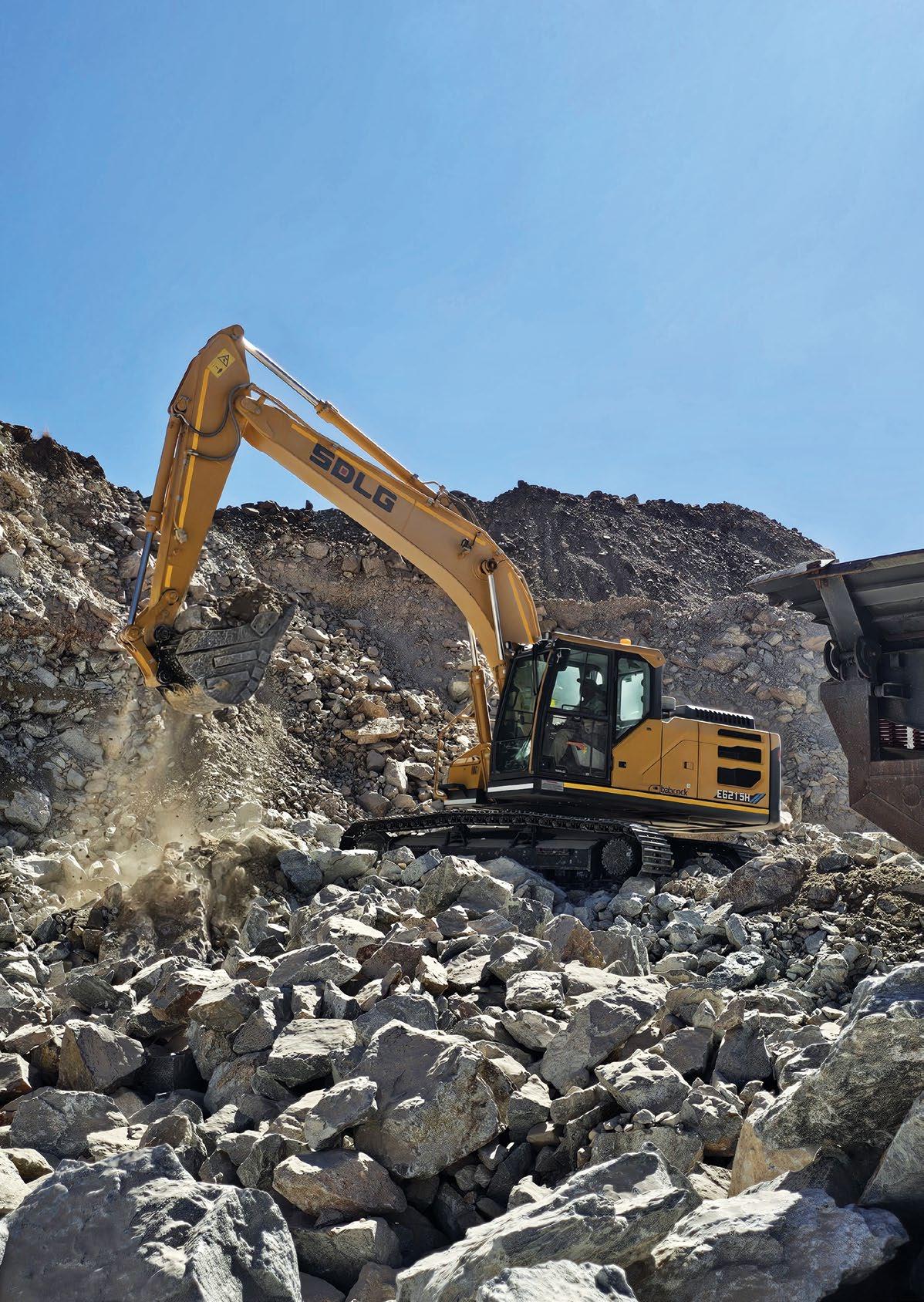

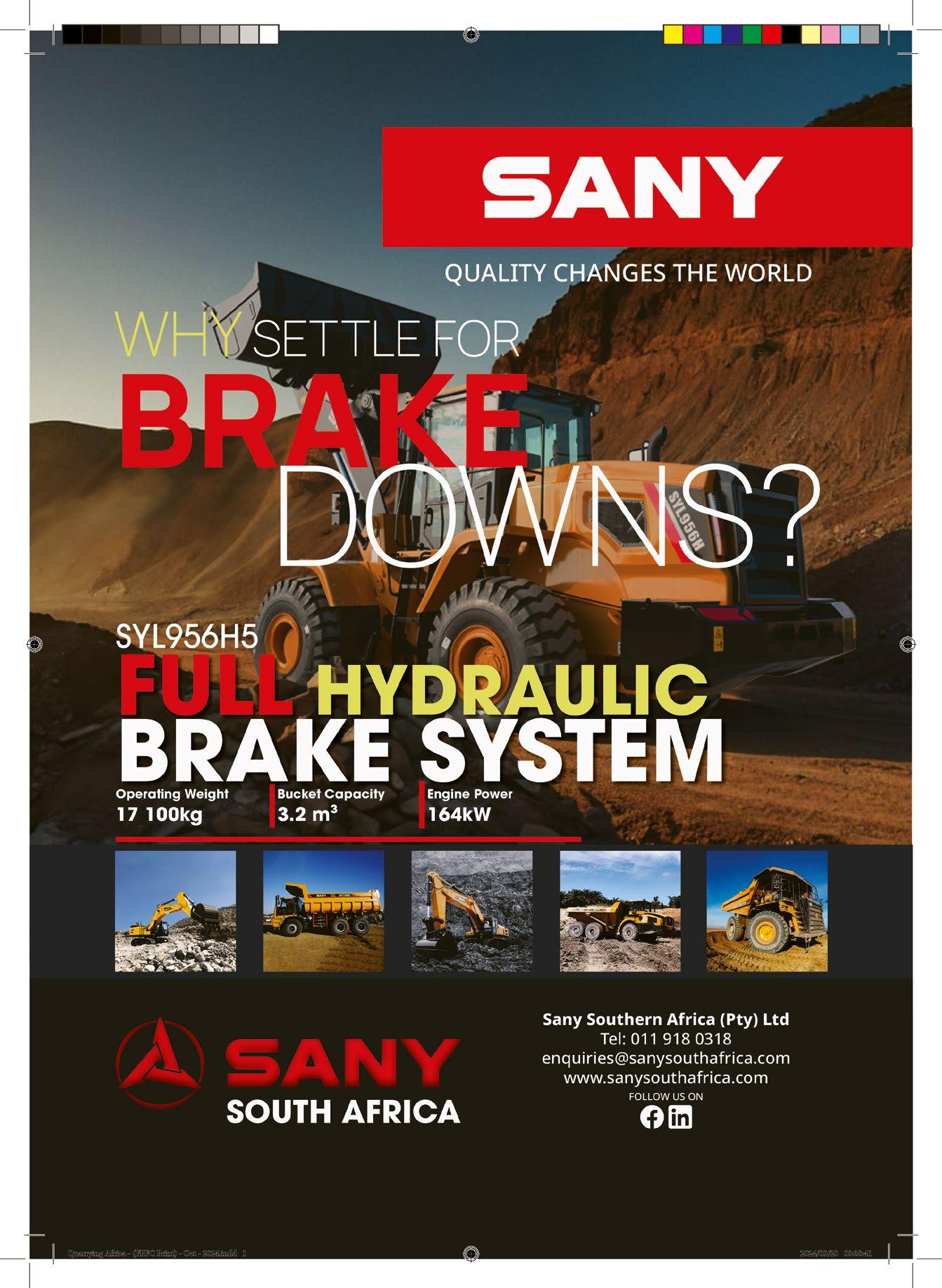
The health and safety crisis associated with mining is a longstanding matter globally and is historically fraught with fatalities, injuries and occupational diseases. The industry is aware that the crisis requires prompt action through the use of available preventive measures by affected stakeholders. Despite the continued trend of unwanted fatalities year in, year out, the South African mining industry believes the quest for Zero Harm is still achievable.
Over the years, the industry has committed to safety milestones in the quest to ensure that every miner returns from work unharmed every day. The first health and safety milestones were agreed by the tripartite Mine Health and Safety Council in 2003 to deliver fundamental improvements in the working environment for all people working in the mining industry. The second set of milestones were revised and agreed in 2014.
record this year. By the end of September, a total of 33 fatalities had been recorded, compared with 34 during the same period last year.
While the continued decline in fatalities is laudable, we would all agree that one death is too many. As an industry, we have an obligation to hunt for the next step change to make Zero-Harm a reality. I fully concur with Rohitesh Dhawan, CEO of the International Council on Mining and Metals (ICMM), who once said that while the mining industry can draw strength from how far it has come, from the days when fatalities were much higher, it should remain deeply uncomfortable until Zero Harm is actually achieved. Zero-Harm is in fact the only acceptable target.
MUNESU SHOKO
Publishing Editor
Email: munesu@quarryingafrica.com
LinkedIn:
Munesu Shoko
Quarrying Africa
The industry recently converged to deliberate on the third iteration of health and safety milestones agreed by the Department of Mineral and Petroleum Resources, organised labour and the Minerals Council. In 2014, the industry had set itself an ambitious target to achieve zero fatalities by December 2020, a 20% reduction in serious injuries per year by December 2016 and a 20% reduction in lost time injuries per year from January 2017. By 2024, these targets seem to remain elusive. The goal for zero fatalities has not yet been achieved, although there has been a marked decline in the number of fatalities reported across major commodities over the years. To provide context, industry figures from the Minerals Council indicate that the number of fatalities related to safety incidents has declined by 35% between 2014 and 2023.
In fact, the record low of 49 fatalities in 2022 was commendable. The industry then regressed in 2023, with 55 fatalities recorded during the year. If the current trajectory persists, the industry is likely to smash the 2022 safety
Is the quest for Zero-Harm far-fetched? I believe Zero-Harm is a tangible and measurable objective, not just a lofty hope. Looking back at how the industry has come together to change the course of safety performance, I am convinced that the Zero-Harm goal is within reach. However, there is still more to be done, such as collaboration and information-sharing to learn from each other’s mistakes. Safety is an area where the industry cannot afford to be competitive, but must be cooperative.
It is therefore encouraging to see major role players in the industry coming together to work towards a common cause. The three stakeholders – the Department of Mineral and Petroleum Resources, organised labour and the Minerals Council – have agreed on the next set of milestones to be achieved by December 2034, including mental health screening, and interventions to improve safety of women in mining, including personal protective equipment specifically designed for women, as well as the reduction of both gender-based violence and femicide in the workplace.
This is particularly important as we look to the future. With these interventions, the industry will ensure that there is no place for discrimination, harassment and assault anywhere in the mining fraternity and the society at large.
Publishing Editor: Munesu Shoko
Sub Editor: Glynnis Koch
Admin: Linda T. Chisi
Design: Kudzo Mzire Maputire
Web Manager: Thina Bhebhe
Quarrying Africa is the information hub for the sub-Saharan African quarrying sector. It is a valued reference tool positioned as a must-read for the broader spectrum of the aggregates value chain, from quarry operators and aggregate retailers, to concrete and cement producers, mining contractors, aggregate haulage companies and the supply chain at large.
Quarrying Africa, published by DueNorth Media Africa, makes constant effort to ensure that content is accurate before publication. The views expressed in the articles reflect the source(s) opinions and are not necessarily the views of the publisher and editor.
The opinions, beliefs and viewpoints expressed by the various thought leaders and contributors do not necessarily reflect the opinions, beliefs and viewpoints of the Quarrying Africa team.
Quarrying Africa prides itself on the educational content published via www.quarryingafrica.com and in Quarrying Africa magazine in print. We believe knowledge is power, which is why we strive to cover topics that affect the quarrying value chain at large.
Printed by:
Email: munesu@quarryingafrica.com
Cell: +27 (0)73 052 4335
Following Babcock’s recent launch of SDLG excavators in South Africa, Amatshe Mining has become one of the first recipients, with seven units hard at work at its Firmabuild Aggregates operation in the West Rand, Gauteng. Deployed for digging and loading duties, the units have already proven their mettle in terms of performance, efficiency and productivity. By Munesu Shoko.
