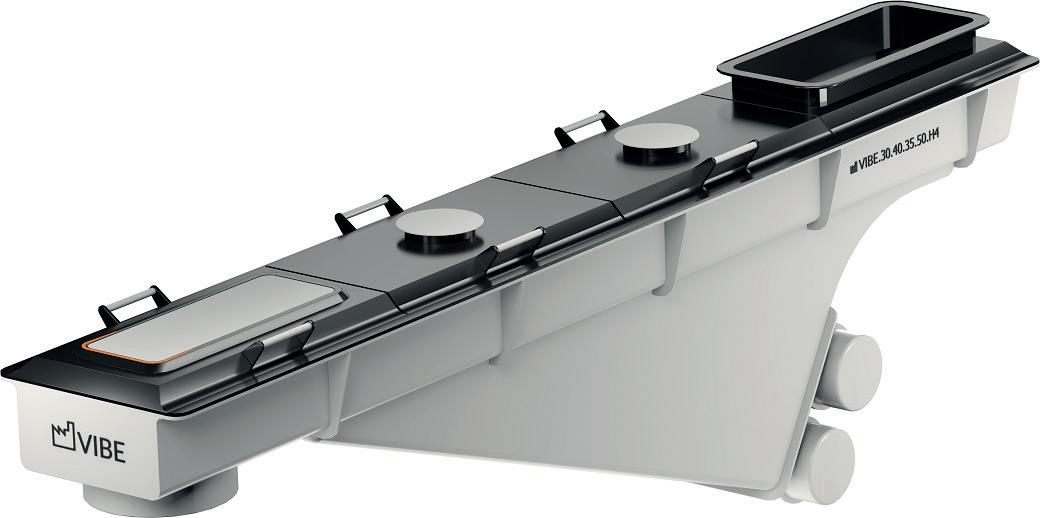
9 minute read
Batch plant: Forglass
VIBE: the high-performance dosing feeder from Forglass
Tomasz Zejer1, Maciej Olesinski ‘ 2, Kacper Musioł3, Andrzej Ciopa4, Radosław Jurek5 discuss an RVDS system which allows for accurate dosing of the feed transferred by feeders with rotating vibrators.
Vibrating feeders are widely used across many industries to transport bulk materials. A particular application of vibrating feeders is the process of precise dosing of materials for the needs of technological processes.
The use of feeders driven by inertial vibrators for this purpose requires the feeder to work near the natural frequency and overcome resonant frequencies during the start-up and coasting of the device.
Overcoming resonance zones and working at near-resonance frequencies may cause uncontrolled flow of the feed from the feeder chute, which has made it impossible to use such solutions in industrial practice.
The possibility of precise dosing with inertial drive feeders is particularly critical to the glass processing industry. The market situation and the increasing demand for glass products have forced glass producers to increase the efficiency of their furnaces.
Production lines with a capacity of 1000-1200 t/day for float glass and 300400 t/day for container glass, which were a phenomenon only a few years ago, have become standard today.
The increased efficiency of glass furnaces requires the equipment preparing and transporting the raw materials to the furnace to increase its effectiveness.
An important role in this process is played by vibratory feeders. These devices, together with the weighing system, are responsible for the correct dosing and weighing of individual raw materials, the process in which the quality and colour of the produced glass, directly depends.
The requirement to maintain high precision of dosing has so far limited the choice of transporting devices to vibrating feeders based on electromagnetic drives, the precision of which comes at the cost of a number of disadvantages for the industry, including: � large mass of the drive, which translates into a greater mass of the entire feeder, � limited length and capacity of feeders, and � limited availability of spare parts - most of the electromagnetic drives are made to order for a specific weight of the feeder, which may mean as much as a three-month waiting period.
Inertial drives allow the construction of feeders of any length, several times greater transport efficiency. However, those feeders have not been used in the glass industry due to their low dosing precision. The reason for this is their inability to stop the transport of the material without stopping the feeder drive. Stopping the inertial drive is associated with the desynchronisation of the motors while passing through the resonance zone and an increase in the kick coefficient when approaching the resonant slope of the feeder, the consequence of which is a complete loss of control over the transport process (from the moment the drive is turned off, until the movement of the feeder body stops).
The presented solution, thanks to a proprietary design, can combine the previously contradictory properties: the possibility of achieving high transport efficiency, with the accuracy of weighing out a precise portion of material, available only for electromagnetic drives. What this means for the industry is: � the possibility of a three-fold increase in the efficiency of dosing feeders while maintaining the same weight of the device, � the possibility of a two-fold reduction in the weight of the dosing feeder while maintaining efficiency � significant reduction of service costs and time. To achieve the above goals, it was necessary to solve the problems presented in this article.
