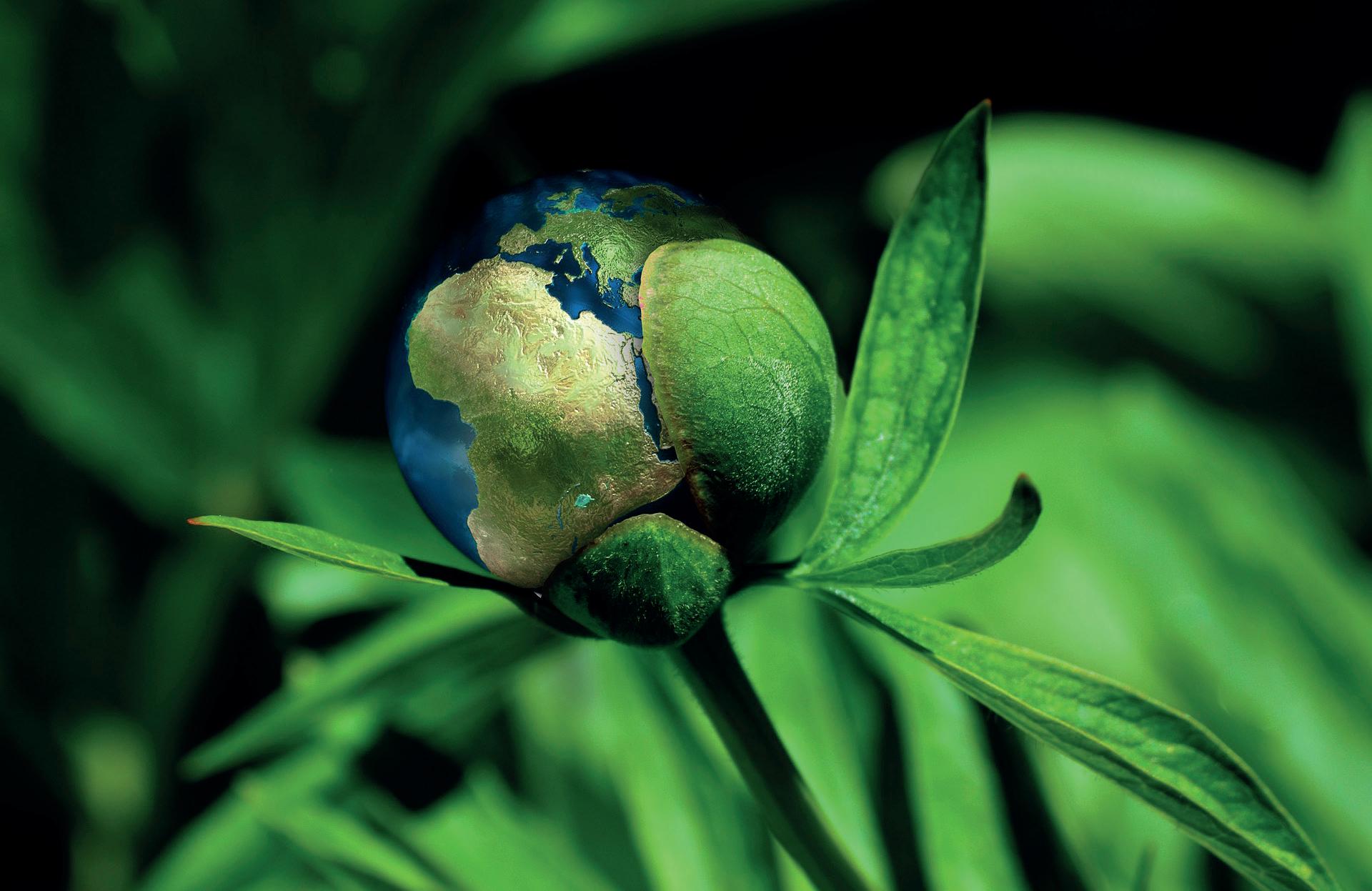
7 minute read
Decarbonisation: Celsian
The best vision is insights
Rene Meuleman* describes some of the alternative fuels for glassmaking and states any move away from fossil fuels will require a change in mindset as well as technology.
Glasgow made it very clear again; the way we manufacture glass will have to change to become carbon neutral and we have less than 30 years to do so. There is no doubt glass manufacturing is an energy intensive industry and being forced to move away from using fossil fuel will need both a change of technology and, most probably a different mindset.