Having previously only distributed SDLG wheel loaders, motor graders and vibratory rollers, Babcock recently expanded the SDLG offering with excavators. While SDLG started manufacturing excavators back in 2010, these were previously not available for the local market. Following the recent introduction of these excavators in South Africa, Amatshe Mining was among the first customers to take delivery of the first SDLG excavators in the local market.
Established in 2017, the company has its roots in gold
7 Amatshe Mining has taken delivery of seven SDLG excavators. The machines, which have all been delivered this year, include five 21-t E6215H and two 35-t E6335F units 14
The 35-t E6335F consumes about 14 litres per hour, which is some eight litres less than a same-sized excavator the company ran before
Following the recent introduction of these excavators in South Africa, Amatshe Mining was among the first customers to take delivery of the first SDLG excavators now available locally
Amatshe Mining currently operates seven SDLG excavators, which are hard at work at its Firmabuild Aggregates operation in the West Rand, Gauteng
One of the central pillars to Amatshe Mining’s buying decision was the existing relationship with Babcock
In addition, Amatshe Mining was already aware of the SDLG quality, having previously run the Chinese manufacturer’s wheel loaders
mining and operates opencast operations in the West Rand. Understandably, the two directors – Izak van Zyl and Eddie Milne – both come from a gold mining background. In August 2018, the company bought its first aggregate operation in Durban Deep, Roodepoort, which is in fact an extension to its gold mining operations. As part of the rehabilitation process, the company turns waste material from its gold operations into aggregates for construction. In February 2023, the company further expanded its quarrying footprint with the acquisition of Firmabuild Aggregates which has been a leading manufacturer
of sand and stone on the West Rand for the past two decades. The operation is located within the same footprint as Amatshe Mining’s gold mining right, where the company basically mines gold from legacy dumps. Here, the company also processes legacy material to produce various sizes of aggregate, including G5-G9 subbase material, 13 mm and 22 mm concrete stone, dump rock and gabion stone, builder’s mix, as well as plaster and building sand, amongst others.
It is at this operation where the new SDLG excavators are hard at work, deployed to dig loose rock, load trucks and feed processing plants. The seven new machines, which have all been delivered this year, include five 21-tonne (t) E6215H and two 35-t E6335H units. “We ordered our first machines in November 2023, a 21-t and a 35-t, which were delivered in January this year. Subsequently, we have added four more 21-t machines and one 35-t unit,” explains Milne.
According to Milne, one of the central pillars to the buying decision was the existing relationship with Babcock. In fact, Milne, in his previous capacity, recalls buying his first ever machine from Babcock back in 2015, a Volvo EC480 excavator, which to date has clocked over 30 000 hours and still counting. In addition, Amatshe Mining was already aware of the SDLG quality, having previously run the Chinese manufacturer’s wheel loaders.
“Our association with the SDLG brand dates back to 2018, when we purchased our first two SDLG front-end loaders, a FL958 and a FL968, before we expanded the fleet over the years. With 20 units running at our operations, we have one of the largest SDLG wheel loader fleets in South Africa,” Milne recalls. “We have found the SDLG offering to be competitively priced, yet it delivers the same production as some of the same size premium solutions we have run before.”
Babcock’s Rob Baker, SDLG equipment sales, agrees, saying that the range is fast becoming recognised as a high-quality, value offering in southern Africa.
“The market is clearly recognising the many advantages the SDLG range offers –competitive pricing, high quality, durability and reliable aftersales support delivered by Babcock through its extensive footprint in the region,” says Baker.
“In our view, this is a good quality, cost-effective, value product with a ‘premium’ touch to it. Given that Volvo Construction Equipment, our major principal, owns 70% of SDLG, one can easily recognise the premium Volvo design heritage in this line of excavators,” adds Mark Senyard, Product Manager – SDLG at Babcock.
When Quarrying Africa visited the site, the SDLG excavators had been operational for between three and six months, but had already impressed with their performance and efficiency. Most of the 21-t units are deployed to load loose material onto tipper trucks, which in turn feed the processing plants.
In addition, these machines are also deployed in the pit, digging and loosening material for loading, as well as feeding in-pit mobile crushers and screens. Despite the daunting nature of this application, Milne has been impressed by the E6215H’s breakout force, which he says is on par with some of the premium solutions in the 21-t size category. In fact, he says, the machine is punching well above its size and performing beyond expectations.
“Given its compact nature, the 21-t machine is wellsized for our operations. We extract material from narrow reef bands. With its 1 m³ bucket, it is easy to do selective mining in such a narrow working environment. The 21-t class size machine is also ideally suited to load the 10 m³ tipper trucks that we use for hauling material from the
Amatshe Mining is impressed by the E6335H fuel efficiency –the machine consumes about 14 litres per hour.
face to the processing plants – it fills a 10 m³ truck with four passes,” says Milne.
Apart from performance, the Amatshe Mining team has been impressed by the range’s fuel efficiency. To provide context, Van Zyl says the 35-t E6335H is consuming about 14 litres per hour, which is some eight litres less than a same-sized excavator the company ran before, while achieving the same level of production. Meanwhile, the 21-t machines are consuming 12-13 litres of diesel per hour which, according to Van Zyl, is still better than the previous machines.
Commenting on what makes the range so fuelefficient, Senyard says the SDLG excavators come with an electronically controlled unit pump which adopts a high-pressure fuel supply system to deliver high injection pressure, sufficient combustion and good power. The engine electric control unit (EECU) controls the fuel supply throughout the process and matches the relationship between the load and the output of the main pump, ensuring both sound performance and fuel consumption. This contributes to a 10% reduction in fuel consumption compared with the previous SDLG generation.
In addition to the performance and efficiency of the SDLG excavators, both Milne and Van Zyl are happy with the support from Babcock, from machine sales to
Watch: Eddie Milne, Director at Firmabuild Aggregates, explains the reasons behind the recent acquisition of SDLG excavators from Babcock.
aftermarket. “Babcock has proven to be a true partner to our business. They collaborate closely with us to find fitting solutions to our needs, be it financing or the machines themselves,” says Milne.
Babcock’s Senyard says the company has established a dedicated sales team to look after the SDLG range. “The brand still benefits from the same Babcock aftermarket support that our customers have become accustomed to,” concludes Senyard. a
In a cutthroat contracting environment where margins are very tight, Danoher Group places value on premium brands with long equipment longevity as one of the primary success factors. This is well illustrated by one of its Metso machines, a 12-year-old Lokotrack LT300HP mobile cone crusher which has amassed more than 30 000 hours and counting. By Munesu Shoko.
It is common knowledge that no one runs a business with the goal of losing money, but when it comes to profit margins, those for crushing contractors in South Africa are among the smallest in the world. In such a volatile and competitive market, Danoher Group, a major contractor which operates some 50 crushing and screening plants in southern Africa, does not leave anything to chance when it comes to the selection of its equipment – critical assets which are key to the success of its business.
Since its inception, Danoher Group has established itself as a household name in the southern African quarrying/mining industry, providing a full basket of contracting services from drilling and blasting to
crushing and screening (mobile and static). One of its key success factors, notes CEO Scott Danoher, has always been the careful selection of its equipment and optimisation of asset performance to ensure efficient operations.
Commenting on what informs the company’s buying decisions, Danoher says, first and foremost, the company runs an established standardisation policy. Trusted brands such as Metso (crushing and screening) are preferred and maintained to the highest standards, ensuring optimal plant availability. Since its inception, Danoher Group has always positioned itself as a premium service provider and
30 000
Over the years, Danoher’s Metso LT300HP crusher with over 30 000 hours, has been deployed on some flagship projects in South Africa and Botswana
In such a volatile and competitive contracting market, Danoher Group does not leave anything to chance when it comes to the selection of its equipment
The company runs an established standardisation policy. Trusted brands such as Metso are preferred and maintained to the highest standards
One of the fundamental factors that informs buying decisions is equipment longevity
With a similar approach to its capital purchases, Danoher buys a large percentage of its spares directly from the Metso OEM supplier, Pilot Crushtec International
this is projected through the equipment it runs and the condition in which it is kept. Reputation, stresses Danoher, is everything for the company and this is mirrored by the service it delivers.
One of the fundamental factors that informs buying decisions, however, is equipment longevity. While there are various factors that affect the longevity of equipment, Danoher says the principal ‘raw material’ is the design of the machine, an area where the Metso product excels.
“We do not necessarily buy a crusher or a truck, for example, for whatever amount, we buy the number of hours that it gives us,” he stresses. “For us, it is also not about the price tag, it is more about the cost per tonne or cost per hour – ‘cradle to grave’, which is a totally different dynamic. We are prepared to pay a premium upfront for, say 30 000 trouble-free hours out of our crushing equipment.”
15
For the past 15 years, Danoher Group has neither retired nor scrapped a machine within its crushing and screening fleet
Based on this approach, for the past 15 years Danoher Group has neither retired nor scrapped a machine within its crushing and screening fleet.
Over the years, the machine, a Metso LT300HP crusher with over 30 000 hours, has been deployed on some flagship projects in South Africa and Botswana. In fact, it has been in Botswana on four occasions during the past 12 years, where it executed some major projects at flagship mines such as Debswana’s Orapa Diamond Mine and Khoemacau, a long-life, copper-silver mine located in the Kalahari Copper Belt. During its stay in Botswana, the machine has also been deployed at Danoher’s own Kgale Quarry in Gaborone. Currently, this particular Metso LT300HP unit has been deployed at a major job in Mbombela, Mpumalanga, where Quarrying Africa was recently invited to see it in action. Here, the machine is working in a train with a Metso LT120 jaw crusher and a Metso LT330D cone-screen combination. The scope of the project entails the production of 350 000 tonnes of road stone for the rehabilitation and upkeep of the N4 Toll Concession. Material from this particular pit is supplied to five road contractors working on five sections of the road project.
After this project, Danoher tells Quarrying Africa that the machine will be deployed at another job near Malalane in Mpumalanga to crush material for the other four sections of the N4 road rehabilitation and maintenance project.
Every asset, says Danoher, has an optimum operating period of peak performance. After a certain period of use, wear and tear takes its toll as the asset ages. Eventually, this calls for some interventions at certain stages of the asset lifecycle.
“We basically expect 30 000 hours out of the motor during the first life of the machine. The crusher itself would probably come out for minor refurbishments a few times before the 30 000-hour mark. The electronics are probably the least robust components of the machine and thus need ongoing work during the life of the machine. The hydraulics, if looked after properly, can last for the whole life of the machine,” explains Danoher.
While the Metso LT300HP machine is still due for a second life overhaul, it has already been afforded a midlife refurbishment.
Key factors that determine the time for a midlife are the cost per hour and availability.
Apart from midlife and second life interventions, Danoher’s equipment generally benefits from a wellexecuted maintenance regime. Site teams are trained to focus their efforts on keeping the assets in good working condition to ensure efficiency and productivity, using preventative maintenance programmes, regular inspection schedules and regular routine maintenance.
“The backbone of our machine longevity is our maintenance philosophy. We instil in our site teams that their core job is maintenance. With a good maintenance regime, production takes care of itself,” explains Danoher.
Capital equipment is costly even at the best of times, says Danoher. Given the tight profit margins in the contracting fraternity, it is even more challenging or downright impossible to purchase new equipment at this stage, unless one is confident in the equipment delivering sufficient hours to make it profitable. Consequently, the company finds comfort in its Metso gear which, according to Danoher, provides unmatched long-life in the industry.
“Ultimately, it becomes a mathematical exercise as to what the second life is going to cost and how many hours more it will provide, versus buying a new machine,” he says.
“We always try to be proactive when it comes to wear checks. We have an online maintenance system where faults are checked and recorded twice a day. Although these interventions are not 100% ‘silver bullet’ solutions, they contribute to machine longevity,” says Danoher. With a similar approach to its capital purchases, Danoher buys a large percentage of its spares directly from the Metso OEM supplier, Pilot Crushtec International. The company also spends significantly in its own spares stockholding at site level to ensure machine uptime.
