
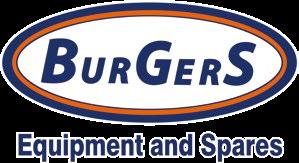
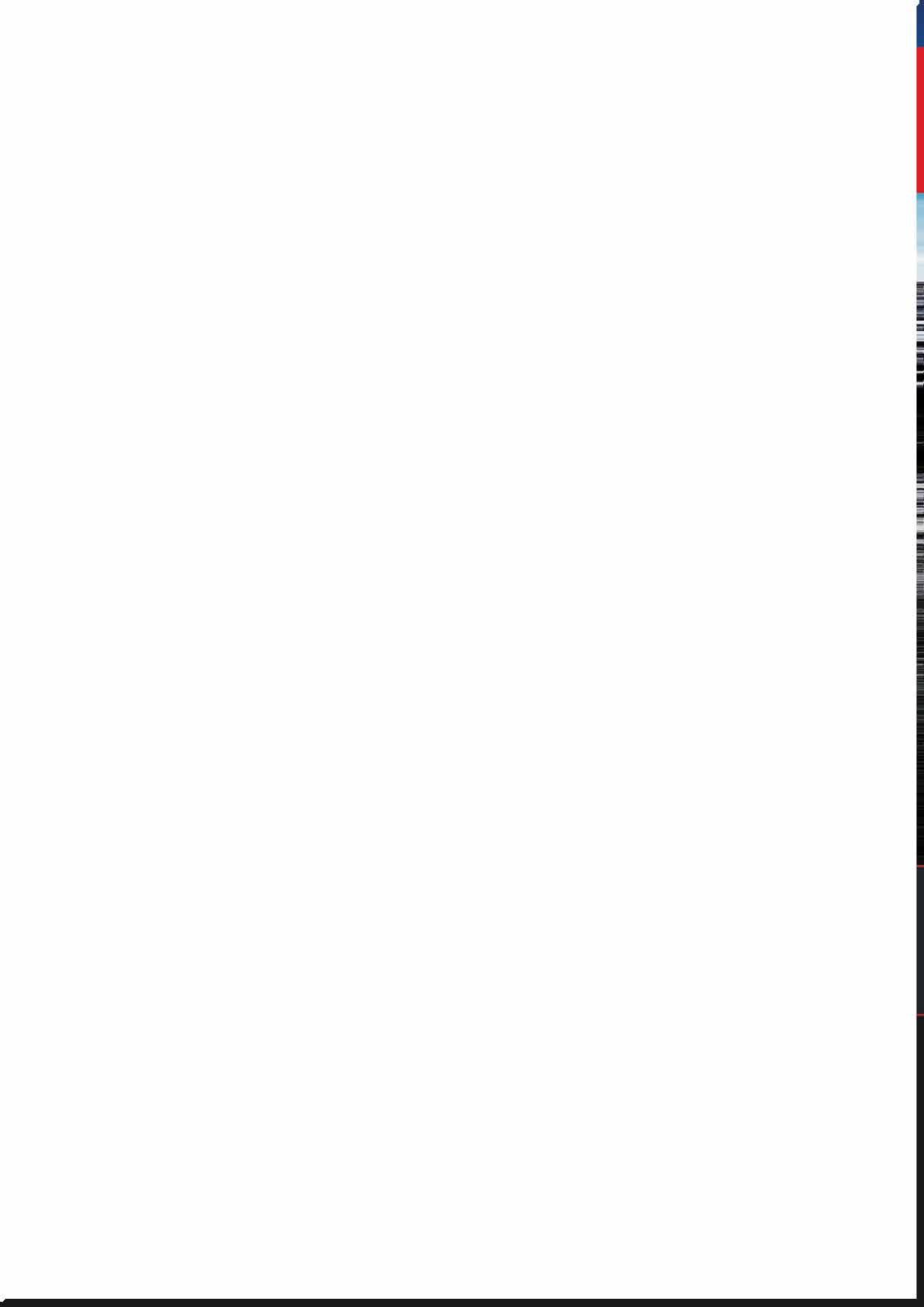
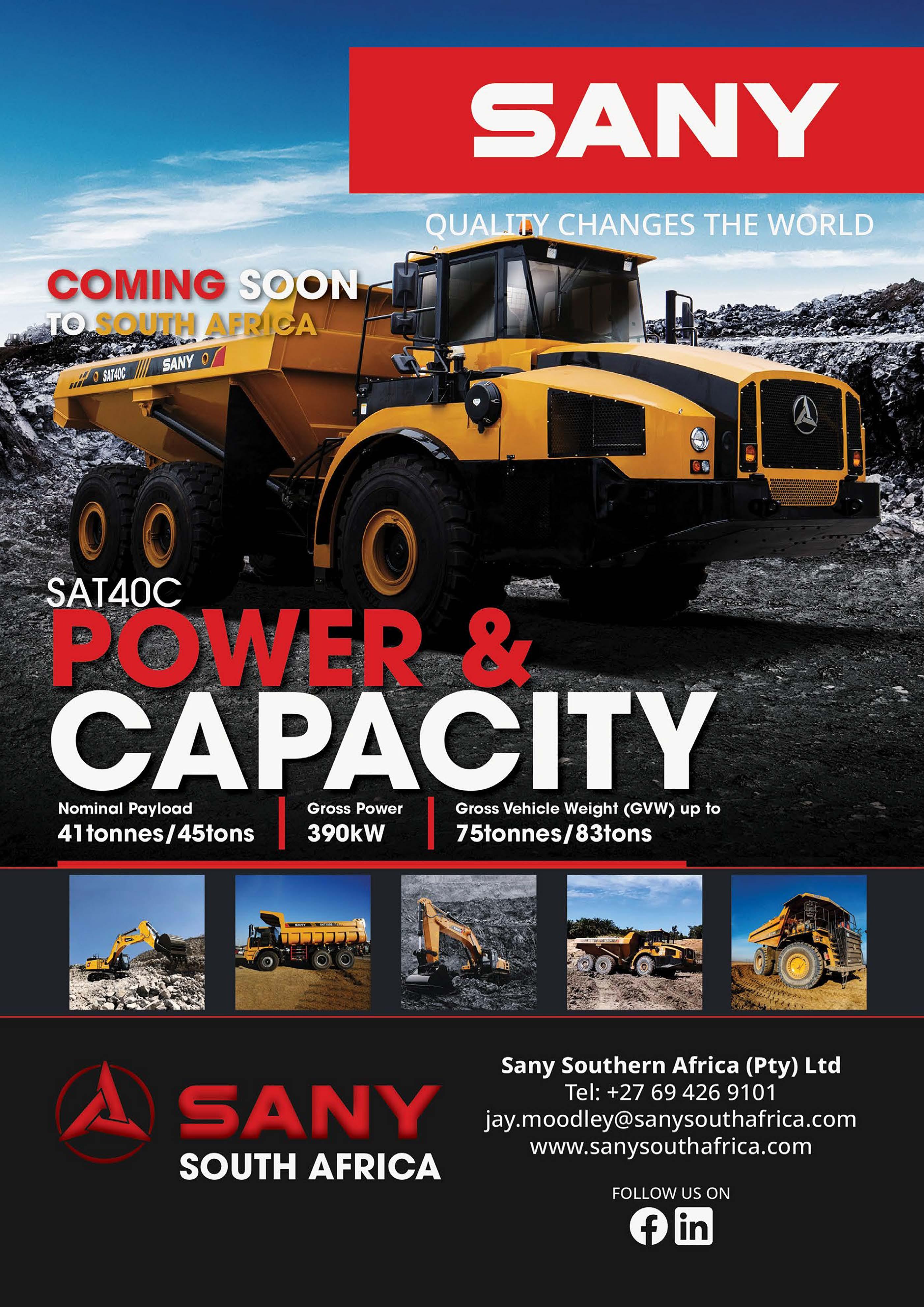
Make no bones about it, the quarrying industry, just like many other sectors of the economy, is undergoing an intense period of change. Having often been criticised for failing to embrace innovation and technological enhancements, there is seemingly a better understanding of the innovation imperative. The choice facing companies today is simple: innovate or perish.
In the face of some recent difficult years, quarrying companies have been compelled to adopt innovation to reduce overheads and improve efficiencies. Those that will survive today’s economic environment and succeed in tomorrow’s are those willing to continually reinvent themselves, their processes, their products and the way they go about their business.
perspective, there are many readily available digital tools which quarries can take up so as to accelerate their digital revolution as well as to fundamentally transform how they operate and make decisions.
It is best to start small by adding to existing technology. Sensors are the starting point for digitalisation as they are where data is created. It is true that almost every earthmoving machine in today’s world utilises some sensors.
MUNESU SHOKO
Publishing Editor Email: munesu@quarryingafrica.com
LinkedIn:
Munesu Shoko
Quarrying Africa
In recent editions, we have cast the spotlight on digitalisation in quarrying. At a time when even the most fundamental elements of business success are being re-evaluated and redefined, one thing has increasingly become clear: technology is no longer a ‘nice to have’; it is a ‘must have’.
Traditionally, there have been many barriers to quarries adopting new technologies, primarily the economies of scale, but in an increasingly digital age, digital transformation has become a distinct possibility as digital tools, data collection and advanced analytics have all evolved.
Digital transformation is about leveraging all the digital tools at the industry’s disposal. From a cost
Digital transformation is, however, not an isolated technological project. Instead, it is the combination of numerous projects that transform every aspect of an operation to be digital-first. One of the necessary steps in the digital transformation journey is automation. Automation is an opportunity for African quarries to improve their safety, efficiency and productivity. The major barrier to implementation of automated systems, especially in Africa, is that there are still uninformed viewpoints on their practicality and costs.
In conclusion, the time to develop an innovation orientation is not tomorrow or next year. It is now. Quarrying companies should start to actively search for new, better, more productive ways of doing things. While change by its very nature can be disruptive, it is very much needed, because let us face it, everything around us is evolving and changing the rules and dynamics of the business and market as a result. To remain relevant and successful, quarrying companies must start to see their core competencies through the lens of the latest technologies.
Publishing Editor: Munesu Shoko
Sub Editor: Glynnis Koch
Business Development Manager: Elmarie Stonell
Admin: Linda T. Chisi
Design: Kudzo Mzire Maputire
Web Manager: Thina Bhebhe
Quarrying Africa is the information hub for the sub-Saharan African quarrying sector. It is a valued reference tool positioned as a must-read for the broader spectrum of the aggregates value chain, from quarry operators and aggregate retailers, to concrete and cement producers, mining contractors, aggregate haulage companies and the supply chain at large.
Quarrying Africa, published by DueNorth Media Africa, makes constant effort to ensure that content is accurate before publication. The views expressed in the articles reflect the source(s) opinions and are not necessarily the views of the publisher and editor.
The opinions, beliefs and viewpoints expressed by the various thought leaders and contributors do not necessarily reflect the opinions, beliefs and viewpoints of the Quarrying Africa team.
Quarrying Africa prides itself on the educational content published via www.quarryingafrica.com and in Quarrying Africa magazine in print. We believe knowledge is power, which is why we strive to cover topics that affect the quarrying value chain at large.
Printed by:
Email: munesu@quarryingafrica.com
Cell: +27 (0)73 052 4335
Following its official launch in South Africa in May 2024, the first LiuGong 856H-E Max battery-electric wheel loader in Africa has been deployed at Samancor Chrome. Having put it through its paces for a few weeks, mining contractor M Civils tells Quarrying Africa that the machine has to date proven its mettle and ushers in a new age in earthmoving by not only reducing environmental impact, but also lowering energy costs. By Munesu Shoko .
educing the environmental impact of the mining industry has become the main priority for the coming decades. While mines and their contracting counterparts will explore a range of new technologies to drive their Environmental, Social and Governance (ESG) agendas, battery-electric equipment is proving to be the best alternative to traditional diesel-powered mining machines.
With that in mind, a strategic quadripartite alliance between Chinese original equipment manufacturer (OEM) LiuGong, its South African dealer, Burgers Equipment & Spares, mining company Samancor Chrome and mining contractor M Civils, has brought the first LiuGong 856H-E battery-electric wheel loader to Africa. At the launch event attended by Quarrying Africa on May 7, 2024, the parties used the same platform to sign an agreement of sale for the first 856H-E. The collaborative effort between the four parties materialised on the back of M Civils’ 2023 visit to LiuGong’s manufacturing facility in China as part of the
423 kWh
Powering the 856H-E Max is a 423-kWh large-capacity lithium-iron phosphate battery from battery manufacturer CATL
The machine can work ten hours in light applications and eight hours in heavy duty applications
2023 LiuGong Global Dealer Conference, confirms Petrus van Blerk, Project Manager at M Civils.
“Upon seeing the 856H-E for the first time in China, we immediately started conversations with Burgers Equipment & Spares and LiuGong about the possibility of bringing the machine to South Africa for a trial run on a mine. The idea also appealed to our long-time client, Samancor Chrome, as part of its own ESG targets. As a mining contracting company that thinks innovation, this makes sense in terms of reducing our cost of operation, while delivering the same production for the mine,” explains Van Blerk.
