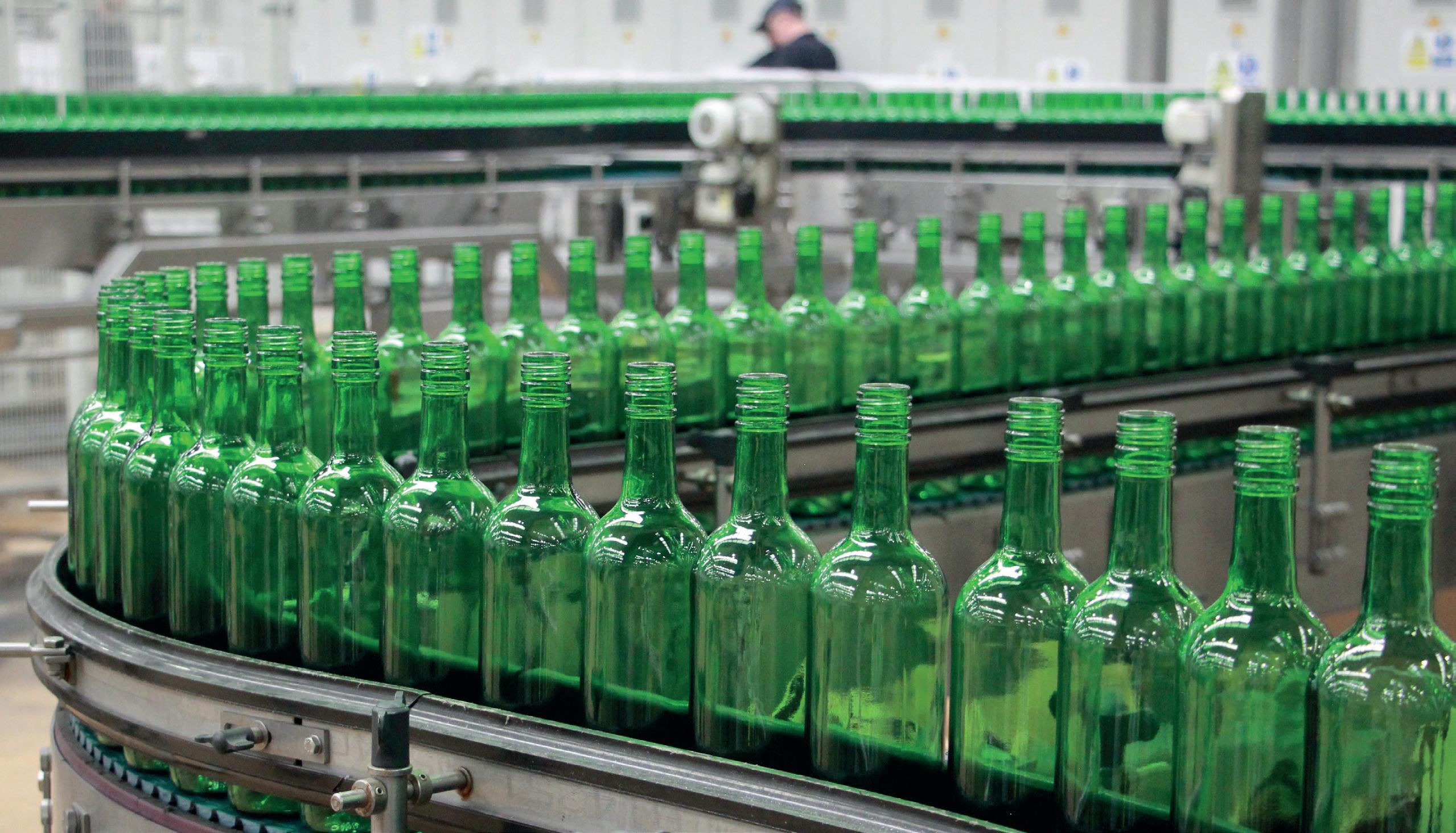
5 minute read
Digital glassmaking: Encirc
Smart bottling: Connecting the data with a digital thread
Stephen Haigh* examines predictions around increased digitalisation in glassmaking, and how data-driven initiatives may shape a new sustainable future for packaging.
All around the world, consumers are becoming more conscious about their own environmental impact and how their choices can significantly affect it. Glass has always had a competitive edge in the packaging sector due to its innate ability to be recycled easily and cost-effectively. Today, as we pair one of the oldest forms of packaging with cutting-edge industry 4.0 technology, we’re only now starting to realise its full potential.
