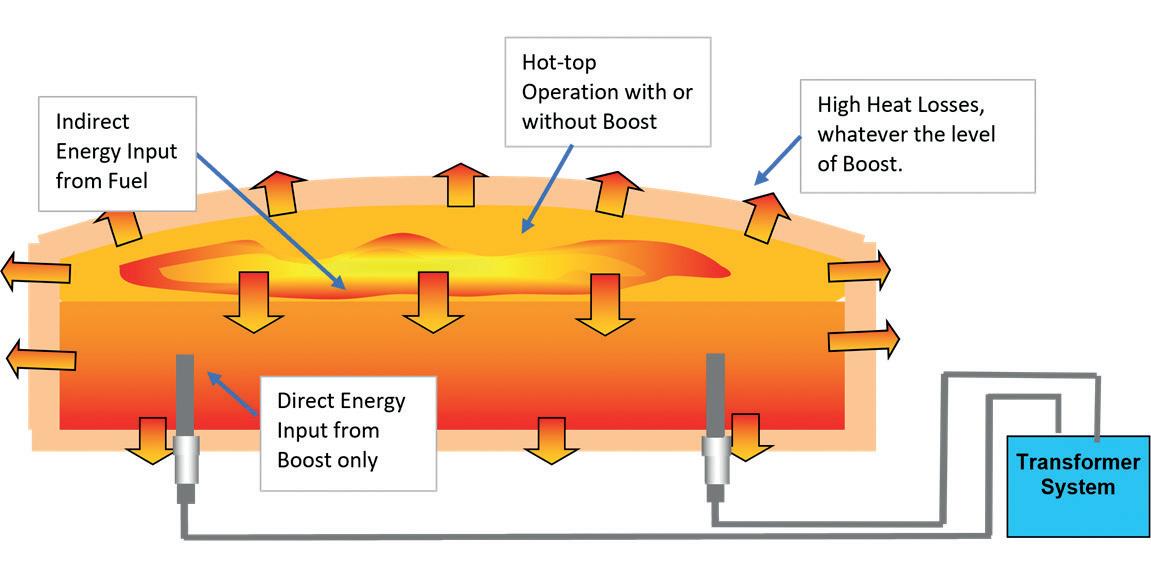
8 minute read
Renewable glass manufacturing Electroglass
Renewable Melting and Conditioning Technology
Richard Stormont* outlines how Electroglass furnaces can meet renewable energy targets by improving energy efficiency, reducing emissions and using a hybrid energy approach.
Glass melting is an energy intensive process. To convert mixed raw materials into melted and refined container glass requires a net energy input of about 2.4 GJ per tonne of glass, with no allowance for the thermal efficiency of the process used. In other words, no allowance for the inevitable heat losses.
Melting recycled glass or cullet requires less energy, around 1.7 GJ per tonne or about 30% less than melting pure batch. Again, this takes no account of process heat losses. It is also difficult to meet today’s glass quality expectations using only cullet, meaning that very few products are made with purely recycled glass.
It is possible to reduce the net melting energy requirements of our glass products. We can to some extent adjust compositions and the raw materials used to slightly lower the melting and refining temperatures required. We can use more cullet, perhaps accepting less than perfect product colour or consistency of colour. Both these approaches, raw materials adjustments and cullet use, can help towards the key objectives of reducing energy consumption, and conserving scarce raw materials resources.
