

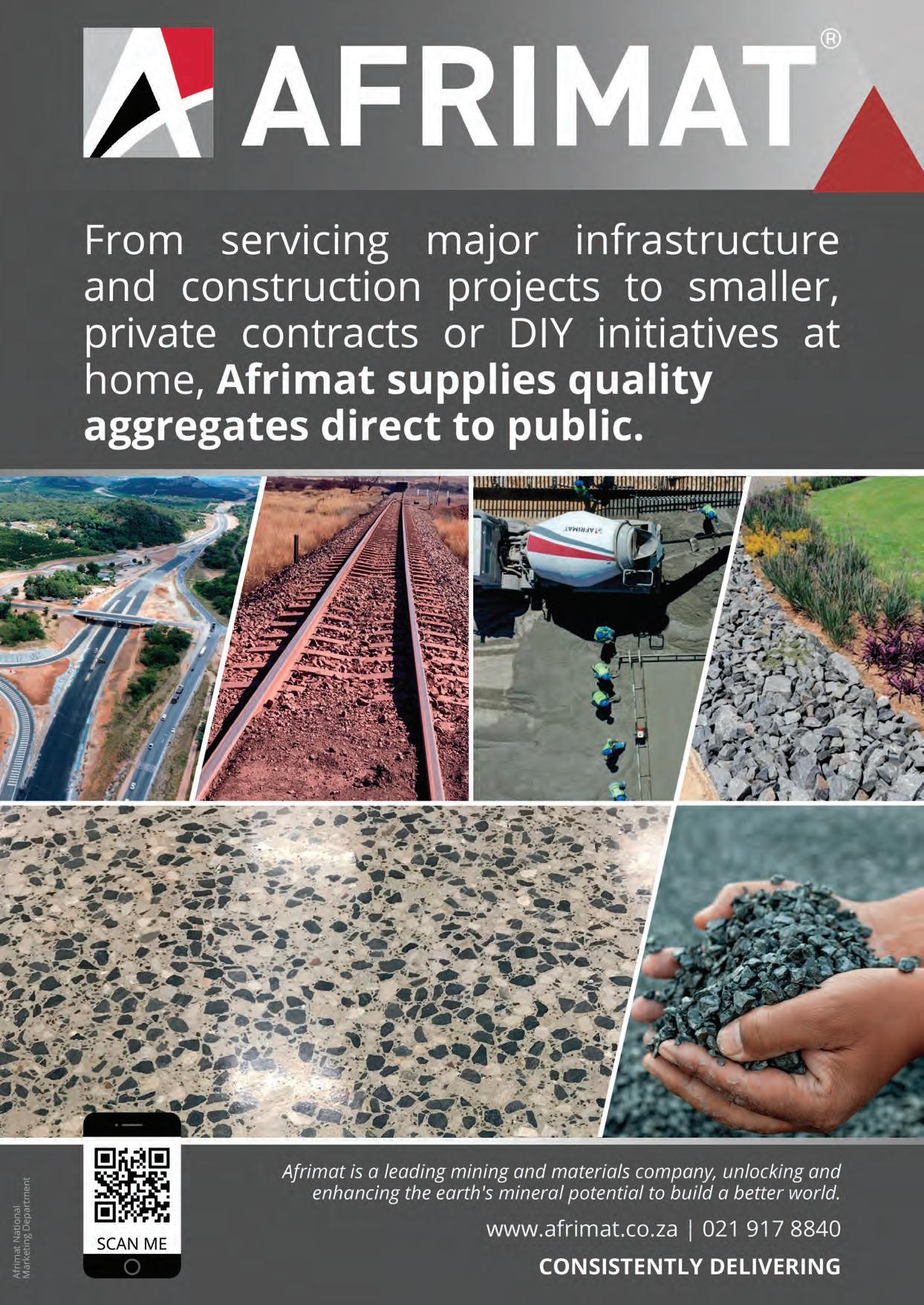
Te current business climate in the aggregates industry is characterised by price volatility, shrinking margins and increasing operational costs. This is exacerbated by a steady decline in the growth of aggregates demand due to the lack of meaningful construction projects.
To survive and operate profitably during such a low growth cycle, quarry owners need to capitalise on the opportunity to improve their productivity and focus on one of the key factors they can control –operational efficiency.
Increasing productivity is one of the key drivers to counter diminishing profit margins as it reduces operating costs effectively. However, the emphasis should not only be on increasing output from the same input, but also on increasing the output while at the same time decreasing the input, thus ultimately adding optimum value to current resources. Research shows that an increase in production will ultimately decrease the operation’s unit cost, especially fixed costs.
One parameter that has a significant effect on unit costs at quarries is the cost of drilling and blasting. Blasting is one of the most important operations and has substantial technical and economic effects on any mining project. The prime aim of blasting is rock fragmentation which is necessary for subsequent processes such as such as load and haul, crushing and screening – in order to achieve higher efficiency. Therefore, good blast design and execution are essential for successful quarry operations. Improper or poor practices in blasting can have a severely negative impact on the economics of an operation.
Load and haul together probably constitute the biggest cost driver for any quarry. Yet, if properly implemented, a load and haul optimisation programme can identify significant opportunities for operational improvement. The cost percentage of this process in the whole production equation is estimated to be
between 25 and 30% based on the whole operation cost, including site personnel and vehicle costs.
So, how can quarry owners reduce their operation’s unit cost related to load and haul? A reduction in the unit cost of loading and hauling can been achieved, on the one hand, by applying new and innovative mining equipment and methods, and on the other hand, by optimising the use of existing equipment. To run a successful load and haul fleet optimisation programme, it is important to ensure that the machinery is correctly matched to the site and application, as well as to fine tune the timing of cycles compared with the number of trucks.
While wet processing increases the value of aggregates, it is also a waterintensive process. Considerable water is lost to evaporation and incorporation into the product. Employing water efficiency practices reduces water loss and saves money. Recycling aggregate wash water can save large quantities of water. Most aggregate producers still use conventional settling ponds or tanks, but these have proved to be enemies of efficiency.
New technology, such as the CDE Combo, an all-in-one wet processing and water recycling plant, offers a practical solution to these concerns. All six processing stages of the CDE Combo plant have been designed with low energy consumption in mind, while operators also benefit from economical water consumption, using an incorporated water management unit that recycles up to 90% of used water directly into the system.
A key talking point here is that primitive and unplanned work, not using technology in a rational way and ignoring research and development findings can all negatively affect producers’ operational efficiency. It is also important to note that operating efficiency will not be achieved by focusing on a single operational process, but paying attention to the production value chain as a whole. a
Publishing Editor: Munesu Shoko
Sub Editor: Glynnis Koch
Admin: Linda T. Chisi
Design: Kudzo Mzire Maputire
Web Manager: Thina Bhebhe
Quarrying Africa is the information hub for the sub-Saharan African quarrying sector. It is a valued reference tool positioned as a must-read for the broader spectrum of the aggregates value chain, from quarry operators and aggregate retailers, to concrete and cement producers, mining contractors, aggregate haulage companies and the supply chain at large.
Quarrying Africa, published by DueNorth Media Africa, makes constant effort to ensure that content is accurate before publication. The views expressed in the articles reflect the source(s) opinions and are not necessarily the views of the publisher and editor.
The opinions, beliefs and viewpoints expressed by the various thought leaders and contributors do not necessarily reflect the opinions, beliefs and viewpoints of the Quarrying Africa team.
Quarrying Africa prides itself on the educational content published via www.quarryingafrica.com and in Quarrying Africa magazine in print. We believe knowledge is power, which is why we strive to cover topics that affect the quarrying value chain at large.
Email: munesu@quarryingafrica.com Cell: +27 (0)73 052 4335
For people wanting to build their own homes over time, AfriSam has opened the door to more concrete possibilities. The company collaborated with its advertising and brand agency, Promise Group and leading architecture firm, BlackStudio, to produce its ‘Plan (a)’ campaign, an invaluable modular house plan.
To ensure a wide reach, this has been published as a double page spread in community papers and is also available to download online at no cost to the consumer. The idea leverages AfriSam’s vision to build a positive Africna future, empowering and inspiring homemakers to plan ahead when constructing their ‘dream house’.
AfriSam’s ‘Plan (a)’ campaign helps people to build their own homes from an architect-approved plan. The modular design allows for the home to be expanded as needs change and financial resources allow. As part of its ongoing branding efforts, AfriSam has for many years provided practical guidance for customers on how best to use its cement and other construction materials. This has included Top Tips on working with cement and concrete, as well as Handy Guides on various aspects of building projects.
In the latest campaign, a carefully designed fit-for-purpose and architectapproved plan for a modular home is being publicised in the media. The social significance of improved home design
The next mounting of Hillhead, the quarrying, construction and recycling exhibition, will take place from 25-27 June 2024 at Hillhead Quarry, Buxton, England.
Hillhead returned with a bang earlier this year as The QMJ Group celebrated the show’s 40th anniversary over three gloriously sunny days in June. Exhibitors and visitors took the opportunity to reconnect with their industry peers, marvel at the plethora of live machinery action taking place, discover the latest
and quality is hard to over-estimate, according to architect Moremi Mowela, co-founder and architect at black-owned architectural practice BlackStudio – one of the collaboration partners in this initiative. He points out that many township areas are considered as transitory spaces by young people and are still ‘dormitory towns’ serving the large cities.
“This leads to many people leaving townships as soon as they have the means, creating a drain on skills and capital,” says Mowela. “This process can be reversed if those residential spaces can become aspirational, thereby playing a transformational role in shaping behaviour.”
He argues that building a professionally designed home – by using AfriSam’s flexible house plan – can be a crucial step in building attractive spaces. When people aspire to live and invest in these areas for the long term, he says, then thriving communities can be fostered. a
product launches, and explore the latest technology and innovations driving digitalisation and decarbonisation across the sector.
With 18 500 visitors in attendance and more than 600 of the world’s leading equipment manufacturers, suppliers and service providers taking part, this year’s Hillhead exhibition was a record breaker, cementing its status as the world’s biggest working quarry event for the mineral products, construction and recycling sectors. a
Surface mining association, ASPASA, has appointed new leadership. Following Nico Pienaar’s retirement earlier this year, Letisha van den Berg has taken the reins as the new director of the association, effective January 2023.
“It is with great pleasure that, after a long and proper search for the ideal person, we announce a new director was selected by the ASPASA MANCOM. We wish to congratulate Letisha van den Berg who was successful in her application for this position. Letisha has many years of experience in the industry. She is passionate about the quarrying industry, and we are confident that she will lead the association forward.”
In addition, the association has announced the election of Collin Ramukhubathi, executive director at Afrimat, as the new chairperson, and Drift Supersand’s Trevor McAdam as the new vice chairperson. Ramukhubathi takes over from Gert Coffee, who has served on the ASPASA MANCOM for over 20 years. a
With the growing popularity and versatility of fibres in concrete, CHRYSO works with local fibre specialist Oxyfibre to offer customers a professional technical design service. This relates to custom applications of CHRYSO Macro polypropylene fibres, which are considered as structural elements in construction.
Izak Louw, operations manager at Oxyfibre, explains that CHRYSO Macro polypropylene fibres compete with the conventional steel mesh as a reinforcement for concrete. As such, these macrofibres are considered as structural elements, and must pass stringent tests to prove the strength and integrity of their physical properties.
“This creates the basis for us to offer a specialised engineering design service for the application of our macrofibres, not only for ground supported slabs but also for precast concrete,” says Louw. “We use the customer’s data on loadings, ground conditions and the kind of activities that will be carried out on the concrete surface – such as rolling loads and racking loads.”
CHRYSO Southern Africa has been the official distributor for Oxyfibre since 2016, with the two firms having built a strong working relationship for many years before that. Oxyfibre makes available both microfibres and macrofibres supplied by Adfil Construction Fibres, whom Oxyfibre represents in sub-Saharan Africa. ADFIL Construction Fibres bases its
Custodianship of operations that produce sand and aggregates is critical to the development of South Africa’s construction industry.
Small-scale surface mines lacking some of the resources needed to ensure day-to-day compliance with legislation and other statutory conditions are turning towards industry association, ASPASA, to fill the voids.
While ASPASA is strongly focused on the mining industry, its association with other professional bodies, such as The Concrete Institute (TCI) and others, can add as much value and is the reason why the association is a long-time associate member of the institute.
The association’s work, in collaboration with all levels of government, private construction sector and labour over the past 30 years, has earned the respect of the industry as well as recognition from all quarters including its overseas peers. It has also led to a great deal of interest from other surface miners, which led to the change of its constitution to admit mines other than just the sand and aggregate quarries it was founded to represent.
ASPASA’s membership includes operations in the salt, dimension stone, diamond, clay and other sectors. The association also provides services aligned with affiliated onsite plants such as readymix and processing plants. When necessary, the association protects and lobbies on behalf of the surface mining industry and provides appropriate training and literature to its members through its various committees.
Some of the key services that contribute to the ever-growing popularity of the association and that assist its members in providing the highest levels of service to the concrete industry include audits, workshops, technical committees and GAIN membership.
