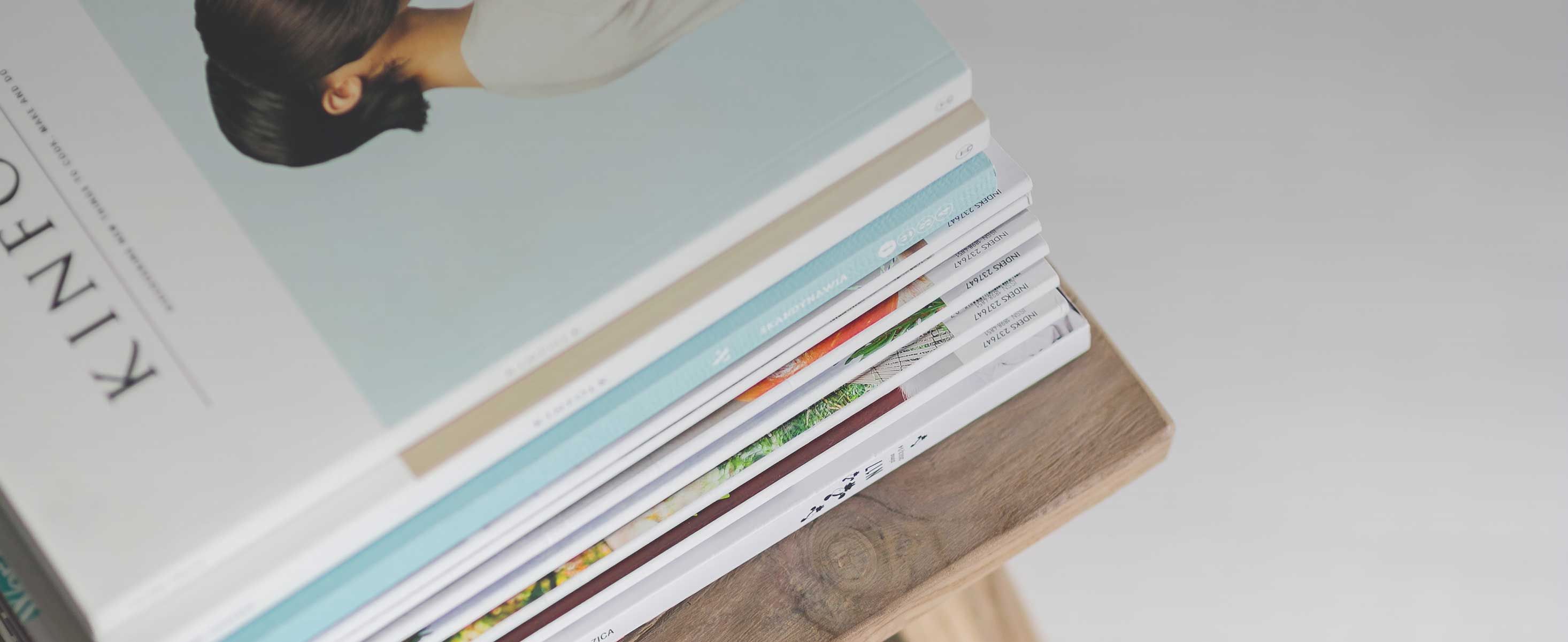
10 minute read
Decarbonisation: IEK
Decarbonising energy-related CO2 emissions in the glass industry
Michael Zier,(1,2) Noah Pflugradt,(1,2) Leander Kotzur,(1,2) and Detlef Stolten(1,2,3) discuss how hydrogen combustion and electric melting will emerge as the main energy supply options for the glass manufacturing industry.
Selective Batching
Pelletization
Recycling
Fluxing Agents Wood
Solid Hydrogen
Gas
Process Control
Submerged Combustion
Oxy-Fuel Firing
Process Intensification
Internal / external use
Gas
Waste Heat Recovery
Preheating
Decarbonization Options
Heat-toPower
Fuel
Electricity
Steam Turbine
TCR
Combustion Air Fuel Solids
Cullet & Batch Cullet TEG Synthetic Methane
Biogas
Submerged Electrodes
Microwaves
Plasma
Organic Rankine Cycle
� Fig 1. Energy-related decarbonisation options classified by efficiency measures and fuel switch. Efficiency measures are further categorized in terms of recycling, process intensification, and waste heat recovery (own classification) – TCR: thermo-chemical heat recovery; TEG: thermoelectric generator (adjusted from [2]).
To mitigate the natural disasters associated with anthropogenic climate change, cross-sectoral (energy, industry, buildings, mobility) greenhouse gas mitigation is essential.
Although historic specific CO2 emissions (tCO2/tglass) in industrialised countries have steadily decreased, the global absolute emissions of the glass industry increased by about 215% in the period from 1995 to 2015 [1] .
Therefore, the glass industry faces the challenge of profoundly decarbonising its production processes. Preserving product quality and process stability, as well as cost-competitiveness, is a prerequisite for this though.
Both energy and raw material prices, as well as their availability, will be crucial for decision-making and these must be evaluated in conjunction with the capital expenditures (CAPEX) of different corresponding melting furnace designs [2] .