Over the years, Danoher and Pilot Crushtec have built a strong working relationship, a key parameter in Danoher’s buying decisions. “Relationships play a crucial role in what we buy. While a good product is principal, we also place value on the relationship with the equipment supplier and the people – that is very important. For us, Pilot Crushtec are more than just suppliers: they have become trusted business partners. Their parts stockholding is impressive and we are generally happy with their technical backup capabilities as well,” concludes Danoher. a
Celebrating 36 years in business this year, Portland Group remains one of the leading construction materials suppliers in the Western Cape Province of South Africa. With a clear growth trajectory, supported by ongoing investments in infrastructure and equipment, the company is well-positioned to capitalise on the construction boom in the region. By Munesu Shoko.
Established in 1988, Portland Group has over the past 36 years enjoyed sustainable growth. Having commenced its business with one operation, the flagship 65-hectare Durbanville Quarry, the company has through the decades expanded operations to include another quarry and a crushing operation, as well as a footprint of readymix plants in all the infrastructure hotspots in the Western Cape, as well as a precast concrete facility.
In recent years, the company has enjoyed massive construction development taking place in the Western Cape, leading to high demand for aggregates and readymix concrete. Portland
Group GM Martin Mostert tells Quarrying Africa that the province has in the last three years witnessed massive investment in construction activity, anchored by road upgrades as well as both commercial and residential building projects.
“We are fortunate to be located right in the thick of construction activity. One of the notable projects that we are currently supplying is the Vissershok road upgrade. Undertaken by H&I Construction, the project is on the doorstep of our Durbanville Quarry. The project – a major bypass off the N7 highway – is a significant piece of infrastructure in the Durbanville area. To provide context, apart from all the G-products, we are also supplying in excess
800 000 t
Apart from all the G-products, Portland Group is also supplying in excess of 800 000 tonnes of overburden for backfilling to the N7 highway, a significant piece of infrastructure in the Durbanville area
Established in 1988, Portland Group has over the past 36 years enjoyed sustainable growth
In recent years, the company has enjoyed massive construction development taking place in the Western Cape, leading to high demand for aggregates and readymix concrete
Western Cape has in the last three years witnessed massive investment in construction activity, anchored by road upgrades as well as both commercial and residential building projects
To enhance its overall capacity, Portland Group has recently invested in two additional quarries
of 800 000 tonnes of overburden for backfilling purposes,” says Mostert.
To meet the high demand for aggregates, Portland Group has embarked on significant plant upgrades at its Durbanville Quarry. The quarry is renowned for its quality aggregates from the natural Malmesbury Hornfels deposits.
“At the moment, we are busy with our second set of upgrades, entailing the installation of a new Techroq
40 km
In April this year, Portland Group further expanded its aggregate capacity with the acquisition of its Portland Paardeberg Quarry just outside Malmesbury, some 40 km from the existing Durbanville Quarry
screen and automated feed bins for the two cone crushers in our plant setup. These upgrades are aimed at increasing capacity,” says Mostert.
The latest enhancements follow hard on the heels of last year’s upgrades, when the company installed a new CH430 cone crusher and a new Techroq vertical shaft impact (VSI) crusher. The cone crusher’s purpose was to increase plant capacity, while the VSI’s rock-on-rock crushing is being used to improve the shape of crushed aggregate particles. In addition, the company installed a new, larger transformer to sustain the new crusher additions to the quarry.
To enhance its overall capacity, Portland Group has recently invested in two additional quarries. About two years ago, Mostert explains, the company opened the Portland Worcester Quarry in Rawsonville. However, this was not a fully operational quarry; rather, it served as a crushing site that processed river material.
“The Portland Worcester Quarry was a short-term project that has now concluded. In fact, at this project, we helped the community with the maintenance of the river, which, due to heavy rains, kept filling up with natural brown stone. When that happened, the river flooded nearby farms and houses. Armed with a river management plan, we removed the brown natural stone and crushed it at a nearby property to produce single-size aggregates such as 20 mm and 14 mm concrete stone.”
The product from this material was unique, and most of it was used to produce exposed aggregate concrete. Here, Portland Group produced between 10 000 and 15 000 tonnes per month (tpm). The material was destined for Portland’s own readymix plants as well as external customers who specialise in exposed aggregate concrete.
In April this year, Portland Group further expanded its aggregate capacity with the acquisition of its Portland Paardeberg Quarry just outside Malmesbury, some 40 km from the existing Durbanville Quarry.
“As a group, we decided to purchase this to have a variety of material to offer our clients. The granite rock here complements our Malmesbury Hornfels deposits from the Durbanville Quarry. Being able to offer different material choices to our customers makes business sense,” he says.
The acquisition of the Portland Paardeberg Quarry also expands Portland’s product range to include high-quality sand from the sand mine on the quarry. Following the acquisition, the company has also invested in a major plant upgrade to boost capacity, entailing the installation of a new jaw crusher and a Sandvik CH430 cone crusher. The Portland Paardeberg Quarry produces between 25 000 and 30 000 tpm of single-size aggregates, while sand production is between 10 000 and 12 000 tpm.
For years, Portland Readymix has provided a range of readymix concretes designed for the whole spectrum of the construction industry. These products are backed by the company’s expertise and tight quality control which brings a guarantee of strength and workability. The company also offers highperformance, decorative and special application concretes to cater for all the industry’s concrete needs.
“We have a rich history of product development, reliability and technical expertise and our products are specifically designed for a wide range of applications. Portland has a unique capability to pool resources and execute large and challenging pours anywhere in the Western Cape,” says Mostert.
The increased demand for concrete has in recent years led to the expansion of readymix plants in Malmesbury Swartland (2022), Saldanha (2023) and Paarl. For years, the company operated two readymix plants in Durbanville before establishing a 36 m³ per hour plant in Paarl Swartland. In Paarl, the company is currently adding a second concrete batching plant, which will take the company’s capacity in the area to 90100 m³ per hour.
In March this year, Portland established a crushing plant to process waste slag for the production of readymix concrete in Saldanha. The 90 m³ per hour plant is Portland Group’s largest readymix concrete batch plant to date.
In 2008, Portland expanded its operations to include the manufacture and installation of precast hollow core slabs. At the time, the company acquired state-of-art technology from Elematic in Finland to make sure that it produces high-quality slabs. The company provides a complete service, from design (by its in-house design team) to manufacture (in its purpose-built factory) and finally installation (by experienced rigging teams).
Portland frequently upgrades its operations and has recently expanded its stockyard to increase storage capacity. Extra casting beds were also installed to increase capacity for production. With these new extensions, the company has created better turnaround times, higher production levels, better handling
Helping miners move less rock, use less energy, use water wisely and create less waste.
Weir is a global leader in mining technology. We recognise that our planet’s future depends on the transition to renewable energy, and that transition can only happen with the metals and minerals our mining customers deliver.
With signature brands including ESCO®, WARMAN®, ENDURON®, GEHO®, CAVEX®, LINATEX®, and MOTION METRICSTM, we combine our deep customer insights, world class engineering, materials science expertise and intelligent automation to deliver innovative end-toend mining technology solutions that help our customers move less rock, use less energy, use water wisely and create less waste — accelerating the path to smart, e cient and sustainable mining.
global.weir
of panels (by use of the extended stockyard), and quicker loading of trucks, which in the end, has had an enormously positive outcome for all involved.
The Portland hollow core production plant, which is situated at the Durbanville quarry premises, produces an average of 700 m² of precast slabs per day. The operation has recently been boosted by the purchase of a new extruder which, according to Mostert, is a significant investment.
To further support growing operations and market demands, the company has recently invested in two 30-t Volvo articulated dump trucks (ADTs) and two excavators (Volvo and SDLG) from Babcock. The two ADTs and the Volvo excavator have been deployed at the Durbanville Quarry.
In addition, Portland has purchased new FAW readymix concrete trucks. The company runs a total fleet of 26 readymix trucks, including 6 m³ and 8 m³ units. “We have a stringent replacement cycle for our readymix trucks. This year alone, we have taken delivery of nine new trucks, with a few more expected before the end of the year,” says Mostert.
Commenting on some of the considerations when investing in new gear, Mostert says the company always places value on the latest technology and equipment to maintain efficiency and competitiveness.
“We also consider the long-term sustainability and operational reliability of equipment. For example, the build quality of the Volvo machines fits the bill for our operational requirements. This is complemented by the
he says.
A member of surface mining industry association, ASPASA, Portland Group maintains high standards of health and safety across its operations. The company invests in regular safety training and certification to ensure that all employees are up-to-date and familiar with the necessary training procedures.
“As part of our safety protocols and procedures, we conduct routine safety audits and inspections of our equipment and facilities. We also continuously invest in safety equipment and technology to protect workers. In addition, we develop emergency response plans and conduct regular safety drills to create familiarity with escape routes, assembly points and communication procedures, promoting a quicker and more organised response,” concludes Mostert. a 90 m³
artin Engineering’s broad variety of both primary and secondary conveyor belt cleaners effectively minimize a multitude of costly carryback issues. Controlling fugitive material of every kind not only slashes unscheduled downtime for cleanup and maintenance but also helps prevent potential injuries to workers. Martin stands ready to provide you with expert, industry-specific advice and assistance on all of your bulk material handling questions and concerns.
To preserve uptime, increase efficiency and maximise productivity in loadout operations at various mines where it operates across South Africa, RT Loaders, part of the Reinhardt Transport Group, has, since 2016, equipped its entire fleet of wheel loaders with Loadrite on-board weighing systems from Loadtech. The company recently became one of the first recipients of the new Loadrite L5000 system, which made its local debut at the start of this year. By Munesu Shoko
RT Loaders is a division within the larger Reinhardt Transport Group (RTG), responsible for loading both RTG and other transporters’ trucks at various loading points at mines. Although the group has always had this function within its ranks, it was previously never a dedicated division. Following the expansion of the loading fleet in recent years, a decision was taken some two years ago to establish a dedicated division to look after the yellow metal fleet deployed at the group’s loadout operations across various mines.
With a fleet in excess of 1 000 trucks across its various renowned transport brands – Reinhardt Transport, Chrome Carriers, Transmac, Amalgamated Bulk and S Hauliers –RTG is one of the largest privately-owned side
tipper transporters on the African continent. The group specialises in bulk transportation of commodities, including chrome, coal, manganese, fertilisers, metallurgical coke, ferro chrome, iron ore, mill scale, grains and gypsum, across South Africa and neighbouring countries.
Headed by divisional manager Gordon Losper, RT Loaders operates a large fleet of 23 Lovol FL968H loaders, four skid steers, four water bowsers, one dozer, one excavator and about nine light-duty vehicles (LDVs). Losper tells Quarrying Africa that the wheel loaders are responsible for loading trucks at various loading points. Given the criticality of these loadout operations, which are responsible for handling about 674 000 tonnes per month or 8-million tonnes per year, on average, the company
1 000
With a fleet in excess of 1 000 trucks across its various renowned transport brands, RTG is one of the largest privately-owned side tipper transporters on the African continent
RT Loaders operates a large fleet of 23 Lovol FL968H loaders, which are all equipped with Loadrite load weighing systems from Loadtech
is impressed by the L5000’s real-time data monitoring and analysis capabilities.
RT Loaders, part of the Reinhardt Transport Group, has, since 2016, equipped its entire fleet of wheel loaders with Loadrite on-board weighing systems from Loadtech
The Loadrite systems have transformed the way in which RT Loaders conducts its loadout processes
The company is one of the first recipients of the new L5000 in South Africa, with two of its wheel loaders –one in Rustenburg and the other in Steelpoort – running with the system
Overall, the L5000 SmartWeigh system is poised to streamline weighing processes, improve productivity and provide valuable insights for better decisionmaking in various industries
has over the years trusted the accuracy and precision of Loadrite on-board weighing systems to eliminate guesswork in its loading operations.
According to Losper, the Loadrite systems have transformed the way in which RT Loaders conducts its
loadout processes. Traditionally, operations relied on weighbridges alone, which are well known to be prone to product errors and inaccurate weight challenges.