Membership of ASPASA requires operations to undergo
manufacturing facilities – as well as its research and development laboratory –in Belgium.
“Most of our customised fibre designs relate to civil engineering applications, such as roads and industrial slabs,” he says. “However, we also provide the design service in smaller contracts for driveways, residential homes and requirements on farms.”
Working closely with CHRYSO, the Oxyfibre engineering team considers the customer’s needs and provides feedback on aspects such as fibre dosage, the size of saw-cuts on a slab and the optimal thickness of the concrete. A good example of the fibre design offering was for a building project where the contractor was looking for an innovative solution. a
two compulsory audits in health and safety, as well as the environment, to ensure compliance with legislation and statutory requirements. These measure the mine’s compliance and provide professional feedback to improve its performance where required.
Workshops provide an important interface between the association and its members in order to update and upskill the industry in order to respond to changing market requirements. The workshops also serve to provide explanations of best practices that improve members’ business practices and profitability.
Chaired and attended by specialists in various fields, technical committees investigate, debate and interact with stakeholders and the industry to gain knowledge and disseminate information about various topics. a
www.quarryingafrica.com
Afrimat has today released interim results for the six months ended 31 August 2022, delivering satisfactory results strongly supported by its diversification strategy.
Andries van Heerden, CEO of Afrimat, says that strategic initiatives contributed positively to performance in the first six months of the financial year. These included the successful commissioning of the Jenkins iron ore mine, the turnaround of the Nkomati anthracite mine, and the group’s continuous improvement of existing operations.
“Diversification, cost reduction and efficiency improvements remain the cornerstone of our strategy and we used these to counter economic impacts, which are beyond our control,” says Van Heerden.
He adds that the results have been negatively affected by the downturn in iron ore prices, the economic slowdown and the rise in input costs such as diesel, explosives and electricity, although this was mostly offset by the results of strategic initiatives.
Group revenue increased by 7,2% from R2,4-billion to R2,6-billion. Operating profit decreased by 12,1% from R582,8million to R512,2-million, resulting in the operating profit margin settling at 19,7%. Headline earnings per share of 252,2 cents was delivered.
The balance sheet remains strong, with a net cash balance of R772,7-million. Net cash from operating activities of R784,1-million was generated, as well as R680-million from a successful equity
raise during the period.
“At present, the group is considered debt free as the cash balance exceeds the borrowings, with sufficient capital to execute on the Group’s strategic plans to support Afrimat’s future growth,” says van Heerden, adding that new business development remains a key component of the group’s growth strategy.
Afrimat consists of four operating units – Construction Materials, Industrial Minerals and Bulk Commodities, as well as the group’s latest addition, Future Materials and Metals, comprising phosphate, vermiculite and rare earth elements. This last unit has expanded Afrimat’s product offering and national footprint.
The Bulk Commodities segment, consisting of the Demaneng and Jenkins iron ore mines, and the Nkomati anthracite mine, contributed 76,8% to the group’s operating profit.
“This excellent performance was largely due to increased volumes from Jenkins coming into production, the successful turnaround of Nkomati from start-up losses which turned to profitability from August 2021, and from cost-saving initiatives,” says van Heerden, adding that the Jenkins mine, which is now fully operational, together with the Demaneng mine, had produced an increase of 21,9% in iron ore sales volume during the current period, compared to the previous period.
Industrial Minerals businesses across all regions delivered satisfactory results,
SANRAL’s significant upgrade of the R63 route from Fort Beaufort to Alice is progressing well. The contractor, Rumdel Construction Cape, is completing the revamp of Fort Beaufort’s main road, while the rural section is well advanced. AfriSam is providing its High Strength Cement for structures such as bridges and culverts.
Rumdel Construction Cape project manager Alistair De Lacy says the project is also having plenty of positive spin-off for local subcontractors,
suppliers and workers.
“To build their capacity while ensuring compliance with the required standards, Rumdel trains, mentors and supervises targeted enterprises at all stages of the project,” says De Lacy. “The contract has provided work for about 800 people, of which about 570 are local.”
Construction materials leader AfriSam is supplying the cement for all structural elements of the contract – for the most part with its High Strength 52.5N Cement. This
however, the impact of the economic slowdown was felt within this segment, resulting in a decrease in operating profit from R49,6-million to R36,8million.
The Construction Materials segment experienced the brunt of the slowdown in economic activity, while the Western Cape businesses were the most impacted due to an overall reduction in construction across the province. The KwaZulu-Natal businesses showed good improvement when compared to the previous period, primarily as a result of an uptick in construction.
The operating profit of this segment remains relatively flat from the comparative period with a slight decrease from R77,8-million to R73,1million.a
is ensuring high quality results for the project’s three new bridges, two bridge widenings, 12 cast-in-situ box culverts and V-drains.
About 4 100 m³ of durability concrete has been poured for the monolithic decks of three bridges, 2 600 m³ for the culverts and 7 000 m³ for side drains and channels. AfriSam is also supplying its specialist road stabilising Roadstab Cement, of which 1 300 tonnes are going into road bypasses and 4 500 tonnes for the main works. a
www.quarryingafrica.com
The decision to invest in two McCloskey scalping screens is paying dividends for South African mining contractor, Franco Le Roux Mining. In an environment where margins continue to shrink, owner Francois Slabbert is particularly impressed by the lower cost per tonne of material produced, as well as the aftersales support from Kemach Equipment, writes Munesu Shoko .
The operating cost structures for mining contractors have increased significantly over the past few years, putting pressure on margins. To run profitable operations in the face of such a tough operating environment, contractors need always to crunch the numbers. One area where this is particularly important is the cost per tonne of material produced.
With that in mind, Franco Le Roux
Mining does not leave anything to chance when it comes to the procurement of its equipment. As Slabbert puts it, “the rand per tonne of material produced is the difference between success and stagnation” in the contract mining environment. This approach was key to the company’s decision to purchase two McCloskey scalpers, which, according to Slabbert, have performed beyond expectations.
Before committing to the deal, the
16 l
The R155 consumes about 16 litres of diesel per hour, which is key to reducing the client’s rand-per-tonne of material produced
10 000 t
The two machines punched well above their capacity by producing 10 000 t of -30 mm product in a 24-hour cycle
The machines are costeffective to run. To provide context, our R155 consumes about 16 l of diesel per hour, which is key to reducing our rand per tonne of material produced.
We offer both options – apron and belt feeder – to suit different customer needs. We understand that customers require different feeder arrangements for different applications. We have taken a deliberate approach to offer unparalleled flexibility in many areas of our offering.
The decision to invest in two McCloskey scalping screens – an R155 and an R230 – is paying dividends for Franco Le Roux Mining
In a gold dump reprocessing application, the machines once proved their capabilities by processing about 20 000 t of head feed in a 24-hour cycle
The R230's heavy duty high energy screen box at 6,1 m x 1,83 m provides high screening capacity and can be raised at the lower end for easy bottom deck access
The R155 high energy screenbox, with a screening area of 4 880 mm x 1 525 mm across, said to be the largest in its class, has impressed operators across applications
Watch: Franco Le Roux Mining recently purchased two McCloskey scalping screens from Kemach Equipment. Owner Francois Slabbert explains the reasoning behind the procurement decision.
company carried out its due diligence. “We were in the market for a scalping screen, and when Kemach Equipment approached us, we spoke to a number of other contractors already running McCloskey scalpers. The feedback from all of them was positive, and we went ahead and purchased our first R230 scalping screen, and never looked back. A few months later, we decided to purchase a second machine, the smaller R230, and we are happy with our decision.”
For Slabbert, it is important for companies to be willing to test new products in the market. While the McCloskey brand is not necessarily new in South Africa, Slabbert believes it is still finding its rightful place in the market. “I understand the need for brand loyalty, but I believe that in the quest for greater operational efficiency, companies should be willing to test new offerings. We were bold enough to try out the McCloskey scalpers and our willingness to try new products has paid off,” he says.
feed the machines between 18 000 and 20 000 t of material. The machines punched well above their capacity and delivered the required material within the prescribed period. We were highly impressed by this feat,” he says.
Apart from production, Slabbert is impressed by the cost-efficiency of the McCloskey screens. “The machines are cost-effective to run. To provide context, the R155 consumes about 16 l of diesel per hour, which is key to reducing our rand per tonne of material produced,” he says.
In addition, Slabbert is happy with the cost of maintenance.
Initially, Franco Le Roux Mining deployed both its R155 and R230 in a gold dump reprocessing application in the Krugersdorp area of the North West Province. However, the R230 has since been moved to process coal in Mpumalanga.
From the onset, the screens ticked all the right boxes, from productivity to cost-efficiency. In the gold dump processing application, the machines once proved their capabilities by processing about 20 000 t of head feed in a 24-hour cycle.
“On the rock dump that we are processing now, we had to deliver 10 000 t of -30 mm product in a 24-hour cycle, which means we had to head
“Both the cost of the parts and Kemach Equipment’s services are cost-effective, which is good news for a low-margin operating environment such as contracting crushing and screening,” adds Slabbert. Machine reliability, says Slabbert, is a key consideration in the contracting fraternity. Given the importance of uptime in the mining environment, the implications of equipment failure have become ever more critical. An unplanned failure can result in significantly higher repair costs than a planned maintenance or repair. Of even more importance is the loss of production associated with unplanned equipment failures. One method to mitigate the impact of failures is to ensure the reliability of the equipment.
“One thing about the McCloskey products is that they don’t easily break; they are durable and reliable machines. In more than a year, we have never had any serious issues with the machines. This is complemented by Kemach Equipment’s
hands-on service support,” says Slabbert.
“As an example, we rented out our R230 in a coal application and in the past six months I have only visited the site once. Every time Kemach Equipment goes to service the machine, they give us detailed reports, which gives us peace of mind knowing that the machines are in a good running state. Owing to this high level of reliability and performance, we have earned a second job from the same client, and we will definitely consider adding another McCloskey machine,” he adds.
The larger McCloskey R230 weighs in at 34 000 kg and is capable of operating as a stand-alone screen, producing finished product or serving as a primary scalping component for large portable crushing units.
“The screen’s heavy-duty high energy screen box at 6,1 m x 1,83 m provides a high screening capacity and can be raised at the lower end for easy bottom deck access,” explains Bradley Karolus, sales specialist at Kemach Equipment.
A significantly longer and wider direct feed Hardox-lined hopper provides a large loading area, while a wide-feed opening allows for the free flow of material and high-volume capacity. The R230’s optimal chute design is said to minimise potential material spillage and blockages.
The R155 scalping screen has proven to be extremely efficient across a wide range of applications. With a screening area of 4 880 mm x 1 525 mm across the high energy screenbox, the R155 is said to be the largest in its class, and has impressed operators across applications, working with difficult materials such as heavy rock, sticky clay and fines, as well as boulder clay.
According to Karolus, McCloskey has one of the
most versatile ranges of scalping screens on the market. For example, the feeding arrangement of the machines can swing between an apron and a belt feeder, whereas most other OEM offerings provide only one of the two.
“We offer both options – apron and belt feeder – to suit different customer needs. We understand that customers require different feeder arrangements for different applications. We have taken a deliberate approach to offer unparalleled flexibility in many areas of our offering,” says Karolus.
However, Karolus believes that the belt feeder is proving to be the most popular feeding option, mainly because it is cheaper to maintain. To provide context, it costs around R400 000 to replace an apron feeder, whereas a belt feeder comes at about R60 000.
“We initially ran our R230 with an apron feeder, but we have since changed to a belt feeder on the R155, which is working well for us in our application,” says Slabbert. “When the material is dry, we produce anything between 250 and 350 tph. In future, we will stick to the belt feeder, which we have found to be a smoother operator.”
Another feature of note is that the top deck of the scalper is interchangeable; it can be configured with grizzly, mesh or punch plate. McCloskey is said to be one of just a few manufacturers in the market that offers such a versatile scalper.
“The ability to change the machine’s conveyors to either side of the machine is another key feature that speaks to the machine’s versatility. Being able to configure the fines and mid-size conveyors in either direction means that one can change their discharge points with ease. This ensures that the wheel loader, which burns the most fuel on site, is not riding too far to feed the machine,” concludes Karolus. a
Key to our success is the investment in our support structures. We carry between R230-million and R270-million of stock at any given time. About 50-75% of this stock are wear and spare parts. We have close to 30 000 line items in our system, which calls for good inventory management skills.
Over the past 32 years, Pilot Crushtec has played a leading role in shaping the local crushing and screening market to be what it is today – challenging norms and pushing boundaries along the way
A big trend in the market has been the move towards mobile equipment
The 2005 introduction of the Pilot Modular solution popularised modular plants, not only in South Africa but across the world
The company is encouraged by the current uptick of sales across several markets in southern Africa
Through its own locally made and imported solutions, Pilot Crushtec has over the past 32 years established itself as a leading name in the crushing and screening space. Over the years, the company has played a leading role in shaping the local crushing and screening market to be what it is today – challenging norms and pushing boundaries along the way.