However, in terms of reducing energy consumption, far more can be achieved by focusing on the heat losses in melting processes. In the large majority of fuelfired furnaces, that produce most of the world’s glass, those losses are greater than the net melting energy required by the glass. In other words, the thermal efficiency of the process is less than 50% and in most cases far less. Even if a fuel-fired furnace is capable of operating at a peak thermal efficiency of around 50%, that figure reduces greatly as soon
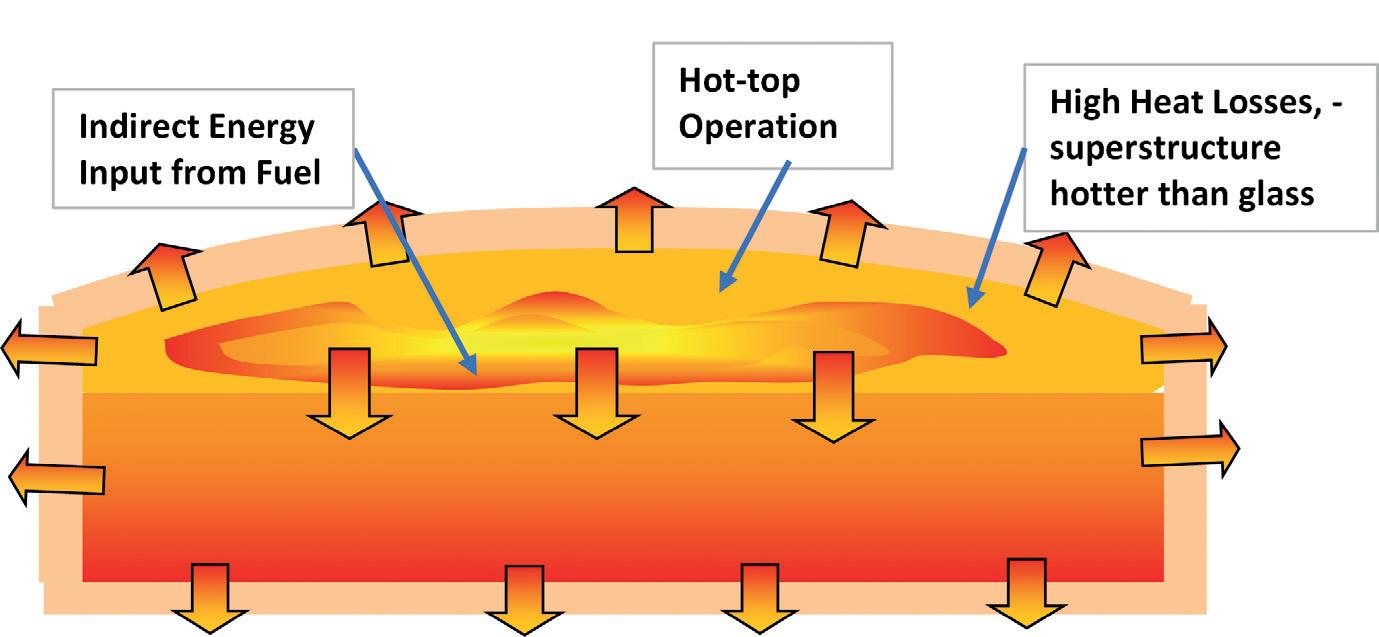
� Fig 1.The Fuel-Fired Furnace – high heat losses, low thermal efficiency.
� Fig 2. Primary sources of energy.
� Fig 3.The Booster or Hybrid option.
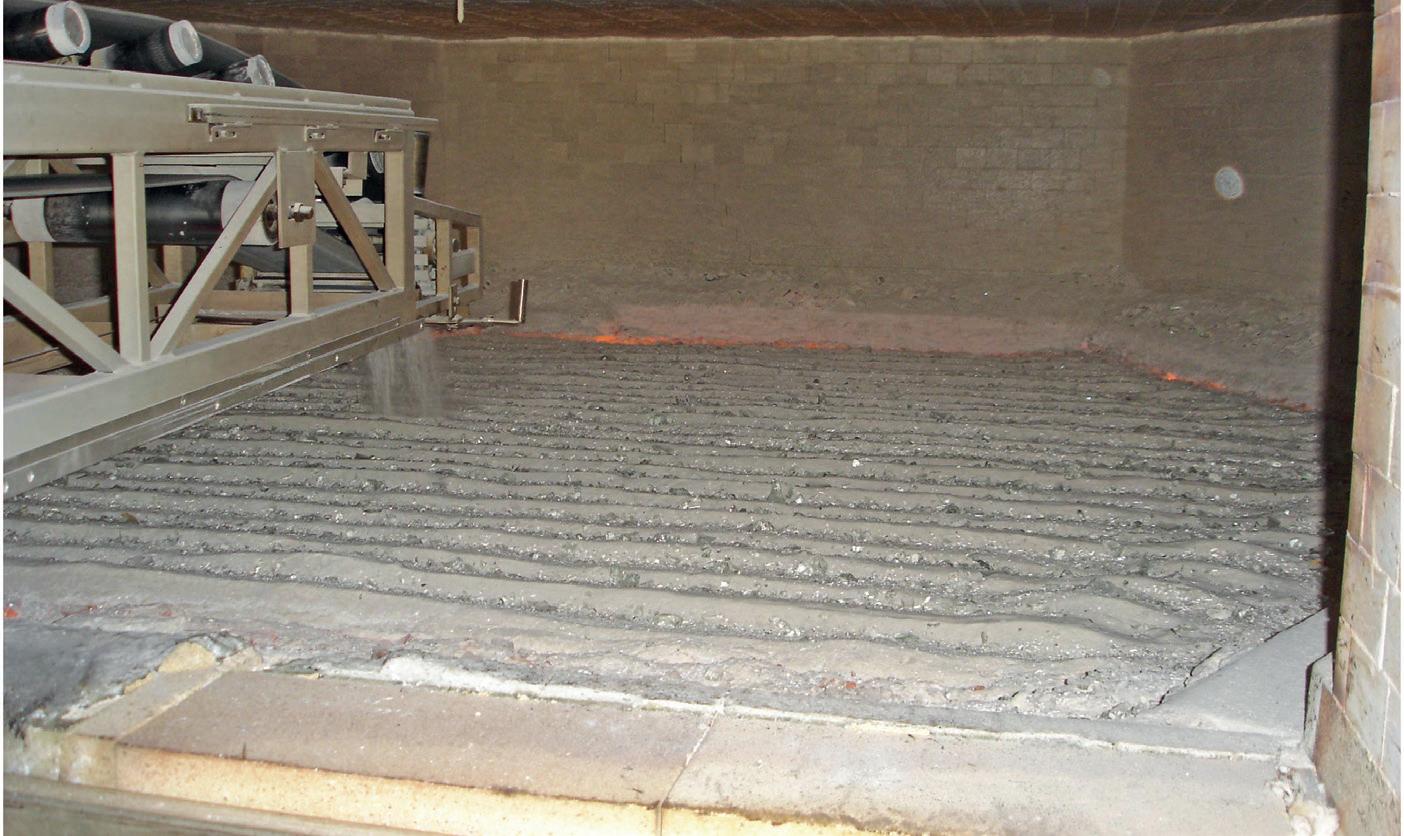
Fig 4.The insulating Batch Blanket of an Electroglass All-Electric Furnace.�
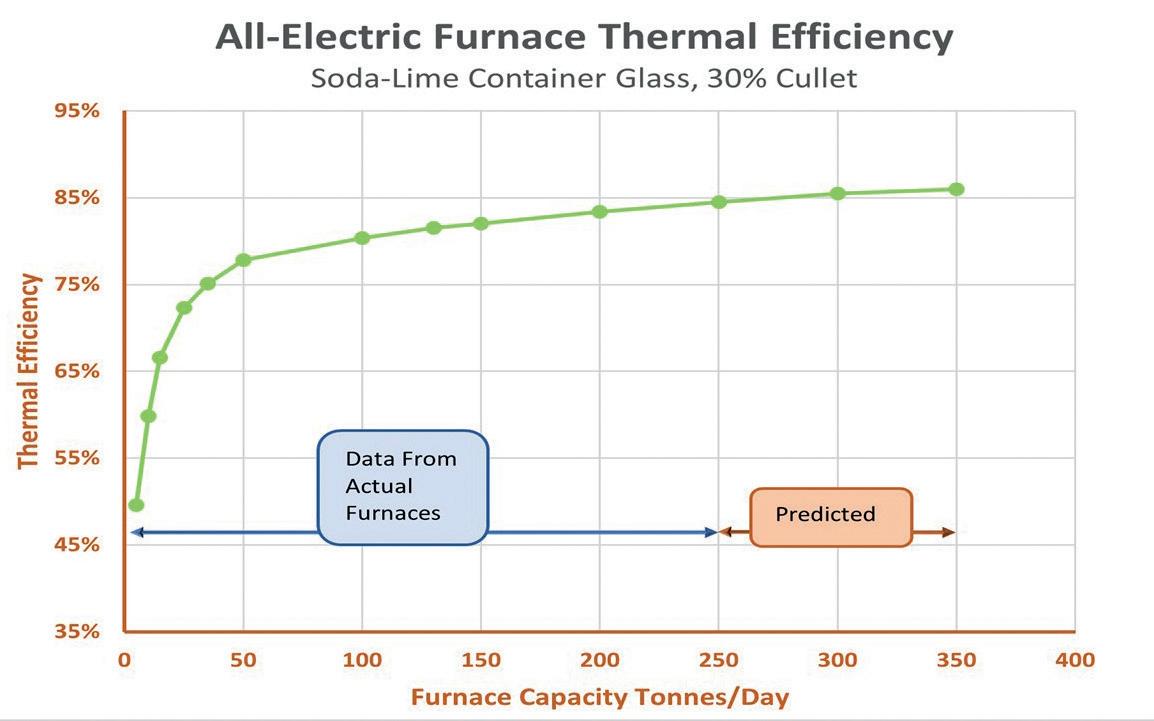
� Fig 5. All-Electric Furnace capacity and thermal efficiency.
as furnace pull is reduced to below its optimum (Fig 1).
