in South Africa. To fill the deep piles underpinning the bridge, AfriSam designed a special self-compacting concrete with extended workability. The concrete was then pumped into the 47-m high pylons from the bottom upwards, a process which had never been attempted before in South Africa.
The run-up to the 2010 Soccer World Cup, says Johnson, was inarguably the most positive business period for AfriSam in recent times. One of the projects of note was the Gautrain, an 80-km high-speed commuter rail system in Gauteng which links Johannesburg, Pretoria, Kempton Park and O. R. Tambo International Airport.
“The Gautrain was a milestone project for us. To provide context, we supplied 200 000 t of cement to the Gautrain Rapid Rail Link Project South Section and nearly 439 000 t of 73 mm ballast. On average,
some 300 t of crushed material was used daily on this project,” explains Dawneerangen.
In addition, Johnson says the Gauteng Freeway Improvement Project (GFIP) was another important project, where AfriSam supplied material for the upgrade of 185 km of Gauteng roads. This was complemented by other big projects such as stadia and bridges.
Elsewhere, AfriSam was a key supplier to the Durban Harbour project between 2007 and 2008. The project entailed widening of the harbour by approximately 150 m and increasing the depth from minus 12 to minus 19 m. AfriSam established two readymix concrete batching plants on site that produced 300 m³ of concrete in an eight-hour shift. In total, AfriSam supplied a total of 124 000 m³ of concrete to the project.
The Leonardo, a mixed-use high-rise development in Sandton which, on completion, was the tallest building in Africa at 234 m, before being surpassed by the 264-m Great Mosque of Algiers Tower in Algeria in April 2019, is yet another notable project in the history of AfriSam. The “key-wall” columns constitute a special feature of the Leonardo. To control the plumb, state-of-the-art specialised GPS technology was used. Hi-tech sonic vibrators were successfully used in the columns for optimum compaction. To counteract friction stresses, aggregate size was reduced to 13,5 mm and 9,5 mm.
The historic 100-year-old Grain Silo complex, a thriving grain storage hub in Cape Town, was repurposed to house the Zeitz Museum of Contemporary Art Africa (MOCAA). AfriSam supplied all the new concrete requirements for this project. The main mix for the silos, including the sleeves, was a prescribed mix of 30 MPa with a 9 mm stone. The mix was developed over a period of testing to ensure that it would have the correct consistency. Aggregates were an important factor in the final mix design as the surface finish had to meet the stringent specifications of the architect but also had to comply with
the workability requirements.
Another milestone project for AfriSam is the Ingula Storage Scheme, Eskom’s third pumped storage scheme with an output of 1 332 MW, which is mostly used during peak-demand periods. The station became fully operational at the end of 2015. Here, AfriSam supplied in excess of 230 000 t of cement from the project’s commencement in 2010. Supply also included 98 000 t of sub-base and 55 000 t of overburden. Approximately 14 000 t of aggregate were supplied for readymix, pipes and manholes.
Other significant projects in the supply history of the company include the Michelangelo Towers, the Sandton Convention Centre, O.R. Tambo Airport Central Terminal Building, the Glen Shopping Centre, BRT Cape Town, Vodacom Head office, Lakeside Mall, Allandale Bridge, Newtown Junction and the Group Five Housing Project in Soshanguve, amongst others.
Commenting on some key trends in the construction materials market, Dawneerangen highlights the greater focus on sustainability. Having embarked on its sustainability journey some three decades ago, AfriSam has over the years introduced a number of initiatives to reduce its carbon footprint. Chief among them is the use of extenders to reduce clinker content in its cement. In 2009, AfriSam was the first cement maker to introduce a CO2 rating system, indicating the carbon footprint of each of its cement products relative to Ordinary Portland Cement (OPC). The company has also become the world’s first construction materials supplier to Carbon Footprint all its production operations, including cement, aggregates and readymix concrete operations.
AfriSam was also the first cement company to publish an environmental policy, having done so in 1994. In 2012, the company became the first cement company to pledge support to Eskom’s R49-million campaign to demonstrate its commitment to the global agenda for energy efficiency. Owing to a number of initiatives, AfriSam has reduced its carbon emissions by 33% since 1990 – making it a leader in decarbonisation efforts in the South African cement sector.
On the readymix concrete side of the business, the company uses supplementary cementitious materials such as slagment and fly ash to reduce the amount of cement in its concrete. “In some mixes, we use up to 70% supplementary cementitious materials, depending on the application,” says Dawneerangen. “Our readymix plants also have strict re-use and recycling processes, and must recycle most of their grey water generated on-site. Some of the plants are now using 100% recycled water as mixing water for concrete at their operations.”
Finally, Johnson says for the company to survive the next 90 years, it has to become more agile, more resourceful and entrepreneurial than ever before. “Being a corporate does not guarantee success anymore. To be relevant in the future, I believe we will have to transform our corporate mindset into operating more entrepreneurially and independently of a traditional corporate structure. Adaptability and resourcefulness will be the order of the day,” concludes Johnson. a
A Trio TC51 cone crusher with conveyer and cone surge hopper for processing material.
In response to the growing demand for solutions that enable crushing contractors to easily move on and between production sites, Weir Minerals Africa is reintroducing its Weir Modular Wheeled Plant (WMWP) concept in Africa. Tiisetso Masekwameng, GM – Crushing & Screening Products, unpacks the solution and its benefits. By Munesu Shoko.
Given the nomadic nature of their operations, crushing and screening contractors place high value on mobility and transportability of their plants.
Bearing that in mind, Weir Minerals Africa’s WMWP concept takes both these parameters to a whole new level.
In an exclusive interview with Quarrying Africa, Masekwameng explains that wheeled plants have always formed part of the Trio crushing and screening offering and make use of Weir Minerals’ Trio crushers, screens and material handling solutions. However, the solution has been completely redesigned to suit new market dynamics.
“Our wheeled plants have been used across the world in sand and aggregates by clients who require
the flexibility of a mobile plant without the complexity needed for additional maintenance obligations of components such as diesel engines and associated tracks on the mobile unit itself. We have found this concept to be a good solution for crushing and screening contractors who want to be able to move their equipment from site to site at short notice,” she explains.
Commenting on targeted applications, Masekwameng says the wheeled plants concept is primarily intended for the construction market, as well as the mining sector, particularly where clients require short-term solutions to help boost production rates during commodity upswings, without constructing a new static plant over a longer lead time. Weir Minerals Africa will use the
tph
Machines used for Weir Minerals’ wheeled plants are in the 50 to 350 tph range
The modular wheeled plants are available in various configurations using simple mobile conveyors to configure a plant for the customer’s requirements.
Weir Minerals Africa is reintroducing its redesigned Weir Modular Wheeled Plant (WMWP) concept in Africa
The WMWP concept takes both mobility and transportability of crushing and screening plants to a whole new level
The solution is targeted for contractors looking for solutions that allow them to easily relocate their plants to infrastructure development hotspots
Wheeled plants eliminate the complexity of having a diesel engine and tracks which require additional maintenance over and above the crushers and screens themselves
upcoming Electra Mining exhibition in September this year to showcase one of the first units.
“Many of our clients in the construction market are looking for solutions that allow them to easily relocate their plants to infrastructure development hotspots. Once they get to site, they want to mobilise quickly and start operating immediately,” says Masekwameng.
This, she adds, means that clients do not always have the time to go through a design and delivery period associated
“Our wheeled plants have been used across the world in sand and aggregates by clients who require the flexibility of a mobile plant without the complexity needed for additional maintenance obligations of components such as diesel engines and associated tracks on the mobile unit itself.
The mobile plant offers a flexibility without the need for maintenance or components like diesel engines and tracks.
with a more permanent, fixed plant which can take months to complete. A solution that can be easily transported and erected on site immediately wins the day in such a scenario. This is particularly true for markets outside of South Africa where commercial quarries are generally few and far between, with borrow pit type of operations more prevalent.
Weir Minerals’ wheeled plants are available in various configurations, starting from primary crushing solutions comprising a hopper, a vibrating grizzly feeder and a jaw crusher, to secondary crushing and stations which consist of a vibrating screen and a cone crusher. To combine these solutions, one can use simple mobile conveyors to configure a plant that is capable of producing aggregates for various end-use requirements.
“More importantly, we utilise equipment that is within the dimensions and weights that can be accommodated on a multi-axle trailer,” she emphasises. “With that comes the limitation of the amount of mass that can be accommodated per axle, in addition to legal road limits on width and height. The machines that we use for our wheeled plants are in the 50 to 350 tonnes per hour (tph) range. Once you go bigger than that, the equipment gets too heavy, and the solution becomes more like a fixed plant.”
Commenting on some key features of the system, Masekwameng makes special mention of the unique hydraulic and mechanical deployment system which requires minimal truck-mounted cranage during site installation. Its purposefully designed hydraulic leg system raises the plant from wheels, levels it and installs main supporting legs without any cranes being required.
When in operation, the plant is supported by structural support legs with the operational load removed from wheels/axles and hydraulic lifts for working safety and structural stability, as well as having reduced noise and vibration. All connections are done with structural pins and bolted connections, resulting in seamless integration of all components. The unique positioning bogey system makes final site-placing of modular wheeled units and conveyors simple and efficient.
The modular primary jaw crushing units are fed directly with excavator or front-end loaders with optional hopper extension for direct dump truck feed. The jaw wheeled units include an integrated overband magnet system for removal of tramp metal. A surge hopper unit with an integrated belt feeder could be added in circuit to ensure proper choke feeding of cone crushers for optimal crushing quality and performance.
According to Masekwameng, one of the major benefits of wheeled plants is that they eliminate the complexity of having a diesel engine
as part of the unit as well as tracks which require additional maintenance over and above the crushers and screens themselves.
“With wheeled plants, our customers can focus their maintenance attention on equipment that is core to their operation –crushers and screens – as the availability of these machines is what earns them money. Wheeled plants can also be transported on the highway depending on the size and road regulations within the client’s jurisdiction. That means customers only need to hook the plant on to the back of a truck and off they go,” she says.
By their nature, wheeled plants are portable crushing and screening solutions with minimal civil requirements, which translates into both time-savings and reduced operational costs for customers.
These solutions can be transported on road with standard horse kingpin connection (South African road transport requirements) or containerised (subject to main equipment size) for shipping to remote sites where sea freight is more economical.
In addition, these plants are designed with safety in mind and ease of maintenance as the highest priority. Various crushing and screening wheeled plant modules seamlessly integrate together with the Weir Modular Conveyor System (WMCS), all powered from a central wheeled generator/master control wheeled unit, with cable racking and routing allowance already provided for.
“WMWP combines all the features and benefits of the robust Trio and Enduron range of equipment in an easy to deploy and relocate, complete crushing and screening solution,” says Masekwameng.
Masekwameng says, given that the sand and aggregates required for infrastructure development are generally high-volume, low-value products, it is difficult for contractors to factor in transportation costs for these materials and still turn a profit when crushing projects are far away from construction sites.
“As such, it becomes important for them to move around to where there is construction development. In our view, demand for solutions that can be easily transported and quickly mobilised is going to increase as the world turns to infrastructure development as a tool to foster economic recovery and development,” concludes Masekwameng. a
Different quarries need different cone crushers. Weir Minerals is the only global manufacturer that offers both. TRIO® live and xed shaft cone crushers are made for modern quarries with advanced hydraulics, wear resistant materials and the latest technology. You get what’s right for your circuit. No unnecessary redesigns needed. Plus, with a lifelong commitment from the Weir Minerals global network, we’ve got you covered. Visit info.global.weir/trio
In the quest for optimal operations, mines, quarries and their contracting counterparts are placing value on innovative solutions in crushing and screening technology. In an exclusive interview with Quarrying Africa, Astec Industries’ Casper Booyse and Ricardo Isaacs unpack some of the emerging trends in this market. By Munesu Shoko.
As part of the OneASTEC business model, Astec Industries Africa Middle East (AME) introduced the Astec range of mobile crushers and screens to the local market some two years ago. Speaking to Quarrying Africa , Casper Booyse, regional sales manager at Astec Industries AME, says there has been a gradual uptake of the range thus far, given the competitive nature of this market, particularly in southern Africa.
The company has already delivered two units in South Africa – a GT205 mobile screen and a GT125 mobile jaw crusher. The Astec GT205, a three-deck mobile screen, was successfully commissioned last year for Astec’s long-standing KwaZulu-Natalbased customer, Lizarox, where it has proven to be up to the task. The GT125 mobile jaw crusher has been deployed in a coal application in Mpumalanga.
In the Middle East, Astec Industries AME has delivered two more units – a GT125 mobile jaw crusher and a GT205 mobile screen. Ricardo Isaacs, regional sales manager at Astec AME, says the two machines were sold through Astec’s Saudi Arabia-based dealer, Al Rashed & Sons, and are hard at work at a project in Jeddah.
