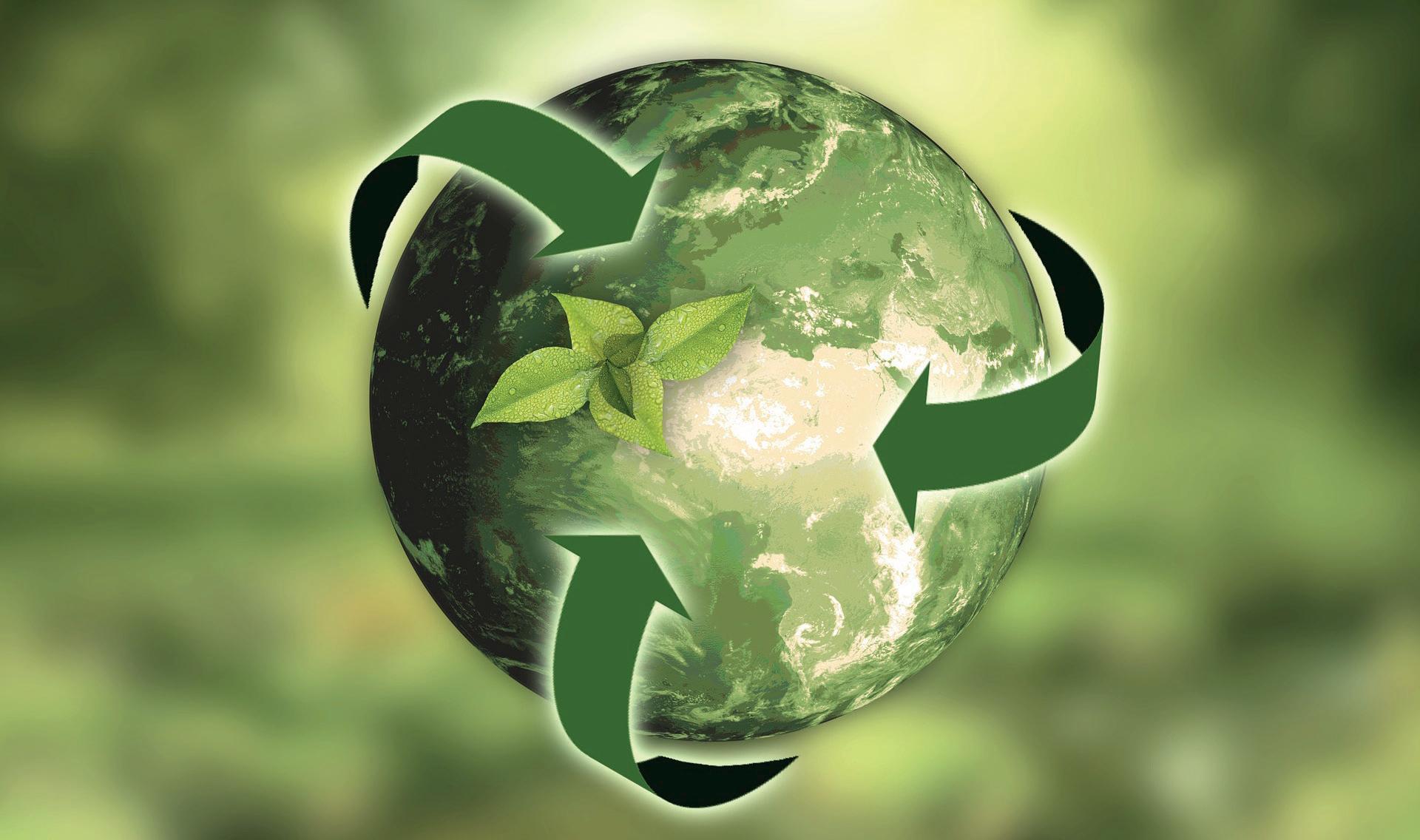
9 minute read
Decarbonisation: BV Glas
Decarbonisation in the glass industry
Johann Overath* discusses the German glass industry’s decarbonisation options and how it will meet the Federal Government’s plan to reduce all emissions by 2045.
Glass is a material indispensable in modern society and is used everywhere: as packaging for food, beverages and medical vaccination vials, as energy-efficient high-performance glazing, as reinforcing glass fibres in wind turbines, as fibre optic cables for the digital infrastructure and as special glass for the semi-conductor industry.
Only with the help of glass products decarbonisation and the transformation to a climate-neutral world will succeed. Nevertheless, the glass industry must also decarbonise or defossilise its processes. The European Union has decided to achieve climate neutrality by the year 2050. In Germany, the goals are even more ambitious. As a result of a ruling by the Federal Constitutional Court, the German government has decided to reduce all greenhouse gas emissions to zero as early as 2045. This means national emission reductions, not compensation through projects in other countries, such as Joint Implementation or Clean Development Mechanism. Therefore, greenhouse gas emissions from glass production must also be reduced to zero.