A lot of attention has been given to ways of improving the performance of essentially fuel-fired furnaces in terms of both energy efficiency and emissions reduction, and there have certainly been improvements.
Oxy-fuel firing has been developed and used for a number of years and more recently firing with hydrogen has been a focus of technical papers and seminars. Both oxygen and hydrogen are abundant and all around us, but not in usable forms for combustion and energy release. They both require investment and processing to isolate, to store and transport.
When focusing on renewable glass manufacturing, we must not just look at reducing energy consumption but at the source of that energy and its sustainability – if it is renewable or non-renewable - and how we produce glass using renewable energy sources.
Primary energy sources
Primary energy sources may be grouped into non-renewable and renewable (Fig 2). Of these, only the non-renewables natural gas and oil can be used directly in the melting process, and they still account for the large majority of the industry’s melting energy consumption.
At the opposite end of the range of melting energy options to fossil fuels, in terms of both emissions and energy efficiency, stands electricity.
Electricity is readily produced using any of these renewable primary sources of energy. It is also the only practical form of glass melting energy that can be released directly into the glass itself, by means of immersed electrodes and joule-effect or resistance heating, with no associated carbon or nitrogen oxides gaseous emissions.
Nuclear energy, while technically nonrenewable, does not release harmful gases and is also quite readily used to generate electricity. As such, many consider it in a similar way to renewables.
Many sectors of the industry have been using electric melting furnaces and forehearths for decades, but others have not. Generally, the high volume sectors of the industry that have made less use of electricity and remain heavily dependent on non-renewable oil and gas.
Melting technology options
There is not one obvious path forward for the entire industry. Different sectors will continue to follow different approaches but sectors that are still heavily reliant on non-renewable fossil fuels all face the same basic choice. The first is to continue taking small steps in the same direction, which will no doubt yield further improvements in energy efficiency, and associated emissions reductions. The second is to truly focus on renewable energy and how to use it. For glass melting, in practice, that means electricity derived from the renewable primary energy sources. The high thermal efficiency of electric melting technology is proven and if that electricity is derived from renewal primary energy sources, there are no associated combustion gas emissions.
Electric boosting of fuel-fired furnaces is well established, and is typically used to increase furnace outputs by 20% to 50%. However, even 50% output uplift from electric boosting means that just 33% of that furnace’s output is being produced electrically.
A recent focus has been on the hybrid furnace approach - essentially using a high level of electric boosting in what may otherwise be a relatively conventional, horizontal, flow hot-top furnace (Fig 3). This certainly increases the proportion of potentially renewable melting energy derived from electricity. However, care is needed when considering the contribution proportions of electricity and fuel. In a furnace, in which (for example) 80% of the glass is deemed produced from electricity and 20% from gas, the ratio of energy usage can be different; only 65% of the total energy input being electric and 35% still coming from fuel. This is due to the very different thermal efficiencies of the two forms of heating.