Commenting on some of the key trends observed during the past two years, Booyse says the mobile crushing and screening market in southern Africa is driven by two capacity ranges – the 200-250 tonnes per hour (tph) and the 400 tph-plus tonnage requirements.
As part of the OneASTEC business model, Astec Industries AME introduced the Astec range of mobile crushers and screens to the local market some two years ago
The company has already delivered two units in South Africa – a GT205 mobile screen and a GT125 mobile jaw crusher
In the past year, Astec Industries has observed an apparent shift towards the use of bigger crushing and screening machines
Another trend of note is the growing demand for dual powered or hybrid mobile crushing and screening solutions
With its GT range, Astec Industries AME is currently focused on the 200-250 tph market segment, targeting quarrying, mining, rental, demolition and recycling sectors
The 400 tph-plus tonnage requirements are mainly for the larger mining projects where high production volumes are the order of the day
The 200-250 tph is driven by contract crushing projects, mainly the borrow pit type ones for road projects. The 400 tphplus tonnage requirements are mainly for the larger mining projects where high production volumes are the order of the day.
Our extensive regional footprint is supported by a large parts stockholding worth millions of rands. Some of the major components, such as the jaw for the GT125 mobile jaw crusher, are built at our Johannesburg facility, which means parts are locally available.
“The 200-250 tph is driven by contract crushing projects, mainly the borrow pit type ones for road projects. The 400 tph-plus tonnage requirements are mainly for the larger mining projects where high production volumes are the order of the day,” explains Booyse.
With its GT (Global Track) range, which is manufactured at Astec’s Omagh, Northern Ireland facility, Astec Industries AME is currently focused on the 200-250 tph market segment, targeting quarrying, mining, rental, demolition and recycling sectors.
The available models in this range include the GT125 jaw crusher, the FT200 cone crusher, the GT440 horizontal shaft impactor (HSI) crusher, the GT165 scalping screen and the GT205 finishing screen. All the crushers are predominantly suited for the 200 tph market, while the screens play in the 300-400 tph market.
“The GT125 is a robust crusher that has proven its capabilities, especially in the United States. A major talking point is the class-leading 38 mm stroke as well as the 25% greater capacity than most of the competitor
models in this size class. The dynamically balanced, large flywheels reduce peak horsepower requirements and allow the machine to operate with a smaller 225-hp Cat C7 engine without sacrificing performance,” explains Isaacs.
The FT200 comes with Astec’s patented tramp metal removal system which protects the crusher from uncrushable material in the crushing chamber. The GT440 HSI is able to track and crush simultaneously, making it the ideal solution for reclaimed asphalt pavement (RAP) applications in road maintenance.
The GT205 comes as either a two-deck or three-deck screen with hydraulic angle adjustments. Astec also offers what it believes to be a unique proposition in mobile screening, a multi-frequency screen, which is basically a conventional screen at the top deck and a high frequency screen at the bottom deck.
The high frequency version screen, explains Isaacs, benefits from the high speeds of 3 800 to 4 200 revolutions per minute (rpm), whereas the conventional
screen runs at 800-900 rpm. The multi-frequency screen is ideally suited for removing clay and reducing the unwanted 75-micron material in the final product.
In the past year, says Booyse, there has been an apparent shift towards the use of bigger crushing and screening machines. This is largely because of the high tonnage requirements in the mining sector where contractors are looking for 350-400 tph mobile solutions.
While Astec AME currently has a specific focus on its GT range, the company can, however, offer the larger FT (Fast Track) range. Manufactured in the United States, the FT range is currently offered as special orders in Africa and Middle East.
However, in future, this range will also be manufactured in Northern Ireland to allow Astec to cater for the bigger machine requirements in the international market. In fact, in June last year, Astec Industries announced plans for a US$5-million factory expansion at its Omagh location in Northern Ireland to better serve growing market demands in the mobile crushing and screening industry. The announcement came a year after the original facility was built to support the increased demand for mobile crushing and screening solutions.
screened oversize material back to the cone crusher. The larger FT300 CC will be launched sometime this year, confirms Booyse.
“The requirement for crusher/screen combinations on one chassis is taking root in the market. This eliminates the need to invest in two machines, thus reducing capital expenditure for customers.
In addition, running one machine instead of two reduces operating costs from a fuel consumption, maintenance and site establishment perspective,” explains Booyse.
Another trend of note is the growing demand for dual powered or hybrid mobile crushing and screening solutions. The main driver behind this trend is the need to improve fuel efficiency and reduce CO 2 emissions.
Hybrid solutions are fitted with an electric-drive system, meaning they can be connected directly to the mains or be powered by an onboard diesel generator –the latter being the case when there is no access to the electricity grid.
On all its HSI crushers, Astec provides a hybrid option. “We have invested in research and development to fast-track the upgrading of other product groups in our crushing and screening range to hybrid variants. At this stage, we have dual power solutions only in our HSI range,” says Booyse.
In June last year, Astec Industries announced plans for a US$5-million factory expansion at its Omagh location in Northern Ireland to better serve growing market demands in the mobile crushing and screening industry
Customers in the region also place significant value on aftermarket support, which informs their buying decisions.
One of the emerging trends in the mobiles market is the requirement for cone crusher/screen combinations, essentially a cone crusher and a screen on one tracked chassis. Basically, the machines feature a detachable screen which is placed just before the crushing chamber, or alternatively, post the crushing chamber.
To cater for this market requirement, Astec offers its Closed Circuit (CC) model, the FT200 CC, which features a detachable screen and return conveyor which guides
This is an area in which Astec has invested significantly. The AME region is supported from the Johannesburg manufacturing facility. However, the company has recently appointed highly qualified dealers across the region to provide sales and service support to customers. Astec has a total of 12 dealer partners in Africa and Middle East, with some of them responsible for several countries in their territories.
One example is Unatrac, which is part of the Cairoheadquartered Mantrac Group, offering sales and support services for all of the equipment in Astec Industries’ Material Solutions division in Nigeria, Ghana, Sierra Leone, Liberia, Kenya, Tanzania, Uganda, Egypt, Iraq and the Ural and Volga regions in Russia. Meanwhile, French company Aramine is the official
dealer of Astec Material Solutions products in several strategic countries in West Africa (Mauritania, Mali, Senegal, Guinea, Ivory Coast, Burkina Faso, Benin, Togo and Niger) and the Maghreb (Algeria, Tunisia and Morocco).
In southern Africa, Astec AME has a direct-to-market approach in South Africa and has dealers in strategic countries such as Namibia, Zimbabwe and Zambia, among others. The company has recently appointed Elite Crushers & Hydraulics as its dedicated agent in
This follows hard on the heels of the recent appointment of Zinpro RDC SARL in the Democratic Republic of Congo (DRC).
“This extensive regional footprint is supported by a large parts stockholding worth millions of rands. Some of the major components, such as the jaw for the GT125 mobile jaw crusher, are built at our Johannesburg facility, which means parts are locally available. This is complemented by 24/7 parts personnel across the region,” concludes Isaacs. a
The Teichmann Group has deployed the Terex WC1150S and the WJ3042i on a crushing project in Namibia.
Following the official African launch last year, the Terex MPS WC1150S wheeled cone crusher and the updated WJ3042i wheeled jaw crusher have become a popular choice for contractors. A case in point is The Teichmann Group, which has deployed these models with great success on a crushing project in Namibia, producing sub-base and road stone products. By Munesu Shoko.
As part of its product expansion programme, Terex Mineral Processing Systems (Terex MPS) introduced the WC1150S cone crusher, a completely new addition to its wheeled crushing range last year. In addition, the company also unveiled the WJ3042i, an updated version of the WJ1175 wheeled jaw crusher.
The two crushers are available as standalone plants or as a multi-plant system with product conveyors for a complete crushing and screening plant. They are both suited to mining and quarrying environments.
The WC1150S and the WJ3042i can be easily set up for aggregates such as concrete and road stone, as well as
base materials.
Several units of these models are already hard at work at various sites across Africa. One of the first companies to take delivery of the WC1150S and the WJ3042i in Africa was The Teichmann Group. Delivered last year, the two machines are part of a plant deployed at a crushing project in Namibia, making sub-base and road stone material for a major road project in the country.
Established in 1995, The Teichmann Group is a dynamic group of companies boasting substantial expertise and experience in a wide range of construction services, mining and agricultural solutions. Its strategic geographical reach extends across Southern, Central and West Africa.
At the heart of the WC1150S is the 225-kW Terex TC1150 cone crusher with a modern, automated control system 3
The Teichmann Group now has three of the WJ3042i and WC1150S crushing plants operating at different sites in Africa
At the heart of the WC1150S is the 225-kW Terex TC1150 cone crusher and a 6’ x 20’ triple-deck screen.
Following their official launch in Africa in 2023, the Terex MPS WC1150S wheeled cone crusher and the updated WJ3042i wheeled jaw crusher have become a popular choice for contractors
One of the first companies to take delivery of the WC1150S and the WJ3042i in Africa was The Teichmann Group
The wheeled plant concept has offered Teichmann Group greater flexibility because of its ease of movement on and between job sites
For this particular deal, PX Equipment was able to deliver the new units, set them up and get product on the floor for The Teichmann Group in a very short time frame
“Our civil engineering companies specialise in construction projects of all sizes. We have experienced teams of qualified engineers and managers who are hands-on and prioritise safety. We offer cost-effective solutions and utilise innovative construction methods, technical expertise and value engineering to deliver successful projects,” says Gary Teichmann, Executive Chairman of The Teichmann Group.
Willem du Plooy, regional business development manager – Africa at Terex MPS, tells Quarrying Africa that the wheeled plant concept has offered The Teichmann Group greater flexibility because of its ease
“The application is a high-wear, tough granite rock, but the plant has performed exceptionally well, producing in-spec quality road products for the contractor. The Teichmann Group now has three of the WJ3042i and WC1150S crushing plants operating at different sites in Africa.
Willem du Plooy, regional business development manager – Africa at Terex MPS
of movement on and between job sites. Setup times are minimised, efficiency is increased and jobs are completed with ease.
In addition, says Du Plooy, the client was impressed by the short delivery time of the plant, especially given the urgent nature of the job. With its 225 kW Terex TC1150 cone crusher with a modern, automated control system, the WC1150S is providing optimal capacity and highquality products to The Teichmann Group.
“As the Terex MPS dealer network continues to grow throughout Africa, the majority of Terex MPS units are now available in stock. In fact, our dealers have already standardised on the WJ3042i and WC1150S. For this particular deal, PX Equipment was able to deliver the new units, set them up and get product on the floor for The Teichmann Group in a very short time frame,” says Du Plooy.
The Teichmann Group’s plant was originally set up with a vertical shaft impact (VSI) crusher in the circuit, but with the WC1150S’s special crushing action, which
provides high reduction and good product cubicity for the production of high-quality aggregate and sub-base materials, the client realised that there was no need for a VSI. Removing the VSI in the circuit resulted in a significant reduction in operating costs, especially given that a VSI by its very nature is an energy-hungry machine.
“The application is a high-wear, tough granite rock, but the plant has performed exceptionally well, producing in-spec quality road products for the contractor. The Teichmann Group now has three of the WJ3042i and WC1150S crushing plants operating at different sites in Africa,” says Du Plooy.
Du Plooy says the new crusher models are gaining quick traction in the market. More units are being commissioned in Africa, he says, proving that the new WJ3042i and WC1150S are quickly becoming the principal choice for contractors.
At the heart of the plant is the 225-kW Terex TC1150 cone crusher and a 6’ x 20’ triple-deck screen. A level sensor over the cone crusher regulates the feed to ensure the chamber is continually choke-fed, thus ensuring maximum production and liner life, as well as optimal product shape. The large onboard triple-deck screen allows for the production of sized products from a single plant.
Equipped with the Terex MPS JW42 jaw crusher and heavy-duty vibrating grizzly feeder, the Terex MPS WJ3042i delivers optimum production across various applications. The compact size, quick setup times, easy transport and simple maintenance make the Terex MPS WJ3042i ideal for quarrying, mining, demolition and recycling. The machine excels in tight spaces and can be effortlessly transported to different project sites, allowing clients to benefit from quick setup times to minimise downtime and maximise efficiency.
“With our ever-growing dealer network, Terex MPS is now able to support its customers in all of Africa, with main hubs and satellite offices in most parts of the continent. Aftermarket support is a key focus of our growth strategy in Africa and we have really fared well in that aspect as we continue to train and support new dealers in Africa,” he says.
Reiterating commitment to its dealers, last year Terex MPS hosted its first Africa Dealer Conference at its Terex MPS India facility, with distributors from Southern, Central, West and North Africa present, as well as those from the Islands of Africa. Following the success of the Africa Dealer Conference in 2023, the 2024 edition will be hosted in South Africa and possibly in Morocco in 2025.