“My father and I started the business in 1990 after he sold his engineering jobbing shop. Having fabricated vertical shaft impactors (VSIs) for the now defunct Austrian company, we had gained experience with crushers. At the time, Nelson Mandela had just been released from prison, so it was the beginning of transformation in South Africa. The mood in the country was positive,” recalls Scherf. “However, there was uncertainty on the business front, and many discouraged us from
The
and
Pilot Crushtec International is this year celebrating the 32nd anniversary of its founding in 1990. In a one-on-one with Quarrying Africa, CEO Sandro Scherf reflects on the humble beginnings, milestones, challenges and successes of the past 32 years. By Munesu Shoko.
investing in a new venture at the time. We took the plunge and went on to establish Pilot Crushtec, and never looked back.”
As the company had gained experience in VSIs and seeing a huge opportunity for this type of crusher, Pilot Crushtec launched its own VSI, named Pilot Tornado. Given the antiquated design of all the competitors, the company developed a modular rotor for its newly designed crushers, and at the time this was ground-breaking. The traditional method was to cover rotors with hard-faced welding. The rotor the company designed was bolted together with no need for welding. It also had bolt-on, replaceable wear parts and worked with rock-on-rock pockets.
The rotors performed extremely well in the company’s Tornado crushers. Pilot Crushtec then developed an adaptor to retrofit them into competitor crushers. One of the first Pilot
Modular VSI rotors was supplied to Readymix Material (now AfriSam’s Rooikraal Quarry), where it was installed in a Barmac crusher. The transformation in maintenance and wear costs was a thousand-fold. In an application where the old hard-face welded rotor needed two hours of service every day, the Pilot Crushtec rotor went for eight months without any need for maintenance or change of wear parts. Word quickly spread in the market, putting Pilot Crushtec on the map.
Building on the success of several Tornado installations in South Africa, and testimony to its engineering prowess, by 1993, the company had begun exporting machines to Austria, Croatia followed by South Korea. Eventually, these machines would be exported to more than 20 countries, including Australia, New Zealand, the UK, Germany, Italy, Bulgaria and Serbia, among others.
“Exporting to South Korea was a big achievement, not only for us as a company, but South Africa at large. Given South Korea’s engineering aptitude, it was a ground-breaking moment to have a South African designed and manufactured product achieving success in such a market,” says Scherf.
For its export triumph, Pilot Crushtec clinched successive Merit Awards for Export Achievements at the 1993 and 1994 South African State President Awards. Further success came in 2006 when its fully mobile, track-mounted TwisterTrac won the SA Pro Awards Competition by Product Award, before being granted the Design Excellence Award by the Design Institute of South Africa in 2008.
“We have conceived, designed and manufactured many pioneering products including the introduction of the first fully mobile tracked VSI crusher, the TwisterTrac, and the first ever fully mobile, tracked double roll crusher in
the world, the DoppiaTrac DR400,” says Scherf. That Pilot Crushtec also popularised modular plant solutions is no overstatement. Since the introduction of the Pilot Modular solution in 2005, the company has had great success with it, prompting the popularity of modular plant solutions globally. “We understood that for us to be successful, we needed to offer a solution rather than a product. We created ready-to-run modules, including all stages of crushing and screening, available ex-stock, and this changed market dynamics, not only in South Africa, but globally,” says Scherf.
After enjoying good success with its Pilot VSI range, the next big move for the company was to acquire the distribution rights of the Finlay brand in 1993. “We initially stocked three machines, which was a gamble at the time because the entire market was only about five units per year, including secondhand machines. Within six months we had sold the three machines and by the end of the year we had put 12 units into the market. That changed the dynamics of the whole market; every supplier in this market started stocking machines, which was a big plus for the industry,” he says.
During its 17-year distributorship spell, Pilot Crushtec sold in excess of 2 000 Finlay machines. The company recorded non-stop growth of 40% per annum on average, right through to 2008, when the global financial crisis hit.
Following the end of its partnership with Finlay, Pilot Crushtec took on the distributorship of Sandvik mobiles in 2013, a relationship that lasted for three-and-a-half years.
A major highlight in the company’s history was the signing of the distributorship agreement with Metso (now Metso Outotec) on 2 April 2016. In September 2017, Pilot Crushtec was awarded the Best New Services Distributor at Metso’s global conference in
Finland. The award was for the “exceptional levels of customer service and support”.
In 2019, the company walked away with the Best Sales Growth Award at Metso’s second global aggregates Distributor Days. Testimony to the company’s capabilities, Pilot Crushtec had become one of Metso’s largest distributors globally in just three years.
“Key to our success is the investment in our support structures. We carry between R230million and R270-million of stock at any given time. About 50-75% of this is stock are wear and spare parts. We have close to 30 000 line items in our system, which calls for good inventory management skills,” he says.
Scherf is of the view that, unlike other sectors of the capital equipment market, the crushing and screening market does not change quickly. “A jaw crusher has not changed much in the past 120 years,” he says. “However, the engineering has been optimised, with weight reduction being one of the notable gains.”
The big change is most apparent in process optimisation, with automation of plants constituting some of the key developments in recent years. Reliability of monitoring technology and the streamlining of the information delivered by monitoring systems are among the big advancements in recent years. Modern systems can provide information that is relevant and that adds value, thus eliminating information overload.
“Another big trend in the market has been the move towards mobile equipment. We have witnessed the dramatic growth of the mobile crushing screening industry in the past 30 years,” says Scherf. The mobile revolution has been accelerated by the growth of the contracting fraternity. Some 30 years ago, recalls Scherf, there were only two big contractors in South Africa. The contracting market has grown significantly and constitutes almost 50% of Pilot Crushtec’s business to date.
Thirty-two years is a long time, especially for a business that operates in cyclical industries such as mining and quarrying. “We have weathered many storms along the way,” says Scherf. “The first big challenge for us was the global financial crisis of 2008. We were, however, cushioned by the massive infrastructure spend in preparation for the World Cup. The weakening rand also put us under pressure, but the market was buoyant.”
The biggest crisis for Pilot Crushtec was the 2014 mining collapse, which was exacerbated by the ailing South African economy. “Getting through 2014, 2015 and 2016 was a real
challenge. We accumulated losses of almost R60-million during this period, but with grit and determination, a lot of hard work and some sacrifices, we got through it,” he says.
“The market bounced back in 2017, and just when it was moving positively and we were seeing solid growth and positive equity, the madness of the Covid reaction hit us in February 2020. The lockdowns, the resultant supply chain challenges and the rising logistics costs as well as the unprecedented input cost increases presented major challenges. Thankfully, it seems, there is some semblance of sanity returning and things are slowly ’normalising’.”
“We had to think differently about business and operating models, risk management frameworks and crisis management to allow for agility at a time when there was a high level of uncertainty. We had to move a number of levers to remain viable,” he says.
In addition, Scherf notes the brain drain is a major challenge for the industry and the country at large. The company has lost five highly experienced technical people in the past three years. As a committed training organisation and to help close the skills gap, Pilot Crushtec has been driving a major technical training programme in association with many of the technical universities. The company recently received an award from the Mangosuthu University of Technology for its role in providing practical experience to students. “We have had 66 students coming though our ranks, 10 of whom have been offered employment,” says Scherf.
While the reaction to Covid has eased, Scherf says the market is nowhere near the pre-Covid levels. The local mobile crushing and screening market has halved in size in the past decade; however Pilot Crushtec has managed to maintain strong market share, especially on the crushing product line.
There is talk of a mining boom, but Scherf believes it hasn’t translated into new capital sales. “We are expecting a good year in 2022, however, the global political environment, especially the Russia/Ukraine war and the talk of a recession in the UK and other European economies, is putting a damper on the potential recovery of the market,” he says.
On the South African front, the political crisis in the country is a serious malaise, harmful to economic performance. However, Scherf is encouraged by the recovery in southern Africa. “In recent years, sales into southern Africa have not been buoyant, but we have seen a strong uptick in enquiries and sales across several markets in the region over the past few weeks, which we hope will offset the downward market trend in South Africa,” concludes Scherf. a
A new ball mill project at Afrimat’s Glen Douglas operation allows the company to beneficiate its sought-after dolomitic product, thus expanding its product offering and diversifying into new market segments. Munesu Shoko was recently on site and filed this report.
For years, diversification has been the operating mantra at Afrimat and remains central to the company’s continued success. Behind the successful diversification is a solid business development team with a sharp eye for new opportunities.
Joanne Giles, New Business Development at Afrimat, explains that the company’s business development team not only focuses on acquisitions, but also on opportunities to expand the product offering from existing operations and to diversify into new markets. Central to this approach is the quest to maximise best value from the resource and create new revenue streams.
A case in point is the new beneficiation
project at the Gauteng-based Glen Douglas operation. Here, Afrimat has invested in a new ball mill plant to allow it to initially expand its agricultural lime (aglime) production and eventually spread its wings more widely into the chemical, asphalt and tile markets. When we visited the site, the first phase of the project, which is focused on the production of aglime, was being commissioned.
“The key driver for this project is to increase Glen Douglas’ product offering and reduce our dependence on the traditional construction materials and metallurgical markets which form the base of our revenue from this operation,” explains Giles.
An opportunity to serve two key markets was identified. Firstly, it was
The first phase of the project has been completed and will allow Afrimat to produce 50 tonnes per hour (tph) of aglime
-1,75 mm
Given the fine nature of aglime, which is about -1,75 mm in size, a ball mill was required to mill the product to the required size
Mill project layout.
the opportunity to increase aglime production to better serve the high demand. Secondly, an opportunity to produce milled dolomitic product for use by a potential customer in the chemical industry was investigated.
The first phase of the project has been completed and will allow Afrimat to produce 50 tonnes per hour (tph) of aglime. While this product is not new to the operation, project engineer Stephan de Villiers explains that the new plant offers the capability of producing aglime in larger quantities.
Traditionally, production of aglime at Glen Douglas entailed the reclamation of fines from the sludge ponds. Given that all products from the main plant at this operation are washed, a huge concentration of fines therefore exists in the ponds. The Afrimat team would reclaim the fine material from the ponds, leave it to dry and then screen it to the required material size.
Using this method proved to be a challenge, mainly due to the time required to dry the product. Given the high demand for aglime, a business case study justified investment in a ball mill plant. A used ball mill was sourced, as well as some second-hand equipment which was refurbished in-house. Some of the required machinery was also reclaimed from some of Afrimat’s old plants.
“Because of the fine nature of aglime, which is
Behind Afrimat’s successful diversification strategy is a solid business development team with a sharp eye for new opportunities
Afrimat has invested in a new ball mill plant to allow it to initially expand its agricultural lime production and eventually spread its wings more widely into the chemical, asphalt and tile markets
The first phase of the project has been completed and will allow Afrimat to produce 50 tonnes per hour (tph) of aglime
The second phase of the project will focus on the production of a milled dolomitic product for use by a potential customer in the chemical industry
about -1,75 mm in size, a ball mill was required to mill the product to the required size. It is difficult to produce fine material of this nature using conventional crushing methods. The ball mill gives us the ability to grind more finely,” explains De Villiers.
When we visited the site, the first phase of the plant was in commissioning phase, with the plant already producing 25 tph. Material from
Because of the fine nature of aglime, a ball mill was required to mill the product to the required size.
The first phase of the project has been completed and will allow Afrimat to produce 50 tonnes per hour of aglime.
the feed bin is fed into the plant via an incline conveyor. The material then goes over a Mac’s Engineering-built high frequency screen.
“Here, we first screen out material that is already in spec (-1,75 mm), which is directly conveyed to the final stockpile. The coarse material (anything over -1,75 mm) goes through a scraper chain conveyor before it is fed into the ball mill, where it is milled to the required fine size,” explains De Villiers.
Material from the ball mill is then picked up by an elevator, which feeds it onto the high frequency screen again to ensure that there are no larger particles reporting to the final stockpile. From here, material is channelled to the final stockpile using two chain conveyors. Given the extra fine nature of the product, an extraction system is installed to reduce dust emission.
The second phase of the project will focus on the production of a milled dolomitic product for use by a potential customer in the chemical industry. Additional market avenues suitable for this
product were identified in asphalt production and the tile adhesive market. To produce this material to the required micron sizes (less than 750 microns), another ball mill will be installed.
“We have already sourced a second ball mill for the second phase of this beneficiation project,” explains De Villiers. “For this phase, we will also need some specialised air classification equipment to classify the material instead of using the screening process,” explains De Villiers.
At the time of writing, De Villiers expected the second phase to commence once the first phase had been ramped up to nameplate capacity. “We could, however, make the micron size material using the first phase setup, but it would require some extra equipment,” he says.
In conclusion, Giles says having a ball mill on site has opened the door for additional products not previously considered. “This concept can be extended to other products and operations within the Afrimat stable. It is the first phase of the Afrimat beneficiation hub which is envisaged to provide continued growth and expansion beyond traditional dolomitic products,” concludes Giles. a
Having embarked on its sustainability journey some three decades ago, AfriSam has over the years introduced a number of initiatives to reduce its carbon footprint. Chief among them is the use of extenders to reduce clinker content in its cement. Quarrying Africa recently visited the company’s Slagment plant to learn more about the role of extenders in reducing AfriSam’s clinker factor. By Munesu Shoko.