The glass industry’s production processes are highly optimised in order to be able to manufacture products of high quality and efficiency with low pollutant emissions. In view of climate targets, but also customer and societal demand, the glass industry is working hard to decarbonise its energy-intensive manufacturing steps.
Melting glass requires process temperatures of up to 1,650°C (comparable to the temperatures in oxygen steel production). The glass industry is thus one of the most energy-intensive industries. The production of glass in Germany uses about 13.5 TWh of natural gas and about 4.0 TWh of electricity. This means that the glass industry covers about 75% of its energy needs with natural gas, which corresponds to about 2% of national German gas consumption.
Direct CO2 emissions amount to about 4.9 million tonnes, of which about 4 million tonnes are emitted from plants subject to emissions trading. About a quarter of these CO2 emissions, about 1 million t, are process-related and come from the thermal decomposition of the carbonate raw materials (similar to the lime and cement industries). In principle, these cannot be reduced by switching to renewable energy sources, be it electricity or CO2-neutral fuels.
The glass industry is therefore facing enormous challenges. Energy savings in the glass melting process are only possible to a small extent, because the specific energy con-sumption today is close to the physical / technical minimum.
Energy efficiency
The Federal Association of the German Glass Industry (BV Glas) represents the economic, environmental and climate policy interests of the glass industry in Germany. It has been working hard to improve energy efficiency in the glass industry since the early 1990s and has communicated the results transparently to politicians and the public. For example, BV Glas, on behalf of the entire glass industry in Germany, has committed itself to reducing specific CO2 emissions by at least 20% by 2012 compared to 1990 as part of the German industry’s climate agreement with the federal government. This target was reviewed by an independent institute every year and the targets were always met. In 2012, a reduction of as much as 24.8% CO2 per tonne of saleable glass was achieved compared to 1990. Furthermore, BV Glas has accompanied the introduction of
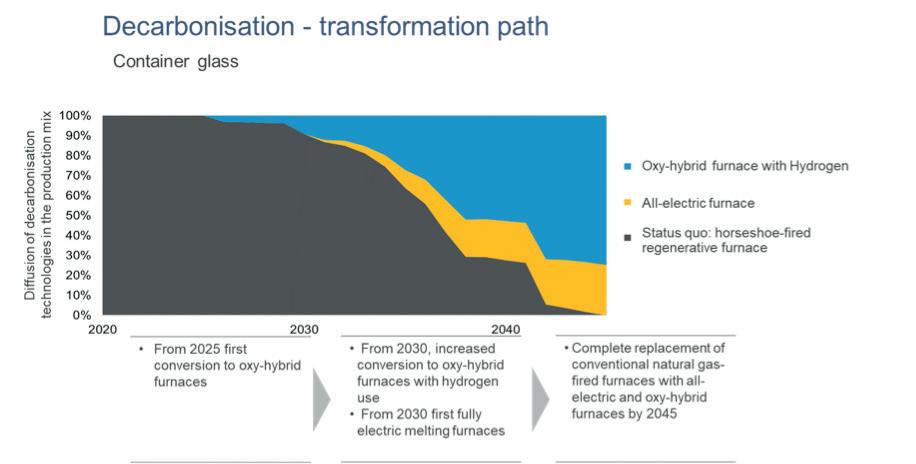
� Fig 1. German glass container industry’s assumed decarbonisation transformation path.
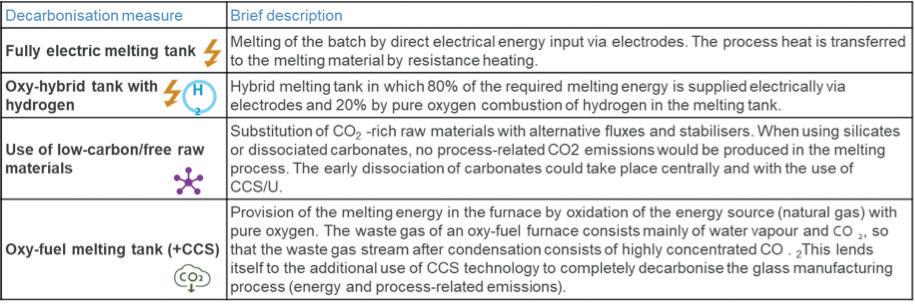
� Table 1 Decarbonisation - Technologies.