Tiaan Burger, MD of Burgers Equipment & Spares, says the deal is exciting and allows the company to pioneer the ‘green’ revolution in the local earthmoving equipment sector. “We are excited to bring the first ever production-size battery-electric piece of earthmoving equipment to Africa on a commercial basis. We do not
The machine has been deployed to load trucks and perform stockpile management duties on site.
M Civils has deployed the first LiuGong 856H-E Max battery-electric wheel loader in Africa at Samancor Chrome in the North West Province of South Africa
When we visited the site in mid-June, the machine had been hard at work for just over two weeks and had already clocked over 100 hours with no teething issues whatsoever
The machine has been deployed to load trucks and perform stockpile management duties on site, where it is loading different types of processed chrome products and waste rock
Feedback from operators has been particularly positive – they have found the machine to be as powerful as its diesel counterpart
believe that this will be a high-sales volume machine, but it allows us to support the mining sector’s sustainability drive and play our part in the protection of the environment,” says Burger.
Li Yi, GM of LiuGong Machinery South Africa, says the OEM has over the years demonstrated its commitment to sustainability by leading the battery-electric equipment revolution in China, the biggest batteryelectric vehicles (BEV) market in the world. Since 2014, the company has made astronomic investments into research and development (R&D) of intelligent equipment solutions. In 2019, LiuGong rolled out its first generation 5-tonne (t) electric wheel loader, before using CONEXPO 2020 to introduce the 856H-E to the global market. To date, LiuGong has already sold in excess of 3 000 battery-electric machines in over 30 countries.
As part of the trial phase, M Civils has deployed the machine at Samancor Chrome in the North West Province of South Africa.
When Quarrying Africa visited the site in mid-June, the machine had been hard at work for just over two weeks and had already clocked over 100 hours with no teething issues whatsoever.
“We have deployed the machine to load trucks and perform stockpile management duties on site, where it is loading different types of processed chrome products and waste rock,” explains Van Blerk. “In the next few weeks, we also plan to deploy it to load trains, which will give us a good indication of the machine’s performance in a non-stop working environment.”
During the first two weeks of operation, the machine had performed beyond expectations. Feedback from operators had been particularly positive – they had found the machine to be as powerful as its diesel counterpart. More importantly, operators are happy with the quiet nature of the machine. The electric motor is smoother and quieter than internal combustion engines, which means that it produces less noise and vibration. This provides for a safer working environment for operators, as it reduces their risk of developing musculoskeletal disorders.
While it is too early to make an informed comparison in terms of the cost of operation between the new electric machine and its diesel equivalent, Van Blerk says early indications are that the machine is cheaper to run just in terms of the diesel/ electric comparison.
“Ideally, we would like to run the machine for at least three months to get a clear picture of the actual savings. The big thing, however, will be the cost of maintenance. We believe the cost of maintenance for battery-electric equipment will be a lot lower than for the diesel-powered machines. Electric machines have fewer moving parts than those powered by combustion engines, which means less maintenance. In addition, batteryelectric parts are usually more reliable than diesel-powered parts, and this can significantly reduce the cost of operation,” says Van Blerk.
Apart from the reduction in operational costs, Burger believes that the main advantage of battery-powered equipment in the mining industry is its environmental friendliness as it does not produce any greenhouse gas emissions. By switching to battery-electric equipment, mines and their contracting counterparts can significantly reduce their environmental impact and improve the health of their workers.
Powering the 856H-E Max is a 423-kWh large-capacity lithium-iron phosphate battery from battery manufacturer
M Civils uses a double input charging system, which fully charges the machine in about 60 - 90 minutes depending on the discharge state of the machine.
CATL. The battery, confirms Burger, is made up of ten individual battery packs. The motor has a kilowatt peak power output of between 160 and 180 kW. According to the OEM, the machine can work ten hours in light applications and eight hours in heavy duty applications. With the Intelligent Battery Management System, it can be fast-charged in 90 minutes.
At Samancor Chrome, M Civils works 24/7, using three eight-hour shifts. During weekends, the contractor deploys two 12-hour shifts. During the first two weeks of operation, the machine has completed both the eight- and 12-hour shifts on a full charge without discharging completely. This is despite the heavy nature of the chrome material that it handles.
“The shift changes provide an opportunity to recharge the machine before each shift. We use a double input charging system, which fully charges the machine in about 60 to 90 minutes depending on the discharge state of the battery. This means that the machine is fully charged before the start of every shift,” explains Van Blerk.
For this particular application’s requirements, the 856H-E has been equipped with several custom components. For example, because it is deployed to handle a chrome product, which by its very nature has a higher density than several other ores, bucket size has been reduced from the standard 3,5 m³ to 2,5 m³. Because chrome is also quite abrasive, a high abrasive wear package has been added to increase the longevity of the bucket.
In line with the Department of Mineral Resources and Energy’s safety regulations, the machine has been equipped with a proximity detection system (PDS) through a partnership between Nerospec and Schauenburg Systems. The mine already uses this technology on some of its existing trackless mobile machinery. However, the
856H-E becomes the first piece of equipment on site to be Level 9-compliant. The machine has also been equipped with a fully automatic fire suppression system. In addition, the machine has been installed with the new flagship Loadrite L5000 SmartWeigh system supplied by Loadtech. With its wi-fi readiness and touchscreen interface, the L5000 provides more convenience, accuracy and efficiency in loading operations. The system’s wireless connectivity enables seamless data transfer and real-time monitoring. The touchscreen interface offers intuitive and user-friendly navigation, enhancing ease of use for operators.
While operation of the machine is quite similar to that of the conventional 856H wheel loader, Van Blerk says M Civils’ operators had to undergo a familiarisation training programme facilitated by LiuGong and Burgers Equipment & Spares.
The 856H-E MAX features intelligent controls and an operator-focused design, including load-sensing hydraulics, an EAT700 transmission with an electroproportional valve for fast, smooth shifting and independent control of the dual-motor drive for added hydraulic lift.
The LiuGong Intelligent Auto Digging System automatically carries out repetitive digging cycles to reduce operator fatigue. Its electric control box also improves transmission efficiency compared to conventional machines, the company says.
“The 856H-E Max offers the highest levels of safety, visibility and comfort, including full ROPS & FOPS protection and a cab design that significantly reduces dust and noise contamination. Its reliability is reinforced by the IP67-rated wiring harness and waterproof integrated battery package,” concludes Burger. a
ASPASA used the Institute of Quarrying Southern Africa (IQSA) annual conference held at the Elangeni Hotel, eThekwini, South Africa, on 11-12 April 2024 to present its annual Environmental Awards. In a one-on-one with Quarrying Africa, auditor Anthony Bowen says the overall standard of environmental compliance has improved significantly in the industry. By Munesu Shoko.
Two years into the revised ASPASA Environmental Audit, auditor Anthony Bowen is satisfied with the level of compliance that the members of the surface mining association have demonstrated in the 2023 audit.
In 2021, ASPASA announced its all-new environmental audit system for its members. The new system was aimed at simplifying the previous About Face Audit and improving member companies’ ability to undertake
effective environmental management.
The new audit, which kicked off in 2022, has been described as more inclusive than the previous one, with criteria that are easy to understand and implement. The new system also calls for a comprehensive attitude towards environmental compliance, rather than the traditional ‘tick box’ approach.
“The overall compliance level achieved by the ASPASA member quarries during the 2023 audit season was exceptional,” says Bowen. “This was as a result of the commitment and
58
A total of 58 operations was audited, compared with 66 in 2022
dedication shown by management teams, environmental specialists and the employees of the various companies.”
The individual quarry operations, adds Bowen, understand the benefits of ensuring a high level of environmental compliance and putting a strong focus on Environmental, Social and Governance (ESG). “It is encouraging to see the level of commitment that site managers and senior managers place on sustainability and the preservation of the environment,” he says.
While environmental compliance has improved significantly in the past two years, Bowen says there are still a
32 The 2023 audit recorded 32 Showplaces, up from 23 in 2022
ASPASA used the IQSA conference held at the Elangeni Hotel, eThekwini, South Africa, on 11-12 April 2024 to present its annual Environmental Awards
The overall compliance level achieved by the ASPASA member quarries during the 2023 audit season was exceptional
Having been named the top performer in the 2022 online audit, Afrimat Hluhluwe took home the Top Performer (Corporate) Award in the 2023 physical audit
The top performer in the Corporate category of the 2023 physical audit was Raumix Rossway
few issues to address on several sites. These include Environmental Management Programme (EMPr) reviews, incident reporting, oil separator management and maintenance, fuel storage facilities and leak tests, firebreaks and prevention measures (excluding plant fires), repeat findings and fallout dust reports and understanding.
“It is, however, important to note that these issues are generally easily rectified and most sites showed a commitment to pay attention to these areas of concern to ensure that they are addressed,” says Bowen.
Just like in 2022, the 2023 audit was divided into two categories –physical audits (conducted on site) and online audits (done remotely).
A total of 58 operations was audited, compared with 66 in 2022. The reduction in the number of operations audited was because all the Lafarge South Africa quarries did not participate in 2023 due to the
Having been named the top performer in the 2022 online audit, Afrimat Hluhluwe took home the Top Performer (Corporate) Award in the 2023 physical audit.
impending acquisition by Afrimat at the time. The 2023 audit recorded 32 Showplaces, up from 23 in 2022. The online audits garnered a total of 26 Showplaces, with eight from the physical audit.
Having been named the top performer in the 2022 online audit, Afrimat Hluhluwe took home the Top Performer (Corporate) Award in the 2023 physical audit. “Afrimat Hluhluwe is a well-run site and they took the audit document as a guideline to achieve compliance. Housekeeping was very good and the attention to detail was noticeable. The environmental specialist for the region, Ashleigh Vorster, does an amazing job to ensure that all the required documentation and reports are in place,” comments Bowen.
KwaZulu-Natal-based Midmar Crushers, which clinched the Top Performer Award in the Independent Quarries category of the online audit in 2022, was the 2023 top performer in the Independent Quarries category of the physical audit.
“Midmar is well run and there is a wonderful commitment from senior and site management to achieve a high compliance standard. The staff on site are all involved and the cooperation is unmatched. They make use of a good consultant, Ronelle Affinand from Noshcon, and she has made sure that the documentation is always up to standard,” explains Bowen.
The top performer in the Corporate category of the 2023 physical audit was Raumix Rossway. The latest
accolade comes on the back of the 2022 Top Performer Award in the physical audit. “Raumix Rossway was exceptional and demonstrated good leadership and support from the management team as well as the buy-in from all staff. One of the key challenges is the operation’s proximity to a built-up area. However, they have maintained very good community relations which, in today’s operating environment, is critical,” says Bowen.
Blurock Quarries, the 2022 Top Independent Performer in the physical audit, walked away with the Top Performer Award in the 2023 online audit. Bowen commends Blurock for its newly built contemporary office block and weighbridge complex, which is equipped with energy saving and eco-friendly materials.
“For example, the energy-efficient air conditioning and lighting systems have reduced Blurock’s carbon footprint dramatically. The top management team is totally committed to having the least impact on the environment as much as possible,” says Bowen.
Eskay Crushers, which trailed Blurock Quarries by a meagre 0,04%, was also named the Top Independent Performer in the online audit. “Eskay Crushers is run by a small team under the leadership of John Davis and it is 100% committed to achieving a high level of environmental compliance. All the staff share a common goal and have embraced the need to be environmentally compliant. The standard on site is remarkable,” says Bowen. Apart from operational audits, Raumix walked away with the Most Innovative Environmental Project Award. The company, says Bowen, has partnered with a service
Blurock Quarries walked away with the Top Performer Award in the 2023 online audit.
provider to implement a waste recycling project on the majority of its sites. Its environmental compliance levels are monitored at senior management level, and the company has over the years exhibited unparalleled commitment to its ESG programmes. On an individual level, Jacomien du Bruyn (Raumix), Ashleigh Vorster (Afrimat) and Ronelle Affinand
(Noshcon), were recognised for their efforts in advancing environmental compliance. The three ladies each received the auditor’s award for Outstanding Environmental Commitment. The same award was also bestowed on John Davis (Eskay Crushers) and Trevor McAdam (Drift Group). a
Judging by the feedback from exhibitors and interactions with delegates at this year’s Institute of Quarrying Southern Africa (IQSA) conference, there is a generally positive sentiment among the quarrying community, with the construction industry showing signs of recovery amid improved project activity in some major provinces. By Munesu Shoko.