Since the introduction of the regenerative furnaces, the glass industry came a long way achieving, year after year, the highest energy efficiency improvement figures among energy
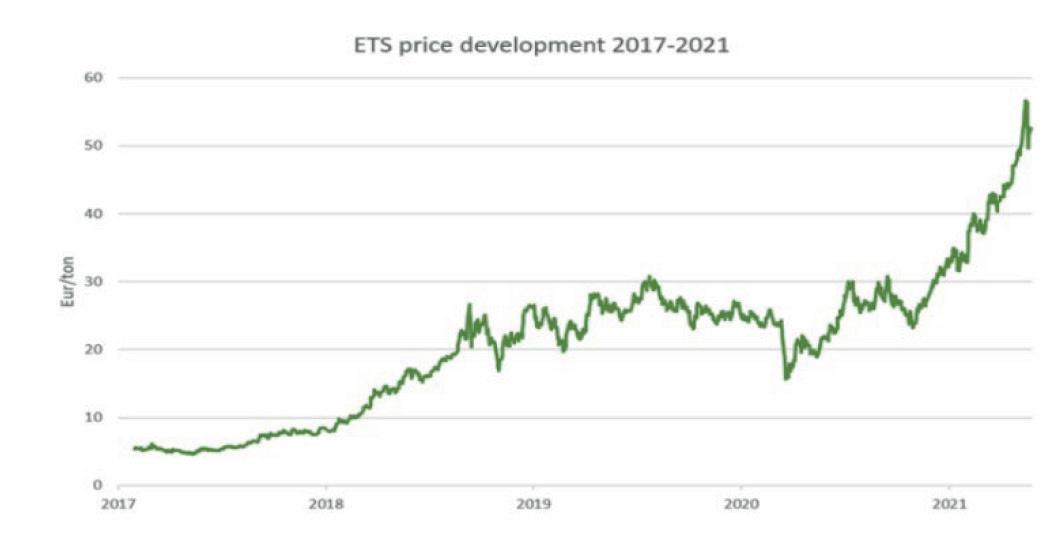
� ETS Price development intensive industries.
Unfortunately, the efficiency improvement of traditional fossil fuel fired furnaces came almost to a standstill around 2000. Does that tell us this technology has been pushed to its energy efficiency limits? Not yet, but it is close to these limits and new melting technologies and the use of renewable energy needs to be considered.
Many new glass furnace designs will emerge, but, before we even dive into what the furnace of the future should look like, we need to answer some other important questions: “What type of renewable energy will become sufficiently available, is it suitable for our processes, will it be energy efficient enough, will it be available at a commercially acceptable price and at the locations where glass manufacturing sites are found?”
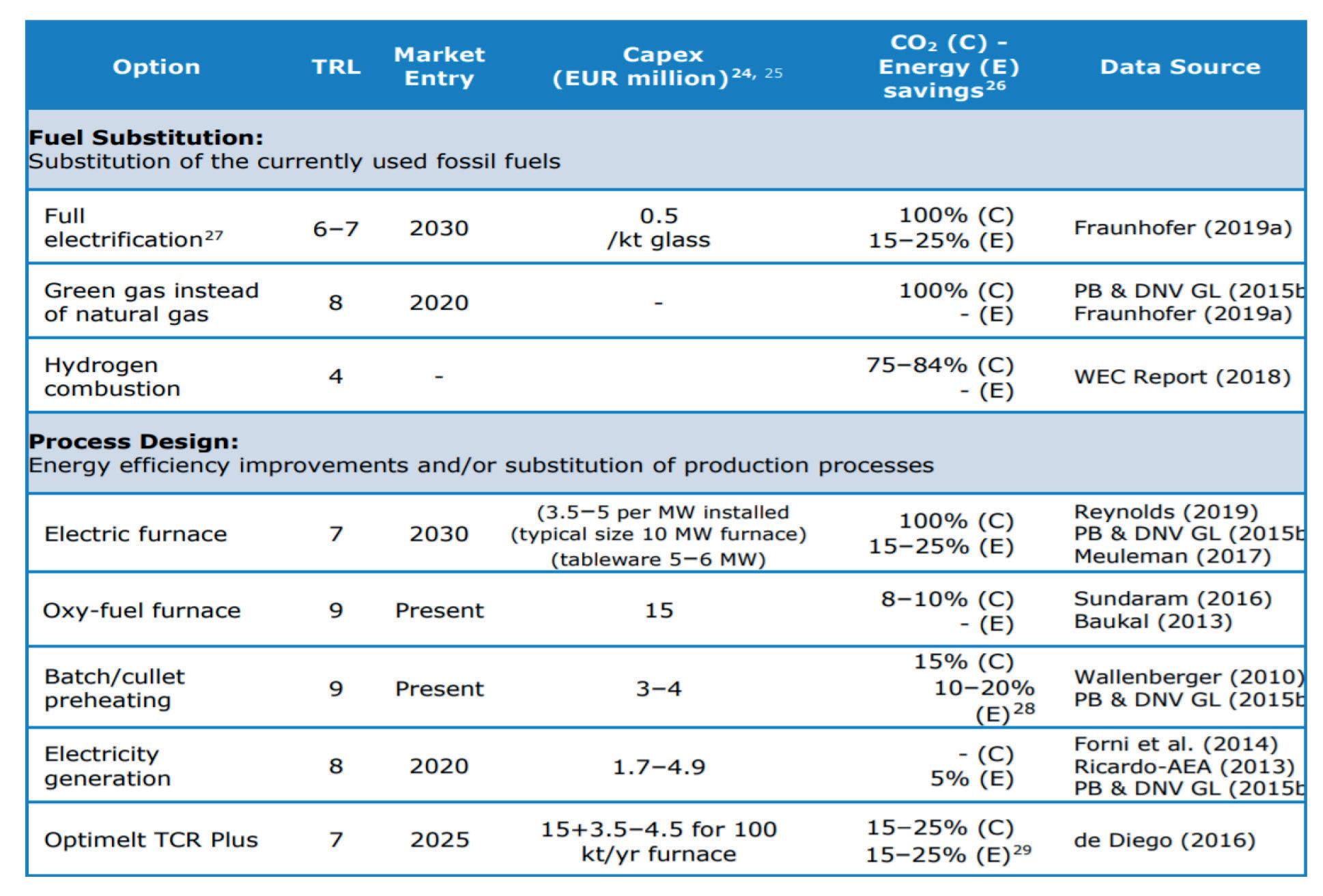
sufficiently. What will happen is it will be used by those who cannot do without it to become green like steel, chemical and cement as well as automotive industries.
Glass industry will use hydrogen only as a heat source, being extremely energy inefficient, while steel for example needs it as a reactant and a heat source in much larger quantities.
From that perspective, it is questionable if hydrogen will become available for the glass industry at an acceptable price level.
Keep in mind that electrical energy in a glass furnace is twice as energy efficient compared to hydrogen combustion and both will finally come from the same renewable energy source which is green electrical power!
Electrical energy
Table 1. The TRL (technology readiness level) of the use of hydrogen in glass applications is low but
� will likely increase due to multiple R&D studies.
Infrastructure
Most of today’s glass manufacturing sites, specifically container glass plants, are not located in recently established industrial areas. Therefore, the majority will not have the renewable energy infrastructure on-site or even close by.