In 2016, South African cement plants produced on average 671 kg of CO2 per tonne (CO2/t) of cement
According to the Association of Cementitious Material Producers, clinker substitution rose from 12% in 1990 to 23% in 2000 and a substantial 41% in 2009
The cement industry is deemed one of the leading climate sinners globally. Available figures show that the industry is responsible for about 7% of the global carbon (CO2) emissions.
In the South African context, the six major cement producers –with a total installed annual capacity of 20-million tonnes (Mt), in a market currently averaging annual cement demand of 13 Mt – are responsible for about 1,7% of the country’s total CO2 emissions.
At a recent media tour of AfriSam’s Slagment operation in Vanderbijlpark, Hannes Meyer, Executive: Cementitious at AfriSam, noted that data from Trade & Industrial Policy Strategies (TIPS), 2020, showed that in 2016, South African cement plants produced on average 671 kg of CO2 per tonne (CO2/t) of cement.
This is above the global average of 642 kg CO2/t cement. However, this ranks lower than the Middle East (712 kg), Russia (707 kg) and North America (745 kg). South Africa’s emissions are, however, higher than those of its other BRICS trading partners, with India producing on average 582 kg CO2/t and Brazil 604 kg CO2/t cement.
“In absolute terms, South Africa lies very much in the middle of the country pack and is neither a weak nor a strong performer. It is also interesting to note the emission trend over time. In 1999, South African plants produced on average 783 kg CO2/t cement. This went down to 706 kg in 2006 and reached an industry low of 665 kg in 2015,” explains Meyer.
Since 2015, emissions per tonne of cement produced have, however,
The cement industry is responsible for about 7% of the global CO2 emissions
In South Africa, the six major cement producers are responsible for about 1,7% of the country’s total CO2 emissions
Owing to a number of initiatives, AfriSam has reduced its carbon emissions by 33% since 1990 – making it a leader in decarbonisation efforts in the South African cement sector
The use of extenders such as ground granulated blast-furnace slag in AfriSam’s cement has resulted in a substantial reduction of its clinker factor without compromising the quality of products
It is interesting to note the emission trend over time. In 1999, South African plants produced on average 783 kg CO2/t cement. This went down to 706 kg in 2006 and reached an industry low of 665 kg in 2015.
increased marginally from 665 kg to 671 kg in 2016. This is in line with a noticeable global trend of an uptick in emissions in most reporting regions.
Another observable trend in South Africa and other countries, says Meyer, is the slow pace of emissions reduction in the past five years. “This seems to indicate that most low-hanging fruits have been picked and that more difficult and expensive mitigation options remain untapped,” he says.
Despite the slow pace of emissions reduction in the cement sector, South African cement firms have really made some significant strides in improving electricity and thermal energy efficiency, thus reducing their carbon footprint. Since 2008, there has been a year-on-year reduction in emissions per tonne of cement, largely driven by the increased focus on clinker substitution.
embarked on our sustainability journey long before it was ‘fashionable’,” says Meyer.
The company has achieved many firsts in the process. Most notably, in 2009, AfriSam was the first cement maker to introduce a CO2 rating system, indicating the carbon footprint of each of its cement products relative to Ordinary Portland Cement (OPC). The company has also become the world’s first construction materials supplier to Carbon Footprint all its production operations, including cement, aggregates and readymix concrete operations.
AfriSam was also the first cement company to publish an environmental policy, having done so in 1994. In 2012, the company became the first cement company to pledge support to Eskom’s R49-million campaign to demonstrate its commitment to the global agenda for energy efficiency.
According to the Association of Cementitious Material Producers (ACMP), clinker substitution rose from 12% in 1990 to 23% in 2000 and a substantial 41% in 2009. However, the industry is pressing for a 60% rise by 2030.
One thing has become increasingly clear in recent years; if the world is to mitigate the existential crisis in which it finds itself, action must be taken now. It is therefore encouraging to see the efforts being made by industry players such as AfriSam, which implemented its sustainability strategy back in the 1990s. “We
Owing to a number of initiatives, AfriSam has reduced its carbon emissions by 33% since 1990 – making it a leader in decarbonisation efforts in the South African cement sector.
To achieve this feat, the company has during this period taken a number of approaches to reduce its carbon footprint. These range from process enhancements to ongoing energyefficiency initiatives at its cement plants, explains Marieta Buckle, process technology manager at AfriSam.
However, clinker reduction has been a major focus in the quest to significantly reduce the company’s carbon footprint. Clinker production,
adds Buckle, is in fact the biggest CO2 contributor in the cement-making process.
To provide context, traditional Portland cement is produced by heating limestone and other minerals at high temperatures of up to 1 450 °C, a process that is carbon-intensive due to the chemical reactions that release large amounts of CO2.
The use of extenders has therefore been central to reducing the clinker factor in the company’s cement products. In fact, Project Green Cement was launched in 2000 to increase the use of extenders to promote more sustainable products. Since then, the company has been a leader in the development of composite (extended) cements.
“The use of extenders in our cement has resulted in a substantial reduction of our clinker factor without compromising the quality of our products,” notes Buckle. For example, AfriSam’s Eco Building Cement, launched in May 2010, has the lowest carbon footprint in the industry at 401 g/kg, nearly half the global average of 890 g/kg at the time. As a result of these efforts, Buckle says the company has reduced its clinker factor by almost 20% since 1990.
Composite cements, explains Claudene Moorgas, GM cementitious central at AfriSam, contain not only clinker, but other cementitious materials such as pulverised fly ash (PFA) from coal-fired power stations and ground granulated blast-furnace slag (GGBS) from steel-making plants.
“Re-using waste products from other industries reduces the amount of limestone that we have to mine and clinker that we have to produce, thus reducing carbon emissions from those processes as well as minimising waste to landfill. We are therefore constantly searching for new extenders and additives to reduce our carbon footprint
further and our impact on the environment at large. The end result is to have less clinker produced per tonne of each final product, thus resulting in less CO2 generated from our operations,” says Moorgas.
AfriSam’s Slagment operation plays a crucial role in the production of composite cements. Established in 1955, the Slagment facility was previously owned by three companies, before AfriSam acquired 100% shares in 2004. AfriSam sources its granulated blast furnace slag from steel producer, ArcelorMittal South Africa, which is strategically located just across the road from the Slagment operation.
Blast furnace slag, a by-product of iron and steel production, has been used in the manufacture of cements at an industrial scale since the second half of the 19th century. Back then, says Moorgas, the practice was to intergrind the blast furnace slag with clinker.
The Slagment company has, however, pioneered the use of separately ground slag in an array of construction applications. It can be used in structures meant for water retention, such as in retaining walls in rivers and ports, as well as in tunnels, for improvement in impermeability. The material also finds good use in mass concreting works such as dams and foundations which require low heat of hydration.
“The use of this product has grown steadily in South Africa and is widely used in countries worldwide,” says Moorgas.
Benefits of this material abound, Moorgas continues. “Blast furnace slag has good cementitious properties, thus providing enhanced strength and durability. A vital aspect of our use of extenders has been our ability to
activate these materials for greater reactivity. Through evolving our chemical and mechanical activation methods, we achieve a more reactive product – allowing us to progressively replace more and more clinker while retaining high cementitious quality and strength performance.”
Moorgas says many flagship structures have been built using slag extended cements, with several success stories recorded locally. At the Ben Schoeman Highway, slagment blend (50:50) was specified for the construction of the 21 km overlay between Pretoria and Johannesburg.
Some 30 000 t of slagment went into this multi-million rand project which was one of the largest and most complex undertaken in South Africa. A continuous reinforced concrete (CRC) overlay was applied, eliminating the need to rehabilitate subsurface layers – a first in the country. Slagment’s superior flexural strength contributed to an extremely durable surface.
Elsewhere, the Matimba Power Station in Limpopo is the first of its kind to be created on an exceptionally large scale in South Africa. In particular, the air-cooled stream-condensing system is the largest of its type in the world. The project called for 72 identical columns, spaced over half a kilometre length. The slender columns required an excellent concrete mix design for efficient sliding. A mix of slagment was used for strength and durability.
At the Richards Bay coast, the dolosse used to
construct breakwaters were made with a 50:50 mix of cement and slagment. The structures are continually subjected to wetting and drying cycles in a marine chloride environment – one of the most aggressive to concrete.
Yet observations at East London and at Port Elizabeth, where the first dolosse were placed in 1967, show that they are still serviceable. In fact, they were in better condition than units made without slagment and placed at later dates, clearly illustrating that slagment minimises marine attack and helps structures stand the test of time.
Another success story is the chimney stack at Sasol 3 in Secunda, the tallest structure built on piled foundations in the southern hemisphere at that time. The 300-m reinforced concrete enclosed four internal flues and was slid at a rate of up to 3 m per shift. With a 30 MPa concrete specified, the use of the 60% slagment in the mix produced the required workability and cohesion to complete this intricate structure successfully.
The Gariep dam on the Orange River constitutes another success story. The giant dam, the largest single construction work ever undertaken in South Africa, covers 374 km² and has a gross storage capacity of 5 958,3 million m³.
“To create this great lake, 1,92 million m³ of concrete was poured; slagment was used in the concrete mix to control temperature and make dense impervious concrete. Completed in 1972, the concrete today looks as good as when it was placed, indicating yet again that slagment is the proven cement extender of choice,” concludes Moorgas. a
The company was the world’s first construction materials supplier to carbon footprint all its production operations, including cement, aggregate and readymix.
Of greatest concern in the management of waste in the quarrying industry is the stone itself, specifically in the form of overburden, screening residual fines and stone fragment.
Solid waste management is a fundamental component of the quarrying value chain. For both economic and environmental benefits, it is recommended that each quarry establishes a waste management plan that includes continuous minimisation and proper management, particularly reuse, recycling and lawful disposal, of all site waste streams. This is the central message from ASPASA, the surface mining industry association’s recently published best practice guideline for waste management. By Munesu Shoko.
It is estimated that 175-million tonnes (t) of quarrying waste are produced each year, and although a portion of this waste may be utilised on site, such as for excavation pit refill or berm construction, it is often difficult to find meaningful use for all waste stone and fines produce. Coupling this with the industry’s other waste streams, such as wastewater sludge and general site trash, it is essential that all operations in the natural stone
industry develop and abide by a waste management plan.
Through implementation of a proactive waste management strategy, unnecessary fines, occupational exposures and environmental degradation may be avoided. Additionally, an opportunity exists for companies to distinguish themselves as socially responsible and environmentally considerate operations. Best Practice
Guideline: Solid Waste Management at
175-million t
It is estimated that 175-million tonnes of quarrying waste are produced each year
As the industry strives for zero harm, an effective waste management plan is key to forging a strong health and safety regime
Decreasing the amount of material lost during the quarrying and crushing processes increases efficiency and the quantity of profitable product.
The greatest waste concern in the quarrying industry is the stone itself, specifically in the forms of overburden, screening residual, wastewater sludge, baghouse fines and stone fragments
Waste from quarry operations can be unsafe and environmentally detrimental
Decreasing the amount of scrap piles, airborne particulates and general trash creates a healthier and safer environment for employees.
Comprehensive, proactive waste management practices will result in a reputation for social responsibility and greater community acceptance of the quarrying operation.
the Quarry & Fabrication Facility, published by ASPASA, suggests approaches for achieving such practices at a quarry site.
Of greatest concern in the management of waste in the quarrying industry is the stone
itself, specifically in the form of overburden, screening residual, wastewater sludge, baghouse fines and stone fragments. There are great differences in waste generation across the industry, due in part to the varying types of products manufactured.
Additional waste created by quarrying operations includes equipment, spent petroleum products, wastewater sludge and trash. Machinery and tools eventually warrant refurbishment or replacement, creating a potential stream of scrap metal and mechanical parts. Proper disposal of petroleum products is mandated by law.
If a wastewater treatment system is in place, as may be required by law, sludge must be utilised or disposed of properly. Further, miscellaneous trash produced by employees must also be consciously managed. Minimisation of each one of these waste streams is feasible by implementing the best practices recommended by the document and by continuously exploring new avenues of mitigation.
Impact of quarry waste Waste from quarry operations can be unsafe and environmentally detrimental. Scrap stone
can create dangerous working conditions as well as an undesirable visual impact if piles are stacked carelessly or not well organised. Runoff from the scrap mounds can cause erosion problems, and fines introduced into natural waterways can suffocate local ecosystems.
Dust from uncovered stockpiles or poorly functioning filtration equipment can cause respiratory, ocular, or dermal irritation for employees and may cause a visual or even respiratory burden on local communities. If the mined stone contains silica, employees could potentially be afflicted with silicosis, a lung disease causing breathing difficulties and sometimes death.
Establishment of a thorough waste management plan translates into a multitude of advantages for the quarry. As the industry strives for zero harm, an effective waste management plan is key to forging a strong health and safety regime.
“Decreasing the amount of scrap piles, airborne particulates and general trash creates a healthier and safer environment for employees. A healthy workforce provides lower health care costs for employers, thus ensuring a high attendance rate and effectively better productivity.”