After a turbulent period marked by a protracted economic slowdown and a lack of meaningful investment in infrastructure development, exacerbated by the COVID-19 pandemic, the South African construction industry is showing signs of recovery. This was the overarching message from the IQSA conference, held in Durban from 11-12 April 2024.
Sustained by government’s renewed focus on infrastructure spending, particularly by the South African National Roads Agency Limited (SANRAL), the construction industry has seen a bit of road project activity in recent times. To provide context, SANRAL announced a R28-billion injection into the construction industry for the first half of 2024.
The announcement came after SANRAL closed
77 tenders worth R6,43-billion in December 2023. At the start of this year, SANRAL CEO Reginald Demana noted that the agency was on a mission to accelerate work in the construction industry early in the first half of 2024 with at least another 70 tenders in the first two months of the year.
The optimism in the sector was apparent at this year’s IQSA conference. Firstly, the number of delegates was a little higher than at the previous show. Secondly, several exhibitors who spoke to Quarrying Africa expressed satisfaction with the type of enquiries at this year’s show.
Casper Booyse, regional sales manager at Astec Industries Africa Middle East, noted an upbeat mood at the show. “We have definitely experienced
SANRAL announced a R28-billion injection into the construction industry for the first half of 2024
225 kW
At the heart of the WC1150S is the 225-kW Terex TC1150 cone crusher and a 6’ x 20’ triple-deck screen
As part of its continuous rollout of new products in the market, Terex MPS had a special focus on its new WC1150S, a cone crusher and screen on one wheeled chassis.
Astec Industries AME experienced a positive sentiment at this IQSA conference compared to the previous one
Loadtech used IQSA 2024 to showcase its L5000 SmartWeigh system from Loadrite
Multotec cast particular spotlight on its polyurethane and rubber screening media
Having distributed VEI systems for the past 14 years, DWS has over time gained significant market share in the local load weighing market
a positive sentiment at this year’s show compared to the previous one. We had some good enquiries this year, with customers exhibiting some positivity,” said Booyse.
“To a great extent, the enquiries were about sandwashing plants and concrete batching plants.”
The same sentiment was echoed by Johan Goosen, regional MD – Africa Middle East at Astec Industries, who noted a degree of positivity due to improved
project rollout, particularly in the road sector. However, said Goosen, the project rollout is more regional than national, with provinces such as KwaZulu-Natal and Western Cape enjoying the lion’s share of the ongoing infrastructure projects.
In KwaZulu-Natal, there have been several noteworthy construction developments in recent months. For example, the N2 and N3 upgrades, which form part of the national government’s key Strategic Integrated Projects (SIP2), are ongoing. Another significant project is the construction of the Cato Ridge Logistics Hub, a multi-billion-rand initiative aimed at boosting economic growth and job creation in the region. The hub is expected to provide state-of-the-art logistics facilities to support the transportation and distribution of goods in and around KwaZulu-Natal. In the Western Cape, SANRAL’s upgrades to the N2 are well underway.
“Quarry operators in the KwaZulu-Natal and Western Cape are seemingly busy on the back of several major projects in these provinces. There are definitely pockets of opportunity in these regions, and we hope that this will extend to other areas such as Gauteng,” says Goosen.
“Despite this, we do not believe the improved business activity has translated into capital sales for original equipment manufacturers (OEMs) such as Astec. However, the existing equipment is now being utilised,
and provision of aftermarket support to our customers is important now more than ever to ensure that these machines are kept running to meet project demands,” adds Goosen.
Glen Webster, operations director at Loadtech, noted a growing interest in technology, especially now that mines and quarries are under pressure to improve productivity and efficiency in their
operations. In today’s operating environment, he said, the importance of measuring cannot be emphasised enough.
Loutjie van der Merwe, Loadrite divisional manager at Loadtech, noted an increasing demand for advanced technology integration such as cloud connectivity to enable real-time data monitoring and analysis. In addition, there is also a growing emphasis on accuracy and precision in load-weighing systems to ensure compliance with industry standards and regulations.
In line with these trends, Van der Merwe believes that the new L5000 SmartWeigh system from Loadrite, with its Wi-Fi readiness and touchscreen interface, will revolutionise the industry by providing more convenience, accuracy and efficiency in weighing operations. The system’s wireless connectivity enables seamless data transfer and real-time monitoring. The touchscreen interface offers intuitive and user-friendly navigation, enhancing ease of use for operators.
Overall, the L5000 SmartWeigh system is poised to streamline weighing processes, improve productivity and provide valuable insights for better decision-making in various industries. Its cutting-edge features, Van der Merwe adds, have the potential to change the way weighing systems are used and perceived, making Loadrite a frontrunner in the market.
For the first time, Multotec exhibited at the IQSA conference this year. Pieter Uys, business development manager –Multotec, expressed satisfaction with the level of interactions with the industry.
“We met both existing and potential customers at the show. We cast particular spotlight on our polyurethane and rubber screening media. I believe that there is a lot of scope for improvement in the choice of screen media in the quarrying industry,” said Uys.
Available in a wide range of apertures for various applications, Multotec’s rubber screening panels are ideal for primary applications with high impact areas and abrasion. “Our rubber panels are highly impact-resistant and have a long lifespan, thus ensuring optimal total cost of ownership for customers,” said Uys. Multotec also offers a wide range
Multotec stand at the IQSA conference (Pieter Uys, business development manager, and Sinegugu Gumede, sales engineer).
of polyurethane panels. These are ideally suited for dewatering applications such as sand processing. The screens are expertly manufactured with selfrelieving apertures, resulting in the unrestricted downward movement of any sized particle – reducing pegging and blinding.
“One of the products that has really done well in the quarrying industry is our polyurethane side tension mat. One of the key advantages is that there is no need for any structural change on customers’ vibrating equipment. The solution fastens and tensions the same way as woven wire mesh, but the advantage of the polyurethane side tension is that one gets a longer lifespan. One of our major quarrying customers has seen 12 times more lifespan out of our polyurethane side tension mat compared to the woven wire mesh they had before,” said Uys.
Terex Mineral Processing jointly exhibited with its South African dealer, ELB Equipment. Speaking to Quarrying Africa, Willem du Plooy, regional business development manager – Africa at Terex MPS, was happy with the overall mood at the show. “It has been a while since we last had the type of engagements we had this year at the IQSA conference. The industry is seemingly on an upward trajectory, as showcased by the solid interest in our plants,” said Du Plooy.
As part of its continuous rollout of new products in the market, Terex MPS had a special focus on its new WC1150S, a cone crusher and screen on one wheeled chassis. The WC1150S cone-screen plant is a highperformance, medium-sized wheeled crushing and screening system.
At the heart of the plant is the 225-kW Terex TC1150 cone crusher and a 6’ x 20’ triple-deck screen. A level sensor over the cone crusher regulates the feed to ensure the chamber is continually choke-fed, thus ensuring maximum production and liner life, as well as optimal product shape. The large onboard triple-deck screen allows for the production of sized products from a single plant.
“We have already commissioned four of the new WC1150S units in Africa to date. We look forward to delivering another unit in South Africa during the third quarter of this year,” said Du Plooy.
“The WC1150S is mainly suited for the quarrying industry, especially for single size material such as road base. It is also adaptable to the mining sector, if need be. We find that our wheeled jaws are popular in the mining sector because they are fully electrically driven and tend to be more reliable than their hydraulic counterparts.”
Dynamic Weigh Systems (DWS) used the show to display a range of its VEI load weighing systems. Having distributed these systems for the past 14 years, Ivan van Heerden, MD of DWS, said the brand had over time gained significant market share in the local market and had probably become the number two player in the load weighing system market in South Africa.
“We had a good show this year. In fact, this is always a good show because it is targeted and you get to meet most of the role players in the South African quarrying sector in one place. This year we had a lot of interest in our products. It was also great to see some of our existing clients who have been running some of our systems for more than 12 years and counting. The mood in the construction and aggregates industry at large is much more positive this year,” said Van Heerden.
DWS saw much interest in its wheel loader scales, which is its core business.
“A major talking point is that we offer almost the same technology, with the same operating system and head units, all the way from the face to the load-out section. This allows for ease of training on the system across dump truck operators, excavator operators and front-end loader operators,” concluded Van Heerden. a
The L 120 – 330 double crusher is a heavy-duty, primary and secondary crushing and screening processing plant that includes a primary jaw crusher, a secondary cone crusher and a finishing screen all on one chassis.
Pilot Crushtec International is introducing the Jonsson range of crushers and screens in southern Africa. In an environment where the preference for larger mobile crushing equipment continues to take root, the Jonsson range offers unprecedented crushing capacities and changes the game with the double crusher concept. By Munesu Shoko.
40
Over the past 40 years, Jonsson has supplied more than 350 tracked machines and in excess of 400 wheeled units globally
The biggest jaw crusher in the Jonsson range, the L 160, weighs in at a mammoth 186 tonnes
100
The double crusher is a mobile concept that is unique to Jonsson and has been on the market since 1998. The company has already sold close to 100 machines across the world
When it comes to crushing and screening, conventional wisdom indicates that larger crushers and screens are key to high production. With the range of Jonsson mobile crushers and screens – now available from Pilot Crushtec –mines, quarries and their contracting counterparts in southern Africa can now meet high production requirements at high operating efficiencies.
P.J. Jonsson och Söner is a Swedish mobile crushing and screening plant provider that has traditionally operated in the Nordic Region. Established in 1953, initially trading in fur and eventually construction machinery and used crushing equipment, Jonsson started manufacturing wheeled crushers in 1984, before venturing into the tracked
market in 1998. Over the past 40 years, the company has supplied more than 350 tracked machines and in excess of 400 wheeled units globally.
Following the 2018 acquisition by Metso, Jonsson has been on a drive to expand its business internationally. “Traditionally, we have always had a strong position in the Scandinavia, as well as other markets such as the United Kingdom, Australia and Germany. In recent years, we have embarked on a journey to expand into new markets, including the United States and southern Africa,” says Delbrant.
Adam Benn, Director, Capital Sales, North EMEA, CEA and Southern Africa at Metso, is excited to expand the existing partnership with Pilot Crushtec with the addition of Jonsson to the Pilot stable. Benn is confident that Jonsson will leverage Pilot Crushtec’s strong reputation and successful operations in southern
Africa to achieve long-term growth.
In the past eight years, Pilot Crushtec has recorded massive success with the Metso brand. Testimony to its legendary service to customers in southern Africa, the company has been named Metso’s 2024 Best After Market Distributor and the Second Biggest Lokotrack Distributor globally in the Large Distributor category.
The latest accolades bring the total number of awards won by Pilot Crushtec to five since becoming the southern African Metso distributor in 2016. After bagging the 2017 Best New Services Distributor Award and the 2019 Best Sales Growth Award, Pilot Crushtec was named Metso’s 2022 Distributor of the Year for Europe, Middle East and Africa (EMEA) region.
“Pilot Crushtec’s dedicated focus on crushing and screening has allowed the company to develop, over the past three decades, a profound understanding of the sector, which uniquely positions it to forge long-lasting connections with its customers in southern Africa,” says Benn. “Metso’s multi-brand approach, which started some ten years ago on the back of an aggressive acquisition drive, resonates with Pilot Crushtec, which already offers
P.J. Jonsson och Söner is a Swedish mobile crushing and screening plant provider that has traditionally operated in the Nordic Region
The range complements the existing Metso offering, particularly at the large tonnage, heavyduty end of the crushing and screening scale
Pilot Crushtec believes that the double crusher concept from Jonsson will be a game changer in the local market
a wide range of products in its stable, including its own locally manufactured crushers.”
Commenting on the thinking behind the introduction of the Jonsson crushing and screening products to the local market, Francois Marais, sales and marketing director at Pilot Crushtec, says the range complements the existing Metso offering, particularly at the large tonnage, heavy-duty end of the crushing and screening scale.
“Jonsson crushers are big! They are much bigger than anything that we have in our current Metso portfolio. To provide some perspective, the biggest jaw crusher in the Jonsson range weighs in at a mammoth 186 tonnes (t). Currently, the largest jaw crusher we offer in our Metso range is a 75-t machine,” explains Marais. “The scale of the equipment is unprecedented in the mobile crushing market. One of the primary jaws can take feed sizes up to 1 m, producing up to 1 200 tonnes per hour (tph), depending on the material.”
The introduction of this range, adds Marais, is informed by emerging trends in the mobile crushing market. The move towards bigger crushing gear has taken root in southern Africa in the past four to five years. “One of the major drivers of this trend is the changing face of the contracting fraternity. Traditionally, contracts were long term, allowing contractors to mobilise their equipment for three to five years on a single site. The situation, however, has changed in the past few years, with contracts becoming much smaller and shorter,” he says.