energy management systems according to ISO 50.001 in the glass industry. Almost all non-SME member companies are certified according to ISO 50.001. BV Glas represents the glass industry in several governmental and non-governmental energy and climate studies and projects. These include: � Study by the Federal Ministry of Economics and Technology (BMWi) “Ener-giewende in der Industrie” (Calculation of climate pathways, measures and costs) � dena - (German Energy Agency). Promotion of lighthouse projects for CO2 reduc-tion in the glass industry � BV Glas is one of the founding members of the Energy Efficiency Networks Initiative of the German government and industry. In the meantime, it has established five energy efficiency networks. Among them GlasNET2.0, which received an award from the BMU and BMWi. � IN4Climate.NRW: Initiative of the Ministry of Economics of the State of North Rhine-Westphalia. The aim is to help shape the transition to a climateneutral in-dustrial sector. � KEI - Competence Centre for Energy-Intensive Industries in Cottbus, participation in the Advisory Board
� RE4iNDUSTRY - European project. Use of renewable energies in the glass industry � HyGlass project with the Gas and Heat Institute, GWI, to investigate the effects of higher hydrogen concentrations in natural gas, but also of pure hydrogen, on combustion processes in glass production.
Energy savings in the glass melting process are only possible to a small extent, as energy consumption today is close to the theoretical energy requirement.
Transformation pathways
Climate neutrality can therefore only be achieved by substituting conventional energy sources with renewable energy sources. The remaining process-related emissions must be reduced via CCS (Carbon Capture & Storage), CCU (Carbon Capture & Utilisation) or by using greenhouse gas-neutral raw materials.
In principle, decarbonisation technologies include the all-electric furnace, the hybrid furnace with hydrogen or other greenhouse gas-neutral fuels, whereby these can be designed as oxygen/fuel or air/fuel heated.
These technologies are not yet available
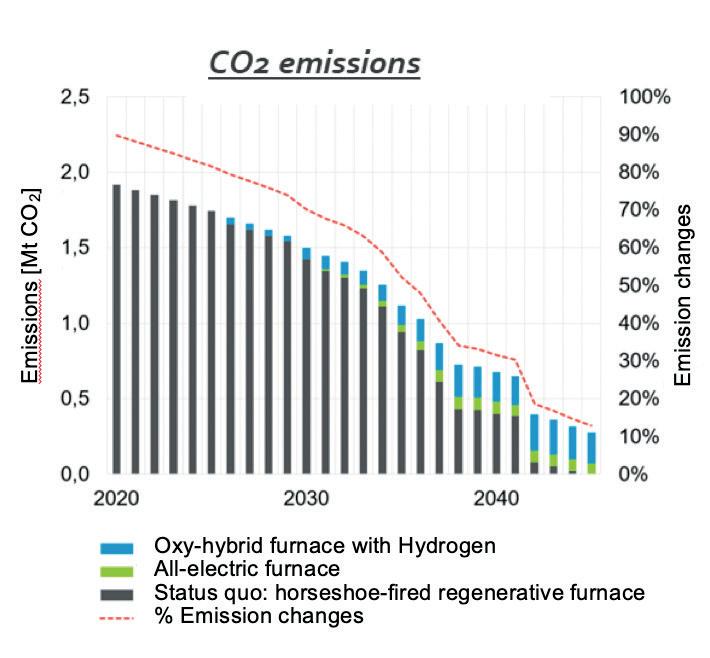
� Fig 2. Resulting reduction in CO2 emissions as a result of the transformation path.
in the required plant size or are still being developed or tested. It should also be borne in mind that not all types of glass can be electrically melted for purely physical reasons.
Furthermore, the size of electric melting furnaces is limited for physical/ technical reasons, so that plants such as those common in the flat glass industry cannot be fully electrified. The use of hydrogen seems inevitable for the glass industry, along with the possible use of synthetic methane or biogases.
Another technology that could be considered - especially for a transitional period - is the already proven oxy-fuel technology with conventional natural gas and subsequent CO2 capture as CCS or CCU. However, CCS is currently controversial in Germany and politically unenforceable, as large parts of the population reject it. Therefore, CCU seems to be the better option in Germany. Furthermore, the use of natural gas is also viewed critically, as the European discussion on taxonomy shows.
This article presents the first results of the study Energy transition in industry by the Federal Ministry of Economics for the container glass and flat glass industry in Germany (calculation of climate pathways, measures and costs). The decarbonisation technologies considered are shown in table 1.
It is assumed that the technologies mentioned will be available on a large scale in the future. Fig 1 shows the assumed decarbonisation transformation path for the container glass industry.
Simplified, the status quo of the container glass industry in Germany is assumed with 100% regenerative horseshoe-fired furnaces or cross-fired furnaces. Although smaller all-electric or oxy-fuel furnaces already exist in the
container glass industry, they are not included for simplicity.
In this decarbonisation scenario, the first conversion to oxy-hybrid furnaces will take place from 2025, which will then be increasingly used from 2030.
Likewise, the first fully electric furnaces will be used from 2030. Around 2040, the last 25-30% of the remaining horse-shoefired furnaces will be replaced by the two technologies in this scenario. The plant mix in 2045 is assumed to be around 70% oxy-hybrid furnaces with hydrogen and around 30% fully electric furnaces.