Proper waste management is also key to reducing storage, transport and disposal costs. With less waste to store and transport, the costs of handling waste are significantly reduced. In addition, landfill fees are avoided, and diesel expenses related to transporting waste are reduced.
A good waste management plan also offers potential for revenue generation. Scrap stone, sludge and other waste products and waste by-products can be sold on an array of markets, from agriculture to construction, thus creating a secondary revenue stream.
Decreasing the amount of material lost during the quarrying and crushing processes increases efficiency and the quantity of profitable product. In effect, the company sees a greater return for every tonne of product sold.
In addition, comprehensive, proactive waste management practices will result in a reputation for social responsibility and greater community acceptance of the quarrying operation.
It is recommended that each facility develops a waste management plan built on three hierarchical principles:
Produce less waste: improve production methods to mitigate all types of waste.
Exploit the value of waste: implement strategies to reuse, recycle, compost, sell, create new products, or otherwise prevent waste from being landfilled or incinerated.
Manage waste properly: follow regulations for lawful disposal of wastes that cannot be given a second life.
A number of practices should be implemented in order to reduce the waste generated during quarrying and processing. By implementing such strategies, additional product is created, operational efficiency is enhanced and occupational hazards are mitigated or even eliminated. Each of these results is a form of cost savings. a
Re-crushing waste material may create a secondary revenue stream for quarries and readymix concrete plants.
As major advances in technology continue to reshape the world, proximity detection systems (PDS) and collision prevention systems (CPS) are ushering in a new era in safety management at mines and quarries, thus reinforcing the industry’s quest for zero harm. However, Anton Lourens, CEO of Booyco Electronics, warns that technology is no silver bullet and people remain central to the industry’s zero-harm drive. By Munesu Shoko.
The days of trying to convince mining and quarrying executives of the imperative of a comprehensive technological roadmap may well and truly be over. There doesn’t appear to be a mine or quarry owner who doesn’t appreciate the immense value, efficiencies and
competitiveness that can be unlocked by fully harnessing the power of technology. More importantly, technology has proven to be a key enabler in safety management.
To achieve zero harm, mines and quarries need a comprehensive, integrated safety portfolio to mitigate numerous risks. The hazards faced by miners every day are
Level 9
Continuous development of PDS technology has allowed the industry to migrate from the warning and advisory systems (Level 7 and 8) to an engineering control intervention (Level 9)
2006
Since its inception in 2006, Booyco Electronics has made significant investments in research and development (R&D) which has truly spurred innovation, invention and progress
Over the past few years, PDS technology has been the focal point for the industry
The attention being paid to PDS today goes even beyond the direct avoidance of accidents. For example, the technology is increasingly part of the development of ‘digital twin’ simulations, where mines are analysing big data to understand their operations better
Booyco went into surface operations in 2010, with its offering initially based on radio frequency, which was the best technology available at the time
wide-ranging, spanning from poor visibility and blind spots, to distraction and slope instability, to name just a few. To mitigate these risks, a comprehensive safety response combining technology and a commitment to zero-harm culture is imperative.
“Technology plays a vital role in mitigating significant risk and achieving better safety
To achieve zero harm, mines and quarries need a comprehensive, integrated safety portfolio to mitigate numerous risks
To mitigate risks, a comprehensive safety response combining technology and a commitment to zero-harm culture is imperative
By adding different technologies, the value proposition to the customer is expanding. The PDS is therefore moving from being a legislative purchase to a valuable tool that offers immense value to the industry.
Lourens, CEO of Booyco ElectronicsWatch: Anton Lourens, MD of Booyco Electronics, discusses the role of technology in achieving zero harm.
Mines and quarries must observe strict health and safety regulations to mitigate the risk of collisions on site.
The PDS has proven to be a relevant and important tool in assisting the industry’s quest to improve safety.
outcomes at mines and quarries. In an environment where human behavioural factors still largely contribute to the occurrence of mine accidents and injuries, technology gives workers the additional tools to work safely,” explains Lourens.
While the value of technology to safe mining cannot be reiterated enough, Lourens stresses that it should be “specific and suitable”. Technology, he says, is no silver bullet; people remain central to successful safety management initiatives on site.
“Technology makes it possible, but people make it happen. It is therefore important for companies to find the right technology which considers organisational culture and the way people operate,” he says. “It has been proven time and again that the PDS, for example, deals with a complex problem statement and that is why I believe that suppliers need to understand the end user before they provide a solution. Are the people on site ready for the complex technology or do they just want a basic system able to be developed as specifically needed? These are some of the important questions that we need to address before rolling out a possible technological solution,” he adds.
One of the technologies at the centre of a new safety regime in the mining industry is around
PDS. Over the past two years, says Lourens, PDS technology has been the focal point for the industry. He believes that there is a growing urgency in the application of PDS solutions in South African mines as a vital element of the zero-harm drive.
The attention being paid to PDS today goes even beyond the direct avoidance of accidents. For example, the technology is increasingly part of the development of ‘digital twin’ simulations, where mines are analysing big data to understand their operations better. This, according to Lourens, has constituted a big developmental step over the past two to three years. Owing to the great amount of operational information available, it is now possible to see how machines interact and operate, which allows for proper traffic flow analysis and implementation of suitable traffic management plans.
“The PDS has proven to be a relevant and important tool in assisting the industry’s quest to improve safety. Over and above its primary functions, the technology can now be used as an evaluation tool to identify hotspots, review heatmaps, analyse traffic flow and inform traffic management plans. It is a supporting tool that can offer a great deal of value to the industry,” he says.
Since its inception in 2006, Booyco Electronics has made significant investments in research
and development (R&D) which has truly spurred innovation, invention and progress. Informed by changing industry requirements, the company has evolved its offering from the first-generation collision warning system to the new generation Booyco CXS solution.
Technology has advanced from simply being a PDS solution, to incorporating several other functions such as tracking and data management. In addition to the safety capabilities, Booyco PDS and CPS solutions are now able to provide customers with the bigger picture, including parameters such as machine standing time, idling times and cycles times, among others.
“We started in underground operations back in 2006, when we established ourselves as a market leader. We went into surface operations in 2010, with our offering initially based on radio frequency (RF), which was the best technology available at the time,” explains Lourens.
“As the world started deploying more and more satellite networks, GPS information became more available and reliable. The PDS has therefore leveraged the availability and reliability of GPS information in order to develop its systems further. Consequently, we have moved from a very basic non-intelligent warning system to a point where we now use GPS information to run algorithms to predict potential incidents and specific scenarios,” he adds.
Continuous development of this technology has therefore allowed the industry to migrate from the warning and advisory systems (Level 7 and 8) to an engineering control intervention (Level 9), with Booyco Electronics among the pacesetters in the development of Level 9 technology.
While Level 7 alerts a mobile machine operator and a pedestrian when they are close to each other, Level 8 goes beyond this to an advisory function, showing the direction in which the
vehicle or pedestrians are moving and advising the operator to slow down or stop.
Level 9 – currently the highest level of intervention – takes it a step further by introducing an engineering control measure. This automatically instructs the machine – or the vehicle’s onboard control system – to slow down, or to perform a safe or emergency stop. However, testing of this technology is ongoing, with industry stakeholders such as the Minerals Council South Africa, PDS manufacturers and original equipment manufacturers (OEMs), working together to find common ground for its effective rollout in surface operations.
The old saying “if you can measure it, you can manage it” rings true of the development that has gone into PDS technology, says Lourens. Leveraging the high level of detail this technology can now produce, the industry presently has the opportunity and capability to address more difficult safety scenarios a lot better than in the past.
Continuous improvement is the name of the game. Looking ahead, Lourens believes that PDS technology will continue to develop, leveraging advancements in areas such as the Internet of Things (IoT) and other technologies. He is also of the view that no single technology will offer a total solution; integration of multiple technologies such as GPS, RF, cameras and radars, amongst others, will be key to providing the industry with the best possible tools to realise zero-harm targets.
“By adding different technologies, the value proposition to the customer is expanding. The PDS is therefore moving from being a legislative purchase to a valuable tool that offers immense value to the industry,” concludes Lourens. a
Epiroc used bauma 2022 to showcase its SmartROC T35 E, its first ever tophammer battery-electric drill rig. The rig is an important step in the shift towards zero emission drilling in surface mines and quarries worldwide. Munesu Shoko attended the event and filed this report.
As the shift towards electromobility in the mining and quarrying sectors gathers pace, several original equipment manufacturers used bauma 2022 to showcase the advances they have made to electrify their offerings. For Epiroc, the show presented a perfect platform to showcase its SmartROC T35 E, its first ever tophammer battery-electric drill rig.
The design of SmartROC T35 E is
based on the well-proven SmartROC T35 surface drill rig. In combination with the experience gained from the development of Epiroc underground battery rigs, this new rig is designed to enhance the environmental standards of quarries and larger construction sites. Besides the low emissions, the rig provides a range of smart features, and delivers high safety, reliability and performance – in a quiet working environment.
“We are proud to present this rig at bauma, as it is a product which
In 2021, Epiroc's goals were validated by the Science Backed Targets initiative as being in line with keeping global warming at a maximum 1,5°C, consistent with the latest climate science and the goal of the Paris Climate Agreement
At bauma 2022, Epiroc showcased its SmartROC T35 E, its first ever tophammer battery-electric drill rig
The design of SmartROC T35 E is based on the well-proven SmartROC T35 surface drill rig
The SmartROC T35 E rig is equipped with both a battery and an electric cable, which improves flexibility considerably
The surface drill rig is fitted with the same type of well-proven batteries and subcomponents as in the Epiroc underground battery solutions
constitutes an important step in our shift to low-carbon operations within quarries and large construction applications. The fact that we are removing emissions from the drilling process is an important step towards a better environment. This accomplishment shows that Epiroc has an important role to play in making our industry more sustainable,” says Hakan Aytekin, vice president marketing, Epiroc Surface division.
The SmartROC T35 E rig is equipped with both a battery and an electric cable, which improves flexibility considerably.
The machines play a vital role in Epiroc’s ambitious sustainability goals for 2030, which include halving CO2 emissions in operations and from sold products
year 2030. With the SmartROC T35 E
“Epiroc has bold sustainability targets in place for the
we are taking a large step towards reaching our promise to offer a full range of emissions-free products for quarries and large construction applications.”Helena Hedblom, Epiroc’s president & CEO
The SmartROC T35 E rig is equipped with both a battery and an electric cable, which improves flexibility considerably.
Operators can choose to drill with the most suitable alternative for the location and occasion. It also allows for quick and smooth transportation in and between sites.
The surface drill rig is fitted with the same type of well-proven batteries and subcomponents as in the Epiroc underground battery solutions. This streamlines spare parts handling and service for customers with several different operations.
“SmartROC T35 E is a result of a successful collaboration between Epiroc and our customers. They have provided us with valuable input, making sure we will deliver a rig with optimised performance and flexibility,” says Ulf Gyllander, global product manager tophammer drill rigs, Epiroc Surface division.
Earlier this year, Epiroc announced that it had agreed with Swedish construction company, Skanska, to field test the SmartROC T35 E. Skanska is currently testing the rig at a quarry near Stockholm. Manufactured in Örebro, Sweden, the machine arrived at the quarry in September.
“A milestone has been reached and a new opportunity has come to reduce our climate impact,” says Johan Eliasson, project manager, Skanska Industrial Solutions AB. “I am very happy about the long collaboration between Epiroc and Skanska, and it is exciting to be able to do this project together. Both companies
have set bold environmental goals – this project really takes a great step towards Skanska´s goal of being completely climate neutral by 2045, which is an important part of our promise to build a better society.”
Epiroc’s battery-electric solutions are attracting strong interest from the market. Customer benefits include emissions-free operations, lower noise pollution and vibrations, as well as higher productivity.
The machines play a vital role in Epiroc’s ambitious sustainability goals for 2030, which include halving CO2 emissions in operations and from sold products. In 2021, the goals were validated by the Science Backed Targets initiative as being in line with keeping global warming at a maximum 1,5°C, consistent with the latest climate science and the goal of the Paris Climate Agreement.
Epiroc will offer its complete fleet of underground mining equipment as emissionfree versions by 2025, and its full fleet for surface operations as emission-free versions by 2030.
“Epiroc has bold sustainability targets in place for the year 2030,” says Helena Hedblom, Epiroc’s President & CEO. “With the SmartROC T35 E we are taking a large step towards reaching our promise to offer a full range of emissions-free products for quarries and large construction applications.” a
Volvo CE has started testing the world’s first fuel cell articulated hauler prototype, the Volvo HX04.
As the sustainability drive gathers pace, several OEMs are sharpening their focus on making hydrogen commercially viable. Will hydrogen help end the industry’s dependence on diesel and aid the transition to a net-zero world? By Munesu Shoko.
Despite all the enthusiasm around electromobility, hydrogen is projected to play a key role in the future of energy and experts believe that its development will happen faster than many might expect.
Prof Marcus Geimer, head of the Mobile Machinery section of the Karlsruhe Institute of Technology, is of the view that if emissions from construction and mining equipment fleets as a whole are to be further reduced, other technologies, apart from batteries, must also be advanced.