To operate profitably in such an uncertain business environment, contractors are therefore turning to bigger mobile crushing equipment to allow them to execute the fewer jobs more speedily. This allows them to increase the volume of work that they can complete within a certain period.
double crusher – which combines the two Nordberg C120 and GP330 crushers and a screen on one compact tracked chassis – is said to be the only mobile unit of its kind available throughout the world.
Weighing in at 133 t, the double crusher concept comes with a Jonsson JF 1050H vibrating grizzly feeder which discharges oversized material into a Nordberg C120 primary jaw crusher
Weighing in at 133 t, the double crusher concept comes with a Jonsson JF 1050H vibrating grizzly feeder which discharges oversized material into a Nordberg C120 primary jaw crusher. Undersize material passes through an independent Jonsson JS0812 vibrating screen where natural fines are removed and larger material is combined with crushed product from the C120 primary crusher. Crushed material from the primary jaw is transferred to an on-board Jonsson JS1632/3H production screen for sizing. Any oversize material from the production screen is sent back to the GP 330 cone crusher for further crushing. Material is crushed in the cone and returned to the screen. The machine – which is capable of delivering products to two stockpile conveyors – can produce anything between 180 and 500 tph, depending on the type of material.
“The double crusher is a mobile concept that is unique to Jonsson and has been on the market since 1998. We have already sold close to 100 machines across the world, mainly in Scandinavia,” explains Delbrant. “This is a heavy duty primary and secondary crushing and screening processing plant that includes a primary jaw crusher, a secondary cone crusher and a finishing screen – all on the same chassis and a single set of tracks.”
Commenting on the range, Marais believes that the double crusher concept from Jonsson will be a game changer in the local market. The Jonsson L 120-330
“Where customers would traditionally need to mobilise and run three separate machines, we can now bring an entire plant on one compact chassis. This is a unique
proposition for the market; instead of three engines to maintain and three machines to transport, now there is only one,” says Marais.
The Jonsson L 120-330 double crusher, adds Marais, will be a big benefit for mining contractors who, by their very nature, place value on ease of plant movement on and between sites. Once on site, they can mobilise and start production in a fraction of the time that it would take them to establish a traditional fixed plant.
Apart from the double crusher, Pilot Crushtec is adding a range of Jonsson jaw and cone crushers. The models have been carefully selected to complement the existing Metso machines available from Pilot Crushtec. To provide perspective, Pilot Crushtec’s existing Metso jaws comprise the LT96, LT106, LT120 and LT130, offering a production capacity range from 100-700 tph. With the addition of the Jonsson L150 and L160, the capacity range increases from 7001 200 tph.
The L150 is a powerful primary jaw crusher which is equipped with a Norberg C150 jaw which comes with a 1 400 x 1 200 mm Jonsson JF 1460 feeder. This machine can be offered with either a Volvo or Caterpillar engine, depending on customer preference. Fully electric and dual power variants are also available. Weighing in at 136 t, the L150 produces up to 700 tph, depending on the material.
The L160, the biggest jaw in the Jonsson range, is equipped with a Nordberg C160 jaw crusher that can
efficiently process large quantities of hard material. Weighing in 185 t, the machine can produce up to 1 200 tph, depending on material. Testimony to its massive size, the L160 can take feed sizes up to 1 000 mm.
In addition, Pilot Crushtec will offer three large Jonsson mobile cone crushers – the L400, L500 and L550 with a capacity range from 400-550 tph. The range complements the existing Metso cone crusher line – the LT200HP/X/S, LT300HP, LT220D and LT330D – offering capacities from 100-350 tph.
The L550, the biggest cone in the Jonsson range, is equipped with a Nordberg GP550 cone crusher, in close circuit with a Jonsson JF 1030 feeder, a Jonsson JS 1214/3 pre-screen and a Jonsson JS 1623/3 production screen. The typical production capacity, says Delbrant, is up to 360 tph, when producing 0-30 mm material. Weighing in at 99 t, the machine can be transported in three pieces and takes up to three hours to assemble upon arrival on site.
On the screening front, Marais tells Quarrying Africa that Pilot Crushtec will offer the L 354 finishing screen only. The screen can process material up to 400 mm. An independent pan feeder controls the material flow.
The feed material is carried up to an independently running double, three-deck screen, with four product conveyors stockpiling three graded products.
“Of note is that the Jonsson range incorporates Metso crushers, a product that we are familiar with and have the expertise to service and support. With energy efficiency and sustainability in mind, dual-powered and fully electric variants are available across all models,” concludes Marais. a
Since its southern African debut in late 2022, the new generation Liebherr 5.1 wheel loader range – comprising the L 550, L 566 and L 580 – has seen a huge uptake in mining, quarrying, general earthmoving and port rehandling applications. Liebherr-Africa reports that nearly 100 units are now operational across applications, with some customers running double-digit fleets. By Munesu Shoko.
When Liebherr-Africa first introduced the new generation Liebherr 5.1 wheel loader range in southern Africa, Tendayi Kudumba, GM Earthmoving Technology, was adamant that the range was going to usher in a new era with its efficiency, increased tipping loads, larger bucket sizes and more engine power, resulting in up to 25% less fuel burn per hour and 15% higher production compared with the previous 5.0 generation.
Fast-forward to a year-and-a-half later, the range has found favour across numerous applications, including quarrying, construction, contract mining and port handling, confirms Lavell Ruthman, head of sales – Earthmoving Technology at Liebherr-Africa.
Since the launch of the new Gen 5.1, LiebherrAfrica has sold nearly 100 units across the
three model lines. The machines have proven themselves in all environments, from coal mining with bigger buckets, to challenging applications such as chrome and manganese.
“The L 550 has particularly been popular in smaller quarrying applications, vessel loading and roadworks, while the L 566 has gained quick traction at larger quarry sites as well as coal, chrome, manganese and iron ore magnetite mines. With its large bucket, the L 580 has mainly been sold at ports for materials handling,” explains Ruthman.
Commenting on why the machines have seen such a quick uptake in a short space of time, Ruthman says the new L 550, L 566 and L 580 wheel loaders feature Liebherr’s proven hydrostatic travel drive, which is renowned for its efficiency. The Liebherr driveline achieves
25%
The range has a particular design focus on efficiency, increased tipping loads, larger bucket sizes and more engine power, resulting in up to 25% less fuel burn per hour and 15% higher production compared with the previous 5.0 generation
Since the launch of the new Gen 5.1, Liebherr-Africa has sold nearly 100 units across the three model lines
A Liebherr L 566 wheel loader heading to a customer site.
The new generation Liebherr 5.1 wheel loader range – comprising the L 550, L 566 and L 580 – has seen a huge uptake in mining, quarrying, general earthmoving and port rehandling applications
a reduction in fuel consumption of up to 25%. Given that fuel is a major cost driver for loading operations, this reduces operating costs significantly. The L 550 benefits from bigger pumps, Liebherr’s own LH pumps are now used on the L 566 and L 580.
Thanks to increases in engine power, the travel drive is even more powerful while maintaining lower levels of fuel consumption. While the L 566 has maintained the same level of engine power (200 kW) as its predecessor, the L 550 and the L 580 benefit from a power increase of 13% (168 kW) and 9% (219 kW), respectively.
“This is advantageous when accelerating or penetrating material and lowers fleet fuel costs. The wheel loaders carry less dead weight and have ideally positioned fuel tanks which do not affect the static tipping load of the machines as fuel levels change,” explains Ruthman.
Continuous tractive force, combined with automatic limited slip differential, prevents wheelspin, thus increasing
Since the launch of the new Gen 5.1, Liebherr-Africa has sold nearly 100 units across the three model lines
Thanks to increases in engine power, the travel drive is even more powerful while maintaining lower levels of fuel consumption
When designing the new wheel loader range, Liebherr paid particular attention to operator comfort, which is a key parameter in enhancing productivity
productivity, while reducing tyre wear by up to 25%.
In addition, the new range benefits from larger and stronger axles as well as increased operating weights, allowing for a marked increase in bucket capacities and ultimately productivity. The previous generation L 580, for example, weighed in at 25 tonnes (t), while the new improved model has a 27-t operating weight, which allows for a 4% standard bucket capacity increase from 5 m³ to 5,2 m³.
“The new L 550 has a 6% bucket capacity increase from 3,2 m³ to 3,4 m³. While the L 556 retains the same axle as its predecessor, the model also benefits, however, from a standard bucket capacity increase of 4% (4 m³ to 4,2 m³),” explains Kudumba.
With the new range, Liebherr has two lift arm versions on offer. Firstly,
The machines have proven themselves in all environments, including quarrying.
the Z-bar kinematics, which come to the fore particularly in the lower lifting range and for the break-out force. Secondly, the P-Kinematics, which have been designed for working with heavy working tools such as high dump buckets and log grapplers.
Finally, Liebherr also offers the High Lift arms – an extended version of the Z-bar kinematics with the longest lift arms in this wheel loader segment. These ensure greater reach and more productive loading procedures at great heights, which is beneficial when loading railway wagons or lorries with high sides.
The working hydraulics of the wheel loaders have impressed local customers with their larger components and new electrohydraulic pilot control. This technology ensures responsive movements of the lift arms, independent of the size or weight of the working tool.
Liebherr also offers a new, standard weighing device on the basis of the electrohydraulic pilot control. The assistance system works automatically as a check scale and provides real time information about the loading procedure. This data helps machine operators to fill dumpers very precisely with the specified quantities and thus avoids overfilling.
high degree of reliability.
“For this reason, Liebherr has installed larger axles than were fitted on predecessor models. Liebherr has drawn on proven components from its other wheel loaders for the core components and steel construction,” says Ruthman.
When designing the new wheel loader range, Liebherr paid particular attention to operator comfort, which is a key parameter in enhancing productivity. The clean lines on the rear as well as the large glass surfaces in the cab facilitate good all-round visibility. Furthermore, the optional reversing camera, which is installed in a protected position in the engine bonnet, helps the machine operator to keep an eye on the area to the rear.
The previous generation L 580 weighed in at 25 t, while the new improved model has a 27-t operating weight, which allows for a 4% standard bucket capacity increase from 5 m³ to 5,2 m³
The new range offers increased safety thanks to the electrohydraulic pilot control. “The electrohydraulic pilot control enables operators to perform individual adjustments on the new wheel loaders. For example, they can set lift limitations and maximum tilt-out heights, thus reducing the risk of accidents in areas where space is restricted. The tilt-out speed can also be programmed to protect lift arm components and the installed equipment,” says Kudumba.
In addition to these optimisations for operating safety, Liebherr has also invested in the operational reliability of the new wheel loaders, given that they are faced with an abundance of challenges: remote operating areas, extreme climates, demanding loading materials and multi-shift operation over a long period, all demand a
Numerous details that have been seamlessly integrated into the wheel loaders’ exterior design make service work easier.
For example, on the L 566 and L 580, the engine bonnet opens to the rear, making the diesel engine freely and safely accessible.
A sturdy cab access leads to the redesigned and spacious operator’s cab. One of the special features of the cab is the height-adjustable 9-inch touch display with intuitive menu navigation. The high-resolution display provides a clear overview of all the wheel loader’s operating information.
“The new Liebherr control lever enables the highly sensitive control of work movements as part of the modern operating concept. All movements can be done with one hand, while the other hand can always remain on the steering column. Hydraulic working tools, such as the log grappler, can also be precisely controlled with the optional mini joystick on the control lever,” concludes Ruthman. a
As part of its continued rollout of production class equipment, John Deere Africa Middle East (AME) has introduced the new 460P articulated dump truck (ADT). The 42-tonne 460P is one of the first ADT models to come to market under the John Deere Performance Tiering strategy. The machine raises the stakes with increased fuel efficiency and a particular focus on operator comfort and safety. By Munesu Shoko.
Having commenced the rollout of its production class equipment in 2022, John Deere AME has further expanded the range with a number of new machines. The company used its Open Day on 18 April 2024 to introduce new production class models to its dealers and customers. On the stage of the arrival lounge were new products from across various product groups such as wheel loaders, bulldozers, excavators and ADTs.
Of note is that the newly introduced products are the first John Deere machines in the local market branded with the new Performance Tiering
system, confirms Griffiths Makgate, sales manager Construction and Forestry AME. In 2022, John Deere announced its Performance Tiering strategy to give customers the flexibility on deciding which products were suitable for their specific economic and application profiles.
“There are three different equipment levels outlined under John Deere’s Performance Tiering strategy – G-Tier, P-Tier and X-Tier. Each tier has different features, based on customer requirements and expected applications,” explains Makgate.