The WC1150S cone-screen plant is a high-performance, medium-sized wheeled crushing and screening system.
“The WJ3042i’s chassis has been redesigned and upgraded to provide better overall access and the Terex MPS JW42 jaw crusher onboard has a new mounting system to reduce the stresses to the chassis while crushing,” says Du Plooy. In addition, the field kit with conveyors and surge bin has been redesigned to accommodate three possible standard layouts for the WJ3042i and WC1150S. The same field kit allows clients to set the plant up for direct all-in feed into the cone crusher or feed the screen directly, ensuring easy layout change as required for different crushing sites. All plants and conveyors are designed to fit in standard containers for easy transport. The entire system, complete with conveyors, can be transported in nine containers. Once on site, each assembled plant can be transported in a one-piece tow, while hydraulic screen lift and hydraulic support legs reduce the cranage and tools required for plant set-up and relocation.
Apart from the WJ3042i and WC1150S, Terex MPS offers the WC1000LS and WC1300 cone crusher models with fourdeck screens and the WV2000 wheeled VSI crusher with a four-deck screen. The wheeled range is complemented by the company’s United States-built portable plants, ranging from wheeled jaws, cones and impact crushers to a wide range of wheeled screening units.
“Terex MPS offers three different types of cone crushers in its range – the MVP series screw bowl, the TC series floating bowl and the TG series floating shaft cone crusher – all available in different sizes on a wheeled portable chassis to suit different customer preferences,” concludes Du Plooy. a
Cutaway of lowprofile ERC primary crusher showing the apron feeder.
For mines and quarries, competitiveness is key in every aspect of their operations. With that in mind, FLSmidth’s new Eccentric Roll Crusher (ERC) range places a particular design focus on increased efficiency and high throughput in primary crushing of hard rock.
By Munesu Shoko.50%
Due to its low profile, the ERC is particularly compact and robust, offering a lower construction height up to 50% lower than other hard rock primary crushers
40%
The integrated grizzly allows for efficient bypassing of fines, thus boosting crusher capacity, reducing energy consumption by up to 40%
7 000 tph
The innovative design with an integrated screen permits capacities of up to 7 000 tonnes per hour
As the first step in processing, primary crushing has a dramatic effect on overall production and ultimately the profitability of a quarry or mine in the long term. To help quarries and mines optimise their operations, FLSmidth has developed its ERC, a groundbreaking solution for the primary crushing of hard rock. The initial four-model range offers capacities from 550 to 7 000 tonnes per hour (tph).
Ideally suited for use in both underground and surface operations, the ERC is said to offer significantly higher efficiency and flexibility than any conventional crushers in the processing of hard rock. With its numerous benefits compared with conventional crushers, the ERC solves several problems that often occur in the first crushing stage.
Demitri Kokoroyanis, regional product line manager – Crushing & Screening, Sub-Saharan Africa, Middle East & South Asia Region (SSAMESA) at FLSmidth, tells Quarrying Africa that the ERC fits in between large jaw crushers and small to medium gyratory crushers, which
are both proven solutions for hard rock applications.
However, jaw and gyratory crushers require large installation heights, something that the ERC addresses with its lower construction height. The ERC patented crushing technology is significantly more compact than alternative primary crushing systems, making it ideal for mobile and semimobile in-pit crushing applications.
FLSmidth has already seen a great deal of interest from the mining industry, confirms Kokoroyanis. The company has sold several units in the market over the past four years, with some being installed in Laos, Asia, and others, it is hoped, soon in Angola.
“We also have clients who have expressed interest in this technology for underground applications, and hopefully the projects will soon gain traction and turn this interest into commercial deals,” he says.
Because of its nature, primary crushing of hard rock can quickly lead to high
wear and ultimately performance losses on the crushing equipment. To address this, the ERC’s roll is mounted eccentrically between the crushing chamber and the integrated screening chamber where the majority of the fines content of the feed material is screened out prior to the crushing chamber. This increases wear resistance, improves efficiency and achieves optimised crushing.
Fines are screened out by means of an integrated grizzly and bypassed through the crusher housing. The coarse particles are transferred into the crushing chamber. The eccentric shaft of the roll is axially guided by two sets of roller bearings and supported in the housing. The rotation of the drive motor is transmitted via a V-belt drive to the eccentric shaft. The inertia of the two flywheels accumulates crushing energy.
The rotating eccentric shaft generates the oscillating motion of the roll. Consequently, the crushing gap between the roll and the jaw in the crusher housing changes continuously. The coarser feed material is continuously crushed between the roll and the jaw as it falls by gravitation until it exits the crushing chamber at the bottom.
One of the key design features of the ERC is the compact, yet robust nature of the crusher. “Due to its low profile, the ERC is particularly compact and robust, offering a lower construction height up to 50% lower
“The innovative design with an integrated screen permits capacities of up to 7 000 tonnes per hour, representing up to 10% higher throughput at same product size compared to industrial benchmarks.
To help quarries and mines optimise their crushing operations, FLSmidth has developed its ERC, a groundbreaking solution for the primary crushing of hard rock
The ERC’s roll is mounted eccentrically between the crushing chamber and the integrated screening chamber to increase wear resistance, improve efficiency and achieve optimised crushing
A particularly effective energy of the oscillating roll with constant stroke in the entire crusher cavity allows for a higher reduction ratio and more effective use of crushing energy
Fines are screened out by means of an integrated grizzly and bypassed through the crusher housing
material
than other hard rock primary crushers. The compact design and a smaller number of components simplifies transportation, installation and maintenance, while reducing CAPEX costs by up to 10%,” explains Kokoroyanis.
Another prime design feature of the ERC is its crushing geometry with an integrated pre-screen. The integrated grizzly allows for efficient bypassing of fines, thus boosting crusher capacity, as well as reducing energy consumption by up to 40% and increasing liner life in the process. Bypassing fines also reduces the risk of compacting and overloading of the crushing chamber.
“The innovative design with an integrated screen permits capacities of up to 7 000 tph, representing up to 10% higher throughput at same product size compared to industrial benchmarks,” explains Kokoroyanis. “Large rocks are fractured at the opening of the jaw and three stages of crushing are executed as the material moves down the crushing chamber.”
Energy costs in the quarrying and mining industry are a significant portion of the overall annual spend. With the ERC crushing principle, quarry owners and mining houses can take back control of their energy spend. A particularly effective kinematic of the oscillating roll with constant stroke in the entire crusher cavity allows for a higher reduction ratio and more effective use of crushing energy. The reduction ratio of 1:10 potentially allows for elimination of secondary crushing stages, depending on the material’s characteristics.
In addition, the high moment of inertia of the roll and flywheels, says Kokoroyanis, contributes to accumulated crushing energy, reducing the power requirements and effectively compensating load peaks.
The ERC features an integrated automatic gap adjustment system. The ERC hydroset is a smart way of equipment protection and flexible machine setting. The patented, fully hydraulic gap setting/ retraction system for the jaw offers a wide range of gap setting options for safe and simple adjustment of product size, compensation of liner wear and release of tramp material or otherwise uncrushable material content.
“As part of the crushing chamber, the adjustable swing jaw enables the gap to be specifically adapted to suit a required product,” says Kokoroyanis. “The adjustment range of up to 220 mm is sufficient to offset wear on the crushing elements.”
The symmetrical arrangement of the roll allows the crusher to be balanced with great precision, thus significantly reducing machine vibrations and loads on surrounding structures, making the crusher ideal for mobile and semi-mobile crushing systems.
“Another special feature of the ERC is its ability to be deployed in underground applications, which place high demands on crushing technology in terms of compactness, mobility and maintenancefriendliness. The combination of the ERC’s features and benefits make it ideal for meeting these demands,” concludes Kokoroyanis. a
To expand its business in Africa, Bunting, a global leader in magnetic solutions, seeks to appoint capable distributors on the continent, with initial focus mainly on South Africa. However, the company is willing to consider opportunities in other regions as well. By Munesu Shoko.
Dubbed the ‘last frontier’ for economic growth, Africa is increasingly becoming an attractive destination for international companies seeking to expand their horizons. One such organisation is Bunting, a leading global magnets and magnetic equipment manufacturer for materials handling, magnetic separation and metal detection.
Bunting’s wide range of equipment features magnetic separation products, metal detection devices, custom magnets and
magnetic assemblies, in-stock neodymium magnets, and more.
Bunting has been a family-owned, familyoperated company since it was founded in Chicago, Illinois in 1959. In 1979, the company relocated its headquarters to Newton, Kansas, and has since branched out to establish multiple new locations in the United States and globally.
To date, Bunting has locations in Bunting-Elk Grove Village, Bunting-DuBois in the United States, as well as Bunting-Berkhamsted, Bunting-Redditch in the United Kingdom; Victoria, Australia; and Ningbo, China.
1959
Bunting has been a family-owned, family-operated company since it was founded in Chicago, Illinois in 1959
Sales manager Bradley Greenwood tells Quarrying Africa that the company seeks to appoint distributors in South Africa. “Our ideal partners would be existing suppliers of capital equipment – particularly crushers, screens and conveyors – to the mining and quarrying sectors in South Africa,” says Greenwood.
Africa, says Greenwood, is a strategic growth market for Bunting. The company sees huge potential and growth opportunities for its extensive line of magnetic solutions on the continent, especially in the extractive sector.
“We realise huge potential for growth and only see the market getting bigger on the back of a global shift towards a greener, electric world,” says Greenwood. The energy transition so critical to meeting the Paris Agreement is heavily dependent on green minerals. Countries such as the Democratic Republic of Congo (DRC) and South Africa are truly
185%
The Bunting ElectroMax overband magnetic separator is said to be 185% stronger and 25% lighter than equivalent permanent overband magnets
The ElectroMax overband magnet is a new product that is selling in huge quantities throughout Europe, the UK and the United States.
Bunting, a global leader in magnetic solutions, seeks to appoint capable distributors in Africa, with an initial focus mainly on South Africa
Bunting’s wide range of equipment features magnetic separation products, metal detection devices, custom magnets and magnetic assemblies, in-stock neodymium magnets, and more
Although the company has had a limited footprint in Africa, Bunting has already executed some flagship projects on the continent
Bunting believes that its ElectroMax and TN77 metal detectors, which prevent production downtime and save on costly process plant repairs, will drive the market in Africa
significant global players with substantial known reserves of green minerals in Africa.
Although the company has had a limited footprint in Africa, Bunting has already executed some flagship projects on the continent. Some of the major products supplied to date include disc separators, electromagnets and induced roll separators.
In Nigeria, the company has successfully installed two magnetic disc separators for processing coltan. The Nigerian mineral processor first contacted Bunting after viewing previously supplied magnetic disc separators operating successfully in other local coltan processing plants. Following a review of the project specification and subsequent recommendations by Bunting’s mineral application engineers, the Nigerian processor ordered two model MDS 3-375 magnetic disc separators.
In another project, Bunting supplied five high-intensity magnetic
separators for SODEX Mines in Nigeria. The mineral processing company specialises in the production of columbite concentrates that are used in the manufacture of superconductive alloys.
Prior to contacting Bunting, SODEX Mines was using old and outdated magnetic separators. Subsequently, the company was experiencing difficulties in upgrading its final product to meet the demands of its customers. With an increasing worldwide demand for its columbite, the company instigated a global search for the best mineral processing technology to improve quality and productivity.
SODEX Mines eventually ordered five high-intensity magnetic separators from Bunting, including three 3-stage high intensity magnetic disc separators and two 2-stage high intensity induced roll magnetic separators. All the magnetic separators were fitted with vibrating feeders to provide an even, steady flow of material into the separation zones.
Commenting on products that he believes will drive the market in Africa, Greenwood is excited about the ElectroMax and TN77 metal detectors, which prevent production downtime and save on costly process plant repairs.
where there are weight and size limitations. It provides additional magnetic power for more difficult tramp metal separation applications, achieving a boosted separation force while remaining compact and light,” explains Greenwood.
The electromagnetic coil produces a high gradient magnetic field that is up to 250% more powerful than comparable equipment. This enables the removal and separation of smaller and more challenging shapes of iron contaminants often missed by other magnetic separation systems. The additional magnetic strength also aids the lifting and removal of heavier tramp ferrous metals; these traits are particularly desirable for customers in industries such as the mobile crusher market.
Five standard models are designed for suspension at a height of 35-55 cm over conveyors with widths of 1 m, 1,2 m, 1,4 m, 1,5 m and 1,8 m across the transfer material belts.
Bunting’s TN77 conveyor belt metal detectors allow customers in the mining, aggregates, and mineral industries to effectively detect ferrous and manganese metal contamination from their product flow in order to purify their product and protect other process equipment downstream in their facilities.
Customers usually have three main concerns associated with installing a new piece of metal detector equipment into their facility. These concerns include the price of cost versus return associated with the purchase and installation of new equipment, the equipment’s ease of installation, and how much support they will receive from the company from whom they are purchasing.