Description
Obtaining a precise dosing function by a vibrating feeder driven by two selfsynchronising vibrators, with opposite directions of rotation, requires that the speed of transporting the material along
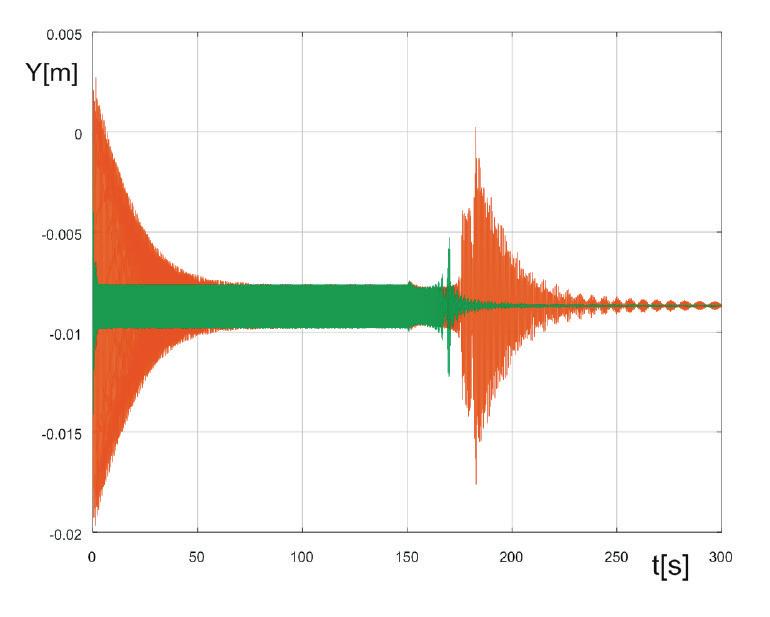
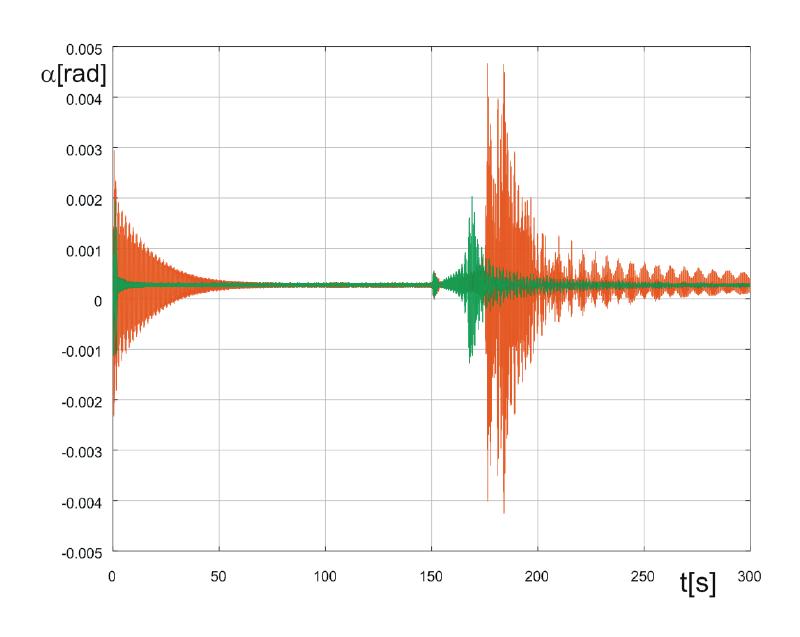
Testing in working conditions
� Fig 2. The influence of RVDS on vertical (left) and angular (right) vibrations of the feeder during start-up, nominal operation and coast-down.
� Fig 3. The influence of RVDS on vertical and angular vibrations of the feeder during start-up, steady operation and quasi-steady coast-down with linearly declining angular velocity of vibrators.
the feeder chute decreases monotonically, along with lowering the angular velocity of the vibrators until the transport is stopped.
Additionally, the transported material cannot, in an uncontrolled manner, slide down from the feeder chute during its start-up and coasting.
The condition for obtaining appropriate dynamic properties of the feeder, allowing for the precise dosing function, is to increase the damping properties of the suspension on elastic steel elements in the range of low operating frequencies, while limiting the damping in the operational range.