Hydrogen is projected to play a key role in the future of energy and experts believe that its development will happen faster than many might expect
Several OEMs have introduced prototypes powered by hydrogen
Volvo Construction Equipment has started testing of what is said to be the world’s first fuel cell articulated hauler prototype, the Volvo HX04
At Bauma 2022, the Liebherr components division introduced two prototypes of its hydrogen engine technology, the H964 and H966
Hyundai Construction Equipment used Bauma 2022 to showcase its 14-t hydrogen excavator developed for the first time in Korea in 2020
The fuelling process for hydrogen vehicles is fast – the Volvo HX04 is charged with 12 kg hydrogen in about 7,5 minutes, enabling it to operate for approximately four hours
Liebherr’s R 9XX H2 is the company’s first crawler excavator to be equipped with an integrated hydrogen combustion engine.
80%
From its initial dual-fuel technology projects, CMB.TECH has seen up to 80% reductions of carbon emissions
“In addition to other hybrid solutions, there is currently a great deal of research being done on hydrogen vehicles with fuel cells, for example. One of the problems to be solved is the tank space, since hydrogen requires a significantly larger volume than diesel for the same energy content. Furthermore, we should keep in mind the possible use of CO2-neutral biogenic fuels – especially for the very large machines and vehicles,” he says.
That hydrogen is today enjoying unprecedented momentum is no overstatement. Both mines and original equipment manufacturers are pressing ahead to make hydrogen an important part of a clean and secure energy future. For example, Anglo American made history last year with the introduction of its world’s largest hydrogenbattery hybrid mine haul truck which was deployed to work at its Mogalakwena mine in South Africa.
Several OEMs have also introduced prototypes powered by hydrogen, which is a key indicator that the industry is not far away from commercial rollout. In fact, the road to hydrogen was one of the central themes at the recently ended Bauma 2022.
Earlier this year, Volvo Construction Equipment (Volvo CE) announced that following the completion of a multi-stakeholder research project aimed at breaking new ground in hydrogen technology, the company had initiated the testing of what is said to be the world’s first fuel cell-articulated hauler prototype, the Volvo HX04.
The results of the project will provide important insights into the possibilities provided by hydrogen and fuel cells as Volvo CE continues research for its future product development programmes.
“While an early prototype, this innovation will give valuable insights into the opportunities of hydrogen in energy transformation alongside battery-electric solutions. We believe that by exploring multiple technologies and working in partnership we can create the best path forward to decarbonise the construction industry,” says Carolina Diez Ferrer, head of Advanced Engineering Programmes at Volvo CE.
The fuelling process for hydrogen vehicles is fast – the Volvo HX04 is charged with 12 kg hydrogen in about 7,5 minutes, enabling it to operate for approximately four hours. Fuel cells work by combining hydrogen with oxygen and the resulting chemical reaction produces electricity which powers the machine. In the process, fuel cells also produce heat that can be used for heating of the cab. Fuel cells only emit one thing – water vapour.
In principle, a fuel cell works much like a battery except that it generates its own electricity from the hydrogen onboard as needed rather than being charged from an external source. Vehicles with fuel cell electric powertrains have an uptime, range, and fuelling time similar to that of combustion enginepowered vehicles.
While battery-electric vehicles and biofuels are commercially available today – as more sustainable alternatives to diesel – commercialisation of hydrogen-powered machines is expected during the second half of this decade.
In yet another development signalling the strides being made in making hydrogen use a reality, Volvo Penta and CMB.TECH have announced a partnership agreement designed to accelerate the development of dual-fuel hydrogenpowered solutions.
The collaboration will include joint projects ranging from pilots to small scale industrialisation, providing increased access to this important technology for reducing greenhouse gas emissions.
CMB.TECH owns, operates and designs large marine and industrial applications powered by hydrogen and ammonia – fuels that it both
manufactures and supplies to its customers. Volvo Penta is a global manufacturer of engines and complete power systems for boats, vessels and industrial applications. The companies have worked together in pilot projects since 2017, successfully adapting Volvo Penta engines to run as a dual-fuel hydrogen and diesel solution via the conversion kit provided by CMB.TECH.
The collaboration will create synergies aimed at leveraging the competences and product offerings of both companies – establishing dual-fuel hydrogen technology as a low-carbon interim solution before suitable zero-emissions alternatives become viable. It is an important step in Volvo Penta’s and CMB.TECH’s joint ambition to help accelerate their customers’ transition to net-zero emissions.
The partnership will cover pilot projects and small-scale industrialisation of a hydrogen dual-fuel solution for selected customers.
“From the initial dual-fuel technology projects we have seen reductions of carbon emissions up to 80%,” says Roy Campe, chief technology
officer at CMB.TECH. “It is clear that the energy transition is a major challenge in many types of applications. With the dual-fuel technology we have been developing over the past few years, we can provide a cost-effective and robust solution for a variety of applications. We think there is huge potential in this solution for customers, both on land and at sea.”
The whole Volvo Group is working intensively to explore solutions to reduce – and ultimately eliminate – greenhouse gas emissions. Volvo Penta strives to team up with suppliers, partners, and customers to accelerate the journey into fossil-free fuels for both on land and at sea applications.
“The development in this area is moving fast and with this partnership we see a great opportunity to further explore and be part of increasing the use and availability of hydrogen solutions. I believe that this dual-fuel approach will appeal to many of our customers by its ease of installation, maintenance, and use. In addition, it will help accelerate our customers’ transition to more sustainable operations,” says Heléne Mellquist, president of Volvo Penta.
The dual-fuel solution’s main advantage is that it will reduce the emissions of greenhouse gases while at the same time provide a robust and reliable solution. And, if hydrogen is not available, the application continues to run on traditional fuel, safeguarding productivity.
“The simplicity of the dual fuel technology allows a quick introduction into many applications. The potential to decarbonise with green hydrogen is huge, but many applications require a fallback scenario of traditional fuel to maintain a viable business. With the dual fuel technology, your asset is future-proof, even without full coverage of a reliable hydrogen infrastructure today,” says Campe.
As part of its decarbonisation drive, Liebherr is one of the pacesetters in the drive towards hydrogen. At Bauma 2022, the Liebherr components division introduced two prototypes of its hydrogen engine technology, the H964 and H966. Each prototype employs different hydrogen injection technologies, a direct injection (DI) and a port fuel injection (PFI).
Initial efforts in the development of a hydrogen engine have considered PFI as a first suitable technology. The first machine running with a 100% hydrogen-fuelled internal combustion engine is the Liebherr R 9XX H2 crawler excavator.
In it, the zero-emission 6-cylinder engine H966 fulfils the specific requirements in terms of power and dynamics. On display at Bauma, the 50-t Liebherr R 9XX H2 hydrogen excavator received the 2022 Bauma Innovation Award in the climate protection category.
Encouraged by the results achieved with the PFI technology, Liebherr further pursues its research and development activities in the field of DI. The 4-cylinder H964 engine prototype is equipped with said technology. In this case, hydrogen is injected directly into the combustion chamber, whereas with the PFI solution it is blown into the air intake port. The DI offers increased potential in terms of combustion efficiency and power density, which makes hydrogen engines an attractive alternative to diesel engines when it comes to more demanding applications.
Liebherr expects to kick off series production of hydrogen engines by 2025. In the meantime, the company sets forth its research activities in fuel injection to further optimise combustion and to ensure maximum power density.
In addition to 100% hydrogenfuelled engines, several research endeavours in the area of alternative fuels are currently in progress. One example is a dual-fuel engine that can run on hydrogen ignited by HVO injection or fully on HVO. This technology will allow for more flexibility in vehicle operation with different configurations.
Hyundai Construction Equipment also used Bauma 2022 to showcase its 14-t hydrogen excavator developed for the first time in Korea in 2020.
Unlike a diesel-powered wheeled excavator, the hydrogen-powered machine has a fuel cell mounted in the rear of the upper-structure. The fuel cell relies on a chemical reaction between the stored hydrogen and oxygen that is present in the air. The fuel cell stack generates electrical energy from this reaction, with an inverter converting this energy into usable electrical power.
This is used to drive the hydraulic pump, to power the machine in the normal way. Hyundai says the only emission from the fuel cell stack is water, a combination of the hydrogen and oxygen. The company says that when the hydrogen is produced using renewable energy, this creates an incredibly low carbon powertrain. For the excavator, the hydrogen is stored on the right-hand side of the machine, opposite the operator’s cab, in high-pressure tanks. a
A recent global safety report for mining indicates a gradual but steady improvement in mine safety, with a total recordable injury (TRI) frequency rate at a low 2,90 –down from 5,07 just a decade ago.
The Safety Performance Report by the International Council on Mining and Metals (ICMM) benchmarked the progress of its members during 2021. The ICMM noted that the industry has focused on “operational, cultural and leadership transformation” in reducing fatalities in recent years.
Blasting solutions specialist BME has concurred that a growing safety culture is a major factor behind positive safety trends in mining, as well as uncompromising compliance with strict safety protocols.
According to Ramesh Dhoorgapersadh, GM for Safety, Health, Environment, Risk and Quality (SHERQ) at the JSE-listed Omnia Group company, safety must be ingrained into every activity, in line with recognised standards and procedures.
“The blasting philosophy of BME is expressed through our innovative products and leading initiation technologies,” says Dhoorgapersadh. “This also means aligning our policies with customer’s own safety protocols and broader regulatory requirements.”
This includes careful adherence to the regulated distances between communities and blasting sites. He highlighted that internationally accepted standards are stringently applied to ensure the safety of communities adjacent to mining areas. These protocols address any possible hazards from blasting such as ground vibration, airborne dust or flyrock.
Tinus Brits, BME’s global product manager – AXXIS, explains that electronic detonation systems play an important role in achieving safe blasting. They allow detonators to be accurately initiated within milliseconds
of each other, staggering the energy release rather than having five or six holes detonating at the same time. Reducing the charge mass per delay thereby reduces the resulting vibration.
“We design our electronic detonators in such a way that key blast impacts are both measurable and predictable,” says Brits. “With our integrated blast planning software, mines can simulate each blast before it is implemented – so that they can predict aspects like ground vibration to ensure it will be within the required parameters.”
He emphasises that in this regard mines apply world-class standards, such as the United States Bureau of Mining (USBM) blast-induced ground vibration criteria. These include the requirement that any blasting in the vicinity of communities, structures, houses, roads or other receptors requires a minimum safety radius. Where BME conducts blasts on behalf of customers, therefore, it applies a blasting radius of one kilometre away from any persons or communities, and 500 m from any material that might be negatively affected.
“For every blast, seismographs are then used to measure the resulting ground vibration and air blast,” he says. “This confirms that the blast did indeed achieve the simulated design parameters, to fall within the regulated limits.”
These vibration reports can confirm that a mine’s blast was fully compliant with relevant standards or regulations, should there be a need for a mine inspector to investigate any blast-related incident.
While a range of safety protocols may be in place to comply with regulations,
BME boasts a recorded case rate of just 0,15% – a world-class rating that places it among South Africa’s best safety performers, and a leader in its industry segment
BME conducts blasts on behalf of customers, therefore, it applies a blasting radius of one kilometre away from any persons or communities, and 500 m from any material that might be negatively affected
Dhoorgapersadh notes that human behaviour is still the cause of incidents that could be avoided. This requires that mines and their suppliers continue to foster a culture of safety that brings behaviour into line with systems.
“BME’s Safety for Life brand, for instance, priorities the safety of employees, communities and the environment,” he says. “By ingraining a safety culture, we can apply and embed our
safety learnings wherever we operate.”
As a result, BME can boast a recorded case rate (RCR) of just 0,15% – a world-class rating that places it among South Africa’s best safety performers, and a leader in its industry segment.
BME has also been recognised at the Chemical and Allied Industries Association (CAIA) Awards for its safety, health and environment (SHE) performance. a
The blasting philosophy of BME is expressed through our innovative products and leading initiation technologies. This also means aligning our policies with customer’s own safety protocols and broader regulatory requirements.Ramesh Dhoorgapersadh, BME GM for Safety, Health, Environment, Risk and Quality. Tinus Brits, BME’s Global Product Manager – AXXIS.
As market forces continue to dictate the innovation imperative in the mining industry, mining companies are increasingly looking to invest in digital technologies to enable them to make informed decisions. This was the overarching observation from Weir Minerals Africa’s interactions with customers at the recently ended Electra Mining Africa 2022.
“Several customers spoke about the need for real time management of important operational parameters at their operations. Mines are moving away from human assumptions to using actual data points for tracking key indicators that make equipment reliable,” says Tiisetso Masekwameng, General Manager – Comminution at Weir Minerals Africa.
To respond to this growing need for digital solutions, Weir Minerals Africa showcased its Synertrex intelligent platform which provides mines with insights into actual costs of running their plants, data to develop strategic improvements to mining operations and the opportunity to performance benchmark every part of their operations.
“Synertrex is a complete digital ecosystem that continually monitors equipment’s performance and integrates with customers’ distributed control systems. This means that advanced analytics are conveyed through a digital interface, making sure our customers have all the indicators delivered to their devices with accuracy and in real time, even if they aren’t at the mine,” explains Masekwameng.