In addition, a key operational headache in conventional operations was the loading of incorrect tonnages in trucks, which resulted in unwanted downtime. In an event that trucks were under- or over-loaded, this would only be discovered at the weighbridge. Consequently, the truck would need to turn back to the loading point to load the correct tonnage. This resulted in unnecessary downtime and high costs associated with re-handling of material.
Loadrite onboard weighing systems are designed to eliminate these problems, which is why RT Loaders has fitted all of its 23 wheel loaders with the technology. Loadrite on-board weighing systems are used to calculate the weight of material in a loader’s bucket, relay this information to the operator and record the weight for later use. The data acquired from tracking the amount of material moved per hour is then used internally as part of an overall business analysis to measure productivity and set benchmarks.
“One of the reasons we opted for Loadrite from the onset is the accuracy and precision of the technology, which is very important to our operations. Although Loadtech generally specifies a single calibration once every three months, we calibrate our systems once every month to keep them in tip-top condition and maintain high levels of accuracy,” explains Losper.
Having access to data from load weighing systems,
adds Losper, is key to ensuring efficient and productive loadout operations. The insights derived from the Loadrite systems can be turned into actionable changes to improve efficiency and productivity.
“The technology is more than just a load weighing system; in our operations we also use the Loadrite system to manage operator performance, which informs our bonus structure. Available data from the system shows the tonnages each operator has loaded. Those who go the extra mile are rewarded, based on a prescribed bonus structure we have in place,” says Losper.
For its wheel loaders, RT Loaders maintains a systematic replacement cycle where machines are traded in for new ones once they reach 8 000 hours. Loadrite systems fitted on these machines are simultaneously traded in for new units to be installed on the new wheel loaders. Loadtech, the sole supplier of the Loadrite system in sub-Saharan Africa, has an excellent buy-back programme for its Loadrite on-board weighing systems.
connectivity enables seamless data transfer and real-time monitoring. The touchscreen interface offers intuitive and user-friendly navigation, enhancing ease of use for our operators.”
Loutjie van der Merwe, Loadrite divisional manager at Loadtech, says with its WiFi readiness and touchscreen interface, the L5000 is revolutionising the industry by providing more convenience, accuracy and efficiency in weighing operations.
“Overall, the L5000 SmartWeigh system is poised to streamline weighing processes, improve productivity and provide valuable insights for better decision-making in various industries. Its innovative features have the potential to change the way weighing systems are used and perceived, making Loadrite a frontrunner in the market,” says Van der Merwe.
Apart from the accuracy and precision of the Loadrite technology, RT Loaders is also pleased with the backup support from Loadtech. “Over the years, dealing with Loadtech has been a breeze, which is why we also use their Loadrite systems in our Performance-Based Standards (PBS) trucks,” says Losper. “Loadtech understands the support we need for our 24/7 operations and it is always there to provide the service we need.”
t
While the majority of the existing loaders within RT Loaders’ fleet are installed with the Loadrite L3180, the company is one of the first recipients of the new L5000 in South Africa, with two of its wheel loaders – one in Rustenburg and the other in Steelpoort – running with the system. Quarrying Africa recently visited RTG’s operation in Rustenburg, where one of the loaders installed with the L5000 is deployed to load trucks. Losper and his team are particularly happy with the L5000’s advanced features.
“We are impressed by the L5000’s real-time data monitoring and analysis capabilities,” explains Losper. “The system’s wireless
In addition, Loadtech has a dedicated data specialist who works closely with RT Loaders and other customers to help interpret and make sense of the data generated by the Loadrite systems. This makes a significant difference in customer operations. Data is one thing and making sense of it is quite another. Having a dedicated data specialist is therefore a big benefit for customers who need to translate data into workable solutions for their businesses.
“In recent times, we have also grown our technical team, which is key to our support capabilities. Consequently, we can now guarantee our customers quick turnaround times for any technical issues. We also offer continuous operator training and stay connected with all our customers,” concludes Van der Merwe. a
At a time when quarries and mines face increasing demand for sustainable and cost-effective production, Scania South Africa used Electra Mining Africa to showcase its upgraded mining tipper. Placing a special design focus on increased productivity and fuel efficiency, the 40-tonne (t) rated payload tipper allows quarries, mines and their contracting counterparts to haul more volumes for less. By Munesu Shoko.
30%
Given that transportation, on average, accounts for about 30% of total mining costs at most opencast operations, mines and quarries are putting efficiency of their hauling gear at the top of their list of priorities
60-t
The new heavy mining tipper comes with a 60-t gross vehicle mass
40-t
The vehicle’s 40-t rated payload plugs the payload gap between conventional tipper trucks and their yellow metal counterparts
Given that transportation, on average, accounts for about 30% of total mining costs at most opencast operations, mines and quarries are putting efficiency of their hauling gear at the top of their list of priorities.
While construction type tippers have traditionally been deemed ideal for light duty applications such as ore rehandling and moving processed material between processing plants and stockpiles, there is a growing acceptance that these trucks are equally robust enough to take on arduous applications such as hauling run of mine (ROM) material from the rock face to the processing plants.
A case in point is Scania’s new G460 XT heavy mining tipper, which headlined Scania South Africa’s exhibit at Electra Mining Africa, the premier mining show which took place from 2-6 September at the Johannesburg Expo Centre. Vinesh Kalu, Segment Manager – Scania Mining at Scania South Africa, tells Quarrying Africa that the heavy mining tipper is built to handle in-pit haulage operations in
mines and quarries.
“I am confident that the new Scania heavy mining tipper will add value to our customers’ operations,” says Kalu. “Today’s mine owner has to grapple with the everchanging face of the market. The new requirements are very clear: operations have to simultaneously cut their emissions and meet efficiency targets or face extinction. With Scania’s unmatched fuel economy and improved payload, the heavy mining tipper offers lower operational costs, making a big difference in our customers’ margins and bottom lines.”
One of the major talking points on the new heavy mining tipper is the increased 60-t gross vehicle mass (GVM) with a rated payload of 40 t, which plugs the payload gap between conventional tipper trucks and their yellow metal counterparts. With its excellent equipment-to-payload ratio and greatly improved technical availability, the new offering can be specially tailored to meet any type of mining-specific demands.
The mining tipper’s 40-t payload, says Kalu, is the most prominent improvement on the new offering compared with its predecessors. The increased truck payload enables mining and quarrying operations to consolidate loads and thus reduce the amount of vehicle movement required to distribute a given quantity of material on site. This yields economic, safety and environmental benefits. In addition, fewer trucks on site translate into less operating costs related to maintenance.
To sustain the increased payload, the new XT mining tipper benefits from a more robust suspension. The new mining tipper is equipped with heavy-duty rear axles with cast-iron housings to stand the test of challenging, rough mining conditions. Both rear axles are equipped with shock absorbers to improve traction and comfort.
“Heavy duty suspension, shock absorbers and anti-roll bars offer increased stability. The Scania Retarder improves braking performance and reduces wear on the wheel brakes, especially on downward slopes,” says Kalu.
Another value proposition of the new G460 XT heavy mining tipper is its fuel efficiency, a critical parameter, not only to help mining and quarrying customers reduce their cost per tonne, but also to meet their emission reduction efforts in line with their Environmental, Social and Governance (ESG) targets.
“The G460 XT mining tipper engine delivers high
“With Scania’s unmatched fuel economy and improved payload, the heavy mining tipper offers lower operational costs, making a big difference in our customers’ margins and bottom lines.”
Scania South Africa used Electra Mining Africa to showcase its new G460 XT heavy mining tipper
One of the major talking points on the new heavy mining tipper is the increased rated payload of 40 tonnes
To sustain the increased payload, the new XT mining tipper benefits from a more robust suspension
Scania South Africa has partnered with Efficient Engineering to develop the tipper body
torque output as well as outstanding fuel efficiency,” says Kalu. With improved engine performance and leading emissions control through the Scania Twin-SCR system, the Scania Super 13-litre engine sets a new industry standard for brake thermal efficiency. This contributes to unrivalled powertrain fuel savings of 8%.
Dual overhead camshafts have been introduced to
enhance gas exchange and deliver unrivalled performance. The highintake air system has been developed specifically for dusty and exposed environments – this solution provides the engine with the cleanest air possible. The Scania Opticruise gearbox ensures smooth automated
gear changing, thus reducing driver fatigue. Scania Opticruise, one of the first automated gear changing systems on the market, has been refined in many steps over the years, and is now one of the smoothest and smartest systems on the market.
For operations that require the driver to be in charge for specific manoeuvring, Scania has introduced Clutch on Demand, a new performance step for Scania Opticruise. Clutch on Demand has an additional clutch pedal for convenient use in special conditions, otherwise the system works as an ordinary automatic clutch system. The new lay-shaft brake provides faster and smoother gear changes to maintain both engine torque and speed.
To meet specific market requirements, Scania South Africa has partnered with Efficient Engineering to develop the tipper body. The enhanced substructures of the bin are able to absorb the impact of the material thrown into the body. The material used to build the bin is suited for heavy duty mining. The projected life of the body has been greatly improved through addressing all the stress points of the bin.
“We have partnered with Efficient Engineering due to its understanding and experience in the mining industry. Efficient Engineering has been building dump bodies for over 30 years. The company has successfully met Scania Mining’s requirement in this build – which is to develop a light yet rugged body that maximises payload efficiency,” concludes Kalu. a
The Sandvik Leopard DI650i is an intelligent down-the-hole drill rig built for high-capacity production drilling applications.
Having made its global debut at Electra Mining Africa 2018, the Sandvik Leopard™ DI650i – an intelligent down-the-hole (DTH) drill rig built for high-capacity production drilling applications in surface mining and large quarry applications – has ‘cut the mustard’ in southern Africa. Scalable automation, ease of maintenance and efficient operation are some of the drill’s value propositions that have been central to its increased uptake. By Munesu Shoko.
From the onset, the design of the Leopard DI650i was meant to provide Sandvik Mining and Rock Solutions with a tool that would constitute a strong challenger for a market-leading position in the global DTH drilling market. When the drill rig was first introduced to the global market in 2018, the larger than 6” segment was dominated by a competitor’s product and the Sandvik Mining and Rock Solutions’ team thus had a special design focus on development of a drill rig capable of succeeding in the challenge of becoming the market leader in this segment.
Fast forward to 2024, the Sandvik Leopard™ DI650i has recorded significant success, not only in southern
Africa, but across the globe, with a large number of units operating in the field. To provide context, a total of 61 units are currently operating in southern Africa alone, confirms Trinity Nkosi, sales engineer, Surface Drills Department at Sandvik Mining and Rock Technology.
The Leopard DI650i, explains Nkosi, places a special design focus on intelligent DTH drilling, championed by scalable automation solutions, representing a major upgrade to the previous Titan range. In addition, the drill rig packs a punch with a combination of proven engineering solutions and innovative new components, ushering in a new era in ease of serviceability, fuel efficiency, safety and higher productivity particularly in challenging rock conditions.
61
A total of 61 Leopard DI650i units are currently operating in southern Africa alone
Having made its global debut at Electra Mining Africa 2018, the Sandvik Leopard DI650i has enjoyed significant success in southern Africa
The Leopard DI650i places a special design focus on intelligent DTH drilling, championed by scalable automation solutions
One of the major features of the Leopard DI650i is the ease of service and maintenance, facilitated by ground-level access for daily maintenance and service points
Thanks to the intelligent control technology applied in both the compressor and the hydraulic system’s cooler fan, customers can expect greater fuel efficiency
The Leopard DI650i is a DTH machine that can drill up to a maximum depth of 53,6 m. Hole diameters range from 115 mm to 203 mm. While this can be scaled up to 222 mm, this would require factory approval due to the need to tailor some of the components on the machine in order to enable it to achieve this hole diameter. For shallow holes, the machine can drill up to a 305 mm hole diameter.
“The Leopard DI650i is ideal for hard rock formations with high resistance to drilling, such as igneous and metamorphic rock, as well as fractured rock formations,” says Nkosi. “While the drill is primarily targeted for mining, it can also be deployed in quarrying, construction and geothermal applications.”