Sufficient on-site electrical power will be limited and hydrogen together with sufficient oxygen supply will, most probably, not be existing.
Bringing in the amount of electrical power and/or hydrogen and oxygen will need investment and could be extremely time consuming.
Hydrogen
Firstly let’s have a look at the definition of green hydrogen: green hydrogen is produced by splitting water using green electricity. 1kg of hydrogen contains 33.33kWh of usable energy.
In 2015 the price of hydrogen was around $0.18/kWh in 2015 but is expected to come down to $0.06/kWh by 2025.
Fuelled by the hydrogen lobby, the glass world is also increasingly talking about the use of hydrogen in their melters.
Recently, a lot of research projects, among them a GlassTrend project, were dedicated to finding out if hydrogen could be used in a traditional oxy-fuel furnace.
It seems, from a combustion process and heat transfer point of view, that hydrogen will work. Next steps will focus on what impact a combustion space filled with water vapour will have on the melting process, foaming, glass quality and refractory wear.
Therefore the TRL (technology readiness level) of the use of hydrogen in glass applications is still relatively low but likely that will go up due to multiple R&D studies, not only those by GlassTrend.
Hydrogen availability
We are far from the point on which green hydrogen will be sufficiently available for the whole industry .
Today, unfortunately 98% of hydrogen comes from natural gas. It should be clear as long as that is the case natural gas should be used instead of hydrogen.
As soon as green hydrogen becomes available it will start to become interesting but again, we are far away from that.
But let’s be positive assuming it will become available soon and, more or less The use of electrical power in the glass melting process is far more energy efficient compared to any combustion process, including hydrogen firing.
It also comes with a minimum of NOx, SOx and of course CO2 emissions.
The burning of hydrogen, which has been produced by using green electrical power in the first place, in an oxyhydrogen furnace will reach an energy efficiency of 45%, while the energy efficiency of electrical power is around 85%. However, there are some negative points that need to be considered.