As part of Synertrex condition monitoring, she adds, sensors are applied to processing equipment and the data they provide is captured and continuously analysed. Customers are therefore able to eliminate guesswork from their operations by having detailed real time insight into how their equipment is performing. Information is displayed on a simple, easy to understand dashboard which can be accessed via any device or integrated into existing operational systems. It will convey real time fact-based insights into machine performance and health, remaining useful life and other crucial operational indicators. a
The Smart Job Configurator in SPECTIVE CONNECT supports the operator in the selection of the correct machine settings.
The SPECTIVE CONNECT digital platform is now available for the MOBICAT MC 120(i) PRO mobile jaw crusher and the MOBICONE MCO 110(i) PRO cone crusher.
SPECTIVE CONNECT now has the “Smart Job Configurator” configuration tool, which helps in the selection of the correct machine settings. For this purpose, the operator simply enters the data of the planned application in the SPECTIVE CONNECT App. It calculates the optimum machine settings automatically, which the operator then transfers to the machine via the SPECTIVE touch panel.
The rapid entry of the machine settings can also be used by an accomplished operator as a quickstart menu independent of SPECTIVE CONNECT. Important settings can therefore be made conveniently via a guided menu.
The new configuration tool also supports the operator in the selection of the best possible crushing tools as well as the recognition of the tools and tracking of their service life. This significantly simplifies the typical workday.
All installed optional belt scales can now also be displayed in SPECTIVE CONNECT. A convenient overview of the current production output is therefore possible via the dashboard. The data is recorded in the reporting and allows conclusions to be drawn about the output and utilisation of the plant. a
Known for its customised heating, cooling and ventilation (HVAC) systems, Booyco Engineering has embraced technology to meet global standards. MD Brenton Spies explains that by leveraging powerful simulation software, the company is able to significantly shorten product prototype development time.
“In the past, the conventional practice in product development was to build a physical prototype and then put it through a series of tests,” says Spies. “Often, these tests would lead to the rebuilding of new prototypes – to progressively remove the weaknesses we discovered by testing.”
The company has invested over R10million in specialised Computational Fluid Dynamics (CFD) and Finite Element Analysis (FEA) software. These are used for modelling factors such as the strength of components, structureborne vibration, and airflow and heat distribution inside its HVACs and conditioned spaces.
“These resources allow us to run simulations and iron out most of the issues before we even build a
prototype,” he says. “The simulations cut down significantly on the time taken by the traditional ‘trial and error’ route in developing solutions for customers, allowing us to get product to the customer faster, saving both time and money.”
This capacity has led to Booyco Engineering becoming an approved supplier to global rail OEMs. Grant Miller, executive director at Booyco Engineering, explains how the company became the first South African supplier to locally manufacture a cooling tower for electric locomotives. Working within the customer’s demanding framework of specifications and standards, the value added by the software was vital to the successful outcome.
“We developed our initial prototype design, which was then systematically verified against the customer specifications using CFD or FEA simulations to ensure the design was producing the expected results,” says Miller.
Only then was a physical test conducted. This test, he says, was almost a formality – to verify the
The cloud-based Metrics monitoring system portfolio is one of Metso Outotec’s key digital solutions for customers. The company is now expanding Metrics to cover the tools, sensors and dashboard access for monitoring customers’ stationary screening equipment.
With its 24/7 online monitoring capabilities, Metrics offers improved safety, increased uptime and throughput and reduced unplanned maintenance. It enables operators, controllers and service professionals to see real-time analysis of vibrating screen performance and bearing condition. Metrics is designed for intuitive operation. An easy-to-read screen dashboard with OEM insights makes it possible to quickly detect potential issues and take corrective action in time.
In June 2022, Metso Outotec announced a global cooperation
agreement with Dynamox, which offers an innovative condition monitoring platform. Metrics for screens is the first solution utilising Dynamox’s easy-toinstall instrumentation that can be complemented with comprehensive value-added services and remote monitoring capabilities in the customer’s value chain.
“The customer feedback received has helped us to offer a solution focused on customer-centricity and sustainability. Metrics for screens helps customers to optimise their process, as they can easily see how the changes implemented have impacted their screening operations. In addition, continuous monitoring helps in the avoidance of several potential breakdowns. It also has a positive impact on sustainability, as running the screen in an optimal way enables increased uptime and less consumption of media, spare parts, oil and energy.
calculations and simulations.
“For the cooling tower we designed and built, we physically vibration-tested the components but not the actual structure,” he says. “This was because the structure weighed about a tonne and a half. But we could conduct a detailed FEA to verify the structure, which satisfied the customer’s requirements.” a
Our strong development roadmap will enable us to release more data-driven and value-added services soon,” says Jan Wirth, technology director with Metso Outotec’s Screening Solutions business.
By combining Metrics with our global service footprint, Metso Outotec and its distributor partners can support customers in making data-driven decisions that impact their screening operations.a
McCloskey International used bauma 2022 to unveil its new J4 jaw crusher. Building on the existing line-up, the J4 comes with a range of features aimed at boosting productivity and offering enhanced durability across applications.
Designed to withstand the toughest conditions worldwide, the J4 delivers high production due to its innovative jaw chamber design and enhanced material flow. The large 1 060 mm x 700 mm jaw opening accommodates large feed sizes, contributing to higher production in material processing.
The material path is enhanced with the 1 064 mm x 4 247 mm grizzly pan feeder under the hopper that allows for better sizing of material with a variety of mesh options. Options of either a short pan feeder to suit the pre-screen or a double deck grizzly pre-screen are available, ensuring suitability and better sizing of material based on the application.
The J4 delivers industryleading stockpiling, with wide main and side conveyors for enhanced material flow. The angle adjustable 1 200 mm wide ToughFlex main conveyor boasts a 3 912 m high stockpile, and with quick release and ground level access, the belt is easy to maintain and service.
ToughFlex is constructed with a special weave of two fabric plies and an additional binder warp (without the need for steel wire) resulting in reduced belt weight. The plies are reinforced to resist
puncturing and are protected with heavy duty wear-resistant top and bottom covers. At the end of its lifespan, ToughFlex belts can be easily recycled unlike belts reinforced with a metal ply. McCloskey engineers have designed the J4 to meet the evolving requirements of today’s projects and operations. Despite the large size of the machine, portability has not been compromised. Mobility on-site and between sites continues to be a feature with remote control tracks to easily move and position the crusher and maximize the efficiency of any project site. Also contributing to efficiency, particularly in remote locations, is the high-volume fuel tank, sufficient to run the J4 for approximately 20 hours.
Technology has been a key factor in the development of the J4, with a 12” DSE control panel for the highest operational performance and reliability providing pushbutton control of the jaw, track and feeder functions. The crusher is fitted with a telematics modem for the new 365SiteConnex programme, a complete connectivity solution for highly accurate monitoring of McCloskey products. 365SiteConnex is based on the latest leading-edge communication technologies to collect, analyse and deliver information on the crushers, screeners and stackers customers rely on to produce the highest quality products with the least amount of downtime. a
Epiroc has agreed to acquire Remote Control Technologies, an Australian company that provides automation and remote-control solutions for mining customers around the world. With this acquisition, Epiroc will be the world-leading automation solutions provider not only for surface and underground rock drilling but also for underground loading and haulage.
Remote Control Technologies, known as RCT, is headquartered in Perth, Australia, with customers in more than 70 countries. The company provides automation and remote-control solutions applicable for either a single machine or an entire mixed fleet of machines regardless of manufacturer or type of equipment. RCT also provides data and information systems, fleet and machine management systems, and machine protection systems.
“Automation is increasingly important for the mining industry to strengthen safety and productivity, and RCT’s advanced solutions complement Epiroc’s existing automation offering well. Together we will provide complete automation and remote-control solutions to support our customers on their journey towards optimal operations,” says Helena Hedblom, Epiroc’s President and CEO. “We are especially pleased that Bob Muirhead, RCT’s founder and a true pioneer within mining automation, will continue in an active management role. We look forward to welcoming the strong RCT team to Epiroc.” a
The rapid evolution of Collision Avoidance Systems (CAS) for surface mines has embraced technologies such as satellite positioning systems, radar and smart vision. Leading CAS specialist Booyco Electronics also points to the value of sensors and tracking technology.
By capturing and processing more data in real time, there is growing potential for these systems to make surface mining even safer.
Underpinning the success of CAS have been years of intensive research and development, says Booyco Electronics CEO, Anton Lourens. This work has actively embraced various new and existing technologies, further raising the reliability and functionality of CAS.
“Pioneering companies such as Booyco Electronics – in this game for over 16 years – have taken advantage of developments in satellite positioning systems, for instance,” says Lourens. “This has enabled us to achieve greater performance in collision algorithms.”
“We have become interested in smart vision systems that allow intelligent perception of people, vehicles, objects and other risks,” he says. “Wearable technology also allows us to enhance
context and to readily distribute safety information. New technologies have even allowed us to embrace cutting edge fatigue detection solutions.”
He explains that Industry 4.0 has brought levels of digitalisation and automation that could not be envisaged until recently. In response, Booyco Electronics has invested vigorously in softwarebased solutions, paving the way for increased flexibility to customise solutions for specific needs.
“This has meant that our equipment can be improved and customised through its software elements rather than its hardware,” he says. “Functionality can therefore be adapted more easily and can be applied remotely through a wireless connection instead of requiring inperson attention on site.”
Rapid developments in sensor and tracking technology were also delivering exciting opportunities to advance CAS capabilities. Integration is really the key to success in these endeavours, he argues.
“We have progressed considerably down the path of combining the power of sensors with information technology,” says Lourens. “This allows
The rapid evolution of Collision Avoidance Systems for surface mines has embraced technologies such as satellite positioning systems, radar and smart vision.
us to capture extensive data about the respective locations of personnel and machinery through proximity detection systems.”
Digitalisation gives Booyco Electronics the ability to upload and analyse this data in real time, so that it can inform on-mine decisions and enhance safety strategies. More than this, CAS can now contribute to emerging automated mine ecosystems. As autonomous mining is gradually rolled out in the sector, CAS can be relied upon to support this process with the necessary safety levels. a
Further boosting its growth plans, Jet Park-based IPR has just become the southern African distributor for the Atlas Copco Pump Division. Previously known as Integrated Pump Rental, local pump and dredging specialist IPR recently rebranded to reflect its expanded market offering. The company will now also sell and rent Atlas Copco’s diesel-driven and submersible pump range.
According to Lee Vine, MD of IPR, the new arrangement will further enhance IPR’s offering to customers. The company has over the past eight years built a significant presence in mining, construction, agriculture and other industrial sectors.
“Representing a leading global brand like Atlas Copco reinforces IPR’s commitment to our customers, which
combines the best quality equipment with our superior service levels,” says Vine. “Our extensive network in the region ensures we are close to customers, and the Atlas Copco range adds further to our capability to meet their site-specific needs.”
The new range includes wet prime and dry prime diesel-driven pumps, as well as submersible pumps for the three key pumping categories – dewatering, sludge and slurry. The diesel-driven pumps range in capacity from a 30 m to 150 m head, with flow rates from 50 to 1 500 m³ per hour. The submersible range of Atlas Copco pumps extends from 0,4 kW to 54 kW power.
“IPR has developed an unsurpassed depth of technical expertise and market knowledge since we launched in 2015,” he says. “Our skills base and
connection to customers have made this collaboration with Atlas Copco a perfect fit for us – adding considerable value for our customer base.”
As IPR product manager for the Atlas Copco range, Steve du Toit highlights that a substantial stockholding to meet demand is in place at IPR’s Johannesburg head office. The company’s well-equipped and professionally staffed service centre is always on hand to support the market.
“The Atlas Copco brand boasts a high level of quality with robust materials of construction for strong performance and rugged wear,” says du Toit. “Features like high chrome impellers and mechanical seal flushing all contribute to optimal reliability and uptime.” a
This year, bauma was once again a magnet for visitors.
A total of about 3 200 exhibitors from 60 countries (2019: 3 684 exhibitors from 63 countries) and more than 495 000 visitors from over 200 countries (2019: 627 603 visitors from over 200 countries) attended bauma 2022, held from October 24 - 30 in Munich. The proportion of international visitors was around 50%.
The top 10 exhibitor countries were, in this order: Germany, Italy, Turkey, Great Britain and Northern Ireland, the Netherlands, France, the United States, Austria, Spain and China. The share of international exhibitors was nearly 65%. Stefan Rummel, the CEO of Messe München, is pleased: “This bauma has again stoked enthusiasm and fascination! After the world fundamentally changed following the last bauma, we are really thrilled that bauma 2022 demonstrates that the trade fair remains a powerhouse of the construction-equipment industry, thanks to our customers’ great variety of innovations, good business deals and many visitors from all over the world.” This is so because bauma displayed its usual strength even in these unsettled times, as Domenic Ruccolo, CSO of
Wirtgen Group and senior vice president of Sales, Marketing and Product Support for Global Construction Equipment at John Deere confirms: “The Wirtgen Group’s joint trade show appearance with John Deere was a resounding success. The interest in our company and our innovative and sustainable products was simply overwhelming. Our participation in the industry’s leading trade fair, bauma, was the most successful in the history of the Wirtgen Group.”