The G-Tier represents a class of rugged and reliable machines designed for light- to mediumduty applications, without all the ‘bells and whistles’.
10%
With upgraded machine sensors and a revamped routing system, the ADT has 10% fewer connection points than its E-Series counterpart
John Deere AME has launched the 42-tonne 460P ADT, one of the first production class models to come to market under the John Deere Performance Tiering strategy
Available on the 460P are three drive modes – Normal, Eco, Traction – which allow operators to adapt to their situations and enhance the abilities of the ADT to fit their applications
With updated machine sensors and improved routing of both hydraulic hoses and electrical harnesses, John Deere has placed value on enhanced reliability
Following the launch of production class equipment in 2022, John Deere AME has seen a quick uptake of its construction range, particularly in the hard rock mining sector
Designed to promote maximum productivity on a range of jobsites, the P-Tier machines come with enhanced features such as a more spacious cab, an option of EH controls and enhanced linkage designs, amongst others. X-Tier machines feature the most innovative technologies, enabling higher levels of productivity and efficiency.
New to the P-Tier portfolio of ADTs is the 460P, an upgrade to the 460E Series II, which made its local debut in 2022. According to Cory Brant, product consultant – John Deere, what truly differentiates the 460P ADT is its remarkable fuel efficiency. Reduced machine weight, combined with three drive modes, deliver improved fuel efficiency.
Available on the 460P are three drive modes – Normal,
15%
Rollover protection alerts the operator to a potential unsafe dump angle and stops the dump cycle. Set at 15% from the factory, the setting can also be user-defined by accessing the owner setting in the monitor
“The three-year journey has been marked by steadfast commitment to the success of the brand. I will be remiss if I do not take a moment to acknowledge our dealer partners for their devotion to John Deere. Their unwavering dedication to customer support has been instrumental in our success.
Eco, Traction – which allow operators to adapt to their situations and enhance the abilities of the ADT to fit their applications. The drive modes optimise features such as the automatic differential-lock system to reduce tyre wear, improve traction in soft conditions, and reduce axle wear by automatically applying themselves only when needed. Customers will find the drive modes highly valuable for their ease of use, uptime and ride quality.
Normal mode is meant for situations where the truck does not always have to be at full throttle and moving at top speed. Eco mode, when conditions allow, helps reduce fuel consumption by smoothing throttle input, reducing maximum revolutions per minute (rpm) and optimising transmission response for the conditions at hand. This is often the case when you have many trucks in a normal haul cycle.
A completely redesigned dump body allows for improved material retention, lower loading height, lower centre of gravity and reduced transport width.
Reduced machine weight, combined with three drive modes, deliver improved fuel efficiency.
Traction enhances the ability of the ADT to maintain grip in soft and slippery underfoot conditions by applying additional control to the automated differential-lock system and powertrain. Whether the truck is hauling through deep, sticky mud, or just pulling away on a hard gravelly surface, Traction mode locks up four differential locks – one in each axle and one in the transmission. All six wheels will be getting equal torque, getting traction, and ensuring little or no harmful slippage, allowing the fully loaded ADT to move as smoothly and efficiently as possible.
A completely redesigned dump body allows for improved material retention, lower loading height, lower centre of gravity and reduced transport width. Quarry and mining customers will value the bin redesign and lower overall dump-body height (for easier loading and
better material retention) for increased uptime and cycle times.
“The wider bin offers better tyre coverage and easier targeting when bench loading with an excavator. The new side-sheet design makes loading height the same from front to back. The bin rail now features an angled top, helping to reduce material spillage during travel. Tailgate arms have been redesigned to maintain a transport width of under 3,7 m. Changes to the headboard offer increased coverage of the articulation joint,” explains Brant.
With updated machine sensors and improved routing of both hydraulic hoses and electrical harnesses, John Deere has placed value on enhanced reliability. “With upgraded machine sensors and a revamped routing system, the ADT has 10% fewer connection points than its E-Series counterpart. This translates to fewer potential leak points, less friction and a more resilient machine,” explains Matt Costello, product marketing manager, –John Deere.
With a range of features that support ease of use and operator comfort, the 460P was built with the operator in mind. Redesigning the layout of the components in the cab and grouping features together and packaging them in a meaningful way, based on the application, are just a couple of examples of how John Deere has incorporated customer feedback and is delivering further improvements.
Standard on the 460P are a variety of owner and operator settings that help ease operation and increase jobsite safety. The onboard features, such as rollover protection, downhill dump protection, frame protection, hill hold, shuttle shifting and descent control, help
eliminate some of the operator inputs, enabling simplified operation. Additional machine benefits from the machine’s dump body limits, standard transmission warm-up cycle, and maximum speed limits, help to keep the operator and machine safer and up and running for longer.
Rollover protection alerts the operator to a potential unsafe dump angle and stops the dump cycle. Set at 15% from the factory, the setting can also be user-defined by accessing the owner setting in the monitor. Downhill dump protection automatically calculates the truck position to make sure the dump body does not travel over-centre when dumping downhill. With auto dump brake enabled and driveline assist active, the service brakes will latch when unloading the machine.
When stopping on an uphill slope, the truck will automatically keep the service brakes applied while the operator moves their foot from the brake pedal to the throttle to keep the truck from rolling backward. If a dump is stopped before material is shed out of the bin, the truck will cushion the bin travel back to cradle to prevent a full bin from aggressively seating onto the frame.
When activated by the operator, descent control will help automatically control the truck speed when driving down a descent through automatic use of the transmission retarder. At truck start up, the transmission will automatically begin a warm-up cycle. This improves not only ride and shift quality but also increases daily productivity by getting the transmission up to operating temperature quickly.
Three years after the introduction of the John Deere branded construction range in Africa, Makgate tells Quarrying Africa that the brand has enjoyed good
growth. “To meet growing demand for our products in Africa and the Middle East, we have beefed up our Construction and Forestry team significantly, including sales and technical teams. Our dealers have also invested heavily in their people to ensure high levels of customer support,” explains Makgate.
Following the launch of production class equipment in 2022, John Deere AME has seen a quick uptake of its construction range, particularly in the hard rock mining sector. Makgate makes special mention of the ADT and grader ranges as the best-selling products. This is closely followed by excavators, which have done exceptionally well in terms of sales.
3,7 m
“Initially, our ADTs have done well in South Africa. However, in recent times, we have seen increased demand in other African markets. We are truly excited about the addition of the 460P, and more recently the 410P, which made its local debut in May 2024. These models cast a special design focus on efficiency, productivity and safety, and we believe we have the right tools to achieve more growth,” says Makgate.
Apart from products, Makgate reports that there has been increased interest from potential dealers who want to distribute and support the John Deere product in Africa and the Middle East. In addition, the company has also seen a growing base of new customers from across the region.
“The three-year journey has been marked by steadfast commitment to the success of the brand. I will be remiss if I do not take a moment to acknowledge our dealer partners for their devotion to John Deere. Their unwavering dedication to customer support has been instrumental in our success,” concludes Makgate. a
As mines, quarries and construction contractors place more value on increased productivity and efficiency in their operations, Ever Star Industries, the distributor of the Powerstar range of trucks in southern Africa, reports a growing shift from 6x4 to 8x4 trucks, particularly in tipper configurations. By Munesu Shoko.
The importance of productivity, be it in construction or mining, cannot be overemphasised. In construction, productivity is a vital component of any project; without it projects are delayed and budgets quickly become overwhelmed.
Given that the industry’s fundamentals
remain challenged in the short to medium term because of the lack of meaningful infrastructure development projects, particularly in South Africa, it is important for both project owners and contractors to pursue productivity/efficiency improvements.
The same goes for quarries and mines, where operators have in recent years
Traditionally, the 6x4 has always been the best seller, but due to recent growth, the 8x4 now represents 50% of Ever Star Industries’ Powerstar sales
obsessively focused on productivity gains. The industry’s equal focus on productivity and efficiency ensures that output increases over time, costs decrease, resulting in profitable operations, even during quieter periods.
One area where these industries are seeking to improve their productivity and control costs is in equipment selection. For example, one of the growing trends in both construction and mining is the increase in demand for 8x4 axle configurations in tipper trucks, confirms Mike Hawkins, senior manager: 50%
17-t
A Powerstar 6x4 truck offers a 12-t payload on a 10 m³ tipper, while an 8x4 provides a 17-t payload
to recent growth,
Ever Star Industries reports a growing shift from 6x4 to 8x4 trucks, particularly in tipper configurations
The trend has taken root in the past two-and-a-half years, with Ever Star Industries doubling the sales of 8x4 tippers during that period
While the 6x4 stock is readily available, Ever Star Industries has three months’ worth of back orders on its 8x4
The major reason behind the shift from the 6x4 to the 8x4 is the latter’s favourable cost of ownership
WATCH: Scan QR Code to watch Mike Hawkins discuss the growing increase in demand for 8x4 axle configurations in tipper trucks.
Commercial, Ever Star Industries.
In an exclusive interview with Quarrying Africa , Hawkins says the trend has taken root in the past two-and-a-half years. In fact, Ever Star Industries has seen its sales of 8x4 tippers double during that period. Traditionally, the 6x4 axle configuration has always been the best seller, but due to recent growth, the 8x4 now represents 50% of Ever Star Industries’ extra-heavy-duty sales.
While the 6x4 stock continues to be in demand, Ever Star Industries has three months’ worth of back orders on its 8x4 line-up, which
means customers have to wait for up to three months for their new 8x4 trucks. “The demand has caught us by surprise this year,” says Hawkins.
“The major reason behind the shift from the 6x4 to the 8x4 is the latter’s favourable cost of ownership. The 8x4 offers a much higher payload than the 6x4, yet fuel consumption is pretty much on a par between the two. This is why it makes sense for both construction and mining operators to go the 8x4 route,” explains Hawkins.
address the need for more power in
To provide context, a Powerstar 6x4 truck offers a 12-t payload on a 10 m³ tipper, while an 8x4 provides a 17-t payload. Barring the two-tyre difference (a 6x4 runs on 10 tyres and the 8x4 with 12), the servicing costs of the two vehicles are generally the same, increasing production capacity over a 6x4.
Commenting on the preferred configurations, Hawkins tells Quarrying Africa that the 8x4 is used mainly as a tipper truck in South Africa. However, in the rest of Africa, customers prefer it for water tankers for dust
suppression purposes in mining and construction.
and mining conditions,
Ever Star Industries currently offers its Powerstar VX 4035 in the 8x4 segment. Powered by a 350 horsepower (hp) Weichai Euro 2 engine, and the model has been one of the company’s flagship products for years.
To address the need for more power in arduous construction and mining conditions, the company will be launching its Powerstar VX 4042 model powered by a 420-hp Weichai engine this year. The model retains all the features of the existing Powerstar VX 4035, but benefits from a larger engine for more power.
“The Powerstar VX 4042 will make its debut in the next two months. We expect the model to gain quick traction, especially in an environment where customers demand more power to make light work of their tough applications,” concludes Hawkins. a
As part of its product expansion programme, Kanu Equipment South Africa has added three new machines to its ever-growing McCloskey range. Sales specialist Bradley Karolus says the latest arrivals – the J4 Jaw Crusher, the C2C Cone Crusher and the ST100T Stacker – have been carefully selected to address local customer needs. By Munesu Shoko.
The J4’s large 1 060 mm x 700 mm jaw opening accommodates large feed sizes, contributing to higher production in material processing
Power is built into the C2C, with a robust 280 Kw engine on board, and high-capacity fuel and hydraulic tanks to reduce the amount of refuelling intervals
With its durable truss frame, optional large V-Bin hopper and base production capacity of 500 tph, with optional upgrades to 800 tph, the McCloskey ST100TR stands well above the competition
Proper equipment selection that secures the production needs of a project as well as minimising the cost of production is one of the major success factors in crushing and screening operations. To boost productivity and minimise owning and operating costs, mines, quarries and their contracting counterparts are demanding solutions that speak directly to their unique operational needs.
Based on this understanding, Kanu Equipment South Africa has in recent years expanded its McCloskey range by bringing in new models to close gaps in its existing offering. The latest models – the J4 Jaw Crusher, the C2C Cone Crusher and the ST100T Stacker – have been specifically brought in to address identified customer needs in the local market.
“The three machines continue the momentum for our product expansion strategy to meet the exact needs of our customers. The new launches are a true testimony to our commitment to provide solutions that address the various pain
points in our customers’ operations,” says Karolus.
Officially launched to the global market at Bauma 2022, the J4 comes with a range of features aimed at boosting productivity and offering enhanced durability across applications. With Kanu Equipment already offering the J45 for the entry-level market, the J4 addresses the needs for difficult hard rock applications.