The path for the resulting CO2 reductions is shown in fig 2.
The graphic shows that CO2 emissions decrease slightly until 2025 due to the higher share of renewable energies in the electricity mix and then moderately after the installation of the first oxy-hybrid furnaces. With the increasing use of electric and oxy-hybrid furnaces, the CO2 emissions drop rapidly until in 2045 only the processrelated emissions remain at 15%.
Assuming that the technologies mentioned are available, the study concludes that climate neutrality would be achievable for the container and flat glass industry in 2045, but would lead to a large increase in production costs.
Production costs in the container glass industry would increase by just under 45% and in the flat glass industry by just under 70% by 2045. This does not yet take into account the decarbonisation of process-related emissions. Since these enormous in-creases in production costs would lead to a loss of competitiveness, the study recom-mends the following policy instruments, which BV Glas also raises as demands on politicians: � Compensation mechanisms: Subsidies to compensate for the additional costs of decarbonisation, e.g. through Carbon Contracts for Difference (CCfD/CfD). � Energy system: Provision of ‘green’ energy at internationally competitive prices � Infrastructure: Expansion of the electricity and gas grids (hydrogen) to ensure a nationwide supply of green energy sources and a high level of supply security.
In principle, the result is not surprising. In its Climate Path Study 2.0, the Federation of German Industries (BDI) also comes to the conclusion that climate neutrality is not availa-ble for free. Enormous investments and efforts are required. The new German govern-ment has recognised this and has combined the topics of economy and climate protection in one ministry.
The next few months will show whether the new government will tackle the transformation in an effective way for industry and implement the necessary regulatory framework.
Despite the enormous challenges, we are convinced that there are also great opportunities for the glass industry, because the glass industry supplies many highly developed products for climate protection and future energy supply.
Furthermore, glass is very resourceefficient due to its unlimited recyclability. This is another advantage for upcoming resource efficiency programmes and last but not least, glass has good prerequisites for food safety and medical applications because of its material properties, as the international COVID19 vaccination campaigns impressively show. �
*Director General, BV Glas, Dusseldorf, Germany www.bvglas.de
Continued<< 46
The previously mentioned open question concerns when low-CO2 hydrogen will be available at a reasonable price.
Finally, the interplay of the outlined decision factors regarding TRLs, product quality, and process stability, energy security, TCO, and greenhouse gas emissions will, together with the aspects of in-house technology know-how and political framework conditions, determine each individual case if hydrogen or electricity are to be the predominant energy resources in the glass industry. �
References
[1] E. G. Hertwich, „Increased carbon footprint of materials production driven by rise in investments“, Nat. Geosci., Bd. 14, Nr. 3, S. 151–155, März 2021, doi: 10.1038/s41561-021-00690-8. [2] M. Zier, P. Stenzel, L. Kotzur, und D. Stolten, „A review of decarbonization options for the glass industry“, Energy Convers. Manag. X, Bd. 10, S. 100083, Juni 2021, doi: 10.1016/j.ecmx.2021.100083. [3] „Jahresbericht des BV Glas 2018“. https://www.bvglas.de/media/BV_Glas/ Jahresbericht_2018.pdf (zugegriffen Okt. 21, 2020). [4] „The Furnace for the Future“, FEVE. https://feve.org/about-glass/furnace-forthe-future/ (zugegriffen Dez. 07, 2021). [5] „Sorg launches hybrid furnace for high tonnage glass manufacturing“, Glass International. https://www.glassinternational.com/news/sorg-launcheshybrid-furnace-for-high-tonnage-glassmanufacturing (zugegriffen Dez. 24, 2020). [6] „Architectural Glass Production Powered by Hydrogen in World First“. https://www.nsg.com/en/media/ ir-updates/announcements-2021/agproduction-powered-by-hydrogen (zugegriffen Dez. 07, 2021). [7] „Kopernikus-Projekte: P2X: Glasherstellung mit Grünem Wasserstoff erfolgreich getestet“. https://www. kopernikus-projekte.de/aktuelles/ news/glasherstellung_mit_guenem_ wasserstoff_erstmalig_erfolgreich_ getestet (zugegriffen Dez. 07, 2021). [8] J. Figgener u. a., „The development of stationary battery storage systems in Germany – status 2020“, J. Energy Storage, Bd. 33, S. 101982, Jan. 2021, doi: 10.1016/j. est.2020.101982.
Contact (1) Institute of Techno-economic Systems Analysis (IEK-3), Forschungszentrum Jülich, Germany (2) Jülich-Aachen Research Alliance, JARA-Energy, Jülich, Aachen, Germany (3)Chair for Fuel Cells, RWTH Aachen University, c/o Institute of Techno-economic Systems Analysis (IEK-3), Forschungszentrum Jülich, Germany