At the centre of the Leopard DI650i’s popularity are a number of features and benefits that have appealed to the market, says Nkosi. Chief among them is the drill’s compatibility with the latest scalable automation solutions. Sandvik’s scalable automation concept offers an intelligent drill rig platform where automation options and digital services can be selected to speed up the production process. All the options can also be easily added and expanded afterwards, according to future automation demands.
As part of its scalable automation concept, Sandvik offers various automation levels – iDrill (onboard operation) and AutoMine® (remote operation). Automated onboard functions allow the rig to work from partial to full autonomously. The operator monitors at fleet level
53,6 m
The Leopard DI650i is a DTH machine that can drill up to a maximum depth of 53,6 m
“The maintenance crew can conduct all daily servicing tasks at ground level on both sides of the machine. The advanced serviceability features have in some instances increased the Leopard DI650i’s availability by up to 20% compared with conventional DTH rigs at a similar technology level.
Trinity Nkosi, sales engineer, Surface Drills Department at Sandvik Mining and Technology.
and takes control only when required. The onboard automation functions of Sandvik’s iSeries surface boom drill rigs form the basis for the remote operation, minimising the risk of human error.
“With on-board automation (Auto Drill), for example, the operator will tram the machine to where it is required, set it up and then press a button for the machine to start drilling on its own. The machine will also add and remove pipes.”
The AutoMine product group – Line-of-Sight, Control Room and Autonomous – offers autonomous and remotely operated drilling. It allows operators to
simultaneously control and monitor multiple surface drills from the comfort and safety of a remote control room.
One operator can control multiple drill rigs simultaneously, either by a line-of-sight setup from a van or trailer close to the operating area. Alternatively, a Control Room option may be selected to operate the drill rigs from any location be it on the mine site, or even from another city. This reduces exposure to noise, dust, vibration and exposure to hazardous environments. The operator monitors the fleet and can easily switch to control the rig requiring detailed attention.
The AutoMine system and intelligent rig control system ensure accurate and efficient drilling operations. The intelligent system helps to use the drill rig’s full potential in the many ways it is designed to be operated. AutoMine includes a safety system designed in accordance with international functional safety standards. This is critical for mines, where operator safety is of paramount importance.
to fleet utilisation, alerts and service indicators. With this package, customers can follow production, understand efficiency, know their fleet, understand performance, identify bottlenecks and review work practices,” explains Nkosi. “For example, one can link alerts to the operator, which helps develop a tailored training plan for the particular operator linked to the alerts.”
My Sandvik Onsite is a monitoring solution that transforms real-time data generated by Sandvik’s iSeries surface drill rigs into actionable insights for productivity improvements. The on-premises solution works on a local network and can be integrated into any surface mining system. “In addition to all the functions found on MySandvik Insight and Productivity, MySandvik OnSite also offers drill health, shift reporting and a production dashboard,” explains Nkosi.
Up to 15% less fuel consumption per hour is achievable largely due to Sandvik’s efficiencydriven design of minimising recirculation of hot air to coolers and having an energy-ondemand principle across the entire machine
When it comes to data monitoring, the MySandvik data portal is available in three subscription levels to access telemetry reports and dashboards. MySandvik Insight is the entry level package, which offers performance reporting for the machine. With insights on fuel consumption and metres drilled, fleet owners can follow production and understand efficiency of their drilling operations.
“With MySandvik Productivity, fleet owners have access
[Subhead] Features and benefits
One of the major features of the Leopard DI650i is the ease of service and maintenance. The majority of work that needs to be done from a service and maintenance perspective can be executed from ground level. In addition, the modular design allows for easy repair and replacement of components.
“The maintenance crew can carry out all daily servicing tasks at ground level on both sides of the machine,” explains Nkosi. “The advanced serviceability features have in some instances increased the Leopard DI650i’s availability by up to 20% compared with conventional DTH
Thanks to the intelligent control technology and designs applied in both the compressor and the hydraulic system’s cooler fan, customers can expect to reduce their fuel consumption significantly compared with conventional DTH rigs.
“Up to 15% less fuel consumption per hour is achievable largely due to our efficiency-driven design of minimising recirculation of hot air to coolers and having an energy-on-demand principle across the entire machine,” says Nkosi. “In addition, the compressor management system reduces compressor load for nondrilling activities, thus reducing fuel consumption. This also speaks to reduced CO2 emissions, which is critical for mines seeking to achieve their Environmental, Social and Governance (ESG) targets.”
rigs at a similar technology level.”
Thanks to the excellent visibility to the drilling area and a single integrated touchscreen graphic user interface (GUI) for all monitoring, diagnostics and mining automation displays, the Leopard DI650i’s ergonomic iCAB cabin provides the operator with a safer, productive working environment. Noise levels are kept low at under 78 dB, well below the 85 dB specified by the MHS Act, thus increasing operator safety and reducing fatigue.
“All the information the operator requires regarding the drilling operation is available on the GUI, while the CANBUS system allows for quicker troubleshooting on the GUI. The iClean function uses a special blend of water and air volume flushing to keep holes open for longer, especially after drilling in fractured ground,” says Nkosi, adding that operators can also expect +20% more tramming power than the same technology level DTH drill rigs.
The machine’s fuel efficiency is further boosted by the iflow control system that eliminates fluctuations in airflow, instead allowing the pressure level to fluctuate in response to more difficult ground conditions and increased back pressure (for example, due to groundwater or collapsing holes). This increases the flushing pressure and penetration rates in most challenging rock conditions, while still retaining the low fuel consumption of the traditional pressure control approach in easy ground conditions.
In southern Africa, customers operating the DI650i benefit from Sandvik Mining and Rock Solutions’ extensive branch footprint across the region, supporting both parts availability and quick service turnaround times.
“On the service side, we have three product masters, eight product specialists and about 40 technicians in our ranks. On the parts side, we have multiple stockrooms across the region, with a 97% parts availability on frequently requested DI650i components,” concludes Nkosi. a
The TRIO TIO 5162 double deck screen offers continuous, reliable operation in wet and dry applications.
Having officially unveiled its Weir Modular Wheeled Plant (WMWP) concept earlier this year, Weir used Electra Mining Africa 2024 to demonstrate the first commercial unit which, from a comminution standpoint, was the major attraction on the company’s stand. Judging from enquiries and customer feedback, the unit has generated a great deal of interest in the market. By Munesu
Shoko.
In response to the growing demand for comminution solutions that place high value on mobility and ease of deployment, Weir announced the reintroduction of its WMWP concept at the start of this year, which was followed by a customer launch event in the first half of the year.
While Weir’s TRIO® brand previously had a legacy range of wheeled plants, which made use of TRIO crushers, screens and materials handling solutions, the solution has been completely redesigned to suit new market dynamics. The WMWP concept now combines all the features and benefits of Weir’s TRIO and ENDURON® ranges of equipment in an easy to deploy and relocate, complete crushing and screening solution.
At Electra Mining Africa, which took place from 2-6 September at the Johannesburg Expo Centre, Weir demonstrated its first commercial unit which, according to Hakan Karlsson, Director Crushing and Screening at Weir, generated a lot of interest, signalling the acceptance the concept has garnered since its official introduction earlier this year.
On display at Electra Mining Africa was the Weir Modular Cone/Screen WMWSC36-5162, a combination of a TRIO TC36 cone crusher and a TRIO TIO 5162
double-deck screen on a single trailer. The solution can be operated as a standalone unit or as part of an existing plant. It can also be integrated as a fully mobile solution, highlighting the versatility of Weir’s wheeled modular plant offering. Soon after Electra Mining, the unit was destined to be deployed at a gold dump reprocessing and aggregate production operation in Gauteng, South Africa.
Jaco Kotzé, Team Leader Comminution Design at Weir, tells Quarrying Africa that the design of the unit was informed by customer feedback. The goal, he says, was to create and deliver a product that meets or exceeds customer needs and expectations.
“Following the customer launch event, we had good customer inputs and insights which, to a great extent, informed the design of the first commercial unit. We took the feedback to heart and fine-tuned the first unit, which we showcased at Electra Mining,” says Kotzé.
From the onset, adds Kotzé, the introduction of the WMWP concept was aimed at addressing specific customer needs in the market. Based on Weir’s feedback collection, the most relevant and useful
At Electra Mining Africa, which took place from 2-6 September at the Johannesburg Expo Centre, Weir demonstrated its first commercial unit which generated a lot of interest
Weir used Electra Mining Africa 2024 to demonstrate the first commercial unit which, from a comminution standpoint, was the major attraction on the company’s stand
Judging from enquiries and customer feedback, the unit has generated a great deal of interest in the market
On display at Electra Mining Africa was the Weir Modular Cone/Screen WMWSC36-5162, a combination of a TRIO TC36 cone crusher and a TRIO TIO 5162 double-deck screen on a single trailer
One of the major features of the WMWP concept is the unique hydraulic and mechanical deployment system which requires minimal truck-mounted cranage during site installation
aspects of the design were always going to be mobility and ease of deployment – key parameters that allow contractors to move on and between production sites.
“Given that the design of the WMWP concept addresses specific customer pain points, we have seen good acceptance in the market. In addition to mobility and ease of deployment, the concept offers the flexibility of a mobile plant and the productivity of a static plant. From an
The machines that Weir uses for its wheeled plants are in the 100 to 350 tonnes per hour range
“Given that the design of the WMWP concept addresses specific customer pain points, we have seen good acceptance in the market. In addition to mobility and ease of deployment, the concept offers the flexibility of a mobile plant and the productivity of a static plant.
Karlsson, Director Crushing and Screening at Weir
economic point of view, customers can enjoy the mobility of the plant without the complexity associated with additional maintenance obligations of components such as diesel engines and tracks related to mobile tracked units,” says Karlsson.
While Weir displayed a cone/screen combination at Electra Mining, the company’s wheeled plant concept will soon be
available in various configurations, starting from primary crushing solutions comprising a hopper, a vibrating grizzly feeder and a jaw crusher, to secondary crushing and stations which consist of a vibrating screen and a cone crusher. To combine these solutions, one can use Weir Modular Conveyors to configure a plant that is capable of producing aggregates for various end-use requirements.
More importantly, Weir utilises equipment that is within the dimensions and weights that can be accommodated on a multi-axle trailer. With that comes the limitation of the amount of mass that can be accommodated per axle, in addition to legal road limits on overall combination length, width and height. The machines that Weir uses for its wheeled plants are in the 100 to 350 tonnes per hour (tph) range. Once the throughput gets bigger than that, says Karlsson, the equipment becomes too heavy, and the solution loses the sense of mobility and resembles a fixed plant.
Commenting on some key features of the system, Kotzé makes special mention of the unique hydraulic and mechanical deployment system which requires minimal truck-mounted cranage during site installation. Its purposefully designed leg system raises the plant from wheels, levels it and installs main supporting legs without any cranes being required.
“The ease of mobilisation on site is a major feature of our wheeled plant concept; no expensive cranage is required. To provide context, we mobilised the unit which we displayed at Electra Mining with the help of a truckmounted crane and within half a day, the unit was fully assembled,” says Kotzé.
When in operation, the plant is supported by structural support legs with the operational load removed from wheels/axles and hydraulic lifts for working safety and structural stability, as well as resulting in reduced noise and vibration. All connections are done with structural pins and bolted connections, resulting in seamless integration of all components.
The modular primary jaw crushing units are fed directly with excavator or front-end loaders, with optional standalone hopper extensions for direct dump truck feed. The jaw-wheeled units include an integrated overband magnet system for removal of tramp metal. A surge hopper unit with an integrated belt feeder could be added in circuit to ensure proper choke feeding of cone crushers for optimal crushing quality and performance.
One of the major benefits of the Weir wheeled plant concept is that it eliminates the complexity of having a diesel engine as part of the unit as well as tracks which require additional maintenance, over and above the crushers and screens themselves. Consequently, customers can focus their maintenance attention on equipment that is core to their operation – crushers and screens – as the availability of these machines is what earns them money.
“By their nature, our wheeled plants are portable crushing and screening solutions with minimal civil requirements, which translates into both time-savings and reduced operational costs for customers,” says Kotzé.