The crusher delivers high production due to its innovative Metso jaw chamber design and enhanced material flow. The large 1 060 mm x 700 mm jaw opening accommodates large feed sizes, contributing to higher production in material processing.
The material path is enhanced with the 1 064 mm x 4 247 mm grizzly pan feeder under the hopper that allows for better sizing of material with a variety of mesh options. Options of either a short pan feeder to suit the pre-screen or a double deck grizzly pre-screen are available, ensuring suitability and better sizing of
The C2C delivers high production from material feed to end product stockpile due to its innovative material flow features.
Kanu Equipment South Africa has in recent years expanded its McCloskey range by bringing in new models to close gaps in its existing offering
The latest models – the J4 Jaw Crusher, the C2C Cone Crusher and the ST100T Stacker – have been specifically brought in to address identified customer needs in the local market
Officially launched to the global market at Bauma 2022, the J4 comes with a range of features aimed at boosting productivity and offering enhanced durability across applications
The ST100T Tracked Stacker has a design focus on minimising downtime, a high degree of mobility, all while providing maximised throughput and stockpile capacity
The ST100T Tracked Stacker has a design focus on minimising downtime, a high degree of mobility, all while providing maximised throughput and stockpile capacity.
material based on the application.
The J4 delivers industry-leading stockpiling, with wide main and side conveyors for enhanced material flow. The angle-adjustable 1 200 mm wide ToughFlex main conveyor boasts a 3 912 m high stockpile height, and with quick release and ground level access, the belt is easy to maintain and service.
ToughFlex is constructed with a special weave of two fabric plies and an additional binder warp (without the need for steel wire) resulting in reduced belt weight. The plies are reinforced to resist puncturing and are protected with heavy duty wear-resistant top and bottom covers. At the end of its lifespan, ToughFlex belts can be easily recycled unlike belts reinforced with a metal ply.
“McCloskey engineers have designed the J4 to meet the evolving requirements of today’s projects and operations,” says Karolus. “Despite the large size of the machine, portability has not been compromised. Mobility on-site and between sites continues to be a feature with remote control tracks to easily move and position the crusher and maximise the efficiency of any project site. Also contributing to efficiency, particularly in remote locations, is the high-volume fuel tank, sufficient to run the J4 for approximately 20 hours.”
Technology has been a key factor in the development of the J4, with a 12” DSE control panel for the highest operational performance and reliability providing push button control of the jaw, track and feeder functions. The crusher is fitted with a telematics modem for the new 365SiteConnex programme, a complete connectivity solution for highly accurate monitoring of McCloskey products. 365SiteConnex is based on the latest leadingedge communication technologies to collect, analyse and deliver information on the crushers, screeners and stackers customers rely on to produce the highest quality products with the least amount of downtime.
As with all McCloskey equipment, safety is paramount, and the J4 is equipped with several features to ensure the workplace and the operator are secure. Engine safety shutdown systems, start-up alarms, full safety guarding, external maintenance access and a tagout capability on the isolator all contribute to the safe operation and maintenance of the equipment. Ground level access also promotes safety, and allows for quick service and maintenance, reducing the downtime for the operation.
Featuring the powerful MC200 cone, the C2C brings all the power of a 200 horsepower (hp)cone crusher to a compact footprint that offers high manoeuvrability together with a host of features aimed at boosting productivity in aggregate, construction, demolition and recycling applications.
The C2C delivers high production from material feed to end product stockpile due to its innovative material flow features. A low feed height, large 6,2 m³ capacity Hardox lined hopper allows for stop function, while the unrestricted feed opening improves intake capability and reduces the risk of blockage.
The J4 comes with a range of features aimed at boosting productivity and offering enhanced durability across applications
As the material enters the cone chamber, features including a long stroke and high speed contribute to high productivity, while ensuring the highest quality of end product with variable speed. Multi-layer crushing delivers great capacity, better reduction and shape combined with less liner wear.
As the material moves to the heavy duty 1 200 mm wide conveyor, the large gap between the crusher discharge and main conveyor feeder enhance material flow. Stockpiles are formed up to 3,3 m and, with ground level access, the belt is easy to maintain and service.
Power is built into the C2C, with a robust 280 Kw engine on board, and high-capacity fuel and hydraulic tanks to reduce the amount of re-fuelling intervals. Mobility on-site and between sites is facilitated with remote control tracks that easily move and position the crusher and maximise the efficiency of any project site. The C2C can be setup and ready to work in less than five minutes.
“The launch of the C2C in South Africa is another example of how we seek to deliver on what our customers are asking for,” says Karolus. “We listened to customers who needed the power of a full-size cone, but also the ability to move their equipment easily on and around their sites. There is no compromise in power or productivity with the C2C.”
The ST100T Tracked Stacker has a design focus on minimising downtime, a high degree of mobility, all while providing maximised throughput and stockpile capacity. Diesel power and a main hydraulic lift are both standards in the Tracked Stacker. The 22,5° angle conveyor allows for a high stockpiling height.
The ST100T is designed with a lift axle option that allows for the machine to switch quickly from track mode to radial mode. The lift axle is mounted on the front of the
track bogie, allowing for radial travel. Aggressive tread patterns allow for additional traction on tough terrain.
“With its durable truss frame, optional large V-Bin hopper and base production capacity of 500 tonnes per hour (tph), with optional upgrades to 800 tph, the McCloskey ST100TR stands well above the competition,” says Karolus. “It is a mining spec conveyor built at McCloskey’s Canadian factory and what it sets it apart is the ability to push volumes up to 800 tph.”
Since assuming the dealership of the McCloskey range, Kanu Equipment as a group has experienced massive growth, not only in South Africa but across the other 14 African countries in which it operates. Karolus says one of the key success factors has been the company’s approach to stock availability.
“Due to the fast-track nature of projects in today’s operating environment, customers can no longer afford the traditional long lead times, which is why Kanu Equipment always commits to a large stockholding in our yard,” says Karolus.
Apart from stock availability, the company has in recent times invested heavily in its people to boost its support capabilities. This has resulted in the recruitment of qualified technicians to support customer operations in the field. To provide context, the company now has 15 technicians stationed at its Johannesburg headquarters, as well as seven in KwaZulu-Natal to support the growing customer base in the region.
“In addition, consignment stock for critical projects helps customers avoid downtime. We have also paid particular attention to the flexibility of our financing options to eliminate hassles for our customers. In fact, we have made it easy and affordable to crush rock,” concludes Karolus. a
As part of its Ultimate Women Programme, which is aimed at driving transformation and promoting diversity in the transport sector, UD Trucks Southern Africa has donated a new 65-seater bus to the Commercial Transport Academy (CTA). The Croner PKE 280 bus will be used for the training of female drivers as part of the CTA’s newly launched Bus Driver Development Programme. Munesu Shoko attended the handover ceremony and filed this report.
The concerted efforts to advance women in generally male-dominated environments such as trucking and the transport industry in general is due in part to associations such as the CTA, that are encouraging gender diversity by empowering women through comprehensive driver learnership programmes, with workplace experience, to individuals across Southern Africa. Equally progressive companies such as UD Trucks Southern Africa (UDTSA) recognise the importance of achieving gender equality and equal opportunities
at all levels of the transport sector, including truck and bus driving.
As part of the unwavering efforts to promote and support the inclusion of women in the sector, UDTSA established its Ultimate Women Programme in 2022. The programme’s primary objective is to drive gender transformation in the transport industry. As part of this programme, UDTSA sponsored two Kuzer light-medium duty trucks to the CTA in November 2022 for the training of women truck drivers. After gaining extensive experience in the year-long programme, the women – with the help of CTA –
30%
UDTSA has already worked hard in the past few years to drive diversity, with 30% of the factory employees being women 1%
When the CTA started its driver training programme in 2021, there was less than 1% female truck drivers in the country
UD Trucks Southern Africa has donated a new 65-seater bus to the Commercial Transport Academy
The Croner PKE 280 bus will be used for the training of female drivers as part of the CTA’s newly launched Bus Driver Development Programme
UDTSA’s continued partnership with the CTA is informed by its dedication to empowering women and leaving a lasting legacy in communities in which it operates
Apart from its partnership with the CTA, UDTSA has its internal targets to diversify its workforce
have managed to secure employment as professional truck drivers.
Following the success of CTA’s driver training programme in the past two years, the association, in partnership with the South African Bus Operators Association (SABOA), Clarendon Transport Underwriting Managers (CTU) (a division of Hollard Trucking) and UDTSA, has launched the Bus Driver Development programme. About 30 female trainees will benefit directly from the initiative.
During the Bus Driver Development Programme, participants will undergo extensive training for a period of 12 months. This will cover technical modules such as vehicle operation and control, defensive driving techniques, traffic laws and regulations, as well as route navigation and planning. Furthermore, the programme will have a strong soft skills component, covering critical modules such as stress management, professionalism and effective passenger communication.
“The programme has grown in leaps and bounds since its inception and we cannot thank UDTSA enough for the unwavering support and the lasting impact this has had in the lives of these young women. With the new focus on training bus drivers, we pledge to continue to work closely with all the key stakeholders that we have partnered with to ensure successful completion of the programme,” says Nicci Scott, founder of CTA.
The U.S. Agency for International Development (USAID) funds 80% of the programme, confirms Scott, with the rest coming from private partnerships. Hollard, through its bus division, CTU, has pledged to sponsor 84 women for 12 months’ worth of stipends of R4 782 each per month. Consequently, bus operators who are willing to take them in for on-job experience will only have to top up a small portion of the stipend.
Support and training are critical components in the journey of a female truck or bus driver. Scott is grateful
for the support from UDTSA and various other partners for their commitment to promoting equal opportunities for women in the transport sector.
Filip Van den Heede, MD of UDTSA, says the company’s continued partnership with the CTA is informed by its dedication to empowering women and leaving a lasting legacy in communities in which it operates.
“One of our core values at UD Trucks is to help break down gender barriers and foster a more inclusive transport community. Empowering women and diversifying the workplace is not a programme that is exclusive to UDTSA, but it is an initiative that is driven across the whole UD Trucks organisation, starting from the headquarters in Japan to all markets in which we are present today,” says Van den Heede.
organisation. To showcase our commitment to diversity and inclusivity, we seek to have a 50% women representation across our entire workforce in the next few years,” he says.
Van den Heede commends the CTA for spearheading programmes that seek to empower women to thrive in the transport industry, highlighting that comprehensive training and resources are essential for their success.
“Gender equality is something that is close to our hearts, and we cannot thank the CTA enough for its dedication to the advancement of women in our industry. We feel we are the piece of the puzzle, but the CTA holds the puzzle together by bringing all the various partners together for a common cause,” says Van den Heede.
On the back of the support from the various partners who share the same vision to create a transformed transport sector, Scott highlights that the CTA’s driver training programme has been a resounding success over the past two-anda-half years.
“When we started the programme in 2021, there was less than 1% female truck drivers in the country. Based on the national surveys that we have conducted as part of our Safer Stops Programme, we have seen a 5% female representation in the trucking sector. This change has to a great extent been made possible by this programme,” says Scott, adding that the CTA has a target to have at least 30% women representation in the trucking sector by 2027.
Despite these early successes, Scott believes that challenges still abound.
Apart from its partnership with the CTA, UDTSA has its internal targets to diversify its workforce. The company has already worked hard in the past few years to drive diversity, with 40% of its office bound workforce and 30% of the factory employees being women. This is a significant achievement, especially given that the company only had two women working in the factory some eight years ago.
Based on the national surveys that the CTA has conducted as part of its Safer Stops Programme, it has to date seen a 5% female representation in the trucking sector
“As a business that operates within the transport sector, we are actively taking steps to create a more diverse and inclusive environment, and we believe that this has to start within the confines of our own
One of the key contests is overcoming the mindset that women are not good enough to drive trucks and buses and need at least two years’ driving experience for them to be capable. There is also a general misconception that women are not safe drivers.
“In contrast, female truck drivers are often recognised for their exceptional safety records and strong organisational skills. Studies have shown that women are generally safer drivers than their male counterparts, with lower rates of violations and accidents. This aspect not only makes them valuable assets to the transport industry but also challenges the stereotypes and misconceptions about women’s capabilities in this field,” concludes Scott. a
The plant for the Ghanian granite quarry has been designed and built to produce a variety of aggregate sizes at a production rate of 250 tph.
Quarry Manufacturing & Supplies (QMS) has successfully installed a 250 tonnes per hour (tph) hard rock aggregate plant. Located just outside the capital city Accra, the equipment for the granite quarry has been designed and installed by QMS experts to produce a variety of material sizes for use on infrastructure projects throughout the country.