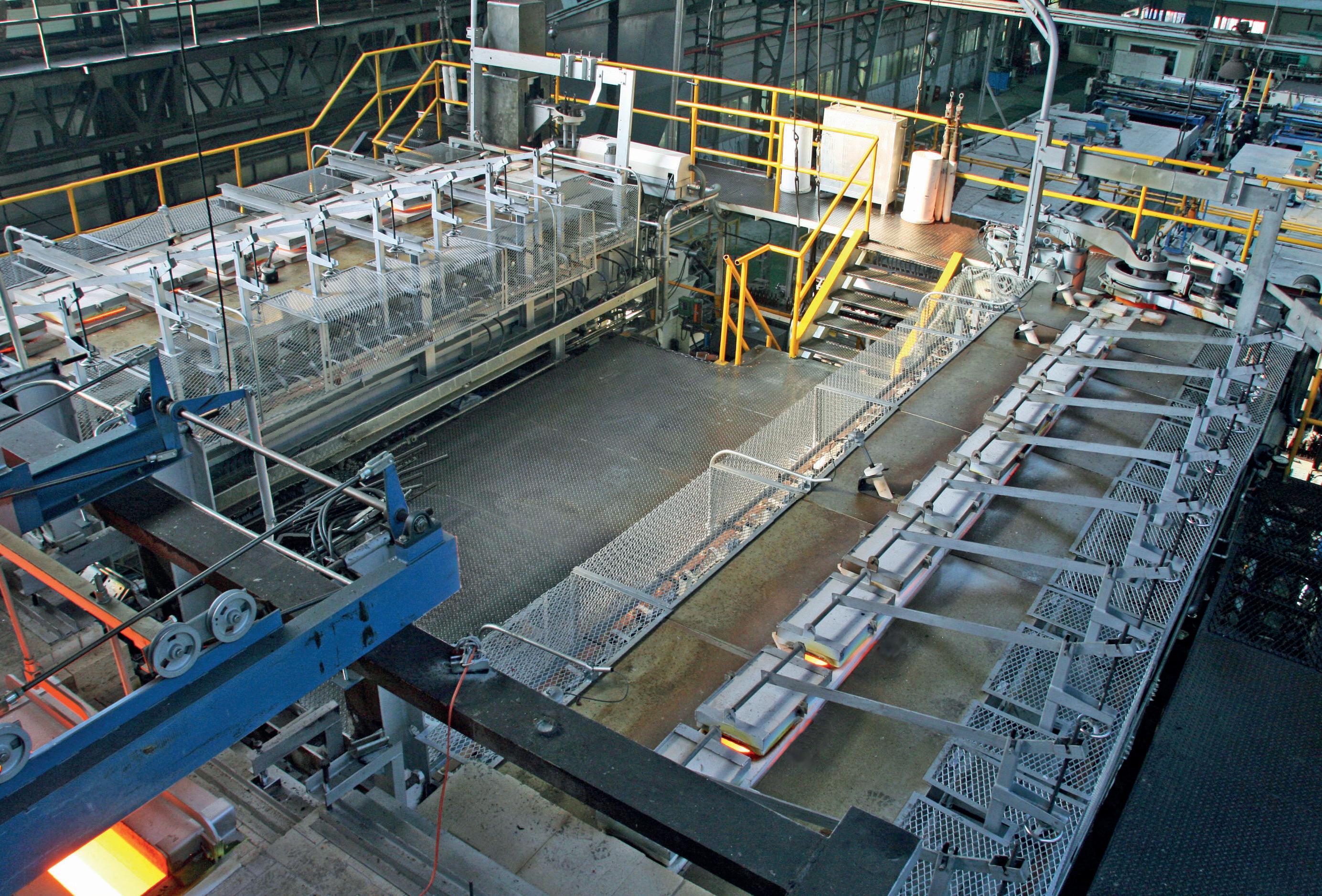
Fig 6. Container glass All-Electric Forehearths.�
To achieve a ratio of 80% electric to 20% fuel in terms of energy input rather than glass produced, the result is that approx. 90% of the glass melted is being produced electrically and just 10% by fuel. As this is still essentially a hot-top furnace with the inevitable high heat losses, from a hot and fuel-fired superstructure, it is much better to go fully electric and cold-top. Melting energy is released directly into the glass itself rather than by heat transfer from a fuel-fired superstructure, and an insulating batch blanket covers the entire surface of molten glass (Fig 4). The excellent thermal insulation provided by the batch blanket means a very low superstructure temperature and therefore very low heat losses. The result is greatly increased thermal efficiency.
The superstructure temperature in an Electroglass cold-top, all-electric melter, as shown in Fig 4, is approx. 100°C or less. Combustion gas emissions are also eliminated.
Furnace size
Energy is the biggest element in the cost of glass production, and the container glass sector (for example) has progressively adopted increasingly larger fuel-fired furnaces with a key objective of improving thermal efficiency and reducing that energy cost.
However, a well-designed, cold-top, all-electric container glass furnace does not need to be of comparable size to be efficient. Fig 5 shows the actual operating thermal efficiency of a range of Electroglass all-electric melters, from less than 10 tonnes/day to over 250 tonnes/ day capacity, all based on soda-lime glass and standardised to 30% cullet.
Even with a capacity of just 25 tonnes/ day, thermal efficiency is over 70%. At 50 tonnes/day it is approx. 78% and at 100 tonnes/day it has reached 80%, twice the thermal efficiency of most much larger fuel-fired furnaces.