This task can be accomplished with the system (patent P.425086) shown in fig. 1 overleaf and pictured first page.
The resonant vibration damping system (RVDS) consists of a spring and a viscous damper connected in series, parallel to the main feeder suspension.
The resonant vibration damping system is attached with one end to the mobile transport system, and the other end to the stationary supporting structure of the device. The appropriate selection of the additional spring’s stiffness and the damping constant of the damper results in a self-regulating system that dissipates energy at low frequencies with low efficiency in the range of the rated operating frequency.
Digital model
The tests of the vibration damping system were carried out on a digital model of a vibrating feeder suspended on tie rods, equipped with the system for damping resonance vibrations and a layered model of the feed.
The parameters of the resonant vibration damping system were selected and the digital feeder model was then loaded with a multi-layer feed model.
Numerical simulations
To assess the effectiveness of the resonant vibration damping system, the selected results of simulation tests obtained for the system without the RVDS system (red colour) and with the RVDS system (green colour) as presented in the diagrams.
First, the influence of RVDS on the start-up process, the steady operation for 150 seconds and the free coast-down of the machine were checked, Fig. 2. The application of the vibration damping system shortened the duration of the transition periods in the vertical direction Y by about: 15x for the start-up, 5x for the coast-down and the reduction of the maximum amplitudes: 1.6x for the start-up, 2.5x for the coast-down.
At the same time, for the α coordinate, the duration of the transition periods was shortened by approximately: 6x for the start-up, 1.7x for the coast-down, and the maximum amplitudes were reduced: 1.8x for the start-up, 2.7x for the coast-down.
In the second case, the operation of RVDS in quasi-steady states was examined. The simulations included switching on the feeder and reaching the nominal speed, steady work for a period of 100 s, then work with a slowly changing, linearly declining supply frequency until the material transport along the feeder chute is stopped, and finally stopping the vibrators, Fig. 3.
