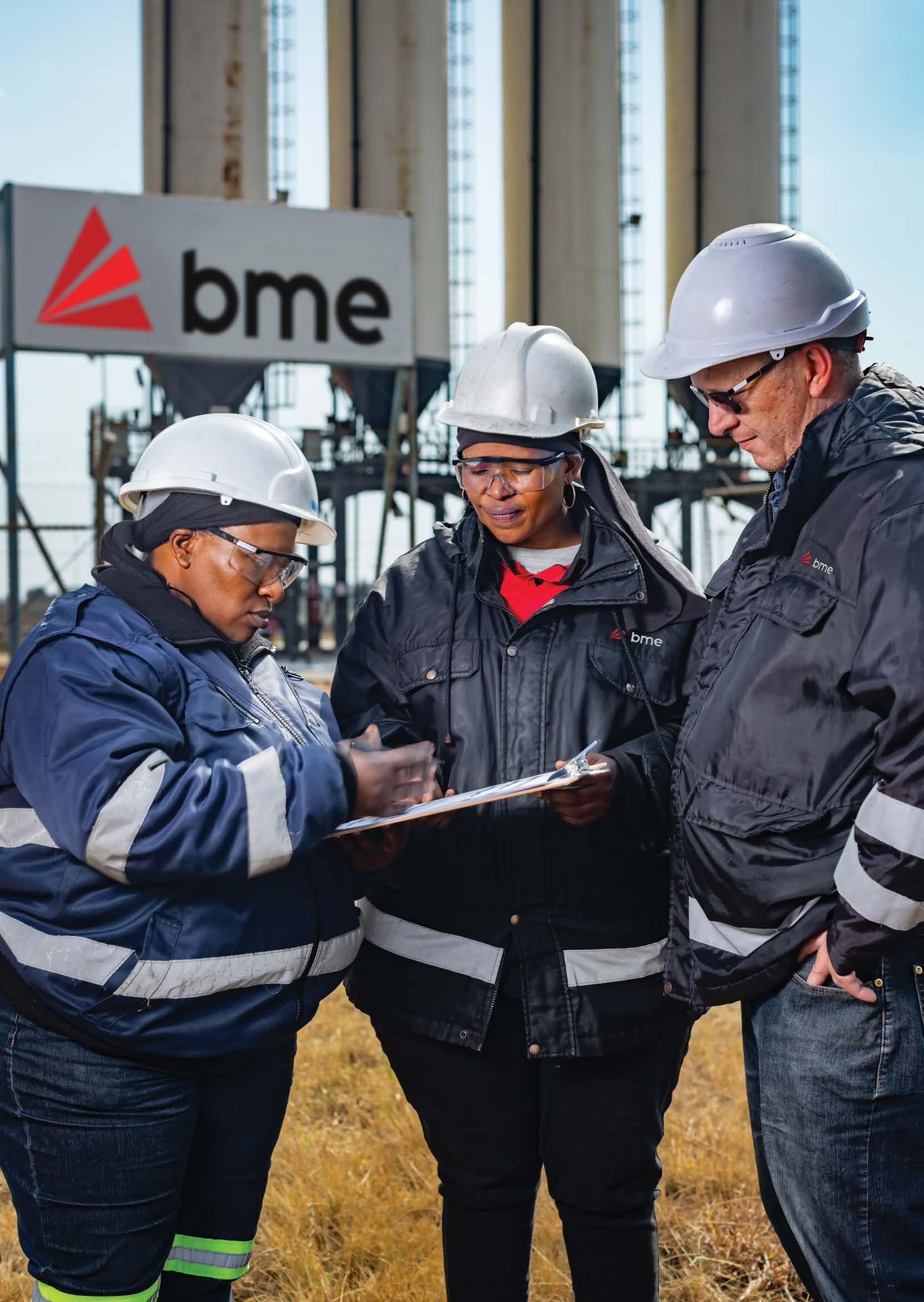


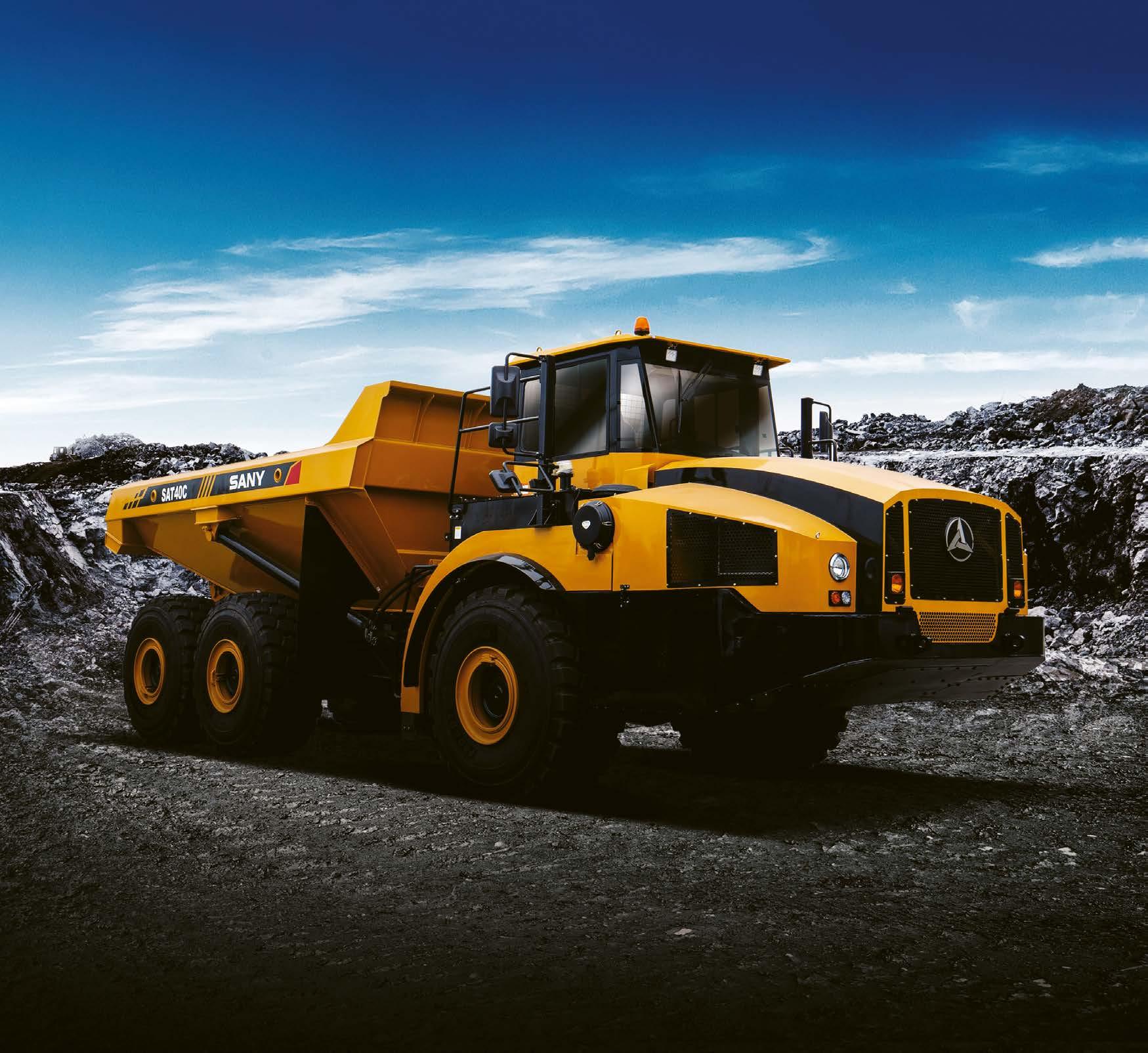
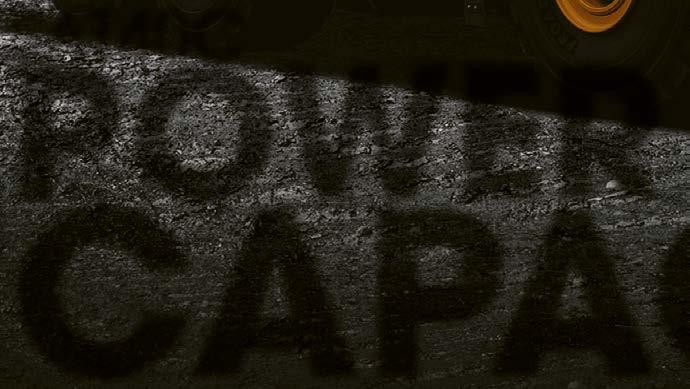
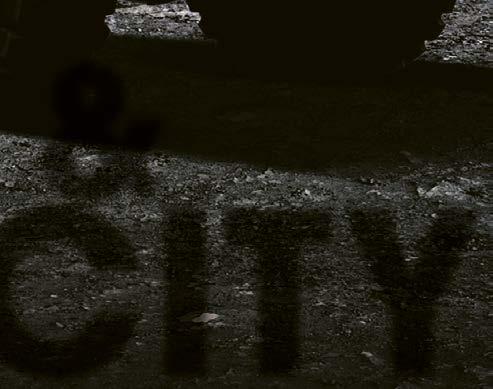
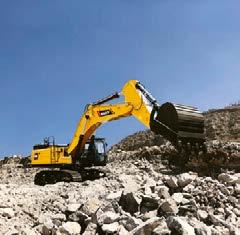

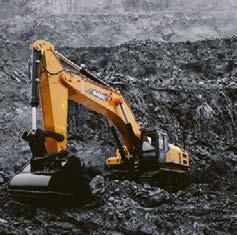
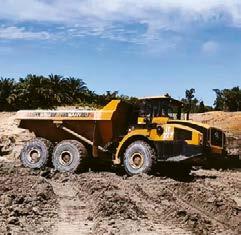
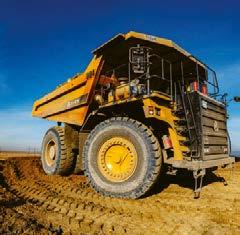
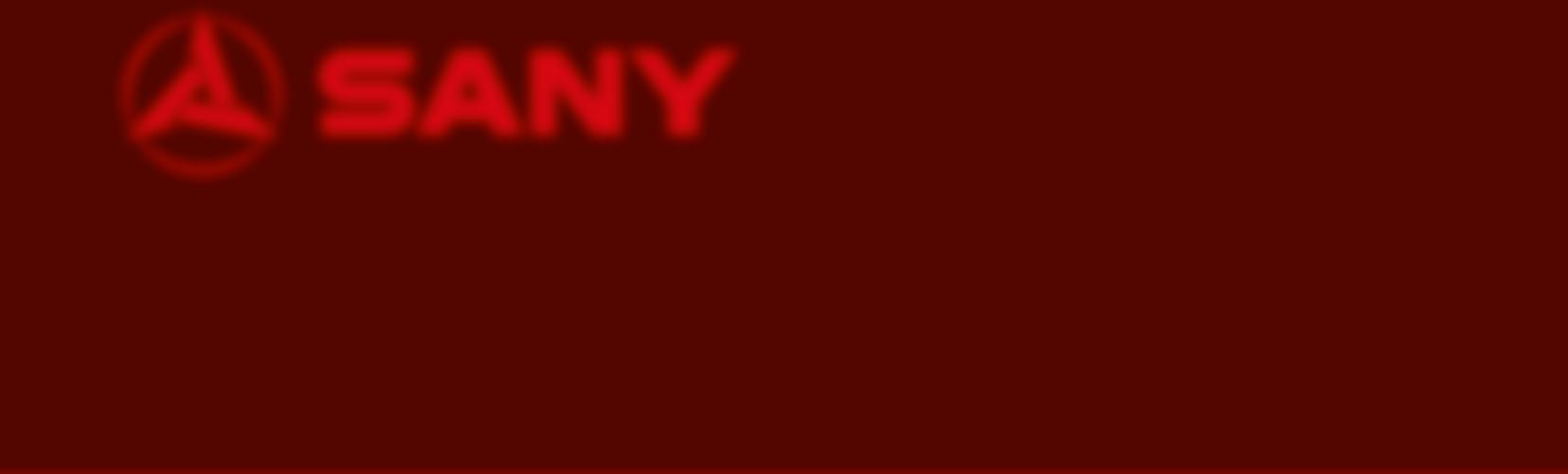
As we bring the curtain down on 2024, one of the key trends we have witnessed this year has been the growing demand for service and maintenance contracts as mines and quarries seek to optimise the health of their mission-critical assets.
The days of trying to convince any fleet owner of the imperative of service level agreements (SLAs) are well and truly over. Many in the industry truly appreciate the immense value, efficiencies and competitiveness that can be unlocked by fully harnessing the power of SLAs.
In my conversations with several executives this year, it is apparent that the demand for original equipment manufacturer (OEM) or dealer service expertise is growing at a rapid pace. One company that comes to mind is Babcock, which has seen an increased uptake of its service contracts in recent years. To provide context, Babcock reports that more than 1 350 Volvo Construction Equipment machines are currently on service contracts.
assets. In addition, contracts offer a predictable cost structure, allowing businesses to plan budgets and avoid unexpected expenses associated with unplanned maintenance events. Another major benefit of service contracts is increased machine uptime. The machines are serviced by experts, thus the scheduled downtime related to maintenance is kept to a minimum. Machines are also serviced according to OEM specifications all the time, resulting in longer asset lifecycles. Specialist technicians may be a better choice for service than internal resources, since they are fully trained on the newest equipment designs and safety procedures.
MUNESU SHOKO
Publishing Editor Email: munesu@quarryingafrica.com
LinkedIn:
Munesu Shoko
Quarrying Africa
As you will see in this edition of Quarrying Africa, Johan Goosen, Regional MD – Africa and Middle East at Astec, also notes that more and more customers, particularly in mining, are becoming reliant on the OEM to provide them with the technical ability. While this trend has taken root in the yellow equipment side of the market, Goosen believes it is only starting to gain traction in crushing and screening.
One of the reasons why local fleet owners are increasingly giving the responsibility of servicing machines to the OEM or the dealer is that it allows them to focus on their core business of production. Service contracts also help mitigate the risk of unexpected breakdowns, reduce costly repairs and extend the lifespan of critical
In a recent conversation with a leading conveyor solutions specialist, one of the key takeaways was that maintenance service contracts are not just a way of controlling and potentially reducing the cost of operation; they are also a safety mechanism. For example, one case study showed a 79% reduction in lost time incidents and a 40% improvement in production using specialty services, which demonstrated payback in days from an annual specialty maintenance contract.
Workloads may preclude staff from maintaining proper compliance or they just might not notice some violations. Outside resources take ownership of the plant’s efficient and productive use of the equipment to improve efficiency, maximise equipment life and safety to add value to the operation.