These solutions can be transported on road with standard horse kingpin connection (South African road transport requirements) or containerised (subject to main equipment size) for shipping to remote sites where sea freight is more economical. Currently, says Kotzé, the plants are designed to meet road legal requirements for southern African countries, but this can be tailored to meet requirements in any other region.
“In addition, these plants are designed with safety in mind and ease of maintenance as the highest priority. Various crushing and screening wheeled plant modules seamlessly integrate together with the Weir Modular Conveyor System (WMCS), all could be powered from a central generator/master control wheeled unit, with cable racking and routing allowance already provided for,” says Karlsson.
With the development of the first unit, Kotzé says Weir has laid a solid foundation for the success of the WMWP concept. The next step is to broaden the range with other solutions such as jaw crushers, horizontal shaft impactors and vertical shaft impactors (VSIs). However, every plant will be tailored to each customer’s operational needs.
“We recently had a specific enquiry about switching out a cone crusher for a VSI to meet the customer’s material shaping needs for an aggregate application. We are therefore broadening the range to cater for the various needs of the market. We already have a full scope of what we want to offer, from primary to secondary and tertiary crushing,” concludes Kotzé. a
Following the official launch of its SAT40C, SANY Southern Africa is the latest entrant into the highly contested local articulated dump truck (ADT) market. With the arrival of the 41-t machine – the last piece of SANY’s mining puzzle – the company believes it has both the product and the competitive edge to challenge for a sizeable share of the market. By Munesu Shoko.
There is a new entrant into the southern African ADT market. SANY Southern Africa used Electra Mining Africa 2024 – which took place from 2-6 September at the Johannesburg Expo Centre – to introduce its first ever ADT to the local market.
In an exclusive interview with Quarrying Africa , Arno Franken, executive sales representative at SANY Southern Africa, the SAT40C ADT allows the company to plug an important gap in its mining product offering. Having already recorded significant successes with its rigid dump trucks, wide body trucks, excavators and wheel loaders in
54%
The 40-t class market constitutes about 750 unit sales per year, representing about 54% of the total ADT market in southern Africa
SANY Southern Africa used Electra Mining Africa 2024 – which took place from 2-6 September at the Johannesburg Expo Centre – to introduce its first ever ADT to the local market
The SAT40C ADT allows the company to plug an important gap in its mining product offering
The ADT comes on the back of rigorous testing in Indonesia and selected southern African markets
SANY’s competitive pricing, without compromising on quality and efficiency, is another major advantage for local ADT customers
37%
SANY’s launch price of the SAT40C is about 37% less than some of the competitive offerings in this size class
the local mining fraternity, Franken says the launch of the ADT now allows SANY customers to source all their mining equipment needs from one stable.
The ADT comes on the back of rigorous testing in Indonesia and selected southern African markets. Based on the feedback from this painstaking testing regime, Franken says the machine is ready to be deployed in the field. “The testing was quite extensive under some of the most challenging mining conditions. To date, we have already put over 120 units to work in the global market and we envisage a quick uptake in southern Africa as well,” says Franken.
Despite the competitive nature of the ADT market, Franken says SANY has done its homework and believes it has the right product and strategy to challenge for a share of the market. Firstly, he says, the company has chosen to debut in the 40-t class market, which is the biggest segment of the local ADT market to date.
To provide context, the 40-t class market constitutes about 750 unit sales per year, representing about 54% of the total ADT market in southern Africa. Key markets include coal, chrome, aggregates and the hard rock mining sector in general. On the back of increased demand, Franken says demand often surpasses available supply, leaving customers to endure long lead times. This is exacerbated by current global supply chain disruptions. In some cases, he says, customers have to wait for as long as 15-20 months to get their hands on new machines.
“Given the prevailing global production and shipping challenges, fleet owners looking to upgrade or replace their mission-critical equipment have to deal with record long lead times. Despite these challenges, customers can expect up to three-month lead times for their new SANY SAT40C ADT. This helps significantly with their planning,” says Franken.
In addition to short lead times, Franken believes SANY’s competitive pricing, without compromising on quality and efficiency, is another major advantage for local ADT customers. To provide context, SANY’s launch price of the SAT40C is about 37% less than some of the competitive offerings in this size class.
Powered by a Weichai engine delivering 390 kW of rated power and maximum torque of 2 300 Nm, the SANY SAT40C offers 41 tonnes of payload. The machine has a 20 m³ SAE-rated operating capacity which, according to Franken, is higher than the 18 m³ on most of the competitive products in this size class. In addition, the truck’s heaped capacity is 25 m³,
compared with 22 m³ on most other competitive products.
One of the key features on the SAT40C is its hydropneumatic suspension system, which reduces vibration loads for both the driver and the machine, increasing comfort. “Many conventional ADTs run standard suspension setups –comprising axles and oscillating frames. With hydropneumatics, the front and rear suspension of the truck operates with oil and gas (nitrogen), which offers good damping effect and maintainability, thus the impact of the rough underfoot conditions can be well absorbed and the driver can be comfortable during operation,” says Franken.
With uptime in mind, SANY placed a premium on easy access to all the service points when designing the SAT40C, which makes it quick and easy for
technicians to conduct service and maintenance on the machine. Any error codes are displayed on the digital screens inside the cab, making it easy for customers to troubleshoot their machines.
Equipped with an integral four-pillar tipping protection design and adjustable cushioned seat, as well as a tiltable and telescopic steering wheel, the cab provides a comfortable operating space and conforms to the requirements of ISO 3471. The cab also provides sound levels of less than 78 dB, thus increasing operator safety and reducing fatigue.
“The frame of the machine is made of high strength steel plates of boxtype construction, and features lightweight, good impact resistance, and high bending and torsional resistance. The cast structure reduces stress concentration and extends the machine’s service life,” concludes Franken. a
ELB Equipment’s partnership with Sumitomo began in 1984.
Key to an enduring partnership that stands the test of time are the alignment and commitment to a common set of values rooted in integrity, sound management and customer-centricity. This is the formula behind industrial equipment supplier ELB Equipment’s successful partnership with Japanese excavator manufacturer, Sumitomo, whose range of excavators offers the reliability and performance demanded by South Africa’s construction and mining sectors. By Chantelle Kotze.
ELB Equipment has over the years thrived on its best-of-breed approach, which has seen the company offer a comprehensive range of leading OEM construction, mining, earthmoving and agriculture equipment, designed to enhance productivity, efficiency and safety, from a single trusted supplier. The company’s partnership with Sumitomo, which began in 1984, fits perfectly into this approach.
The Sumitomo range of tracked excavators has been built for use in various applications, from smallscale earthmoving and construction applications, to large-scale, heavy-duty mining projects. The range includes the SH210-6 with a 21-t payload, SH260-6 with a 26-t payload, SH300-6 with a 30-t payload, SH350LC-6 with a 35-t payload, SH490LHD-6 Mass with a 49-t payload, SH700LHD-5B Mass with a
70-t payload, and the SH800LHD-5B Mass with a 80-t payload, all of which are available from ELB Equipment’s ten branches located throughout South Africa and the company’s southern African dealer network.
The range of excavators is driven by powerful, yet fuel-efficient Isuzu engines, combined with advanced hydraulic systems for smooth operation in demanding digging and loading operations. The excavators are also equipped with a rugged undercarriage for improved mobility and stability, as well as locally made general-purpose buckets that have been developed to withstand the tough African operating conditions. The buckets can also be modified to suit customers’ specific requirements.
Moreover, the excavator cabs were designed not only for operator comfort and usability but also with operator safety as a key priority. The spacious and
The 21-t Sumitomo SH210-6, while the smallest in the range, is the flagship excavator within the range and the one in highest demand within the domestic market
ELB Equipment’s partnership with Sumitomo is entrenched in both companies’ belief in ensuring customer satisfaction by innovating to meet customers’ specific requirements
The Sumitomo range of tracked excavators is built for use in various applications from small-scale earthmoving and construction applications to largescale, heavy-duty mining projects
The smaller 21-t, 26-t and 30-t payload Sumitomo excavators are preferred within the domestic quarrying sector
Sumitomo excavators meet the domestic market’s need for affordable yet reliable, high-quality, equipment, with dependable 24/7 aftersales service and consistent parts and maintenance availability and support
The Sumitomo excavators are equipped with a rugged undercarriage for improved mobility and stability in rough terrain.
comfortable air-conditioned cabs have an adjustable seat, improved operator visibility and are equipped with a locally-fitted window guard.
Gavin Baard, area sales manager at ELB Equipment, tells Quarrying Africa that the 21-t Sumitomo SH210-6, while the smallest in the range, is the flagship excavator within the range. It is also the one in highest demand within the domestic market, followed by the 26-t and 30-t excavators. This is due to their versatility in several
500
While the maintenance frequency depends on the operating conditions and usage intensity, service intervals generally take place after every 500-hours worked
“The 21-t Sumitomo SH210-6, while the smallest in the range, is the flagship excavator within the range and the one in highest demand within the domestic market, followed by the 26-t and 30-t excavators, due to their versatility in application.
sectors, ease of manoeuvrability, ease of transport and fuel efficiency, he says.
These smaller payload excavators are also the preferred size within the domestic quarrying sector, Baard adds.
Despite this, Baard notes an increasing trend in enquiries by customers for larger-sized, higher payload 70-t and 80-t excavators. However, these larger excavators are being received primarily by the mining sector, he says.
Besides enhancing overall productivity, efficiency and safety for users, Baard says Sumitomo’s excavators are aligned to the domestic market’s need for
ELB Equipment maintains a 24-hour turnaround time in any breakdown situation and carries the critical Sumitomo excavator spare parts at its branches for efficient servicing and maintenance.
and unanticipated issues and ultimately ensure the excavator is able to work for its over 20 000-hour lifespan,” he highlights.
affordable yet reliable, high-quality equipment, with dependable 24/7 aftersales service and consistent parts and maintenance availability and support.
In response to this, ELB Equipment maintains a 24-hour turnaround time in any breakdown situation and carries the critical Sumitomo excavator spare parts at its branches for more efficient servicing and maintenance, explains Baard.
in
Baard says that while the maintenance frequency depends on the operating conditions and usage intensity, service intervals take place after every 500-hours worked. “These intervals help to extend productivity, improve equipment availability, limit downtime due to unexpected
In terms of the growing industry-wide trend towards connectivity and realtime monitoring of equipment, and as part of the aftersales service offering, Sumitomo’s equipment can be monitored via the company’s G@Nav real-time information management system. This system uses GPS satellite tracking to transmit data from the excavator to the Sumitomo Data Centre.
The interactive and downloadable G@Nav application enables customers to receive equipment information such as location, fuel level, equipment utilisation and operation data, performance data and diagnostic trouble codes, allowing the customer and supplier to monitor and maintain the equipment more effectively.
In acknowledging the collaborative nature of its partnership with Sumitomo, Baard said ELB Equipment prides itself on the longstanding partnership, which is entrenched in both companies’ belief in ensuring customer satisfaction by innovating to meet customers’ specific requirements.
“Our single supplier philosophy has meant that we can offer a comprehensive array of best of breed equipment that can be tailored to suit our customers’ specific needs from one trusted and knowledgeable supplier. This ensures streamlined and efficient equipment management and service support for our customers, thereby increasing their productivity and in turn fostering longstanding client relationships,” explains Baard.
“It also provides our clients with peace of mind that the OEM range we have assembled is in fact market-leading equipment,” he concludes. a
Lower commodity prices and higher operating costs in the domestic mining, quarrying and construction sectors are squeezing profit margins. In response, asset owners are exploring the use of heavy-duty construction tippers for hauling applications to boost productivity and lower cost per tonne in a sector where traditional yellow metal haulers remain the standard. A local fleet services company identified the need for an extra heavy-duty truck chassis for challenging environments, leading to the development of a rugged vehicle designed for these tough conditions. By Chantelle Kotze.