Based in England, QMS has, since its formation in the 1980s, grown to be one of the United Kingdom’s leading manufacturers, suppliers and providers of aftermarket support of crushing, screening and stockpiling equipment. With a hard-won reputation for providing the equipment, parts and services the industry needs, QMS has recently finalised construction of a bespoke granite plant located just outside the Ghanian capital of Accra. The company was tasked with designing, installing and then supporting the new plant, which is the latest of its installations in Africa.
Following secondary crushing, the material is fed to the first screening station where an SVI-C02M 1,83 m x 6 m double-deck inclined screen produces the first three products
“The plant for the Ghanian granite quarry has been designed and built to produce a variety of aggregate sizes at a production rate of 250 tph. Our equipment has to not only be able to meet the quarry owner’s production targets, but also consistently produce the sizes required to make the quarry a profitable ongoing concern,” explains Jonathan Beck, MD of QMS. “Furthermore, although we will be supporting the quarry throughout its operational lifetime, the plant has to be hard-wearing and easily maintained by quarry staff.”
The plant has been designed and installed to produce six product sizes: 0-5, 6-8, 9-12, 13-16, 17-22
250 tph
The plant for the Ghanian granite quarry has been designed and built to produce a variety of aggregate sizes at a production rate of 250 tph
Quarry Manufacturing & Supplies recently installed a 250 tph hard rock aggregate plant for a granite quarry in Accra, Ghana
The company was tasked with designing, installing and then supporting the new plant, which is the latest of its installations in Africa
Although QMS will be supporting the quarry throughout its operational lifetime, the plant has to be hard-wearing and easily maintained by quarry staff
Given the importance of the granite quarry to Ghana in supplying the material for the country’s urgently needed infrastructure developments, equipment choice was essential
and 23-28 mm from an initial feed size of 650 mm. The feed material initially goes to the primary jaw crusher station. This consists of a QMS 1 200 mm x 750 mm jaw crusher – JB-1275 – with hydraulic clamping and adjustment. In addition, the station consists of a GF 1043 grizzly feeder, a feed hopper and support structure. A primary surge tunnel with vibrating feeder feeds the material to the secondary crushing station which consists of a B3-XC secondary cone crusher with corresponding support structure, including walkways. Following secondary crushing, the material is fed
The plant has been designed and installed to produce six product sizes: 0-5, 6-8, 9-12, 13-16, 17-22 and 23-28 mm from an initial feed size of 650 mm
A primary surge tunnel with vibrating feeder feeds the material to the secondary crushing station which consists of a B3-XC secondary cone crusher with corresponding support structure, including walkways.
to the first screening station where an SVI-C02M 1,83 m x 6 m double-deck inclined screen produces the first three products. Any oversize is now fed to the tertiary feed hopper, which includes a vibratory feeder, before being fed to the tertiary crushing stage. This is undertaken by a QMS B4 cone crusher.
As perhaps the most crucial part of the process, the choice of cone crusher was vital. The rugged yet precise and productive QMS B-Series cone crushers feature a unique hydraulic system which provides automatic overload protection by allowing the head assembly to drop, permitting the passage of tramp iron and other non-crushable material.
The system then automatically returns the head assembly to its original position. The unique design of the hydraulic system means the crusher operates at a definite setting with less setting drift and greater stability throughout the circuit. The crusher setting is instantaneously maintained even after passing a piece of uncrushable material.
“A blend of high motor power, large eccentric throw and increased speed gives the B-Series greater capacity than other crushers of comparable size, whilst the truly modern design creates excellent product shape and can be configured to maximise production of premium single-sized aggregates,” explains Beck.
Following the tertiary stage of crushing, the material is fed along the QMS supplied and installed conveyors to the second screening stage. This consists of an SVI-C03M 1,83 m x 6 m triple-deck screen to produce the final material sizes. As well as providing all support structure, including walkways, QMS designed and installed all
the conveyors as well as provided an electrical package which includes all electrical panels, cabling, and container, as well as QMS’s own in-house full plant automation and sequencing system.
Given the importance of the granite quarry to Ghana in supplying the material for the country’s urgently needed infrastructure developments, equipment choice was essential. Explaining why the quarry chose QMS, Beck says: “We believe we offer a range of crushers and screens that are a match to anyone else’s in the market, with regards to the cost-to-performance ratio. As we are able to support our equipment with our own engineers in Africa and have the industry knowledge to adapt any plant to suit the quarry, mine or aggregate plant’s unique requirements, we believe that our products and service provide the ideal solution whatever the size of operation.”
With the Ghanaian quarry now approaching full operational efficiency, and the country in need of the aggregates that the QMS equipment will help produce, the installation is only the first of many such plants QMS is set to deliver in Ghana and Africa.
“QMS has a reputation for equipment and plant design excellence. Our crushers, screens, feeders, conveyors, process control systems and other associated equipment are now used throughout the world in some of the most demanding of applications,” explains Beck.
Beck adds that the actual installation of a quarry plant is just a primary step as QMS prides itself on supporting its equipment wherever it is found in the world. “We don’t just make and install the equipment; we also support and upgrade all our plants, as well as provide aftermarket care on equipment made by other manufacturers. It is our belief that when a QMS plant becomes operational that is only the start of the story. We provide the expertise, know-how and drive to keep customers’ operations working at full efficiency, as well as carry a full parts inventory for maximised uptime, even in countries many miles from the UK, such as Ghana.
“All at QMS take pride in making sure that our customers are able to be as efficient and productive as possible as long as there is a requirement to do so,” concludes Beck. a
Matthew Armstrong, business development analyst at MAJOR.
As the infrastructure demand increases, so does the need for building materials. Now more than ever, producers must evaluate their operations and ensure they are equipped with the right tools to maximise their production. Here are three considerations to improve an operation’s efficiency and profitability. By Matthew Armstrong, business development analyst at MAJOR.
While it is often overlooked, screen media are a critical factor when evaluating screening efficiency. Where most screen media fall short is in delivering efficient stratification. Highvibration wire screens, on the other hand, are strategically designed to promote material stratification and offer exceptional screening performance.
The unique high-vibration movement accelerates material stratification, causing coarse material to rise quickly to the top of the material bed. Fines and near-size material meets the screen much faster which reduces material recirculation to the crusher and prevents
lost revenue and expensive replacements ‘down the road’.
Issues such as blinding, pegging and clogging will also diminish an operation’s profitability potential. While some screen media is tapered to try to mitigate these problems, their design often limits the extent to which they can resolve severe issues. High-vibration screen media was designed to combat these common challenges. Its independent wires offer high frequency vibrations from hook to hook that prevents material from settling in and on the screen panels.
Screen boxes and screen media in particular take on a lot of day-to-day stress which means staying on top of maintenance in order to prevent costly downtime is crucial. Producers can use vibration analysis technology to get the information they need to prevent unforeseen breakdowns, as well as optimise their vibrating screens for maximum performance.
Vibration analysis technology gathers data on the screen box by measuring parameters such as g-force, stroke, rpm and, in some cases, lateral movement, a measurement not offered by many alternative vibration analysis systems. This allows producers to fine-tune their machine for maximum productivity. If questions come up or further analysis is needed, working with a trusted manufacturer to analyse test results will maximise productivity.
Partnering with an OEM for a customfit screen is an important step towards maximising profits. From troubleshooting and diagnostics to understanding the correct installation of screen media, a reliable manufacturer will be with you every step of the way. When it comes to maintenance or training, manufacturers often offer the service either through site visits or via a nearby dealer. The benefit will be a crew with shared knowledge of proper installation and maintenance that could be worth thousands of dollars in unexpected downtime prevention.
Boosting profits is always a topic for discussion when it comes to staying competitive in the industry. Investing in high-vibration screen media will help achieve heightened material stratification, improved material quality, and ultimately, more profits. a
The JBI Industrial Solutions team installing the PFREUNDT WK60 on a Sumitomo excavator.
During trials at a local Rustenburg-based mine, the WK60 excavator scale recorded loading accuracies of between 96% and 97%
JBI Industrial Solutions, the distributor of the PFREUNDT range of load weighing systems in South Africa, has launched the WK60 hydraulic excavator scale in the local market. With its digital weighing data acquisition, precise measurement and intuitive operation, the system unlocks transparency in material flow. By Munesu Shoko.
The WK60 excavator scale makes its South African debut following its official factory launch in October 2023 80
PFREUNDT has to date seen an impressive uptake, with more than 80 installations since October 2023
JBI Industrial Solutions used the Institute of IQSA conference to officially introduce the new PFREUNDT WK60 hydraulic excavator scale to the South African market
Local mining and quarrying companies are increasingly cognisant of the fact that loading weighing systems play a significant role in optimising their operations
One of the key benefits of the WK60 is the provision of optimal loading of haulers with permissible payload, thus avoiding overloading and underloading
Mine managers can also use the system to track their cycle times and see how long each dump truck takes at the loading point
JBI Industrial Solutions, together with its German principal, PFREUNDT, used the Institute of Quarrying Southern Africa (IQSA) conference in April to officially introduce the new WK60 hydraulic excavator scale to the South African market.
Stephen Luediger, sales manager at PFREUNDT, tells Quarrying Africa that the new excavator scale makes its South African debut following its official factory launch in late 2023. “We initially introduced the WK60 to the
German market in October last year, before rolling it out to the global market at the start of 2024. We have to date seen an impressive uptake, with more than 80 installations in a very short space of time. The feedback from customers has been very positive. We are excited to launch the WK60 in South Africa, a growing market for our systems,” says Luediger.
Jaco Beukes, MD of JBI Industrial Solutions, says local mining and quarrying companies are increasingly cognisant of the fact that loading weighing systems play
a significant role in optimising their operations and are looking to take advantage of the improvements that this technology can make to their loading and hauling operations.
“Every dump truck has a target payload. When that payload is not being measured, it is possible that the truck is not carrying the rated payload in every cycle. At the same time, overloading trucks can cause structural damage, increase fuel burn, reduce component life and negatively impact tyre life. With the WK60 excavator scale, all these issues are addressed to ensure productive and efficient loading operations,” says Beukes.
One of the key benefits of the WK60, says Beukes, is the provision of optimal loading of haulers with permissible payload, thus avoiding overloading and underloading. This helps operators avoid double handling of material by loading the right weight the first time. In addition, operations can optimise loadout operations and track productivity through real-time visibility of material movement.
“With the arrival of the WK60 excavator scale, local quarrying and mining operations can now measure bucket-by-bucket payloads and ensure trucks are loaded accurately the first time. In addition, mine managers can also use the system to track their cycle times and see how long each dump truck takes at the loading point. This helps identify and eliminate any possible bottlenecks in the system to ensure optimal cycle times,” says Beukes. Knowing accurate load cycle counts allows for more effective management of excavators and material. In-
field time stamped reports additionally monitor material inventories and production for easy reporting of loading activity throughout the day. Accurate excavator payloads assist in calculating blast totals. Bucket counts, payload data and trip counts assist mine planning to work closer to mine design, and aids in the planning process for new mines.
With the WK60, mine managers can also track and monitor loading of trucks and tonnes moved on a daily, weekly or monthly basis. Information on the tonnes loaded and moved by each dumper is readily available.
“The WK60 ensures transparency of material flow from the pit to the stockpiles. By analysing and evaluating the recorded data via the PFREUNDT Web Portal, internal material movements can be traced. This helps to optimise operating processes, for example, by avoiding unnecessary idling, thus energy is saved and costs are reduced,” explains Beukes. “By installing this solution, operations can simplify their loading processes and save time and money.”
Before the official launch in April, JBI Industrial Solutions had been trialling the system at a mine in Rustenburg, North West Province. After three months of trialling the system, the mine has expressed great satisfaction. In fact, the operators, the actual users of the system, have commended the WK60 for its ese of use. The operators were quick to understand the system because it offers simple and intuitive operation through a touch display.
“We exposed a total of seven operators to the excavator installed with the WK60 to gauge the accuracy of the system, especially given that each operator has an
individual style of operation. Despite the difference in the level of operating skills, the system recorded loading accuracies of between 96% and 97%. Impressed by the system, the customer has gone on to place an order of
three WK60 scales, marking the first commercial sale in South Africa. Judging by the number of enquiries thus far, we expect to commission more systems during this year,” concludes Beukes. a
Under the ‘Power Up’ theme, DTSA marked the first step towards its quest for sustainable transport at a launch event attended by dealers and customers in Lanseria, Johannesburg on May 21, 2024.
Having become the first truck manufacturer to bring a 100% electric truck to South Africa with the 2020 introduction of the FUSO eCanter, Daimler Truck Southern Africa (DTSA) has commercially launched its eActros range of heavy-duty trucks. The initial range is targeted at distribution applications, with a construction variant only expected in a few years’ time. By Munesu Shoko.