As the larger portion of CO2 emissions is produced by generating the process heat needed to melt the glass, it is logical to first reduce these energy-related emissions. Fig 1 illustrates different energy-related decarbonisation options, which are classified in terms of fuel switch, process intensification, waste heat recovery, and recycling. The most significant options are discussed in the following and their ellipses presented in bold in Fig 1.
Switching the fuel to renewable energy carriers is by far the most important
Specific energy consumption (SEC) Lifetime CAPEX Footprint Load flexibility NOx emissions Other Regenerative end-port fired
o
o Regenerative side-port fired
o
+ Temp. profile + High capacity Oxy-Fuel
o
o
+ + Temp. profile + Glass quality + Stable flame - Oxygen price Electric melting
o
++ + No carry-over - Capacity - Cullet share -Not every glass
Table 1. Strengths and weaknesses of different glass furnace types (adjusted from [2]).�
option, as it will enable 100% abatement of energy-related CO2 emissions.
In the medium to long term, hydrogen combustion and electric melting will emerge as the main energy supply options, but their distribution is uncertain.
Alternative fuels such as biogas or biomethane will not be widely used, as their availability is limited and thus most likely steady prices cannot be assured.
Electric melting processes by plasma or microwaves are currently not applicable on an industrial scale due to their low technology readiness levels (TRLs). Because of additional efficiency losses and investment costs, synthetic methane will be more expensive than hydrogen [2] .
With respect to waste heat recovery, two main developments must be considered.
First, the share of electrical energy for melting will increase and thus usable waste heat in flue gases will decrease.
Second, the energy price level for fuels will rise as ever more greenhouse gas emissions from fossil fuels are priced globally. In addition, the marginal costs of renewable fuels are higher than those of fossil fuels, as additional processing stages such as electrolysis are necessary.
Consequently, heat recovery applications will be used in which hydrogen is burned as the main energy resource, resulting in usable amounts of exhaust gas and correspondingly usable waste heat.
The preheating of cullet (and batch) reduces fuel consumption by about 15%, but requires additional know-how in order to be operated successfully.
Among the different heat-to-power options, the organic rankine cycle (ORC) is considered the best in the glass industry, mainly due to it most likely having the lowest levelised cost of electricity (LCOE), superior reliability, and low maintenance.
Thermo-chemical heat recovery (TCR) combines oxy-fuel combustion with a heat recovery process. Natural gas is mixed with about 20% of the recirculated hot flue gas (mainly H2O and CO2) to reform the gas.
This produces a hot synthesis gas that mainly consists of hydrogen and carbon monoxide, increases the calorific value, and therefore improves specific energy consumption (SEC) by 30% (in comparison to an air-regenerative furnace). However, this option requires fossil natural gas, and is therefore not a sustainable long-term solution.
Among the process intensification options, oxy-fuel combustion and advanced process control systems will serve an important function. With the reduction of the nitrogen share for oxyfuel combustion, the gas flow through the furnace decreases, leading to an efficiency enhancement of approximately 10% compared to air regenerative furnaces.
Furthermore, oxygen may be used as an oxidator in combination with hydrogen, which will mostly be produced via water electrolysis. As oxygen is a byproduct of the electrolysis process, oxygen costs will probably decline. Advanced process control systems may slightly contribute to CO2 reduction, but are a necessary condition to compensate for fluctuating energy prices and availability, e.g., gas, hydrogen, or electrcity [2] .
The recycling of cullet, a low hanging fruit, accelerates the melting process, thus reducing specific energy consumption (SEC) as well as energy-related CO2 emissions. An increase of 10% recycled cullets improves energy efficiency by 2.5%. In addition, process-related emissions are reduced because cullet does not entail chemical reactions that emit CO2 [2]. For green glass, production with 100% cullet is possible.
However, cullet availability and cost with the appropriate quality requirements is an issue for every glass type [3] .
The summary indicates the future energy supply of a profoundly or fully decarbonised glass industry will be renewable electricity and hydrogen.
To further evaluate the probability distribution of future electricity and hydrogen in the glass industry, different criteria such as furnace type, TRL, or energy security are addressed in the following.
Table 1 summarises the strengths and weaknesses of different glass furnace types. Theoretically, hydrogen can be used in furnaces where natural gas or fuel oil is currently used, but design modifications, especially for burner systems, must be accounted for.
When comparing different melting furnaces using combustion technology, the oxy-fuel furnace performs better than regenerative furnaces in all areas (SEC, CAPEX, footprint, load flexibility, NOx emissions), except for service life.
Although oxy-fuel furnaces use different refractory materials than airregenerative furnaces, their lifetimes are shorter, mainly because of higher temperatures and higher water contents in the waste gas.
The decisive factor for or against oxygen–hydrogen furnaces will be the development of the oxygen price. The anticipated installation of large electrolyser capacities may also be a key development that will contribute to lower oxygen prices.
Thereby, the major argument against oxygen can be negated [2] .
Cold top all-electric furnaces (EM) use submerged electrodes and offer the most efficient energy transfer into the glass melt.
Due to a different process behaviour, a large number of operating conditions change.