First of all, the amount of electrical power that can be fed into an existing furnace is limited.
Drilling holes in the bottom of an existing, older furnace is a very risky operation even considering that modelling studies showed that 20-25% of electrical power can be installed into a traditional furnace design before convection current disturbances will lead to glass defects.
Having that said, increasing the
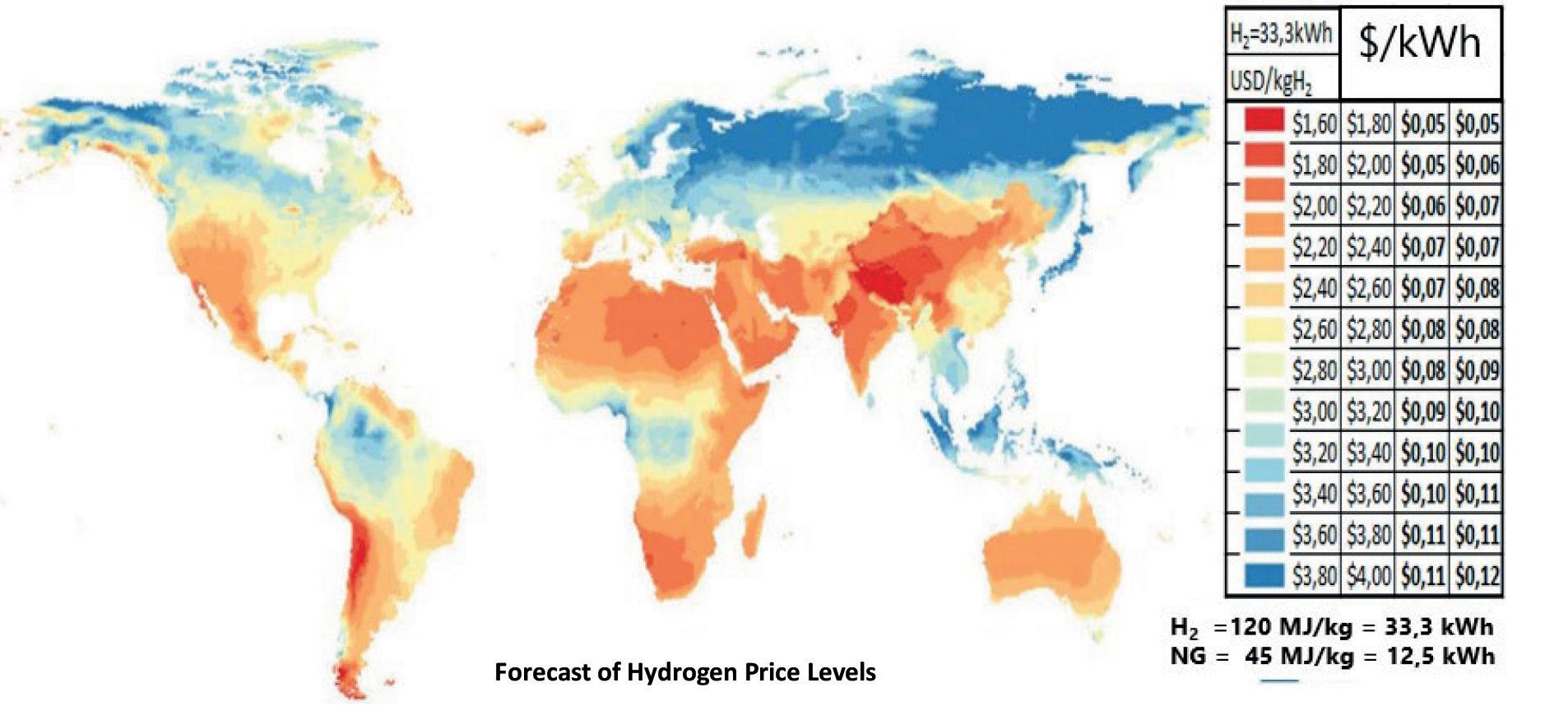
amount of electrical melting power during a furnace repair should still be considered, but modelling studies should be used to find the optimum position of electrodes.
In cases in which >60% of electrical melting energy will be installed, regenerators will become worthless and a switch towards oxy-fuel need to be considered.
In other words, if more electrical power needs to be installed new furnace designs will need to be considered and it is, in our opinion, questionable if those design will have a similar footprint compared to the furnaces we use today, specifically if such a design needs to cope with all the desired flexibility of colour, pull-rate and cullet percentages.