At the core of the issue is lower operating costs and improved production. The work should match or improve efficiency regarding downtime and throughput. If the criteria of compliance, cost savings and efficiency are met, then the maintenance service contract has provided a tenable ongoing solution. a
Publishing Editor: Munesu Shoko
Sub Editor: Glynnis Koch
Admin: Linda T. Chisi
Design: Kudzo Mzire Maputire
Web Manager: Thina Bhebhe
Quarrying Africa is the information hub for the sub-Saharan African quarrying sector. It is a valued reference tool positioned as a must-read for the broader spectrum of the aggregates value chain, from quarry operators and aggregate retailers, to concrete and cement producers, mining contractors, aggregate haulage companies and the supply chain at large.
Quarrying Africa, published by DueNorth Media Africa, makes constant effort to ensure that content is accurate before publication. The views expressed in the articles reflect the source(s) opinions and are not necessarily the views of the publisher and editor.
The opinions, beliefs and viewpoints expressed by the various thought leaders and contributors do not necessarily reflect the opinions, beliefs and viewpoints of the Quarrying Africa team.
Quarrying Africa prides itself on the educational content published via www.quarryingafrica.com and in Quarrying Africa magazine in print. We believe knowledge is power, which is why we strive to cover topics that affect the quarrying value chain at large.
Printed by:
Email: munesu@quarryingafrica.com
Cell: +27 (0)73 052 4335
In a strategic move aimed at providing end-to-end solutions to the mining value chain – from rockbreaking to mineral processing – Omnia Holdings recently announced the rebranding of its Protea Mining Chemicals (PMC) business under the unified BME brand. The move allows BME to take mining solutions beyond the mining bench and extend the value offering to the milling and comminution circuit.
By Munesu Shoko
40
BME’s 40-year success in the market stems from its ability to deliver futurefit solutions in the mining industry
2
PMC has always been working in the same space as BME and the two brands share the same customers and contribute to the same value chain, which means it makes perfect sense to put both businesses under one umbrella
1
The consolidation of Omnia’s mining offering under one stable unlocks significant value to the global mining value chain by providing solutions in both rock-breaking and mineral processing
he alignment of Omnia Holdings’ BME and PMC brands under a single unified mining division, BME, ushers in a
new era in the global mining value chain. Nishen Hariparsad, GM Technology and Marketing at BME, says the alignment means that the blasting and explosives business previously called BME will now be rebranded as BME Blasting Solutions, while PMC has been rebranded as BME Metallurgy.
Commenting on the strategic intent of the alignment, Hariparsad tells Quarrying Africa that, fundamentally, it should be acknowledged that PMC has always been working in the same space as BME and the two brands share the same customers and contribute to the same value chain, which means it makes perfect sense to put both businesses under one umbrella.
“This allows us to coordinate activities and provide a more cohesive solution to
address our customers’ pain points,” he says. “Everything we do and the strategies we pursue are always consistent with our values, purpose and vision, and this rebrand reinforces our commitment to delivering sustainable future-fit solutions for the industry. Having blasting solutions and metallurgy in one basket allows our customers to unlock value and efficiency, as well as optimise yield and improve their operations.”
As part of the rebrand, Omnia’s mining business will focus on two revitalised offerings, BME Blasting Solutions, specialising in explosives and initiation systems, and BME Metallurgy, dedicated to mining chemicals and metallurgical solutions for enhanced mineral recovery.
“BME’s 40-year success in the market stems from its ability to deliver futurefit solutions in the mining industry. Over the years, the company has evolved to offer a set of activities and products that deliver value beyond blasting, hence BME Blasting Solutions,” says Hariparsad. “On the other hand, the mining chemicals
Omnia Holdings recently announced the rebranding of its Protea Mining Chemicals (PMC) business under the unified BME brand
The alignment means that the blasting and explosives business previously called BME will now be rebranded as BME Blasting Solutions, while PMC has been rebranded as BME Metallurgy
This alignment ensures BME takes mining solutions beyond the mining bench and extends our value offering to the milling and comminution circuit
From improved fragmentation, optimal blast outcomes to increasing recoveries, enhancing metal grades and improving yield – the value proposition that BME has for the market is unique, targeted and holistic
business has over the years consistently raised the bar in adding value to respective mining chemistries, whether in the base metals space or other mineral fields, hence the name BME Metallurgy, which speaks to the mineral and metal sciences domain.”
Commenting on the synergies between the two offerings, Hariparsad says the consolidation of Omnia’s mining offering under one stable unlocks significant value to the global mining value chain by providing solutions in both rock-breaking and mineral processing. These two processes are closely linked, coming at the beginning and
“This alignment ensures BME takes mining solutions beyond the mining bench and extends our value offering to the milling and comminution circuit. From improved fragmentation, optimal blast outcomes to increasing recoveries, enhancing metal grades and improving yield – the value proposition that BME has for the market is unique, targeted and holistic.
Hariparsad, GM Technology and Marketing at BME
end of the mining phase. The quality of blasting on a mine, for example, affects how effectively minerals can be liberated in the process plant.
“The BME Metallurgy function offers a selection of services downstream of the milling and comminution circuit, while BME Blasting Solutions is instrumental in the upstream value share of our mining customers’ operations. Together, the two brands are stronger and geared to offer a holistic solution to the industry,” he says.
Adding to the synergies, Hariparsad says both BME Blasting Solutions and BME Metallurgy operate in an environment plagued by consistent operational challenges and technical conundrums. The current pain points range from poor fragmentation and environmental concerns through to lower production efficiencies, yield inefficiencies and increased energy consumption, amongst others.
The rebranded BME business, says Hariparsad, allows BME to tackle these challenges with a dual focus – upstream and downstream of the mill circuit – for the sole purpose of providing a comprehensive solution to the industry.
“The synergy is about delivering efficiencies – be it production efficiencies, yield optimisation or environmental efficiencies – across the mining value chain. Under the BME Blasting Solutions banner, we have always had innovative blasting solutions that are instrumental in delivering consistent feedstock to the mill circuit. With BME Metallurgy, we can now take it further by providing performance chemicals that are key to optimising yield extraction and improving purity grades,” he says.
Commenting on the value proposition, Hariparsad says the alignment gives mining customers enhanced access to a fully integrated value proposition and solution. “This alignment ensures BME takes mining solutions beyond the mining bench and extends our value offering to the milling and comminution circuit. From improved fragmentation, optimal blast outcomes to increasing recoveries, enhancing metal grades and improving yield – the value proposition that BME has for the market is unique, targeted and holistic,” he says.
Another key aspect of the value to the customer is the safety that BME ensures in terms of handling, storage and applications, as well as supply chain solutions for procurement and transportation. Customers, adds Hariparsad, can rest assured that the aligned BME will meet the highest levels of compliance in both blasting solutions and mining chemicals.
In addition, he says, the rebranding strongly aligns with the purpose of Omnia, which is “innovating to enhance life, creating a greener future”. Both BME Blasting Solutions and BME Metallurgy contribute to sustainable and cost-effective mineral liberation.
“Energy efficiency in particular is taking centre stage in the mining industry. Electricity is an expensive utility requirement for the energy-hungry mining industry. Good blasting techniques can reduce energy consumption in mines by improving the quality of feedstock to the crushing plant, which, in turn, can lead to less energy being used in the crushing and screening stages. Through tailored performance chemistry we are also able to reduce energy consumption for customers, which not only reflects positively in their balance sheet, but also helps meet their sustainability goals,” concludes Hariparsad. a
With over 40 years of expertise, BME integrates Blasting Solutions and Metallurgy to deliver a complete mining solution. From precision explosives and initiation systems to advanced chemical and metallurgical processing, we optimise the entire mining value chain – enhancing performance, profitability, and efficiency.
As a global industry player, we’re committed to sustainability and safety, providing innovative solutions that minimise environmental impact while maximising operational safety. Our technical expertise spans key regions, including the Americas, Africa, Indonesia, and Australia.
From humble beginnings crushing 6 m³ of aggregate per week using a laboratory crusher back in 1965, Eskay Crushers has over the years grown to be one of the flagship quarries in South Africa. Despite its small size, the quarry is setting the bar high in terms of both productivity and compliance. By Munesu Shoko.
Located in Piet Retief, a small town situated in Mpumalanga province, South Africa, Eskay Crushers was founded some 60 years ago by Bob Hawker, initially producing a meagre 6 m³ of aggregate per week. Robert and Phillip Hawker, the two sons of the late founder, took over from their father in the early 70s, building the business up to its current status.
Speaking to Quarrying Africa, MD John Davis relates how, in the founding days, a construction contractor, the only client at the time, would come to fetch a single 6 m³ truck load of material every Monday. Over the years, the business has grown gradually to become the formidable quarry operation it is today. This is despite the fact that it is located in a very small town with very limited and cyclic construction activity.
One of the defining moments in the history of the quarry, says Davis, was when it clinched a contract to supply material for the construction of a major railway line within its vicinity. In fact, that contract funded the construction of the current processing plant back in 1982. Over the years, the plant has been upgraded to improve both production and efficiency.
The major talking point, however, is how Eskay Crushers is setting the bar high in terms of compliance, not only in health and safety, but also in environmental management. To provide context, the operation was among the top four quarries in the 2023 ISHE Audit, a stringent annual health and safety audit conducted by surface mining association, ASPASA. With a 95,88% score, Eskay
95,88%
With a 95,88% score, Eskay Crushers ranked fourth in the 2023 ISHE Audit, highlighting its commitment to health and safety compliance
150 tph
As a result of the plant upgrades and fine-tuning of the existing plant setup, Eskay Crushers has been able to increase its plant production capacity from 100 tph to 150 tph
Located in Piet Retief, a small town situated in Mpumalanga province, South Africa, Eskay Crushers was founded some 60 years ago by Bob Hawker, initially producing a meagre 6 m³ of aggregate per week
Over the years, the business has grown gradually to become the formidable quarry operation it is today. This is despite the fact that it is located in a very small town with very limited and cyclic construction activity
The major talking point, however, is how Eskay Crushers is setting the bar high in terms of compliance, not only in health and safety, but also in environmental management
Continuous improvement is the name of the game for Eskay Crushers, which is important in helping the team identify weaknesses, improve processes and enhance innovation and efficiency, while maximising employee engagement
Crushers ranked fourth in the 2023 ISHE Audit.
In the same year, the operation was named the Top Independent Performer in the online version of the Environmental Audit, highlighting its commitment to environmental management on site. In fact, Davis received the auditor’s award for Outstanding Environmental
Commitment, recognising his efforts in advancing environmental compliance.
For Davis, however, compliance is not about scores; it is about creating a safe working environment that allows every worker to return home to their families unharmed every day. Equally, environmental management is not just about creating a favourable environmental profile, but more about building a legacy for the next generation.
“I commend ASPASA for its efforts in helping us with our compliance management. Under the association’s guidance, the industry has upped its game in terms of compliance. For me, however, our efforts over the years are not about scoring a high mark in the audit; it is more about ensuring continuous improvement. Every year, we recognise our shortcomings and try to improve on that. Our achievements in recent years are a culmination of these small, continual improvements,” he says.
While the operation is passing the compliance test with flying colours, Davis says that compliance by its very nature is not without challenges. Compliance can be expensive, he says, more so for a small operation of Eskay Crushers’ stature. All operations, irrespective of size and operating profile, must adhere to a variety of rules and principles. Having to play on the same playing field as the bigger players and the mainstream mines with a bigger purse can be challenging, but it has to be done.
“Although we are doing it according to the lawbook, I believe there could be better ways to make safety easier to implement. However, I understand why the regulator makes it complicated to comply; the overarching intent
Having initially been installed in 1982, the plant has benefited from major upgrades in recent times.
is to ensure that we create a safe working environment to achieve the industry’s quest for Zero Harm,” says Davis.
Central to Eskay Crushers’ safety and environmental excellence is a team that shares a common goal and has embraced the need to work safely all the time and to be environmentally compliant. “We promote a team ethic across our operation. We treat each other with dignity and respect, which is key for us to work pulling together towards a common goal. Without the team, we would not be able to achieve what we have achieved,” he says.
Continuous improvement is the name of the game for Eskay Crushers, which is important in helping the team identify weaknesses, improve processes and enhance innovation and efficiency, while maximising employee engagement.
focus on proper documentation, a parameter which sounds basic but is one of the true cornerstones of good compliance practices.
“One of the major initiatives we are busy with on the health and safety side is trying to bring our work in line with the written procedures, or vice versa. In many cases, operations end up with procedures that state one thing and people doing it in a different way,” says Davis.
In addition, competence within the team is critical. Competencies can help employees identify areas for improvement and advance all areas of the business. To ensure a competent workforce on site, management at Eskay Crushers places a high value on continuous on-the-job training for its 26 workers and a few contractors on site. Continuous training, he says, helps employees improve their skills and knowledge, which can lead to higher performance levels. The quarry also makes use of knowledgeable consultants, who fill some of the crucial knowledge gaps and form an integral part of the Eskay Crushers team.
Commenting on some of the initiatives implemented on site, Davis makes special mention of the unrelenting
On the environmental side of things, Davis says one of the focus areas has been alien vegetation control, which is continual by its nature. Controlling alien vegetation in mines and quarries is important because invasive plants can threaten biodiversity, water resources and the environment.
The other focus area is water management and, in particular, stormwater control which, due to the quarry being on a slope that starts right at the top of the operation and ends in the Mkhondo River, is of vital importance. Waste management and rehabilitation of disturbed areas are other key focus areas of the environmental management plan.
Community relations is another big focus area for Eskay Crushers. The quarry strives to forge close relationships with its immediate neighbours and works hard to implement its social and labour plans. This, says Davis, is no easy feat, but remains work in progress.
Eskay Crushers mines and processes a competent granite rock. One of the key challenges on site is the complex geology – the rock is a granite-quartzite mixture with many intrusions, which makes it difficult to blast. Unlike a
dolerite rock which turns out to be blocky and fragments well during blasts, the type of rock at Eskay Crushers has weathered top layers and complex jointing sets, which lead to loss of energy during blasts, resulting in poorer fragmentation, characterised by big boulders.
One of the interventions in recent times has been the appointment of a blasting contractor that brings a wealth of knowledge to blast effectively in the face of the challenging geology. “In addition, we have adjusted the size of the burden to hole diameter ratio, spacing to burden ratio, stemming length to burden ratio, and ultimately the charge/powder factor, which is the relationship between the explosive and the rock mass. These all have a big effect on the level of fragmentation,” explains Davis.
The challenge, however, is to get the right balance between these blasting techniques and some of the recent blasting requirements from the regulator to ensure safety. For quarries, one of the biggest challenges is their proximity to communities and existing infrastructure. In line with the requirements of South Africa’s Regulation 4.16(2) of the Mining Health and Safety Act’s Explosives Regulations of 2018, quarries need to acquire a licence to blast within 500 m of structures.