Steffen Günther, a member of the Board of Directors of Liebherr, also expresses his satisfaction: “bauma proved to be a very successful trade fair for us. We generated a lot of enthusiasm among the large audience. The conversations were outstanding. We
are already looking forward to the next bauma trade fair now.”
Fred Cordes, chairman of the Management Board at Zeppelin (CAT), adds: “bauma was long overdue – as demonstrated by the overwhelming rush of visitors to our booth and the extraordinary interest in Cat construction machinery and Zeppelin services.”
In terms of business deals as well, bauma proved once again it is the platform for the industry. Alexander Greschner, chief sales officer at Wacker Neuson Group, says: “Visitors flocked to our stand, and we had a lot of very good discussions. From the very first day we were able to achieve sales success on the same level as 2019 and beyond.” a
Liebherr’s 50-tonne R 9XX H2 hydrogen excavator has received the 2022 Bauma Innovation Award in the climate protection category. This is the first Liebherr hydraulic excavator to be powered by a hydrogen engine.
The R 9XX H2 is powered by a Liebherr H966 hydrogen combustion engine. The engine has six cylinders and uses port fuel injection (PFI), which Liebherr employs along with direct injection (DI) for its hydrogen engines. Liebherr’s components product segment plans to start with the series production of hydrogen
motors by 2025.
Year 2022 sees the 13th presentation of the Bauma Innovation Award. Its five categories – climate protection, digitalisation, mechanical engineering, building and research – reflect political, social, economic and ecological challenges. The expert jury’s focus on criteria such as practical orientation, economic potential, environmental protection aspects, resource conservation, efficiency and humanisation the workplace.
The prize is awarded by Messe München and the German Mechanical Engineering Industry
Association (VDMA), together with the Federation of the German Construction Industry (HDB), the German
Construction Confederation (ZDB) and the German Building Materials Federation (bbs). a
Liebherr hydrogen excavator wins Bauma Innovation Award
A Trio EF3606 pan feeder installed by Weir Minerals Africa at OMV’s Stilfontein crushing plant has increased production by 40% and helped to create a safer working environment
OMV’s target was 1 300 tonnes (t) per day, but the plant could only produce 1 000 t. As Weir Minerals Africa has been working successfully with OMV for more than five years, OMV requested their help in increasing the plant’s capacity.
The lack of plant capacity was deemed a result of the stockpile reclaim chutes regularly becoming blocked, resulting in an inconsistent feed to the cone crushers. As the cone crushers were unable to be choke fed, OMV often experienced an inconsistent product, crusher inefficiencies and uneven wear of their cone crusher liners.
To address this issue, OMV had to constantly monitor and manually clear the feed from the chutes. Manually clearing the feed presented a considerable safety risk, as rocks would fall out of the chute once the blockage was removed.
To provide a reliable and consistent feed to the cone crushers, a Trio EF3606 vibrating pan feeder was selected. The Trio EF series is perfectly designed to perform in surge tunnels or under surge bins, controlling the feed rate to the
next stage of processing. Combining the Trio pan feeder with a variable speed drive (VSD) and a programmable logic controller (PLC) allowed the feeder to alter its speed, based upon the levels of feed already within the cone crusher’s bins.
Weir Minerals Africa’s engineers also redesigned the chute system and used 3D laser scanning equipment to ensure the new structure and chutes would fit within the existing footprint. The team used simulation software to reproduce
BLT WORLD – a specialist in bulk materials handling – has launched ScrapeTec’s new SureSupport conveyor system, designed to improve material take-up and maximise the efficiency of skirting and sealing. This is achieved by correcting belt tracking, providing an effective seal at the transfer points, preventing material spillage and enhancing dust control.
“The newly designed SureSupport system delivers support and stability to the belt at transfer points, which increases the effectiveness of side sealing, enhances dust suppression and minimises material spillage,” explains Ken Mouritzen, MD of BLT WORLD.
“In conventional conveyors, the force of falling bulk materials causes a high belt load in the transfer area, resulting in belt degradation and increased material, energy and maintenance costs. To compensate for the belt load and to maintain efficient sealing within the transfer area, the idler density can be increased in the feed area. Although this measure may improve efficiency, it does not fully eliminate belt damage.” a
and optimise the particle flow through the new chute design.
After commissioning, OMV’s capacity was immediately increased to 1 400 tonnes per day, a 40% daily production improvement that resulted directly from the consistent feed to the cone crusher.
Furthermore, no blockages have been experienced since the new feeder has been installed. The plant has increased its uptime to as much as 99,5% of its 10-hour shifts, and the safety risk of clearing the chute has been removed. a
Getting the best performance and life from vibrating screens requires realtime data on their operating conditions, according to Kwatani’s Kenny MayhewRidgers. This is now possible with sensors and digital technology, which bring many benefits over traditional paper-based systems.
“Where machine data recording –combined with periodic inspections and regular maintenance – can be captured in the digital sphere, you can generate a complete picture of the equipment’s lifecycle,” says MayhewRidgers. “Real-time data monitoring is a game changer for screen reliability and performance.”
Wherever there are operational deviations from the prescribed norm, sensor-generated data can quickly alert the right people on the mine – giving them the ability to react timeously, he says. Importantly, this technology also allows patterns to be detected in the relationship between component life and throughput.
“By analysing these patterns, the mine can make well-informed decisions about its maintenance strategies, being aware of the optimal conditions for its equipment duty,” he says. “It also gives us, as original equipment manufacturers, the opportunity to compare machine performance in detail across different customer sites – so that we can adapt and advise accordingly.”
Where Kwatani sees one customer getting longer life from their exciters, for instance, the relevant data is easily available to make comparisons
and identify distinguishing factors. He explains that Kwatani can monitor its vibrating screens using industrial sensors and measurement technology which is readily available and supported worldwide. In other words, it is not so specialised that it becomes unaffordable; neither is it so complicated that customers cannot maintain it themselves.
“What is key to the successful application of digital technology is that the raw data that we process must be analysed to become useful for decision making and planning,” says Mayhew-Ridgers. “This means streaming it seamlessly to databases and allowing our customers to visualise the information effectively.”
To do this, Kwatani partners with
One of the important features of the Doosan stand at Bauma was the dedicated Innovation Centre, where the company unveiled the new generation XiteCloud ‘All-in-One Platform’ for Smart Construction under the company’s ‘Powered by Innovation’ banner.
In 2019 in South Korea, Doosan introduced Concept-X, the world’s first unmanned automated and integrated control solution for construction, quarrying and mining sites. XiteCloud
is the first stage in commercialising Concept-X.
With XiteCloud, a customer can manage multiple tasks such as surveys, terrain analysis, machine purchases, equipment operation and construction management on a single platform, thereby reducing construction costs and saving time, while increasing work accuracy, which in turn raises productivity. XiteCloud also allows customers to manage multiple projects on a single platform, accumulating and
system integrators and works closely with its mining customers so that the end-users get the most out of the information without spending time and money to process the raw data themselves.
This digital monitoring can also help to overcome a common challenge in many mining operations: working in silos. Paper systems do not easily lend themselves to sharing of data across different aspects of the operation. This in turn makes it difficult to improve equipment performance on a holistic basis. The availability of various streams of data on a single platform enhances transparency between service technicians, foreman, engineers and the OEM of equipment on site. a
managing data that can be utilised for future decision making/business.
At Bauma 2022, Doosan showcased the new All-in-One Platform for smart construction, based around the Xitecloud system. The All-in-One Platform introduces a range of new solutions that form part of the XiteCloud system all of which will be demonstrated at Bauma, covering many aspects of construction management, including XiteCore, XiteFleet, XiteAnalyst, XiteSIM, XiteSafety and XiteAuto. a
On any belt conveyor system that moves bulk materials, the belt must run straight and true to maximise its life, minimise fugitive material and safety hazards, and achieve high system efficiency. There can be many consequences of a mistracking belt, but all result in higher costs and increased maintenance. Even a slight belt misalignment can lead to a variety of issues, from small annoyances to full-blown catastrophes.
The most obvious effects include spillage and dust that require personnel to do clean-up, which is unproductive work that introduces risks from activities in close proximity to the moving conveyor. Spillage from noncentred cargo often finds its way into idlers and pulleys, reducing bearing life and causing them to seize, leading to friction damage on the belt and potentially starting a fire.
A misaligned belt can also come in contact with the stringer, causing fraying, shredding or splice damage. Great lengths of valuable belting can be destroyed with surprising speed, and even the support structure itself can be damaged. A compromised bracket or support can cause a catastrophic idler failure, which could damage other components of the system and require extensive downtime to repair. Further, there is potential for injury from
a damaged belt or loose idler, not to mention the increased exposure to injury from too frequent a need to clean.
“I have been working around conveyors for 20 years, and I have seen thousands of belts,” observes Martin Engineering process engineer Dan Marshall.
“I have seen just about every problem that can be caused by a mistracking belt, but one thing I have never seen is a belt that runs true right out of the box. All conveyors, no matter
how well designed and built, have some belt wander.”
A wide variety of circumstances can lead to mistracking, and operators have tried many things to correct the alignment. Some have elected to place an obstacle such as a block of wood in the belt path, so it won’t travel too far out of line. This occasionally improves the situation, but more often it is just a temporary solution and the belt will eventually slice through the obstacle.
Many operators have realised that pivoting an idler is a quicker and more effective way to steer a belt. This common approach is called “knocking an idler,” striking it with a hammer to move it slightly and realign the belt.
Equipment manufacturers have also designed components to help align a belt, and these solutions can be successful in specific applications. They include specially shaped rollers, angled idlers and devices that apply pressure to the belt edge to push it back in line.
“While these mechanisms can improve a belt that’s consistently off-centre in one direction, they do not react to dynamic belt movement, meaning that they don’t correct intermittent belt wander,” adds Marshall. “To combat such changing conditions, engineers designed the tracking idler. Unlike the edge correction approach, the
device senses belt movement in either direction and pivots the idler slightly to steer the belt back into position. It doesn’t apply a great deal of force to the edges, which can damage a belt and splices. When the belt is running true, it remains centred, and when it senses a misaligned condition, it gently corrects the belt.”
Unfortunately, to accommodate limited space availability, tracking idlers typically have short sensing arms. This requires a fairly large belt displacement to create a small movement of the idler. While these designs do tend to improve tracking, there are limits to how much correction they can deliver, and short sensing arms can actually pinch a belt if the idler pivots too far. To combat this, some operators choose to “tie off” a tracking idler to limit its movement. While the practice can help preserve the belt, it doesn’t address significant mistracking.
To overcome the limitations of existing belt alignment devices, Martin Engineering has invented and patented a Multi-Pivot Belt Tracker, which employs sensors, pivoting idlers and geometry to align a wandering belt. The sensors avoid pinching the belt, and the engineered geometry amplifies any detected misalignment to create a greater pivot.
Multi-Pivot Belt Trainers use
longer arms than other designs, positioning the guide rolls further from the pivot roller, as well as closer to the belt edge. The closer proximity allows guide rolls to sense very slight misalignments and make immediate corrections. Rather than waiting for a powerful mistracking force, the longer arms require considerably less pressure to move the pivot roller. The result is better correction with no pinch points and less wear on conveyor and tracking equipment, thus ensuring a longer and more efficient service life. Specific designs are available for both the load-carrying belt path and the return run.
“Installing trackers is the economical solution, but operators should definitely carry out a full analysis and also consider addressing other causal issues,” Marshall adds. “By focusing solely on belt alignment, plant personnel may miss other opportunities to increase production and relieve some of the burdens on their system.”
Keeping the belt centred and moving quickly are key to high production, controlled operating cost and a safer workplace.
“Misalignment causes downtime and costs money. But nothing causes more downtime and expense than a destructive belt fire or other catastrophe as a result of inattention to mistracking problems,” concludes Marshall. a
Surface mining industry association, ASPASA, has called on law enforcement agencies to crack down on all illegal mining activities.
As more serious crimes perpetrated by illegal miners grab the headlines, other equally serious safety and environmental crimes that have the potential to affect communities are taking place.
Simultaneously, legal mining operations and those who purchase the mined minerals (sand, aggregate, gold) need to remain up to date with new legislation and regulations to avoid falling foul of the law or buyers being complicit in these illegal activities.
Individuals, companies and even municipalities are mistakenly under the impression that they can remove ground or minerals wherever they want to, but this is not the case. The Mineral Petroleum Resources Development Act (MRPDA) is clear that once a material is taken away from its natural state it is, in fact, being mined.
Any sort of mining needs to be done in a manner that does not affect surrounding communities, harm the environment, or detract
from future land use possibilities whether mining for gold, coal, clay, or aggregates.
“These are costly exercises and when ignored by illegal miners gives them a massively unfair advantage over legal operators in the industry. They don’t pay royalties, tax, or make any other statutory contributions to the government or towards the
sustainability of the industry,” says ASPASA.
“Nor do they need to observe safety, health, environment, and quality legislation which means they can expose their employees to inhumane working conditions, as well as cause untold damage to the environment without fear of retribution.” a
www.quarryingafrica.com