250%
The ElectroMax is a new product that is selling in huge quantities throughout Europe, the UK and the United States. It is ideal for distributors to hold and sell from stock. The Bunting ElectroMax overband magnetic separator is said to be 185% stronger and 25% lighter than equivalent permanent overband magnets.
Ideal for applications in the recycling, aggregates, minerals and mining industries, Bunting’s new ElectroMax provides customers with a smaller, lighter and more compact system without any compromise in separation performance. The low-profile, air-cooled electromagnetic conveyor meets the ever-increasing demand for highpowered, light and compact electromagnets.
“The ElectroMax is ideally suited for any application
“Bunting’s TN77 metal detector addresses all these concerns with ease. The TN77 pays for itself with the first piece of tramp metal it detects – the cost of expensive repairs associated with the damages tramp metal can cause far exceeds the cost of investing in TN77 metal detectors,” explains Greenwood. Installing the TN77 is simple and fast, taking less than one day with no need to remove the belt of the existing conveyor. The design of this metal detector means that it easily fits onto customers’ existing conveyors, allowing material to pass beneath it with ample clearance.
“In addition to these two products, Bunting also offers permanent overband or suspension magnets, metal detectors, electromagnets, eddy current separators and a whole range of mineral separation equipment,” concludes Greenwood. a
For more information on dealer partnership opportunities, get in touch with Bradley Greenwood: bgreenwood@buntingmagnetics.com
Over the years, Powerstar has become the jewel of the construction tipper truck market in South Africa, establishing itself as a market leader in that segment.
Having established itself as a household name in the South African tipper truck market, Powerstar, under the stewardship of Ever Star Industries (ESI), has in recent years seen expanded growth in cross-border markets. To unlock the next wave of cross-border success, ESI has fortified its aftermarket regime with a strong dealer footprint across southern Africa. By Munesu Shoko.
Since taking over the local distribution of Powerstar back in 2010, Ever Star Industries has put the brand on a continuous growth trajectory. The Powerstar brand made its local debut as far back as 2006 under the distributorship of Super Group at the time.
During the early days, completely built units were shipped into the country, before ESI started assembling locally at its production facility in Pietermaritzburg, KwaZulu-Natal, in 2007. In 2010, ESI took over the sales and support duties of the brand in southern Africa, ushering in a period of constant growth for the brand.
Over the years, Powerstar has become the jewel of the construction tipper truck market in South Africa, establishing itself as a market leader in that segment. The South African dominance has been replicated in cross-border countries such as Zimbabwe, Mozambique, Botswana, Zambia and
Namibia. More recently, Zambia and the Democratic Republic of Congo (DRC) have been added to that ever-growing list.
Rodney Selesnick, senior head of sales at ESI, says the company currently ships out about 800 trucks per year, which is close to capacity for its current infrastructure. Of this number, between 200 and 300 units are destined for cross-border markets every year. Given the increased demand, Selesnick says there are plans to increase the capacity of the assembly plant to 1 500 units per year to cope with the growth in southern Africa.
“In recent years, the challenge has shifted from finding customers, to stock availability. To provide context, our next three semi-knocked-down (SKD) shipments for tippers and water tankers have already been sold out before they have arrived. One of our cross-border clients who runs in excess of 200 Powerstar trucks has just placed an order for 30 more units. Our dealers are doing extremely well, with
Ever Star Industries currently ships out about 800 trucks per year, which is close to capacity for its current infrastructure at its assembly plant
Over the years, Powerstar has become the jewel of the construction tipper truck market in South Africa, establishing itself as a market leader in that segment
The South African dominance has been replicated in cross-border countries such as Zimbabwe, Mozambique, Botswana, Zambia and Namibia
As part of its growth strategy in southern Africa, the company has invested heavily in its dealer partners across the region
The favourable price point, complemented by the proven lower total cost of ownership, is another major success driver of the Powerstar range in southern Africa
hardly any stock on the ground due to the high demand,” explains Selesnick.
One of the growth pillars of the Powerstar truck has always been the strong aftermarket regime created by ESI. As part of its growth strategy in southern Africa, the company has invested heavily in its dealer and business partners across the region. In Namibia, ESI has two dealer partners which, according to Selesnick, are doing very well. The same goes for Botswana, where the single dealer appointed to look
Of the 800 annual truck sales, between 200 and 300 units are destined for cross-border markets
“In recent years, the challenge has shifted from finding customers, to stock availability. To provide context, our next three semi-knocked-down shipments for tippers and water tankers have already been sold out before they have arrived.
after that market is gradually growing its sales.
In Mozambique, ESI has a dedicated sales dealer and a separate service dealer. The Eswatini dealer takes care of both sales and service of the range, while Lesotho, currently a small market, is supported by ESI’s existing dealer in the Free State, South Africa. The Zambian dealer, and the DRC dealer, are both part of the same group, and while the DRC has, and is plagued, by conflict, political upheaval, and instability, it is showing signs of renewed energy and growth. Following the introduction of lefthand derivatives in its offering, ESI can now offer its Powerstar range to the DRC market. Zimbabwe, supported by an extremely capable dealer, has been one of the more exciting markets in recent years. To provide context, between 2015 and 2016, Zimbabwe
only accounted for about 12 to 16 units per year. In 2023, a whopping 150 units were sold into this market. Over and above the spectacular product range lies an unrivalled aftersales support, which has been key to the Zimbabwean growth.
“Traditionally, a big challenge in cross-border markets such as Zimbabwe has always been the influx of used truck imports from, for example, the UK,” says Selesnick. “However, the situation has changed dramatically in recent years, with imports falling away due to the unavailability of spares, support and higher costs.”
In addition, the government of Zimbabwe appointed Bureau Veritas in 2016 to conduct pre-shipment assessment in order to ensure that all listed imported products, such as pre-used trucks, meet quality, safety, health and environmental standards in line with the World Trade Organisation agreements. A lot of direct imports from foreign countries have struggled to meet these requirements.
ESI, confirms Selesnick, has already been issued with its Certificate of Conformity by Bureau Veritas.
“By introducing the Consignment Based Conformity Assessment, the Zimbabwean government has successfully stopped the importation of delinquent, nonquality products into the country,” he says.
One of the major growth pillars of the Powerstar range in southern Africa is the tough nature of the product. Most of the operators running the Powerstar, says Selesnick, have realised that the truck is rugged, giving them three to four lifecycles, even in arduous applications such as construction and mining.
The favourable price point, complemented by the proven lower total cost of ownership (TCO), is another major success driver of the Powerstar range in southern Africa. To provide context, says Selesnick, an injector for
the 2628 or 4042 8x4 truck costs around R600, while a new engine for a Powerstar truck is in the region of R130 000, and a gearbox is around R70 000. These components have proved to provide several lifecycles for the truck. For example, ESI has tracked some engines in tippers and water tankers that have already clocked over 1-million km, and counting.
“Our secret to success is, however, not only due to the quality and the price point of the truck, but also the huge investment we have made in parts and aftermarket service. At any given time, our parts stockholding is greater than R120-million, housed in three big warehouses, of which two were recently acquired, and situated close to our Pietermaritzburg assembly plant,” says Selesnick.
One of the growth pillars in southern Africa is the lean structure at ESI, which allows for quick decision-making. For example, in his cross-border team, Selesnick has four people who are responsible for the sales targets of 300-400 units per year, representing 40% of ESI’s annual truck sales.
In terms of the range, Selesnick says ESI has not changed the blueprint for its success and has for years kept its tried and trusted product offering. The range starts with the 2628 series, which is offered standard in tipper form with a short wheelbase. A long wheelbase option is available, which can be fitted with a conventional dropside. A 2628 concrete mixer is also available.
The 1627 can undertake several roles – it has been used as a military support vehicle, a water tanker, a tipper, container carrier and dropside. It is a 4x4 truly designed for tough African conditions, says Selesnick.
The 3335, which comes as a long wheelbase truck, is suited for mining operations, where it can be deployed to carry high-density materials such as chrome. The 8x4 version of the 3335 is a multi-role truck which can be deployed as a tipper, water tanker and drill rig carrier. In fact, it is highly preferred in drill rig applications because of the heavy nature of the machinery it has to carry, the added benefit of dual turning axles, and the availability of sufficient engine power for the task at hand.
“The 2642 is a well-priced truck tractor which can do just about anything. It is cost-effective in terms of both the price and maintenance cost. It is used extensively in crossborder markets because of the poor state of roads in many of those countries. In terms of application, it is ideally suited for side tipping, and for example in coal, and other relevant mining sectors. We have also engineered a special long wheelbase for carrying bricks, an application where high horsepower is a necessity,” he says. “Depending on seasons, the best sellers are the 2628, the 2642 truck tractor and the 3335 8x4.”
Commenting on the outlook of the business this year, Selesnick says ESI has done its homework and 2024 is going to be a year of satisfying customer needs and focusing on internal processes to improve production. “We are incredibly happy with the robust dealer network we have in all markets. We have in the past two years invested in training – both technical and sales. A skilled workforce is essential for our future success,” concludes Selesnick. a
For effective feed control, the mass flow of the conveyed bulk material must be measured.
As digital transformation in the extractive industry continues apace, the role of measuring devices cannot be stated enough. Sensors are the starting point for digitalisation as they are the point at which data is created. It is therefore important that the measurement technology used to control and monitor processes at quarries and mines is fit for purpose. By Munesu Shoko.
As quarrying and mining operations continue to drive their digitalisation efforts in the quest to enhance operational efficiency and increase productivity, it is important to remember that sensors are the basis for success in digitalisation and automation.
In a one-on-one with Quarrying Africa, Clint Viviers, technical product specialist at VEGA Instruments SA, a leading sensor and measuring instrument manufacturer, says the point of measurement is where process control starts. Without measuring devices, says Viviers, trends such as digitalisation and automation would not be possible.
“Before automation came to the fore, manual systems were the order of the day. Operators, for example, would open and close valves, start and
stop pumps and conveyors manually,” says Viviers.
“With the advent of automation, manual processes are a thing of the past. However, it is important to remember that measuring devices are a major part of the automation journey. Given that digitalisation and automation offerings are generally reliant on sensors, the first step for quarries and mines is to ensure that they have reliable measuring devices.”
In the instrumentation world, there are several technologies available, including level and pressure transmitters, as well as nucleonics, flowmeters and analytical, amongst others. However, VEGA specialises in a smaller basket of these technologies – level, pressure and nucleonics – which has allowed the company to be at the forefront of cutting-edge
1 000
The measuring ranges of pressure transmitters from VEGA start at a few millibar and extend to extreme pressures up to 1 000 bar
Without measuring devices, trends such as digitalisation and automation would not be possible.
As quarrying and mining operations continue to drive their digitalisation efforts, sensors are the basis for success
VEGA is one of the leading manufacturers of level measurement technology in the world, mainly for solid material applications
VEGA’s pressure measuring techniques can be used to measure not only process or differential pressure, but also level, volume, density or mass flow in all areas of process technology
In the quarrying environment, VEGA’s non-contact sensors can be used for level measurement and point level detection in crushers and for level measurement of stockpiles
advancements in its chosen domain.
In fact, VEGA is one of the leading manufacturers of level measurement technology in the world, mainly for solid material applications. However, the company also offers liquid measurement solutions, for example, level detection in water tanks used for dust suppression at quarries.
VEGA’s pressure measuring techniques can be used to measure not only process or differential pressure, but also level, volume, density or mass flow in all areas of process technology. The measuring ranges of pressure transmitters start at a few millibar and extend to extreme pressures up to 1 000 bar. Different measuring cells are used in these pressure instruments.
VEGA offers a wide range of nucleonic level detectors. The product range includes radiation-based sensors for continuous level measurement, radiation-based sensors
±2 mm
With an accuracy of up to ±2 mm, customers can trust non-contact radar level sensors to consistently provide accurate measurements
“Given that digitalisation and automation offerings are generally reliant on sensors, the first step for quarries and mines is to ensure that they have reliable measuring devices.
for density measurement and radiation-based sensors for mass flow determination.
In addition, there are various communication protocols for integrating these measuring devices into process control systems. The 4 to 20 mA signal, says Viviers, is the most common protocol used for communication between the measuring devices and a programmable logic controller (PLC). Other communication protocols include the HART Protocol, one of the first ever to be developed, as well as the Profibus, Foundation Fieldbus and Modbus.
“We also offer a wireless communication protocol in instances where measuring points are remote or where it is difficult to run cables due to a difficult access to a measuring point in the plant, for example. In addition, copper cable theft is a concern in our local market, thus mines often opt for wireless options,” explains Viviers.
While VEGA offers a wide range of cutting-edge measurement solutions, Viviers believes that the company’s non-contact radar level sensors have revolutionised level measurement in industrial processes.