“We have recently done one Code of Practice (COP) for minimum standards on ground vibration, noise, airblast and flyrock near surface structures and communities. To some extent, we find these requirements to be counter-productive to good fragmentation. There is almost a trade-off between fragmentation and health and safety, and the latter has to win. We are continuously fine-tuning our blasting parameters to ensure that we can still achieve good fragmentation while meeting these requirements,” says Davis.
Eskay Crushers operates a very complicated plant. To
provide context, the secondary and tertiary parts of the plant alone have a total of five crushers, five screens and 24 conveyor belts. This, however, allows the team to produce a range of products with ease.
Generally, the quarry produces various sizes of washed roadstone – 7 mm, 10 mm, 14 mm and 20 mm. This is complemented by normal concrete stone in various sizes – 20 mm, 26 mm and 37 mm. In addition, the operation produces different sizes of crusher run such as G1, G2, G4, G5 and G7, as well as handstone for gabion baskets and ballast for railway lines. On average, the quarry currently produces about 8 000 tonnes per month (tpm), which can be pushed up to about 30 000 tpm when demand is high.
Having initially been installed in 1982, the plant has benefited from major upgrades in recent times. For example, the team installed a Trio 12x52 granulator as a secondary crusher in recent years, as well as an Osborn SBS 38H gyro as a tertiary crusher. In addition, a new vertical shaft impact (VSI) from Techroq has just been installed to improve the shape and quality of the product.
The quarry is also currently busy with the installation of a new primary crusher, an Astec 3042, which replaces the old Astec (previously Osborn) 2536 which was installed in 1982. Davis commends the durability, simplicity and resilience of the Astec offering, which has served the company well for over 40 years with no issues.
“As a result of these plant upgrades and fine-tuning of the existing plant set up, we have been able to increase our plant production capacity from 100 tph to 150 tph. With the addition of a new primary crusher, we expect to ramp up to 200 tph. The idea is to increase our tonnes per hour – which allows us to work the same hours but produce more. Apart from increased productivity, this offers the benefit of reduced input costs related to wear and tear and electrical costs,” concludes Davis. a
Different quarries need different cone crushers. Weir Minerals is the only global manufacturer that offers both. TRIO ® live and xed shaft cone crushers are made for modern quarries with advanced hydraulics, wear resistant materials and the latest technology. You get what’s right for your circuit. No unnecessary redesigns needed. Plus, with a lifelong commitment from the Weir Minerals global network, we’ve got you covered. Visit info.global.weir/trio
Some three years after Astec’s famed move to unify its 16 brands under the OneASTEC business model, a move which reinforced the group’s ‘Rock to Road’ strategy, a solid foundation for future growth has been laid. In a one-on-one with Quarrying Africa, Johan Goosen, Regional MD – Africa and Middle East at Astec, unpacks the impact of the strategy to date, industry trends shaping the market and his outlook on the business. By Munesu Shoko.
The launch of the OneASTEC business model in 2021 ushered in a new era for Astec and its customers throughout the world, and the same impact has been experienced in the Africa Middle East (AME) region. Having previously focused on the Osborn brand alone, says Goosen, the Rock to Road strategy, a key lever of the OneASTEC business model, has allowed Astec AME to expand its product range significantly, thus opening up new markets and allowing customers to acquire most of their capital equipment requirements from one source.
The company’s operations are divided into two
primary business segments. Material Solutions incorporates aggregate, material handling and processing solutions, including crushers, screens, apron feeders, rock breakers and bulk material handling equipment. Infrastructure Solutions encompasses road building, asphalt and concrete plants, as well as thermal and storage solutions. Living up to the Rock to Road billing, Astec now offers equipment for every phase of the road construction process – from quarrying, crushing and processing the aggregate, to concrete production and road surfacing – providing more than a hundred products to customers in the aggregates, construction, infrastructure and mining value chain.
2030
Astec Industries has a strategic growth plan to double its global business at group level by 2030
With the networks that the company has created, Astec Industries AME expects to see exponential growth in the next two to three years
Some three years after Astec’s famed move to unify its 16 brands under the OneASTEC business model, a move which reinforced the group’s ‘Rock to Road’ strategy, a solid foundation for future growth has been laid
The impact of the Rock to Road strategy has been twofold – product growth and footprint growth, both of which are central to the growth of the Astec business
To support its expanded product portfolio in such a big market area, the company had to develop a formidable channel-to-market, while maintaining a direct-to-market approach in South Africa
Looking ahead, Astec Industries AME has a twopronged approach to growing its business – sales and manufacturing
“The impact of the Rock to Road strategy has been twofold – product growth and footprint growth, both of which are central to the growth of our business,” says Goosen. “To date, I believe we provide the broadest product portfolio of any other original equipment manufacturer (OEM) in the world in the Rock to Road value chain, which gives us a competitive edge.”
The product growth has also had a massive impact on Astec AME’s local manufacturing activities. Traditionally home to the Osborn range only, which in itself represented one of the widest ranges in the comminution and material handling space, the Astec AME manufacturing facility has added several other products to its local manufacturing portfolio.
For example, the production of Astec Industries’ Titan series cone crushers for the market outside of the US is relocating to South Africa. The group’s Johannesburgbased Astec South Africa division will start with manufacturing of the T200 at its Elandsfontein facility during the first quarter of 2025. The production of the rest of the range of Titan cone crushers, including the T300, T400 and T500, will follow soon after the T200.
The strategy is geared at optimising Astec’s international manufacturing footprint and maximising efficiencies within Astec’s Materials Solutions group. It also forms part of Astec’s drive to consolidate operations and to become more flexible in production capabilities in order to meet customers’ demands within the regions.
However, adds Goosen, from a business growth perspective, the Rock to Road strategy has not yet realised its full potential. This is largely due to the macro-economic environment in South Africa, where project owners such as the South African National Road Agency Limited (SANRAL) and municipalities have been under pressure in recent years, leading to a depressed infrastructure development market.
“We have, however, started to see an uptick in construction activity in the past 12 months, with SANRAL bringing several meaningful projects to the market. Consequently, we have also started to see some good movement of our products into these projects. For instance, we recently demonstrated our new Astec RX-600ex-4 cold planer on the R21 highway rehabilitation in Gauteng. We have also just supplied our Astec SB-3000 Shuttle Buggy and other road building equipment to projects in the Western Cape,” explains Goosen.
While the local market has not fully capitalised on Astec’s Rock to Road capability, Goosen is positive that the product awareness created over the past three years has laid a solid foundation for future growth, especially at a time when construction projects are starting to come to market.
“Customers are now aware of what we have from a product perspective and the performance of our equipment. Going into 2025, we are confident that we will start seeing this awareness turning into sales. We have both the inventory and support in place to fulfil the needs of the market,” he says.
Apart from product expansion, another significant impact the strategy has had is the growth of Astec’s footprint in Africa and Middle East. To support its expanded product portfolio in such a big market area, the company had to develop a formidable channelto-market, while maintaining a direct-tomarket approach in South Africa.
Over the past three years, Astec AME has appointed highly qualified dealers across the region to provide sales and service support to customers. To date, the company has a total of 12 dealer partners in the region, with some of them responsible for several countries in their territories.
One example is Unatrac, which is part of the Cairoheadquartered Mantrac Group, offering sales and support
services for all of the equipment in Astec Industries’ Material Solutions division in Nigeria, Ghana, Sierra Leone, Liberia, Kenya, Tanzania, Uganda, Egypt, Iraq and the Ural and Volga regions in Russia. Meanwhile, French company Aramine is the official dealer of Astec Material Solutions products in several strategic countries in West Africa (Mauritania, Mali, Senegal, Guinea, Ivory Coast, Burkina Faso, Benin, Togo and Niger) and the Maghreb (Algeria, Tunisia and Morocco).
In southern Africa, Astec AME has dealers in strategic countries such as Namibia, Zimbabwe and Zambia, among others. The company has recently appointed Elite Crushers & Hydraulics as its dedicated agent in Botswana. This follows hard on the heels of the recent appointment of Zinpro RDC SARL in the Democratic Republic of Congo (DRC), a key market to date.
While it has taken time to establish the brand and the product simultaneously in most of these regional markets, Goosen is confident that the dealer partners are now well equipped to sell and support the product in their respective markets, and opportunities are starting to come through. With such a strong dealer network, the company has once again built a solid foundation for growth. The past three years, declares Goosen, have been about creating the base, and now it is time to reap the rewards.
“We have a strategic growth plan to double our global business at group level by 2030. As Astec AME, we have an even more ambitious target to do a lot more than that. With the networks that we have created, we expect to see exponential growth in the next two to three years,” says Goosen.
Commenting on some trends observed, Goosen starts by highlighting the global move towards newer solutions such as electric and hybrid equipment. These
are driven by the Environmental, Social and Governance (ESG) agenda. While developed markets have gone further down this road, Goosen believes that the local market is still lagging behind.
Another trend of note, he adds, is the growing need for information and access to information that the equipment generates as customers seek to make data-informed decisions to optimise their operations. This has been a major product development strategy for Astec Industries in the past few years.
In fact, the company has made some major acquisitions of technology-focused companies in the United States and Europe to reinforce its digital solutions offering.
The acquisition of MINDS allowed Astec to enhance its equipment solutions for asphalt road building, aggregate processing and concrete production with a suite of plant automation and control systems. The March 2022 transaction followed Astec’s November 2020 purchase of Grathwol Telematics. These acquisitions were instrumental to the launch of ASTEC Digital, a game-changer for the Rock to Road industry, offering customers greater control, efficiency and sustainability.
Closer to home, says Goosen, one of the notable trends is that more and more customers, particularly in mining, are becoming reliant on the OEM to provide them with the technical ability. While this trend has taken root in the yellow equipment side of the market, Goosen believes it is only starting to gain traction in crushing and screening.
“The need for OEM technical support from a crushing and screening point of view is growing. Whereas in the past we would only be required to come out to assist with major breakdowns or a major liner change on a big machine, we are starting to see the need for man-on-site type of arrangements. This is largely due to the fact that mines are struggling with competence to support their own equipment,” reasons Goosen.
Looking ahead, Goosen tells Quarrying Africa that Astec Industries AME has a two-pronged approach to growing its business – sales and manufacturing. On the back of the product expansion and footprint extension in recent years, the next step is to drive sales to grow the business.
The other part of the growth strategy is to further grow the company’s manufacturing capability in South Africa. In an environment with a relatively lower labour cost base than developed markets such as the United States and Europe, there is huge potential to grow local manufacturing for export markets.
However, says Goosen, the downside is a challenging economic environment that makes it difficult to sustain manufacturing businesses and allow them to flourish. “As a country, we need to have discussions on how we can sustain manufacturing-led growth and become competitive on a global scale. A strong local supply chain is critical for the full realisation of our local manufacturing capabilities,” says Goosen.
To close the skills gap, Astec AME is investing heavily in its skills development programmes. To provide context, the company has vibrant learnership, apprenticeship and internship programmes aimed at supporting its manufacturing capabilities by creating the much needed competency to become globally competitive. The company will also continue to invest in its Elandsfontein manufacturing plant to allow for the addition of more product lines.
“For example, in 2025 we will be launching a range of standard skip-mounted modular plants. These will be made in our Elandsfontein manufacturing facility for the rest of the Astec group. These will be targeted at junior miners and aggregate operations,” concludes Goosen. a
A fleet of John Deere 410P articulated dump trucks (ADTs) has given NVJ Legacy, an upcoming mining contractor, a firm base for growth in such a cutthroat trading environment. Delivered on a John Deere rental facility in September this year, the two ADTS are deployed in a 24/7 coal stockpiling application, delivering high levels of performance, availability, productivity and fuel efficiency. Munesu Shoko was recently on site and filed this report for Quarrying Africa.
Having previously run a different brand of ADTs, NVJ Legacy first switched to John Deere in May this year, initially taking delivery of two 42-t 460P articulated haulers and a 744P wheel loader in a stockpiling application at a coal mine in Mpumalanga, South Africa.
After carefully evaluating its operational needs, the mining contractor concluded that the 42-t rated payload articulated haulers, together with a 744P wheel loader, with a 26 630 kg operating weight, were somehow too big for the operation at hand.
Taking advantage of the flexibility of the John Deere rental facility, NVJ Legacy swapped the existing fleet for two 38-t 410P articulated haulers and a midsized 724P wheel loader with 19 859 kg of operating weight. The smaller machines, says Victor Lepotho, operations director at NVJ Legacy, are correctly sized
NVJ Legacy first switched to John Deere in May this year, initially taking delivery of two 42-t 460P articulated haulers and a 744P wheel loader
Taking advantage of the flexibility of the John Deere rental facility, NVJ Legacy swapped the existing fleet for two 38-t 410P articulated haulers and a mid-sized 724P wheel loader, which fit its operational needs
The John Deere rental division was established to offer flexible and cost-effective equipment solutions to the market
Rental gives contract miners such as NVJ Legacy access to the equipment they need with minimal upfront costs and credit constraints associated with outright purchasing
The machines are deployed to haul processed material (-50 mm) from the processing plant to the stockpiles.
NVJ Legacy is contracted to stockpile processed material (-50 mm), moving about 5 000 t per day, which equates to about 200 000 t per month
The current fleet of 410P machines is running between 350-400 hours per week, and has to date done just over 1 000 trouble-free hours, achieving a massive 99% availability
The dealer comes out to service the machines at 500-hour intervals, allowing NVJ Legacy to focus on its core business, which is production
Taking advantage of the flexibility of the John Deere rental facility, NVJ Legacy swapped the existing two 42-t 460P units for two 38-t 410P articulated haulers
The fleet has to date done just over 1 000 troublefree hours, achieving a massive 99% availability.
for the scope of the contract, which entails the hauling of processed material (-50 mm) from the processing plant to the stockpiles, moving about 5 000 t per day, which equates to about 200 000 t per month.
Commenting on what necessitated the switch to John Deere, Lepotho tells Quarrying Africa that the team first stumbled upon a fleet of John Deere ADTs working at a certain coal mine in Mpumalanga. Aware of the John Deere reputation in the farming sector, the management team investigated the performance of these machines. Feedback from that mine was positive, which generated increased interest from NVJ Legacy.
To gather more information on the machines, the NVJ team attended the John Deere Open Day on 18 April 2024, where the original equipment manufacturer (OEM) introduced new production class models to its dealers and customers. Of note is that the new products that made their debut on the day were the first John Deere machines in the local market branded with the new Performance (P) Tiering system, including the 460P and the 744P.
itself in such an unforgiving business environment.
“As a start-up, we have to prove our capabilities before our scope of work can be expanded, which is critical to our growth. How best do we do it? By maintaining high levels of machine availability, productivity and efficiency. The John Deere rental facility has given us access to new premium gear without having to ‘break the bank’. To date, the machines have helped us to prove our mettle at this particular contract. To provide context, the current fleet of 410P machines is running between 350-400 hours per week, and has to date done just over 1 000 trouble-free hours, achieving a massive 99% availability,” says Lepotho.