Therefore, different characteristics, such as pull rate flexibility, a limited cullet share, or lower furnace lifetimes (strong
TRL Electricity
6-7
Hydrogen
5-6
Product quality and process stability
Eligible for many glass types Increased water content in the flue gas
Limited pull flexibility Ideally like natural gas
Energy security energy price volatility
Storage of large quantities not cost-efficient Short term availability depends on grid capacity Storage of large quantities cost-efficient Short term availability uncertain
Static switching between hydrogen / gas and electricity Dynamic switching between hydrogen and gas
Total cost of ownership
Depends (CAPEX, OPEX, lifetimes, energy prices, efficiencies, CO2 prices) GHG reduction Depends (electricity mix, PPAs, subcontracting, certificates of origin) High (only low CO2-intense hydrogen is reasonable)
� Table 2. The TRL, advantages, and disadvantages of hydrogen combustion and electric melting in the glass industry.
convection currents stress the walls of the furnace) must be considered. A limited capacity of approximately 250 tGlass/d may be overcome by means of modular approaches [2] .
Hybrids of EM and combustionbased technologies are used to smooth out the disadvantages of fuel-fired and electrically-heated furnaces.
Depending on the ratio of the energy sources introduced, one can speak of electric boosting (EB <= 20% electric energy share) or hybrid melters (HMs). In comparison to all-electric melting, the lifetime, cullet share, and pull, as well as material flexibility, may be increased by HMs [2] .
First, hybrid melting systems with pull rates of up to 400 tGlass/d and electrical energy shares of up to 80% are projected (FEVE – furnace of the future) and commercially-available [4] [5] .
The flexible switching of energy supply between fossil or renewable fuel and electricity is limited by the time required to achieve a sufficiently stable temperature distribution after a fuel switch, which can offer acceptable glass quality. This can take up to several days, posing a challenge to the practical implementation of flexible hybrid furnaces.
Table 2 displays the advantages and disadvantages clustered according to TRL, product quality, and process stability, energy security, as well as energy price volatility, cost-competitiveness, and the GHG reduction of hydrogen combustion and electric melting in the glass industry.
The TRL for electric melting is higher than for hydrogen combustion, as it is already applied in special glass applications with smaller capacities. However, all-electric melting in large-scale containers or flat glass furnaces is nonexistent. Recently, the TRL for hydrogen combustion has rapidly increased.
For instance, there has been the successful application of hydrogen combustion for container glass (air regenerative end-port fired furnace), flat glass (air regenerative side-port fired furnace), and speciality glass (oxy-fuel furnace) [6] [7]. Concerns regarding higher flame temperatures, different flame lengths, higher flame velocities, and a reduced heat transfer into the glass melt have not been confirmed.
From a product quality and process stability perspective, it is advantageous that in principle, many types of glass may be melted fully electrically.
Amber glass, for example, is problematic, as it tends to foam and thus the batch blanket cannot be kept stable.
To increase the electrical content for foaming glasses, a transition away from cold top design to hybrid designs is promising. Likewise, hybrid design allows for high melting capacities and increased pull rate flexibility while increasing the electric share. In hydrogen combustion, slightly increased fractions of water vapour are present in the exhaust gas for air combustion.
In oxy-fuel combustion, an atmosphere consisting only of water vapour and the gases emitted from the batch can be present. The increased water vapour concentration could negatively influence the service life of the refractory materials or may even lead to water inclusions in the glass melt and therefore to quality problems [2] .
With regard to supply safety, at the energy quantities required by the glass industry, hydrogen storage is less expensive, although the CAPEX of batteries has dropped dramatically in recent years [8]. However, the short-term availability of green hydrogen remains unclear. Provided that burner systems, fuel, and oxidizer feed lines, as well as the necessary control technology are adapted, the composition of the fuel (eg natural gas or hydrogen) and oxidiser (eg air or oxygen) can be varied.
This advantage is immense, as an existing melting furnace design could be maintained and, at the same time, the energy supply could be varied depending on different external conditions, such as the energy prices of natural gas and hydrogen, the CO2 price, and political regulations (Table 2).
With respect to the total cost of ownership (TCO), slight advantages are on the side of the electrical energy supply.
Although the trend points away from the cold top design and thus larger CAPEX are to be anticipated, this also means that longer lifetimes can be expected while maintaining the better efficiency levels.
In addition, electricity will be the most economical energy type during periods when renewables are producing electricity (the global expansion of photovoltaic and wind power plants will continue to grow exponentially, as these are already the lowest-cost alternatives for electricity generation and their cost reductions will continue).
In times when there is a shortage of renewable energy, it is conceivable hydrogen will be cheaper than electricity.
Long term, global electricity production will be based on renewable energy sources. Until then, the greenhouse gas emissions of companies highly depends on the composition of the electricity mix in the local electricity market.
Possible ways to decouple from the electricity mix include power purchase agreements (PPAs), in-house electricity production, or certificates of origin that reduce the CO2 emissions in the balance sheet of a company.
Due to its favourable storage properties, hydrogen offers the possibility of decoupling from local markets in terms of time and place.