In non-contact level measurement with radar, the sensor sends microwave signals towards the medium from above. The surface of the medium reflects the signals back in the direction of the sensor. Using the received microwave signals, the sensor determines the distance to the product surface and calculates the level from it. Liquids and solids are commonly measured with this measuring technique.
“What sets these sensors apart is their noncontact measurement technique. Unlike traditional measurement methods, such as float switches or magnetostrictive sensors, VEGA’s radar sensors do not come in direct contact with the process medium. This eliminates the risk of sensor wear, clogging, or deterioration, ensuring long-term reliability and reducing maintenance costs,” explains Viviers.
One of the primary advantages of VEGA’s noncontact radar level sensors is their exceptional accuracy and reliability. These sensors employ cutting-edge technology that allows them to overcome challenges posed by erratic process conditions, such as temperature variations, foam, or dust. With an accuracy of up to ±2 mm, customers can trust these sensors to consistently provide accurate measurements.
VEGA’s non-contact radar level sensors incorporate advanced signal processing capabilities that allow them to filter out interferences caused by noise and dust. This ensures that level measurements are precise and accurate, even in the presence of obstacles. Additionally, these sensors can also automatically compensate for heavy build-up on the sensor antenna, thanks to the software capabilities.
In the quarrying environment, VEGA’s non-contact sensors can be used for level measurement and point
level detection in crushers and for level measurement of stockpiles. Rock crushing is a very demanding operation. The extremely noisy and dusty conditions inside a rock crusher make it difficult to obtain reliable, accurate readings with ultrasonic or laser level sensors, which are better suited to other applications. With solutions such as the VEGAPULS 6X non-contact radar sensor, quarries can ensure reliable level measurement in the crusher, unaffected by strong dust generation and noise.
The VEGAPULS 6X new radar level sensor combines the best of the previous 80 GHz, 26 GHz and 6 GHz sensors, such as VEGAPULS 64 and VEGAPULS 69, in one device. One of the most important innovations in the VEGAPULS 6X is its radar chip, designed and developed by VEGA. At the sensor’s heart is the pulsating technology that empowers it to fulfil the high expectations in terms of precision and reliability. This is mainly thanks to its ability to self-diagnose during operation, which makes it possible to monitor the accuracy and performance of the sensor seamlessly and continually.
As a sensor and measuring instrument manufacturer, VEGA has been developing innovative measurement technology for over 60 years and is represented in over 80 countries by subsidiaries and sales partners. For nearly 30 years, the South African subsidiary has established a wide sales footprint in all major mining destinations across Africa. a
“One of our key strengths is our closeness to our customers. While most of the cross-border countries such as Botswana, Mozambique, Zimbabwe and Botswana are supported from our South African headquarters, we have dedicated personnel in markets further north, such as Nigeria, Côte d’Ivoire and the Democratic Republic of Congo (DRC), amongst others. In future, the plan is to at least have dedicated personnel in each African country within our jurisdiction,” concludes Viviers. a
Like many other segments of the mining value chain, drilling and blasting techniques have over the years become more and more technical. This, says James R Linton, national product manager – FRD & RT Drills at ELB Equipment, has required that drill rigs become more efficient, faster, reliable and low-maintenance to cope with the higher demands of production. By
Munesu Shoko.
Mines and quarries are under extreme pressure to increase output while lowering input in order to remain profitable. One area where this is apparent is in drilling and blasting. Drilling, in particular, is the first unit operation that has a significant bearing on other downstream functions in the mining value chain.
Modern drilling operations are defined by efficiency and reliability, two factors that are fundamental in reducing operational costs and maximising productivity. Consequently, the utilisation of innovative drilling technologies holds the promise for efficient and productive operations.
According to Linton, drilling and blasting techniques have become increasingly technical over the past 35 years, calling for the constant evolution of drilling technology to meet customers’ ever-growing and changing requirements in the quarrying and mining sector at large.
“Furukawa Rock Drills (FRD) is on a continuous quest to upgrade its equipment to meet the performance, safety and efficient operation procedures required in the marketplace, with a large emphasis on ergonomics and ease of operation,” explains Linton. The range is distributed by ELB Equipment in southern Africa.
The close cooperation between the Japanese original equipment manufacturer (OEM) and its
8,5%
By selecting the appropriate engine speed according to the rock quality, the Intelligent Drilling System helps reduce fuel consumption by up to 8,5%
Drilling and blasting techniques have become increasingly technical over the past 35 years, calling for the constant evolution of drilling technology to meet customers’ ever-growing and changing requirements
Furukawa Rock Drills is on a continuous quest to upgrade its equipment to meet the performance, safety and efficient operation procedures required in the marketplace
The FRD HCRL100-E3 is a radical upgrade of the previous FRD HCR 1500 ED-II model, which had become popular among mining, quarrying and construction contractors across southern Africa
The Intelligent Drilling System, FRD’s semi-automatic drilling control which automatically provides for optimal drilling conditions according to changes in rock quality
southern African representative has culminated in the development of products that speak directly to the local clientele’s requirements. A case in point is the all-new FRD HCRL100-E3 crawler drill launched in August 2023 to drive down the cost of drilling in southern Africa. The raft of changes on this model was informed by customer input and feedback from FRD’s longtime distribution partner, ELB Equipment.
“The latest adaptations are the culmination of decades of successful operations in the field, in Africa, which has allowed FRD to continue fine-tuning its offering for even better performance, speed and cost-per-metre drilled,” says Linton.
The FRD HCRL100-E3 is a radical upgrade of the previous FRD HCR 1500 ED-II model, which had become popular among mining, quarrying and construction contractors across southern Africa. The launch of the FRD HCRL100-E3 late last year ushered in a new era in economic drilling in southern Africa.
Linton makes special mention of the Intelligent Drilling System (iDS), FRD’s semi-automatic drilling control which automatically provides for optimal drilling conditions according to changes in rock quality. This results in smoother drilling, reduced hole deviation (a major factor in production efficiency) and extension of the service life of drilling accessories. With the iDS engaged, the drill will only use as much power as is needed to save fuel and minimise unnecessary wear and tear on the system.
23 m/h
In a chrome application where the ore dips at around 12 degrees, sometimes at a depth of 20 m, the HCRL100-E3 is cutting at 23 m/hour with a 127 mm drill bit
“Furukawa Rock Drills is on a continuous quest to upgrade its equipment to meet the performance, safety and efficient operation procedures required in the marketplace, with a large emphasis on ergonomics and ease of operation.
The iDS is complemented by the power-saving mode on the new 280-kW Caterpillar C9.3 engine with an auto idle feature which provides economical fuel consumption. With the Super Economy Mode PLUS fuel-saving technology, the engine speed during drilling (impact and blow operation) can be selected from four levels: 1 600, 1 800, 2 000 and 22 00 rpm.
By selecting the appropriate engine speed according to the rock quality, this patented fuel-saving technology contributes to improved fuel efficiency while maintaining impact performance. This reduces fuel consumption by up to 8,5% and enables more power to be channelled towards increased speed and more metres drilled per shift with drill bits up to 127mm diameter.
The dual damper mechanism and wedge-shaped piston
The FRD HCRL100-E3 is a radical upgrade of the previous FRD HCR 1500 ED-II model, which had become popular among mining, quarrying and construction contractors across southern Africa.
shape, with extreme energy transfer efficiency, enable quick response to a wide range of different rock types. High crushing efficiency is achieved by optimal control according to the load. No complicated operation is required, and stable and comfortable drilling is possible with no wasted power.
The dual damper mechanism (shock absorber with special structure) presses the bit against the bedrock in order to reliably transfer the energy of the impact wave of the impact piston to the bit. This causes crushing of the bedrock, and enabling drilling with the proper thrust force.
least two more units into the market by August 2024,” he says.
Equipment has put four FRD
Since its launch in August 2023, the HCRL100-E3 has been well received by customers in southern Africa. ELB Equipment, confirms Linton, has already put four units into the market, with the fifth unit currently being prepared for commissioning at a fluorspar mine in Limpopo. “We anticipate deploying at
Of the four units already in the field, three are working in chrome applications in the North West Province of South Africa, while the remaining unit is running at a large bridge construction application. “The performance of the HCRL100-E3 in the chrome application has been astounding. Here, the ore dips at around 12 degrees, sometimes at a depth of 20 m. The HCRL100-E3 is cutting at 23 m/hour with a 127 mm drill bit,” explains Linton.
Apart from the FRD HCRL100-E3, ELB Equipment offers FRD’s full range of drill rigs catering for the mining and construction industries from start-up and production to geotechnical applications. These range from pneumatic crawler drills to hydraulic top hammer and medium range down-the-hole (DTH) crawler drills. “In fact, FRD has a unit for every rock drilling application,” concludes Linton. a
QA/QC is one the most important, if not principal, factors in successful blast outcomes at any opencast mine.
After nearly five years of operation, ERG Industrial, a specialist in blast optimisation for quarries and mines, has made key observations in blasting processes. Of note, MD Eugene Preis tells Quarrying Africa, is that mines and quarries are ‘leaving money on the table’ by neglecting blasting basics such as quality assurance and quality control (QA/QC). By Munesu Shoko.
Established in July 2019, ERG Industrial has over the past five years changed the face of blasting, a critical parameter in the quarrying and mining value chain. Reflecting on the journey thus far, Preis says the past five years have been a learning curve for the company.
Commenting on some key observations made during that time, Preis says one that quickly comes to mind is the lack of proper QA/QC procedures in both the mining and quarrying sectors, which has led to the introduction of a new
consulting division within ERG Industrial.
“QA/QC is one the most important, if not principal, factors in successful blast outcomes at any opencast mine,” he says. “By neglecting this basic function in their blasting processes, quarries and mines are ‘leaving money on the table’ – a hefty amount of money for that matter.”
This, he says, is true for some of the biggest mines in South Africa. At one of the flagship mines in the country, ERG Industrial discovered that compliance to charge heights was only 8%. Only 8% of the holes were within an “acceptable”
8%
At one of the flagship mines in the country, ERG Industrial discovered that compliance to charge heights was only 8%
QA/QC is one the most important, if not principal, factors in successful blast outcomes at any opencast mine
By neglecting this basic function in their blasting processes, quarries and mines are ‘leaving money on the table’
To help mines and quarries improve their QA/QC, ERG Industrial has developed a Drill and Blast Gap Analysis tool to investigate every aspect of the drill and blast value chain
ERG Industrial has observed a growing understanding of the value of energy confinement in blasting
deviation of 10% and the rest were massively overcharged or undercharged – a recipe for poor blast outcomes.
To help mines and quarries improve their QA/QC, ERG Industrial has developed a Drill and Blast Gap Analysis tool which allows the team to investigate every single aspect of the drill and blast value chain in order to unearth any potential issues and facilitate continuous improvement. “We use the gap analysis tool to identify opportunities to make small improvements that have the potential to achieve massive outcomes,” says Preis.
Using this method, ERG Industrial has changed the fortunes of a quarry that was previously struggling with poor blast outcomes. “The first thing we did was to ask to be involved in the whole process, from the staking out of the block for drilling, to the firing of the blast to observe their QA/QC,” says Preis.
On the first blast, ERG Industrial discovered some massive discrepancies. For example, the stemming length was supposed to be 3 m as per the blast design, but only 30% of the holes were within the acceptable
3 m
At one of the quarries, the stemming length was supposed to be 3 m as per the blast design, but only 30% of the holes were within the acceptable 10% deviation
“QA/QC is one the most important, if not principal, factors in successful blast outcomes at any opencast mine. By neglecting this basic function in their blasting processes, quarries and mines are ‘leaving money on the table’ – a hefty amount of money for that matter.
10% deviation. There was also a massive discrepancy between the stipulated hole depth and what the contractor had drilled. After presenting these findings to both the quarry owner and the blasting contractor, an action plan and related key performance indicators (KPIs) were drawn up for the next blast, imposing at least a 5% deviation on all parameters.
“The next blast went much better than the first one,” says Preis. “By continuously identifying opportunities for continuous improvement, the third blast was the best ever in the history of the quarry. Bear in mind that this was achieved by not changing the blast design, but just the extra attention to QA/QC. We advised the contractor to take at least a day extra, for example, to drill the block and then measure to ensure that every hole is of the correct depth,” explains Preis.
After these QA/QC initiatives, the quarry has no need for a pecker anymore, even on a 500-hole blasting block. The key takeaway here is that operations can unleash massive gains by prioritising QA/QC without spending a cent more on their blasting budget. In the quarrying industry, oversize is the ‘devil’ because the objective is to crush material as fine as possible. You can imagine the cost implications of setting off a blast and then have a pecker 24/7 to deal with the boulders.