The UD Miner was developed in response to a gap in the market for an extra heavy-duty chassis for use in challenging and tough mining, quarrying and construction environments
The UD Miner is based on the UD Trucks Quester CGE440 (E57C) extra-heavyduty model with an 8x4 rigid axle configuration
When compared to yellow metal equipment, such as articulated dump trucks, there are cost, fuel efficiency and productivity benefits to using a heavy-duty tipper truck, such as the UD Miner, in the mining, construction and quarrying sector
The UD Trucks dealer network has sold 647 Quester 8x4 axle configuration models in the past few years
Reytjie Laubscher, the MD of South African fleet services company Laubstar Fleet Services, together with UD Trucks Southern Africa, spearheaded the development and refinement of an extra heavy-duty tipper truck solution suitable for load and haul applications in demanding
60 countries
UD Trucks currently operates in more than 60 countries and on all continents
“As customers have indicated their excitement regarding the development of this vehicle, we now have several demonstrations booked during the rest of the year in which we will showcase the UD Miner in customers’ own operations.
29-t
The UD Miner has a 29-t off-road and 23-t on-road payload
“The UD Trucks dealer network has sold 647 Quester 8x4 axle configuration models and 1 619 Quester 6x4 axle configuration models in the last few years in South Africa alone.
mining and construction operations requiring higher payloads. From this development journey, which began in 2020 (but was disrupted by the COVID-19 pandemic), a powerful vehicle – dubbed the UD Miner – was born and launched to market at Electra Mining Africa 2024 in September this year.
Lichtenburg-headquartered Laubstar is an authorised dealer of Japanese commercial vehicle solutions provider UD Trucks, and owns the UD Trucks Lichtenburg, Upington, Kathu, Potchefstroom and Klerksdorp franchises. The company is also a distributor of aftermarket vehicle parts, accessories and systems through which it provides the domestic trucking industry
with premium trucks, trailers and services.
Laubstar’s specialist service offering allows the company to develop and custom-make trucks for the logistics, transport, commercial vehicle, mining and construction industries. It is also thanks to this diverse offering that the UD Miner came into being.
Laubscher tells Quarrying Africa that although UD Trucks has a long and rich history with 4x2, 6x4 and 8x4 tipper trucks built for the mining and construction industry, currently operating in more than 60 countries and on all continents, the development of the UD Miner pushes
The UD Miner is a specially-customised version of the UD Trucks Quester CGE440 (E57C) extra-heavy-duty model with an 8x4 rigid axle configuration.
the envelope and further demonstrates UD Trucks’ reputation of ‘Ultimate Dependability’.
The UD Miner is a specially customised version of the UD Trucks Quester CGE440 (E57C) extra-heavyduty model with an 8x4 rigid axle configuration that has also been equipped with a MegaTon II heavy-duty mining tipper body for in-pit hauling and load and haul applications at mines, construction sites and quarries, offering a 29-t off-road and 23-t on-road payload.
The UD Trucks Quester range of vehicles has 25 variants, all of which have been specifically developed for various types of heavy-duty construction and mining applications, and is designed for handling high payloads. The models in this range are offered in several chassis lengths, with different gearbox options, engine capacities and axle configurations, depending on their intended application, which makes the Quester range capable of handling tough jobs, with ease.
precise gear shifting and improved fuel efficiency.
The UD Miner’s MegaTon II heavy-duty mining tipper body has a 12 mm Hardox 500 wear-plate floor with 8 mm Hardox 500 sides, as well as dual tipping cylinders, a falling object protection system (FOPS) and inclination sensors, for safer operation.
Laubscher goes on to explain that the custom-made extra heavy-duty tipper truck solution was dubbed the UD Miner by Laubstar due to the modifications and upgrades made to the vehicles allowing it to take on the more demanding mining environment.
47 000 kg
Additional features of the Quester range that have been designed for heavy-duty applications are the truck’s robust chassis for rough and hilly conditions, a steel off-road bumper with high ground clearance and approach angle, a rolling-form frame suitable for both vertical and torsion stressors, and the 4x2 tractor or rigid, 6x4 tractor, or rigid and 8x4 rigid axle configurations.
Laubscher explains that the UD Miner has been designed for an off-road gross vehicle mass (GVW) of up to 47 000 kg, making it an ideal solution for heavy-duty operations in challenging environments. It has an 11-litre GH11E Euro III diesel engine that produces 330 kW of power at 1 900 rpm and 2 010 Nm of torque at 1 1001 400 rpm, together with a 12-speed gearbox with an automated manual transmission for easier and more
In terms of the upgrades and features that have been added to the Quester CGE440 (E57C) extra-heavy-duty model truck to create the UD Miner, Laubscher explains that engine protection plates have been added for increased underbody protection – a critical consideration for off-road applications, together with suspension upgrades for higher payloads and improved stability on rugged terrain.
Moreover, the UD Miner has been fitted with tilt sensors for improved off-road stability and handling on uneven terrain, while larger-than-normal 24-inch tyres provide improved handling and operational stability when carrying heavy loads in the most severe working conditions.
The UD Miner has also been fitted with an upright exhaust system to minimise dust emanating from exhaust fumes emitted towards the haul road, an automatic lubrication system, a pedestrian detection system as a legal safety requirement at local mine sites, and load cells for accurate and real-time payload measurement, Laubscher points out.
The custom-made extra heavy-duty tipper truck solution was dubbed the UD Miner due to the modifications and upgrades made to allow it to take on the more demanding mining environment.
Although the UD Miner was custom-designed as a tipper for in-pit hauling applications at mines, construction sites and quarries, Laubscher says the versatility of the Quester extra-heavy chassis allows it to be customised for use in several extra heavy-duty applications such as a water bowser, large off-road rollbacks, support vehicles, vacuum tanks, drill rigs, concrete mixers or even large mobile pumps, as well as for crane applications, or brick-handling applications.
As customers have indicated their excitement regarding the development of this vehicle, we now have several demonstrations booked during the rest of the year in which we will showcase the UD Miner in customers’ own operations, said Laubscher.
When compared to yellow metal equipment, such as articulated dump trucks, there are several standout
benefits to using a heavy-duty tipper truck such as the UD Miner, in the mining, construction and quarrying sector.
Willie Botha, sales manager at Laubstar, highlights the diverse range of variants in the UD Trucks Quester range that are suited for use in these sectors in several different applications. These are backed by a large dealer network with a large holding of spare parts.
“From a cost savings point of view, there are not only savings on the initial purchase price of the vehicle, but also on the overall durability of these trucks. Combined with their ease of maintenance and of serviceability as well as lower service, maintenance and repair costs, lower overall vehicle operating costs are the final outcome,” he points out.
Another major benefit of the Quester range is its fuel efficiency, due to the high torque and pulling power of the engine at low rpm, adds Botha.
When compared to yellow metal equipment, the Quester range of vehicles, which is rated for both on-road and off-road use, can complete more loads per shift. As driving distances increase, the speed of the Quester vehicles improves cycle times, leading to increased productivity.
According to Botha, heavy-duty vehicle sales within the UD Trucks dealers that Laubstar owns, have exceeded expectations. “The UD Trucks dealer network has sold 647 Quester 8x4 axle configuration models and 1 619 Quester 6x4 axle configuration models in the last few years in South Africa alone,” he says.
As the Quester range of vehicles continues to prove itself as a tough and versatile contender in the southern African mining, quarrying and construction sectors, Laubscher says that Laubstar, as a UD Trucks dealer, will continue to innovate and support the needs of the sector through improved vehicle efficiency and productivity, by finding ever smarter, more climatefriendly and sustainable ways for its customers to enhance their businesses. a
The partnership between Booyco Electronics and SafeGauge provides advanced wireless diagnostic tools for large mining, construction and earthmoving equipment, enhancing safety and operational efficiency.
SafeGauge technology enables remote monitoring and testing of machinery, reducing the need for workers to be near equipment during hazardous live testing procedures, minimising the risk of injury, including serious fluid injection injuries or crushing and pinching.
SafeGauge technology is renowned for enabling remote monitoring and testing of critical systems on heavy machinery without exposing workers to the dangerous conditions typically associated with live testing and equipment maintenance.
Louis Venter, area sales manager at Booyco Electronics, says that by allowing artisans to conduct tests and gather real-time data remotely, SafeGauge eliminates the need for workers to be in close proximity (line of fire) to large machines during potentially hazardous procedures. This innovation significantly reduces the risk of injury, creating a safer work environment across operations.
The SafeGauge range of equipment includes various specialised tools designed for different measurement needs. The PT (Pressure Transducer) Series is used to measure pressures in hydraulic and pneumatic systems, while the DI (Dial Indicator) Series is designed for measuring clearance, tolerance and wear on machine components. The TM (Tacho Meter) Series measures fan speeds and other rotating components, the LD (Laser Displacement) Series tracks wear on moving parts and the PR (Push Rod) Series is used to measure displacement between two fixed points.
Venter explains that all data collected by these tools can be processed through the Multitool Pro, which allows for real-time generation of reports and graphs.
“With its built-in cloud connectivity, the system makes it easy to export or share data instantly, streamlining operations and improving decision-making efficiency,” he adds.
Venter says that one of the most prominent benefits of SafeGauge equipment is the enhancement of artisan safety. “Heavy-duty machinery in the mining and construction industries can present significant risks during maintenance or diagnostic processes, particularly when it involves hydraulic systems or high-pressure environments,” he continues. “SafeGauge’s wireless
system allows these tasks to be performed without workers needing to be near the equipment, mitigating the danger of exposure to moving parts or sudden pressure releases.”
In addition to safety improvements, SafeGauge contributes to increased operational efficiency. By enabling real-time monitoring and remote diagnostics, equipment issues can be identified and addressed faster, reducing unplanned downtime and preventing costly failures. This proactive maintenance approach not only keeps operations running smoothly but also extends the life of key machinery components, minimising the need for expensive replacements.
“For businesses in mining, construction, forestry, agriculture and earthmoving, where operational continuity is crucial, SafeGauge’s ability to deliver timely diagnostics and maintenance insights is invaluable. It allows maintenance teams to perform their duties more effectively, ensuring equipment remains in optimal condition,” Venter says. “The result is higher productivity and lower maintenance costs, adding value to both dayto-day operations and long-term capital investment.”
“Through Booyco Electronics’ distribution of SafeGauge in Southern Africa, local operations now have access to this world class safety and efficiency solution, helping companies meet stringent safety standards and drive operational excellence in even the most demanding environments,” Venter concludes. a
Contact with the support structure can cause serious belt damage.
The moment a conveyor belt begins to wander, the safety and productivity of the system quickly degrade, and the cost of operation rises. Even a slight belt misalignment can lead to a variety of issues, from small annoyances to full-blown catastrophes involving a conveyor system. By Andrew Timmerman, global engineering manager, Martin Engineering.
Amisaligned belt can also come into contact with the stringer, causing fraying, shredding or splice damage. If this condition is not noticed right away, great lengths of valuable belting can be destroyed, and the structural steel itself can be damaged.
In fact, a high-speed belt edge rubbing on the support structure can cut through steel mounts with surprising speed, leaving a razor-sharp edge that poses a safety risk. Further, a compromised bracket or support can cause a catastrophic idler failure, which could damage other components of the system. All of these consequences of mistracking result in added expenses, higher maintenance and reduced efficiency.
Dave Mueller, senior product specialist at Martin Engineering, points out that beyond the many causes for mistracking, the belt training system that came with the conveyor may in some cases actually worsen the problem.
“We are seeing increased belt speeds and greater
cargo loads across most industries,” explains Mueller. “But some systems are equipped with belt tracking devices that are not able to handle those higher thresholds. We often see OEM trainers tied off with rope or chain in an attempt to drive a belt back into line.”
In the vast majority of cases, mistracking is a problem that can be corrected. Belt behaviour is based on a set of principles, which serve as the guidelines for ‘belt training’. Training a belt is the process of adjusting the conveyor structure, rolling components and load conditions to correctly centre the belt. Wandering is prevented by first understanding the basic patterns of belt behaviour and then following established procedures to carefully align the structure and components to correct any fluctuations in the belt’s path.
Belt drift can begin in any part of the conveyor system, and identifying mistracking is the first step
During the observation procedure, if the belt moves to one side and stays there, the problem may be one of three things: the head pulley lagging is not consistent, the last few carrying idlers prior to the pulley are out of alignment or the head pulley itself is not properly adjusted
When the belt is not centre-loaded, the cargo weight pushes the belt toward the more lightlyloaded side.