Proven energy efficiency of an Electroglass 250 tonnes/day furnace is 84%, or just 700 kWh per tonne of glass produced. There is limited experience of electric furnaces larger than this, but current designs for 300 to 350 tonnes/ day can be only marginally more efficient than this. It is time to rethink the focus on furnace size as necessary for production efficiency, as well as the switch to clean, renewable energy. Two or three smaller, but highly efficient, electric furnaces could meet the goals of renewable energy use times three, minimising energy costs and eliminating environmentally harmful emissions.
Don’t forget the forehearths
The melting process understandably receives most of the attention in efforts to maximise thermal efficiency, reducing energy consumption and cost, and in assessing and comparing its environmental impact and sustainability. However, there is another key area where there is an established, proven and highly successful technology readily available to eliminate fossil fuel use, and its associated emissions, while greatly reducing energy consumption and operating costs.
All-Electric Distributors and Forehearths have been widely used in various industry sectors for decades, especially for the volatile glasses such as the borosilicates and fluoride opal compositions. They have also been successfully used in the container glass sector for a long time, but have received limited attention. This is rightly
� Fig 7. All-Electric Furnaces and Forehearths control panels in Electroglass’ workshops.
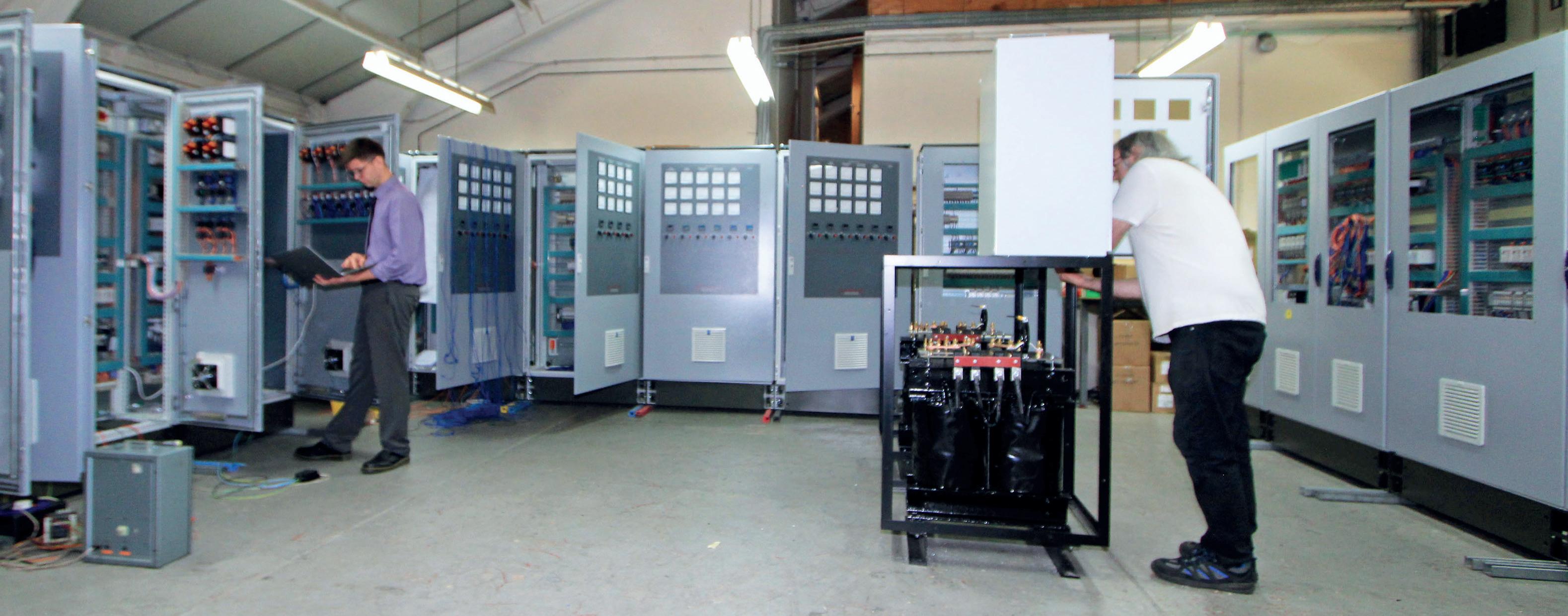
changing. In the large majority of cases, energy cost savings of between 60% and 90% are achieved with a well-designed, all-electric forehearth compared with its gas-fired equivalent, as demonstrated when the two forehearths in Fig 6; a 36inch channel and a 48-inch channel were converted from gas to electric heating.