There is a negative correlation between flexibility, furnace size and energy efficiency. In other words: there will be no ‘one size fits all’ carbon neutral furnace design.
Where to start?
The decarbonisation of the glass industry to meet the Paris Climate Agreement is a major challenge and can be divided into three main subjects:
� What types of renewable energy sources will become available and when will they be available at my site(s)? � Which impact will they have on CapEx and OpEx? � What are the available technical solutions to use them?
Answering these questions can be compared to the chicken – egg problem. Why would we need to investigate the technical solutions to use a specific renewable energy source if we know upfront that it will not become sufficiently available and will most likely be too expensive. Or if we do not know that a specific energy source will work out in our specific glass making process why would even wait for it?
Discussing this internally we concluded that we are looking at a multi-dimensional question matrix that needs to be solved for almost each and every different situation. It’s even more complex because the solution needs to cover the decarbonisation strategy for next 30 years. We face a mix of crisp technical challenges, commercial considerations, local situations, and a sense of looking into a blurred crystal ball.
Finding synergies
In order to lower successfully and finally minimise your carbon footprint it will be likely you will need to start looking at synergies with others. What can be used from others and what can be shared with others? Waste heat, energy flexibility to stabilise the grid, waste becoming raw materials, etc are important subjects.
At CelSian, together with our partners, we contribute to untangle these complex questions for 30 years and together we will rule out as many question marks as possible, take care of the risk assessment, find the synergies with others, and provide the best strategy for your future licence to operate and to stay in business in the most profitable way. �
References:
https://www.pbl.nl/en/publications/ decarbonisation-options-for-the-dutchcontainer-and-tableware-glass-industry
https://www.iea.org/reports/the-future-ofhydrogen
*Business Development Director, CelSian, Eindhoven, The Netherlands www.celsian.nl
Glass experts
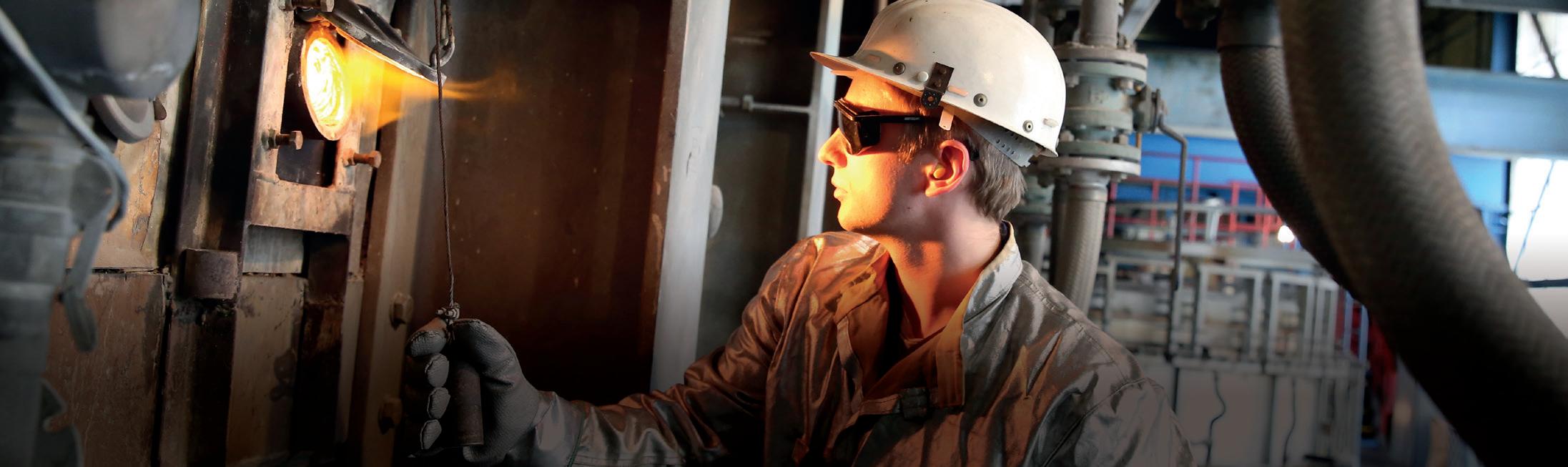
Furnace support Process optimization Training and R&D
Celsian’s aim is to minimize the cost of making glass for end users and the environment. We have an agile team of glass experts using proven methods like furnace modelling, laboratory measurements and practical furnace health checks to optimize glass melting processes. We also train operators and glass technologists through our standard course, dedicated programs and various e-learning modules. We strive to be the best partner for optimization of glass production worldwide.