“Operations can add value by putting a ‘magnifying glass’ on their processes and the execution of blasts. I have always said, especially with regard to quarries, if you really want to see improvements, forget about the fancy technology. Go back to basics, get your house in order and develop your KPIs for your contractors around QA/QC. Even appointing someone in-house to manage this aspect would not be as costly as the losses incurred through poor blasts,” says Preis.
Another key observation, says Preis, is that most operations have moved from pyrotechnic to electronic blasting systems. However, he says, the majority of these operations are not capitalising on the full potential of the electronic systems.
One of the major benefits and a principal reason for adopting electronic blasting systems is the flexibility of timing. Unlike the traditional shock tube solutions, electronic blasting systems allow blasting contractors to be creative with timing.
With electronics, he says, it is a blank page, i.e. one can choose one’s own timing, even at an individual hole level. Despite this obvious flexibility, more than
half of the sites that use electronics are still using shock tube timing.
“They deploy electronic blasting technology –which is generally up to five times the cost of shock tube – but they are still timing it the shock tube way. That is mainly because of the lack of knowledge and experience with the new technology,” he says.
Preis has also observed a growing understanding of the value of energy confinement in blasting, with many in the industry realising that stemming should not be an afterthought. In blasting, he says, energy follows the path of least resistance and, in most cases, it is right up and out the blasthole. Good stemming therefore creates more resistance at the top of the blast hole and directs the energy to where it is needed – the rock mass.
“We do see a trend where people are starting to focus more on energy confinement in blasts. Several operations are now paying more attention to the quality of their stemming and realise that it is not just a matter of throwing any material in the hole to resist the force,” he says. “The knock-on effect of better energy containment is significant. On the health and safety side, there is a marked reduction in flyrock, noise and airblast. From a productivity point of view, there is an improvement in fragmentation. Good stemming is thus a principle of creating better resistance in the blast hole, leading to a range of benefits.”
Another trend of note, says Preis, is the change in behaviour by suppliers to the mining sector, particularly
relating to explosives providers. Some five years ago, he says, many of the explosive suppliers were prioritising volume over value. The KPI for the explosive provider’s site manager, for example, was to push certain tonnes of product per month.
“In recent years we have seen a shift from that attitude. Explosive suppliers are now driven by the need to create value for the customer, not only pushing volumes. It is true not just for explosive providers, but all the other suppliers in the mining value chain. Creating value for the client has become important. There is this apparent shift from pushing volumes to pushing value. That is the narrative we have always created with our own business from the very start – we are not in it to make a quick buck, but we are there to offer value to our clients for the long haul,”
A Lintec UCP90 Concrete Batching Plant supplied to a Mali-based contractor.
Lintec & Linnhoff will be exhibiting at the upcoming Big 5 Construct South Africa in June. Tony Chakra, Regional Sales Manager, Middle East and Africa, tells Quarrying Africa that the company’s presence at what is dubbed the ‘largest construction exhibition in South Africa’ is testimony to the significance it places on the African market. By Munesu Shoko
The African continent is a key region for Lintec & Linnhoff, a global leader in asphalt mixing and concrete batching plants, representing one of the company’s largest markets. Highlighting the growth prospects in Africa, Chakra refers to Mordor Intelligence’s report, which notes that the African Construction Market size is valued at US$58,42-billion in 2024 and is expected to reach USD74,81-billion by 2029, growing at a CAGR of 5,07%.
With that in mind, he says, Lintec & Linnhoff remains firmly committed to the region and will continue to listen and respond to the needs of its customers by providing industry-leading solutions that offer exceptional solutions for infrastructure projects in African countries.
Lintec & Linnhoff asphalt mixing and concrete batching plants are already hard at work in several countries in Africa, thanks to the company’s reputation as a global leader in the manufacturing of construction equipment solutions, as well as pre-
The Africa Construction Market size is valued at US$58,42-billion in 2024 and is expected to reach USD74,81-billion by 2029, growing at a CAGR of 5,07%
A Lintec CSD2500B containerised asphalt-mixing plant produced hot mix asphalt for surfacing work on a 14,2-km highway construction project in Abidjan, Côte d’Ivoire.
The Lintec CDP series of continuous asphalt-mixing plants ranges from 30-160 tph
Lintec & Linnhoff’s presence at this year’s Big 5 Construct South Africa is testament to the importance it places on the African market
In recent years, Lintec & Linnhoff has expanded its business in multiple markets in Africa. To date, the company is well-represented across the continent through dealership agreements with partners in Egypt and Nigeria
At the Big 5 Construct South Africa in June this year, Lintec & Linnhoff will be promoting its popular range of Linnhoff TSD, Linnhoff NVX, Lintec CDP and Lintec CSD models
Judging by the feedback from customers, African markets require mobility, thus small- to mediumsized asphalt and concrete batching plants are best suited for infrastructure projects across the continent
and after-sales customer service.
The company’s presence at Big 5 Construct South Africa, which will take place from 4-6 June 2024 at the Gallagher Convention Centre in Johannesburg, is testament to the importance it places on the African market, says Chakra.
“The exhibition plays a key role in allowing us to strengthen our connection with our customers in their home markets. Our customer relationships are built on quality, trust and service, with the exhibition serving as a platform to engage in conversations that help us understand our customers’ needs and help them to improve their operations,” he says.
In recent years, Lintec & Linnhoff has expanded its business in multiple markets in Africa. To date, the company is well-represented across the continent through 5,07%
distribution partners in countries like Egypt, Ethopia, Kenya and Nigeria. Chakra shares that there are also plans to further expand the distributor network this year.
Lintec & Linnhoff’s asphalt mixing and concrete batching plants have to date completed many major construction projects across Africa. A case in point is in Gabon, where the Lintec CDP12001M continuous asphalt-mixing plant supported the construction of a municipal project producing 100-120 tonnes (t) of hot mix asphalt per hour. In Côte d’Ivoire, a Lintec CSD2500B containerised asphalt-mixing plant produced hot mix asphalt for surfacing work on a 14,2-km highway construction project in Abidjan.
In Madagascar, a Lintec UCP60 concrete batching plant has been used by a Japanese contractor for the redevelopment of the Toamasina Port project. In Mali, a Lintec UCP90 supplied high-quality concrete to local contractors to support the nationwide push to increase public housing construction.
Further examples include Egypt, where a Lintec CSD2500B containerised asphalt-mixing plant completed its first job on an important municipal highway contract in Aswan; and Cameroon, where a Lintec CSM4000 containerised asphalt-mixing plant was commissioned to build the country’s first expressway.
Other flagship projects were executed in Ghana, where a Linnhoff TSD1500 MobileMix asphalt-mixing plant achieved remarkable progress on a high-profile road project; as well as in Ethiopia, where the Linnhoff TSD 1500 MobileMix asphalt plant worked on Ethiopian roads and highways.
At this year’s Big 5 Construct South Africa, Lintec & Linnhoff will be promoting its popular range of TSD,
CDP, CSD and NVX models.
The Linnhoff TSD MobileMix asphalt-mixing plant is ideal for short-term projects when time is of the essence. Featuring the company’s trademark doublescreen drum technology, the Linnhoff TSD range reduces overall operating costs and fuel consumption by eliminating the need for hot elevators and vibrating screens. They are also designed with four fully integrated basic mobile modules, with a built-in chassis for easy mobility.
“The Lintec CDP series of continuous asphalt-mixing plants ranges from 30-160 tph. They can be assembled on a suitable and solid compacted ground, without the need for concrete foundations. They are conceptualised for easy and quick setup and dismantling, making them suitable for short-term projects or mobilisation from one project to another,” says Chakra.
mixing plants are built in ISO-certified sea containers and are the first of their kind in the industry. The Lintec CSD asphalt-mixing plants feature a modular construction that allows for easy transportation and convenient installation, representing the ideal choice for both small and big project requirements.
With a capacity that ranges from 80 to 240 tph, and batch sizes from 1 350 to 3 000 kg, Lintec’s CSD asphalt-mixing plants offer superior and unique energy-saving technology
With a capacity that ranges from 80 tph to 240 tph, and batch sizes from 1 350 kg to 3 000 kg, Lintec’s CSD asphaltmixing plants offer superior and unique energy-saving technology that brings cutting-edge sustainability, low total cost of ownership and reduced energy consumption. In addition, all plants are pre-assembled with quality that is guaranteed from rigorous test cycles, ensuring fast and smooth setup, low shipping costs and efficient transportation.
In addition, the Lintec CSD containerised asphalt-
The Linnhoff NVX NovaMax asphaltmixing plants are designed for the most efficient asphalt-mixing operation with hot elevator and vibrating screens. Its modules are configured for quick installation and a compact footprint, making it an economical asphalt-mixing plant suitable for any paving project.
Commenting on market drivers, Chakra says, judging by the feedback from customers, African markets require mobility, thus small- to medium-sized asphalt and concrete batching plants are best suited for infrastructure projects across the continent.
“The market is also price-sensitive, so we need to ensure that we remain competitive, while also demonstrating the value that our cutting-edge plants bring to the industry. Lintec & Linnhoff is backed by 100 years of collective German expertise, and our brands provide powerful and innovative solutions that meet industry standards for environmental impact, recyclability and reusability for thousands of prestigious infrastructure projects worldwide,” concludes Chakra. a
B&E International’s ROG division provides a full range of drilling and blasting services.
Having previously operated as an internal service provider to the Crushing and Screening division, B&E International’s Drilling and Blasting business has been expanded into a fully-fledged, commercial ‘rock-on-ground’ (ROG) division that caters for external customers as well. Contracts Manager Mark Roberts unpacks the thinking behind the latest development. By Munesu Shoko
Renowned for its integrated crushing, mining and mineral processing solutions, B&E International, part of the larger Raubex Group, has always had a Drilling and Blasting component to its business. Traditionally, this division was largely meant to support the company’s Crushing and Screening division. However, with effect from August 2023, the business has been expanded into a standalone, commercial ‘rock-on-ground’ division that also caters for external ROG clients.
Headed by Contracts Manager Mark Roberts, the division provides a full range of drilling and blasting services, including specialised blasting techniques, pre-splitting, post-splitting, trench blasting, inplace treatment and smooth blasting. The service offering further includes full blast
B&E International, part of the larger Raubex Group, has always had a Drilling and Blasting component to its business
With effect from August 2023, the business has been expanded into a standalone, commercial ‘rock-onground’ division that also caters for external ROG clients
The expansion of the division positions B&E International as a one-stop shop for the mining, quarrying and construction industries in South Africa
The division has grown significantly, more than tripling its staff complement in the past three months
Previously, this division owned nine drill rigs, with the capability of drilling holes from 76 mm to 127 mm
From August 2023 to date, the ROG division has bolstered its fleet from nine to 23 surface drill rigs
designs (for specific applications), face profiling and bore-tracking, while observing ‘mass per delay’ effects to ensure restricted blasting control requirements on all projects. “From basic principles to fragmentation analysis, as well as monitoring of environmental effects by means of measuring air and ground shockwaves, we do it all,” he says
Roberts tells Quarrying Africa that the expansion of the division positions B&E International as a one-stop shop for the mining, quarrying and construction industries in South Africa, offering a full suite of services from rock-onground to product-on-the-ground.
“Since taking over as MD of B&E International, Chris Weideman has always had a vision to grow the drilling and blasting side of the business beyond its internal jurisdiction, and his vision has come to fruition,” says Roberts.
“Our ROG division will serve quarries, the civils market and large mining operations,” says Roberts. “The expansion comes at a time when we see a marked improvement in tendering activity in the civil projects space. In fact, we have already picked up a number of projects in the civils market, as well as the quarrying sector.”
Following the arrival of Roberts in August last year, the division has grown significantly, more than tripling its
staff complement in the last three months. With more projects in the offing, Roberts expects his division to grow at least four to five times than what it was before he came on board.
“Our growth to date has largely been driven by quarrying and civils projects that we have acquired. At present, large mining contracts constitute approximately 30% of our business and our goal is to grow this percentage split to at least 50%.”
Commenting on the projects acquired thus far, Roberts says the division is already doing work at more than 18 quarries all over South Africa. The client base includes some of the major construction materials groups in the country. In addition, the division has been contracted by one of the major construction contractors in the country to provide a full suite of drilling and blasting services at two of its flagship projects. Meanwhile, the division continues to execute a couple of internal projects, supporting B&E International’s Crushing and Screening division.
To cater for the growing project base, the division has invested heavily in its plant. Previously, this division owned nine drill rigs, with the capability of drilling holes from 76 mm to 127 mm. To grow the capability,
especially to cater for larger hole size requirements, the division has already invested in five new drill rigs, allowing it to drill hole sizes from 92 mm to 140 mm. The next natural step is the expansion into larger hole diameters, in excess of 140 mm for the opencast mining sector.
The five new machines comprise three Sandvik Pantera DP1500i and two Epiroc PowerROC T50 surface drill rigs. In total, the company now owns seven large surface drill rigs, having recently purchased a used Sandvik Pantera DP1500i and an Epiroc PowerROC T50 from an auction. Four of the larger units have been deployed at a project in Rustenburg, with one each working in Lesotho and the Western Cape.