With fuel constituting a major portion of any mine’s operational costs, the fuel economy of the 410P has been impressive to both the contractor and the mine. Given that the mine runs a “wet contract”, it keeps track of each contractor’s fuel bill.
The John Deere 410P haulers have proven to be a cut above the rest on site, with the fuel consumption way below the mine’s benchmark.
Upon further discussions with both John Deere and the dealer, NVJ Legacy was thrilled to learn of the John Deere rental facility which, according to Lepotho, was ideally suited for an upcoming contractor seeking to establish
To cater for the various needs of the market, John Deere recently introduced a rental facility through its dealers.
Griffiths Makgate, sales manager Construction and Forestry AME at John Deere, says the Rental division was established to offer flexible and cost-effective equipment solutions to the market.
Rental, adds Makgate, gives contract miners access to the equipment they need with minimal upfront costs and credit constraints associated with outright purchasing. Renting also reduces the need for a down payment and allows mining contractors, especially start-ups such as NVJ Legacy, to redirect the little cash they have to other
pressing areas of their business.
“Rental makes sense for most emerging mining contractors such as NVJ Legacy. Buying new equipment comes at a huge upfront cost, which most start-ups cannot afford. Given the growing local procurement strategy in mining, where local mining contractors are given preference as part of mining companies’ enterprise development efforts, rental makes sense for these young companies,” says Makgate.
With the John Deere rental fleet serviced and maintained by the dealer, NVJ Legacy has eliminated the headache associated with servicing own equipment, keeping parts and employing a dedicated service team on site.
“The dealer comes to service our machines at 500-hour intervals. This gives us the opportunity to focus on our core business, which is production. If there is a possible issue, the JDLink™ telematic portal is quick to pick it up and issues are resolved timeously,” says Lepotho.
Having run the 410P – which made its local debut in May this year – for about two months, Lepotho has been impressed with the performance of the truck. Of particular interest is the power and speed with which the ADT goes about its duties on site. Operators have also been impressed by the comfort of the truck.
The quiet, pressurised cab of the 410P features an easy-to-read monitor and rear-camera display plus an optional automatic temperature control (ATC) system that allows operators to simply select a desired temperature to get and stay comfortable. Standard highback air-suspension seat adjusts multiple ways for all-day support. Operator comfort, says Lepotho, translates into productive operations.
With fuel constituting a major portion of any mine’s operational costs, the fuel economy of the 410P has
been impressive to both the contractor and the mine. Given that the mine runs a “wet contract”, it keeps track of each contractor’s fuel bill. According to Lepotho, the John Deere 410P haulers have proven to be a cut above the rest on site, with the fuel consumption way below the mine’s benchmark.
This is made possible by the three drive modes –Normal, Eco, Traction – which allow operators to adapt to their situations and enhance the abilities of the ADT to fit their applications. Normal mode is for situations where the truck does not always have to be at full throttle and moving at top speed. Eco mode, when conditions allow, conserves fuel by smoothing throttle input, reducing maximum revolutions per minute (rpm) and optimising transmission response to match prevailing conditions. Traction applies added control to the auto-differentiallock system and powertrain to maximise traction over soft and slippery ground.
Lepotho is also impressed by the JDLink™ connectivity service, which makes it easy for the mining contractor to stay connected and on top of its business. With this technology, NVJ Legacy has been able to run data-driven operations, tracking various operational parameters such as machine location, engine hours, fuel level, machine performance, idling times and machine health data.
“All things considered, we are very happy with our decision to opt for John Deere. Firstly, the machines have performed beyond expectations, putting us in good stead to get our contract scope expanded. Secondly, we are grateful to John Deere for its partnership. Despite the fact that we are just a small company, they treat us like any other big customer. The service has been impeccable and the rental facility speaks directly to our operational needs. In future, even when the procurement profile shifts to outright purchase, we will remain loyal to John Deere,” concludes Lepotho. a
RMS utilises a datadriven study of abnormal behaviour in terms of both crusher performance and health to generate tangible remedial action informed by data.
To help customers make data-driven decisions and improve productivity, sustainability and overall cost efficiency, Sandvik Rock Processing has introduced Remote Monitoring Service (RMS) in Africa, initially on a pilot basis. The digital solution analyses crushing data to identify abnormalities and develop predictive solutions to increase uptime and reduce operating costs. By Munesu Shoko.
RMS is the latest addition to Sandvik Rock Processing’s suite of digital technologies, joining the Automation and Connectivity System and SAM by Sandvik cloudbased digital assistant
The alerts from RMS, available 24/7, help to reduce high wearing of crusher components, which is detrimental to material consistency and has negative cost implications
With RMS, mines can expect improved safety, a crucial parameter for an industry that is driving for Zero-Harm
s quarries and mines seek to optimise their operations and ensure continuous improvement, remote monitoring of crushing data is becoming a crucial element of day-to-day procedures. To meet this growing need, Sandvik Rock Processing is for the first time piloting its RMS in Africa.
Nils-Peter Ahlqvist, Sales Support Manager Africa & Latin America – Crushing Division at Sandvik Rock Processing, tells Quarrying Africa that the trial regime in Africa follows hard on the heels of successful pilot projects in other regions of the world. In fact, there are already a few customers who are running it on a commercial basis elsewhere in the world.
While RMS is new to the crushing business, explains Ahlqvist, it is an established technology in underground mining, where sister company, Sandvik Mining and Rock Solutions has deployed it for many years, including southern Africa. This provides ample lessons and reference points for Sandvik Rock Processing as it rolls out the technology for the first time.
RMS is a new set of advanced digital services. The system is designed to translate vast amounts of data acquired from Sandvik crushers into actionable recommendations, thus reducing operating costs and boosting productivity and sustainability. RMS, explains Ahlqvist, is the latest addition to Sandvik Rock Processing’s suite of digital technologies, joining the Automation and Connectivity System (ACS) and SAM by Sandvik cloud-based digital assistant. ACS is a platform that delivers real-time performance management, enabling operators to monitor and optimise crusher performance and productivity. SAM by Sandvik collects information from all connected Sandvik equipment to provide a complete overview of the entire operation. Customers can look at the status of their connected equipment, communicate across teams, view alerts and notifications, proactively order spare parts, and much more.
“With RMS, we are bringing to market a next-level digital solution that complements our existing ACS and
SAM by Sandvik solutions. The ACS is where the data originates from, before it is fed into SAM. With RMS, both customers and Sandvik experts can now access crushing performance data and alerts in SAM from anywhere in the world. This represents a new leg in our digital revolution,” says Ahlqvist.
“That, combined with our expertise in comminution, allows us to offer customers next-level support through real-time monitoring of equipment and help with proactive recommendations to improve cost optimisation, equipment utilisation and driving more productive operations,” he adds.
RMS utilises a data-driven study of abnormal behaviour in terms of both crusher performance and health to generate tangible remedial action informed by data.
In essence, Sandvik experts continuously monitor and analyse crushing data remotely. They can identify root causes for any alerts or abnormalities reported by the system and then develop actionable recommendations before catastrophic failures occur.
“RMS is taking proactive maintenance to another level by using data acquired from the equipment, merging it with Sandvik Rock Processing’s technical expertise, a vast global pool of reference data and in-depth analytical skills to produce actionable recommendations for continuous improvement of mining operations,” says Ahlqvist. “In
“RMS presents a daily overview of the crushing fleet, including effective operating hours, energy efficiency, location of equipment, alarms and parameter changes. We also provide customers with a monthly report of what happened and what needs to be done in the future to avoid previous abnormalities the system would have picked up.
As quarries and mines seek to optimise their operations and ensure continuous improvement, remote monitoring of crushing data is becoming a crucial element of day-to-day procedures
To meet this growing need, Sandvik Rock Processing is for the first time piloting its Remote Monitoring Services (RMS) in Africa
RMS is a new set of advanced digital services. The system is designed to translate vast amounts of data acquired from Sandvik crushers into actionable recommendations
RMS utilises a data-driven study of abnormal behaviour in terms of both crusher performance and health to generate tangible remedial action informed by data
addition, it presents a daily overview of the crushing fleet, including effective operating hours, energy efficiency, location of equipment, alarms and parameter changes.
We also provide customers with a monthly report of what happened and what needs to be done in the future to avoid previous abnormalities the system would have picked up.”
Through RMS alerts, Sandvik Rock Processing was recently able to make actionable recommendations to avoid a potential catastrophic crusher failure for a customer. “Having received non-stop alerts via RMS, our technicians advised the customer to stop the crusher immediately. Upon inspection, it was discovered that the crusher was about to burn a bush, which would have caused a lot more damage to the crusher itself. This allowed the client to only replace a minor part of the crusher, instead of a possible major overhaul as a result of a catastrophic failure,” says Ahlqvist.
With RMS, mines can expect increased efficiency within their operations. Continuous analysis of real-time data round-the-clock helps operations get the most out of their equipment, minimising downtime and maximising uptime. Higher uptime translates into higher machine utilisation, which in turn reduces cost per hour.
In addition, the data gathered on crusher performance makes optimisation easier with the ultimate goal of enhancing business performance. The alerts, available 24/7, also help to reduce high wearing of crusher components, which is detrimental to material consistency and has negative cost implications.
With RMS, customers can monitor, analyse and optimise energy consumption to reduce waste and maximise efficiency. Running efficient operations also results in lower carbon emissions. This is particularly important in mining, where stakeholders not only pay attention to the profitability of a mining operation, but also expect clear results in decarbonisation and sustainability at large. RMS therefore helps customers achieve larger tonnage output with fewer emissions, while extending the life of the equipment and its components.
“With RMS, mines can also expect improved safety, a crucial parameter for an industry that is driving for ZeroHarm. The technology allows operators and technicians to monitor crushing equipment from the comfort of an office on the mine or even at the head office, thus taking them out of harm’s way. Having less people in the process plant reduces the risk of safety incidents,” concludes Ahlqvist. a
The introduction of the Metso HRC 8 high pressure grinding roll by Pilot Crushtec International marks a new era in the southern African manufactured sand market. The machine takes sandmaking to the next level by producing significantly more fines than conventional crushing, while offering improved shape and gradation at a much lower cost of operation. By Munesu Shoko.
With sourcing of sand from natural sources such as rivers and coastlines outlawed in many African countries, manufactured sand is proving to be the most economical and ecological alternative. Yet, the production of sand using conventional crushing solutions such as vertical shaft impact (VSI) and cone crushers has its limitations.
Before VSIs became as common as they are now, cone crushers were preferred, but they are an uneconomical way of producing sand. The downside
50%
The HRC 8 consumes up to 50% less power in sand production compared to other technologies for the same volume of net product
The HRC 8 uses a method of inter-particle comminution by drawing in a bed of material between two rotating rollers
The rollers, one of which is in a fixed position and another floating, generate an extremely high pressure that is applied to the layer of material between the rolls, extruding the feed material down to the desired smaller grain sizes
The HRC 8 can provide a notable increase in throughput. The flange design maximises the amount of material that is crushed by pulling the feed into the crushing zone
By reducing energy consumption and increasing wear life of components, the HRC 8 helps lower operational costs
is that for cone crushers to produce sand, one needs to crush with a very tight closed side setting (CSS), which by its nature is not economical because of the extremely high wear it causes, plus some other adverse operating conditions as a consequence of this requirement like high power demand and continuous ring bouncing condition due to the fines generated, with further
130 To date, Metso has some 130 HRC machines operating in the world, with 80% in manufactured sand, and the rest in quarrying and reprocessing
“Due to its ability to produce very fine material with fewer unwanted microfines in the final product, we believe that in some applications, the HRC 8 may eliminate the requirement for washing.
damages to the machine main components.
While the VSI has proved itself as the ultimate sandmaker, producing high-quality manufactured sand with a consistent shape and gradation, it is inherently a power-hungry machine, which makes it unfavourable, especially in an environment where energy efficiency is becoming a principal parameter. Depending on the application conditions, VSIs high circulating loads and wear rates, could make the operation cost intensive.
In addition, the VSI is highly dependent on constant feed material, which means there is a high possibility of excess fines. To mitigate excess fines in sand-making, washing has become a go-to solution for ultra fines removal. Given the water shortages in southern Africa and several other regions on the continent, washing is often out of the question.
Considering these challenges, Francois Marais, sales and marketing director at Pilot Crushtec, believes that the introduction of the HRC 8 marks a new era in manufactured sand and aggregate production. The HRC 8, he says, has a completely different crushing principle from other conventional solutions such as impact crushing.
The HRC 8 uses a method of interparticle comminution by drawing in a bed of material between two rotating rollers. The rollers, one of which is in a fixed position and another floating, generate an extremely high pressure that is applied to the layer of material between the rolls, extruding the feed material down to the desired smaller grain sizes. The HRC 8’s adjustable pressure allows customers to vary the curve grading for finer or more coarse grading.
Some six years ago, Metso became the first global aggregates equipment manufacturer to introduce an HPGR crusher in manufactured sand and aggregates. Oldemar Meneses, product manager, HRC Technology at Metso, says the move was informed by the realisation of a gap in the market for a machine that could produce fines with fewer unwanted microfines (0,075 mm) in the final product. Customers, he says, were also looking for a machine suitable for difficult applications where waste material from the crushing and screening processes
(material with low mass gradings, difficult to crush by a VSI or other types of compression crushing) could be processed to obtain a high quality sellable product.
“To help customers address these pain points, the HRC 8, based on Metso’s existing HRC 800, was introduced in 2018, specifically for the manufactured sand and aggregate industry. The HRC 8 works in applications where traditional cone and VSI crushers cannot. It can handle material that is small in size and very difficult feed materials that are challenging to process by any other technology, even those with high abrasiveness, low crushability, high moisture and fines,” explains Meneses.
tph
The uptake of the technology in the sand market has been remarkable.
To date, Metso has some 130 HRC machines operating in the world, with 80% in manufactured sand, and the rest in quarrying and reprocessing.
The HRC 8 is the ultimate solution for the manufactured sand market where fines must meet a defined end product specification. The quality of sand can be adjusted and optimised, thus reducing the amount of cement and asphalt required in concrete mixes or asphalt. The machine produces a gradation according to customer needs and delivers a perfect cubical shape for concrete and asphalt sands.
In some applications, non-sellable waste materials can be reprocessed by the HRC 8 to correct the gradation curve and particle shape, converting them into highvalue sellable products. This not only addresses the cost factor, but also speaks to the manufactured sand sector’s drive for sustainable operation.
“In typical sand-making with VSIs, for example, there is generally a high percentage of ultra fines – the unwanted 0,075 micron material, which calls for wet processing. Due to its ability to produce very fine material with fewer unwanted microfines in the final product, we believe that in some applications, the HRC 8 may eliminate the requirement for washing,” explains Marais.
Based on customer feedback from Metso’s global installed base, Meneses tells Quarrying Africa that customers in the manufactured sand market have particularly commended the HRC 8 for its throughput, energy efficiency, reduced operating costs, as well as safety and ease of maintenance.