Digitalisation is undoubtedly becoming one the most important developments in the world of glass making as we enter this new phase of the sector’s evolution. Capturing and making use of data provides an enormous amount of opportunity and could be used to offer clarity on each individual glass item’s lifespan – but we need to work out how to do this most effectively. Central to this will be understanding the true value all stakeholders can gain by using data from each stage of a container’s journey.
The current picture in glass technology
As a leading business in the technology sector, Siemens invests enormously in understanding where trends are heading. Predicting the market’s next move is a key part of our business strategy so we can develop innovations which are ahead of their time and help our customers grow.
There are a number of key shifts happening in the glass sector currently, which we see as having a major impact on the future of the industry. These include: � An increased use of digitalisation and automation in manufacturing, providing vast opportunities to further improve the glass production process
� Harnessing the power of data to connect workers, factories, customers and consumers
� Decarbonisation and the race to net zero, which continues to dominate conversation with new technological solutions coming to the fore all the time.
Collaboration is key to making sure we get the most out of these trends – and not simply one-to-one partnerships. It’s vital that industries group together to explore new possibilities, working with partners and suppliers to share knowledge and achieve our common goals.
The power of digitalisation
We know that digitalisation and the creation of ‘smart bottles’ will soon enable
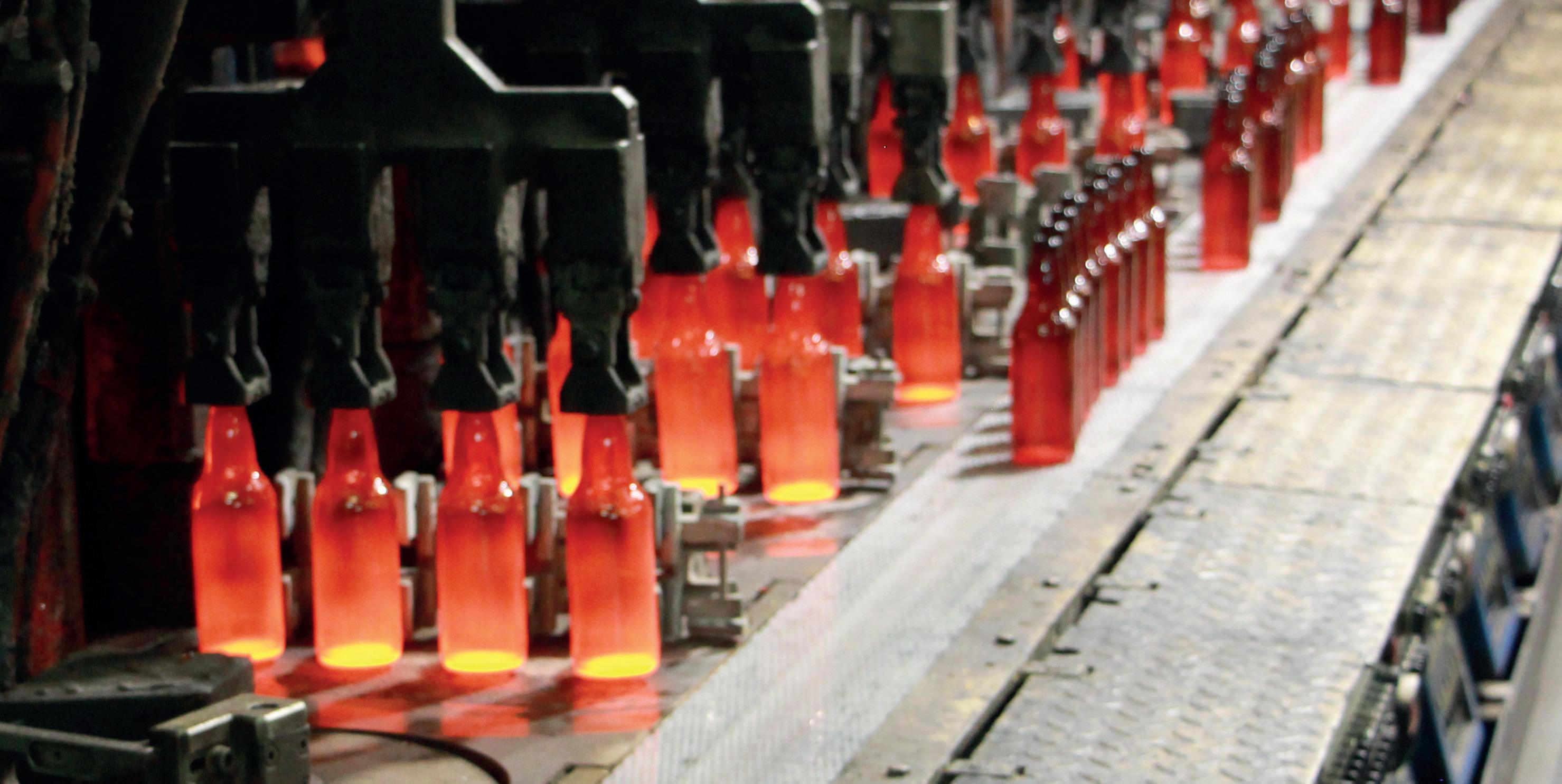
a product, and the materials that make it, to be tracked through technology like blockchain and digital twinning – from its raw materials right through to the end of its lifespan when it is recycled again. This transparency of the complete journey is imperative if we’re to better understand the individual product’s carbon impact.