Under the ‘Power Up’ theme, DTSA marked the first step towards its quest for sustainable transport at a launch event attended by dealers and customers in Lanseria, Johannesburg on May 21, 2024. In the arrival lounge was the Mercedes eActros 300, comprising a 4x2 rigid, a 6x2 rigid and a 4x2 truck tractor. In addition, the eActros 400, in a 6x2 rigid variant, also made its debut. The eActros line was joined by six new eCanter units. While the eActros range is immediately available
for sale to customers, the plan for the eCanter entails the rollout of extended collaborative trials with selected customers, confirms Deon de Vries, Head of Sales: Mercedes-Benz Trucks at DTSA. Each of the six available units will be allocated to a customer for a three-month trial period, specifically for in-city distribution.
The objective of the extended eCanter trials is for customers to establish performance and infrastructure requirements to successfully run battery electric trucks in their fleets. The eCanter will
300 km
The eActros 300 is equipped with three lithium-ion battery packs with a battery capacity of 336 kWh and offers a travel range of up to 330 km 2
“While we know that to reach our ultimate goal of offering 100% CO2 neutral products by 2050 will require various zero emission technologies, this launch represents a vital first step for us in building a sustainable future for transportation.
Daimler Truck Southern Africa has commercially launched its eActros range of heavy-duty trucks in South Africa
The range consists of the eActros 300, comprising a 4x2 rigid, a 6x2 rigid and a 4x2 truck tractor. In addition, the eActros 400, in a 6x2 rigid variant, also made its debut
The eActros 300 charges its batteries from 20% to 80% at 160 kW in 1 hour 15 minutes 3
The eActros 400 charges its batteries from 20% to 80% at 160 kW in 1 hour 40 minutes 3
400 km
The eActros 400 is equipped with four lithium-ion battery packs with a battery capacity of 448 kWh and offers a travel range of up to 400 km 4
be available for sale on an operating lease basis after the completion of customer trials.
Data from the International Energy Agency (IEA) shows that transport accounts for 21% of global CO2 emissions. Road transport accounts for three-quarters of transport emissions, which means that the sector is responsible for 15% of total CO2 emissions in the global economy. Against this backdrop, transport demand is expected to grow worldwide in the coming decades as the global population increases and incomes rise. In fact, the IEA expects demand for passenger and freight aviation to triple by 2070. These factors will result in a large increase in transport emissions.
As a major contributor to the global greenhouse emissions, the transport sector should lead the sustainability shift, stresses Maretha Gerber, President and Group CEO at DTSA, who says that major technological innovations such as e-mobility and hydrogen can help offset the rise in demand and the expected increase in transport emissions.
“Our customers are demanding carbon neutral solutions to support their own sustainability strategies. Investors are also looking for businesses that have sustainability at the core of their strategies. Equally, sustainability matters for a healthier environment so that we can beneficially enable the future by protecting the world that we live in, thus allowing for future generations to thrive. It is therefore crucial for us as a pioneer in the global transport industry to commit to decarbonisation and lead the shift to sustainable transportation through the provision of carbon neutral solutions such as the eActros and the eCanter,” explains Gerber.
The launch of the eActros and the eCanter in South Africa, adds Gerber, is a massive feat for DTSA. “While we know that to reach our ultimate goal of offering 100% CO2 neutral products by 2050 will require various zero emission technologies, this launch represents a vital first step for us in building a sustainable future for transportation. We look forward to our customers’ feedback in order to better support them as we tread new grounds,” says Gerber.
The rollout of e-mobility solutions goes beyond products, notes Gerber. With its integrated solutions, DTSA will support customers in all phases of the electrification of their fleets, and also in all areas of their associated processes – from customer-specific eConsulting and digital services such as MercedesBenz Uptime, to financing solutions.
The eActros 300 is equipped with three lithium-ion
battery packs with a battery capacity of 336 kWh 1 and offers a travel range of up to 330 km 2 . The eActros 300 charges its batteries from 20% to 80% at 160 kW in 1 hour 15 minutes 3 . The gross vehicle mass of the eActros 300 rigid variants ranges from 19 to 27 t, offering body and payloads ranging from 8,2 to 16,1 t. The eActros 300 truck tractor has a gross combination mass of 40 t.
The eActros 400 is equipped with four lithium-ion battery packs with a battery capacity of 448 kWh 1 and offers a travel range of up to 400 km 4. The eActros 400 charges its batteries from 20% to 80% at 160 kW in 1 hour 40 minutes 3. The eActros 400 has a gross vehicle mass of 27 t, offering a body and payload of up to 15,4 t.
Justin Barnard, Product Strategy: DTSA, says the maximum energy at which the eActros can be charged is 160 kW, which is equivalent to the total household electricity supply of 10 houses. The system is designed to set the maximum battery charge capacity at 80%, explains Barnard. This is because there is an opportunity to further charge the batteries through recuperation.
Recuperation, commonly referred to as regenerative braking in the context of electric vehicles, is a mechanism that captures and stores energy typically wasted during braking. Instead of solely relying on traditional friction-based brakes that convert kinetic energy into heat, recuperation converts this kinetic energy back into electrical energy, which is then used to recharge the vehicle’s battery.
“During recuperation, the electric motor in the electric vehicle switches over to generator mode when the vehicle is braked. The wheels then transmit the kinetic energy via the driveline to the generator and back to the batteries,” says Barnard.
In terms of batteries, Daimler Truck uses lithium-ion, which has a high energy density. There is, however, flexibility in terms of the number of batteries on the vehicle, depending on customer needs. “Should a customer prioritise payload at the expense of range, we offer a threepack battery solution with a usable capacity of 97 kWh per pack. However, should the customer require range more than payload, we can add an additional battery pack to some of our variants and make it four,” explains Barnard.
This flexibility in battery capacity is made possible by the eAxle, said to be a unique feature to Mercedes-Benz. The eAxle incorporates an electric motor, two-speed transmission and half-shafts to the rear wheels. “All the other OEMs have gone for the so-called central motor mount system – just replacing the diesel engine with an electric motor, but
With its integrated solutions, DTSA will support customers in all phases of the electrification of their fleets.
retaining the transmission, the propshaft and the normal drive axle. This approach takes so much space and is quite heavy,” says Barnard.
With the eAxle, Daimler Truck has integrated two electric motors in the front of the drive axle, along with a two-speed transmission. This allows for a very compact, lightweight and efficient drive axle. Currently, this drive axle configuration is available for the 4x2 and 6x2 variants.
Major concerns have been raised about possible safety issues with high voltage (HV) batteries in electric trucks. Truck batteries can get hot when discharging a lot of energy, such as when climbing up a hill, or during charging. They can also be affected by particularly cold or hot weather. With that in mind, the liquid-cooling within the eActros battery packs helps them maintain a temperature of 20 to 25 degrees Celsius, which is the window in which they are most effective.
From a construction point of view, the batteries are protected by special side crash elements fitted to the frame. The aluminium profile of these elements enables as much energy as possible to be absorbed. Integrated in them are also sensors which can detect a crash situation. In such a case, the HV battery would be automatically isolated from the rest of the vehicle. For emergency service crews, there are additional isolation points located under the seats, with which the HV system can be deactivated.
When switched off, the system ensures within just a few seconds that there is no residual voltage in the HV system (outside of the battery), which would otherwise
Notes:
pose a risk of injury. Besides automatic deactivation, if the driver detects a danger, they also always have the possibility of manually actuating the HV shutoff installed in the cab. When the HV system is deactivated, the drive system and continuous brake function no longer work. If the low-voltage system (24 V) remains activated, the service brakes, lighting, hazard warning lights and steering continue to work.
The eActros 300 and eActros 400 also impress with a wide range of other safety systems. For example, the Active Brake Assist 5, for the first time ever, now operates with a combination of radar and a camera system and can independently initiate braking within the system limits, not only at the tail end of traffic jams, but also when in the vicinity of pedestrians close by, so that collisions will be prevented. Other safety features include Attention Assist, Lane Keeping Assist and Stability Control Assist, amongst others.
The eActros is mostly noiseless in operation. In some cases, this may lead to dangerous situations, for example, if pedestrians or other users only notice the electric truck too late. In order to avoid such dangerous situations, the eActros is equipped as standard with an external Acoustic Vehicle Alerting System (AVAS).
“The acoustic warning system in the eActros comprises two speakers – one at the front and one at the rear of the vehicle. They are connected with one another and with the vehicle. Depending on the driving conditions, sounds for driving forwards and reversing are played. The forwards noise simulates a quiet fan noise, while in reverse, an intermittent two-tone sound is emitted,” concludes Barnard. a
1. Nominal capacity of a new battery, based on internally defined general conditions. This can vary depending on the application and environmental conditions.
2. The range was determined in-house under optimal conditions, among other things, with three battery packs after preconditioning in partially loaded distribution haulage without a trailer with a 4x2 axle configuration at an outside temperature of 20°C and may deviate from the values determined in accordance with (EU) Regulation 2017/2400.
3. The eActros can be charged with up to 160 kW: Based on
figures determined in accordance with company-internal experience, under optimal conditions – including when connected to a regular 400A DC charging station at an ambient temperature of 20 °C – the three battery packs need a little longer than 1 hour to charge from 20 to 80%.
4. The range was determined in-house under optimal conditions, among other things, with 4 battery packs after preconditioning in partially loaded distribution haulage without a trailer at an outside temperature of 20°C and may deviate from the values determined in accordance with (EU) Regulation 2017/2400.
AfriSam
AfriSam is a leading construction materials group in southern Africa. Since establishing its first cement plant in 1934, the company has grown into a formidable construction materials group with operations in South Africa, Lesotho and Eswatini.
www.afrisam.co.za
Babcock
Through several business units, Babcock offers a range of products and services, including construction and mining equipment, engineering solutions for steam generation and power plants, crane hire and gear rental, industrial generators, welding equipment and DAF truck sales and service.
www.babcock.co.za
With more than 16 years of experience in Proximity Detection Systems solutions, Booyco Electronics has supplied over 6 500 sets of mining vehicle equipment installations across southern Africa, as well as more than 55 000 pedestrian RFID installations.
www.booyco-electronics.co.za
Bunting
Bunting’s range of magnetic separators and metal detectors for quarries and mines ensures the protection of crushers, screens and conveyors. Overband magnets, suspension magnets and pulley magnets automatically remove tramp ferrous metal from conveyed quarried rock. www.bunting-redditch.com
IPR
IPR is recognised across the SADC region as the pump, heavy duty slurry handling and dredging specialist operating in underground and surface mining, quarrying, construction, wastewater, petrochemical and oil and gas sectors. www.pumprental.co.za
LOADTECH Load cells Onboard Weighing are specialists in onboard weighing providing complete solutions onboard your heavy goods vehicle, primarily in the application of load cell and transducer systems for payload protection and accuracy in the commercial vehicle sector. www.loadtech.co.za
Pilot Crushtec International
Pilot Crushtec International (Pty) Ltd is South Africa’s leading supplier of mobile and semi-mobile crushing, screening, recycling, sand washing, stockpiling, compacting and material handling solutions. www.pilotcrushtec.com
Sandvik
As a world-leading mining equipment manufacturer, Sandvik Mining and Rock Solutions is committed to improving your productivity and profitability. Our products and services provide you maximum value in terms of performance, quality, safety, flexibility and total economy. www.rocktechnology.sandvik/en/
Astec
Astec Industries has been a global leader in providing innovative Rock to Road™ solutions since 1972, specialising in equipment for asphalt road building and aggregate processing. www.astecindustries.com
John Deere
John Deere offers a comprehensive range of construction equipment, including ADT’s, excavators, loaders, dozers, graders, skid steers and TLB’s, designed to enhance productivity, efficiency, and performance on job sites of all sizes. www.deere.africa/en/construction
Lintec & Linhoff
Lintec & Linnhoff is a global manufacturer and distributor of leading-edge solutions for the asphalt and concrete industries under the Lintec and Linnhoff brand names. Its products include asphalt mixing plants, concrete batching plants, pavement related technologies, and specialist concrete cooling solutions.
www.lintec-linnhoff.com
Schauenburg Systems is a South African company that specialises in providing technology solutions for safety and productivity in mining and industrial markets. It positions itself as an active partner for digital transformation to meet the needs of the “Connected Worker.” The company has a strong focus on innovation and has a brand promise of “Innovation that Saves”. www.schauenburg.co.za
Weir Minerals
Weir Minerals Africa offers a wide range of equipment solutions including pumps, hydrocyclones, valves, dewatering equipment, wear-resistant linings, rubber products, screens and crushers – backed throughout the product lifecycle by high levels of aftermarket support.
www.global.weir
SANY
Sany Southern Africa is a subsidiary of Sany Group, a leading manufacturer of construction, mining and port machinery with over 20 R&D centres and manufacturing bases all over the world. www.sanysouthafrica.com