The HRC 8 can provide a notable increase in throughput. The flange design maximises the amount of material that is crushed by pulling the feed into the crushing zone. This method prevents the material passing the rollers and increases efficiency and throughput.
The patented arch-frame, on the other hand, eliminates downtime caused by skewing. One can also adjust the speed and pressure of the machine depending on the material conditions and application requirements.
“Depending on the reduction ratio, the size being produced and the screening efficiency, we have most operations in the sand manufacturing market running the machine at 60-80 tonnes per hour (tph), which is a remarkable throughput,” says Meneses.
Thanks to the ability to handle a continuous stream
“Depending on the reduction ratio, the size being produced and the screening efficiency, we have most operations in the sand manufacturing market running the machine at 60-80 tph, which is a remarkable throughput.
Oldemar Meneses, product manager, HRC Technology at Metso
of material, HRC’s are considered to be energy efficient grinding machines in general. The HRC 8 goes a bit further; it directs the feed material straight to the crushing zone and adjusts the speed and pressure in order to avoid energy wastage.
The machine uses a combination of high pressure and a unique patented roller design to achieve a fine grind with minimal energy input. The arch-frame roller design eliminates the need for a spring-loaded frame, which ensures even pressure distribution across the whole width of the rolls, resulting in sound performance and longer wear life.
“The reduced power required to run the machine compared to traditional impact and even cone crushers is another big benefit of the HRC 8. To provide context, where customers would traditionally require 250300 kW of power to produce 50 t of manufactured sand, they now use only 120 kW with the HRC technology. In fact, the machine consumes up to 50% less power in sand production compared to other technologies for the same volume of net product,” explains Meneses.
Equipped with a robust wear protection system, the HRC 8 minimises maintenance downtime and extends the operational life of the machine. The wear protection system includes carbide studs on the rolls and a wearresistant feed system.
“The machine runs at a very low speed – a maximum of 32 rpm – resulting in reduced roller wear. As a result, some of the customers running this machine in manufactured sand only replace their wear parts once every six months or once a year, depending on application. Customers have found this machine to be almost maintenance-free because the number of replacement parts is minimal,” says Meneses.
By reducing energy consumption and increasing wear life of components, the HRC 8 helps lower operational costs. Its efficient grinding mechanism also reduces the need for secondary crushing, further cutting down operational expenses.
for their operational needs.”
0,075
During the design of the HRC 8, Metso cast a special focus on safety and ease of maintenance. The key to improving safety during maintenance is to minimise the need for maintenance. With the HRC 8, maintenance downtime has been reduced by using robust components, while high-pressure rock-onrock crushing enables long wear-life of the manganese tyres. The patented split shaft allows for the tyres to be replaced quickly, without full machine disassembly, making the changeout of wear components easy and effortless.
In typical sand-making with VSIs, for example, there is generally a high percentage of ultra fines – the unwanted 0,075 micron material, which calls for wet processing. Due to its ability to produce very fine material with fewer unwanted microfines in the final product, we believe that in some applications, the HRC 8 may eliminate the requirement for washing.
“Due to the low speed at which the rolls move, there is also very little machine vibration and far less wear on the manganese parts. You can imagine the operational benefit of only having to change the manganese wear parts once every year, for example. On VSIs, in some cases these may need to be changed every week depending on the application. However, it is important to note that there is still a place for other crushing solutions – for some customers, a VSI will still be suitable
The machine is also encapsulated with guards to eliminate the risk for operators during operation – the operator cannot access the moving parts.
Ahead of the official launch, Pilot Crushtec has brought the first HRC 8 into South Africa. Marais tells Quarrying Africa that the machine will be mounted on a mobile tracked chassis, making it the world’s first tracked HRC 8. In addition, Pilot Crushtec will also have on offer a static module on a skid frame, complete with handrails and walkways.
“The tracked approach will allow for ease of machine movement on or between sites, especially during the demo period. We will be trialling the machine on various local customer sites to prove its effectiveness,” concludes Marais. a
Water management, often an afterthought, is one of the most critical activities of any quarrying or surface mining operation, which is why it is crucial to have an effective dewatering system in place. The process of choosing the right pump for optimal water control therefore calls for careful consideration of a number of factors. By Munesu Shoko.
For both productivity and cost efficiency reasons, water management should be a priority for every quarry or surface mine. Traditionally, water control was never the first thing that came to mind when thinking of productive and efficient operations. In recent years, however, this has all changed
as operations place high value on their dewatering needs.
Why dewatering? In quarries and mines, water accumulation – whether from rain, groundwater seepage or both – can wreak havoc on operations through structural damages, equipment damages or even health and safety hazards, amongst other problems.
64 kW
IPR’s submersible pumps range from 0,4 to 64 kW
250 As part of the rental facility, IPR services its pumps after every 250 hours
IPR’s self-priming diesel-driven pump sets are suitable for dewatering applications where power is not readily available.
For both productivity and cost efficiency reasons, water management should be a priority for every quarry or surface mine
Dewatering plays an integral role in keeping mining areas free of flooding or water accumulation, thus ensuring uninterrupted operations
Choosing a reputable supplier such as IPR ensures peace of mind that mines will always be guided to make the correct decision to ensure optimal water management
After the technical details such as flow and head have been established, then comes the type and capacity of pump required
Consequently, says Lee Vine, MD of IPR, dewatering plays an integral role in keeping mining areas free of flooding or water accumulation, thus ensuring uninterrupted operations.
Equally important is the selection of a pump that meets each operation’s unique dewatering needs, stresses Steve du Toit, sales manager at IPR. The effects of choosing the wrong pump for the application at hand, he says, can be detrimental, with low pumping efficiency and higher costs among some of the obvious downsides.
There are several factors to consider when selecting a dewatering pump for optimal water management.
Before delving into the technical aspects that inform pump selection, Du Toit says the principal factor is choosing the right supplier that offers both the correct product and the right expertise to guide the selection process.
It is true that selecting a dewatering pump is dependent on application requirements, says Du Toit. However, in IPR’s view, the principal consideration should always be the expertise of the supplier. After observing the prevailing site conditions and the future changes to the pit, a knowledgeable supplier will then advise on the type of pump required and all the other technical considerations to be made, based on these unique site requirements.
“Each installation starts with a detailed assessment of site-specific dewatering requirements. Through that process, IPR’s technical experts get a clear understanding of the unique conditions of the mine, such as water volume, pit dimensions and site-specific challenges. After that process, the company then recommends the most appropriate equipment and strategies for dewatering, ensuring optimal performance and cost efficiency for the customer,” says Du Toit.
Vine says choosing a reputable supplier such as IPR ensures peace of mind that mines will always be guided to make the correct decision to ensure optimal water
Dealing with a supplier that can offer a wide range of choices to suit the operation’s needs is important.
pump can move at a given time), which in turn determine the size and type of pump required.
“When choosing the size of the pump, it is also important to remember that the prevailing conditions will change over time as the pit gets deeper, which also changes parameters such as the required flow and pump head. Consequently, a pump that would have been ideal for an operation today might not be the right fit some three months later, for example. That is why it is important to keep us involved throughout the project,” says Vine.
management. “As a dredging and dewatering specialist, we have many years of experience in this field. Mines and quarries are there to produce, and we are there to take care of their dewatering needs. Getting us involved from the onset to ensure the right pump for the right application, results in efficient dewatering and cost savings for the mine,” says Vine.
Before selecting a pump for a mine’s dewatering needs, it is important to assess the specific site conditions, such as where the water is being pumped from and where it will be discharged. Considering the type and volume of water to be pumped, as well as the rate at which it accumulates will inform parameters such as head (the height at which a pump can raise the fluid up) and flow (the amount of water the
After the technical details such as flow and head have been established, then comes the type and capacity of pump required. Dealing with a supplier that can offer a wide range of choices to suit the operation’s needs is important. For example, IPR offers both diesel-driven and submersible dewatering pumps.
Designed to be fully submerged in water during operation, submersible pumps are ideal for operations where continuous dewatering is required. “These encapsulated pumps can be completely submerged in liquid and are most frequently used to transport drainage water, excess groundwater or any other
liquids with suspended solids,” explains Du Toit. IPR’s submersible pumps range from 0,4 to 64 kW.
IPR’s self-priming diesel-driven pump sets are suitable for dewatering applications where power is not readily available. Engineered and sized to meet specific site dewatering requirements, these pump sets are built locally by IPR and offer the option of being either traileror skid-mounted, depending on site requirements.
After the technical specifications have been identified, says Vine, the next consideration should be the capital situation for the client. The financial position of the mine or quarry determines whether to buy or to rent a dewatering pump. If capital outlay is a problem, rental will be ideal.
“Rental eliminates the need for a substantial upfront capital expenditure, freeing up the much needed budget for other pressing needs. In addition, rental costs can be classified as operational expenses, and this is especially important where dewatering is a critical necessity, yet there is no capex available,” says Vine.
In addition to classifying rental costs as operational expenses, customers also have the benefit of having one fixed charge for their dewatering needs per month, with no ‘hidden’ costs such as maintenance, unexpected repairs and even professional training. As part of the rental facility, IPR services its pumps after every 250 hours,
during which time it can determine any changes in the pit and offer the customer the right pump to meet the current needs.
In the event where the project is long term and capital is available, outright purchase would be the right option for the mine. Purchasing a dewatering pump, says Du Toit, also makes sense where the mine would like to have outright ownership and wishes to reduce the total overall cost of the dewatering pump installation. Large capital equipment such as dewatering pumps build equity over time, especially if the equipment is well maintained. Pumping equipment with long lifespans are assets that will grow the value of the business.
When choosing a mission-critical asset such as a dewatering pump, it is also important to factor in the reputation of the brand and the aftermarket regime behind it. For example, a premium product such as Atlas Copco, supplied and supported by IPR, ensures reliability, a good warranty programme and, more importantly, parts availability and aftersales support from IPR.
“Operations that buy or rent their dewatering pumps from trusted suppliers such as IPR can be confident that their equipment is always dependable and operates at peak performance because all repairs and servicing are done by expert technicians,” concludes Du Toit. a
Conveyor belt mistracking is one of the major problems experienced on conveyor systems across all bulk material handling industries, including quarrying and mining. Tru-Trac Rollers’ Guy Fitt and Douglas van der Westhuizen unpack some of the basic conveyor belt tracking ‘rules’ to follow and how the company’s new Apex Taper Trough Tracker, said to be the next leap forward in belt tracking technology, ushers in a new era in eliminating belt misalignment. By Munesu Shoko.
One of the most common causes of unscheduled downtime on conveyor systems is conveyor belt mistracking. Belt misalignment causes spillage, belt edge damage, damage to the structure, increased power consumption and increased labour costs. Misaligned belts will ultimately result in lost production, increased operating costs and safety hazards.
Although there are many factors that cause belt misalignment, belt mistracking issues are often attributed to conveyor belts alone, which in most cases is unjustified as conveyor systems are more than just belts. It is therefore essential to be fully aware of the basic characteristics of the different belt tracking components and for these to be employed correctly. Key to the belt running ‘true’ are both structural and non-structural factors.
The Apex Taper Trough Tracker’s inline taper wing rollers are designed for compatibility with trough angles up to 60 degrees
One of the most common causes of unscheduled downtime on conveyor systems is conveyor belt mistracking
It is important to make sure that all the structural conveyor components such as pulleys, idlers, take-ups and the supporting structure are properly aligned at all times
One of the critical non-structural factors to eliminating belt mistracking in conveyor systems is housekeeping. Cleanliness is essential to good belt tracking
One of the major talking points on Tru-Trac’s new Apex Taper Trough Tracker is its proven performance. The combination of tapers and the unique centre pivot offers fast, autonomous and continuous tracking in all conditions
On the structural front, says Van der Westhuizen, it is important to make sure that all the structural conveyor components such as pulleys, idlers, take-ups and the
The Apex Taper Trough Tracker’s inline taper wing rollers can flatten as low as 10 degrees for easy installation and transportation
supporting structure are properly aligned at all times. In fact, these should be the principal areas of concern whenever trying to identify belt tracking problems. All pulleys, snub rollers, troughing and return idlers must be square with the frame parallel to each other, and also be level.
“Constant condition monitoring of conveyor components is one of the best practices in ensuring correct belt tracking at all times,” says Van der Westhuizen. “Always check the condition of your pulley laggings and idlers. Make sure the idler frames are square and straight. What we have observed in many instances is that some of the idler frames are bent during installation, causing incessant belt misalignment problems during operation. It is therefore crucial to ensure that the idler frames are square and straight from the onset.”
In addition, to be properly steered, the belt needs to be in full contact with the idlers and pulleys at all times. A lack of contact or having material in between these components will definitely result in belt mistracking.
One of the critical non-structural factors to eliminating belt mistracking in conveyor systems is housekeeping. Cleanliness is essential to good belt tracking. “For me, the number one best practice in belt tracking is housekeeping; if something is clean, it works better,” says Van der Westhuizen.
Excessive material buildup, he adds, can cause misalignment, especially on idlers and pulleys. It can also cause the conveyor belt to jam or stop altogether, resulting in production delays and lost productivity. In the worst case scenario, the excess material can damage the belt itself, leading to costly repairs or even to the need for replacement. This is particularly the case in quarries, where there is a lot of fine dust and water in the processes, which exacerbate accumulation of material on idlers and pulleys.
Fitt agrees, saying that regular inspection and maintenance of the conveyor plays a crucial role in preventing the possibility of mistracking occurring. It is essential to regularly inspect idlers and their rollers to ensure the idlers are aligned properly and the rollers are running evenly.ditions.
From the onset, the birth of Tru-Trac Rollers nearly 30 years ago was informed by the need for continuous innovation to help industries deal with belt misalignment issues, says Fitt, thus allowing customers to achieve maximum conveyor system performance, resulting in optimal production output at the lowest possible cost. Over the years, Tru-Trac has continuously evolved its offering to provide the industry with the very best of solutions to solve common conveyor problems such as belt misalignment. A case in point is the patented Tru-Trac
Apex Taper Trough Tracker range.
“Designed for high performance, the Apex Taper Trough Tracker is a culmination of nearly 30 years of experience and two years of research and development, followed by a stringent testing regime in tough operating environments across commodities. We are glad to finally offer the market with what we believe is the next leap forward in belt tracking technology,” says Fitt.
One of the major talking points on the Apex Taper Trough Tracker is its proven performance. The combination of tapers and the unique centre pivot offers fast, autonomous and continuous tracking in all conditions.
design’s protruding adjustment bolts, eliminating space constraints and potential safety hazards. Adjustments are now quick and straightforward, allowing for easy angle setting of the wing rollers.
“The Apex Taper Trough Tracker’s inline taper wing rollers are designed for compatibility with trough angles up to 60 degrees and can flatten as low as 10 degrees for easy installation and transportation. This is a significant upgrade to the maximum 50 degrees trough angle on the previous system,” says Fitt.