The use of the RVDS system resulted in a 5.8-fold decrease in the amplitudes of maximum vertical vibrations in quasistationary resonance and a 4.5-fold decrease in the amplitudes of maximum angular vibrations in quasi-stationary resonance.
To confirm the accuracy of the results obtained in theoretical considerations, a full-scale feeder was tested on a specially constructed test stand (Fig. 4), which allows testing feeders with continuous circulation of the feed. A feeder equipped with RVDS was tested on the stand. The pilot installation was made using a suspension with increased internal damping. Additionally, a test feeder was also installed in a working glass factory.
The possibilities of building dosing feeders with inertial drives are not limited to those equipped with RVDS. The mechanical parameters of the feeder can be selected in such a way that it is possible to use standard metal-rubber suspensions with increased internal damping – known as the ROSTA type.
The energy dissipation coefficient of metal-rubber suspensions at the level of Υ=0.4-0.5 allows for the precise dosing process.
An example and confirmation of these possibilities is the implementation of the system for precise dosing of the batch components at the British glassworks Stoelzle Flaconnge.
For this purpose, a feeder with an inertial drive, 4250 mm in length and with the capacity of ~ 30 t/h, was
Continued>>
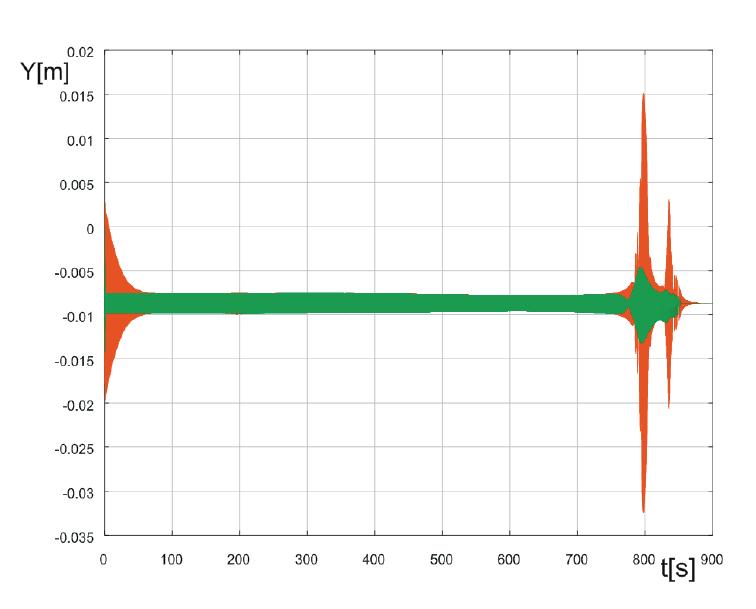
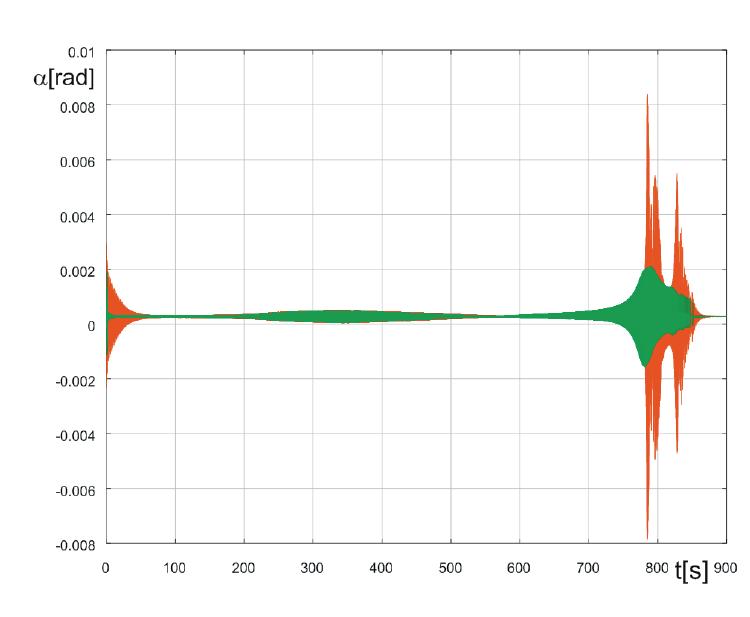
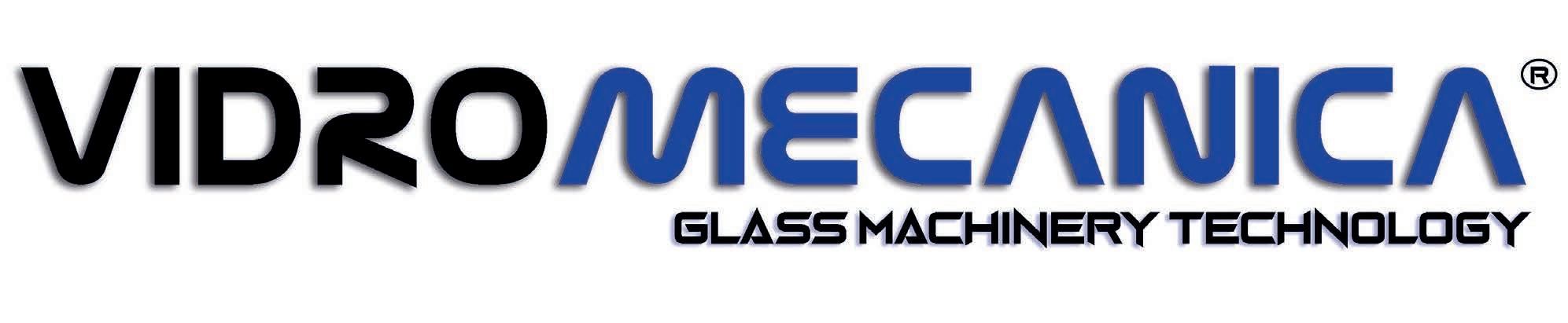
Decorating lehrs
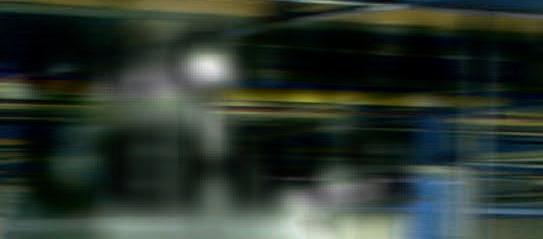
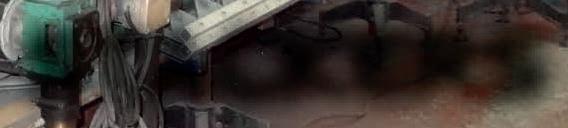
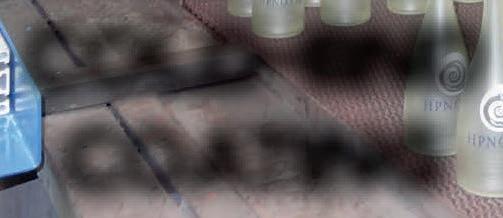

stackers
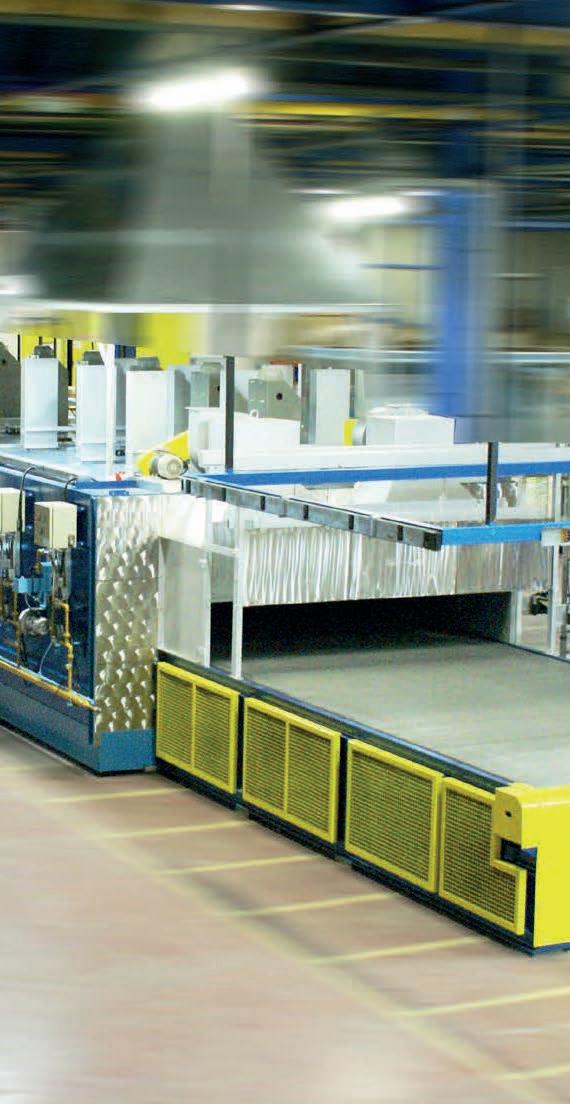
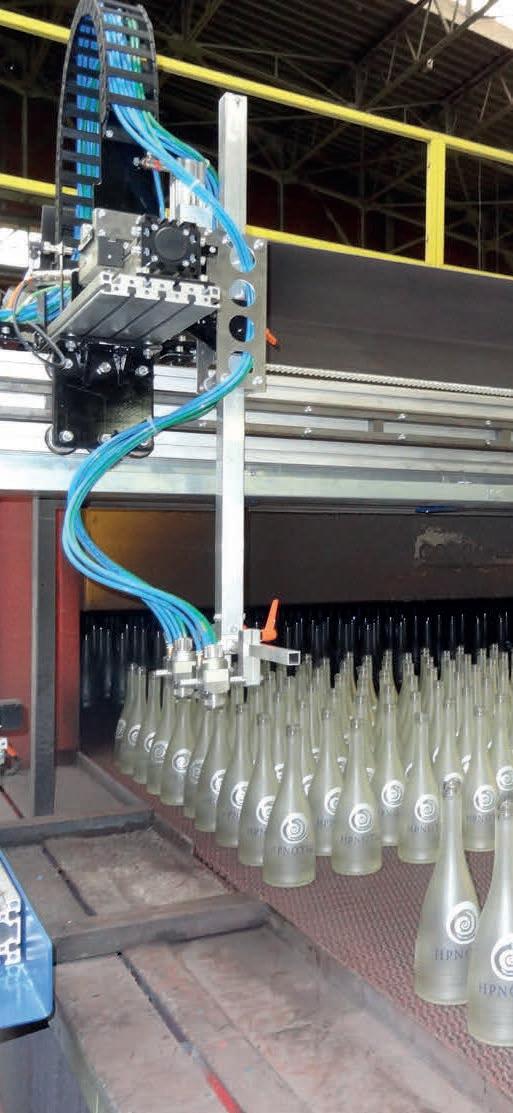
Cold-end coating

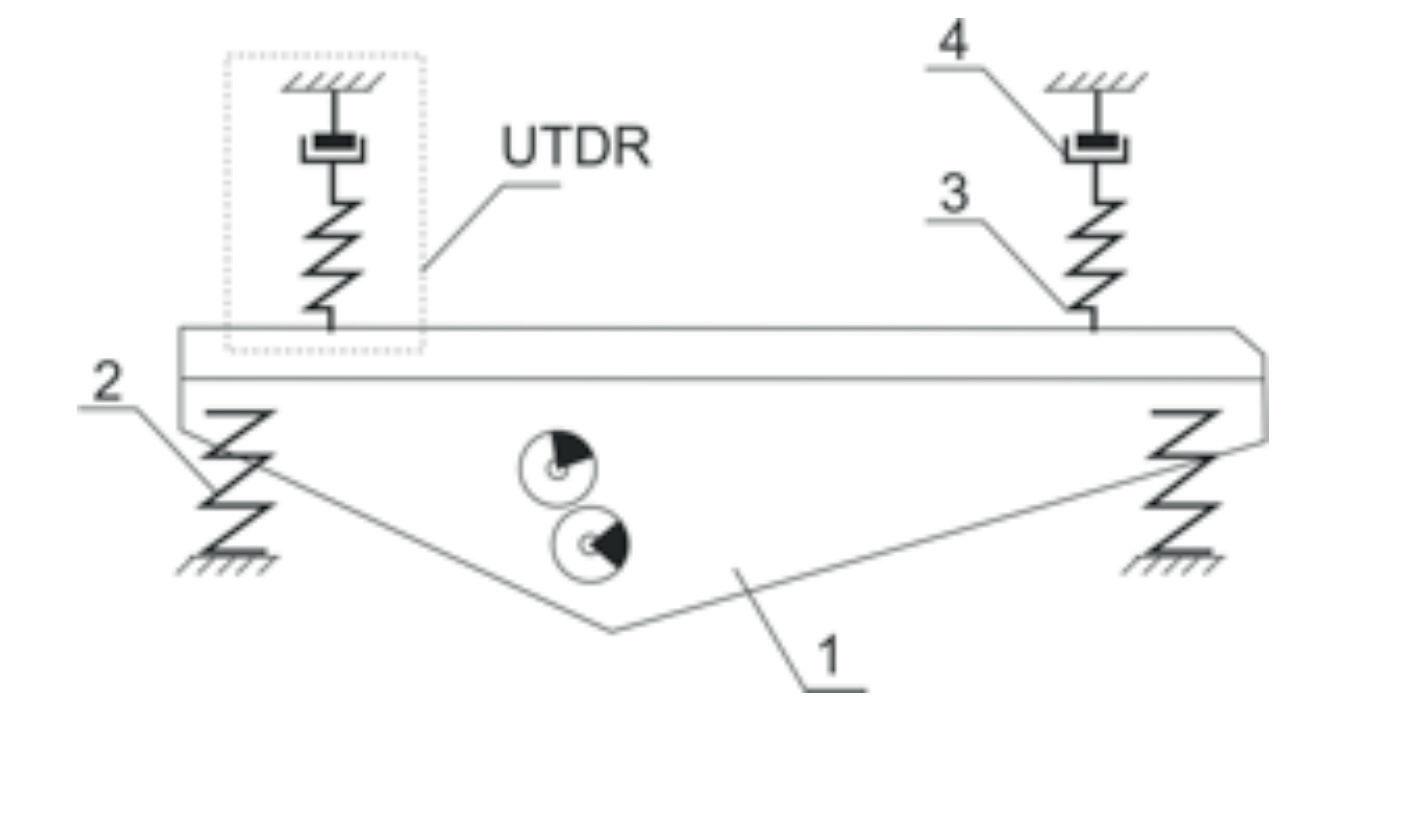
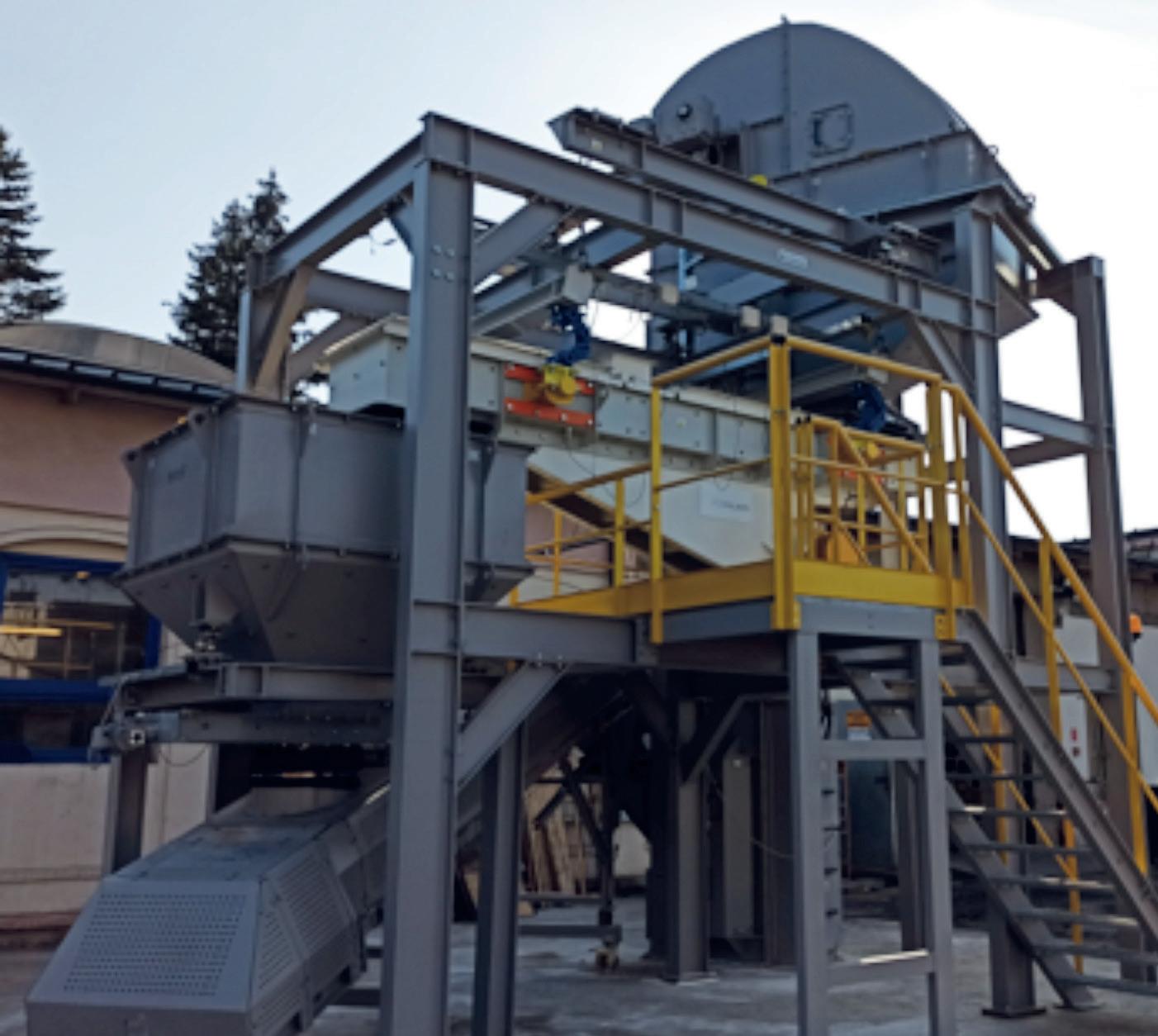
designed, built and installed in place of the existing feeder with electromagnetic drives, dosing soda to the mixer.
The feeder is controlled by the main control and measurement system of the glassworks, which allows for the recording of individual material dosing cycles. One of the recorded cycles is shown in Fig. 5. The weighing algorithm starts with the chute in a fast mode (50Hz). Dosing continues until the weight defined in the dosing system control’s visualisation panel is reached. Exceeding this point causes the change of speed to slow (23Hz). The chute continues dosing in idle mode until the weight reaches the value equal to the target weight minus the weight value of the material that will slide off the feeder when the transport is stopped at idle speed.
After the end of the cycle in automatic mode, the algorithm checks the deviation of actual weight from the set value, on the basis of which it selects a different speed change point and a stop point with each cycle to remove the weighing error (Fig. 5).
During operation of the feeder in reallife conditions, the dosing efficiency was two times greater than the previous feeder’s with electromagnetic drive. The error obtained with this installation is less than 0.1% of the set value.
Conclusions
The RVDS system allows for accurate dosing of the feed transferred by feeders with rotating vibrators.
The computer simulation analyses of the system’s operation proved the full suitability of the RVDS system for the process of precise dosing. In particular, they showed that this system does not interfere with the operation of the feeder in nominal conditions, while allowing limiting the vibration amplitudes in the transient resonance states and during the material dosing process to values that are acceptable in practice.