Producing these smart bottles is the first half of the equation – the second concerns what we do with the data they produce. If the sector can create viable smart bottles which can harness the information involved in their lifecycle, we’ll be in a situation where we can create a unique data map for packaging.
This will allow us to see where the gaps in efficiency are, and where improvements are required throughout the supply chain to make glass bottles even more sustainable. Increased digitalisation across the board is crucial to the longterm success of glassmaking – helping the market become more efficient and more profitable while also being kinder to the environment, in a time when this is more important than ever.
Smart bottle production
As far as digital technology in production goes, at Siemens, we utilise virtual plant technology to allow our customers and partners to simulate their own plant environment and run virtual test lines before they commit to a realworld production. Everything from plant layout to material flow, processes, product design and implementation can be simulated in a virtual environment, allowing our customers to check and adapt their approach and accurately test their production capabilities without incurring huge costs associated with a real-life test run.
This use of this technology offers a number of benefits, such as flexibility, maintaining the real-world plant’s availability, health and safety benefits, cost savings and presenting the opportunity to optimise systems.
Digital technology at Encirc
The DEEP Control project at Encirc, a revolutionary digital project facilitated by Siemens, aims to reduce the company’s carbon emissions by more than 15,600 tonnes every year.
The new process control solution has digitally linked Encirc’s furnaces to its 14 production lines at its plant. The project will reduce the environmental impact of every bottle Encirc produces while providing further opportunities for digital-led efficiency across the business.
The DEEP Project makes use of the latest technology available with Siemen’s MindSphere platform and dashboard. MindSphere is a leading industrial Internet of Things (IoT) service solution which uses advanced analytics and AI, to collect, analyse, and share data between all parts of a system to optimise operations.
As part of the DEEP Control Project, the MindSphere platform can be used to create a digital twin of the plant. Using this, tests and experiments can be done to explore how different factors will affect the glass, furnaces and forming lines without needing to shut off or adapt the actual site.
The opportunity to test new adaptions and experiment without losing production or creating unknown end results will be incredibly beneficial when testing new fuels such as hydrogen or biofuel and when trialling new lightweighting methods.
The value of data
So, following the production stage, what could we do with the vast amounts of data that smart operations can produce? For manufacturers, drinks brands, retailers and so on, there’s a lot that can be gained from understanding more about a glass container’s lifespan.
For manufacturers, gaining access to more data can mean they can make better use of resources by connecting with recyclers and retailers, gaining deeper understanding into levels of sales, and the levels of recycled cullet in the market, where it is in the country, how close they are to receiving shipments, and then planning accordingly. For drinks brands, they can ensure their packaging is able to contribute to the circular economy with each bottle’s carbon footprint tracked and adjusted depending on its route throughout the market.
However, there is still work to be done around drilling down smart bottles’ ultimate value and usefulness to consumers, as opposed to businesses. The answer may lie in a digital deposit return scheme. Rewarding end consumers for glass bottles they recycle is likely to be the best way to close the loop and deliver truly smart bottles.
When we can track the raw materials in each bottle, the plant and furnace used to craft it, which customer bottled it, where it was sold, and then when it was recycled, we gain a full, accurate picture of the bottle’s lifecycle. And, when we have that virtually mapped out before us, we can really start to identify opportunities and make exciting changes in glassmaking for the future. Glass’s data-driven journey has only just begun, and the benefits look to be limitless. �
*Head of the Glass Sector, Siemens UK, https://new.siemens.com/global/en/ markets/glass-solar/glass-industry.html Encirc, Elton, UK www.encirc360.com