The flat-packed nature of the system allows for easy handling and installation.
“The compact and flat-packed nature of the system also means that there is less wasted space in shipping containers/ crates, which saves on shipping costs. This is important, especially given the rising shipping costs across several major trading routes globally,” says Van der Westhuizen.
In addition, the improved customcompounded GRIP-TRAC™ rubber lagging and patented tread pattern on the wing rolls offer enhanced traction and tracking performance as well as extended working life of the replaceable wing rolls, further reducing total cost of ownership.
Increased responsiveness is yet another key benefit of the new Apex Taper Trough Tracker. The optimised centre of gravity and weight distribution offers improved stability, control and balance. This enhances sensitivity to belt misalignment and tracking performance by increasing efficiency and responsiveness.
Tru-Trac used Electra Mining Africa to showcase how the new Apex Taper Trough Tracker ushers in a new era in belt tracking technology and several clients who visited the company’s stand were thrilled by the capabilities of this groundbreaking offering
“The Apex Taper Trough Tracker is a radical upgrade of our previous systems. The upgraded system now includes enhancements for durability and better protection against dust, especially in fine dust environments,” says Van der Westhuizen.
With its compact design, the Apex Taper Trough Tracker can be installed effortlessly in tight spaces, such as under hoods or on tripper cars. The new cantilevered wing roll and cradle replace the previous
“Belt misalignment is one of the biggest issues for quarries and mines. It can result in higher operating costs, capacity losses, unscheduled shutdowns, material spillage and unsafe operator conditions. We used Electra Mining Africa to showcase how the new Apex Taper Trough Tracker ushers in a new era in belt tracking technology and several clients who visited our stand were thrilled by the capabilities of this groundbreaking offering. Operations that are already running the system have also expressed great satisfaction with the exceptional performance of the Apex Taper Trough Tracker,” concludes Fitt. a
Our Bell 4x4 ADTs are the answer for job sites that don’t need a 6x6. Eliminating the middle axle means no tyre scu ng, thus less damage to the tyres and road surface. With a tighter turning circle compared to their standard 6x6 counterparts, they are highly manoeuvrable in tight spaces. Even better - they give you the same product at a lower overall cost.
Contact your nearest Bell dealer today for more information.
Conveyor belt accessories specialist, Mato Products, has introduced its MDP light-duty range of belt cleaners – its first ever for quarrying/aggregate applications. With a special design focus on parameters such as smaller pulley diameters and a reduced capital cost, the MDP range fits the bill for the cost-conscious quarrying sector. By Munesu Shoko.
Traditionally renowned for its mechanical conveyor belt fastening systems, Mato Products, part of the Multotec Group, has since 2016 expanded its product line to include a range of belt cleaners. The latest addition to the growing line is the MDP light-duty belt cleaner, which made its debut at Electra Mining Africa 2024, and is geared to address specific belt-cleaning requirements for aggregate operations.
As part of the rollout plan, Mato Products has identified a number of major quarries across various provinces in South Africa for trial purposes. This will allow customers to prove the concept before they purchase.
Benjamin Sibanda, MD of Mato Products, tells Quarrying Africa that belt cleaners are not one-sizefits-all solutions and, for long, quarries have been compelled to work with whatever is available on the market, which results in poor cleaning performance and reduced wear life of their belt cleaners. One of the primary considerations when designing the MDP range was the issue of correct sizing to meet the specific requirements for quarries. Generally, quarries run smaller conveyor systems with both smaller belt width and head pulley diameters, compared with their mainstream mining counterparts. According to Sibanda, the width of the belt cleaner must match the width of the material path
120-185 mm
The MDP comes with a solid blade with 120-185 mm blade height for pulley diameters between 150 and 500 mm, which perfectly fits the typical smaller head pulleys often found in quarry conveyors
Mato Products has launched its MDP light-duty range of belt cleaners – its first ever for quarrying/ aggregate applications
One of the primary considerations when designing the MDP range was the issue of correct sizing to meet the specific requirements for quarries
Given that quarrying by its nature is a cost-conscious industry that produces high-volume, low-margin material, the MDP casts special design focus on the reduction of capital cost
To reduce maintenance costs, the MDP belt cleaner adopts Mato Products’ slide-on and slide-off principle for easy installation and maintenance
The Mato Products’ MDP light-duty belt cleaner is geared to address requirements for aggregate operations.
at the point of discharge from the belt. Equally, smaller head pulleys require smaller belt cleaners and blades to correctly fit their radius.
“With that in mind, the MDP comes with a solid blade with 120-185-mm blade height for pulley diameters between 150 and 500 mm, which perfectly fits the typical smaller head pulleys often found in quarry conveyors. The belt cleaner therefore fits perfectly around the head pulley to ensure constant contact between the blade and the belt for effective material removal over the life of the cleaner,” explains Sibanda. “Sizing the belt cleaner correctly to the head pulley ensures that it maintains the proper angle of attack on the belt, resulting in optimal cleaning performance and reduced wear life.”
Given that quarrying by its nature is a cost-conscious industry that produces high-volume, low-margin material, the MDP casts special design focus on the reduction of capital cost, with several features that
35-40%
The cost of the two tensioners constitutes about 35-40% of the total capital cost of a belt cleaner
“Having one instead of two tensioners reduces the cost of the belt cleaner significantly. To provide context, the cost of the two tensioners constitutes about 35-40% of the total capital cost of a belt cleaner. It is, however, important to note that the MDP retains the same compression spring system as some of our larger belt cleaners in our range.
speak directly to that effect. “As much as quarries want to achieve the same belt cleanliness as mining, the operators often allude to the fact that their pockets are not as ‘deep’. We therefore designed the MDP belt cleaner with that in mind,” says Sibanda.
The biggest cost component in a belt cleaner, he stresses, resides in the end assemblies. To reduce the cost significantly, Mato designed the MDP with a one-sided tensioning system end assembly. Given the typical smaller size of the conveyor belts in quarrying, a
It is important to use the right Mato belt cleaner for your application to achieve better results – belt cleaners are not a one-size fits-all solution.
one-sided tensioning end assembly system works perfectly fine with this belt cleaner.
“Having one instead of two tensioners reduces the cost of the belt cleaner significantly. To provide context, the cost of the two tensioners constitutes about 35-40% of the total capital cost of a belt cleaner,” says Sibanda. “It is, however, important to note that the MDP retains the same compression spring system as some of our larger belt cleaners in our range.”
Another cost cutting feature is that the MDP is designed not to clean the whole width of the belt – the belt cleaner only cleans the centre of the belt where conveyed material runs. According to Sibanda, most conveyor belts run material in the middle of the belt, leaving 50-150 mm of space on the outer edges. Maintaining blade-to-belt contact across the whole width of the conveyor belt therefore means that there is unnecessary cleaning action and wear over the 150 mm area on the outer edges of the belt.
“Oftentimes when this happens, the result is a ‘smiley’ blade, which calls for continuous shimming on the edge of the blade. We have therefore reduced our solid blade by 50-150 mm on either side. For example, if you are cleaning a 1 200 mm belt, we deploy a 1 050 mm solid blade, which targets the area that needs to be cleaned only. By taking this approach, we minimise both maintenance time and costs related to the shimming of the belt,” explains Sibanda.
To reduce maintenance costs further, the MDP belt cleaner adopts Mato Products’ slide-on and slide-off principle for easy installation and maintenance, while eliminating the need for special tools or training when maintenance is performed.
50-60%
The drop-on, drop-off feature reduces maintenance and blade replacement time by close to 50%, potentially even up to 60%
“The traditional approach of nuts and bolts takes a lot of time when replacing a blade. The drop-on, drop-off feature reduces maintenance and blade replacement time by close to 50%, potentially even up to 60%, thus improving uptime for the customer’s operations,” says Sibanda. “By reducing maintenance time, we can also service more belts or sites within the same timeframe, which is the main reason that we
are always looking to improve on the current equipment we have.”
In cases where there is carryback, often the blame is laid squarely on belt cleaners. Sibanda stresses that for belt cleaners to effectively perform their duties, they must be ideally suited to the application at hand. Therefore, selecting the right belt cleaner calls for the careful evaluation of several different factors. If the rest of the components on a conveyor system are not spot-on, there are bound to be problems – lots of them, for that matter.
To help clients scope their belt cleaners correctly, Mato Products conducts what it calls the Conveyor Assessment Along the Length of the Conveyor (CAALC) concept. Through this process, a number of areas along the length of the conveyor are inspected due to their influence on the effectiveness of the belt cleaner.
The first area to look at, he says, is at the tail of the conveyor, to inspect components such as pulley condition, pulley leggings, return idlers, top idlers, troughing frames, the chute and the condition of the conveyor belt itself. It is also important to ensure that the belt is secured properly to avoid mistracking and ultimately spillage, which in turn leads to carryback.
Along the length of the belt is the second area to inspect. For example, there is need to check for carryback under the belt, which could push the conveyor belt up. Also check for ceased idlers or return rollers, which are central to accumulation of fines and ultimately carryback.
The third area to check is at the head, where a lot could go wrong, says Sibanda. For example, if the pulley legging is worn out or incorrectly installed, it is difficult for the belt cleaner to achieve the effectiveness that is desired. In addition, any vibration and unevenness of the drive pulley could also result in poor cleaning performance.
“After the CAALC process, we compile a report for the client with all our findings at the various areas along the length of the conveyor belt. Beyond the findings, we also give recommendations and the scope of what needs to be done to arrest any pitfalls along the conveyor system. We go beyond just the belt cleaners; in fact, we really add a great deal of value to the industry,” concludes Sibanda. a
FLS’s NexGen polyurethane is a heavy duty and hard-wearing screen panel that combines the physical properties of rubber and polyurethane elastomers.
The choice of screen media plays a critical role in achieving efficient and productive screening operations. In a one-on-one with Quarrying Africa, Chris Currie, Service Line Manager at FLS, highlights some of the key factors to consider when evaluating an operation’s screen media needs and how the company’s new NexGen polyurethane screen panel changes the game in the screen media market. By Munesu Shoko.
Screening media solutions are small and low-cost wear parts when compared with major equipment in the mining and mineral processing industry. Due to their size and individual cost, these panels are often taken for granted even though poorly performing screen media can result in the loss of production, increased maintenance, downtime and poor product quality.
Screening media panels are therefore a critical part of mineral and aggregate processing as they help separate the desired particles from the unwanted ones. The screening process ensures that only the valuable particles are further processed, which increases efficiency and reduces operational costs.
Choosing the appropriate screening media therefore impacts the quality of the final product and has a significant bearing on the operation’s bottom line. Given the wide pool of screen media solutions
to choose from – ranging from rubber and woven wire to wedge wire and polyurethane – there are various important factors that influence the choice of screen media to ensure the right solution for the right application.
“Screen media panels are critical in the overall processing equation. Wrong panel selection can be detrimental, leading to common enemies of efficient screening such as pegging and blinding, which in turn lead to reduced throughput and poor screening efficiency,” says Currie.
Commenting on some key factors that affect screen media selection, Currie highlights that one of the principal considerations in any buying decision must be the support from the screening media supplier. It is important to consider the supplier’s technical support, manufacturing
95%
Whenever it designs its screens, FLS targets at least 95% screening efficiency
Screening media panels are a critical part of mineral and aggregate processing as they help separate the desired particles from the unwanted ones
One of the principal considerations in any buying decision must be the supplier’s technical support, manufacturing support and service support capabilities
Operation characteristics such as application and process, capacity required, feed rate and percentage of feed being recirculated have a big influence on the choice of screening media
FLS is launching its NexGen polyurethane, a heavy duty and hard-wearing screen panel for large particle applications
support and service support capabilities.
As a leading supplier of mineral processing equipment, FLS has many years of experience with the advantages and limitations of each type of screening medium, allowing it to provide ideal recommendations that are as customised to each operation’s processes. Every mine needs screen media solutions that are configured exactly for the specific challenges faced at that particular operation.
In addition, FLS provides screen media optimisation services and field trials as part of a service to provide tailored recommendations for panel type, size, aperture size and shape, position, motion and other important parameters.
On the technical front, one of the important factors is material characteristics. This includes the type of material being processed, size distribution, shape of material, moisture content, weight and density, abrasiveness, corrosiveness, stickiness and temperature, amongst others.
“Given the wide array of screen media panels and material options available, a determination of the ideal screen arrangement must consider numerous operation and material characteristics. If this is not done, one may be left with a poorly performing screen,” says Currie. “For example, if the material is abrasive, a more wear-resistant screening medium would be ideal.”
In addition, operation characteristics such as application and process, capacity required, feed rate and percentage of feed being recirculated have a big influence on the
3
The NexGen polyurethane material screen panel, which made its official debut at Electra Mining Africa 2024, comes to market on the back of a nearly three-year testing regime across commodities
“Screen media panels are critical in the overall processing equation. Wrong panel selection can be detrimental, leading to common enemies of efficient screening such as pegging and blinding, which in turn lead to reduced throughput and poor screening efficiency.
choice of screening media. The chosen screen panels should have the capacity to handle the required feed rate and throughput without causing excessive wear or damage to the screen itself.
“Equally important is the choice of a screen medium based on its ability to efficiently separate the desired material from the unwanted material,” says Currie. “Informed by the application and process type, operations should choose the screening media type that gives them the longest wear life possible. This not only increases screening efficiency and productivity, but also reduces waste and operational costs.”
Speaking of long wear life, FLS is launching its NexGen polyurethane, a heavy duty and hard-wearing screen panel for large particle applications. Combining physical properties of rubber and polyurethane elastomers, the NexGen has better wear-resistance in highly abrasive applications where rubber and traditional polyurethane panels generally struggle.
“The new NexGen polyurethane material screen panel is ideally suited for early stage screens and trommels where there is generally high abrasion. Due to its extremely durable properties, it lasts longer than rubber or standard polyurethane in those high-impact applications. In some instances, it has been proven to offer double the screen panel wear life of rubber in these high-abrasion applications,” says Currie.
One of the major benefits of the long wear life is the reduction of costs. Frequent screen panel replacement leads to high maintenance and opportunity cost, whilst also lowering equipment productivity. In addition, regular replacement means that screen maintenance personnel have to spend an incredible amount of time on the screen changing panels, increasing safety risk in the process.
“With increased wear life also comes a significant reduction in waste, not just in the material itself, but also in the supply chain. Less frequent panel changes mean that there is less energy used, less transport required and less stock needed, which in turn is a huge sustainability tick for our customers,” says Currie.
With screening panels, he adds, screening efficiency is a very big factor. “Whenever we design our screens, we target at least 95% screening efficiency. With the premium material that we have used in designing the NexGen polyurethane panels, we are able to run a smaller
ligament, which can give us more open area. A higher percentage of open area in screening panels improves screening efficiency and material throughput. This is because it gives particles more opportunities to pass through the screen,” says Currie.