The accuracy of dosing achieved by the RVDS-equipped Vibe feeder in reallife working conditions at the level of +/− 0.1% of the set mass proves that the efficient inertial drives instead of the electromagnetic drives in the construction of dosing feeders is not only viable – it is the way of the future. �
� Fig 4. Full-scale test stand – Forglass, location: Zawada.
� Fig.1. 1. Feeder with RVDS (Polish: UTDR) resonance damping system. 1-vibrating feeder, 2-main feeder suspension, RVDS - resonant vibration damping system, 3-RVDS spring, 4-RVDS damper
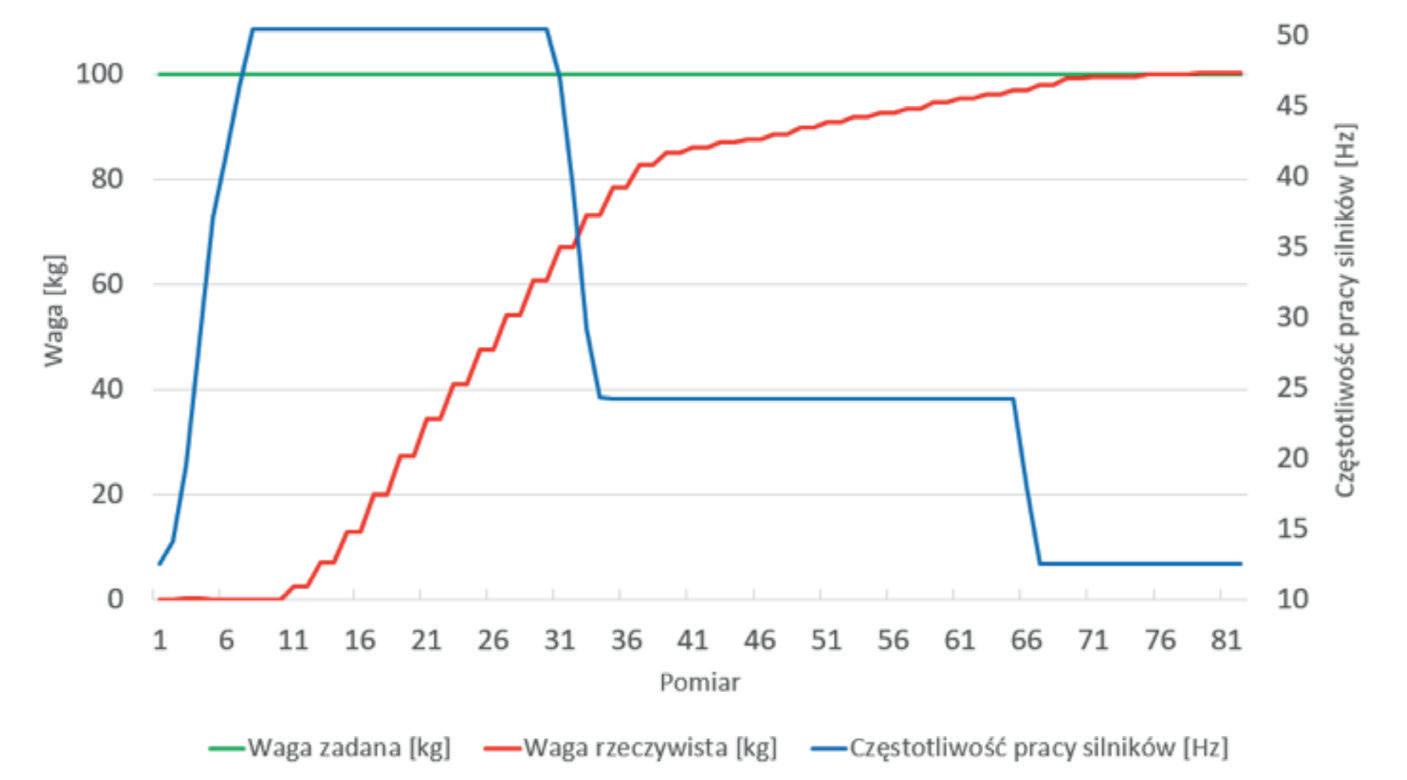
� Fig. 5. The course of the dosing process recorded by the glassworks control and measurement equipment.
*1 R&D Technical Director, 2 Design Engineer, 3 Design Engineering Team Leader, 4 Chief Automation Specialist, 5 Automation Engineer Forglass, Wadowicka, Kraków; Poland https://forglass.eu www.vibe-feeder.eu