“From August 2023 to date, we have bolstered our fleet from nine to 23 surface drill rigs. This is testimony to the scale of expansion and the growth achieved within a short space of time,” says Roberts. “
One of the key competitive edges is the team’s wealth of knowledge in drilling and blasting. It starts right at the top, with Roberts’ three decades worth of experience. Roberts moved to B&E International with members of a team that he has previously worked with for many years, which includes drillers, supervisors and artisans.
Blasting operations, says Roberts, can be a daunting
task, especially for those who may be unfamiliar with the processes. The use of explosives makes any blasting operation inherently dangerous. Having an experienced team that understands the intricacies of blasting, following a strict adherence to the blasting plan, allows for smooth, safe and efficient blast outcomes all the time.
Having assembled an experienced team means that the division has the safety stability required in blasting operations. They are a meticulous team which is very familiar with all the quality and safety requirements in blasting. This is particularly important at quarrying operations, where flyrock and air blasts, for example, are out of the question, especially given that most quarries are located in the midst of communities.
Another benefit, adds Roberts, is that there is an element of trust, both internally and externally. Knowing his teams’ capabilities, Roberts trusts their skills and commitment to the cause. In addition, most of the customers the division has picked up are already familiar with most of the team members and know their competencies.
“We have assembled a strong team, and each individual has sharpened their skills over many years in this specialised drilling and blasting field. Together with the B&E International culture, which has made the company successful for many years in the industry, we believe we have a good recipe for success,” concludes Roberts. a
Blasting is the single most critical operation affecting the entire mining or quarrying cycle. The current pain points in blasting stem from several key elements, including safety, community relations, legislation and production requirements. In a one-on-one with Quarrying Africa, Hennie du Preez, Manager for AXXIS Support at BME, discusses how electronic initiation systems can address these challenges and optimise the whole mining process. By Munesu Shoko.
The increased economic and operational pressures demand that today’s mines and quarries stay ahead to remain competitive. One area where this is particularly crucial is in blasting – a critical function that greatly influences operational efficiency, costs and the success of all the other downstream processes such as load and haul, as well as crushing and screening.
Apart from regulations and production demands, some of the common pain points for quarries when it comes to blasting are ground vibrations, coupled with the risk of fly-rock, not to mention noise and dust creation.
With the advent of electronic initiation systems, says
Du Preez, it is now possible not only to meet higher safety levels and environmental impact control, but to also gain more blast control and improve fragmentation, thus delivering more downstream value to the whole operation.
With the AXXIS Silver, BME’s cost-effective electronic system for operations with less demanding blasting needs, quarries can free themselves from the limitations of conventional pyrotechnic solutions and improve blast outcomes.
In an environment where safety is principal, the regulator, the Department of Mineral Resources and
BME successfully blasted next to a pipeline in Vereeniging, Gauteng, where the peak particle velocity (PPV) was kept at less than 50
0,0025%
With the AXXIS Silver, the accuracy of detonation delays is unmatched, and reaches 0,0025% firing accuracy for consistent quality blasting that results in optimal rock fragmentation and consistency
Blasting is a critical function that greatly influences operational efficiency.
The current pain points in blasting stem from several key elements, including safety, community relations, legislation and production requirements
With the advent of electronic initiation systems, it is now possible not only to meet higher safety levels and environmental impact control, but to also gain more blast control and improve fragmentation
With the AXXIS Silver, quarries can free themselves from the limitations of conventional pyrotechnic solutions and improve blast outcomes
The accuracy and reliability of electronic detonators brings more energy to the rock and delivers better fragmentation
Energy (DMRE), is pushing quarries to adopt electronic blasting systems to improve safety, a principal parameter in blasting and the mining cycle in general. As a result, Du Preez notes that the majority of quarries in South Africa have migrated from pyrotechnic to electronic initiation systems in recent years, with very few operations still using shock tube alternatives.
“Electronic blasting systems allow safer blasting for a few reasons. Firstly, there is little risk of unintended detonation, as the blast command is encrypted. With our AXXIS Silver system, we even have a dual basis of safety through the innovative use of both dual capacitors and dual voltage,” he says. “Secondly, the blasts can be better controlled, which means less risk of fly-rock or vibration
“Electronic blasting systems allow safer blasting for a few reasons. Firstly, there is little risk of unintended detonation, as the blast command is encrypted. With our AXXIS Silver system, we even have a dual basis of safety through the innovative use of both dual capacitors and dual voltage.
damage; this is becoming more important for quarries as urban settlements expand and encroach on quarry boundaries.”
Using its AXXIS technology, BME has executed some of the most challenging blasts, with limited ground vibrations, in recent times. For example, the company successfully blasted next to a pipeline in Vereeniging, Gauteng, where the peak particle velocity (PPV) had to be extremely low. It is common knowledge that closer distances lead to higher PPV values, but by using the AXXIS electronic system, BME achieved a PPV of less than 50. In Midrand, the company blasted at a civil site next to a gym and office building with a minimum vibration of 5 and less. Another milestone project is the Clanwilliam Dam construction blasting where the PPV was less than 12,6.
A further safety benefit, he adds, relates to risks outside of the quarry itself. While pyrotechnic detonators have been deployed for criminal purposes such as cash-in-transit heists and ATM bombings, electronic detonators are unlikely to be used in this way as they require a whole detonation system to make them work. In addition, electronic detonators can be readily tracked from source to site, ensuring that every detonator that is manufactured can be closely monitored until it is initiated in the blasthole.
With all the easy rock already mined out and blasting becoming more difficult by the day, quarries have come
to a point where mining has become even more difficult, yet equipment and energy costs keep rising and the industry demands stringent product specifications. Du Preez says there is a better understanding that electronic blast systems take blast efficiency to a whole new level.
One of the key benefits of electronic detonators is the bottom-line value they offer to quarries. The accuracy and reliability of these detonators brings more energy to the rock and delivers better fragmentation. This in turn means a smoother process with less time spent breaking over-sized material. This improves the loading and hauling efficiency, while reducing the energy required in the crushing and screening process.
With the AXXIS Silver, says Du Preez, the accuracy of detonation delays is unmatched, and reaches 0,0025% firing accuracy for consistent quality blasting that results in optimal rock fragmentation and consistency. The programmability of 15 seconds with 1-millisecond intervals allows for blast designs to be precision-designed, resulting in better fragmentation. “The benefits of good fragmentation are well documented,” says Du Preez. “Firstly, it eliminates the need for costly secondary blasting or mechanical breaking of oversize material. Secondly, there is a positive impact on downstream processes such as load and haul. Crusher throughput also increases due to improved overall particle size distribution. The overarching benefit from all this is reduced energy consumption in the mining value chain, which constitutes a sustainability effort achieved.” a
To grow its business, Beowolf Mining, a leading supplier of drilling consumables to the quarrying and mining sectors, has set its sights on expanding its footprint in Africa. Director of sales Riaan Theron unpacks the African expansion strategy and some of the key trends in the drilling market. By Munesu Shoko .
Having traditionally served the South African mining market, Beowolf Mining has adopted an expansion strategy to grow its business in Africa. While the South African mining sector is grappling with its own challenges, Theron believes that the local market will remain an important mining destination for years to come.
However, says Theron, issues such as legislative uncertainty, the lack of exploration investment as well as energy constraints, are impacting new investment in mining. In the wake of these documented challenges, Beowolf Mining has taken a strategic decision to
expand its geographical footprint and diversify its business into new commodity areas.
“Our African expansion drive started some five years ago, with initial focus on West Africa, particularly Burkina Faso and Guinea, where we have already secured business from two big mining houses. We have identified a big gap in terms of both quality product and good service in these markets,” says Theron. “The expansion into West Africa complements our existing cross border business in key markets such as Botswana, Zimbabwe and Namibia.”
Despite the focus on Africa, Theron is still positive about prospects of growth in South Africa. “In spite
R2-million
At one of the large open pit mines in South Africa, Beowolf Mining spent about R2-million on R&D to ensure that the type of carbide and the design of the drill bits were 100% suited to the application
5
Beowolf Mining’s African expansion drive started some five years ago, with initial focus on West Africa, particularly Burkina Faso and Guinea, where it has already secured business from two big mining houses
Having traditionally served the South African mining market, Beowolf Mining has adopted an expansion strategy to grow its business in Africa
Its African expansion drive started some five years ago, with initial focus on West Africa, particularly Burkina Faso and Guinea
One of the biggest emerging trends is the need for stock availability, not only in the drilling consumables market, but across the mining supply chain
In a world where a one-size-fits-all approach has lost relevance, mines and quarries now place value on custom-made solutions that address their specific needs on site
of the existing challenges, I believe economic sense will prevail at some point when it comes to legislative certainty. I am of the view that the government will at some point prioritise a conducive environment for more mining investment,” he says.
Commenting on some new trends in the drilling consumables market, Theron has observed an influx of new suppliers in the market, but many of them do not last long. The reason for their early demise is that many of the new suppliers are importing their drilling consumables from overseas traders and not necessarily from manufacturers, which makes it difficult for them to provide the necessary aftermarket support for their products. To run a sustainable drilling consumables business, he stresses, there is need for consistent quality and ‘value for money’ for the client.
One of the biggest emerging trends, notes Theron, is the need for stock availability, not only in the drilling consumables market, but across the mining supply chain.
Maintaining adequate inventory has become critical for the product-intensive mining industry. “In mining, time is money, and therefore clients expect their suppliers to carry enough stock to meet their operational needs. This is despite the current challenges with our South African ports and the general catastrophe within the global supply chain,” he says.
As part of its new business strategy, Beowolf Mining has in the past few years increased its monthly shipments from its overseas suppliers to build up adequate stock levels and ensure availability locally. Keeping enough stock, says Theron, increases chances of getting new business as customers look for suppliers with inventory.
In a world where a one-size-fits-all approach has lost relevance, Theron says mines and quarries now place value on custom-made solutions that address their specific needs on site. In response to that trend, Beowolf Mining invests heavily in research and development (R&D) to ensure provision of custom-made solutions to its customers.
“We believe in providing tailor-made products for different types of applications and ore bodies,” says Theron. “At one of the large open pit mines in South Africa, we spent about R2-million on R&D to ensure that the type of carbide and the design of the drill bits were 100% suited to the application. As a result, the client is getting maximum life out of their drill bits.”
In recent years, adds Theron, the drilling equipment market has not only seen a hastening trend towards
consolidation within the supplier community, but also an expansion of the range of products and services offered under one roof. This has created true ‘one-stop shops’ that are able to service a wide range of customers’ needs from one stable.
Convenience, says Theron, is one of the many reasons why customers prefer to deal with a one-stop- drilling solutions provider such as Beowolf Mining. Instead of having to go to multiple suppliers, buyers for mines and quarries can simply go to one location for all their requirements. Apart from convenience, dealing with a single supplier for a whole range of drilling needs means faster turnaround times for increased uptime.
Over the years, Beowolf Mining has bolstered its product offering with a complete range of rockdrilling tools and drill rigs to meet its customers’ requirements. The extensive range includes down the hole (DTH) drilling equipment, hydraulic open pit drill rigs, DTH drill rigs, drill rig lubricants, top hammer drilling equipment, drifters and drifter spares. Additionally, they offer refurbishment of hydraulic drifters. In recent times, selfdrilling anchors have become a big part of the company’s business.
In addition, Beowolf Mining has developed an app designed to monitor drilling consumables. Traditionally, available apps are original equipment manufacturer (OEM) solutions dedicated to monitoring parameters such as engine hours and fuel consumption. Beowolf Mining’s app, says Theron, is the first of its kind that is dedicated
to consumables. The solution will be showcased for the first time at this year’s Electra Mining Africa in September.
Apart from drilling consumables, Beowolf Mining is in a joint venture with its sister company, JMH Equipment, for the sales of Soosan crawler drills, previously known as Junjin, from South Korea. The company has been marketing this range of crawler drills for the past 10 years, with some 55 units already operating in the South African mining industry alone. Several units have also been exported to Botswana, Angola and Namibia.
“The range will soon be expanded with larger rotary and DTH drills following JMH Equipment’s recent appointment as the exclusive distributor of Revathi Equipment Limited’s range in Africa. This will allow us to offer a complete range of drill rigs for all open pit applications from aggregates operations to large opencast mines. After 24 years in the game, now we can confidently say we offer a full drilling package,” concludes Theron. a
To simplify the digitalisation process for quarry operators, Volvo CE has developed solutions that are compatible with any machinery, offering a ‘plug and play’ experience.
Digital transformation is taking root across industries, and with good reason. By providing new approaches to reducing costs, improving productivity, optimising efficiency and uptime, digitalisation is a profit engine for quarries and mines at large. By Munesu Shoko .