In the vast majority of cases, mistracking is a problem that can be corrected. Belt behaviour is based on a set of principles, which serve as the guidelines for ‘belt training’
Training a belt is the process of adjusting the conveyor structure, rolling components and load conditions to correctly centre the belt
Wandering is prevented by first understanding the basic patterns of belt behaviour and then following established procedures to carefully align the structure and components to correct any fluctuations in the belt’s path
Installing trackers is the economical solution, but operators should do a full analysis and consider also addressing other causal issues
toward correction. All of the traits listed below could be indicators of mistracking.
Edge Fraying – Probably an indication that the belt is rubbing on the conveyor frame at some point, degrading the edge, reducing the usable width and increasing the chance of a fire.
Excessive spillage – Could mean that one side of the belt has drifted higher on the trough angle, allowing cargo to discharge along the belt path.
Idler fouling – An off-centre load and uneven belt plane can foul idlers. Bearing abrasion can then cause the idler to seize, and the ensuing friction against the running belt can erode its coating and increase the risk of fire. Off-centre at head or tail pulley – This type of drift can lead to a fast-moving belt coming into contact with the conveyor stringer structure. There is also a chance of
Employing either a pivoting carrying roll or troughing set, short arms on both sides of the frame are positioned in advance of the pivoting roller and end in guide rolls located 25 to 75 mm from the belt edge
splice failure, which puts the entire system in jeopardy of the fast-moving belt detaching and causing a serious injury to workers in close proximity.
Lack of tail pulley protection – On many systems, the belt collects lumps of spilled material on the non-carrying side. If these objects are not removed, they can become trapped between the tail pulley and the belt, causing mistracking and often doing significant damage to both.
Uneven discharge – As the belt drifts to either side of the head pulley, the belt cleaners do not properly clean the entire surface, causing excessive carryback. Material collects on the pulleys and structure, fouling the return side of the belt, resulting in slippage, lost product and other negative effects.
Uneven loading – If the belt path leading from the tail pulley into the loading zone is uneven, the cargo can be loaded off-centre and cause excessive spillage. This may also be caused by inadequate transfer point design.
Starting at the head pulley, the belt should also be inspected for cupping, bow/camber (a long curvature) or crooked splicing. When observing the empty belt running over the head pulley, a cambered belt will drift to one side in the middle of the camber and then slowly return to centre as the belt travels through the head pulley. If a splice is crooked, the belt’s path will jump quickly to one side as the splice travels across the pulley. If it is discovered that these factors are the cause of mistracking, adjusting the conveyor’s rolling components will not correct the issue. The only options are either replacing the belt, or – in the case of crooked splice(s) – re-splicing the belt, assuming there is enough extra belting in the take-up system to allow removal of the faulty splice section.
During the observation procedure, if the belt moves to one side and stays there, the problem may be one of three things: the head pulley lagging is not consistent, the last few carrying idlers prior to the pulley are out of alignment or the head pulley itself is not properly adjusted.
Mistracking just after the head pulley on the conveyor’s return has two main causes. The first might be that the lagging is missing on one end of the pulley, so the pulley’s diameter is off-centre, placing uneven pressure on the belt and causing it to wander. If this is not the case, then the belt cleaning system may have been mounted slightly askew, putting greater pressure on one side of the belt and pulley. This uneven friction can also lead to mistracking.
Once operators and maintenance professionals properly identify the type of misalignment, they can then seek out the cause. “We have observed that there are three groups
Adjusting idlers for tracking can make correcting the belt for changes in speed or material harder later.
of common causes for mistracking,” Mueller points out.
“One is a fault with the belt or splice, another group is the conveyor’s structure, components or environment, and the last is due to improper material loading.”
Belt and Splice – If the belt is poorly manufactured or stored improperly, it can bow or camber. Poor installation of a vulcanised or mechanical splice can result in a splice that causes belt tracking problems. Exposure to the elements or to chemicals can degrade the carcass (plies or cords) and the cover of the belt. Faults and damage caused by mismatching the belt to the application and/or operating environment can require frequent replacement.
Conveyor Structure – Inaccurate alignment of the conveyor stringer structure can have subtle but lasting effects on the belt’s performance. Structural misalignment can happen due to age, bumps caused by machinery, effects of seismic activity, or even ground settling.
Outdoor conveyors – High winds require ‘wind loops’ to keep the belt in line. Exposure to extreme temperatures on one side of the conveyor can make components expand, causing changes in friction.
Improper Loading – The load’s centre of gravity will seek the lowest point of the troughing idlers, so if the belt is not centre-loaded, the weight of the cargo pushes the belt toward the conveyor’s more lightly-loaded side. This can be corrected by installing a central loading transfer chute or by using deflectors, grids or chute bottoms that can be adjusted to correct the placement of the load on the belt.
A common procedure to correct the wandering belt is to slightly adjust the return and carrying idlers against the direction of the mistracking. Unfortunately, the approach does not work on reversing belts. An even more serious consequence is that over time a number of the idlers may be misaligned, ‘fighting’ each other, as it were, to correct the alignment.
When idler training is not successful as a long-term solution, operators may be faced with a situation where the training procedure is repeated on a frequent (sometimes daily) basis. At that point, managers should consider installing some form of engineered training solution to mitigate the problem.
Engineered training solutions are devices that sense the position of a belt and, through a mechanism or geometry change, actively adjust its path. Some of the most common types include:
Belt Misalignment Switches – The wandering belt pushes a lever arm and activates a switch, which either sets off an alarm or stops the system. Costly downtime can result from these systems.
Vertical Edge Guides – These are positioned perpendicular to the belt’s path to keep the edge away from the conveyor structure and should not be used to compensate for persistent misalignment problems. Use of these guides is most practical on short, low-tension systems and is not particularly effective on thin belts, as operators have experienced the belt rolling over on itself.
Vee Idlers and Rollers – Set on both the cargo side and return side of the belt, these use a trough configuration and edge brackets that rely on a centering force to correct the belt path, which can add stress on the belt
and lead to damage. These systems are more expensive and require more maintenance than a conventional return idler.
Crowned Pulleys – The raised portion of the pulley (the crown) touches the belt first and the outer sections of the belt on both sides produce a force driving it toward the centre.
Dynamic Belt-Tracking Systems – These use the force of the mistracking belt on an arm that moves an idler, creating a steering action that directs the belt back into the centre.
In-Line Sensing Roll Trainers – These have vertical guide rolls that are mounted on both sides of the belt, in line with the roller, with the centreline running through the idler’s pivot point. Movement of the belt against either guide roll causes the roll to move in the direction of the misalignment, pivoting the entire idler.
Leading Sensing-Roll Trainers
– Employing either a pivoting carrying roll or troughing set, short arms on both sides of the frame are positioned in advance of the pivoting roller and end in guide rolls located 25 to 75 mm from the belt edge.
Martin
Torsion-Spring Trainers – These improve upon the leading sensing-roll trainer design by removing one sensing roll and incorporating a spring into the pivot, which keeps the one remaining sensing roll in constant contact with the belt edge.
Multi-Pivot Belt Trainers – These use longer arms than other designs, positioning the guide rolls further from the pivot roller, as well as closer to the belt edge. The closer proximity allows guide rolls to sense very slight
misalignments and make immediate corrections. Rather than waiting for a powerful mistracking force, the longer arms require considerably less force to move the pivot roller. The result is better correction with no pinch points and less wear on conveyor and tracking equipment, for a longer and more efficient service life.
Total conveyor analysis
“Installing trackers is the economical solution, but operators should do a full analysis and consider also addressing other causal issues,” Mueller adds. “By focusing solely on belt alignment, plant personnel may miss other opportunities to increase production and relieve some of the burden on their system.”
Off-centred loading is a major cause of mistracking. To remedy these issues, some conveyor accessory manufacturers offer well-engineered modern equipment such as loadcentering transfer chutes, highimpact cradles, adjustable slider cradles, an assortment of cleaner blades created for specific applications and redesigned chute box technology. Keeping the belt centred and moving quickly is the key to high production, a low cost of operation and a safer workplace. “Misalignment causes downtime and costs money,” Mueller concludes. “But nothing causes more downtime and expense than a destructive belt fire or other catastrophe as a result of inattention to mistracking problems.” a
AfriSam
AfriSam is a leading construction materials group in southern Africa. Since establishing its first cement plant in 1934, the company has grown into a formidable construction materials group with operations in South Africa, Lesotho and Eswatini.
www.afrisam.co.za
Babcock
Through several business units, Babcock offers a range of products and services, including construction and mining equipment, engineering solutions for steam generation and power plants, crane hire and gear rental, industrial generators, welding equipment and DAF truck sales and service.
www.babcock.co.za
With more than 16 years of experience in Proximity Detection Systems solutions, Booyco Electronics has supplied over 6 500 sets of mining vehicle equipment installations across southern Africa, as well as more than 55 000 pedestrian RFID installations.
www.booyco-electronics.co.za
Bunting
Bunting’s range of magnetic separators and metal detectors for quarries and mines ensures the protection of crushers, screens and conveyors. Overband magnets, suspension magnets and pulley magnets automatically remove tramp ferrous metal from conveyed quarried rock. www.bunting-redditch.com
IPR
IPR is recognised across the SADC region as the pump, heavy duty slurry handling and dredging specialist operating in underground and surface mining, quarrying, construction, wastewater, petrochemical and oil and gas sectors. www.pumprental.co.za
LOADTECH Load cells Onboard Weighing are specialists in onboard weighing providing complete solutions onboard your heavy goods vehicle, primarily in the application of load cell and transducer systems for payload protection and accuracy in the commercial vehicle sector. www.loadtech.co.za
Pilot Crushtec International
Pilot Crushtec International (Pty) Ltd is South Africa’s leading supplier of mobile and semi-mobile crushing, screening, recycling, sand washing, stockpiling, compacting and material handling solutions. www.pilotcrushtec.com
Sandvik
As a world-leading mining equipment manufacturer, Sandvik Mining and Rock Solutions is committed to improving your productivity and profitability. Our products and services provide you maximum value in terms of performance, quality, safety, flexibility and total economy. www.rocktechnology.sandvik/en/
Astec
Astec Industries has been a global leader in providing innovative Rock to Road™ solutions since 1972, specialising in equipment for asphalt road building and aggregate processing. www.astecindustries.com
John Deere
John Deere offers a comprehensive range of construction equipment, including ADT’s, excavators, loaders, dozers, graders, skid steers and TLB’s, designed to enhance productivity, efficiency, and performance on job sites of all sizes. www.deere.africa/en/construction
Lintec & Linhoff
Lintec & Linnhoff is a global manufacturer and distributor of leading-edge solutions for the asphalt and concrete industries under the Lintec and Linnhoff brand names. Its products include asphalt mixing plants, concrete batching plants, pavement related technologies, and specialist concrete cooling solutions.
www.lintec-linnhoff.com
Schauenburg Systems is a South African company that specialises in providing technology solutions for safety and productivity in mining and industrial markets. It positions itself as an active partner for digital transformation to meet the needs of the “Connected Worker.” The company has a strong focus on innovation and has a brand promise of “Innovation that Saves”. www.schauenburg.co.za
Weir Minerals
Weir Minerals Africa offers a wide range of equipment solutions including pumps, hydrocyclones, valves, dewatering equipment, wear-resistant linings, rubber products, screens and crushers – backed throughout the product lifecycle by high levels of aftermarket support.
www.global.weir
SANY
Sany Southern Africa is a subsidiary of Sany Group, a leading manufacturer of construction, mining and port machinery with over 20 R&D centres and manufacturing bases all over the world. www.sanysouthafrica.com
Our cutting-edge Lintec CDP12001M mobile continuous asphalt mixing plant has been engineered for superior performance. The CDP asphalt mixing plant delivers topquality asphalt quickly and directly at your job site. Say goodbye to transportation delays and hello to seamless, on-the- go operations. Elevate your projects with our innovative solutions and experience true mobility redefined. — Your road to success starts here. CDP12001M, Gabon
www.lintec-linnhoff.com info@lintec-linnhoff.com