In another series of projects for a major container-making group, involving eight forehearths that were converted from gas or newly installed, the operating energy cost savings compared with gas range from 71% (three highcapacity forehearths) through 75% (two forehearths) to 86% (three very high capacity forehearths). Such savings translate to rapid payback times, and, of course, the complete elimination of combustion gas emissions. These combined with thermal homogeneity results equal to or better than equivalent gas forehearths, precision temperature control and ease of operation. This makes electric forehearth technology the logical way forward for the industry, irrespective of the technology adopted for the melting furnace.
These are not isolated projects. The adoption of electric melting and conditioning in every sector of the industry is growing fast and with the ability to eliminate the use of fossil fuels, adopt renewable energy sources and reduce operating costs, this is not surprising. �
*Managing Director, Electroglass, UK http://www.electroglass.co.uk
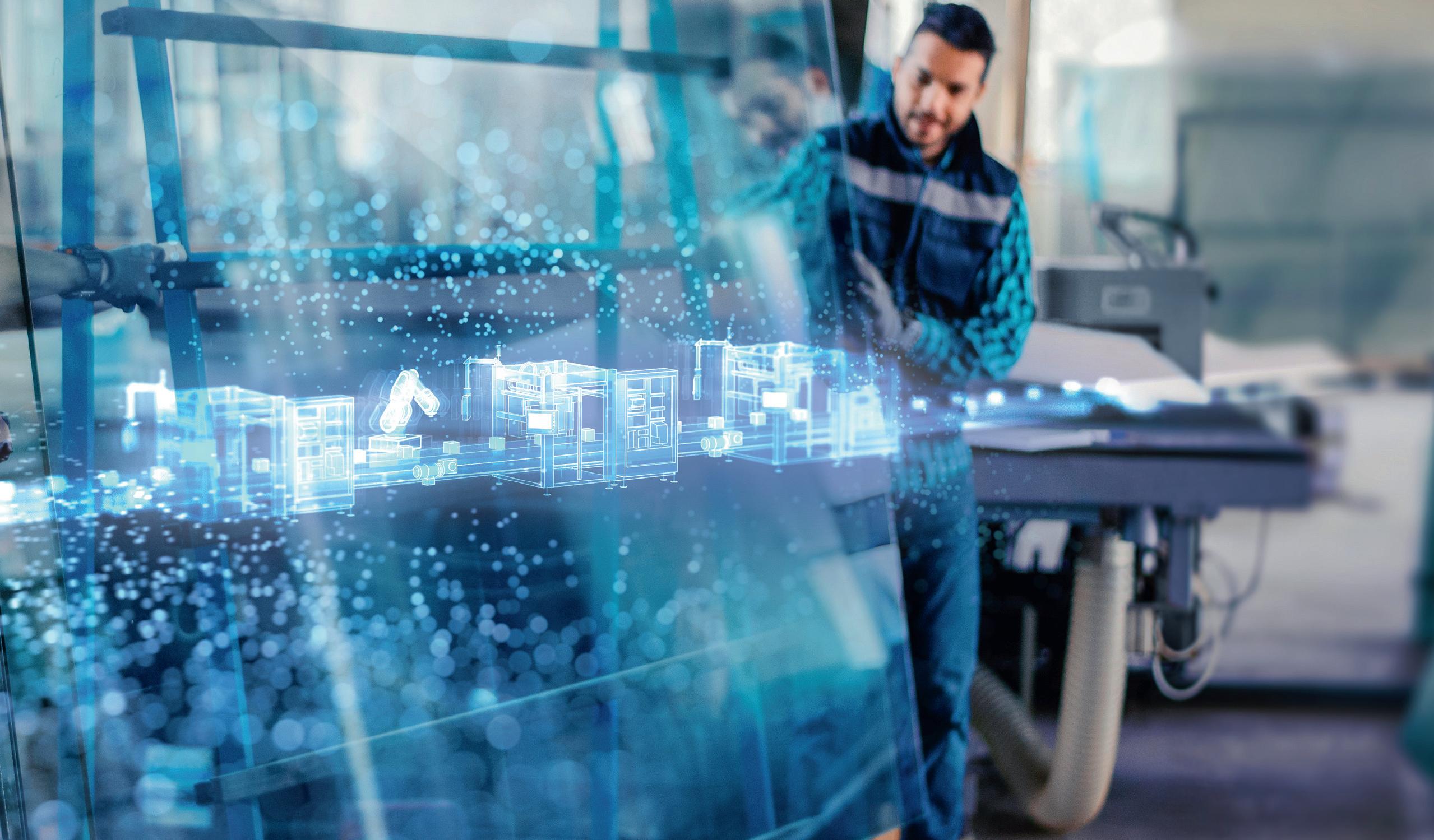
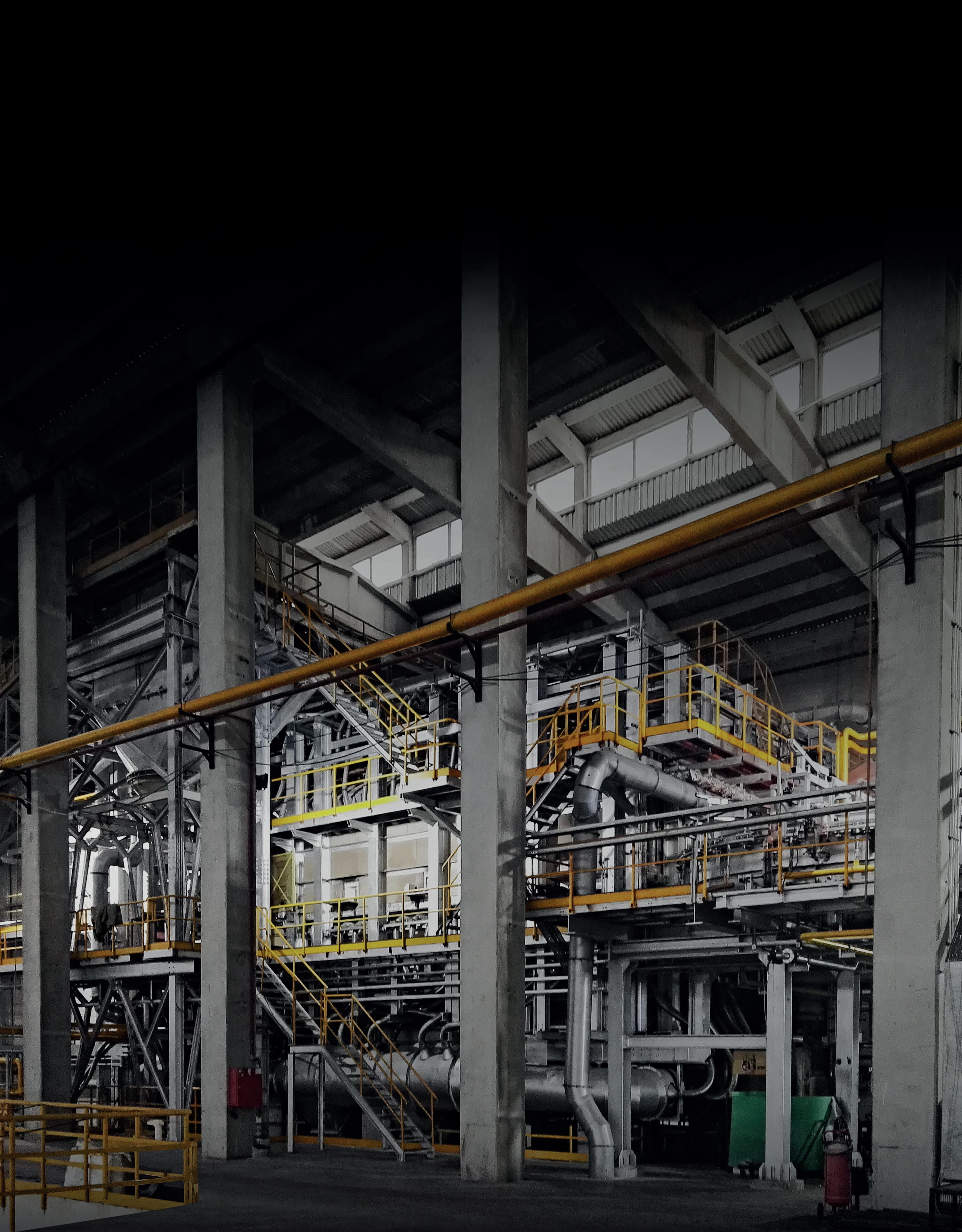