The NexGen polyurethane material screen panel, which made its official debut at Electra Mining Africa 2024, comes to market on the back of a nearly three-year testing regime across commodities. A case in point was at a major iron ore mine in the Northern Cape, South Africa, where the NexGen polyurethane material significantly increased wear life.
The mine, explains Currie, conducted a multi-supplier wear optimisation study on its vibrating screen panels. Along with several other manufacturers, FLS supplied a full deck of its most suitable wear material. The company’s premium NexGen polyurethane panels were installed side-by-side with multiple different options, including standard thermoplastic polyurethane (TPU) injection moulded panels, injection moulded rubber and other open cast polyurethane options. The application experienced highwear rates and the aim was to improve panel wear life to increase cost efficiency and availability, while decreasing panel maintenance costs. The panels were installed on a doubledeck scalping screen situated in the mine’s beneficiation plant. A competitor’s injection moulded panels were removed from operation and scrapped due to high wear just two weeks into the trial, as were other injection moulded panels from other suppliers after one month of installation. The pattern was repeated several times and all competitor panels were replaced in the early stages of the trial.
In comparison, the NexGen polyurethane screen panel
proved to be highly durable and cost-effective, lasting six months, with a wear rate significantly outperforming other competitor materials. No panel failures were experienced and only normal wear and tear was seen on the polyurethane borders. The tonnage passed over the screen was 1,1-million tonnes of -80 mm iron ore material, with a total of 2 622 run hours.
Elsewhere, FLS recommended the NexGen to a coal mine in Australia, which was looking to increase the productivity of its vibrating screens and decrease its maintenance costs. Historically, FLS had performed a lengthy optimisation process and recommended standard modular polyurethane and wedge wire screen media for the plant. The polyurethane panels had a wear life ranging from three to six weeks of continuous operation and management was looking to reduce the total cost of operation.
FLS screen media experts analysed the situation and recommended the NexGen polyurethane screen panels, which were installed across the feed and intermediate section of a drain and rinse screen to assess the media performance. The vibrating screen was run for a cumulative utilisation period of three weeks before the first inspection shutdown.
The test went on for another five weeks to monitor the wear rates and ligament loss on the trial panels. The total duration of the trial was about 18 weeks and the test panels were replaced with new panels at least once during this period to gauge repeatability. In fact, the new panels survived for ten weeks, compared to the five weeks of most of the standard polyurethane panels used. Doubling the screen media wear life lowered maintenance time and media costs, while increasing safety and productivity.
Currie tells Quarrying Africa that following the conclusion of the test period, the manufacture of the NexGen polyurethane screen panels commenced at FLS’s Delmas, Mpumalanga, South Africa facility. At the time of writing, the company was busy revamping the facility to bolster local screen media manufacturing capacity.
“We have also invested in a new machine specifically for the manufacture of NexGen polyurethane screen panels as well as additional moulding stations. We are focused on boosting our local manufacture within the region to allow us to respond quickly to our customers’ needs,” concludes Currie. a
Bunting’s ElectroMax-Plus overband magnet is a compact and powerful solution for efficient ferrous metal separation in recycling, mining and quarrying applications, featuring enhanced magnetic strength and innovative air-cooled technology.
In a groundbreaking development for the quarrying industry, Bunting has unveiled its latest innovation – the ElectroMax-Plus overband magnet. The cutting-edge magnetic separator is set to revolutionise ferrous metal removal in quarries across Africa, offering unparalleled performance in a compact and lightweight package. By Munesu Shoko.
The design objective of creating a more compact and powerful electromagnetic overband magnet led the Bunting engineering team to develop the ElectroMax-Plus. The ElectroMax-Plus extends Bunting’s comprehensive range of overband and suspension magnets. In addition to standard
sizes, Bunting also designs and manufactures bespoke models which are application-specific.
Electromagnetic overband magnets use an oilcooled or air-cooled wire coil to generate a deep and strong magnetic field. The electromagnetic force radiates from a coil wound around a steel core and mounted inside a steel box with a thick steel back-bar.
This focuses the magnetic field in one direction: down towards the conveyed material. In operation, an overband magnet, suspended over conveyors, screens and vibratory feeders, lifts and removes ferrous metals such as iron rebar and beverage steel cans.
Overband magnets are a common feature on many mobile screens and crushers. In such applications, minimising weight and size is crucial and, subsequently, operators use standard ceramic ferrite or, less frequently, neodymium rare earth permanent overband magnets rather than electromagnets.
600 mm
The ElectroMax-Plus can operate at a suspension height of up to 600 mm, a substantial improvement over the 450 mm limit of standard models
The design objective of creating a more compact and powerful electromagnetic overband magnet led the Bunting engineering team to develop the ElectroMax-Plus
The introduction of the ElectroMax-Plus addresses a critical need in the quarrying sector for more powerful yet compact magnetic separation solutions
Unlike traditional electro overband magnets, it utilises an air-cooled system instead of oil. This innovative approach significantly reduces the unit’s weight and size, while maintaining optimal performance
Its ability to combine increased magnetic strength with reduced weight makes it an ideal choice for both stationary and mobile quarrying operations
105%
At a suspension height of 500 mm, it boasts an impressive 105% stronger force index compared to the standard ElectroMax model
The ElectroMax-Plus stands out from its predecessors and competitors with its exceptional magnetic strength.
Neodymium permanent overband magnets produce a strong but shallow magnetic force and often experience problems with belt and motor damage due to large ferrous metal clamping against the magnet block. The magnetic field of the light and compact ElectroMax-Plus is both deep and strong, enabling excellent separation performance at higher suspension heights.
In addition, simply turning off the electromagnet releases any extremely large, entrapped tramp ferrous metal. The shape and nature of this magnetic field means there is less wear to the self-cleaning belt mechanism (for example, belt, motor gearbox and bearings).
The ElectroMax-Plus stands out from its predecessors and competitors with its exceptional magnetic strength. At a suspension height of 500 mm, it boasts an impressive 105% stronger force index compared to the standard ElectroMax model. This remarkable increase in power translates into superior ferrous metal separation, even in challenging conditions. The incredible additional magnetic force removes small tramp ferrous metal commonly missed by permanent overband magnets.
The ElectroMax-Plus comes with several innovative features. Unlike traditional electro overband magnets, it utilises an air-cooled system instead of oil. This innovative approach significantly reduces the unit’s weight and size, while maintaining optimal performance.
The ElectroMax-Plus can operate at a suspension height of up to 600 mm, a substantial improvement over the 450 mm limit of standard models. This extended reach allows for more flexible installation options and improved separation efficiency.
Despite its enhanced power, the ElectroMax-Plus is 25% lighter than equivalent permanent overband magnets. This weight reduction is crucial for mobile crushing and screening equipment, where every kilogram matters.
Another major benefit is its versatility. The ElectroMaxPlus is designed to excel in various quarrying applications, including protecting crushers and screens from damaging tramp metal, removing ferrous contaminants from conveyed materials and enhancing product purity in aggregate production.
its enhanced
Its powerful magnetic field is capable of capturing a wide range of ferrous debris, from large steel plates to small wire fragments, ensuring comprehensive protection for downstream equipment.
The introduction of the ElectroMax-Plus addresses a critical need in the quarrying sector for more powerful yet compact magnetic separation solutions. Its ability to combine increased magnetic strength with reduced weight makes it an ideal choice for both stationary and mobile quarrying operations.
Alison Flower, General Manager of Bunting’s Redditch operation in the United Kingdom, emphasises the significance of this innovation: “The new ElectroMax-Plus provides a real alternative to neodymium rare earth overband magnets. There is the requested additional magnetic strength, without the operating problems – as experienced with some neodymium rare earth overband magnets.”
As quarries across Africa seek to optimise their operations and improve product quality, the ElectroMax-Plus overband magnet emerges as a gamechanging solution. “Its blend of power, efficiency and versatility positions it as a top contender in the magnetic separation market, promising to elevate the standards of ferrous metal removal in the quarrying industry,” concludes Coleman. a
Electro Overband Magnets
Permanent Overband Magnets
Magnetic Dsc Separators
Suspension Magnets Metal Detectors
Dealers & Distributors
Wanted
Booyco Engineering’s anti-idle auxiliary Power Unit (APU) is set to revolutionise surface mining and quarrying operations.
As part of its continuous innovation strategy, heating, ventilation and air conditioning (HVAC) specialist Booyco Engineering has launched its new anti-idle auxiliary power unit (APU). In an environment where temperature is deemed a Class A hazard, the APU allows mines and quarries to keep their HVAC systems running while the main diesel engine of the machine is off, thus reducing fuel costs and carbon emissions, without compromising operator comfort and safety. By Munesu Shoko.
Leading HVAC specialist Booyco Engineering used Electra Mining Africa in September this year to unveil its groundbreaking diesel-saving innovation to the mining and quarrying industry. The APU is basically a small generator that is designed to run an HVAC system of a mining machine such as a dump truck, excavator or wheel loader, while the main engine of that particular machine is switched off.
Brenton Spies, MD of Booyco Engineering, tells Quarrying Africa that this is particularly helpful in
situations where mining machines have to stand for long periods, for example, while waiting to load or to be loaded. Traditionally, he says, switching off the machine during such periods was standard procedure. However, on the back of new health and safety laws, this is no longer possible.
With heat and body stress defined as a Category A safety hazard, it is therefore mandatory – as long as the operator is inside the cab – for HVAC systems to be kept running at all times, even when the machine is not productive. In fact, heavy machine operators are
40
The APU is a culmination of Booyco Engineering’s 40 years of experience as an HVAC service provider to mines and quarries
46°C
The HVAC unit is T3-rated and is suitable for operation in ambient temperatures up to 46°C
Booyco Engineering has developed an anti-idle auxiliary Power Unit that will result in significant cost savings and a reduction in carbon emissions.
Booyco Engineering used Electra Mining Africa to unveil its groundbreaking diesel-saving innovation to the mining and quarrying industry
The anti-idle auxiliary power unit (APU) is basically a small generator that is designed to run an HVAC system of a mining machine while the main engine is switched off
This is particularly helpful in situations where mining machines have to stand for long periods, for example, while waiting to load or to be loaded
Significantly, the cost of the APU is offset by its relatively short payback period, thanks to its low running costs
now even entitled to stop work if the HVAC system is not functioning properly. This is in direct contrast to 15 years ago when operators would just work with an open window if the HVAC system stopped working for any reason, exposing the operator to potentially hazardous dust and silica particles.
“Based on our understanding of the challenges in the mining sector, we realised that there was a gap in
the market for a unit that could keep not only the HVAC running, but also other related systems such as filtration systems, communication systems and proximity detection systems, while the main diesel engine of the machine is off,” says Spies. “This led to the design of the APU, which we believe is a groundbreaking advancement for the mining industry, enabling operations to enhance efficiency, reduce operating costs and meet carbon emission targets, whilst ensuring operator safety and comfort at all times.”
On most mining machinery, the APU is mounted on the back of the cab. The 24-VDC air conditioning system used in mining trucks and other equipment integrates seamlessly with APU. The HVAC unit is T3-rated and is suitable for operation in ambient temperatures up to 46°C. The APU can be connected directly to the main diesel tank of the piece of equipment. With minimal piping and wiring, connecting the unit is quick and easy.
“The APU is a culmination of Booyco Engineering’s 40 years of experience as an HVAC service provider to mines and quarries. We have cut our teeth across a number of demanding sectors, designing, manufacturing and maintaining HVAC systems for customers in the railway, defence and mining industries. We are therefore used to designing HVAC systems to a very high specification in
order to ensure they survive the high vibration, dust and extreme temperature environments they are expected to operate in. We have taken that experience and applied it to the APU and our standard HVAC range,” says Spies.
The big benefit of the APU is the diesel saving that comes with the ability to power the HVAC system with a much smaller engine compared to that of the mining truck, for example. Given that transportation, on average, accounts for a large portion of the total mining costs at most opencast operations, deploying the APU will result in significant cost savings for the mine or quarry.
“In high ambient temperatures prevalent on southern African and for that matter most mines worldwide, truck operators often keep the main engine running to maintain a comfortable cab temperature while waiting to be
loaded. While this is understandable in terms of health and safety, this practice can be costly – the truck can consume large volumes of diesel per hour through idling,” says Spies.
For example, a typical 100-tonne (t) truck runs with a 21-litre engine, which consumes between 37,5 and 94 litres of diesel per hour, depending on duty cycle. In low-duty cycles, such a truck can consume between 37,5 and 56,3 litres of diesel per hour. In contrast, the APU only consumes, at most, 1,5 litres of diesel per hour.
Significantly, the cost of the APU is offset by its relatively short payback period, thanks to its low running costs. While the payback period varies depending on the mine and each vehicle’s standing periods, Spies reckons that the payback period for the APU will be, on average, between six to 12 months.
In addition, a significant reduction in fuel consumption translates into reduced carbon emissions. This is particularly important for Environmental, Social and Governance- (ESG-) focused mining companies that seek to build strong relationships with communities, regulators, employees, customers and suppliers. ESG has now become such a critical component of any mining company’s strategy in the face of the green revolution.
“The APU is a valuable asset in hot climates such as those found across many mining destinations in Africa. A typical yellow metal hauler’s cabin is tantamount to a glass box. If, for example, one is operating in hot climates of about 40°C without any ventilation, temperatures in the cabin can rise to as high as 65-70°C in as little as 30 minutes, which is life-threatening. It is therefore important to ensure that HVAC systems are running at all times,” says Spies.
Although the APU, just like Booyco Engineering’s HVAC systems, is designed to withstand tough operating conditions, Spies reiterates the need for regular maintenance to ensure that the unit operates at optimal performance rates at all times.
1,5 l
Booyco Engineering has been supplying and maintaining HVAC systems in mining for more than 35 years, during which time it has been offering its manon-site service. The company still has units operating in these harsh conditions even after two decades, owing to the ruggedness and fit-for-purpose design of the units, as well as the complementary maintenance regime.
“If a mine or quarry buys HVAC systems from us and also signs up for a man-on-site contract, we offer a five-year warranty. That is how much trust we have in our design and manufacturing capabilities. However, it is obviously not just about buying a quality product, but also about maintaining it,” concludes Spies. a
We know the drill!
• Refurbishment of hydraulic drifters
• Management of GET products via app
• Complete refurbishment of hammers on site
• Resharpening of drill bits on site
• Rand/USD contracts per meter on drilling tools
ENERGY-SAVING ECONOMICAL EFFICIENT
MAXDRILL ROCK TOOLS
“GLOBAL DRILLING INDUSTRY EXPERTS
Email: riaan@beowolfmining.co.za
Cell: +27 82-576-6349
Website: www.beowolfmining.co.za
In line with its strategy to ‘close the loop’, SEWEURODRIVE has introduced a new range of planetary gearbox units in Africa. The SEW PPK and SEW P2.e series not only closes the gap between the existing P-Series and the larger XP-series, but also expands the company’s offering into new industry sectors. By Munesu Shoko.