Digital solutions are becoming increasingly vital to quarries’ daily operations. As Andrey Komov, Head of Productivity for Region International at Volvo Construction Equipment, puts it, digitalisation is no longer just a buzzword; it is transforming how quarries operate.
There is a general school of thought that quarries by their nature produce high-volume, low-cost material and are therefore price-sensitive in everything they procure. Given this scenario, how can they embark on digital transformation in a cost-effective manner?
In quarries, he says, where work is repetitive and involves moving large amounts of materials in a continuous production environment, even minor improvements in efficiency can lead to significant boosts in productivity or cost savings over time.
“However, identifying these opportunities for enhancement can be challenging without access to machine and production data, highlighting the crucial role of digitalisation,” he says. “Contrary to common belief, implementing digital solutions in quarries does not necessarily require a hefty budget or a one-time overhaul. We are reshaping the perception that digitalisation is only feasible for those with substantial financial resources.”
Volvo CE’s subscription-based solutions empower customers to start their digitalisation journey regardless of budget constraints, enabling them to initiate small-scale implementations and refine their approach along the way, rather than waiting for the perfect plan.
To further simplify the process for quarry operators, Volvo CE has developed solutions that are compatible with any machinery, offering a ‘plug and play’ experience. While these solutions seamlessly integrate with Volvo
24/7
ActiveCare is a 24/7 remote monitoring service that analyses CareTrack data for the customer
By partnering with Volvo CE and addressing these key considerations, quarry operators can navigate their digital transformation journey with a clear roadmap and achieve significant improvements in efficiency, productivity and profitability.
Net zero
Maximising efficiency now also paves the way for the transition to electric machines in the future as the industry aspires to net zero quarrying
“Contrary to common belief, implementing digital solutions in quarries does not necessarily require a hefty budget or a one-time overhaul. We are reshaping the perception that digitalisation is only feasible for those with substantial financial resources.
By optimising efficiency, uptime and productivity, it helps achieve the highest production output at the lowest cost
Tools such as machine telematics and production monitoring software provide valuable insights for streamlining processes, minimising wasted time and resources, and ultimately increasing output
Digital transformation can also drive sustainability. Improved efficiency often translates into reduced fuel consumption and lower emissions, minimising environmental impact
When considering technologies to accelerate digital transformation in quarries, the selection greatly hinges on the unique circumstances and objectives of each quarry
machines through the Volvo Co-Pilot platform, they remain adaptable across different equipment brands. Volvo CE, adds Komov, is constantly learning with its customers, and its list of solutions will continue to grow over time.
The benefits of investing in digital transformation abound. First of all, says Komov, digitalisation is a profit
engine for quarries. By optimising efficiency, uptime and productivity, it helps achieve the highest production output at the lowest cost. Tools such as machine telematics and production monitoring software provide valuable insights for streamlining processes, minimising wasted time and resources, and ultimately increasing output.
“Digital transformation can also drive sustainability. Improved efficiency often translates into reduced fuel consumption and lower emissions, minimising environmental impact. Maximising efficiency now also paves the way for the transition to electric machines in the future as we aspire to net zero quarrying,” he says.
At the same time, digitalisation can elevate safety standards, and this is paramount in quarries. Real-time location tracking of personnel and equipment, people and object detection systems with automated braking, as well as improved operator skill and safety awareness all contribute to a safer work environment.
In addition, in today’s competitive labour market where attracting and retaining skilled workers is a challenge, digitalisation makes quarries more appealing workplaces. Automated processes, reduced administrative burdens and the implementation of innovative technologies create a more modern and engaging work environment that can attract a wider talent pool.
What are some of the key factors quarry operators should consider when embarking on a digital transformation
journey? The first factor to consider for a successful transition is partnership, says Komov. Every quarry has unique challenges and goals, and Volvo CE encourages collaboration to develop a customised digitalisation programme.
“Our four-step process – Insight, Analyse, Improve and Sustain – involves careful listening to a customer’s needs and crafting a solution that delivers sustainable improvements. This programme leverages various services to address specific requirements and if an off-the-shelf solution does not exist, we will brainstorm and develop a custom approach to meet a customer’s unique needs,” explains Komov.
Another factor, he adds, is connectivity. To measure parameters in real-time, it is essential to have strong connectivity using machine telematics or tablet solutions. Unfortunately, there are no shortcuts to achieving this. Volvo CE machines can be equipped with satellite telematics in areas without mobile network coverage, but this option is expensive due to the high cost of satellite connectivity.
In addition, building employee buy-in is essential because digital transformation requires adopting new ways of working. Success hinges on clear communication of the business case and buy-in from everyone involved.
“Ensure your entire team is on board, committed and kept informed of tangible improvements and their impact on the bottom line. Remember, digital transformation is a team effort; it cannot be delegated to a single person or group,” stresses Komov.
By partnering with Volvo CE and addressing these key considerations, quarry operators can navigate their digital transformation journey with a clear roadmap and achieve significant improvements in efficiency, productivity and profitability.
Through a range of available solutions, Volvo CE uses machine data and digital tools to optimise a quarry’s safety, efficiency, environmental impact and productivity across the entire machine lifecycle – from planning to maintenance.
Firstly, at the planning stage, gone are the days of guesswork when it comes to deploying machines. “Our SiteSimulation tool creates a digital twin of the quarry, incorporating optional drone imagery. This allows us to calculate the exact number and size of machines the operation needs, along with the optimal driving routes, to achieve production targets (tonnes per hour or cost per tonne) with maximum efficiency. Even if it means recommending fewer machines, this data-driven approach builds trust and empowers the customer to succeed,” says Komov.
Secondly, when it comes to day-to-day
operations, operator skill has a significant impact on the quarry’s bottom line. CareTrack, Volvo CE’s telematics system, collects data on operator behaviour and fuel efficiency. This data is used to identify opportunities for training and track progress over time. However, stresses Komov, training goes beyond courses.
Volvo Co-Pilot with Load Assist includes an Operator Coaching app that provides real-time feedback to improve efficiency and productivity. Operators can see how their technique impacts performance and develop good habits. Additionally, Volvo Co-Pilot with Haul Assist features a Connected Map function showing the real-time location and status of other machines on site, promoting safety awareness, preventing congestion and reminding operators of the speed limits.
The On-Board Weighing functionality, available on Load Assist for wheel loaders, Haul Assist for haulers and Dig Assist for excavators, further optimises operations. Operators and site managers can see the load percentage in real time on the Volvo Co-Pilot screen, while lights on the hauler indicate the status, preventing dangerous overloading or wasteful underloading.
In addition, digitalisation is a gamechanger for maintenance, especially preventative maintenance. CareTrack data helps fleet managers understand the health of their machines and schedule service at optimal times to minimise disruption. ActiveCare takes this a step further. It is a 24/7 remote monitoring service that analyses CareTrack data for the customer.
An algorithm sorts through machine fault codes, alarms or alerts, assigns probable causes, and prioritises them for technicians to take preventative action and maintain maximum uptime. This proactive approach empowers technicians to address minor issues at the appropriate time and prevent these from turning into larger, expensive problems that will seriously impact uptime. This, says Komov, is now gaining traction with several Volvo CE dealers in Africa.
When considering technologies to accelerate digital transformation in quarries, Komov adds, the selection greatly hinges on the unique circumstances and objectives of each quarry. To this end, Volvo CE tailors programmes specifically to meet customer needs. Apart from the
above-mentioned technologies such as SiteSimulation, Volvo Co-Pilot and ActiveCare, he highlights a number of others that could be advantageous for quarrying customers.
“Performance Indicator provides realtime insights into crucial metrics such as production volume from each machine (measured via the On-Board Weighing system on Volvo machines), payload utilisation (including underloading, overloading and carry-back), and fuel efficiency (measured in tonnes per litre), amongst other things,” he says.
“Customers can establish target volumes and promptly address deviations, as data seamlessly integrates into digital management systems, streamlining operations and eliminating paperwork. This tool works best with Connected Map.”
Connected Load Out, meanwhile, digitises the load-out process by automating orders and load tickets, thereby fostering seamless communication between loader operators, site offices and incoming trucks. This realtime oversight facilitates more informed decision-making and process control, resulting in time and cost savings.
In addition, EcoOperator training uses Volvo simulators to support the rapid development of operator competency without the need for diesel consumption or risk of machine damage. To ensure accessibility, Volvo CE has devised a solution whereby simulators are housed within shipping containers equipped with climate control, allowing training delivery anywhere in the world.
In conclusion, Komov says quarry owners should consider that their competitors are bound to embrace this transformation sooner or later, if they have not already done so. While starting early might pose some challenges, being late could have severe repercussions for the business. Volvo CE is keen to support quarries on this journey, “as it resonates with its mission of enhancing the quality of life on our planet”.
Komov concludes: “Through collaboration with our customers, we aim to enhance their efficiency and contribute to sustainable development by reducing carbon emissions and optimising resource utilisation – always prioritising the health, safety and well-being of individuals. That is why we are committed to fostering innovation and working closely with our customers to create a cleaner, safer and more interconnected world, day by day.” a
AfriSam
AfriSam is a leading construction materials group in southern Africa. Since establishing its first cement plant in 1934, the company has grown into a formidable construction materials group with operations in South Africa, Lesotho and Eswatini.
www.afrisam.co.za
Babcock
Through several business units, Babcock offers a range of products and services, including construction and mining equipment, engineering solutions for steam generation and power plants, crane hire and gear rental, industrial generators, welding equipment and DAF truck sales and service.
www.babcock.co.za
With more than 16 years of experience in Proximity Detection Systems solutions, Booyco Electronics has supplied over 6 500 sets of mining vehicle equipment installations across southern Africa, as well as more than 55 000 pedestrian RFID installations.
www.booyco-electronics.co.za
Bunting
Bunting’s range of magnetic separators and metal detectors for quarries and mines ensures the protection of crushers, screens and conveyors. Overband magnets, suspension magnets and pulley magnets automatically remove tramp ferrous metal from conveyed quarried rock. www.bunting-redditch.com
IPR
IPR is recognised across the SADC region as the pump, heavy duty slurry handling and dredging specialist operating in underground and surface mining, quarrying, construction, wastewater, petrochemical and oil and gas sectors. www.pumprental.co.za
LOADTECH Load cells Onboard Weighing are specialists in onboard weighing providing complete solutions onboard your heavy goods vehicle, primarily in the application of load cell and transducer systems for payload protection and accuracy in the commercial vehicle sector. www.loadtech.co.za
Pilot Crushtec International
Pilot Crushtec International (Pty) Ltd is South Africa’s leading supplier of mobile and semi-mobile crushing, screening, recycling, sand washing, stockpiling, compacting and material handling solutions. www.pilotcrushtec.com
Sandvik
As a world-leading mining equipment manufacturer, Sandvik Mining and Rock Solutions is committed to improving your productivity and profitability. Our products and services provide you maximum value in terms of performance, quality, safety, flexibility and total economy. www.rocktechnology.sandvik/en/
Astec
Astec Industries has been a global leader in providing innovative Rock to Road™ solutions since 1972, specialising in equipment for asphalt road building and aggregate processing. www.astecindustries.com
John Deere
John Deere offers a comprehensive range of construction equipment, including ADT’s, excavators, loaders, dozers, graders, skid steers and TLB’s, designed to enhance productivity, efficiency, and performance on job sites of all sizes. www.deere.africa/en/construction
Lintec & Linhoff
Lintec & Linnhoff is a global manufacturer and distributor of leading-edge solutions for the asphalt and concrete industries under the Lintec and Linnhoff brand names. Its products include asphalt mixing plants, concrete batching plants, pavement related technologies, and specialist concrete cooling solutions.
www.lintec-linnhoff.com
Schauenburg Systems is a South African company that specialises in providing technology solutions for safety and productivity in mining and industrial markets. It positions itself as an active partner for digital transformation to meet the needs of the “Connected Worker.” The company has a strong focus on innovation and has a brand promise of “Innovation that Saves”. www.schauenburg.co.za
Weir Minerals
Weir Minerals Africa offers a wide range of equipment solutions including pumps, hydrocyclones, valves, dewatering equipment, wear-resistant linings, rubber products, screens and crushers – backed throughout the product lifecycle by high levels of aftermarket support.
www.global.weir
SANY
Sany Southern Africa is a subsidiary of Sany Group, a leading manufacturer of construction, mining and port machinery with over 20 R&D centres and manufacturing bases all over the world. www.sanysouthafrica.com
New LeopardTM DI650i down-the-hole surface drill rig offers long-term productivity and superior stability with robust and reliable main components – seamlessly integrated with state-of -the-art technical solutions. Scalable automation, easy maintenance and outstanding movability are the features that make LeopardTM DI650i a premium product, which is an honor to own.
Leave your paw print and enjoy the smooth, efficient ride.