Latest from SEW-EURODRIVE is an exciting range of planetary gear units – the SEW PPK and SEW P2.e series. Built to provide the key benefits that SEW planetary gear units are renowned for – compact design for spaceconstrained conditions, along with high torque and low-speed outputs – the range complements the existing lines and offers innovative capabilities in new industrial applications.
“The launch of the SEW PPK and SEW P2.e series speaks directly to our ‘closing the loop’ strategy,” explains Edwin Weyers, Business Development Manager for Projects at SEW-EURODRIVE.
“Traditionally, the existing P-series was our flagship offering, but it was somehow limited in terms of sizes and application areas. In addition, we have always offered our large-scale, custom-built XP-
series. Through our 90 years of experience in developing and constructing gear units, we realised that there was need for a small and medium-sized range to close the gap between the P-series and the larger XP-series.”
The SEW PPK planetary gear units complement SEW-EURODRIVE’s product line in the torque load range under the proven P-series. Offering a torque range from 10 to 18 kNm, the SEW PPK covers a gear ratio range from 65 to 390:1. The ratio can be further reduced by adding a primary reducer before the planetary head, allowing for ratios up to 10 650:1 for a much lower speed capability. With the SEW PPK, the load is distributed across multiple planet gears, resulting in significantly higher power
2-124 kNm
Available with torque ratings from 2 to 124 kNm, the SEW P2.e range covers gear ratios from 15,2 to 332:1
“Traditionally, the existing P-series was our flagship offering, but it was somehow limited in terms of sizes and application areas. In addition, we have always offered our large-scale, custom-built XP-series. Through our 90 years of experience in developing and constructing gear units, we realised that there was need for a small and medium-sized range to close the gap between the P-series and the larger XP-series.
10-18 kNm
Offering a torque range from 10 to 18 kNm, the SEW PPK covers a gear ratio range from 65 to 390:1
Latest from SEW-EURODRIVE is an exciting range of planetary gear units – the SEW PPK and SEW P2.e series
The SEW PPK planetary gear units complement SEWEURODRIVE’s product line in the torque load range under the proven P-series
While most planetary gearboxes have a three-stage design only, the SEW P2.e can also be supplied in a two-stage model
Typical applications for the SEW P2.e in the mining and quarrying industry include crushers, apron feeders, clarifiers and thickeners
offers great flexibility for the end user. On the output end, a solid shaft with key and a splined solid shaft are available.
When looking for a hollow shaft gear unit, customers can choose between a splined hollow shaft and a hollow shaft with shrink disk. On the input gear end, the motor connection is made either via an exposed shaft-end or a motor adapter. Access to the complete modular motor system from SEW-EURODRIVE with extensive options such as brakes and encoders also offers further degrees of freedom.
Available with torque ratings from 2 to 124 kNm, the SEW P2.e range covers gear ratios from 15,2 to 332:1. While most planetary gearboxes have a three-stage design only, the SEW P2.e can also be supplied in a two-stage model. The SEW P2.e encompasses all the benefits of the SEW PPK, but goes a step further with a broader spectrum of diversity in its speed – up to 100 rpm – as well as in ratio and torque.
The high-strength, durable materials with advanced heat treatment allow the gear units to withstand extreme loads and resist wear, thus making light work of high torque requirements. “The gears are engineered for high torque capacity with robust, precise teeth to handle intense forces efficiently,” says Weyers.
density and thus enabling smaller dimensions compared with other gear unit types. This makes the range perfect for all heavy-duty applications that require a robust, compact design and high gear ratios.
In addition to gear unit design such as flange and foot mounting, the variance at the input and output
“In essence, these planetary gear systems produce high torque by distributing the load across several gears and using gear ratios to multiply the input torque. The efficient and compact design allows for the high torque to come from a relatively small package,” adds Weyers.
With this compact design, coupled with its flexibility
and high thermal limit rating, this gear unit is ideally suited for continuous heavy duty applications where space is at a premium. Typical applications for the SEW P2.e in the mining and quarrying industry include crushers, apron feeders, clarifiers and thickeners. Other industrial applications range from screw presses and slewing gears to wood panel shredders, ring pan mixers and batch plants, amongst others.
One of the major talking points is the exceptional thermal limit rating, which is made possible by the integrated fan in the motor interface. The fan aspirates air radially, accelerates it and generates a cooling stream of air with a high flow rate.
“The SEW P2.e is the only planetary gear unit on the market with an integrated fan coupled directly between the motor and the planetary head. Consequently, it boasts a large cooling area (two to four times larger than some of the competitor offerings in this size class) – a condition which is central to the high thermal limit rating. Despite its high power density, the SEW P2.e series therefore boasts a best-in-class thermal limit rating,” explains Weyers.
The direct bearing system, which is completely different to traditional planetaries, puts the SEW P2.e in a league of its own. “With the direct bearing system, we do away with the outer ring, which results in a more compact solution and longer bearing life. Doing away with the outer ring allows for the installation of much larger bearings in a compact space, thus improving the service life of gears,” explains Weyers.
24%
SEW P-series unit models. This allows customers to easily migrate to the SEW P2.e units without having to alter their operating environment or existing infrastructure.
“Our SEW planetary gear units work on a modular system. Parts’ commonality across ranges is a common feature. For example, the new SEW P2.e shares the same parts with the previous P-series and XP-series ranges. This increases operational flexibility and reduces procurement, logistical and training costs for customers,” says Weyers.
Given its nearly century experience in developing and constructing gear units for numerous customer applications, SEW-EURODRIVE has over the years amassed vast tribological expertise. Based on this and the results of longterm testing, the company has developed a special formulation for its premium gear unit lubricants.
GearOil by SEW-EURODRIVE increases the performance of SEW EURODRIVE gear units – be they standard, servo or industrial. It reduces friction between the gear wheels because it develops an outstanding lubrication film that increases the service life of the lubricant itself, as well as that of wear parts such as sealing rings and bearings. In addition, it protects gear units from corrosion and also from oil foaming damage. The self-cleaning properties of the lubricants prevent deposits as they bind water and dirt particles.
Compared with predecessor units, the SEW P2.e comes with variable motor interfaces. The direct motor mounting means there is no need for the motor adapter flange that is otherwise normally required – so this is a particularly space-saving design. “The direct motor mounting allows for installation of bigger motors. In addition, the various input adapters help with a high level of flexibility to meet varying customer requirements,” says Weyers.
Reduced weight is another major benefit of going the SEW P2.e route. With its lightweight gear unit design, the SEW P2.e is 24% lighter and 10% shorter in length, compared with some of the same-sized units on the market.
While the SEW P2.e benefits from several upgrades, SEW-EURODRIVE has been careful to retain the same critical dimensions as previous
“By using our premium gear unit lubricants, end users have peace of mind that their investments are protected – a high level of resistance to ageing reduces wear and increases service life. Customers can expect up to 50% longer service intervals and a long shelf life of up six years if they are using the special SEW-EURODRIVE approved lubricants,” says Weyers.
“Collectively, these features – the unique bearing design, direct mounting of motors, high torque, high thermal limit rating and our own SEW lubricants –demonstrate that the SEW gear units can effectively manage demanding conditions in quarrying and mining, which are characterised by dust, vibration and high loads, while, all the while, maintaining high performance and reliability,” concludes Weyers. a
In the safety- and productivity-conscious world of mining, correct and effective operation of both Proximity Detection Systems (PDS) and Collision Prevention Systems (CPS) are vital.
While their primary objective is to ensure the safety of people, Proximity Detection Systems (PDS) and Collision Prevention System (CPS) installations also have a direct bearing on other critical parameters such as equipment availability and productivity. Through its field support service technicians, Booyco Electronics ensures the intended benefits and objectives of implementing the technology are realised.
PDS/CPS solutions are critical safety systems in both surface and underground mining environments, particularly due to the significant risk posed by the operation of trackless mobile machinery (TMM) deployed to work in these environments. To ensure correct and reliable functionality of these systems, Charl Marais, General Manager – Field Services at Booyco Electronics, stresses the need for a regular and robust maintenance regime, customised to specific customer needs.
“Given that we work with safety systems, field support service is a critical arm of our business to ensure that all machines fitted with PDS/CPS solutions comply with our Section 21 responsibilities, as specified by the Mine Health Safety Council,” he explains.
The Booyco Electronics Field Services team is responsible for interfacing with customers, starting from project execution (installation, testing and commissioning of new systems) through to complete
lifecycle management of the product. Services include scheduled and unscheduled maintenance, breakdown and repair services, auditing and provision of spare parts as well as upgrades to enhance product capabilities or extension services to lengthen product lifecycle.
“We have more than 200 technicians across South Africa, supporting both Service Level Agreements (SLA) and non-SLA customers. This is complemented by dedicated technical support staff for each area to assist with more advanced tasks,” explains Marais.
Booyco Electronics offers a wide variety of services that can be tailored to individual customer requirements, considering aspects such as fleet size, system type and maintenance requirements as well as monitoring and data requirements, amongst others.
“Our maintenance schedules are adapted based on fleet size, system type and level of protection implemented (Level 7, 8 or 9) and typically include a minimum of one full system functionality test per vehicle per month,” he says. “For each customer, we have a defined scope of work in accordance with the SLA in place. For non-SLA customers, we generally have a different arrangement as may be required.”
For SLA customers, response time is generally less than two hours, while for non-SLA customers this depends on the location and availability of technicians within the area.
Understanding the extreme importance of maintaining uptime and production on TMMs, Booyco Electronics ensures its systems have minimal impact on production as a result of its strong ability in servicing customers on a breakdown basis.
This is facilitated by a branch network that encompasses all major mining destinations, namely eMalahleni, Kuruman, Lydenburg, Richards Bay, Rustenburg, Steelpoort and Welkom, to ensure timely response to breakdowns. The footprint is also constantly reviewed to accommodate new customer requirements.
Given the constant improvements and new advancements in PDS technology, Booyco Electronics continuously adapts its field support services to keep up with the pace of innovation. “We constantly advise our customers on the latest PDS/CPS improvements and advancements available on the market to ensure the best fit-for-purpose solutions,” says Marais.
“We also continually find ways of improving efficiency in our service delivery through the use of technology to manage our operations. Examples include mobile applications for time and travel management, digital certificates of compliance (COC) and service support applications as well as digital customer satisfaction surveys which are currently being developed,” he adds.
In addition, Booyco Electronics places a major focus on increasing its value proposition by using existing data via the Booyco Electronics Asset Management System (BEAMS) interface to not only improve safety, but also to assist customers increase productivity by, for example, removing bottlenecks in production and optimising traffic management.
A case in point is a major mining house which recently embarked on a ‘vehicle risk identification’ project spanning its global operations. The company contacted Booyco Electronics for assistance with data to help understand its operational risk (vehicle-to-vehicle and vehicle-to-people interactions) at one of its South African mines where the Booyco PDS has been in use for a number of years.
“Although the mine did not purchase the BEAMS software suite, we were able to access the data and provide the mining house’s global team with valuable input to help them understand the operational risk and to identify ‘hotspots’ for mitigation,” concludes Marais. a
AfriSam
AfriSam is a leading construction materials group in southern Africa. Since establishing its first cement plant in 1934, the company has grown into a formidable construction materials group with operations in South Africa, Lesotho and Eswatini.
www.afrisam.co.za
Babcock
Through several business units, Babcock offers a range of products and services, including construction and mining equipment, engineering solutions for steam generation and power plants, crane hire and gear rental, industrial generators, welding equipment and DAF truck sales and service.
www.babcock.co.za
With more than 16 years of experience in Proximity Detection Systems solutions, Booyco Electronics has supplied over 6 500 sets of mining vehicle equipment installations across southern Africa, as well as more than 55 000 pedestrian RFID installations.
www.booyco-electronics.co.za
Bunting
Bunting’s range of magnetic separators and metal detectors for quarries and mines ensures the protection of crushers, screens and conveyors. Overband magnets, suspension magnets and pulley magnets automatically remove tramp ferrous metal from conveyed quarried rock. www.bunting-redditch.com
IPR
IPR is recognised across the SADC region as the pump, heavy duty slurry handling and dredging specialist operating in underground and surface mining, quarrying, construction, wastewater, petrochemical and oil and gas sectors. www.pumprental.co.za
LOADTECH Load cells Onboard Weighing are specialists in onboard weighing providing complete solutions onboard your heavy goods vehicle, primarily in the application of load cell and transducer systems for payload protection and accuracy in the commercial vehicle sector. www.loadtech.co.za
Pilot Crushtec International
Pilot Crushtec International (Pty) Ltd is South Africa’s leading supplier of mobile and semi-mobile crushing, screening, recycling, sand washing, stockpiling, compacting and material handling solutions. www.pilotcrushtec.com
Sandvik
As a world-leading mining equipment manufacturer, Sandvik Mining and Rock Solutions is committed to improving your productivity and profitability. Our products and services provide you maximum value in terms of performance, quality, safety, flexibility and total economy. www.rocktechnology.sandvik/en/
Astec
Astec Industries has been a global leader in providing innovative Rock to Road™ solutions since 1972, specialising in equipment for asphalt road building and aggregate processing. www.astecindustries.com
John Deere
John Deere offers a comprehensive range of construction equipment, including ADT’s, excavators, loaders, dozers, graders, skid steers and TLB’s, designed to enhance productivity, efficiency, and performance on job sites of all sizes. www.deere.africa/en/construction
Lintec & Linhoff
Lintec & Linnhoff is a global manufacturer and distributor of leading-edge solutions for the asphalt and concrete industries under the Lintec and Linnhoff brand names. Its products include asphalt mixing plants, concrete batching plants, pavement related technologies, and specialist concrete cooling solutions.
www.lintec-linnhoff.com
Schauenburg Systems is a South African company that specialises in providing technology solutions for safety and productivity in mining and industrial markets. It positions itself as an active partner for digital transformation to meet the needs of the “Connected Worker.” The company has a strong focus on innovation and has a brand promise of “Innovation that Saves”. www.schauenburg.co.za
Weir Minerals
Weir Minerals Africa offers a wide range of equipment solutions including pumps, hydrocyclones, valves, dewatering equipment, wear-resistant linings, rubber products, screens and crushers – backed throughout the product lifecycle by high levels of aftermarket support.
www.global.weir
SANY
Sany Southern Africa is a subsidiary of Sany Group, a leading manufacturer of construction, mining and port machinery with over 20 R&D centres and manufacturing bases all over the world. www.sanysouthafrica.com
The new R 945 crawler excavator replaces the previous R 950 SME. Its completely updated design is characteristic of the new range of "generation 8" machines. And in order to provide even greater comfort, better ergonomics and more enhanced performance, the architecture of the R 945 has also been completely revamped.